Стационарный кран с вращающейся колонной грузоподъемностью 3 тонны




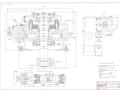
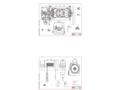
- Добавлен: 25.10.2022
- Размер: 2 MB
- Закачек: 2
Описание
Состав проекта
![]() |
![]() ![]() ![]() ![]() |
![]() ![]() ![]() |
![]() ![]() ![]() ![]() |
![]() ![]() ![]() ![]() |
![]() ![]() ![]() |
Дополнительная информация
Мех-м поворота.dwg

Технические характеристики: 1. Частота вращения крана
обмин: 1.5 2. Электродвигатель: Тип: MTF 011-6 Мощность
кВт 1.7 Частота вращения
обмин 850 3. Редуктор: Тип: РЧ160 Передаточное отношение: 80 4. Тормоз: Тип: ТКГ-160 Тормозной момент
N 7211A ГОСТ 27365-87
(пробка условно не показана)
Стационарный кран с вращающейся колонной гп 3 т
МГТУ им. Н.Э. Баумана кафедра РК4 группа РК4-71
Стационарный поворотный кран Q=5т
Общий вид.dwg
;1. Грузоподъемность
т 3 2. Высота подъема груза
м 18 3. Группа режима работы 4А 4. Скорость подъема груза
ммин 8 5. Вылет крюка
м наибольший 4 наименьший 0
6. Угол поворота консоли 270° 7. Скорость поворота
Стационарный кран с вращающейся колонной гп 3 т
МГТУ им. Н.Э. Баумана кафедра РК4 группа РК4-71
Электроталь.dwg

Стационарный кран с вращающейся колонной гп 3 т
МГТУ им. Н.Э. Баумана кафедра РК4 группа РК4-71
Техническая характериситика i-3
;1. Грузоподъемноcть
т 3 2. Высота подъема груза
м 18 3. Группа режима работы 4М 4. Скорость подъема груза
ммин 8 5. Электродвигатель тип 4АВ112В8У3 мощность
обмин 670 6. Канат 13-Г-I-Л-Н-1764 ГОСТ 3077-80
ОПУ.dwg

Стационарный кран с вращающейся колонной гп 3 т
МГТУ им. Н.Э. Баумана кафедра РК4 группа РК4-71
РПЗ.docx
и ордена Трудового Красного Знамени
Государственный Технический Университет им. Н. Э. Баумана
Расчетно-пояснительная записка
к курсовому проекту на тему
“Стационарный кран с вращающейся колонной грузоподъемностью 3т”
Факультет:Робототехника и комплексная автоматизация
Группа:РК4-71 (Подъемно-транспортные машины)
Студент: Филиппенко Светлана Владимировна
Руководитель:Ромашко Александр Мефодиевич
Техническое задание.3
Расчет механизма подъема.4
1.Выбор схемы полиспаста.4
2.Определение максимального усилия в ветви каната набегающего на барабан.4
4.Мощность электродвигателя и его выбор.5
5.Определение диаметра барабана.5
6.Определение длины барабана.5
7.Определение частоты вращения барабана.6
8.Определение передаточного отношения и выбор редуктора.6
9.Проектные расчеты диаметров валов8
10.Предварительный расчет длины вала.9
11.Конструирование корпуса редуктора.9
12.Расчет стенки барабана на прочность.10
13.Проверка стенки барабана на устойчивость.10
14.Расчет крепления конца каната на барабане.11
15.Расчет подшипников барабана.12
16.Расчет тормоза.13
17.Расчет грузоупорного тормоза15
18.Расчет промежуточного вала редуктора17
18.1Подбор подшипников качения на заданный ресурс17
18.2Расчет промежуточного вала на статическую прочность20
19.Определение времени пуска и ускорения .22
20.Определение времени торможения и замедления .22
Опорно-поворотное устройство24
1.Определение нагрузок действующих на ОПУ24
2.Определение реакций в опорах.24
3.Момент сопротивления повороту крана от сил трения в опорно-поворотном устройстве24
4.Момент сил инерции25
5.Определение мощности и выбор электродвигателя.25
6.Проверка выбранного электродвигателя26
7.Определение предельного расчетного момента муфты27
8.Определение необходимой силы прижатия диска27
9.Определение тормозного момента на валу двигателя28
Техническое задание.
