Кран полукозловой грузоподъемностью 3,2 т




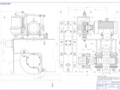
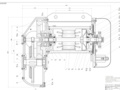
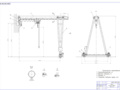
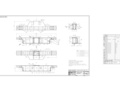
- Добавлен: 25.10.2022
- Размер: 2 MB
- Закачек: 1
Описание
Состав проекта
![]() |
![]() |
![]() ![]() |
![]() ![]() ![]() ![]() |
![]() ![]() ![]() ![]() |
![]() ![]() |
![]() ![]() ![]() ![]() |
![]() ![]() ![]() ![]() |
![]() ![]() ![]() ![]() |
![]() |
![]() ![]() ![]() |
![]() ![]() ![]() |
![]() ![]() ![]() |
Дополнительная информация
Концевая балка+Спецификация.dwg

ГOCT 5264-80*-T1- 10
А1 СДМ2-08.03.000 СБ Сборочный чертеж
*Pазмеры для справок. 2. Неуказанные сварные соединения выполнить сплошным швом 5 ГОСТ 5264-80* по всему контуру сопрягаемых элементов. 3. Электрод Э42А ГОСТ 9466-75*. 4.Общие допуски по ГОСТ 30893.1-2002: Н14
±IT142. 5.Крепежные и посадочные отверстия от сварочных брызг предохранить."
Общий вид (Спецификация).dwg

Балка концевая нижняя
Балка концевая верхняя
МОЙ ОБЩИЙ ВИД.dwg

Неуказанные предельные отклонения: H14
Соосность валов обеспечить при сборке
После сборки обкатать без нагрузки в течении часа
После обкатки масло слить и залить в редуктор масло
индустриальное И-40А ГОСТ 20799-75.
Межанизм передвижения
Механизм передвижения крана
*Размеры для справок. 2. Неуказанные предельные отклонения: H14
h14± IT142. 3. После сборки обкатать без нагрузки в течении часа. 4. После обкатки масло слить и залить в редуктор масло индустриальное И-40А ГОСТ 20799-75.
Технические характеристики 1. Грузоподъемность
q*;4. Скорость подъема груза
МОЙ ПОДЪЕМ.dwg

Неуказанные предельные отклонения: H14
Соосность валов обеспечить при сборке
После сборки обкатать без нагрузки в течении часа
После обкатки масло слить и залить в редуктор масло
индустриальное И-40А ГОСТ 20799-75.
Межанизм передвижения
*Размеры для справок 2. Неуказанные предельные отклонения размеров H11
h14 3.Обкатать без нагрузки в течение не менее одного часа. Резкий шум и стук не допускается. 4. Перед обкаткой залить в редуктормасло индустриальное И-40А ГОСТ 20799-75
Механизм подъема груза
мое передвижение.dwg

Неуказанные предельные отклонения: H14
Соосность валов обеспечить при сборке
После сборки обкатать без нагрузки в течении часа
После обкатки масло слить и залить в редуктор масло
индустриальное И-40А ГОСТ 20799-75.
Межанизм передвижения
Механизм передвижения крана
*Размеры для справок. 2. Неуказанные предельные отклонения: H14
h14± IT142. 3. После сборки обкатать без нагрузки в течении часа. 4. После обкатки масло слить и залить в редуктор масло индустриальное И-40А ГОСТ 20799-75.
Спецификация передвижение.docx
Механизм передвижения крана
Подшипник ГОСТ 5721-75
Шпонка ГОСТ 23360-78
МУВП с тормозным шкивом
Спецификация птм механизм подъема.doc
Подшипник ГОСТ 8338-75
Шпонка ГОСТ 23360-78
Электродвигатель АОЛС2-32-4
Рном=4 кВт; n=1500 обмин
Передня Л.И1.docx
Белорусский национальный технический университет
Факультет транспортных коммуникаций
Кафедра: “ Строительные и дорожные машины “
по дисциплине «Подъемно-транспортные машины»
« Кран полукозловой »
Исполнитель: ст. гр. 114129 Каратай А. А.
Руководитель: доцент Передня Л.И.
Описание конструкции крана6
Расчет механизма подъема груза8
Расчет механизма передвижения крана26
Расчет металлоконструкции концевой балки37
Техника безопасности при эксплуатации крана53
Список использованных источников60
Пояснительная записка: 60 стр. 14 рис. 1 табл. 8 источников.
КАНАТ МЕХАНИЗМ ПОДЪЕМА МЕХАНИЗМ ПЕРЕДВИЖЕНИЯ КРАНА НАПРЯЖЕНИЕ КОНЦЕВАЯ БАЛКА.
В данном курсовом проекте представлена конструкция основных элементов полукозлового передвижного крана грузоподъемностью 32 т произведен расчёт его основных параметров.
Разработаны мероприятия по охране труда и технике безопасности.
Задачей данного курсового проекта является разработка и расчет полукозлового крана грузоподъемностью 32 тонн. Разработка включает в себя расчет основных параметров составных частей и механизмов крана а именно механизма подъема груза механизма передвижения крана и металлоконструкции.
В данном проекте также представлено описание конструкции полукозлового крана и его работы. Разработаны мероприятия по охране труда при эксплуатации данного крана.
Описание конструкции крана
Полукозловые краны — это краны мостового типа мост (пролетные строения) которых установлен на опоры перемещающиеся по рельсам установленным на бетонные фундаменты. Кран называют полукозловым если мост одной стороной опирается на крановый путь а другой на опорные стойки.
