Стационарный поворотный кран грузоподъемностью 4 тонны




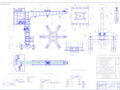
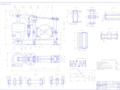
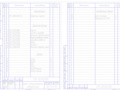
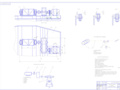
- Добавлен: 25.10.2022
- Размер: 2 MB
- Закачек: 2
Описание
Состав проекта
![]() |
![]() ![]() ![]() ![]() |
![]() ![]() |
![]() ![]() |
![]() ![]() ![]() ![]() |
![]() ![]() ![]() ![]() |
![]() ![]() ![]() |
![]() ![]() |
![]() ![]() |
![]() ![]() ![]() ![]() |
Дополнительная информация
mpg2.dwg

Номинальная грузоподъемность
Скорость подъема груза
Высота подъема груза
Группа режима работы
Класс нагружения крана
Класс использования механизма
Группа режима работы механизма подъема груза
Коэффициент использования механизма по
Коэффициент использования механизма в течении года
Коэффициент использования механизма в течении суток
Средняя относительная продолжительность рабочего
Схема одвеса груза к барабану
Кинематическая схема МПГ
vid_obschiy.dwg

Место установки мостового крана
Номинальная грузоподъёмность
Скорость подъёма груза
Высота подъёма груза
Группа режима работы крана
К средний ГОСТ 25546-82
Класс нагружения крана
Коэф. использования по грузоподъёмности
Класс использования механизма
Коэф. использования в течении года
Коэф. использования в течении суток
Средняя относительная продолжительность работы механизма
Число включений механизма
Группа режима работы МПГ
зубчатая цилиндрическая
Кинематическая схема МПГ
Кинематическая схема механизма передвижения тележки
Технические характеристики
Кинематическая схеме поворота крана
tkg-200-1.dwg

Ширина тормозной колодки
Максимальный тормозной момент
Отход колодки от шкива начмакс мм
Допустимая продолжительность включений
Коэффициент трения накладки о шкив
График работы пружины
kursovaya_var_4.doc
Стационарный поворотный кран
Составление технических данных необходимых для расчёта механизма подъёма груза
1 Механизм подъёма груза – стационарный поворотный кран
2 Номинальная грузоподъёмность – Q = 40 кН.
3 Скорость подъёма груза – V = 036 ммин.
4 Высота подъёма груза – Н = 8 м.
5 Пролёт (вылет) крана – Lmax= 6 м.
6 Группа режима работы – 4К
7 Класс нагружения крана – Q3
8 Класс использования механизма – А4
9 Группа режима работы механизма подъёма груза – 4М
10 Место установки ГПМ – открытая площадка
11 Коэффициент использования механизма по грузоподъёмности Кгр=08
12 Коэффициент использования механизма в течение года Кг=06
13 Коэффициент использования механизма в течение суток Кс=066
14 Средняя относительная продолжительность рабочего цикла механизма – ПВ 25%
15 Число включений механизма в течение часа - h = 120
16 Срок службы крана - Т = 10 лет
Выбор схемы размещения механизма подъёма груза на стационарном поворотном кране
Рисунок 1 – Стационарный поворотный кран
1 Выбор схемы подвешивания груза.
Принимаем согласно [128] для рассматриваемого механизма сдвоенный полиспаст. Для обеспечения нормального положения крюковой подвески при неравномерной вытяжки ветвей каната обоих полиспастов применяют установку балансира или что чаще уравнительного блока С (Рис. 2). В большинстве конструкций используют однослойную навивку на барабан.
1.1 Схема подвешивания груза к барабану.
1.2 Определение кратности полиспаста.
Кратность полиспаста – это отношение числа ветвей на которые распределяется действие груза к числу ветвей набегающих на барабан.
где m - число ветвей на которые распределяется действие груза.
mб - число ветвей набегающих на барабан.
1.3 Определение числа параллельных потоков.
