Проект участка на базе станков с ЧПУ по изготовлению деталей транспортной машины




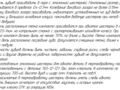
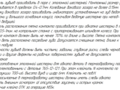
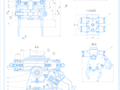
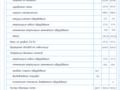
- Добавлен: 24.01.2023
- Размер: 4 MB
- Закачек: 0
Описание
Состав проекта
![]() |
![]() |
![]() ![]() ![]() |
![]() |
![]() |
![]() ![]() ![]() ![]() |
![]() |
![]() ![]() ![]() ![]() |
![]() ![]() ![]() |
![]() ![]() ![]() |
![]() ![]() ![]() |
![]() ![]() ![]() |
![]() ![]() ![]() |
![]() ![]() ![]() |
![]() ![]() ![]() |
![]() ![]() ![]() |
![]() ![]() ![]() |
![]() ![]() ![]() ![]() |
![]() ![]() ![]() |
![]() ![]() ![]() |
![]() ![]() ![]() |
![]() ![]() ![]() |
![]() ![]() ![]() |
![]() ![]() ![]() |
![]() ![]() ![]() |
![]() ![]() ![]() |
![]() ![]() ![]() ![]() |
![]() ![]() ![]() ![]() |
![]() |
![]() ![]() ![]() ![]() |
![]() ![]() ![]() |
![]() ![]() ![]() ![]() |
![]() ![]() ![]() ![]() |
![]() ![]() ![]() ![]() |
![]() ![]() ![]() ![]() |
![]() ![]() ![]() ![]() |
![]() ![]() ![]() ![]() |
![]() ![]() ![]() ![]() |
![]() ![]() ![]() ![]() |
![]() ![]() ![]() |
![]() ![]() ![]() |
![]() ![]() ![]() |
![]() ![]() ![]() |
![]() ![]() ![]() |
![]() ![]() ![]() |
![]() ![]() ![]() ![]() |
![]() ![]() ![]() ![]() |
![]() ![]() ![]() |
![]() ![]() ![]() |
![]() ![]() ![]() ![]() |
![]() ![]() ![]() |
![]() ![]() ![]() ![]() |
![]() ![]() ![]() ![]() |
![]() ![]() ![]() ![]() |
![]() ![]() ![]() ![]() |
![]() ![]() ![]() ![]() |
![]() ![]() ![]() ![]() |
![]() ![]() ![]() |
![]() ![]() ![]() ![]() |
![]() ![]() ![]() |
![]() ![]() ![]() ![]() |
![]() ![]() ![]() ![]() |
![]() ![]() ![]() ![]() |
![]() ![]() ![]() ![]() |
![]() ![]() ![]() ![]() |
![]() ![]() ![]() ![]() |
![]() ![]() ![]() ![]() |
![]() |
![]() ![]() ![]() |
![]() ![]() ![]() |
![]() ![]() ![]() |
![]() ![]() ![]() |
![]() ![]() ![]() |
![]() ![]() ![]() |
![]() ![]() ![]() |
![]() |
![]() ![]() ![]() |
![]() ![]() ![]() |
![]() ![]() ![]() |
![]() ![]() ![]() |
![]() ![]() ![]() |
![]() ![]() ![]() |
![]() |
![]() ![]() ![]() |
![]() ![]() ![]() |
![]() ![]() ![]() |
![]() ![]() ![]() |
![]() ![]() ![]() |
![]() ![]() ![]() |
![]() ![]() ![]() |
![]() |
![]() ![]() ![]() |
![]() ![]() ![]() |
![]() ![]() ![]() |
![]() ![]() ![]() |
![]() ![]() ![]() |
![]() ![]() ![]() |
![]() ![]() ![]() |
![]() |
![]() ![]() ![]() |
![]() ![]() ![]() |
![]() ![]() ![]() |
![]() ![]() ![]() |
![]() ![]() ![]() |
![]() |
![]() ![]() ![]() ![]() |
![]() ![]() ![]() ![]() |
![]() ![]() ![]() |
![]() |
![]() ![]() ![]() ![]() |
![]() ![]() ![]() ![]() |
![]() ![]() ![]() ![]() |
![]() ![]() ![]() |
![]() ![]() ![]() ![]() |
![]() ![]() ![]() ![]() |
![]() ![]() ![]() ![]() |
![]() |
![]() ![]() ![]() |
![]() ![]() ![]() |
![]() ![]() ![]() |
![]() ![]() ![]() ![]() |
![]() ![]() ![]() ![]() |
![]() ![]() ![]() |
![]() ![]() ![]() |
![]() ![]() ![]() |
![]() ![]() ![]() |
![]() ![]() ![]() ![]() |
![]() ![]() ![]() |
Дополнительная информация
OP1_50_1.cdw