Целью данного курсового проекта является проектирование стационарного крана с вращающейся колонной.
Скорость передвижения электротали
Группа режима работы
Управление краном осуществляется с пола с помощью пульта управления.
Данная работа содержит расчёты механизма подъёма и механизма поворота крана а также сборочные чертежи механизма подъёма крана механизма поворота крана опорно-поворотного устройства крана и чертёж общего вида крана.
Расчет механизма подъема.
1.Выбор схемы полиспаста.
На рис.1 показана предпочтительная схема полиспаста.
Рис. 1 Схема полиспаста.
– кратность полиспаста;
– количество набегающих канатов;
– количество обводных блоков.
2.Определение максимального усилия в ветви каната набегающего на барабан.
где G – номинальный вес поднимаемого груза;
Принимаем КПД подшипников [4] тогда
где – максимальное рабочее натяжение в полиспасте;
– разрывное усилие каната в целом.
Для 4-ой группы режима работы – коэффициент использования каната [9].
Выбираем диаметр каната из условия:
Расчетная площадь сечения всех проволок
Канат двойной свивки типа ЛК-О (в прядях имеются слои составленные из проволок одинакового диаметра) диаметром 13 мм грузовой марки I оцинкованный крестовой левой свивки нераскручивающийся маркировочной группы 1764 МПа.
-Г-I-Л-Н-1764 ГОСТ 3077-80.
4.Мощность электродвигателя и его выбор.
где – КПД редуктора [4]
Для 4-ой группа режима работы [1].
Выбираем электродвигатель 4АВ112В8У3:
Габаритный размер электродвигателя определяющий диаметр барабана:
5.Определение диаметра барабана.
Диаметр барабана определяем из соотношения:
где – коэффициент выбора диаметра барабана [9].
Принимаем из нормального ряда диаметров барабанов.
6.Определение длины барабана.
Шаг нарезки примем .
где – расстояние до начала нарезки;
– длина рабочей части барабана;
– число рабочих витков
– длина части барабана на которой размещается разгружающие витки регламентированные нормами техники безопасности [9];
– длина части барабана на которой размещается крепление каната.
Тогда длина барабана
7.Определение частоты вращения барабана.
где – скорость каната набегающего на барабан
тогда частота вращения барабана
8.Определение передаточного отношения и выбор редуктора.
где – частота вращение электродвигателя
Номинальный крутящий момент на выходном валу редуктора (крутящий момент на валу барабана):
Выберем редуктор зубчатый цилиндрический двухступенчатый по соосной схеме внешнего зацепления косозубый однопоточный.
Расчет редуктора производится на ЭВМ ниже приводится распечатка расчета.
=========================РЕЗУЛЬТАТЫ РАСЧЕТА========================
Характеристика механизма
Передаточное отношение механизма
Вращающий момент на быстроходном валу
Частота вращения быстроходного вала
Передаточное отношение .
Коэффициент ширины венца
Межосевое расстояние мм ..
Угол зацепления град ..
Угол наклона зубьев град
Модуль зацепления (нормальный) мм
Силы в зацеплении Н:
Вращающий момент на шестерне ..
Контактные напряжения МПа:
при номинальной нагрузке:
при максимальной нагрузке:
Параметры зубчатого колеса
Коэффициент смещения исходного контура
Ширина зубчатого венца мм ..
Твердость поверхности зубьев HRCэ
Напряжение изгиба МПа:
Номинальные крутящие моменты:
на промежуточном валу
на быстроходном валу
где зуб = 0965 -- КПД первой и второй ступеней редуктора.
