Разработка привода главного движения токарно - карусельного станка 1525




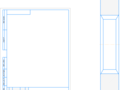
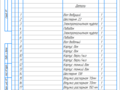
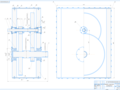
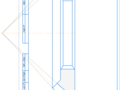
- Добавлен: 04.11.2022
- Размер: 13 MB
- Закачек: 0
Описание
Состав проекта
![]() |
![]() ![]() ![]() |
![]() ![]() ![]() |
![]() ![]() ![]() |
![]() |
![]() |
![]() ![]() ![]() ![]() |
![]() ![]() ![]() |
![]() ![]() |
![]() ![]() ![]() |
![]() ![]() ![]() |
![]() |
![]() |
![]() |
![]() |
![]() |
![]() |
![]() |
![]() |
![]() |
![]() |
![]() ![]() ![]() ![]() |
![]() |
![]() |
![]() |
![]() |
![]() |
![]() |
![]() |
![]() |
![]() |
![]() ![]() ![]() |
![]() |
![]() |
![]() ![]() ![]() |
![]() ![]() ![]() |
![]() |
![]() |
![]() ![]() ![]() ![]() |
![]() |
![]() ![]() ![]() ![]() |
![]() |
![]() |
![]() |
![]() |
![]() |
![]() |
![]() |
![]() |
![]() |
![]() |
![]() |
![]() |
![]() |
![]() |
![]() |
![]() ![]() ![]() |
![]() |
![]() |
![]() |
![]() |
![]() |
![]() ![]() ![]() |
![]() ![]() ![]() |
![]() ![]() ![]() |
Дополнительная информация
Содержание.docx
Обоснование технической характеристики
1 Виды работ выполняемых на станках заданного типа
2 Выбор и расчет режимов резания
Структурное проектирование привода с регулированием скорости выходного звена частотно-регулируемым двигателем
1 Разработка структурной сетки коробки скоростей
2 Разработка кинематической схемы проектируемого станка
3 Выбор электродвигателя
4 Построения графика вращения шпинделя
Проектирование зубчатого зацепления и валов передачи
1 Определение передаточных отношений и числа зубьев зубчатых колес.
2 Построение зубчатых колес в среде КОМПАС Shaft и их расчет на прочность
Конструирование и расчет валов
1 Определение минимальных диаметров валов
Введение.docx
В качестве режущего инструмента на токарных станках применяют резцы разнообразных форм а так же сверла зенкеры и развертки метчики.
Токарные станки с ЧПУ являются наиболее универсальными станками токарной группы. Предназначенные для выполнения разнообразных операций на деталях широкой номенклатуры; используются главным образом в крупносерийном и массовом производствах.
Номенклатура токарных станков включает в себя множество станков отличия между которыми заключается в максимальном диаметре обрабатываемой заготовки различных модификациях и степенью точности
SAPR_LR_7_-_Metod_KE_2011.doc
Лабораторная работа №7
Данная работа предназначена для изучения применения метода конечных элементов (МКЭ) для решения инженерных задач при проектировании.
Для детали спроектированной в лабораторной работе №5 выполнить линейный статический анализ напряженного состояния методом конечных элементов. При этом:
)Указать величину и точку расположения наибольшего эквивалентного напряжения (найти координаты).
)Указать величину и точку расположения наибольшего перемещения. Определить форму деформации вала. Построить график перемещений ступеней вала.
)Представить эпюры эквивалентного напряжения перемещений и коэффициента запаса прочности.
)Дать заключение о годности детали и дать рекомендации по улучшения конструкции детали по критериям прочности жесткости и минимальной массы.
Некоторые теоретические сведения
МКЭ численный метод. Относится к исследованию сложных систем по частям (диакоптика см. ПРИЛОЖЕНИЕ Д). Вариационный метод – частный случай метода Ритца.
Понятие конечного элемента впервые введено Тернером в 1956 году 3 с целью аппроксимации сплошной среды с бесконечным числом степеней свободы совокупностью подобластей (элементов) имеющих конечное число степеней свободы. Между элементами устанавливается определенная связь через узловые точки. В узловых точках вводятся фиктивные силы эквивалентные поверхностным напряжениям распределенным по границам элементов.
Суть метода рассмотрим на примере 4 простой конструкции состоящей из одного стержня (рисунок 1). Сетка одномерная. Жесткость упругого материала определяется
гдеk – жесткость материала (коэффициент упругости);
К стержню в точках 1 и 2 приложены силы F1 F2 . Точки 1 и 2 через которые стержень соединен с другими элементами будем называть узлами. Под действием F1 F2 узлы сместятся на x1 и x2 . Можно записать
Или в векторной форме
Усложним задачу разбив стержень на два элемента (рисунок 3).
Матричное уравнение будет иметь вид
Детали конструкций описываются чаще всего трехмерными сплошными элементами. Соотношение силы и перемещения для таких элементов уже в значительной степени зависят от геометрии элемента а не только от коэффициента упругости. Общее выражение матрицы жесткости имеет вид
где (B) – матрица описания геометрии элемента
(D) – матрица отношения напряжения и деформации (которое включает модули Юнга и коэффициент Пуассона)
(Bt) – транспонированная матрица (B)
Обычно для описания элемента вводятся следующие понятия:
Область – определяется через относительные положения узлов элемента.
Степень свободы – направления возможного перемещения каждого узла.
Размерность матрицы жесткости зависит от общего числа степеней свободы узлов сетки. В общем случае размерность матрицы жесткости для объекта определяется произведением количества узлов сетки на количество степеней свободы узла.
Краткие сведения о программных средствах решения задачи
Данная работа может быть выполнена в среде любого интегрированного пакета программ САПР (CADCAE) имеющего модули для инженерного анализа.
К таким программам можно отнести в первую очередь SOLID Works имеющим модуль инженерного анализа. В Ошибка! Закладка не определена. даны некоторые указания по технике работы с этой программой и с модулем SIMULASTION для анализа методом конечных элементов. Все указания даны для SOLID Works 2010.
Можно также рекомендовать программы: ANSYS NASTRAN Unigraphics CATIA и др. имеющие модуль инженерного анализа.
Анализируемая модель детали создается в КОМПАС-3D и импортируется в SOLID Works посредством форматов PARASOLID x_t или x_b. Можно использовать и другие форматы обмена трехмерных моделей.
