Разработка технологического процесса восстановления детали №130-3401065 Вал рулевой сошки DOC CDW DWG




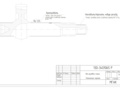
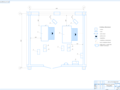
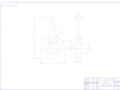
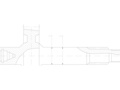
- Добавлен: 25.01.2023
- Размер: 710 KB
- Закачек: 0
Описание
Состав проекта
![]() |
![]() |
![]() ![]() |
![]() |
![]() ![]() ![]() |
![]() ![]() ![]() ![]() |
![]() ![]() ![]() |
![]() |
![]() ![]() ![]() |
![]() ![]() ![]() |
![]() ![]() ![]() |
![]() ![]() ![]() |
![]() ![]() ![]() |
![]() ![]() ![]() ![]() |
![]() ![]() ![]() |
![]() ![]() ![]() |
![]() ![]() ![]() |
![]() ![]() ![]() ![]() |
![]() |
![]() ![]() ![]() |
![]() |
![]() ![]() ![]() |
![]() |
![]() ![]() ![]() |
![]() ![]() ![]() |
![]() ![]() ![]() |
![]() ![]() ![]() |
![]() ![]() ![]() |
Дополнительная информация
Спецификация планировки.doc
Собственное изготовление
Тумбочка инструментальная
Станок круглошлифовальный
Механический участок
Планировка механического участка.cdw

- потребитель электроэнергии
-место складирования деталей
-подвод горячей и холодной воды
с отводом в канализацию
Механический участок
4 Заключение.docx
В процессе выполнения проекта изучены возможные способы восстановления детали изучена техника безопасности и охраны труда при выполнении ремонтных работ. Составленный маршрут восстановления детали позволяет избежать лишних переходов что позволяет повысить производительность труда и повышает качество ремонтируемой детали.
Выполнены ремонтный чертеж детали и планировка участка механической обработки составлена технологическая документация.
1 Титульный лист.doc
восстановления детали
№ 130 3401065 Вал рулевой сошки
МК-1.DOC
Код наименование операции
Обозначение документа
Код наименование оборудования
ХХ ХХ ХХ 005 4110 Токарная ИОТ № 63
Токарно- винторезный станок 16К20 2 19149 4 1Р 1 1 1 30 1
ХХ ХХ ХХ 010 4130 Шлифовальная ИОТ № 62
Станок круглошлифовальный 3У12А 2 19630 4 1Р 1 1 1 30 1
ХХ ХХ ХХ 015 9120 Наплавка в среде углекислого газа ИОТ № 48
Установка для дуговой наплавки в среде СО2 У-651 2 11620 3 1Р 1 1 1 30 1
ХХ ХХ ХХ 020 7171 Хромирование ИОТ № 49
Ванна для хромирования
Ванна улавливания электролита 2 18355 3 3 1 1 1 30 1
ОК ТОкарная.DOC
Вал сошки рулевого управления
Наименование операции
Оборудование устройство ЧПУ
Обозначение программы
Токарно-винторезный станок 16К20
мм мм мм - ммход мммин мин-1 мс
Установить деталь в патрон станка и закрепить.
Центра ГОСТ 13212-79. Хомутик Патрон поводковый ГОСТ 13334-67
Шлифовать изношенные шейки выдерживая размер.L=170 мм
Круг ПП400-40СМ1-СМ3 Скоба 3783 мм ГОСТ 18355-73
Снять деталь и уложить в тару.
Контроль рабочим 25%
МК-2.DOC
Код наименование операции
Обозначение документа
Код наименование оборудования
ХХ ХХ ХХ 025 4130 Шлифовальная ИОТ № 62
Станок круглошлифовальный 3У12А 2 19630 4 1Р 1 1 1 30 1
ХХ ХХ ХХ 030 4110 Токарная ИОТ № 63
Токарно- винторезный станок 16К20 2 19149 4 1Р 1 1 1 30 1
ХХ ХХ ХХ 025 Контрольная ИОТ № 85
Стол ОТК 4 3 1О 1 1 1 20 1
0.1 Титульный.doc
Учреждение образования
«Минский государственный автомеханический колледж»
-370106 Техническая эксплуатация автомобилей
Разработка технологического
процесса восстановления детали № 130-3401065
Пояснительная записка
Вал сошки.dwg

Размер шеек под сальник и опорных шеек по рабочему чертежу ø 38
Размер резьбовой шейки по рабочему чертежу М27-1
5 Список использованных источников.docx
Барановский Ю.В. Режимы резания металлов. Справочник. Изд. 3-е переработанное и дополненное. – М.:«Машиностроение» 1972 г. – 363 с.
Карагодин В.И. Ремонт автомобилей и двигателей: Учеб. для студ. сред. проф. учеб. заведений В. И. Карагодин Н. Н. Митрохин. - 2-е изд. стер. -М.: Издательский центр «Академия» 2003. - 496 с.
