Разработка конструкции привода главного движения токарно-винторезного станка 1А616




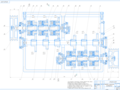
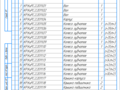
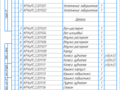
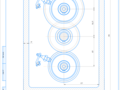
- Добавлен: 25.01.2023
- Размер: 5 MB
- Закачек: 1
Описание
Разработка конструкции привода главного движения токарно-винторезного станка 1А616
Состав проекта
![]() |
![]() |
![]() |
![]() ![]() ![]() ![]() |
![]() |
![]() ![]() ![]() ![]() |
![]() |
![]() ![]() ![]() ![]() |
![]() |
![]() ![]() ![]() ![]() |
![]() |
![]() ![]() ![]() ![]() |
![]() ![]() ![]() ![]() |
![]() ![]() ![]() |
![]() |
![]() |
![]() |
![]() ![]() ![]() ![]() |
![]() ![]() ![]() |
![]() |
![]() |
![]() |
![]() ![]() ![]() ![]() |
![]() ![]() ![]() ![]() |
![]() |
![]() ![]() ![]() ![]() |
![]() |
![]() |
![]() |
![]() ![]() ![]() ![]() |
![]() |
![]() |
![]() |
![]() |
![]() |
![]() ![]() ![]() ![]() |
![]() |
Дополнительная информация
Шпиндель.cdw

Общие допуски по ГОСТ 30893.1
Правильность геометричности формы повепхности конуса
проверять калибром по краске. Площадь пятна контакта при
толщине слоя краски 0
5 мм должна быть не менее 90% полной
площади контактируемых поверхностей
Нагрев на наружном кольце переднего подшипника при
установлении теплового равновесия не должен превышать 70
Узел обкатывать в течение 30 минут на 1600 мин
Для смазки зубчатых передач и подшипников использовать масло
индустриальное И-20А ГОСТ 20799-75.
Течи масла из под крышек
уплотнений и по местам соединений
Коробка скоростей - Спецификация.spw

Электромагнитная муфта ЭТМ042-1А
Винт М5х16 ГОСТ 11738-84
Винт М5х20 ГОСТ 17475-80
Винт М6х18 ГОСТ 1491-80
Винт М10х30 ГОСТ 11738-84
Гайка М6 ГОСТ 5927-70
Шпонка 8 х 7 х 32 ГОСТ 23360-78
Шпонка 6 х 6 х 32 ГОСТ 23360-78
Подшипник 205 ГОСТ 8338-75
Подшипник 1000905 ГОСТ 8338-75
Штифт 3 х 14 ГОСТ 3128-70
Коробка скоростей (Свёртка).cdw

Передняя бабка.cdw

проворачиваться от руки свободно
Боковой зазор в зубчатых передачах не менее 0.05 мм.
Тепловой зазор в подшипниковых узлах переборного вала не
Радиальное биение зубчатых колес при измерении по дуге
делительной окружности не более 0.03 мм.
Радиальное биение шпинделя не более 0.01 мм.
Осевое биение шпинделя не более 0.01 мм.
Корбка скоростей.cdw

проворачиваться от руки свободно
Боковой зазор в зубчатых передачах не менее 0.05 мм.
Тепловые зазоры в подшипниковых узлах валов не менее 0.3 мм.
Радиальное биение зубчатых колес при измерении по дуге
делительной окружности не более 0.03 мм.
Уровень шума на холостом ходу не должен превышать 60 Дб.
Передняя бабка - Спецификация.spw

Болт М6х20 ГОСТ 7808-70
Болт М8х25 ГОСТ 7808-70
Болт М12х25 ГОСТ 7808-70
Болт М10х22 ГОСТ 7808-70
Винт М6х14 ГОСТ 1491-72
Винт М10х30 ГОСТ 11738-72
Гайка М33х2 ГОСТ 11871-73
Гайка М58х2 ГОСТ 11871-73
Гайка М60х2 ГОСТ 11871-73
Шайба 6 ГОСТ 6402-70
Шайба 10 ГОСТ 6402-70
Шайба 12 ГОСТ 6402-70
Шайба 33 ГОСТ 11872-73
Шайба 58 ГОСТ 11872-73
Шайба 60 ГОСТ 11872-73
Винт М12 х 25 ГОСТ 11738-84
Винт М6 х 20 ГОСТ 17475-80
Черновик.cdw
Электродвигатель 4А112МА6У3
- частота вращения -955 мин
Диапазон частот вращения 22
Структурная сетка кинематической структуры
График частот вращения
Вертикальная плоскость YOZ
Горизонтальная плоскость XOZ
Передняя бабка (Свёртка).cdw

Пояснительная записка.docx
УЧРЕЖДЕНИЕ ОБРАЗОВАНИЯ
«БАРАНОВИЧСКИЙ ГОСУДАРСТВЕННЫЙ УНИВЕРСИТЕТ»
Факультет инженерный й
Кафедра технологии машиностроения н
Дата регистрации работы на кафедре
Отметка о допуске к защите
по дисциплине «Конструирование и расчёт станков»
Тема: «Разработка конструкции привода главного движения токарно-винторезного станка»
и инж. факультет 4 курс гр. ТМ-41
студент (факультет курс группа)
фамилия имя отчество
ученое звание ученая степень должность
на курсовую работу (проект)
ч (фамилия имя отчество)
Дисциплина Конструирование и расчёт станков
(фамилия имя отчество)
Курсовая работа: 58 с. 9 рис. 3 табл. 6 источников.
Разработка конструкции привода главного движения токарно-винторезного станка.
Объектом и предметом исследования является привода главного движения токарно-винторезного станка.
Цель работы: разработать конструкцию привода главного движения токарно-винторезного станка.
В процессе работы разработана конструкция привода главного движения токарно-винторезного станка.
Областями возможного практического применения являются все отрасли тяжелой промышленности.
Автор подтверждает что приведенный в работе расчетно-аналитический материал правильно и объективно отражает состояние исследуемого процесса а все заимствованные из литературных и других источников теоретические методологические и методические положения и концепции сопровождаются ссылками на их авторов.