Усилие от веса груза передается на барабан по двум потокам.(mб = 2)
1.4 Определение кпд полиспаста.
где t – число отклоняющих блоков
б – кпд блока (б = 098 согласно [2] )
Выбор каната для механизма подъема груза.
1 Определение максимального натяжения каната.
Максимальное в канате имеет место в точке набегания каната на барабан.
где q – вес крюковой подвески согласно [5] q = Q · 002
2 Определение требуемой разрывной нагрузки каната в целом.
По нормам Госгортехнадзора расчет канатов сводится к определению максимального натяжения и разрывного усилия по которому выбирают тип и размеры каната.
z – коэффициент запаса прочности. Для механического привода и группы режима работы механизма 4М согласно [1] z = 42.
Практикой эксплуатации рекомендуются следующие конструкции канатов для их использования в кранах в качестве подъемных и тяговых элементов: канаты с органическим сердечником ЛК-Р 6 канат с металлическим сердечником ТЛК-РО 6x36+7x7 (ГОСТ 7669-80). Принимаем по рекомендациям [145] стальной канат с органическим сердечником типа ЛР 6x19+1 О.С. (ГОСТ 2688-80).
ЛК – линейное касание проволок в пряде
– шесть прядей в канате
– девятнадцать проволочек в каждой пряде.
О.С. – один органический сердечник.
В грузоподъемных машинах применяют канаты с пределом прочности проволочек в = 1600 2000 МПа. ближайшее разрывное усилие каната по данным [3479] Sраз = 147000 Нмм2 при диаметре каната dk = 15 мм.
3.1 Обозначение каната по ГОСТ 3081-80
Канат 15 – Г – – Л – О – Н – 1770 ГОСТ 3081-80
Н – нераскручивающийся
70 – временное сопротивление разрыву
3.3 Определение фактического коэффициента запаса прочности.
Запас прочности обеспечивается.
Определение геометрических параметров барабана.
В большинстве случаев в грузоподъемных машинах применяются нарезные барабаны для однослойной навивки каната. Канавки нарезанные на поверхности барабана (по винтовой линии) увеличивают поверхность соприкосновения чем уменьшают напряжение смятия устраняют трение между соседними витками и износ каната. Поэтому при нарезных барабанах срок службы каната увеличивается.
1 Определение диаметра барабана.
Диаметр барабана определяется исходя из обеспечения требуемой долговечности каната. Минимальный диаметр барабана по центрам каната согласно [127]
где h1 – коэффициент зависящий от типа ГПМ и группы режима работы механизма подъема груза для группы 4М согласно [12] h1 = 25.
Уточняем значение с нормальным рядом размеров и принимаем Dб = 160 мм.
2 Определение размеров канавок на барабане.
При однослойной навивки каната на барабан размеры канавок можно определить по рекомендациям [1259]. Для dk = 15 мм рекомендуются R = 85 мм t = 18 мм h = 75 мм.
D – диаметр барабана D2 – диаметр намотки t – шаг нарезки R – радиус канат d – диаметр каната – толщина стенки барабана.
3 Определение длины барабана.
Для сдвоенного барабана симметрично на внешней поверхности нарезаются винтовые канавки правого и левого направления.
3.1 Определение необходимого числа витков на каждой половине барабана.
где - число неприкосновенных витков (2 3) [2 5 6]
зап – число запасных витков согласно нормам Госгортехнадзора принимают зап = 15 2 (приняли зап = 2). Принимаем л.п. = 26
3.2 Определение длины нарезной части на каждой половине барабана.
3.3 Определение размера для размещения уравнительного блока.
По рекомендации в [5] принимаем С = 200.
3.4 Определение расстояния от места крепления каната до края барабана.
3.5 Определение общей длины барабана.
Выбор и расчет крепления каната на барабане.
Нормами Госгортехнадзора обусловлено крепление каната на барабане или прижимными планками или клиновыми зажимами обеспечивающими надежность крепления.