Ремонт автомобилей: учебник для автотранспортных техникумов Румянцев С.И. и др.;Под редакцией Румянцева С.И.- 2-е изд.перераб. И доп.-М.: Транспорт1988.-237 с.:ил.табл.
Скепьян С.А.Курсовое проектирование:учеб.пособиеС.А.Скепьян.-Минск:Новое знание ;М.:ИНФРА-М2011.-235с.:ил.(среднее проффесиональное образование)
Ярошевич В.К.Технология производства и ремонта автомобилей: учеб. пособие В.К. Ярошевич А.С. Савич В.П. Иванов.- Минск: Адукацыя и выхаванне2008.-640 с.
Проектирование предприятий автомобильного транспорта: учеб. Для студентов специальности «Техн. эксплуатация автомобилей» учреждений обеспечивающих получение высш. образования М.М. Болбас [и др.]; под ред. М.М. Болбаса.- Мн.: Адукацыя i выхаванне 2004.- 528 с.: ил.
Охрана труда: учеб. пособие А.А. Челноков Л.Ф. Ющенко.-3-е изд. испр. -Минска: Выш. Школа.2007.-463 с.
3 Конструкторская часть.docx
1 Анализ существующих конструкций приспособления
При выборе хомутика необходимо следить за тем чтобы конец детали на которую надевается хомутик свободно входил в отверстие хомутика. В то же время при слишком большом отверстии самозажимной хомутик не сработает а у обыкновенного хомутика зажимной болт будет скользить по цилиндрической поверхности обрабатываемой детали и согнется.
Если хомутик надевается на обработанный конец детали то чтобы не испортить поверхности ее между деталью и стенками отверстия в хомутике и под зажимной болт его кладут медную прокладку или обертывают конец детали медной полоской.
2 Назначение устройство и принцип действия приспособления
Передачу вращения от шпинделя к обрабатываемой заготовке установленной в центрах станка 6 осуществляют с помощью хомутика. Более удобен в работе самозатягивающий хомутик в котором хвостовик 1 закреплен в корпусе 2 подвижно на оси . Нижняя часть хвостовика обращенная к заготовке выполнена эксцентрично по отношению к оси и имеет насечку. Для установки хомутика на заготовку вал 5 хвостовик 1 наклоняют в сторону пружины 4 которая после установки хомутика предварительно затягивает заготовку хвостовиком. В процессе обработки палец-поводок 3 патрона производит окончательную затяжку заготовки хвостовиком пропорционально силе резания.
3 Технико-экономическое обоснование конструкции приспособления
Экономическая целесообразность выбора и применения станочных приспособлений в любом производстве особенно в серийном и массовом определяется их окупаемостью. Все затраты на оснащение производства приспособлениями должны быть компенсированы за счет экономии производственных затрат. В общем виде экономическая целесообразность применения приспособлений может быть выражена в ожидаемой экономии при применении приспособления к затратам на изготовление приспособления и на его эксплуатацию.
Целесообразность оснащения производственного процесса специальными приспособлениями подтверждают расчетом.
Для снижения себестоимости изготовления приспособления и сменных наладок в их составе следует широко использовать стандартизованные узлы и детали.
Важным показателем совершенства конструкции является условие равной прочности и равной долговечности всех элементов поскольку наличие в конструкции хотя бы одного недостаточно долговечного элемента снижает надежность конструкции в целом. Главное на что было обращено внимание при проектировании - чтобы ни один из этих элементов не выходил из строя раньше намеченного срока очередного планового ремонта.
Экономические аспекты при проектировании проявляются при выборе материалов термообработки упрочняющей технологии формы и способы изготовления детали. Технологичность деталей и узлов является одним из важнейших условий в создании приспособлений с оптимальными технико-экономическими показателями. При серийном производстве наиболее экономичным является формообразование деталей (частичная или кончательная) методом литья или пластическим деформированием (обработка давлением) в отличии формообразования снятием стружки.
При этом ускоряется процесс производства уменьшается расход материалов и снижаются затраты на электроэнергию и инструмент.
Поскольку до 50% общей трудоемкости изготовления приспособлении падает на сборочные операции а от качества сборки в большей степени зависит качество приспособления. Для осуществлению удобной сборки и разборки были исключены ручные операции неправильное взаимное положение сопряженных
узлов (например с помощью штифтов и болтов устанавливаемых без зазора). Было уменьшено число деталей сделана удобная компоновка узлов с легко доступными местами крепления.
Экономичность надежность долговечность к.п.д. и другие показатели приспособления в большей степени зависят от изнашивания рабочих поверхностей. Трение и изнашивание наносят огромный ущерб народному хозяйству. Установлено что 85 90% машин выходят из строя в результате изнашивания деталей и только 10 15% - по другим причинам например из - за поломок которые в свою очередь являются следствием изменения условий работы вызванное износом сопряженных поверхностей который снижает их изгибную прочность и выносливость. Предусмотрены защитные устройства предупреждающие попадание абразивных частиц в зону контакта.
