Проектирование привода главного движения токарного станка МК53КС



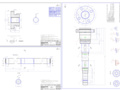
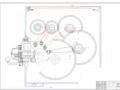
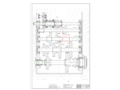
- Добавлен: 25.01.2023
- Размер: 757 KB
- Закачек: 0
Описание
Состав проекта
![]() |
![]() |
![]() ![]() ![]() ![]() |
![]() ![]() ![]() |
![]() ![]() ![]() ![]() |
![]() ![]() ![]() |
![]() ![]() ![]() ![]() |
Дополнительная информация
1Д325_z18_per2_razv.dwg

Техническая характеристика: 1. Число скоростей z=18 2. Мощность привода 5
кВт. 3. Пределы частот вращения шпинделя nmax=2000 мин
nmin=40 мин 4. Регулирование ступенчатое при помощи коробки скоростей с перебором.
Технические требования 1. Вращение входного вала коробки должно быть плавным
без толчков и заеданий. 2. В коробку залить масло И20 по ГОСТ 20799-75. 3. Динамическую балансировку производить в собранном виде.
D-8x36x40xH12a11 x8xF10j7
D-8x40x45xH12a11 x8xF10j7
D-8x46x52xH12a11 x8xF10j7
1Д325_P4_z18_perebor2_PZ.doc
В данном курсовом проекте выполняются проектно-конструкторские работы по созданию приводов главного движения подач токарно-револьверного станка по типу базового модели 1Д325. Проведены предварительный кинематический расчет уточненный силовой расчет и динамический расчет.
Графическая часть представлена двумя листами формата А1 на которых показаны развертка и свертка коробки скоростей.
Спроектировать приводы главного движения и подач горизонтально-фрезерного станка по типу базовой модели 6П80Г.
Тип привода – разделенный ступенчатый.
Пределы частот вращения:
Максимальная частота вращения: nma
Минимальная частота вращения: nm
Передаваемая мощность P = 5.2 кВт;
Число скоростей: z = 18;
Кинематический расчет привода главного движения.
В данном случае привод имеет ступенчатое регулирование. Он сочетает ступенчатую коробку скоростей с асинхронным двигателем. По [1] предполагаемый диапазон регулирования привода главного движения
где nma nmin=40 мин-1 максимальная и минимальная частоты вращения шпинделя соответственно.
По рекомендации [6] подбирается асинхронный двигатель 4АМ100S2УЗ имеющий мощность Р=4 кВт и частоту вращения n=1430 мин-1. Тогда согласно [1] знаменатель ряда j
По стандартному ряду принимается φ=141. Расчетная частота вращения шпинделя nрасч=118 мин-1:
В соответствии со структурной формулой привода коробка позволяет реализовать восемнадцать скоростей вращения выходного вала
Рисунок 1. структурная сетка привода главного движения
График частот вращения шпинделя и кинематическая схема коробки показаны на рис. 2 и 3.
Рисунок 2. График частот вращения шпинделя.
Рисунок 3. Кинематическая схема коробки скоростей
Подбор чисел зубьев осуществляется по нормалям станкостроения [1] и [2]. Откуда для рассматриваемых передач можно записать:
Определение потерь на каждом валу привода.
Известна формула для определения потерь на валах привода [2]:
где h hзп = 098 – КПД зубчатой передачи; hп = 099 – КПД подшипников. Тогда можно записать
Определение мощностей на валах.
Передаваемая валом мощность находится по формуле [5]
Предварительно диаметры валов находятся по формуле (см. [1]).
где K Pi – мощность на валу кВт ni – частота вращения вала мин–1.
Определение крутящих моментов.
Определение модуля зубчатой передачи
Исходные данные для расчета:
Коэффициент зависящий от материала зубчатых колес по [1] Kd = 770
Число зубьев шестерни z1 = 41 крутящий момент Mк1 = 29.9 Н·м коэффициент зависящий от распределения нагрузки по ширине зуба khb = 1.0. Коэффициент зависящий от распределения нагрузки по длине зуба kfb = 1.01. Передаточное отношение u = 1.26 отношение ширины венца к делительному диаметру
= 0.2. Принимаем материал сталь 40ХH. При этом допускаемые контактные напряжения соответствующие базовому числу циклов нагружения по [1]
H = 1000 МПа. Допускаемые изгибные напряжения соответствующие базовому числу циклов нагружения по [1] F = 320 МПа. Базовое число циклов нагружения для контактных напряжений по Nho = 100000000. Базовое число циклов нагружения для изгибных напряжений по [1] Nho = 4000000. Частота вращения n = 1250 мин-1. Коэффициент формы зуба по [1] Yf = 3.7. Коэффициент учитывающий тип колеса-прямозубые Km=14 по [1]. Коэффициент для контактных напряжений по [1] Khl = 1. Допускаемые контактные напряжения H=1000·1=1000 МПа. Расчетный коэффициент для изгибных напряжений Kfl=1. Допускаемые изгибные напряжения F = 320·1=320.