Полукозловые краны установленные обычно на большой высоте передвигаются по путям уложенным на строительных конструкциях здания поэтому особенно важно чтобы вес их был минимальным а нагрузки на подкрановый путь не превышали обычные монтажные нагрузки предусмотренные проектом здания.
Полукозловые краны изготовляют по конструктивным различным схемам в зависимости от которых выполняют не только остов и грузовую тележку крана но в значительной мере и остальные его узлы и механизмы. Пролет этих кранов определяется опорной базой. При высоте подъема 7 12 м это обеспечивает транспортирование через опоры большинства штучных грузов а также возможность относительно простого монтажа путем стягивания опорных стоек как правило достаточно несложных по конструкции и обладающих малой металлоемкостью.
Современные краны этого типа обычно имеют однобалочный мост с двухрельсовой подвеской грузовой тележки. Однако конструкция ходовой части таких тележек относительно сложна необходимость образования проемов для прохода ходовых колес тележек усложняет узлы примыкания стоек к мосту. Эти недостатки устранены в кранах с монорельсовой подвеской грузовой тележки. Вместе с тем износостойкость полок монорельсов обычно невелика а грузовые тележки подвержены поперечному раскачиванию. Поэтому такие краны целесообразно изготавливать для условий ограниченной интенсивности эксплуатации и для грузоподъемности не более 20 32 т.
В двухбалочных кранах применяют простые по конструкции двухрельсовые опорные грузовые тележки типовых мостовых кранов; размещение подвески между балками моста позволяет на 10 15 % уменьшить высоту крана. Но двухбалочные мосты сложны при изготовлении и металлоемки что оправдывает использование таких схем только в кранах с относительно небольшими (до 25 м) пролетами или при наличии каких-либо дополнительных условий.
Рисунок 1– Кран полукозловой: 1 – балка главная 2 – механизм подъема груза 3 – токопровод 4 механизм передвижения 5 – балка концевая 6 – опора.
Полукозловый кран (рисунок 1) состоит из несущей металлической конструкции механизмов подъема передвижения грузовой тележки и передвижения крана. Мост 1 крана жестко соединенный с опорой 6 образует совместно с ней пространственную раму. Рама опирается на ходовые тележки с установленными на них автоматическими противоугонными захватами и ручными рельсовыми захватами. Для того чтобы разгрузить подкрановые пути от усилий распора и горизонтальных сил возникающих вследствие температурных изменений мост соединяют с ходовой тележкой через короткую гибкую опору при помощи горизонтального шарнира.
Каждая ходовая тележка снабжена самостоятельным механизмом передвижения 4 управляемым общим командоконтроллером.
Развитие конструктивных форм полукозловых кранов тесно связанное с их назначением и условиями установки целиком зависело от успешного решения основной проблемы — снижения собственного веса крана и прежде всего веса его металлических конструкций. Уже первые полукозловые краны отличались сравнительно небольшим весом полученным главным образом за счет снижения подвижной нагрузки.
Расчет механизма подъема груза
Для крна грузоподъемностью 32 т выбираем двукратный полиспаст Uп = 2 (рисунок 2).
Рисунок 2 – схема запасовки грузового каната
Усилие в канате набегающем на барабан при подъеме груза H [1стр.53]:
где Q – номинальная грузоподъемность крана кг;
z – число полиспастов в системе;
u – кратность полиспаста;
– общий КПД полиспаста и обводных блоков.
где бл – КПД одного блока [1таб.2.1];
В соответствии с формулой (1):
Расчетное разрывное усилие в канате при максимальной нагрузке на канат [3стр.24]:
где k – коэффициент минимальный коэффициент использования каната
(для режима работы М5 k =56) [3таб.2.3].
С учетом данных из таблицы III. 1.1[1] выбираем по ГОСТ 2688 – 80 канат двойной свивки типа ЛК-Р конструкции 6×19(1 + 6 + 6 6) +1о.с. диаметром d=13 мм имеющий при маркировочной группе проволок 1764 МПа разрывное усилие F=89000 H.
Канат грузовой (Г) первой марки (I) из проволоки без покрытия () правой свивки () нераскручивающийся (Н):
Канат 13-Г-I-Н-1764 ГОСТ 2688-80.
Фактический коэффициент запаса прочности [3стр.24]:
Требуемый диаметр барабана по средней линии навитого стального каната мм [3стр.24]:
где dк – диаметр каната мм;
h1 – коэффициент выбора диаметра барабана (для режима работы М6 h1=20) [1таб.2.7стр.59];
Диаметр барабана по дну канавки [2стр.57]:
Диаметр барабана окончательно будет принят после подбора электродвигателя.
По ГОСТ 6627-74 выбираем однорогий кованный крюк с номером заготовки крюка 12.
Статическая мощность двигателя механизма подъема груза [1стр.65]:
g – ускорение свободного падения мс2;
VГ – скорость подъема груза мс;
– КПД механизма [1таб.1.18стр.стр.23].
С учетом полученных данных и условий задания выбираем электродвигатель крановый встраиваемый типа АОС2-32-4 [4таб.2стр35]:
– Номинальная мощность
– Момент цнерции ротора Iр = 00125 кг·м2.
Толщину стенки барабана определяют из расчета на сжатие [1стр.61]:
где максимальное натяжение в канате набегающем на барабан при подъеме груза Н;
t – шаг витков каната на барабане м;
допускаемые напряжения сжатия для материала барабана МПа.