При оценке экономичности приспособления учтены затраты на материалы изготовление и эксплуатацию поскольку одним из важных показателей при такой оценке является массогабаритный характер.
приспособа А2.dwg

Хомутик самозахватывающий Сборочный чертеж
на КД.dwg

0.3Введение.doc
Анализ состояния ПТБ предприятий автомобильного транспорта Беларуси показывает что оно во многих случаях не соответствует нормативному уровню: недостаточно производственных площадей низок уровень механизации технологических процессов технического обслуживания и ремонта. ПТБ автотранспортных предприятий в своем развитии отстает от требований обуславливаемых изменениями в структуре парка подвижного состава.
В развитии авторемонтного производства страны важную роль сыграла целенаправленная работа заводов-изготовителей по повышению ресурса рам кабин и кузовов что способствовало резкому снижению объемов капитального ремонта полнокомплектных автомобилей. Эта тенденция вызывает изменение функций авторемонтных предприятий которые становятся преимущественно предприятиями по капитальному ремонту агрегатов.
Наряду с развитием традиционных ведомственных АРП производственные объединения автомобильной промышленности внедряют фирменные системы обслуживания и ремонта новых моделей.
В соответствии с такими тенденциями в сфере авторемонтного производства основными задачами его дальнейшего развития и совершенствования являются:
повышение технического уровня действующих АРП углубление их специализации и развитие производственных связей по кооперации;
увеличение объемов ремонта в связи с ростом производства автомобилей;
освоение ремонта автомобилей (составных частей) новых моделей;
внедрение новых прогрессивных технологических процессов и оборудования.
Развитие авторемонтного производства предусматривает строительство новых реконструкцию и техническое перевооружение действующих АРП.
Целью данного курсового проекта является разработка технологического процесса восстановления детали № 130 3401065 Вал рулевой сошки
1 Общая часть.docx
Вал рулевой сошки №130-3401065 расположен в корпусе рулевого механизма рулевого управления.
Вал сошки изготовлен за одно целое с зубчатым сектором которым входит в зацепление с рейкой. На валу имеются шлицы на которые устанавливается сошка и передается вращающий момент. Также имеется резьбой конец для крепления сошки к валу посредством гайки. На другом торце выполнено отверстие для стопорного кольца и установки регулировочного винта. На валу имеется поверхность под сальник и поверхность для втулки вала(для установки в корпус картера)
Вал рулевой сошки изготовлен из стали 25ХГТ. Химический состав механические технологические и эксплуатационные свойства материала детали приведены в таблицах 1.1 1.2 и 13.
Таблица 1.1- Химический состав стали 25ХГТ ГОСТ 4543-71
Наименование и марка материала
Химический элемент и его процентное содержание %
Таблица 1.2 – Механические свойства стали 25ХГТ ГОСТ 4543-71
Временное сопротивление при растяжении В МПа
Относительное удлинение Л%не менее
Таблица 1.2 – Технологические и эксплуатационные свойства стали 25ХГТ
Наименование и марка
термической обработки
Обрабатываемость резанием
Свариваемость при восстановлении
0-950 С0 воздухзакалка850 С0 масло отпуск 200 С0 вода .
2 Технические требования на дефектацию детали
Исходным документом для разработки технологического процесса восстановления детали является «Карта технических требований на дефектацию детали» в которой приводятся следующие требования: общие сведения о детали перечень возможных ее дефектов способы выявления дефектов допустимые без ремонта размеры детали и рекомендуемые способы устранения дефектов.
Таблица 3-Карта технических требований на дефектацию детали
Наименование детали
(сборочной единицы): Вал рулевой сошки
№ детали по каталогу:
(обозначение по чертежу)
(наименование марка номер стандарта
Способ установления дефекта и средства контроля
Допустимый без ремонта
Осмотр. Кольцо резьбовое М27х15
Повреждение не более 2х витков
Вибродуговая наплавка
Износ шеек под сальник(2) и опорных шеек вала(3)
Сварка в среде углекислого газа
Ремонтный вала рулевой сошки представлен в приложении А.
3 Дефекты и причины их возникновения
Вал рулевой сошки является ответственной деталью рулевого механизма и в процессе эксплуатации он испытывает знакопеременные нагрузки передаваемые от рулевой трапеции. В результате чего теряет свои эксплуатационные свойства и происходи изменение размеров поверхностей скручивание изгиб.
Дефект 1 – Срыв или износ резьбы- следствие частой разборки-сборки неправильной затяжки несносность вала и сошки.
Дефект 2 – Износ шеек под сальник и опорных шеек вала– следствие сухого трения биения в результате повышенных вибраций.
4 Технические требования к отремонтированной детали
Основными поверхностями вала рулевой сошки подвергающимися износу являются шеек под сальник и опорных шеек вала а также резббовая поверхность
После ремонта размер шеек под сальник и опорных шеек вала должен соответствовать размерам рабочего чертежа: а именно
- диаметр должен быть мм . Размер соответствует 7 квалитету точности с отклонением f т.е. диаметр мм. Шероховатость поверхности Ra=1.25 мкм соответствует 7 классу шероховатости.