Описание модуля SIMULASTION и основные рекомендации по его использованию приведены в Справочные сведения SolidWorks Simulation (в меню SIMULASTION Справка).
Модуль SIMULASTION интегрирован с программой трехмерного моделирования SolidWorks. Модуль SIMULASTION применяется для решение задач по нахождению напряжений смещений деформаций температурных полей и оптимизации. Используется SIMULASTION FFE (Fast Finite Element) технология в которой модуль SIMULASTION использует решатели: Direct Sparse Solver и New FFE (Fast Finite Element – быстрый конечный элемент) Solver. Первый решатель построен на технологии обработки и хранения разреженных матриц. Второй является итерационным решателем. Выбор между решателями определяется по результатам эффективности вычислений. Оптимизация применяется для поиска оптимальных параметров конструкции удовлетворяющей определенным требованиям.
Программа может выполнить:
Линейный статический анализ чтобы вычислять смещения деформации и напряжения;
Линеаризированный анализ продольного изгиба (выпуклый) для вычисления критических нагрузок продольного изгиба и соответствующих форм;
Частотный анализ для вычисления резонансных частот и соответствующих форм колебаний;
Анализ установившихся и переходных состояний термических процессов для вычисления температуры температурные градиенты и изменения потоков тепла;
Оптимизационное проектирование;
Расширенный динамический анализ линейных систем с различными видами нагрузок во времени и частотами воздействия;
Нелинейный статическийдинамический анализ;
Процесс дискретизации формы детали (разбиение на элементы) выполняется в автоматическом режиме.
Программа анализа методом конечных элементов создает математическую модель объекта таким образом что можно имитировать поведение объекта в его рабочей среде. Метод конечных элементов моделирует геометрию модели и ее материалы а также встречающиеся нагрузки и ограничения. В процессе анализа модели автоматически создается система уравнений решение которой дает информацию о поведении модели под нагрузкой. Можно представить результаты в графических или табличных форматах.
Подготовка модели для анализа
Внимание важно! Так как данная работа требует повышенных вычислительных ресурсов: большого объёма оперативной памяти и высокой скорости обмена данными рекомендуется все файлы: исходных данных промежуточных данных а также результатов поместить временно в отдельной папке на рабочем столе компьютера. После окончания работы папку переместить на постоянное место хранения. Далее по ходу выполнения работы будут даны указания как настраиваются программы для правильного доступа к данным.
Подготовку модели можно рекомендовать в следующей последовательности.
)В КОМПАС-ГРАФИК 3D создать трехмерную модель исследуемого вала. На рисунке 4 показан пример исходной модели вала.
)Для симуляции нагрузок и ограничений на вал создать модель сборки вала с сопряженными деталями (рисунок 5).
)Для уменьшения порядка системы алгебраических уравнений упростить модель сборки для этого: зубчатые колёса шкивы и муфты заменить частью их ступиц причём наружный диаметр заменяющей части принимается из расчета учитывающего уменьшение влияния концентрации напряжений от шлицевых канавок шпоночных канавок резьбы и т.п. если они имеются на ступицах. Это превышение можно рекомендовать в пределах 5 10 раз глубины шпоночного или шлицевого паза или шага резьбы для резьбового соединения
гдеDНАР – наружный диаметр мм;
t2 – глубина шпоночного паза 1 мм;
для шлицевого соединения
D d – наружный и внутренний диаметры шлицев соответственно мм.
Подшипники убираются из модели т.к. в программе для анализа имеется возможность моделировать подшипниковое соединение. Полностью подготовленная модель сборки для анализа вала показана на рисунке 6.
)Подготовленную модель экспортировать в SolidWork с помощью формата Parasolid: команда Сохранить как установить тип файла x_t или x_b Сохранить.
)Запустить программу SolidWork.
)Открыть файл модели сборки в формате Parasolid в SolidWork. При этом будут созданы новые файлы сборки в формате sldasm и всех деталей сборки в формате sldprt. Также в процессе открытия может быть предложено выполнить распознавание структуры геометрии – рекомендуется отказаться от этой операции т.к. в процессе распознавания может быть допущена неправильная интерпретация некоторых геометрических элементов модели и её искажение в целом.
)Сохранить модель сборки в формате sldprt. Описать свойства файла:
Автор Фамилия Имя Отчество
Заметки Отчет по лабораторной работе № 7. Анализ МКЭ.
)Ввести в модель дополнительные объекты вспомогательной геометрии. В приложении А приведены приёмы ввода вспомогательной геометрии. Для сборки вала рассматриваемого примера для оси вращения ввести вспомогательную геометрию – ось.
)Для удобства доступа в дальнейшем к результатам анализ отдельных деталей можно создать вид с разнесёнными частями. В приложении Б приведена последовательность команд для создания вида с разнесёнными частями.
Подготовка расчетной модели и запуск анализа
Расчетная модель описывает все исходные условия для анализа: материал деталей составляющих сборку закрепление силовые нагрузки и конечно-элементное описание геометрии сборки.
)Выбрать режим работы SIMULASTION.
)Настроить пути сохранения результатов работы модуля SIMULASTION. Для этого в текстовом меню SolidWorks выбрать раздел Simulastion выбрать команду Параметры . В окне Настройки пользователя в закладке Настройки по умолчанию выбрать на дереве Результаты результатов и указать временную рабочую папку установить для опции Папка отчётов Папка результатов.
)Командой Новое исследование открыть окно Исследование.
)Установить тип анализа Статическое и дать имя (имя исследования можно оставить предложенное по умолчанию). Командой ОК закрыть окно Исследование.
В окне дерева данных появится структура условий анализа (рисунок 7).
Далее все параметры условий анализа будем назначать с помощью указания курсором на дереве нужного объекта и вызова локального меню правой клавишей мышки.
)Назначение материалов деталей сборки. Командой Применить материал открыть окно Материал (рисунок 8) и выбрать материал для всех деталей сборки. Назначение материала индивидуально для каждой детали выполняется указанием соответствующей детали на дереве и выбором команды Применить материал из локального меню. Если в списке материалов нет российских то следует подобрать из имеющихся ориентируясь на вкладку Свойства Предел прочности на растяжение и Предел текучести. Командами Применить и Закрыть выйти из окна Материал.
)Назначение условий контакта сопряженных деталей сборки. На дереве указать Глобальный контакт. Из локального меню командой Редактировать определение открыть окно Компонент соприкасания и установить опцию Нет проникновения. Здесь также можно установить коэффициент трения.
