Разработка технологического процесса изготовления и ремонта вала




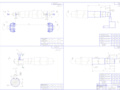
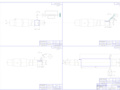
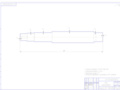
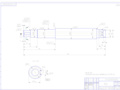
- Добавлен: 25.10.2022
- Размер: 1 MB
- Закачек: 0
Описание
Состав проекта
![]() |
![]() |
![]() |
![]() ![]() ![]() |
![]() ![]() ![]() |
![]() ![]() ![]() |
![]() ![]() ![]() |
![]() ![]() |
![]() ![]() ![]() ![]() |
![]() |
![]() ![]() ![]() ![]() |
![]() ![]() ![]() ![]() |
![]() ![]() ![]() |
![]() ![]() ![]() ![]() |
![]() ![]() ![]() ![]() |
![]() ![]() ![]() ![]() |
![]() ![]() ![]() |
![]() ![]() ![]() ![]() |
![]() ![]() ![]() ![]() |
![]() |
![]() ![]() ![]() |
![]() ![]() ![]() |
![]() ![]() ![]() |
![]() ![]() ![]() |
Дополнительная информация
Ремонт.dwg
Заплавить изношенный шпоночный паз
Эскизы востановления
Режимы восстановления
Электромагнитная наплавка
Вал (заготовка).dwg
Неуказанные радиусы 2 2
Неуказанные уклоны 3 5
Остальные требования к штамповке по ГОСТ 26358-84
Сталь45 ГОСТ 1050-88
эскизы операц.dwg
Фрезеровать в размер
Фрезеровать шпоночный паз шириной
h=5мм на длине L=28 мм на
деталь.dwg
Сталь45 ГОСТ 1050-88
Ремонт.cdw

Заплавить изношенный шпоночный паз
Эскизы востановления
Режимы восстановления
Электромагнитная наплавка
Ремонт.cdw

Заплавить изношенный шпоночный паз
Эскизы востановления
Режимы восстановления
Электромагнитная наплавка
Вал (заготовка).cdw

Неуказанные радиусы 2 2
Неуказанные уклоны 3 5
Остальные требования к штамповке по ГОСТ 26358-84
Сталь45 ГОСТ 1050-88
деталька.frw

эскизы операц.cdw

Фрезеровать в размер
Фрезеровать шпоночный паз шириной
h=5мм на длине L=28 мм на
деталь.cdw

Сталь45 ГОСТ 1050-88
Вал (заготовка).cdw

Неуказанные радиусы 2 2
Неуказанные уклоны 3 5
Остальные требования к штамповке по ГОСТ 26358-84
Сталь45 ГОСТ 1050-88
деталька.frw

эскизы операц.cdw

Фрезеровать в размер
Фрезеровать шпоночный паз шириной
h=5мм на длине L=28 мм на
деталь.cdw

