Разработка проекта участка по групповой обработке деталей на базе станков с ЧПУ




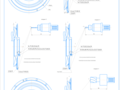
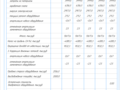
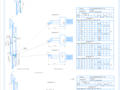
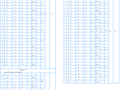
- Добавлен: 04.11.2022
- Размер: 2 MB
- Закачек: 1
Описание
Состав проекта
![]() |
![]() |
![]() |
![]() ![]() ![]() ![]() |
![]() |
![]() |
![]() ![]() ![]() |
![]() ![]() ![]() |
![]() ![]() ![]() |
![]() ![]() ![]() |
![]() ![]() ![]() |
![]() ![]() ![]() |
![]() ![]() ![]() |
![]() |
![]() ![]() ![]() ![]() |
![]() ![]() ![]() |
![]() ![]() ![]() |
![]() ![]() ![]() |
![]() ![]() ![]() |
![]() ![]() ![]() |
![]() ![]() ![]() ![]() |
![]() ![]() ![]() ![]() |
![]() ![]() ![]() ![]() |
![]() ![]() ![]() ![]() |
![]() ![]() ![]() |
![]() ![]() ![]() |
![]() ![]() ![]() |
![]() ![]() ![]() ![]() |
![]() |
![]() ![]() ![]() |
![]() |
![]() |
![]() ![]() ![]() |
![]() ![]() ![]() ![]() |
![]() ![]() ![]() |
![]() ![]() ![]() |
![]() |
![]() |
![]() ![]() ![]() ![]() |
![]() ![]() ![]() ![]() |
![]() ![]() ![]() |
![]() ![]() ![]() |
![]() ![]() ![]() |
![]() |
![]() ![]() ![]() |
![]() ![]() ![]() |
![]() ![]() ![]() |
![]() ![]() ![]() ![]() |
![]() |
![]() ![]() ![]() |
![]() ![]() ![]() ![]() |
![]() |
![]() ![]() ![]() |
![]() |
![]() ![]() ![]() |
![]() ![]() ![]() ![]() |
![]() ![]() ![]() ![]() |
![]() ![]() ![]() |
![]() ![]() ![]() |
![]() ![]() ![]() ![]() |
![]() ![]() ![]() |
![]() |
![]() ![]() ![]() |
![]() ![]() ![]() ![]() |
![]() |
![]() ![]() ![]() |
![]() ![]() ![]() |
![]() ![]() ![]() ![]() |
![]() |
![]() ![]() ![]() |
![]() ![]() ![]() ![]() |
![]() ![]() ![]() ![]() |
![]() ![]() ![]() |
![]() |
![]() ![]() ![]() |
![]() ![]() ![]() |
![]() ![]() ![]() |
![]() ![]() ![]() |
![]() |
![]() ![]() ![]() |
![]() ![]() ![]() |
![]() ![]() ![]() |
![]() ![]() ![]() ![]() |
![]() ![]() ![]() |
Дополнительная информация
Наладка на 005.cdw

5 КOМБИНИРОВАННАЯ С ЧПУ
Резец отрезной 2177-0005 Т15К6 ГОСТ 18892-73
Резец К014980.000-00 Т15К6 ТУ 2-035-1040-86
Резец К014980.000-01 Т15К6 ТУ 2-035-1040-86
Резец SSSCR88D06 T15К5 ТУ 19-4206-95-83
Т2:0-1-2-3-4-5-6-7-8-0
Таблицы к наладке на 010.cdw
035-230-1224 ОСТ 2И20-5-80
0 КОМБИНИРОВАННАЯ С ЧПУ
Фреза 01.3.0036.000-04 ТУ 2-035-812-81
Чистый.cdw

Планировка.cdw
График загрузки станков
Условные обозначения:
- подвод сжатого воздуха.
- подвод смазочно охлажд. жид.
- подвод электроэнергии.
- главный пульт управления.
Магистральный проезд
- медицинская аптечка
- стружко-уборочный конвейер
- склад стеллажного типа
ППВ - позиция приема-выдачи
ТТ - транспортная тележка
Наладка на 010.cdw
0 КОМБИНИРОВАННАЯ С ЧПУ
Резец Т15К6 SSSCA88D06 ТУ19-4206-95-83
Резец Т15К6 К014980.000-00 ТУ2-035-1040-86
Т2: 0-1-2-3-4-5-6-7-8-9-10-11-12-0
Резец канавочный Т15K6
приспособа(контрольное2).cdw
Покрытие нерабочих поверхностей эмаль МЛ-152
Приспособление настраивать по эталонному кольцу.
Схват.cdw

Захватное устройство
транспортируемой заготовки 10
Диаметр захватываемой заготовки 316 мм
РТК.cdw

-грузоподъмность на одну руку
-число степеней подвижности
-система управления
-способ программирования
-погрешность позиционирования
ПР мод. СМ160Ф2.81.01
максимальный обрабатываемый диаметр
-мощность ЭД главного привода
Полуавтомат токарный многоцелевой
Токарный многоцелевой па мод. 1П756Ф4
Магазин-накопитель заготовок
Пристаночный накопитель заготовок
Накопитель готовых деталей
Экономика.cdw

отменённая амортизация
заменяемого оборудования
Остаточная стоимость
внедряемого оборудования
Чистая дисконтированная
Экономическая оценка
Проект участка на базе станков с ЧПУ по изготовлению
Приращения доходов и расходов
затраты на материалы
энергия электрическая
текущий ремонт оборудования
амортизация нового оборудования
Налог на прибыль (24%)
Приращение доходов от инвестиций
Коррекция денежных потоков
Продажа старого оборудования
Высвобождение площадей
Чистый денежный поток
Коэффициент дисконтирования
Прогноз денежных потоков для проекта участка
Приспособа(патрон).cdw

Приспособление сбалансировать с
деталью. Дисбаланс 50 гсм.
Покрытие нерабочих поверхностей
красная ГОСТ 6631-74.
Ислед(лист1).cdw
Проект участка на базе станков с ЧПУ по изготовлению
Накопительное устройство типа
Накопительное устройство
Загрузочно-накопительное устройство
Загрузочно-накопительное устройство
типа тактового стола
Загрузочно-накопительное
устройство типа подъемника
Приспособа(фрезерная).cdw
Приспособление фрезерное
Приспособление работает с пневмогидроприводом
Гидросистему испытать маслом под давлением
МПА в течении 5 мин.
Нерабочие поверхности приспособления окрасить
в кремовый цвет эмалью НЦ132К ГОСТ 6631-74
Наладка на 010(2).cdw