Анализ конструкций современных металлорежущих станков аналогичных проектируемому .. 4
1 Описание конструкций и системы управления станка-прототипа 4
2 Описание конструкций и системы управления и принцип работы
проектируемого узла . ..10
3 Расчёт и обоснование основных технических характеристик
проектируемого узла 10
4 Описание кинематической схемы проектируемого узла построение
структурной сетки и графика частот 11
5 Расчёт мощности привода и крутящих моментов на валах 18
6 Расчёт передач устройств и механизмов привода станка ..21
6.1 Расчёт зубчатых зацеплений привода .21
6.2 Расчёт клиноременных передач 29
6.3 Предварительный расчёт валов 35
6.4 Уточнённый расчёт вала 36
6.5 Выбор подшипников .43
6.6 Расчёт шлицевого соединения ..44
6.7 Расчёт шпоночное соединение .47
6.8 Выбор электромагнитных муфт 48
7 Расчет шпиндельного узла на жесткость и угол кручения .49
8 Обоснование конструкции шпинделя выбор материала и термической
Описание и расчеты системы смазки шпиндельного узла и привода
главного движения в целом .. .55
Анализ конструкций современных металлорежущих станков аналогичных проектируемому
Токарно-винторезные станки предназначены для выполнения самых разнообразных операций: обработки резцами наружных и внутренних цилиндрических конических и фасонных поверхностей торцевых плоскостей нарезания наружных и внутренних резьб отрезки сверления зенкерования и развёртывания отверстий.
Токарные станки делятся на универсальные и специализированные. Первые предназначены для выполнения самых разнообразных операций перечисленных выше. Специализированные станки предназначены для обработки отдельных деталей гладких и ступенчатых валов больших размеров прокатных валков осей колёсных пар железнодорожного транспорта.
Токарные универсальные станки классифицируются по основным размерам: наибольшему диаметру обрабатываемой заготовки наибольшей длине обрабатываемой заготовки массе точности и целевому назначению.
Производство токарно-винторезных станков развивается по пути совершенствования управления повышения точности надёжности увеличения диапазона скоростей и подач.
1 Описание конструкций и системы управления станка-прототипа
Согласно исходным данным и проекту наибольший диаметр обрабатываемой заготовки над станиной Dmax = 320 мм. Поэтому принимаем за прототип токарно-винторезный станок модели 1А616.
Станок модели 1А616 предназначен для токарной обработки сравнительно небольших деталей из различных материалов как
быстрорежущими так и твердосплавными инструментами в условиях индивидуального и серийного производства. На станке можно нарезать резцом метрические дюймовые модульные и питчевые резьбы. Общий вид станка изображен на рисунке 1.1.Основные технические характеристики станка приведены в таблице 1.1.
Таблица 1.1 – Основные характеристики станка
Наибольший диаметр обрабатываемой заготовки мм:
над верхней частью суппорта
Расстояние между центрами мм
Наибольшая длина обточки мм
Диаметр отверстия в шпинделе мм
Высота от опорной поверхности резца до линии центров мм
Наибольшее расстояние от оси центров до кромки резцедержателя мм
Перемещение на один оборот лимба мм
метрическая шаг в мм
модульная шаг в модулях
дюймовая число ниток на 1
питчевая шаг в питчах
Наибольший ход резьбы в модулях
Мощность электродвигателя главного движения кВт
Число оборотов электродвигателя в минуту
Основные узлы станка (рисунок 1.1): А – гитара сменных колес; Б – передняя бабка с переборным устройством звеном увеличения шага и реверсивным механизмом; В – фартук с механизмом подач; Г – суппорт с быстродействующим четырехпозиционным резцедержателем Д – задняя бабка; Е – станина; Ж – встроенный шкаф с электрооборудованием; 3 – задняя тумба; И – система охлаждения; К – поддон для сбора охлаждающей
Рисунок 1.1 – Общий вид станка модели 1А616
жидкости и стружки; Л – коробка скоростей; М – передняя тумба. Н – коробка подач.
Органы управления (рисунок 1.1): 1 – рукоятка установки типа резьбы или подачи; 2 – рукоятка установки нормального или увеличенного шага; 3 – рукоятка реверсирования перемещения суппорта; 4 – рукоятка управления перебором; 5 – рукоятка переключения множительного механизма коробки подач; 6 – пуговка включения ходового винта или ходового валика; 7 – рукоятка ручного поперечного перемещения суппорта; 8 – рукоятка быстрого отвода суппорта в поперечном направлении; 9 – рукоятка поворота и закрепления четырехпозиционного резцедержателя; 10 – рукоятка ручного перемещения верхней части суппорта; 11 – рукоятка закрепления пиноли задней бабки; 12 – рычаг закрепления корпуса задней бабки на направляющих станины; 13 – маховичок ручного перемещения пиноли задней бабки; 14 и 20 – рукоятки включения выключения и реверсирования главного электродвигателя; 15 – рукоятка включения и выключения маточной гайки продольного ходового винта; 16 – рукоятка включения и выключения поперечной подачи суппорта; 17 – рукоятка включения и выключения продольной подачи суппорта; 18 – кнопка для выключения реечной шестерни; 19 – маховичок ручного продольного перемещения суппорта; 21 и 22 – рукоятки управления коробкой скоростей; 23 – рукоятка установки шага резьбы или величины подачи.
Движения в станке. Движение резания – вращение шпинделя с обрабатываемой деталью. Движение подач — прямолинейное поступательное перемещение суппорта с резцом в продольном и поперечном направлениях от ходового валика. Движение образования винтовой поверхности — прямолинейное поступательное перемещение суппорта с резьбовым резцом в продольном направлении от ходового винта. Вспомогательные движения — ручные установочные перемещения суппорта корпуса и пинолн задней бабки и поворот четырехпозиционного резцедержателя.
Принцип работы. Обрабатываемая деталь устанавливается в центрах или закрепляется в патроне. В резцедержателе суппорта могут быть закреплены четыре резца. Инструменты для обработки отверстий вставляются в конус пиноли задней бабки. Сочетанием вращательного движения детали с поступательным перемещением резца на станке можно обрабатывать цилиндрические конические винтовые и торцовые поверхности.
Конструктивные особенности. В станке модели 1A6I6 применен разделенный привод движения резания.
Приводкой шкив установлен на шпинделе между его опорами однако конструкция задней опоры шпинделя допускает замену клиновых ремней без демонтажа шпинделя.
Торможение привода станка достигается подключением постоянного тока в обмотку статора электродвигателя.
Движение резания. Привод движения резания у станка модели 1A6I6 является разделенным. Он состоит из двух клиноременных передач двенадцатиступенчатой коробки скоростей и переборного устройства.
Приводной вал II (рисунок 1.2) коробки скоростей связан с электродвигателем мощностью 45 кВт клиноременной передачей 135 – 168.