Наиболее широкое применение имеет крепление каната планками прижимающими канат к барабану. При навивке канат из первой крайней канавки на барабане сразу переводят через одну канавку в третью для чего частично вырубают выступы нарезки разделяющие канавки. При этом среднюю канавку используют для установки крепежных винтов. Каждая прижимная планка крепится с помощью одного или двух винтов. Независимо от расчета согласно правилам Госгортехнадзора устанавливают не менее двух одновинтовых планок. В случае крепления прижимных планок двумя винтами для каната диаметром до 31 мм устанавливают по одной планке и по две планки при большем диаметре каната.
1 Схема крепления каната на барабане.
2 Определение усилия выдергивающего канат из под планки.
Вследствие уменьшения натяжения каната в месте его крепления к барабану за счет регламентированных нормами техники безопасности полутора неприкосновенных витков натяжение каната перед прижимной планкой выражается формулой:
где – минимальный коэффициент трения между канатом и поверхностью барабана согласно [12] = 016;
α – минимальный угол обхвата барабана неприкосновенными витками α = 3 т. е. α = 942 рад;
S'max – максимальное рабочее натяжение в канате при подъеме груза при действии возможных нагрузок S'max = Smax · Кдин
где Кдин - коэффициент динамических нагрузок зависит от характера изменения пускового момента двигателя высоты подъема груза скорости подъема груза.
где апр – коэффициент учитывающий пусковые характеристики двигателя: для двигателей с короткозамкнутым ротором апр = 1; для двигателя с фазным ротором и управлением от силового контролера апр = 08; для двигателя с фазным ротором и управлением магнитным контролером апр = 06.
Ек – модуль упругости стальных канатов согласно [2] Ек = 12 · 1011 Нмм2;
Ак – площадь живого сечения металла каната:
где – коэффициент заполнения металлом сечение каната согласно [2] = 05.
3 Определение размеров болта крепящего накладку к барабану.
3.1 Схема соединения накладкой с трапецеидальной канавкой.
3.2 Определение необходимой силы прижатия накладки к барабану.
где Z – число накладок в одном креплении в нашем случае Z = 2;
- минимальный коэффициент трения между канатом и накладкой согласно [12] при трапецеидальной форме сечения канавки
α1 – угол обхвата барабана витками крепления каната α1 = 2 = 628 рад.
4 Определение суммарных напряжений в теле болта.
Болт находится в сложнонапряженном состоянии.
где 13 – числовой коэффициент учитывает напряжение кручения возникающее при затяжке винтов;
А1 – площадь поперечного сечения в теле болта на которую действует сила F;
к – коэффициент запаса надежности крепления каната к барабану учитывающий возможные отклонения фактического значения коэффициента трения от расчетного и влияние динамических нагрузок согласно [12] ;
Ми – изгибающий момент Ми = Skp ·
Wи – момент сопротивления в теле болта .
Согласно [5] для dк = 16 мм возможно использовать болт с резьбой М8 для которого dвн = 665 мм
5 Выбор материала для изготовления болта и определение допускаемых напряжений.
Принимаем согласно [7] для изготовления болта Сталь 20 для которой в = 400Нмм2 т = 240Нмм2.
Согласно [7] допускаемое напряжение определяют по формуле
где [n] – коэффициент равный 25 согласно [7].
Уравнение прочности тела болта
Условие прочности соблюдается! 2067 96
элементов механизма подъема и определение их параметров.
1 Выбор схемы механизма подъема груза.
Принимаем схему механизма подъема груза рекомендованную в [125] (Рис. 8).
