Проект участка на базе станков с ЧПУ по изготовлению деталей запорной арматуры




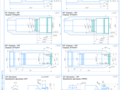
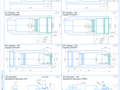
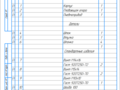
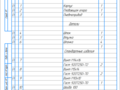
- Добавлен: 24.01.2023
- Размер: 4 MB
- Закачек: 0
Описание
Состав проекта
![]() |
![]() |
![]() ![]() ![]() ![]() |
![]() ![]() ![]() ![]() |
![]() ![]() ![]() |
![]() ![]() ![]() ![]() |
![]() ![]() ![]() ![]() |
![]() ![]() ![]() ![]() |
![]() ![]() ![]() ![]() |
![]() ![]() ![]() ![]() |
![]() |
![]() |
![]() ![]() ![]() ![]() |
![]() ![]() ![]() ![]() |
![]() ![]() ![]() ![]() |
![]() ![]() ![]() ![]() |
![]() ![]() ![]() ![]() |
![]() ![]() ![]() ![]() |
![]() ![]() ![]() ![]() |
![]() ![]() ![]() ![]() |
![]() ![]() ![]() ![]() |
![]() ![]() ![]() ![]() |
![]() ![]() ![]() ![]() |
![]() |
![]() ![]() ![]() ![]() |
![]() ![]() ![]() ![]() |
![]() ![]() ![]() ![]() |
![]() ![]() ![]() ![]() |
![]() ![]() ![]() ![]() |
![]() ![]() ![]() ![]() |
![]() ![]() ![]() ![]() |
![]() ![]() ![]() ![]() |
![]() ![]() ![]() ![]() |
![]() ![]() ![]() ![]() |
![]() ![]() ![]() ![]() |
![]() ![]() ![]() ![]() |
![]() ![]() ![]() ![]() |
![]() ![]() ![]() ![]() |
![]() ![]() ![]() ![]() |
![]() ![]() ![]() ![]() |
![]() ![]() ![]() ![]() |
![]() ![]() ![]() ![]() |
![]() ![]() ![]() ![]() |
![]() ![]() ![]() ![]() |
![]() ![]() ![]() ![]() |
![]() ![]() ![]() ![]() |
![]() ![]() ![]() ![]() |
![]() ![]() ![]() ![]() |
![]() ![]() ![]() ![]() |
![]() ![]() ![]() ![]() |
![]() |
![]() ![]() ![]() ![]() |
![]() ![]() ![]() ![]() |
![]() ![]() ![]() ![]() |
![]() ![]() ![]() ![]() |
![]() ![]() ![]() ![]() |
![]() |
![]() ![]() ![]() ![]() |
![]() ![]() ![]() ![]() |
![]() |
![]() ![]() ![]() ![]() |
![]() ![]() ![]() ![]() |
![]() ![]() ![]() ![]() |
![]() |
![]() ![]() ![]() ![]() |
![]() ![]() ![]() ![]() |
![]() |
![]() ![]() ![]() ![]() |
![]() ![]() ![]() ![]() |
![]() ![]() ![]() ![]() |
![]() |
![]() ![]() ![]() ![]() |
![]() ![]() ![]() ![]() |
![]() ![]() ![]() ![]() |
![]() |
![]() ![]() ![]() ![]() |
![]() ![]() ![]() ![]() |
![]() ![]() ![]() ![]() |
![]() |
![]() ![]() ![]() ![]() |
![]() ![]() ![]() ![]() |
![]() ![]() ![]() ![]() |
Дополнительная информация
фрезерная.cdw

Сверло центровочное
Сверло спиральное Р6М5
Дисковая трёхсторонняя фреза
Проект участка на базе станков с ЧПУ по изготовлению
деталей запорной арматуры
Инструментная наладка
на токарную операцию
Операция фрезерная с ЧПУ
Станок с ЧПУ модели СВМ-1 Ф4
Втулка с конусом Морзе 2
Патрон(приспособ)+оправка.cdw

