14-storey two-section residential building in the city of Uralsk


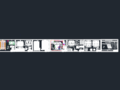
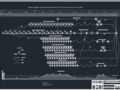
- Added: 05.05.2021
- Size: 7 MB
- Downloads: 3
Description
Recently, in the Republic of Kazakhstan and the West Kazakhstan region, in particular, the construction of multi-storey residential buildings has been intensively carried out, this is necessary to create comfortable living conditions for the population.
The design of a 14-story residential building, in the future and its construction, which at the moment is one of the successful and developing enterprises.
Construction, being a material-intensive, labour-intensive, capital-intensive, energy-intensive and knowledge-intensive production, contains a solution to many local and global problems, from social to environmental.
Construction is one of the main areas of production activity. As a result of construction production, completed construction products are created - a building or a construction of various functional purposes. The main place in the development of construction, especially recently, is given to technical progress, in this area of production there is a constant development process. It is a multi-stakeholder process for the continuous improvement of working methods, technologies and production organizations based on science, technology and best practices. Saving public labor is the main task of technological progress. The main goal of scientific and technological progress in construction is the growth of industrialization, that is, the very development, progress, which is a complex system that includes rationally organized design, mechanized and automatic production of building materials and structures, products and parts for the specialized production of construction and installation work on the construction site.
The design of residential buildings is based on the principles of synthesis of functional, architectural, artistic, technical and economic aspects of architecture. The purpose of the design is to find such solutions of residential buildings that best meet their purpose, are convenient for people, have high architectural and artistic qualities, provide buildings with strength, cost-effective construction and operation in compliance with environmental and hygienic standards.
The main areas of improving the quality of construction production include:
- introduction of computer technologies at the design stage;
- application of new technologies;
- high level of comfort of buildings and structures.
To obtain high-quality and reliable construction products, it is necessary that all construction processes are interconnected and aimed at improving construction efficiency.
The specific advantages of the current construction are the reduction of steel consumption, leakage, freezing due to the lack of joints and cutting of structures are excluded. In addition, the unlimited number of types of elements and a wide choice of possibilities for designing geometric forms of structures led to the creation of new, more acceptable space-planning solutions for buildings, the implementation of previously impossible architectural ideas.
Industrial formwork in combination with the concrete manufacturing technique and its supply to the concreting site made this method comparable in terms of technical and economic indicators with prefabricated house building.
In addition, modern developments in the developing life of society have led to the need to create comfortable housing that meets the full range of requirements of a business person.
Thanks to the capacity to produce building materials, this organization has advantages.
All railway products have high quality, smooth surface and comply with GOST and standards applicable in the Republic of Kazakhstan.
The diploma project on the topic "14-storey two-section residential building" reveals the possibilities of designing and developing optimal technological solutions and determining the necessary organizational conditions for the implementation of construction processes, work, construction of the building as a whole.
Project's Content
![]() ![]() ![]() |
![]() ![]() ![]() |
Additional information
Contents
Contents
INTRODUCTION
ARCHITECTURAL AND STRUCTURAL SECTION
General part
Site Plot Plan Description
Configuration and features of the space-planning solution of the building
Technical and economic indicators of the building
Environmental protection activities
Structural characteristics of the building
Description of exterior and interior finishes
Engineering equipment of the building
DESIGN SECTION
Determination of foundation depth
Sizing the Foundation
To Calculate and Design a Multi-Stop Slab Panel
Loadings
Calculation of coating plate elements by strength
Defining Geometric Characteristics
Prestress losses to crimping forces
Calculation of strength of sections inclined to longitudinal axis of panel
Calculation of deflections
Calculation of crack opening panel
ORGANIZATIONAL AND TECHNOLOGICAL SECTION
Schedule
General part
Schedule Design
Selection of methods of basic construction works
Define requirements for labor costs, materials, structures, machine time
Construction Plot Plan Design
Concept of Construction Plan
Calculation of installation facilities
Define Warehouse Requirements
Determining the need for temporary facilities
Construction Site Water Supply
Temporary power supply of the construction facility
Job Instruction for Ceramic Floors and Internal Surface Lining (for 1section of typical floor)
Calculation of scope of works for ceramic floors and for lining of internal surfaces
Selection and justification of machines and mechanisms adopted for performance of works
Selection and justification of accepted methods of work execution
Determination of labour intensity of works
Safety precautions
Safety and Fire Safety
Calculation of vehicle requirements for two types of transportation of materials
Calculation of construction plan required resources
ECONOMIC DIVISION
General Instructions
Consolidated cost estimate for construction
Local cost estimate for roofing works
Local estimates for special activities
CONCLUSION
LIST OF LITERATURE USED
Introduction
Recently, in the Republic of Kazakhstan and the West Kazakhstan region, in particular, the construction of multi-storey residential buildings has been intensively carried out, this is necessary to create comfortable living conditions for the population .