Т1: 0-1-2-3-4-5-6-7-8-9-10-11-12-13-14-15-16
-18-19-20-21-22-23-24-25-26-27-28-29-30-О
Т3: 0-1-2-3-4-5-6-7-8-9-10-11-12-13-14-15-16
Т2: 0-1-2-3-4-5-6-7-8-9-10-11-12-13-14-15-16
Записка.doc
Федеральное государственное образовательное учреждение
высшего и профессионального обучения
«ВОЛЖСКАЯ ГОСУДАРСТВЕННАЯ АКАДЕМИЯ
Кафедра технологии конструкционных материалов
Дипломный проект на тему:
«Разработка проекта участка по групповой обработке деталей на базе станков с ЧПУ»
Пояснительная записка
Характеристика объектов производства
Технологический раздел
1. Определение типа производства
2. Анализ конструкции детали на технологичность
3. Анализ базовых технологических процессов
5. Разработка маршрутного технологического процесса
6. Выбор технологических баз и последовательности переходов
7. Выбор средств технологического оснащения
8. Расчет припусков и операционных размеров
9. Расчет режимов резания
10. Техническое нормирование операций
11. Технико – экономическое обоснование проектного ТП
Конструкторский раздел
1. Проектирование станочных и контрольных приспособлений
2. Проектирование средств автоматизации производственных процессов
Исследовательский раздел «Загрузочно-накопительные устройства»
Производственные расчеты и разработка планировки
2. Форма организации выполнения технологических процессов
3. Производственная структура участка
5. Проектирование подсистем
6. Строительные решения
7. Технико-экономические показатели участка
Безопасность и экологичность проекта
1. Характеристика безопасности применяемого в проекте оборудования технических устройств производственных процессов.
2. Экологическая безопасность и охрана окружающей среды
3. Безопасность проекта в чрезвычайных ситуациях.
Организационно-экономический раздел
1 Организация складского хозяйства
2 Экономическая оценка проекта
Список использованных источников
Данный дипломный проект содержит расчетно-пояснительную записку графическую часть комплект технологической документации.
В дипломном проекте разрабатываются процессы обработки деталей типа диска на основе группового производства. Групповой метод – это такой метод унификации технологии производства при котором для группы однородной по тем или иным конструкторско - технологическим признакам продукции устанавливаются однотипные высокопроизводительные методы обработки с использованием однородных и быстропереналаживаемых орудий производств.
При выполнении проекта решаются вопросы о классификации деталей выборе комплексной детали рассматриваются различные способы изготовления предложенной детали. Анализируется реальный базовый вариант технологического процесса изготовления данной детали. После анализа разрабатывается маршрут технологического процесса изготовления детали представителя разрабатывается операционная технология т. е. выбираются базы и средства технологического оснащения. Определяется содержание и последовательность выполнения технологических переходов режимы резания. Определяются нормы технологического времени.
Конструкторская часть содержит вопросы проектирования станочных и контрольных приспособлений средств автоматизации.
В исследовательской части дипломного проекта дана классификация и сделан краткий обзор загрузочно - накопительных устройств.
Рассматриваются вопросы безопасности и экологичности проекта организации производства разрабатывается планировка участка дается экономическая оценка проекта.
Комплект технологической документации содержит маршрутные и операционные технологические процессы операционные карты и карты контроля.
Данная работа содержит практические сведения по реальным процессам применяемым в машиностроении
Технология машиностроения – это наука об изготовлении машин требуемого качества в установленном производственной программой количестве и в заданные сроки при наименьших затратах живого и овеществленного труда т.е. при наименьшей себестоимости.
Одной из важнейших задач научно-технического прогресса является комплексная механизация и автоматизация промышленного производства направленные на повышение производительности труда улучшение качества продукции и других технико-экономических показателей производства.
Решение этой задачи связано с созданием гибких производственных систем (ГПС). Они беспечивают комплексную автоматизацию многономенклатурного производства на базе широкого использования многоцелевого технологического оборудования с программным управлением и микропроцессорных управляюще-вычислительных средств в комплексе с промышленными роботами автоматизированными транспортно-накопительными устройствами системами инструментального обеспечения удаления отходов контроля технологических процессов и оборудования автоматизации проектно-технологических конструкторских и планово - производственных работ.
Опыт использования ГПС показал что при их рациональной эксплуатации переход от отдельных станков с ЧПУ к автоматизированным комплексам повышает эффективность в 2-3 раза коэффициент загрузки станков до 085-09 а коэффициент сменности до 2-3.
Гибкие производственные системы – это наиболее эффективное средство автоматизации серийного производства позволяющие переходить с одного вида продукции на другой с минимальными затратами времени и труда ГПС позволяет снизить потребность в квалифицированных станочниках повысить качество продукции.
ГПС – это комплекс технологических средств состоящий из многоцелевых станков с ЧПУ или других металлообрабатывающих станков с ЧПУ оснащенных механизмами автоматической смены инструмента автоматической смены заготовок и транспортирования их со склада до зоны обработки при помощи различных транспортных средств например при помощи самоходных роботизированных тележек Этот комплекс связан единым математическим обеспечением реализующим работу оборудования в автоматическом режиме с минимальным участием человека. ГПС рентабельны только при эксплуатации в 2-3 смены.
Дипломный проект – завершающая процесс обучения квалификационная работа основным содержанием которой является самостоятельное комплексное решение инженерных организационных экономических и других задач.
ХАРАКТЕРИСТИКА ОБЪЕКТОВ ПРОИЗВОДСТВА.
Конструкторское - технологическое подобие деталей определяется совокупностью признаков. При классификации деталей по конструктивным характеристикам берут за основу следующие признаки: геометрическую форму функциональный параметрический конструктивный признаки; служебное назначение наименование. В соответствии с ЕСКД на все детали установлены шесть классов: 71 72 73 74 75 76 [1 2]
Классы деталей содержат номенклатуру:
Класс 71 - тела вращения типа колец дисков шкивов блоков втулок стаканов валов штоков и другие. В этом классе классифицируются детали - тела вращения которые делятся на три диапазона по соотношению длины детали L к наибольшему диаметру D: c L = 0.5 D; c 0.5 D L> 2 D и с L>2 D.
Параметрический признак характеризуется отношение L D позволяет детали типа дисков колец фланцев шкивов отделить от деталей типа втулок стаканов пальцев и деталей типа валов шпинделей осей штоков и т.п.
Класс 72 - тела вращения с элементами зубчатого зацепления; трубы сегменты
Класс 73 - детали не тела вращения: корпусные опорные емкостные.
Класс 74 - детали не тела вращения: плоскостные рычажные грузовые тяговые аэрогидродинамические; изогнутые из листов полос лент; профильные.
Класс 75 - тела вращения и (или) не тела вращения: кулачковыекарданные; с элементами зацепления санитарно - технические пружинныекрепежные и другие.
Класс 76 - детали технологической оснастки выполняющие самостоятельные функции (сверла метчики режущие пластины матрицы пуансоны и тому подобные).
В основу технологической классификации положены следующие основные признаки: размерная характеристика группа материалов вид деталей по технологическому методу изготовления вид исходной заготовки квалитетпараметр шероховатости технологические требования характеристика толщины характеристика массы и т.д.
В соответствии с заданием остановимся на деталях - телах вращения (71 класса). Как уже было отмечено выше эти детали делятся на три диапазона в зависимости от LD кроме того делятся на группы и подгруппы в зависимости от наличия на них отверстий пазов шлицев и других конструктивных элементов.
Детали типа полых цилиндров.
К этому типу как простые детали близкие к правильной форме полого цилиндра так и детали представляющие собой тела вращения со сложной внутренней поверхностью при наружном очертании не всегда соответствующем цилиндру например втулки стаканы обоймы фланцы ступицы колес и другие. Все детали полых цилиндров характеризуются соотношением 05DL=2D - где L и D соответственно длина и наибольший наружный диаметр детали. К основным поверхностям подлежащим обработке относятся внутренние и наружные цилиндрические поверхности и торцы. Черновая и чистовая обработка таких деталей ведется обычно на станках токарной группы а отделочные операции на бесцентрово и внутришлифовальных станках.
Для изготовления деталей данного типа применяют самые разнообразные конструкционные материалы: серые и ковкие чугуны углеродистые и легированные стали цветные металлы тестолит капрон и другие. Заготовками для небольших деталей простой формы с диаметром отверстий до 20 - 25 мм обычно служат калиброванные или горячекатанные прутки а также отливки без отверстий. Для деталей с диаметром отверстия более 25 мм в качестве заготовок используют сварные трубы полые отливки поковки штамповки с прошитым отверстием.
К таким деталям относятся валы оси штоки круглые тяги трубы пальцы и т.п.
Наибольшее распространение получили валы имеющие различное служебное назначение конструктивную форму и размеры. Наиболее ответственными у валов являются посадочные цилиндрические и торцевые поверхности под подшипники шестерни муфты рабочие кромки манжет уплотнения а также шлицевые поверхности зубчатые венцы кулачки. Материал деталей выбирают в зависимости от их служебного назначения.
К таким деталям могут относиться маховики крышки различные кольца диски трения шкивы зубчатые колеса. Конструктивной особенностью деталей этого типа является то что они имеют форму тел вращения у которых высота детали не превышает половины наибольшего наружного диаметра. Эти детали как правило имеют центральное цилиндрическое коническое резьбовое или шлицевое отверстие.
Конструкция ряда деталей предусматривает наличие отверстий для крепления которые расположены по окружности.
Главными поверхностями деталей типа дисков являются торцы и короткие цилиндрические конические наружные и внутренние поверхности обрабатываемые в основном при вращении детали.
К большинству деталей типа дисков предъявляются высокие требования по точности прочности жесткости износостойкости коррозионной стойкости и к другим свойствам определяемым их служебным назначением.
Из деталей типа дисков для дипломного проектирования была подобрана группа деталей (рис.1.1 1.2 1.3 1.4 1.5) сходных по конструкторско- технологическим признакам.
Группой называется совокупность деталей характеризуемая при обработке общностью оборудования оснастки наладки всего технологического процесса или отдельных операций. При создании групп принимаются во внимание габариты деталей так как они определяют тип оборудования и размеры технологической оснастки. Кроме этого учитывается следующее: общность геометрической формы и поверхностей подлежащих обработке; их точность и шероховатость; однородность заготовок; серийность; экономичность процесса. Группа деталей при групповом производстве характеризуется единством: в смысле конструкторском технологическом (общность технологий) инструментальном (общность оснащения) и организационно-плановом (единое планирование и организация производства).
Выбранные детали (крышки корпуса) имеют одинаковые: посадочные точные отверстия крепежные отверстия пазы канавки. Материал деталей – сталь 38ХС и сталь 40Х ГОСТ 4543-71
Детали имеют сходные виды обработки: токарные операции фрезерные зубодолбежные сверлильные.
При построении групповых процессов механической обработки за основу берется комплексная деталь. Под комплексной понимается реальная или условная деталь содержащая в своей конструкции все основные элементы характерные для деталей данной группы и являющаяся ее конструкторско - технологическим представителем.
Под основными элементами понимаются поверхности определяющие конфигурацию детали и технологические задачи решаемые в процессе их обработки. Основные элементы служат главным признаком для отнесения детали к тому или иному классификационному подразделению.
В качестве комплексной детали за основу берем самую сложную деталь из группы – крышка 1. (рис 1.1) Эта деталь включает в себя все элементарные поверхности которыми обладают детали данной группы (точные центральные отверстия крепежные отверстия расположенные вне оси детали пазы зубчатый венец канавки наклонные отверстия).
ТЕХНОЛОГИЧЕСКИЙ РАЗДЕЛ
В зависимости от широты номенклатуры регулярности стабильности и объёма выпуска продукции различают следующие типы производства: единичное серийное массовое.
Тип производства по ГОСТ 31121-84 характеризуется коэффициентом закрепления операций:
>=Kзо10 - массовое и крупносерийное производство;
>=Кзо20 - среднесерийное производство;
>=Кзо40 - мелкосерийное производство;
=Кзо – единичное производство.
Величина коэффициента закрепления операций определяется по формуле 2.1
где О - суммарное число различных операций выполняемых на производственном участке в
Р- суммарное число рабочих мест на которых выполняются данные операции.
Тип производства рассчитываем следующим образом:
Определяем расчетное количество станков необходимых для выполнения каждой станочной операции:
где N =4800 шт.- объем годового выпуска деталей оговоренный в задании на проектирование
tш-к – штучно-калькуляционное время i-ой операции уменьшенное на 20% мин Fо- эффективный годовой фонд времени работы станка. Fo=3975ч.
Кв- средний коэффициент выполнения норм времени. Кв=1.
Кр- коэффициент учитывающий потери по организационно-техническим причинам.
Данные по каждой операции заносим в таблицу 2.1
Определяем принятое количество оборудования на каждой станочной операции Si для чего расчетное количество станков Срi округляем до целых значений.
Рассчитываем коэффициент загрузки каждого рабочего места:
Определяем число операций закрепленных за одним рабочим местом:
где hн- нормативный коэффициент загрузки оборудования hн=075.
Рассчитываем величину коэффициента закрепления операций:
где -общее число рабочих мест на которых выполняются все станочные операции по изготовлению детали.
Расчет типа производства
Токарно - винторезный 1К62
Обрраб.центр МА655С630
Зубодолбежный па 5М150
Рад.сверлильный 2А55
Тип производства – крупносерийное.
Характерной особенностью серийного производства является изготовление деталей партиями. Увеличение количества деталей в партии является положительным фактором так как с повторением одних и тех же приемов возрастает навык рабочего а следовательно увеличивается производительность труда сокращается штучно-калькуляционное время на операцию и снижается себестоимость изготовления детали. С другой стороны неоправданное увеличение размера партии отрицательно сказывается на производственном процессе — увеличиваются незавершенное производство и площади занятые цеховыми и межоперационными складами заготовок и деталей.
Количество заготовок в партии для одновременного запуска (n) при групповой форме организации производства можно определить упрощенно по формуле 3.9 [3]:
где Sn — количество запусков в год.
Количество заготовок в партии для одновременного запуска
Принимаем объем партии запуска – 400шт.
Установив тип производства и метод его организации приступаем к анализу технологичности изделия выбору заготовки и разработке технологического процесса.
2.1.Служебное назначение
Каждое изделие предназначено для выполнения определённой функции. Под служебным назначением детали понимают максимально уточнённую и чётко сформулированную задачу для решения которой предназначена деталь.
В дипломном проекте рассматривается изделие - крышка. Деталь - крышка входит в конструкцию редуктора. Редуктор - это механизм состоящий из передач с зацеплением с постоянным передаточным отношением. В редукторе крышка является центральной шестерней по которой происходит обкат сателлитов. Редуктор предназначен для уменьшения угловой скорости и увеличения вращающего момента на выходном валу. Деталь выбранная в качестве объекта для проектирования достаточно трудоемка в изготовлении содержит разнообразные поверхности и конструктивные элементы : отверстия пазы зубья. К многим предъявляются высокие требования по точности и качеству.
Технологический процесс разрабатывается для детали крышка редуктора.
2.2. Анализ на технологичность
В соответствии с служебным назначением крышка редуктора имеет сложную форму.
Для технолога важно выявить основные поверхности детали влияние их взаимного расположения точности шероховатости на работоспособность изделия.
Различные базирующие поверхности деталей с точки зрения их функционального назначения можно отнести к категории основных или вспомогательных баз. Основными с помощью которых детали присоединяются к рамам корпусам в большинстве случав являются плоские поверхности или сочетание плоской поверхности и одного или двух базовых отверстий. Вспомогательными базами деталей являются главные отверстия по ним базируются шпиндели валы а также плоские поверхности и их сочетания которые определяют положение различных присоединяемых узлов и деталей.
У данной детали имеются также резьбовые крепежные отверстия. Они предназначены для фиксации достигнутого положения присоединяемых сборочных единиц. Работа механизмов означает формирование размерных связей обеспечивающих выполнение служебного назначения. В размерных связях узлов машины корпусная деталь участвует размерами своих поверхностей. Эти размерные параметры детали непосредственно определяют точность положения одного комплекта вспомогательных баз относительно другого или точность положения вспомогательных баз относительно основных баз детали. В соответствии с этим к точности геометрической формы размеров базирующих поверхностей деталей предъявляются повышенные требования.
Основными базами данной крышки являются: цилиндрическая поверхность 2 и торец 3.
Первый комплект вспомогательных баз - цилиндрическая поверхность 13 и торец
Второй комплект вспомогательных баз –цилиндрическая поверхность 1 и торец 5.
Основные рабочие поверхности данного корпуса – зубчатый венец
Пазы 91617 – вспомогательные поверхности
Канавка 8 – является сепаратором в нее устанавливаются накатом шарикоподшипники.
Отверстия 12 служат для подвода смазки.
Отверстия 15 14 – являются крепежными поверхностями.
В соответствии со служебным назначением поверхностей к ним предъявляют соответствующие требования взаимного расположения точности и шероховатости.
Основные базы: пов.2 – Ra2.5 допуск торцового биения 005.
Первый комплект вспомогательных баз: пов.13 - пов.3 – Rz20.
Второй комплект вспомогательных баз: пов.1 - Ra2.5 допуск торцового биения к поверхностям 2 и 3 005мм.
Основные рабочие поверхности: пов.8 - Ra1.25 допуск соосности
к поверхности 2 01мм
Пов.7 – Rz20 допуск плоскостности 01мм.
Остальные поверхности – IT12 Ra12.5.
У данной крышки довольно сложная конструкция. Так как требования к взаимному расположению поверхностей не слишком высоки и объем удаляемого металла небольшой то выбор метода изготовления заготовки определяется сложностью конструкции.
Унификация формы и размеров обрабатываемых поверхностей позволяет применить в большинстве случаев стандартный инструмент. В результате анализа конструкции выявлены также некоторые возможности по ее упрощению а следовательно и повышению ее технологичности. Предлагается устранить все бобышки по контуру детали . Это приведет к упрощению конструкции заготовки т.е. к снижению трудоемкости ее изготовления к упрощению конструкции станочных приспособлений снимется ориентации заготовки перед установкой на станок.
Материал крышки - сталь 38ХС
Химический состав и механические свойства приведены в таблице 2.2
Сталь 38XС ГОСТ 4543-71
Механические свойства
Количественная оценка технологичности [4]
Коэффициент использования материала
Ким = Мд Мз = 10.2 16 = 0.637(2.7)
где Мд - масса детали;
Мз - масса заготовки
Полученное значение коэффициента использования материала говорит о невысокой технологичности выбранного способа получения заготовки так как для серийного автоматизированного производства удовлетворительное значение коэффициента использования материала - не ниже 0.7
Коэффициент точности обработки
Ктч = 1 – 1 Аср = 1 – 1 11.6 = 0.91(2.8)
где Аср - средний квалитет точности обработки детали по всем поверхностям.
Коэффициент шероховатости поверхности
Кш = 1 Бср = 1 8.5 = 0.11(2.9)
где Бср - среднее числовое значение параметра шероховатости всех поверхностей детали.
Так как Ктч = 0.91 >0.8 и Кш = 0.11 0.32 то деталь можно считать технологичной.
3.Анализ базового технологического процесса
Базовый маршрутный техпроцесс приведен в таблице 2.3
Установленная общая последовательность механической обработки контрольных операций выбрана верно.
Заготовка детали – штамповка на ГКМ. В данных условиях производства при данной форме детали и её размерах штамповка - это наиболее оптимальный способ получения заготовки.
Материал детали - сталь 38ХС ГОСТ 4543-71. Она удовлетворяет требованиям служебного назначения и обладает хорошими свойствами пластической деформации.
В технологии производства детали целесообразно соблюдать принцип постоянства баз так как при смене баз в ходе технологического процесса точность обработки снижается из-за погрешности взаимного расположения новых и применявшихся ранее технологических баз. Однако в базовом технологическом процессе применялись несколько комплектов технологических баз. Подобные допущения возможно объяснить большим количеством операций переустановов заготовки т.е. износом поверхностей принятых в качестве технологических баз а также невозможностью обработки некоторых поверхностей на применяемом оборудовании с одних и тех же баз.
Для обработки детали используется специальный и стандартный режущий инструмент (резцы фрезы сверла зенкеры и пр.); стандартный и специальный контрольный инструмент (штангенциркуль калибры-пробки шаблоны контрольные приспособления). Среди применяемых марок материала для режущего инструмента были использованы кроме быстрорежущих сталей и некоторые марки твердых сплавов группы ТК.
Назначенные режимы резания обеспечивают заданную точность обработки но недостаточно экономически выгодны что обусловлено применяемым материалом режущего инструмента (быстрорежущие стали).
В базовом технологическом процессе используются следующие марки станков:
Токарно-винторезный 1К62
Токарный сЧПУ1П732РФ3
Обрабатывающий центрМА655С630
Радиально-сверлильный2А55
Моечная машина МКП-0620
Можно отметить что в базовом технологическом процессе применяются станки с ручным управлением и станки с ЧПУ. По мощности и точности оборудование вполне удовлетворяет требованиям предъявляемым выполняемыми операциями но достижение заданной точности на станках с ручным управлением требует квалифицированного рабочего персонала.
Контрольные средства соответствуют данному типу производства и требованиям точности.
Базовый маршрутный техпроцесс
Наименование операции
Заготовительная – штамповка
Токарный с ЧПУ 1П732РФ3
Обраб.центр МА655С630
Радиально-сверлильный 2А55
Нормы времени на операции
Для изготовления детали большую роль играет выбор рационального вида исходной заготовки и способа её получения. Наиболее широко для получения заготовок применяют следующие методы: литьё обработка металлов давлением и сварка а также их комбинации. Наиболее распространенным методом получения стальных заготовок деталей машин является обработка давлением. Выделяют ковку и штамповку. Ковка является рациональным и экономически выгодным процессом получения качественных заготовок с высокими механическими свойствами в условиях мелкосерийного и единичного производств. Ковкой изготавливают самые разнообразные заготовки например: валы диски цапфы шпиндели фланцы муфты и т.д. К основным недостаткам ковки можно отнести низкую производительность трудоемкость изготовления большие припуски и напуски что приводит к значительному увеличению объема механической обработки и расхода металла.
