Разработка автоматизированного участка по изготовлению корпусных деталей на базе многоцелевых станков типа ОЦ и станков с ЧПУ





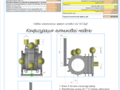
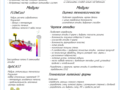
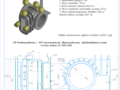
- Добавлен: 24.01.2023
- Размер: 17 MB
- Закачек: 3
Описание
Состав проекта
![]() |
![]() |
![]() ![]() ![]() ![]() |
![]() ![]() ![]() ![]() |
![]() |
![]() |
![]() ![]() ![]() ![]() |
![]() |
![]() ![]() ![]() ![]() |
![]() |
![]() |
![]() ![]() ![]() ![]() |
![]() ![]() ![]() ![]() |
![]() ![]() ![]() ![]() |
![]() |
![]() ![]() ![]() ![]() |
![]() ![]() ![]() ![]() |
![]() |
![]() |
![]() ![]() ![]() ![]() |
![]() |
![]() ![]() ![]() ![]() |
![]() |
![]() |
![]() ![]() ![]() ![]() |
![]() |
![]() |
![]() ![]() ![]() ![]() |
![]() |
![]() ![]() ![]() ![]() |
![]() ![]() ![]() ![]() |
![]() ![]() ![]() ![]() |
![]() |
![]() ![]() ![]() |
![]() ![]() ![]() |
![]() ![]() ![]() |
![]() ![]() ![]() |
![]() ![]() ![]() |
![]() ![]() ![]() |
![]() ![]() ![]() |
![]() ![]() ![]() |
![]() ![]() ![]() |
![]() ![]() ![]() |
![]() ![]() ![]() |
![]() ![]() ![]() |
![]() ![]() ![]() |
![]() ![]() ![]() |
![]() ![]() ![]() |
![]() |
![]() ![]() ![]() ![]() |
![]() ![]() ![]() ![]() |
![]() ![]() ![]() ![]() |
![]() ![]() ![]() ![]() |
![]() ![]() ![]() ![]() |
![]() |
![]() |
![]() ![]() ![]() ![]() |
![]() ![]() ![]() ![]() |
![]() ![]() ![]() ![]() |
![]() ![]() ![]() ![]() |
![]() |
![]() |
![]() |
![]() |
![]() |
![]() ![]() ![]() ![]() |
![]() ![]() ![]() ![]() |
![]() |
![]() |
![]() |
![]() |
![]() ![]() ![]() ![]() |
![]() |
![]() |
![]() ![]() ![]() ![]() |
![]() |
![]() ![]() ![]() ![]() |
![]() ![]() ![]() ![]() |
![]() ![]() ![]() ![]() |
![]() ![]() ![]() ![]() |
![]() |
![]() |
![]() |
Дополнительная информация
10 Исслед2.cdw

внедрения предлагаемой технологии
Литье в песчано-глинистую форму
Формовочные уклоны до 2
в сторону увеличения
Неуказанные радиусы 5 мм
Всего залитого металла 840
питателей литниковой системы 125 кг
термоизоляционных вставок 5
Выход годного составил 80
Проект автоматизированного участка по изготовлению деталей
Технико-экономические
показатели внедрения
предлагаемой технологии
Конфигурация литниковой модели
Годовой экономический эффект составил 462 545
4 Наладка2.cdw

Оправка: борштанга специальная.
Поворот стола на 180
обработка второго фланца аналогично
Режущая пластина CNMM 190608-R5
Оправка: борштанга специальная
Циклограмма работы инструмента:
Режущая пластина CNMG120408-MF2
Режущая пластина VNMG 160404-M3
Т03: Резец: MCLNL 3232 Режущая пластина: CNMM 190608-
Координаты опорных точек траектории представлены
в расчетно-пояснительной записке табл 2.13.
Инструментная наладка на операцию 010
выполнена на 4 листах. (Лист 2)
Проект автоматизированного участка по изготовлению деталей
ХМ25Л ТУ 41112-017-00218147-99
Обрабатывающий центр Trevisan DS900300C
Спецификация2.spw

Болт М8 х 45 ГОСТ 7798-70
Винт М6 х 14 ГОСТ P 50383-92
Гайка М8 ГОСТ 5915-70
Рым-болт М20.19 ГОСТ 4751-73
Шайба 8 Н ГОСТ 6402-70
Шпонка 6 х 6 х 20 ГОСТ 23360-78
Мотор-редуктор SF8156
5 Наладка3.cdw

Режущая пластина ADGT1204PER-D51 WKP35
Циклограмма работы инструмента:
Режущая пластина ADGT1204PER-D51
Режущая пластина ADGT1204PER-D51 WKP25
Координаты опорных точек траектории представлены
в расчетно-пояснительной записке табл 2.14.
Инструментная наладка на операцию 010
выполнена на 4 листах. (Лист 3)
Проект автоматизированного участка по изготовлению деталей
ХМ25Л ТУ 41112-017-00218147-99
Обрабатывающий центр Trevisan DS900300C
10 Исслед1.cdw

в теле заготовки. Выход годного составил 51
Определение оптимального
расположения прибылей
Компьютерное моделирование действующей
литейной технологии корпуса задвижки
Разработка литниковой модели
корпуса задвижки с использованием
Трехмерная модель действующей
Трёхмерная модель предлагаемой
В результате изменения
конфигурации прибылей и
применения теплоизолирующих
вставок усадочных дефектов в теле
отливки не обнаружено. Вся усадка
расположилась в пределах прибылей
Выход годного составил: 80
Проект автоматизированного участка по изготовлению деталей
Моделирование процесса литья
М о д е л и р о в а н и е
9Мероприятия по Автом.cdw

моделирования процесса литья
- расчет любых видов гравитационной заливки;
- литье под низким давлением;
- встроенный мастер создания прибылей;
- встроенный мастер создания литниковых систем.
Модуль расчета гидродинамики
- данные о температуре;
- давлении металла в любой точке.
Модуль оптимизации технологии
подбор оптимальных параметров ТП:
- температура заливаемого металла;
- продолжительность заполнения;
Трассирование потока в
Стальная отливка с оптимизированными
прибылями 13% увеличение выхода годного
достигнуто автоматически
разработки технологии изготовления отливок
из черных и алюминиевых сплавов в сырых разовых формах;
- разработки технологии изготовления отливок;
из алюминиевых сплавов литьём под давлением.
Оценка технологичности
Позволяет проработать чертеж детали
с целью определения возможности
изготовления отливки выбранным способом.
Позволяет определить:
положение отливки в форме и выбрать плоскость разъема;
- возможность получения отверстий в литье;
- количество отливок в форме;
- возможность формирования полостей;
- минимальные толщины стенок;
- в соответствии с требуемой точностью отливки значение припусков
- на механическую обработку
- расположения поверхностей;
- место подвода металла с выявлением тепловых узлов
прибылей и холодильников;
Разработать и оформить чертеж отливки в соответствии с
Технология литейной формы
-определить границы сложного стержня;
- разработать схему литейной формы с размещением стержней и болванов;
- разработать или выбрать схему ЛПС и провести расчет
Проект автоматизированного участка по изготовлению деталей
Автоматизация конструкторско-
технологической подготовки
в литейном производстве
13Экономикаконец.cdw

Проект автоматизированного участка по изготовлению деталей
Технико-экономические
Годовой выпуск продукции
Колличество установленного
Коэффицент загрузки
изготовления деталей
Технологическая себестоимость изделия
а) основные материалы
б) энергия на техноло-
в) Зп производственных
рабочих с отчислениями
г) Затраты на текущий
д) Расходы на амморти-
Показатели эффективности проекта
б)чистый дисконтиро-
в) период окупаемости
3 Наладка1.cdw

Оправка: борштанга специальная.
Инструментная наладка на операцию 010
выполнена на 4 листах. (Лист 1)
Поворот стола на 180
обработка второго фланца аналогично
Резец: S50V-MCLNRR19
Оправка: борштанга специальная
Циклограмма работы инструмента:
Режущая пластина CCMT 09T308-F1
Т02: Резец Режущая пластина CCMT 09T308-
Проект автоматизированного участка по изготовлению деталей
ХМ25Л ТУ 41112-017-00218147-99
Обрабатывающий центр Trevisan DS900300C
13Экономика.cdw

Проект автоматизированного участка по изготовлению деталей
Технико-экономические
Годовой выпуск продукции
Колличество установленного
Коэффицент загрузки
изготовления деталей
Технологическая себестоимость изделия
а) основные материалы
б) энергия на техноло-
в) Зп производственных
рабочих с отчислениями
г) Затраты на текущий
д) Расходы на амморти-
Показатели эффективности проекта
б)чистый дисконтиро-
в) период окупаемости
1Сравнительная технология базовый.cdw

Обрабатывающий центр ИР1250ПМФ4
Радиально-сверлильный 2М57
0 Сверлильная (обработка с двух сторон
с переустановом заготовки)
5 Токарная. Токарно-карусельный 1541
Эскиз аналогичен эскизу операции 010
Проект автоматизированного участка по изготовлению деталей
Сравнительная технология
изготовления корпуса
ХМ25Л ТУ 41112-017-00218147-99
0 Токарная. Токарно-карусельный 1541
5 Карусельная Токарно-карусельный 1516Ф3
Сравнительная технология выполнена на двух листах. Лист1
Спецификация1.spw

Болт М24 х 80 ГОСТ 7798-70
Болт М12 х 30 ГОСТ 7798-70
Болт М36 х 280 ГОСТ 7798-70
Винт М20 х 65 ГОСТ 11738-84
Винт М8 х 16 ГОСТ 1491-80
Гайка М72 х 2 ГОСТ 11871-88
Опора 7035-0537 ГОСТ 4740-68
Палец 7030-0909 22g6 ГОСТ 12209-66
Рым-болт М24.19 ГОСТ 4751-73
Шайба 24 Н ГОСТ 6402-70
Шайба 20 Н ГОСТ 6402-70
Шайба 65 ГОСТ 9649-78
2Сравнительная технология проектный.cdw

0 Комбинированная с ЧПУ Горизонтальный
обрабатывающий центр
Trevisan модель DS 900300C
Проект автоматизированного участка по изготовлению деталей
Сравнительная технология
изготовления корпуса
ХМ25Л ТУ 41112-017-00218147-99
Величина годовой экономии по приведенным
затратам равна 9687668
Литье в песчано-глинистую форму
Формовочные уклоны до 2
в сторону увеличения
Неуказанные радиусы 5 мм
Всего залитого металла 840
питателей литниковой системы 125 кг
термоизоляционных вставок 5
Выход годного составил 80
Годовой экономический эффект составил 462545
Сравнительная технология выполнена на двух листах. Лист2
6 Наладка 4.cdw

выполнена на 4 листах. (Лист 4)
Центральная пластина SPGX 0903-C1 T3000D
Периферийная пластина SCGX 070308-P1
Фасочная пластина SD200-C45
Циклограмма работы инструмента:
Фреза R396.19 -2522.3S-4003-3-065A
Пластина 396.19 -4003.ON1.0ISO
Сверло SD502-33-66-40R7
0 Комбинированная с ЧПУ
Поворот палеты на 180
аналогично обрабатывается второй фланец
Проект автоматизированного участка по изготовлению деталей
ХМ25Л ТУ 41112-017-00218147-99
7Приспособление.cdw

Покрасить поверхности 1
эмалью АК-194 ТУ 6-10-901-75.
Данное приспособление может использоваться для более крупных
деталей подобного типа с максимальным диаметром фланцев до
Неуказанные предельные отклонения размеров отверстий Н14
Сварные швы по ГОСТ 5264-80.
12Планировка.cdw

- Промышленный пылесос
- Верстак для наладки инструментов
- Инструментальный склад
Площадь участка S=984 м
Условные обозначения:
- аптечка медицинская
- подвод сжатого воздуха.
- подвод смазочно охлажд. жид.
- подвод электроэнергии.
График загрузки станков
Внутрицеховой проезд
Магистральный проезд
8ЗУ.cdw