Значение модуля по контактным напряжениям
Значение модуля по изгибным напряжениям
Из конструктивных соображений принимается m=2 мм.
Коэффициент зависящий от материала зубчатых колес по [1] Kd = 770. Число зубьев шестерни z1 = 37. Крутящий момент M = 36.23 Н·м. Коэффициент зависящий от распределения нагрузки по ширине зуба по [1] khb = 1.0. Коэффициент зависящий от распределения нагрузки по длине зуба по [1] kfb=1.01. Передаточное отношение u = 1.26. Отношение ширины венца к делительному диаметру = 0.2. Материал сталь 40ХH. Допускаемые контактные напряжения соответствующие базовому числу циклов нагружения по [1] H = 1000 МПа. Допускаемые изгибные напряжения соответствующие базовому числу циклов нагружения по [1] F = 320 МПа. Частота вращения n=1000 мин-1. Коэффициент формы зуба по [1] Yf=3.71. Коэффициент учитывающий тип колеса-прямозубые Km=14 по [1].
Коэффициент для контактных напряжений Khl = 1. Допускаемые контактные напряжения H=1000·1=1000. Расчетный коэффициент для изгибных напряжений Kfl=1. Допускаемые изгибные напряжения F = 320·1=320 МПа.
Из конструктивных соображений принимается m=2.5 мм.
Коэффициент зависящий от материала зубчатых колес по [1] Kd = 770. Число зубьев шестерни z1 = 20. Крутящий момент M = 55.6 Н·м.
Коэффициент зависящий от распределения нагрузки по ширине зуба по [1] khb = 1.02. Коэффициент зависящий от распределения нагрузки по длине зуба по [1] kfb = 1.04. Передаточное отношение u = 4.00. Отношение ширины венца к делительному диаметру = 0.4. Материал сталь 40ХH. Допускаемые контактные напряжения соответствующие базовому числу циклов нагружения по [1] H=1000. Допускаемые изгибные напряжения соответствующие базовому числу циклов нагружения по [1] F = 320. Базовое число циклов нагружения для контактных напряжений по [1] Nho = 100000000. Базовое число циклов нагружения для изгибных напряжений по [1] Nho = 4000000. Частота вращения n = 630 мин-1 . Коэффициент формы зуба по [1] Yf = 4.08. Коэффициент учитывающий тип колеса-прямозубые Km=14 по [1]. Расчетное число циклов нагружения Nhe=75600000. Коэффициент для контактных напряжений Khl=1. Допускаемые контактные напряжения H=1000·1=1000 МПа. Коэффициент для изгибных напряжений Kfl=1. Допускаемые изгибные напряжения F= 320·1=320 МПа..
Из конструктивных соображений принимается m=3 мм.
Коэффициент зависящий от материала зубчатых колес по т. Kd = 770. Число зубьев шестерни z1 = 20. Крутящий моментM = 271.2. Коэффициент зависящий от распределения нагрузки по ширине зуба по [1] khb = 1.02. Коэффициент зависящий от распределения нагрузки по длине зуба по [1] kfb=1.04. Передаточное отношение u = 4.00. Отношение ширины венца к делительному диаметру =0.6. Материал сталь 40ХH. Допускаемые контактные напряжения соответствующие базовому числу циклов нагружения по [1].H=1000.Допускаемые изгибные напряжения соответствующие базовому числу циклов нагружения по [1] F = 320. Базовое число циклов нагружения для контактных напряжений по [1]. Nho = 100000000. Базовое число циклов нагружения для изгибных напряжений по [1] Nho = 4000000. Частота вращения n = 125 мин-1. Коэффициент формы зуба по [1] Yf = 4.08. Коэффициент учитывающий тип колеса-прямозубые Km=14 по [1]. Расчетное число циклов нагружения Nhe = 15000000. Коэффициент для контактных напряжений Khl=1. Допускаемые контактные напряжения
H = 1000 ·1=1000 МПа. Коэффициент для изгибных напряжений Kfl = 1. Допускаемые изгибные напряжения F = 320 ·1=320 МПа.
Из конструктивных соображений принимается m=3.5 мм.
Геометрические параметры зубчатых передач рассчитываются по следующим формулам:
Делительный диаметр d=m·z мм.
Внешний диаметр da=d-2.25·m мм.