деталей запорной арматуры
Заготовка 108 закреплена в самоцетрирующем
зажимном приспособлении.
Соотношение плеч 1:2
Привод пневматический Р = 4 кгс см
Ход поршня Н = 45 мм.
записка (диплом)редакт.doc
Введение . . . . . . . . . . . . . . . . . . . . . . . . . . . . . . . . . . . . . . . . . . . . . . . . . . . . . . .3
Характеристика объектов производства . . . . . . . . . . . . . . . . . . . . . . . . . . . 4
Технологический раздел. . . . . . . . . . . . . . . . . . . . . . . . . . . . . . . . . . . . . . . . . 5
1. Служебное назначение и анализ на технологичность . . . . . . . . . . . . . . . 5
2. Определение типа производства . . . . . . . . . . . . . . . . . . . . . . . . . . . . . . . . 6
3 Анализ базовых технологических процессов. . . . . . . . . . . . . . . . . . . . . . .8
4. Выбор заготовки . . . . . . . . . . .. . . . . . . . . . . . . . . . . . . . . . . . . . . . . . . . . . .9
5. Разработка маршрутных технологических процессов . . . . . . . . . . . . . . .10
6. Технологические расчеты . . . . . . . . . . . . . . . . . . . . . . . . . . . . . . . . . . . . . . 12
7. Разработка операционного технологического процесса . . . . . . . .. . . . . .27
8. Технико-экономическое обоснование проектного тех. процесса. . . . . . 28
9. Описание и расчёт инструментных наладок и УП. . . . . . . . . . . . . . . . . . 29
Конструкторский раздел . . . . . . . . . . . . . . . . . . . . . . . . . . . . . . . . . . . . . . . . .30
1. Проектирование станочного и контрольного приспособлений . . . . . . . .30
2. Проектир. средств автоматизации производственного процесса
“ Компоновка РТК ”. . . . . . . . . . . . . . . . . . . . . . . . . . . . . . . . . . . . . . . . . . . . . . 35
Исследовательский раздел . . . . . . . . . . . . . . . . . . . . . . . . . . . . . . . . . . . . . . .42
1. Анализ методов получения заготовок литьём . . . . . . . . . . . . . . . . . . . . . . 42
Производственные расчеты и разработка планировки . . . . . . . . . . . . . . .. .56
Безопасность и экологичность проекта . . . . . . . . . . . . . . . . . . . . . . . . . . . . .60
Организация производства . . . . . . . . . . . . . . . . . . . . . . . . . . . . . . . . . . . . . . .69
Экономическая оценка проекта . . . . . . . . . . . . . . . . . . . . . . . . . . . . . . . . . . .71
Заключение . . . . . . . . . . . . . . . . . . . . . . . . . . . . . . . . . . . . . . . . . . . . . . . . . . . . . .82
Список используемых источников. . . . . . . . . . . . . . . . . . . . . . . . . . . . . . . . . . . 83
Приложения . . . . . . . . . . . . . . . . . . . . . . . . . . . . . . . . . . . . . . . . . . . . . . . . . . . . .85
Целью данного дипломного проекта является проектирование участка на базе станков с ЧПУ по изготовлению корпусных деталей разработка операционного технологического процесса на выполнение операций применение полученных знаний за время обучения в университете.
В данном дипломном проекте анализируется предложенная деталь (цилиндр колесного тормоза). Решается комплекс технологических задач таких как: выбор заготовки назначение припусков на обработку поверхностей на каждую операцию разрабатывается операционная технология т.е. выбираются базы и средства технологического оснащения. Определяются режимы резания нормы технологического времени с расчетами сравнительной экономической эффективности. Для разработки исследовательского раздела используется дополнительная техническая литература. Конструкторский раздел содержит описание работы и расчет станочного приспособления расчет средств автоматизации. В разделе по БЖД рассматриваются вопросы по: безопасности труда на участке обеспечению экологической безопасности и безопасность проекта в ЧС. В организационно-экономической части рассчитывается срок окупаемости проектируемого участка по обработке рассматриваемой группы деталей.
Дипломный проект содержит расчетно-пояснительную записку графическую часть (13 листов чертежей и спецификации) комплект технологической документации.
Данный проект содержит практические сведения по реальным процессам и оборудованию применяемому в машиностроении.
Машиностроение является важнейшей отраслью народного хозяйства опре6деляющей уровень и темы развития всех других отраслей промышленности сельского хозяйства энергетики транспорта и др.
Быстрое развитие машиностроительного производства настоятельно требовало научного разрешения вопросов связанных с изготовлением машин требуемого качества в установленном производственном программой количестве и в заданные сроки при наименьших затратах живого и вещественного труда т.е. при наименьшей собственности.
Проектирование технологических процессов изготовления деталей машин является одним из наиболее ответственных этапов технологической подготовки производства. Технологический процесс должен обеспечивать высокую производительность труда и требуемое качество изделий при минимальных затратах на их изготовление.
Характеристика объектов производства
Среди большого разнообразия машиностроительной продукции весьма распространенную группу составляют корпуса которые служат для размещения отдельных деталей механизмов и агрегатов. Являясь важнейшими элементами конструкции машин эти детали должны обеспечивать точность взаимного расположения установленных на них деталей и сборочных единиц как статическом положении так и при эксплуатации изделия.
В соответствии с целевым назначением корпусные детали должны обладать следующими свойствами: прочностью жесткостью герметичностью виброустойчивостью долговечностью.
Прочность является основным критерием работоспособности для корпусных деталей подвергаемых большим нагрузкам главным образом ударным и переменным.
При изготовлении корпусных деталей должны быть обеспечены в установленных пределах параллельность и перпендикулярность осей основных отверстий относительно друг друга и плоских поверхностей.
В зависимости от конструктивного исполнения и сложности к корпусным деталям предъявляются технические требования:
- точность расстояния между двумя параллельными плоскостями
- диаметры основных отверстий под посадку подшипников должны соответствовать 6 – 8 квалитетам.
- параметры шероховатости плоских базирующих поверхностей
Ra=25 – 63мкм поверхностей главных отверстий Ra=125 – 016мкм а для ответственных деталей до Ra=008мкм.
Технологический раздел
1. Служебное назначение и анализ технологичности детали.
Одним из важных этапов проектирования является отработка конструкции детали на технологичность. Целью данного этапа является выявление возможности снижения себестоимости и трудоемкости изготовления без ущерба для служебного назначения детали за счет незначительных изменений в ее конструкции.
В результате качественной оценки детали на технологичность можно сделать следующие выводы:
Материал детали – сталь 25Л ГОСТ 977-88 полностью соответствует условиям эксплуатации и требованиям по прочности износостойкости поверхностным деформациям и т.п.
Конструкция детали обеспечивает достаточную жесткость при механической обработке на металлорежущем оборудовании.
Деталь имеет элементы удобные для закрепления заготовки при обработке.
Формы поверхностей подлежащих обработке не представляют сложности (в основном – поверхности вращения); имеется возможность максимального использования стандартизованных и нормализованных режущих и измерительных инструментов.
С точки зрения обеспечения заданной точности и шероховатости поверхностей деталь не представляется сложной.
Количественную оценку технологичности проведем по следующим показателям: коэффициенты использования материала (КИ.М.) точности обработки (КТ.Ч.) шероховатости поверхности (КШ).
Коэффициент использования материала:
Здесь МД и МЗ – соответственно массы детали и заготовки в базовом варианте кг.
Данное значение Ки.м свидетельствует о рациональном использовании материала в условиях среднесерийного производства.
Определим коэффициент точности [2]:
где Аср – средний квалитет точности обработки детали по всем поверхностям.
Согласно чертежу детали ориентировочно можно определить АСР = 10.
Тогда КТ.Ч. = 09. Так как КТ.Ч. > 08 то деталь можно считать по этому
параметру технологичной.
На основании качественного и количественного анализа на технологичность можно сделать следующий вывод: деталь вполне технологична нет необходимости вносить в ее конструкцию какие-либо изменения.
2.Определение типа производства.
Тип производства по ГОСТ 3.1121-84 характеризуется коэффициентом закрепления операций (КЗ.О.):
КЗ.О. 10 – массовое и крупносерийное производство;
КЗ.О. 20 – среднесерийное производство;
КЗ.О. 40 – мелкосерийное производство;
КЗ.О. – единичное производство.
Величина коэффициента закрепления операций определяется по формуле [25]:
где О – суммарное число различных операций выполняемых на производственном участке в течение месяца;
Р – суммарное число рабочих мест на которых выполняются данные операции.
Определим расчётное количество станков необходимых для выполнения каждой станочной операции (Cpi) [25]:
где N-объём годового выпуска деталей шт.;
tшт – штучное время i-ой операции мин.
Fо- эффективный годовой фонд времени работы станка;
Кв – средний коэффициент выполнения норм времени. При обработке на станках с ручным управлением Кв =11 – 12 на станках с ЧПУ автоматах полуавтоматах и агрегатных станках Кв =10;
Кр- коэффициент учитывающий потери по организационно-техническим причинам. Для расчетов можно принять Кр = 095.
Определяем принятое количество оборудования на каждой станочной операции (Si ) для чего расчетное количество станков (Cpi ) округляется увеличением до целых значений. .
Рассчитываем коэффициент загрузки каждого места (зi ) [25]:
Определяем число операций закреплённым за одним рабочим местом(Оpmi )
где н нормативный коэффициент загрузки оборудования .Для расчётов примем =07.
Количество заготовок в партии для одновременного запуска можно определить по формуле [25]:
где Sn- количество запусков в год. Для крупносерийного производства
Результаты вычислений представлены в таблице 1.
Тип производства крупносерийный.
Объем годового выпуска N = 9800шт.
Общий объем годового выпуска всех деталей N = 85400шт.
3.Анализ базовых технологических процессов
При изготовлении основной и дополнительных деталей на базовом предприятии технологические процессы их изготовления построены по принципу дифференциации операций с использованием универсального и полуавтоматического оборудования. Данный принцип построения технологического процесса подразумевает использование широкой номенклатуры технологической оснастки вспомогательного режущего инструмента. При изготовлении деталей часто мешаются их базовые поверхности.
Кроме того при обработке деталей используются устаревшие конструкции инструмента и марки инструментальных материалов.
Перечисленные выше недостатки базового технологического процесса существенно увеличивают себестоимость и трудоемкость изготовления деталей.
Более подробно рассмотрим технологический процесс изготовления основной детали.
5. Заготовка - отливка
0. Токарная операция. Оборудование – токарно-винторезный станок 1К62;
На этой операции проводится черновое точение заготовки с одной стороны а именно подрезка торца и точение канавки.
5.Токарная операция с ЧПУ. Оборудование – токарной станок 1П756ДФ3;
На этой операции проводится подрезка торца растачивание отверстий и нарезание резьбы.
0. Токарная операция с ЧПУ. Оборудование – токарной станок 1П756ДФ3;
На этой операции проводится окончательная подрезка торца растачивания отверстия под резьбу и нарезание резьбы.
0.Фрезерная. Оборудование – Вертикально фрезерный станок 6Н12.
На этой операции фрезеруются пазы.
0.Сверлильная операция. Оборудование – сверлильный станок 2А55; приспособление –кондуктор. На этой операции проводится сверление 2 отверстий на ушах стойки.
5.Слесарная. Верстак. Приспособление – тиски. Притупляются острые кромки.
При близком ознакомлении с базовым технологическим процессом выявляется возможность перекомпоновки операций в связи с вводом высокопроизводительных станков с ЧПУ. Это приведет к уменьшению вспомогательного времени увеличению концентрации переходов а значит к увеличению производительности и точности обрабатываемой детали.
Для уменьшения основного времени рационально будет применить современные конструкции режущего инструмента.
Выбор вида исходной заготовки является ответственным этапом разработки технологического процесса так как коренным образом влияет на технологию механической обработки детали.
Особенно важно правильно выбрать заготовку для условий автоматизированного производства когда обработка ведется на автоматических линиях специальных и агрегатных станках полуавтоматах и автоматах.
Исходя из физико-механических свойств материала детали наиболее лучшим методом получения заготовки является литьё. В условиях серийного производства наиболее рациональным способом получения заготовки является литьё в песчаных формах.
Себестоимость заготовки:
КТ КС КВ КМ КП – коэффициенты зависящие соответственно от класса точности группы сложности массы марки материала и объема производства
МЗ МД - масса соответственно заготовки и детали: МЗ = 2238 кг; МД = 15кг.
Sотх - цена 1 т отходов Sотх = 80 руб.
КТ = 1 – для отливок нормальной точности;
КС = 07 – для отливок в песчаных формах;
КВ = 087 – для заготовок массой от 10 до 25 кг;
КМ = 122 – для заготовок из стали 40Х;
КП = 088 – для второй группы серийности.
S заг. =(2238107087122088)-(2238-15)=467руб.
Затраты на годовой выпуск заготовок S = 467 4800 = 22416 руб. (по ценам 1981г.).
Расчет себестоимости заготовки произведен по методике изложенной в технической литературе [2]. Данный метод расчета себестоимости является неточным т.к. он не учитывает других факторов влияющих на себестоимость заготовки.
5. Разработка маршрутных и операционных технологических процессов.
Маршрутные технологические процессы изготовления основной и дополнительных деталей разработаны на основе базового технологического процесса и ориентированы на автоматизированное производство. Технологические процессы их изготовления построены по принципу концентрации операций. При этом сокращается число установок заготовок на станок широко применяется многоинструментная обработка одной или нескольких поверхностей. При этом повышается точность взаимного расположения обрабатываемых поверхностей производительность обработки за счет снижения основного и вспомогательного времени сокращается длительность производственного цикла упрощается календарное планирование возрастают требования к точности станка его технологическим возможностям.
Маршрутное описание технологического процесса заключается в сокращенном описании всех технологических операций в маршрутной карте в последовательности их выполнения без указания переходов и технологических режимов.
Построение технологического маршрута обработки во многом определяется конструктивно-технологическими особенностями детали. Выбор маршрутной технологии существенно зависит от типа производства уровня автоматизации и применяемого оборудования.
Выбор станка на операцию определяется возможностью изготовления на нем деталей необходимой конфигурации и размеров а также обеспечения качества ее поверхности.
Проектный маршрутный технологический процесс представлен в таблице 2.2 и комплекте технологической документации в приложении.
Наименование и краткое
Технологические базы приспособление
Заготовительная – литьё
Подрезать торцы точить диаметр 78h12 точить под углом 45 с диаметра 71 напроход
Токарно-винторезный станок 16К25Ф3
патрон трехкулачковый самоцентрирующий.
Подрезать торец 31 расточить диаметры 61708787точить фаску
патрон трехкулачковый самоцентрирующий кулачки.
Подрезать торец в размер 260
Расточить диаметр 57 под резьбу диаметр 61 .Точить фаску
Фрезеровать 2 паза шириной 19
Центровать 2 отверстия
Сверлить 2 отверстия диаметром 14H12
Приспособление фрезерное
6 Технологические расчеты.
2.1. Определение припусков операционных размеров и допусков на обработку.
Припуски на механическую обработку поверхностей заготовки могут быть определены:
опытно-статистическим методом;
расчетно-аналитическим методом.
В данной работе для поверхностей 61 и 260 припуски определяем расчетно-аналитическим способом для остальных - по таблицам 3.
Опытно-статистический метод.
Масса детали m=15кг.
Материал заготовки: 25Л.
Годовой выпуск: 13800шт.
Деталь относится к 1 весовой группе отливок (6 таблица 2).
Тип производства: серийный.
Способ литья: литьё в песчанно-глинистые формы .
Степень точности поверхностей отливок: 13 (6 таблица 5).
Класс точности размеров: 9 (6 таблица 7).
Ряд припусков: 3 (6 таблица 7).
Радиус закругления - 5 мм. Литейные уклоны - 7°.
Размер детали по чертежу мм
Расчетно-аналитический метод.
Расчет припусков аналитическим методом ведем согласно методике 345.
Технологический маршрут обработки поверхности состоит из чернового и чистового растачивания. Токарная обработка производится в трехкулачковом самоцентрирующем патроне.
Используя составленный маршрутный технологический процесс записываем технологические переходы для обрабатываемых поверхностей в порядке последовательности их выполнения (см. табл.2.3.).
Минимальный припуск при обработке отверстий (двусторонний припуск):
– суммарные отклонения расположения поверхности;
ei – погрешность установки заготовки при выполняемом переходе.
Значения Rz i-1 h i-1 определяем для каждого технологического перехода по соответствующим таблицам.