)Назначение условий закрепления. На дереве указать Крепления. Из локального меню командой Крепление подшипника открыть окно Крепление. На модели указать цилиндрическую грань на которую устанавливается подшипник. Если требуется выполнить анализ с учётом жёсткости подшипников то устанавливается опция Свободно и для выбранных направлений смещений записывается величина жёсткости. В приложении Г приведены значения жёсткости для некоторых видов подшипников. Командой ОК закрыть окно. Далее повторить описанные действия для крепления остальных подшипников.
)Назначение нагрузки. Исходя из условий работы рассчитать силы и крутящие моменты действующие в анализируемой конструкции.
Для рассматриваемого примера (рисунок 9):
Делительные диаметры зубчатых колёс мм
Передаваемый момент Нм
Тангенциальные составляющие сил зацеплений Н
Силы в зацеплениях Н
На дереве указать Внешние нагрузки. Из локального меню командой Сила открыть окно СилаВращающий момент и установить опцию Сила. На модели указать цилиндрическую грань первого зубчатого колеса. Установить опцию Выбранное направление. На дереве Сборки (в окне пространства построения) указать плоскость Top Plane. В окне СилаВращающий момент в поле Перпендикулярно плоскости вписать значение величины силы в зацеплении первого колеса. Командой ОК закрыть окно. Далее повторить описанные действия для второго колеса.
Передаваемые моменты назначаются также командой Сила . В окне СилаВращающий момент установить опцию Вращающий момент. На дереве Сборки (в окне пространства построения) указать на Axis (ось). На модели указать цилиндрическую грань первого зубчатого колеса. Вписать значение вращающего момента. Командой ОК закрыть окно. Далее повторить описанные действия для второго колеса при этом указать опцию Реверс направления. Если на валу происходит разделение потока передаваемой энергии по нескольким направлениям (например шевронные колёса) то необходимо строго соблюсти равенство сумм крутящих моментов в противоположных направлениях.
)Выполнить разбиение модели на элементы. На дереве указать Сетка. Из локального меню командой Создать сетку открыть окно Сетка. В окне параметров принять к сведению оптимальные значения параметров сетки установленные системой: Глобальный размер и Допуск. Их изменяют в том случае если процедура автоматической генерации сетки не выполнится.
Если генерация сетки не выполняется или требуется более плотная сетка то параметры Глобальный размер и Допуск меняют движком Коэффициент сетки в окне Плотность сетки или вписыванием величины сетки в поле Глобальный размер. Командой ОК закрыть окно и запустить процесс генерации сетки.
)Выполнить анализ модели. Командой Запуск запустить процесс расчёта.
Подготовка результатов для рассмотрения и анализа
На рисунке 10 показано окно полностью сформированного дерева данных для анализа результатов работы программы.
Перед рассмотрением результатов рекомендуется для вспомогательных деталей:
во-первых скрыть их изображения в разделе Сборка командой Погасить из локального меню скрываемого элемента и
во-вторых исключить их из анализа в разделе Детали командой локального меню Исключить из анализа. На рисунке 10 на дереве данных показаны исключенные детали Колесо 1 Колесо 2 Шпонка 1 и Шпонка 2.
Просмотр и анализ напряжений
)Открыть для просмотра эпюру напряжений для этого указать на объект Напряжение (-vonMises-) и выбрать из локального меню команду Отобразить.
По умолчанию система выводит эпюру напряжений под названием von Mises. Это название широко применяется в зарубежной технической литературе (гипотеза Губера-Мизеса). В России оно известно как четвертая гипотеза прочности для упруго пластичных материалов.
)На эпюре напряжений (рисунок 11) указать место наибольшего напряжения для этого на дереве указать объект Напряжение 1 (-vonMises-) командой локального меню Параметры графика открыть окно Параметры графика и установить опцию Отобразить максимальное примечание. Командой ОК закрыть окно. В отчёте дать объяснение почему деталь имеет в данном месте самое высокое напряжение.
)На шкале соответствия цветов величинам напряжений отметить чертой предел текучести материала и дать предварительное заключение о пригодности исследуемого вала. Дать предложения о возможных мерах по повышению прочности вала.
Просмотр и анализ перемещений
)Открыть для анализа эпюру Перемещение (-Расположение результата-) (рисунок 12).
По умолчанию система выводит эпюру Результирующих перемещений (геометрическая сумма перемещений по координатам).
Для определения формы деформации вала на дереве указать объект Перемещение 1 (Расположение результата-) командой локального меню Редактировать определение открыть окно Эпюра перемещения и установить опцию Деформированная форма - Авто. Командой ОК закрыть окно.
)Для построения графика деформации вала открыть два окна (рисунок 13) и установить вал в одном окне в положение вид спереди (из группы команд Ориентация видов) а в другом окне – в положение вид снизу. Может быть приняты и другие комбинации ориентаций видов в окнах важно чтобы шпоночные пазы или другие подобные элементы формы не оказались в местах зондирования.
)Создать две новые эпюры перемещений: по оси Z и оси Y (т.е. перпендикулярно оси вращения вала в рассматриваемом примере ось вращения вала направлена вдоль X).
Для этого на дереве для объекта Результаты из локального меню выбрать команду Определить эпюру перемещение в окне Эпюра перемещение для опции Отображение выбрать Перемещение Z. Закрыть окно. Таким же образом создаётся эпюра Перемещение Y.
)Из локального меню объекта Перемещение 2 (Расположение Z-) выбрать команду Зондирование и открыть окно Результаты зондирования. Курсором указать на модели последовательно cлева направо (так удобнее) точки приблизительно посредине каждой ступени вала (рисунок 13).
)Далее обработку результатов удобно провести в программе Excel. Для этого в окне Результаты зондирования выделить курсором все строки поля Результаты и скопировать выделенное в буфер обмена. Открыть программу Excel и вставить из буфера таблицу результатов зондирования.
)Повторить зондирование для эпюры Перемещение 2 (Расположение Y-) в окне Вид снизу. Результаты зондирования также передать в тоже окно Excel. На рисунке 14 в строках столбца P набрана формула геометрической суммы значений перемещений по осям соответственно Z и Y.
гдеZ и Y – значения перемещений по осям Z и Y мм.
На рисунке 14 приведён график изгиба вала по результатам геометрической суммы перемещений в точках зондирования.
