Проект привода главного движения токарного станка на базе станка с ЧПУ модели 16М20Ф3141




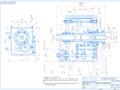
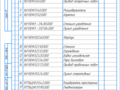
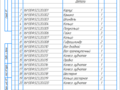
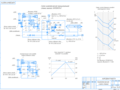
- Добавлен: 25.01.2023
- Размер: 354 KB
- Закачек: 2
Описание
Проект привода главного движения токарного станка на базе станка с ЧПУ модели 16М20Ф3141
Состав проекта
![]() |
![]() |
![]() ![]() ![]() ![]() |
![]() ![]() ![]() ![]() |
![]() ![]() ![]() ![]() |
![]() ![]() ![]() ![]() |
![]() ![]() ![]() |
![]() ![]() ![]() ![]() |
Дополнительная информация
Шпиндельный узел.spw

Станок16М30Ф3141.cdw

Шпиндельный узел.cdw

Спецификация-станок.spw

Кинематика станка.cdw

Рекомендуемые чертежи
- 29.05.2022
- 25.01.2023
- 22.11.2015