Устройство загрузочное
Техническая характеристика:
Номинальная грузоподьемность - 2000 кг.
Технические требования:
Покрасить поверхности 1
эмалью АК-194 ТУ 6-10-901-75.
Неуказанные предельные отклонения размеров отверстий Н14
Сварные швы по ГОСТ 5264-80.
6.1.doc
Данные о номенклатуре выпускаемых деталей годовом объеме выпуска массах заготовок и деталей а также станкоемкость по операциям представлены ниже.
Детали выпускаемые на участке:
Корпус ЗКС 160-150 в 5 исполнениях;
Стойка ТЛ 13001-250 в 5 исполнениях;
Крышка КЗ 13011-500 в 7 исполнениях;
Корпус КЗ 11005-250 в 8 исполнениях;
Корпус КЗ 13011-500 в 4 исполнениях;
Корпус КЗ13029-300.1 в 3 исполнениях;
Корпус ЗКС 160-015 в 2 исполнениях;
Корпус КЗ21216-015 в 2 исполнениях.
Детали обрабатываемые на станке Tevisan DS30070C:
Корпус ЗКС 160-150 (Деталь-представитель)
Годовой объем выпуска N = 250 шт
Наибольший габаритный размер детали – 444 мм
Масса детали –1014 кг
Масса заготовки – 125 кг
Корпус ЗКС 160-150-01
Годовой объем выпуска N = 220 шт
Корпус ЗКС 160-150-02
Годовой объем выпуска N = 240 шт
Корпус ЗКС 160-150-03
Годовой объем выпуска N = 200 шт
Корпус ЗКС 160-150-04
Годовой объем выпуска N = 230 шт
Стойка ТЛ 13001-250 (Деталь-представитель)
Годовой объем выпуска N = 730 шт
Наибольший габаритный размер детали – 650 мм
Масса детали – 1136 кг
Масса заготовки – 12 кг
Стойка ТЛ 13001-250-01
Годовой объем выпуска N = 680 шт
Масса детали – 1196 кг
Стойка ТЛ 13001-250-02
Годовой объем выпуска N = 700 шт
Стойка ТЛ 13001-250-03
Годовой объем выпуска N = 660 шт
Стойка ТЛ 13001-250-04
Годовой объем выпуска N = 650 шт
Детали обрабатываемые на станке Tevisan DS600200C:
Крышка КЗ 13011-500 (Деталь-представитель)
Годовой объем выпуска N = 180 шт
Наибольший габаритный размер детали – 818 мм
Крышка КЗ 13011-500-01
Годовой объем выпуска N = 175 шт
Крышка КЗ 13011-500-02
Крышка КЗ 13011-500-03
Годовой объем выпуска N = 170 шт
Крышка КЗ 13011-500-04
Крышка КЗ 13011-500-05
Годовой объем выпуска N = 160 шт
Крышка КЗ 13011-500-06
Корпус КЗ 11005-250 (Деталь-представитель)
Наибольший габаритный размер детали – 716 мм
Масса детали – 412 кг
Масса заготовки – 536 кг
Корпус КЗ 11005-250-01
Годовой объем выпуска N = 235 шт
Корпус КЗ 11005-250-02
Корпус КЗ 11005-250-03
Годовой объем выпуска N = 235
Корпус КЗ 11005-250-04
Годовой объем выпуска N = 230
Корпус КЗ 11005-250-05
Корпус КЗ 11005-250-06
Корпус КЗ 11005-250-07
Детали обрабатываемые на станке Tevisan DS900300C:
Наибольший габаритный размер детали – 960 мм
Масса детали – 600 кг
Масса заготовки – 710 кг
Корпус КЗ 13010-500.1
Масса детали – 725 кг
Масса заготовки – 910 кг
Корпус КЗ 13010-500.1-01
Масса детали – 675 кг
Корпус КЗ 13010-500.1-07
Годовой объем выпуска N = 190 шт
Корпус КЗ13029-300 (Деталь-представитель)
Наибольший габаритный размер детали – 711 мм
Масса детали –372 кг
Масса заготовки – 509 кг
Корпус КЗ13029-300.1-06
Масса детали –455 кг
Корпус КЗ13029-300.1-10
Детали обрабатываемые на станке MK7702 и 7Д430:
Годовой объем выпуска N = 6000 шт
Масса заготовки –2 кг
Корпус ЗКС 160-015-05
Годовой объем выпуска N = 500 шт
Детали обрабатываемые на станке MK7702 и 6520Ф3:
Корпус КЗ21216-015 (Деталь-представитель)
Годовой объем выпуска N = 7200 шт
Масса детали – 103 кг
Масса заготовки – 17 кг
Корпус КЗ21216-015-07
Годовой объем выпуска N = 400 шт
Данные расчета приведенной программы детали типа корпус
Приведенная программа
Приведенное количество
Среднее значение квалитета точности kt
Среднее значение параметра шероховатости Ra мкм
Коэффициенты приведения
Данные расчета приведенной программы детали типа стойка
Данные расчета приведенной программы детали типа крышка
Корпус КЗ11005-250-05
Корпус КЗ11005-250-06
Корпус КЗ11005-250-07
Форма организации выполнения технологических процессов
На участке выполняются операции механической обработки и промежуточного контроля сборка и окончательный контроль выполняются на других участках.
Участок спроектирован по принципу подетально-групповой специализации. За каждым рабочим местом закреплена одна технологическая операция. Производство непоточное.
Производственная структура участка
Участок предназначен для изготовления корпусных деталей. В состав участка входит оборудование для металлообработки а именно: многоцелевые станки с ЧПУ со сменными столами-спутниками модели Trevisan DS 30070C Trevisan DS 60070C Trevisan DS 900300C МК70277 долбежный станок 7Д430 фрезерный станок 6520Ф3 . Кроме станков в структуру участка входит верстак для слесарных работ места загрузки-разгрузки деталей место для установки деталей в приспособления средства уборки стружки место мастера.
Заготовительные операции производятся вне участка во вспомогательных производствах завода.
Расчёт количества станков в линии степень их загрузки и использования
Методика расчета взята из [10].
Расчетное количество станков:
гдеТ –суммарная станкоемкость обработки годового количества деталей на станках данного типоразмера ст-ч.
Фо –эффективный годовой фонд времени работы оборудования ч.
Рассчитаем количество станков Trevisan DS900300C необходимых для выполнения комбинированной операции
Фо=3850 ч – для станков типа ОЦ
Принимаем один станок Trevisan DS 900300C.
Определим коэффициент загрузки станков:
где - расчётное количество оборудования
- принятое количество станков.
Так как Кз меньше рекомендованного значении [Кз]=09 то Ки- коэффициент использования станка принимаем равным 1.
Количество станков с учётом коэффициента использования:
Таким образом окончательно принимаем 1 станок Trevisan DS 900300C.
КзКи=075 1=075 (6.4)
Для наглядности данные по расчету сведем в таблицу 6.7.
Количество станков степень их загрузки и использования
Годовой объём выпускаNшт
Стойка ТЛ13001-250.4
В итоге расчёта получили средний коэффициент загрузки станков 058 что соответствует нормативам предъявляемых к непоточному производству.
Проектирование системы удаления стружки
Методика расчета взята из [5].
Для выбора способа удаления и переработки стружки определяют её количество образующееся на 1м2 участка в год.
Данные расчёта представим в виде таблицы 6.8.
Расчет годового объема стружки
Годовой объем выпуска
Вес стружки за год кг
Расчет площадей производственных участков выполняется по формуле:
где - количество единиц производственного оборудования;
- удельная производственная площадь.
На 1м2 приходится 064 т в год. По результатам расчета принимаем для удаления стружки комбинированную систему уборки стружки
Общий вид пневматической системы уборки стружки изображен на схеме на рис.6.1.
Рис.6.1. Система уборки стружки
Рис.6.2. Общий вид вакуумной установки
Назначение: Стационарная вакуумная система - идеальное решение для сбора стружки от станков применяется для удаления сварочных аэрозолей пригодна для очистки локальных рабочих мест и объемных торговых площадей. Может обслуживать до 6 станков.
Описание: Вакуумный пылесос с прямо приводным боковым канальным вентилятором. Пылесос собран как единое целое на базе стальной рамы вместе с "YD"-стартером автоматическим стартстопом автоматической системой очистки фильтра блоком управления и интегрированным 24В трансформатором. В комплекте 50л контейнер на роликах.
Фильтр: При входе в систему воздушный поток снижает скорость и проходит через фильтрующий мешок тонкой очистки. Супертонкие частицы отделяются на поверхности рукавных фильтров из специально обработанного полиэфира. Обработка не позволяет мелким частицам проникать в толщу материала. Таким образом создан легко очищаемый фильтр с долгим сроком жизни. Степень фильтрации согласно BIA категории F.
Концепция фильтра в установке уникальна поскольку сочетает высокую эффективность фильтра с долгим сроком жизни.
В установке используется очистка фильтра при помощи краткого импульса обратного потока атмосферного воздуха. В момент быстрого открытия клапана расположенного над фильтрами возникает мощный импульс воздуха стряхивающий стружку и пыль с рукавов.
Рис.6.3. Принцип действия фильтрующей системы установки
Низкий уровень шума - очевидное требование к современной производственной среде. Вакуумная установка разработана в соответствии с современными требованиями по шуму оборудована эффективными шумоглушителями и шумопоглощающим кожухом. Кожух легко снимается для обслуживания.
Численность производственных рабочих
Число рабочих Рс обслуживающих участок механической обработки определим по формуле[4]:
где Кз – коэффициент загрузки станка;
Фр – эффективный годовой фонд времени работы рабочего чел-ч;
Км – коэффициент многостаночного обслуживания;
Ки – коэффициент использования станка;
Фо – эффективный годовой фонд времени работы оборудования ч.
Станки: Trevisan DS 30070C Trevisan DS 600200C Trevisan DS 900300C:
Станки: MK7702 6520Ф3:
Таким образом общее число рабочих – станочников при многостаночном обслуживании равно 4.
Также на участке необходимо разместить двух слесарей для обеспечения установки деталей в приспособление и одного слесаря который будет производить размерную настройку инструмента.
Описание подсистемы складирования и транспортирования
Краткие сведения о станке Trevisan DS 30070C
Размеры стола-спутника мм .600 х 600
Емкость инструментального магазина ..46
Габаритные размеры станка ..7000 × 3100 × 3000 мм
Краткие сведения о станке Trevisan DS 600200C
Размеры стола-спутника мм .1200 х 1200
Емкость инструментального магазина ..54
Габаритные размеры станка ..8000 × 6000 × 4000 мм
Краткие сведения о станке Trevisan DS 900300C
Размеры стола-спутника мм .1250 × 1250 мм
Емкость инструментального магазина ..80
Габаритные размеры станка ..8900 × 7400 × 4500 мм
Краткие сведения о станке МК7702
Размеры стола-спутника мм .. .330 × 500 мм
Емкость револьверной головки .. ..12
Габаритные размеры станка .. ..3000 × 1708 × 1952 мм
Краткие сведения о станке 7Д430
Длина хода долбяка мм 120 × 320 мм
Габаритные размеры станка ..2850 × 2160 × 3010 мм
Краткие сведения о станке 6520Ф3
Размеры стола-спутника мм . 250×630 мм
Габаритные размеры станка .. 3050× 2150 ×2185 мм
По произведенным выше расчетам принимаем число станков на участке 6 при среднем коэффициенте загрузки 0.21.
Кроме трех многоцелевых станков модели Trevisan DS 30070C Trevisan DS 600200C Trevisan DS 900300C токарного станка МК7702 долбежного станка 7Д430 и фрезерного 6520Ф3. в состав системы основного технологического оборудования входит
- инструментальный склад;
- место работы с инструментом.
Транспортирование осуществляется по следующему маршруту:– склад - верстак - станок(Trevisan DS 30070C)- верстак – склад.
Транспортирование осуществляется по следующему маршруту:– склад верстак - станок(Trevisan DS 900300C)- верстак – склад
Транспортирование осуществляется по следующему маршруту:– склад - тара - станок(МК7702)-тара – склад
Транспортирование осуществляется по следующему маршруту:– склад - тара - станок(7Д430)- тара – склад
Транспортирование осуществляется по следующему маршруту:– склад тара - станок(6520Ф3)- тара – склад.
Ввиду значительного разнообразия обрабатываемых деталей на участке создание общего склада для хранения заготовок сопряжено с некоторыми трудностями. Значительный разброс габаритных размеров заготовок и деталей а так же их масс усложняет проектирование единого склада состоящего из стандартных ячеек.
Исходя из приведенного выше анализа номенклатуры а так же из количества обрабатываемых деталей и напряженности грузопотоков предлагается в качестве единого склада заготовок и готовых деталей зону кантовки. Куда будут привозится заготовки всех обрабатываемых деталей. Крупногабаритные изделия будут обрабатываться по штучно а мелкие изделия будут приходить в стандартной таре.
Далее тара с мелкими изделиями будет транспортироваться к обрабатывающему оборудованию в таре операционными партиями а крупногабаритные заготовки предварительно будут транспортированы на специальное рабочее место где будет произведена выверка и установка их на приспособление затем вместе с которым они и будут транспортированы непосредственно на обрабатывающий станок.
Итого склад заготовок и готовых изделий будет представлять из себя место для их непосредственного складирования место для установки на приспособления и совокупность подъемно-транспортных устройств.
Инструментальный склад
Рис.6.4. Автоматизированный склад
Автоматический кран штабелёр является необходимым звеном в цепочке современного складского комплекса обеспечивающим высокую эффективность работы склада. Автоматический штабелер способствует решению проблем хранения и транспортировки товаров на складе. Высокая производительность системы транспортировки отличает автоматический штабелёр использующийся для назначения товаров на краткосрочное хранение добавление или буферное складирование продукции а также складирование промежуточных продуктов между стадиями производства.
Автоматизированные складские системы являются залогом успеха любого современного торгового и промышленного предприятия поскольку позволяют экономить значительное количество средств затрачиваемых на хранение и транспортировку товаров. Автоматизированный склад – современное решение хранения и транспортировки товаров и продукции.
В качестве примера выбираем автоматизированные системы складирование таких фирм как KARDEX SSI SCHAFER – лидерами в производстве автоматизированных складов для любых грузов.
1.doc
При всей своей кажущейся простоте трубопроводная арматура является весьма сложной конструкцией от качества работы которой многое зависит. Потому задвижки клапаны краны и затворы требуют к себе пристального внимания со стороны изготовителей чтобы их прочность и долговечность в нужный момент не подвела. Задвижки здесь - весьма важная по своей функциональности деталь. В зависимости от многих параметров их делят на несколько видов. По своей форме задвижки бывают параллельные и клиновые. Клиновые являются запорными устройствами перекрытие прохода в которых обеспечивается сдвигом затвора перпендикулярно движущемуся потоку. Как правило эти задвижки востребованы для транспортировки воды пара нефти аммиака некоторых нефтепродуктов. Уплотнительные поверхности на клиновом затворе находятся под углом по отношению друг к другу. Сам же клин бывает цельным упругим цельным жестким или же может состоять из двух дисков которые покрываются высоколегированной сталью. Благодаря этому есть возможность производить замену сальниковой набивки во время работы. Параллельные задвижки отличаются от клиновых тем что уплотнительные поверхности их затворов расположены параллельно друг другу а не под углом. Они также могут быть как однодисковыми (шиберными) так и двухдисковыми.
Разные задвижки имеют разное направление движения шпинделя. В зависимости от этого параметра они разделяются на две категории. В первой шпиндель является выдвижным. То есть при закрытии либо открытии задвижки он работает поступательными либо винтовыми движениями. Такие задвижки как правило довольно больших габаритов. Ко второй категории относят задвижки с вращаемым не выдвижным шпинделем. Они меньше по высоте и используются для транспортировки воды нефтепродуктов и ряда других потоков которые не вызывают коррозию. Все остальное транспортируются через задвижки с выдвижным шпинделем.
В качестве запорных устройств на трубопроводах используют стальные задвижки. Они востребованы для перекрытия газообразных и жидких потоков в условиях перепадов давления. Стальные клиновые задвижки могут использоваться в условиях высоких температур до 565°С а вот чугунные задвижки предназначены для полного включения потока среды либо же его отключения. Они выдерживают температуру до 225 градусов Цельсия. На горизонтальном трубопроводе чугунные задвижки устанавливаются маховиком вверх шпиндель при этом расположен вертикально. На вертикальном же трубопроводе они ставятся плашмя и шпиндель повернут горизонтально. Стальные и чугунные задвижки относятся к ремонтируемым изделиям.
Задвижки поддаются как ручному управлению так и автоматическому (с помощью специальных электроприводов). Последний способ удобен благодаря своим широким возможностям. Он позволяет нажатием кнопок останавливать запорное устройство в любом промежуточном положении. Также производится автоматическое отключение двигателя когда затвор достигает крайнего положения. Если же есть датчик положения затвора то на пульте отображается степень открытия или закрытия прохода.
В целом задвижки имеют ряд преимуществ которые также хотелось бы отметить. При их использовании подача среды обеспечивается в любом направлении они имеют малую строительную длину способны перекрывать потоки как жидкой так и более вязкой среды. Гидравлическое сопротивление при этом весьма незначительное. Задвижки имеют следующие характеристики:
- Рабочей средой может выступать пар масло нефть вода щелочь кислота и многое другое;
- Температурный порог задвижки - до 450 градусов;
- Выдерживается давление до 25 МПа;
- Довольно большие колебания возможного диаметра Ду: от 50 до 1200.
Срок службы задвижек зависит от их правильной установки подготовки рабочей поверхности и среды в которой она будет действовать. Устанавливаемая задвижка фланцевая должна в точности соответствовать указанным в паспорте техническим характеристикам и средам несоответствие может привести к преждевременной порче задвижки. Нельзя устанавливать задвижку маховиком вниз так как в этом случае при ее открытии жидкость или пар могу вытечь. При монтаже задвижки также следует обращать внимание на то чтобы фланцы были установлены без перекосов.
Корпусные детали широко применяются в машиностроении. Конструктивной особенностью деталей этого типа является то что они имеют сложную форму и довольно высокие требования по точности размеров расположению поверхностей прочности жесткости износостойкости коррозионной стойкости и другим свойствам определяемым их назначением. В отношении точности обработки к корпусным деталям предъявляют следующие основные требования:
– точность геометрической формы плоских поверхностей;
– точность расстояния между двумя параллельными плоскостями;
– точность относительного поворота плоских базирующих поверхностей;
– точность диаметральных размеров и формы отверстий;
– точность относительного положения осей отверстий;
– параллельность или перпендикулярность осей отверстий или осей отверстий и плоскостей.
К обрабатываемым поверхностям предъявляются также определенные требования в отношении шероховатости поверхностей.
Большинство корпусных деталей изготовляют из серого чугуна и углеродистой стали; применяют также ковкий чугун легированные стали цветные сплавы и т.д. Заготовки корпусных деталей изготовляют литьем литьём и сваркой. Литые заготовки получают литьем в песчано-глинистые формы в кокиль в оболочковые формы под давлением.
В данном дипломном проекте разрабатывается автоматизированный участок по изготовлению элементов запорной арматуры.
На данном участке изготовляется следующая номенклатура деталей:
Корпус задвижки ЗКС160-015
с условным проходом 15мм
Корпус клапана запорного
Основной деталью дипломного проекта является корпус задвижки КЗ13011-500.
Рис. 1.1. Изготовляемая деталь – корпус задвижки
Данная деталь входит в состав сборочной единицы (задвижка клиновая) которая является готовым изделием.
Задвижки клиновые с выдвижным шпинделем предназначены для установки их на трубопроводах в качестве запорных устройств для водогазонефтяных смесей.
Корпусные детали изготавливаются из стали 25Л 12Х18Н12МЗТЛ ХМ25Л или из материала заказчика методом литья.
Рабочей средой задвижки являются жидкие и газообразные неагрессивные нефтепродукты вода пар. Допускается применение на других рабочих средах не агрессивных к материалам деталей задвижек.
Задвижка стальная относится к классу восстанавливаемых ремонтируемых изделий.
Задвижки изготовляются с клином жесткой конструкции.
Климатическое исполнение по ГОСТ 15150: У1; ХЛ1.
Задвижки изготовляются с ручным управлением под электропривод с нормальным и взрывозащитным электроприводом а также со специальным типом и требованиями по управлению.
Рабочее давление задвижек: 16 МПа; 25 МПа; 40 МПа.
Присоединение к трубопроводу: фланцевое по ГОСТ 12818 с ответными фланцами по ГОСТ12820 или ГОСТ 12821.
Корпус задвижки рассматриваемый в данном курсовом проекте изготовлен из стали ХМ25Л. Деталь-корпус предназначена для размещения в ней запорного механизма который обеспечивает функционирование задвижки.
Химический состав материала ХМ25Л
Механические свойства материала ХМ25Л
Относительное удлинение
Относительное сужение
ТЕХНОЛОГИЧЕСКИЙ РАЗДЕЛ
1. Определение типа производства
Тип производства по ГОСТ 3.1121-84 характеризуется коэффициентом закрепления операций (КЗ.О.):
КЗ.О. 10 – массовое и крупносерийное производство;
КЗ.О. 20 – среднесерийное производство;
КЗ.О. 40 – мелкосерийное производство;
КЗ.О. – единичное производство.
Величину коэффициента закрепления операций с достаточной для учебного проекта точностью можно рассчитать следующим образом [9]:
а) Определяем расчетное количество станков необходимых для каждой станочной операции (Срi):
N – объем годового выпуска деталей; N = 180 шт.;
tШТ-К – штучно-калькуляционное время
Fo – эффективный годовой фонд времени работы станка;
Кв – средний коэффициент выполнения норм времени:
при обработке на станках с ручным управлением Кв = 12;
при обработке на станках с ЧПУ автоматах полуавтоматах и агрегатных станках Кв = 10;
Кр – коэффициент учитывающий потери по организационно-техническим причинам Кр = 095.
При расчете по данной формуле в качестве tШ-К используем штучно-калькуляционное время базового технологического процесса скорректированное путем уменьшения на 10-20%. Корректировка производится с учетом последующего усовершенствования базового технологического процесса и некоторого сокращения трудоемкости изготовления детали. Результаты расчета Срi сведены в таблицу 2.1.
б) Определяем принятое количество оборудования на каждой станочной операции (Si) для чего расчетное количество станков (Срi) округляем увеличением до целых значений.
в) Рассчитываем коэффициент загрузки каждого рабочего места (зi):
г) Определяем число операций закрепленных за одним рабочим местом (Ормi):
где н – нормативный коэффициент загрузки оборудования.
д) Рассчитываем величину коэффициента закрепления операций:
где Рi – общее количество рабочих мест на которых выполняются все станочные операции по изготовлению детали без учета станков-дублеров. Результаты расчета сводим в таблицу.2.1. Имеем: КЗ.О. = 107.
Результаты расчета коэффициента закрепления операций
Номер и наименование операции
0 Комбинированная ЧПУ
В результате расчетов устанавливаем тип производства - среднесерийное. Серийное производство характеризуется изготовлением или ремонтом изделий периодически повторяющимися партиями. Для среднесерийного производства коэффициент закрепления операций принимают от 10 до 20. Серийный тип производства характеризуется изготовлением ограниченной номенклатуры деталей партиями повторяющимися через определенный промежуток времени. Это позволяет использовать наряду с универсальным специальное оборудование. При проектировании технических процессов предусматривают порядок выполнения и оснастку каждой операции. Для организации серийного производства характерны следующие черты: цехи как правило имеют в своем составе предметно-замкнутые участки оборудование на которых расставляется по ходу типового технологического процесса. Предметная специализация участков делает целесообразным обработку партии деталей параллельно на нескольких станках выполняющих следующие друг за другом операции. Как только на предыдущей операции заканчивается обработка нескольких первых штук они передаются на следующую операцию до окончания обработки всей партии. При построении технологического процесса целесообразно применять станки с числовым программным управлением обрабатывающие центры. Это оборудование позволяет повысить концентрацию выполнения операций и обладают достаточно большой степенью гибкости.
2. Анализ конструкции детали на технологичность
Одним из важных этапов проектирования является отработка конструкции детали на технологичность. Оценка технологичности может производиться количественно и качественно с расчётом показателей технологичности по ГОСТ14.201-83 . При этом качественная оценка предшествует количественной и характеризует технологичность обобщённо.
Целью данного этапа является выявление возможности снижения себестоимости и трудоемкости изготовления без ущерба для служебного назначения детали за счет незначительных изменений в ее конструкции.
В результате качественной оценки деталей на технологичность можно сделать следующие выводы:
Материал детали – хладостойкая модифицированная литая сталь ХМ25Л ГОСТ 1583-93 полностью соответствует жестким условиям эксплуатации при низких температурах и требованиям по прочности износостойкости поверхностным деформациям и т.п.
Конструкция детали обеспечивает достаточную жесткость при механической обработке на металлорежущем оборудовании.
Деталь имеет элементы удобные для закрепления заготовки при обработке но при базировании заготовки по необработанным поверхностям возникает большая погрешность базирования.
Имеется возможность использования стандартизованных режущих и измерительных инструментов.
С точки зрения обеспечения заданной точности и шероховатости поверхностей деталь не представляется сложной.
Низкие скорости резания при обработке на токарных станках вследствие большого дисбаланса детали.
Наличие поверхностей которые невозможно обработать без применения специальных режущих инструментов таких как специальные отогнутые резцы борштанги.
Количественную оценку технологичности корпуса проведем по следующим показателям: коэффициенты использования материала (КИ.М.) точности обработки (КТЧ.) шероховатости поверхности (КШ).
Рис.2.1. Анализ чертежа детали
Результаты анализа рабочего чертежа корпуса
Наименование поверхностей
Количество поверхностей
Параметр шероховатости Ra
Центральное отверстие 585Н11
Торец магистрального фланца 585h12
Торец центрального отверстия
Выточка среднего фланца
Тыльная сторона фланца
Торец среднего фланца
Торец выточки фланца
Наружная цилиндрическая поверхность 580
Коэффициент использования материала:
где: МД и МЗ – соответственно массы детали и заготовки в базовом варианте кг.
Найденный коэффициент использования материала удовлетворяет требованию технологичности детали. Чем выше коэффициент использования материала тем лучше экономия металла режущего инструмента машинного времени.
Коэффициент точности:
гдеАСР - средний квалитет точности обработки детали по всем поверхностям.
Согласно чертежу детали ориентировочно можно определить АСР = 125. Тогда КТ.Ч. = 092. Так как КТ.Ч. > 08 то деталь можно считать по этому параметру технологичной.
Коэффициент шероховатости:
Здесь БСР – среднее числовое значение параметра шероховатости всех поверхностей детали.
Ориентировочно БСР = 1122 мкм.
Тогда КШ = 009 Так как КШ 032 то деталь можно считать и по этому показателю технологичной.
На основании качественного и количественного анализа на технологичность можно сделать следующий вывод: деталь вполне технологична нет необходимости вносить в ее конструкцию какие-либо изменения.
3. Анализ базового технологического процесса
В результате проведения анализа базового технологического процесса изготовления задвижки клиновой были выявлены следующие моменты:
– способ получения заготовки для заданного годового объема выпуска и материала детали является вполне рациональным;
– общая последовательность обработки детали включая все операции технологического процесса – механическая обработка технический контроль установлена обоснованно;
– одним из недостатков базового технологического процесса является использование неавтоматизированных станочных и контрольных приспособлений;
– сильная дифференциация операций приводит к низкой загрузке оборудования и как следствие снижению производительности;
– технологические возможности станков соответствуют параметрам выполняемых на них операций;
– в технологическом процессе используется оборудование как с ручным так и программным управлением что соответствует требованиям предъявляемым к серийному производству но определенная ограниченность возможностей оборудования приводит к излишним затратам времени и материала на формирование поверхности детали;
– применение токарных станков модели 1541 для обработки магистральных фланцев не позволяет обрабатывать деталь на высоких скоростях по причине высокого дисбаланса детали;
– применение устаревших режущих материалов таких как Т5К10 либо Т15К6 также не позволяет обрабатывать деталь на более высоких режимах.
Рис. 2.2. Обрабатываемые поверхности детали
Маршрутный технологический процесс (базовый вариант)
Краткое содержание операций
Обработка 1-го магистрального фланца.
Точить остаток прибыли; точить поверхность 1;
точить поверхность 4; расточить поверхность 5;
Токарно-карусельный станок 1541
Цилиндричес-кая поверхность 6 и торец7.
Обработка 2-го магистрального фланца.
Обработка аналогична операции № 010
Аналогично операции № 010
0 Комбинирован-ная с ЧПУ
Фрезеровать прибыль на фланце;
Фрезеровать торец 8;
Фрезеровать торец выточки 9
Зацентровать 14 отверстий 10;
Обрабатываю-щий центр ИР1250ПМФ4
Расточить начерно поверхность 1112
Расточить начисто поверхность 111213141516
Токарный станок 1516Ф3
Сверлить 20 отверстий 17 в первом и втором магистральном фланце;
Сверлильный станок 2М57
Сверлить 14 отверстий 18 зенковать фаску в отверсии 18 нарезать резьбу в отверстии 18
Зачистить заусенцы в 20 отверстиях в 1-ои и 2-ом фланцах и в 14 отверстиях в среднем фланце
Стол слесарный БМА 04-26
Промыть деталь и обдуть сжатым воздухом.
Моечная машина НКА 98-83
0 Испытание гидравлическое
Испытать деталь на прочность плотность.
Исправление дефектов литья мех. обработка (по необходимости)
Аналогично операции №050
Проверить размеры шероховатость поверхностей технические требования.
Основываясь на проведенном анализе ориентируясь на условия автоматизированного производства разработаны следующие предложения по изменению базового технологического процесса:
– заменить оборудование с ручным управлением (1541 2М57) на оборудование с программным управлением;
– старое оборудование с программным управлением (ИР-1250ПМФ4 1516Ф3) заменить на новое высокопроизводительное более экономичное;
– повысить концентрацию выполнения операций за счет применения станков типа «обрабатывающий центр»;
– проектируя механическую обработку учесть возможность применения так называемого высокоскоростного резания что позволит резко повысить производительность и уменьшить износ режущего инструмента;
– заменить старый инструмент - новым позволяющим достигать более высоких скоростей резания и лучшее качество обрабатываемой поверхности;
– учитывая возможности нового оборудования и повышение концентрации операций перераспределить припуски на механическую обработку сократив расход дорогостоящего материала детали.
Выбор вида исходной заготовки является ответственным этапом разработки технологического процесса так как коренным образом влияет на технологию механической обработки детали. Особенно важно правильно выбрать заготовку для условий серийного автоматизированного производства.