Обычно механизмы подъема (Рис.8) состоят из зубчатого цилиндрического или червячного редуктора 1 соединенного через муфту 3 с электродвигателем 4 и тормозного устройства 2. Выходной вал редуктора соединяется с барабаном 5. На барабане закреплен гибкий грузовой элемент соединенный с грузозахватным устройством. Соединение валов механизмов рекомендуется выполнять с помощью зубчатых муфт. Допускается также применение упругих втулочно-пальцевых муфт. Соединение двигателя с редуктором часто выполняется с применением вала-вставки позволяющей создать наиболее удобное расположение элементов механизма на металлоконструкции тележки. У механизмов подъема имеющих неразмыкаемую кинематическую связь барабана с двигателем в качестве тормозного шкива можно использовать одну из полумуфт соединения двигателя с редуктором. Если эта муфта является упругой (втулочно-пальцевая пружинная и т. п.) то по правилам Госгортехнадзора в качестве тормозного шкива можно использовать только полумуфту находящуюся на валу редуктора. При этом упругие элементы муфты при торможении не нагружены и срок службы их увеличивается. Согласно правилам Госгортехнадзора механизмы подъема груза и изменения вылета стрелы выполняют так что опускание груза или стрелы возможно только двигателем.
2 Выбор электродвигателя
2.1 Определение потребной мощности двигателя при установившемся движении груза.
где м – кпд механизма подъема груза: м = р · п · бар
где р – кпд передачи мощности р = 098i здесь i – число ступеней в редукторе. в нашем случае возможно использовать трехступенчатый редуктор.
бар – кпд барабана по рекомендации в [5] бар = 097.
Pп = ((5+2)*8)(60*0886) =0783
По рекомендации в [57] возможно использовать асинхронный двигатель с контактными кольцами и фазным ротором типа MTF. Асинхронные двигатели с контактными кольцами фазным ротором (МТ МВТ MTF МТН) по сравнению с короткозамкнутыми имеют металлоемкость и габаритные размеры несколько больше они сложнее по устройству и управлению более дорогие однако позволяют обеспечивать плавность пуска и торможения и изменять в достаточных размерах пусковые моменты допускают регулирование скорости в двигательном и тормозном режимах имеют меньшие потери энергии в обмотках при переходных процессах. Основная особенность таких двигателей — возможность уменьшения при помощи реостата пускового тока при одновременном увеличении пускового момента. Вследствие простоты конструкции и значительного пускового момента они являются наиболее распространенными в крановых механизмах.
– единая серия; М – металлургический; Т – переменного тока; F – класс изоляции (155°).
2.2 Определение частоты вращения барабана.
2.3 Определение требуемого общего передаточного числа передачи.
Возможно использовать редуктор типа Ц2У среди которых имеются редуктора с передаточными отношениями 25; 315.
Расхождение по передаточному отношению составят:
При выборе частот вращения валов предпочтение следует отдавать более скоростным двигателям выбираем двигатель 4MTF132L6.
2.4 Эскиз двигателя.
3.1 Определение максимального длительно действующего крутящего момента на тихоходном валу редуктора.
Тт = 11((2*138*0375)(2*097)) = 015кН
где доп iдоп – кпд и передаточное число дополнительных передач если он присутствуют.
3.1.1 Определение эквивалентного крутящего момента на тихоходном валу редуктора.
где кдн – коэффициент долговечности
где кпн – коэффициент переменности нагрузки для МПГ и режима работы механизма подъема груза 4М согласно [19] кпн = 0554;
ксс – коэффициент срока службы согласно [9]
где NOH – базовое число циклов нагружения зубьев колеса тихоходной передачи.
NΣ – суммарное число циклов нагружения.
Принимаем согласно [1723] для изготовления колеса Сталь 20 с улучшенной термообработкой до ННВ = 195 220. Согласно [1723] NOH = 12 · 106.
Для однородной структуры материала ксс можно принять 1≤ ксс ≤ 28.
Для поверхностной закалки ксс можно принять 1≤ ксс ≤ 18.
3.2 Выбор типа редуктора и его параметров.
Работоспособность редуктора сохраняется если выполняется условие:
где ТТном – допускаемый длительно действующий момент на тихоходном валу редуктора. В нашем случае Ц2У по [17] имеется редуктор с передаточным отношением i = 315
3.3 Проверка обеспечения подъема груза.