Область применения штамповки - серийное и массовое производство. Штамповка на кривошипных прессах в 2-3 раза производительнее штамповки на молотах припуски и допуски уменьшаются на 20-30% расход металла снижается на 10-15% . Заготовки для деталей-тел вращения типа стержней с утолщениями колец втулок деталей со сквозными и глухими отверстиями целесообразно получать на горизонтально ковочных машинах (ГКМ).
Учитывая все выше сказанное выберем способ изготовления заготовки (крышки) - штамповка на горизонтально ковочных машинах.
Определение стоимости заготовки получаемой на ГКМ[5]
Sзаг=((Сi1000)*Mз*Кт*Кс*Кв*Км*Кп) - (Мз-Мд)*Sотх1000(2.10)
где Сi - базовая стоимость одной тонны заготовок р.
Кт Кс Кв Км Кп - коэффиценты зависящие соответственно от класса точности группы сложности массы марки материала и объема производства.
Мз Мд - соответственно масса заготовки и готовой детали кг.
Sотх - цена одной тонны отходов р.
С Sотх=80 р; Кт=1; Кс=088; Кв=079; Км=121; Кп=1.
Sзаг=((3731000)*16*1*088*079*121*1) - (16 - 102)*801000=453 р.
Определение стоимости заготовки проводилось по ценам на 1991г.
5. Разработка маршрутного технологического процесса изготовления детали
Технологический процесс представляет собой совокупность различных операций в результате выполнения которых изменяется форма размеры выполняется соединение деталей в сборочные единицы и изделия осуществляется контроль требований чертежа и технических условий. Маршрутное описание технологического процесса заключается в сокращенном описании всех технологических операций в маршрутной карте в последовательности их выполнения без указания переходов и технологических режимов.[11]
Технологические процессы разрабатывают при проектировании. Перед разработкой ТП необходимо получить и изучить информацию которая делится на базовую руководящую и справочную.
Базовая - сведения содержащиеся в конструкторской документации на изделие объем выпуска сроки подготовки производства. Рабочий чертеж детали содержит все размеры технические требования к качеству и шероховатости марку и твердость материала.
Руководящая - сведения по развитию отрасли план выпуска материала средств технологического оснащения стандарты на ТП.
Справочная - сведения о прогрессивных методах обработки каталоги номенклатурные справочники оборудования и оснастки. Материалы по выбору технологических нормативов (режимы обработки припуски расход материала и др.) и др. справочные материалы.
Всю механическую обработку разбивают по операциям и таким образом выявляют последовательность выполнения операций их число. Для каждой операции выбирают оборудование и определяют конструктивную схему приспособления.
Задачей каждого предыдущего перехода является подготовка поверхности заготовки под последующую обработку и каждый последующий метод ( операция или переход) должен быть точнее предыдущего т. е. обеспечивать более высокое значение показателей качества детали. Поэтому механическая обработка делится на:
черновую обработку когда удаляется большая часть припуска что позволяет обнаружить возможные дефекты заготовки; на первых одной-двух операциях. При базировании по черновым базам обрабатываются основные технологические базы;
чистовую обработку когда в основном обеспечивается требуемая точность:
далее идут операции местной обработки по ранее обработанным поверхностям отделочные операции когда достигается требуемая шероховатость поверхности и окончательно обеспечивается точность детали.
Контроль в ТП предусмотрен с целью технологического обеспечения заданных параметров качества обработанной детали.
Разработанный ТП должен содержать общий план обработки детали и описание содержания операций ТП и выбор типа оборудования. Он должен быть прогрессивным обеспечивать повышение производительности труда и качества детали сокращать материальные и трудовые затраты и быть экологически безопасным.
Построение технологического маршрута обработки во многом определяется конструктивно-технологическими особенностями детали. Выбор маршрутной технологии существенно зависит от типа производства уровня автоматизации и применяемого оборудования.
При серийном производстве применяют универсальные станки с ЧПУ агрегатные специализированные и специальные станки. Перспективным в серийном производстве является применение гибких производственных систем (линий участков цехов) особенно при наличии условий для групповой организации производства.
Выбор станка на операцию определяется возможностью изготовления на нем деталей необходимой конфигурации и размеров а также обеспечения качества ее поверхности.
В основу разрабатываемого маршрутного техпроцесса положен базовый вариант техпроцесса. На основе анализа базового варианта были внесены следующие предложения по совершенствованию процесса изготовления данной детали:
)так как большинство операций в базовом варианте являются однотипными (точение сверление фрезерование) то учитывая форму детали и тип производства (серийное) имеет смысл применить принцип концентрации операций то есть выполнить необходимую обработку на токарных многоцелевых станках с ЧПУ;
)требуется провести максимально возможную замену режущего инструмента на прогрессивный отвечающий требованиям высокой производительности и экономической эффективности кроме того применение стандартного режущего инструмента позволяет сократить номенклатуру применяемого инструмента;
)точность применяемого оборудования позволяет заменить шлифовальную операцию тонким точением на токарном многоцелевом станке с ЧПУ и совместить ее с другими видами обработки.
С учетом вышеперечисленных предложений был разработан проектный вариант маршрутного технологического процесса.
Проектируемый маршрутный технологический процесс приведен в табл.2.5
Проектируемый маршрутный техпроцесс
Комбинированная с ЧПУ
Многоцелевой токарный па 1П756Ф4
Зубодолбежный па 5M150
Фрезерный с ЧПУ 6Р11Ф3-01
6 Выбор технологических баз и последовательности переходов
Выбор технологических баз имеет первостепенное значение при проектировании технологических процессов. При выборе баз учитывается класс детали вид операции точность и другие факторы.
Для установки заготовок на первой операции технологического процесса используют черные (необрабатываемые) поверхности применяемые в качестве технологических баз. Эти поверхности используют однократно при первой установке так как повторная установка на необработанную поверхность может привести к значительным погрешностям во взаимном расположении обработанных при этих установках поверхностей. Выбранная черная база должна обеспечивать равномерное распределение припуска на механическую обработку и наиболее точное взаимное расположение обработанных и необработанных поверхностей детали. В качестве черных баз принимаем наружную цилиндрическую поверхность и торец 7 (рис.2.1).
На первых операциях технологического процесса обрабатывают будущие базы (это основные плоские поверхности и отверстия). В качестве технологических баз для последующей обработки принимаем внутреннюю цилиндрическую поверхность 2 и торец 3 (рис.2.1).
Содержание и последовательность выполнения технологических переходов
Последовательность выполнения технологических переходов должна обеспечивать достижение заданной точности и экономию вспомогательного времени. Применение принципа концентрации операций многоцелевых с автоматической сменой инструмента позволяет достичь указанных требований.
Анализ конструкции детали на технологичность применяемого оборудования и базового технологического процесса показывает что обработку данной крышки возможно провести за четыре установа. По количеству необходимого инструмента и приспособлений обработку крышки выполняем за четыре операции.
Операция 005. Установ на черновые базы. Обработка детали с одной стороны. На данной операции технологические переходы будут следующими:
)точение торца крышки (пов.1);
)точение торца крышки (пов.4);
)точение торцевой канавки (пов.3);
)черновое растачивание отверстия (пов.2);
)чистовое растачивание отверстия (пов.2);
)тонкое растачивание отверстия (пов.2);
)точение поверхности 10;
)точение поверхности 7;
)точение канавки (пов.5);
)точение поверхности 6;
)фрезерование паза (пов.9);
)фрезерование паза (пов.8);
Операция 010. Установ на обработанное отвестие диаметром 180мм и торец. Обработка детали с другой стороны. На данной операции технологические переходы будут следующими:
)точение торца крышки (пов.2);
)точение торца крышки (пов.5);
)растачивание отверстия (пов.3);
)черновое растачивание отверстия (пов.1);
)чистовое растачивание отверстия (пов.1);
)тонкое растачивание отверстия (пов.1);
) черновое точение поверхности 7;
)чистовое точение поверхности 7;
)тонкое точение поверхности 7;
)точение цилиндрической поверхности 10;
)точение канавки (пов 8);
)точение торцевой канавки (пов.4);
)точение торцевой канавки (пов.6);
)черновое точение канавки (пов.6);
)чистовое точение канавки (пов.6);
)центровка всех крепежных отверстий.
)сверление 12 отверстий 7Н14;
)нарезание резьбы в 12-и отверстиях М8-7Н;
)сверление 12 отверстий 15Н14;
)фрезерование пазов (пов.8 и 10);
Операция 015. Установ на обработанное отвестие диаметром 180мм и торец.
На данной операции производят долбление зубьев.
)долбить зубья (пов.1);
Операция 025. Установ на обработанное отвестие диаметром 180мм и торец. Обработка шести наклонных отверстийдетали. На данной операции технологические переходы будут следующими:
)центровка шести отверстий;
)сверление шести отверстий;
7 Выбор средств технологического оснащения
Наиболее универсальными и удовлетворяющими требованиям принципа концентрации являются многоцелевые станки. Многоцелевые станки токарной группы позволяют объединять на одном рабочем месте токарную сверлильную фрезерную обработку нарезание резьбы. Автоматическая смена инструмента позволяет значительно сократить вспомогательное время. Особенно эффективны такие станки в серийном и мелкосерийном производстве в условиях широкой номенклатуры обрабатываемых деталей.. Исходя из вышеизложенных преимуществ выбираем многоцелевой токарный полуавтомат 1П756Ф4. При этом учитывалось соответствие габаритных размеров заготовок по отношению к размерам рабочей зоны оборудования требования обеспечения точности и качества обрабатываемой поверхности.[8]
Станки модели 1П756Ф4 предназначены для комплексной обработки в автоматическом режиме сложных деталей из черных цветных металлов и легких сплавов станки оснащены устройствами ЧПУ инструментальными магазинами механизмами смены инструмента замены деталей и устройствами удаления стружки.
Станки модели 1П756Ф4 предназначены для работы как в режиме автоматического функционирования так и для работы в составе ГПС. Станки обеспечивают возможность высокопроизводительного выполнения основных технологических операций металлообработки:
)точение различных поверхностей включая криволинейные и сложно-пространственные формы;
)центрование сверление рассверливание зенкерование и развертывание точных отверстий;
)растачивание отверстий с точным координатным расположением;
)нарезание резьбы метчиками и резцами.
К необходимой технологической оснастке относятся: станочные приспособления для закрепления детали режущий и вспомогательный инструмент.
Режущий инструмент выбираем соответствующим технологическим переходам по [6].
8) резец проходной SSSCR88D06 Т15К6 ТУ 19-4206-95-83;
567) резец расточной K014980.000-00 T15K6 ТУ 2-035-1040-86;
) резец отрезной 2177-0005 Т15К6 ГОСТ 18892-73;
) резец подрезной 2112-0005 Т15К6 ГОСТ 18880-73
) фреза концевая Т15К6 16 z=6 ГОСТ 6396-78;
10) резец проходной SSSCR88D06 Т15К6 ТУ 19-4206-95-83;
6131516) резец расточной K014980.000-00 T15K6 ТУ 2-035-1040-86;
9) резец подрезной 2112-0005 Т15К6 ГОСТ 18880-73
) резец специальный Т15К6;
14) резец отрезной 2177-0005 Т15К6 ГОСТ 18892-73;
) сверло центровочное 035-2317-0102 ОСТ 24-20-5-80;
)сверло2300-6983ГОСТ 886-77;
)метчикМ8Н2ГОСТ 3266-81;
)сверло6113-0852ГОСТ 22627-77;
) фреза концевая01.03.0036.000-04 ТУ 2-035-812-81;
) фреза концевая01.03.0036.000-03 ТУ 2-035-812-81;
Долбяк m6*z21IА 2530-0268 ГОСТ 9323-79;
Вспомогательный инструмент выбираем для соответствующего режущего инструмента по [6].
)Резцедержатель с цилиндрическим хвостовиком с перпендикулярным открытым пазом 1-30 ОСТ2 П15-3-84;
)Резцедержатель удлиненный с цилиндрическим хвостовиком с перпендикулярным и параллельными открытыми пазами 1-30 ОСТ2 П15-5-84
)Втулка переходная с цилиндрическим хвостовиком 30-16 ОСТ2 П12-12-84;
)Втулка переходная с цилиндрическим хвостовиком 80-40 ОСТ2 П12-12-84;
)патрон цанговый с диапазоном зажима 5-25мм19-11 ГОСТ 17201-71;
)патрон регулируемый резьбонарезной М3-М106161-0173 ГОСТ 22627-77;
)патрон цанговый 191113040 ТУ 2-035-986-85
Измерительный инструмент:
-штангенциркуль ШЦ-1 ГОСТ 166-80;
-нутромер ТУ 3-3-1396-76;
-пробка-калибр 15H14 ПР ГОСТ 14815-69;
-пробка-калибр 15H14 НЕ ГОСТ 14816-69;
-штангенглубиномер ШГ-200 ГОСТ 162-80;
-пробка-калибр М8-7Н 221-3036 ГОСТ 14821-69;
-пробка-калибр 7H12 ГОСТ 14810-69;
-индикатор ИЧ10кл0 ГОСТ 577-68;
-штатив Ш-11Н-8 ГОСТ 10197-70;
-приспособление специальное
образцы шероховатости поверхностей ГОСТ 2789-73;
8 Расчет припусков и операционных размеров
При проектировании технологических процессов механической обработки заготовок необходимо установить оптимальные припуски которые обеспечили бы заданную точность и качество обрабатываемых поверхностей
Для отверстия 125G7(+0.054;+0.014) и наружной цилиндрической поверхности 345(+0061;+0.004) расчет припусков операционных размеров и размеров заготовки проведём расчетно-аналитическим методом. Для остальных поверхностей расчет проведём опытно-статистическим методом.
8.1. Расчет припусков аналитическим методом
8.1.1. Расчет припусков на диаметр 345k7(+0.061;+0.004)
Проведем расчет припусков на обработку и промежуточных предельных размеров для поверхности с размерами 345k7(+0.061;+0.004) по методике изложенной в [2].
)Обработка данной поверхности состоит из чернового чистового и тонкого точения . Записываем переходы обработки в таблицу 5. В таблицу также записываем соответствующие заготовке и каждому технологическому переходу значения элементов припуска Rz и h.
) Отклонение расположения
Отклонение расположения рассчитываем по формуле:
где см – смещение принимаем 750мкм;
кор - корбление принимаем 500мкм;
з=корсм = 750500 = 810 мкм
Остаточное отклонение расположения заготовки определяют по формуле:
где kу – коэффициент уточнения (после черновой обработки 006)
ост = 810 0.06 = 40 мкм
В связи с закономерным уменьшением отклонений расположения поверхностей при обработке за несколько переходов на стадиях чистовой и отделочной обработки ими пренебрегают.
) Погрешность установки у определяется по формуле:
где б - погрешность базирования;
з - погрешность закрепления;
пр - погрешность приспособления.
Погрешность установки при укрупненных расчетах можно определить по справочной литературе в зависимости от схемы закрепления заготовки диаметра базы качества обработки базы. По [7] она составляет 300 мкм.
Остаточные погрешности устаноки:
kу – коэффициент уточнения (после черновой обработки 006)
у ост= 300 0.06 = 15 мкм
В связи с закономерным уменьшением погрешности при обработке за несколько переходов на стадиях чистовой и отделочной обработки ими пренебрегают.
) Рассчитываем минимальные припуски 2Zmin по формуле [7]:
Zmin = 2 (Rz + h + i-1 + уост i(2.15)
) Рассчитываем значение dр формуле:
dр i-1 = dр i - 2Zmin i(2.16)
черновое точение570 мкм
чистовое точение140 мкм
тонкое точение65 мкм
) Записываем значения dmin округляя значения dр.
) Рассчитываем dmax по формуле
dmax i-1 = dmin i + Tdi(2.17)
) Определяем припуски на механическую обработку по формуле:
zmax i = dmax i-1 - dmax i(2.18)
zmin i = dmin i-1 - dmin i(2.19)
Расчет припусков на обработку и предельных размеров на размер 345k7(+0.061;+0.014)
Расчетный припуск 2Zmin мкм
Расчетный размер dр мм
Предельные размеры по переходам
Проверка расчета: Tdз - Tdд + 2Zmax - 2Zmin = 3200 - 57 + 2996 – 6139 = 0
8.1.2. Расчет припусков на диаметр 125G7(+0.054;+0.014)
Проведем расчет припусков на обработку и промежуточных предельных размеров для поверхности с размерами 125G7(+0.054;+0.014).
)Обработка данной поверхности состоит из чернового чистового и тонкого растачивания . Записываем переходы обработки в таблицу 6. В таблицу также записываем соответствующие заготовке и каждому технологическому переходу значения элементов припуска Rz и h.
где экс - эксентриситет принимаем 1400мкм
см – смещение принимаем 500мкм;
з=14002 + 5002 = 1480 мкм
ост = 1480 0.06 = 74 мкм
Погрешность установки при укрупненных расчетах можно определить по справочной литературе в зависимости от схемы закрепления заготовки диаметра базы качества обработки базы. По [7] она составляет 60 мкм.
уост= 60* 0.06 = 3 мкм
) Рассчитываем минимальные припуски 2Zmin
) Рассчитываем значение dр
черновое точение400 мкм
чистовое точение100 мкм
тонкое точение40 мкм
) Определяем припуски на механическую обработку
Расчет припусков на обработку и предельных размеров на размер 125G7(+0.054;+0.014)
Расчет. припуск 2Zmin мкм
Расчет. размер dр мм
Проверка расчета: Tdз - Tdд + 2Zmax - 2Zmin = 2500 - 40 + 5054 – 7514 = 0
8.2 Расчет припусков опытно-статистическим методом
Расчет припусков ведем по методике изложенной в [1].
Масса детали m = 10.2 кг
Масса штамповки m = 16 кг (Ким = 0.637)
Материал штамповки - Сталь 38XС ГОСТ 4543-71
) Назначаем припуски на размеры с учетом конструктивных особенностей заготовки по рекомендуемым данным табл.17 и допуски по табл.22 [1]. Размеры детали припуски допуски размеры заготовки в таблицу 2.8.
Размеры заготовки - штамповки
9 Расчет режимов резания
Определение режимов резания ведётся одновременно с заполнением операционных карт технологического процесса в которых должны быть данные об оборудовании о способе обработки характеристики обрабатываемой детали которые используются для расчетов режимов резания.[8]
В качестве глубин резания принимаем максимальные припуски.
Подачи при чистовой обработке выбирают в зависимости от требования параметра шероховатости обработанной поверхности и радиуса закругления при вершине режущего инструмента [8].
Скорость резания для токарной обработки определяется по формуле:
V=(Cv*Kmv*Knv*Kuv*Kv*K1v*Kr)(Tm*tx*Sy)(2.20)
где Cv - учитывает факторы не вошедшие в формулу;
Kmv - коэффицент учитывающий влияние физико - механических свойств обрабатываемого материала;
Knv - коэффицент учитывающий влияние состояния поверхностного слоя;
Kuv - коэффицент учитывающий влияние инструментального материала;
Kv - коэффицент учитывающий влияние главного угла в плане;
K1v - коэффицент учитывающий влияние вспомогательного угла в плане;
Kr - коэффицент учитывающий влияние радиуса на вершине резца;
m - показатель степени учитывающий период стойкости инструмента;
y - показатель степени учитывающий величину подачи;
Частота вращения шпинделя рассчитывается по формуле:
где d-расчетный диаметр мм
Подача минутная определяем по формуле:
где n- частота вращения шпинделя обмин;
Пример расчета режимов резания для точения.
Черновое точение торца.
Период стойкости инструмента Т = 50мин
Глубина резания t = 22 мм; Подача S = 0.6 ммоб
Расчетный диаметр d = 140 мм
Используя [8] назначим коэффиценты
Cv =330; Kmv=064; Kr =1; Knv=0.8; Kuv=1; Kv=0.8; K1v=1; y=0.45; m=0.2;
V=(330*0.64*0.8*0.8*1*1*1) (5002*2.20.15*0.60.45) = 74 ммин
n=1000*743.14*140 = 168 обмин
Sм=0.6*168 = 101 мммин
Определение режимов резания для сверления.
V= (Cv*Dq*Kv)Tm*Sy(2.23)
q - коэффицент учитывающий диаметр сверления;
Пример расчета режимов резания для сверления;
Сверление отверстия диаметром 15 мм;
S=0.23ммоб; T=45мин;
По справочной литературе [17] назначим коэффиценты:
Cv =9.8; Kmv=064; K Kuv=1; y =0.5; m =0.2; q =0.4;
V=(9.8 * 150.4 * 0.64*1*1)(4502*0.230.5) = 17.9 ммин;
n=1000*17.93.14*15 = 355 обмин;
Sм=023*355=816 мммин;
Определение режимов резания для фрезерования.
V=Cv*Dq*Kv Tm*t(2.25)
где D - диаметр фрезы; Sz - подача на зуб; B - ширина фрезерования;
z - число зубъев фрезы;
u - коэффицент учитывающий ширину фрезерования;
p - коэффицент учитывающий число зубъев фрезы;
Пример расчета режимов резания для фрезерования;
Фрезерование паза концевой фрезой 40;
T= 120 мин; q = 0.44; y=0.26; u = 0.1; Sz =0.15 обмин; p =0.13; m =0.37;
V=(234*400.44*0.51)(1200.37*2.50.24*0.150.26*200.1*40.13) = 83 ммин;
n=1000*833.14*40= 660 обмин;
Sм=015*4*660 = 396 мммин
Определение режимов резания при нарезании резьбы.
V=Cv*Dq*KvTm*Sy(2.28)
где D - диаметр резьбового отверстия;
Kv=Кmv+Kuv+Kтv;(2.29)
Пример расчета режимов резания при нарезании резьбы ;
Нарезание резьбы в отверстии М8
Кmv=0.8; Kuv=1; Kтv=1.25; S=1.5ммоб; Cv=64.8; y=0.5; q=1.2; m=0.9; T=90 мин.
V =64.8*81.2*0.8*1*1.25 900.9*1.50.5 = 5.6 ммин;
n=1000*5.63.14*8 = 223 обмин
Sм=223*15 = 334 мммин
Для остальных переходов режимы резания расчитаны аналогично и занесены в таблицы 2.9 - 2.12
Режимы резания на операцию 005
Режимы резания на операцию 010
Режимы резания на операцию 015
Режимы резания на операцию 020
Проверка мощности станка.
где Cp =300 - коэффицент учитывающий параметры не вошедщие в формулу;
t = 4 мм - глубина резания;
S = 0.6 мм - подача;
y = 0.75 - показатель степени учитывающий влияние подачи;
V = 74 ммин - скорость резания;
n = -0.15 - показатель степени учитывающий влияние скорости резания;
Kp = Kmp*Kp*Kp*(2.32)
где Kmp = 158 - коэффицент учитывающий влияние материала;
Kp = 1 - коэффицент учитывающий влияние угла ;
Pz = 10*300*4*0.60.75*74-0.15*1.58*1*1*1 = 67773 H;
Определение потребной мощности
N = Pz*V 1020*60 30;(2.33)
N = 67773*74 1020*60 = 8.1 30 кВт;
Обработка на станке 1П756Ф4 при при данных режимах обработки возможна.
10Техническое нормирование операции
10.1Техническое нормирование 05 операции
Техническое нормирование операции производим с учетом формул [9]. Данные по нормам времени выбираем из [10].
Основное время рассчитывается по формуле:
где l – длина пути резания
Автоматическое вспомогательное время
Учитывая приближенность данного расчета для нормирования вспомогательного времени используем усредненные данные по конкретному станку - время на смену инструмента равное 12 с и время вспомогательных быстрых перемещений без учета времени на разгон и торможение рабочих органов станка реализацию специфических технологических приемов и т.п.
tв а = tсм i + tуп(2.35)
где tсм – время на смену инструмента tсм = 12 с;
tуп – время ускоренных перемещений tуп=57 с.
tв а = 14 + 57 = 111 мин
Штучное время рассчитывается по формуле:
tшт =( tавт + tвсп.р) (1+) (2.36)
где tавт - автоматическое (программное) время рассчитываемое по формуле:
где tо –основное время на обработкуtо а = 393 мин
tв а - автоматическое вспомогательное времяtв а = 111 мин
tавт = 393 + 111 = 504 мин
tв р = tуст.+ tзакр + tвкл;
tв р -вспомогательное ручное время не перекрываемое машинным временем
tуст.- время на установку и снятие деталиtуст.=0.19 мин
tзакр.- время на закрытие и открытие рабочей зоныtзакр.=0.06 мин
tвкл.- время на включение и выключение станкаtвкл.=0.06 мин
tвсп.р = 0.06 + 0.06 + 019 = 0.31 мин
k=7-коэффициент учитывающий время на личные потребности регламентированные перерывы обслуживание рабочего места
tшт = (504 + 0.31) 107 = 552 мин
Подготовительно-заключительное время
Подготовительно-заключительное время рассчитываем по формуле:
Тпз = Тпз1+ Тпз2 + Тпз3(2.37)
где Тпз1= tпз+tозн+ tинс+ tус.инст+ tус.пр.+ tпр.сч.уст.+ tв.пр+ tуст.нуля +tпр.обр(2.38)
где tпз - время на получение задания и инструментаtпз = 9 мин
tозн - время на ознакомлениеtозн = 2 мин
tинс - время на инструктаж мастераtинс = 2 мин
tус.инст - время на установку снятие инструментаtус.инст = 1 мин
tус.пр. - время на установку снятие программоносителя tус.пр. = 1 мин
tпр.сч.уст. - время на проверку работоспособности считывающего устройстваtпр.сч.уст. = 12 мин
tв.пр - время на ввод программы в память tв.пр = 14 мин
tуст.нуля - время на установку координат станка для инструмента tуст.нуля = 25 мин
tпр.обр - время на пробную обработку;tпр.обр =6 мин
Тпз= 4 + 2 + 2 + 5*1 + 1 + 1.2 + 1.4 + 25*5 +6 = 35 мин
Штучно-калькуляционное время
Штучно-калькуляционное время рассчитываем по формуле:
где n - партия запуска n = 400
tшт.к.= 552 +35400 = 5.6 мин
Для остальных операции расчет проведен аналогично
операция Тпз= 35; tшт =1622 мин; tшт.к =163 мин
операция Тпз= 31; tшт =195 мин; tшт.к =1957 мин
операция Тпз= 30; tшт =1225 мин; tшт.к =1232 мин
операция Тпз= 15; tшт =17 мин; tшт.к =1704 мин
операция Тпз= 13; tшт =21 мин; tшт.к =213 мин
операция Тпз= 24; tшт =693 мин; tшт.к =699 мин
11 Технико-экономическое обоснование технологического
Целесообразность разработанного ТП механической обработки заготовки на основе сравнительной экономической эффективности двух вариантов: базового и проектного.
Экономическая эффективность рассчитывается по величине годовой экономии на приведенных затратах [11]
гдеСп' Сп"-сумма годовых приведенных затрат базового и проектного вариантов руб.
Сп= (Стi+Eн*Ki)(2.40)
где i-номер технологической операции
Cтi-годовая технологическая себестоимость i-ой операции руб.
Ki-сумма годовых капитальных затрат i-ой операции руб.
Ен-нормативный коэффициент эффективности капитальных вложений Ен=0.15
Определение капитальных затрат
Капитальные затраты определяем по формуле:
Кi=Срi(Коi+Кздi+Кслi+Кжi+Кпуi)(2.41)
где Срi-расчетное количество станков требуемых для обработки годового выпуска деталей на i-ой операции шт.
Коi- вложение средств в оборудование руб.
Кздi- вложения в производственные помещения руб.
Кслi- вложения в служебно-бытовые помещения руб.
Кжi- вложения в жилищное и культурно-бытовое строительство руб.
Кпуi-вложения в комплект управляющих программ руб. (определяется по таблицам)
Вложение средств в оборудование определяем по формуле:
Коi=Ктоi+Кптi+Ккi (2.42)
где Ктоi-вложения в технологическое оборудование руб.
где Цтоi-оптовая цена станкаруб.
Кт-коэффициент учитывающий расходы на транспортировку
Кптi-вложения в подъемно-транспортное оборудование руб.
Ккi-вложения в средства контроля руб.
Вложения в производственные помещения определяем по формуле:
Kздi=Цпп (S+Sy) Y(2.44)
где Цпп-стоимость 1 кв.м производственной площади механического цеха р.
S-площадь занимаемая станком кв.м
Sy-площадь занимаемая выносными элементами кв.м
Y-коэффициент учитывающий дополнительную производственную площадьприходящуюся на дополнительное оборудование Y=4
Кслi=Цсп*Sсл(Рст+Рн+Рдоп) (2.45)
гдеSсл-площадь служебно-бытовых помещений приходящегося на одного рабочего (7 кв.м)
Цсп - стоимость 1кв.м служебно-бытовых помещений Цсп=200 руб.
РстРн - количество станков и наладчиков приходящихся на один станок
Рст = (tш-к*N)(60*Fр*Kв*d)(2.46)
где Fр- действительный годовой фонд времени рабочего (1860 ч)
Kв- средний коэффициент выполнения нормы времени Кв=1.2
d-количество станков обслуживаемых одним рабочим шт.
Рн=(tн*N)(60*Fр*n) (2.47)
где tн- время наладки станка и время пробной обработки
n-число деталий в партии запуска
Рдоп-дополнительная рабочая сила приходящаяся на один станок с ЧПУ и затрачиваемая на подготовку управляющей программы обслуживание и ремонт.
Рдоп=0.5[(tш-к*N+tн*Sп)(Fo*60*Kзаг)] (2.48)
где Fo-эффективный годовой фонд времени работы оборудования
Кзаг-коэффициент загрузки
Кжi=Цж(Рст+Рн+Рдоп) (2.49)
где Цж - стоимость жилкультбытстроительства приходящегося на одного рабочего Цж=6600 руб.
Расчет технологической себестоимости приближенным способом
Основан на использовании нормативов себестоимости одного машино-часа работы оборудования.
Стi=(Счс+Счи+Счэ+Сча+Счр+Счэл+Счп+Счир)*tш-к*N6000+Собсл+Спу+Спп+Ссл (2.50)
где Счс Счн Счэ-нормативы затрат по заработной плате станочников наладчиков и электронщиков приходящихся на 1 час работы оборудованиясо всеми начислениями кч
Сча Счр Счэл-нормативы затрат на амортизацию оборудования ремонт и электроэнергию приходящихся на 1 час работы станкакч
СчпСчир-нормативы затрат на амортизацию и ремонт приспособлений и инструмента на 1 час работы кч
Собсл-годовые затраты на обслуживание и ремонт ЧПУ руб.
Спу-годвые затраты на подготовку и возобновление управляющих программ руб.
СппСсл-годовые затраты на амортизацию и содержание производственных и служебных помещений руб.
Сравнение вариантов технологических процессов
Для расчета экономической эффективности используем программу на ЭВМ
Объем годового выпуска деталей4800шт
Количество операций в базовом варианте10
Количество операций в проектном варианте2
Коэффициент выполнения норм для станков:
с ручным управлением12
Коэффициент инфляции в станкостроении1
Маршрут обработки в базовом техпроцессе 005 токарная с ЧПУ
5 Комбинированная с ЧПУ
0 Комбинированная с ЧПУ
Маршрут обработки в проектном техпроцессе
5 Комбинированная с ЧПУ
где tшт-к.- штучно-калькуляционное время.
Fo – эффективный годовой фонд времени работы станка.
S+Sу – суммарная площадь занимаемая станком с выносным оборудованием.
Цто – оптовая цена станка без учета коэффициента инфляции.
Ср – расчетное количество станков на данной операции.
К – сумма годовых капитальных затрат на данной операции.
Ст – годовая технологическая себестоимость данной операции.
Сп – годовые приведенные затраты на данной операции.
Величина годовой экономии на приведенных затратах:74827245 руб.
КОНСТРУКТОРСКИЙ РАЗДЕЛ
1.Расчет станочных и контрольных приспособлений.
1.1 Конструирование и расчет станочного приспособления.
1.1.1 Проектирование фрезерного приспособления
Для установки и закрепления детали на станке 6Р13Ф3-01 было спроектировано приспособление. Конструкция этого приспособления приведена в графической части.
Краткие сведения о работе этого приспособления.
Базирование обрабатываемой детали на данном приспособлении происходит по центральному отверстию торцу а в угловом положении по одному из крепежных отверстий.
Закрепление заготовки производится механизированным приводом. Привод перемещает шпильку 2 и прихват 3 вправо при этом пальцы стакана 6 входящие в винтовые пазы прихвата поворачивают последний и затем происходит закрепление заготовки. Поворот прихвата необходим для облегчения снятия - установки обрабатываемой детали.
Расчет сил закрепления
Расчет сил закрепления производится с учетом действия осевой силы. Действием крутящего момента в данном случае можно пренебречь.
Рис. 3.1. Схема для расчета силы закрепления от смещения.
Р - осевая сила [H];
Q - cила закрепления;
f - коэффицент трения;
Р=10Ср*Dq*Sy*Kp(3.1)
где Ср =68 - коэффицент учитывающий обрабатываемый материал вид обработки материал режущей части инструмента.
D = 6 мм - диаметр обрабатываемого отверстия
q = 1; - показатель степени.
S = 023 ммоб - подача;
y = 0.7 - показатель степени;
D=04 м - диаметр заготовки;
Kp=158 - коэффицент учитывающий материал обрабатываемой заготовки.
Р=10*68*61*02307*158=2304Н
Q = k*P(f1+3*f2) - исходная сила;
f1 = f2 = 018 - коэффицент трения;
К =2.5 - коэффицент запаса учитывающий нестабильность силовых воздействий на заготовку;
Q = 2.5*2304(0.18+3*0.18) = 8000H
Данную силу на тяге может обеспечить пневмогидропривод двустороннего действия диаметром 53 мм
1.1.2 Проектирование токарного приспособления
Для установки и закрепления детали на станке 1П756Ф4 был спроектирован патрон с быстрой переналадкой положения кулачков. Конструкция этого патрона приведена в графической части.
Краткие сведения о работе и переналадке этого патрона.
Подкулачники 11 патрона зацепляются со спиральным диском 12 в котором выполнен зубчатый венец внутреннего зацепления являющийся наружным колесом планетарной передачи. Центральная шестерня 15 передачи установлена на шлицах ползуна 9. Винтовые пазы ползуна взаимодействуют с пальцами кольца 5 закрепленного на корпусе патрона. На водиле 7 планетарной передачи установлнны сателлиты 13 и колесо самотормозящейся червячной передачи. Выступы на торцах червяка 17 входят в отверстия втулок 8.
Для переналадки положения кулачков на требуемый диаметр ключом вращают втулку 8 которая посредством червяка и колеса 4 поворачивает водило. При этом сателлиты обкатываясь по неподвижной шестерне вращают спиральный диск перемещая радиально кулачки на требуемый диаметр.
Закрепление кулачков призводится механизированным приводом. Привод перемещает тягу 14 и ползун 9 влево при этом пальцы кольца 5 входящие в винтовые пазы ползуна поворачивают последний в результате центральная шестерня поворачивает спиральный диск перемещающий кулачки 3. При этом вследствии самоторможения червяка водило остается неподвижным.
Механизм патрона состоит из двух элементарных зажимных механизмов:
)клиноплунжерного в котором клиновыми парами являются пальцы кольца и пазы ползуна;
)центрирующего клиноплунжерного в котором клиновыми парами являются витки спирали и зубья реек на кулачках а плунжерами - три кулачка скользящие в направляющих корпуса патрона.
Уравнение сил механизма патрона в общем виде
W - суммарная сила зажима заготовки в патроне;
где К =2.5 - коэффицент запаса учитывающий нестабильность силовых воздействий на заготовку;
M = Pz * h; - момент от силы резания Рz;(3.4)
h = 0156 м - плечо действия силы
n = 3 - колличество кулачков;
f = 018 - коэффицент трения;
i2 - передаточные отношения клиноплунжерных механизмов.
Так как в винтовой паре 1 винтовой паз действует на палец кольца 5 как односкосый клин то (3.5)
Так как в винтовой паре 2 виток спирали действует на зуб рейки кулачка как односкосый клин с трением только по наклонной поверхности то
М = 67773 * 0156 = 1057 Нм
W = 2*25*1057 04*018 = 73420 Н;
Q = 73420*0.121*0.121 = 1075 H;
Данную силу на тяге патрона может обеспечить поршневой пневмоцилиндр двустороннего действия диаметром 63 мм (ГОСТ 15608-81) при давлении 063 МПа
1.2 Конструирование и расчёт контрольного приспособления.
Разработаем контрольное приспособление для проверки трех поверхностей (торцевое биение поверхностей 13 17 (рис. 2.1) и радиальное биение поверхности 1 (рис.2.1) не более 005 мм относительно поверхностей 3 и 2). Вращение детали будет осуществляться с помощью электродвигателя а её зажим подъём и отвод индикаторов с помощью пневмоцилиндров. Общий вид приспособления приведен на рис.3.2. Деталь (поз.5) устанавливается на поворотный стол (поз.9). Закрепление производится с применением пневмопривода передающего толкающее усилие на клиновую пару (поз.2 и 4). Три ползуна (поз.4) в свою очередь непосредственно закрепляют заготовку.
Произведём расчет частоты вращения детали на столе приспособления:
Условно зададим вращение детали 60 обмин. Выберем двигатель с небольшой мощностью 4А80В с частотой вращения 1500 обмин. Тогда передаточное отношение должно быть n=150060=25 такое передаточное отношение можно задать с помощью однозаходной червячной пары.
Подберём пневмоцилиндры для зажима детали и поднятия стойки с датчиками.
В связи с тем что силы возникающие в процессе контроля и поднятия стойки с датчиками малыследовательно большого усилия на штоке пневмоцилиндра не требуется. Исходя из этого пневмоцилиндры двустороннего действия с минимальными толкающими и тянущими усилиями на штоке по ГОСТ 15608-81.
Основные параметры пневмоцилиндра приведены в таблице 3.1
Статическая сила на штоке Мпа
При конструировании приспособлений следует исходить из следующих основных принципов: 1.Максимальная унификация и стандартизация конструкции в которой должна должна быть обоснована необходимость использования оригинальных деталей и сборочных единиц; 2.Ориентация на типовые конструкции приспособлений; 3.Стремление к наибольшей простоте приспособления при выполнении требуемой жесткости и прочности конструкции; 4.Обепечение длительности срока и удобства эксплуатации высокой степени ремонтопригодности.
При проектировании приспособлений для ГПС особенно важно стремиться к достижению более высокой степени переналадки.
Рис.3.2 Конструкция контрольного приспособления.
Суммарная погрешность контрольного приспособления может быть расчитана по формуле [12]
=у +p +э +б 2+з 2+п 2+э 2+м 2(3.2)
где у-систематическая составляющая погрешностей изготовления установочных элементов приспособления;
p-ситематическая составляющая погрешностей передаточных устройств;
э-систематическая составляющая погрешностей эталона;
б - погрешность базирования детали в контрольном приспособлении;
з - погрешность закрепления детали в приспособлении;
п - случайная составляющая погрешность передаточных устройств;
э-случайная составляющая погрешность изготовления эталона;
м - погрешность метода измерения вызываемые погрешностями измерительных (отсчётных) устройств колебаниями температуры и т.д.
Если систематические погрешности у p э могут быть учтены при настройке контрольного приспособления то они исключаются из расчёта.
Суммарная погрешность не должна превышать 20 30% допуска контролируемого параметра.
При разработке многомерных контрольных приспособлений в которых за одну установку проверяется несколько параметров суммарная погрешность сопоставляется с наименьшим из допусков контролируемых параметров.
Произведём расчёт погрешности контрольного приспособления при контроле торцевого биения.
В связи с тем что на рассматриваемом приспособлении измеряется не абсолютная величина а относительная (торцевое биение) принимаем погрешности у p ээ =0.
При данной схеме установки и закрепления б и з=0
Погрешность метода измерения при использовании электроконтактных датчиков м=0001мм
Погрешность передаточных устройств у данного приспособления п=0015мм
Рассчитанная погрешность составляет 30% от контролируемого параметра (0.05 мм) следовательно точность контрольного приспособления обеспечена.
Расчет погрешности контрольного приспособления при контроле радиального
биения поверхности 1.
В связи с тем что на рассматриваемом приспособлении измеряется не абсолютная величина а относительная (радиальное биение) принимаем погрешности у p ээ =0.
При данной схеме установки и закрепления б = 0; з=001 мм
Погрешность передаточных устройств у данного приспособления п=0005 мм
2 Проектирование средств автоматизации производственных процессов
«Проектирование РТК»
Наиболее целесообразной формой внедрения ПР в серийное производство служит применение роботизированных технологических комплексов (РТК) на базе которых в дальнейшем возможно создание роботизированных технологических участков цехов заводов. На базе одних и тех же моделей станков могут создаваться РТК различных компоновок.
Компоновка РТК механической обработки показана в графической части. Многостаночный РТК механической обработки деталей тел вращения выполнен по линейной схеме с роботом портального типа (УМ160Ф2.81.01)
Линейные компоновки РТК с применением портальных ПР характеризуются следующими особенностями: занимают небольшую производственную площадь; обеспечивают переналадку и ремонт оборудования без остановки работы всего комплекса возможность визуального наблюдения за работой оборудования обеспечивает безопасные условия обслуживающему персоналу.
Данный комплекс предназначен для комбинированной обработки деталей массой до 160 кг в условиях серийного производства. ПР в составе комплекса выполняет следующие операции: загрузку станков (1П756Ф4) заготовками выгрузку межоперационное транспортирование раскладку деталей на столах-накопителях.
Заготовки в магазине-накопителе располагаются в ориентированном виде. Комплекс включает в себя два станка типа «обрабатывающий центр» и промышленный робот портального типа два магазина-накопителя систему ЧПУ промышленного робота.
На станках производится обработка детали с двух сторон.
Управление роботом осуществляется устройством модели УПМ-331. Данное устройство предусматривает возможность работы в режиме диалога «станок-робот». Устройство построено по принципу синхронного микропрограммного автомата с конечным числом состояний и жестким циклом управления. Устройство унифицировано по структурно-алгоритмическому и конструкторско-технологическому признакам. Операционно-логический блок совместно с микропрограммным автоматом обеспечивает взаимодействие всех блоков устройства и выполняет функцию центрального управления и логической обработки информации.
Проектирование и выбор отдельных узлов агрегатов и устройств.
Магазин-накоптель предназначенный для накопления и подачи заготовок типа «диск». Магазин может встраиваться в состав любых видов роботизированных систем обработки деталей типа «тела вращения». Для возможности использования его с другими типами оборудования предусмотрено регулирование по высоте а также замена некоторых видов направляющих
Захватное устройство промышленного робота.
Захватное устройство промышленного робота предназначено для захватывания предмета обработки и удержания его в процессе перемещения. Захват детали производится по наружным поверхностям.
Данное захватное устройство оснащено встроенным датчиком касания пружинно-рычажного типа. Схват предназначен для деталей типа дисков. Так же данный схват имеет одну пару губок зажим и разжим которых осуществляется за счёт осевого движения тяги жестко связанных с ней зубчатой рейкой. Рейка находится в зубчатом зацепление с зубчатым сектором нарезаемых на рычагах зажимных губок
Расчёт механических захватных устройств включает проверку на прочность деталей захвата. Кроме того необходимо определить силу привода захватного устройства силу в местах контакта заготовки и губок проверить отсутствие повреждений поверхности заготовки или детали при захватывании возможность удержания заготовки при манипулирование особенно в моменты резких остановок.
Соотношение между силами P и F на губках или моментом M на губках захватного устройства определяют из условий статического равновесия.
Rn – реакция на nй захват от расчётной нагрузки;
f - коэффициент трения губки захвата о деталь;
для закалённых губок без насечки при твёрдости HRC 55 = 0.3-0.35.
где mc – модуль зубчатого сектора
rc – полное число зубьев сектора;
Определим диаметр гидроцилиндра по рассчитанной силе привода:
Для определения фактической производительности необходимо построить циклограмму работы РТК (отобразить совместную работу двух станков и промышленного робота портального типа)
линейные перемещения ммскорость ммс
Угловые перемещения град.скорость градс
На станках ведется параллельная обработка крышки (операция 005)
Последовательность выполняемых команд промышленным роботом станками приведена в таблице 3.2.
Циклограмма работы комплекса изображена на рис. 3.4.
Последовательность выполнения действий РТК
Исходная позиция: рука ПР находится над станком 1 первая позиция захватного устройства свободнаво второй находится заготовка.
Ввод руки в рабочую зону станка =65
Перемещение П.Р x=-18мм
Разжим кулачков патрона
Перемещение П.Р x=18мм
Вывод руки из рабочей зоны станка =-65
Поворот руки ПР =180
Сжатие кулачков патрона
Снятие обработанной заготовки со станка 1 установка новой заготовки
Перемещение к позиции разгрузки (тара):
Опускание руки z=-300мм
Перемещение П.Р x=1700мм
Опускание руки z=-150мм
Перемещение П.Р у=2020мм
Перемещение к станку 2.
Выгрузка обработанной заготовки в тару и загрузка новой заготовки
Снятие обработанной заготовки со станка 2 установка новой заготовки
Перемещение к станку 1.
Выгрузка обработанной заготовки в тару и загрузка новой заготовки.
Рис. 3.4. Циклограмма работы РТК
Определение производительности
где Fф - фактическое время работы РТК за определенный период времени (год месяц смену) ч; Для смены Fф=8ч
Тц - длительность цикла мин (можно определить по циклограмме работы РТК)
ис=075 - коэффициент использования оборудования учитывающий суммарные потери времени.
Разработанный РТК обеспечивает требуемую производительность (50 шт).
ИССЛЕДОВАТЕЛЬСКИЙ РАЗДЕЛ
«Загрузочно - накопительные устройства»
Все загрузочно - накопительные устройства можно подразделить по способам приема хранения перемещения выдачи видам размерам заготовок на группы и подгруппы:
) Конвейеры непрерывного действия;
а) ленточные конвейеры;
б) цепные конвейеры;
в) роликовые конвейеры;
г) двухвалковые конвейеры;
д) винтовые конвейеры;
е) вибрационные конвейеры;
ж) пневматические полусамотечные конвейеры;
з) лотковые самотечные конвейеры;
и) тележечные конвейеры;
) Конвейеры дискретного действия;
а) шаговые конвейеры с убирающимися собачками;
б) шаговые конвейеры с поворачивающимися захватными устройствами
в) перекладывающие планочные конвейеры;
г) пилообразные конвейеры;
д) гребенчатые конвейеры;
е) шаговые конвейеры - накопители с управляемыми собачками;
) Подъемники непрерывного действия;
а) цепные подъемники;
б) вибрационные подъемники;
) Подъемники дискретного действия;
а) шаговые подъемники;
б) толкающие подъемники;
Бункерные загрузочные устройства.
а) ковшеобразные бункеры;
б) цилиндрические с предбункером;
в) ящичные ковшеобразные для стержневых заготовок;
г) ящичные бункеры для плоских заготовок;
д) цилиндрические бункеры для плоских заготовок;
е) автоматические бункеры с дисковым захватным устройством;
ж) автоматические бункеры с ножевым захватным устройством
Магазинные загрузочные устройства.
а) магазины со спиральным лотком;
б) многодисковые магазины для колец фланцев;
в) зигзагообразные магазины;
г) спиральные магазины;
д) стержневые магазины;
е) лотковые магазины для колец фланцев;
ж) магазины с барабанным захватным устройством для валиков;
Магазинные загрузочные устройства также можно подразделить по видам лотков:
жесткие прямые сваренные из полос;
гибкие прямые и изогнутые;
открытые и закрытые;
Основные представители данных групп приведены в графической части.
Далее подробнее рассмотрим каждую из групп
Конвейером называют машину для непрерывного транспортирования изделий. Отличительной особенностью многих конструкций конвейеров наряду с выполнением функций по перемещению заготовок является возможность образования небольших межоперационных заделов обеспечивающих независимую работу сложных станков в составе АЛ. Имеются конструкции конвейеров которые при транспортировании производят распределение заготовок на несколько потоков (см. ниже).
Транспортные средства бывают стационарные т.е. неподвижно установленные на полу цеха и подвижные. К первому виду относят различные конвейеры ко второму - различные тележки (электрокары самоходные тележки работающие по автоматическому циклу и др.).
По способу транспортирования конвейеры делят на непрерывного и прерывистого (дискретного) действия.
Конвейеры непрерывного действия. Наиболее распространены ленточные (рис. 4.1 а) и цепные (рис. 4.1 б) конвейеры. Грузонесущим и тяговым органом для перемещения заготовок 3 в таких конвейерах служит лента 4 (обычно металлическая) или втулочно-роликовая цепь 7 которые натянуты на барабаны 7 или звездочки б смонтированные в корпусе 5. Для предотвращения их провисания предусмотрены направляющие планки 2. Такие конвейеры применяют для относительно легких заготовок 3 допускающих изнашивание поверхности из-за проскальзывания ленты (цепи) под заготовками. Кроме того конвейеры с металлической лентой используют для транспортирования стружки.
Роликовые конвейеры состоят из роликов 2 укрепленных на осях в корпусе 5 (рис. 4.1 в). Роликам сообщается вращение от привода 1 через замкнутую цепь 6 и звездочки 4 закрепленные на осях роликов. Перемещение заготовок 3 или приспособлений-спутников происходит под действием сил трения возникающих между образующей роликов и заготовками что позволяет подавать их с подпором. Ролики посажены на оси с небольшим натягом через фрикционные втулки запрессованные в ролики что позволяет им проскальзывать в момент нахождения под остановленными заготовками. Конвейер-распределитель состоит из корпуса 2 внутри которого на звездочках 7 натянута замкнутая цепь 8 с консольно укрепленными (через шаг) пальцами 4 перемещающими детали 3 (кольца фланцы) по направляющей 5 (рис. 4.1 г). Заготовки подаются в конвейер через механизм приема 1 (с отсекателем) а выдаются через механизмы выдачи 6. Такой конвейер применяют для распределения катящихся заготовок между параллельно действующими станками.
Двухвалковые конвейеры используют для перемещения с подпором цилиндрических заготовок 3 (рис. 4.1 б)) например колец втулок дисков. При перемещении заготовки вращаются что позволяет применить указанные конвейеры для загрузки — выгрузки бесцентровых крупношлифовальных станков. Валковые конвейеры имеют разные исполнения в зависимости от формы валков 5. Наиболее распространенной конструкцией является конвейер с коническими валками с углом конуса при вершине до 2°. Вращение двум валкам укрепленным в корпусе 4 сообщается от привода 1 через цепную передачу 2 и звездочки 6 .установленные на осях валков.