Сталь45 ГОСТ 1050-88
титул+содерж.docx
МИНИСТЕРСТВО ОБРАЗОВАНИЯ И НАУКИ РОССИЙСКОЙ ФЕДЕРАЦИИ
ГОСУДАРСТВЕННОЕ УЧРЕЖДЕНИЕ ВЫСШЕГО ПРОФЕССИОНАЛЬНОГО ОБРАЗОВАНИЯ
«БЕЛОРУССКО-РОССИЙСКИЙ УНИВЕРСИТЕТ»
«Строительные дорожные подъемно-транспортные машины и оборудование»
«Технология производства и ремонт строительных и дорожных машин»
Разработка технологического процесса изготовления и ремонта изделия
Технологический процесс изготовления детали . . 4
1 Анализ технологичности детали . . 4
2 Определение типа производства . . 5
3 Выбор метода получения заготовки . . .5
4 Выбор маршрута механической обработки 8
5 Расчет припусков ..9
6 Выбор оборудования и приспособлений 9
7 Расчет режимов резания 10
Технологический процесс ремонта детали ..15
1 Анализ возможных дефектов 15
2 Восстановление качества детали 15
2.1 Восстановление посадочной поверхности лазерной наплавкой ..15
2.2 Восстановление шпоночного паза заплавкой в среде СО2 17
2.3 Восстановление шпоночного паза заплавкой под флюсом ..17
2.4 Восстановление посадочной поверхности электромагнитной наплавкой..18
Список литературы 21
Маршрутная карта.docx
Сталь 45 ГОСТ 1050-88
Код наименование операции
Обозначение документа
Код наименование оборудования
5 Фрезерно-центровальная ИОТ № 06
МP-73 3 1 1 1 236 1 8
А616 3 1 1 1 236 1 14
5 Фрезерная ИОТ № 13
Р11 3 1 1 1 236 1 17
0 Сверлильная ИОТ № 14
Р53 3 1 1 1 236 1 22
5 Шлифовальная ИОТ № 11
Записо4ка(final).doc
Разработка оптимального технологического процесса изготовления и ремонта каждой конкретной детали может нести значительную экономическую выгоду в масштабах целого предприятия. Поэтому такое большое внимание уделяется созданию новых перспективных способов создания изделий.
Технический прогресс ведет к увеличению сложности проектируемых объектов повышению их качества надежности и долговечности требуя применения новых технологических решений улучшения качества и сокращение сроков проектных работ. Достичь положительных результатов возможно лишь в случае использования современных средств САПР на всех этапах проектирования а на этапе конструкторского проектирования заложены возможности использования прогрессивных технологических решений.
В связи с этим повышаются требования предъявляемые к конструктору который должен обладать широким кругозором в вопросах проектирования производства и эксплуатации проектируемых объектов.
Целью курсовой работы является закрепление углубление и обобщение полученных знаний а также приобретение практических навыков для разработки технологических процессов изготовления и ремонта деталей с использованием прогрессивных технологий и анализа технологических решений.
Технологический процесс изготовления детали
1 Анализ технологичности детали
При производстве данной детали необходимо выполнять строгие технологические требования. Деталь достаточно технологична допускает применение высокопроизводительных режимов обработки имеет хорошие базовые поверхности для первоначальных операций и довольно проста по конструкции.
Программа выпуска: 10000Материал: Сталь 45 ГОСТ 1050-88.
На рисунке 1.1 представлен общий вид детали.
Рисунок 1.1 – Общий вид детали.
Материал детали - конструкционная углеродистая сталь 45 (ГОСТ 1050-88) широко используется для изготовления различных видов и типоразмеров шестерен коленчатых и распределительных валов шпинделей работающих в условиях требующих повышенной прочности и износостойкости.
Таблица 1.1 - Химический состав стали 45 (ГОСТ 1050-88).
Таблица 1.2 - Механические свойства стали 45 (ГОСТ 1050-88).
Предел прочнос-ти в МПа
Относи-тельное удлинение
Относи-тельное сужение %