Литьё RZ =200 мкм h = 250 мкм.
Черновое растачивание RZ = 100 мкм h = 100 мкм.
Чистовое растачивание RZ = 25 мкм h = 25 мкм
Суммарное значение пространственных погрешностей при обработке отверстия в патроне определяется 3 :
гдеом - отклонение заготовки детали в зависимости от способа крепления;
ц – величина отклонения расположении заготовки центровки.
Находим 3 ом = 024 мм ц = 047 мм. Тогда имеем:
Остаточные пространственные отклонения с достаточной для практических целей точностью определяем по эмпирической формуле:
Здесь КУ – коэффициент уточнения формы:
после чернового растачивания КУ = 006; ρост = 0032мм;
после чистового растачивания КУ = 004; ρост = 0021 мм;
Рассчитанные значения заносим в соответствующие графы таблицы
Минимальный припуск:
- под черновое обтачивание:
- под чистовое обтачивание:
Минимальный расчетный размер для каждого технологического перехода:
- после чернового обтачивания:
- после чистового обтачивания:
Предельные значения припусков определяем как разность наибольших предельных размеров и - как разность наименьших предельных размеров предшествующего и выполняемого переходов:
Аналогично определяются припуски и на размер 65.
Определим погрешность установки:
При установке заготовки в 3-х кулачковый патрон:
Тзаг - допуск на заготовку Тзаг=1600 мкм
- погрешность закрепления для трех кулачкового патрона.
Погрешность установки на последующих переходах определяется аналогично.
Результаты занесём в таблицы
Расчет припусков на обработку и предельных размеров по технологическим переходам (ø61)
Растачивание черновое
Расчет припусков на обработку и предельных размеров по технологическим переходам (260)
Растачивание чистовое
6.2. Расчет режимов резания.
Элементы режимов резания устанавливаются в следующей последовательности:
определяется глубина резания t;
выбирается подача S;
рассчитывается по эмпирическим формулам скорость резания V;
рассчитывается частота вращения шпинделя станка n;
корректируются по паспортным данным станка S и n;
уточняется скорость резания;
определяется момент и мощность резания (при необходимости);
производится проверка рассчитанных режимов резания.
В данной работе расчет режимов резания производим для двух операций: фрезерной и токарной.
6.2.1.Расчет режимов резания для фрезерной операции.
Принимаем глубину резания t = 31 мм. Подачу назначаем согласно рекомендациям [10] Sz = 006 мм. Скорость резания:
Здесь коэффициент СV и показатели степеней myрu и x зависят от вида обработки материала режущей части обрабатываемого материала и величины подачи.
При фрезеровании стали 25Л имеем:
CV = 690; m = 035; y = 05; q = 02х=03y=04бu=0.1р=0 (табл. 3940 [10])
Т – стойкость фрезы Т = 120 мин;
где Кмv – коэффициент учитывающий качество обрабатываемого материала ;
Кnv – коэффициент учитывающий состояние поверхности заготовки
Киv – учитывает коэффициент учитывающий материал инструмента
Тогда скорость фрезерования:
Частота вращения шпинделя:
гдеD – диаметр обрабатываемой поверхности D = 80 мм.
Принимаем частоту вращения n=800 мин.
Отсюда находим минутную подачу:
Находим силы резания:
где Сp=261x=09y=08u=11w=0.1 Тогда получаем:
где D-диаметр фрезы мм
Находим мощность резания:
Принимаем глубину резания t = 7 мм. Подачу назначаем согласно рекомендациям [10] S = 020 мм. Скорость резания:
Здесь коэффициент СV и показатели степеней m y и x зависят от вида обработки материала режущей части обрабатываемого материала и величины подачи.
При сверлении отверстий в заготовке из стали 25Л имеем:
CV = 7; m = 02; y = 07; q = 04 (табл. 2930 [10])
Т – стойкость резца Т = 45 мин;
где Кмv – учитывает влияние на скорость резания материала заготовки; КМ=08;
Киv – учитывает глубину сверления КП = 10;
Кlv – учитывает материал инструмента КИ = 10
Тогда скорость резания:
гдеD – диаметр обрабатываемой поверхности D = 14 мм.
Принимаем частоту вращения n=550 мин.
Уточняем скорость резания в связи с принятой стандартной частотой вращения шпинделя:
Находим мощность резания:
гдеMкр – крутящий момент:
гдеСМ= 00345; у = 08; q= 20; Kp= 6978.
Тогда мощность резания:
Данные для центровочного сверла выбираем из справочника и заносим в операционную карту.
6.2.1. Расчет режимов резания для токарной операции.
Резец 2120-4148 Т5К6:
Принимаем глубину резания t = 5 5 мм. Подачу назначаем согласно рекомендациям [10] S = 08 мм. Скорость резания:
Здесь коэффициент СV и показатели степеней m y u p и x зависят от вида обработки материала режущей части обрабатываемого материала и величины подачи.
CV = 340; m = 02 y = 045 x = 015 (табл. 2930 [10])
Т – стойкость резца Т = 50 мин;
где КМV – учитывает влияние на скорость резания материала заготовки; КМ=08;
КПV– учитывает состояние поверхности КП =085;
КИV – учитывает материал инструмента КИ = 1
Частота вращения шпинделя:
гдеD – диаметр обрабатываемой поверхности D = 88 мм.
Принимаем частоту вращения n=350 мин.
Вычислим величину силы резания:
где CP=300; y=075; n1=1
Мощность резания определяется по формуле:
Мощность которую должен обеспечить станок:
где Nдв – мощность электродвигателя привода главного движения кВт; – механический КПД.
Данные для других инструментов выбираем из справочника и заносим в операционную карту.
6.3. Техническое нормирование операций.
6.3.1. Техническое нормирование фрезерной операции:
В серийном производстве определяется норма штучно-калькуляционного времени ТШ-К:
гдеТШТ – норма штучного времени;
ТП-З – норма подготовительно-заключительного времени;
n – размер партии запуска.
гдеtО – основное время;
tВ – вспомогательное время;
tОБС – время на обслуживание рабочего места;
tЛП – время перерывов на отдых и личные потребности.
Нормирование фрезерной операции 025 проводим согласно рекомендациям приведенным в [210]. Основное время на операцию складывается из затрат времени на каждый технологический переход:
Основное время на каждый технологический переход определяем по известной формуле:
гдеL – длина обрабатываемой поверхности;
Вспомогательное время: (2.21.)
гдеtВУ – время на установку и снятие заготовки; tВУ = 03 мин;
tМВ – время на вспомогательные ходы ; tМВ = 082 мин;
tкон – время на контроль ; tкон = 010мин;
Время на обслуживание рабочего места и личные потребности берутся в процентах от оперативного времени:
Норма подготовительно-заключительного времени при обработке на станке СВМ-1 Ф4 ТП-З = 36 мин.
гдеN – годовой выпуск деталей N = 9800;
Sn – число запусков в год (принимаем Sn = 12).
Тогда штучно-калькуляционное время:
6.3.2. Техническое нормирование токарной операции(015)
Нормирование токарной операции 015 с ЧПУ проводим согласно рекомендациям приведенным в [210]. Основное время на операцию складывается из затрат времени на каждый технологический переход:
Вспомогательное время:
гдеtВУ – время на установку и снятие заготовки; tВУ = 014 мин;
tМВ – время на вспомогательные ходы ; tМВ = 114 мин;
tкон – время на контроль ; tкон = 015мин;
Время обслуживания рабочего места и время на личные потребности составляет 10 % от оперативного времени. Тогда:
Норма подготовительно-заключительного времени при обработке на станке 1П756ДФ3 ТП-З = 30 мин.
6.3.3. Техническое нормирование токарной операции(020)
Нормирование токарной операции 020 с ЧПУ проводим согласно рекомендациям приведенным в [210]. Основное время на операцию складывается из затрат времени на каждый технологический переход:
tМВ – время на вспомогательные ходы ; tМВ = 0933 мин;
Тогда tВ = 1233 мин.
7. Разработка операционного технологического процесса.
Операционные технологические процессы изготовления основной детали а также маршрутные технологические процессы по изготовлению дополнительных деталей можно найти в комплекте документов.
8.Технико-экономическое обоснование
проектного технологического процесса.
Технический прогресс в машиностроении характеризуется непрерывным совершенствованием технологии изготовления изделий. В свою очередь это требует научно-обоснованного подхода к анализу экономичности разрабатываемых технологических процессов механической обработки деталей и экономическому стимулированию их внедрения.
Целесообразность разработанного технологического процесса механической обработки заготовки определяется на основе сравнительной экономической эффективности двух вариантов: базового и проектного на примере сравнения отдельных технологических операций.
Приведем сведения о маршрутах обработки. Базовый технологический процесс состоит из 5-и операций:
В проектном варианте технологического процесса последние две операции объединяются и производятся на станке СВМ1 Ф4 а также первую операцию переводим на станок с ЧПУ.
В соответствии с действующей методикой расчета экономической эффективности новой техники в машиностроении общим экономическим показателем эффективности является величина годовой экономии на приведенных Δ Сп определяемая из уравнения:
Δ Сп=Сп1-Сп11 (2.25.)
где Сп1 и Сп11 – соответственно сумма годовых приведенных затрат базового и проектного вариантов р.
Сумма годовых приведенных затрат по каждому варианту можно определить по формуле:
Сп=(Сi+En·Ki) (2.26)
EH – нормативный коэффициент эффективности капитальных вложений ЕН=015;
Кi – сумма годовых капитальных затрат на i-ой операции по вариантам р.
Расчет ведем в соответствии вышеуказанной методике по специальной программе. Результаты расчёта приведены в приложении.
9. Описание и расчёт инструментных наладок.
В данном дипломном проекте спроектированы 3 инструметных наладки. Выбрана система координат определены координаты точек движения режущего инструмента. В таблице на каждом листе представлены режимы резания и время обработки.
На первом листе графической части дипломного проекта представлена инструментная наладка токарной обработки основной детали(стойки) на токарном станке с ЧПУ 1П756ДФ3(операция №015).
На данной операции обработка ведётся пятью инструментами(проходным проходным и резьбовым резцами).
Материал режущей части Т5К10.
На втором листе представлена наладка этой же детали на токарном станке с ЧПУ 1П756ДФ3(операция №020).
На данной операции обработка ведётся тремя инструментами(проходным проходным канавочным и резьбовым резцами).
На третьем листе представлена инструментная наладка фрезерной операции на станке СВМ1 Ф4(операция №025).
На данной операции обработка ведётся тремя инструментами(дисковой фрезой и центровочным и спиральным свёрлами).
Конструкторский раздел
1 Проектирование станочного и контрольного приспособлений.
Интенсификация производства в машиностроении неразрывно связана с техническим перевооружением и модернизацией средств производства на базе применения новейших достижений науки и техники. Техническое перевооружение подготовка производства новых видов продукции машиностроения и модернизация средств производства неизбежно включают процессы проектирования средств технологического оснащения и их изготовления.
В общем объеме средств технологического оснащения примерно 50% составляют станочные приспособления. Применение станочных приспособлений позволяет:
)надежно базировать и закреплять обрабатываемую деталь с сохранением ее жесткости в процессе обработки;
)стабильно обеспечивать высокое качество обрабатываемых деталей при минимальной зависимости качества от квалификации рабочего;
)повысить производительность и облегчить условия труда рабочего в результате механизации приспособлений;
)расширить технологические возможности технологического оборудования.
В данной работе проектируется приспособление для фрезерной операции отверстий на станке СВМ-1 Ф4. Чертёж приспособления выполнен на формате А1.
1.1. Расчёт фрезерного приспособления.
Сила зажима должна обеспечить надежное закрепление заготовки в приспособлении и нe допускать сдвига поворота или вибрации заготовки при обработке.
На деталь действует сила резания от фрезы Рz и крутящий момент возникающая при сверлении. Необходимо определить силу зажима детали в приспособлении. Схемы действия сил представлена на рис. 3.1.
Составим уравнения равновесия сил и моментов:
Относительно точки F:
тогда осевая сила будет равна
Относительно точки U:
отсюда осевая сила равна
Очевидно что наиболее сильная осевая сила при фрезеровании. Значит расчёты по диаметру болта ведём для осевой силы Q=21903907H.
Определим внутренний диаметр резьбы болта:
где - допускаемое напряжение болта
Выбираем из справочника( 11):
- наружный диаметр резьбы болта
-средний диаметр резьбы болта
Для достижения необходимой осевой силы Q с помощью затягивающей гайки необходимый момент составит:
где - угол наклона резьбы
- коэффициент трения на торце гайки
- наружный диаметр шайбы
- диаметр отверстия для установки болта
1.2 Расчет контрольного приспособления на точность.
Это приспособление служит для контроля соосности детали стойка и сопрягаемой с ней деталью крышка.
Суммарная погрешность контрольного приспособления может быть рассчитана по формуле:
гдеу – систематическая составляющая пограничностей изготовления установленных элементов приспособления;
р – систематическая составляющая погрешностей передаточных устройств;
э – систематическая составляющая погрешностей изготовления эталона;
ЕБ – погрешность базирования детали в контрольном приспособлении;
Ез – погрешность закрепления детали в приспособлении;
ЕП – случайная составляющая погрешностей передаточных устройств;
Еэ – случайная составляющая погрешностей изготовления эталона;
Ем – погрешности метода измерения вызываемые погрешностями измерительных (отсчетных) устройств колебаниями температуры и др.
Систематические погрешности у р э учитываем при настройке контрольного приспособления следовательно их из расчета исключаем
Еб=12 Т 67 + Тбиен=001+01=011
Рассчитываем суммарную погрешность:
1.3. Расчёт токарного приспособления.
Заготовка с диаметром базы 108 закреплена в самоцентрирующем зажимном приспособлении. На неё действуют радиальные силы число которых n и крутящий момент. Произведём расчёт данного приспособления.
Найдём силу зажима действующую на зотовку:
где Dз= 108; f- коэффициент трения f = 025; n = 1.
Мк выбираем из режимов резания; Мкр = 768524 Нм
Исходя из схемы приведённой на рис3.2. мы можем вычислить силу Q необходимую для трёхкулачкого патрона.
Отсюда видно что сила Q будет равна
Исходя из полученных данных выбираем пневмоцилиндр который устанавливаем на патрон.
2. Проектирование средств автоматизации
производственного процесса “Компоновка РТК”.
На операции 15 технологического процесса штучное время составляет Тшт.=2712 мин.
тип производства – среднесерийный то необходима автоматизация данной токарной операции. В качестве способа автоматизации выбираем роботизацию.
Роботизация – это автоматизация механообрабатывающего производства на основе использования промышленных роботов. Основными этапами роботизации являются: выбор объекта роботизации формирование системы задач и требований к проектированию РТК внедрение и эксплуатация РТК. Основными источниками экономической эффективности ПР и РТК являются: повышение производительности оборудования или повышение производительности труда в результате замены ручного труда при загрузке деталей транспортировании деталей и выполнении основных технологических операций.
Компоновка РТК механической обработки показана на графическом листе 8 дипломной работы.
Данный комплекс предназначен для токарной обработки деталей до 40 кг в условиях серийного производства. Роботизированный комплекс состоит из токарного станка с ЧПУ 1П756ДФ3 ПР портального типа мод. МА80Ц25.09 магазин-накопитель склад-стелаж для технологической оснастки систему ЧПУ ПР. Управление роботом осуществляется устройством модели МС-2101. Данное устройство предусматривает возможность работы в режиме диалога «станок-робот». Устройство построено по принципу синхронного микропрограммного автомата с конечным числом состояний и жестким циклом управления.
Техническая характеристика ПР МА80Ц25.09:
-грузоподъемность – 40 кг;
-число степеней подвижности – 5;
-привод – гидравлический;
- наибольшие линейные перемещения мм:
по оси X( при скорости 08 мс) -1080
по оси r( при скорости 04 мс) -500
- наибольшие угловые перемещения град:
(при скорости 153радс=90градс) -100
(при скорости 076радс=45градс) -90
(при скорости 153радс=90градс) -90
Помимо перечисленного оборудования в состав РТК входят магазин-накопитель заготовок и деталей со специальной тарой оснащенных специальной технологической оснасткой для укладки и ориентации заготовок с возможностью захватывания ПР.
2.2. Захватное устройство.
Захватное устройство ПР предназначено для базирования и удержания объекта в определенном положении при манипулировании. На листе графической части 9 показана конструкция двух позиционного захватного устройства для деталей типа стойка. За счет профилирования губок схвата достигается высокая стабильность установки (005 007 мин).
Схваты роботов осуществляют функции: удерживают объект манипулирования во время его транспортирования; базируют положения объекта манипулирования относительно манипулятора. Схваты удерживают объект манипулирования с помощью сил трения возникающих при кинематическом воздействии его элементов на объект манипулирования фиксации объекта манипулирования по имеющимся на нем выступам отверстиям штифтам позам и другим поверхностям которые могут быть использованы в качестве баз а также электромагнитных сил и вакуума.
