Разработка привода главного движения станка ИР500ПМФ4




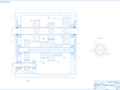
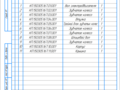
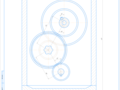
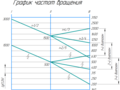
- Добавлен: 04.11.2022
- Размер: 481 KB
- Закачек: 1
Описание
Курсовой проект - Разработка привода главного движения станка ИР500ПМФ4
Состав проекта
![]() |
![]() |
![]() ![]() ![]() |
![]() ![]() ![]() ![]() |
![]() ![]() ![]() ![]() |
![]() ![]() ![]() ![]() |
![]() ![]() ![]() ![]() |
![]() ![]() ![]() |
Дополнительная информация
ПОЯСНИТЕЛЬНАЯ ЗАПИСКА.docx
НАЦИОНАЛЬНЫЙ ИССЛЕДОВАТЕЛЬСКИЙ ЯДЕРНЫЙ УНИВЕРСИТЕТ
Факультет заочного обучения
Кафедра «Технология машиностроения»
ПОЯСНИТЕЛЬНАЯ ЗАПИСКА К КУРСОВОМУ ПРОЕКТУ
КП.150305-167.00.000 ПЗ
По дисциплинеМЕТАЛЛОРЕЖУЩИЕ СТАНКИ
Тема: Разработка привода главного движения станка ИР500ПМФ4
РазработчикЖуравлев А.Н. студент группыКТОз-41
Руководитель проектаВласов Станислав Николаевич
Отметка о допуске проекта к защитеДата
Проект защищен с оценкойДата
Шпиндель корпус операция инструмент режимы резания подача станок частота.
На базе горизонтального обрабатывающего центра ИР500ПМФ4 спроектирован привод главного движения выполнен кинематический расчет.
ОБЩИЕ СВЕДЕНИЯ О МЕТАЛЛОРЕЖУЩИХ СТАНКАХ6
НАЗНАЧЕНИЕ И ПРИНЦИП РАБОТЫ СТАНКА8
ОСНОВНЫЕ ТЕХНИЧЕСКИЕ ХАРАКТЕРИСТИКИ СТАНКА9
ОСНОВНЫЕ УЗЛЫ СТАНКА10
КИНЕМАТИЧЕСКИЙ АНАЛИЗ СТАНКА12
1 ОПРЕДЕЛЕНИЕ ЧИСЛА ЗУБЬЕВ КОЛЁС ЗУБЧАТЫХ ПЕРЕДАЧ16
2 ОПРЕДЕЛЕНИЕ МОЩНОСТЕЙ И КРУТЯЩИХ МОМЕНТОВ НА ВАЛАХ19
3 ПРОЕКТНЫЙ РАСЧЁТ ДИАМЕТРОВ ВАЛОВ21
4 ПРОЕКТНЫЙ РАСЧЁТ ЗУБЧАТЫХ ПЕРЕДАЧ22
4.1 РАСЧЕТ ЦИЛИНДРИЧЕСКОЙ ЗУБЧАТОЙ ПЕРЕДАЧИ 23
4.2 РАСЧЕТ ЦИЛИНДРИЧЕСКОЙ ЗУБЧАТОЙ ПЕРЕДАЧИ 25
4.3 РАСЧЕТ ЦИЛИНДРИЧЕСКОЙ ЗУБЧАТОЙ ПЕРЕДАЧИ 27
4.4 РАСЧЕТ ЦИЛИНДРИЧЕСКОЙ ЗУБЧАТОЙ ПЕРЕДАЧИ 28
СПИСОК ИСПОЛЬЗУЕМЫХ ИСТОЧНИКОВ30
Автоматизация технологического процесса механической обработки имеет место в условиях крупносерийною и массового производства где применяются станки-автоматы заменившие универсальные и специализированные станки. Автоматы управляются при помощи механических устройств которые в условиях мелкосерийного и единичного производства нерентабельны ввиду их сложной переналадки. Возникла необходимость в средствах автоматизации которые позволяли бы производить частую переналадку станков при обработке деталей малых партий или отдельных деталей. Эта задача решается применением станков с электронными системами управления которые называют станками с программным управлением.