Винтовые конвейеры используют для перемещения заготовок поперек и вдоль оси. В первом случае (рис. 4.1 е) спирали 4 винтов 5 находящихся в корыте 6 расположены так чтобы заготовка 3 лежала между ними без перекоса. Винтам сообщается синхронное вращение от привода 7 через цепную передачу 1 и звездочки 2. Для перемещения заготовок вдоль оси винты установлены таким образом чтобы выступы одного винта свободно входили бы во впадины другого. В этом случае заготовка перемещается по наружной поверхности спиралей между винтами.
Вибрационные конвейеры используют в тех случаях когда затруднительно перемещать заготовки 3 другими способами (например из-за их сцепляемости). Основным недостатком указанных конвейеров является возможность вибрации соседних металлорежущих станков. Конвейер состоит из лотка 2 (рис. 4.1ж) пружин 1 и основания 6. Лоток получает движение от электромагнитного вибратора 4 с упругим звеном 5.
Пневматический полусамотечный конвейер (рис. 4.1 з). Перемещение заготовок 3 в корпусе 4 конвейера расположенного наклонно под углом меньшим угла трения осуществляется сжатым воздухом (давление 001 - 002 МПа) подаваемым через отверстия 5 или 2 просверленные под углом на опорной 4 а иногда и на боковых 1 поверхностях. Заготовки двигаются в корпусе под действием струй сжатого воздуха образующих воздушную прослойку толщиной 001—002 мм между заготовками и поверхностью 4.
Лотковые самотечные конвейеры предназначены для гравитационного перемещения заготовок качением по роликам или скольжением по наклонной (в большей части прямой) поверхности длиной 2—5 м и более (рис. 4.1 и к). Угол наклона конвейеров устанавливается в зависимости от способа перемещения заготовок их массы и материала. При перемещении деталей качением а = 5 10° (рис. 1 и) а при скатывании по роликам а = 3 5° (рис. 4.1 к). Для каждой конкретной заготовки и способа ее перемещения производится подбор угла наклона конвейера с учетом допустимой скорости соударения деталей при которой на поверхности их (при ударах) не образуются дефекты в виде забоин вмятин и пр. Конвейер для перемещения заготовок 4 качением состоит из опорной 3 и двух боковых 2 стенок (рис. 4.1 и). Для предотвращения самопроизвольного выпадания заготовок 4 (особенно при большом угле наклона) предусмотрена предохранительная полоса 1. В конвейерах для перемещения заготовок 4 по свободно вращающимся роликам 6 (рис. 4.1 к) последние устанавливают на осях 8 укрепленных в боковых стенках 2 которые между собой жестко соединяют стяжками 7. В качестве ролика используют шарикоподшипник или два шарикоподшипника запрессованные во втулку. Для уменьшения скорости перемещения заготовок в лотковых конвейерах применяют амортизаторы 5 свисающие ремни а также разные конструкции спусков.
Pиc. 4.1. Конвейеры непрерывного действия
Конвейеры прерывистого действия. Шаговые конвейеры наиболее распространены и бывают двух типов: с убирающимися собачками (рис. 4.2д) или поворачивающимися захватными устройствами (рис.4.2б). У первого типа конвейеров заготовки 3 (спутники) перемещают по направляющим 2 захваты в виде подпружиненных храповых собачек 4 укрепленных на осях в штанге 1 совершающей возвратно-поступательное движение с помощью гидравлического цилиндра 5. При движении штанги вперед собачки упираются в заготовки и перемещают их на шаг. При обратном ходе собачки утапливаются в штангу и проходят под заготовкой не передвигая ее. Основным недостатком конвейера является засорение стружкой храповых собачек. У второго типа конвейеров (см. рис. 4.2 б) заготовки 3 перемещают по направляющим 2 захватные устройства в виде флажков 4 укрепленных неподвижно на круглой штанге 1 совершающей последовательно возвратно поступательное и вращательное движения с помощью гидравлических цилиндров 5 и 7 и рычага 6. При движении штанги вперед флажки упираются в заготовки и перемещают их на шаг. Затем штанга поворачивается на угол (при котором флажки не задевают детали) и возвращаются в исходное положение. Далее флажки опускаются и цикл повторяется. Вероятность засорения стружкой флажков в этом конвейере меньше.
Перекладывающие планочные конвейеры обычно применяют для перемещения заготовок 3 для которых не допускается повреждение обработанной поверхности при скольжении по направляющим 2 (рис 4.2 в). Заготовки движутся по направляющим последовательным перекладыванием посредством планки 1 совершающей движение от вращающихся эксцентриков 4 по сложному циклу: подъем движение вперед опускание движение назад.
Пилообразные конвейеры применяют для перемещения заготовок типа вал поперек оси. Конвейер одинарного действия (рис. 4.2г) состоит из двух неподвижных пилообразных реек 2 между которыми размещены две подвижные рейки 1 перемещаемые вверх — вниз от кулачкового (кривошипного) механизма 4. В результате этого движения подвижные рейки перебрасывают заготовки 3 через вершины неподвижных реек. Для увеличения производительности в конвейерах двойного действия (рис. 4.2д) подвижные рейки 1 смещены относительно неподвижных 2 на полшага. Принцип работы конвейера аналогичен предыдущему. Детали скатываются по наклонной части реек под действием силы тяжести.
Гребенчатые конвейеры предназначены для перемещения заготовок с заплечиками типа шатун (рис. 4.2 е) и имеют две направляющие 1 между которыми размещена гребенка 2 совершающая движение вверх — вниз (с амплитудой 8—10 мм) с помощью приводного механизма 4. В процессе перемещения шатун 3 заплечиками большой головки опирается на гладкие направляющие 1 а нижней частью малой головки — на зубцы гребенки при наклоне шатуна на угол 6—10° от вертикальной плоскости по ходу движения. При подъеме гребенки шатун смещается большой головкой по направляющим в сторону наклона а при опускании гребенки он смещается малой головкой в ту же сторону; в результате шатуны перемещаются вперед.
Шаговый конвейер-накопитель с управляемыми собачками. Рассмотренные выше шаговые конвейеры (см. рис. 4.2 а б) не обеспечивают использование запаса заготовок поэтому они не могут быть накопителями. Конвейер с управляемыми собачками помимо перемещения деталей выполняет функцию их накопления. Он включает две направляющие 3 по которым движутся детали 7 (рис. 4.2 ж) с помощью двойной штанги 1 с собачками 11 (действующими от гидроцилиндра 9) размещаемой между направляющими. На одной из направляющих 3 на осях 14 установлены поворотные рычаги 5 контроля наличия заготовки 7. При отсутствии заготовки короткий конец рычага поднимается а длинный опускается.
Собачки на штанге закреплены на осях 10. Над одной штангой установлены планки 4 каждая из которых шарнирно через ось 6 связана с собачкой 11 а также со штангой 1 через звено 13 несущее ролик 8. Такое соединение образует систему параллелограммов обеспечивающих управление положением собачек. При движении штанги 1 влево крайняя левая планка 4 наталкиваясь на неподвижный упор 2 на направляющей 3 поворачивает все звенья 13 и собачки 11 (по часовой стрелке) в нерабочее положение. При перемещении штанги вправо ролик 8 звена 13 одного из параллелограммов наталкивается на опущенный длинный конец рычага 5 на свободной позиции II. В результате этого при дальнейшем передвижении штанги происходит поворот звена 13 и собачки 11 данного параллелограмма а также (через планки 4) звеньев и собачек последующих параллелограммов против часовой стрелки. Собачки принимают рабочее положение опираясь на упоры 12 (см. рис. 4.2 ж штриховая линия) - Штанга двигаясь вперед захватывает на позиции 1 собачками заготовки 7 расположенные до позиции II и перемещают их на шаг. Если позиция II окажется занятой то постепенно весь конвейер заполнится заготовками. При освобождении позиции II все заготовки на конвейере передвинутся на шаг.
Для перемещения деталей с окончательно обработанной опорной поверхностью применяют также проходной конвейер-накопитель с управляемыми подъемными собачками в котором детали транспортируются перекладыванием.
Рис. 4.2. Конвейеры прерывистого действия
Подъемником называют машину для вертикального транспортирования изделий. По способу транспортирования подъемники разделяют на подъемники непрерывного и прерывистого действия.
Подъемники непрерывного действия.
Цепные подъемники для колец фланцев (рис. 4.3д) изготовляются в различных исполнениях одно - и многоканальные с приемом и выдачей деталей в одном и разных направлениях без распределения (сбора) деталей на несколько потоков и с распределением (сбором) без мойки деталей и с мойкой и др. Подъемники собирают из унифицированных узлов и могут переналаживать по высоте и диаметру на другой тип детали в определенном диапазоне.
Подъемник включает корпус 2 в котором на валах установлены звездочки 4 11 несущие замкнутую втулочно-роликовую цепь 8 с прикрепленными (через шаг) поводками 9 для удержания деталей 10. Верхней звездочке 4 сообщается вращение от привода 6 через цепную передачу. В корпусе предусмотрены направляющие 7 образующие канал для перемещения деталей. Поступают детали в подъемник (под действием силы тяжести) через наклонный лоток приема 1 а выходят по наклонному лотку выдачи 5 при наталкивании детали на скошенную сторону копира 3 закрепленного в корпусе.
Цепные подъемники для поршней гильз колец и т.п. перемещаемых на торцах (рис. 4.3 б) для удержания деталей 6 имеют крестообразные люльки 2 подвешенные через оси 11 к двум цепям 7 натянутым на звездочки 8 12 которые смонтированы в корпусе 1. Поступление детали 6 происходит по наклонному лотку 4 с роликами с которого деталь толкателем 5 (поочередно) заталкивается на приемную полку 3 корпуса 1 имеющую крестообразную прорезь для прохода люльки 2. При выходе деталей из подъемника каждая люлька проходит через крестообразную прорезь сделанную в наклонном лотке 10 установленном на корпусе в верхней части. При опускании люльки через лоток деталь остается на роликах 9 и под действием силы тяжести выкатывается из подъемника.
Вибрационные подъемники (рис. 4.3 в) используют для перемещения мелких деталей 2 по винтовому лотку 3 прикрепленному к вертикальной трубе 4 установленной на основании 1. Трубе сообщаются круговые колебания от дисбалансового вибратора 5. Основными недостатками подъемника являются: необходимость заполнения всей трассы лотка деталями а также появление при работе сильного шума и вибрации пола.
Подъемники прерывистого действия. Толкающие подъемники (рис. 4.3 г) применяют для перемещения деталей типа колец фланцев столбом на небольшую высоту (до 1 м). Детали 4 перемещает в шахте 3 подъемника ползун 1 совершающий возвратно-поступательное движение с помощью кривошипно-шатунного механизма 6.Детали в шахте при опускании ползуна задерживаются подпружиненной защелкой 2. Поступают детали в подъемник по наклонному лотку 5. Подъемник имеет недостатки: по окончании работы в шахте остается задел деталей; возвратно-поступательное движение механизмов не позволяет подъемнику работать с большой производительностью.
Шаговый подъемник используют для перемещения крупных деталей типа колец подшипников гильз поршней на торце. В корпусе 3 подъемника (рис. 4.3 д) размещена замкнутая цепь 8 натянутая на звездочки 27. Нижняя звездочка 2 получает вращение от электродвигателя через редуктор 1. На лицевой стороне корпуса на направляющих укреплена подвижная каретка 4 с приводными роликами 12. Каретка соединена с цепью 8 и при ее перемещении может занимать нижнее А и верхнее Б положения. В верхней части корпуса предусмотрено приводное устройство для вращения роликов 12 каретки в положении Б состоящее из электродвигателя с редуктором 6 и звездочки 5. Ролики на каретке через оси и звездочки 10 (рис. 4.3 д вид Р) соединены замкнутой цепью 9. В положении А на ролики каретки устанавливается деталь 13. При пуске электродвигателя цепь 8 поднимает каретку 4 с деталью в положение Б и останавливается при этом вращающаяся звездочка 5 редуктора 6 соединяется с цепью 9. Благодаря этому ролики 12 начинают вращаться и перемещать деталь из каретки 4 на конвейер 11.
3 Бункерные и магазинные загрузочные устройства
Накопители используют в АЛ и в ГПС. Для отдельных станков обычно накопители не применяют а ограничиваются бункерными загрузочными устройствами в которых имеются емкости для хранения заготовок (деталей). В отдельных случаях в несинхронных АЛ межоперационные заделы организуются на транспортных устройствах в первую очередь на конвейерах. Следует иметь в виду что наличие накопителей в АЛ и в ГПС оказывает существенное влияние на повышение коэффициента технического использования оборудования за счет сокращения общих простоев. Моделирование АЛ из пяти участков с коэффициентом технического использования каждого 095 показало что коэффициент использования линии в целом равен 079 при нулевом запасе каждого межучасткового накопителя и 093 при запасе на 15 мин.
Вместимость межоперационных накопителей АЛ обычно выбирают из расчета 05—2-часового запаса исходя из надежности встраиваемого оборудования технологических и организационных предпосылок. При неодинаковой сменности работы оборудования АЛ вместимость межлинейных накопителей может быть значительно больше (запас на 8 ч и более). По мере ухудшения показателей надежности оборудования эффективность Линии от введения межоперационных накопителей увеличивается. Увеличение вместимости накопителя оказывает положительное влияние на эффективность линии только до определенного предела. При коэффициенте технического использования оборудования 095 увеличение запаса заготовок в накопителе на работу с 15 до 120 мин дает повышение коэффициента технического использования линии всего на 1 % а при 07- на 8 %.
В синхронных АЛ транспортная система не может быть использована в качестве накопителя задела. Заготовки находящиеся на холостых позициях линии не относят к заделу так как не могут быть использованы в период простоя отдельных станков.
4 Накопители автоматических линий
Автоматический бункер (рис. 4.4 д) состоит из основания 1 чаши 2 с открытым верхом и скошенным дном наклонного подъемника 3 лотка 7 выдачи деталей 6 и лотка 11 возврата в чашу деталей (типа колец) не успевших скатиться в лоток выдачи. В подъемнике имеются две замкнутые цепи 5 натянутые на верхние и нижние пары звездочек из которых верхним звездочкам сообщается вращение от электродвигателя с редуктором 12 через цепную передачу 10. Для предотвращения заклинивания деталей 6 в чаше 2 нижняя часть цепей 5 установленных на звездочках 14 изогнута для образования подвижного дна.
Угол наклона подъемника 3 может изменяться за счет поворота его на оси 13 при навинчивании гаек 9 (с правой и левой резьбами) на тяги 8. На цепях 5 укреплены наклонные планки 4 для захвата деталей из чаши и подъема их к лотку выдачи. Наклон планок 4 может быть различным в зависимости от исполнения бункера.
Автоматический магазин со спиральным лотком для поршней крупных колец гильз (рис. 4.4 6) представляет собой каркас сваренный из четырех швеллеров 13 основания 14 и двух дисков 1 8. На дисках жестко укреплены вертикальные стяжки 2 с кронштейнами 11 несущими один или несколько наклонных спиральных лотков 7 образующих однозаходную или многозаходную спираль (по числу лотков). На рис. 4.4 б показан однозаходный лотковый магазин. На лотке предусмотрен отсекатель 12 для поштучной выдачи поршней 9 (или других деталей).
Аналогичная конструкция магазина применяется для приема хранения и выдачи клапанов 5. В этом случае спиральный лоток изготовляют из проволоки 6 (диаметром 8—10 мм) прикрепляемой к кронштейну 3 скобами 4 (см. рис. 4.4б). Для скольжения головок клапанов 5 по спиральному проволочному лотку угол наклона равен 15-20°. С целью увеличения вместимости выпускают магазины для клапанов с вращающимся барабаном на котором смонтированы несколько спиральных лотков образующих многозаходную спираль.
Автоматический многодисковый магазин для колец фланцев (рис. 4.4в) состоит из каркаса сваренного из четырех швеллеров 5основания 12 и крышки 9. На швеллерах на уголках 1 установлены диски 3 с лотками 4 выполненными из полос в виде архимедовой спирали. В центре магазина проходит вал 8 закрепленный в подшипниках крышки 9 и основания 12. На валу над каждым диском установлены четыре щеткодержателя 6 несущие щетки 7 с капроновыми нитями. Валу 8 через коническую пару зубчатых колес 14 сообщается вращение от электродвигателя с редуктором 13 .смонтированным на основании. Детали 11 поступают в магазин через наклонный лоток 10 соединенный с лотком 4 верхнего диска. Выходят детали по лотку 75 из лотка нижнего диска. Все лотки дисков соединены между собой соединительными лотками 2 таким образом что обеспечивается связь конца спирали верхнего лотка (через отверстие у центра) с началом спирали нижележащего диска (у периферии). Детали 11 в канале лотка верхнего диска перемещаются от периферии к центру под действием вращающихся щеток. Дойдя до отверстия в диске детали проваливаются в соединительный лоток и по нему поступают к началу спирального лотка второго диска где движение деталей повторяется.
Автоматический лотковый магазин дпя колец фланцев представляет собой сварной каркас 5 с установленными в несколько рядов наклонными лотками 2 зигзагообразной формы (рис. 4.4 г). Перемещение деталей 1 по лоткам производится под действием силы тяжести. Подача деталей в магазин происходит с помощью механизма распределения 3 деталей по лоткам а выдача — с помощью механизма соединения 6 деталей в один поток действующих от пневматических цилиндров 4 и 7.
Автоматический бункер с дисковым захватным устройством для шариков пальцев шайб (рис. 4.4 д) состоит из чаши 2 с открытым верхом на дне которой на оси размещен диск 4 с карманами по его периферии для захвата деталей 3 Диск приводится в движение от электродвигателя через червячную передачу 5. В диске укреплен ворошитель 1 для перемешивания деталей. На дне чаши 2 предусмотрено отверстие для прохода детали из кармана диска 4 в трубу выдачи 6.
Автоматический бункер с ножевым захватным устройством для роликов (рис. 4.4 е) имеет чашу 3 с открытым верхом и боковыми наклонными стенками между которыми располагается плоский нож 6 с призматическим углублением на верхней рабочей части. Нож закреплен на оси 7 и может совершать относительно чаши 3 качательное движение от привода 2. Против переднего края ножа расположена трубка 1 выдачи деталей 5. При подъеме ножа в верхнее положение некоторые ролики оказываются в призматическом углублении вдоль ножа и по нему соскальзывают к отверстию сбрасывателя 4 и пройдя его поступают в трубку 1. При неправильном положении на ноже ролик 5 сбрасывателем 4 отбрасывается в чашу. Угол а наклона рабочей части ножа в верхнем положении составляет 30—35°.
Автоматический магазин с барабанным захватным устройством для валиков (рис. 4.4 ж) представляет чашу 6 со скошенными к. центру стенками между которыми размещен барабан 8 с тремя продольными прорезями выполненными по окружности валика 7 В левой скошенной стенке чаши предусмотрено отверстие для прохода валика 7 при загрузке его с помощью шибера 2 действующего от гидравлического цилиндра 1. Напротив отверстия находится защелка 5 предотвращающая выпадение деталей из чаши в то время когда шибер находится в нижнем положении. Барабану 8 сообщается при необходимости (при загрузке деталей) вращение от привода 9. Загрузка магазина валиками может осуществляться или сверху в чашу или с подводящего конвейера 3 через наклонный лоток 4 и шибер 2. Выдача валиков из магазина на отводящий конвейер 10 происходит при повороте барабана 8.
Рис. 4.4 Бункерные и магазинные загрузочные устройства.
Магазинные загрузочные устройства также подразделяются по способам перемещения заготовок. Для этого применяются различные виды лотков спусков
Чаще всего применяют лотки для самотечного перемещения деталей. Лотки для полусамотечного (с применением сжатого воздуха) перемещения используют редко для легких деталей когда угол наклона к горизонту невозможно установить больше угла трения. Наряду с перемещением лотки сохраняют ориентирование деталей.
Спуски применяют для вертикального перемещения деталей под действием силы тяжести. С целью исключения свободного падения деталей в прямых вертикальных спусках и уменьшения конечной скорости спуски выполняют зигзагообразной (рис. 4.5 г) винтовой (рис. 4.5 д) или ступенчатой формы. Во всех спусках при изменении направления движения детали при повороте скорость спуска сокращается:
Лотки разделяют на жесткие прямые сваренные из полос 8 9 (рис. 4.5б) гибкие прямые (рис. 4.5ж и) и изогнутые (рис.4.5в е з) открытые (рис. 4.5 б в ж и) и закрытые (рис. 4.5 д е з). Опорной наклонной плоскостью для деталей в лотках может быть полоса 6 (см. рис. 4.5 а б ж) стенка 20 (см. рис. 4.5 е з) прутки 16 (см. рис. 4.5 в) шарикоподшипники 24 (см. рис. 4.5 и) или ролики 22 (см. рис. 4.5 е). При перемещении деталей в лотках часто производится кантование (поворот) детали 3 (рис. 4.5 е з).
При качении на наружной поверхности круглых деталей (колец дисков и пр.) в лотках с опорными полосами угол наклона лотков составляет 10-15° (см. рис. 4.5 а б ж) при скольжении клапанов 17 и других деталей (поршней гильз) на торце в лотках с опорными полосами прутками угол наклона увеличивается до 25—30° (см. рис. 4.5 в).
При перемещении плоских деталей в лотках (см. рис. 4.5 е и) по роликам или шарикоподшипникам угол наклона уменьшают до 3-5°. В спиральной части гибких лотков угол наклона обычно увеличивается на 20-30%.
Лотки собирают из унифицированных деталей. Особенностью гибких лотков является возможность подгонки их (в том числе и радиуса Rср изгиба лотка) по месту в зависимости от местоположения оборудования в пределах ± 5-10 мм что упрощает монтаж. Гибкий лоток изготавливается из стальной ленты поставляемой в бунтах. Для предотвращения выпадения деталей из лотков сверху предусматривается предохранительная полоса 1 (см. рис. 5 а) или стенка 19 (см. рис. 4.5 с з). Ролики 22 (см. рис. 4.5 с) или шарикоподшипники 24 (рис. 4.5 и) укрепляют на боковых стенках 23 на осях 21 с помощью гаек 5. Боковые стенки этих лотков соединяют между собой посредством длинных втулок 25 через которые проходят шпильки 2. После сборки на шпильки навинчивают гайки 5.
Проходимость деталей в лотках (лотковых конвейерах). Проходимостью деталей называют свойство перемещаться в лотках и лотковых конвейерах без задержки и потери ориентации (самовольного переворачивания). Плавность и скорость перемещения деталей зависит от их массы соотношения размеров детали и лотка параметров шероховатости вдверхности скольжения и прогиба лотка степени загрязнения лотка и деталей (стружкой маслом СОЖ и пр.) и др. Тяжелые детали при всех прочих равных условиях перемещаются лучше легких. На выпуклых 1 вогнутых участках лотка скорость перемещения замедляется.
Рис. 4.5. Наклонные лотки и спуски
5 Использование поддонов и кассет
Данные накопители могут применяться в конструкциях стеллажей - накопителях кассетных магазинах.
При обработке различных деталей средних размеров типа вал в ГПС для межоперационного накопления применяют накопители в виде поддонов 4 собранных в штабеля 13 14 (рис. 4.6) . Особенностью накопления заготовок 5 и обработанных деталей 3 в поддонах является возможность тесного складирования что предопределяет получение наибольшей вместимости по сравнению с вместимостью других конструкций накопителей. Работа с использованием системы поддонов для накопления с управлением ЧПУ происходит в следующей последовательности: в зависимости от вида обработки выбирается требуемый штабель 14 поддонов с заготовками. С помощью выдвижного (подъемного) стола 16 самоходной тележки 17 перемещаемой по рельсам 18 штабель 14 устанавливают на приемную позицию Г. Эта позиция как и позиция В где расположен штабель с обработанными деталями находится в зоне обслуживания портальным автооператором (штабелеукладчиком) 10. По окончании обработки и полного заполнения деталями 3 поддона 4 установленного на каретке 2 в позиции А каретка с поддоном перемещается по направляющей 1 на позицию Б. Рабочий орган автооператора 10 опускается и его захватные устройства 11 заскакивают в углубления 15 сделанные в стенках поддона 4. Далее рабочий орган с поддоном поднимается автооператор 10 по траверсе 12 перемещается на позицию В и поддон с деталями устанавливается на штабель 13. Автооператор 10 перемещается на позицию Г забирает верхний поддон с заготовками со штабеля 14 и устанавливает на каретку 2 ожидающую поддон на позиции Б. Далее каретка возвращается в позицию А обслуживаемую автооператором 9. Здесь рука 6 автооператора забирает крайнюю по порядку заготовку 5 а на ее место рука 7 устанавливает обработанную деталь 3. После этого автооператор 9 перемещается к станку для снятия рукой 7 обработанной детали и загрузки станка рукой 6 новой заготовки. Затем автооператор перемещается на позицию А.