При i = 315 и выбранном двигателе произойдет изменение частоты вращения грузового барабана.
Действительная скорость подъема груза составит:
Расхождение с заданной скоростью составляет:
Окончательно принимаем редуктор с передаточным отношением i = 315.
3.4 Уточнение параметров выбранного редуктора.
Установим редуктор Ц2У – 100 для которого i = 315 ТТном = 315 Н·м межосевое расстояние aw = 180 мм = 096.
0 – межосевое расстояние на тихоходной передаче
3.5 Эскиз редуктора.
3.6 Схема присоединительных валов редуктора.
4 Расчет барабана на прочность.
4.1 Определение толщины стенки барабана.
Барабаны выполняются литыми из чугуна или стали и сварными стальными. Стенки барабана испытывают сложное напряжение сжатия кручения и изгиба.
Принимаем для изготовления барабана чугун СЧ – 24. Исходя из технологии изготовления литого барабана толщину стенки определяют по формуле:
где Dб* - диаметр барабана по дну канавок;
4.3 Определение допускаемых напряжений.
Согласно [1] для чугуна СЧ – 24 при группе режима работы механизма 4М []сж = 115 МПа.
4.4 Определение напряжений сжатия в теле барабана.
Напряжения сжатия в стенке барабана определяют по теории напряженного состояния кольца нагруженного равномерно распределенным по его внешней поверхности давлением. Наибольшее напряжение возникает на внутренней поверхности кольца:
Условие сж []сж выполняется для данного материала.
4.5 Определение напряжений изгиба в теле барабана.
4.6 Определение напряжений кручения в теле барабана.
4.7 Проверка прочности барабана на совместное действие напряжений сжатия кручения и изгиба.
Условие прочности выполняется т. к.
4.8 Проверка стенки барабана на устойчивость.
Надо учитывать что стенка барабана нагруженная радиальным давлением от витков каната может потерять устойчивость.
При расчете на устойчивость запас устойчивости цилиндрической стенки барабана принимают из условия:
где n – рекомендуемый запас устойчивости: [n] = 17 для стальных барабанов и [n] = 20 для чугунных барабанов согласно [1]; к – критическое напряжение в цилиндрической стенке МПа.
где Ебар — модуль упругости материала стенки барабана МПа: для сварных стальных барабанов Ебар = 21 · 105 для литых стальных барабанов Ебар = 19 · 105 и для чугунных барабанов Ебар =105 согласно [1]; — коэффициент учитывающий влияние деформации стенки барабана и каната:
Здесь Екан — модуль упругости стальных канатов: для шестипрядных канатов с органическим сердечником Екан = 9 · 104 МПа и для таких же канатов с металлическим сердечником Екан = 11 · 105 МПа согласно [1]; Акан — площадь сечения всех проволок каната мм2:
где – степень заполнения металлом сечения каната согласно [2] = 05; Rвн – радиус внутренней поверхности стенки барабана:
Критические напряжения к не должны быть более 08 т для стальных барабанов и более 06 в.и для чугунных барабанов. Если фактический запас устойчивости оказывается меньше рекомендуемого то надо или увеличивать толщину стенки или ввести в конструкцию барабана дополнительные ребра жесткости.
Устойчивость оболочки барабана обеспечена!
5 Выбор крюковой подвески и крюка.
Выбор типа крюковой подвески. По типу крюка они бывают с однорогим и с двурогим крюком. Если в задании не указано для перемещения каких грузов предназначен кран то можно выбирать любой тип. Если кран предназначен для перемещения длинномерных грузов наиболее предпочтительна крюковая подвеска с двурогим крюком.
5.1 Выбор типоразмера крюковой подвески.
Первое условие – грузоподъемность крюковой подвески не должна быть меньше заданной грузоподъемности: Qn ≥ Q. Второе условие – режим работы крюковой подвески должен соответствовать режиму работы механизма.