Основным преимуществом таких станков является возможность их переналадки при переходе на обработку новой детали в весьма короткое время при централизованной подготовке технологических программ. Программа позволяет проектировать системы дистанционного управления станками и создавать при этом легко переналаживаемые автоматические линии и участки комплексной обработки деталей. Если программа автоматического действия станка не имеет непосредственной связи с его структурой кинематикой и конструкцией или выражена в абстрактной форме при помощи кода (под которым понимается система символов обусловливающая определенные действия выраженные в виде цифр букв их комбинаций и т. д.) то такая система является принципиально отличной от применяемой на станках-автоматах и обладает большими потенциальными возможностями и эксплуатационными удобствами.
В настоящее время наблюдается тенденция на повышение уровня автоматизации производственных процессов. В производство все более внедряется автоматизированное оборудование работающее без непосредственного участия человека или значительно облегчающее труд рабочего. Это позволяет значительно сократить трудоемкость производственного процесса снизить себестоимость выпускаемой продукции увеличить производительность труда. Поэтому главная задача инженеров — разработка автоматизированного оборудования расчет его основных узлов и агрегатов выявление наиболее оптимальных технических решений и внедрение их в производство.
В данном курсовом проекте выбран электродвигатель определены передаточные отношения каждой ступени коробки а также мощности крутящие моменты частоты вращения каждого вала. Рассчитаны модули для каждой передачи. Определены основные размеры зубчатых колес.
Целью данной работы является изменение диапазона регулирования привода главного движения станка ИР500ПМФ4.
ОБЩИЕ СВЕДЕНИЯ О МЕТАЛЛОРЕЖУЩИХ СТАНКАХ
Металлорежущие станки обеспечивают изготовление деталей разнообразной формы с высокой точностью размеров и заданной шероховатостью поверхности. Металлорежущие станки классифицируются по следующим признакам.
По степени специализации: универсальные применяемые для обработки деталей широкой номенклатуры; специализированные предназначенные для обработки однотипных деталей сходных по конфигурации но имеющие различные размеры; специальные применяемые для обработки деталей одного типоразмера. Специализированные и специальные станки используют в крупносерийном и массовом производстве а универсальные — в единичном и мелкосерийном производстве.
По точности: нормальной точности — класс Н; повышенной точности — класс П; высокой точности — класс В; особо высокой точности — класс А; прецизионные — класс С.
По массе: легкие — до 1 т средние — до 10 т тяжелые — свыше 10 т. Тяжелые станки в свою очередь делятся на крупные (от 10 до 30 т) тяжелые (от 30 до 100 т) и особо тяжелые (более 100 т).
По виду выполняемых работ и применяемых режущих инструментов все выпускаемые станки согласно классификации делят на девять групп каждая группа разделена на десять типов станков.
В моделях станков с программным управлением для обозначения степени автоматизации добавляется буква «Ф» с цифрой: Ф1 — станки с цифровой индикацией и преднабором координат; Ф2 — станки с позиционными и прямоугольными системами; ФЗ — станки с контурными системами; Ф4 — станки с универсальной системой для позиционной и контурной обработки. Для станков с цикловыми системами программного управления введен индекс Ц.
НАЗНАЧЕНИЕ И ПРИНЦИП РАБОТЫ СТАНКА
Металлорежущие станки предназначенные для выполнения большого числа различных технологических операций без переустановки обрабатываемых деталей имеющих устройство автоматической смены инструмента и оснащенных системами ЧПУ называют многоцелевыми.
Корпусные и плоские детали можно обрабатывать с одной установки с нескольких сторон (до пяти).
Типовыми технологическими операциями являются растачивание сверление зенкерование развертывание цекование нарезание резьбы метчиками фрезерование плоскостей контуров и фасонных поверхностей. При высокой концентрации выполняемых технологических операций для многоцелевых станков характерна высокая точность обработки (6-7 квалитет).
Многоцелевые станки снабжают необходимым режущим инструментом расположенным в специальном инструментальном магазине. В соответствии с заданной управляющей программой используется любой инструмент из магазина требуемый для обработки соответствующей поверхности.