The design of a 14-story residential building, in the future and its construction, which at the moment is one of the successful and developing enterprises.
Construction, being a material-intensive, labour-intensive, capital-intensive, energy-intensive and knowledge-intensive production, contains a solution to many local and global problems, from social to environmental.
Construction is one of the main areas of production activity. As a result of construction production, completed construction products are created - a building or a construction of various functional purposes. The main place in the development of construction, especially recently, is given to technical progress, in this area of production there is a constant development process. It is a multi-stakeholder process for the continuous improvement of working methods, technologies and production organizations based on science, technology and best practices. Saving public labor is the main task of technological progress. The main goal of scientific and technological progress in construction is the growth of industrialization, that is, the very development, progress, which is a complex system that includes rationally organized design, mechanized and automatic production of building materials and structures, products and parts for the specialized production of construction and installation work on the construction site.
The design of residential buildings is based on the principles of synthesis of functional, architectural, technical and economic aspects of architecture. The purpose of the design is to find such solutions of residential buildings that best meet their purpose, are convenient for people, have high architectural and artistic qualities, provide buildings with strength, cost-effective construction and operation in compliance with environmental and hygienic standards.
The main areas of improving the quality of construction production include:
introduction of computer technologies at the design stage;
application of new technologies;
high level of comfort of buildings and structures.
To obtain high-quality and reliable construction products, it is necessary that all construction processes are interconnected and aimed at improving construction efficiency.
The specific advantages of the current construction are the reduction of steel consumption, leakage, freezing due to the lack of joints and cutting of structures are excluded. In addition, the unlimited number of types of elements and a wide choice of possibilities for designing geometric forms of structures led to the creation of new, more acceptable space-planning solutions for buildings, the implementation of previously impossible architectural ideas.
Industrial formwork in combination with the concrete manufacturing technique and its supply to the concreting site made this method comparable in terms of technical and economic indicators with prefabricated house building.
In addition, modern developments in the developing life of society have led to the need to create comfortable housing that meets the full range of requirements of a business person.
Thanks to the capacity to produce building materials, this organization has advantages.
All railway products have high quality, smooth surface and comply with GOST and standards applicable in the Republic of Kazakhstan.
The diploma project on the topic "14-storey two-section residential building" reveals the possibilities of designing and developing optimal technological solutions and determining the necessary organizational conditions for the implementation of construction processes, work, construction of the building as a whole.
Architectural and structural section
1.1 General part
The site of the designed 14-storey residential building is located in the city of Uralsk.
The plot allocated for the construction of a residential building has a flat terrain, is free from development, there are no valuable green spaces. Natural conditions:
Regulatory data for Uralsk:
Climate - sharply continental - continental, dry hot summers and snowy cold winters;
average annual wind speed - 2.9 m/s
average annual humidity - 69%
annual rainfall up to 400 mm;
normative depth of ground freezing - 0.8 m;
seismicity of the construction area - points;
the predominant wind direction in winter - northeast;
the prevailing wind direction in summer - western;
maximum height of snow cover per year - 67 cm;
the average January temperature is 19 ° C;
average July temperature + 29.9 ° C;
heating period from 15.10. up to 15.04;
the site is composed of sandy-clay soils, loams;
Altitude: 37 m;
For the relative elevation 0.000, the level of the clean floor of the 1st floor of the building is taken, which corresponds to the absolute elevation according to the general plan.