Грузовые крюки изготовляют ковкой или штамповкой из низкоуглеродистой стали 20 допускается изготовление крюков из стали 20Г. Применение высокоуглеродистой стали и чугуна недопустимо из-за малой пластичности материала и опасности внезапного излома крюка. После ковки или штамповки проводят нормализацию для снятия внутренних напряжений. Применение литых стальных крюков ограничено из-за возможности образования внутренних дефектов металла при литье. Для изготовления которых ковкой требуется мощное кузнечнопрессовое оборудование. Механической обработке подвергается только хвостовик крюка на котором нарезается резьба — треугольная при грузоподъемности до 10 т и трапециевидная при большей грузоподъемности. С помощью этой резьбы крюк закрепляется на траверсе крюковой подвески.
После изготовления крюк испытывают на прочность под нагрузкой превышающей его номинальную грузоподъемность на 25%. При испытании крюк выдерживают под нагрузкой не менее 10 мин; после снятия нагрузки на крюке не должно быть трещин надрывов остаточных деформаций.
При применении стандартного крюка (соответствующей номинальной грузоподъемности) расчет сечений крюка производить не требуется.
Для принятой схемы подвешивания груза принимаем крюковую подвеску по ОСТ 24.191.08-81
5.2Эскиз крюковой подвески.
6 Выбор муфты для соединения электродвигателя с редуктором.
Применяем муфту с тормозным шкивом.
6.1 Определение расчетного момента для выбора муфты.
где Т – момент на валу где устанавливается муфта
к1 – коэффициент учитывающий степень ответственности механизма для МПГ согласно [15] к1 = 13 при среднем режиме работы.
к2 – коэффициент учитывающий режим работы механизма при среднем режиме работы к2 = 12 согласно [5].
Принимаем муфту МУВП №1.
Коническая расточка не более
Проверка двигателя на возможность разгона груженого механизма с ускорением допустимым по условиям нормальной эксплуатации.
В период разгона механизма должно соблюдаться условие:
где tp.max – максимально допустимое время разгона. По рекомендациям в [13] принимаем tp.max = (2 3) с.
tp.min – минимально допустимое время разгона по условию ограничения динамических нагрузок в процессе пуска механизма. c
где [а] – допустимое ускорение груза: для механосборочных цехов [а] = 02 мс2; для погрузочно-разгрузочных работ согласно [1] [а] = 08 мс2.
Действительное время разгона определяют из выражения Тср.пуск = Тр
где Тср.пуск – средний пусковой момент двигателя в период разгона
Тр – момент сопротивлению движению в период разгона (приведенный к валу двигателя).
1 Определение среднего пускового момента двигателя.
2 Определение момента сопротивления движению приведенного к валу двигателя.
В период разгона имеет место: Тр = Тст + Тдин' + Тдин''
где Тст – момент статического сопротивления приведенный к валу двигателя
Тдин' – динамический момент для сообщения ускорения поступательно движущимся массам приведенный к валу двигателя
Тдин'' – динамический момент для сообщения ускорения вращающимся массам.
где м – кпд передачи мощности согласно [12] м = 091.
это уравнение справедливо только при условии равноускоренного движения: .
- частота вращения соответствующая установившемуся движению
- линейная скорость груза
- плечо действия сил инерции
- переход от частоты вращения барабана к частоте вращения вала электродвигателя
- переход от момента сил инерции груза к моменту сил инерции на валу электродвигателя.
где 11 – коэффициент учитывающий влияние деталей частота вращения которых меньше частоты вращения электродвигателя
Σ I = Ip + IM – сумма моментов инерции деталей частота вращения которых равна частоте вращения вала двигателя.
Условие tp.max > tp > tp.min выполняется 2 > 08 >066.
Выбор и расчет тормозного устройства.
1 Выбор типа тормозного устройства.