- резьбовая поверхность должна соответствовать размеру М27х15 .Размер соответствует 6 квалитету точности с отклонением g.
5 Выбор размера партии деталей
В условиях серийного ремонтного производства (по опыту ремонтных предприятий) размер партии принимают равным месячной или квартальной потребности в ремонтируемых или изготавливаемых деталях.Месячная программа восстанавливаемых по маршруту деталей N мес.определяется по формуле
N мес. =Na Kp n 12 (1.1)
гдеNа – годовая производственная программа ремонта агрегатов или автомобилей шт.; Кр – коэффициент ремонта (принимается по данным авторемонтного предприятия); n – число одноименных деталей на автомобиле шт.
N мес. =8500 07 1 12=495 шт.
Размер партии деталей (должен быть равен числу кратному 5) Zравен
где Х – число запусков в месяц (принимается не более трех);
2 Технологическая часть.docx
Вал рулевой сошки перемещается по производственным участкам завода согласно маршруту № 1. На данном маршруте устраняются дефекты: износ шеек под сальник и опорных шеек вала срыв или повреждение резьбы.
Вал рулевой сошки относится к классу круглые стержни к 4 группе (валы шлицевые)
2 Выбор рационального способа восстановления детали
Выбор способа восстановления деталей зависит от их конструктивно-технологических особенностей и условий работы износа технологических свойств самих способов восстановления определяющих долговечность отремонтированных деталей и стоимость их восстановления и применяемость способа. Выбор рационального способа восстановления представлен в таблице 2.1.
Таблица 2.1 – Выбор рационального способа восстановления детали
Номер и наименование дефекта
Принятый способ ремонта
- Срыв или повреждение резьбы
- Износ шеек под сальник и опорных шеек вала
Из потенциально возможных способов восстановления по критериям применимости долговечности и экономичности принимаем для 1 дефекта способ НУГ(Наплавка в среде углекислого газа) для 2-Х (хромирование железнение рекомендуется при износе более 015 мм)
3Выбор технологических баз
Технологическая база-это поверхность ось точка детали посредством которой производиться ее установка на станке или в приспособлении относительно режущего инструмента
При восстановлении вала рулевой сошки технологическими базами будут являться центровые отверстия и шейка
4 Технологические схемы устранения каждого дефекта
На устранение каждого дефекта детали разрабатывается технологический процесс. Схема подефектного устранения группы дефектов вала рулевой сошки представлена в таблице 2.2.
Таблица 2.2–Схема подефектного технологического процесса устранения дефектов
Наименование и содержание операции
Срыв или повреждение резьбы
Точить изношенную резьбу
Наплавить изношенную поверхность
Точит поверхность под резьбу
Центровые отверстия шейка
степень точности 4 h
Износ шеек под сальник и опорных шеек вала
Шлифовать изношенные шейки для удаления износа и восстановления геометрической формы
Хромировать шейки вала сошки
Шлифовать шейки вала сошки в номинальный размер
Центровые отверстия шейка
5 Определение промежуточных припусков допусков и размеров
Дефект – Износ шеек под сальник и опорных шеек вала. Диаметр отверстия по чертежу равен . Материал детали 25ХГТ ГОСТ 4543-71. Длина вала сошки равна мм. Шероховатость обработанной поверхности равна Ra 12.Диаметр изношенного отверстия .
Определение промежуточных припусков и размеров для следующего технологического процесса:
Шлифовальная1. Шлифовать изношенные шейки вала сошки
Хромирование1.Хромировать шейки вала сошки
Шлифовальная1.Шлифовать шейки в номинальный размер.
Диаметр шеек по после шлифования равен размеру по рабочему чертежу
Диаметр отверстия после хромирования d1. мм равен
где2h-припуск на шлифование
Принимаем 2h= 04 мм .Тогда
Диаметр шеек после шлифования dоравен
где2ho-припуск на шлифование
Принимаем 2h0= 01 мм .Тогда
Припуск на хромирование 2hХмм равен:
Дефект – Срыв или повреждение резьбы. Размер по чертежу равен М15х15. Материал детали 25ХГТ ГОСТ 4543-71. Длина резьбового конца равна 30 мм.
Токарная1. Точить изношенную резьбу
Наплавка1.Наплавить резьбовой конец вала
Токарная 1.Точить поверхность под резьбу
Нарезать резьбу М27-15 6g
Размер резьбовой шейки перед нарезанием резьбы равен
Диаметр вала после наплавки d1. мм равен
где2h- припуск на точение
Принимаем 2h= 2 мм .Тогда
Диаметр шейки после точения изношенной резьбы dоравен
где2ho-припуск на чистовое точение
Принимаем 2h0= 2 мм .Тогда
Припуск наплавку в среде углекислого газа 2hУмм равен:
6 Технологический маршрут восстановления детали
Разработка процессов восстановления детали производится по маршрутной технологии что способствует рациональному использованию оборудования экономии энергоресурсов и исключению встречных потоков перемещения деталей по производственным участкам ремонтного предприятия.
