Design of Plasticized, Hydrophobic Portland Cement and HSE Production Line


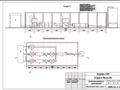
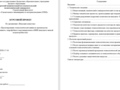
- Added: 17.12.2020
- Size: 448 KB
- Downloads: 1
Description
Perm National Research Polytechnic University Construction Faculty Department "Construction Engineering and Materials Science (SIM)" COURSE PROJECT In the discipline "Binding Substances" On the topic: "Design of a technological line for the production of plasticized, hydrophobic Portland cement and GNV (binding low water demand) Perm 2019.
Calculation of production work: around the clock, without a weekend. Enterprise Performance G = 500 020 tons/year
Contents Introduction 3 1. Technical information. 5 1.1 Material, chemical and mineralogical composition of the product. 5 1.2 Physical and chemical processes occurring during hardening of binder. 7 1.3 Conditions of composite destruction (corrosion) on binder. Scope. 9 1.4 Raw materials. 10 1.5 Quality indicators of finished product and methods of their determination 14 1.6 Analysis of significant production flow charts 20 1.7 Technological factors affecting product quality 27 1.8 Rules of acceptance, marking, transportation and storage of finished product 28 2. Design section. 34 2.1 Design functional process diagram of product production. 34 2.2 Calculation of production charges and preparation of material balance of the main process unit. 35 2.3 Process Line Production Program Calculation. 35 2.4 Selection of main mechanical and process equipment. 34 2.5 Calculation of specific energy loads. 37 List of literature 39
Components: Specification, Process Line, Section 1-1 and 2-2, PP
Soft: AutoCAD 2017
Project's Content
![]() ![]() ![]() |
![]() ![]() ![]() |
Additional information
Contents
Introduction
1. Technical Information
1.1 Material, chemical and mineralogical composition of the product
1.2 Physical and chemical processes occurring during hardening of binder
1.3 Conditions of composite destruction (corrosion) on binder. Scope of Application
1.4 Raw Materials
1.5 Quality indicators of finished product and methods of their determination
1.6 Analysis of significant production flow charts
1.7 Process factors affecting product quality
1.8 Rules of acceptance, marking, transportation and storage of finished product
2. Design Section
2.1 Design functional process diagram of product production
2.2 Calculation of production charges and material balance of the main process unit
2.3 Process Line Production Program Calculation
2.4 Selection of main mechanical and process equipment
2.5 Calculation of specific energy loads
List of literature
Introduction
Cement is an artificial inorganic hydraulic binder. One of the main building materials. When interacting with water, aqueous solutions of salts and other liquids, it forms a plastic mass, which then solidifies and turns into a stone-like body.
Portland cement is a hydraulic binder, the composition of which is dominated by calcium silicates (7080%). Portland cement is a product of fine grinding of clinker with addition of gypsum (35%).
The hydrophobic Portland cement differs from the common one in its reduced hygroscopicity during storage and transportation in adverse conditions, as well as the ability to give solution and concrete mixtures increased mobility and ease of laying, and to hardened solutions and concrete - increased frost resistance. The production of hydrophobic cements requires the installation of a precise metering device that uniformly feeds the mills with a hydrophobic additive when grinding the cement.
Hydrophobic cement is not afraid of humidification; he does not follow, does not turn into a coma and for a long time almost does not lose activity. Hydrophobic additives are also plasticizers, that is, contribute to the plasticity of the cement dough. When mixing solution and concrete mixtures, hydrophobic films are removed from cement particles with mechanical action of aggregates on them and do not adversely affect the strength of solutions and concrete.
Plasticized Portland cement was prepared by adding about 0.25% LST (based on dry matter) to clinker milling. It differs from the usual Portland cement in its ability to give solution and concrete mixtures increased mobility. The plasticizing effect is used to reduce the water cement ratio, increase frost resistance and waterproof concrete. If I/C is retained, cement consumption can be reduced (approximately 1015%) without deterioration of concrete quality.