Чертежом задается материал изготовляемой детали – хладостойкая модифицированная литая сталь ХМ25Л. Данный сплав не пригоден для пластического деформирования но обладает хорошими литейными свойствами следовательно метод изготовления заготовки – литье.
В настоящее время литье является одним из наиболее распространенных методов формообразования. Литье обладает рядом преимуществ: изготовление отливок практически неограниченных габаритов и массы получение заготовок из сплавов не поддающихся пластической деформации и ряд других.
Способ изготовления определяется исходя из серийности производства массы объема выпуска и некоторых конструктивных и технологических особенностей детали. Учитывая довольно большие габаритные размеры детали соответственно большую массу относительно мягкие требования чертежа по шероховатости и точности поверхности в качестве способа изготовления предлагается использовать литье в песчано-глинистые формы [2].
Этот способ применяется как правило при изготовлении крупных отливок в условиях среднесерийного производства.
Технологичность конструкции литой заготовки
Применение в качестве материала заготовки хладостойкую модифицированную литую сталь ХМ25Л обеспечивает свободную усадку элементов отливки. Устранение усадочных дефектов достигается конструкцией с равномерной толщиной стенок.
Внешние контуры отливки представляют собой сочетание простых геометрических тел сочленяемых плавными переходами. Необрабатываемые поверхности отливки перпендикулярные к плоскости разъема имеют конструктивные уклоны что уже предусмотрено чертежом детали.
Деталь средних размеров по массе относится к отливкам II весовой группы.
Положение отливки в форме
Принимаем горизонтальное положение наибольших габаритных размеров отливки. В этом случае уменьшается неоднородность сплава при литье упрощается обеспечение твердения заготовки.
Определение параметров заготовки
Определим шероховатость поверхности заготовки по степени точности поверхности отливки. Наибольший габаритный размер для выбора – 960 мм; степень точности поверхности отливки – 16 шероховатость поверхности Ra= 63 мкм.
Класс точности размеров и масс – 12 ряд припусков – 5.
Составим сводную расчетную таблицу 2.3 размеров заготовки.
Размер по чертежу детали
Примечание: 1. Литейные радиусы 5 мм.
Литейные уклоны 2° в сторону увеличения тела детали.
В данном дипломном проекте исследовательская часть посвящена анализу действующей технологии литья корпуса задвижки и разработке метода её совершенствования на основе системы компьютерного моделирования SolidCast.
В результате работы были выявлены существенные недостатки действующей литниковой системы. Была сконструирована новая литниковая система с применением прогрессивных материалов таких как термоизолирующие вставки которые позволяют уменьшить размер прибылей. Таким образом стало возможным повысить выход годного с 516 % до 803 %.
Себестоимость заготовки
Себестоимость заготовки определяется по формуле:
КТ КС КВ КМ КП – коэффициенты зависящие соответственно от класса точности группы сложности массы марки материала и объема производства
МЗ МД - масса соответственно заготовки и детали:
Sотх - цена 1 т отходов Sотх = 298 руб.
Себестоимость заготовки при литье в песчано-глинистые формы:
КТ = 10 – литье в песчаные формы;
КС = 12 – для отливок 4 –й группы сложности;
КВ = 082 – для заготовок массой более 63 кг;
КМ = 126 – для заготовок из легированной стали;
КП = 11 – для девятой группы серийности.
Sзаг =(710101208212611)-(710-600)=3453 руб. (по ценам 1981г.)
Затраты на годовой выпуск заготовок: S1=3453*180=62154 руб.
Себестоимость заготовки при литье в металические формы:
КС = 118 – для отливок 4 –й группы сложности;
КВ = 081 – для заготовок массой более 63 кг;
КМ = 12 – для заготовок из легированной стали;
КП = 115 – для девятой группы серийности.
Sзаг =(7051011808112115)-(705-600)=2925 руб. (по ценам 1981г.)
Затраты на годовой выпуск заготовок: S1=2952*180=52650 руб.
Экономический эффект составил:
Э=S1-S2=62154-52650=9504 руб.
Окончательно выбираем способ изготовления заготовки: литье в песчано-глинястую форму.
Данный метод расчета себестоимости [9] является неточным т.к. он не учитывает некоторые другие факторы влияющие на себестоимость заготовки.
5. Разработка маршрутного технологического процесса
На основании анализа базового технологического процесса изготовления детали и выбора метода получения заготовки разработаем проектный вариант маршрутного технологического процесса обеспечивающий требования рабочего чертежа детали при одновременном снижении затрат на ее изготовление. В качестве основного технологического оборудования для проектного варианта маршрутного технологического процесса выбираем горизонтальный двухшпиндельный обрабатывающий центр Trevisan DS 900300C. Данный обрабатывающий центр имеется на предприятии «Икар» и предназначается для обработки сложных тяжёлых корпусных деталей. Все характеристики данного станка полностью удовлетворяют условиям обработки проектного варианта техпроцесса.
Основной отличительной особенностью горизонтально-расточных центров фирмы Trevisan является наличие двух независимых шпинделей расположенных в шпиндельном узле.
Базовый шпиндель предназначен для выполнения основных операций с использованием вращающегося инструмента: фрезерование плоскостей и уступов нарезание резьбы сверление и развертывание отверстий.
Токарный план-суппорт предназначен для выполнения любых операций в основе которых положена токарная обработка: подрезка торцов наружное и внутреннее точение обработка наружных и внутренних канавок нарезание резьбы резцом (в том числе конической) задняя подрезка фланцев точение фасок. Основным движением является вращение инструмента с одновременным программируемым перемещением вдоль оси «U» перпендикулярно к оси вращения план-суппорта. Перемещение вдоль оси «U» происходит за счет шариковинтовой пары по направляющим от независимого привода.
Преимуществом данного метода обработки по сравнению с использованием стандартного шпинделя является фиксированное положение заготовки в процессе обработки (и таким образом точность обработки не зависит от массы детали).
Данная система обработки обеспечивает стабильность процесса резания отсутствие инерционных сил возникающих при вращении заготовки и повышенную точность обработки в пределах +-0010мм.
Шпиндельный узел имеет главный двигатель который обеспечивает вращение базового шпинделя и план-суппорта.
Важным преимуществом данной конфигурации станков является минимизация использования специального инструмента (для обработки сложных внутренних поверхностей) за счёт программирования план-суппорта под различные виды обработки.
Применение этого станка с использованием прогрессивных режущих инструментов таких как резцы фрезы со сменными пластинами сверла со сменными пластинами фирмы Seco Walter позволит значительно сократить основное время обработки детали.
Рис 2.4.Горизонтальный двухшпиндельный обрабатывающий центр Trevisan модель DS 900300C
Технические характеристики станка
Программируемый план-суппорт
Перемещение по оси “U”
Стандартный расточной шпиндель
Палетная система с гидравлическим приводом
Габаритные размеры паллеты
Максимальная нагрузка на паллету
Точность позиционирования по осям
Точность повторяемости по осям
Максимальная длина инструмента
Максимальный вес инструмента
Время смены инструмента
Инструментальный магазин
поз. (спец. 80 поз.)
Энергетические требования станка
Установочная мощность станка
Габаритные размеры станка
Разрабатываемый маршрут можно условно представить в следующем виде:
Получение заготовки (отливка).
Механическая обработка.
Данный маршрутный технологический процесс был составлен на основе анализа существующих типовых маршрутных технологических процессов. В соответствии с чертежом детали разработаем технологический маршрут и оформлен в виде таблицы 2.6.
Рис. 2.5. Обрабатываемые поверхности детали
Технологический маршрут
Литье в песчаной форме
Точить поверхность 1;
точить поверхность 4;
точить поверхность 5;
Расточить начерно и начисто поверхности 67;
точить поверхности 8910;
Поворот паллеты на 180;
Аналогично обработать второй фланец
Поворот паллеты на 90;
Фрезерование поверхности 11;
Фрезерование торца выточки 12;
Сверлить 14 отверстий 13;
Зенковать фаску 14 в 14 отверстиях;;
Нарезать резьбу 15 в 14 отверстиях;
Сверлить 20 отверстий 16;
По трем горловинах в призмах
5 Испытание гидравличес-кое
6 Выбор технологических баз и последовательности технологических переходов
Выбор технологических баз и последовательности технологических переходов является ответственным этапом проектирования технологических процессов от которого в немалой степени зависят качество производительность и эффективность процесса изготовления машин.
На операции 010 заготовка базируется на три призмы по необработанным поверхностям и зажимом сверху. Такое базирование позволяет обработать всю деталь полностью за один установ. В начале обработки происходит обмер всей детали измерительной головкой ReniShaw то есть станок определяет ноль детали. Затем на первой позиции происходит обработка первого магистрального фланца а именно: наружные внутренние и торцевые поверхности фланца. После обработки фланца происходит поворот стола на 180º. На второй позиции происходит аналогичная обработка второго магистрального фланца. на третьей позиции обрабатывается средний фланец: сверлится 14 отверстий и нарезается резьба а также происходит обработка поверхностей находящихся в сопряжении с крышкой. На четвертой и пятой позиции происходит обработка крепежных отверстий первого и второго магистрального фланца.
7 Выбор и проектирование средств технологического оснащения
Режущий инструмент выбираем из литературы [1718] в соответствии с переходами. Для точения наружных цилиндрических поверхностей подрезки торцев выбираем державку типа S.
Для чернового растачивания внутренних цилиндрических поверхностей принимаем державку типа М. Для чистового растачивания внутренних цилиндрических поверхностей принимаем державку типа D.
Тип и размер пластины определяются выбором державки. Для выбора стружколома и сплава пластины воспользуемся системой Secolor. По этой системе выбираем для черновой обработки стружколом R5 а для чистовой обработки сружколом MF2.
При фрезеровании используем инструмент фирмы Walter.
Применяем фрезу F 4042.B27.080.Z06.16 с наружным диаметром 80 мм и числом режужих пластин равным 6.
При сверлении отверстий используем свёрла perfoMAX
8. Расчет припусков и операционных размеров
Расчет припусков аналитическим методом ведем согласно методике [13] для поверхностей 585H11 и 340H12
Технологический маршрут обработки поверхности 585H11 состоит из чернового и чистового точения.
Используя составленный маршрутный технологический процесс записываем технологические переходы для обрабатываемых поверхностей в порядке последовательности их выполнения (см. таблицу 2.7).
Минимальный припуск при обработке наружных и внутренних поверхностей (двусторонний припуск):
– суммарные отклонения расположения поверхности;
ei – погрешность установки заготовки при выполняемом переходе.
Значения Rz i-1 h i-1 определяем для каждого технологического перехода по соответствующим таблицам:
Отливка RZ =300 мкм h = 300 мкм.
Черновое точение RZ = 100 мкм h = 100 мкм
Чистовое точение RZ = 25 мкм h = 25 мкм
Суммарное значение пространственных погрешностей (отклонение от плоскостности) определяется:
где – отклонение от параллельности плоскости в мкм на 1 мм (08 мкм);
Δкор= – коробление корпусных деталей в мкм на 1 мм
L – длина плоскости (700мм).
Остаточные пространственные отклонения с достаточной для практических целей точностью определяем по эмпирической формуле:
Здесь КУ – коэффициент уточнения формы:
- после чернового точения КУ = 006;
Погрешность установки:
где Еб - погрешность базирования
Ез - погрешность закрепления
Рассчитанные значения Δ заносим в соответствующие графы табл. 2.7;
Погрешность установки на последующих переходах определяется аналогично.
Минимальный припуск:
- под черновое точение 585H11:
- под чистовое точение 585H11:
Максимальный расчетный размер для каждого технологического перехода:
Наименьшие предельные размеры вычисляем вычитанием допуска от округлённого наименьшего предельного размера.
- для чистового точения 585H11:
- для чернового точения 585H11:
Предельные значения припусков определяем как разность наибольших предельных размеров и - как разность наименьших предельных размеров предшествующего и выполняемого переходов:
(Tdз- Tdд) - (Zmax-Zmin) = (9000-440) - (15856-7296) = 0.
Аналогично определяются припуски и на размер 340H12.
Результаты расчета припусков приведены в таблицу 2.7 и таблицу 2.8.
Расчет припусков на обработку и предельных размеров по технологическим переходам 585H11
Растачивание черновое
Растачивание чистовое
Расчет припусков на обработку и предельных размеров по технологическим переходам 340H12
9. Расчет режимов резания
Выбор режимно-инструментального оснащения для токарного перехода
Расчёт режимов резания проведём по методике изложенной в каталоге Seco [17]
Разработаем технологическую операцию на токарную обработку (черновое и чистовое растачивание) с применением прогрессивного режимно-инструментального оснащения.
Обработка внутренней цилиндрической поверхности 585H11 с шероховатостью Ra=63 мкм и торца 340H11 с шероховатостью Ra=63 мкм.
Процедура пошагового выбора оптимальной сменной многогранной пластины:
Определить материал заготовки подлежащий обработке:
Материал заготовки: сталь ХМ25Л ТУ 41112-017-00218147-99
Группа материала заготовки – 3.
Выбрать способ обработки внутренних поверхностей заготовки:
Так как при обработке заготовки необходимо проточить внутренний диаметр отверстия выберем наиболее пригодную для этих операций схему обработки из представленных на стр.72 [17].
Далее по ссылке исходя из выбранной схемы переходим на стр.7879 [17] содержащую более детальную информацию о параметрах резцедержателя.
Выбираем резцедержатель:
- при черновом растачивании MCLNL 3232R19
- при чистовом растачивании DCLNL 3232R12
Определить тип сменной многогранной пластины
- при черновом растачивании CNMM 190616-R5
- при чистовом растачивании CNMG1204-MF2
Черновое растачивание:
Резцедержатель MCLNL 3232R19
Пластина CNMM 190616-R5 t=2-12мм; f=03-1мм
Чистовое растачивание:
Резцедержатель DCLNL 3232R12
Пластина CNMG1204-MF2 t=02-3мм; f=01-04мм
Выбрать режимы резания из технической информации:
- при черновом растачивании f=04 ммоб – по техническим данным ей соответствует скорость резания Vc=235 ммин.
- при чистовом растачивании f=01 ммоб – по техническим данным ей соответствует скорость резания Vc=320 ммин. Стр.36 [17]
Выбор режимов резания для токарного перехода
По исходным данным определяем
Уточняем скорость резания
Потребляемая мощность
– удельная сила резания;
Удельная сила резания:
Средняя толщина стружки:
Мощность которую обеспечивает станок:
где – мощность электродвигателя привода главного движения кВт;
Скорость снятия металла:
Черновое внутреннее точение
5; t=705мм; f=04мм; VC =235 ммин
Принимаем частоту вращения n=128 обмин
Уточняем скорость резания в связи с принятой частотой вращения шпинделя:
=1500 – сила резания;
Таким образом 1864 333 следовательно процесс резания может происходить.
Чистовое внутреннее точение
5; t=085мм; f=01мм; VC =320 ммин
Принимаем частоту вращения n=175 обмин
Таким образом 108 333 следовательно процесс резания может происходить.
Выбор режимно-инструментального оснащения для фрезерного перехода
Расчёт режимов резания проведём по методике изложенной в каталоге Walter select [18]
Разработаем технологическую операцию на фрезерование с применением прогрессивного режимно-инструментального оснащения.
Обработка уступа глубиной 15мм с шероховатостью Ra=63 мкм.
Процедура пошагового выбора инструментального оснащения
Группа материала заготовки – Р.
Выбрать условия обработки:
Для чернового фрезерования выбираем
Для чистового фрезерования выбираем WKP25.
Выступающая часть инструмента – короткая. Жесткость станка и системы зажима заготовки – хорошая.
Выбираем подходящий инструмент в соответствии с данной операцией и индивидуальными требованиями:
Выбираем тип обработки – в нашем случае необходима обработка уступов.
По типу обработки выбираем режущий инструмент –
Фреза F 4042.B27.080.Z06.16
Определяем оптимальную марку и геометрию сменной пластины соответствующего режущего инструмента. Для этого необходимо учитывать ранее выбранные условия обработки (Шаг 2) и материал обрабатываемой заготовки.
Для чернового фрезерования выбираем ADGT1204PER-D51
Для чистового фрезерования выбираем ADGT1204PER-D51 WKP25.
Выбираем из технической информации режимы резания.
По группе материала заготовки и выбранной для каждого типа пластины условия обработки выбираем скорости резания.
Для чернового фрезерования с условием обработки WKP35 Vc=220 ммин.
Для чистового фрезерования с условием обработки WKP25 выбираем Vc=260 ммин.
По группе материала заготовки типу обработки выбранному инструменту и максимальной глубине резания определяем скорости подачи.
Для чернового фрезерования:
Инструмент – Фреза F 4042.B27.080.Z06.16
Максимальная глубина резания t=740 мм.
Выбираем скорость подачи - fz=020 ммзуб.
Для чистового фрезерования:
Максимальная глубина резания t=020 мм.
Выбираем скорость подачи - fz=015 ммзуб.
Выбор режимов резания для фрезерного перехода
z - число зубьев фрезы
Скорость снятия металла:
Черновое фрезерование
ae=47 мм t=740 мм Vc=220 ммин fz=020 мм Dc=80 мм z=6
Количество оборотов:
Принимаем частоту вращения n=876 обмин
Потребляемая мощность:
Таким образом 1754 333 следовательно процесс резания может происходить.
Скорость съёма металла:
Чистовое фрезерование
ае=47 мм t=02 мм Vc=260 ммин fz=015 мм Dc=80 мм z=6
Количество оборотов:
Средняя толщина стружки:
Удельная сила резания:
Таким образом 051 333 следовательно процесс резания может происходить.
Скорость съёма металла:
Выбор инструментального оснащения для сверлильного перехода
Разработаем технологическую операцию на сверление с применением прогрессивного режимно-инструментального оснащения.
Обработка 40 отверстий 33мм и глубиной 40мм.
Определяем материал заготовки подлежащий обработке:
По диаметру и глубине отверстия выбираем тип сверла - выбираем свёрла SD502 – это свёрла со сменными пластинами. Данный тип сверла имеет диапазон диаметров от 15-59мм и глубину сверления порядка 2×. Сверло SD502-33-66-32R7 со сменными пластинами:
Центральная пластина SPGX 11Т3-C1 сплав T3000D
Периферийная пластина SCGX 09Т308-P1 сплав T3000D
Выбираем из технической информации режимы резания
По группе материала заготовки выбранной модели сверла и центральной и периферийной пластин и их сплавов выбираем скорость резания и подачу:
Vc=155 ммин f=018 ммоб.
Выбор режимов резания для сверлильного перехода (обработка отверстий 33мм)
Сверло SD502-33-66-32R7
Центральная пластина SPGX 11Т3-C1
Периферийная пластина SCGX 09Т308-P1
- диаметр сверления 33мм;
- глубина сверления 66мм;
- скорость резания Vc=125 ммин;
- подача f=018 ммоб.
Принимаем частоту вращения n=1500 обмин
Область поперечного сечения отверстия:
kc=2100 Нмм2 - удельная сила резания
k=90º sink=1 - для свёрл с пластинами. [17]
Сводная таблица режимов резания
Вид обработки инструмент
Глубина резания t мм
Скорость резания Vммин
Точить поверхность 710
Режущая пластина CNMG190608-M5
Точить торец магистрального фланца
Точить тыльную сторону торца
Режущая пластина CCMT 09T308-F1
Расточить поверхность 585H11 начерно
Режущая пластина CNMM 190608-R5
Точить торец 340H12 начерно
Расточить поверхность 585H11 начисто
Режущая пластина CNMG120408-MF2
Точить торец 340H12 начисто
Расточить поверхность 486
Режущая пластина DNMG150608-M5
Расточить поверхность 506
Режущая пластина DNMG150608-M5
Расточить поверхность 510H12
Расточить канавку 520±35
Режущая пластина VNMG 160404-M3
Фрезеровать торец выдерживая размер 570
Режущая пластина ADGT1204PER-D51 WKP35
Фрезеровать уступ в размер 650+07 240+07
Режущая пластина ADGT1204PER-D51 WKP25
Сверло SD-265-50-40R7
Центральная пластина SPGX 0903-C1 T3000D
Периферийная пластина SCGX 070308-P1
Фасочная пластина SD200-C45
Нарезать резьбу 14 отв. М30-7Н начерно
Фреза R396.19 -2522.3S-4003-3-065A
Пластина 396.19 -4003.ON1.0ISO
Нарезать резьбу 14 отв. М30-7Н начисто
Сверлить 2 группы по 20 отв. 33
Сверло SD502-33-66-40R7
10. Техническое нормирование операций
В серийном производстве определяется норма штучно-калькуляционного времени ТШ-К: [9]
гдеТШТ – норма штучного времени;
ТП-З – норма подготовительно-заключительного времени;
n – размер партии запуска.
где tО – основное время;
tВ – вспомогательное время;
tОБС – время на обслуживание рабочего места;
tЛП – время перерывов на отдых и личные потребности.
Основное время на каждый технологический переход определяем по известной формуле:
гдеL – длина обрабатываемой поверхности;
Vf – минутная подача;
Определим основное время на токарные переходы.
Основное время перехода по обработке 710 будет равным:
Основное время перехода по обработке торца магистрального фланца будет равным:
Основное время перехода по обработке тыльной стороны фланца будет равным:
Основное время чернового перехода по обработке 585H11 будет равным:
Основное время чистового перехода 585H11 будет равным:
Основное время перехода по обработке 486 будет равным:
Основное время перехода по обработке 506 будет равным:
Основное время перехода по обработке 510H12 будет равным:
Основное время перехода по обработке канавки 520 будет равным:
Определим основное время на фрезерные переходы.
Основное время перехода по обработке плоскости среднего фланца будет равным:
Основное время чернового перехода по обработке уступа среднего фланца будет равным:
Основное время чистового перехода по обработке уступа среднего фланца будет равным:
Определим основное время на сверлильные переходы.
Основное время перехода по обработке отверстия 33 будет равным:
Основное время перехода по обработке отверстия 265 будет равным:
Основное время перехода по обработке резьбы М30 будет равным:
Вспомогательное время:
гдеtВУ – время на установку и снятие заготовки; tВУ = 0 мин;(так как установка следующей детали происходит во время обработки предыдущей)
top – время на ориентацию заготовки в системе станка; top=35 мин;
tМВ – время на вспомогательные ходы ; tМВ = 346 мин;
tК – время на контроль; tК= 524 мин;
tин= 033 мин - время на смену инструмента; tин= 033 мин;
tпов= 016 мин - время поворота стола на 360º. tпов= 016 мин;
Время на вспомогательные ходы определяется по формуле:
гдеL – длина холостого хода;
tМВ1 =226 - время на вспомогательные ходы токарных переходов;
tМВ2 =018 - время на вспомогательные ходы фрезерных переходов;
tМВ3 =102 - время на вспомогательные ходы сверлильных переходов;
Тогда tВ = 346+12*033+7*016+2*008+524+15; tВ=172мин.
Время обслуживания рабочего места и время на личные потребности составляет 12 % от оперативного времени. Тогда:
Норма подготовительно-заключительного времени при обработке на станке Trevisan DS900: ТП-З = 28 мин.
ТП-З = ТП-З 1 + ТП-З 2 + ТП-З 3 мин (2.37)
где ТП-З 1 – время на ознакомление с документами осмотр заготовки инструктаж мастера установление рабочих органов станка установка перфоленты мин; ТП-З 1 =12 мин;
ТП-З 2 – время на получение наряда получение инструмента необходимого для наладки; ТП-З 2 =16 мин;
ТП-З 3 – время пробную обработку детали; ТП-З 3 =0 мин.
гдеN – годовой выпуск деталей N = 180;
Sn – число запусков в год (принимаем Sn = 12).
Тогда штучно-калькуляционное время:
Результаты нормирования операций сводим в таблицу 2.10.
Результаты нормирования операций
№ и наименование операции
11. Технико-экономическое обоснование проектного технологического процесса
Целесообразность разрабатываемого технологического процесса механической обработки деталей определяется на основе сравнительной экономической эффективности двух вариантов: базового и проектного [9].
В качестве базового варианта используем заводской технологический процесс изготовления деталей. При анализе сравниваем только те операции которые претерпели изменения при проектировании.
В соответствии с действующей методикой расчета экономической эффективности новой техники общим экономическим показателем является величина годовой экономии на приведенных затратах DСп определяемая из уравнения:
DСп = Сп – Сп (2.39)
где Сп и Сп – соответственно сумма годовых приведенных затрат базового и проектного вариантов при выполнении равных объемов работы р.
Сумму годовых приведенных затрат по каждому варианту можно рассчитать по формуле:
Сп = (Стi+Ен · Кi) (2.40)
Ен – нормативный коэффициент эффективности капитальных вложений Ен=015;
Кi – cумма годовых капитальных затрат на i-ой операции по вариантам р.
Определение капитальных затрат
Капитальные затраты включают вложения средств в оборудование производственные и служебно-бытовые помещения жилищное и культурно-бытовое строительство комплект управляющих программ. Однако для приближенных расчетов капитальных затрат на каждую операцию технологического процесса на ранней стадии технологической подготовки производства можно использовать упрощенную формулу:
Ki = Cpi · (Koi+Kздi+Kпуi) (2.41)
где Cpi – расчетное количество станков требуемых для изготовления годового выпуска деталей на i-ой операции по вариантам шт
где N – объем годового выпуска деталей оговоренный в задании на проектирование шт;
tш-к – штучно-калькуляционное время
Fo – эффективный годовой фонд работы станка(табличные данные);
Кв – средний коэффициент выполнения норм времени. При обработке на станках с ручным управлением Кв=1.2 а при использовании станков с ЧПУ Кв = 10;
Кзд – вложение в производственные помещения занимаемые оборудованиемр;
Кпуi – вложение средств в комплект управляющих программр.
Капитальные вложения в оборудование (Коi) состоят из капитальных вложений в технологическое оборудование (Ктi) подъемно-транспортное оборудование (Кптi) средства оснащения и контроля (Ккi):
Коi = Ктоi + Кптi + Ккi (2.43)
Капитальные вложения в технологическое оборудование для каждой операции определяются по формуле:
Ктоi = Цтоi · Кт · Ки (2.44)
где Цтоi – оптовая цена станка.
Кт – коэффициент учитывающий расходы на транспортировку и монтаж станка. Для расчетов рекомендуется принимать Кт = 1;
Ки – коэффициент инфляции учитывающий повышение тарифных ставок уровня рентабельности производства стоимости сырья материалов топлива энергии и т.д.
Суммарную величину капитальных вложений в подъемно-транспортное оборудование средства оснащения и контроля отнесенную к i-ой операции можно рассчитать используя формулу:
где - коэффициент сокращения количества станков на i – ой операции при переходе с базового варианта на проектный.
- суммарное принятое количество станков в базовом варианте на которых на d – операциях выполнялся тот же объем работы.
Стоимость производственного помещения занимаемого станков на i-ой операции (Кздi):
Кздi = Цпп · (S + Sу) · (2.47)
где Цпп – стоимость 1 м² производственной площади механического цехар
(S+Sy) – суммарная площадь занимаемая станком вместе с выносными устройствами (устройства ЧПУ электрошкаф и др.)
- коэффициент учитывающий дополнительную производственную площадь приходящуюся на единицу оборудования.
Дополнительная производственная площадь включает площадь между станками элементами здания площадь проездов и проходов для транспортирования материалов изделий и движений людей; площадь вспомогательных отделений цеха: заготовительного контрольного ремонтной базы складов и т.д.
Стоимость управляющих программ для операций выполняемых на станках с ЧПУ (Кпуi) зависит от конфигурации и размеров детали количества и сложности выполнения технологических переходов от типа и модели используемого металлообрабатывающего оборудования применяемой вычислительной техники метода программирования и других факторов.
Для универсальных станков с ручным управлением величина Кпу учитывает расходы по разработке пробной технологии выполнения анализируемой станочной операции. При укрупненных расчетах можно принять эту величину равной 25% стоимости управляющей программы регулирующей выполнение того же объема работы на оборудовании с ЧПУ.
Расчет технологической себестоимости
Величина годовой технологической себестоимости при использовании приближенного способа с достаточной для производственных расчетов точностью может быть определена по формуле:
где Счс Счн Счэл – нормативы затрат по заработной плате станочников наладчиков и электронщиков приходящихся на один час работы оборудования со всеми начислениями рч;
Сча Счр Счэл – нормативы затрат на амортизацию оборудования ремонт и электроэнергию приходящихся на один час работы станка рч;
Счп Счир – нормативы затрат на амортизацию и ремонт приспособлений и рабочего инструмента приходящихся на один час работы станка рч;
Собсл – годовые затраты на техническое обслуживание и ремонт устройств ЧПУ р;
Спп – годовые затраты на амортизацию и содержание производственных
В данном дипломном проекте представлено технико-экономическое обоснование вариантов механической обработки результаты расчета приведены в таблице 2.11 и таблице 2.12.
Сравнение вариантов технологического процесса
Сравнение вариантов технологического процесса производится с помощью программы «Станок» составленной по методическому указанию «Определение экономической эффективности технологических процессов» Орлов В.Н. Курган 1994г. данные заносятся в документ MS Access 2003 из которого программа берет сведения для расчета экономии.
а) годовой объем выпуска: 180 шт.;
Базовый технологический процесс
Технол. себестоимость руб.
Приведенные затраты руб.
Проектный технологический процесс:
Величина годовой экономии: 968766865 руб.
12 Описание и расчёт инструментальных наладок
В данном разделе наладка выполнена на комбинированную операцию (010). На наладке вычерчен эскиз детали с установочными и зажимными элементами приспособления в тонких линиях. Обрабатываемые поверхности вычерчены утолщенной линией. Показана траектория движения инструмента опорные точки.
Наладка представлена на четырех листах графической части: на первом листе показана обработка магистрального фланца: точение наружной цилиндрической поверхности торца и тыльной стороны фланца на втором листе обработка внутренних цилиндрических поверхностей магистрального фланца на третьем показана обработка центрального фланца: фрезерование плоскости уступа. На четвертом листе показано сверление отверстий магистрального и центрального фланца.
Координаты опорных точек наладки (лист 2)
0 Комбинированная с ЧПУ
ОЦ Trevisan DS900300C
Т05 Seco Резец S32T-PDUNL15 Режущая пластина DNMG150608-M5
Т06 Seco Резец MVJNR 2020K16 Режущая пластина VNMG 160404-M3
Поворот стола на 180 обработка второго фланца аналогично
Координаты опорных точек наладки (лист 3)
Т07: Фреза F 4042.B27.080.Z06.16 Режущая пластина ADGT1204PER-D51 WKP35
Т08: Фреза F 4042.B27.080.Z06.16 Режущая пластина ADGT1204PER-D51 WKP25
СОДЕРЖАНИЕ.doc
Технологический раздел: 12
1. Определение типа производства 12
2. Анализ конструкции детали на технологичность 14
3. Анализ базового технологического процесса 17
4. Выбор заготовки 20
5. Разработка маршрутного техпроцесса 24
6. Выбор технологических баз и последовательности технологических переходов 28
7. Выбор и проектирование средств технологического оснащения 29
8. Расчет припусков и операционных размеров 29