Приняв в качестве материала для изготовления барабана чугун марки СЧ 15 ГОСТ 1412-70 допускаемое напряжение в стенке барабана:
где предел прочности на сжатие МПа;
коэффициент запаса прочности [2прил.ХV];
Из условия технологии изготовления литых барабанов толщина стенки должна быть не менее 12 мм и определяется по формуле [1стр.62]:
где Dб.д – диаметр барабана по дну канавки м;
С учетом подбора электродвигателя и толщины стенки диаметр барабана по дну канавки будет равен :
Принимаем диаметр по средней линии навитого стального каната
Рисунок 3 – Профиль канавок барабана
Длина каната навиваемого на барабан с одного полиспаста [1стр.60]:
где Н – высота подъема груза м;
Uп – кратность полиспаста;
D – диаметр барабана по средней линии навитого каната м;
z1 – число запасных ( неиспользуемых ) витков на барабане до места
крепления (z1=15 2);
z2 – число витков каната находящихся под зажимным устройством на
Рабочая длина барабана для навивки каната с одного полиспаста [1стр.60]:
где Lк – длина каната навиваемого на барабан м;
t – шаг витка [1табл.2.8стр60];
m – число слоев навивки;
dк– диаметр каната м;
- коэффициент не плотности навивки;
Приняв в качестве материала для изготовления барабана чугун марки СЧ15 (барабан литой) проводим проверочный расчет барабана на смятие (сжатие).
Находим напряжение сжатия в стенке барабана [2стр.66]:
где Fб – усилие в канате Н;
t – шаг витков каната на барабане м;
[сж] – допускаемое напряжение сжатия для материала барабана МПа.
Проверочный расчет на совместное действие изгиба и кручения можно не производить если LбD3 и и кр при этом обычно не превышают 10-15% от расчет ведут только по .
Проверочный расчет на совместное действие изгиба и кручения можно не производить.
Канат крепится к барабану прижимными планками с трапецеидальными канавками где канат удерживается силой трения создаваемой затяжкой.
Рисунок 4 – Схема крепления каната к барабану
Натяжение закрепляемого конца каната (рисунок 4) [1стр63]:
где – коэффициент трения между канатом и барабаном;
α – угол обхвата барабана запасными витками каната рад.
Приняв =014 и α=4 для двух витков получим:
Рисунок 5 – Схема определения силы прижатия планки к барабану
Необходимая сила прижатия болтов (рисунок 5)[1стр63]:
где f – приведенный коэффициент трения между канатом и планкой с учётом её желобчатой формы.
Тогда сила прижатия составит ():
Приведенное напряжение в болтовом соединении [1стр64]:
где d – диаметр болта м;
lс – расстояние между центрами масс сечений каната и стенки барабана мм:
где Z – число болтов (планок). Принимаем болт М18 из стали 35 по ГОСТ 1759.4-87 с пределом прочнотси тогда . – допускаемое напряжение на разрыв материала болта МПа.
Выразим число необходимых болтов (планок) Z:
Z > [Z] 2 условие выполняется.
Номинальный момент на валу двигателя [2стр.77]:
Требуемое число оборотов барабана в минуту рассчитывается по формуле [2стр.77]:
где Uп – кратность полиспаста;
D – расчетный диаметр барабана м;
Общее передаточное число привода механизма [1стр.65]:
По ГОСТ 2185-66 выбираем нормализованное значение передаточного числа U=71.
Погрешность передаточного числа:
Передаточное число отличается от заданного значения менее чем на 5% что допустимо.
Момент статического сопротивления на валу двигателя в период пуска Нм [2стр.78]:
где m – число ветвей навиваемых на барабан;
– усилие в канате набегающем на барабан при подъеме груза Н;
– КПД механизма подъема [2рис.36]
Номинальный момент передаваемый муфтой принимается равным моменту статических сопротивлений Тм = Мс = 3415 м.
Расчетный момент для выбора соединительной муфты Нм [1стр 41]:
где к1 – коэффициент учитывающий степень ответственности механизма [1таб.35];
к2 – коэффициент учитывающий режим работы механизма[1таб.35];
Из табл. .5.9 [1стр.340] выберем ближайшую по требуемому крутящему моменту упругую втулочно-пальцевую муфту № 1 с тормозным шкивом диаметром Dт = 200 мм и наибольшим передаваемым крутящим моментом 500 Нм. Момент инерции муфты Iм=0125 кгм2.
Момент инерции ротора двигателя и муфты:
Средний пусковой момент двигателя:
Tном – номинальный пусковой момент двигателя Нм
Время пуска при подъеме груза с [1стр.30]:
где Мпуск. – средний пусковой момент двигателя Нм;
– коэфициент учитывающий влияние вращающихся масс привода механизма ( = 11 12);
I – момент инерции ротора двигателя и муфты кгм2;
n – частота вращения двигателя мин-1;
Мст – момент статического сопротивления на валу двигателя в период пуска Нм;
Q – номинальная грузоподъемность крана кг;
V – скорость механизма подъема мс;
– КПД механизма подъема.
Фактическая частота вращения барабана:
где nдв – частота вращения двигателя мин-1;
Фактическая скорость подъема груза [1стр.34]:
где D – расчетный диаметр барабана м;
Ускорение при пуске [1стр.31]:
где – наибольшее допускаемое ускорение мс2 ;
– условие выполняется.
Полученные значения t и соответствуют рекомендациям табл. 1.19 и 1.25 [1].