Твердость до термообра-ботки
2 Определение типа производства
Определим величину партии запускаемой в производство одновременно:
где а – периодичность запуска данной детали в днях (а=6);
d – количество рабочих дней в году (d=255);
N – годовая программа.
Примем размер партии равных 236 деталей.
3 Выбор метода получения заготовки
Изготовление любой детали начинается с заготовки которая с помощью механической пластической термической химической и (или) иной обработки доводится до формы размеров и качества готовой детали заданных конструктором.
Метод получения заготовки для детали определяется назначением и конструкцией детали материалом техническими требованиями масштабом и серийностью выпуска а также экономичностью изготовления.
В рамках данной курсовой проанализируем два варианта получения заготовки: заготовка из проката и заготовка полученная штамповкой.
Расчет себестоимости для конкретных способов получения заготовки проведем предполагая что чистовая механическая обработка для всех вариантов одинакова.
Рассчитаем стоимость получения заготовки из проката (с.11 [1]):
где mпр - масса заготовки из проката кг (mпр = m1пр=1667кг - масса одного погонного метра проката данного профиля);
Ц1пр - цена 1 кг проката (табл. 2.1 [1]);
B - минутная зарплата рабочих производящих черновую механическую обработку заготовок (B » 002 004 мин);
Tшк1 - штучно-калькуляционное время черновой обработки детали которое ориентировочно определяется по формуле Tшк k - количество проходов инструмента (Принимая глубину резания для одного прохода равной 2 3 мм имеем k = 1;
l0 = l2 + 2×l1+ l Tшк
q - накладные расходы механического цеха в % к основной зарплате
Рассчитаем стоимость получения заготовки полученной штамповкой
где mш - масса прутка перед штамповкой кг (на 2 8 % больше массы готовой детали; плюс масса металла в отверстии 16 (157 кг))
mш = 391 · 108 + 157 = 58 кг;
Cш.р - стоимость штамповочных работ (Cш.р = 0005 mш =58·0005=003у.е.);
qш - накладные расходы штамповочного цеха (50 100 %);
Cшт - стоимость штампа (Cшт = 10 mш =10·58=58 у.е.);
nшт - количество заготовок изготавливаемых одним штампом (до 10 тыс.);
Tшк3 - штучно-калькуляционное время черновой обработки детали которое ориентировочно определяется по формуле Tшк k - количество проходов инструмента (Принимая глубину резания для одного прохода равной 2 3 мм имеем k = 1;
Рассчитаем экономический эффект:
Окончательно принимаем штамповку в качестве способа получения заготовки.
Заготовка будет иметь вид и размеры показанные на рисунке 1.2.
Рисунок 1.2 – Эскиз заготовки
4 Выбор маршрута механической обработки
Таблица 1.3 – Маршрут обработки детали.
Наименование операции и перехода
Фрезерно-центровальная
Фрезеровать торцы 34 и 44 в размер L=376 мм;
Сверлить центровые отверстия 5мм L=12 мм.
Фрезерно-центровальный станок МР-73
Точить 54 мм до 505 мм на L=190 мм за 1 проход t=2;
Точить 44 мм до 40 мм на L=40 мм за 2 прохода t=2;
Точить конус в размер за 2 прохода t=2;
Точить 44 мм до 405 мм на L=83 мм за 1 проходt=2;
Точить 39 мм до 355 мм на L=31 мм за 1 проходt=2;
Точить 34 мм до 305 мм на L=32 мм за 1 проходt=2;
Снять фаски 16х45о на 30 на 40;
Привод: 3-х кулачковый патрон. Закрепить в центрах.
Фрезеровать шпоночный паз шириной b=10мм h=5мм на длине L=28мм на 30;
Вертикально-фрезерный станок 6Р11. Закрепить в тисках и центрах.
Вертикально-сверлильная
Сверлить отверстие 16;
Цековать отверстие 32 на глубину L=10мм.
Вертикально-сверлильный станок 2Р53. Закрепить в тисках.
Шлифовать с 505 до 50h8 на длине L=190мм;
Шлифовать с 405 до 40k6 на длине L=83мм;
Шлифовать с 355 до 35h8 на длине L=31мм;