Внутренний диаметр dv=d+2·m мм.
Таблица 1. Геометрические параметры зубчатых передач
Уточненный силовой расчет привода главного движения
Модуль m=2 мм делительный диаметр зубчатого колеса d = 0.092 м площадь поперечного сечения ременной передачи s0 = 0.001 м2 крутящий момент Mk = 29.9 Н·м расстояния между силовыми факторами L1 = 0.09 м L2 = 0.278 м L3 = 0.32 м. Схема проекций сил на оси показана на рис.
Рисунок 4. Схема свертки для вала 1
Окружная сила в зубчатом зацеплении
Px2 = 2·Мкрd=650.0 Н.
Сила от ременной передачи
Py1 =Px1·0.5= 482.8 Н.
Py2 =Px2·0.5= 325.0 Н.
Результирующая сила от зубчатой передачи
Q2 =1.1· Px2= 715.0 Н.
Результирующая сила от ременной передачи
Q1 = 1.1· Px1=1062.16 Н.
от ременной передачи
Q1x = Q1·cos(60)= 531.57 Н.
от зубчатой передачи
Q2x = Q1·cos(63)= 324.95 Н.
Рисунок 5. Схема развертки для вала 1
Q1y =Q1·sin(60)= 919.57 Н.
Q2y = Q2·sin(63)= 636.88 Н.
- L1·Q1x+ L2·Q2x-( L1+ L2)·Rbx=0
Rbx=( L2·Q2x- L1·Q1x) ( L1+ L2)= -42.490.598=-71.06 Н.
- L3·Q2x-( L1+ L2+ L3)·Q1x+( L1+ L2)·Rbx=0
Rbx= (L3·Q2x+( L1+ L2+ L3)·Q1x) ( L1+ L2)=-469.70715080.598=-785.46 Н.
Уравнение моментов в плоскости x
Mx11 = Q1x·x1=47.8 Н·м.
Mx12 = Q1x·(x2+0.09)+ Rax·x2= -22.7 Н·м.
Mx13 = Rbx·x= -22.7 Н·м.
Эпюра моментов в плоскости x
Рассмотрим плоскость y:
-259.8171774 + 0.598 Rby = 0
8.8662239 + 0.598 Ray = 0
Уравнение моментов в плоскости y
My1= Q1y·y=182.8 Н·м.
My2= Q1y·(y2+0.09)+ Ray·y2= 139. Н·м.
My3= Rby·y= 139. Н·м.
Максимальный момент Н:м
Принимаем d = 3. см. Значения справочных коэффициентов K1x=0.2 K2x = -0.5 K1y = 0.2 K2y = -0.35.
Угол наклона упругой линии в плоскости x от каждой силы
Результирующий угол наклона упругой линии в плоскости x
Угол наклона упругой линии в плоскости y от каждой силы
Результирующий угол наклона упругой линии в плоскости y
Результирующий угол наклона
По рекомендации [4] допустимый угол наклона упругой линии [q]=0001 тогда [q]>q или 000100008. Т.о. рассчитываемый вал проходит по данному критерию прочности.
Также нужно определить прогиб
Прогиб в плоскости x
Результирующий прогиб в плоскости x
Прогиб в плоскости y
Результирующий прогиб в плоскости y
Результирующий макс. прогиб
y1 = 0.0002319681039
Максимально допустимый прогиб
Модуль m=2.5 мм делительные диаметры зубчатых колес d1= 0.092 м d2=0. 0925 м крутящий момент Mk = 36.23 Н·м расстояния между силовыми факторами L1 = 0. 27м L2 = 0. 082 м L3 = 0.24 м. Схема проекций сил на оси показана на рис.
Окружные силы действующие в зубчатом зацеплении
Px1 = 2·Мкрd1=787.608 Н.
Px2 = 2·Мкрd2=783.352 Н.
Рисунок 6. Схема свертки для вала 2
Py1 =Px1·0.5= 393.804 Н.
Py2 =Px1·0.5= 391.676 Н.
Q1 =1.1· Px2= 866.369 Н.
Q2 = 1.1· Px2= 861.687 Н.
Q1x =Q1·cos(60)= 393.753 Н.
Q2x =Q1·cos(60)= 391.626 Н.
Q1y =Q1·sin(60)= 771.721 Н.
Q2y =Q1·sin(60)= 767.550 Н.
Рассмотрим плоскость x:
Вычисление реакции опоры В нужно производить по формуле
- L1·Q1x+ ( L1+ L2)·Q2x-( L1+ L2+ L3)·Rbx=0
Rbx=(- L1·Q1x+ ( L1+ L2)·Q2x)=- 31.5390420.592 -53.275 Н.