VNB is a new class of highly efficient hydraulic binders with a number of advantages over traditional Portland cement. The process of producing VNB is based on mechanochemical activation of the raw material composition at the optimal ratio of components. The creation of new types of binders ensures a decrease in the consumption of clinker part of cement compared to the modern level by 4050%, brings the production of binders closer to construction sites and, as a result, reduces transportation costs to 70%. Based on these binders, construction materials of low energy intensity are created.
Conditions of binder destruction (corrosion). Application areas. [4, 7, 8]
Corrosion is a chemical process of material destruction under the influence of aggressive environmental factors. Corrosion is divided into two types: chemical and physical.
Corrosion of plasticized, hydrophobic PC and VNB rarely occurs, since the production of this binder includes water repellent additives of surfactant.
Scope:
Plasticizing PP is used on a par with ordinary PP for concrete and reinforced concrete ground, underground and underwater structures, especially undergoing multiple alternate freezing and thawing or moistening and drying. It can also be used for the production of conventional and pre-stressed prefabricated concrete and reinforced concrete structures, in mortars based on a complex binder of cement, lime and other ground mineral additives.
Hydrophobic Portland cement is used primarily in cases where it is necessary to store cement for a long time before use or to transport it over long distances. It is very advisable to use it for cladding and plaster of buildings, since it prevents fading on the surface of plaster. Hydrophobic Portland cement can be rationally used in the manufacture of concretes for road, airfield construction and the construction of hydraulic structures. Also, this cement can be used for the same purposes as the plasticizing PC.
The scope of GNB is largely determined by the content of the clinker component therein.
VNV with a high content of the clinker component (VNB100... VNB70) are effective for the manufacture of prefabricated and monolithic reinforced concrete structures operated under increased loads, as well as for accelerating the construction period and reducing the cost of thermal moisture treatment until it is completely abandoned .
Binders with an average content of clinker component (VNB40... VNB60) can be used to replace PP grades M400... M600, in the manufacture of products and structures from concrete classes B30... B45.
Binders with low content of clinker component (VNB30) should be used in concrete of class B30. Their use in reinforced concrete structures is possible with the protection of reinforcement.
Process factors affecting product quality. [1, 2, 3]
As the results of numerous experiments show, self-stress and linear expansion of cement are directly dependent on the gypsum content in the cement. The increase of its amount in cement causes a significant increase in the amount of expansion and self-tension.
Static treatment of numerous experiments taking into account the content of calcium aluminates introduced into the clinker PC showed a decrease in the expansion value with an increase in the ratio of Al2SO3 to SO3. An increase in the ratio from 0.8 to 3 is accompanied by a decrease in the expansion of cement stone from 2 to 0.1%. In order to increase the strength of cement stone, it is necessary to finer crush raw materials (in our case, min. additives and gypsum stone). The more C3A is contained, the greater the cement expansion.
Rules of acceptance, marking, transportation and storage of the product. Manufacturer's warranties. [1, 2, 3]
Acceptance Rules
1. Cement acceptance is carried out by the manufacturer's technical control service. Delivery of cement that has not passed acceptance is not allowed.
2. Cement is accepted in batches. The volume of the batch, with the exception of shipments in ships, shall not exceed the capacity of one silo. When cement is shipped in ships, the volume of the lot may exceed the capacity of one silo. In this case, the lot volume is established by agreement of the manufacturer with the consumer.
3. The Technical Inspection Service carries out cement acceptance based on production inspection data and acceptance tests.
4. Test results are recorded in a journal. The acceptance test log shall be numbered, trimmed and sealed with the manufacturer's seal. The journal is the official document of the manufacturer certifying the quality of the product.
5. A batch of cement can be accepted and delivered if the test results for all indicators meet the requirements of the regulatory document, unless the contract (contract) for the supply of cement provides otherwise in terms of the recommended indicators.
6. Acceptance and delivery of a batch of cement is carried out before the end of strength tests. If a significant defect is established after the strength test is completed, this batch of cement is considered not to comply with the requirements of the regulatory document for the strength class (grade).