Шлифовать с 305 до 30h11 на длине L=32мм;
Кругло-шлифовальный станок 3131. Закрепить в центрах. Привод: поводковый патрон.
При обработке поверхности минимальный припуск для каждого i-го перехода можно оценить по следующей формуле (с.16 [1]):
ei - погрешность установки заготовки на данной операции мкм.
Минимальный припуск под точение:
Минимальный припуск под шлифование:
6 Выбор оборудования и приспособлений
Принимаем для фрезерной операции 005 станок фрезерно-центровальный МР-73. Обороты: 180; 250; 360; 500; 700; 1000; 1440; 2000. Подача: 01; 02; 03; 04; 05; 06 ммоб. Мерительный инструмент: ШЦ-I-125 ГОСТ 166-89.
Принимаем для токарных операций токарно-винторезный станок 1А616. Максимальный диаметр обработки над станиной – 180мм. Максимальный диаметр обработки над суппортом – 36мм. Максимальный диаметр обрабатываемого прутка – 165мм. Высота центров – 750мм. Частота вращения шпинделя мин-1: 16 20 25 35 40 50 63 80 100 125 160 200 250 315 400 500 630 800 1000 1250 1600. Продольная подача шпинделя: 005; 006; 007; 008; 01; 012; 015; 017; 02; 025; 03; 035; 04; 05; 06; 07; 08; 10; 12; 14; 16; 20; 24; 28 ммоб. Способ установки: патрон. Привод: 3-х кулачковый патрон. Мерительный инструмент ШЦ-I-500 ГОСТ 166-89 ШЦ-I-1250 ГОСТ 166-89.
Принимаем для фрезерной операции 015 шпоночно-фрезерный станок 6Р11. Частота вращения шпинделя: 65; 80; 100; 125; 160; 200; 240; 300; 375; 480; 600; 720; 900; 1125; 1440; 1800 мин-1. Фрезерная головка: поворот ± 90 градусов. Мерительный инструмент: ШЦ-I-125 ГОСТ 166-89.
Принимаем для вертикально-сверлильной операции 020 вертикально-сверлильный станок 2Р53. Частота вращения шпинделя: 20; 25; 315; 40; 50; 63; 80; 100; 125; 160; 200; 250; 320; 400; 500; 640; 800; 1000; 1280; 1600; 1800;
00 мин-1. Подача шпинделя: 007; 009; 011; 017; 022; 028; 04; 056; 09; 14; 18; 25 ммоб. Мерительный инструмент: ШЦ-I-125 ГОСТ 166-89.
Принимаем для шлифовальной операции 025 кругло-шлифовальный станок 3131. Частота вращения шлифовального круга 2110 мин-1. Размер шлифовального круга 350х40х127 мм. Привод поводковый патрон. Частота вращения детали 40 400 мин-1. Мерительный инструмент микрометр МК 50-1 по ГОСТ 6507-78.
7 Расчет режимов резания
Исходными данными для этого являются принятый маршрут механической обработки детали и назначенные припуски для каждого перехода что соответствует глубинам резания ti.
Принимаем материал лезвия инструмента: твердосплавная пластина Т15К6 период стойкости – Т=120мин. Для сверления: Р18 – Т = 10мин.
В зависимости от вида обработки назначим подачу инструмента s.
Затем определяется скорость резания ммин:
где Cv - коэффициент скорости резания (табл. 2.8 [1]);
T - период стойкости инструмента мин (табл. 2.6 [1]);
t - глубина резания мм;
s - подача инструмента ммоб;
m x y - показатели степеней (см. табл. 2.8).
При фрезеровании поверхности:
Cv = 1000; Т = 120 мин; t = 2 мм; s = 07 ммоб; m = 027; y = 03.
После оценки произведем вычисление проекций сил резания по координатным осям:
t - глубина резания мм (при отрезке и фасонном точении - ширина лезвия резца);
v - скорость резания ммин;
xi yi ni - показатели степеней (см. табл. 2.9 [1]).
После вычисления силы резания оценивается крутящий момент при резании Mк Н×м
где D - обрабатываемый диаметр при точении или диаметр фрезы мм.
Определяем частоту вращения шпинделя станка обмин:
Определяем мощность при фрезеровании кВт:
Согласно паспорту станка выбираем n = 700 мин-1 . Тогда фактическая скорость примет значение:
Режимы резания для остальных переходов заносим в таблицу 1.4.
Таблица 1.4 – Режимы резания.