Поскольку график действительной загрузки механизма подъема не задан воспользуемся усредненным графиком использования механизма по грузоподъемности (рисунок 6) построенным на основе опыта эксплуатации кранов. Определим моменты развиваемые двигателем и время его пуска при подъеме и опускани груза в различные периоды работы механизма. По графику действительной загрузки при заданном тяжелом режиме работы (М6): механизм работает с номинальным грузом Q= 3200 кг – 2 подъема и 2 опускания с грузом 075Q= 2400 кг – 4 подъема и 4 опускания с грузом 0195Q=624кг – 1 подъем и 1 опускание с грузом 005Q=160 кг – 3 подъема и 3 опускания.
Рисунок 6- Усредненный график загрузки механизма подъема
Натяжение каната у барабана при подъеме груза [1стр.53]:
Момент при подъеме груза [2стр.78]:
Время пуска при подъеме [1стр.30]:
Натяжение каната у барабана при опускании [1стр.53]:
Момент при опускании груза [2стр.78]:
Время пуска при опускании [1стр.30]:
Произведенные расчеты всех показателей и полученных данных сводим в таблицу 1.
Таблица 1 – Моменты развиваемые двигателем и время его пуска
Наименование показателей
Результаты расчета при массе поднимаемого груза кг
Натяжение каната у барабана при подъеме груза
Момент при подъеме груза
Время пуска при подъеме
Натяжение каната у барабана при опускании груза
Момент при опускании груза
Время пуска при опускании груза
Средняя высота подъема груза составляет 05 08 номинальной высоты [2стр.82]:
Время установившегося движения [2стр.82]:
Сумма времени пуска при подъеме и опускании груза за цикл работы механизма [2стр.82]:
Общее время включений двигателя за цикл [2стр.82]:
Среднеквадратичный момент [1стр.36]:
где – общее время пуска механизма в разные периоды работы с различной нагрузкой с;
–сумма произведений квадрата моментов статических сопротивлений движению при данной нагрузке на время установившегося движения при этой нагрузке;
t – общее время включения электродвигателя за цикл с.
Среднеквадратическая мощность двигателя кВт [1стр.36]:
Во избежание перегрева электродвигателя необходимо чтобы развиваемая двигателем среднеквадратичная мощность удовлетворяла условию:
– условие соблюдается двигатель не перегревается.
Момент статического сопротивления на валу двигателя при торможении механизма [2стр.84]:
где U – общее передаточное число между тормозным валом и валом барабана;
Fб – усилие в канате Н;
z – число полиспастов по схеме;
Dб – расчетный диаметр барабана м;
м – КПД механизма подъема при номинальном грузе;
Необходимый по нормам тормозной момент развиваемый тормозом выбираем из условия [2стр84]:
где кт – коэффициент запаса торможения [2таб.18стр84];
Из таблицы III.5.11 [1стр.341] выбираем тормоз ТКГ- 200 с тормозным моментом 250 Нм диаметром тормозного шкива Dт = 200 мм. Регулировкой можно получить требуемый тормозной момент Тт = 4936 Н м.
Определяем время торможения при опускании груза (при подъеме груза это время будет меньше так как в этом случае момент от веса груза и тормозной момент действуют в одном направлении) [1стр.30]:
где – коэфициент учитывающий влияние вращающихся масс привода механизма = 11 125;
nдв – частота вращения двигателя мин-1;
Мт – тормозной момент Нм;
– момент статического сопротивления на валу тормоза при торможении механизма Нм;
V – скорость механизма мс;
мех – КПД механизма.
Из таблицы 1.22 [1] для среднего режима работы находим путь торможения механизма подъема груза:
Время торможения(предположим что скорость подъема и опускания груза одинаковы) [1стр.30]:
Замедление при торможении [1стр.31]:
Что соответствует данным таблице 1.25[1].
Расчет механизма передвижения крана
Рассчитаем механизм передвижения полукозлового крана:
Грузоподъемность Q = 32 т.
Пролет крана L= 8 м.
Высота подъема груза Н=6 м.
Скорость передвижения Vпер =06 мс.
Рисунок 7 –Кинематическая схема привода
Ориентировочная масса полукозлового крана [1стр.33]:
где Q – грузоподъемность крана т;
L – пролет крана м;
По таблице 1.29 [1] найдем рекомендуемый диаметр ходовых колес
DK = 400 мм. Коэффициент трения качения ходовых колес по рельсам с плоской головкой = 00005 [1табл. 1.28стр.33]. Коэффициент трения в подшипниках качения ходовых колес f = 0015 (подшипники конические) [2таб.26стр.106].
Диаметр цапфы вала ходового колеса [2стр.106]:
dK = (02 025) DK (52)
где DK – диаметр ходовых колес.
Общее сопротивление передвижению крана от статических нагрузок [1стр.68]:
где сопротивление трения при движении крана;
сопротивления от уклона пути;
где kр – коэфициент учитывающий сопротивление от трения реборд колес о рельсы и от трения токосъемника от троллеи [2таб.28стр.107];
m – масса полукозлового крана кг;
Q – грузоподъемность крана кг;
g – ускорение свободного падения м
f – коэффициент трения в подшипниках качения ходовых колес;
dK – диаметр цапфы вала ходового колеса мм;
– коэффициент трения качения ходовых колес по рельсам;
DK – диаметр ходовых колес мм.