Трёхваловая коробка скоростей имеет три двойных подвижных блока шестерен Б1 Б2 и Б3 и одну одиночную подвижную шестерню 55. Вал III получает вращение от вала II через шестерни 41 – 26. когда блок Б1 как показано на схеме сдвинут влево либо через шестерни 39 – 31 при крайнем правом положении блока Б1 или посредством шестерен 14 – 55. В последнем случае шестерня 55 вводится в зацепление с шестерней 14 а блок Б1 устанавливается в среднее нейтральное положение.
Два двойных блока шестерен Б2 и Б3 позволяют увеличить количество скоростей на выходном валу IV коробки скоростей до двенадцати.
Рисунок 1.2 – Кинематическая схема станка модели 1А616
Нижний ряд чисел оборотов от 11 до 280 в минуту передается шпинделю как показано на схеме через перебор. Вращение от коробки скоростей посредством клиноременной передачи 174 – 174 сообщается полому валу V и далее через шестерки 34 – 68. вал VI и зубчатую передачу 2 – 80 шпинделю VII.
Верхний ряд чисел оборотов шпиндель получает при включенной зубчатой муфте М1 непосредственно от полого вала V.
2 Описание конструкций и системы управления и принцип работы проектируемого узла
Проектируемый привод главного движения выбранного станка прототипа содержит асинхронный двигатель две клиноременных передачи трёхваловую коробку скоростей переборное устройство и шпиндельный узел. Переборное устройство и шпиндельный узел смонтированы в корпусе передней бабки. Переключение оборотов в коробки скоростей осуществляется посредством электромагнитных муфт. Шпиндель получает девять чисел оборотов от вала IV и девять чисел оборотов через шестерни перебора на валах VI и VII. Включение перебора производится отдельными рукоятками одна из которых передвигает шестерни а вторая – зубчатую муфту.
3 Расчёт и обоснование основных технических характеристик проектируемого узла
Проектируемый узел — привод главного движения. Максимальная частота вращения шпинделя минимальная . Эффективная мощность резания . Число ступеней частот вращения .
Определяем диапазон регулирования чисел оборотов шпинделя [1]:
где nmax nmin – соответственно максимальное и минимальное числа оборотов
Определяем знаменатель геометрического ряда чисел оборотов шпинделя [1]:
где Zn – число ступеней частот вращения.
Принимаем стандартное значение .
Из нормали станкостроения Н11-1 для знаменателя геометрического ряда выписываем стандартный ряд частот вращения шпинделя мин–1: n1 = 40 n2 = 50 n3 = 63 n4 = 80 n5 = 100 n6 = 125 n7 = 160 n8 = 200 n9 = 250 n10 = 315 n11 = 400 n12 = 500 n13 = 630 n14 = 800 n15 = 1000 n16 = =1250 n17 = 1600 n18 = 2000.
4 Описание кинематической схемы проектируемого узла построение структурной сетки и графика частот
Принимаем вариант структуры кинематической цепи как в прототипе принятого станка с механизмам перебора. Здесь сложены две кинематические цепи структуры которых [1]:
Группы колес являются общими для двух цепей и поэтому образуют основную структуру. Они сообщают напрямую шпинделю 9 высоких частот вращения и через переборную группу сообщают шпинделю 9 низких частот вращения.
Число скоростей привода
Принимаем число передач в группах .
Характеристика групповых передач согласно принятого варианта структуры кинематической цепи .Структурная формула привода примет вид:
Структурную сетку строим для каждой структуры отдельно первая обеспечивает ряд частот вторая (рисунок 1.3).
Рисунок 1.3 – Структурная сетка кинематической структуры
Структурная сетка строится следующим образом на равном расстоянии друг от друга проводим вертикальные линии число которых должно быть на единицу больше чем число групповых передач. Проводим ряд горизонтальных параллельных прямых с интервалом φ число горизонтальных прямых равно числу ступеней частот вращения шпинделя Zn = 18. На первой левой вертикальной линии разделив ее на две части и на середине каждой части наносим точки O1 и O2 из которой симметрично в соответствии с числом передач в группах по принятой структурной формуле проводим лучи. Расстояние между лучами должно быть равно Xi – характеристике соответствующей группы. Структурная сетка содержит следующие данные о приводе: число групп передач число передач в каждой группе диапазон регулирования групповых передач и всего привода.
При построении графика частот вращения необходимо учитывать следующие указания:
а)во избежание чрезмерно больших диаметров зубчатых колес а также для нормальной и бесшумной их работы необходимо чтобы передаточные отношения были в допустимых пределах — 14 ≤ i ≤ 2.
б)для уменьшения крутящих моментов а следовательно массы деталей и всего привода необходимо сообщать по возможности более высокие частоты вращения промежуточным валом что достигается применением больших передаточных отношений между шпинделем и валом и меньших последующими промежуточными валами.
С учетом вышеуказанного график частот вращения строим в следующей последовательности: на равном расстоянии друг от друга проводим вертикальные линии число которых равно числу валов коробки скоростей. На равном расстоянии друг от друга проводим горизонтальные линии которым присваиваем порядковый номер частот вращения начиная с по . Лучи проведенные между вертикальными линиями обозначают передачу между двумя валами с передаточным отношением i = φm где m - число интервалов перекрытых лучом. Для φ =126 число понижающих интервалов должно быть не более m ≤ 6 а повышающих не более m ≤ 3.
Дальнейшее построение ведем согласно принятого варианта структурной сетки. На рисунке 1.4 изображён график частот вращения.
Рисунок 1.4 – График частот вращения
Опираясь на кинематическую схему привода главного движения станка-аналога и используя структурную сетку построим кинематическую схему проектируемого узла. Так как числа зубьев зубчатых колес пока неизвестны все зубчатые колеса на кинематической схеме изобразим одинакового размера. Кинематическая схемы привода изображена на рисунке 1.5.
Рисунок 1.5 – Кинематическая схема привода главного движения
Определим передаточное отношение в каждой группе передач по формуле [1]:
где - принятый знаменатель ряда чисел оборотов
u - количество интервалов
По найденным передаточным отношениям по таблице 4.3 [1] отыскиваем такое значение суммы чисел зубьев Σz для каждой элементарной двухваловой передачи которое обеспечивает требуемое значение передаточного числа и результаты сведём в таблицу 1.2.