При выборе типа схвата необходимо учитывать множество факторов основными из которых являются свойства объекта манипулирования масса форма и ее изменения в процессе обработки на технологическом оборудовании требования к времени захвата и точности удерживания свойства захватываемой поверхности.
Исходные данные: масса объекта манипулирования 17 кг; Расчет сил действующих в местах контакта ЗУ с объектом манипулирования ведем согласно указаниям. Составляем расчетную схему (рисунок 1). Тогда силы N1 и N2 определяются следующим образом:
Где Rn - сила реакции на п-ю губку захвата;
Rn = mg = 2238* 9.8 =21932 H
jj- угол между проекцией силы Rn на плоскость и силой Ni
m- коэффициент трения губки захвата с заготовкой;
Имеем из уравнения (10.1):
где - коэффициент трения
Рис. 3.3. Расчетная схема для определения сил
Усилие удержания заготовки F Н:
В качестве привода ведущего звена используем гидроцилиндр
Такой привод имеет следующие преимущества:
-простота управления;
-невысокая стоимость;
-отсутствие источников загрязнения;
-пожаро- и взрывобезопасность.
Недостатками пневматических приводов является: необходимость устройств подготовки сжатого воздуха невысокая статистическая жесткость.
Определим диаметр поршня привода схвата из соотношения
где Р- усилие привода схвата
- давление энергоносителя для пневмопривода 04мПа;
- КПД привода =085 095;
Диаметр поршня привода принимаем 1700 мм.
2.3. Расчет производительности.
Для расчета производительности необходимо показать алгоритм работы роботизированного комплекса который приведён в таблице 3.1.
Исходное положение: Рука ПР во втянутом положении находится перед рабочей зоной станка захватное устройство (ЗУ) разжато.
Останов станка открытие ограждения.
Снятие детали со станка.
Выдвижение руки робота на линию центров
Разжим кулачков патрона.
Сдвиг каретки вправо
(вывод детали из патрона)
Задвижение руки робота.
Перемещение каретки ПР к магазину накопителю(в отсек с готовыми деталями)
Выдвижение руки робота
Втягивание руки на 1500 мм
Перемещение каретки ПР к магазину накопителю(в отсек с заготовками)
Зажим ЗУ(захват заготовки)
Снятие детали и установка новой заготовки
Задвижение руки робота
Сдвиг каретки вправо(к шпинделю станка)
Сдвиг каретки влево(ввод заготовки)
Зажим кулачков патрона
Для определения длительности цикла работы комплекса с учетом перекрытия (совмещения) времени выполнения отдельных приемов и действий необходимо построение циклограммы работы РТК.
Циклограмму отроим в масштабе 1с = 1 мм в соответствии с разработанным алгоритмом работы. Циклограмма представлена на 8 листе графической части.
Определяем длительность цикла работы Тц = 57+143=200с=335мин.
По циклограмме определим время простоев оборудования:
Простой станка Тпр1 = 57с =095мин.
Простой ПР Тпр = 200-57=143с=24мин.
Производительностью РТК называется количество обрабатываемого продукта в единицу времени. Зная период рабочего цикла определяем цикловую производительность РТК. Методика расчета представлена в 5.
Расчет номинальной сменной производительности:
Qц=480335 =14328 (3.7)
Принимаем Qц= 143 шт.
Рассчитаем фактическую сменную производительность:
где - коэффициенты потерь
- коэффициент учитывающий простои по техническим причинам;
- коэффициент учитывающий потери времени на переналадку оборудования;
- коэффициент потерь по организационным причинам.
Сравним полученный результат с требуемой производительностью для чего предварительно определим такт выпуска по формуле:
где - суммарный объем выпуска по всей номенклатуре деталей закрепленных за РТК N=85400 шт.
Fд- эффективный годовой фонд времени работы оборудования
Fд =3470 ч- для двухсменного работы РТК
Fд =5120 ч- для трехсменного работы РТК
Тогда для двухсменного режима работы РТК
для трехсменного работы РТК
Тогда требуемая производительность
Qсм2=480243=1973Принимаем Qсм2=197 шт.
Qсм3=480359=1337шт. Принимаем Qсм3=138 шт.
- сменная производительность деталей (изделий) в смену.
- продолжительность рабочей смены;
- длительность (время) цикла мин;
Окончательно получаем шт.
Принимаем ёмкость магазина накопителя .
Получено повышение производительности.
Таким образом обработка детали в РТК производительнее чем обычная обработка Это в свою очередь означает что автоматизация данного технологического процесса целесообразна.
Исследовательский раздел.
1. Анализ методов получения заготовок литьём.
Литейное производство занимает ведущее положение в производстве заготовок деталей для всех отраслей современного машиностроения. При изготовлении машин на отливки приходится в среднем более 20% их себестоимости и трудоемкости. Такое его значение объясняется целым рядом серьезных преимуществ перед другими способами получения заготовок среди которых первым следует назвать возможность изготовления отливок практически любой конструктивной сложности; вторым — возможность получения заготовок— отливок с минимальным объемом механической обработки требуемой для получения готовой детали и третьим вытекающим из двух первых — обеспечение наиболее высокого коэффициента использования металла (КИМ) при изготовлении деталей машин.
Отливки изготавливаются из самых различных литейных сплавов. При этом однако эти сплавы должны удовлетворять определенным требованиям в отношении необходимого уровня их литейных свойств.
В нашей промышленности существуют различные технологические процессы получения заготовок методом литья. Самым распространенным и универсальным является литье в разовые песчаные формы. Используется литье в разовые керамические формы в постоянные металлические формы. Изготавливаются отливки методом литья под давлением центробежным способом и др. Все эти технологические процессы имеют определенные возможности и области применения.
Изготовление отливок в песчаных формах
Назначение литейной формы состоит в том чтобы обеспечить необходимую конфигурацию и размеры отливок заданную точность и качество поверхности определенную скорость охлаждения залитого металла способствующую формированию надлежащей структуры и качества отливки. Элементы песчаной литейной формы показаны на рис. 4.1. «Для изготовления песчаной формы необходимо иметь модельный комплект и другую литейную оснастку. Модельный комплект должен включать в себя всю оснастку для получения полости формы. Он состоит из модели отливки стержневого ящика моделей элементов литниковой системы прибыли и выпора. При необходимости модельный комплект должен включать также шаблоны для контроля размеров и конфигурации формы.
Модель служит для получения отпечатка в форме 1 (рис. 4.1) стержневой ящик — для изготовления стержня 8 который устанавливается в форму с целью создания полости в отливке. Кроме того в литейной форме имеются литниковая воронка 10 стояк 11 зумпф 13 шлакоуловитель 12 и питатели 14 15 представляющие в совокупности литниковую систему. Литниковая система нужна для подвода жидкого металла из заливочного ковша к полости формы . Зумпф предохраняет нижнюю полуформу от размыва и попадания продуктов ее размыва в
полость формы и в отливку. Шлакоуловитель необходим для предотвращения попадания шлака и других частиц в полость формы.
Прибылью 7 называют технологический прилив предотвращающий образование усадочных раковин и пор в теле отливки. Через выпор 5 выходят воздух и газы которые образуются в полости формы во время ее заливки расплавленным металлом. Газы возникают и в порах формовочной и стержневой смесей. Если их не удалять то они могут попасть в отливку образуя газовые раковины. Поэтому для лучшего удаления газов в верхней и нижней полуформах а также в стержнях устраивают вентиляционные каналы 6 способствующие выходу газов.
Уплотнение формовочной смеси 2 в нижних и верхних полуформах как правило выполняют в опоках 3 4 представляющих собой открытые с противоположных сторон металлические ящики. После изготовления полуформ низа и верха и стержней производят сборку форм и их заливку жидким металлом.
После затвердевания и охлаждения отливок до требуемой температуры их извлекают из формы путем разрушения последней на выбивных решетках.
Далее отливки "подвергают обрубке (отделению литниковой системы прибылей заусенцев и других) и очистке затем если необходимо — термообработке. Перед сдачей в механический цех все отливки проходят необходимый контроль. В некоторых случаях литейные дефекты могут быть устранены путем заварки пропитки специальными составами или другими способами.
Рис 4.1. Устройство литейной формы.
Материалы из которых изготовляют песчаные формы называют формовочными. Основные требования предъявляемые к формовочным материалам: огнеупорность низкая стоимость недефицитность нетоксичность долговечность. Различают исходные материалы формовочные смеси для изготовления форм стержневые смеси для изготовления стержней отработанные смеси и материалы для окраски и отделки форм и стержней.
Исходными являются материалы из которых приготовляют формовочные и стержневые смеси а также материалы для окончательной отделки форм и стержней.
Формовочные и стержневые смеси представляют собой предварительно подготовленные взятые в определенной пропорции равномерно перемешанные между собой исходные материалы.
Материалами для окончательной отделки форм и стержней служат огнеупорные литейные краски замазки клеи и другие часто называемые вспомогательными.
Применяется при единичном производстве отливок (ремонтное литье уникальные единичные отливки). Например необходимо изготовить отливку эскизкоторой представлен на рис.4.2 а. Модель изготавливают обычно из дерева наиболее дешевого легко обрабатываемого материала. Размеры модели должны быть больше размеров отливки на величину литейной усадки металла и припуска на механическую обработку (если таковая предусмотрена).
В рассматриваемом случае наиболее простой является формовка по цельной неразъемной модели. Модельные плиты могут быть деревянными или легкими металлическими. Модель устанавливается на модельную плиту 2 где помещают опоку 3 (рис. 4.2. б). Поверхность модели и плиты посыпают разделительным составом (сухим песком) для уменьшения прилипания смеси к оснастке. Затем на модель насыпают формовочную смесь уплотняя ее трамбовкой (ручной или пневматической). Уплотнение повышает проч ность формовочной смеси. После уплотнения смеси счищают ее излишки опоку вместе со смесью и моделью снимают с модельной плиты одновременно поворачивая полуформу на 180° в нескольких местах ее прокалывают стальной проволокой с заостренным концом (душником) для создания вентиляционных каналов. На перевернутую опоку устанавливают вторую опоку 4 таких же размеров в свету модели стояка с воронкой 5 и выпора 6 (рис. 4.2.в) после чего в опоку насыпают формовочную смесь и уплотняют ее. По расположению при заливке формы металлом эта опока называется опокой верха. В верхней полуформе душником накалывают вентиляционные каналы 7. Далее из формы удаляют модели отливки стояка и выпора. Для этого после извлечения моделей стояка и выпора снимают верхнюю полуформу одновременно поворачивая ее на 180°. Модель находящуюся в нижней полуформе осторожно расталкивая извлекают. От отпечатка модели стояка в нижней полуформе вручную прорезают канал через который во время заливки жидкий металл пойдет от стояка в полость формы. Подобный канал прорезают и к выпору. Устраняют возможные дефекты формы возникшие при извлечении моделей и других операциях обдувают обе полуформы сухим сжатым воздухом для удаления возможного засора и производят сборку формы. Готовая форма показана на рис. 4.2. г.
Для получения более высокого качества поверхности отливок используют два вида формовочной смеси: облицовочную и наполнительную. Облицовочной смесью формируют слой формы толщиной 10—50 мм с которым непосредственно соприкасается жидкий металл во время его заливки и последующего охлаждения. Для уменьшения физико-химического взаимодействия между металлом и материалом формы в состав облицовочной смеси вводят более огнеупорные материалы.
Рис. 4.2. Эскиз отливки (а); технологических операций формовки (б в) и собранной формы (г).
Машинная формовка применяется для повышения производительности труда и точности отливок. Существует большое разнообразие формовочных машин упрощенная классификация которых приведена в табл. 4.1. На заводах массового производства (автомобильных тракторных и др.) действуют автоматизированные формовочные линии. На рис. 4.3 приведены схемы некоторых формовочных машин.
Рис 4.3. Схемы уплотнения формовочных смесей.
При уплотнении на встряхивающих формовочных машинах (рис. 4.3. а) модельная плита с моделью 2 опокой 3 и наполнительной рамкой 4 устанавливаются на стол формовочной машины 5. Из бункера сверху в опоку насыпают смесь. Под поршень 6 подается воздух под давлением (5 6) -105 Па поднимающий стол до тех пор пока не откроется выпускное отверстие 7 через которое воздух из-под поршня уходит в атмосферу. Стол при этом резко опускается вниз ударяясь о цилиндр 8. Смесь уплотняется за счет движения по инерции вниз. Так повторяется несколько десятков раз. Смесь хорошо уплотняется у модели верхние же ее слои остаются недоуплотненными. Доуплот-нение осуществляют вручную или допрессовкой на той же машине. Прессование полуформ может быть верхним и нижним. При верхнем прессовании сначала уплотняются слои формовочной смеси расположенные в верхней наполнительной рамке (рис 4.3. б).
При нижнем прессовании: (рис. 4.3 в) сначала уплотняются слои смеси находящиеся на модельной плите и самой модели. Для достижения большей равномерности уплотнения формовочной смеси по высоте опоки прессовая колодка иногда делается профильной повторяя профиль модели. Прессовые формовочные машины производят до 120 полуформ в час с наибольшими размерами опок в свету 760 X 680 X 1 Ю мм.
Разновидностью верхнего прессования является уплотнение формовочной смеси так называемой многоплунжерной прессовой головкой (рис. 4.3. г) состоящей из нескольких десятков независимых друг от друга плунжеров работающих под давлением масла или воздуха. Такое прессование обеспечивает наибольшую равномерность уплотнения по всему объему опоки.
При пескодувно-прессовом уплотнении (рис. 4.3.д) весь процесс осуществляется в два этапа. Сначала в полость заключенную между вертикально расположенными модельными плитами 2 и 3 формовочная смесь 4 подается пескодувным методом с помощью воздушного давления предварительно уплотняясь. Затем модельная плита 3 подается поршнем влево прессуя смесь. По окончании прессования плита 2 сначала отходит влево затем разворачивается вверх занимая положение показанное штрихпунктиром на рисунке. Ком смеси модельной плитой 3 подается влево до упора в предыдущий ком 5 плотно прилегая к ранее изготовленным формам после чего все формы передвигаются влево к заливочной установке. Весь процесс от уплотнения смеси до заливки металлом автоматизирован. Производительность автоматизированной формовочной линии составляет 360 форм в час и более (при наличии стержней — 300 форм в час). Существует также процесс вакуумно-прессового уплотнения форм.
При гравитационном уплотнении (рис. 4.3. е) смесь поднимается на определенную высоту в бункер 1 из которого через шибер 2 попадает в дозатор 3. Благодаря быстрому открыванию дна дозатора 4 смесь в виде компактного кома по шахте 5 свободно падает в опоку или стержневой ящик б.* Уплотнения только гравитационным способом недостаточно. Поэтому для доуплотнения применяют подпрессовку усилием (5 10) 105 Па (гравитационно-прессовый способ) или вибрацию (гравитационно-вибрационный способ).
При единичном и мелкосерийном производстве крупных отливок для уплотнения форм используют пескометный способ (рис. 4.3.ж).
Формовочная смесь ленточным транспортером подается на быстро вращающийся ротор с ковшом. Последний захватывая смесь бросает ее в опоку установленную на модельной плите (или в стержневой ящик) производя таким
образом уплотнение. Пескометная головка может перемещаться в горизонтальной плоскости. Управление пескометом осуществляется оператором наблюдающим одновременно за процессом наполнения опоки. Производительность пескометов колеблется от 6 до 50 м3ч уплотненной формовочной смеси.
При изготовлении форм импульсным методом (рис. 4.3.з) на модельную плиту 1 с вентами 2 (тонкие отверстия через которые проходит воздух но не проходит смесь) устанавливаются опока 3 и наполнительная рамка 4 после чего они заполняются формовочной смесью. Над наполнительной рамкой устанавливается импульсная головка 5 и вся оснастка прижимается друг к другу (герметизируется). Из специальной магистрали 6 в ресивер 7 головки поступает сжатый воздух. При уплотнении запорный клапан 8 поднимается вверх пропуская сжатый воздух через отверстие 9 в полость 10. Из полости 10 через отверстия 11 воздух устремляется в полость прессования 12 уплотняя смесь 13. Пройдя через смесь воздух уходит в атмосферу через венты 2. При этом давление над смесью от максимального падает до атмосферного за доли секунды. Под действием сжатого воздуха смесь наполнительной рамки перемещается в опоку и уплотняется. Уплотнение производится однократным импульсом.
Специальные способы литья
Отличительными особенностями отливок получаемых специальными способами по сравнению с литьем в песчаные формы являются как правило их более высокая точность лучшее качество поверхности меньшие величины припусков на механическую обработку.
Литье в кокиль. Кокиль — это литейная форма изготовленная из металла. Основные достоинства кокилей по сравнению с песчаными формами — более высокие производительность труда точность отливок качество их поверхности.
