Проект участка на базе станков с ЧПУ по изготовлению деталей трансмиссии транспортной машины




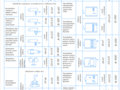
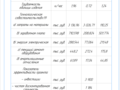
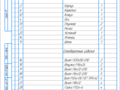
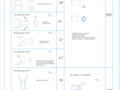
- Добавлен: 24.01.2023
- Размер: 1 MB
- Закачек: 0
Описание
Состав проекта
![]() |
![]() |
![]() |
![]() ![]() ![]() ![]() |
![]() ![]() ![]() ![]() |
![]() ![]() ![]() ![]() |
![]() ![]() ![]() ![]() |
![]() ![]() ![]() ![]() |
![]() |
![]() ![]() ![]() ![]() |
![]() ![]() ![]() ![]() |
![]() ![]() ![]() ![]() |
![]() ![]() ![]() ![]() |
![]() ![]() ![]() ![]() |
![]() |
![]() ![]() ![]() ![]() |
![]() ![]() ![]() ![]() |
![]() ![]() ![]() ![]() |
![]() ![]() ![]() ![]() |
![]() ![]() ![]() ![]() |
![]() |
![]() ![]() ![]() ![]() |
![]() ![]() ![]() ![]() |
![]() ![]() ![]() ![]() |
![]() ![]() ![]() ![]() |
![]() ![]() ![]() ![]() |
![]() |
![]() |
![]() ![]() ![]() ![]() |
![]() |
![]() ![]() ![]() ![]() |
![]() ![]() ![]() ![]() |
![]() ![]() ![]() ![]() |
![]() |
![]() ![]() ![]() ![]() |
![]() ![]() ![]() ![]() |
![]() ![]() ![]() ![]() |
![]() |
![]() ![]() ![]() ![]() |
![]() ![]() ![]() ![]() |
![]() ![]() ![]() ![]() |
![]() ![]() ![]() ![]() |
![]() |
![]() ![]() ![]() ![]() |
![]() ![]() ![]() ![]() |
![]() ![]() ![]() ![]() |
![]() |
![]() ![]() ![]() ![]() |
![]() ![]() ![]() ![]() |
![]() |
![]() ![]() ![]() ![]() |
![]() ![]() ![]() ![]() |
![]() ![]() ![]() ![]() |
![]() ![]() ![]() ![]() |
![]() |
![]() ![]() ![]() ![]() |
![]() |
![]() ![]() ![]() ![]() |
![]() ![]() ![]() ![]() |
![]() ![]() ![]() ![]() |
![]() |
![]() ![]() ![]() ![]() |
![]() |
![]() ![]() ![]() ![]() |
![]() ![]() ![]() |
![]() |
![]() |
![]() |
![]() |
![]() |
![]() |
![]() |
![]() |
![]() |
![]() |
![]() |
![]() |
![]() |
![]() |
![]() |
![]() |
![]() |
![]() |
![]() |
![]() |
![]() |
![]() |
![]() |
![]() |
![]() |
![]() |
![]() ![]() ![]() ![]() |
![]() ![]() ![]() ![]() |
![]() ![]() ![]() |
![]() |
![]() |
![]() ![]() ![]() ![]() |
![]() ![]() ![]() |
![]() |
![]() ![]() ![]() ![]() |
![]() ![]() ![]() ![]() |
![]() |
![]() |
![]() ![]() ![]() ![]() |
![]() |
![]() ![]() ![]() ![]() |
![]() |
![]() ![]() ![]() ![]() |
![]() ![]() ![]() ![]() |
![]() ![]() ![]() ![]() |
![]() ![]() ![]() |
Дополнительная информация
Маршрут карта (лист 3).frw

Титульный.frw

Маршрут карта (лист 1).frw

Маршрут карта (лист 2).frw

Карта Эскиза на дет5.frw

Карта Эскиза на дет1.frw

Маршрут карта (лист 3).frw

Титульный.frw

Маршрут карта (лист 1).frw

Маршрут карта (лист 2).frw

Маршрут карта (лист 3).frw

Титульный.frw

Маршрут карта (лист 1).frw

Маршрут карта (лист 2).frw

Карта Эскиза на дет3.frw

Маршрут карта (лист 3).frw

Титульный.frw

Маршрут карта (лист 1).frw

Карта Эскиза на дет4.frw

Маршрут карта (лист 2).frw

Комплект документов.frw

Операционная карта (лист 2).frw

Карта Эскизов на операцию 010.frw

Операционная карта (лист 1).frw

Маршрут карта (лист 3).frw

Маршрут карта (лист 1).frw

Маршрут карта (лист 2).frw

Операционная карта (лист 2).frw

Операционная карта (лист 3).frw

Карта Эскизов на операцию 005.frw

Операционная карта (лист 1).frw

Операционная карта (лист 2).frw

Карта Эскизов на операцию 025.frw

Операционная карта (лист 1).frw

Карта Эскизов на операцию 035.frw

Операционная карта (лист 1).frw

Операционная карта (лист 2).frw

Операционная карта (лист 3).frw

Операционная карта (лист 1).frw

Карта Эскизов на операцию 015.frw

Карта эскизов на заготовку.frw

Операционная карта (лист 2).frw

Карта Эскизов на операцию 030.frw

Операционная карта (лист 1).frw

ЭКОНОМИКА.сdw..cdw

МОЙ ПЛАН.cdw

план РТК.cdw

Схват.cdw

сравнит.cdw

2.cdw

1.cdw

контр.приспособление-готово.cdw

фрезерное присп.(только 2-ой лист).cdw

приспособление-готово.cdw

Спецификация1.cdw

Спецификация2.cdw

Рекомендуемые чертежи
- 24.01.2023
- 24.01.2023