Максимальные крутящие моменты создаваемые максимальным моментом двигателя:
на промежуточном валу
9.Проектные расчеты диаметров валов
Предварительные оценки значений диаметров (мм) валов редуктора (сталь 40Х улучшение + закалка) определяют по формулам [5].
а) Быстроходный вал:
принимаем по стандартному ряду: .
Диаметр вала под подшипник качения:
dП ≥ d +2* tцил=28+2*35 =35 мм
По стандартному ряду посадочных диаметров под подшипники принимается dП = 35 мм
Диаметр заплечика подшипника:
d БП = dП + 3*r=35 + 3* 2 =41 мм
Принимается d БП = 42 мм
б) Промежуточный вал:
Диаметр заплечика колеса:
d БК ≥ dК + 3*f=48 + 3* 16 =528 мм
Принимается d БK = 53 мм.
dП ≥ dK -3 * r=48-3*3 =39 мм
По стандартному ряду посадочных диаметров под подшипники принимается dП = 40 мм
d БП = dП + 3*r=40 + 3* 3 =49 мм
Принимается d БП = 48 мм.
dП ≥ d +2* tцил=71+2*3 =77 мм
По стандартному ряду посадочных диаметров под подшипники принимается dП = 80 мм
d БП = dП + 3*r=80 + 3* 3.5 =905 мм
Принимается d БП = 90 мм
Диаметр под колесо: d К= d БП=90 мм.
10.Предварительный расчет длины вала.
Предварительные оценки значения длин (мм) различных участков стального вала редуктора определяют по формулам [5]:
Для промежуточного вала:
Длина ступицы колеса:
lст=12*dК=12*48=576 мм. Принимаем lст=60 мм.
Для тихоходного вала:
lст=12*dК=12*90=108 мм. Принимаем lст=110 мм.
По технологическим и конструкторским причинам а также после предварительного силового анализа длины вала изменены.
11.Конструирование корпуса редуктора.
Чтобы поверхности вращающихся колес не задевали за внутренние поверхности стенок корпуса между ними оставляют зазор:
где L – расстояние между внешними поверхностями деталей передач.
Расстояние между дном корпуса и поверхностью колес:
b ≥ 3* a b ≥ 3*12 =36 мм.
Расстояние между торцовыми поверхностями колес:
Толщина стенки отвечающая требованиям технологии литья необходимой прочности и жесткости корпуса:
Корпус имеет довольно простую форму поэтому сравнивая литье по выплавляемым моделям и литье в оболочковые формы которое значительно дешевле первого выбираем второй способ. Этот способ применяется для отливок простой формы из чугуна и стали.
12.Расчет стенки барабана на прочность.
Так как 4-я группа режима работы то выбирают материал барабана – чугун СЧ15.
Толщина стенки барабана:
Проверка толщины стенки из условия прочности:
– допустимое напряжение для чугуна СЧ15 [10].
13.Проверка стенки барабана на устойчивость.
При расчете на устойчивость запас устойчивости цилиндрической стенки барабана принимают из условия
где – рекомендуемый запас устойчивости [1];
– критическое напряжение в цилиндрической стенке МПа:
где – модуль упругости для чугунных барабанов [1];
– коэффициент учитывающий влияние стенки барабана и каната:
Здесь – модуль упругости стального каната [1].
Значит запас устойчивости:
14.Расчет крепления конца каната на барабане.
Нормами техники безопасности регламентировано полтора дополнительных витка уменьшающих натяжение каната в месте крепления к барабану. Поэтому натяжение каната перед прижимной планкой в точке А (см. рис.2) будет
где – максимальное рабочее натяжение в канате при подъеме груза;
– коэффициент динамических нагрузок зависящий от характера изменения пускового момента двигателя от высоты подъема и скорости груза диаметра каната;
– основание натурального логарифма;
– коэффициент трения между канатом и барабаном
– угол обхвата барабана дополнительными витками каната.
Рис. 2 Схема закрепления каната на барабане.