Вычисление реакции опоры А нужно производить по формуле
- L3·Q2x-( L2+ L3)·Q1x+( L1+ L2+ L3)·Rax=0
Rbx= (- L3·Q2x-( L2+ L3)·Q1x)( L1+ L2+ L3)=32.7982260.592=55.402 Н.
Проверка правильности по сумме всех сил в этой плоскости
Рисунок 7. Схема развертки для вала 2
Mx11=x·Rax= 14.96 Н·м.
Mx12= (0.27+x) ·Rax-Q1x·x= -12.79 Н·м.
Mx13=-x·Rby= -12.79 Н·м.
-61.812930 + 0.592 Rby = 0
Откуда сама реакци опоры В
-64.282162 - 0.592 Ray = 0
Откуда сама реакци опоры А
My1 =y·Ray= -29.32 Н·м.
My2=(0.27+y) ·Ray-Q1y·y= 25.05 Н·м.
My3=-y·Rby= 25.06 Н·м.
Эпюра моментов в плоскости y
Результирующие моменты M
Максимальный момент =32.92 Н·м.
Результирующая опорная реакция Ra
Результирующая опорная реакция Rb
Значения справочных коэффициентов K1x = 0.05 K2x = -0.12 K1y = 0.05 K2y = -0.02.
Угол наклона упругой линиии в плоскости x
Угол наклона упругой линиии в плоскости y
По рекомендации [4] допустимый угол наклона упругой линии [q]=0001 тогда [q]>q или 000100002. Т.о. рассчитываемый вал проходит по данному критерию прочности.
Прогиб в плоскости x от каждой силы
Прогиб в плоскости y от каждой силы
Модуль m=3 мм делительные диаметры зубчатых колес d1= 0.1475 м d2=0.060м крутящий момент Mk = 55.6 Н·м расстояния между силовыми факторами L1 = 0.306 м L2 = 0.046 м L3 = 0.24 м. Схема проекций сил на оси показана на рис.
Рисунок 8. Схема свертки для вала 3
Px1 =2·Мкрd1= 753.898 Н.
Px2 =2·Мкрd2= 1853.33 Н.
Py1 =Px1·0.5= 376.949 Н.
Py2 =Px2·0.5= 926.665 Н.
Q1 =1.1· Px1= 829.288 Н.
Q2 =1.1· Px2= 2038.66 Н.
Q1x =Q1·cos(63)= 376.901 Н.
Q2x =Q2·cos(52)= 1255.86 Н.
Q1y =Q1·sin(63)=738.691 Н.
Q2y =Q2·sin(52)=1605.91 Н.
- L1·Q1x+ (L1+ L2)·Q2x-( L1+ L2+ L3)·Rbx=0
Rbx=(- L1·Q1x+ ( L1+ L2)·Q2x)=326.731014 0.592 = 0
Rbx= (- L3·Q2x-( L2+ L3)·Q1x)( L1+ L2+ L3)=-193.6127140.592 = 0
Mx11=x·Rax= -100.1 Н·м.
Mx12=(0.306+x) ·Rax-Q1x·x= -132.5 Н·м.
Mx13=-x·Rby= -132.5 Н·м.
-791.319766 + 0.592 Rby = 0
6.684026 - 0.592 Ray = 0
My1=y·Ray= 308.4 Н·м.
My2= (0.306+y) ·Ray-Q1y·y=320.8 Н·м.
My3=y·Rby= 320.9 Н·м.
Рисунок 9. Схема развертки для вала 3
Результирующие мом M
Принимаем d0 = 3.5 см K1x = -0.1 K2x = 0.2 K1y = 0.2 K2y = 0.19.
Угол наклона упругой линии в плоскости y
Модуль m=3.0 мм делительные диаметры зубчатых колес d1= 0.237 м d2=0.070 м крутящий момент Mk=271.2 Н·м расстояния между силовыми факторами L1= 0.306 м L2= 0.124 м L3= 0.163 м. Схема проекций сил на оси показана на рис.
Рисунок 10. Схема свертки для вала 4
Px1 =2·Мкрd1= 2288.60 Н.
Px2 = 2·Мкрd3=7748.58 Н.
Py1 =Px1·0.5= 1144.30 Н.
Py2 =Px2·0.5= 3874.29 Н.
Q1 =1.1· Px1= 2517.46 Н.
Q2 =1.1· Px2= 8523.44 Н.
Q1x =Q1·cos(52)= 1550.82 Н.
Q2x =Q2·cos(35)= 6983.50 Н.
Q1y =Q1·sin(52)= 1983.07 Н.
Q2y =Q2·sin(35)= 4886.68 Н.