Под маршрутной понимается технология составленная на комплексе дефектов а маршрутом называется последовательность выполнения технологических операций с минимальными перемещениями детали.
При разработке маршрутов восстановления деталей необходимо руководствоваться следующими принципами:
- сочетание дефектов в каждом маршруте должно быть действительным и базироваться на результатах исследования закономерностей появления дефектов данной детали;
- маршрут должен предусматривать технологическую взаимосвязь сочетаний дефектов со способами восстановления;
- количество маршрутов восстановления детали должно быть минимальным;
- восстановление деталей по маршрутной технологии должно быть экономически целесообразным и учитывать технологическую необходимость и возможность восстановления отдельных поверхностей.
. Технологический маршрут ремонта крышки подшипника опоры промежуточного вала оборудование и оснастка представлены в таблице 2.3
Таблица 2.3 -Технологический маршрут ремонта оборудование и оснастка
операции (по переходам)
Приспособление и вспомогательный инструмент
Установить деталь в центра и закрепить
Точить изношенные резьбу выдерживая размер Ra = 125 мкм.L=35 мм
Снять деталь и уложить в тару
Токарно- винторезный станок 16К20
Патрон поводковый ГОСТ 13334-67
Проходной резец Т16К6.
Штангенциркуль ШЦ 1-125-01 ГОСТ 166-88-
Установить деталь и закрепить
Шлифовать изношенные шейки выдерживая размер
Станок кругло шлифовальный
ГОСТ 13212-79.Хомутик
Круг ПП600-40СМ1-СМ3
00 Наплавка в среде углекислого газа
Установить деталь и закрепить
Наплавит резьбовую шейку выдерживая размер L=35мм
Установка для дуговой наплавки в среде СО2 У-651.
Источник тока ПСУ-500
Проволока ПП-АН-122.
Штангенциркуль ШЦ1-125
Установит деталь в подвеску и закрепить
Хромировать поверхность шеек выдерживая размер мм
Ванна хромирования. Ванна обезжиривания. Ванна улавливания электролита(собств. изгот.)
Подвеска специальная.
Загрузочное устройство.
Шлифовать шейки вала в номинальный размер d=. мм.
Круг ПП400-40х306СМ1-СМ3
Точить наплавленную шейку выдерживая размер d=272 мм
Нарезать резьбу М27х15 6g
Кольцо резьбовое М27-6g
Проверить размер d= Ra = 1.25 мкм.
Проверить 3 отверстия . равномерно расположенных по окружности.L=20 мм
7 Выбор оборудования и технологической оснастки
Выбор оборудования осуществляют с учетом обеспечения оптимальной производительности при условии обеспечения требуемого качества восстановления деталей. В соответствии с необходимым оборудованием по каждой операции технологического процесса осуществляется подбор технологической оснастки режущего и измерительного инструмента.
Для выполнения токарных работ выбираем токарно-винторезный станок 16К20.КПД 075.Крепление детали производим в трехкулачковом патроне. Растачивание производим проходным резцом. В качестве измерительного инструмента выбираем микрометр и образцы шероховатости.
Для шлифовальных работ выбираем круглошлифовальный станок 3У12А. Деталь крепиться в патроне и обрабатывается шлифовальным кругом. Наибольший диаметр устанавливаемой заготовки - 200мм длина - 500 мм скорость перемещения стола (003 50 ммин). Режущий инструмент для данной операции шлифовальный круг ПП400х40х306. Мощность электродвигателя – 3кВт. КПД станка – 075.
Для хромирования выбираем ванны для хромирования обезжиривания и улавливания электролита. Также используется подвеска специальная загрузочное устройство таль Q=025.
Для наплавки в среде углекислого газа выбираем установку для дуговой наплавки в среде СО2 У651. Источник тока ПСУ-500 .Проволока ПП-АН-122.
8 Расчет режимов обработки
Расчет режимов обработки определяют для операций с разбивкой их на переходы.
Точить изношенные резьбу выдерживая размер Ra = 125 мкм.L=30 ммОпределить режимы резания при растачивании изношенной поверхности под сальник перед запрессовкой ДРД на токарно – винторезном станке 16К20.
По нормативам принимаем проходной прямой резец с пластинкой Т16К6 и геометрическими параметрами: φ = 90°; γ = 0°; λ =+5°; φ1 = 5° и резьбовой резец с геометрическими параметрами: φ = 60°; γ = 10°
Определение припуска на обработку на сторону
где - диаметр детали после и до обработки
=27 мм =25 мм (из расчета припусков на обработку)
Определение числа переходов i: i =1
Определение глубины резания t мм:
Определение стойкости резца с твердосплавной пластиной Тр мин: Тр=50 мин
Определение оборотной теоретической подачи инструмента ммоб
Корректируем по паспорту станка: S0 = 08 ммоб
Определение скорости резания v ммин :
v = vтабл · k1 · k2 · k3 (2.3)
где vтабл – табличное значение скорости резанияммин
k1 – коэффициент зависящий от обрабатываемого материала;
k2 – коэффициент зависящий от стойкости инструмента;
k3 – коэффициент зависящий от отношения длины резания к диаметру.