В поддонах заготовки (детали) могут располагаться в два ряда или в один (длинные заготовки) При использовании двухрядных поддонов после обработки заготовок первого ряда каретке 2 сообщается перемещение для обработки заготовок второго ряда. Фиксирование поддонов в штабеля происходит на направляющем 19.
Кассетные магазины предназначены для хранения главным образом крупных деталей (гильз поршней колец ). Особенностью такого магазина является наличие съемной кассеты что позволяет (для увеличения общей вместимости магазина) складировать кассеты с деталями вне магазина и выдавать из этого запаса детали через магазин.
Кассеты и поддоны также могут использоваться отдельно как самостоятельная накопительная система.
Рис. 4.6. Система накопителей заготовок в поддонах.
Тактовый стол (ТС) предназначен для хранения заготовок и подачи их в зону захвата промышленного робота. Заготовку можно устанавливать непосредственно на пластину стола если форма и размеры заготовки позволяют это сделать либо на специальные приспособления - спутники которые крепят к пластинам тактового стола.
Готовую деталь можно ставить на тактовый стол или в специальную тару. Тактовый стол подбирают исходя из габаритов и массы заготовок.
Компоновочная схема тактового стола приведена в графической части.
Учитывая тип производства номенклатуру деталей обрабатываемых на проектируемом РТК в качестве средства накопления и поштучной выдачи заготовок был выбран зигзагообразный магазин - накопитель рассмотренный ранее. Данный магазин обладает достаточно большой емкостью при небольших габаритных размерах. Также возможно при необходимости наращивание емкости за счет присоединения дополнительных секций.
Проектирование загрузочно - накопительного устройства.
Магазин-накопитель относится к разряду накопителей с зигзагообразным скатом. Заготовки загружаются в ориентированном состоянии и на позицию загрузки подаются поштучно. Конструктивно магазин-накоптель (рис. 4.7) выполнен в виде рамы (поз. 5.) зигзагообразного лотка (поз. 1) в котором непосредственно накапливаются заготовки (поз. 4) . Для поштучной выдачи заготовок механизм отсекателя (поз. 3). Загрузка магазина производится сверху при помощи транспортера.
Рис.4.7 Магазин-накопитель
Расчет магазина-накопителя
Магазин-накопитель должен удовлетворять по емкости требуемой производительности то есть емкость накопителя не должна быть меньше величины фактической производительности а по возможности должна быть больше.
Определим оптимальный угол качения необходимы для свободного скатывания заготовок.
Tg>= нач где коэффициент учитывающий качение к=005
Определим оптимальный угол наклона зигзагообразной части.
z =3100400=775; zпр=8
Принимаем емкость накопителя (одной секции) Е=35 шт.
Высота зигзагообразной части
Н3=358(3100*tg3o+400)=2400 мм
Общая высота накопителя определяется как Н=Н3+h(4.4)
где Н3 - высота зигзагообразной части h - конструктивная высота.
Габаритные размеры накопителя допускают встраивание в РТК и обеспечивают устойчивое положение.
Данный магазин накопитель может накапливать до 70 заготовок (в двух секциях) этого вполне достаточно для бесперебойной работы РТК в течении смены (требуемая производительность комплекса при Nсум.=24000 шт.Qтр=50шт).
Годовой объем выпуска N =4800 шт.
Размер партии для одновременного запуска n = 400
Наибольший габаритный размер детали – 400мм.
Масса детали –102кг.
Масса заготовки – 16кг
Материал – Сталь 38ХС
Маршрутный технологический процесс изготовления
Годовой объем выпуска N = 4800 шт.
Наибольший габаритный размер детали –380мм.
Масса детали –127кг.
Масса заготовки – 201кг.
Наибольший габаритный размер детали –500 мм.
Масса заготовки – 376
Материал - Сталь 40Х
Наибольший габаритный размер детали –500мм.
Масса детали –205кг.
Масса заготовки – 332кг.
Наибольший габаритный размер детали –428мм.
Масса заготовки – 345кг.
Маршрутный технологический процесс изготовления.
2.Форма организации выполнения технологических процессов.
Все технологические процессы обрабатываемых на участке деталей представлены в приложении в комплекте технологической документации. Практически все операции кроме заготовительной выполняются на участке.
Участок является участком подетально-групповой специализации. За каждым рабочим местом закреплено несколько технологических операций. Операция содержит несколько технологических переходов. Перемещается деталь в таре от склада к рабочему месту и между станками. Производство непоточное.
3.Производственная структура участка
Участок предназначен для изготовления деталей – тел вращения типа диска.. В состав участка входит оборудование для металлообработки а именно токарные обрабатывающие центры зубообрабатывающее оборудование фрезерные станки места контроля системы обеспечения функционирования. Операции заготовительные производятся вне участка во вспомогательных производствах завода
Расчет количества основного оборудования
Расчет количества основного технологического оборудования производится на основе разработанных технологических процессов изготовления изделий. Для этого определяется время работы станков ( станкоемкость ) на различных операциях затем с учетом объема выпуска изделий каждого наименования расчитывается количество станков.
Определения количества технологического оборудования
Расчетное количество оборудования
где Fо=- эффективный годовой фонд времени при двухсменном режиме работы;
Fо= 3915 – для станков с ручным управлением и полуавтоматов
Fо= 3835 – для станков с ЧПУ
Полученное значение округляем до ближайшнго большего целого Ср
Коэффициент загрузки оборудования
при Кз меньше нормативного Ки принимаем равным 1 при Кз больше нормативного принимаем Ки согласно данных табл.3.4 [13] и уточняем количество технологического оборудования
Полученное значение округляют до ближайшнго большего целого Сп
Уточняем коэффициент загрузки оборудования
5.Проектирование подсистем
5.1.Расчет характеристик склада
Определение количества наименований деталеустановок
где F - месячный фонд времени работы станка ч;
F = Fоб * hз 12 (5.6)
Fоб=3900ч.- эффективный годовой фонд времени при двухсменном режиме работы;
hз=085-нормативный коэффициент загрузки оборудования.
F=3900*08512=27625 ч.
S = 6- число станков в ГПС;
Тср - средняя станкоемкость изготовления одной деталеустановки мин.
m - число операций технологического процеса изготовления детали-представителя;
Тср = 82277 = 1175 мин.
N =400шт.- месячный объем выпуска детали-представителя
Округляем до ближайшего большего целого Кнаим = 85 шт.
Определение оптимальной емкости склада
Округляем до ближайшего большего целого Eс =94шт.
Изделия транспортируются в таре – тип Т-025 с габаритными размерами L*B*H=600*800*500; В каждой паре помещается 5 заготовок.
размеры ячейки склада 630*850*530; количество ячеек 94:5=188 = 20 шт.
Длина склада L=630*202=6300мм.
количество ячеек по высоте Qh=2шт.
Высота склада H=530*2+450=1510мм.
Станки располагаются в две линии склад располагается между ними в 1 ряд. (рис. 5.1). С каждой стороны его обслуживает 1 кран – штабелер.
количество ячеек Ql = 94шт.
длина склада L=6800 мм.
ширина с учетом пространства для работы крана штабелера B=1595мм.
площадь склада S=5.78м2
производственная площадь участка S = 5918 м2
Станки располагаются в две линии с центральным проездом для рельсовой тележки склад располагается с торца в 1 ряд.
тогда количество ячеек Ql = 94шт.
длина склада с учетом пространства для работы крана штабелера L = 59220 мм.
ширина проезда Впр = 1500 мм.
площадь склада S=578 м2
производственная площадь участка S = 680 м2
5.2. Расчет количества транспортных устройств и их загрузки
Для определения числа перемещений транспортного устройства в течении месяца воспользуемся маршрутом обработки детали - представителя. В процессе изготовления деталь – представитель перемещается по следующему маршруту: стеллаж позиция загрузки – разгрузки станок№1 (операция 005) станок№2 (операция 010) позиция загрузки – разгрузки стеллаж; позиция загрузки – разгрузки станок№3 (операция 015) позиция загрузки – разгрузки стеллаж; позиция загрузки – разгрузки станок№4 (операция 020) позиция загрузки – разгрузки слесарное отделение (операция 25) позиция загрузки – разгрузки моечная машина (операция 030) позиция загрузки – разгрузки стеллаж; позиция загрузки – разгрузки контрольное отделение (операция 035) позиция загрузки – разгрузки стеллаж.
Коэффициент загрузки транспортного устройства
где Ттр – суммарное время работы транспортного устройства в течение месяца ч;
Fтр – месячный фонд работы транспортного устройства ч.
а) для крана штабелера
Ткш=(Кстел-поз*Тстел-поз+Кст-ст*Тст-ст+Кпоз-ст*Тпоз-ст+Кстел-ст*Тстел-ст)(5.8)
б) для рельсовой тележки
Ткш = (Кпоз-ст*Тпоз-ст+ Кст-ст*Тст-ст)(5.9)
где Кстел-поз - количество перемещений от стеллажа к позиции загрузки - разгрузки
Кпоз-ст - количество перемещений от позиции загрузки - разгрузки к станку
Кст-ст - количество перемещений от станка к станку
Кстел-ст - количество перемещений от стеллажа к станку
Таким образом количество перемещений транспортного устройства при изготовлении детали – представителя равно:
“позиция – стеллаж” - 6
“позиция – станок” - 6
“станок – станок” - 2
Тогда при месячном объеме выпуска деталей на участке 2000 шт.
“позиция – стеллаж” - 12000
“позиция – станок” - 12000
“станок – станок” - 4000
Средние длины перемещений крана штабелера:
“позиция – стеллаж” - 1236м.
“позиция – станок” - 2658м.
“станок – станок” - 5м
Средняя длина вертикального перемещения транспортного устройства - 12м.
Для крана штабелера СА –ТСС 05 скорость:
горизонтального перемещения – 125мс (75ммин)
вертикального перемещения – 03мс (18ммин)
Тпод.1 = (123675)+(1218) = 023 мин.
Тпод.2 = (205875)+(1218) = 034 мин.
Тпод.3 = (575)+(1218) = 013 мин.
Принимая Тк=002 Тсп=015 получим Т1=08мин; Т2=102мин; Т3=06мин.
определим коэффициент загрузки крана штабелера
Ткш = (12000*08+12000*102+4000*06) = 4045 ч.
Ккш = 4045(325) = 124
Так как Ккш больше нормативного то применение АТСС с совмещенными подсистемами складирования и транспортирования невозможно.
Рассмотрим вариант№2
Для рельсовой тележки ТПА-025 скорость равна 60ммин
Средние длины перемещений:
“позиция – стеллаж”по вертикали – 05м.
по горизонтали – 1236м.
Тпоз-стел = (0518)+(123675) = 019 мин; тогда Т1=072мин
“позиция – станок”-28м.
“станок – станок”-5м
Тпоз-ст = (2860) = 046 мин; тогда Т2=126мин
Тст-ст = 560 = 008 мин; тогда Т3=05мин
Ткш = (12000*072) = 144ч.
Троб = (12000*1265+4000*05) = 2863ч.
определим коэффициент загрузки крана штабелера и робокара
Кроб = 2863 325 = 088
При данном объеме производства возможно применение только второго варианта АТСС с раздельными подсистемами складирования и транспортирования хотя первый вариант меньших капитальных затрат и занимает меньшую производственную площадьно загрузка крана штабеллера превышает допустимую норму.
5.3.Расчет системы стружкоуборки
Определим массу стружки в год
Для выбора способа удаления и переработки стружки определяют её количество образующееся на 1м2 цеха в год.
Данные для расчёта представлены в таблице 5.6.
Годовой обьем выпуска шт.
Общая масса стружки 236.4 т. Площадь участка 678.7 м2. На 1м2 приходится 035 т в год. По рекомендациям в [14] необходимо предусмотреть линейные конвейеры вдоль станочных линий со специальной тарой в конце конвейера. Заполненная стружкой тара вывозится на участок переработки.
По длине и ширине спроектированного участка примем ширину пролёта 24 м шаг колонн 12 м и высоту здания 72 м ширину межцехового проезда 26м ширину магистрального проезда 46 м. Планировка участка и график загрузки оборудования представлены на листе 11.
Количество технологического оборудования- 6 единиц
Занимаемая площадь 680м2
Удельная площадь 1133м2
Средний коэффициент загрузки и использования оборудования 085
1. Характеристика безопасности применяемого в проекте оборудования технических устройств производственных процессов. Нормирование условий труда на рабочих местах выбор методов и средств защиты от ОВПФ при выполнении технологических операций в соответствии с нормативными документами ССБТ.
Условия труда на рабочих местах производственных помещений и площадок складываются под воздействием большого числа факторов различных по своей природе формам проявления характеру действия на человека. В соответствии с ГОСТ 12.01.003-74* (СТ СЭВ 790-77) опасные и вредные производственные факторы подразделяются по своему действию на следующие группы: физические химические биологические психофизические.
Физически вредными производственными факторами являются повышенная запыленность и загазованность воздуха рабочей зоны высокий уровень шума и вибрации недостаточная освещенность рабочей зоны и т.д.
Оборудование на проектируемом участке должно регулярно проходить технический осмотр в ходе которого определяется его безопасность и соответствие требованиям норм экологической безопасности.
Оборудование применяемое на участке должно быть снабжено специальными защитными и оградительными устройствами которые уменьшают риск травмирования рабочих.
Микроклимат на рабочем месте в производственных помещениях определяется температурой воздуха относительной влажностью скоростью движения воздуха барометрическим давлением и интенсивностью теплового излучения от нагретых поверхностей.
Производственные помещения должны соответствовать требованиям СНиП 11-2-80 СНиП 11-89-80 санитарных норм проектирования промышленных предприятий СН 245-71. Бытовые помещения должны соответствовать требованиям СНиП 11-92-76.
Естественное и искусственное освещение производственных помещений должно соответствовать требованиям СНиП 11-4-79.
Уровень шума не должен превышать 80 дБА.
На случай пожара в цехе должны быть предусмотрены средства пожаротушения и эвакуационные выходы.
На участке должна быть естественная и общеобменная вентиляция.
Местная вентиляция должна обеспечивать удаление пыли мелкой стружки и аэрозолей СОЖ из рабочей зоны станков.
1.2. Выбор сигнальных цветов и знаков безопасности для проектируемого участка оборудования.
Предупреждение несчастных случаев.
На предприятиях значительное число причин несчастных случаев относят к ²неосторожности² и ²невнимательности² пострадавших или других лиц. При расследовании таких случаев необходимо в должной мере учитывать что ²неосторожность² и ²невнимательность² являются факторами психологического характера тесно связанными с такими человеческими категориями как ²настроение² ²восприятие² ²память² и что во многих случаях для профилактики необходимы различные организационно-технические мероприятия включая мероприятия по технической эстетике и инженерной психологии.
Для предупреждения таких случаев эффективным средством является цветовое оформление машин и производственных помещений рациональное применение сигнальных цветов и знаков безопасности.
Для мобильных машин при выборе сигнального цвета и определении порядка нанесения его на наружную поверхность необходимо учитывать данные о причинах аварий и несчастных случаев а также максимальную скорость движения машины и результаты исследований в области цвета.
Привлечение внимания к опасности соответствующим цветом должно найти широкое применение в стационарных машинах и различных технических сооружениях.
Назначение и область применения основных и вспомогательных сигнальных цветов.
цвет используемый для усиления значения основного цветового сигнала.
Запрещение сигнализация о непосредственной опасности и указание устройства для прерывания или движения
Ограждаемые участки машин и знаки запрещающие различные действия. Кнопки и рычаги выключения и аварийные - ²Стоп²; лампы сигнализирующие о нарушении технологического процесса или условий безопасности; противопожарные устройства и т.п.
Предупреждение сигнализация о необходимости внимания осторожности действий
Наружные элементы оборудования не полностью ограждающие механизмы; сигнальные лампы предупреждающие о предстоящем переключении автоматических станков и линий; элементы внутрицеховых транспортных средств; строительные конструкции для сигнализации об опасности и т.п.
Разрешение сигнализация о безопасности
Кнопки и рычаги ²Пуск²; пункты первой помощи аптечки; знаки разрешающие различные действия; таблички
продолжение таблицы 6.1.
указывающие запасные и аварийные выходы и для другой информации направленной на обеспечение безопасности
Промежуточное значение между красным и желтым
Для повышения контраста между машинами и фоном. Допускается нанесение цвета на внутренние поверхности ограждающих устройств и ограждаемые участки машин и механизмов
Производственно-техническая информация
Оформление производственной информации не связанной с понятиями об опасности или предосторожности
Усиление контраста основных цветов безопасности; надписи на желтом белом и оранжевом фоне
Для обозначения направления движения для пояснительных надписей и символов а также для приборов контроля и т.п.
Усиление контраста основных цветов безопасности; надписи на красном зеленом синем и черном фоне
Для обозначения границ проходов проездов и рабочих мест а также направления движения и пояснительных надписей на знаках и т.п.
2.Экологическая безопасность и охрана окружающей среды
2.1 Экологический анализ проекта выбор методов и средств защиты от негативных воздействий проектируемого участка
Экологическая безопасность проекта обеспечивает следующим образом. На проектируемом участке применяется СОЖ – 5% эмульсия МГЛ-205 и индустриальное масло И-20. Отработанные СОЖ собирают в специальные емкости. Водную и масленую фазу используют в качестве компонентов для приготовления эмульсий. Масляная фаза эмульсий поступает на регенерацию или сжигается. Концентрация нефтепродуктов в сточных водах при сбросе их в канализацию соответствует требованиям СН и П II-32-74. Водную фазу СОЖ очищают до ПДК или разбавляют до допустимого содержания нефтепродуктов и сливают в канализацию. В состав СОЖ должны входить компоненты не являющиеся вредными или достаточно легко обезвреживаемые имеющимися средствами. Нормы шума на рабочих местах регламентируются ГОСТ 12.1.003-83 «ССБТ. Шум. Общие требования безопасности». Стружка удаляется из цеха и поступает на переработку а СОЖ после дополнительной очистки и охлаждения снова подается к режущим инструментам.
2.2Меры безопасности при работе с СОЖ
Нефтяные масла и эмульсии применяются во всех отраслях машиностроения как смазочно-охлаждающие жидкости при механической обработке металла. Огромный контингент работающих в промышленности подвергается воздействию этих соединений. Это воздействие осуществляется двояким путем: на кожу при контакте с маслами и эмульсиями и через органы дыхания куда поступает смешанный аэрозоль образующийся при разбрызгивании СОЖ.
Химический состав и концентрация частиц СОЖ и аэрозоля в воздухе рабочей зоны находится в непосредственной зависимости от скорости и глубины резания металла вида СОЖ и расходе ее в единицу времени.
Уровень загрязнения спецодежды и кожных покровов станочников нефтяными маслами зависит от характера технологического процесса наличие укрытия рабочей зоны и вида СОЖ.
В результате длительного воздействия аэрозоля индустриальных масел развиваются хронические заболевания органов дыхания функциональные и биологические изменения в органах и системах а также снижение имуннобиологической реактивности организма.
Профилактические мероприятия при работе с СОЖ основываются на установленных нормативах предельно допустимого содержания аэрозоля индустриальных масел в воздухе рабочих помещений.
Основные мероприятия по оздоровлению производственной среды должны осуществляться на базе комплексной механизации и автоматизации процессов механической обработки металла позволяющих почти полностью устранить или резко сократить с СОЖ и его аэрозолями.
В связи с широким внедрением в промышленность скоростных режимов резания жаропрочных и сверхтвердых сплавов новых технологических процессов применением многокомпонентных СОЖ с химически активными присадками особое значение приобретают требования к конструкции новых станков в частности к более полному укрытию зоны резания и оборудованию местного и эффективного отсоса что позволяет снизить содержание аэрозоля с продуктами термоокислительного до допустимых величин.
Эффективна замена масляного охлаждения эмульсионным т.к. при его использовании концентрация масляного аэрозоля и углеводов в рабочей зоне не превышают предельно допустимых значений а окись углерода и другие продукты термораспада не обнаруживаются. При этом осуществляется контроль за содержанием в эмульсиях щелочи (не более 025%) нафтеновых кислот (не более 20%) нафтеновых мыл (не более 1%) кальцинированной соды (не более 03%) и других возможных химически активных присадок.
В проекте детали обрабатываются на станках с ЧПУ которые позволяют вести обработку деталей практически без участия работающего следовательно контакт с аэрозолями СОЖ почти полностью устранен.
Необходима так же централизованная подача СОЖ и периодическая очистка от примесей не реже одного раза в месяц. Очистку следует проводить с применением антимикробных добавок.
Для защиты кожных покровов большое значение имеет снабжение работающих спецодеждой из легкой гладкой мягкой непромокаемой и непроницаемой для охлаждающих масел и жидкостей ткани.
Должны проводиться периодические медицинские осмотры не реже одного раза в два года.
Важную роль в обеспечении функциональной пригодности СОЖ наряду с выбором ее вида и марки играют процессы очистки и регенерации СОЖ. Таким образом удается не только экономить СОЖ но и уменьшать количество отходов сбрасываемых в окружающую среду.
Регенерацию масел производят для удаления шлака и других загрязнений. После предельного времени эксплуатации свойства СОЖ теряются полностью и к дальнейшему применению она становится непригодна.
3.Безопасность проекта в чрезвычайных ситуациях
3.1. Анализ вероятных ЧС.
Серьезную угрозу безопасности человека представляет возникновение чрезвычайных ситуаций обусловленных крупномасштабными авариями катастрофами загрязнением и разрушением биосферы стихийными бедствиями. Чрезвычайные ситуации возникают крайне редко. Тем не менее вызываемые ими жертвы среди населения разрушения и социально-экономические последствия огромны – сопоставимы с военно-политическими конфликтами.
В Курганской области ведется активная работа по формированию и совершенствованию системы управления природопользованием системы управления охраной труда и территориальной подсистемы РСЧС.
Самым возможным ЧП природного характера на территории города может быть наводнение. Вследствие этого предприятия располагают на возвышенном месте и на достаточном удалении от реки.
Возможно заражение людей инфекционными заболеваниями. Подвержение человека заболеванию зависит от условий жизни иммунитета уровня санитарно-гигиенической культуры состояния лечебно-профилактической и санитарно-профилактической работы.
Возможным ЧП антропогенного характера является истощение водных ресурсов загрязнение источников питьевой воды. Ухудшение ее качества представляет большую опасность для здоровья людей.
Возможным ЧП техногенного характера являются транспортные аварии: воздушные железнодорожные автомобильные; различные пожары взрывы.
Возможные ЧП на проектируемом участке: транспортные аварии (железнодорожные автомобильного транспорта); пожары вследствие неправильной эксплуатации оборудования не соблюдения правил техники безопасности и поломки оборудования.
3.2. Оценка пожарной опасности и пожарная профилактика проектируемого объекта.
Пожары на машиностроительных предприятиях представляют большую опасность для работающих и могут причинять огромный материальный ущерб.