Сопротивление от уклона пути [1стр 68]:
где угол наклона пути [1таб.2.10];
Двигатель механизмов передвижения крана выбирается по пусковому моменту. Значение пускового момента должно быть таким при котором отсутствует пробуксовка ведущих колес незагруженного крана по рельсам а коэффициент запаса должен быть не менее 12.
Для предварительного выбора двигателя определяем сопротивление передвижению загруженного крана в пусковой период [2 cтр106]:
где –среднее ускорение крана при пуске [1 c.108].
Мощность предварительно выбираемого двигателя с учетом инерционных нагрузок [2 cтр109]:
где – сопротивление передвижению крана в пусковой период;
Vnep – скорость передвижения крана;
– ориентировочное значение КПД механизма передвижения моста крана [1 табл. 1.18];
– средняя кратность пускового момента равная среднему арифметическому максимальной и минимальной кратности пускового момента. В соответствии с [2 cтр109] для асинхронного двигателя;
Поскольку в приводе рассчитываемого механизма передвижения должно быть установлено два одинаковых электродвигателя на каждый из них приходиться мощность равная :
Подбираем двигатель из условия:
По каталогу [1таб.3.1стр 300] предварительно выбираем электродвигатель 4А71В6У3 с мощностью на валу 055 кВт . Частота вращения 900 обмин. Момент инерции ротора 20210-3 кгм2.
Номинальный момент двигателя:
где Рс – статическая мощность привода;
n – частота вращения двигателя;
Частота вращения ходового колеса [2стр109]:
где Vnep – скорость передвижения;
DK – диаметр ходовых колес;
Требуемое передаточное число привода [2стр110]:
где n – частота вращения двигателя;
nк – частота вращения ходового колеса;
Расчетная мощность для выбора редуктора [1стр.40]:
Рр = 22 055= 121 кВт.
Исходя из этой мощности и требуемого передаточного числа из табл. III.4.16 [1] выбираем для среднего режима работы и частоты вращения быстроходного вала
nб =1000 мин-1 редуктор типа ВК-550 с передаточным числом uр = 2906.
Фактическая частота вращения колеса [2стр.110]:
Фактическая скорость передвижения крана с номинальным грузом [2 cтр.121]:
Отличается от ближайшего значения 063 мс из стандартного ряда на 156 % что допустимо.
Полагаем что общее число ходовых колес крана z = 4 из них приводных zпр = 2. Примем коэффициент сцепления ходовых колес с рельсами φ = 015 [1стр.33] коэффициент запаса сцепления kφ = 12 [1 таб.1.27стр.32];
Максимально допустимое ускорение крана при пуске мс2 [1стр.33]:
где zпр – число приводных ходовых колес крана;
z – число ходовых колес крана;
φ – коэффициент сцепления ходовых колес с рельсами;
kφ – коэффициент запаса сцепления;
dK – диаметр цапфы вала ходового колеса;
kр – коэфициент учитывающий условия работы;
g – ускорение свободного падения;
m – масса полукозлового крана;
Fр – ветровая нагрузка на кран в рабочем состоянии (Fp = 0);
Наименьшее допускаемое время пуска по условию сцепления [2стр.121]:
где Vперф – фактическая скорость передвижения крана;
amax – максимально допустимое ускорение крана при пуске.
Средний пусковой момент двигателя [1стр.35]:
Тном – номинальный момент двигателя;
Момент статических сопротивлений при работе крана без груза (определение значений Fnep = F'nep приводится ниже):
где F'пер – сопротивление передвижению крана без груза;
uр – передаточное число редуктора;
Расчетный момент для выбора соединительных муфт [1стр.41]:
Тм = Тмном k1 k2 ; (70)
где k1 – коэффициент учитывающий степень ответственности механизма [1табл.1.35стр42].
k2 – коэффициент учитывающий режим работы механизма механизма [1табл.1.35стр42].
Тм = 764 · 12 · 12 = 1100 · м ;
Из табл. III.5.6 [1] выбираем упругую втулочно-пальцевую муфту с крутящим моментом 315 · м. Диаметр муфты D = 90 мм момент инерции:
Iм' = 01 m D2 ; (71)
где m – масса муфты [1таб.1.36стр42].
D – наибольший диаметр муфты;
Iм' = 01 · 16· 0092 = 0002 кг м2.
Фактическое время пуска механизма передвижения без груза [1стр.30]:
где – коэфициент учитывающий влияние вращающихся масс привода механизма = 12;
I – момент инерции ротора двигателя и муфты;
Тср.п – средний пусковой момент двигателя;
Тс – момент статического сопротивления на валу двигателя в период пуска;
V – скорость механизма;
Что согласуется с данными табл. 1.19 [1].
Фактическое ускорение крана без груза при пуске:
где tп – фактическое время пуска механизма передвижения без груза;
Vперф – фактическая скорость передвижения крана.
Проверяем фактический запас сцепления. Для этого найдем:
а) суммарную нагрузку на приводные колеса без груза:
где m – масса полукозлового крана;
zпр – число приводных ходовых колес крана;
g – ускорение свободного падения.
б) сопротивление передвижению крана без груза:
где kр – коэфициент учитывающий условия работы;
DK – диаметр ходовых колес.
Фактический запас сцепления равен:
где Fпр – суммарная нагрузка на приводные колеса без груза;
F'пер – сопротивление передвижению крана без груза;
a – фактическое ускорение крана без груза при пуске;
f – коэффициент трения в подшипниках качения ходовых колес;
Полученные значения t и α соответствуют рекомендациям таблицы 1.19 и 1.25 [1].