Принимаем :vтабл = 93 ммин; k1 = 1; k2 = 12; k3 = 0.8.
v = 93 · 1 · 12 · 1 =89.28 ммин
Определение теоретической частоты вращения шпинделя :
Принимаем фактическое( паспортное) значение частоты вращения шпинделя:
Определение фактической скорости резания:
Определение осевой силы резания Рz кг
Рz = Ртабл ·К1·К2 (2.6)
где Рz табл-табличное значение значение силы резаниякгс
К1К2 – коэффициент зависящий от обрабатываемого материала коэффициент зависящий отскорости резания и переднего угла
Принимаем :Ртабл = 170 кг;К1 = 085; К2 = 11
Ртабл =170·085·11=15895 кгс
Определение мощности резания Nрез кВт
Nрез =PzVФ6120 (2.7)
Nрез=1589584786120=22
Приверка достаточность мощности станка:
гдеNДВ-мощность электродвигателя
Принимаем :NДВ=10 кВт;
Реализация назначенного режима возможна
Шлифовать изношенные шейки выдерживая размер Ra=16 мкм
Расчет скорости шлифовального круга
n – число оборотов круга по станку
Расчет скорости и числа оборотов детали
Скорость детали Vдет=40ммин
где d—диаметр детали
Уточняем по паспорту станка
где —доля ширины шлифовального круга (025 05)
где l—длина шлифования
Sм= Sм(табл)К1К2К3 (2.13)
где Sм(табл)—минутная подача по таблице
К1—коэффйициент зависящий от обработанного материала и скорости круга
К2—коэффйициент зависящий от припуска и точности
К3—коэффйициент зависящий от диаметра круга количества кругов и характера поверхности
Sм=065·11·09·1=064 мммин
Слой снимаемый при выхаживании
5 Наплавка в среде углекислого газа
Наплавить резьбовую шейку выдерживая размер L=25мм
Марка проволоки НП 40.
Диаметр проволоки dэ=16
Плотность тока Da = 96 Амм2.
Сила сварочного тока I А :
I = 0785 dэ2 · Da (2.14)
I = 0785 162 · 96 = 19292 А
Масса расплавленного метала G р.м. гмин равен:
G р.м. = I · αн60 (2.15)
G р.м. = 19292 · 11160 = 3555 гмин
Объем расплавленного металла Q р.м. см3мин равен:
Q р.м. = G р.м.γ(2.16)
Q р.м. = 3555785 = 452см3мин
Скорость подачи электродной проволоки Vпр ммин равна:
Vпр = Q р.м.0785 · dэ2(2.17)
Vпр = 4520785 · 162 = 226 ммин
Скорость наплавки Vн ммин равна:
Vн = (0785 · dэ2 · Vпр · К · а)(t · S) (2.18)
Подача (шаг наплавки)
Vн = (0785 · 162 ·226·086·092)(16 · 25) = 09 ммин
Частота вращения детали n мин-1
n = 1000 · Vн · d (2.19)
n = 1000 · 09314 · 292 =981 мин-1
Принимаем n = 10 мин-1
Полярность обратная напряжение 28 В
Род тока постоянный
Вылет электрода 8 11мм
Смещение электрода 2 4 мм
Хромировать поверхность шеек выдерживая размер мм.L=120
Параметры режима обработки следующие
h-толщина слоя h=025 мм
p-плотность осажденного металла p=71 гдм3
Dk-катодная плотность тока Dk=50 А
c-электролитический эквивалент с=0342
-выход металла по току =11 32 %
9 Расчет норм времени
Оперативное время мин :
где-основное время мин; -вспомогательное время мин.
Основное время определяется по формуле
где-длина рабочего хода инструмента мм;
-фактическая подача инструмента за один оборот детали ммоб;
- фактическая частота вращения деталимин-1 ;i- количество переходов.
Принимаем: мм=08 =250 i=1
Вспомогательное время на операцию на операцию мин
где- вспомогательное время на установку-снятие детали мин;
- вспомогательное время на переход мин;
вспомогательное время на замеры детали
Принимаем: =2 мин =016 =016
Дополнительное время мин :
где- процент от оперативного времени на организационно-техническое обслуживание рабочего места отдых и личные надобности соответственно%
Штучно-калькуляционное время мин
где- подготовительно-заключительное время мин ; Z-число деталей в партии.
Принимаем: =10 мин Z=495
где-длина шлифования детали
h-припуск на обработку на сторону мм;
-коэффициент зачистных ходов;
- поперечная минутная подача.
- продольная подача;
- частота вращения детали.
Принимаем: =170; h=05;=17 =064; =20;
11 Требования техники безопасности при проведении восстановительных работ
Согласно задания необходимо рассмотреть требования безопасности при шлифовальной операции на участке механической обработки.