Пожарная безопасность может быть обеспечена мерами пожарной профилактики и активной пожарной защиты. Понятие пожарной профилактики включает комплекс мероприятий необходимых для предупреждения возникновения пожара или уменьшения его последствий. Под активной пожарной защитой понимаются меры обеспечивающие успешную борьбу с возникающими пожарами или взрывоопасной ситуацией.
Взрывоопасность электроустановок.
Правила устройства электроустановок" регламентируют устройство электрооборудования в производственных помещениях и для наружных технологических установок. Выбор и установку электрооборудования производят в соответствии с этими правилами на основе классификации взрывоопасных зон и смесей.
Взрывоопасность зон определяют возможностью выделения газов ЛВЖ или горючих пылей с нижним пределом воспламенения 65гм3 и ниже. При образовании взрывоопасной смеси в объеме превышающем 5% объема помещения последнее полностью является взрывоопасным а при объеме смеси равном 5% объема помещения и меньше взрывоопасной считается зона в пределах 5 м по вертикали и горизонтали от технологического аппарата из которого выделяется горючее вещество.
Для наружных установок размер взрывоопасной зоны устанавливают в зависимости от условий в которых может образовываться взрывоопасная смесь (05-20 м по вертикали и горизонтали от места выделения горючего вещества).
Зона класса В-I. К ней относятся помещения в которых могут образовываться взрывоопасные смеси паров и газов с воздухом при нормальных условиях работы (например помещения в которых производится слив ЛВЖ в открытые сосуды).
Зона класса В-Iа. В эту зону входят помещения в которых взрывоопасные смеси не образуются при нормальных условиях эксплуатации оборудования но могут образовываться при авариях или неисправностях.
Зона класса В-Iб. К этому классу относятся:
Помещения в которых могут содержаться горючие пары и газы с высоким нижним пределом воспламенения ( 15% и более ) обладающие резким запахом (например помещения аммиачных компрессоров );
Помещения в которых возможно образование лишь локальных взрывоопасных смесей в объеме менее 5% объема помещения.
Зона класса В-Iг. В эту зону входят наружные установки в которых находятся взрывоопасные газы пары и ЛВЖ (например газгольдеры сливоналивные эстакады и т.п.).
Зона класса В-II. К ней относятся помещения в которых производится обработка горючих пылей и волокон способных образовывать взрывоопасные смеси с воздухом при нормальных режимах работы (например открытая загрузка и выгрузка из оборудования мелко дисперсных горючих материалов).
Зона класса В-IIа. В эту зон входят помещения в которых взрывоопасные пылевоздушные смеси могут образовываться только в результате аварий и неисправностей (например разгерметизация пневмотранспортирующего оборудования с применением азота сепарационные установки с механической загрузкой и т.д.).
Помещения и установки в которых содержатся ГЖ и горючие пыли нижний концентрационный предел которых выше 65 гм3 относят к пожароопасным и классифицируют следующим образом.
Зона класса П-I. К ней относят помещения в которых содержатся ГЖ (например минеральные масла).
Зона класса П-II. В эту зону входят помещения в которых содержатся горючие пыли с нижним концентрационным пределом выше 65 гм3.
Зона класса П-IIа. К ней относятся помещения в которых содержатся твердые горючие вещества не способные переходить во взвешенное состояние.
Установки класса П-III. К ним относятся наружные установки в которых содержатся ГЖ (с температурой вспышки выше 61°С) или твердые горючие вещества.
Пожарная профилактика.
Мероприятия по пожарной профилактике разделяются на организационные технические режимные и эксплутационные.
Организационные мероприятия предусматривают правильную эксплуатацию машин и внутризаводского транспорта правильное содержание зданий территории противопожарный инструктаж рабочих и служащих и т.д.
К техническим мероприятиям относятся соблюдение противопожарных правил норм при проектировании зданий при устройстве электропроводов и оборудования отопления вентиляции освещения правильное размещение оборудования.
Мероприятия режимного характера – это запрещение курения в не установленных местах производства сварочных и других работ в пожароопасных помещениях и т.д.
Эксплутационными мероприятиями являются своевременные профилактические осмотры ремонты и испытания технологического оборудования.
Требования пожарной безопасности к электроустановкам.
Условия безопасного применения электрооборудования регламентируются ПЭУ согласно которым все электрооборудование подразделяют на взрывозащищенное для пожароопасных установок и нормального исполнения.
Во взрывоопасных зонах разрешается применять только взрывозащищенное электрооборудование обеспечивающее безопасность его использования во взрывоопасных средах.
Во взрывоопасных помещениях и зонах наружных установок применяют специальное электроосветительное оборудование во взрывозащищенном исполнении. В помещениях класса В-I используют стационарные светильники во взрывонепроницаемом искробезопасном или специальном исполнении. В помещениях классов В-Iа и В-II – в любом взрывозащищенном исполнении. В помещениях классов В-Iб и В-IIа – пыленепроницаемые.
В помещениях класса П-I электрооборудование должно иметь брызгозащищенное закрытое обдуваемое или продуваемое исполнение. В помещениях класса П-II – закрытое обдуваемое или продуваемое с замкнутым циклом охлаждения. В наружных установках класса П-III – закрытое или закрытое продуваемое.
Во всех помещениях искрящие части машин заключают в пыленепроницаемые колпаки. Светильники в помещениях П-I и П-II должны иметь пыленепроницаемое исполнение а для помещений класса П-IIа допускаются открытые светильники. В наружных установках класса П-III применяют светильники в пыленепроницаемом и взрывозащищенном исполнении.
1 Организация складского хозяйства
Организация складского хозяйства Задачи складского хозяйства заключаются в приеме хранении учете материалов и регулировании уровня их запаса подготовке готовой продукции к отправке потребителю. Важную роль в организации работы складов играет подготовка материалов к выдаче в производство путем организации заготовительных отделений. На складах выполняется большой объем погрузочно-разгрузочных работ работ по перемещению материалов. Поэтому основным направлением в развитии складского хозяйства является комплексная механизация и автоматизация работ улучшение использования складских помещений а также организация материально-технического снабжения на основе оптовой торговли внедрение систем материально-технического снабжения типа «точно вовремя» («джит» — США «канбан» — Япония) которые значительно сокращают объем складских запасов.
По функциональному назначению склады подразделяются на заводские и цеховые. Так в составе складов машиностроительного завода могут быть центральный материальный склад (главный магазин) склад металлов (или склады по видам металлов) склад изделий смежных производств склад запасных частей и оборудования склад шихты и формовочных материалов.
Устройство и оснащение складов зависят от ряда факторов. Определяющие из них — грузооборот длительность хранения вид применяемой тары объем и частота поставок и отправлений вид используемого подвижного состава. В зависимости от этих факторов материалы и готовые изделия могут храниться на специально оборудованных открытых площадках под навесами в отапливаемых и неотапливаемых помещениях. Например склады тарных и штучных грузов размещают как правило в закрытых специально оборудованных помещениях. Тарные и штучные грузы хранятся на стеллажах в штабелях в контейнерах на поддонах с многоярусной установкой. Могут храниться материалы на аккумулирующих устройствах средств непрерывного транспорта.
Для механизации погрузочно-разгрузочных работ и внутри складских операций применяют различные устройства и машины: краны-штабелеры электропогрузчики кран-балки и мостовые краны электрокары и различного рода средства непрерывного транспорта. Для комплексности механизации используют быстродействующие автоматические стропы и захваты. В последние годы получили развитие автоматизированные склады тарно-штучных грузов оборудованные системами машин обеспечивающими транспортировку установку и поиск материалов по специальным программам с использованием роботов. Автоматизированные склады являются неотъемлемой частью автоматизированно-транспортных систем ГАП. По конструкционным особенностям различают следующие типы автоматизированных складов: с клеточными стеллажами и автоматическим стеллажным краном-штабелером автоматическим мостовым краном-штабелером с гравитационными стеллажами и автоматическими стеллажными каретками-операторами с автоматическими элеваторными стеллажами автоматические подвесные склады.
Для комплексной механизации и автоматизации транспортных операций большое значение имеет укрупнение грузовых единиц путем применения контейнеров и средств пакетирования (поддоны всех типов стропы кассеты обвязки прокладки и т. п.). Парк контейнеров и средств пакетирования
к=Gk[1+(к.н.+к.р.)100]qk
где Gк — объем перевозок грузов (грузооборот) на расчетный период т; к.н.к.р.—потребность в контейнерах (средствах пакетирования) в связи с неравномерностью перевозок нахождением в ремонте % от общего парка; qк— выработка на один контейнер (средство пакетирования) за расчетный период т; qк = (qк.с.(Fк+Fп) То [здесь (qк.с.— статическая нагрузка контейнера средства пакетирования т; Fк—число календарных дней в расчетном периоде; Fп—время нахождения контейнеров (средств пакетирования) в простое дн.; То— среднее время оборота контейнера средства пакетирования сут.].
Для оценки уровня оснащенности складов погрузочно-разгрузочными средствами и механизмами применяют показатель насыщенности средствами механизации:
где Qп=т —суммарная грузоподъемность всех средств механизации т; Qckл— грузооборот склада за расчетный период т.
Основные направления совершенствования работы транспортного и складского хозяйства — это улучшение структуры парка подъемно-транспортных и транспортных машин внедрение транспортных и складских систем с автоматическим адресованием грузов автоматизированных складов автоматизированных контейнерных площадок совершенствование организации перевозок и складских процессов.
К технико-экономическим показателям работы транспортного и складского хозяйств относятся: удельный вес транспортно-складских расходов в себестоимости продукции себестоимость перевозки грузов; затраты на машино-час работы транспортного средства или подъемно-транспортной машины себестоимость складского хранения 1 т груза и др.
В подсистеме АСУП техническое обслуживание производства и управление процессами обслуживания рассматривается как неотъемлемая часть управления всей системой производственных процессов предприятия. Подсистема состоит из ряда подсистем более низкого уровня: инструментального ремонтного энергетического транспортного и складского обслуживания. В них решаются задачи планово-учетного характера календарного планирования и регулирования хода производственных процессов а также обеспечивается их координация с процессами основного производства. Так в подсистеме «Инструмент» определяется потребность в оснастке и формируются планы ее производства ведется учет и анализ выполнения плана осуществляется календарное планирование работы инструментального хозяйства устанавливаются и регулируются уровни запасов определяются оборотные фонды инструмента ведется учет его движения в ЦИСе ИРК. В подсистеме «Энергия» разрабатываются плановые и составляются фактические энергобалансы нормируется расход энергоресурсов ведется учет их потребления осуществляется управление производством энергии в соответствии со спросом. В подсистеме «Ремонт» учитывается наличие и состояние оборудования (возраст наработка) простои и отказы; разрабатываются и контролируются выполнения графиков ППР определяются материальные и трудовые ресурсы ремонтного хозяйства. В подсистеме «Транспорт — склад» разрабатываются маршруты движения транспортных средств рассчитываются грузопотоки и грузооборот ведется планирование и учет транспорта учитывается движение материалов в складском хозяйстве регулируется уровень их запасов.
Учитывая все выше сказанное тип производства габаритные размеры обрабатываемой заготовки при проектировании гибкого автоматизированного участка изготовления деталей - тел вращения для выполнения функций складирования был выбран автоматизированный склад. Обслуживание данного склада производится с помощью крана штабеллера. Хранение и перемещение заготовок производится в таре (Т-025). Перемещение заготовок в таре по цеху производится при помощи рельсовой тележки.
Количественная оценка экономических результатов улучшения условий и повышения безопасности труда при расчёте величины годовой экономии может быть дана путём следующих экономических показателей: экономии затрат за счёт сокращения численности работающих; экономии затрат за счёт повышения работоспособности достигаемой в результате улучшения условий труда; экономии затрат на социальное страхование получаемой в результате снижения травматизма на производстве. Для определения перечисленных показателей используем расчёт приведёный в 5 разделеа также данные полученные на заводе во время дипломной практики.
В данном дипломном проекте проектируется разрабатывается и рассчитывается новый производственный участок механической обработки. Участок разрабатывается на основе базового производственного участка. Заменяется устаревшее оборудование высвобождаются площади оптимизируются режимы резания повышается безопасность и надежность внедряемого оборудования уменьшается число рабочих снижаются затраты на материалы энергоносители заработную плату затраты на текущий ремонт оборудования и амортизационные отчисления. Следовательно снижается себестоимость изделия и сроки окупаемости проекта.
Ожидаемые результаты проекта
Размер необходимых инвестиций 12823.0 тысяч рублей
Срок окупаемости проекта 1.04 года
Чистая дисконтированная стоимость 21493.8 тысяч рублей
2.2 Характеристика предприятия
Сильной стороной предприятия является высокая квалификация научно-технического персонала и организация производства.
Слабая сторона - это ориентация производства на военный заказ высокая текучесть кадров низкая заработная плата и низкая автоматизация и механизация производства.
Основная номенклатура выпускаемых изделий: транспортная машина специального назначения. Данная машина не имеет аналогов в мире. Её отличительная черта высокая огневая мощь. СМ -сельскохозяйственные машины трактора автоприцепы лесоповальное оборудование трансмиссии транспортных средств.
На проектируемом участке обрабатывается группа деталей которые входят в состав редукторов и трансмиссий транспортных машин.
Базовая деталь крышка входит в коробку скоростей транспортной машины специального назначения.
Проектируя новый участок предприятие стремится в будущем снизить затраты на материал энергоносители производственные площади заработную плату и повысить производительность тем самым снизить себестоимость продукции.
Загрузка оборудования на участке представлена в таблице 5.1. Степень износа оборудования в среднем составляет 60%. Технология изготовления базовой детали представлена приложениями в технологической документации.
2.3 План производства
Исходные данные берутся их таблицы 5.1 и представленного в приложении комплекта технологической документации на разработанный технологический процесс данные взятые во время практики на предприятии. Также необходимые данные из базового технологического процесса и базового участка. Годовой объём партии деталей каждого вида 4800 штук.
Используя таблицу 5.1 составляем таблицу 7.1 по расчёту количества рабочих мест на участке и их балансовой стоимости.
Расчет количества рабочих мест на участке и их балансовая стоимость
Занимаемая площадь участка S = 150 м2
Занимаемая площадь участка S = 550м2
На основе спроектированной планировки участка в разделе 5 определяем площадь необходимых помещений. Расчёт капитальных вложений проекта сведён в таблицу 7.3.
Структура капитальных вложений
Производственное оборудование
Подъёмно-трансп оборудование
% от стоимости оборудования
Приспособления и инструменты
Величина капитальных вложений (инвестиций) по проектному варианту определяется по формуле (7.1)
Кпр=Кн+Кна-Клик+Книр (7.1)
гдеКн-стоимость нового оборудования приспособлений и других средств
Кна-стоимость ликвидируемых в связи с внедрением нового технологического процесса существующих основных средств (учитывается как 20-30% недоамартизированной части от первоначальной стоимости)
Клик-выручка от реализации внедрённого оборудования к концу службы его (10-20% ликвидационная стоимость)
Книр-затраты на производственную и организационно-техническую подготовку производства включая затраты на научно-исследовательские проектные и опытно-конструкторские работы.
Кпр = 11100000 + 2556000 – 1110000 + 277000 = 12823000 руб
2.4 Определение технологической себестоимости
Рассчитываются те статьи себестоимости продукции которые различаются в базовом и проектном вариантах.
Затраты на материал рассчитываются по формуле (7.2)
Зм= S(PmiЦmi-PoiЦoi) (7.2)
гдеРmi-вес заготовкикг
Цmi-цена кг материала. Для стали Цmi=3.8 руб
Цoi-цена кг отходов. Для стали Цoi=0.5 руб
m-количество видов деталей
N=24000-партия деталей
Результаты расчета приведены в таблице 7.4
Расчет затрат на материалы
Стоимость материала руб.
Стоимость стружки руб.
Зм = (53732 - 2675)*24000 = 12253680 руб.
Расчет затрат на материалы(базовый проект)
Зм = (72922 – 52) = 16253280 руб.
Затраты на энергию рассчитываются по формуле (7.3)
Зэ= S ti*Ni*Km*Kn*Э (7.3)
где ti-штучное время на i-ой операции
Ni-установленная (потребляемая) мощность или расход энергии
Km = 045-коэффициент использования мощности
Kn = 095-коэффициент местных потерь
Э = 18 рубкВт*ч - тариф на электроэнергию
Расчет затрат на электроэнергию
Расчет затрат на электроэнергию(базовый проект)
Затраты на заработную плату рассчитываются по формуле (7.4)
Ззп= S аi*ti*Kg*Kc*Кдоп (7.4)
где ai-часовая тарифная ставка на i-ой операции
ti-продолжительность технологической операции
Kg-коэффициент доплат к основной заработной плате Kg=115
Kc-коэффициент отчислений на социальные нужды Кс=138
Кдоп- коэффициент дополнительной заработной платы Кдоп=135
Расчет заработной платы
Часовая тарифная ставка рубч.
Расчет заработной платы(базовый проект)
Затраты на текущий ремонт времени рассчитываются как 4% от стоимости оборудования.
Зтз = 004*7500000 = 300000 руб.
Зтз = 004*12780000 = 511200 руб.
Затраты на амортизацию рассчитываются по формуле (7.5)
гдеFэ-эффективный фонд работы оборудования ч
Кб-балансовая стоимость оборудования
На-норма амортизации% На=15%
kз-коэффициент загрузки оборудования
kв-коэффициент выполнения норм
Расчет амортизационных отчислений
Расчет амортизационных отчислений(базовый проект)
Результаты расчёта проектного и базового участков сведены в таблицу 7.12
Расчет технологической себестоимости
Элементы технологической
Затраты на материалы
Затраты на зароботную плату и социальные нужды
Затраты на текущий ремонт оборудования
Амортизационные отчисления
Для данного дипломного проекта рекомендован сокращённый вариант финансового раздела и упрощённую схему прогнозирования денежных потоков учитывающих инвестиционную деятельность.
Коэффициент дисконтирования для года t определяется по формуле (7.6)
где r=022 -ставка дисконта
Kg 1 =1(1+0.22)=0.82
Kg 2 =1(1+022)2 =0.67
Kg 3 =1(1+0.22)3 =0.55
Kg 4 =1(1+0.22)4 =0.45
Kg 5 =1(1+0.22)5 =0.37
t-количество лет срока окупаемости t=5 лет
По таблице на листе графической части определили период окупаемости проекта. Оценка эффективности проекта определяется по показателям чистой дисконтированной стоимости и сроку окупаемости проекта.
Проект считается эффективным если ЧДС>0 за срок окупаемости. Так как ЧДС>0 то предлагаемый проект участка экономически целесообразен.
При выполнении проекта были разработаны процессы обработки деталей типа диска на основе группового производства решены вопросы о классификации деталей выборе комплексной детали рассмотрены различные способы изготовления предложенной детали сделан анализ реального базового варианта технологического процесса изготовления данной детали. После анализа был разработаны: маршрут технологического процесса изготовления детали представителя операционная технология т. е. были выбраны базы и средства технологического оснащения определены содержание и последовательность выполнения технологических переходов режимы резания нормы технологического времени. В результате применения новой технологии (нового оборудования режимов обработки) было значительно сокращено количество технологического оборудования время на обработку деталей.
В конструкторской части проекта содержатся вопросы проектирования станочных и контрольных приспособлений средств автоматизации. Спроектированные станочные и контрольное приспособления позволили сократить вспомогательное время на переналадку повысили производительность что сделало возможным их использование на проектируемом гибком автоматизированном участке (ГАУ). Примененные средства автоматизации (автоматический склад кран штабеллер рельсовая тележка промышленные роботы магазин - накопитель) позволили облегчить или исключить участие человека при выполнении большинства операций технологического процесса повысить производительность и качество.
В исследовательской части дипломного проекта дана классификация и сделан краткий обзор загрузочно - накопительных устройств выбран наиболее приемлемый вариант загрузочно накопительного устройства для спроектированного РТК.
В разделе безопасность и экологичности проекта рассмотрены вопросы: безопасность труда при механической обработке материалов резанием; шумовые загрязнения окружающей среды характеристика источников шума в проектируемом цехе нормирование шума на территории предприятия и в жилом массиве; обеспечение устойчивости работы проектируемого участка в условиях ЧС.
При планировании и организации производства были определены: форма организации выполнения технологических процессов производственнвя структура участка состав участка. На основе сравнения был выбран наиболее предпочтительный вариант планировки цеха выбраны оптимальные строительные решения.
При выполнении раздела «Организация производства» были выделены общие проблемы организации производства. Наибольшее внимание было уделено вопросу - организация складского хозяйства. Для проектируемого гибкого автоматизированного участка предложена оптимальная в данных условиях система складировании заготовок и готовых деталей.
СПИСОК ИСПОЛЬЗУЕМЫХ ИСТОЧНИКОВ
Выбор способа изготовления заготовок. Методические указания. -Курган: КМИ 1995.-42 с.
Горбацевич А.Ф. Шкред В.А. Курсовое проектирование по технологии машиностроения-Мн: Выш. школа1983.-256 с.
Гжиров Р.К. Серебреницкий П.П. Программирование обработки на станках с ЧПУ: справочник. - Л: Машиностроение1990.
Технология машиностроения Методические указания к выполнению курсового проекта для студентов направления 552900.-Курган: КМИ 1995.-42 с.
Справочник технолога-машиностроителя В 2-х т. Т1 Под ред. А.Г. Косиловой Р.К. Мещерекова - М: Машиностроение 1986.-496 с.
Кузнецов Ю.И. Маслов А.Р. Байков А.Н. Оснастка для станков с ЧПУ: Справочник - М: Машиностроение 1990.-512 с
Краткий справочник металлистапод ред. Орлова П.Н. Скороходова Е.А. – М: Машиностроение1987.-960 с.
Справочник технолога-машиностроителя В 2-х т. Т2 под ред. А.Г. Косиловой Р.К. Мещерекова - М: Машиностроение 1986.-496 с.
Мосталыгин Г.П. Толмачевский Н.Н. Технология машиностроения - М: Машиностроение 1990.-288 с
Общемашиностроительные нормативы времени и режимов резания для нормирования работ выполняемых на универсальных и многоцелевых станках с ЧПУ. В 2-х ч. Ч.1. - М: Экономика 1990.-206 с
Мельников Г.Н. Вороненко В.П. Проектирование механосборочных цехов. - М: Машиностроение1990.-351 с.
Технология машиностроения (специальная часть): учебник для машиностроительных специальностей вузов А.А.Гусев и др. – М: Машиностроение 1986.–480 с.
Инструмент для станков с ЧПУ: Справочник под ред. Ординарцева. – М: Машиностроение1987.
mar1.cdw