9. Расчет режимов резания 34
10. Техническое нормирование операций 44
11. Технико-экономическое обоснование проектного техпроцесса 47
12.Описание и расчет инструментальных наладок 51
Конструкторский раздел. 55
1. Проектирование станочного приспособления 55
Автоматизация производственных процессов 62
1 Проектирование загрузочного устройства 62
2 Автоматизация конструкторско-технологической подготовки в
литейном производстве 69
Исследовательский раздел 82
Производственные расчеты и разработка планировки 96
Безопасность и экологичность проекта 117
Организация производства 135
Организационно-экономический раздел 145
Список использованных источников 160
3.doc
1 Проектирование станочного приспособления
Данный раздел посвящен конструированию станочного приспособления для комбинированной операции №010.
Приспособление базируется по двум отверстиям и плоскости на паллете станка DS900300C. Собранное приспособление включающее паллету базирующие элементы и элементы зажимных устройств устанавливается на поворотный стол станка.
Станочное приспособление для закрепления обрабатываемой заготовки должно позволять вести обработку с одного установа поэтому учитывая сложную пространственную форму заготовки и схему базирования на данной операции приспособление должно быть спроектировано специально для данной заготовки.
Учитывая расположение основных баз заготовки примем схему базирования по трем горловинам на установочные опоры. Для закрепления детали используем винтовой зажим.
Расчет станочного приспособления на силу закрепления
Методика расчета и справочные данные приведены в [1516].
Рассчитаем силу закрепления в трех наиболее нагруженных переходах: точение цилиндрической поверхности 710фрезерование торца уступа сверление отверстий 33 в магистральном фланце.
Рис. 3.1. Схема закрепления детали
Сила зажима должна обеспечить надежное закрепление заготовки в приспособлении и не допускать сдвига поворота или вибрации заготовки при обработке. Определим две расчетные формулы силы закрепления:
- от тангенциальной составляющей силы резания стремящей повернуть заготовку вокруг точки О.
Тогда расчетная формула будет иметь вид:
W – сила закрепления Н;
К – коэффициент запаса который вводят в формулу при вычислении силы закрепления для надежного закрепления заготовки;
f1 f2 – коэффициенты трения в местах контакта заготовки с опорами и с зажимным механизмом соответственно.
Коэффициент запаса рассчитывают по формуле:
гдеКо=15 - коэффициент гарантированного запаса;
К1=12–коэффициент учитывающий увеличение сил резания из-за неровностей при черновой обработке;
К2=10–коэффициент учитывающий увеличение сил резания вследствие затупления режущего инструмента;
К3=12–коэффициент учитывающий увеличение сил резания при прерывистом резании;
К4=13–коэффициент характеризующий постоянство сил закрепления для немеханизированных приспособлений;
К5 = 10 – коэффициент характеризующий удобство зажима;
К = 15· 12· 10· 12 ·13 · 10=281
- от осевой составляющей силы резания стремящей сдвинуть заготовку.
- осевая сила резания;
N – нормальная сила реакции опоры Н;
R – сила реакции опоры от действия осевой силы Н;
f=022 – коэффициент трения Н;
Рис. 3.2. Схема закрепления детали
Определим две расчетные формулы силы закрепления:
Сверлильный переход.
Рис. 3.3. Схема закрепления детали
Рассмотрим вторую схему сверления отверстия 33.
Рис. 3.4. Схема закрепления детали
- от осевой составляющей силы резания стремящей повернуть заготовку вокруг точки А.
Для дальнейшего расчета принимаем наибольшую силу зажима W=28427Н.
Рассчитаем винтовой зажим.
Номинальный диаметр винта рассчитывается по формуле:
где - напряжение растяжения (сжатия) винта МПа.
Выбираем резьбу M27 мм; P =3 мм
По известным диаметру и шагу резьбы принимаем половину угла при вершине резьбы =30 и приведенный угол трения в резьбе φпр=640'.
Вычисляем угол подъема резьбы
Из условия отсутствия вмятин по таблице 5 [15] выбираем конец винта под пяту.
Определяем момент необходимый для закрепления заготоки.
Примем длину рукоятки 550 мм тогда необходимое усилие будет равно:
9.doc
Для определения перечисленных показателей используем методику изложенную в [7] а также данные полученные на базовом предприятии во время прохождения преддипломной практики.
Ожидаемые результаты проекта:
- размер необходимых инвестиций 794343 тыс. руб.
- срок окупаемости проекта 29 года.
- чистая дисконтированная стоимость 871168 тыс.руб.
Характеристика предприятия и описание продукции
Тип производства преобладающий на заводе – серийный. Соответственно оборудование применяемое на заводе универсальное и специализированное. На заводе широко применяется оборудование с числовым программным управлением: токарные станки с ЧПУ сверлильно-фрезерно-расточные станки с ЧПУ широкое применение на заводе нашли станки с ЧПУ типа “обрабатывающий центр”. Приспособления применяемые на станках токарной группы как правило универсальные на станка же фрезерных расточных сверлильных находят применение и специальные приспособления. Режущий инструмент применяемый в производстве в основной своей массе так же универсальный (резцы проходные расточные отрезные свёрла зенкеры зенковки развёртки различные виды фрез) и специализированный (червячные фрезы зуборезные гребёнки различные виды протяжек и т. п.).
Основные виды выпускаемой продукции являются:
- трубопроводная арматура;
- изготовление заготовок методом литья;
- ремонт трубопроводной арматуры.
Изделия подразделяются по назначению на:
- Общепромышленного назначения;
- специального назначения;
Проектируя новый участок предприятие стремится снизить затраты на материал энергоносители производственные площади заработную плату и повысить производительность тем самым снизить себестоимость продукции. Загрузка оборудования на участке представлена в таблице Технология изготовления рассматриваемых деталей представлена в приложениях (комплект технологической документации).
Более подробный анализ технологии изготовления подобных деталей приведен в разделе 2
Исходные данные для расчетов по проектируемому варианту берем из раздела 6 (номенклатура изготовляемых изделий на участке их годовые объемы выпуска количество потребного оборудования и т.д.) и представленного в приложении комплекта технологической документации а также используем данные полученные во время прохождения преддипломной практики на базовом предприятии. Годовой объем выпуска деталей обрабатываемых на участке – 2000Тип производства – мелкосерийный.
Занимаемая площадь базового участка S = 2400 м2 площадь проектного участка
S = 984 м2. Высвобождается - 1416 м2. Стоимость 1 м2 = 15 000 руб.
Экономия: 141615000=21240 тыс. руб.
Величина капитальных вложений по проектному варианту:
где - стоимость нового оборудования приспособлений и других средств;
- стоимость ликвидируемых в связи с внедрением нового технологического процесса существующих основных средств (учитывается как неамортизированная часть от первоначальной стоимости);
- выручка от реализации внедренного оборудования к концу службы его (ликвидационная стоимость).
Приобретаемое оборудование:
Расчёт капитальных вложений проекта сведён в таблицу 9.7.
Определение технологической себестоимости
Рассчитываются те статьи себестоимости продукции которые различаются в базовом и проектном вариантах.
Затраты на материал рассчитываются по формуле (9.2)
где - норма расхода материалов;
- цена материала за единицу веса:
для стали ХМ25Л руб.;
для стали 12Х18Н9ТЛ ;
- количество видов деталей;
- цена отходов: для стали руб.
- количество покупных изделий;
- цена покупных изделий
Затраты на энергию рассчитываются по формуле (9.3)
Где - продолжительность технологической операции мин;
- установленная (потребляемая) мощность или расход энергии;
- коэффициент использования мощности;
- коэффициент местных потерь;
- тариф на электроэнергию.
Затраты на заработную плату засчитываются по формуле (9.4)
где - часовая тарифная ставка на
- продолжительность технологической операции мин;
- коэффициент доплат к основной заработной плате;
- коэффициент отчислений на социальные нужды;
- коэффициент дополнительной заработной платы;
Расчет затрат на материал
Годовой объем выпуска
Вес стружки за год кг
Цена материала руб. кг
Годовая стоимость материала тыс.руб.
Годовая стоимость стружки тыс.руб.
Стоимость стружки руб.кг
Продолжение Таблицы 9.2
Расчёт затрат на электроэнергию
Затраты на энергию Зэ тыс. руб.
Расчет заработной платы
Час.тариф.ставка ai рубч
Затраты на зарплату Зэ тыс. руб.
Корпус КЗ13029-300.1
Затраты на текущий ремонт рассчитываются как 4% от стоимости оборудования.
Затраты на оборуд. тыс.руб.
Затраты на тек. рем. тыс.руб.
Затраты на амортизацию рассчитываются по формуле (9.5)
где - эффективный фонд работы оборудования ч;
- балансовая стоимость оборудования;
- норма амортизации;
- коэффициент загрузки оборудования;
- коэффициент выполнения норм.
Расчёт амортизационных отчислений
Балансовая стоимость тыс. руб.
Норма амортизации На
Фонд вр. раб. ст. Fэф
Затраты на аморт. Ззп тыс.руб.
Корпус задвижки ЗКС160-150
Расчёт технологической себестоимости
Производственное оборудование
Подъемно-транспортное оборудование
Приспособления и инструменты
Средство уборки стружки и инструментальный склад
Кпр=1009536+21417-23661=794343 тыс. руб.
Для данного дипломного проекта рекомендован сокращённый вариант финансового раздела и упрощённую схему прогнозирования денежных потоков учитывающих инвестиционную деятельность. Прогноз денежных потоков приведён в таблице 9.9.
Коэффициент дисконтирования для года t определяется по формуле (9.6)
где r = 012 - ставка дисконта
Коэффициент дисконтирования
По таблице 9.9.определяем период окупаемости проекта. Оценка эффективности проекта определяется по показателям чистой дисконтированной стоимости и сроку окупаемости проекта.
Прогноз денежных потоков для проекта участка
Инвестиции в проект участка
Приращения доходов и расходов
энергия электрическая
текущий ремонт оборудования
амортизация нового оборудования
Налог на прибыль (20%)
Приращение доходов от инвестиций
Коррекция денежных потоков
Амортизация нового оборудования
Продажа старого оборудования
Высвобождение площадей
Ликвидационная стоимость внедряемого оборудования
Чистый денежный поток
Чистая дисконтированная стоимость (ЧДС)
ЧДС нарастающим итогом
Срок окупаемости инвестиций лет
Проект считается целесообразным так как ЧДС>0 и составляет 871168 тыс. руб.
5.doc
Моделирование процесса литья корпуса задвижки в системе ”SolidCAST”
Основной деталью дипломного проекта является крупногабаритная корпусная деталь ”Корпус задвижки”. Способ изготовления заготовки для этой детали является литье в песчано-глинястую форму. Так как на производстве существует трудность в изготовлении таких отливок. Существует относительно большой процент брака низкий выход годного. Поэтому было принято решение исследовательский раздел посвятить анализу действующей литниковой системы и разработке рациональной системы на основе программного продукта SolidCAST которая позволит снизить трудности в изготовлении отливок.
Так как доля отливок в общей массе ряда машин например металлорежущих станков паровых турбин тракторов и т.д. превышает 50% поэтому литейное производство является основной заготовительной базой современного машиностроения.
Широкое применение способа изготовления заготовок литьём объясняется тем что литьем можно изготовлять заготовки сложной конфигурации которые другими методами (ковкой штамповкой сваркой) получать более трудоемко дорого или вообще невозможно.
Универсальность является основным достоинством литья.заготовок изготовляемых литьём может варьироваться от нескольких граммов до десятков и даже сотен тонн размеры заготовок также различны. Изготовляться они могут из самых разнообразных металлов и сплавов.
Также очень важным достоинством литья является возможность максимального приближения размеров получаемой отливки к размерам готовой детали в следствии чего значительно сокращаются отходы металла в стружку при механической обработке.
Отливки отвечающие требованиям эксплуатации обладают заданными механическими свойствами а в некоторых случаях и специальными свойствами в интервале рабочих температур. Чтобы получить отливку с требующимися эксплуатационными свойствами необходимо выбирать надлежащий сплав и технологию.
Важнейшая задача литейного производства - сокращение потерь брака. Эта задача заключается в выявлении анализе характера обнаруженных дефектов определении причин возникновения назначении и выполнении мероприятии по предотвращению дефектов.
Во время затвердевания отливки происходит ряд нежелательных процессов которые могут вызвать образование усадочных полостей так называемых усадочных раковин. Этот процесс называется усадкой. Отливки с усадочными раковинами в сечении в большинстве случаев непригодны для использования поэтому при их изготовлении пытаются вывести усадочную раковину в дополнительный объем называемый прибылью.
Рис.5.1. Внешний вид Рис. 5.2. Расположение прибылей
отливки с дефектом виде на литниковой модели
Плотное строение отливки может быть обеспечено лишь при осуществлении притока жидкости из прибыли. Естественно что сплав в ней должен затвердевать в последнюю очередь. Стремятся чтобы на прибыли уходило как можно меньше сплава и чтобы они действовали с должной эффективностью. Поэтому необходимо управлять температурными полями затвердевающей системы отливка-прибыль. В идеальном случае добавочный объем сплава полностью перемещается в затвердевающую отливку причем на затвердевающей отливке никакого избытка металла не остается. На практике нельзя рассчитывать на идеальную величину прибыли.
Для уменьшения расхода металла целесообразно применение тепловой защиты прибыли. Защита состоит из теплоизоляционной вставки которая замедляет затвердевание прибыли с наружной стороны.
Рис. 5.3. Теплоизолирующая вставка
Рис. 5.4. Виды изотермических оболочек
Применение теплоизолирующих вставок (обкладок) позволяет значительно повысить выход годного литья по сравнению с традиционными не утепленными прибылями.
Рис. 5.5. Использование теплоизолирующих вставок и фильтров в литниковых моделях
Еще одной из немаловажных проблем литейного производства являются неметаллические включения всегда присутствующие в расплавленном металле и вызывающие такие дефекты как шлаковые и газовые раковины газовую пористость что снижает качество отливок и их механические свойства. Последующие операции по удалению дефектов заметно усложняют и удорожают процессы обработки отливок. Образование неметаллических включений вызвано перемешиванием шлака с металлом при его плавке сливе в раздаточный ковш и заливке в литейную форму прочими факторами.
Применение керамических фильтров типа ФКТ существенно снижает образование перечисленных дефектов. Материал фильтров – модифицированный карбид титана.
Рис. 5.6. Керамические фильтры
Фильтры ФКТ выдерживают температуру до 2000° С не имеют ограничений по типу фильтруемых сплавов что является их преимуществом по сравнению с фильтрами из традиционных видов керамики (кварц корунд окись циркония и др.). Кроме снижения количества твёрдых и жидких неметаллических включений использование фильтров позволяет снизить содержание растворённого в металле кислорода и за счёт этого снизить газовую пористость отливок. Эта особенность присуща только данным фильтрам.
Анализ действующей технологии литья корпуса задвижки и разработка рекомендации по её совершенствованию на основе использования систем компьютерного моделирования.
Моделируемая технология: литьё в песчаные формы
Отливка: корпус задвижки
Материал: сталь ХМ25Л
Цель – убедиться что компьютерное моделирование позволяет спрогнозировать брак на этапе проектирования технологии и доработать технологию так чтобы свести брак к нулю либо до минимальных показателей.
Проведем анализ действующей технологии литья корпуса задвижки
По известному чертежу заготовки создаем 3D модель
Рис. 5.7. 3D модель корпуса задвижки
Создаем 3D модель исходной литниково-питающей системы предоставленной специалистами предприятия
Рис. 5.8. Общий вид литниково-питающей системы
Результаты анализа существующей технологии
Расчетный параметр: плотность металла в отливке
Результаты полученные в системе SOLIDCast после анализа предоставленной технологии показали наличие брака в отливках (зоны неплотного металла).
Рис. 5.9. Зоны неплотного металла в отливке
Данный результат говорит о возможном возникновении пористости на центральном и боковых фланцах отливки.
Основные характеристики литниковой модели:
Литье в песчано-глинистую форму
Всего залитого металла: 13554 кг
Зона подачи расплава: 164 кг
формовочной смеси: 21038 кг
Выход годного при этом составил 516 %
Делаем вывод что использования прибылей данной конфигурации для изготовления отливки корпуса задвижки неэффективно.
Проектирование литниковой системы с учетом анализа заводской технологии.
По результатам анализа существующей литниковой системы спроектируем новую систему. Для достижения наибольшего эффекта была изменена конфигурация прибылей место их расположения и применены теплоизолирующие вставки
Определение рационального расположенных прибылей.
Рис. 5.10. Наличие дефектных мест в отливке
Проанализировав дефектные места в отливке принимаем решение расположить прибыли на трех фланцах.
Шар имеет минимальную площадь поэтому его теплоотдача минимальна. Следовательно шар является наиболее оптимальной геометрической фигурой.
Прибыли на трех фланцах принимаем в виде шара.
Результаты анализа проектной технологии
Рис. 5.11. Этап моделирования
После анализа литниковой системы принимаем решение применить термоизоляционные вставки.
Рис. 5.12. Этап моделирования
На следующем этапе принято решение установить прибыли на торец центрального фланца и на центр отливки.
Рис. 5.13. Общий вид проектной литниковой системы
Рис. 5.14. Зоны неплотного металла в отливке.
Поскольку при данной литниковой системе дефектов в теле отливки не обнаружено то принимаем решение оставить данную литниковую систему и принять ее за проектный вариант.
Всего залитого металла 8401 кг
формовочной смеси: 25128 кг
термоизоляционных вставок 5106 кг
Выход годного составил 803 %
В результате изменения конфигурации прибылей и применения теплоизолирующих вставок вся усадка расположилась в пределах прибылей.
Выход годного составил 803 %.
Рис. 5.15. Чертеж проектной литниковой системы
Расчет годового экономического эффекта предлагаемой технологии
где Гэк- Годовой экономический эффект руб.
Оэк- Общая экономия руб.
Зобщ- Общие затраты руб.
где Эз- Экономия от разности затрат на основные материалы руб.
Эээ- Экономия эл.эн. топлива зарплаты руб.
Зобщ= Звст+ Зпес (5.3)
где Звст- Затраты на вставки теплоизолирующие
Зпес- Затраты на формовочную смесь
Эз=(Зомф- Зомп)* Твып (5.4)
где Зомф- Затраты на основной материал (с учетом ТЗР) при факт. ВГ руб.
Зомп- Затраты на основной материал (с учетом ТЗР) при план. ВГ руб.
Твып- Годовая программа выпуска тн
Зомп=Мзавп* ЗомфМзваф (5.5)
где Мзавп- Металлозавалка при плановом выходе годного тн
Мзваф- Металлозавалка при фактическом выходе годного тн
Мзавп =ТвыпПвг*100 (5.6)
Мзваф =ТвыпФвг*100 (5.7)
где Пвг- Планируемый выход годного %
Фвг- Фактический выход годного %
где М- Вес отливки кг
Т- Годовая программа выпуска шт.
Эээ=(Зэ+Зт+Зп)*Эг (5.9)
где Зэ- Затраты на электроэнергию руб.
Зт- Затраты на топливо руб.
Зп- Заработная плата ( с учетом доп. и соц. отчислений) руб.
Эг- Экономия годного литья тн
Эг=Эж* Пвг100 (5.10)
где Эж- Экономия жидкого металла тн
Эж=Мзваф – Мзавп (5.11)
Звст=Цвндс*Пвпг (5.12)
где Цвндс- Затраты на вставка теплоизол. цена без НДС руб
Пвпг- Затраты на вставка теплоизол. потребность на годовую программу
Зпес=Цпндс*Ппгп (5.13)
где Цпндс-. Затраты на формовочную смесь . цена без НДС руб
Ппгп- Затраты на формовочную смесь потребность на годовую программу
где Нв- Затраты на вставки теплоизолирующие норма на 1 тн годного литья
Ппгп =Нп*Твып (5.15)
где Нп- Затраты на формовочную смесь норма на 1 тн годного литья
Расчет ведется по программе в MS Excel
Результаты сведены в таблицу 5.1
Исходные данные по отливке
Годовая программа выпуска шт.
Фактический выход годного %
Планируемый выход годного %
Исходные данные для расчета экономии металла
Годовая программа выпуска тн
Металлозавалка при факт. ВГ тн
Металлозавалка при план. ВГ тн
Экономия жидкого металла тн
Экономия годного литья тн
Исходные данные по затратам на производство 1 тн литья
Затраты на основной материал (с учетом ТЗР) при факт. ВГ руб.
Затраты на эл.эн. руб.
Затраты на топливо руб.
Заработная плата ( с учетом доп. и соц. отчислений) руб.
Затраты на основной материал (с учетом ТЗР) при план. ВГ руб.
Расчет экономии металла в денежном выражении
Экономия от разности затрат на основные материалы руб.
Экономия эл.эн. топлива зарплаты руб.
Затраты на вставка теплоизол
Норма на 1 тн годного литья
Потребность на годовую программу
Затраты на формовочную смесь
Годовой экономический эффект руб.
ВВЕДЕНИЕ.doc
В настоящее время примерно 75% от общего объема машиностроительных изделий приходится на долю мелко- и среднесерийного производства. Такое положение обусловлено как непрерывным расширением области деятельности человека так и быстрым изменением спроса разных групп потребителей. Создаваемые машины характеризуются повышением их производительности быстроходности удельной мощности и надёжности при снижении весовых и габаритных показателей. Это влечёт за собой использование новых высокопрочных имеющих специальные свойства конструкционных материалов которые в большинстве случаев являются труднообрабатываемыми. Однако технический прогресс определяется не только улучшением конструкций машин но и непрерывным совершенствованием технологии их производства. Разработка технологических процессов изготовления деталей представляет собой один из ответственных этапов подготовки производства. Технологические процессы должны обеспечивать высокое качество изделий в соответствии с техническими условиями эксплуатации при минимальных затратах времени и средств.
На современном этапе развития машиностроения решающими средствами существенного повышения эффективности производства является автоматизация производственного процесса которая освобождает человека от ряда функций управления и одновременно повышает его роль как организатора и руководителя производства. Автоматизация означает применение качественно новых систем машин при которых без содействия человека но под его контролем выполняются функции обработки транспортирования обрабатываемых заготовок или инструментов контроля качества регулирования и управления производственным процессом. Необходимость автоматизации обусловлена прежде всего участием в современном производстве большого количества механизмов протеканием производственных процессов с большой скоростью и трудностью их регулирования человеком ввиду его ограниченных физиологических возможностей. Кроме того жёсткие требования к качеству продукции обуславливают повышение точностных параметров технологических процессов которые невозможно обеспечить без использования средств автоматизации.
В машиностроении автоматизация уже много лет является реальностью для крупносерийного и массового производства где широко используются полуавтоматы автоматы специальные и агрегатные станки автоматические и роторные линии а также другие средства жёсткой автоматизации производственных процессов. Однако увеличение номенклатуры выпускаемых изделий смещение производства в сторону мелко- и среднесерийного частые перестройки действующего производства связанные с переходом от одного вида продукции к другому не могут быть обеспечены традиционными средствами автоматизации.
Решение этой проблемы возможно через широкое внедрение в производство гибких автоматизированных систем представляющих качественно новый этап в комплексной автоматизации производственного процесса вследствие их создания на основе широкого применения программно управляемого технологического оборудования микропроцессорных устройств средств автоматизации проектно-конструкторских технологических и производственных работ. Основу автоматизации гибких автоматизированных производственных систем составляют программируемое технологическое оборудование управляющие вычислительные комплексы и методы групповой технологии что позволяет обеспечить переход на безлюдную или малолюдную технологию в условиях многономенклатурного производства.
Вопросы обеспечения высокого качества выпускаемой продукции и внедрения гибких автоматизированных производств тесно связаны между собой. Известно что изделия изготовленные на гибких производственных системах (ГПС) более качественны в силу многочисленных контрольных и диагностических устройств и машин управляющих процессом изготовления деталей.
Преобладающей тенденцией развития технологии в автоматизированном производстве является внедрение малоотходной и малооперационной технологии использование точных заготовок близких по форме и размерам к готовым изделиям что способствует экономии металла уменьшению объема механической обработки сокращению производственного цикла изготовления деталей и снижению себестоимости продукции в целом.
Заключение.doc
Для операций механической обработки были разработаны операционные технологические процессы в процессе работы над которыми осуществлялся выбор технологических баз последовательности технологических переходов режимов резания.
В разделе «Безопасность и экологичность проекта» были рассмотрены: безопасность труда на проектируемом участке обеспечение экологической безопасности проекта; безопасность проекта в чрезвычайных ситуациях.
В экономической части проанализированы необходимые затраты на инвестиции в проект участка и рассчитана возможная прибыль которая позволяет окупить проект участка за приемлемый срок.
В разделе автоматизации производства рассмотрен вопрос загрузки крупногабаритных корпусных деталей.
При разработке данного дипломного проекта широко использованы возможности современной компьютерной техники и применены различные технические и графические программные пакеты.
Исследовательский раздел посвящен моделированию процесса литья корпуса задвижки в системе “SolidCAST”.
На одну из операций технологического процесса разработана инструментная наладка проведен выбор инструментального оснащения проведено нормирование. Оценка экономической эффективности проектного участка также производились при помощи пакета Microsoft Excel. Все листы графической части разработаны с применением графического пакета "Компас 3D V9".
Diplom (титул).DOC
ФЕДЕРАЛЬНОЕ АГЕНТСТВО ПО ОБРАЗОВАНИЮ
КУРГАНСКИЙ ГОСУДАРСТВЕННЫЙ УНИВЕРСИТЕТ
Кафедра «Технология машиностроения»
Расчётно-пояснительная записка
Специальность - Технология машиностроения (151001)
Ученое звание ученая степень Фамилия И.О
Библиографический список.doc
Безопасность и экологичность проекта: методические указания к выполнению раздела «Безопасность и экологичность проекта» в дипломных проектах для специальностей 12.01 12.02. – Курган: КМИ 1993. – 33 с.
Выбор способа изготовления заготовок. Методические указания.– Курган: КМИ 1995.–42 с.
Денисенко Г.Ф. Охрана труда. – М: Высшая школа 1985.
Курсовое проектирование деталей машин. Под ред. С.А. Чернавский К.Н. Боков И.М. Чернин – М: Машиностроение 1988.–416 с.
Мельников Г.Н. Вороненко В.П. Проектирование механосборочных цехов. – М: Машиностроение 1990. – 351 с.
Методические указания по оформлению технологической документации при выполнении курсовых и дипломных проектов для студентов специальностей 12.01 07.01 21.03 12.02 15.02 15.06.–Курган: КМИ1992–36 с.
Методические указания для выполнения организационно–экономической части дипломного проекта специальности 120100 "Технология машиностроения". Курган1999.–c.14
Методические указания к выполнению дипломного проекта для студентов специальности 120100. Курган1996.–c.50
Мосталыгин Г.П. Орлов В.Н. Проектирование технологических процессов обработки заготовок. – Свердловск: УПИ. 1991.–112 с.
Новицкий Н.И. Пашуто В.П. Организация планирование и управление производством: Учеб. -метод. пособие Под ред. Н.И. Новицкого. – М.: Финансы и статистика 2006. – 576 с.
Охрана труда в машиностроении Под общ. ред. Е.Я. Юдина С.В. Белова – 2–е изд. – М: Машиностроение 1983.
Справочная книга по охране труда в машиностроении. Под общей ред. О.Н. Русака. – Л: Машиностроение 1989. – 540 с.
Справочник технолога–машиностроителя В 2–х т. Т1 Под ред. А.Г. Косиловой Р.К. Мещерекова – М: Машиностроение 1986.–496 с.
Справочник технолога–машиностроителя В 2–х т. Т2 Под ред. А.Г. Косиловой Р.К. Мещерекова – М: Машиностроение 1986.–496 с.
Станочные приспособления: Справочник. В 2–х т. Т.1 Под ред. Б.Н. Вардашкина В.В. Данилевского. – М: Машиностроение 1984. – 592 с.
Станочные приспособления: Справочник. В 2–х т. Т.2 Под ред. Б.Н. Вардашкина В.В. Данилевского. – М: Машиностроение 1984. – 656 с.
8.doc
Организация и планирование процессов создания и освоения новой техники
Сущность содержание и задачи подготовки производства
Создание новых видов продукции в машиностроении осуществляется в процессе подготовки производства. Подготовка производства протекает вне рамок производственного процесса. Задача подготовки производства состоит в том чтобы обеспечить необходимые условия для функционирования производственного процесса. Но в отличие от таких процессов подготовительной фазы как приобретение предметов труда наем рабочей силы и других повторяющихся систематически при каждом обороте производственных фондов подготовка производства стала единовременным актом осуществляемым при переходе предприятия на выпуск новой продукции. Процесс подготовки производства. Подготовка производства – это процесс непосредственного приложения труда коллектива работников в целях разработки и организации выпуска новых видов продукции или модернизации изготовляемых изделий. Процесс подготовки производства представляет собой особый вид деятельности совмещающий выработку научно-технической информации с се превращением в материальный объект - новую продукцию.По виду и характеру работ процессы подготовки производства подразделяются на исследовательские конструкторские технологические производственные и экономические. В основе выделения этих процессов лежит вид трудовой деятельности.Процессы научных исследований технических и организационных разработок и другие работы инженерного характера являются основными для подготовительной стадии. В них входят: проведение исследований инженерных расчетов проектирование конструкций технологических процессов форм и методов организации производства экспериментирование экономические расчеты и обоснования.Основными процессами подготовки производства являются и процессы изготовления и испытания макетов опытных образцов и серий машин. Они называются экспериментальными производственными процессами. По расположению во времени и пространстве процессы подготовки производства делятся на операции работы стадии фазы.Операция - первичное звено процесса создания новой техники. Она выполняется на одном рабочем месте одним исполнителем и состоит из ряда последовательных действий. Операции объединяются в работы.Работа - совокупность последовательно выполняемых операций которая характеризуется логической завершенностью и законченностью действий по выполнению определенной части процесса.Стадия - совокупность ряда работ связанных между собой единством содержания и методов выполнения обеспечивающая решение конкретной задачи подготовки производства.Фаза - комплекс стадий и работ характеризующий законченную часть процесса подготовки производства; связана с переходом объекта работ в новое качественное состояние.По отношении к объекту управления выделяются собственно процессы подготовки производства и процессы управления подготовкой производства.Содержание подготовки производства. Создание новой продукции в отраслях машиностроения осуществляется в определенной последовательности фаз единого процесса подготовки производства:- теоретические исследования имеющие фундаментальный и поисковый характер; прикладные исследования в процессе которых полученные на первом этапе знания находят практическое применение;- опытно-конструкторские работы в ходе выполнения которых полученные знания и выводы исследований реализуются в чертежах и образцах новых машин;- технологическое проектирование и проектно-организационные работы в процессе выполнения которых разрабатываются технологические методы изготовления и формы организации производства новых изделий;- техническое оснащение нового производства заключающееся в приобретении и изготовлении оборудования технологической оснастки и инструмента а также при необходимости - и в реконструкции предприятий и их подразделений;- освоение производства новой продукции когда созданные на предыдущих этапах конструкции изделий и методы их изготовления проверяются и внедряются в производство;