При горизонтальной компоновке ось вращения шпинделя расположена горизонтально и такие станки чаще всего используются для обработки сложных корпусных деталей. Шпиндельная бабка перемещается по вертикальным направляющим стойки которая может быть подвижной или неподвижной.
ОСНОВНЫЕ ТЕХНИЧЕСКИЕ ХАРАКТЕРИСТИКИ СТАНКА
Таблица 3.1 – Основные технические характеристики станка.
Технические характеристики
Размеры рабочей поверхности стола мм
Наибольшая масса обрабатываемого изделия кг
Конус для крепления инструмента в шпинделе
Частота вращения шпинделя мин-1
Мощность электродвигателя привода вращения шпинделя кВт
Емкость инструментального магазина шт.
Габаритные размеры станка (Д х Ш х В) мм
Масса станка (без электрооборудования гидростанции устройств ЧПУ и смены столов) кг
ОСНОВНЫЕ УЗЛЫ СТАНКА
На рисунке 4.1 представлены основные узлы станка:
Устройство автоматической смены столов-спутников. Автоматическая смена плит-спутников обеспечивает работу станков в автоматическом режиме исключая из технологического цикла обработки время на установку и снятие деталей;
Шпиндельная бабка. Лобовая бесконсольная шпиндельная бабка расположена внутри портальной стойки. Жесткий шпиндель с диаметром под передний подшипник 105 мм и конусом № 50 изготовлен из цементированной стали с высокой поверхностной твердостью (HRC 62). Шпиндель монтируется в отдельном корпусе на прецизионных роликовых и упорно-радиальном шариковом подшипниках что обеспечивает оптимальную точность жесткость и виброустойчивость;
Стол. Перемещается по отдельной станине которая крепится на общем основании (станине станка). Поворотный стол имеет 72 позиции через 5°. Установка стола происходит в автоматическом режиме;
Манипулятор (автооператор) и;
Инструментальный магазин. Расположены вне рабочей зоны. Вращающейся инструментальный магазина барабанного типа с кодированными гнездами емкостью на 30 инструментов. Выбор инструмента в любой последовательности с последующей гидромеханической фиксацией инструментального магазина осуществляется во время механической обработки;
Станина. Все узлы станка смонтированы на жесткой Т-образной станине которая является общим основанием.
Все базовые детали имеют оребренную конструкцию и обеспечивают максимальную жесткость и виброустойчивость при высокопроизводительной обработке гарантируют длительное сохранение точности.
Рисунок 4.1. – Основные узлы станка.
КИНЕМАТИЧЕСКИЙ АНАЛИЗ СТАНКА
На рисунке 5.1 представлена заводская кинематическая схема станка. Впоследствии мы пересчитаем зубчатые передачи главного привода с учетом необходимых частот вращения шпинделя при определенных режимах резания.
Главное движение шпиндель III получал от регулируемого электродвигателя постоянного тока M1 (N = 14 кВт nном = 1000 мин-1; nmax = 3000 мин-1) через двухступенчатую коробку скоростей. Изменение частоты вращения шпинделя производится в пределах 1000 – 3150 мин-1 при постоянной мощности и 21 – 1000 мин-1 при постоянном моменте. С блока зубчатых колес z= 33 z = 66 крутящий момент на шпиндель передавался через зубчатую муфту таким образом шпиндель полностью разгружен от изгибающих сил возникающих от приводных колес.
Заводская кинематическая схема коробки скоростей представлена на рис. 5.2.
Расширяем диапазон регулирования до ближайших стандартных значений. Принимаем:
Выбираем электродвигатель постоянного тока.
Принимаем двигатель постоянного тока типа 2ПН160М: .
Диапазон регулирования двигателя равен:
Рисунок 5.1. – Кинематическая схема станка модели ИР500ПМФ4.
Рисунок. 5.2 – Кинематическая схема коробки скоростей.
Диапазон регулирования частот вращения на шпинделе равен:
Число ступеней механического регулирования:
Если округлить число в меньшую сторону то получим небольшой разрыв в средней части диапазона регулирования а именно там у нас происходит наибольшее число операций резания. Поэтому округляем значение в большую сторону для получения гарантированного перекрытия скоростей.
Получившаяся кинематическая схема коробки скоростей изображена на рисунке 5.3.
Рисунок. 5.3 – Разработанная кинематическая схема коробки скоростей.