Максимальное допустимое замедление крана при торможении:
По таблице 1.26 [1] принимаем aТmax = 015 мс2.
Время торможения крана без груза:
aТmax – максимально допустимое ускорение крана.
Сопротивление при торможении крана без груза:
где m – масса полукозлового крана кг;
Момент статических сопротивлений на тормозном валу при торможении крана в предположении что тормоз установлен на валу двигателя и нет уклона пути:
где FТтр – сопротивление передвижению крана без груза Н;
DK – диаметр ходовых колес мм;
Момент сил инерции при торможении крана без груза:
где – коэфициент учитывающий влияние вращающихся масс привода механизма;
tт – время торможения крана без груза с;
V – скорость механизма мc;
Расчетный тормозной момент на валу тормоза:
где ТинТ – момент сил инерции при торможении крана без груза;
ТсТ – момент сил инерции при торможении крана без груза;
Из таблицы .5.14 [1] выбираем тормоз типа ТКГ-200 с диаметром тормозного шкива DT=200 мм и наибольшим тормозным моментом Тт=250 Н м.
Минимальная длина пути торможения по таблице 1.23 [2стр.128].
где k – коэфициент сцепления;
S = 0642 15 = 043 м.
Фактическая длина пути торможения:
где V – скорость механизма;
tт – время торможения крана без груза.
Что соответствует рекомендациям таблице 1.26 [1].
Расчет металлоконструкции концевой балки
Исходя из условий работы выбираем материал сталь 09Г2С ГОСТ 19281-89. Производим расчет по допустимым напряжениям [3.стр114]:
где – допустимое напряжение;
– предел текучести материала;
– коэффициент запаса прочности;
Для стали 09Г2С = 265 МПа.
Принимаем = 160 МПа для расчета концевых балок.
Определяем массу моста крана по графику представленному на рисунке 8. Данный график характеризует массу металлических конструкций половин сварных мостов (без концевых балок).
Рисунок 8 – график масс половин крановых мостов
Из рисунка 8 находим ориентировочно массу главной балки 1000 кг.
Вес механизма передвижения определяем на основании аналогичных конструкций в зависимости от типа привода и грузоподъёмности. Принимаем массу тали 400 кг.
Главную балку рассматриваем как балку на двух опорах загруженную постоянными нагрузками в вертикальной плоскости.
В расчетном положении таль с грузом находится в крайнем положении у концевой балки.
Рисунок 9 – Расчетное положение тали с грузом
Составим уравнения равновесия позволяющие выразить искомые реакции в опорах:
где – сила тяжести номинального груза;
– сила тяжести тали;
– сила тяжести главной балки ;
– крайнее положение грузовой тележки конструктивно принимаем = 13 м.
– реакции найдены правильно.
Расчет концевой балки ведем по максимальной опорной реакции.
Рисунок 10 – Расчетная схема концевой балки на вертикальные нагрузки
Определим реакции в опорах :
Составляем уравнения для поперечных сил и изгибающих моментов:
Рассмотрим левую часть.
Участок 1 0≤ Z1≤175;
Рассмотрим правую часть балки:
Участок 2. 0≤ Z2≤175;
Рисунок 11 – Расчетная схема балки нагруженной собственной силой тяжести
Рассмотрим правую часть.
Инерционные силы возникающие при пуске или торможении тали с грузом вызывают изгибающий момент в опасном сечении концевой балки:
где – сила инерции при торможении или пуске тали с грузом:
Максимальный момент действующий на концевую балку:
Высоту балки назначают в зависимости от размера пролета по соотношению [2стр.135]:
Принимаем толщину стенки = 6 мм .
Определяем оптимальную высоту балки:
где- момент сопротивления поперечного сечения балки [5стр141]:
Тогда согласно формуле ()
Исходя из конструкторских соображений принимаем Н=550 мм.
Определяем расстояние между стенками [2стр.135]:
Проверка: исходя из условия обеспечения удобства сварочных работ
Определяем свес полок над стенками: при автоматической и полуавтоматической сварке ; принимаем
Определяем ширину полки при рельсе между стенками: [2.стр135]
Толщина верхнего пояса [2стр135]:
Толщина нижнего пояса [2стр135]:
Определяем высоту стенки [2стр135]:
Полученную высоту стенки необходимо проверить с учетом ее толщины:
Определяем высоту опорной части [2стр135]:
Принимаем исходя из конструкторских соображений = 230 мм.
Определяем длину скоса концевых участков пролетной балки [2стр135]:
Принимаем С = 460 мм.
Рисунок 12 – Поперечное сечение концевой балки
Выбрав основные размеры крановых балок определяют геометрические параметры расчетных сечений.
Площадь сечения балки есть сумма площадей сечений верхней и нижней полок и стенок:
Площади каждого пояса равны:
Рисунок 13 – Расчетное сечение балки
Статический момент сечения равен сумме статических моментов его элементов:
где – статический момент 1–го элемента сечения относительно оси проходящий через крайние волокна всего сечения.
Статический момент верхнего пояса:
Статический момент нижнего пояса:
Статический момент стенки:
Статический момент сечения балки:
Статический момент всего сечения:
Определяем момент инерции сечения относительно главной центральной оси х – х проходящей через центр тяжести.