Основы организации подготовки производства
Главная задача подготовки производства - создание и организация выпуска новых изделий. Для ее решения необходимо четко сочетать все многообразные процессы подготовки производства рационально соединять личные и вещественные элементы процесса создания новой техники определять экономические отношения между участниками работ по подготовке производства. Возникает необходимость организовать процессы подготовки производства. Организация процессов создания новых видов продукции машиностроения охватывает проектирование осуществление на практике и совершенствование системы подготовки производства. Система подготовки производства - это объективно существующий комплекс материальных объектов коллективов людей и совокупность процессов научного технического производственного и экономического характера для разработки и организации выпуска новой или усовершенствованной продукции. Организация подготовки производства направлена на рациональное сочетание всех элементов процесса создания и освоения новой техники в пространстве и во времени установление необходимых связей и согласование действий участников этого процесса создание условий для повышения заинтересованности ученых инженеров производственников в ускоренной разработке и организации производства новой высокоэффективной техники.Учитывая особенности процессов создания новой техники необходимо при построении и совершенствовании системы подготовки производства руководствоваться рядом специфических принципов.Принцип комплексности предполагает необходимость проведения работ по подготовке производства по единому плану охватывающему все процессы - от научных исследований до освоения новой техники и учитывающему комплекс возникающих при этом технических организационных экономических и других проблем.
Принцип специализации требует чтобы за каждым подразделением предприятия закрепились такие виды деятельности по созданию и освоению новой техники которые отвечают характеру специализации этих подразделений.Принцип научно-технической и производственной интеграции рассматривается как совокупность условий обеспечивающих достижение единой и общей цели в результате деятельности определенного множества специализированных подразделений и исполнителей.Принцип комплектности документации и составных частей изделий требует одновременного выполнения комплекса работ к моменту времени когда дальнейшее их продолжение возможно только при наличии полного комплекта документации или составных частей изделий.Принцип непрерывности работ по созданию новой продукции требует ликвидации значительных перерывов во времени между фазами процесса подготовки а внутри их - между стадиями работами операциями.Принцип пропорциональности можно рассматривать как требование производственных возможностей (пропускной способности) всех подразделений объединения или предприятия занятых подготовкой производства.Принцип параллельности в организации работ по подготовке производства выражается в совмещении во времени различных фаз стадий работ.Обеспечение строгой последовательности работ и прямоточность. Соблюдая этот принцип необходимо чтобы разработка и освоение новой продукции осуществлялись с присущей только этому виду последовательностью работ. Прямоточность понимается как обеспечение кратчайшего маршрута движения технической документации и наименьшего пути проходимого новым изделием по всем стадиям его разработки и освоения.
Организационная структура системы подготовки производства
Создание рациональной организационной структуры системы подготовки производства базируется на использовании научных принципов его организации.Одним из основных направлений работы по формированию структуры системы подготовки производства является определение состава подразделений которые должны функционировать на предприятии в период разработки и освоения новой продукции.
Структура являясь формой системы определяется ее содержанием т.е. процессами протекающими в системе. Отсюда следует что разработка структуры органов подготовки производства должна базироваться на исследовании процессов создания и освоения новой продукции. Основным классификационным группам процессов создания новой продукции должны соответствовать структурные подразделения в которых и будут осуществляться эти процессы.
Основные группы процессов подготовки производства и соответствующие им структурные единицы
Процессы полготовки производства
Структурные единицы подразделения
Отдел изучения потребностей научно-исследовательские тематические отделы отдел (бюро) технико-экономических исследований.
Конструкторские тематические отделы технологическая служба отдел стандартизации и нормализации центральная заводская лаборатория отдел организации производства труда и управления.
Макетные мастерские экспериментальное производство цехи мелких серий производственные цехи
Служба научно-технической информации отдел кадров и подготовки кадров отдел материально-технического снабжения инструментальное хозяйство отделы главного механика и энергетика отдел и цех нестандартного оборудования служба управления качеством.
Бюро технической документации складское хозяйство транспортное хозяйство.
Вычислительный центр отдел управления разработками и подготовкой производства планово-экономический производственный отделы отдел труда и заработной платы бюро по рационализации.
Принцип строгой последовательности работ и прямоточности предполагает необходимость совершенствования пространственного расположения структурных единиц системы подготовки производства и обеспечение рациональных взаимосвязей между подразделениями предприятия. Не менее важна и сложна проблема установления взаимосвязей между подразделениями. Основные положения рационализации системы взаимосвязей между подразделениями участвующими в процессах подготовки производства базируются на следующих принципах: документ должен по возможности формироваться в одном подразделении; число согласовывающих и утверждающих инстанций должно быть сведено к минимуму; маршрут движения документа должен исключать возвраты петли и движение в направлении обратном ходу его маршрута. Использование принципа пропорциональности при организации подготовки производства требует обеспечения равенства производственных возможностей (пропускной способности мощностей) всех подразделений занятых созданием новых изделий. При этом должны учитываться ресурсы трех видов: люди (рабочие инженерно-технические и научные работники) основные фонды (площади производственное и научное оборудование) материальные ресурсы (материалы специальная литература нормативы и др.).При проектировании производственной структуры фактическая пропускная способность подразделений сопоставляется с плановой и выравнивается за счет перераспределения ресурсов и работ повышения производительности труда работников увеличения сменности работы оборудования.Структура органов подготовки производства во многом зависит от сложившейся системы подготовки. На предприятиях машиностроения функционируют три разновидности таких систем: централизованная при которой вся работа по конструированию технологическому и организационному проектированию осуществляется в заводских службах и других подразделениях; децентрализованная при которой основная тяжесть работы по технологической и организационной подготовке переносится на цеховые органы; смешанная когда работа по подготовке производства распределяется между центральными и цеховыми органами.На предприятиях машиностроения с массовым и крупносерийным типом производства подготовка производства новых изделий осуществляется как правило централизованно. На заводах серийного производства преобладает смешанная система подготовки а на предприятиях единичного и мелкосерийного типа - децентрализованная.
Организация подготовки производства во времени.
Время подготовки производства - это продолжительность пребывания средств производства разрабатывающих организаций и предприятий в подготовительной стадии производственного процесса. Оно складывается из рабочего периода и времени перерывов.Рабочим периодом называется время создания новых видов продукции в течение которого выполняются трудовые процессы. В ходе этих процессов осуществляются научные исследования инженерные разработки освоение новой продукции в производстве и эксплуатации.Время перерывов характеризует календарный период времени в течение которого тот или иной объект не испытывает на себе трудовых усилий. Время перерывов подразделяется на перерывы обусловленные режимом труда работающих; возникающие между фазами стадиями работами; обусловленные конструктивно-технологическими особенностями изделий и недостатками в организации и планировании производства.
Время подготовки производства счисляется в календарных днях или часах. Если время подготовки и перерывов исчисляется в календарном времени то рабочий период измеряется рабочим временем т.е. трудовыми затратами. Время подготовки производства исчисленное в единицах календарного времени представляется как цикл подготовки производства а в единицах рабочего времени как трудоемкость работ.
Цикл подготовки производства. Цикл подготовки производства конкретного изделия представляет собой календарный период времени в течение которого выполняется весь комплекс работ по разработке и освоению выпуска нового вида продукции. Цикл подготовки производства новой продукции включает в себя длительность всех этапов работ и время перерывов между ними.Процессы подготовки производства во времени могут быть организованы разными методами: последовательным выполнением операций работ и фаз без перерывов между ними; последовательным выполнением и наличием перерывов между операциями работами или фазами; путем организации параллельно-совмещенного выполнения операций работ и фаз подготовки производства. В зависимости от выбранного метода организации подготовки производства ее продолжительность будет различной.
Длительность цикла подготовки производства и освоения выпуска новых видов продукции несмотря на тенденцию к сокращению продолжает оставаться чрезвычайно высокой. На многих машиностроительных предприятиях период от начала разработки технического задания до выпуска изделий составляет в среднем 3-5 лет что в несколько раз превышает затраты времени на подготовку производства на аналогичных зарубежных предприятиях.Конкретные меры по сокращению времени подготовки производства предусматривают высокий уровень ее организации основанный на применении научных принципов. Сокращение времени подготовки производства является главной задачей организационной деятельности при создании новых видов продукции. Реализация этой задачи призвана обеспечить ускорение научно-технического прогресса во всех отраслях народного хозяйства.
Основными направлениями этой работы могут быть: сокращение времени рабочего периода за счет проведения мероприятий по сокращению трудовых затрат: сокращение времени перерывов в процессе подготовки производства внедрение параллельно-совмещенного метода организации работ.
Экономическое значение фактора времени при создании новой техники. Удлинение сроков подготовки производства и освоения выпуска новых видов продукции отрицательно влияет на темпы научно-технического прогресса и эффективность производства. Продолжительные сроки освоения выпуска новых эффективных машин замедляют поступление техники в соответствующие отрасли ведут к снижению темпов их технического перевооружения ухудшению показателей производительности труда и рентабельности производства. Кроме того нередки случаи когда новая техника устаревает еще до начала ее производства. Существенно ухудшаются при удлинении сроков подготовки производства технико-экономические показатели работы предприятий осваивающих новую технику. Отрицательные результаты длительных сроков создания и освоения новой техники проявляются в замедлении оборачиваемости оборотных средств вследствие роста объема незавершенного производства и увеличения запасов специального оборудования и оснащения; в снижении достигнутого уровня производительности труда что является следствием отвлечения трудовых ресурсов на создание новой техники без соответствующего увеличения выпуска продукции; в частичном повышении себестоимости продукции которое является следствием ухудшения использования оборудования и площадей повышенных затрат в сфере исследований и разработок роста доли накладных расходов и т.п.
В настоящее время для планирования и управления процессами создания и освоения новой техники широко применяются методы сетевого планирования и управления (СПУ) в основу которых положена модель описывающая объект управления в виде сетевого графика.
Сетевой график по сравнению с ленточным имеет ряд преимуществ в частности: на нём широко просматриваются взаимосвязи между работами; в график легко вводятся ранее не предусмотренные работы; на графике может быть легко выявлена технологическая последовательность работ которая определяет конечные сроки всей разработки – критический путь; по сетевому графику можно определять резервы времени работ не лежащих на критическом пути что позволяет наиболее рационально перераспределять наличные людские материальные и финансовые ресурсы; этот график даёт возможность оптимизировать план предстоящих работ.
Сетевой график представляет собой план работ по созданию сначала промежуточной продукции с определённой степенью готовности а в конце – полному его завершению т.е. достижению конечной цели.
Разработаем план по технологической подготовке производства на участке в виде сетевого графика на основе перечня работ и трудоёмкости их выполнения.
Методика расчета взята из [10].
Продолжительность выполнения каждой работы (i - j) определяется по формуле
– трудоёмкость работы (
– численность исполнителей работы (
– коэффициент выполнения норм времени (принимается равным 1).
Подставив в формулу (1) соответствующие данные по первой работе из табл.8.2 получим
Аналогично производим расчёты по всем остальным работам а результаты заносим в гр.6 табл.8.2.
Перечень работ по технологической подготовке производства на участке
Численность исполнителей чел.
Продолжительность выполнения работ недель
Разработка программы выполнения работ
Технологический анализ конструкций изделий
Разработка проектной технологической документации
Анализ загрузки производственных мощностей
Проектирование специального технологического оборудования
Разработка рабочей технологической документации и нормативов
Заказ покупка и доставка нового технологического оборудования
Разработка технологической части проекта
Разработка строительной документации на фундаменты
Изготовление специального технологического оборудования
Проектирование транспортно-складской системы
Разработка энергетической части проекта
Демонтаж старого оборудования
Изготовление фундаментов под оборудование
Изготовление транспортно-складской системы
Реконструкция инженерных сетей и вентиляции
Монтаж и отладка оборудования на участке
Монтаж и отладка транспортно-складской системы
Освоение производственных мощностей
Построение сетевого графика осуществляться на основании данных приведенных в гр.1 3 табл.8.1 (Рис.8.1).
Рис. 8.1 Сетевой график работ по технологической подготовке производства на участке
Кодирование сетевого графика.
Коды событий проставляются по возрастанию от i до j
Расчёт параметров сетевого графика.
Расчёт параметров сетевого графика
- расчет ранних сроков свершения событий ();
- расчет поздних сроков свершения событий ();
- резервов времени свершения событий ().
Для расчёта параметров сетевого графика (кружки) делятся на четыре сектора. В верхних секторах проставляют коды событий. В левые секторы в процессе расчёта вписывают наиболее ранние сроки свершения событий () а в правые – наиболее поздние сроки свершения событий (). В нижних секторах проставляют календарные даты или резервы событий ().
Расчёт наиболее ранних сроков свершения событий ведётся слева направо начиная с исходного события и заканчивая завершающим событием. Ранний срок свершения исходного события принимается равным нулю ( = 0). Ранний срок свершения j-го события определяется суммированием продолжительности работы ведущей к j-му событию и раннего срока предшествующего ему i-го события. Это при условии если в j-е событие входит одна работа а если j-му событию предшествует несколько работ то определяют ранние сроки выполнения каждой работы и из них выбирают максимальный по абсолютной величине и записывают в левом секторе события
Аналогично расчёт ведётся до завершающего события.
Расчёт наиболее поздних сроков свершения событий ведётся справа налево начиная с завершающего события и заканчивая исходным. Поздний срок свершения завершающего события принимается равным раннему сроку этого события. Это значение записывают в правый сектор события.
Наиболее поздний срок свершения i-го события определяется как разность между сроками последующего j-го события записанным в правом секторе и продолжительностью работы ведущей из i-го события к j-му событию. Это значение вписывают в правый сектор i-го события если из этого события выходит одна работа а если из i-го события выходит несколько работ то выбирают минимальное значение и записывают правый сектор i-го события это и будет поздним сроком свершения i-го события.
Аналогично расчёт ведётся до исходного события.
Расчёт резервов времени на свершение событий.
Резерв времени i-го события определяется непосредственно на сетевом графике вычитанием величины раннего срока свершения i-го события из величины позднего срока свершения i-го события
Рис.8.2 Сетевой график и график движения людских ресурсов
7.doc
Проблемы экологической безопасности сегодня как никогда стоят перед человечеством. Машиностроительная отрасль продолжает по инерции развиваться по принципу “максимальной эксплуатации” ресурсов природы. Актуальность темы исследования обусловлена современным состоянием природоохранной деятельности большинства предприятий машиностроения. Современная концепция устойчивого развития Российской Федерации и регионов ориентирована на снижение техногенного воздействия предприятий на окружающую среду при одновременном экономическом росте производства. Обеспечить такое развитие возможно при условии использования в производственном процессе современных малоотходных и ресурсосберегающих технологий.
На предыдущих этапах развития технологии наибольшее внимание при создании новой техники машин и механизмов уделялось таким показателям как производительность стоимость. Однако в настоящее время безопасность и экологичность обеспечение комфортных условий труда сведение к минимуму риска для рабочих становятся наиболее важными условиями. Соблюдение данных условий говорит о высоком техническом уровне предприятия определяющем его конкурентоспособность на мировом рынке.
Для обеспечения комфортных условий труда превращение всех производств в безопасные необходимо техническое перевооружение машиностроительных предприятий безопасной техникой.
Для обеспечения безопасности труда необходимо соблюдение:
- стандартов по безопасности труда;
- правил по технике безопасности;
- инструкций по охране труда.
Особое внимание обращается на соблюдение этих требований при создании новых видов оборудования разработке и реализации производственных процессов.
В государственных стандартах по безопасности труда сформулированы требования:
- к производственным процессам;
- промышленной продукции;
- средствам защиты рабочего персонала;
установлены нормы и требования на параметры характеризующие:
- запыленность и загазованность воздуха рабочей зоны;
- электро и взрывобезопасность;
- пожарную безопасность.
Безопасные и экологичные производственные процессы оборудование являются материальной основой обеспечения жизнедеятельности человека и одной из основных целей управления безопасностью труда и экологической безопасностью предприятия.
Анализ безопасности труда на проектируемом объекте
Существует большое число факторов которые характеризуют условия труда на рабочих местах производственных помещений. Эти факторы различны по своей природе формам проявления характеру действия на человека. При механической обработке металлов пластмасс и других материалов на металлорежущих станках возникает ряд физических химических психофизиологических и биологических опасных (ОФ) и вредных (ВФ) производственных факторов. Они подразделяются по своему действию на группы в соответствии с ГОСТ 12.01.003-74* .
В состав проектируемого участка входят:
Три обрабатывающих центра Trevisan отличающихся по номенклатуре обрабатываемых изделий
Токарный станок МК7702;
Фрезерный станок 5220Ф3;
Долбежный станок 7Д340;
Инструментальный склад;
Исходя из состава участка проанализируем его на наличие опасных и вредных факторов.
Опасные физические факторы:
- движущие части производственного оборудования;
- передвигающиеся изделия и заготовки;
- стружка обрабатываемых материалов;
- осколки инструментов;
- высокая температура поверхности обрабатываемых деталей и инструмента;
- повышенное напряжение в электроцепи или статического электричества при котором может произойти замыкание через тело человека
При обработке хрупких материалов (чугуна латуни бронзы графита карболита текстолита) на высоких скоростях резания стружка от станка разлетается на значительное расстояние (3-5 м).
Металлическая стружка особенно при точении вязких металлов имеющая высокую температуру (400-600 С) и большую кинетическую энергию представляет серьезную опасность не только для работающего на станке но и для лиц находящихся вблизи станка. Наиболее распространенными у станочников являются травмы глаз. Глаза повреждались отлетающей стружкой пылевыми частицами обрабатываемого материала осколками режущего инструмента и частицами абразива.
В связи с этими проблемами на проектируемом участке используется оборудование с закрытой зоной обработки. К тому же была спроектирована автоматизированная система удаления стружки которая представляет собой разводку труб по участку а рабочим агрегатом является вакуумная турбина. Вся стружка автоматически удаляется из зоны обработки и поступает на место складирования и дальнейшей переработки.
Физически вредные производственные факторы:
- повышенная запыленность и загазованность воздуха рабочей зоны
- высокий уровень шума и вибрации
- недостаточная освещенность рабочей зоны
- наличие прямой и отраженной блескости
- повышенная пульсация светового потока.
Запыленность воздушной среды в зоне дыхания станочников при точении фрезеровании и сверлении хрупких материалов может превышать предельно допустимые концентрации только при наличии средств защиты. При точении латуни и бронзы количество пыли в воздухе помещения относительно невелико (145-20 млкуб.м.). Однако некоторые сплавы (латунь ЛЦ40С и бронза Бр ОЦС 6-6-3) содержат свинец поэтому токсичность пыли образующейся при их точении следует оценивать с учетом количества в сплаве свинца приняв его предельно допустимую концентрацию. Размер пылевых частиц в зоне дыхания колеблется в широком диапазоне - от 2 до 60 мкм. При обработке латуни бронзы карболита графита на повышенных скоростях резания (V=300-400 ммин) количество пылевых частиц размером до 10 мкм составляет 50-60 % общего их числа.
При обработки полимерных материалов происходят механические и физико-химические изменения их структуры. При работе режущим тупым инструментом происходит интенсивное нагревание вследствие чего пыль и стружка превращаются в парообразное и газовое состояние а иногда возникает воспламенение материала например при обработке текстолита. Таким образом при обработке пластмасс в воздух рабочей зоны поступает сложная смесь паров газов и аэрозолей являющихся химическими вредными производственными факторами.
Продукты термоокислительной деструкции могут вызывать наркотическое действие изменения со стороны центральной нервной системы сосудистой системы кроветворных органов внутренних органов а также кожно-трофические нарушения. Аэрозоль нефтяных масел входящих в состав смазывающе-охлаждающей жидкости (СОЖ) может вызывать раздражение слизистых оболочек верхних дыхательных путей способствовать снижению иммунобиологической реактивности.
По степени поражения человека электрическим током проектируемый участок относится к помещениям с повышенной опасностью поскольку имеются в наличие три условия создающих повышенную опасность:
- токопроводящая металлическая технологическая пыль;
- токопроводящие железобетонные полы;
- возможность одновременного прикосновения человека к имеющим соединение с землей металлоконструкциям складов технологическому оборудованию и к металлическим корпусам электрооборудования.
Основные меры защиты от поражения током:
- обеспечение недоступности токоведущих частей находящихся под напряжением для случайного прикосновения (изоляция расположение их на недоступной высоте и т.д.);
- электрическое разделение сети на отдельные электрически н е связанные между собой участки с помощью специальных разделяющих трансформаторов;
- устранение опасности поражения при появлении напряжения на корпусах кожухах и других частях электрооборудования что достигается использованием двойной изоляции выравниванием потенциала защитным заземлением занулением защитным отключением и др.;
- организация безопасной эксплуатации электроустановок.
Микроклимат на рабочем месте в производственных помещениях определяется:
- температурой воздуха;
- относительной влажностью;
- скоростью движения воздуха;
- барометрическим давлением;
- интенсивностью теплового излучения от нагретых поверхностей.
Поскольку проектируемый участок не предполагает размещения моечно-сушильного агрегата то на микроклимат будут влиять только технологические процессы резания (нагрев использование СОЖ) а также нагрев электрооборудования.
Производственные помещения в которых осуществляются процессы обработки резанием должны соответствовать требованиям СНиП 2.09.02-85 а так же гигиеническим требованиям к микроклимату производственных помещений СанПиН 2.2.4.548-96. Все помещения должны быть оборудованы средствами пожаротушения по. СНиП 21-07-97 «пожарная безопасность зданий и сооружений».
Естественное и искусственное освещение производственных помещений должно соответствовать требованиям СНиП 23.05.95.
Уровень шума не должен превышать 80 дБА.
На случай пожара в цехе должны быть предусмотрены средства пожаротушения и эвакуационные выходы.
На участке должна быть естественная и общеобменная вентиляция.
К психофизиологическим вредным производственным факторам процессов обработки материалов можно отнести физические перенапряжение зрения монотонность труда перегрузки при установке закреплении и съеме крупногабаритных деталей но так как время обработки крупных деталей весьма велико то этот фактор не представляет опасности.
К биологическим факторам относятся болезнетворные микроорганизмы и бактерии проявляющиеся при работе с СОЖ.
Влияние цветового оформления интерьера на безопасность труда. Выбор сигнальных цветов и знаков безопасности для проектируемого участка оборудования
По мере технического прогресса в промышленности обусловленного применением новых видов энергии и материалов широким внедрением различных механизмов и машин в том числе автоматического действия непрерывным ростом скоростей давлений и мощностей возникла необходимость в целях предупреждения аварий и несчастных случаев в унификации и применении сигнальных цветов и знаков безопасности на промышленных предприятиях. Во многих странах в этой области проводятся психофизиологические светотехнические и инженерные исследования обосновываются и издаются соответствующие нормативы и рекомендации.
Цвет воспринимается не только зрением; в его восприятии участвуют другие чувства – осязание слух вкус; в связи с этим цвет способен активно влиять на нашу деятельность.
В науке различают прямое психофизиологическое воздействие цвета на человека вызывающее например чувство радости или печали создающее впечатление легкости или тяжести какого-либо предмета удаленности или близости его и вторичное воздействие связанное с ассоциациями.
Таким образом рациональное цветовое оформление производственных помещений (включая оборудование) в сочетании с соответствующим освещением позволяет достичь определенных психофизиологических эффектов например сгладить неприятное впечатление от неправильных пропорций помещения улучшить условия зрительной работы повысить безопасность труда и т.д.
Весьма важна психофизиологическая роль цвета в технике безопасности. Использование цвета в качестве закодированного носителя информации об опасности может явиться дополнительным средством предупреждения несчастных случаев и аварий.
На предприятиях значительное число причин несчастных случаев относят к ²неосторожности² и ²невнимательности² пострадавших или других лиц. При расследовании таких случаев необходимо в должной мере учитывать что ²неосторожность² и ²невнимательность² являются факторами психологического характера тесно связанными с такими человеческими категориями как ²настроение² ²восприятие² ²память² и что во многих случаях для профилактики необходимы различные организационно-технические мероприятия включая мероприятия по технической эстетике и инженерной психологии.
Для предупреждения таких случаев эффективным средством является цветовое оформление машин и производственных помещений рациональное применение сигнальных цветов и знаков безопасности.
Для мобильных машин при выборе сигнального цвета и определении порядка нанесения его на наружную поверхность необходимо учитывать данные о причинах аварий и несчастных случаев а также максимальную скорость движения машины и результаты исследований в области цвета.