-L1·Q1x+ (L1+ L2)·Q2x-( L1+ L2+ L3)·Rbx=0
Rbx=(L1·Q1x+ ( L1+ L2)·Q2x) ( L1+ L2+ L3)=-3477.455920.593=-5864.2 Н.
Rbx= (L3·Q2x+( L1+ L2+ L3)·Q1x) ( L1+ L2)=-1583.39584 - 0.593 Rax = 0
Рисунок 11. Схема развертки для вала 4
Mx1 =- x·Rax= -817.1 Н·м.
Mx2= (0.306+x) ·Rax-Q1x·x= -955.9 Н·м.
Mx3= -x·Rby= -955.9 Н·м.
94.45298 + 0.593 Rby = 0
-227.38775 - 0.593 Ray = 0
My1= -y·Ray= -117.4 Н·м.
My2= (0.306+y) ·Ray-Q1y·y=-410.8 Н·м.
My3=- y·Rby= -410.8 Н·м.
Принимаем K1x = -0.13 K2x=0.05 K1y = 0.13 K2y = -0.05.
Модуль m=3.5 мм делительный диаметр зубчатого колеса d1=0.126м крутящий момент Mk =261.8 Н·м расстояния между силовыми факторами L1=0.14 L2=0.174 м L3 =0.427 м. Схема проекций сил на оси показана на рис.
Рисунок 12. Схема свертки для вала 5
Диаметр делительной окружности зубчатого колеса d = 0.126 м диаметр подшипника опоры А (внутренний) d1 = 45 мм (наружный) D1= 90 мм диаметр опоры В (внутренний) d2 = 100 мм (наружный) D2= 150 мм крутящий момент Mk = 261.8 Н·м составляющие силы резания Pz = 4000 Н Py=2000 Н
L1= 0.14 м L2= 0.174 м L3= 0.427 м E = 2МПа = 0.2
Px2 =2·Мкрd= 4155.56 Н.
Py2 = Px1·0.5=2077.78 Н.
Q2 =1.1· Px2= 4571.12 Н.
Q2x =Q1·cos(35)= 3745.25 Н.
Q2y =Q1·sin(35)= 2620.73 Н.
90.89525 + 0.174 Rbx = 0
Откуда сама реакции опоры В
3.22175 - 0.174 Rax = 0
Откуда сама реакции опоры А
-1855.05873 + 0.174 Rby = 0
-1747.05171 - 0.174 Ray = 0
Рисунок 13. Схема развертки для вала 5
Расчет на жесткость для шпинделя сводится к определению радиального биения переднего конца шпинделя по формуле:
где PZ=4000 H тангенциальная составляющая силы резания Н; JA JB осевые моменты инерции в сечениях А и В мм4; jA jB жесткости в сечениях А и В Нмм; a=100 мм величина консоли; b=586 мм межопорное расстояние; E=2·105 МПа модуль упругости материала шпинделя.
Радиальная жесткость:
Согласно рекомендациям справочной литературы наименьшее поле допуска деталей обрабатываемых на данном станке должно быть .
Приведенный момент масс для вала определяем по формуле:
где это момент инерции сосредоточенной массы например зубчатого колеса муфты и т.п.; Jl12 моменты инерции пролетов вала слева и справа от данной сосредоточенной массы (т.е. это моменты инерции распределенных масс)
Поэтому динамический расчет привода главного движения состоит из отдельных частей:
Вычисление суммарного момента инерции всей системы (на этом же этапе нужно найти момент инерции двигателя и приводного элемента). На этой стадии вычисляются приведенные моменты инерции отдельных валов после чего они суммируются;
Определение суммарной податливости всей системы (здесь определяются податливости составляющих систему элементов с учетом передаточных отношений зубчатых колес и нагрузок на подшипниковые узлы);
Анализ устойчивости системы. Здесь осуществляется приведение системы из многомассовой к двухмассовой и определяется приведенный момент инерции всей системы и строится амплитуднофазочастотная характеристика системы (АФЧХ). На основании этого графика делается заключение об устойчивости системы.
Определение эквивалентного приведенного момента инерции системы
1 Определение момента инерции двигателя.
В данном случае используется двигатель постоянного тока поэтому формула для вычисления момента имеет вид ( см. [1]).