Крепление каната к барабану осуществляют с помощью прижимной планки закрепляемой двумя шпильками.
Суммарное усилие растяжения шпилек:
где – приведенный коэффициент трения;
– угол наклона боковой [1].
Тогда суммарное усилие
Кроме растяжения шпильки испытывают также изгиб вызываемый силами трения между планкой и канатом на участках АБ и ВГ которые стремятся сдвинуть планку в направлении действия силы натяжения в канате и тем самым изгибают шпильки. Эти силы трения воспринимаемые каждой шпилькой равны
За точку приложения силы Т принимают точку соприкосновения шайбы с планкой а за его плечо изгиба l – расстояние от этой точки до поверхности барабана.
Суммарное напряжение в каждой шпильке:
где – коэффициент запаса надежности крепления каната к барабану [3];
– коэффициент учитывающий напряжение кручения при затяжке шпилек;
– внутренний диаметр резьбы шпилек;
Принимаем шпильку М12 тогда тогда
15.Расчет подшипников барабана.
Подшипник рассчитывается по эквивалентной нагрузке:
Рис. 3. График нагружения подшипников барабана.
Выбираем шариковые радиальные сферические двухрядные подшипники №1211. У этих подшипников Сr=27000 [7] Н > Qэ.
Номинальный тормозной момент:
Расчетный тормозной момент:
Нормальное усилие на колодках:
где f = 04 – коэффициент трения стали по вальцованной ленте [2].
Вес рычага соединяющего ротор электромагнита с размыкающим кулачком РР = 3Н. Требуемое усилие электромагнита:
Требуемый ход электромагнита при отходе колодок = 01 мм и допускаемом износе обкладок между регулировками = 05 мм:
Принят электромагнит МИС-4100 который имеет Рм = 42 Н h = 25 мм.
Наибольшее давление на обкладках:
где В = 25 мм – ширина колодки = 90° - угол обхвата колодкой шкива.
Расчет шлицевого соединения.
Боковые поверхности зубьев шлицевого соединения работают на смятие а основание их – на изгиб и срез.
Для применяемых соотношений элементов шлицевых соединений основным является расчет на смятие.
- максимальный крутящий момент создаваемый максимальным моментом двигателя на быстроходном валу;
φ = 075 – коэффициент учитывающий неравномерность распределения нагрузок по рабочим поверхностям зубьев;
F – площадь всех боковых поверхностей зубьев с одной стороны на 1 мм длины;
- для прямобочных (прямоугольных) зубьев;
здесь z = 6 – число зубьев; DB = 34 мм – наружный диаметр зубьев вала; da = 28 мм - диаметр отверстия шлицевой втулки; f = 04 мм – размер фаски; r = 03 мм – радиус закругления [7];
[см] = 15 МПа – допускаемое напряжение на смятие (материал сталь 40Х закалка). [11]
17.Расчет грузоупорного тормоза
Мпр = 4454 Н·м – крутящий момент на промежуточном валу (место установки тормоза);
f = 012 – коэффициент трения вальцованной ленты по стали в масле [2];
f0 = 01 – коэффициент трения по стали в масле угол трения ρ = 5°40’ [2].
Резьба винта тормоза прямоугольная двухзаходная: наружный диаметр резьбы dн = 60 мм внутренний диаметр резьбы dв = 48 мм и шаг резьбы t = 24 мм.
Угол наклона нитки резьбы:
Условие работоспособности тормоза:
Условие выполнено. Здесь средний радиус дисков трения:
Осевое усилие в тормозе:
Линейная скорость на диске тормоза отнесенная к среднему диаметру дисков трения
где [p] = 1 МПа при работе дисков в масле [9].
Расчет храпового колеса.
Храповое колесо выполнено из стали 45. Параметры для расчета:
допускаемое линейное давление с учетом динамического характера нагрузок [q] = 40 Нм соотношение между шириной зуба b и модулем зацепления храпового колеса m =bm=1.
Рис. Храповой останов:
– ось собачки закрепленная на неподвижных элементах механизма.