Хранение и транспортировка абразивного инструмента осмотр установка его на станках а также эксплуатация должны соответствовать требованиям ГОСТ 2447-82 "Головки шлифовальные. Технические условия"
Устанавливать абразивные круги на станки разрешается только специально обученным рабочим.
Перед установкой все круги должны быть отбалансированы. При обнаружении дисбаланса круга после первой правки или в процессе работы он должен быть повторно отбалансирован. Отрезные и обдирочные круги перед их установкой на станок разрешается не балансировать.
При установке абразивного круга необходимо между фланцами и кругом устанавливать прокладки из картона или другого эластичного материала толщиной 05 - 1 мм. Прокладки должны выступать за фланец по всей окружности на 1 - 5 мм.
Перед началом работы круг установленный на шлифовальный станок должен быть проверен на ходу (вхолостую) при рабочем числе оборотов: круг диаметром до 400 мм - не менее 2 минут свыше 400 мм - не менее 5 минут.
К работе можно приступать только убедившись в том что круг не имеет биения а биение шпинделя шлифовального станка не превышает 003 мм.
Защитный экран по отношению к кругу должен располагаться симметрично. Ширина экрана должна быть больше высоты круга не менее чем на 150 мм. Конструкция экрана должна предусматривать поворот вокруг оси для регулирования его положения в зависимости от величины обрабатываемой детали и износа шлифовального круга в пределах 20° исключая полное его откидывание. Поворот экрана на угол более 20° должен быть сблокирован с пуском шпинделя станка. При невозможности использования стационарного защитного экрана должны применяться защитные очки или защитные козырьки закрепленные на голове рабочего.
Испытания установка и правка абразивных кругов производятся специально назначенными и подготовленными рабочими или мастером.
принимать круги без отметки об их испытании;
производить правку кругов неспециальным инструментом;
при обработке изделий шлифовальным кругом применять рычаги для увеличения нажима на круг;
использовать в качестве охлаждающих жидкости вредно влияющие на здоровье рабочих или механическую прочность круга;
выполнять работу боковыми (торцовыми) поверхностями кругов специально не предназначенных для такого вида работ;
работать на станке у которого установлены два круга на одном шпинделе если размер одного круга по диаметру отличается от другого более чем на 10%.
При уменьшении диаметра круга вследствие его срабатывания число оборотов круга может быть увеличено но так чтобы не превышалась окружная скорость допустимая для данного круга.
В организации где применяется абразивный инструмент должны быть утверждены инструкции:
по установке и эксплуатации абразивного инструмента;
по испытанию кругов на прочность.
Для поддержки изделий подаваемых к шлифовальному (заточному) кругу вручную должны применяться подручники или заменяющие их приспособления. Подручники должны быть передвижными позволяющими устанавливать их в требуемом положении по мере срабатывания круга.
Шлифовальные станки при работе без охлаждения должны быть оснащены пылеотсасывающими устройствами.
Абразивные круги во время работы должны ограждаться кожухами. Работать без защитного кожуха не допускается. Кожухи изготавливаются из стального литья или листовой стали в соответствии с ГОСТ 12.3.028-82.
Круги диаметром 30 мм и более кроме кругов типов ПН ПР К и М а также все круги диаметром 150 мм и более перед установкой на станок должны испытываться на прочность при скорости и продолжительности вращения указанных в ГОСТ 12.3.028-82.
Круги подвергшиеся какой-либо механической переделке химической обработке не имеющие маркировки а также срок гарантии которых истек непосредственно перед установкой на шлифовальный станок должны быть испытаны на
У каждого станка на видном месте должна быть вывешена таблица с указанием допустимой рабочей окружной скорости используемого абразивного круга и числа оборотов в минуту шпинделя станка.
У каждого станка должна быть вывешена табличка с указанием лица ответственного за его эксплуатацию.
11 Технологическая документация
Маршрутная карта является основным документом в котором указываются все операции в порядке их выполнения выбранное оборудование информация о детали нормы времени и др.
Операционная карта предназначена для описания операции с указанием переходов информации о технологической оснастке и режимах обработки.
В данном курсовом проекте составлена маршрутная карта и операционная карта на одну из операций технологического процесса. Комплект технологических документов представлен в приложении Б.
12 Расчет годового объема работ
При проектировании участка восстановления деталей (механического) годовой объем работ чел-ч определяется по формуле
гдеt- трудоемкость восстановительной операции чел-ч;
n- количество одноименных деталей в агрегате или автомобиле шт;
N- годовая производственная программа шт;
Кр-маршрутный коэффициент ремонта.
Расчет годового объема работ механического участка представлен в виде таблицы 2.4.
Таблица 2.4-Рассет годового объема работ
Количество одноименных деталей в агрегате nшт
производственная программа
Маршрутный коэффициент ремонта детальКр
Годовой объем работ чел-ч (н.-ч)
13 Расчет годовых фондов времени
Годовые фонды времени - рабочих оборудования рабочих мест (рабочих постов) определяют исходя из режима работы участка. Различают два вида годовых фондов времени: номинальный и действительный.