Продолжение таблицы 1.4 – Режимы резания.
В заключении расчетов режимов резания определяется основное время обработки То (мин) и штучно-калькуляционное ТШК (мин) для каждой операции. Общая зависимость для основного времени:
k - количество проходов инструмента;
n - частота вращения шпинделя станка (обмин) или число двойных ходов в минуту для станков с прямолинейным главным движением;
Штучно-калькуляционное время для каждой операции вычисляется как сумма:
Tшк = Tо + Tв + Tоб + Tф
где TВ - вспомогательное время связанное с установкой заготовки и её закреплением управлением станком текущими измерениями детали которое ориентировочно принимается Tв = (001 02) Tо ;
TОБ - время обслуживания станка то есть на его уборку смазку и привидение в рабочее состояние которое составляет 1 6 % от Tо ;
TФ - время на физические надобности рабочего принимаемое 4 8 % от суммы Tо и Tв .
Следует иметь в виду что при массовом производстве Tв Tоб и Tф минимальны и часто перекрываются основным временем.
Рассчитаем основное и штучно-калькуляционное время для 1 перехода 005 операции:
Tшк = 014+ (01·014) + (0035·014) + (006·014)=017мин
Результаты расчетов для остальных операций сведем в таблицу 1.5.
Таблица 1.5 – Основное и штучно-калькуляционное время.
калькуляционное время
Технологический процесс ремонта детали
1 Анализ возможных дефектов
Изнашивание – это процесс постепенного изменения размеров и формы тело в процессе работы.
Вал может иметь следующие дефекты (рис. 2.1):
-износ рабочих поверхностей (2 3 4);
-износ шпоночного паза (поверхность 1).
Рисунок 2.1 – Схема изношенных поверхностей вала
2 Восстановление качества детали
2.1 Восстановление посадочной поверхности лазерной наплавкой.
В качестве источника энергии используется лазер с интенсивностью излучения света не менее 1012 кВтмм2.
Перед наплавкой на поверхность детали наносят шихту которая чаще всего представляет собой порошкообразную смесь металлов и неметаллических материалов. Закрепление шихты на поверхности детали осуществляют с помощью клеев.
В качестве квантового генератора чаще используют рубиновые реже газовые (CO2 + N2 + He) лазеры.
В данной установке рубиновый стержень или газонаполненная колба облучается импульсной лампой которая запитывается электроэнергией от конденсаторной батареи. Отражатель (корпус) и заднее зеркало направляют луч на полупрозрачное зеркало а затем на поворотное линзу и деталь на которой нанесена шихта. Для защиты зоны расплава от окисления используют аргон.
Оборудование: комплект для лазерной наплавки в который входит газовый лазер ЛГП-702 мощностью 08 кВт установка для наплавки СКС-011-1-02 с оснасткой приспособление для управления лазерным лучом система газообеспечения.
Материалы: порошок СНГН.
При данном методе наплавки весьма мала зона теплового воздействия на деталь. Поэтому деформации её практически отсутствуют что позволяет ремонтировать самые разные по размерам детали.
Таблица 2.1 – Маршрут восстановления поверхности 2.
Наплавить поверхность до 355 мм L=31 мм
Шлифовать 355 мм до 35h8 мм L=31 мм
Таблица 2.2 – Маршрут восстановления поверхности 3.
Наплавить поверхность до 405 мм L=83 мм
Шлифовать 405 мм до 40k6 мм L=83 мм
2.2 Восстановление шпоночного паза заплавкой в среде СО2. В качестве защитного газа используем углекислый газ СО2.
Материалы наплавки. Применяем проволоку диаметром 05 – 20 мм марки Нп-30ХГСА.
Оборудование. Используем полуавтомат А-537. В качестве наплавочного автомата используем переоборудованный аппарат А-580 который выпускается для наплавки под флюсом а также наплавочную головку ОКС-1252А комплектуемый источником тока ПСУ-500. В качестве источника тока используем также выпрямитель ВСГ-3А и сварочный преобразователь ПСГ-300.