Таблица 1.2 – Результаты вычислений
Поп принятым зубчатым колёсам уточним числа оборотов шпинделя составив для каждого числа оборотов управление кинематического баланса (смотрите график частот вращения). Ошибка полученных чисел оборотов не должна превышать процент ошибки полученного числа оборотов номинального
5 Расчёт мощности привода и крутящих моментов на валах
Определим мощность двигателя привода главного движения для универсальных станков с учётом перегрузки двигателя (стр. 20 [2]):
где – эффективная мощность резания;
– КПД пары подшипников качения;
– КПД цилиндрической зубчатой передачи;
– КПД пары клиноременной передачи;
Мощность требуемая на передачу для токарных станков составляет 3-4% мощности привода [2]:
Принимаем электродвигатель асинхронный двигатель с короткозамкнутым ротором типа 4А100L4У3 мощностью Nэ = 4 кВт nэ = 1430 мин-1.
Для определения крутящих моментов на валах в коробках скоростей приводов главного движения универсальных станков в качестве расчётной частоты вращения шпинделя принимается не nmin а подсчитывается для токарных станков по формуле [2]:
В качестве расчётной частоты принимаем ближайшее значение (смотрите график частот вращения рис 4): nр = n7 = 160 мин–1 расчётная цепь на графике выделена жирной линией.
Определим расчётные крутящие моменты на валах по расчётной цепи [3]:
На валу VII (на шпинделе):
6 Расчёт передач устройств и механизмов привода станка
6.1 Расчёт зубчатых зацеплений привода
Выбор материала и термообработки зубчатых колес
Для получения зубьев сравнительно высокой контактной выносливости с прочной сердцевиной и для уменьшения габаритов зубчатых колес и следовательно всего привода принимаем для изготовления всех колес сталь 40ХН. Принимаем термообработку зубчатого венца нагревом ТВЧ до твердости 48 53 HRCэ. Механические характеристики принимаем по таблице 1П.7 [3]: Т = 750 МПа.
Определяем допускаемые контактные напряжения при расчете на выносливость по формуле [4]:
где Hlimb – базовый предел контактной выносливости поверхностей
зубьев соответствующий базовому числу циклов
sH – коэффициент безопасности (sH = 12);
KHL – коэффициент долговечности учитывающий влияние срока
службы и режима нагружения передачи (KHL = 1).
Среднюю твёрдость H поверхности зубьев находим по формуле:
Предел контактной выносливости зубьев Hlimb определяем по формуле:
Определяем допускаемые напряжения изгиба зубьев по формуле [4]:
где – предел выносливости зубьев при изгибе соответствующий
базовому числу циклов перемены напряжений (по таблице
sF – коэффициент безопасности (sF = 12);
– коэффициент учитывающий влияние двустороннего
приложения нагрузки (для реверсивных передач
– коэффициент долговечности учитывающий влияние
срока службы и режима нагружения (для длительно
работающих передач ).
Определим ориентировочное значение межосевого расстояния a1 между валами II–III по формуле [4]:
где – вспомогательный коэффициент (для стальных прямозубых
U1 – передаточное число ();
– передаваемый крутящий момент Нм;
– коэффициент учитывающий неравномерность распределения
нагрузки по ширине венца;
– коэффициент ширины шестерни относительно межосевого
– допускаемое контактное напряжение Нмм2.
Коэффициент учитывающий неравномерность распределения нагрузки по ширине венца зависит от коэффициента ширины шестерни относительно делительного диаметра :
По графику на рисунке 9.5 [4] находим
Определяем модуль зацепления:
Принимаем стандартное значение модуля
Уточняем межосевое расстояние:
Определяем ширину венца колеса:
Принимаем b2 = 13 мм.
Определяем ширину венца шестерни:
Определим степень точности колёс:
где n = 800 мин–1 – максимальное число оборотов для зацепления Z1 – Z2 (смотрите график чисел оборотов).
По таблице 9.10 [4] принимаем 8-ую степень точности. Основные размеры зубчатых колёс сводим в таблицу 1.3.
Определим ориентировочное значение межосевого расстояния a2 между валами III–IV по формуле (1.7):
Принимаем b2 = 12 мм.
где n = 1250 мин–1 – максимальное число оборотов для зацепления Z7 – Z8 (смотрите график чисел оборотов).
По таблице 9.10 [4] принимаем 7-ую степень точности. Основные размеры зубчатых колёс сводим в таблицу 1.3.
Определим ориентировочное значение межосевого расстояния a3 между валами V–VI. Поскольку валы V и VII соединяются посредством муфты то необходимо чтобы межосевое расстояние между валами V и VI равнялось межосевому расстоянию между валами VI и VII то есть a3 = a4. Поэтому принимаем передаваемый крутящий момент на VII валу.
Определим ориентировочное значение межосевого расстояния a3 = a4 между валами VI–VII и V–VI по формуле (1.7):
Принимаем b2 = 17 мм.
Определим степень точности колёс Z15 – Z16:
где n = 160 мин–1 – максимальное число оборотов для зацепления Z15 – Z16 (смотрите график чисел оборотов).
По таблице 9.10 [4] принимаем 9-ую степень точности.
Определим степень точности колёс Z13 – Z14:
где n = 448 мин–1 – максимальное число оборотов для зацепления Z13 – Z14 (смотрите график чисел оборотов).
Проверочный расчёт зубчатой передачи.
Производим проверочный расчёт по контактным напряжениям наиболее нагруженного зубчатого зацепления Z15 – Z16 по формуле 9.7 [4] – в этом зацеплении наибольший крутящий момент:
где – коэффициент учитывающий форму сопряжённых поверхностей
зубьев в полюсе зацепления;
– коэффициент учитывающий механические свойства материалов
– коэффициент учитывающий суммарную длину контактных линий;
– удельная расчётная окружная сила Нмм.
Коэффициент определяется по формуле [4]:
где – угол наклона зубьев по делительному цилиндру:
где – коэффициент торцевого перекрытия определяется по формуле [4]:
Удельная расчётная окружная сила определяется по формуле [4]:
где – коэффициент учитывающий распределение нагрузки между
зубьями (для прямозубых передач
– определяем по графику на рисунке 9.5 [3] ();
– коэффициент учитывающий динамическую нагрузку
возникающую в зацеплении [4]:
где – удельная окружная динамическая сила Нмм [4]:
где – коэффициент учитывающий влияние вида зубчатой передачи и
модификации профиля головок зубьев (
– коэффициент учитывающий влияние разности шагов зацепления
зубьев шестерни и колеса (;
– окружная скорость мс.
Прочность передачи по контактным напряжениям обеспечена.