Кокили бывают неразъемные (вытряхные) и разъемные рис. 4.4. Все применяемые типы кокилей могут быть одно-гнездные и многогнездные (т. е. для получения одной отливки или нескольких) немеханизированные (ручные) механизированные автоматизированные и автоматические.
Материалы используемые для изготовления кокилей должны хорошо противостоять термическим ударам возникающим при заливке металла иметь высокие механические свойства при повышенных температурах хорошо обрабатываться быть недефицитными и недорогими. Наиболее полно этим требованиям удовлетворяет чугун иногда используют сталь алюминиевые и другие сплавы. Для мелких отливок из чугуна и стали материалом кокилей является чугун легированный хромом и никелем. Кокили для средних и крупных отливок из черных сплавов изготавливают из сталей легированных хромом молибденом и никелем Формы для отливок из алюминиевых и магниевых сплавов выполняют из серого чугуна а также из алюминиевых сплавов.
Удаление газа из рабочей полости кокиля во время заливки металла осуществляется по разъему формы. Кроме этого в плоскости разъема делают специальные каналы а в стенках формы — вентиляционные пробки через которые дополнительно удаляется газ.
Подвод металла в кокилях осуществляют сверху снизу (сифоном) или сбоку через щелевые питатели. При подводе металла сверху возможно его разбрызгивание в полости формы. Поэтому такой подвод осуществляется для несложных отливок имеющих небольшую высоту. При подводе металла снизу (сифоном) металл
поступает плавно рис. 4.5. Для ослабления удара падающей струи применяют зигзагообразные стояки 1.
Рис. 4.4. Разновидность кокилей.
Рис. 4.5. Кокиль с зигзагообразным стояком и щелевым питателем.
Литье по выплавляемым моделям. Сущность способа со
стоит в получении специальных моделей из легкоплавких
материалов сборке их в блоки покрытии модельных бло
ков огнеупорной оболочкой удаление моделей прокаливание оболочковых форм и заливки в них жидкого метала. К преимуществам литья по выплавляемым моделям относят возможность получения сложных отливок из разнообразных сплавов.
В зависимости от механизма удаления моделей из оболочек их материалы можно разделить на выплавляемые растворяемые и выжигаемые. Наиболее широко распространенные составы выплавляемых моделей содержат парафин ■стеарин буроугольный и торфяной воски (битумы) этил-целлюлозу натуральный и синтетический церезин и др. Основными составляющими растворяемых моделей являются: карбамид азотные и азотнокислые соли щелочных металлов и некоторые другие вещества. К третьей группе модельных материалов следует отнести вспенивающиеся и компактные термопласты (полистирол блочный вспенивающийся суспензионный).
Центробежное литье. Центробежным литьем называют способ изготовления отливок при котором металл заливается в форму и затвердевает в ней под действием центробежных сил. Расплавленный металл заливается во вращающуюся форму приводимую в движение специальной машиной называемой центробежной. Различают машины с вращением формы вокруг вертикальной и горизонтальной (или наклонной ) оси рис. 4.6.
Центробежным способом литья с вращением формы вокруг горизонтальной оси получают отливки типа тел вращения: трубы кольца втулки гильзы и т. д. На машинах с вращением формы вокруг вертикальной оси кроме отливок типа тел вращения получают также фасонные отливки имеющие сравнительно тонкие стенки. Центробежные силы в этом случае используют для улучшения заполняемое формы металлом и получения более плотной отливки. Центробежный способ литья позволяет изготовлять также .двухслойные биметаллические отливки (отливки из двух различных сплавов). При нем заливают сначала сплав одного состава затем другого.
В России центробежным способом получают корпуса полых валов из коррозионно-стойких сталей диаметром до 1500 мм длиной до 10 м массой до 60 т; налажено производство биметаллических прокатных валков (с наружным слоем имеющим повышенную износостойкость и внутренним слоем с повышенной пластичностью); выпускают крупные биметаллические втулки диаметром более 1000 мм для подшипников жидкостного трения и многие другие
При центробежном литье применяют в основном три типа литейных форм: металлические нефутерованные металлические футерованные и разовые формы изготовляемые различными методами. Металлические футерованные формы применяют при литье труб втулок и т. д. имеющих сложный наружный профиль затрудняющий свободную усадку.
Разовые формы применяют при изготовлении центробежным литьем фасонных отливок. При этом формы могут быть получены различными способами: по выплавляемым моделям из керамических стержней из песчаных смесей.
При необходимости такие формы заливают в вакууме или среде нейтральных газов. С этой целью вращающееся устройство в котором установлена форма закрывается герметично неподвижным кожухом соединенным с устройством для вакуумирования или баллонами с нейтральными газами. Так заливают турбинные лопатки турбинные колеса из легко окисляющихся сплавов и т. п. детали.
Рис. 4.6. Центробежное литье.
Литье под давлением. Сущность процесса состоит в том что жидкий металл поступает в рабочую полость металлической формы (пресс-формы) под давлением составляющим (300 3000)-105 Па. Скорость впуска металла в полость формы составляет 05 140 мс. Литьем под давлением получают отливки массой от нескольких граммов до нескольких десятков килограммов по сложности —от элементов замка «молния» до блока цилиндров в автомобиле «Волга». При массовом производстве литье под давлением является весьма рентабельным. Отливки получаемые этим способом имеют самый высокий коэффициент использования металла. Получение ряда деталей литьем под давлением оказывается в 50 раз и более дешевым чем их изготовление из проката механической обработкой. 24 При литье под давлением используют различные машины классификация которых приведена в табл. 4.2.
Работа поршневой машины с холодной вертикальной камерой прессования (рис.4.7.) состоит в следующем. Ось камеры прессования этой машины располагают параллельно плоскости разъема пресс-формы 3. Металл заливают на ниж ний поршень 4 камеры который не позволяет проникать ему в форму.
Жидкий металл будет заходить в литниковое отверстие 5 и полость формы после опускания вниз прессующего поршня 2 в результате чего нижний поршень 4 отжимаясь вниз откроет литниковое отверстие. Металл войдя в контакт со стенками формы затвердевает. Прессующий поршень поднимается вверх освобождая путь нижнемупоршню который при подъеме отрезает пресс-остаток от литника выталкивая его из камеры прессования. Форма очищается смазывается и закрывается. Цикл повторяется.
Ось горизонтальной холодной камеры прессования (рис. 4.7.б) располагают перпендикулярно плоскости разъема формы. Горизонтальная камера связана с неподвижной полуформой 2. Жидкий металл заливают в горизонтальную камеру через специальное окно 3. Поршень 4 двигаясь вправо запрессовывает металл в полость формы. Пресс-остаток захватывается поршнем при холостом ходе и выбрасывается из камеры прессования.
Рис. 4.7. Литье под давлением.
Литье в оболочковые формы. Литейная форма здесь представляет собой оболочку толщиной 6 10 мм изготовленную из дискретной огнеупорной основы (наполнитель) и синтетической смолы в качестве связующего. Принцип получения оболочек заложен в свойствах связующего материала способного необратимо отверждаться при нагревании. Литьем в оболочковые формы изготовляют отливки средней массы 5 15 кг (редко 100 150 кг) практически из любых сплавов. Расход смеси уменьшается в 10 12 раз по сравнению с литьем в обычные песчаные формы.
В качестве огнеупорной основы широко используют кварцевый песок. Повышение содержания примесей в песке приводит к увеличенному расходу связующего повышенной газотворности смеси пониженному качеству поверхности отливок. Ввиду малого расхода и возможности регенерации несмотря на значительное удорожание при литье в оболочковые формы становится рентабельным применять корунд электрокорунд и в особенности циркон. Качество отливок при этом значительно повышается.
Связующим материалом являются фенолоформальдегидные синтетические смолы. Эти смолы при нагревании конденсируются проходя три стадии:
резольную А резитольную В и резитную С. Смола в стадии А плавится жидкоподвижна способна обволакивать тонкой пленкой поверхность зерен огнеупорной основы. Температура плавления составляет 100 200° С. Дальнейший нагрев переводит смолу в стадию В когда она сначала становится вязкой затем резиноподобной. В стадии С смола окончательно отверждается. Начиная с температуры выше 400° С фенолоформальдегид-ная смола подвергается деструкции (т. е. разлагается под воздействием теплоты на элементарные вещества).
Кроме огнеупорной основы и связующего в смеси вводят специальные добавки: растворители (керосин ацетон некоторые спирты и другие вещества уменьшающие количество пыли в смесях и их сегрегацию) смазывающие материалы (стеарат цинка озокерит и др. предотвращающие пригорание смесей к модельной оснастке) и некоторые другие добавки. Существует несколько способов изготовления оболочек: бункерный пескодувный и др. При бункерном способе (рис. 4.8.) на поворотном бункере со смесью 2 закрепляется предварительно нагретая до 200 270° С модельная металлическая плита с моделью 3 (рис. 11а) после чего бункер поворачивается на 180° С. Смесь падает на модельную плиту облегая всю ее рабочую поверхность (рис. 4.7.6). Синтетическая смола прилегающей к модельной плите смеси нагревается расплавляется затем отверждается. Толщина слоя зависит от времени выдержки смеси на модели ее температуры и теплофизических свойств наполнителя. При достижении необходимой толщины бункер поворачивается в исходное положение. Непрореагировавшая смесь с модельной плиты ссыпается вниз (рис. 11 в). Для лучшего и более быстрого отверждения смеси модельная плита с оболочкой подается в печь нагретую до температуры 280 320° С где идет окончательный процесс конденсации смолы. После отверждения оболочка снимается с модельной плиты и направляется на сборку форм. Весь процесс получения оболочек длится несколько минут. Съем оболочек осуществляется специальными толкателями монтируемыми на каждой модельной плите. Параллельно по такой же технологии изготавливают вторую полуформу (оболочку) а также стержни которые могут быть сплошными или полыми. Полые или оболочковые стержни полученные рассматриваемым процессом в последние годы начали использовать не только при литье в оболочковые формы но и при обычном литье в песчаные формы.таких стержней на 40 80% меньше массы сплошных они легко выбиваются из отливок формируют высокое качество поверхности и т. д
Рис. 4.8. Бункерный способ получения оболочковых полуформ.
Производственные расчеты и
разработка планировки.
Время обработки детали(Тш-к)
Годовой объем выпуска деталей NS =61400 шт.
1. Транспортная и складская система.
Одними из основных функций транспортной системы являются:
Прием со склада единиц и доставка к соответствующим позициям системы.
Функция возврата грузовых единиц;
Функция межоперационного транспортирования;
Функция обмена грузовых единиц между транспортом.
Выбор вида и конструкций транспортных устройств зависит от степени совмещения складирования и транспортирования.
Учитывая характер проектируемого участка выбираем АТСС с краном - штабелером и совмещенными системами складирования и транспортирования.
Для обслуживания склада выбираем кран – штабелер модели
СА –ТСС – 05 который обладает следующими техническими характеристиками:
грузоподъемность – 500 кг.
высота стеллажа – 5200 мм.
Скорость передвижения крана штабелера (Х – 96 ммин Y – 18 ммин).
Расположим склад вдоль линии станков. Оборудование будет располагаться в два ряда с учетом размеров системы.
Также складская система содержит пристаночные магазины накопители заготовок тару с готовыми деталями промежуточные накопительные станции общецеховые склады.
2. Расчёт количества станков на участке степень их
загрузки и использования.
Расчетное количество станков[25]:
гдеТ –суммарная станкоемкость обработки годового количества деталей на станках данного типоразмера ст-ч.
Фо –эффективный годовой фонд времени работы оборудования ч.
Рассчитаем количество токарных станков 16К20Ф3:
Фо=3935 ч – для станков с ЧПУ
Определим коэффициент загрузки токарных станков:
где - расчётное количество оборудования
- принятое количество станков.
Ки - коэффициент использования станка принимаем равным 1.
Количество станков с учётом коэффициента использования:
Таким образом для проектируемого участка окончательно принимаем два станка модели СВМ1 Ф4.
Для остального оборудования расчёт производится аналогично и сводится в
Количество станков – 6
Средний коэффициент загрузки станков Кз = 0776
Габаритные размеры станков (мм):
П756ДФ3 3825×2140×2640
3. Проектирование системы удаления стружки.
Для выбора способа удаления и переработки стружки определяют её количество образующееся на 1м2 участка в год.
Данные расчёта представим в виде таблицы 5.2..
Годовой объем выпуска
Вес стружки за год ткв.м
Площадь участка 484 м2. На 1м2 приходится 14 тонн в год. По результатам расчета принимаем для удаления стружки ленточный конвейер.
4. Численность производственных рабочих.
В непоточном производстве число рабочих Рс обслуживающих участок механической обработки определим по формуле [5.4]:
Кз – коэффициент загрузки станка;
Фр – эффективный годовой фонд времени работы рабочего чел-ч;
Км – коэффициент многостаночного обслуживания;
Ки - коэффициент использования станка;
Фо – эффективный годовой фонд времени работы оборудования ч;
Станок 16К25Ф3: Принимаем: 1 чел.
Станок 1П756ДФ3: Принимаем: 3 чел.
Станок СВМ1Ф4: Принимаем: 2 чел.
Таким образом общее число рабочих – станочников при двухсменном режиме работы равно 6.
Безопасность и экологичность проекта.
Обеспечение безопасности жизнедеятельности человека является важнейшей проблемой современности. Научно-технический прогресс наряду с благами принес и неисчислимые бедствия связанные с травмоопасностью и аварийностью производства его экологической опасностью повышением риска гибели человека.
Ежегодно в стране происходит около 19 млн. несчастных случаев. Растет число крупных промышленных аварий с тяжелыми последствиями усугубляется экологическая обстановка.
Безопасность – одна из самых запущенных сторон деятельности в нашей стране. В связи с этим важнейшее социальное и экономическое значение имеет решение проблем безопасности жизни и деятельности человека в условиях современного производства и в среде обитания.
Целью данного раздета является систематизация и практическая реализация знаний в решении инженерных задач в области безопасности производственной деятельности экологии профилактики прогнозирования и ликвидации последствий чрезвычайных ситуаций.
1.1 Анализ опасных и вредных производственных факторов условий труда на рабочих местах выбор методов и средств защиты при выполнении технологического процесса
Условия труда на рабочих местах производственных помещений и площадок складываются под воздействием большого числа факторов различных по своей природе формам проявления характеру действия на человека. При механической обработке металлов пластмасс и других материалов на металлорежущих станках (токарных фрезерных сверлильных шлифовальных заточных и др.) возникает ряд физических химических психофизиологических и биологических опасных (ОФ) и вредных (ВФ) производственных факторов. Они подразделяются по своему действию на группы в соответствии с ГОСТ 12.01.003-74 ( СТ СЭВ 790-77).
В состав проектируемого участка входят:
)моечно-сушильный агрегат;
Исходя из состава участка проанализируем создаваемые на нем ОФ и ВФ.
Движущие части производственного оборудования передвигающиеся изделия и заготовки стружка обрабатываемых материалов осколки инструментов высокая температура поверхности обрабатываемых деталей и инструмента повышенное напряжение в электроцепи или статического электричества при котором может произойти замыкание через тело человека - относятся к категории физически опасных факторов.
Так при обработке хрупких материалов (чугуна латуни бронзы графита карболита текстолита и др.) на высоких скоростях резания стружка от станка разлетается на значительное расстояние (3-5 м).
Металлическая стружка особенно при точении вязких металлов (сталей) имеющая высокую температуру (400-600 С) и большую кинетическую энергию представляет серьезную опасность не только для работающего на станке но и для лиц находящихся вблизи станка. Наиболее распространенными у станочников являются травмы глаз. Глаза повреждались отлетающей стружкой пылевыми частицами обрабатываемого материала осколками режущего инструмента и частицами абразива.
Физическими вредными производственными факторами характерными для процесса резания являются повышенная запыленность и загазованность воздуха рабочей зоны высокий уровень шума и вибрации недостаточная освещенность рабочей зоны наличие прямой и отраженной блескости повышенная пульсация светового потока.
При отсутствии средств защиты запыленность воздушной среды в зоне дыхания станочников при точении фрезеровании и сверлении хрупких материалов может превышать предельно допустимые концентрации. Размер пылевых частиц в зоне дыхания колеблется в широком диапазоне - от 2 до 60 мкм. При работе режущим тупым инструментом происходит интенсивное нагревание вследствие чего пыль и стружка превращаются в парообразное и газовое состояние а иногда возникает воспламенение материала например при обработке текстолита. Таким образом при обработке пластмасс в воздух рабочей зоны поступает сложная смесь паров газов и аэрозолей являющихся химическими вредными производственными факторами.
