Разработка технологического процесса восстановления детали гитара для ткацкой машины типа СТБ




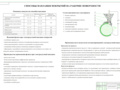
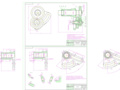
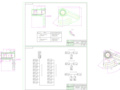
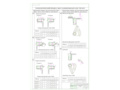
- Добавлен: 24.01.2023
- Размер: 1 MB
- Закачек: 0
Описание
Состав проекта
![]() |
![]() |
![]() |
![]() ![]() ![]() ![]() |
![]() ![]() ![]() ![]() |
![]() ![]() ![]() ![]() |
![]() ![]() ![]() ![]() |
![]() ![]() ![]() ![]() |
![]() ![]() ![]() ![]() |
![]() ![]() ![]() ![]() |
![]() ![]() |
![]() ![]() ![]() |
![]() ![]() ![]() |
![]() ![]() ![]() |
Дополнительная информация
НИЧ.dwg

Приспособление.dwg

Гитара.dwg

Техпроцесс.dwg

ремонт чертеж.dwg

Кинематическая схема.dwg

Компоновка ремонтного участка.dwg

Рекомендуемые чертежи
- 25.01.2023
- 24.01.2023
- 20.03.2015
- 24.01.2020