125_1.frw

045.CDW

080.cdw

020.CDW

010.CDW

035_2.CDW

015.CDW

025.CDW

035_1.CDW

040.CDW

005.cdw

030.CDW

120.CDW

105.CDW

125_2.CDW

075_1.CDW

075_2.CDW

100.CDW

050.CDW

OP1_70_1.cdw

OP4_10_1.cdw

OP1_50_1.cdw

oper 50.CDW

OP1_60_1.cdw

OP1_45.cdw

OP1_10_1.cdw

OP1_65_1.cdw

OP1_15_1.cdw

OP1_30.cdw

OP1_40_1.cdw

OP1_55_1.cdw

oper 15.CDW

oper 45 .CDW

oper 10.CDW

oper 80_1.CDW

oper 05.CDW

OP1_05_1.CDW

OP1_45_1.cdw

TK_80_1.cdw

OP1_05.CDW

oper 30.CDW

OP1_10_2.cdw

oper 80.CDW

OP1_10_1.cdw

OP1_65_1.cdw

OP1_15_1.cdw

OP1_30.cdw

OP4_10_2.cdw

OP1_55_1.cdw

OP1_05_1.CDW

OP1_45_1.cdw

OP1_05.CDW

TK_135_2.cdw

OP1_10_2.cdw

TK_135_1.cdw

OP1_30_1.cdw

OP_120_1.cdw

OP1_90_1.cdw

OP_115_1.cdw

MAR2_4.CDW

MAR2_1.CDW

MAR2_3.CDW

MAR2_5.CDW

MAR2_2.CDW

2.CDW

TIT2.CDW

TIT1.CDW

MAR1_2.CDW

MAR1_1.CDW

MAR1_3.CDW

MAR1_4.CDW

1.CDW

MAR3_3.CDW

MAR3_5.CDW

TIT3.CDW

3.CDW

MAR3_1.CDW

MAR3_2.CDW

MAR3_4.CDW

MAR5_2.CDW

MAR5_3.CDW

MAR5_4.CDW

TIT5.CDW

MAR5_5.CDW

MAR5_1.CDW

5.CDW

4.CDW

TIT4.CDW

MAR4_1.CDW

MAR4_2.CDW

MAR4_3.CDW

сравнение.cdw

1ртк.cdw

SP3RUKA.CDW

Оправка.cdw

Патрон мембранный спецификация.cdw

Приспособление контрольное.cdw

Оправка спецификация 2.CDW

Приспособление контрольное спецификация.cdw

Патрон мембранный.cdw

Оправка спецификация.cdw

Наладка 0051.CDW

Наладка 010.CDW

Наладка 005.CDW

1планир.cdw

кл.cdw

RUKA.CDW

SP1RUKA.CDW

SP1RTK.CDW

EKONOM.CDW

кл1.cdw

SP2RUKA.CDW

Рекомендуемые чертежи
- 24.01.2023
- 24.01.2023
- 24.01.2023