Продукты термоокислительной деструкции (предельные и непредельные углеводороды а также ароматические углеводороды) могут вызывать наркотическое действие изменения со стороны центральной нервной системы сосудистой системы кроветворных органов внутренних органов а также кожно-трофические нарушения. Аэрозоль нефтяных масел входящих в состав смазывающе-охлаждающей жидкости (СОЖ) может вызывать раздражение слизистых оболочек верхних дыхательных путей способствовать снижению иммунобиологической реактивности.
Кроме того самым существенным решением с точки зрения безопасности является введение комплексной автоматизации которая позволила сократить численность рабочих непосредственно находящихся у станка.
По степени поражения человека электрическим током проектируемый участок относится к помещениям с повышенной опасностью поскольку имеются в наличие три условия создающих повышенную опасность:
)токопроводящая металлическая технологическая пыль;
)токопроводящие железобетонные полы;
)возможность одновременного прикосновения человека к имеющим соединение с землей металлоконструкциям складов технологическому оборудованию и к металлическим корпусам электрооборудования.
Основные меры защиты от поражения током:
обеспечение недоступности токоведущих частей находящихся под напряжением для случайного прикосновения (изоляция расположение их на недоступной высоте и т.д.);
электрическое разделение сети на отдельные электрически не связанные между собой участки с помощью специальных разделяющих трансформаторов;
устранение опасности поражения при появлении напряжения на корпусах кожухах и других частях электрооборудования что достигается использованием двойной изоляции выравниванием потенциала защитным заземлением занулением защитным отключением и др.;
организация безопасной эксплуатации электроустановок.
Микроклимат на рабочем месте в производственных помещениях определяется температурой воздуха относительной влажностью скоростью движения воздуха барометрическим давлением и интенсивностью теплового излучения от нагретых поверхностей.
На микроклимат на участке существенное влияние будет оказывать исправность и режим работы моечно-сушильного агрегата который использует процессы мойки связанные с повышенной влажностью и сушки связанные с нагревом. Кроме того в значительно меньшей степени на микроклимат будут влиять технологические процессы резания (нагрев использование СОЖ) а также нагрев электрооборудования.
Уровень шума не должен превышать 80 дБА.
На случай пожара в цехе должны быть предусмотрены
На участке должна быть естественная и общеобменная вентиляция.
Возможно применение местная вентиляция обеспечивающей удаление пыли мелкой стружки и аэрозолей СОЖ из рабочей зоны станков.
К психофизиологическим вредным производственным факторам процессов обработки материалов можно отнести физические перегрузки при установке закреплении и съеме крупногабаритных деталей перенапряжение зрения монотонность труда.
К биологическим факторам относятся болезнетворные микроорганизмы и бактерии проявляющиеся при работе с СОЖ.
1.2Требования безопасности к автоматизированным участкам
Современные машиностроительные предприятия оснащаются самыми различными видами технологического оборудования. Его использование облегчает труд человека делает его более производительным. Однако в ряде случаев работа этого оборудования связана с возможностью воздействия на работающих опасных и вредных факторов. Основным направлением облегчения и оздоровления труда повышение его производительности является механизация и автоматизация работ и технологических процессов.
Механизация способствует ликвидации тяжелого физического труда снижению травматизма уменьшает численность персонала. Особое значение с точки зрения охраны труда имеет механизация подачи заготовок в рабочую зону при обработке. Автоматизация – высшая ступень механизации способствует ликвидации существенного различия между умственным трудом и физическим. При комплексной автоматизации ТП выполняются последовательно без вмешательства человека.
Применение управляющих машин экономит усилия работника ускоряет выполнение операции и значительно облегчает труд. Ведение ПП при помощи управляющих машин исключает ошибки всегда возможные при непосредственном управлении. Применение управляющих машин не только облегчает труд но и делает его безопасным.
Создание ГАП не является чисто технической задачей. Поэтому для достижения ожидаемого от комплексной автоматизации эффекта необходимо прежде всего в основу оптимального функционирования любой автоматизированной производственной системы ее элементных технологий закладывать требование
решения двух взаимосвязанных задач обеспечение конечной цели производства и обеспечения безопасности трудового процесса.
Поэтому наличие и количество опасных и вредных производственных факторов вероятность возникновения опасных (ОС) критических (КС) и аварийных ситуаций (АС) формирующих несчастные случаи или аварии степень и характер их отрицательного воздействия на окружающую среду или производственный персонал представляют собой один из главных комплексных показателей качества любого автоматизированного комплекса или гибкой производственной системы (ГПС).
Основной базой технических средств для создания ГАП в настоящее время являются серийно выпускаемые металлорежущие станки с ЧПУ. В исходном состоянии они не отвечают ни требованиям безопасности ни требованиям ГАП. Расширение их возможностей за счет объединения их в управляемые от ЭВМ гибкие автоматизированные комплексы с автоматическими складами и транспортом без системного анализа оценки степени и характера отрицательного воздействия опасных и вредных производственных факторов на человека и окружающую среду разработки эффективных средств контроля и управления средствами обеспечения безопасности ПП может привести не только к появлению гибких производственных систем с высокими уровнями скрытой потенциальной опасности но и к непредвиденным в недалеком будущем отрицательным социальным последствиям.
Установлено что наиболее травмоопасной ситуацией является прямой контакт «человек-машина» когда человек выполняет такие операции как перепрограммирование наладку ремонт установку снятие инструмента монтаж смазку или чистку. Наибольшему риску быть травмированными с этой точки зрения подвергаются работники следующих профессий требующих прямого контакта с оборудованием: слесари-монтажники сборщики электротехники наладчики бригадиры.
Операторы обслуживающие автоматизированные комплексы значительно реже подвергаются риску быть травмированными по сравнению с этими видами профессий. Это объясняется тем что при возникновении каких-либо проблем связанных с вынужденной остановкой оборудования снижением его производительности качества выпускаемой продукции выходом из строя и т.п. выявлением причин и устранением неисправностей занимаются специалисты с высоким уровнем подготовки.
Основными причинами формирующими ОС КС и АС при эксплуатации ГПС по ГОСТ 12.2.072-82 «ССБТ. Роботы промышленные роботизированные технологические комплексы и участки. Общие требования безопасности» являются:
непредусмотренные движения исполнительных устройств оборудования при наладке ремонте во время обучения и исполнения управляющей программы;
внезапный отказ в работе технологического оборудования совместно с которым работает ПР;
ошибочные действия оператора или наладчика во время наладки и ремонта при работе в автоматическом режиме;
доступ человека в рабочее пространство ПР функционирующего в режиме исполнения программы;
нарушение условий эксплуатации;
нарушение требований эргономики и безопасности труда при планировке участка (размещение технологического оборудования ПР пультов управления загрузочных и разгрузочных устройств. накопителей транспортных средств и др.).
1.3. Требования к размещению оборудования и организации рабочих мест
Планировка участка должна обеспечивать свободный доступ обслуживающего персонала к основному и вспомогательному оборудованию к органам управления и аварийного отключения всех видов оборудования и механизмов входящих в их состав. При организации участков необходимо предусматривать максимальную автоматизацию основных и вспомогательных и технологических операций и видов работ связанных с взаимодействием на работающих опасных и вредных факторов оставляя за операторами функции управления и контроля.
При манипулировании и перемещении заготовок готовых изделий и т.п. вблизи рабочих мест устанавливают защитные сетки и другие устройства исключающие травмирование персонала при случайном падении предметов манипулирования.
Пульт управления размещается по ГОСТ 22269-76 за пределами зоны ограждения с обеспечением оператору возможности хорошего обзора за работой оборудования входящего в состав комплекса и окружающего его пространства.
Освещенность пультов управления должна составлять по ГОСТ 12.2.072-82 не менее 400 лк. Освещенность в рабочей зоне устанавливается СниП II-4-79 и отраслевыми нормами.
Оборудование и механизмы образующие в процессе производства вредные газы аэрозоли излучения требующие использования технологических жидкостей с вредным эффектом должны оснащаться устройствами и механизмами обеспечивающими нормализацию воздушной среды производственных помещений. Так агрегаты машины механизмы и другие устройства которые в процессе производства образуют пыль мелкую стружку выделяют вредные жидкости газы и т.п. оснащаются пылеприемники газоулавливающими и другими устройствами для отсоса из зоны обработки загрязненного воздуха и его очистки.
2.Меры безопасности при работе с СОЖ.
2.1.Экологический анализ проекта выбор методов и средств защиты от негативных воздействий проектируемого участка
Экологическая безопасность проекта обеспечивает следующим образом. На проектируемом участке применяется СОЖ – 3-4% эмульсия МГЛ-205 и индустриальное масло И-20. Отработанные СОЖ собирают в специальные емкости. Водную и масленую фазу используют в качестве компонентов для приготовления эмульсий. Масляная фаза эмульсий поступает на регенерацию или сжигается. Концентрация нефтепродуктов в сточных водах при сбросе их в канализацию соответствует требованиям СН и П II-32-74. Водную фазу СОЖ очищают до ПДК или разбавляют до допустимого содержания нефтепродуктов и сливают в канализацию. Нормы шума на рабочих местах регламентируются ГОСТ 12.1.003-83 «ССБТ. Шум. Общие требования безопасности». Стружка удаляется из цеха и поступает на переработку а СОЖ после дополнительной очистки и охлаждения снова подается к режущим инструментам.
2.2.Меры безопасности при работе с СОЖ
При механической обработке деталей используются СОЖ и рабочие подвергаются действию этих соединений. Это воздействие осуществляется двояким путем: на кожу при контакте с маслами и эмульсиями и через органы дыхания куда куда поступает смешанный аэрозоль образующийся при разбрызгивании СОЖ.
Основные мероприятия по оздоровлению производственной среды должны осуществляться на базе комплексной механизации и автоматизации процессов механической обработки металла позволяющих почти полностью устранить или резко сократить с СОЖ и его аэрозолями.
В связи с широким внедрением в промышленность скоростных режимов резания новых технологических процессов с применением многокомпонентных СОЖ с химическими активными присадками особое значение приобретают требования к конструкции новых станков в частности к более полному укрытию местного эффективного отсоса что позволяет снизить содержание аэрозоля до допустимых величин.
Эффективна замена масляного охлаждения эмульсионных т.к. при его использовании концентрация масляного аэрозоля и углеводов в рабочей зоне не превышает предельно допустимых значений а окись углерода и другие продукты термораспада не обнаруживаются.
В проекте детали обрабатываются на станках с ЧПУ которые позволяют вести обработку деталей практически без участия работающего следовательно контакт с аэрозолями СОЖ почти полностью устранен.
Необходима так же централизованная подача СОЖ и периодическая очистка от примесей не реже одного раза в месяц. Очистку следует проводить с применением антимикробных добавок.
Для защиты кожных покровов большое значение имеет снабжение работающих спецодеждой из легкой гладкой мягкой непромокаемой и непроницаемой для охлаждающих масел и жидкостей тканей.
Должны проводиться периодические медицинские осмотры не реже одного раза в два года.
Важную роль в обеспечении функциональной пригодности СОЖ наряду с выбором ее вида и марки играют процессы очистки и регенерации СОЖ. Таким образом удается не только экономить СОЖ но и уменьшать количество отходов сбрасываемых в окружающую среду.
3.Безопасность проекта в чрезвычайных ситуациях
3.1.Анализ вероятных ЧС техногенного антропогенного и природного характера на проектируемом участке
В соответствии со строительными нормами и правилами (СН и П II-90-81) производственные и склады по взрывной взрывоопасной и пожарной опасности подразделяются на место категорий: А Б В Г Д е. Проектируемый участок относится к категории Д т.е. производства с непожароопасными технологическими процессами где имеются несгораемые вещества и материалы в холодном состоянии. Все помещения оборудованы средствами пожаротушения по ГОСТ 12.4.009-83. Огнестойкость стен здания повышают облицовкой или огитурированием металлических конструкций. В соответствии с СН и П II-2-80 число эвакуационных выходов из здания помещения и с каждого этажа должно составлять не менее двух. Применяются автоматические средства обнаружения пожаров. Определение концентрации токсичных веществ в зоне аварии производится методом прогнозирования и по данным разведки.
3.2.Обеспечение устойчивости работы проектируемого участка в условиях ЧС.
Под устойчивостью функционирования объекта народного хозяйства понимают способность его в чрезвычайных ситуациях выпускать продукцию в запланированном объеме и номенклатуре а в случае аварии (повреждения) восстанавливать производство в минимально короткие сроки.
На устойчивость функционирования участка в ЧС влияют следующие факторы: надежность защита рабочих и служащих от последствий стихийных бедствий аварий а так же воздействия первичных и вторичных поражающих факторов. ОМП и других современных средств нападения: способность инженерно-технического комплекса объекта противостоять в определенной степени этим воздействием: надежность системы снабжения объекта всем необходимым для производства продукции (сырьем топливом электроэнергией газом водой и т.п.); устойчивость и непрерывность управления производством; подготовленность объекта к ведению С и ДНР и работ по восстановлению нарушенного производства.
Перечисленные факторы определяют и основные требования к устойчивому функционированию участка в условиях чрезвычайных ситуаций и пути его повышения.
Пути и способы повышения устойчивости функционирования участка в условиях чрезвычайных ситуаций в мирное и а военное время весьма многообразны и определяются конкретными специфическими особенностями каждого отдельного предприятия.
Выбор наиболее эффективных путей и способов повышения устойчивости функционирования возможен только на основе всесторонней тщательной оценки каждого предприятия.
Оценка устойчивости объекта к воздействию различных поражающих факторов проводится с использованием специальных методик.
Исходными данными для проведения расчетов по оценке устойчивости участка являются: возможные максимальные значения параметров поражающих факторов; характеристики объекта и его элементов.
Параметры поражающих факторов обычно задаются вышестоящим штабом ГО и ЧС. Однако если такая информация не поступала то максимальные значения параметров поражающих факторов определяются расчетным путем.
Оценка степени устойчивости объекта к воздействию сейсмической (ударной) волны заключается в выявлении основных элементов объекта (цехов участков систем) от которых зависит его функционирование и выпуск необходимой продукции; определенной предела устойчивости каждого элемента и объекта в целом; сопоставление найденного предела устойчивости объекта с ожидаемым значением сейсмической (ударной) волны и заключении о его устойчивости.
Оценка устойчивости объекта к воздействию светового излучения ядерного взрыва заключается в определении максимального значения светового импульса; определим степени огнестойкости зданий и сооружений выявление сгораемых элементов зданий конструкций и веществ; определении значений световых импульсов при которых происходит воспламенение элементов из сгораемых материалов; нахождение предела устойчивости здания к световому излучению и сопоставление этого значения с ожидаемым максимальным световым импульсом на объекте.
Оценка устойчивости объекта к воздействию проникающей радиации ядерного взрыва заключается в определении максимального значения дозы излучения ожидаемой на объекте определение степени поражения людей и повреждения материалов и приборов чувствительных к радиации.