Technical solutions adopted in the drawings comply with the requirements of environmental, sanitary, fire and other standards applicable in the territory of the Republic of Kazakhstan.
1.3 Configuration and features of the space-planning solution of the building
The designed building is a 14-story two-section residential building with a basement. Floor height - 3.0m, number of floors - 14; the total height of the building is -43.5 m.
On each floor are designed: 4-room, 3-room and 2-room apartments. A total of 84 apartments in a 14-story building.
In the designed residential building, each apartment consists of the following rooms:
- living rooms (sleeping, children's); - living room-dining room;
- kitchen; - front (corridor);
- bathroom, (shower); - toilet;
- loggia, (balcony); - pantry.
All living rooms are illuminated by natural light in accordance with the requirements of the SNiP, the rooms in the apartments have separate entrances, the height of the room is 2.7 m. The building designed two elevators with a lifting capacity of 320kg each, as well as two garbage chambers.
The house is designed with all necessary types of engineering support: heating, hot water supply, water supply system, sewerage, ventilation, power supply, communication and alarm system.
1.5 Environmental protection measures
14-storey residential building refers to buildings that do not require special measures for environmental protection. The most basic requirements must be met:
The territory of construction of a residential building is fenced in order to avoid free access to it by unauthorized persons.
The construction area and workplaces should be sufficiently illuminated.
Construction sites are equipped with sanitary and hygienic rooms, which are located on the site, taking into account the minimum transitions from them to the places of work.
On the construction territory, on-site roads are arranged, and the places of passages and driveways are indicated by signs. Areas dangerous to traffic shall be protected or marked at their borders with warning signs and signals visible day and night.
Passages for workers located on ledges, slopes and slopes with a slope of more than 20 ° are equipped with ladders or ladders with one-sided railings. In places of crossing ditches, trenches make bridges with a width of at least 0.6 m with railings with a height of 1 m.
Fire safety
Fire safety measures are performed in accordance with SNiP 2.01.02-85 "Fire safety standards," SNiP 2.08.01-85. "Residential buildings."
The building belongs to the second class, to the second degree of fire resistance and durability.
The building has two evacuation exits. In the high-rise part of the building, staircases are designed for non-smoke Opening of doors from staircases, common corridors, rooms with more than 5 people in them - is provided towards evacuation routes. External doors do not have locks and locks outside. Non-combustible finishing materials are used for interior finishing of walls and ceilings of rooms.
Bearing building structures, ventilation channels and enclosing structures of ventilation chambers are accepted from non-combustible materials. All wooden elements of structures are subjected to deep impregnation with flame retardants.
1.6 Structural characteristics of the building
The structural system of a 14-storey two-section residential building is solved with a arceless scheme with load-bearing longitudinal (transverse) brick walls. The spatial rigidity of the building is ensured by the joint work of longitudinal and transverse brick walls, united by horizontal slab disks.
Bases
The foundation for a 14-story two-section residential building is a ribbon on a natural base.
Foundations on a natural base, like any foundations, are designed to transfer loads from the load-bearing structures of the structure to the soils of the base. The foundations are assigned the task of distributing the pressure on the sole so that the deformations of the bases that occur at the same time and, most importantly, their unevenness do not exceed the limit values set by the relevant standards.
The tape foundation is laid along the wall paths. It is designed for the construction of houses from heavy building materials, for example, from brick.
Walls
External walls are designed in the form of multilayer masonry, 510 mm thick from silicate brick according to GOST 37995 .
Floors and coverings
Slabs - prefabricated reinforced concrete from multistage panels.
The roof is with a semi-passable ventilated cold attic. The attic floor is insulated by a 100 mm thick layer of foam concrete
In accordance with the design scheme, structures, floors and coatings are hard disks when transferring wind loads to load-bearing structures, for which it is necessary to carefully seal the seams between the slabs with cement mortar.