Привлечение внимания к опасности соответствующим цветом должно найти широкое применение в стационарных машинах и различных технических сооружениях.
Во многих случаях может значительно повысить надежность работы человека сократить число неправильных ошибочных действий в опасной ситуации рациональное использование сигнальных цветов.
Сигнальные цвета разделяются на две группы: основные и вспомогательные.
К основным сигнальным цветам относятся красный желтый и зеленый. Выбор этих цветов вытекает из психофизиологических особенностей их восприятия заключающихся во-первых в способности вызывать определенные эмоции и во-вторых в различной скорости возбуждения этих реакций.
Красный цвет по данным физиологов повышает кровяное давление и действует возбуждающе. Он вызывает условный рефлекс направленный на самозащиту и поэтому используется для предупреждения о непосредственной опасности требующей немедленной реакции.
Желтый цвет не оказывающий столь интенсивного эмотивного воздействия как красный способствует сосредоточению внимания и поэтому используется для обозначения возможной опасности.
Зеленый цвет понижающий кровяное давление способствующий успокоению и традиционно ассоциирующийся с отсутствием опасности используется как сигнал безопасности.
В качестве вспомогательных сигнальных цветов приняты оранжевый занимающий по психофизиологическим особенностям восприятия промежуточное место между красным и желтым и синий цвет – для производственной информации не содержащей сведений об опасности или предосторожности.
Белый и черный цвета также отнесены к вспомогательным. Они предназначены для усиления контраста основных сигнальных цветов.
Для того чтобы сигнальные цвета были хорошо заметны они должны быть интенсивными т.е. насыщенными и в то же время достаточно светлыми. Для обеспечения максимальных цветовых различий между сигнальными цветами необходимо также чтобы они имели предельно достижимые различия по цветовому тону. Основные сигнальные цвета должны контрастировать с фоном и быть стойкими т.е. заметно не изменяться под влиянием различных факторов внешней среды.
Основные сигнальные цвета наносятся на элементы строительных конструкций и технологического оборудования на подъемно-транспортные устройства и другие сооружения в целях привлечения внимания к опасности или для сигнализации о безопасности. Основные сигнальные цвета могут наноситься на элементы строительных конструкций и оборудования полосами чередующиеся с полосами контрастирующего цвета.
Назначение и область применения основных и вспомогательных сигнальных цветов
Цвет для усиления значения основного цветового сигнала
Запрещение сигнализация о непосредственной опасности и указание устройства для прерывания или движения
Ограждаемые участки машин и знаки запрещающие различные действия. Кнопки и рычаги выключения и аварийные - ²Стоп²; лампы сигнализирующие о нарушении технологического процесса или условий безопасности; противопожарные устройства и т.п.
Предупреждение сигнализация о необходимости внимания осторожности действий
Наружные элементы оборудования не полностью ограждающие механизмы; сигнальные лампы предупреждающие о предстоящем переключении автоматических станков и линий; элементы внутрицеховых транспортных средств; строительные конструкции для сигнализации об опасности и т.п.
Разрешение сигнализацияо безопасности
Кнопки и рычаги ²Пуск²; пункты первой помощи аптечки; знаки разрешающие различные действия; таблички указывающие запасные и аварийные выходы и для другой информации направленной на обеспечение безопасности
Промежуточное значение между красным и желтым
Для повышения контраста между машинами и фоном. Допускается нанесение цвета на внутренние поверхности ограждающих устройств и ограждаемые участки машин и механизмов
Производственно-техническая информация
Оформление производственной информации не связанной с понятиями об опасности или предосторожности
Усиление контраста основных цветов безопасности; надписи на желтом белом и оранжевом фоне
Для обозначения направления движения для пояснительных надписей и символов а также для приборов контроля и т.п.
Усиление контраста основных цветов безопасности; надписи на красном зеленом синем и черном фоне
Для обозначения границ проходов проездов и рабочих мест а также направления движения и пояснительных надписей на знаках и т.п.
Имеет большое значение для предупреждения аварий и несчастных случаев применение знаков безопасности построенных на общих научно обоснованных принципах и рациональное их размещение в производственных помещениях и на оборудовании.
К общим принципам построения знаков безопасности отнесены следующие: геометрическая форма знака должна иметь определенное смысловое значение взаимосвязанное с символическим значением основных сигнальных цветов которыми покрывается поле знака. Количество форм должно быть минимальным не более трех-четырех; символы наносимые на знаки должны быть простыми всем понятными.
Знак безопасности – это геометрическая фигура определенного символического значения на цветном поле которой нанесен символ или текст поясняющие характер опасности инструктивные указания или информацию по безопасности. Такие знаки делятся на три основные группы: запрещающие предупреждающие инструктивные или предписывающие.
Особую группу составляют производственные знаки не содержащие понятий опасности или предосторожности.
Каждой группе знаков соответствуют определенная геометрическая форма и цвет. Знаки запрещающие имеют форму круга основной цвет поля красный. Знаки предупреждающие имеют форму равностороннего треугольника основной цвет поля желтый. Знаки инструктивные по безопасности имеют форму прямоугольника основной цвет поля зеленый. Знаки производственные не содержащие понятий опасности или предосторожности имеют форму прямоугольника основной цвет синий.
Символ на знаках безопасности – это простое и всем понятное изображение характера опасности мер предосторожности инструктивных указаний или информации по безопасности.
Основные группы знаков безопасности могут относиться к различным категориям опасностей. В связи с этим знаки безопасности для производственных условий целесообразно классифицировать по основным группам.
Знаки электробезопасности.
Знаки радиационной безопасности.
Знаки по предупреждению отравлений.
Знаки пожарной безопасности.
Знаки взрывобезопасности.
Знаки по предупреждению химических ожогов.
Знаки по предупреждению механических повреждений.
Знаки безопасности общего назначения и ограничения различных параметров.
Экологическая безопасность и охрана окружающей среды
Анализ экологичности производства
В данной дипломной работе производится разработка участка на котором предполагается размещение оборудования рабочих мест а также установки для утилизации отходов производства.
На окружающую среду и в целом на биосферу крайне отрицательно влияют промышленные загрязнения которые при определенных условиях могут трансформироваться в различные соединения и вызывать нежелательные воздействия на биосферу.
Жесткие выбросы в атмосферу представляют собой аэрозоли образованные мельчайшими капельками распыленных жидкостей (кислот масел СОЖ и т.п.). На участке должны быть предусмотрены средства очистки воздуха.
При обработке заготовок на металлорежущем оборудовании приходится использовать смазывающие охлаждающие жидкости в связи с этим принимаются специальные меры по хранению использованию и утилизации полностью переработанной СОЖ.
Выбор СОЖ необходимо осуществлять учитывая что следующие их виды имеют соответствующее разрешение Министерства здравоохранения страны в соответствии с ГОСТ 12.3.025 – 80:
- масляные СОЖ: МР-1;МР-2У; МР-3; МР-4; МР-63; ОСМ-3; ОСМ-5; ЛЗ-СОЖ 2СО; МЗ-СОЖ 2СИО; ЛЗ-1ПО; ЛЗ-1ПИО; ЛЗ-СОЖ 1Т.
- эмульсолы: укринол-1 (эмульсии 15; 33; 57; 10; 16%-ные); аквол-2 (эмульсии 3; 57; 10%-ные); ИХП-45Э (эмульсии 5; 10%-ные);
- синтетические и полусинтетические жидкости: аквол-10 (эмульсии 2; 52; 10%-ные); аквол-11 (эмульсии 3; 55; 10%-ные); НСК-5у (эмульсия 10%-ная).
Массовая доля вещества (%) в рабочих растворах СОЖ на водной основе не должна превышать:
Нафтеновых кислот в эмульсоле
Нафтеновых мыл в эмульсоле
Кальцинированной соды
Свободной гидроокиси натрия
хлор- серо- фосфоросодержащие присадки
Периодичность замены СОЖ должна устанавливаться по результатам контроля ее содержания но не реже одного раза в шесть месяцев при лезвийной обработке одного раза в месяц – при абразивной обработке для масляных СОЖ и одного раза в три месяца для водных СОЖ. Очистку емкостей для приготовления СОЖ трубопроводов и систем подачи следует проводить один раз в шесть месяцев для масляных и один раз в три месяца для водных СОЖ.
Хранить и транспортировать СОЖ необходимо в чистых стальных резервуарах цистернах бочках бидонах и банках а также в емкостях изготовленных из белой жести оцинкованного листа или пластмасс.
Отработанные СОЖ необходимо собирать в специальные емкости. Водную и масляную фазу можно использовать в качестве компонентов для приготовления эмульсий.
Еще одним не маловажным фактором загрязнения окружающей среды на проектируемом объекте является большое количество образования пыли при обработке металлов на металлорежущих станках. Чтобы устранить этот фактор на участках цехах а также во всех производственных помещениях устанавливаются вентиляционные системы большинство из которых обладает фильтрующим действием.
Также при обработке заготовок на станках образуется стружка утилизация которой тоже является проблемой производства.
Однако на данном участке спроектирована автоматизированная система удаления стружки. Также была спроектирована система по брикетированию стружки для дальнейшей переплавки либо продажи.
Производственные сточные воды используемые предприятием подлежат обязательной очистке от различных вредных примесей. Техническую воду необходимо охлаждать очищать от механических примесей масел разбавлять и затем возвращать в производство.
Промышленные твердые отходы должны собираться и отправляться для переработки.
Тепловое загрязнение биосферы предприятием на котором разрабатывается участок незначительно.
Шум вибрация ультразвук инфразвук должны быть в пределах нормы.
Очистка СОЖ и регенерация отработанных масел
В процессе эксплуатации масел в них накапливаются продукты окисления загрязнения и другие примеси которые резко снижают качество масел. Масла содержащие загрязняющие примеси не способны удовлетворять предъявляемым к ним требованиям и должны быть заменены свежими маслами. Отработанные масла собирают и подвергают регенерации с целью сохранения ценного сырья что является экономически выгодным.
В зависимости от процесса регенерации получают 2-3 фракции базовых масел из которых компаундированием и введением присадок могут быть приготовлены товарные масла (моторные трансмиссионные гидравлические СОЖ пластичные смазки). Средний выход регенерированного масла из отработанного содержащего около 2-4 % твердых загрязняющих примесей и воду до 10 % топлива составляет 70-85 % в зависимости от применяемого способа регенерации. Для восстановления отработанных масел применяются разнообразные технологические операции основанные на физических физико-химических и химических процессах они заключаются в обработке масла с целью удаления из него продуктов старения и загрязнения. В качестве технологических процессов обычно соблюдается следующая последовательность методов: механический для удаления из масла свободной воды и твердых загрязнений; теплофизический (выпаривание вакуумная перегонка); физико-химический (коагуляция адсорбция). Если их недостаточно используются химические способы регенерации масел связанные с применением более сложного оборудования и большими затратами.
Физические методы позволяют удалять из масел твердые частицы загрязнений микрокапли воды и частично – смолистые и коксообразные вещества а с мощью выпаривания – легкокипящие примеси. Масла обрабатываются в силовом поле с использованием гравитационных центробежных и реже электрических магнитных и вибрационных сил а также фильтрование водная промывка выпаривание и вакуумная дистилляция. К физическим методам очистки отработанных масел относятся также различные массообменные и теплообменные процессы которые применяются для удаления из масла продуктов окисления углеводородов воды и легкокипящих фракций.
Отстаивание является наиболее простым методом он основан на процессе естественного осаждения механических частиц и воды под действием гравитационных сил.
В зависимости от степени загрязнения масла и времени отведенного на очистку отстаивание применяется либо как самостоятельно либо как предварительный метод предшествующий фильтрации или центробежной очистке. Основным недостатком этого метода является большая продолжительность процесса оседания частиц до полной очистки удаление только наиболее крупных частиц размером 50-100мкм.
Фильтрация – процесс удаления частиц механических примесей и смолистых соединений путем пропускания масла через сетчатые или пористые перегородки фильтров. В качестве фильтрационных материалов используют металлические и пластмассовые сетки войлок ткани бумагу композиционные материалы и керамику. Существует следующий метод повышения качества очистки масел – увеличивается количество фильтров грубой очистки и вводится в технологический процесс вторая ступень – тонкая очистка масла.
Центробежная очистка осуществляется с помощью центрифуг и является наиболее эффективным и высокопроизводительным методом удаления механических примесей и воды. Этот метод основан на разделении различных фракций неоднородных смесей под действием центробежной силы. Применение центрифуг обеспечивает очистку масел от механических примесей до 0005% массы что соответствует 13 классу чистоты ГОСТ 17216-71 и обезвоживание до 06% массы.
Физико-химические методы нашли широкое применение к ним относятся коагуляция адсорбция и селективное растворение содержащихся в масле загрязнений разновидностью адсорбционной очистки является ионно-обменная очистка.
Коагуляция т. е укрупнение частиц загрязнений находящихся в масле в коллоидном или мелкодисперсном состоянии осуществляется с мощью специальных веществ – коагулятов к которым относятся электролиты неорганического и органического происхождения поверхностно активные вещества (ПАВ) не обладающие электролитическими свойствами коллоидные растворы ПАВ и гидрофильные высокомолекулярные соединения.
Процесс коагуляции зависит от количества вводимого коагулянта продолжительности его контакта с маслом температуры эффективности перемешивания и т.д. Продолжительность коагуляции загрязнений в отработанном масле составляет как правило 20-30 мин. после чего можно проводить очистку масла от укрупнившихся загрязнений с помощью отстаивания центробежной очистки или фильтрования.
Адсорбционная очистка отработанных масел заключается в использовании способности веществ служащих адсорбентами удерживать загрязняющие масло продукты на наружной поверхности гранул и на внутренней поверхности пронизывающих гранулы капилляров. В качестве адсорбентов применяют вещества природного происхождения (отбеливающие глины бокситы природные цеолиты) и полученные искусственным путем (силикагель окись алюминия алюмосиликатные соединения синтетические цеолиты).
Адсорбционная очистка может осуществляться контактным методом – масло перемешивается с измельченным адсорбентом перколяционным методом – очищаемое масло пропускается через адсорбент методом противотока – масло и адсорбент движутся навстречу друг другу. К недостаткам контактной очистки следует отнести необходимость утилизации большого количества адсорбента загрязняющего окружающую среду. При перколяционной очистке в качестве адсорбента чаще всего применяется силикагель что делает этот медом дорогостоящим. Наиболее перспективным методом является адсорбентная очистка масла в движущемся слое адсорбента при котором процесс протекает непрерывно без остановки для периодической замены регенерации или отфильтрования адсорбента однако применение этого метода связано с использованием довольно сложного оборудования что сдерживает его широкое распространение.
Ионно-обменная очистка основана на способности ионитов (ионно-обменных смол) задерживать загрязнения диссоциирующие в растворенном состоянии на ионы. Иониты представляют собой твердые гигроскопические гели получаемые путем полимеризации и поликонденсации органических веществ и не растворяющиеся в воде и углеводородах. Процесс очистки можно осуществить контактным методом при перемешивании отработанного масла с зернами ионита размером 03-20мм или преколяционным методом при пропускании масла через заполненную ионитом колонну. В результате ионообмена подвижные ионы в пространственной решетке ионита заменяются ионами загрязнений. Восстановление свойств ионитов осуществляется путем их промывки растворителем сушки и активации 5%-ным раствором едкого натра. Ионно-обменная очистка позволяет удалять из масла кислотные загрязнения но не обеспечивает задержки смолистых веществ.
Селективная очистка отработанных масел основана на избирательном растворении отдельных веществ загрязняющих масло: кислородных сернистых и азотных соединений а также при необходимости полициклических углеводородов с короткими боковыми цепями ухудшающих вязкостно-температурные свойства масел.
В качестве селективных растворителей применяются фурфурол фенол и его смесь с крезолом нитробензол различные спирты ацетон метил этиловый кетон и другие жидкости. Селективная очистка может проводиться в аппаратах типа "смеситель - отстойник" в сочетании с испарителями для отгона растворителя (ступенчатая экстракция) или в двух колоннах - экстракционной для удаления из масла загрязнений и ректификационной для отгона растворителя (непрерывная экстракция). Второй способ экономичнее и получил более широкое применение.
Разновидностью селективной очистки является обработка отработанного масла пропаном при которой углеводороды масла растворяются в пропане а асфальтосмолистые вещества находящиеся в масле в коллоидном состоянии выпадают в осадок.
Химические методы очистки основаны на взаимодействии веществ загрязняющих отработанные масла и вводимых в эти масла реагентов. При этом в результате химических реакций образуются соединения легко удаляемые из масла. К химическим методам очистки относятся кислотная и щелочная очистки окисление кислородом гидрогенизация а также осушка и очистка от загрязнений с мощью окислов карбидов и гидридов металлов. Наиболее часто используются:
Сернокислотная очистка
По числу установок и объему перерабатываемого сырья на первом месте в мире находятся процессы с применением серной кислоты. В результате сернокислотной очистки образуется большое количество кислого гудрона - трудно утилизируемого и экологически опасного отхода. Кроме того сернокислотная очистка не обеспечивает удаление из отработанных масел полициклических аренов и высокотоксичных соединений хлора.
Гидрогенизационные процессы все шире применяются при переработке отработанных масел. Это связано как с широкими возможностями получения высококачественных масел увеличения их выхода так и с большой экологической чистотой этого процесса по сравнению с сернокислотной и адсорбционной очистками.
Недостатки процесса гидроочистки - потребность в больших количествах водорода а порог экономически целесообразной производительности составляет 30-50 тыс. тгод. Установка с использованием гидроочистки масел как правило блокируется с соответствующим нефтеперерабатывающим производством имеющим излишек водорода и возможность его рециркуляции.
Процессы с применением натрия и его соединений
Для очистки отработанных масел от полициклических соединений (смолы) выскотоксичных соединений хлора продуктов окисления и присадок применяются процессы с использованием металлического натрия. При этом образуются полимеры и соли натрия с высокой температурой кипения что позволяет отогнать масло. Выход очищенного масла превышает 80 %. Процесс не требует давления и катализаторов не связан с выделением хлороводорода и сероводорода. Процесс Lubrex с использованием гидроксида и бикарбоната натрия (Швейцария) позволяет перерабатывать любые отработанные масла с выходом целевого продукта до 95 %.
Для регенерации отработанных масел применяются разнообразные аппараты и установки действие которых основано как правило на использовании сочетания методов (физических физико-химических и химических) что дает возможность регенерировать отработанные масла разных марок и с различной степенью снижения показателей качества.
Необходимо отметить что при регенерации масел возможно получать базовые масла по качеству идентичные свежим причем выход масла в зависимости от качества сырья составляет 80-90% таким образом базовые масла можно регенерировать еще по крайней мере два раза но это возможно реализовать при условии применения современных технологических процессов.
Одной из проблем резко снижающей экономическую эффективность утилизации отработанных масел являются большие расходы связанные с их сбором хранением и транспортировкой к месту переработки.
Безопасность проекта в чрезвычайных ситуациях
Чрезвычайная ситуация— это состояние при котором в результате возникновения источника ЧС на объекте определенной территории или акватории нарушаются нормальные условия жизни и деятельности людей возникает угроза их жизни и здоровью наносится ущерб имуществу населения народному хозяйству и природной среде.
Под источником чрезвычайных ситуаций понимают опасное природное явление аварию или опасное техногенное происшествие широко распространенные инфекционные болезни людей сельскохозяйственных животных и растений а также применение современных средств поражения в результате чего происходит или может произойти ЧС.
Все чрезвычайные ситуации (ЧС) классифицируются как конфликтные и бесконфликтные характеризующиеся скоростью и масштабами распространения
К конфликтным ситуациям относятся военные столкновения экономические кризисы социальные взрывы национальные и религиозные конфликты разгул уголовной преступности террористические акты идр.
К бесконфликтным ЧС относятся техногенные экологические и природные явления вызывающие ЧС.
По скорости распространения все ЧС делятся на внезапно возникшие быстро умеренно и медленно распространяющиеся.
По масштабам распространения все ЧС делятся на локальные местные территориальные региональные федеральные и трансграничные.
Чрезвычайные ситуации техногенного характера: транспортные аварии; пожары взрывы; внезапное обрушение зданий сооружений; аварии на электроэнергетических системах; аварии на очистных сооружениях.
Чрезвычайные ситуации природного характера: геофизические опасные явления; природные пожары.
Возможными источниками опасности на предприятии являются: технологическое оборудование машины механизмы аккумуляторы насосы технологический процесс шум вибрации запылённость.
Возможными ЧС антропогенного характера является истощение водных ресурсов загрязнение источников питьевой воды. Ухудшение ее качества представляет большую опасность для здоровья людей. Возможно заражение людей инфекционными заболеваниями.
Вероятные ЧС техногенного характера на проектируемом участке: транспортные аварии автомобильного транспорта электротранспорта; пожары вследствие неправильной эксплуатации оборудования не соблюдения правил техники безопасности и поломки оборудования.
Прогнозирование и оценка возможных последствий ЧС (стихийных бедствий техногенных аварий экологических бедствий) на проектируемом предприятии и разработка мероприятий по их предотвращению
Предприятия машиностроительной промышленности часто отличаются повышенной пожарной опасностью так как их характеризует сложность производственных установок значительное количество легковоспламеняющихся и горючих жидкостей сжиженных горючих газов твердых сгораемых материалов большое количество емкостей и аппаратов в которых находятся пожароопасные продукты под давлением; разветвленная сеть трубопроводов с запорно-пусковой и регулирующей арматурой; большая оснащенность электроустановками.
Данные показывают что основной причиной пожаров на машиностроительных предприятиях является нарушение технологического процесса. В известной мере это связано с большим разнообразием и сложностью технологических процессов. Они как правило помимо операций механической обработки материалов и изделий включают процессы очистки и обезжиривания сушки и окраски связанные с использованием веществ обладающих высокой пожарной опасностью. Сложность противопожарной защиты современных машиностроительных предприятий усугубляется их гигантскими размерами большой плотностью застройки увеличением вместимости товарно-материальных складов применением в строительстве облегченных конструкций из металла и полимерных материалов обладающих низкой огнестойкостью.
Пожарная безопасность может быть обеспечена мерами пожарной профилактики и активной пожарной защиты. Понятие пожарной профилактики включает комплекс мероприятий необходимых для предупреждения возникновения пожара или уменьшения его последствий. Под активной пожарной защитой понимаются меры обеспечивающие успешную борьбу с возникающими пожарами или взрывоопасной ситуацией.
Основы противопожарной защиты предприятий определены стандартами: ГОСТ 12.1.004-85 ²Пожарная безопасность. Общие требования². Этими стандартами возможная частота пожаров и взрывов допускается такой чтобы вероятность их возникновения в течение года не превышала 10-6 или чтобы вероятность воздействия опасных факторов на людей в течение года не превышала 10-6 на человека.
Для оценки пожарной опасности того или иного технологического процесса необходимо знать какие огнеопасные вещества или смеси используются или получаются или могут образовываться в процессе производства внутри технологических аппаратов при каких условиях и по каким причинам они могут оказаться вне их. Более высокую опасность имеют предприятия с наличием веществ способных образовывать взрывоопасные смеси с воздухом (горючие газы ЛВЖ горючие пылевидные материалы).
Проектирование и эксплуатация всех промышленных предприятий регламентируются "Строительными нормами и правилами" "Правилами устройства электроустановок" а также "Типовыми правилами пожарной безопасности для промышленных предприятий". В соответствии со СНиП 21-07-97 все производства делятся по пожарной взрывной и взрывопожарной опасности на следующие категории.
Категория А – взрывопожароопасные; к этой категории относятся производства в которых применяются горючие газы с нижним пределом воспламенения 10% и ниже жидкости с температурой вспышки до 28ºС включительно при условии что указанные газы и жидкости могут образовывать взрывоопасные смеси в объеме превышающем 5% объема помещения; вещества которые способны взрываться и гореть при взаимодействии с водой кислородом воздуха или друг с другом; такими производствами являются многие окрасочные цехи объекты с наличием сжиженных газов и т.д.
Категория Б – взрывопожароопасные; к этой категории относятся производства в которых используются горючие газы нижний предел воспламенения которых выше 10% а также жидкости с температурой вспышки выше 28 и 61ºС включительно или нагретые до температуры вспышки и выше; горючие пыли или волокна нижний концентрационный предел воспламенения которых 65 гм3 и ниже при условии что указанные газы жидкости и пыли могут образовывать взрывоопасные смеси в объеме превышающем 5% объема помещения; например производства с наличием аммиака с возможностью образования газовзвесей древесной или другой горючей пыли.
Категория В – пожароопасные; к этой категории относятся производства в которых применяются жидкости с температурой вспышки выше 61ºС. Горючие пыли или волокна нижний предел воспламенения которых более 65 гм3 твердые сгораемые вещества и материалы способные только гореть но не взрываться при контакте с воздухом водой или друг с другом.
Категория Г – к этой категории относятся производства в которых используются негорючие вещества и материалы в горячем раскаленном или расплавленном состоянии а также твердые вещества жидкости и газы которые сжигаются или утилизируются в качестве топлива.
Категория Д – это производства в которых обрабатываются негорючие вещества и материалы в холодном состоянии (цехи холодной обработки материалов и т.д.).
Категория Е – взрывоопасные; к этой категории относятся производства в которых применяются взрывоопасные вещества (горючие газы без жидкой фазы и взрывоопасные пыли) в таком количестве при котором могут образовываться взрывоопасные смеси в объеме превышающем 5% объема воздуха в помещении и в котором по условиям технологического процесса возможен только взрыв (без последующего горения); вещества способные взрываться (без последующего горения) при взаимодействие с водой кислородом воздуха или друг с другом.
Категория производства по пожарной опасности в значительной степени определяет требования к зданию его конструкциям и планировке организацию пожарной охраны и ее техническую оснащенность требования к режиму и эксплуатации.
Для облегчения определения категории промышленных предприятий по пожаровзрывоопасности изданы специальные указания – СН 463-74. Основу этого документа составляет методика определения максимально возможного объема взрывоопасной смеси при аварийном истечении горючих газов и ЛВЖ.
Расчетный объем такой смеси (м3) определяют по формуле.
где Е – количество вещества поступившего в помещение рассчитываемого по формуле.
где Еа – из аппарата
Еи – в результате испарения при проливе г;
с – нижний предел воспламенения гм3.
Если величина В не превышает 5% объема помещения то производство не является взрывоопасным.
В том случае когда величина В превышает 5% свободного объема П помещения а взрывоопасная среда создается при аварийном проливе ЛВЖ то дополнительно рассчитывают время Ти испарения вещества в количестве достаточном для образования взрывоопасной смеси в 5% объеме помещения:
где И – коэффициент учитывающий влияние скорости и температуры воздушного потока на испарение
Р – давление насыщенных паров жидкости при средней температуре жидкости Па;
М – молярная масса вещества;
Ф – поверхность испарения м2.
Если Ти1 ч то предприятие относится к взрывопожарным.
Мероприятия по пожарной профилактике разделяются на организационные технические режимные и эксплутационные.
Организационные мероприятия предусматривают правильную эксплуатацию машин и внутризаводского транспорта правильное содержание зданий территории противопожарный инструктаж рабочих и служащих и т.д.
К техническим мероприятиям относятся соблюдение противопожарных правил норм при проектировании зданий при устройстве электропроводов и оборудования отопления вентиляции освещения правильное размещение оборудования.
Мероприятия режимного характера – это запрещение курения в не установленных местах производства сварочных и других работ в пожароопасных помещениях и т.д.
Эксплутационными мероприятиями являются своевременные профилактические осмотры ремонты и испытания технологического оборудования.
Во взрывоопасных зонах разрешается применять только взрывозащищенное электрооборудование обеспечивающее безопасность его использования во взрывоопасных средах.