Дать заключение о пригодности конструкции вала по жесткости (пользуясь рекомендациями приведенными в лабораторной работе №5). Максимальный прогиб валов несущих зубчатые колеса не должен быть более 00002 - 00003 от расстояния между опорами а допустимый прогиб ступеней под колесами не должен превышать
где m – модуль зацепления мм. Для m = 3 [] = 0.03 . Максимальное перемещение консольной ступени вала по результатам рисунка 14 = 0.049 > [] вывод: в данном примере вал не удовлетворяет условиям жесткости. Вывод отразить в отчете.
Анализ запаса прочности
)Открыть для анализа эпюру Запас прочности 1(-FOS-). В этой эпюре (рисунок 15) найти место расположения минимального коэффициента запаса прочности. Дать заключение о прочности вала и рекомендации по усовершенствованию с целью уменьшения массы.
Обратите внимание что коэффициент запаса прочности в окне Запас прочности описан формулой
Limit – допускаемое напряжение МПа.
Однако надо учесть что при адаптации программы для Росси разработчики пропустили это изображение формулы фактически же программа адаптирована к российской методике определения коэффициента запаса прочности
)Создать новую эпюру Запас прочности 2(-Максимальное напряжение vonMises -) (рисунок 16)
Для этого на дереве для объекта Результаты из локального меню выбрать команду Определить эпюру проверка запаса прочности в окне Запас прочности в поле Критерий вместо Авто выбрать Максимальное напряжение vonMises нажать кнопку Далее для опции Предел текучести установить множитель 1 нажать ещё раз кнопку Далее установить опцию Области ниже запаса прочности установить коэффициент запаса прочности например 2.5. Закрыть окно.
На рисунке 16 области окрашенные в красный цвет не удовлетворяют по прочности.
Автоматическая генерация отчёта работы программы
)Сформировать отчёт командой Отчет. В окне Параметры отчёта заполнить поля:
В поле Включенные разделы: удалить разделы расчёты для которых не выполнялись в процессе работы программы например: результаты датчиков силы свободного тела силы реакции балки силы шпилек и т.п.
Для раздела Вывод описать основные выводы например: Вал не работоспособен по жесткости и прочности. Требуется оптимизация размеров вала по критериям жесткости и прочности.
Название Автор Организация Дата.
Указать путь для отчета – личная папка студента (рекомендуется временно расположить папку на рабочем столе и после окончания работы скопировать её в постоянное место хранения).
Формат отчета указать html. Если на компьютере установлен MS Office 2010 то отчёт может быть сгенерирован в Microsoft Word.
Команды Применить и Опубликовать.
В дополнительных материалах представлен отчёт в формате htm для рассматриваемого примера.
Создание отчета о работе в целом
Отчет должен содержать:
)Пояснительную записку в формате DOC с общим описанием выполненной работы которая должна содержать:
Цель и задачи работы.
Исходные данные в виде рисунка модели детали с закреплениями и нагрузками. Величины нагрузок должны быть представлены в сопроводительной таблице.
Результаты анализа в виде эпюр:
Эквивалентного напряжения. В отдельной таблице указать величину и точку расположения наибольшего эквивалентного напряжения (найти координаты).
Перемещений. В отдельной таблице указать величину и точку расположения наибольшего перемещения.
Коэффициента запаса прочности. В отдельной таблице указать величину и точку расположения минимального коэффициента запаса прочности.
Заключение о годности детали и дать рекомендации по улучшения конструкции детали по критериям прочности жесткости и минимальной массы.
)Набор файлов полученных в результате выполнения работы. Все файлы отчета должны быть названы одинаково по форме: САПР-7 Фамилия> где Фамилия> - фамилия студента. Все материалы файлы отчета должны быть помещены в отдельную папку с таким же именем как и файлы. Всего должно быть не менее 5-ти файлов:
Пояснительная записка в формате DOC.
Исходная модель в формате CDW.
Обменный файл в формате PARASOLID.
Рабочий фай в формате SLDPRT.
Файл автоматически генерированного отчета в формате DOC или HTML.
)Что такое линейный тип анализа чем отличается нелинейный тип анализа от линейного?
)Что понимается под конечным элементом?
)Что такое матрица жесткости?
)Как определяется размерность матрицы жесткости?
Ли К. Основы САПР (CADCAMCAE). – СПб.: Питер 2004. – 560 с.
Норри Д. Де Фриз Ж. Введение в метод конечных элементов Пер. с англ. – М.: Мир 1981. – 304 с.
Turner M.J Clough R.W. Martin H.C. Topp L.J. Stiffness and Deflection Analisis of Complex Structures J. Aero. Sci. 23 805 – 823 (1956).
Б. Хокс Автоматизированное проектирование и производство Пер. с англ. – М.: Мир 1991. – 296 с.
Зенкевич О. Метод конечных элементов в технике. – М.: Мир 1975. – 473 с.
Л. Сегерлинд Применение метода конечных элементов: Пер. с англ. – М.: Мир 1979.
Интерактивные учебные пособия SolidWorks Simulation.
ТЕХНИЧЕСКИЕ И ПРОГРАММНЫЕ СРЕДСТВА
Процессор: Intel Pentium 4 CPU
Скорость процессора: 17 ГГц
Операционная система: Microsoft Windows XP Professional 2002 Пакет обновления 1
Создание объектов вспомогательной геометрии
Установить режим работы Сборка. В меню Справочная геометрия:
На модели выбрать цилиндрическую поверхность на которую будет накладываться радиальная нагрузка
В меню Вставка Справочная геометрия Точка
в окне параметров опция Центр дуги на модели указать дугу цилиндрической поверхности на которую будет накладываться радиальная нагрузка
В меню Вставка Справочная геометрия Ось
в окне параметров опция ЦилиндрическаяКоническая грань на модели указать цилиндрическую поверхность для которой создаётся ось
)Вставить дополнительную систему координат:
В меню Вставка Справочная геометрия Система координат
в окне параметров поле Исходная точка вводится указанием на дереве конструирования объект Точка (или Исходная точка если вспомогательные точки не создавались)
в окне параметров поле Ось Z вводится указанием на дереве построения на объект Ось 1
На рисунке А.1 показаны системы координат для отверстий к которым прикладывается нагрузка.