Jdv=0.075*G*(0.5*d30)2
где G масса двигателя d30 внешний диметр ЭД взятые из справочных данных [1]. При заданной массе G= 56.00 кг и диаметре d30=0.2350 мм
Jdv=0.075* 56.00*(0.2350*0.5) 2=5798.6250*10-5
Поскольку в данном случае приводным элементом является ременная передача то расчет начинается с определения ее приведенных моментов инерции. Момент инерции Jl=78.04*0.1000*0.0300^4=0.6321*10-5
Момент инерции шкива Jшк11=78.04*0.0700*0.18004=573.4629*1010-5
Суммарный момент инерции шкива J=573.4629*10-5
определяется по формуле J1+(Jl1+Jl2)3=573.4629*10-5+13*(0.6321+0.0000) *10-5=573.6736*10-5
Теперь можно перейти к расчету приведенных моментов на каждом валу
Вычисление моментов инерции длин вала №1
Момент инерции длины Jl11=*0.0000*0.00104=0.0000*10-5
Момент инерции длины Jl1=0.0000*10-5
Момент инерции длины Jl21=*0.3680*0.03004=2.3262*10-5
Момент инерции длины Jl2=2.3262*10-5
Момент инерции длины Jl31=*0.3200*0.03504=3.7475*10-5
Момент инерции длины Jl3=3.7475*10-5
Кол-во сосредоточенных масс на данном валу n=2
Для них можно записать что
Момент инерции ступеньки 1 распределенной массы 1
J11=78.04* 0.080* 0.1804=655.3862*10-5
Суммарный приведенный момент инерции данной массы J=J1+(Jl1+Jl2)3=655.3862*10^(-5)+13*(0.0000+2.3262)*10-5=656.1616*10-5
Момент инерции ступеньки 1 распределенной массы 2
J21=78.04* 0.278* 0.1104=317.6383*10-5
С учетом передаточного отношения этот м. и. равен Jj^2=317.6383*10-5 1.00^2=317.6383*10-5
Суммарный приведенный момент инерции данной массы
J1+(Jl1+Jl2)6=317.6383*10-5+16*(2.3262+3.7475) *10-5=318.6505*10-5
Суммарный момент инерции для всего вала J=973.7998*10-5
Вычисление моментов инерции длин вала №2
Момент инерции длины Jl11=*0.0860*0.03504=1.0071*10-5
Момент инерции длины Jl1=1.0071*10-5
Момент инерции длины Jl21=*0.2040*0.03504=2.3890*10-5
Момент инерции длины Jl2=2.3890*10-5
Момент инерции длины Jl31=*0.0820*0.03504=0.9603*10-5
Момент инерции длины Jl3=0.9603*10-5
Момент инерции длины Jl41=*0.2400*0.03504=2.8106*10-5
Момент инерции длины Jl4=2.8106*10-5
Кол-во сосредоточенных масс на данном валу n=3
J11=78.04* 0.066* 0.0624=7.6108*10-5
Суммарный приведенный момент инерции данной массы J=J1+(Jl1+Jl2)6=7.6108*10-5+16*(1.0071+2.3890)* 10-5=8.1768*10-5
J21=78.04* 0.016* 0.0554=1.1426*10-5
Момент инерции ступеньки 2 распределенной массы 2
J22=78.04* 0.026* 0.0864=11.0990*10-5
Момент инерции ступеньки 3 распределенной массы 2
J23=78.04* 0.020* 0.0944=12.1859*10-5
Суммарный приведенный момент инерции данной массы J=J1+(Jl1+Jl2)6=24.4275*10-5+16*(2.3890+0.9603) *10-5=24.9857*10-5
Момент инерции ступеньки 1 распределенной массы 3
J31=78.04* 0.034* 0.0824=11.9964*10-5
Момент инерции ступеньки 2 распределенной массы 3
J32=78.04* 0.020* 0.1204=32.3647*10-5
С учетом передаточного отношения этот м. и. равен Jj2=44.3612*10-5 1.512=19.4558*10-5
J1+(Jl1+Jl2)6=19.4558*10-5+16*(0.9603+2.8106) *10-5=20.0843*10-5
Суммарный момент инерции для всего вала J2=52.6183*10-5
Вычисление моментов инерции длин вала №3
Момент инерции длины Jl11=78.04*0.1720*0.04004=3.4363*10-5
Момент инерции длины Jl1=3.4363*10-5
Момент инерции длины Jl21=*0.1320*0.04004=2.6371*10-5
Момент инерции длины Jl2=2.6371*10-5
Момент инерции длины Jl31=*0.0470*0.04004=0.9390*10-5
Момент инерции длины Jl3=0.9390*10-5
Момент инерции длины Jl41=*0.2400*0.04004=4.7948*10-5