Производим проверочный расчёт по напряжениям изгиба по формуле 9.11 [4]:
где – коэффициент учитывающий форму зуба;
– коэффициент учитывающий наклон зуба (для прямозубых передач
– коэффициент учитывающий перекрытие зубьев (=1);
По графику на рисунке 9.6 [4] определим : .
Определим менее прочное звено: Расчёт производим по колесу Z15 так как отношение меньше.
– коэффициент учитывающий динамическую нагрузку возникающую
Прочность зубьев по напряжениям изгиба обеспечена.
Таблица 1.3 – Основные размеры цилиндрических зубчатых колёс
Ширина зубчатого венца b1 мм
Ширина зубчатого венца b2 мм
Дели-тельный d = m z
Выст-упов da = = d + +2m
Впадин df = d – – 25m
6.2 Расчёт клиноременных передач
)Произведем расчет клиноременной передачи от вала электродвигателя к коробке скоростей к валу II привода главного движения. Ранее определили: NЭ = 4 кВт число оборотов электродвигателя nэ = 1430 мин–1.
По таблице 1П.35 [3] выбираем клиновый ремень нормального сечения А ширина ремня b =13 мм ширина ремня по нейтральной линии bр = 11 мм толщина h = 8 мм площадь поперечного сечения А = 81 мм2.
По таблице 1П.36 [3] минимально допустимый расчётный диаметр ведущего (малого) шкива .
При коэффициенте скольжения = 001 002 (расчетное значение = 0015) диаметр dр2 ведущего шкива:
Принимаем стандартное значения dр2 = 125 мм.
Определяем фактическое передаточное число Uф и проверяем его отклонение ΔU от заданного U [3]:
Межосевое расстояние в интервале от до [3]:
где – толщина клинового ремня мм.
Полученное значение округляем до ближайшего стандартного: .
Уточненное межосевое расстояние по формуле [3]:
Таким образом имеем межосевое расстояние
Угол обхвата ремнем меньшего шкива
Определяем допускаемую мощность [P] передаваемую одним клиновым ремнем в условиях эксплуатации рассчитываемой передачи
Скорость ремня V (мс):
В зависимости от полученной величины V линейным интерполированием определяем приведенную мощность [P0] передаваемую одним клиновым ремнем.
Для сечения ремня A при dр1 = 90 мм по табл. 1П.38 [3] имеем:
V = 5 мс [Р0] = 084 кВт;
V = 10 мс [Р0] = 139 кВт.
Тогда при V= 67 мс методом интерполяции:
Коэффициент угла обхвата α1 по таблице 1П.39 [3] на ведущем (меньшем) шкиве (α1 = 170°) Сα = 098.
Для передаточного числа Uф коэффициент Сu по таблице 1П.40 [3] (Uф = =141) Си =105.
Коэффициент длины ремня [3]:
l0 – базовая длина для соответствующего сечения ремня мм.
Для сечения ремня A ( l0 =1700 мм):
Коэффициент режима нагрузки Сp =12.
Тогда допускаемая мощность передаваемая одним клиновым ремнем в условиях эксплуатации рассчитываемой передачи [3]:
Определяем число ремней по формуле [3]:
где Сz – коэффициент числа ремней.
При мощности на ведущем (меньшем) шкиве Р1 = Ртр= 4 кВт задаваясь коэффициентом Сz = 09 имеем:
Примем количество ремней
Определение силу предварительного натяжения F0(Н) одного клинового ремня [3]:
где q — масса 1 м длины ремня; для ремня сечения A q = 0105 кгм.
Определяем консольную нагрузку на вал F(Н) ременной передачи:
)Рассчитаем клиноременную передачу соединяющую IV и V валы. Ранее определили мощность на IV валу:
Исходя из того что максимальная частота вращения вала IV по графику частот вращения равна 2000 мин-1 по таблице 1П. 35[3] выбираем клиновый ремень нормального сечения А ширина ремня b =13 мм ширина ремня по нейтральной линии bр = 11 мм толщина h = 8 мм площадь поперечного сечения А = 81 мм2.
Принимаем диаметры ведущего и ведомого шкивов Dр3 = Dр3 = 160 мм.
Определяем фактическое передаточное число Uф и проверяем его отклонение ΔU от заданного U:
Межосевое расстояние в интервале от до :
Уточненное межосевое расстояние
Принимаем межосевое расстояние
Для сечения ремня A при dр1 = 160 мм по табл. 1П.38 [1] имеем:
V = 15 мс [Р0] = 320 кВт;
V = 20 мс [Р0] = 378 кВт.
Тогда при V= 1675 мс методом интерполяции:
Коэффициент длины ремня:
Тогда допускаемая мощность передаваемая одним клиновым ремнем в условиях эксплуатации рассчитываемой передачи:
Определяем число ремней по формуле:
где Сz — коэффициент числа ремней:
При мощности на ведущем (меньшем) шкиве Р1V = 35 кВт задаваясь коэффициентом Сz = 09 имеем:
Определение силу предварительного натяжения F0(Н) одного клинового ремня:
где q — масса 1 м длины ремня; для ремня сечения A q = 0105 кгм. Тогда:
6.3 Предварительный расчёт валов
Диаметры валов определим из условия прочности на кручение (12. [4])
где T – крутящий момент на валу Нмм;
– допускаемое условное напряжение при кручении Нмм2.
При ориентировочном расчёте валов принимается 10 20 МПа.
Ориентировочный диаметр вала II:
Принимаем диаметр выходного конца вала Принимаем диаметр вала под подшипник d2 = 25 мм под электромагнитными муфтами принимаем диаметр вала dм = 25 мм.
Ориентировочный диаметр вала III:
Принимаем диаметр вала под подшипниками d3 = 25 мм а под зубчатыми колёсами dк = 30 мм.
Ориентировочный диаметр вала IV:
Принимаем диаметр вала под подшипник d4 = 25 мм под электромагнитными муфтами принимаем диаметр вала dм = 25 мм.
Ориентировочный диаметр вала V:
Поскольку вал V полый вал шестерня то принимаем диаметр внутренний dвнутр=45 мм диаметр наружный dп=60 мм.
Ориентировочный диаметр вала VI:
Принимаем диаметр вала под подшипник d6 = 30 мм.
Ориентировочный диаметр вала VII:
Принимаем диаметр вала под подшипник d7 = 35 мм.
6.4 Уточнённый расчёт вала
Рассчитаем вала VI. Крутящий момент на валу TVI = 68 Нм расчётное число оборотов вала по расчётной цепи n = 448 мин–1 когда в зацеплении находятся зубчатые колёса Z13–Z14 с валом VI и Z15–Z16 с валом VII.