1 ОПРЕДЕЛЕНИЕ ЧИСЛА ЗУБЬЕВ КОЛЁС ЗУБЧАТЫХ ПЕРЕДАЧ
Путем долгого и мучительного поиска с перебором различных вариантов знаменателя ряда и передаточных соотношений был найден оптимальный вариант который удовлетворяет нашим требованиям (Рисунок 5.4).
Число зубьев колес группы передач обусловлено межосевым расстоянием А которое должно быть одинаковым для всех передач одной группы и передаточным отношением выраженным в форме:
Модули зацепления прямозубых передач в пределах одной группы чаще всего одинаковы.
Следовательно сумма зубьев:
Исходя из условий компактности передач величину и наименьшее число зубьев в приводах главного движения ограничивают в пределах
Рисунок. 5.4 – График частот вращения.
Наименьшее общее кратное для всех сумм – 21.
Находим число зубьев:
Так как количество зубьев слишком мало – умножаем полученные результаты на 5 и получаем их true значение:
Условия (5.1) и (5.2) выполняются то есть число зубьев рассчитано верно. Т.к. в каждом диапазоне регулирование бесступенчатое и есть перекрытие диапазонов то по вычисленным значениям определяем действительное значение чисел оборотов в крайних точках.
2 ОПРЕДЕЛЕНИЕ МОЩНОСТЕЙ И ПЕРЕДАВАЕМЫХ КРУТЯЩИХ МОМЕНТОВ НА ВАЛАХ
Определим общий коэффициент полезного действия (КПД) привода:
где и – коэффициенты полезного действия закрытой передачи и пары подшипников качения соответственно. Степени равные соответственно числу пар подшипников и зубчатых передач. Их количество определяем по кинематической схеме.
Требуемая мощность двигателя:
Выбранный электродвигатель подходит по данному параметру. Двигатель постоянного тока типа 2ПН160М:
Максимальная мощность на валах коробки скоростей:
Максимальные крутящие моменты на валах расчетной кинематической цепи:
Результаты расчета сведены в таблицу 5.1.
Таблица 5.1 – Максимальные мощности и крутящие моменты на валах.
Частота вращения n обмин
Передаваемая мощность Р кВт
Передаваемый крутящий момент Т Н·м
3 ПРОЕКТНЫЙ РАСЧЁТ ДИАМЕТРОВ ВАЛОВ
В качестве материала валов выбираем термически обработанную сталь 45. Твердость стали НВ = 235 262. Проектный расчет валов выполняется по напряжениям кручения.
Определяем минимально допустимые диаметры для сплошных валов.
где – допускаемое напряжение кручения.
Для расчёта принимаем равным 20 МПа.
Минимально допустимая площадь поперечного сечения для полого шпиндельного вала:
Конструктивно принимаем внутренний диаметр шпиндельного вала равным 16 мм внешний – 40 мм ().
Рассчитанные значение диаметров округляем до ближайшего большего значения в соответствии с ГОСТ под подшипники и принимаем эти значения за диаметры шеек валов под подшипники т.о.
В соответствии с этими диаметрами выбираем подшипники для валов:
I: 205 (d=25 мм; D=52 мм; B=15 мм);
II: 206 (d=30 мм; D=62 мм; B=16 мм);
III: 208 (d=40 мм; D=80 мм; B=18 мм).
4 ПРОЕКТНЫЙ РАСЧЁТ ЗУБЧАТЫХ ПЕРЕДАЧ
Для равномерного изнашивания зубьев и лучшей их прирабатываемости твердость шестерни НВ1 назначаем больше твердости колеса НВ2.
Выбираем для шестерни НВ 269 302 для колеса НВ 235 262.
Определяем среднюю твердость зубьев шестерни и колеса:
Определим допускаемые контактные напряжения для зубьев шестерни и колеса .
Так как то прямозубая передача рассчитывается на прочность по меньшему значению т.е. по значению колеса.