Roof
The roof is made of polymer-bitumen build-up material. The abutment points are glued on top with additional layers to a height of at least 150 mm. Over the waterproofing carpet, the coating has a protective layer in the form of a sprinkle of ceramic gravel with dimensions of 310mm.
Crossing points
All openings in the inner and outer walls are covered with bridges.
Floors
Floors in residential rooms meet the requirements of strength, resistance, wear, sufficient elasticity, noiselessness, convenience of cleaning. Flooring in apartments is taken from linoleum on heat-absorbing base. Floors in bathrooms and sanitary units are made of ceramic tiles. Bracing is made of cement sand mortar.
Windows and doors
Windows and doors are accepted according to GOST 2316678 * in accordance with the room area. All living rooms have natural lighting. Rooms in apartments have separate entrances. To ensure quick evacuation, all doors open outside in the direction of traffic on the street based on the conditions for evacuating people from the building in case of fire. Door boxes are fixed in openings to unsepted wooden plugs laid in masonry during masonry of walls. Doors are equipped with handles, latches and tie-in locks.
Kitchens
Kitchens are equipped with exhaust and natural ventilation, washing and gas stove.
Bathrooms and sanitary facilities
Bathrooms and sanitary units are equipped with natural exhaust ventilation.
Stairwell
In the center of the building section is an elevator shaft. Above the shaft in the attic is the elevator engine room. The stairwell is planned as an internal day-to-day operation, made of prefabricated reinforced concrete elements. Two-march staircase resting on staircases. Slope of stairs 1:2. From the stairwell there is access to the roof through a metal staircase equipped with a fire-resistant door. The stairwell has artificial and natural lighting through window openings. All doors along the stairwell and in the vestibule open towards the exit from the building according to fire safety conditions. The stairs fencing is made of metal links, and the handrail is lined with plastic.
Refuse chute
The garbage duct at the bottom ends in the garbage chamber with a storage bin. Accumulated garbage in the bunker is poured into garbage carts and immersed in garbage collection machines and taken to the city waste dump. The walls of the garbage chamber are lined with glazed tiles, the floor is metal. In the waste chamber there is a cold and hot water pipe with a mixer for washing the waste duct, equipment and premises of the waste chamber. The garbage chamber is equipped with a drain with water draining into the household sewage system. A heating coil is provided in the floor. At the top, the garbage duct has an exit to the roof to ventilate the garbage chamber and through the garbage collection valves to remove stagnant air from the staircases, as well as smoke in the event of a fire. The entrance to the garbage chamber is separate, from the side of the street.
Organizational and Technical Section
3.1 Schedule
3.1.1 General part
Perform the works in accordance with the rules for the production and acceptance of construction and installation works and compliance with the construction production technology set out in the relevant chapters of SNiP 3.01.0185. The designed building has a structural scheme with transverse and longitudinal bearing walls. Floors in residential rooms, corridors - parquet; in bathrooms, showers, bathrooms and kitchens - ceramic tiles; on staircases - mosaic. Interior decoration of the building: in residential rooms, corridors - cover with you; ceilings - water emulsion whitewash; windows, doors - oil painting; bathrooms, showers, bathrooms and kitchens - facing with ceramic tiles.; storerooms - lime whitewash .
Water supply - combined household drinking water from the external network (hot water supply). Electric receivers - power supply from local networks. Low-current devices - telephone communication, radio. Sewerage - economic and fecal in the city network.
The following preparatory works shall be performed at the construction site prior to the start of the main construction and installation works:
cutting off the vegetal layer of soil with a bulldozer while preserving it for landscaping;
creating a geodetic basis for construction;
earthworks and planning works;
arrangement of temporary roads in accordance with the construction plan;
installation of temporary buildings and structures, arrangement of temporary engineering networks;
arrangement of storage areas, sites for pre-assembly, arrangement of canopies for storage of equipment and materials.
Excavation works shall be performed by excavator. Pit bottom cleaning is performed manually. Excess soil is exported by car dump trucks to the allotted place.
It is planned to carry out installation of designs of an elevated part of the building the tower crane.