Номинальный годовой фонд времени рабочего ч учитывает полное календарное время работы и определяется по формуле:
где - количество календарных; выходных и праздничных дней в году; — количество праздничных дней в году; — средняя продолжительность рабочей смены ч ;
— сокращение длительности смены в предпраздничные дни ч ;
— количество праздников в году.
Принимаем =365=101 =9 =8=1
Действительный годовой фонд времени ч учитывает фактически отрабатываемое время рабочим в течение года с учетом отпуска и потерь по уважительным причинам и определяется по формуле:
где — продолжительность отпуска рабочего календарные дни дни ;
– коэффициент учитывающий потери рабочего времени по уважительным причинам.
Номинальный годовой фонд времени работы оборудования ч учитывает время в течение которого оно может работать при заданном режиме рботы и определяется по формуле:
где – количество смен работы.
Действительный годовой фонд времени работы оборудования ч учитывает неизбежные простои оборудования в профилактическом обслуживании и в ремонтах и представляет собой время в течение которого оно может быть полностью загружено производственной работой:
где - коэффициент учитывающий потери времени на выполнение планово-предупредительного ремонта оборудования . =003
14 Расчет численности основных производственных рабочих
Списочное чел и явочное чел количество производственных рабочих определяется по формулам:
где - годовой объем работ чел-ч;
- годовой фонд времени рабочего соответственно действительный и номинальный;
- коэффициент учитывающий перевыполнение рабочими норм выработки.
Расчет численности производственных рабочих представлен в таблице 2.5
Таблица 2.5-Расчет численности производственных рабочих на участке
Номер и наименование работ (объект сборки или вид работ)
Наименование и код проффесии
На каждой операции принимаем по 1рабочему с расчетом что они будут заниматься восстановлением других деталей.
15 Организация технологического процесса на участке
Проектируемый участок предназначен для механической обработки деталей при восстановлении. На данном будут подвергаться токарным и шлифовальным работам валы рулевой сошки.
Тип производства на участке — массовое. Участок работает в одну смену. Число работающих — один токарь 4-го разряда и шлифовщик 4 разряда.
Вал рулевой сошки поступают на проектируемый участок с разборочного участка разгружаются с электрокары. Детали вручную устанавливаются на станки и закрепляются в приспособлениях для последующей обработки.
16 Расчет количества технологического подъемно-транспортного оборудования и выбор организационной оснастки
Некоторое оборудование (в том числе и организационную оснастку) не рассчитывают а подбирают по фактической потребности и технологическим соображениям. При выборе оборудования для каждой технологической рации необходимо учитывать размер партии восстанавливаемых деталей рабочую зону оборудования габаритные размеры расположение детали при обработке требования к экономичности ремонта а также предусмотреть механизацию и процессов восстановления. Подобранное технологическое оборудование и организационная оснастка представлена в таблице 2.4.
Таблица 2.4-Ведомость технологического оборудования и организационной оснастки
Номер и наименование операции
и модель оборудования
Технологическое оборудование и оснастка
Станок токарно-винторезный 16К20
Шлифовальный станок 3У12А
Организационная оснастка
Тумбочка инструментальная
17 Расчет площади участка
Площадь участка м2 определяется по формуле:
где- площадь занимаемая напольным оборудованием м2
- коэффициент учитывающий плотность расстановки оборудования на участке.
18 Планировка участка восстановления
Толщина наружных стен сварочного участка 510 мм внутренних 250 мм. Колонны квадратного сечения и имеют размер 500х500 мм. Окна имеют размер 2000х1600 мм. Ширина дверей 1500 мм. Оборудование расставлено в соответствии с требования ми ТНПА. Планировка представлена на 1 листе графической части проекта. Спецификация к ней в приложении В пояснительной записки.
0.2 Содержание.doc
2 Технические требования на дефектацию детали
3 Дефекты детали и причины их возникновения
4 Технические требования к отpемонтиpованной детали
5 Выбор pазмеpа партии деталей
Технологическая часть
2 Выбор рационального способа восстановления детали
3 Выбор технологических баз
4 Технологические схемы устранения дефектов
6 Технологический маpшpут восстановления детали
7 Выбор оборудования и технологической оснастки
8 Расчет режимов обработки
9 Расчет норм времени
10 Требования безопасности при выполнении восстановительных работ
11 Технологическая документация
12 Расчет годового объема работ
13 Расчет годовых фондов времени
14 Расчёт числа основных рабочих
15 Организация технологического процесса на участке
16 Расчёт количества технологического подъемно-транспортного оборудования и организационной оснастки
17 Расчёт площади участка
18 Планировки участка восстановления
Констpуктоpская часть
1 Анализ конструкций существующих приспособлений
2 Устройство и принцип действия приспособления
3 Технико-экономическое обоснование конструкции приспособления
Список использованных источников
Приложение А (Ремонтный чертеж)
Приложение Б (Технологическая документация)
Приложение В (Спецификации)
Рекомендуемые чертежи
- 25.01.2023
- 25.01.2023
- 24.01.2023
- 24.01.2020