Момент инерции длины Jl4=4.7948*10-5
J11=78.04* 0.040* 0.0854=16.2949*10-5
Момент инерции ступеньки 2 распределенной массы 1
J12=78.04* 0.030* 0.1824=256.8763*10-5
Суммарный приведенный момент инерции данной массы J=J1+(Jl1+Jl2)6=273.1713*10-5+16*(3.4363+2.6371) *10-5=274.1835*10-5
J21=78.04* 0.031* 0.1444=104.0229*10-5
J22=78.04* 0.042* 0.0684=7.0081*10-5
С учетом передаточного отношения этот м. и. равен Jj^2=111.0310*10-5 4.00^2=6.9394*10-5
J1+(Jl1+Jl2)6=6.9394*10-5+16*(2.6371+0.9390) *10-5=7.5355*10-5
J31=78.04* 0.020* 0.1584=97.2693*10-5
J32=78.04* 0.072* 0.0804=23.0149*10-5
Момент инерции ступеньки 3 распределенной массы 3
J33=78.04* 0.020* 0.1204=32.3647*10-5
Суммарный приведенный момент инерции данной массы J=J1+(Jl1+Jl2)6=152.6489*10-5+16*(0.9390+4.7948) *10-5=153.6046*10-5
Суммарный момент инерции для всего вала J3=434.7275*10-5
Вычисление моментов инерции длин вала №4
Момент инерции длины Jl11=*0.0800*0.04504=2.5601*10-5
Момент инерции длины Jl1=2.5601*10-5
Момент инерции длины Jl21=*0.2260*0.04504=7.2323*10-5
Момент инерции длины Jl2=7.2323*10-5
Момент инерции длины Jl31=*0.1260*0.04504=4.0322*10-5
Момент инерции длины Jl3=4.0322*10-5
Момент инерции длины Jl41=78.04*0.1630*0.04504=5.2162*10-5
Момент инерции длины Jl4=5.2162*10-5
J11=* 0.030* 0.1644=169.3612*10-5
J12=* 0.049* 0.1144=64.5852*10-5
Суммарный приведенный момент инерции данной массы J=J1+(Jl1+Jl2)6=233.9464*10-5+16*(2.5601+7.2323) *10-5=235.5784*10-5
J21=* 0.030* 0.1834=262.5687*10-5
J22=* 0.056* 0.0924=31.3081*10-5
J23=* 0.030* 0.2284=632.6710*10-5
Суммарный приведенный момент инерции данной массы J=J1+(Jl1+Jl2)6=926.5477*10-5+16*(7.2323+4.0322) *10-5=928.4251*10-5
J31=* 0.054* 0.0804=17.2612*10-5
J32=* 0.035* 0.2244=687.6657*10-5
С учетом передаточного отношения этот м. и. равен Jj^2=704.9269*10-5 4.00^2=44.0579*10-5
J1+(Jl1+Jl2)6=44.0579*10-5+16*(4.0322+5.2162) *10-5=45.5993*10-5
Суммарный момент инерции для всего вала J4=1208.0615*10-5
Вычисление моментов инерции длин вала №5
Момент инерции длины Jl11=*0.1200*0.05004=5.8530*10-5
Момент инерции длины Jl1=5.8530*10-5
Момент инерции длины Jl21=*0.3060*0.06504=42.6277*10-5
Момент инерции длины Jl2=42.6277*10-5
Момент инерции длины Jl31=*0.3080*0.09004=157.7023*10-5
Момент инерции длины Jl3=157.7023*10-5
Момент инерции длины Jl41=*0.0000*0.00104=0.0000*10-5
Момент инерции длины Jl4=0.0000*10-5
J11=* 0.030* 0.1854=274.2366*10-5
J12=* 0.039* 0.1024=32.9445*10-5
Суммарный приведенный момент инерции данной массы J=J1+(Jl1+Jl2)6=307.1811*10-5+16*(5.8530+42.6277) *10-5=315.2612*10-5
J21=* 0.035* 0.2704=1451.5779*10-5
J22=* 0.062* 0.1064=61.0847*10-5
J23=* 0.035* 0.1264=68.8442*10-5
Суммарный приведенный момент инерции данной массы J=J1+(Jl1+Jl2)6=1581.5069*10-5+16*(42.6277+157.7023)*10-5=1614.8952*10-5
J31=* 0.080* 0.1804=655.3862*10-5
С учетом передаточного отношения этот м. и. равен Jj2=655.3862*10-5 1.002=655.3862*10-5
J1+(Jl1+Jl2)3=655.3862*10-5+13*(157.7023+0.0000) *10-5=707.9536*10-5Суммарный момент инерции для всего вала J=2585.5426*10-5
Расчет податливостей
Определение податливости электромагнитного поля асинхронного двигателя
Из силового расчета: номинальная частота вращения nd=1430.0 мин-1
Из силового расчета: номинальная мощность Pnom= 4.000 кВт
Из справочных материалов: число полюсов p= 4
Номинальный крутящий момент Mnom=9.55* 41430.0=26.713 Н*м.
