Проект участка на базе станков с ЧПУ по изготовлению корпусных деталей




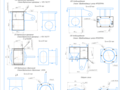
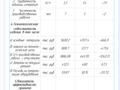
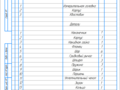
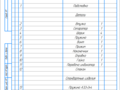
- Добавлен: 24.01.2023
- Размер: 2 MB
- Закачек: 1
Описание
Состав проекта
![]() |
![]() ![]() ![]() |
![]() |
![]() ![]() ![]() |
![]() ![]() ![]() |
![]() ![]() ![]() ![]() |
![]() |
![]() |
![]() |
![]() |
![]() ![]() ![]() |
![]() ![]() ![]() |
![]() |
![]() ![]() ![]() |
![]() ![]() ![]() |
![]() ![]() ![]() ![]() |
![]() ![]() ![]() |
![]() ![]() ![]() ![]() |
![]() |
![]() ![]() ![]() ![]() |
![]() ![]() ![]() |
![]() ![]() ![]() ![]() |
![]() ![]() ![]() ![]() |
![]() ![]() ![]() ![]() |
![]() ![]() ![]() |
![]() ![]() ![]() ![]() |
![]() ![]() ![]() ![]() |
![]() ![]() ![]() ![]() |
![]() ![]() ![]() ![]() |
![]() ![]() ![]() |
![]() ![]() ![]() |
![]() ![]() ![]() |
![]() ![]() ![]() ![]() |
![]() ![]() ![]() ![]() |
![]() ![]() ![]() ![]() |
![]() ![]() ![]() |
![]() ![]() ![]() ![]() |
![]() ![]() ![]() ![]() |
![]() ![]() ![]() ![]() |
![]() ![]() ![]() |
![]() ![]() ![]() |
![]() ![]() ![]() ![]() |
![]() ![]() ![]() |
![]() ![]() ![]() ![]() |
![]() |
![]() ![]() ![]() ![]() |
![]() ![]() ![]() ![]() |
![]() ![]() ![]() |
![]() ![]() ![]() |
Дополнительная информация
Приспособление установочное 2.cdw

Компановка участка.frw

Спецификация ИГ Лист1.cdw

Спецификация ПК1.cdw

база.cdw

Наладка 02.frw

Схемы измерения.cdw

Спецификация ПУ 1.cdw

Экономика.frw

Приспособление контрольное.cdw

Измерительная головка.cdw

Сравнительная технология.frw

Наладка 03.frw

Планировка.cdw

Спецификация ИГ Лист2.cdw

Методы дефектоскопии.cdw

Наладка 01.frw

Спецификация ПУ2.cdw

Титульный лист1.cdw

Приспособление установочное1.cdw

Спецификация ПУ3.cdw

Рекомендуемые чертежи
- 24.01.2023
- 24.01.2023
- 24.01.2023
Свободное скачивание на сегодня
- 22.08.2014
- 29.08.2014