Разработка привода главного движения токарного станка




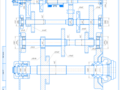
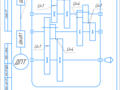
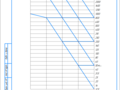
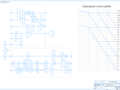
- Добавлен: 25.01.2023
- Размер: 143 KB
- Закачек: 1
Описание
Состав проекта
![]() |
![]() |
![]() ![]() ![]() |
![]() ![]() ![]() ![]() |
![]() ![]() ![]() |
![]() ![]() ![]() |
![]() ![]() ![]() ![]() |
![]() ![]() ![]() ![]() |
![]() ![]() ![]() |
![]() ![]() ![]() ![]() |
Дополнительная информация
белок.cdw

развертка станка.cdw

Привод гл. кинемат..cdw

структуная сетка.cdw

Рекомендуемые чертежи
- 22.11.2015
- 29.05.2022
- 13.02.2022
Свободное скачивание на сегодня
- 22.08.2014
- 29.08.2014