Критический крутящий момент
Mk=Mnom*lamb=26.713* 3.0000000=80.1399 Н*м.
Едв=1(2*р*Мкр)=1(2*4*80.1399)=155.9*10-5
Определение податливости ременной передачи
По справочным данным принимаем:
-площадь поперечного сечения ремня F= 0.81 *10-5 м 2
-расчетная длина ветви L= 1.0 м
-диаметр первого шкива Dср= 0.090 м
-диаметр второго шкива Dср= 0.090 м
Податливость первого шкива
eшк1= 1.0(2* 0.090 2*3500 *10-6* 0.81*10-6)= 0.0001*10^(-5) радНм
Податливость второго шкива
ешк2= 1.0(2* 0.090 2*3500*10-6* 0.81*10-6)= 0.0001*10^(-5) радНм
Расчет крутильной податливости для каждого вала производится по методике изложенной в работе.
1 Расчет крутильной податливости для вала 1
Количество элементов данного участка: 1
Элемент 1. Сплошной вал
D=0.0300м l=0.3570м
Суммируя эти значения податливостей можно получить крутильную податливость
вала без учета податливостей подшипников и зубчатых колес
е1=( 5.60) *10-5= 5.60*10-5
2 Расчет крутильной податливости для вала 2
Элемент 1. Шлицевой вал
диаметр d=0.0350м и длина l=0.0820м
е2=( 0.69) *10-5= 0.69*10-5
3 Расчет крутильной податливости для вала 3
диаметр d=0.0400м и длина l=0.0480м
е3=( 0.24) *10-5= 0.24*10-5
4 Расчет крутильной податливости для вала 4
диаметр d=0.0450м и длина l=0.1240м
е4=( 0.38) *10-5= 0.38*10-5
5 Расчет крутильной податливости для вала 5
Количество элементов данного участка: 2
Элемент 1.Вал диаметра D с осевым отверстием d
Коэффициент К=1(1-dD)= 2.429
D=40.0000м d=68.0000м l=0.1170м
Элемент 2.Вал диаметра D с осевым отверстием d
Коэффициент К=1(1-dD)= 2.000
D=50.0000м d=100.0000м l=0.1620м
е5=(0.07+0.02)*10-5= 0.09*10-5
Момент инерции двигателя
Моменты инерции валов
Суммарный момент инерции системы
J=(973.7998+52.6183+434.7275+1208.0615+2585.5426+2313.71)*10-5 =2977.57·10-5
Податливости валов системы
Податливость всей системы
Уравнения для построения АФЧХ на комплексной плоскости
Принимаем =0 тогда Re=0.03 а Ie=0
=1000 тогда Re=0.01 а I=-0.014
=1Т1 тогда Re=0 а Ie=-0.035
=6000 тогда Re=-0.017 а Ie=-0.026
=7000 тогда Re=-0.017 а Ie=-0.013
=10000 тогда Re=-0.000003 а Ie=-0.0000000000020
Вывод: т.к. крайняя координата АФЧХ на рисунке 5 правее -1 то можно сделать вывод об устойчивости данной системы.
1Д325_z18_per2_svertk.dwg

1Д325z18_perr2_specific.doc
Селективный механизм
Шпонка ГОСТ 23360-80
Кольцо ГОСТ 13941-86
Кольца ГОСТ 13942-86
Подшипник ГОСТ 8838-75
Подшипник ГОСТ 8890-75
Подшипник ГОСТ 9890-75
1Д325_z18_per2_det.dwg

HRC 45..52 2. Неуказанные предельные отклонения размеров: диаметров H12
прочих +IT122. 3. Данные для контроля зубчатых венцов выбираются по ГОСТ 1643-72.
Улучшить HRC 32..35. 2. Неуказанные предельные отклонения размеров: диаметров H12
прочих +IT122. 3. Неуказанные радиусы R0.5
Изм.Лист №докум. ПодписьДата
Кафедра:"МСиК" гр. 97МС2
Кафедра:"МСиК" гр. 99МС2
Исходный контур по ГОСТ13755-68
Коэффициент смещения
Форма закругления зубьев
Перекос шпоночного паза на его длине не более 0.025. 2. Улучшить HRC 32..35. 3. Конец шпинделя выполнить по ГОСТ 12593-72. 4. Отклонение от цилиндричности поверхностей Г и Д не более 0.002 мм. 5. Торцевое биение поверхности Е относительно общей оси не более 0.003 мм. 6. Поверхности Г и Д подвергнуть термообработке ТВЧ h 1..1.5 мм.
Рекомендуемые чертежи
- 22.11.2015
- 29.05.2022
- 22.04.2022