Наиболее опасно для элементов останова положение когда собачка упирается в вершину зуба храпового колеса (рис.). Прочность кромок определяют по уравнению:
где P – окружная сила определяемая из уравнения:
где D – внешний диаметр храпового колеса; z – число зубьев храпового колеса; МК – крутящий момент действующий на валу храпового колеса.
Ширина собачки на 4 мм шире зуба храпового колеса чтобы компенсировать возможные неточности монтажа.
Пусть z = 17 m = 20. Тогда D = 17·20 = 340 мм.
Условие прочности выполнено.
Расчет шпоночного соединения.
Для диаметра вала принимаем призматическую шпонку по [5].
Определяем расчетную длину призматической шпонки:
(сталь 35 нормализация)
Принимаем длину шпонки .
Расчетная схема шпоночного соединения.
18.Расчет промежуточного вала редуктора
18.1Подбор подшипников качения на заданный ресурс
18.1.1Определение сил нагружающих подшипник
Силы действующие в зацеплении:
-осевая сила на шестерне
-окружная сила на шестерне
-радиальная сила на шестерне.
-осевая сила на колесе
-окружная сила на колесе
-радиальная сила на колесе.
Реакции в плоскости XOZ:
Реакции в плоскости ZOY:
18.1.2Выбор подшипника
Выбирается подшипник шариковый радиальный однорядный легкой серии 208 по ГОСТ 8338-75 [7].
Более нагруженной является опора В дальнейший расчет будет вестись по ней.
18.1.3Расчет на ресурс
где - коэффициент эквивалентности. Для режима нагружения 4 KE=05 [5].
V=1 при вращении внутреннего кольца подшипника относительно направления радиальной нагрузки.
Окончательно принимаем ; .
Эквивалентная динамическая радиальная нагрузка
где - коэффициент безопасности по таблице 7.4 [5] ; - температурный коэффициент [5].
Расчетный ресурс (долговечность) подшипника (ч).
где - коэффициент долговечности по таблице 7.5 [5] ; - коэффициент характеризующий совместное влияние на долговечность особых свойств металла деталей подшипника и условий его эксплуатации [5] (шариковый подшипник).
Так как расчетный ресурс больше требуемого: то предварительно выбранный подшипник 208 пригоден. При требуемом ресурсе надежность выше 90%.
18.1.4Подбор посадки подшипника
Внутреннее кольцо подшипника вращается вместе с валом относительно действующей радиальной нагрузки следовательно нагружение циркуляционное.
по таблице 7.6 [5] выбирается поле допуска на вал k6.
Наружное кольцо подшипника неподвижно относительно радиальной нагрузки и подвергается местному нагружению.
По таблице 7.7 [5] выбирается поле допуска отверстия H7.
18.2Расчет промежуточного вала на статическую прочность
Моменты в опасном сечении:
Коэффициент перегрузки
где – максимальный кратковременно действующий вращающий момент
-номинальный (расчетный) вращающий момент.
В расчете определяют нормальные и касательные напряжения в рассматриваемом сечении вала при действии максимальных нагрузок:
где – суммарный изгибающий момент – крутящий момент – осевая сила и – моменты сопротивления сечения вала при расчете на изгиб и кручение – площадь поперечного сечения.
Частные коэффициенты запаса прочности по нормальным и касательным напряжениям
Общий коэффициент запаса прочности по пределу текучести.
Статическую прочность считают обеспеченной если где
Рассмотрим сечение и произведем следующие расчеты приняв диаметр вала равным внутреннему диаметру прямоугольной резьбы:
Материал вала сталь 45 ;
Значит вал в рассматриваемом сечении прочен.
Тихоходный вал прочен.
19.Определение времени пуска и ускорения .
Определяем фактическое ускорение:
20.Определение времени торможения и замедления .
где k ≥15 – коэффициент запаса торможения.
Опорно-поворотное устройство
1.Определение нагрузок действующих на ОПУ
Стрела крана состоит из двутавра №22приваренного к нему листа 4550х240х10 и подкоса; длина стрелы L1=455м.