Момент инерции сечения относительно оси х–х равен сумме моментов инерции его элементов относительно той же оси:
Момент инерции верхней полки:
Момент инерции нижней полки:
Момент инерции стенки балки:
Момент сопротивления сечения балки относительно нейтральной оси для верхнего пояса:
Аналогично определяем моменты инерции и моменты сопротивления сечения балки относительно вертикальной центральной оси у–у проходящей через центр тяжести сечения:
Статический момент верхней полки относительно вертикальной оси ОУ:
Статический момент нижней полки:
Статический момент левой стенки:
Статический момент правой стенки:
Момент инерции сечения относительно центральной оси у–у:
Момент инерции сечения левой стенки:
Момент инерции сечения правой стенки:
Момент сопротивления сечения балки относительно нейтральной оси у–у:
Напряжения в поясах концевой балки:
- момент сопротивления сечения концевой балки.
Напряжение в поясах концевой балки от действия собственной силы тяжести.
Напряжения в поясах концевой балки от действия сил инерций:
Наибольшие нормальные напряжения сжатия в верхнем и нижнем поясах концевой балки:
После расчета на прочность главные балки крана проверяют на статическую и динамическую жесткость.
Расчет на статическую жесткость заключается в определении прогиба главной балки от действия подвижной нагрузки [5стр.204].
Определим перемещения по способу Верещагина. Для этого перемножаем эпюры Мр и Ме .
9 55 условие выполняется.
Рисунок 14 – Эпюры изгибающих и поперечных сил
Техника безопасности при эксплуатации крана
Правила устройства и безопасной эксплуатации грузоподъемных кранов [2] разработаны в соответствии с Законом Республики Беларусь от 10 января 2000 года "О промышленной безопасности опасных производственных объектов" (Национальный реестр правовых актов Республики Беларусь 2000 г. № 8 2138) и обязательны для всех организаций независимо от их организационно-правовой формы и формы собственности а также для индивидуальных владельцев грузоподъемных кранов.
Правила устанавливают требования к проектированию устройству изготовлению реконструкции монтажу установке ремонту эксплуатации и диагностированию грузоподъемных кранов их узлов и механизмов включая приборы и устройства безопасности а также грузозахватных органов грузозахватных приспособлений и тары.
Правила распространяются на:
- краны всех типов включая мостовые краны-штабелеры с машинным приводом и краны-манипуляторы;
- грузовые электрические тележки передвигающиеся по надземным рельсовым путям совместно с кабиной управления;
- краны-экскаваторы используемые для работы только с крюком подвешенным на канате или электромагнитом;
- электрические тали;
- подъемники крановые;
- лебедки с машинным приводом предназначенные для подъема груза и (или) людей;
- грузозахватные органы;
- грузозахватные приспособления;
- тару за исключением специальной тары применяемой в металлургическом производстве а также в морских и речных портах требования к которой устанавливаются отраслевыми правилами и (или) нормами.
Машинист грузоподъемных кранов обязан:
- знать требования Правил;
- знать инструкцию для машинистов грузоподъемных кранов а также инструкцию завода-изготовителя по монтажу и эксплуатации крана;
- знать безопасные способы строповки зацепки грузов и складирования;
- контролировать работу стропальщика и отвечать за действия прикрепленного к нему для прохождения стажировки ученика а также за нарушения требований изложенных в Правилах должностной инструкции и инструкции завода-изготовителя по монтажу и эксплуатации крана;
- проверять наличие приборов и устройств безопасности на кране (конечных выключателей указателя грузоподъемности в зависимости от вылета стрелы сигнального прибора аварийного рубильника ограничителя грузоподъемности анемометра нулевой блокировки); проверять исправность съемных грузозахватных приспособлений и тары; сообщать о замеченных неисправностях железнодорожного пути ответственному за безопасное производство работ кранами;
- производить работы с использованием крана только по сигналу стропальщика. Если стропальщик дает сигнал действуя вопреки инструкции то машинист по такому сигналу не должен производить требуемый маневр крана. За повреждения причиненные действиями крана вследствие выполнения неправильно поданного сигнала несут ответственность как машинист так и стропальщик подавший неправильный сигнал. Обмен сигналами между стропальщиком и машинистом должен производиться по установленному в организации порядку. Сигнал "Стоп" крановщик обязан выполнять независимо от того кто его подает;
- определять по указателю грузоподъемности грузоподъемность крана для каждого вылета стрелы. При работе крана на уклоне а железнодорожного крана также по кривой когда указатель вылета не учитывает уклона вылет стрелы определять фактическим промером при этом замеряется горизонтальное расстояние от оси центральной колонны крана до центра свободно висящего крюка;
- перед подъемом груза предупредить стропальщика и всех находящихся около крана лиц о необходимости уйти из зоны поднимаемого груза и возможного опускания стрелы. Перемещение груза можно производить только при отсутствии людей в зоне работы крана.