Режимы сварки в углекислом газе
Диаметр проволоки мм05-07
Вылет электрода мм5-8
Таблица 2.3 – Маршрут восстановления заплавкой в среде СО2.
Заплавить шпоночный паз до 30 мм L=28 мм
Фрезеровать шпоночный паз шириной b=10мм h=5мм на длине L=28мм на 30
Фрезерный станок 692М. Закрепить в тисках и центрах.
2.3 Восстановление шпоночного паза заплавкой под флюсом. Это такой сварочный процесс при котором подача электродной проволоки и её перемещение вдоль детали подача защитных и легирующих материалов в зону дуги осуществляется механизированным способом.
– стабильно высокое качество шва;
– повышение производительности труда;
– возможность использовать рабочих низкой квалификации.
Параметры и режимы восстановления:
– проволока марки МП-50 диаметром 16 мм;
– частота вращения детали n = 3 мин-1;
– шаг наплавки t = 35 ммоб;
– скорость подачи электродной проволоки V = 2 ммин;
Таблица 2.4 – Маршрут восстановления заплавкой под флюсом.
2.4 Восстановление посадочной поверхности электромагнитной наплавкой. Сущность электромагнитной наплавки заключается в нанесении покрытия из ферромагнитного порошка удерживаемого силами магнитного поля во время пропускания через зоны контакта частиц порошка между собой и деталью постоянного тока большой силы.
К полюсному наконечнику и детали подводят напряжение. Покрытие образуется за счет нагрева частиц порошка их оплавления и закрепления на восстанавливаемой поверхности. При этом удельная мощность достигает значений 50 – 5000 кВтсм2.
Для повышения стабильности и равномерности покрытия в рабочий зазор подают пасту состоящую из смеси порошков со связующим (жидким стеклом) в соотношении (по объему) 2:1. При увеличении плотности тока до 3 Амм2 можно получить покрытие толщиной около 2 мм.
Наплавочный материал: У30Х28Н4С4.
Оборудование: аппарат МЭС-1. После наплавки необходимые поверхности обтачивают и шлифуют под номинальный размер.
Таблица 2.5 – Маршрут восстановления поверхности 4.
Наплавить поверхность до 505 мм L=190 мм
Шлифовать 505 мм до 50h8 мм L=190 мм
В результате проведенной работы разработан технологический процесс изготовления и ремонта детали при этом были учтены все существующие рекомендации и выбран наиболее оптимальный вариант технологического процесса который способствует наименьшей себестоимости изготовления детали. При разработке курсового проекта были рассчитаны припуски на обработку заданной поверхности а также режимы резания при точении этой поверхности и выбраны оптимальные варианты ремонта детали.
В результате получены практические навыки выбора оптимального варианта процесса изготовление что важно для дальнейшей работы в области конструирования и способствует развитию инженерного подхода к проектированию машин механизмов и отдельных деталей.
Технология производства и ремонта строительных и дорожных машин. Методические указания к практическим занятиям для выполнения курсовой работы. Составитель Е.В. Кузнецов. – Могилев: БРУ 2007. – 35 с.
Курсовое проектирование по технологии машиностроения А.Ф. Горбацевич В.А. Шкред - Мн.: Выш. школа 1983. -256 с. ил.
Дипломное проектирование по технологии машиностроения В.В. Бабук П.А. Горезко К.П. Забродин и др. - Мн.: Выш. школа 1979. -464 с. ил.
Справочник технолога-машиностроителя в 2-х томах. Под ред.
А.Г. Косиловой и Р.К. Мещерякова. -М.: Машиностроение 1973 1985. -1187 с.
Ремонт дорожных машин автомобилей и тракторов. Под ред.
В.А. Зорина. - М.: Машиностроение 2001. -400 с.
Рекомендуемые чертежи
- 13.12.2022
- 10.06.2015
- 04.11.2022