Масса механизма подъема Мпод250кг.
Масса металлоконструкции колонны и опорно-поворотного устройства Мк3т.
Вес груза с механизмом подъема:
G= (Q+ Мпод ) g = (3000+ 250 ) 981=318825 Н.
Gстр= Мстрg=250 981=24525 H.
Вес металлоконструкции колонны и опорно-поворотного устройства:
Gк = Мк·g=3000·981=29430 H.
2.Определение реакций в опорах.
Реакции в опорах определим из уравнений статики.
Для нижней опоры выберем подшипники шариковые радиальные сферические двухрядные №1613 ГОСТ 28428-90 (С0r=333 кН [7] > НА) и шариковые упорные однорядные №8107 ГОСТ 7872-89 (С0а=665 кН [7] > VА). В качестве верхней опоры выберем обойму с вертикальными роликами.
3.Момент сопротивления повороту крана от сил трения в опорно-поворотном устройстве
Момент сил трения в опорно-поворотном устройстве:
где Мтр.в и Мтр.н – момент сил трения в верхней и нижней опорах.
где f=0015 – приведенный коэффициент трения скольжения в обойме роликов [8]
d1 = 300 мм – внутренний диаметр обоймы.
где d2 = 65 мм и d3 = 35 мм – внутренние диаметры подшипников.
4.Момент сил инерции
где – момент инерции (относительно оси поворота) медленно поворачивающихся частей крана груза и вращающихся частей механизма поворота
- коэффициент учета инерции вращающихся частей механизма поворота [8]
Jм.п.ч. - момент инерции (относительно оси поворота) медленно поворачивающихся частей крана и груза
mj – масса j-ой медленно поворачивающейся части
xj – расстояние от центра массы j-ой медленно поворачивающейся части до оси поворота крана
- коэффициент приведения геометрических радиусов вращения к радиусам инерции [8]
– угловое ускорение крана
– допустимое линейное ускорение груза для кранов грузоподъемностью до 32 т для перегрузки штучных грузов при ручной строповке (таб. 2.16 [8]).
5.Определение мощности и выбор электродвигателя.
-предварительное КПД механизма;
- кратность среднего пускового момента двигателя
nк- частота вращения крана
По ГОСТ 1452-77: при отсутствии дополнительных требований предусмотренных техническим заданием на проектирование крана ветровая нагрузка учитываемая при определении мощности приводных двигателей крановых механизмов не должна превышать 70 % от статической составляющей ветровой нагрузки на кран или на соответствующий элемент крана или на груз.
Выбираем электродвигатель МТF-011-6. Крановые электродвигатели серии MTF предназначены для привода крановых и других механизмов работающих в кратковременных и повторно-кратковременных режимах в том числе с частыми пусками и электрическим торможением.
Электродвигатели могут быть использованы также для механизмов длительного режима работы.
Тип электродвигателя
Мощность электродвигателя (ПВ 25%) кВт
Частота вращения обмин.
Максимальный момент Нм
6.Проверка выбранного электродвигателя
Время разгона tp. до номинальной скорости:
Jp=0021 –момент инерции ротора электродвигателя
Jм=0057 –момент инерции соединительной муфты
u-передаточное число механизма поворота
где -передаточное отношение редуктора
-передаточное отношение открытой зубчатой передачи
К передаточному отношению прибавляем единицу т.к. передача имеет внешнее зацепление
Полученное время разгона соответствует рекомендациям 3-5 сек.
7.Определение предельного расчетного момента муфты
- передаточное число и КПД передачи между валом двигателя и муфтой
8.Определение необходимой силы прижатия диска
-коэффициент трения для пары трения закаленная сталь- закаленная сталь
-средний радиус поверхностей дисков
-число пар трущихся поверхностей
-коэффициент учитывающий неравномерность работы всех фрикционных дисков
Проверим могут ли фрикционные диски выдерживать давление от расчетной силы прижатия
-следовательно необходимое прижимное усилие можно обеспечить
Определим величину подтяжки пружины.