Во взрывоопасных помещениях и зонах наружных установок применяют специальное электроосветительное оборудование во взрывозащищенном исполнении. В помещениях класса В-I используют стационарные светильники во взрывонепроницаемом искробезопасном или специальном исполнении. В помещениях классов В-Iа и В-II – в любом взрывозащищенном исполнении. В помещениях классов В-Iб и В-IIа – пыленепроницаемые.
Применение автоматических средств обнаружения пожаров является одним из основных условий обеспечения пожарной безопасности в машиностроении так как позволяет оповестить дежурный персонал о пожаре и месте его возникновения.
АННОТАЦИЯ.doc
Разрабатывается маршрут технологического процесса получения деталей размера рассчитываются припуски операционные размеры и размеры заготовки.
Разрабатывается операционный технологический процесс детали представителя а именно выбираются базы и средства технологического оснащения. Определяется содержание последовательность выполнения технологических переходов и режимы резания. Определяются нормы технологического времени.
Сравниваются два технологических процесса обработки детали: в базовом технологическом процессе и в проектном технологическом процессе. Для комбинированной операции проектного технологического процесса строятся наладки.
Конструкторский раздел содержит описание работы и расчет установочного приспособления.
Дипломный проект содержит раздел по БЖД экономический раздел а также производственные расчеты и разработку планировки участка по изготовлению корпусов.
Графическая часть содержит 13 листов чертежей и спецификации.
-4 листа наладки на комбинированную операцию;
-2 листа сравнительной технологии базового технологического процесса и проектного;
-1 лист приспособления;
-2 листа исследовательского плана;
-2 листа автоматизации;
-1 лист планировки разрабатываемого участка;
-1 лист экономического обоснования проекта.
Данный проект содержит практические сведения по реальным процессам и оборудованию применяемом в машиностроении.
4.doc
1 Проектирование загрузочного устройства для крупногабаритных корпусных деталей
Данный раздел посвящен проектированию загрузочного устройства.
Загрузочное устройство – предназначено для захватывания предметов обработки и удержания их в процессе перемещения.
В зависимости от принципа действия загрузочные устройства делят на механические вакуумные и магнитные. По числу рабочих позиций загрузочные устройства всех типов разделяют на однопозиционные и многопозиционные. Захватные устройства изготавливают несменными и сменными.
Учитывая массу и габаритные размеры деталей выбрано загрузочное устройство механического типа. Захват детали производится по двум внутренним поверхностям магистральных фланцев и внутренней поверхности центрального фланца. Вид захвата определяется формой массой и свойствами захватываемого предмета.
К захватным устройствам предъявляются следующие требования:
Надежность захватывания и удержания объекта во время перемещения.
Недоступность повреждений предмета обработки.
Возможность установки детали на приспособление.
Так как заготовка характеризуется большими габаритными размерами массой а также отсутствие необходимости в быстрой смене заготовок на паллете станка выбираем однопозиционное загрузочное устройство для корпусных изделий.
Три зажимные губки свободно установлены на своих осях. На цилиндрической поверхности губки выполнены червячные зубчатые секторы входящие попарно в зацепление с червяком. Крутящий момент червячному валу через муфту передает мотор-редуктор установленный на раме загрузочного устройства.
Расчет ЗУ включает: нахождение крутящего момента действующего на червячное колесо геометрический и силовой расчет червячной передачи определение момента на червяном валу и выбор мотор-редуктора. Далее по общей массе заготовки и загрузочного устройства определяется требуемая таль к консольному крану.
Объект непосредственно поддерживается губками силы трения практически не участвуют в удержании. По необходимой скорости закрепления губками заготовки примем число оборотов червячного колеса равным 3 обмин.
Рассчитаем крутящий момент на червячном колесе.
Рис 4.1 Схема действия сил
Составляем уравнение моментов относительно точки А:
Произведем геометрический и силовой расчет червячной передачи по справочной литературе [4].
Крутящий момент на червячном колесе 159 Нм;
Число оборотов на червячном колесе 3 обмин;
Число оборотов червяка 24 обмин;
По справочной литературе [4] определяем основные параметры червячной передачи:
Межосевое расстояние 80мм;
Коэффициент диаметра червяка 8;
Число витков червяка 4;
Число зубьев червячного колеса 32;
Остальные параметры червячной передачи определяем по программе Компас-Shaft-2D.
Рис 4.2 Ввод данных для геометрического расчета
Рис 4.3 Ввод данных для расчета на прочность
Результаты расчета сведем в две таблицы.
Геометрический расчет цилиндрической червячной передачи
Наименование параметра
Число витков (число зубьев)
Коэффициент диаметра червяка
Вид обработки червяка
Угол профиля исходного контура
Коэффициент высоты головки
Коэффициент расчетной толщины
Коэффициент радиуса кривизны переходной кривой
Коэффициент радиального зазора у поверхности переходной кривой
Коэффициент смещения червяка
Определяемые параметры
Межосевое расстояние мм
Делительный диаметр мм
Начальный диаметр червяка мм
Делительный угол подъема
Начальный угол подъема
Основной угол подъема
Основной диаметр червяка мм
Высота витка червяка мм
Высота головки витка червяка мм
Наибольший диаметр червячного колеса мм
Длина нарезанной части червяка мм
Ширина венца червячного колеса мм
Радиус кривизны переходной кривой червяка мм
Радиус выемки поверхности вершин зубьев червячного колеса мм
Радиус выемки впадин червячного колеса мм
Угол скашивания торцев зубчатого венца червячного колеса
Контролируемые и измерительные параметры
Расчетный шаг червяка мм
Делительная толщина по хорде витка червяка мм
Высота до хорды витка мм
Диаметр измерительного ролика мм
Размер червяка по роликам мм
Отсутствие подрезания зубьев червячного колеса
Отсутствие заострения зубьев червячного колеса
Коэффициент перекрытия
Наименьшая суммарная длина контактных линий
Расчет на прочность при действии максимальной нагрузки
Твердость поверхности червяка HRC
Исходная расчетная нагрузка Н*м
Число оборотов на червяке обмин
Определяемые параметры
Скорость скольжения мс
Расчет на контактную прочность
Расчетное контактное напряжение МПа
Допускаемое контактное напряжение МПа
Коэффициент запаса по контакту
Расчет на прочность при изгибе
Расчетное напряжение изгиба МПа
Допускаемое напряжение изгиба МПа
Коэффициент запаса по напряжениям изгиба
Определим силы в зацеплении червячной передачи:
Окружная сила червячного колеса (Ft2) и осевая сила червяка (Fa1)
Окружная сила червяка (Ft1) и осевая сила червячного колеса (Fa2)
Радиальная сила червяка (Fr1) и червячного колеса (Fr2)
Т2=15900 Нмм – крутящий момент;
d2=128 мм - делительный диаметр червячного колеса;
γ=26 - делительный угол подъема;
Определим крутящий момент червяка
По крутящему моменту и числу оборотов на червяке выбираем цилиндрический мотор-редуктор SF8156. [19 ]
Характеристика мотор-редуктора
Номинальная частота вращения вых. вала обмин
Номинальный крутящий момент на выходном валу Нм
По суммарной массе заготовки и загрузочного устройства выбираем таль электрическую ТЭ 200-5110 со следующими характеристиками:
Скорость подъема ммин (мс)
Скорость передвижения ммин (мс)
2.Автоматизация конструкторско-технологической подготовки в литейном производстве
В условиях рыночной экономики каждое промышленное предприятие основным источником существования которого являются доходы от реализации выпускаемой продукции способно обеспечить успешное ведение бизнеса только при условии разработки и производства высококачественной продукции в кратчайшие сроки и с минимальной себестоимостью.
Трудность состоит в том что необходимо постоянно совершенствовать производственные технологии т.е. совокупности способов и технических средств обеспечения процессов разработки и производства продукции. Опыт развития всех отраслей мировой промышленности неопровержимо доказывает что в современных условиях только таким способом можно обеспечить экономическую стабильность предприятия и как следствие на серьезной основе строить перспективные планы развития.
Перспективные промышленные технологии для предприятий отечественной промышленности является одним из важнейших факторов рыночной выживаемости. Благодаря внедрению современных информационных технологий в промышленность достигается качественно новый уровень производства и производственных отношений:
- существенно сокращаются сроки разработки проектирования подготовки
производства и выпуска изделий;
- существенно сокращается трудоемкость материалоемкость энергоемкость
и другие виды ресурсов необходимых для разработки и производства изделий;
- расширяется ассортимент выпускаемой продукции;
- повышается уровень сложности и качество выпускаемой продукции;
- повышается фактор творчества в работе и квалификация персонала.
Математическое моделирование илитейные технологии
Вразличных областях науки итехники широко используется метод математического моделирования. Этот метод включает всебя разработку физических иматематических моделей численных методов ипрограммного обеспечения проведение численного эксперимента спривлечением средств вычислительной техники (его результаты анализируются ииспользуются впрактических целях). Втехнике итехнологии преимущества метода математического моделирования очевидны: оптимизация проектирования сокращение затрат на отработку повышение качества продукции уменьшение эксплуатационных расходов ит.д. Математическое моделирование существенно преобразует также сам характер научных исследований устанавливая новые формы взаимосвязи между экспериментальными иматематическими методами.
Применение математического моделирования влитейной промышленности привело кпоявлению большого числа программных пакетов спомощью которых более или менее успешно решаются задачи скоторыми литейщики сталкиваются вповседневной практике.
Воснове математической модели литейных процессов лежат уравнения тепломассопереноса: уравнения теплопроводности Навье-Стокса диффузии кинетические уравнения фазовых превращений ит.д. Расчетная область включает не только объем занимаемый расплавом но также иформообразующую среду сразличными граничными иначальными условиями.
Программы для моделирования литейных процессов распространенные внастоящее время восновном различаются степенью полноты учитываемых при моделировании факторов. Второе различие связано сметодами получения ирешения разностных уравнений: уравнения тепломассопереноса могут быть записаны вдифференциальном или интегральном виде.
Метод конечных разностей(МКР)
Базируется на уравнениях вдифференциальной форме при этом дифференциальные операторы заменяются конечно-разностными соотношениями различной степени точности. Как правило они строятся на ортогональных сетках (прямоугольной цилиндрической ит.д.). Это позволяет факторизовать операторы исвести решение многомерной задачи кпоследовательности одномерных задач азначит намного упростить иускорить решение общей системы уравнений. Кнедостаткам следует отнести плохую аппроксимацию границ сложных областей что не слишком принципиально для уравнений теплопроводности но довольно существенно для уравнений гидродинамики. Метод также плохо работает вслучае тонкостенных отливок когда толщина стенок становится сравнимой сшагом сетки.
Метод конечных элементов(МКЭ) иметод конечного объема(МКО)
Базируются на уравнениях тепломассопереноса винтегральном виде. Область вкоторой решаются уравнения разбивается на элементы внутри которых строятся аппроксиманты функций на основе системы базисных функций определенных на элементе. «Проектируя» интегральные уравнения на эти базисы получают систему разностных уравнений. Эта система значительно сложнее принятой вМКР ее решение требует больших ресурсов памяти инемалого времени. Преимущество МКЭ - хорошая аппроксимация границы недостатки - необходимость добротного генератора конечных элементов сложность уравнений невозможность факторизации.
МодификацииМКО пытаются соединить всебе простоту ифакторизациюМКР ихорошую аппроксимацию границ между различными материалами иразличными фазами.
Наиболее наглядно разница между МКЭ и МКР видна по способу дискретизации геометрии. При МКЭ расчетная геометрия (КЭ-сетка) представляет из себя набор относительно крупных неправильных треугольных пирамид непрерывно без пересечений заполняющих расчетную область произвольной конфигурации - собственно геометрию моделируемого объекта. Применительно к ЛП это будет геометрия отливки и формы. (На самом деле вид конечного элемента может быть любым в том числе и с криволинейными гранями однако чаще всего используются тетраэдальные четырех узловые элементы.) При МКР расчетная геометрия чаще всего представляет из себя набор относительно мелких параллелепипедов полученных наложением непрерывной прямоугольной ортогональной сетки на прямоугольную расчетную область в которую вписана геометрия отливки и формы. (В общей разностной постановке конфигурация ячейки может быть и не параллелепипедом а например в 2D правильным шестиугольником но неортогональные сетки практически не применяются.) На рис.4.4 показан пример элементных и разностных разбивок для цилиндра.
Рис.4.4. Разбивки цилиндра при МКЭ и МКР при близких значениях густоты сетки.
Степень дискретности разбивки определяется в МКЭ и МКР несколько по разному. В МКЭ значения расчетной функции определяются в узлах сетки поэтому размерность матрицы при решении зависит от количества узлов сетки (места где сходятся вершины элементов) а не от количества элементов (тетраэдальных пирамид) которых обычно в несколько раз больше чем узлов. В МКР же количество узлов и количество ячеек (параллелепипедов) близки по значениям однозначно связаны друг с другом и густоту сетки обычно определяют количеством ячеек. На рис.4.4 видно что при близких значениях дискретности конечно-элементная сетка гораздо более адекватно описывает реальную геометрию. Более того очевидно что разностная сетка в отличие от элементной даже при очень большей густоте всегда принципиально неправильно будет описывать любые поверхности непараллельные граням габаритного параллелепипеда представляя их «зубчатым» рельефом. К особенностям сетки МКЭ можно отнести также то что все узлы элементной сетки в отличие от разностной сетки находятся непосредственно на реальной поверхности моделируемого тела причем это правило сохраняется при любой даже очень грубой дискретности элементной сетки. Кроме того дискретность элементной сетки может легко изменяться – в относительно массивных частях геометрии (прибыли и т.п.) сетка может быть в несколько раз разреженнее чем в областях с мелкими фрагментами (тонкими стенками и т.п.). Узлы же разностной сетки с увеличением густоты лишь приближаются к реальной поверхности и в общем случае всегда находятся либо «над» либо «под» ней. В общем случае ошибка в линейных размерах тела при разностной разбивке достигает размера ячейки.
Практика показывает что оптимальный подход состоит не ввыборе какого-то одного метода решения ависпользовании комбинации различных методов - это позволяет получить выигрыш вскорости точности иадекватности получаемых результатов экспериментальным данным.
Рассмотрим возможности моделирования литейного процесса на основе программных продуктов: SolidCAST ProCAST и САПР “Отливка”.
SolidCAST является одним из самых доступных и распространенных программных комплексов направленным на решение технологических задач в литейном производстве.
Основные возможности по SolidCAST:
- расчет любых видов гравитационной заливки;
- литье под низким давлением;
- встроенный мастер создания прибылей;
- встроенный мастер создания литниковых систем;
SOLIDCast позволяет увидеть процесс кристаллизации отливки до производства оснастки обнаружить и исправить ошибки. Заливка тестовой отливки производится – на экране а не в цехе. Разработка прибылей литниковой системы и их испытание ведется до производства первой реальной отливки. Анализ литья – это снижение сроков производство высококачественных отливок с максимальным выходом годного. Это означает снижение стоимости увеличение прибыли и повышение конкурентоспособности литейного производства.
Рис 4.5 Процесс литья стального корпуса вентиля
SOLIDCast может применяться для моделирования заливки серого и ковкого чугунов сталей алюминиевых магниевых медных и никелевых сплавов а также любых других. В базе данных программы содержатся несколько сотен сплавов.
С помощью SOLIDCast возможно смоделировать процессы литья в землю в кокиль по выплавляемым моделям. Можно использовать любые элементы как то: утеплители холодильники доливка в прибыли каналы охлаждения нагревательные элементы а также всё что используется в литейном производстве.
SOLIDCast содержит мастера проектирования прибылей и литниковых систем. Также есть мастер расчёта прибылей чугунных отливок и стопорных ковшей. Эти инструменты позволяют спроектировать технологию с нуля за считанные минуты используя реальные расчёты и не основываясь на приблизительной оценке простой геометрии!!
В SOLIDCast можно импортировать 3D модели из любой CAD-системы или построить её средствами самой системы.
Графическое отображение результатов – очень мощное средство представления информации. Можно создавать не только цветные иллюстрации но и AVI-файлы.
Рис 4.6 Модель алюминиевой отливки с литниковой системой спроектированные с помощью SolidCast
К основной программе SolidCAST может быть подключено еще два дополнительных модуля: FLOWCast и OptiCAST
FLOWCast - это гидродинамический модуль. FLOWCast работает в совокупности с системой анализа литья металлов SOLIDCast и использует модели этой системы.
Гидродинамический анализ позволяет увидеть на экране монитора как расплавленный металл протекает через литниковую систему и заполняет полости формы. FLOWCast моделирует конвекцию передачу и излучение тепла в полостях формы. Это позволяет предупреждать и исправлять такие виды брака как недоливы преждевременная кристаллизация и перегрев формы появление оксидных плён или эрозия формы из-за высокой скорости течения металла.
FLOWCast имеет два вида анализа заполнения формы. Первый – быстрый алгоритм который имеет несколько упрощающих допущений. Для большинства процессов быстрый алгоритм обеспечивает быстрый и точный гидродинамический анализ течения металла во время заполнения с расчётом температурных полей.
Рис 4.7 Заполнение оболочки с помощью FLOWCast
Полный алгоритм обеспечивает полный набор возможностей – “Компьютерный гидродинамический анализ” для анализа течения металла с использованием решения уравнения Навье-Стокса. С помощью FLOWCast возможно проанализировать распределение температурных полей скорости течения и давление металла во время заполнения под любым углом зрения и в любом сечении.
FLOWCast интегрирован в SOLIDCast и использует модели и сетки созданные в SOLIDCast. Поскольку SOLIDCast - это самая простая в использовании система моделирования литья гидродинамический модуль также очень прост в работе. Необходимо только импортировать из CAD-системы 3D-модель или создать её в SOLIDCast средствами самой системы и запустить FLOWCast для начала гидродинамического анализа.
Результаты расчёта из FLOWCast могут быть использованы в SOLIDCast для моделирования кристаллизации отливки на основе полученных данных что в итоге даёт полный комплекс для моделирования литейных процессов.
Рис 4.8 Трассирование потока в алюминиевой отливке
OptiCAST позволяет оптимизировать разработку литейной технологии.
Оптимизация – это технология когда инженер берёт за основу начальный вариант построения технологии изготовления отливки с прибылями и литниковой системой в виде 3D-моделей в системе SOLIDCast. Затем необходимо выбрать следующие параметры:
Переменные параметры: Это параметры которые могут изменяться во время поиска оптимального решения. Типичным примером является высота и диаметр литейной прибыли. Другим примером может быть температура расплава время заливки или начальная температура формы.
Ограничения: Это параметры качества согласно которым будет приниматься решение и приемлемости результатов. Например степень пористости может выступать в качестве параметра оптимизации ограничивая численно минимально допустимое значение плотности материала. Выход годного также может выступать в качестве ограничения.
Оптимизирующая функция: Это тот параметр который следует увеличить или уменьшить в целях оптимизации. Например это может быть увеличение выхода годного уменьшение пористости или снижение общего времени кристаллизации.
Когда все параметры заданы запускается процесс Оптимизации. Это подразумевает серию расчётов в каждом из которых переменные изменяются изменение модели расчёт и оценка результатов – всё проходит полностью в автоматическом режиме без участия пользователя до тех пор пока не будет достигнут желаемый результат.
Используя OPTICast инженер-технолог может начать работать с исходным вариантом технологии и позволить компьютеру изменять её и анализировать для достижения приемлемого – оптимального – результата.
Сейчас впервые технология компьютерного моделирования входит в литейное производство в качестве действенного и простого в использовании инструмента для проектирования литейных технологий. OPTICast позволяет повысить выход годного и качество получаемых отливок до оптимального уровня в то время как инженер освобождается от необходимости тратить время на проектирование технологий путём повторяющихся проб и ошибок.
Рис 4.9 Стальная отливка с оптимизированными прибылями 13% увеличение выхода годного достигнуто автоматически с заданным качеством отливки
Программный комплекс ProCAST позволяет решать практически любые технологические задачи связанные с литьем металлов.
ProCAST позволяет моделировать любую литейную технологию:
- любая гравитационная заливка (литье в кокиль в ПГС по выплавляемым моделям и т.д.);
- литье под регулируемым давлением (литье под высоким давлением литье под низким давлением литье с противодавлением литье вакуумным всасыванием и т.д.);
- центробежное литье;
- непрерывное литье;
- литье по газифицируемой модели.
Программа ProCAST имеет отличный встроенный генератор 2D и 3D сеток позволяющий получить максимально корректную расчетную сетку за минимальное время.
Рис 4.10 Расчетная сетка
Имеется встроенный химический калькулятор благодаря которому можно получить все необходимые тепло-физические свойства любого сплава прямо в программе
Программа ProCAST позволяет определить:
- распределение тепловых полей в отливке и форме;
- оценить уровень возникающих напряжений в отливке и металлической оснастке
позволяет расчитывать цикличные нагрузки.
ProCAST отвечает задачам производства
Основанный на проверенной технологии конечных элементов ProCAST представляет законченное решение охватывающее широкий спектр процессов литья металлов и сплавов.
Покрытие всех производственных задач для широкого спектра процессов литья.
Литьё в землю гравитационное наклонное литьё.
Ключевые факторы успеха в гравитационном литье связаны с оптимизацией системы литников и исключением областей возможной усадки.
Литьё по выплавляемым моделям литьё в оболочковые формы.
ProCAST хорошо приспособлен для решения задачи литья по выплавляемым моделям. Например ProCAST может автоматически генерировать сетку отражающую оболочковую форму допускает неодинаковую толщину и многослойность. При этом учитывается теплоизлучение с эффектами затенения которые важны для высокотемпературных сплавов.
ProCAST предоставляет возможность моделирования заполнения формы затвердевания и формирования микроструктуры.
Расположение стояков и применение изолирующих или экзотермических подводов их влияние на усадку может быть изучено на компьютере и визуализировано на экране для достижения оптимального качества отливки.
Литьё в кокиль под низким давлением
Чтобы реально воспроизвести заводские условия можно проводить моделирование рабочих циклов формы до состояния когда температурные условия выйдут в стационарный режим. Рассчитанные температурные поля дают возможность рассчитать заполнение формы и затвердевание отливки.
Параметры процесса могут быть отрегулированы так что будет достигнуто оптимальное качество процесса за наименьшее время.
Литьё в кокиль под высоким давлением
ProCAST позволяет решать такие специфичные задачи литья под высоким давлением как жидкая штамповка и литье в полутвердой фазе. Оптимальный профиль скоростей плунжера конструкция литников и проливаемость могут быть легко определены в процессе моделирования даже у тонкостенных изделий. Термомеханические циклы кокиля могут рассчитываться не только с целью увеличения его жизненного цикла но и для повышения производительности снижая таким образом риски и затраты.
ProCAST является модульной программой.
Это позволяет подобрать наиболее оптимальную конфигурацию для пользователя а так же подключать по мере необходимости новые модули к уже имеющимся.
Основные модули ProCAST:
MeshCAST – модуль подготовки расчетной сетки. В MeshCAST создается как двухмерная так и объемная расчетная сетка. Так же возможен импорт поверхностной сетки в форматах STL Patran и некоторых других. MeshCAST изначально был разработан как генератор расчетной сетки для анализа литейной технологии.
PreCAST – модуль подготовки исходных данных для решения задачи. В этом модуле задаются все характеристики процесса используемые материалы и т.д. Главной особенностью модуля PreCAST является наличие встроенного химического калькулятора благодаря которому отпадает необходимость в поиске данных о сплавах на стороне. Вы заносите химический состав сплава и получаете все необходимые для расчета тепло-физические свойства материала.
ProCAST основан на проверенной конечно-элементной технологии.
Конечно-элементный метод подразумевает точность представления геометрии и меньшее число элементов необходимых для моделирования тонкостенных отливок.
Наилучшее описание геометрии
Конечно-элементные сетки начинаются с элементов расположенных на поверхности геометрических фигур и далее располагаются автоматически сквозь весь внутренний объем что обеспечивает отличное геометрическое описание тела.
Меньшее число элементов
Конечно-элементный метод позволяет представить геометрию с помощью элементов разного размера. Тонкие секции или области сложных фигур могут иметь элементы мельче чем в других областях обеспечивая точночть расчетов и представления и снижая число необходимых элементов.
Затвердевание деформация и течение жидкого металла вдоль стенок сложной формы по тонким каналам лучше всего рассчитывается с помощью конечных элементов в виду сглаженности и точности сетки.
ProCAST создан специалистами по литью для решения металлургических проблем
Благодаря точному конечно-элементному описанию геометрии становится возможным предсказание течения металла в форме и выявление следующих недостатков:
Размывание песчаной формы и турбулентное течение;
Дефекты заполнения и холодные спаи;
Расположение засоров.
Расчеты течения проводятся с помощью уравнения Навье-Стокса и могут быть проведены совместно с термическим анализом и вычислением напряжений.
Холодные спаи и дефекты заполнения
Некоторые критические условия такие как холодная форма маленькая скорость заполнение или низкая температура отливки могут вести к проблемам с заполнением. Совместные расчет течения и термический анализ позволяют конструктору оценить падение температуры расплава во время заполнения формы. Преждевременное затвердевание может существенно повлиять на характер заполнения. Учитывая этот феномен ProCAST так же прогнозирует когда и где могут возникнуть недолив или холодный спай. Необходимые конструкционные изменения могут быть проверены с очень малыми затратами непосредственно на компьютере.
Воздушные пузырьки и окисные плены в местах ограниченного течения ухудшают качество отливаемой детали. ProCAST позволяет моделировать турбулентное течение которое может привести к неметеллическим включениям. Места появления данных дефектов могут быть легко найдены. В этом случае можно оптимизировать литниковую систему и местоположения выпоров и шлаковиков при литье под высоким давлением.
В процессе затвердевания при кажущейся гладкости протекания процесса на поверхности в отливках могут возникать серьезные дефекты. Например когда стояки не обеспечивают достаточной подпитки могут возникнуть крупные дефекты такие как усадочные раковины. ProCAST дает возможность бороться с этими дефектами для всех типов сплавов путем модификации и изменения размеров и мест литников.
Время жизни формы «горячее» растрескивание и разломы
В ProCAST осуществлена уникальная возможность совмещенных термического гидродинамического расчета и расечта напряжений. Полный анализ проводится одновременно на одной и той же сетке. С помощью ProCAST можно изучить термальные нагрузки на форму во время ее заполнения а так же влияние зазора между отливкой и формой при затвердевании. Горячие трещины пластические деформации остаточные напряжения и геометрические отклонения - это те задачи которые успешно решаются нашими клиентами.
Макропористость легко рассчитывается с помощью стандартного решателя. Микропористость требует дополнительного модуля для точного расчета интердендритной усадки и газового наполнения.
Предназначена дляразработки технологии изготовления отливок изчерных иалюминиевых сплавов всырых разовых формах иалюминиевых сплавов литьём поддавлением. Основана насистематизированных иупорядоченных современных представлениях изнаниях вобласти литейного производства. Обеспечивает высокий уровень проектирования иразработку оптимальной инаиболее экономичной технологии изготовления отливок.
Наименование программ входящих вСАПР «Отливка»:
Оценка технологичности.
Позволяет проработать чертеж детали сцелью определения возможности изготовления отливки выбранным способом. Впроцессе диалога заполняется инакапливается необходимая технологическая документация.
САПР «Чертеж отливки»
Предоставляет возможность технологу вдиалоговом режиме взависимости отконструктивных особенностей отливки итехнологии изготовления (опочная илибезопочная формовка литье алюминиевых сплавов поддавлением).
·положение отливки вформе ивыбрать плоскость разъема;
·возможность получения отверстий влитье (проливаемость отверстий);
·количество отливок вформе;
·возможность формирования;
·литые резьбы (длялитья поддавлением);
·минимальные толщины стенок;
·всоответствии стребуемой точностью отливки дифференцировано накаждую поверхность значение припусков намеханическую обработку допуски размеров масс формы ирасположения поверхностей;
·литейные уклоны литейные радиусы;
·место подвода металла свыявлением тепловых узлов установкой прибылей ихолодильников;
2.Разработать иоформить чертеж отливки всоответствии стребованиями ЕСКД.
САПР «Технология литейной формы».
Позволяет: определить границы сложного стержня параметры знаковых частей дляпростого стержня разработать схему технологии литейной формы сразмещением стержней иболванов; разработать иливыбрать схему ЛПСипровести расчет дляотливок.
Эскиз опер эск 2.cdw