Развертка КС.cdw

Спецификация развертка.spw
Втулка распорная 70мм
Втулка распорная 150 мм
Крышка подшипника 150мм глухая
Крышка подшипника 150мм сквозная
Крышка подшипника 320мм глухая
Крышка подшипника 320 сквозная
Болт М10x30 ГОСТ 15591-70
Болт М10x105 ГОСТ 15591-70
Болт М10x115 ГОСТ 15591-70
Болт М20x50 ГОСТ 15591-70
Болт М20x200 ГОСТ 15591-70
Подшипник 180614 ГОСТ 8882-75
Подшипник 382630 ГОСТ 18572-81
Подшипник KK 70X78X50 ГОСТ 24310-80
Реферат.DOC
КОРОБКА СКОРОСТЕЙ СТАНОК ТОКАРНЫЙ РЕЖИМЫ РЕЗАНИЯ КИНЕМАТИЧЕСКИЙ РАСЧЕТ СТРУКТУРНАЯ СЕТКА МОДУЛЬ ВИНТ ПРОЧНОСТЬ ЖЕСТКОСТЬ.
Целью курсового проекта является проектирование основных узлов станка: коробки скоростей.
Указанная цель достигается выполнением расчетов режимов резания кинематического расчета расчетом основных деталей привода и изображение их на чертежах. Использованы наиболее простые и удобные в изготовлении детали. Проведен анализ различных кинематических схем коробки скоростей. Предполагаемый экономический эффект от применения данного станка не известен.
ПЗ3.docx
Проанализировав параметры аналогичных станков в качестве прототипа выбираем станок токарно-карусельный 1525.
Таблица 1 - Характеристика станков
Класс точности станка по ГОСТ 8-71
Диаметр устанавливаемой детали мм не более
Высота устанавливаемой детали мм не более
Масса устанавливаемой детали кг не более
Диаметр планшайбы мм
Число программируемых суппортов
Перемещения суппортов мм по осям:
Число подач суппортов по каждой оси
Бесступенчатое регулирование
Пределы измерения подач ммоб
Скорость установочных перемещений суппортов мммин
Число скоростей планшайбы
Частота вращения планшайбы обмин
Мощность привода планшайбы кВт
Масса станка с электрооборудованием т
ОБОСНОВАНИЕ ТЕХНИЧЕСКОЙ ХАРАКТЕРИСТИКИ
1 Виды работ выполняемых на станках заданного типа
Виды работ которые будут выполняться на проектируемом станке аналогичны работам которые выполняются на станке-прототипе а именно: черновое точение чистовое и черновое растачивание протачивание торцевых поверхностей.
2 Выбор и расчет режимов резания
Режимы резания выбираются по таблицам (по экспериментальным данным).
Сила резания при точении
Мощность резания при точении
Таблица 2 - Список работ составленный в Excel и импортированный в Word:
Обрабатываемый материал
Диаметр обработки D мм
Растачивание чистовое
Растачивание черновое
Продольное и поперечное точение черновое
Протачивание торцевых поверхностей
Таблица 3 - Данные необходимые для построения графиков
По результатам полученным в таблице строим графики:
Рисунок 1 - График мощностей
Рисунок 2 - График моментов
СТРУКТУРНОЕ ПРОЕКТИРОВАНИЕ ПРИВОДА С РЕГУЛИРОВАНИЕМ СКОРОСТИ ВЫХОДНОГО ЗВЕНА ЧАСТОТНО-РЕГУЛИРУЕМЫМ ДВИГАТЕЛЕМ
1 Разработка структурной сетки коробки скоростей
Требуемый диапазон R регулирования привода определяется по формуле:
Для токарно-карусельного станка с nmin = 9 nmax = 140
Mmax = 11945 NРmax = 1274 и nрасч N = 10 выбираем nэ ном = 1500 Rб = 10.
Требуемый диапазон регулирования коробки:
– знаменатель ряда частот в геометрической прогрессии φ = 1.26.
Рисунок 3. Структурная сетка
2 Разработка кинематической схемы проектируемого станка
После выбора варианта структурной сетки приступаем к разработке кинематической схемы привода главного движения станка. При этом за основу берем кинематическую схему привода главного движения станка-прототипа.
Рисунок 4 – Кинематическая схема
3 Выбор электродвигателя
По расчетным данным подходящий электродвигатель найден в среде Компас 3D v.15. Электродвигатель 4АМУ250М4 с выходными данными приведенными ниже в таблице:
Число оборотов обмин
Точное число оборотов в минуту обмин
Рисунок 5 - Сведения об электродвигателе.
Ранее заводами Украины производились общепромышленные трехфазные асинхронные электродвигатели серий 4АМУ 4АМСУ 4АМРУ АИРУ. Буква «У» в маркировке как раз об этом и сообщает. На сегодняшний день эти серии больше не выпускаются по тем или иным причинам. Электродвигатели серий 4АМУ 4АМСУ 4АМРУ АИРУ — это обычные стандартные общепромышленные электродвигатели с короткозамкнутым ротором которые легко заменяютсясовременными сериями АИР. Разница между сериями с цифрой «4» в начале и без нее или с цифрой «5» (например 4АМУ и 5АМУ) — только в степени влагопылезащиты.В связи с чем для дальнейшего расчета выбираем электродвигатель АИР250М4.
Рисунок 6 - исполнение IM1081 (1082)
Рисунок 7 - исполнение IM2081 (2082)
Установочные и присоединительные размеры мм
4 Построения графика вращения шпинделя
График частот вращения шпинделя строят в соответствии с принятой структурной сеткой и разработанной кинематической схемой проектируемого станка.
Рисунок 8 - График частот вращения шпинделя.
ПРОЕКТИРОВАНИЕ ЗУБЧАТОГО ЗАЦЕПЛЕНИЯ И ВАЛОВ ПЕРЕДАЧИ
1 Определение передаточных отношений и числа зубьев зубчатых колес.
В группе передач для наименьшего передаточного отношения группы назначаем для шестерни минимальное число зубьев Z1 = 22. Тогда
Для второй передачи группы числа зубьев Z3 и Z4 находим решая простую систему уравнений:
Модули передач можно рассчитать в программном продукте
Для расчета потребуются ранее определенные данные.
Для примера расчета выберем зубчатые колеса: z1-z2.
Войдя в программу АРМ Trans выбираем: Тип передачи – прямозубое внешнего зацепления Тип расчета – Проектировочный В диалоговом окне «Основные данные» вводим данные для расчета:
Рисунок 9 – Основные параметры зубчатого колеса
После ввода данных для расчета рассчитываем зубчатую передачу
Рисунок 10 – Геометрические параметры
Рисунок 11 – Параметры материалов
Рисунок 12 – Силы в зацеплении
2 Построение зубчатых колес в среде КОМПАС Shaft и их расчет на прочность
Пример расчета z1-z2.