Согласно Правилам Госгортехнадзора механизмы подъема груза и изменения вылета стрелы с машинным приводом должны быть снабжены тормозами нормально-замкнутого типа автоматически размыкающимися при включении привода механизма. Применение в этих механизмах управляемых тормозов нормально-разомкнутого типа и тормозов постоянно замкнутых (не размыкаемых при работе механизма) не допускается. Механизмы подъема с ручным приводом должны быть снабжены автоматически действующими тормозами замыкаемыми весом транспортируемого груза.
На механизмах передвижения и поворота грузоподъемных машин с электроприводом применяют тормоза нормально-замкнутые и комбинированные. Однако на механизмах поворота башенных и портальных кранов могут применяться и тормоза нормально-разомкнутого типа.
Примем за основу проектируемого тормоза – тормоз колодочный с электрогидравлическим толкателем типа ТКГ – 200.
2 Схема тормоза ТКГ – 200.
Расчетная схема тормоза ТКГ – 200.
Торможение осуществляется за счет потенциальной энергии пружины.
В данной конструкции необходимо производить следующие регулировки:
) Изменение усилия затяжки пружины (изменяется величина тормозного момента);
) Регулирование величины отхода колодок;
) регулирование хода штока гидротолкателя.
Для изготовления полумуфты и тормозного шкива применим Сталь 45Л. Для изготовления фрикционных накладок можно использовать вальцованную тормозную ленту для которой согласно [710] f = 042 048 [р] = 06 МПа Толщина ленты считается по зависимости b = 20 + 5 · n где n = 0 1 2 bmax = 130 мм.
3 Определение статического тормозного момента от веса груза приведенного к тормозному валу.
Тсм = ((60+002)*0375*091)(2*2*315) = 0004кН м
3.1 Определение требуемого тормозного момента.
где – коэффициент запаса торможения согласно [1] = 175 для группы режима 4М.
3.2 Определение необходимой силе трения между колодкой и шкивом.
3.3 Требуемое нажатие колодки на шкив.
3.4 Усилие пружины замыкающей тормоз.
4 Расчет замыкающий пружины.
Для изготовления пружины используем проволоку из Стали 60С2А со следующими механическими характеристиками: в = 1600 Нмм2 т = 1000 Нмм2.
4.1 Определение предельного усилия на торце пружины при её полном сжатии.
где кз – коэффициент учитывающий необходимость дополнительного сжатия пружины при регулировки тормоза согласно [7] кз = 13 16.
4.2 Определение диаметра проволоки.
Исходя из допускаемых напряжений кручения определяем диаметр проволоки:
где к – коэффициент кривизны согласно [8] к = 105 125;
λ = Dcp d – отношение среднего диаметра пружины к диаметру проволоки согласно [8] λ = 4 16;
[] – допускаемое напряжение в пружине согласно [8] [] = 07 09 т [] = 700 900 Нмм2.
Принимаем диметр пружины согласно ГОСТ 9389 – 75 d =25 мм.
4.3 Определение геометрических параметров пружины.
4.3.1 Определение среднего диаметра пружины.
Dcp = 7 · 4 = 28 мм принимаем Dcp = 30 мм.
4.3.2 Определение рабочей длины пружины.
Lp = (03 05)Dш = (03 05)·200 = (60 100)мм принимаем Lp = 100мм.
4.3.3 Определение наименьшего зазора между витками пружины в рабочем состоянии.
≥ (01 025)d = (01 .. 025)·25 = (025 0625)мм принимаем = 06 мм.
4.3.4 Определение шага рабочих витков пружины.
t = d + = 25 + 06 = 31 мм.
4.3.5 Определения числа рабочих витков.
принимаем Zp = 34 витка.
4.3.6 Определение длины полностью сжатой пружины.
Lnp = Zp · d = 34 · 25 = 85 мм
4.3.7 Определение поджатия пружины из свободного состояния до рабочего.
4.3.8 Определение длины пружины в свободном состоянии.
LCB = Lnp + ΔL = 85 + 40 = 125 мм.
4.3.9 Определение шага витков пружины в свободном состоянии.