Основные мероприятия по повышению устойчивости проводимые на объектах в мирное время предусматривают: защиту рабочих и служащих и инженерно-технического комплекса от последствий стихийных бедствий аварий а также первичных и вторичных поражающих факторов ядерного взрыва: обеспечение надежности управления и материально-технического снабжения; светомаскировку объекта; подготовку его к восстановлению нарушенного производства и переводу на режим работы в условиях ЧС.
Надежная защита рабочих и служащих является важнейшим фактором повышения устойчивости работы любого объекта народного хозяйства. С этой целью возводятся защитные сооружения: убежища для укрытия наибольшей работающей смены предприятия и ПРУ в загородной зоне для отдыхающей смены и членов семей.
От устойчивости зданий и сооружений зависит в основном устойчивость всего объекта. Повышение их устойчивости достигается устройством каркасов рам подкосов промежуточных опор для уменьшения пролета несущих конструкций.
Невысокие сооружения для повышения их прочности частично обсыпают грунтом.
Основные мероприятия по повышению устойчивости технического оборудования ввиду его более высокой прочности по сравнению со зданиями в которых ого размещается заключаются в сооружении над ним специальных устройств (в виде кожухов зонтов и т.п.) защищающих его от повреждения обломками разрушающихся конструкций.
Электроэнергия должна поступать на объект с двух направлений при питании с одного направления необходимо предусматривать автономный (аварийный) источник (передвижную электростанцию).
Особое внимание должно уделяется устойчивости систем снабжения газом. Вся система газоснабжения закольцовывается что позволяет отключить поврежденные участки и использовать сохранившиеся линии.
Исключительно важное значение имеет создание устойчивой системы водоснабжения объекта. Снабжение водой должно осуществляться от двух источников – основного и резервного один из которых должен быть подземным.
Устойчивость работы объектов во многом определяется также надежностью систем паро - и теплоснабжения. Промышленные объекты должны иметь два источника пара и теплавнешний (ТЭЦ) и внутренней (местные котельные). Котельные необходимо размещать в подвальных помещениях или специальном оборудованном отдельно стоящем защитном сооружении.
Тепловая сеть закольцовывается параллельные участки соединяются. Паропроводы прокладываются под землей в специальных траншеях. На паротепловых сетях устанавливаются запорно-регулирующие приспособления.
Подготовка объектов к восстановлению должна предусматривать планы первоочередных восстановительных работ по нескольким вариантам возможного повреждения разрушения объекта с использованием сил самих объектов имеющихся строительных материалов с учетом при необходимости размещения оборудования на открытых площадках перераспределения рабочей силы помещения и оборудования.
Для своевременного и организованного проведения мероприятий по повышению устойчивости объекта разрабатывается план – график последовательности их осуществления в угрожаемый период.
Организация производства.
1.Организация складского хозяйства
Задачи складского хозяйства заключаются в приеме хранении учете материалов и регулировании уровня их запаса подготовке готовой продукции к отправке потребителю. Важную роль в организации работы складов играет подготовка материалов к выдаче в производство путем организации заготовительных отделений. На складах выполняется большой объем погрузочно-разгрузочных работ работ по перемещению материалов. Поэтому основным направлением в развитии складского хозяйства является комплексная механизация и автоматизация работ улучшение использования складских помещений а также организация материально-технического снабжения на основе оптовой торговли внедрение систем материально-технического снабжения типа «точно вовремя» которые значительно сокращают объем складских запасов.
По функциональному назначению склады подразделяются на заводские и цеховые. Так в составе складов машиностроительного завода могут быть центральный материальный склад (главный магазин) склад металлов склад изделий смежных производств склад запасных частей и оборудования склад шихты и формовочных материалов.
Устройство и оснащение складов зависит от ряда факторов. Определяющие из них – грузооборот длительность хранения вид применяемой тары объем и частота поставок и отправлений вид используемого подвижного состава. В зависимости от этих факторов материалы и готовые изделия могут храниться на специально оборудованных открытых площадках под навесами в отапливаемых и не отапливаемых помещениях. Например тарные и штучные грузы хранятся на стеллажах в штабелях в контейнерах на поддонах с многоярусной установкой.
Для механизации погрузочно-разгрузочных работ и внутри складских операций применяют различные устройства и машины: краны – штабелеры электропогрузчики кран-балки и мостовые краны электрокары и различного рода средства непрерывного транспорта. Для комплексности механизации используют быстродействующие автоматические стропы и захваты. В последние годы получили развитие автоматизированные склады тпрно-штучных грузов оборудованные системами машин обеспечивающими транспортировку; установку и поиск материалов по специальным программам с использованием роботов.
Для комплексной механизации и автоматизации транспортных операций большое значение имеет укрепление грузовых единиц путем применения контейнеров и средств пакетирования (поддоны всех типов стропы кассеты обвязки прокладки и т.п.). Парк контейнеров и средств пакетирования
к=Gk(1+(к.н.+ к.р.) 100)·qk (7.1.)
где Gk – объем перевозок грузов (грузооборот) на расчетный период; к.р – потребность в контейнерах в связи с неравномерностью перевозок нахождением в ремонте % от общего парка; qk – выработка на один контейнер за расчетный период т;
qk=qk.c.(Fk+Fп) Т0 (7.2.)
где qk.c. – статистическая нагрузка контейнера средства пакетирования; т; Fk – число календарных дней в расчетном периоде; Fп – время нахождения контейнеров в простое дн.; Т0 – среднее время оборота контейнера средства пакетирования сут.
Для оценки уровня оснащенности складов погрузочно-разгрузочными средствами и механизмами применяются показатель насыщенности средствами механизации:
где Qп=т – суммарная грузоподъемность всех средств механизации т; Qскл – грузооборот склада за расчетный период т.
Основные направления совершенствования работы транспортного и складского хозяйства – это улучшение структуры парка подъемно-транспортных и транспортных машин внедрение транспортных и складских систем с автоматическим адресованием грузов автоматизированных контейнерных площадок совершенствование организации перевозок и складских процессов.
К технико-экономическим показателям работы транспортного и складского хозяйств относятся: удельный вес транспортно-складских расходов в себестоимости продукции себестоимость перевозки грузов; затраты на Машино-час работы транспортного средства или подъемно-транспортной машины себестоимость складского хранения 1 т. груза и др.
Экономическая оценка проекта.
В данном дипломном проекте проектируется новый производственный участок механической обработки деталей типа зубчатых колес.
Участок разрабатывается на основе анализа базового производственного участка путем его модернизации. Внедряется высокопроизводительное автоматизированное оборудование высвобождаются площади оптимизируются режимы резания повышается безопасность внедряемого оборудования
снижаются затраты на материалы энергоносители уменьшается число рабочих особенно рабочих с низкой квалификацией снижаются затраты на заработную
плату соответственно снижается себестоимость изделия.
Для определения перечисленных показателей используем методику изложенную в [19] а также данные полученные на базовом предприятии во время прохождения преддипломной практики.
ОЖИДАЕМЫЕ РЕЗУЛЬТАТЫ ПРОЕКТА
Размер необходимых инвестиций 81906 тыс. руб.
Срок окупаемости проекта261 года
Чистая дисконтированная стоимость 474545 тыс. руб.
2. Характеристика предприятия
Сильной стороной предприятия является высокая квалификация научно-технического персонала и организация производства.
Слабая сторона это низкая заработная плата и низкая автоматизация и механизация производства.
Основная номенклатура выпускаемых изделий:
-Фонтанная арматура;
- Сёдла клин стойка ;
3. План производства
Исходные данные для расчетов по проектируемому варианту берем из раздела 6 (номенклатура изготовляемых изделий на участке их годовые объемы выпуска количество потребного оборудования и т.д.) и представленного в приложении комплекта технологической документации а также используем данные полученные во время прохождения практики на базовом предприятии.
Годовой объем выпуска деталей обрабатываемых на участке - 85400
Тип производства среднесерийный.
Занимаемая площадь проектного участка S = 484 м2.
Стоимость 1 м2 = 5 000 руб.
Величина капитальных вложений по проектному варианту:
где Кн - стоимость нового оборудования приспособлений и других средств;
Кна - стоимость ликвидируемых в связи с внедрением нового технологического процесса существующих основных средств (учитывается как неамортизированная часть от первоначальной стоимости);
Клик - выручка от реализации внедренного оборудования к концу службы его (ликвидационная стоимость).
Приобретаемое оборудование.
Расчёт капитальных вложений проекта сведён в табл. 8.7.
4. Определение технологической себестоимости
Рассчитываются те статьи себестоимости продукции которые различаются в базовом и проектном вариантах.
Затраты на материал рассчитываются по формуле:
Зм= S(PmiЦmi – Poi Цoi) (8.1)
где Рmi -вес заготовки кг
Цmi -цена кг материала. Для стали Цmi=18 руб.
Цoi -цена кг отходов. Для стали Цoi=064 руб.
m-количество видов деталей
Затраты на энергию рассчитываются по формуле:
Зэ= S tiNiKmKnЭ (8.2)
где ti-штучное время на i-ой операции
Ni -установленная (потребляемая) мощность или расход энергии
Km = 09-коэффициент использования мощности
Kn = 095-коэффициент местных потерь
Э = 18 руб.кВтч - тариф на электроэнергию.
Затраты на заработную плату засчитываются по формуле:
Ззп= S аitiKgKcКдоп (8.3)
где ai-часовая тарифная ставка на i-ой операции
ti-продолжительность технологической операции
Kg-коэффициент доплат к основной заработной плате Kg=115
Kc-коэффициент отчислений на социальные нужды Кс=135
Кдоп -коэффициент дополнительной заработной платы Кдоп=118
Вес стружки за год кг
Цена материала руб кг.
Стоимость материала тыс. руб.
Стоимость стружки тыс. руб.
Стоимость стружки руб.кг
Затраты на электроэнергию.
Затраты на энергию Зэ тыс. руб.
Затраты на заработную плату.
час тариф ставка ai рубч
Затраты на зарплату Зэ тыс. руб.
Затраты на текущий ремонт рассчитываются как 4% от стоимости оборудования.
Затраты на текущий ремонт
затраты на оборудование
затраты на текущий ремонт
Затраты на амортизацию рассчитываются по формуле:
где Fэ - эффективный фонд работы оборудования ч;
Кб - балансовая стоимость оборудования тыс. руб.;
На = 15%-норма амортизации;
Kз -коэффициент загрузки оборудования;
Kв -коэффициент выполнения норм;
Затраты на амортизационные отчисления.
балансовая стоимость тыс. руб.
норма амортизации На
Затраты на аморт. Ззп
Расчет технологической себестоимости.
Производств оборудование
Подъемно-транспортное оборудование
Приспособления и инструменты
Калькуляция себестоимости продукции.
Калькуляция себестоимости продукции
Название статей затрат
Основные материалы за вычетом отходов
энегия и топливо для технологических целей
Основная и дополнительная заработная плата производственных рабочих
Отчисления от заработной платы на социальные нужды
Расходы на содержание и эксплуатацию оборудования
Себестоимость по участку
Для данного дипломного проекта рекомендован сокращённый вариант финансового раздела и упрощённую схему прогнозирования денежных потоков учитывающих инвестиционную деятельность. Прогноз денежных потоков приведён в таблице 7.10.
Коэффициент дисконтирования для года t определяется по формуле:
где r = 022 - ставка дисконта
коэффициент дисконтирования
По таблице 8.10.определяем период окупаемости проекта. Оценка эффективности проекта определяется по показателям чистой дисконтированной стоимости и сроку окупаемости проекта.
Прогноз денежных потоков для проекта участка
Инвестиции в проект участка
Приращения доходов и расходов
затраты на материалы
энергия электрическая
текущий ремонт оборудования
амортизация нового оборудования
отмененная амортизация заменяемого оборудования
Налог на прибыль (24%)
Приращение доходов от инвестиций
Коррекция денежных потоков
Продажа старого оборудования
Остаточная стоимость внедряемого оборудования
Высвобождение площадей
Чистый денежный поток
Коэффициент дисконтирования
Чистая дисконтированная стоимость (ЧДС)
ЧДС нарастающим итогом
Срок окупаемости инвестиций лет
Все расчёты проведены на ЭВМ с помощью пакета EXCEL.
В данном дипломном проекте разработан участок на базе станков с ЧПУ по изготовлению корпусных деталей отвечающим требованиям гибкого автоматизированного производства и экономической эффективности. жизнедеятельности деталям машин и проектированию приспособлений
Для операций механической обработки были разработаны операционные технологические процессы в процессе работы над которыми осуществлялся выбор технологических баз последовательности технологических переходов режимов резания норм времени.
В конструкторском разделе спроектированы и рассчитаны станочные приспособления средства автоматизации.
В исследовательской части проекта раскрыта и проанализирована тема получения заготовок корпусных деталей литьем в кокиль.
В разделе «Безопасность и экологичность проекта» были рассмотрены темы по безопасности труда на проектируемом участке обеспечению экологической безопасности проекта и безопасности проекта в чрезвычайных ситуациях.
В экономической части проанализированы необходимые затраты на инвестиции в проект участка и рассчитана возможная прибыль которая позволит окупить данный проект участка за 2 года и 7 месяцев.
При разработке данного дипломного проекта широко использованы возможности современной компьютерной техники и применены различные технические и графические компьютерные пакеты. Оценка экономической эффективности проектного участка производились при помощи пакета Microsoft Excel. Все листы графической части разработаны с применением графического пакета "Компас 6 – 3D".
Список используемых источников.
Безопасность и экологичность проекта: методические указания к выполнению раздела «Безопасность и экологичность проекта» в дипломных проектах для специальностей 12.01 12.02. – Курган: КМИ 1993. – 33 с.
Выбор способа изготовления заготовок. Методические указания.-Курган: КМИ 1995.-42 с.
Горбацевич А.Ф. Шкред В.А. Курсовое проектирование по технологии машиностроения - Мн: Высш. школа1983.-256 с.
Горошкин А.К. приспособления для металлорежущих станков: Справочник.-7-е изд. перераб. и доп. – М.: Машиностроение1979. – 303 с.
Денисенко Г.Ф. Охрана труда. - М: Высшая школа 1985.-354с.
Инструмент для станков с ЧПУ: Справочник Под ред. Ординарцева. – М: Машиностроение1987.-487с.
Кузнецов Ю.И. Маслов А.Р. Байков А.Н. Оснастка для станков с ЧПУ: Справочник - М: Машиностроение 1990.-512 с
Мельников Г.Н. Вороненко В.П. Проектирование механосборочных цехов. – М: Машиностроение 1990. – 351 с.
Методические указания по оформлению технологической документации при выполнении курсовых и дипломных проектов для студентов специальностей 12.01 07.01 21.03 12.02 15.02 15.06.-Курган: КМИ1992-36 с.
Методические указания для выполнения организационно-экономической части дипломного проекта специальности 120100 "Технология машиностроения". Курган1999.- 14c.
Методические указания к выполнению дипломного проекта для студентов специальности 151001. Курган2005.-c.45
Моисеев Ю.И. Котюк В.А. Классификация и выбор систем складирования транспортирования и инструментального обеспечения ГАП Учебное пособие. Курган: КМИ 1993.-32с.
Моисеев Ю.И. Технологическое проектирование ГПС в машиностроении Учебное пособие. Курган: КМИ 1996.
Мосталыгин Г.П. Орлов В.Н. Проектирование технологических процессов обработки заготовок. – Свердловск: УПИ. 1991.-112 с.
Мосталыгин Г.П Толмачевский Н.Н. Технология машиностроения - М: Машиностроение 1990.-288 с
Общемашиностроительные нормативы времени и режимов резания для нормирования работ выполняемых на универсальных и многоцелевых станках с ЧПУ. В 2-х ч. Ч.1. - М: Экономика 1990.-206 с
Орлов В.Н. Технология изготовления деталей транспортных машин: Учеб.пособие.-Курган: Изд-во Курганского гос.ун-та2000.-262 с.
Охрана труда в машиностроении Под общ. ред. Е.Я. Юдина С.В. Белова – 2-е изд. – М: Машиностроение 1983.-356с.
Режимы резания металлов. Справочник. Под ред. Ю.В.Барановского. изд 3-е перераб. и доп. М. «Машиностроение»1972.-407 с.
Справочная книга по охране труда в машиностроении. Под общей ред. О.Н. Русака. – Л: Машиностроение 1989. – 540 с.
Справочник технолога-машиностроителя В 2-х т. Т1 Под ред. А.Г. Косиловой Р.К. Мещерекова - М: Машиностроение 1986.-496 с.
Справочник технолога-машиностроителя В 2-х т. Т2 Под ред. А.Г. Косиловой Р.К. Мещерекова - М: Машиностроение 1986.-496 с.
Станочные приспособления: Справочник. В 2-х т. Т.1 Под ред. Б.Н. Вардашкина В.В. Данилевского. – М: Машиностроение 1984. – 592 с.
Станочные приспособления: Справочник. В 2-х т. Т.2 Под ред. Б.Н. Вардашкина В.В. Данилевского. – М: Машиностроение 1984. – 656 с.
Технология машиностроения Методические указания к выполнению курсового проекта для студентов направления 552900.-Курган: КМИ 1995.-42 с.
П р и л о ж е н и я
РТК(Планировка)готова.cdw