Определение допускаемых напряжений изгиба для зубьев шестерни и колеса :
Т.к. передача реверсивная:
4.1 РАСЧЕТ ЦИЛИНДРИЧЕСКОЙ ЗУБЧАТОЙ ПЕРЕДАЧИ
Определим ориентировочное межосевое расстояние мм:
где – вспомогательный коэффициент. Для прямозубых передач Ка=495;
– коэффициент ширины венца колеса равный 028 036;
– передаточное отношение передачи;
– вращающий момент на тихоходном валу Нм;
– допускаемое контактное напряжение колеса с менее прочным зубом ;
– коэффициент неравномерности нагрузки по длине зуба. Для прирабатывающихся зубьев = 1.
Принимаем по стандартному ряду = 100 мм.
Определяем модуль зацепления:
где – вспомогательный коэффициент равный 68;
– делительный диаметр колеса;
– ширина венца колеса;
– допускаемое напряжение изгиба материала колеса с менее прочным зубом Нмм2.
Делительный диаметр колеса мм:
Ширина венца колеса мм:
По стандартному ряду принимаем .
Таблица 5.2 – Основные геометрические параметры передачи в мм.
Диаметр вершин зубьев
Диаметр впадин зубьев
4.2 РАСЧЕТ ЦИЛИНДРИЧЕСКОЙ ЗУБЧАТОЙ ПЕРЕДАЧИ
Принимаем по стандартному ряду = 125 мм.
– делительный диаметр колеса мм;
– ширина венца колеса мм;
Щирина венца колеса мм:
Таблица 5.3 – Основные геометрические параметры передачи в мм.
4.3 РАСЧЕТ ЦИЛИНДРИЧЕСКОЙ ЗУБЧАТОЙ ПЕРЕДАЧИ
Т.к. модуль у зубчатых колес передвижного блока рекомендуется брать одинаковым а его и межосевое расстояние для этой передачи определили в п.5.4.2 то здесь определим только делительный диаметр колеса мм равный:
Таблица 5.4 – Основные геометрические параметры передачи в мм.
4.4 РАСЧЕТ ЦИЛИНДРИЧЕСКОЙ ЗУБЧАТОЙ ПЕРЕДАЧИ
Таблица 5.5 – Основные геометрические параметры передачи в мм.
В процессе выполнения курсового проекта по дисциплине «Металлорежущие станки» были получены навыки по проектированию привода главного движения и по выбору электродвигателя для этого привода выполнен кинематический расчет.
На всех стадиях разработка конструкции основывалась на экономичности принимаемых решений возможной технологии изготовления и сборки условиях эксплуатации и обслуживания сроке службы и надежности:
важным показателем совершенства конструкции является условие равной долговечности всех элементов;
в проекте постарался использовать стандартные изделия (подшипники крышки подшипников шпонки уплотнения и т.д.) а так же стандарты на различные элементы проектируемых деталей.
СПИСОК ИСПОЛЬЗУЕМЫХ ИСТОЧНИКОВ
Металлорежущие станки. Методические указания к лабораторным работам для студентов направлений 151900 – «Конструкторско-технологическое обеспечение машиностроительных производств» и 151000 – «Технологические машины и оборудование» дневной и заочной форм обучения сост. С.Н. Власов. – Димитровград : ДИТИ НИЯУ МИФИ. – 2014. – 94 с.
Шейнблит А.Е. Курсовое проектирование деталей машин: учеб. пособие для ССУЗов – 2-е изд. перераб. и доп. – Калининград : Янтарный Сказ 2002.
Проектирование металлорежущих станков и станочных систем. В 3-х т. Т.1. Под общ. ред. А.С. Проникова. – М. : МГТУ им. Н.Э.Баумана: Машиностроение 1994. – 444 с.
спецификация Коробки скоростей.cdw

КП.150305.167.00.001 СБ
Вал электродвигателя
Тройной блок зубчатых колес
КП.150305.167.01.001
КП.150305.167.02.001
КП.150305.167.03.001
КП.150305.167.04.001
КП.150305.167.05.001
КП.150305.167.06.001
КП.150305.167.07.001
КП.150305.167.08.001
КП.150305.167.09.001
КП.150305.167.10.001
КП.150305.167.11.001
Фрагмент2.frw

Кор. скор. ИР500ПМФ4 разв.cdw

Кор. скор. ИР500ПМФ4 свер.cdw

Фрагмент1.frw

Рекомендуемые чертежи
- 22.11.2015
- 13.02.2022