Указанные требования машинист должен выполнять также при подъеме и перемещении грейфера или грузоподъемного магнита; при погрузке и разгрузке вагонеток автомашин и прицепов к ним железнодорожных полувагонов и платформ убедиться в отсутствии людей на транспортных средствах; устанавливать крюк подъемного механизма над грузом так чтобы при подъеме груза исключалось косое натяжение грузового каната; при подъеме груза массой близкой к разрешенной грузоподъемности для данного вылета стрелы поднять его на высоту не более 200-300 мм чтобы убедиться в устойчивости крана и исправности действия тормозов после чего производить его подъем на нужную высоту; при подъеме стрелы следует следить чтобы она не поднималась выше положения соответствующего наименьшему рабочему вылету; при подъеме и опускании груза находящегося вблизи стены колонны штабеля железнодорожного вагона автомашины станка или другого оборудования предварительно убедиться в отсутствии людей между поднимаемым грузом и указанными частями здания транспортными средствами или оборудованием а также в невозможности задевания стрелой или поднимаемым грузом стен колонн вагона и других препятствий. Укладка грузов в полувагоны на платформы и вагонетки а также снятие его должны производиться без нарушения равновесия полувагонов вагонеток и платформ и под наблюдением лица ответственного за безопасное производство работ кранами; перед подъемом груза из колодца канавы траншеи котлована и перед опусканием груза в них предварительно убедиться путем опускания порожнего (ненагруженного) крюка в том что при его низшем положении на барабане остается не менее 15 витка каната не считая витков находящихся под зажимным устройством; укладывать и разбирать грузы равномерно без нарушения установленных для складирования грузов габаритов; внимательно следить за канатами в случае спадания их с барабана или блоков образования петель или обнаружения повреждений канатов необходимо приостановить работу крана.
Машинист грузоподъемного крана несет ответственность за нарушения требований Правил; ему запрещается:
- устанавливать кран под действующей линией электропередачи любого напряжения. Устанавливать кран или производить перемещение груза на расстоянии ближе 30 м от крайнего провода линии электропередачи машинист может только при наличии наряда-допуска подписанного главным инженером или главным энергетиком организации являющейся владельцем крана. Работа крана в этом случае должна производиться под непосредственным руководством ответственного лица назначенного приказом по организации с указанием его фамилии в наряде-допуске;
- при наличии у крана двух механизмов подъема одновременная их работа. Крюк неработающего механизма должен быть всегда поднят в наивысшее положение;
- отключать приборы безопасности;
- производить подъем или опускание груза когда в зоне работы крана находятся люди;
- допускать к обвязке или зацепке грузов лиц не имеющих удостоверения стропальщика а также применять грузозахватные приспособления без бирок или клейм. Машинист в этих случаях должен прекратить работу краном и поставить в известность лицо ответственное за безопасное производство работ кранами;
- поднимать или кантовать груз масса которого превышает грузоподъемность крана для данного вылета стрелы. Если машинист не знает массы груза то он должен получить в письменном виде сведения о массе груза у лица ответственного за безопасное производство работ кранами;
- опускать стрелу с грузом до вылета при котором грузоподъемность крана будет меньше массы поднимаемого груза;
- производить резкое торможение при повороте стрелы с грузом;
- подтаскивать груз по земле рельсам и лагам крана при косом натяжении канатов а также передвигать железнодорожные вагоны платформы вагонетки или тележки при помощи крюка;
- поднимать крюком или грейфером груз засыпанный землей или примерзший к земле заложенный другими грузами укрепленный болтами
или залитый бетоном;
- освобождать краном защемленные грузом съемные грузозахватные приспособления;
- поднимать железобетонные изделия с поврежденными петлями неправильно обвязанный груз находящийся в неустойчивом положении подвешенный за рог двурогого крюка а также в таре заполненной выше бортов;
- укладывать груз на электрические кабели и трубопроводы а также на краю откоса или траншеи;
- поднимать груз с находящимися на нем людьми а также груз выравниваемый массой людей или поддерживаемый руками;
- передавать управление краном лицам не имеющим прав на управление краном а также допускать к самостоятельному управлению учеников и стажеров без своего наблюдения за ними;
- производить погрузку и разгрузку автомашин при нахождении людей в кабине;
- поднимать баллоны со сжатым или сжиженным газом не уложенные в специальные контейнеры.
В данном курсовом проекте изложены:
) Общие расчеты механизмов полукозлового крана грузоподъемностью 32 т скорость подъема груза 013 мс высота подъема груза 6 м пролет 8 м .
) Методика выбора и проверки электродвигателей редукторов муфт и тормозов механизмов подъема груза и передвижения крана;
) Методика расчета металлоконструкции крана;
) Разработаны меры безопасности при эксплуатации крана.
Список использованных источников
Кузьмин А.В. Марон Ф.Л. Справочник по расчётам механизмов подъёмно-транспортных машин. - М.: Высш. Школа 1983. - 350с.
Иванченко Ф.К. и др. Расчеты грузоподъемных и транспортирующих машин.- К.: Вища школа 1978.
С.А.КазакВ.Е.Дусье и др.Курсовое проектирование грузоподъемныхмашин -Высш.шк.1989.-319с.
Абрамович И.И. Котельников Г.А. Козловые краны общего назначения. М.: Машиностроение 1983.-232с.
Руденко Н.Ф. Александров М.П. и Лысяков А.Г. Курсовое проектирование грузоподъемных машин. Изд. 3-е переработанное и дополненное – М.: Машиностроение 1971. - 464с.
Справочник по кранам: В 2 т. Т. 1. Характеристики материалов и нагрузок. Основы расчета кранов их приводов и металлических конструкцийВ.И. Брауде М.М. Гохберг И.Е. Звягин и др.; Под общ. ред. М.М. Гохберга. - М.: Машиностроение 1988. - 536с.: ил.
Гохберг М.М. Металлические конструкции подъемно-транспортных машин. - М.: Машиностроение 1969. - 520с.
И.Н.ЖивейновГ.Н.КарасевИ.Ю.Цвей. Строительная механика и металлоконструкции строительных и дорожных машин: Учебник для вузов по специальности «Строительные и дорожные машины и оборудование». М.: Машиностроение 1988. – 280с.