МОД. МА80Ц.25.09 И СТАНКА МОД. 1П756ДФ3
Промышленный робот мод. МА80Ц25.09
Токарный станок с ЧПУ 1П756ДФ3
Магазин-накопитель заготовок.
Стелаж для хранения заготовок.
устройство управления промышленным роботом.
Устройство управления промышленным роботом
Производительность РТК Q=143 штсмену
ХАРАКТИРИСТИКА ЗАХВАТНОГО УСТРОЙСТВА
Номинальная грузоподъемность - 40кг.
Наибольшее угловое перемещение :
относительно продольной оси - 180
относительно поперечной оси - 90
Наибольшая ошибка позиционирования -
Время зажима разжима - 1с
Диапазон размеров захватываемых деталей -100-280 мм
Давление впневмосистеме - P=0.5-0.6 МПа
Проект участка на базе станков с ЧПУ по изготовлению
деталей запорной арматуры
Циклограмма работы РТК
Заготовка.cdw

Приспособление контрол.cdw

внутренней резьбы М90 и отверстия 67 детали стойка и наружного
1 и внутреннего 32 сопрегаемой с ней
Проект участка на базе станков с ЧПУ поизготовлению
деталей запорной арматуры.
Приспособление контрольное
Наладка токар.cdw

ИТ2-3-4-5-6-7-8-9-10-11-12-13-14-3-ИТ2
Резец проходной ГОСТ 21151-75
ИТ2-3-15-16-17-18-12-ИТ2
Резец резьбовой ГОСТ 18885 -73
Резец канавочный ГОСТ 2008-80
ИТ2-12-19-20-19-21-22-21-12-ИТ2
Проект участка на базе станков с ЧПУ по изготовлению
деталей запорной арматуры
Инструментная наладка
на токарную операцию
Операция токарная с ЧПУ 015
Станок с ЧПУ модели 1П756ДФ3
Резец PCLNR 40*32 R19 Т5К10
Резец 2120-4148 Т5К10
Резец 2120-4149 Т5К10
приспособление Фрез((с приводом)готов.cdw

деталей запорной арматуры
Давление в системе Р = 10 Мпа
Зажимное усилие Q = 21904 Н
Нерабочие поверхности приспособления
красить в светло-зелёный цвет эмалью
нитроглифталевой НУ-К Гост 6631-65
Спецификация(схват).cdw

Спецификация(ток присп).cdw

Специфа(контрол).cdw

Спецификация(фрез присп).cdw

фрезерная.cdw

Сверло центровочное
Сверло спиральное Р6М5
Дисковая трёхсторонняя фреза
Проект участка на базе станков с ЧПУ по изготовлению
деталей запорной арматуры
Инструментная наладка
на токарную операцию
Операция фрезерная с ЧПУ
Станок с ЧПУ модели СВМ-1 Ф4
Втулка с конусом Морзе 2
Патрон(приспособ)+оправка.cdw

деталей запорной арматуры
Заготовка 108 закреплена в самоцетрирующем
зажимном приспособлении.
Соотношение плеч 1:2
Привод пневматический Р = 4 кгс см
Ход поршня Н = 45 мм.
РТК(Планировка)готова.cdw

МОД. МА80Ц.25.09 И СТАНКА МОД. 1П756ДФ3
Промышленный робот мод. МА80Ц25.09
Токарный станок с ЧПУ 1П756ДФ3
Магазин-накопитель заготовок.
Стелаж для хранения заготовок.
устройство управления промышленным роботом.
Устройство управления промышленным роботом
Производительность РТК Q=143 штсмену
ХАРАКТИРИСТИКА ЗАХВАТНОГО УСТРОЙСТВА
Номинальная грузоподъемность - 40кг.
Наибольшее угловое перемещение :
относительно продольной оси - 180
относительно поперечной оси - 90
Наибольшая ошибка позиционирования -
Время зажима разжима - 1с
Диапазон размеров захватываемых деталей -100-280 мм
Давление впневмосистеме - P=0.5-0.6 МПа
Проект участка на базе станков с ЧПУ по изготовлению
деталей запорной арматуры
Циклограмма работы РТК
Заготовка.cdw

Приспособление контрол.cdw

внутренней резьбы М90 и отверстия 67 детали стойка и наружного
1 и внутреннего 32 сопрегаемой с ней
Проект участка на базе станков с ЧПУ поизготовлению
деталей запорной арматуры.
Приспособление контрольное
Наладка токар.cdw

ИТ2-3-4-5-6-7-8-9-10-11-12-13-14-3-ИТ2
Резец проходной ГОСТ 21151-75
ИТ2-3-15-16-17-18-12-ИТ2
Резец резьбовой ГОСТ 18885 -73
Резец канавочный ГОСТ 2008-80
ИТ2-12-19-20-19-21-22-21-12-ИТ2
Проект участка на базе станков с ЧПУ по изготовлению
деталей запорной арматуры
Инструментная наладка
на токарную операцию
Операция токарная с ЧПУ 015
Станок с ЧПУ модели 1П756ДФ3
Резец PCLNR 40*32 R19 Т5К10
Резец 2120-4148 Т5К10
Резец 2120-4149 Т5К10
приспособление Фрез((с приводом)готов.cdw

деталей запорной арматуры
Давление в системе Р = 10 Мпа
Зажимное усилие Q = 21904 Н
Нерабочие поверхности приспособления
красить в светло-зелёный цвет эмалью
нитроглифталевой НУ-К Гост 6631-65
Маршрутная карта 2(05).frw

наименование оборудования
ед.единицы или материала
СМ Проф. Р УТ КР КОИД ЕН ОП Кшп Тп.з Тшт
эскиз(05).cdw

эскиз(опер010).cdw

Операц карта(опер010)2.cdw

эскиз(опер020).cdw

Операц карта11.cdw

Обозначение программы
Установить и снять деталь
Сталь 25Л ГОСТ 977-88
Приспособление патрон
Точить поверхность 1
Расточить отверстие 2
Резец PCLNR R19 Т5К10
пластина CNUM 05114-1906
Резец 2120-4148 Т5К10
штангенциркуль 8511-4089
Штангенциркуль ШЦ-1-125-0
Калибр-пробка 70H9 ПР ГОСТ14812-69
калибр-пробка 70Н9 НЕ ГОСТ 14814-69
Операц карта(опер020)2.cdw

пробка М60*2-7Н НЕ ГОСТ 17757-72
КР-РМ-100%;ОТК-10%;КР-РМ-100%
(эскиз)1.cdw

Операц карта2(05).cdw

КР-РМ-100%;ОТК-105%;КМ-РМ-100%
Штангенциркуль ШЦ-1-125-0
Операц карта(0,5).cdw

Наименование операции
Обозначение программы
Установить и снять деталь
Сталь 25Л ГОСТ 977-88
Приспособление фрезерное
Фрезеровать 2 паза 1
Центровать 2 отверстия 2
Штангенциркуль ШЦ-1-125-0
Комплект РМР(05).cdw

Курганский государственный университет
на технологический процесс механической обработки
Операц карта(опер020)1.cdw

Обозначение программы
Установить и снять деталь
Сталь 25Л ГОСТ 977-88
Приспособление патрон
Точить поверхность 1
Расточить отверстие 2
поверхность 4 и фаску 5
Резец PCLNR R19 Т5К10
пластина CNUM 05114-1906
Резец 2120-4148 Т5К10
штангенциркуль 8511-4089
Штангенциркуль ШЦ-1-125-0
Заготовка.cdw

Операц карта22.cdw

Нарезать резбу в отверстии 8
пробка М90*2-7Н ПР ГОСТ 17756-72
пробка М90*2-7Н НЕ ГОСТ 17757-72
Резец 2120-4148 Т5К10
штангенглубинометр ШГ-300-0
КР-РМ-100%;ОТК-10%;КР-РМ-100%
(эскиз)2.cdw

Маршрутная карта 1(05).frw

Код наименов.операции
Код наименование оборудования
Обозначение документа
Сталь 25Л ГОСТ 977-88
Токарный станок с ЧПУ 16К25Ф3
контр11.cdw

Наименование операции
Наименование материала
Наименование средств ТО
Сталь 25Л ГОСТ 977-88
Контролируемые параметры
Спец.штангенциркуль 8511-4030
Шаблон 8371-0081 МН 1419-61
ПробкаМ90x2-7H ПР 8221-0242
ПробкаМ90x2-7H НЕ 8221-1242
ПробкаМ60x2-7H НЕ 8221-1183
ПробкаМ60x2-7H ПР 8221-0183
ШтангенциркульШц1-125-0
эскиз.cdw

Операц карта(опер010)1.cdw

Обозначение программы
Установить и снять деталь
Сталь 25Л ГОСТ 977-88
Приспособление патрон
Точить поверхность 1
Резец 2102-0055 Т5К10
Резец 2103-0057 Т5К10
шаблон 8371-0081 МН1419-61
Штангенциркуль ШЦ-1-125-0
Точить поверхность 2 и фаску 3
Наладка токар(020).cdw

ИТ2-3-4-5-6-7-8-9-3-10-11-12-3-ИТ2
Резец проходной ГОСТ 21151-75
Резец резьбовой ГОСТ 18885 -73
Проект участка на базе станков с ЧПУ по изготовлению
деталей запорной арматуры
Инструментная наладка
на токарную операцию
Операция токарная с ЧПУ 020
Станок с ЧПУ модели 1П756ДФ3
Резец PCLNR 40*32 R19 Т5К10
Резец 2120-4148 Т5К10
6 станков(планировка).cdw

Проект участка на базе станков с ЧПУ по изготовлению
Условные обозначения:
График загрузки оборудования
МАГИСТРАЛЬНЫЙ ПРОЕЗД
- медицинская аптечка
КП - контрольный пункт
МСА - моечно-сушильный агрегат
- стружко-уборочный конвейер
- склад стеллажного типа
Схват.cdw

относительно поперечной оси -
Наибольшая ошибка позиционирования-
Проект участка на базе станков с ЧПУ по изготовлению
деталей запорной арматуры
Захватное устройство
ХАРАКТИРИСТИКА ЗАХВАТНОГО УСТРОЙСТВА
Номинальная грузоподъемность-40кг.
Наибольшее угловое перемещение :
Время зажима разжима-1с
Диапазон размеров захватываемых деталей-100-280 мм
Давление пневмоприводов -P=0.5-0.6 МПа
Сравнительная технология3.cdw

Токарно-винторезный 1К62
Вертикально-фрезерный 6Н12
Вертикально-фрезерный СВМ1Ф4
Проект участка на базе станков с ЧПУ по изготовлению
деталей типа pfgзапорная арматура
Сравнительная технология
Наладка токар(020).cdw

ИТ2-3-4-5-6-7-8-9-3-10-11-12-3-ИТ2
Резец проходной ГОСТ 21151-75
Резец резьбовой ГОСТ 18885 -73
Проект участка на базе станков с ЧПУ по изготовлению
деталей запорной арматуры
Инструментная наладка
на токарную операцию
Операция токарная с ЧПУ 020
Станок с ЧПУ модели 1П756ДФ3
Резец PCLNR 40*32 R19 Т5К10
Резец 2120-4148 Т5К10
6 станков(планировка).cdw

Проект участка на базе станков с ЧПУ по изготовлению
Условные обозначения:
График загрузки оборудования
МАГИСТРАЛЬНЫЙ ПРОЕЗД
- медицинская аптечка
КП - контрольный пункт
МСА - моечно-сушильный агрегат
- стружко-уборочный конвейер
- склад стеллажного типа
Схват.cdw

относительно поперечной оси -
Наибольшая ошибка позиционирования-
Проект участка на базе станков с ЧПУ по изготовлению
деталей запорной арматуры
Захватное устройство
ХАРАКТИРИСТИКА ЗАХВАТНОГО УСТРОЙСТВА
Номинальная грузоподъемность-40кг.
Наибольшее угловое перемещение :
Время зажима разжима-1с
Диапазон размеров захватываемых деталей-100-280 мм
Давление пневмоприводов -P=0.5-0.6 МПа
Спецификация(схват).cdw

Спецификация(ток присп).cdw

Специфа(контрол).cdw

Спецификация(фрез присп).cdw

Сравнительная технология3.cdw

Токарно-винторезный 1К62
Вертикально-фрезерный 6Н12
Вертикально-фрезерный СВМ1Ф4
Проект участка на базе станков с ЧПУ по изготовлению
деталей типа pfgзапорная арматура
Сравнительная технология
Комплект РМР(05).cdw

Курганский государственный университет
на технологический процесс механической обработки
Заготовка.cdw

эскиз(опер010).cdw

Операц карта(опер010)2.cdw

Операц карта(опер010)1.cdw

Обозначение программы
Установить и снять деталь
Сталь 25Л ГОСТ 977-88
Приспособление патрон
Точить поверхность 1
Резец 2102-0055 Т5К10
Резец 2103-0057 Т5К10
шаблон 8371-0081 МН1419-61
Штангенциркуль ШЦ-1-125-0
Точить поверхность 2 и фаску 3
Маршрутная карта 2(05).frw

наименование оборудования
ед.единицы или материала
СМ Проф. Р УТ КР КОИД ЕН ОП Кшп Тп.з Тшт
Маршрутная карта 1(05).frw

Код наименов.операции
Код наименование оборудования
Обозначение документа
Сталь 25Л ГОСТ 977-88
Токарный станок с ЧПУ 16К25Ф3
эскиз(05).cdw

Операц карта2(05).cdw

КР-РМ-100%;ОТК-105%;КМ-РМ-100%
Штангенциркуль ШЦ-1-125-0
Операц карта(0,5).cdw

Наименование операции
Обозначение программы
Установить и снять деталь
Сталь 25Л ГОСТ 977-88
Приспособление фрезерное
Фрезеровать 2 паза 1
Центровать 2 отверстия 2
Штангенциркуль ШЦ-1-125-0
Операц карта11.cdw

Обозначение программы
Установить и снять деталь
Сталь 25Л ГОСТ 977-88
Приспособление патрон
Точить поверхность 1
Расточить отверстие 2
Резец PCLNR R19 Т5К10
пластина CNUM 05114-1906
Резец 2120-4148 Т5К10
штангенциркуль 8511-4089
Штангенциркуль ШЦ-1-125-0
Калибр-пробка 70H9 ПР ГОСТ14812-69
калибр-пробка 70Н9 НЕ ГОСТ 14814-69
Операц карта22.cdw

Нарезать резбу в отверстии 8
пробка М90*2-7Н ПР ГОСТ 17756-72
пробка М90*2-7Н НЕ ГОСТ 17757-72
Резец 2120-4148 Т5К10
штангенглубинометр ШГ-300-0
КР-РМ-100%;ОТК-10%;КР-РМ-100%
эскиз.cdw

(эскиз)1.cdw

(эскиз)2.cdw

контр11.cdw

Наименование операции
Наименование материала
Наименование средств ТО
Сталь 25Л ГОСТ 977-88
Контролируемые параметры
Спец.штангенциркуль 8511-4030
Шаблон 8371-0081 МН 1419-61
ПробкаМ90x2-7H ПР 8221-0242
ПробкаМ90x2-7H НЕ 8221-1242
ПробкаМ60x2-7H НЕ 8221-1183
ПробкаМ60x2-7H ПР 8221-0183
ШтангенциркульШц1-125-0
эскиз(опер020).cdw

Операц карта(опер020)2.cdw

пробка М60*2-7Н НЕ ГОСТ 17757-72
КР-РМ-100%;ОТК-10%;КР-РМ-100%
Операц карта(опер020)1.cdw

Обозначение программы
Установить и снять деталь
Сталь 25Л ГОСТ 977-88
Приспособление патрон
Точить поверхность 1
Расточить отверстие 2
поверхность 4 и фаску 5
Резец PCLNR R19 Т5К10
пластина CNUM 05114-1906
Резец 2120-4148 Т5К10
штангенциркуль 8511-4089
Штангенциркуль ШЦ-1-125-0
Рекомендуемые чертежи
- 24.01.2023
- 24.01.2023