7. Each batch of cement or part thereof delivered to one address shall be accompanied by a quality document.
8. The quality document shall be marked with the manufacturer's control mark, signed by the head of the technical control service or his deputy and sent to the consumer simultaneously with cement or no later than three days, not counting the date of shipment of cement.
9. At the request of the consumer, the manufacturer is obliged to inform him of the results of all acceptance tests of this batch of cement.
Marking
1. Marking of cement in bags is carried out on each bag in any part of it. When packing cement in soft containers, the marking is applied to the label embedded in a special pocket on the soft container.
It is allowed to apply marking with indelible paint on the side surface of the soft container in any part of it.
2. During fine packing of cement marking is applied on label, which is glued on jar or bag, or is inserted between external and internal layers of bag, or marking is applied directly on jar or bag.
Only if the outer layer of the bag is made of a transparent material is it allowed to insert the label into the bag.
3. The marking shall be clear and contain:
- manufacturer name and its trademark;
- cement symbol and (or) its full name in accordance with the regulatory document;
- strength class (grade) of cement, if the normative document provides division by strength classes (grade);
- designation of regulatory document, according to which cement is supplied;
- average net mass of cement in the package or net mass of cement in the vehicle;
- mark of conformity when delivering certified cement (if provided for by the certification system).
4. When delivering cement in a small package, each package shall have a brief instruction on its use, which may be reproduced on or attached to the package.
When delivering coloured cement, a strip of appropriate colour shall be applied to the package.
5. When forming transport bags of cement bags, the upper row of bags must be laid so that markings on the bags are clearly visible. The upper row bags are additionally marked as per GOST 14192.
6. When delivering cement in a small package placed in an enlarged container, the label is also pasted onto the container. At the same time, the number of packages in the container is additionally indicated on the label.
7. Each vehicle (including when delivering cement without packaging) is provided with a label indicating all the details and additionally the cement lot number and shipment date. The label is attached to the vehicle in an accessible location in any way to ensure its safety during transportation.
Packaging
1. Cement is shipped in or without packaging. When delivered without packaging, cement shall be shipped in specialized transport.
2. For cement packing the following is used:
- paper five- or six-layer bags according to GOST 2226, sewn or glued with a closed neck with a valve of LM, BM or BMP grades. Paper bags of foreign production can be used, the quality indicators of which are not lower than the requirements of GOST 2226;
- soft containers with a waterproof insert or other package that securely protects cement from wetting and contamination, according to the relevant regulatory documents.
For small packaging, polyethylene jars, bags, as well as other packaging ensuring the safety of cement, are used according to the relevant regulatory documents.
3. The gross mass limit of the cement bag shall not exceed 51 kg.
4. The average gross weight of the cement bag is determined by weighing 20 bags selected by random batch selection and dividing the result by 20.
The average weight of the bag is determined by weighing 20 bags selected by random selection from a batch of obtained bags and dividing the result by 20.
The average net weight of cement in the bag is determined by subtracting the average weight of the bag from the average gross weight of the bag with cement.
Deviation of the average net weight of cement in bags of this batch from the net weight indicated on the package must not be more than m-0.2 + 0.5 kg.
The deviation of the net weight of cement in a separate bag from that indicated on the package shall not exceed 1 kg.
5. The gross weight of the soft cement container is determined immediately after filling.
The average net weight of cement in the soft container is determined by subtracting from the gross weight of the soft container with cement the average weight of the soft container determined in a similar manner to the average weight of the paper bag.
The deviation of the average net weight of cement in a soft container from that indicated on the package shall not exceed ± 3%.
6. The net mass of cement in a separate package during fine packing shall be (3; 5) ± 0.05 kg, (10; 20) ±0.3 kg.
Transportation and Storage
Cement is transported by all modes of transport in compliance with the Rules for transportation of goods established for transport of this mode and the requirements of other documentation approved in accordance with the established procedure of GOST 1017885.
The manufacturer shall supply cement in a serviceable and cleaned vehicle.
When cement is transported without packaging or in bags, it must be protected from moisture and contamination.