Код наименование оборудования
Обозначение документа
Сталь 38ХС ГОСТ 4543-71
Многоцелевой токарный па 1П756Ф4
без ОК; КЭ; ИОТ N 95
без ОК; КЭ; ИОТ N 66
Вертикально-фрезерный с ЧПУ 6Р13Ф3-01
без ОК; КЭ; ИОТ N 67
без ОК; КЭ; ИОТ N 84
tit1.cdw
Утверждаю: Зав.кафедрой Давыдова М.В.
на технологический процесс механической обработки
Студент гр. ТЗ-6111 Васюков С.А.
Руководитель Баитов П.А.
Министерство образования и науки РФ
mar2.cdw
наименование оборудования
сб.единицы или материала
Обозначение документа
Машина моечная МКП-0620
без ОК; КЭ; ИОТ N 91
oper05_4(Васюков).cdw

КР-РМ-100%; KM-PM-5%; OTK-5%
oper05_1(Васюков).cdw

Обозначение программы
Установить и снять деталь
Резец SSSCR88D06 Т15К6 ТУ 19-4206-95-83
Трехкулачковый спец патрон
oper05_3(Васюков).cdw
Резец К014980.000-00 Т15К6 ТУ2 035-1040-86
Точить поверхность 7
Резец SSSCR88D06 Т15К6 ТУ 19-4206-95-83
Резец отрезной 2177-0005 Т15К6 ГОСТ 18892-73
Точить поверхность 6
Резец подрезной 2112-0005 Т15К6 ГОСТ 18880-73
oper05_2(Васюков).cdw
Резец К014980.000-00 Т15К6 ТУ2 035-1040-86
Расточить начерно отверстие 2
Расточить начисто отверстие 2
Расточить тонко отверстие 2
oper35(Васюков).cdw

Наименование средств ТО
Наименование операции
Наименование оборудования
Контролируемые параметры
Технический контроль
Проверить размеры 16
Проверить размеры 22
Проверить размеры 27
Проверить размеры 34
Проверить допуски торцевого биения
Проверить шероховатость
Нутромер ТУ 3-3-1396-76
Штангенциркуль ШЦ-400-0
Приспособление специальное
Пробка 15Н14 ГОСТ 14815-69
Штангенглубиномер ШГ-200 ГОСТ 162-80
Пробка М8-7Н8221-3036 ГОСТ 186-80
Пробка 6Н14 ГОСТ 14810-69
Индикатор ИЧ10кл0 ГОСТ 577-68
Образцы шероховатости ГОСТ 2789-73
oper015(Васюков).cdw
Обозначение программы
Установить и снять деталь
Долбить зубчатый венец 1
Долбяк m6*z21 2530-0268 ГОСТ9323-79
Приспособление специальное
КР-РМ-100%; KM-PM-5%; OTK-5%
эскиз(015).cdw

oper10_2(Васюков).cdw

Резец К014980.000-00 Т15К6 ТУ2 035-1040-86
Расточить начерно отверстие 1
Расточить начисто отверстие 1
Расточить тонко отверстие 1
oper10_6(Васюков).cdw

Нарезать резьбу в 12 отверстиях выдерживая размеры 14
Сверлить 12 отверстий выдерживая размеры 18
Сверло 6113-0852 ГОСТ 17201-71; Патрон 22627-77
Фрезеровать паз 9 выдерживая размер 26
Фреза 01.3.0036.000-04 ТУ 2-035-812-81; Втулка 80-40 ГОСТ
Фрезеровать пазы выдерживая размеры 28
КР-РМ-100%; KM-PM-5%; OTK-5%
oper10_5(Васюков).cdw
Резец К014980.000-00 Т15К6 ТУ2 035-1040-86
Расточить начисто канавку 6 выдерживая размеры 3
Центровать все крепежные отверстия
Сверло 035-2317-0102 ОСТ 24-20-5-80; Патрон ГОСТ 22627-77
Сверлить 12 отверстий выдерживая размеры 32
Сверло 2300-6983 ГОСТ 886-77; Патрон ГОСТ 17201-71
oper10_4(Васюков).cdw
Резец К014980.000-00 Т15К6 ТУ2 035-1040-86
Точить канавку 8 выдерживая размеры 15
Точить канавку 4 выдерживая размер 8
снять фаску выдерживая размеры 4
Точить канавку 6 выдерживая размеры 2
oper10_1(Васюков).cdw

Обозначение программы
Установить и снять деталь
Резец SSSCR88D06 Т15К6 ТУ 19-4206-95-83
Трехкулачковый спец патрон
oper10_3(Васюков).cdw
Точить начерно поверхность 7
Резец подрезной 2112-0005 Т15К6 ГОСТ 18880-73
Точить начисто поверхность 7
Точить тонко поверхность 7
Точить поверхность 10 выдерживая размер 1
oper020(Васюков).cdw
035-2317-0102 ОСТ 24-26-5-80; Втулка ГОСТ 26538-85;
2300-6983 ГОСТ 886-77; Втулка ГОСТ 26538-85;
Наименование операции
Обозначение программы
Установить и снять деталь
Центровать 6 отверстий 1
Приспособление специальное
Сверлить 6 отверстий 1
КР-РМ-100%; KM-PM-5%; OTK-5%
эскиз(020).cdw

mar1(Васюков).cdw
Код наименование оборудования
Обозначение документа
Сталь 38ХС ГОСТ 4543-71
Многоцелевой токарный па 1П756Ф4
Зубодолбежный па 5М150
без ОК; 20121.00001; ИОТ N 95
без ОК; 20141.00003; ИОТ N 72
141.00001; 60141.00001; ИОТ N 66
Вертикально-фрезерный с ЧПУ 6Р13Ф3-01
без ОК; 20141.00004; ИОТ N 67
141.00002; 60141.00005; ИОТ N 66
mar2(Васюков).cdw
наименование оборудования
сб.единицы или материала
Обозначение документа
Машина моечная МКП-0620
без ОК; КЭ; ИОТ N 84
103.00001; 60103.00001; ИОТ N 91
tit1.cdw

Курганский Государственный университет
Утверждаю: Зав.кафедрой Давыдова М.В.
на технологический процесс механической обработки
Студент гр. ТЗ-6111 Васюков С.А.
Руководитель Баитов П.А.
mar1(Васюков).cdw

Код наименование оборудования
Обозначение документа
Сталь 40Х ГОСТ 4543-71
Многоцелевой токарный па 1П756Ф4
без ОК; КЭ; ИОТ N 95
без ОК; КЭ; ИОТ N 66
без ОК; КЭ; ИОТ N 84
Машина моечная МКП-0620
tit1.cdw

Утверждаю: Зав.кафедрой Давыдова М.В.
на технологический процесс механической обработки
Студент гр. ТЗ-6111 Васюков С.А.
Руководитель Баитов П.А.
Министерство образования и науки РФ
mar2.cdw
наименование оборудования
сб.единицы или материала
Обозначение документа
без ОК; КЭ; ИОТ N 91
mar1.cdw
Код наименование оборудования
Обозначение документа
Сталь 38ХС ГОСТ 4543-71
Многоцелевой токарный па 1П756Ф4
Зубодолбежный па 5М150
без ОК; КЭ; ИОТ N 95
без ОК; КЭ; ИОТ N 72
без ОК; КЭ; ИОТ N 66
Вертикально-фрезерный с ЧПУ 6Р13Ф3-01
без ОК; КЭ; ИОТ N 67
tit1.cdw
Утверждаю: Зав.кафедрой Давыдова М.В.
на технологический процесс механической обработки
Студент гр. ТЗ-6111 Васюков С.А.
Руководитель Баитов П.А.
Министерство образования и науки РФ
mar2.cdw
наименование оборудования
сб.единицы или материала
Обозначение документа
Машина моечная МКП-0620
без ОК; КЭ; ИОТ N 84
без ОК; КЭ; ИОТ N 91
titul.cdw
Курганский государственный университет
Утверждаю: Зав.кафедрой
на технологический процесс механической обработки
mar1.cdw
Код наименование оборудования
Обозначение документа
Сталь 38ХС ГОСТ 4543-71
Многоцелевой токарный па 1П756Ф4
без ОК; КЭ; ИОТ N 95
без ОК; КЭ; ИОТ N 66
Вертикально-фрезерный с ЧПУ 6Р13Ф3-01
без ОК; КЭ; ИОТ N 67
без ОК; КЭ; ИОТ N 84
tit1.cdw

Утверждаю: Зав.кафедрой Давыдова М.В.
на технологический процесс механической обработки
Студент гр. ТЗ-6111 Васюков С.А.
Руководитель Баитов П.А.
Министерство образования и науки РФ
mar2.cdw
наименование оборудования
сб.единицы или материала
Обозначение документа
Машина моечная МКП-0620
без ОК; КЭ; ИОТ N 91
Рекомендуемые чертежи
- 24.01.2023
- 29.07.2014
- 24.01.2023