Окружное усилие в зацеплении Z15–Z16:
Окружное усилие в зацеплении Z13–Z14:
где α – стандартный угол профиля (α = 20º).
Определим реакции опор в двух плоскостях. Для этого составим расчётную схему вала (рисунок 1.6). Расстояние между опорами и прикладываемыми силами принимаем из чертежа привода: a = 46 мм b = 1275 мм c = 103 мм.
Для вертикальной плоскости ZOX:
ΣМАY = 0; –Fr13·a – Fr15·(a+b) + RBY · (a+b+c) = 0 =>
=> RBY = (Fr13·a + Fr15·(a+b)) ·(a+b+c) =
= (253·46 + 707·(46+1275))(46+1275+103) = 4857 Н.
ΣМBY = 0; Fr15·c + Fr13·(c+b) – RAY · (c+b+a) = 0 =>
=> RAY = (Fr15·c + Fr13·(c+b)) (c+b+a) =
= (707·103 + 253·(103+1275))(103+1275+46) = 4743 Н.
–RAY + Fr13 + Fr15 – RBY = –4743 + 253 + 707 – 4857 = 0 =>
=> реакции найдены правильно.
Для горизонтальной плоскости YOX:
ΣМАX = 0; Ft13·a – Ft15·(a+b) + RBX ·(a+b+c) = 0 =>
=> RBX = (Ft15·(a+b) – Ft13·a)(a+b+c) =
= (1943·(46+1275) – 694·46) (103+1275+46) = 11037 Н.
Рисунок 1.6 – Расчётная схема вала VI
ΣМBX = 0; Ft15·c – Ft13·(c+b) – RAX ·(c+b+a) = 0 =>
=> RAX = (Ft15·c – Ft13·(c+b))(c+b+a)=
= (1943·103 – 694·(103+1275))(103+1275+46) = 1453 Н.
RAX + Ft13 – Ft15 + RBX = 1453 + 694 – 1943 + 11037 = 0 =>
Определяем суммарные реакции опор:
Определяем значения изгибающих моментов в характерных сечениях вала и строим эпюры моментов для двух плоскостей (рисунок 1.6):
Под колесом Z13 – MY13 = –RAY · a = –4743 0046 = –2182 Н·м;
Под колесом Z15 – MY15 = RBY · c = 48570103 = 5003 Н·м.
Под колесом Z13 – MX13 = – RAX · a = – 1453 0046 = – 668 Н·м;
Под колесом Z15 – MX15 = RBX · c = 11037 0103 = 11368 Н·м.
Определяем значения суммарного изгибающего момента:
Строим эпюру крутящего момента (рисунок 1.6).
Определяем значения эквивалентных изгибающих моментов в этих же сечениях:
Самое нагруженное сечение под колесом Z15.
Определяем диаметр вала в самом нагруженном сечении Z15:
Ранее принятое значение d = 32 мм. Это больше чем требуется по расчёту. Прочность по напряжениям изгиба обеспечена.
Проверка вала на выносливость является проверкой на усталостную прочность. Эта проверка состоит в определении запасов прочности в опасных сечениях проверяемого вала.
Для наиболее опасного сечения вала (сечение) определяем коэффициент запаса усталостной прочности S и сравниваем его с допускаемым значением [S] принимаемым обычно 15 25 [3].
где – коэффициент запаса прочности по нормальным напряжениям [3]:
где – предел выносливости стали при симметричном цикле изгиба МПа;
(по таблице 9.1 [3] );
– суммарный коэффициент учитывающий для данного сечения вала
влияние всех факторов на сопротивление усталости при изгибе;
– амплитуда напряжений цикла МПа;
– коэффициент характеризующий чувствительность материала к
асимметрии цикла напряжений;
– среднее напряжение цикла МПа ().
где – эффективный коэффициент концентрации напряжений (по таблице
– коэффициент влияния абсолютных размеров поперечного сечения
(по таблице 9.6 [3] )
– коэффициент влияние шероховатости поверхности ( по таблице 9.7
– коэффициент влияние упрочнения (по таблице 9.8 [3] ).
Амплитуду напряжений цикла определяем по формуле [3]:
где M – результирующий изгибающий момент Нмм;
W – осевой момент сопротивления сечения вала мм3.
где d – диаметр вала мм;
– для шлицев лёгкой серии .
Коэффициент характеризующий чувствительность материала к асимметрии цикла напряжений определяем по формуле:
где – предел прочности МПа.
где – предел выносливости стали при симметричном цикле изгиба МПа;
– амплитуда напряжений цикла МПа
асимметрии цикла напряжений
– среднее напряжение цикла МПа ();
(по таблице 9.6 [3] );
WK – полярный момент сопротивления сечения вала мм3.
Сопротивление усталости вала в опасном сечении обеспечивается.
6.5 Выбор подшипников
При расчёте вала определили реакции опор RA = 496 Н RB = 1206 Н. Выбор подшипников произведём для наиболее нагруженной опоры B.
Пригодность предварительно выбранного подшипника определяется сопоставлением расчётной динамической грузоподъёмности Cрасч с базовой C [3]:
Для радиальных подшипников условие имеет вид [3]:
где – расчётная радиальная динамическая грузоподъёмность Н;
– радиальная эквивалентная динамическая нагрузка Н;
– показатель степени ( для шариковых подшипников );
– частота вращения одного из колец подшипника мин–1
– требуемая долговечность (ресурс) подшипника ч ();
– коэффициент режима нагрузки (по таблице 10.1 [2] );
– коэффициент характеризующий совместное влияние на ресурс
подшипника качества металла колец тел качения и условий
эксплуатации (по таблице 10.2 [2] );
– базовая радиальная динамическая грузоподъёмность подшипника
Н (по ГОСТ 8338–75 .
Радиальная эквивалентная динамическая нагрузка определяется по формуле [3]:
где X – коэффициент радиальной нагрузки (по таблице 10.3 [2] X = 1);
V – коэффициент вращения зависящий от того какое кольцо
вращается (при вращение внутреннего кольца V =1);
kб – коэффициент безопасности учитывающий характер нагрузки
kТ – температурный коэффициент (kТ = 1).
По принятому диаметру вала под подшипник d = 30 мм устанавливаем подшипник радиальный лёгкой серии условное обозначение 206 ГОСТ 8338–75 с динамической грузоподъёмностью Cr = 195 кН.
Для остальных валов принимаем шариковые радиальные однорядные подшипники по ГОСТ 8338–75 по принятому диаметру вала под подшипник.