Выбираем пружину 1086-1091 по ГОСТ 18793-80 со следующими параметрами
Dп- диаметр пружины
d- диаметр проволоки или прутка
G- модуль сдвига материала пружины (пружинная сталь)
- число рабочих витков пружины
-усилие сжатия одной пружины не превышает допустимого значения для выбранной пружины
- величина поджатия каждой пружины
9.Определение тормозного момента на валу двигателя
Выбираем тормоз ТКГ-160 с номинальным тормозным моментом 100Нм
Настраиваем тормоз на момент 43 Нм
-данное значение ускорения удовлетворяет рекомендуемому значению ускорения при ручной строповое для крана грузоподъемностью до 32 т
) Александров М.П. Подъемно-транспортные машины: Учебник для машиностроит. спец. вузов. – 6-е изд. перераб. – М.: Высшая школа 1985. - 520 с. ил.
) Руденко Н.Ф. Курсовое проектирование грузоподъемных машин М.: Машиностроение 1971.
) Справочник по кранам: в 2 т. Т. 1. Характеристики материалов и нагрузок. Основы расчёта кранов их приводов и металлических конструкций В.И. Брауде М.М. Гохберг И.Е. Звягин и др.; Под общей ред. М.М. Гохберга. - Л.: Машиностроение. Ленингр. отд-ние 1988. - 536 с.: ил.
)Справочник по кранам: в 2 т. Т. 2. Характеристики и конструктивные схемы кранов. Крановые механизмы их детали и узлы. Техническая эксплуатация кранов М.П. Александров М.М. Гохберг А.А. Ковини и др.; Под общей ред. М.М. Гохберга. - Л.: Машиностроение. Ленингр. отд-ние 1988. - 559 с.: ил.
) Конструирование узлов и деталей машин: Учеб. пособие для студ. техн. спец. вузов П.Ф. Дунаев О.П. Леликов. - 8-е изд. перераб. и доп. - М.: Издательский центр «Академия» 2004. - 496 с.
) Подъёмно-транспортные машины: Атлас конструкций: Учеб. пособие для студентов втузовМ.П. Александров Д.Н. Решетов Б.А. Байков и др.; Под ред. М.П. Александрова Д.Н. Решетова. - 2-е изд. перераб. и доп. - М.: Машиностроение 1987. - 122 с.: ил.
) Атлас конструкций узлов и деталей машин: Учеб. пособие Б.А. Байков А.В. Клыпин И.К. Ганулич и др.; Под ред. О.А. Ряховского. – М.: Изд-во МГТУ им. Н.Э. Баумана 2005. – 384с.: ил.
)Казак С.А. и др. Курсовое проектирование ГПМ. - М.: Высшая школа 1989. - 318 с.
)Промышленная безопасность при эксплуатации грузоподъемных кранов: сборник документов. Серия 10. Выпуск 7 колл. авт. – 2-е изд. испр. – М.: Федеральное государственное унитарное предприятие «Научно-технический центр по безопасности в промышленности» 2005. – 288с.
Правила устройства и безопасной эксплуатации грузоподъемных кранов (ПБ 10-382-00)
)Анурьев В.И. Справочник конструктора-машиностроителя: В 3 т. Т.1 – 2-е изд. перераб. и доп. Под ред. И.Н. Жестковой. – М.: Машиностроение 2001. – 920 с.: ил.
)Анурьев В.И. Справочник конструктора-машиностроителя: В 3 т. Т.2 – 2-е изд. перераб. и доп. Под ред. И.Н. Жестковой. – М.: Машиностроение 2001. – 912 с.: ил.
)Анурьев В.И. Справочник конструктора-машиностроителя: В 3 т. Т.3 – 2-е изд. перераб. и доп. Под ред. И.Н. Жестковой. – М.: Машиностроение 2001. – 864 с.: ил.
Рекомендуемые чертежи
- 25.10.2022