Cement must be stored separately according to types (types) and strength classes (grades): in unpackaged form - in silos or other closed containers, and cement in packaging - in dry rooms.
Mixing of cements of different types (types) and strength classes (grades), as well as its contamination with foreign impurities and humidification are not allowed.
Cement shall not be stored without packing in barn-type warehouses.
During storage, bags with cement are laid closely on pallets in stacks with height not exceeding 1.8 m with provision of free approach to them.
Cement is allowed to be stored in soft containers and bags made using waterproof materials, under a canopy or in open areas, provided the integrity of the waterproof package.
To prevent the fitting of soft containers and bags, they should be stacked on pallets with a height of no more than three tiers.
Manufacturer's guarantees
The manufacturer guarantees compliance of cement with GOST 311082003, subject to the rules of its transportation and storage when delivered without packaging at the time of delivery, but not more than 60 days from the date of shipment, and when delivered in container - within 60 days from the date of shipment.
Warranty shelf life of VNV is not less than 6 months .
Selection of main mechanical equipment [6]
Based on the production program, using the reference books for the equipment, we will select the process equipment:
Select a mill for grinding components (clinker, gypsum stone and surfactant W < 0%; fr. < 0.08mm).
The selection of mills will be carried out based on the necessary productivity of the mill. According to the design characteristics, the mill capacity should be 57.7 tons/h.
The best equipment will be the following mill:
Ball mill with central unloading (SO5) (MSC 2136)
Drum dimensions, mm
internal diameter - 2700
operating length - 3600
Number of drum revolutions per second - 0.25
Performance, t/h - 50-120
Electric motor power in kW - 380
Overall dimensions, m:
length - 10
width -6.27
height - 5.05
Weight, t - 81.2.
Pick up a gypsum stone crusher (fr. = 60 mm, W < 3.5%)
According to production calculations, the productivity should be 4.22 t/h or 1.51m3/h.
Thus, the most optimum crusher, the following crusher will be: Shchekovy crusher (ShchDS1.6h2.5)
Loading hole dimensions (length x width), m - 0.16x0.25
The largest size of the tins. piece, m - 0.13
Nominal outlet to slot, m - 30
Capacity at nominal slot, m3/h - 3.0
Electric motor power, kW - 7.5
Overall dimensions, m:
• length - 0.88
• width - 1.07
• height - 1,085
Weight without engine, t - 1.37
Select crusher for clinker PC (fr. = 60 mm, W < 1%)
According to production calculations, the crusher capacity for the PP clinker should be 52.74 tons/h.
Thus, the most optimal crusher will be the following crusher: Cone crusher (KSD - 900B (SM560B))
Performance, t/h - 48-86
Diameter of movable cone base, mm - 900
Largest size of material to be loaded, m - 1
Loading hole width in m - 0.115
Eccentric bushing speed, rpm - 5.42
Electric motor power, kW - 55
Weight (without electrical equipment), t - 3.79
Dimensions in m:
• Length 2.68
• Width 1.82
• Height 2.25
Selection of drying units:
According to production calculations, the dryer capacity for clinker PP should be 53.1 t/h.
The most optimal option will be the following dryer: Dryer drum SM-7203
Outside diameter of drum, mm - 2800
Drum length, mm - 14000
Drum speed, rpm - 4.06.0
Drive power consumption, kW - 28
Overall dimensions, mm not more than:
length - 14032
width - 4434
height - 4340
Performance - 5070 t/h
Weight - 70 t
According to production calculations, the capacity of the gypsum dryer should be 4.4 tons/h.
The most optimal option will be the following dryer: Dryer drum SM-1013
Outer diameter of drum, mm - 1600
Drum length, mm - 8000
Drum speed, rpm - 4.1
Drive power consumption, kW - 7
Overall dimensions, mm not more than:
• length - 9850
• width - 2800
• height - 3550
Performance - 4.5 t/h
Weight - 13.9 tons
курсовая.dwg
Similar materials
- 24.01.2023
Free downloading for today
- 24.01.2023