6.6 Расчёт шлицевого соединения
Произведём проверочный расчёт подвижного шлицевого соединения на валу VI. Номинальные размеры шлицев Z x d x D = 8 x 32 x 36 мм.
Материал приводного вала сталь 45 термообработка шлицевого отверстия – улучшение HB 220 280 смазка средняя срок службы Lh = 10 000 ч частота вращения вала по расчётной схеме n = 448 мин–1.
По таблице 5.5 [4] определяем удельный суммарный статический момент: SF = 163 мм3мм и средний диаметр:
Определим среднее давление по формуле 5.8 [4]:
где – крутящий момент на валу VI Нмм;
– удельный суммарный статический момент мм3мм;
l – рабочая длина соединения мм (l = 86 мм).
Определим допускаемое среднее давление на смятие по формуле 5.10 [4]:
где – предел текучести материала шлицев меньшей твёрдости;
– коэффициент безопасности ();
– общий коэффициент концентрации нагрузки при расчёте на смятие;
– коэффициент долговечности.
Принимаем предел текучести материала сталь 45 коэффициент безопасности S = 13.
где – коэффициент неравномерности распределения нагрузки между
– коэффициент продольной концентрации нагрузки;
– коэффициент учитывающий концентрацию нагрузки в связи с
погрешностью изготовления ().
Коэффициент определим в зависимости от параметра по таблице 5.7 [4]:
Коэффициент определим по формуле:
где – коэффициент концентрации нагрузки от закручивания вала (по
– коэффициент концентрации давления от относительного смещения
нагрузки (по рисунку 5.12 [2] .
где – коэффициент переменности нагрузки ();
– коэффициент числа циклов.
Соединение удовлетворяет условию прочности на смятие так как
Определим допускаемое среднее давление на износ по формуле 5.11 [4]:
где – допускаемое условие давление при базовом числе циклов и
постоянном режиме работы (по таблице 5.6 [3]
– общий коэффициент концентрации нагрузки при расчёте на износ;
– коэффициент условий работы.
где – коэффициент учитывающий условия смазки соединения (
– коэффициент учитывающий условия осевого закрепления ступицы
на валу и её перемещений под нагрузкой ().
Соединение удовлетворяет условию прочности на смятие так как
6.7 Расчёт шпоночное соединение
Рассмотрим шпоночное соединение вала VI . Длина ступицы шкива материал шпонки – сталь 45. Крутящий момент на валу – Т2 = 2528 Н·м.
Полная длина шпонки:
l = lст – (5 10) = 60 – (5 10) = 50 55 мм.
Принимаем стандартное значение l = 56 мм.
Расчётная длина шпонки для исполнения 1 (оба торца шпонки скругленные)
lр = l – b = 56 – 12 = 44 мм.
Тогда расчётные напряжения смятия при вращающем:
где T2 – крутящий момент на быстроходном валу Н·м;
d – диаметр вала мм;
h – высота шпонки мм;
t1 – глубина паза вала мм;
lр – рабочая длина шпонки мм.
Что меньше [см] = 100 МПа. Условие прочности на смятие выполняется.
6.8 Выбор электромагнитных муфт
Номинальный передаваемый момент муфты Mн должен быть больше максимального приведенного к ней статического момента нагрузки T имеющего место после включения муфты страница 76 [1]:
где k – коэффициент запаса (k = 11 16).
Крутящий момент на валу II TII = 3616 Нм тогда: По таблице 3.25 [1] принимаем на вал II бесконтактные электромагнитные муфты 07 габарита для которой Mн = 63 Нм с гладким посадочным отверстием d = 25 мм. Обозначение муфты: ЭТМ042-1А.
Крутящий момент на валу IV TIV = 2681 Нм тогда: По таблице 3.25 [1] принимаем на вал II бесконтактные электромагнитные муфты 07 габарита для которой Mн = 63 Нм с гладким посадочным отверстием d = 25 мм. Обозначение муфты: ЭТМ042-1А.
7 Расчет шпиндельного узла на жесткость и угол кручения
При расчете определяют упругое перемещение шпинделя в сечении его переднего конца для которого производится стандартная проверка шпиндельного узла на жёсткость. Это перемещение принимают в качестве упругого перемещения переднего конца шпинделя.
В перемещении учитывают только деформации тела шпинделя и его опор.
Упругое перемещение переднего конца шпинделя определим по формуле 6.2 [1]
где – сила резания Н;
– длина консольной части шпинделя м;
– модуль упругости материала шпинделя Па;
– среднее значение момента инерции сечения консоли м4;
– среднее значение момента инерции сечения шпинделя в пролете
– длина шпинделя между опорами м;
– коэффициент защемления;
– радиальная жесткость передней опоры ;
– радиальная жесткость задней опоры ;
– сила действующая на шпиндель со стороны привода Н;
– расстояние от точки приложения силы до передней опоры м.
Исходя из формулы эффективной мощности резания
определим силу резания:
где – скорость резания.
где – максимальный диаметр заготовки;
– число оборотов шпинделя по расчётной схеме.
Составляющие силы резания радиальную Py и осевую Px определим пользуясь приближёнными соотношениями ( страница 229 [5]):
Модуль упругости материала шпинделя сталь 40Х
Коэффициент защемления по таблице 6.22 [1] . Принимаем
Из компоновочной схемы находим расстояния a b = 975 мм; l = 487 мм.
Радиальные жёсткости и определяем по рисунку 6.15 [1]. .
Сила действующая на шпиндель со стороны приводы равна:
Среднее значение момента инерции сечения консоли :
где – средний диаметр сечения консоли.
где – диаметры и длины участков шпинделя мм;
– длина консольной части шпинделя мм.
Среднее значение момента инерции сечения шпинделя в пролете между опорами :
где – средний диаметр сечения шпинделя в пролёте между опорами.
– длина шпинделя между опорами мм.
На рисунке1.7 изображена расчётная схема шпинделя.
Перемещение переднего конца шпинделя под действием силы РZ:
Перемещение переднего конца шпинделя под действием силы РY.
Допускаемый прогиб конца шпинделя [1]
Угол поворота (рад) в передней опоре [1]
Рисунок 1.7 – Расчётная схема шпинделя
Горизонтальная плоскость
Вертикальная плоскость
Суммарный угол поворота в одну плоскость:
Допускаемый угол поворота шпинделя в одну плоскость [6]
Значит шпиндель по жёсткости соответствует заданным режимам работы.