010 Операц ЧПУ 1.cdw

(Seco) Оправка: борштанга специальная
Штангенциркуль ШЦ-III-320-1000-0
Наименование операции
Обозначение программы
Комбинированная с ЧПУ
Trevisan DS 900300C Fanuc-31i
Установить и снять деталь
Приспособление специальное
Shell Macron 201 F-.32
Загрузка заготовки в зону обработки
Ориентировать заготовку в системе станка
Точить однократно поверхность 1 по программе
010 Операц ЧПУ 5.cdw

Штангенциркуль ШЦ-III-320-1000-0
Штанген глубиномер ШГ-160-0
Фреза F4042.B27.080.Z06.16 Режущая пластина ADGT1204PER-D51WKP25(Walter)
-50-40R7(Seco) Оправка специальная
Фрезеровать поверхность 11 по программе
Фрезеровать поверхность 12 начерно по программе
Фреза F4042.B27.080.Z06.16 Режущая пластина ADGT1204PER-D51WKP35(Walter) Оправка специальная
Фрезеровать поверхность 12 начисто по программе
Сверлить 14 отв. 13 по программе
Контрольный Эскиз2.cdw

Контрольный Эскиз1.cdw

Титульник.cdw

на технологический процесс механической обработки
Министерство образования и науки РФ
Курганский государственный университет
010 Операц ЧПУ 6.cdw

(Seco) Оправка специальная
Штангенциркуль ШЦ-I-125-0
Нарезать резьбу М30-7Н
отв начерно по программе.
Фреза R396.19 -2522.3S-4003-3-065A Пластина 396.19 -4003.ON1.0ISO (Seco) Оправка специальная;
отв начисто по программе.
-7Н 8221-1109 ГОСТ 17756-72
Сверлить 20 отв. 14 по программе
010 Операц ЧПУ 3.cdw

Штангенциркуль ШЦ-III-320-1000-0
Штанген глубиномер ШГ-160-0
Резец DCLNL 3232P12. Режущая пластина CNMG120408-MF2 (Seco) Оправка: борштанга специальная
Резец DCLNL 3232P12. Режущая пластина CNMG120408-MF2 (Seco); Оправка: борштанга специальная
Точить поверхность 7 начерно по программе
Точить поверхность 6 начисто по программе
Точить поверхность 7 начисто по программе
Эскиз опер эск 1.cdw

Контрольная карта.cdw

заусенцев и острых кромок
обработанных поверхностей
Штангенциркуль ШЦ-III-320-1000-0
Штангенциркуль ШЦ-I-125-0
Наименование материала
Наименование средств ТО
Наименование операции
Наименование оборудования
Контролируемые параметры
Технический контроль
Образцы шероховатости ГОСТ 9378-75
Маршрутная карта 1.frw

Код наименов.операции
Код наименование оборудования
Обозначение документа
0 Комбинированная с ЧПУ
Машина моечная НКА 98-83
К20110.00001 К20110.00002
К60141.00001; К20141.00003 К20141.00004; ИОТ №67.
010 Операц ЧПУ 4.cdw

Штангенциркуль ШЦ-III-320-1000-0
Резец S32T-PDUNL15 . Режущая пластина DNMG150608-M5 (Seco) ; Оправка: борштанга специальная
Резец MVJNR 2020K16 . Режущая пластина VNMG 160404-M3 (Seco) ; Оправка: борштанга специальная
Поворот стола на 180
Точить однократно поверхность 8 по программе
Точить однократно поверхность 9 по программе
Точить однократно поверхность 10 по программе
Аналогично обработать второй фланец
ЗАГГГГГ эск 2.cdw

010 Операц ЧПУ 2.cdw

(Seco) Оправка: борштанга специальная
Штангенциркуль ШЦ-III-320-1000-0
Оправка: борштанга специальная
Резец SCACL1212M09. Режущая пластина (Seco) Оправка: борштанга специальная
Резец MCLNL 3232P19. Режущая пластина CNMM 190608-(Seco) Оправка: борштанга специальная
Штанген глубиномер ШГ-160-0
. Точить однократно поверхности 2
Точить однократно поверхность 4 по программе
Точить поверхность 5 по программе
Точить поверхность 6 начерно по программе
Маршр карта 2.frw

наименование оборудования
ед.единицы или материала
СМ Проф. Р УТ КР КОИД ЕН ОП Кшп Тп.з Тшт
Машина моечная НКА 98-83
К60102.00002; К20102.00005; К20102.00006 ИОТ №91.
ЗАГГГГГГэск 1.cdw

010 Операц ЧПУ 7777.cdw

Аналогично обработать второй фланец
КР-РМ-100%; OTK-10%; KM-PM-5%
Рекомендуемые чертежи
- 24.01.2023