Для обеспечения нормального контакта пружины с ограничивающими поверхностями необходимо поджать с каждой стороны 075 витка затем торцы зашлифовать тогда полная длина пружины LCB.n = LCB + 15d = 125 + 15 · 25 = 12875 мм. Длина пружины при расторможенном состоянии Lp.p = Lp - e·(cl3) = 100 – 22 · (60170) = 922 мм.
Усилие на торцах пружины при расторможенном состоянии тормоза определяется
4.4 Проверка прочности пружины при большем сжатии.
Условие прочности выполняется т. к. и 7063 ≤ 900.
4.5 Проверка рабочих поверхностей фрикционных накладок по удельному давлению.
Условие выполняется!
Расчет процессов торможения МПГ.
Уравнение моментов при торможении имеет вид
где Тт – номинальный момент развиваемый тормозом Тт = 0007 кН · м;
Т'т.ст – статический момент от груза с крюковой подвеской;
Т'т.ин и Т''т.ин - моменты от сил инерции соответственно движущихся поступательно масс и вращающихся масс приведенные к тормозному валу.
1 Определение времени торможения при подъеме груза.
2 Определение времени торможения при опускание груза.
3 Определение ускорения при торможении поднимаемого и опускаемого груза.
Согласно п.7 [а] = 02 мс2
Расчет динамических нагрузок в механизме подъема груза при пуске.
1 Приведение массы вращающихся частей к грузу.
где – коэффициент учитывающий влияние вращающихся деталей частота вращения которых меньше частоты вращения вала двигателя принимаем = 11;
Ip и IM – моменты инерции ротора и муфты;
2 Определение жесткости канатного полиспаста.
где Ек – модуль упругости материала каната Ек = 90000 МПа;
Fk – площадь сечения каната заполненного металлом
где – степень заполнения металлом сечения каната = 05 согласно [1];
zk – число ветвей каната между массами m1 и m2 zk = 4;
l – наименьшая длина полиспаста l 1000мм.
3 Определение движущей силы F приведенной к грузу.
4 Определение собственной частоты колебания массы.
5 Определение периода собственных колебаний.
6 Определение максимального динамического усилия при пуске механизма подъема груза.
Согласно [7] динамические усилия в упругих связях при пуске изменяются по ассиметричному закону.
Максимальное динамическое усилие возникает если cos pt = -1.
7 Определение коэффициента динамичности с выбранным двигателем при пуске МПГ.
Расчет динамических нагрузок при торможении.
1 Определение усилия торможения приведенного к грузу.
2 Определение максимальных динамических нагрузок в упругой связи при торможении.
3 Определение коэффициента динамичности при торможении.
Определение максимальных динамических нагрузок.
Максимальная нагрузка возникает при подъеме груза с подхватом т. е. двигатель МПГ включается при наличии слабины каната. При этом груз подхватывается двигателем уже имеющим достаточно высокую частоту вращения. Если принять что подх = подъема то
1 Определение коэффициента динамичности при подъеме груза с подхватом.
Значение кд соответствует группе режима работы механизма 4М.
Подъемно-транспортные машины. Александров М. П. 1986г.
Грузоподъемные механизмы. Александров М. П. 2000г.
Подъемно-транспортные машины. Вайнсон А. А.«Машиностроение»
ПТМ. Атлас конструкций. Александров М. П.1989г.
Справочник по расчетам подъемно-транспортных машин. Марон Ф.К.
Расчеты ГПМ и ТМ. Иванченко Ф. К. 1984г.
Тормозные устройства. Александров М. П. 1985г.
Приводы машин. Длоуги В. В. 1982г.
ГосГорТехНадзор России .«Правила устройства и безопасной эксплуатации грузоподъемных кранов.»1993г.
Расчет деталей машин на прочность. Бергер И. А. и другие.
spets_obschiy_vid.dwg

Механизм передвижения тележки
Механизм поворота крана
Рекомендуемые чертежи
- 25.10.2022