8 Обоснование конструкции шпинделя выбор материала и термической обработки
Шпиндельные узлы с двухрядным роликовым подшипником типа 182000 и упорно-радиальным шариковым подшипником типа 178800 применяют в средних и тяжелых токарных фрезерных фрезерно-расточных и шлифовальных станках. В передней опоре первый подшипник предназначен для восприятия радиальной нагрузки второй - для осевой [1].Типовая компоновка шпиндельного узла представлена на рисунке 1.8.
Рисунок 1.8 – Типовая компоновка шпиндельного узла
Конец шпинделя принимаем по ГОС 12593-93 условное обозначение: Конец шпинделя 4 ГОС 12593-93. В передней опоры шпинделя установлен один роликовый радиальный двухрядный подшипник с короткими цилиндрическими роликами серии диаметров 1 серии ширин 3 с размерами d = 65 мм D = 100 мм B = 26 мм условное обозначение подшипника: Подшипник 3182113 ГОСТ 7643-75; и один упорно-радиальный шариковый двухрядный подшипник с углом контакта 60º с размерами d = 65 мм H = 44 мм условное обозначение подшипника: Подшипник 178813 ГОСТ 20821-75. В задней опоре шпинделя установлен один роликовый радиальный двухрядный подшипник с короткими цилиндрическими роликами серии диаметров 1 серии ширин 3 с размерами d = 35 мм D = 62 мм B = 20 мм условное обозначение подшипника: Подшипник 3182107 ГОСТ 7643-75. Роликовые подшипники установлены с предварительным натягом. Радиальный зазор в роликовом подшипнике передней опоры регулируется с помощью гайки которая через втулку (см. сборочный чертёж) надвигает на коническую шейку шпинделя с конусностью 1:12 внутренне кольцо подшипника. В результате деформации внутреннего кольца происходит разжим его и тем самым устанавливается необходимый радиальный зазор шпинделя в микронах.
Для изготовления шпинделя принимаем легированную сталь 40Х с закалкой ответственных поверхностей до твёрдости 48 56 HRC с использованием индукционного нагрева [1].
Описание и расчеты системы смазки шпиндельного узла и привода главного движения в целом
Жидкие смазочные масла хорошо отводят теплоту от шпиндельных опор уносят из подшипников продукты изнашивания делают ненужным периодический надзор за подшипниками. При выборе вязкости масла учитывают частоту вращения шпинделя температуру шпиндельного узла и ее влияние на вязкость масла.
Систему смазывания жидким материалом выбирают исходя из требуемой быстроходности шпинделя с учетом его положения (горизонтальное вертикальное или наклонное) условий подвода масла конструкции уплотнений.
Так как параметр быстроходности равен
– наружный диаметр подшипника мм;
– диаметр отверстия подшипника мм;
– максимальная частота вращения шпинделя ().
Поскольку то по таблице 6.19 [1] выбираем циркуляционное смазывание без охлаждения масла для передней опоры и задней опор.
Циркуляционное смазывание осуществляется автономной системой предназначенной только для шпиндельного узла или системой общей для него и коробки скоростей. Масло подается в шпиндельную опору. Для улучшения циркуляции масла предусматривают отверстия в наружном кольце подшипника в роликах. Чтобы обеспечить надежное попадание смазочного материала на рабочие поверхности подшипников масло подводят в зону всасывания то есть к малому диаметру дорожек качения радиально-упорных шариковых и роликовых подшипников которым присущ насосный эффект. Предусматривают свободный слив масла из опоры благодаря чему не допускают его застоя и снижают температуру опоры. В резервуаре или с помощью специального холодильника масло охлаждается. С повышением частоты вращения шпинделя разница между количеством выделяющейся теплоты и отводимой от подшипникового узла увеличивается а при высокой частоте вращения через подшипники невозможно прокачать нужный объем масла Например двухрядные роликоподшипники создают большое гидравлическое сопротивление и перемешивание слишком большого объема масла приводит не к снижению а к повышению температуры опоры.
Прокачивание через шпиндельную опору нескольких тысяч кубических сантиметров масла в минуту не только позволяет надежное смазывание но и обеспечивает отвод теплоты от опоры то есть создает режим "охлаждающего" смазывания. Расход масла при таком смазывании зависит от типа подшипника частоты его вращения и вязкости масла. Дня конических роликоподшипников q= (5 10) d. Для радиально-упорных подшипников при d 50 мм Q = 500.. 1500 см3мин при d > 120 мм Q > 2500 см3мин. Для смазывания упорно-радиальных подшипников при d = 30 80 мм Q = 100 1000 см3мин при d = 80 180 мм Q = 500 5000 см3мин при d> 180 мм Q = 2000 10 000 см3мин [1].
Подвод масла к электромагнитным муфтам осуществляем внутренним способом через устройство осевого типа центральное отверстие просверленное в валу на котором находится муфта. Подшипники на которых установлены зубчатые колёса связанные с муфтами смазываются струёй масла с подачей через радиальное отверстие просверленное в валу. Муфты смазываем маслом И–20А. На рисунке 1.9 изображён способ внутреннего подвода масла к электромагнитным муфтам через устройство осевого типа.
Рисунок 1.9 – Способ внутреннего подвода масла к электромагнитным муфтам через устройство осевого типа.
Кочергин А.И. Конструированиек и расчет мсталлорежущих станков и станочных комплексов. Курсовое проектирование: Учеб. пособие для вузов. – Мн.: Высш. шк. 1991. - 382 с.: ил.
Металлорежущие станки: метод. указания для студентов В.И. Глубокий. – Минск 1983 г.
Санюкевич Ф. М. Детали машин. Курсовое проектирование: Учебное пособие – 2-е изд. испр. и доп. – Брест: БГТУ 2004. – 488 с.
Детали машин в примерах и задачах. Н.Н. Ничипорчик; под ред. Н.Н. Ничипорчик – «Вышэйшая школа» 1978 г.
Основы теории резания металлов. В.Ф. Бобров; под ред. В. Ф. Бобров – «Машиностроение» 1975 г.
Ачеркан Н.С. «Металлорежущие станки». Том 2 «Машиностроение» 1965г.
Рисунок 1.4 - График частот вращения.cdw

Рисунок 1.5 - Кинематическая схема привода.cdw

Рисунок 1.7 - Расчётная схема шпинделя.cdw

Рисунок 1.6 - Расчётная схема вала VI.cdw

Рисунок 1.3 - Структурная сетка кинематической группы.cdw

Рекомендуемые чертежи
- 10.02.2022
- 29.05.2022