Для построения колес потребуются данные таблицы №1. В программе «КОМПАС» запускаем «Менеджер библиотек - Расчет и построение – Валы и механические передачи 3D – Механические передачи – Шестерня цилиндрическая с внешними зубьями».
Далее на панели «Инструментов» запускаем расчет в модуле «КОМПАС Gears». В открывшемся окне выбираем вкладку: «Геометрический расчет» В диалоговом окне «Геометрический расчет; закладка Станица 1» вводим требующиеся для расчета данные:
Рисунок 13 – Геометрический расчет
Далее выбираем вкладку: «Страница 2» и производим окончательный расчет передачи затем заканчиваем расчет и нажимаем клавишу «возврат в главное окно»
Рисунок 14 – Геометрический расчет
После возврата в «главное окно» для расчета становится доступен «расчет на прочность». При вводе данных задаем максимальную нагрузку. Выбираем материал схему расположения передачи а также задаемся расчетной нагрузкой и числом оборотов на ведущем колесе.
Рисунок 15 – Расчет на прочность
КОНСТРУИРОВАНИЕ И РАСЧЕТ ВАЛОВ
1 Определение минимальных диаметров валов.
Минимальный диаметр валов находится по формуле:
После расчетов согласно справочнику 3 с.17 принимаем минимальные диаметры валов
Пример расчета вала №1
После сборки колес в среде КОМПАС геометрические параметры вала можно определить конструируя его «по месту» в сечении самой сборки. После окончательного построения вала требуется произвести проверочный расчет
Проверочный расчет валов коробки скоростей рассчитывается в программном продукте АРМ Shaft.
На рабочем поле операцией «Цилиндр» выстраивается конструкция рассчитываемого вала задаются опоры. С помощью инструментальной панели расставляются силы и моменты кручения в точке их приложения по расчетной цепи. Во вкладке Материал выбираем конструкционную сталь Ст45 используемую для изготовления валов. В команде «Рассчитать – Общий расчет вала » вводим частоту вращения вала и задаемся ресурсом работы изделия и во вкладке Результаты просматриваем интересующие нас рассчитанные программой характеристики по результатам расчета которых оценивается вал.
Рисунок 16 - Коэффициент запаса по усталостной прочности.
Рисунок 17 - Реакции в опорах.
Рисунок 18 - Эквивалентное напряжение.
Рисунок 19 - Угол кручения
В ходе курсового проекта были произведены необходимые расчеты при проектировании заданного технологического металлообрабатывающего оборудования (станка); проанализированы существующие конструкции аналогичных станков и выбраны из них наиболее подходящий станок-прототип; обоснована техническая характеристика станка; произведен кинематический расчет привода главного движения и расчет основных деталей привода.
По расчетным данным была вычерчена развертка коробки скоростей за общий вид проектируемого станка был принят общий вид станка-прототипа.
«Проектирование технологического металлообрабатывающего оборудования»: метод. указ. к выполнению курсового проекта Сост. Н.А. Кутний. – Хабаровск: Изд-во Хабар. гос. техн. ун-та 2002. – 79с.
Справочник технолога-машиностроителя. В 2-х т. Под ред. А.Г. Косиловой и Р.К. Мещерякова. – М.: Машиностроение 1985. 496 с.
«Расчет режимов резания»: метод. указ. по курсовому проекту по металлорежущим станкам Сост. В.В. Жуловян. – ХПИ. Хабаровск 1992.
Биргер И. А. Шорр Б. Ф. Шнейдерович Р. И. Расчет на прочность деталей машин: Справочное пособие.- М. 1966. – 616 с.
Детали и механизмы металлорежущих станков Под ред. Д. Н. Решетова: В 2 т. – М. 1972. Т. 2. – 520 с.
Детали машин: Атлас конструкций Под ред. Д. Н. Решетова. – М. 1979. – 367 с.
Кучер И. М. Металлорежущие станки. Основы конструирования и расчета. – Л. 1969. – 720 с.
Лизогуб В. А. Конструирование и расчет шпиндельных узлов направляющих и механизмов подач металлорежущих станков: Учеб. пособие. – М. 1985. – 90 с.
Анурьев В.И. Справочник конструктора-машиностроителя. В 3 т. Т. 2 В.И. Анурьев. –М.: Машиностроение 2001.–912 с.
исходник вала 2 конички.cdw

косозубая исходник 30.cdw

исходник вала 3.cdw

2 Глава.docx
1 Виды работ выполняемых на станках заданного типа
Виды работ которые будут выполняться на проектируемом станке аналогичны работам которые выполняются на станке-прототипе а именно: черновое точение чистовое и черновое растачивание протачивание торцевых поверхностей.
2 Выбор и расчет режимов резания
Режимы резания выбираются по таблицам (по экспериментальным данным).
Сила резания при точении
Мощность резания при точении
Список работ составленный в Excel и импортированный в Word:
Обрабатываемый материал
Диаметр обработки D мм
Растачивание чистовое
Растачивание черновое
Продольное и поперечное точение черновое
Протачивание торцевых поверхностей
Данные необходимые для построения графиков
По результатам полученным в таблице строим графики:
Рисунок 1 - График мощностей
Рисунок 2 - График моментов
4 Глава.docx
1 Определение передаточных отношений и числа зубьев зубчатых колес.
В группе передач для наименьшего передаточного отношения группы назначаем для шестерни минимальное число зубьев Z1 = 22. Тогда
Для второй передачи группы числа зубьев Z3 и Z4 находим решая простую систему уравнений:
Модули передач можно рассчитать в программном продукте
Для расчета потребуются ранее определенные данные.
Для примера расчета выберем зубчатые колеса: z1-z2.
Войдя в программу АРМ Trans выбираем: Тип передачи – прямозубое внешнего зацепления Тип расчета – Проектировочный В диалоговом окне «Основные данные» вводим данные для расчета:
Рисунок 4 – Основные параметры зубчатого колеса
После ввода данных для расчета рассчитываем зубчатую передачу
Рисунок 2 – Геометрические параметры
Рисунок 3 – Параметры материалов
Рисунок 4 – Силы в зацеплении
2 Построение зубчатых колес в среде КОМПАС Shaft и их расчет на прочность
Пример расчета z1-z2.
