Проектирование привода главного движения для специального станка на базе серийно выпускаемой модели 1708




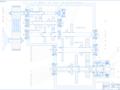
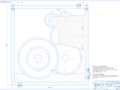
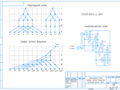
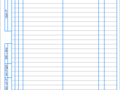
- Добавлен: 25.01.2023
- Размер: 751 KB
- Закачек: 0
Описание
Состав проекта
![]() |
![]() |
![]() ![]() ![]() ![]() |
![]() |
![]() ![]() ![]() ![]() |
![]() ![]() ![]() ![]() |
![]() ![]() ![]() ![]() |
![]() ![]() ![]() ![]() |
![]() ![]() ![]() |
![]() ![]() ![]() ![]() |
Дополнительная информация
Свертка2.cdw

1.frw

2.frw

Спецификация.cdw

Развертка.cdw

Схема.cdw

Рекомендуемые чертежи
- 25.01.2023
- 29.05.2022
- 16.11.2023
- 22.11.2015