Finishing works are planned to be carried out:
plaster - the plaster mobile station with application of rastvoronasos of CO48A and zatirochny CO112 cars;
painting - with use of painting station CO115, spackling EO53 installation, an airbrush manual, kraskoraspylitel manual, CO61 electroairbrush. The construction complex includes the construction of on-site networks.
Economic section
4.1 General Instructions
The pricing mechanism in construction has specific features. First of all, this is due to the individual nature of the buildings and structures under construction. Such circumstances do not allow setting uniform selling prices for construction products, as is done in other sectors of the national economy. Therefore, the price is mainly calculated individually on the basis of estimated documentation in accordance with the scope of work, methods of production technology and unit rates for certain types of work. To estimate the cost of construction products, a special pricing system has been developed. The current pricing system in construction is a separate part of the national standards of Construction Codes and Regulations (SNiP), part IV-2001 "Estimated Norms and Regulations."
The estimated cost is the basis for determining the amount of capital investments, financing construction, forming contractual prices for construction products, settlements for construction and installation works performed, payment for the costs of acquiring equipment and delivering it to construction sites, as well as for reimbursement of other costs from the funds provided for by the consolidated estimated calculation. On the basis of the estimated documentation, accounting, economic calculation and evaluation of the activities of construction and installation organizations and customers are carried out. Based on the estimated cost, the book value of the assets put into operation for the built enterprises, buildings and structures is determined. The estimated cost is the basis for the calculation of the feasibility of the designed facility, the justification and the decision on its construction.
Local estimates determine the estimated cost of certain types of work, structural elements of buildings and structures. The estimated cost when compiling local estimates for civil and special works consists of direct costs, overhead costs and planned savings.
Direct costs in local estimates are determined by multiplying the quantities of work accepted according to the working drawings by the corresponding price .
Overhead costs take into account the costs of construction and installation organizations related to the creation of general production conditions, its maintenance, organization and management .
Planned accumulations represent the normative profit of construction and installation organizations taken into account in the estimated cost of construction and installation works.
Conclusion
On the basis of the assignment, a diploma project was developed on the topic: a 14-story two-section residential building in the city of Uralsk.
The architectural and construction part of the project reflected volumetric and structural solutions, as well as materials for the construction of the main structural elements of the building.
In the design and structural part, the calculation of a multistage coating plate was carried out. As a result of the calculation, reinforcement was selected, and all the necessary strength and crack resistance checks were checked.
In the organizational and construction part, a comparison of technological solutions was made, as a result of which construction machines and mechanization tools were adopted, namely: for earthworks - bulldozer DZ130, excavator EO4321; for transportation - car MAZ516B; for installation works - self-propelled crane of underground part KS2561E; for an elevated part KB674A3 tower crane; for concrete and reinforced concrete works - concrete mixer SB130. A process plan for roofing works was developed. As new technologies, the use of mineral wool PAROC for heat insulation of the roof was proposed. Based on the volume of work, the labor costs of workers and machine time were calculated, the result of which was the development of a construction schedule. The construction period according to the calendar plan was 11 months. The maximum number of workers per shift on schedule was 88 people. Based on the maximum number of workers per shift, a construction plan was calculated and designed, in which the areas of warehouses and sites, the composition and area of temporary buildings, the construction site's need for water, electricity, compressed air were calculated.
In the economic part, estimates for roofing and civil works are presented. Most rationally approached the choice of building materials.
To protect the environment, the main hazards and measures to eliminate them were identified at the preparatory stage, as well as at the stages of the construction of the facility and the improvement of the territory.
The life safety section describes the main safety requirements for the transportation of materials, the operation of machines and mechanisms, the performance of work, as well as an assessment of the chemical situation in an accident - ammonia spill from the tank at a distance of 1200 m from the construction site.
As a result of the diploma project, the goals and objectives were achieved. The construction of the facility is carried out using new materials, more productive mechanisms, the least labor-intensive and most efficient technologies and methods of work are used, which was reflected in the final result.
Similar materials
- 09.07.2014
- 15.01.2022
- 09.07.2014
Free downloading for today
Other materials
- 04.11.2022