Для построения колес потребуются данные таблицы №1. В программе «КОМПАС» запускаем «Менеджер библиотек - Расчет и построение – Валы и механические передачи 3D – Механические передачи – Шестерня цилиндрическая с внешними зубьями».
Далее на панели «Инструментов» запускаем расчет в модуле «КОМПАС Gears». В открывшемся окне выбираем вкладку: «Геометрический расчет» В диалоговом окне «Геометрический расчет; закладка Станица 1» вводим требующиеся для расчета данные:
Рисунок 5 – Геометрический расчет
Далее выбираем вкладку: «Страница 2» и производим окончательный расчет передачи затем заканчиваем расчет и нажимаем клавишу «возврат в главное окно»
Рисунок 6 – Геометрический расчет
После возврата в «главное окно» для расчета становится доступен «расчет на прочность». При вводе данных задаем максимальную нагрузку. Выбираем материал схему расположения передачи а также задаемся расчетной нагрузкой и числом оборотов на ведущем колесе.
Рисунок 7 – Расчет на прочность
Конструирование и расчет валов
3.1 Определение минимальных диаметров валов.
Минимальный диаметр валов находится по формуле:
После расчетов согласно справочника 3 с.17 принимаем минимальные диаметры валов
Пример расчета вала №1
После сборки колес в среде КОМПАС геометрические параметры вала можно определить конструируя его «по месту» в сечении самой сборки. После окончательного построения вала требуется произвести проверочный расчет
Проверочный расчет валов коробки скоростей рассчитывается в программном продукте АРМ Shaft.
На рабочем поле операцией «Цилиндр» выстраивается конструкция рассчитываемого вала задаются опоры. С помощью инструментальной панели расставляются силы и моменты кручения в точке их приложения по расчетной цепи. Во вкладке Материал выбираем конструкционную сталь Ст45 используемую для изготовления валов. В команде «Рассчитать – Общий расчет вала » вводим частоту вращения вала и задаемся ресурсом работы изделия и во вкладке Результаты просматриваем интересующие нас рассчитанные программой характеристики по результатам расчета которых оценивается вал.
В ходе курсового проекта были произведены необходимые расчеты при проектировании заданного технологического металлообрабатывающего оборудования (станка); проанализированы существующие конструкции аналогичных станков и выбраны из них наиболее подходящий станок-прототип; обоснована техническая характеристика станка; произведен кинематический расчет привода главного движения и расчет основных деталей привода; выбрана схема шпиндельного узла и произведен расчет его основных параметров.
По расчетным данным была вычерчена развертка коробки скоростей сделана деталировка нескольких деталей включая шпиндель. За общий вид проектируемого станка был принят общий вид станка-прототипа.
3 Глава.docx
1 Разработка структурной сетки коробки скоростей
Требуемый диапазон R регулирования привода определяется по формуле:
Для токарно-карусельного станка с nmin = 9 nmax = 140
Mmax = 11945 NРmax = 1274 и nрасч N = 10 выбираем nэ ном = 1500 Rб = 10.
Требуемый диапазон регулирования коробки:
– знаменатель ряда частот в геометрической прогрессии φ = 1.26.
Рисунок 3. Структурная сетка
2 Разработка кинематической схемы проектируемого станка
После выбора варианта структурной сетки приступаем к разработке кинематической схемы привода главного движения станка. При этом за основу берем кинематическую схему привода главного движения станка-прототипа.
3 Выбор электродвигателя
По расчетным данным подходящий электродвигатель найден в среде Компас 3D v.15. Электродвигатель 4АМУ250М4 с выходными данными приведенными ниже в таблице:
Число оборотов обмин
Точное число оборотов в минуту обмин
Рисунок 4 - Сведения об электродвигателе.
Ранее заводами Украины производились общепромышленные трехфазные асинхронные электродвигатели серий 4АМУ 4АМСУ 4АМРУ АИРУ. Буква «У» в маркировке как раз об этом и сообщает. На сегодняшний день эти серии больше не выпускаются по тем или иным причинам. Электродвигатели серий 4АМУ 4АМСУ 4АМРУ АИРУ — это обычные стандартные общепромышленные электродвигатели с короткозамкнутым ротором которые легко заменяютсясовременными сериями АИР. Разница между сериями с цифрой «4» в начале и без нее или с цифрой «5» (например 4АМУ и 5АМУ) — только в степени влагопылезащиты.В связи с чем для дальнейшего расчета выбираем электродвигатель АИР250М4.
Рисунок 5 - исполнение IM1081 (1082)
Рис. 6 - исполнение IM2081 (2082)
Установочные и присоединительные размеры мм
4 Построения графика вращения шпинделя
График частот вращения шпинделя строят в соответствии с принятой структурной сеткой и разработанной кинематической схемой проектируемого станка.
Рисунок 6 - График частот вращения шпинделя.
1 Глава.docx
Проанализировав параметры аналогичных станков в качестве прототипа выбираем станок токарно-карусельный 1525.
Таблица 1. Характеристика станков
Класс точности станка по ГОСТ 8-71
Диаметр устанавливаемой детали мм не более
Высота устанавливаемой детали мм не более
Масса устанавливаемой детали кг не более
Диаметр планшайбы мм
Число программируемых суппортов
Перемещения суппортов мм по осям:
Число подач суппортов по каждой оси
Бесступенчатое регулирование
Пределы измерения подач ммоб
Скорость установочных перемещений суппортов мммин
Число скоростей планшайбы
Частота вращения планшайбы обмин
Мощность привода планшайбы кВт
Масса станка с электрооборудованием т
Обоснование технической характеристики
1 Виды работ выполняемых на станках заданного типа
Виды работ которые будут выполняться на проектируемом станке аналогичны работам которые выполняются на станке-прототипе а именно: черновое точение чистовое и черновое растачивание протачивание торцевых поверхностей.
2 Выбор и расчет режимов резания
Режимы резания выбираются по таблицам (по экспериментальным данным).
