Полукозловой кран грузоподъёмностью 3,2 тонны




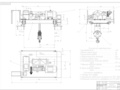
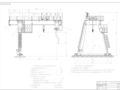
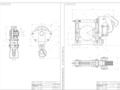
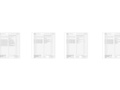
- Добавлен: 25.10.2022
- Размер: 1 MB
- Закачек: 0
Описание
Состав проекта
![]() |
![]() ![]() ![]() ![]() |
![]() ![]() ![]() |
![]() ![]() ![]() ![]() |
![]() ![]() ![]() ![]() |
![]() ![]() ![]() ![]() |
Дополнительная информация
rryirsresreryersres.dwg

Крюковая подвеска и тормоз.dwg

Чертёж главного вида.dwg

rrsrrrerr-ryirrsrrr-rssrr.dwg

Рекомендуемые чертежи
- 25.10.2022