Сила резания при точении
Мощность резания при точении
Список работ составленный в Excel и импортированный в Word:
Обрабатываемый материал
Диаметр обработки D мм
Растачивание чистовое
Растачивание черновое
Продольное и поперечное точение черновое
Протачивание торцевых поверхностей
Данные необходимые для построения графиков
По результатам полученным в таблице строим графики:
Рисунок 1 - График мощностей
Рисунок 2 - График моментов
СТРУКТУРНОЕ ПРОЕКТИРОВАНИЕ ПРИВОДА С РЕГУЛИРОВАНИЕМ СКОРОСТИ ВЫХОДНОГО ЗВЕНА ЧАСТОТНО-РЕГУЛИРУЕМЫМ ДВИГАТЕЛЕМ
1 Разработка структурной сетки коробки скоростей
Требуемый диапазон R регулирования привода определяется по формуле:
Для токарно-карусельного станка с nmin = 9 nmax = 140
Mmax = 11945 NРmax = 1274 и nрасч N = 10 выбираем nэ ном = 1500 Rб = 10.
Требуемый диапазон регулирования коробки:
– знаменатель ряда частот в геометрической прогрессии φ = 1.26.
Рисунок 3. Структурная сетка
2 Разработка кинематической схемы проектируемого станка
После выбора варианта структурной сетки приступаем к разработке кинематической схемы привода главного движения станка. При этом за основу берем кинематическую схему привода главного движения станка-прототипа.
Рисунок 4 – Кинематическая схема
3 Выбор электродвигателя
По расчетным данным подходящий электродвигатель найден в среде Компас 3D v.15. Электродвигатель 4АМУ250М4 с выходными данными приведенными ниже в таблице:
Число оборотов обмин
Точное число оборотов в минуту обмин
Рисунок 5 - Сведения об электродвигателе.
Ранее заводами Украины производились общепромышленные трехфазные асинхронные электродвигатели серий 4АМУ 4АМСУ 4АМРУ АИРУ. Буква «У» в маркировке как раз об этом и сообщает. На сегодняшний день эти серии больше не выпускаются по тем или иным причинам. Электродвигатели серий 4АМУ 4АМСУ 4АМРУ АИРУ — это обычные стандартные общепромышленные электродвигатели с короткозамкнутым ротором которые легко заменяютсясовременными сериями АИР. Разница между сериями с цифрой «4» в начале и без нее или с цифрой «5» (например 4АМУ и 5АМУ) — только в степени влагопылезащиты.В связи с чем для дальнейшего расчета выбираем электродвигатель АИР250М4.
Рисунок 6 - исполнение IM1081 (1082)
Рис. 7 - исполнение IM2081 (2082)
Установочные и присоединительные размеры мм
4 Построения графика вращения шпинделя
График частот вращения шпинделя строят в соответствии с принятой структурной сеткой и разработанной кинематической схемой проектируемого станка.
Рисунок 8 - График частот вращения шпинделя.
ПРОЕКТИРОВАНИЕ ЗУБЧАТОГО ЗАЦЕПЛЕНИЯ И ВАЛОВ ПЕРЕДАЧИ
1 Определение передаточных отношений и числа зубьев зубчатых колес.
В группе передач для наименьшего передаточного отношения группы назначаем для шестерни минимальное число зубьев Z1 = 22. Тогда
Для второй передачи группы числа зубьев Z3 и Z4 находим решая простую систему уравнений:
Модули передач можно рассчитать в программном продукте
Для расчета потребуются ранее определенные данные.
Для примера расчета выберем зубчатые колеса: z1-z2.
Войдя в программу АРМ Trans выбираем: Тип передачи – прямозубое внешнего зацепления Тип расчета – Проектировочный В диалоговом окне «Основные данные» вводим данные для расчета:
Рисунок 9 – Основные параметры зубчатого колеса
После ввода данных для расчета рассчитываем зубчатую передачу
Рисунок 10 – Геометрические параметры
Рисунок 11 – Параметры материалов
Рисунок 12 – Силы в зацеплении
2 Построение зубчатых колес в среде КОМПАС Shaft и их расчет на прочность
Пример расчета z1-z2.
Для построения колес потребуются данные таблицы №1. В программе «КОМПАС» запускаем «Менеджер библиотек - Расчет и построение – Валы и механические передачи 3D – Механические передачи – Шестерня цилиндрическая с внешними зубьями».
Далее на панели «Инструментов» запускаем расчет в модуле «КОМПАС Gears». В открывшемся окне выбираем вкладку: «Геометрический расчет» В диалоговом окне «Геометрический расчет; закладка Станица 1» вводим требующиеся для расчета данные:
Рисунок 13 – Геометрический расчет
Далее выбираем вкладку: «Страница 2» и производим окончательный расчет передачи затем заканчиваем расчет и нажимаем клавишу «возврат в главное окно»
Рисунок 14 – Геометрический расчет
После возврата в «главное окно» для расчета становится доступен «расчет на прочность». При вводе данных задаем максимальную нагрузку. Выбираем материал схему расположения передачи а также задаемся расчетной нагрузкой и числом оборотов на ведущем колесе.
Рисунок 15 – Расчет на прочность
Конструирование и расчет валов
3.1 Определение минимальных диаметров валов.
Минимальный диаметр валов находится по формуле:
После расчетов согласно справочника 3 с.17 принимаем минимальные диаметры валов
Пример расчета вала №1
После сборки колес в среде КОМПАС геометрические параметры вала можно определить конструируя его «по месту» в сечении самой сборки. После окончательного построения вала требуется произвести проверочный расчет
Проверочный расчет валов коробки скоростей рассчитывается в программном продукте АРМ Shaft.
На рабочем поле операцией «Цилиндр» выстраивается конструкция рассчитываемого вала задаются опоры. С помощью инструментальной панели расставляются силы и моменты кручения в точке их приложения по расчетной цепи. Во вкладке Материал выбираем конструкционную сталь Ст45 используемую для изготовления валов. В команде «Рассчитать – Общий расчет вала » вводим частоту вращения вала и задаемся ресурсом работы изделия и во вкладке Результаты просматриваем интересующие нас рассчитанные программой характеристики по результатам расчета которых оценивается вал.
В ходе курсового проекта были произведены необходимые расчеты при проектировании заданного технологического металлообрабатывающего оборудования (станка); проанализированы существующие конструкции аналогичных станков и выбраны из них наиболее подходящий станок-прототип; обоснована техническая характеристика станка; произведен кинематический расчет привода главного движения и расчет основных деталей привода; выбрана схема шпиндельного узла и произведен расчет его основных параметров.
По расчетным данным была вычерчена развертка коробки скоростей сделана деталировка нескольких деталей включая шпиндель. За общий вид проектируемого станка был принят общий вид станка-прототипа.
Рекомендуемые чертежи
- 22.11.2015
- 10.02.2022
- 25.01.2023