Дипломный проект (техникум) - Разработка технологического процесса изготовления вала




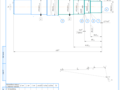
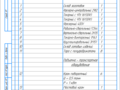
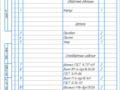
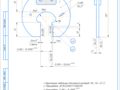
- Добавлен: 04.11.2022
- Размер: 2 MB
- Закачек: 5
Описание
Дипломный проект (техникум) - Разработка технологического процесса изготовления вала
Состав проекта
![]() |
![]() |
![]() ![]() ![]() |
![]() |
![]() |
![]() ![]() ![]() |
![]() ![]() ![]() |
![]() ![]() ![]() ![]() |
![]() |
![]() |
![]() |
![]() |
![]() |
![]() |
![]() |
![]() |
![]() |
![]() |
![]() ![]() ![]() |
![]() ![]() ![]() |
![]() ![]() ![]() |
![]() ![]() ![]() |
![]() ![]() ![]() |
![]() ![]() ![]() |
![]() ![]() ![]() ![]() |
![]() |
![]() ![]() ![]() |
![]() ![]() ![]() |
![]() |
![]() |
![]() ![]() ![]() |
![]() |
![]() |
![]() ![]() ![]() |
![]() ![]() ![]() |
![]() |
![]() |
![]() ![]() ![]() ![]() |
![]() ![]() |
![]() ![]() ![]() |
![]() ![]() |
![]() ![]() ![]() |
![]() ![]() ![]() |
![]() |
![]() |
![]() ![]() ![]() ![]() |
![]() ![]() ![]() ![]() |
![]() ![]() ![]() ![]() |
![]() |
![]() ![]() ![]() ![]() |
![]() |
![]() ![]() ![]() ![]() |
![]() ![]() ![]() ![]() |
![]() ![]() ![]() ![]() |
![]() ![]() ![]() ![]() |
![]() ![]() ![]() ![]() |
![]() ![]() ![]() ![]() |
![]() ![]() ![]() ![]() |
![]() ![]() ![]() ![]() |
![]() ![]() ![]() ![]() |
![]() |
![]() ![]() ![]() ![]() |
![]() ![]() ![]() ![]() |
![]() ![]() ![]() ![]() |
![]() ![]() ![]() ![]() |
![]() |
![]() ![]() ![]() ![]() |
![]() ![]() ![]() ![]() |
![]() ![]() ![]() ![]() |
Дополнительная информация
тех процесс вал.doc
КОМПЛЕКТ ТЕХНОЛОГИЧЕСКОЙ ДОКУМЕНТАЦИИ
изготовления детали «Вал»
ГОСТ 3.1118-82 Форма 1
ДП.15.02.08.017.11.000
Код наименование операции
Обозначение документов
Код наименование оборудования
60 Фрезерно-центровальная
Фрезерно-центровальный 2982
Кран поворотный 7878-0000 Q=05 тс
А. Установить закрепить снять
ХХ ХХ ХХ ХХ Прихват 7011-0706 ГОСТ 4736-69
ХХ ХХ ХХ ХХ Призма 7033-0039 ГОСТ 12195-66
Фрезеровать торцы 1 2 023
1 801 ХХ ХХ Фреза 2214-0397 ГОСТ 26595-85
3 311 ХХ ХХ Штангенциркуль ШЦ-III-250-800-005 ГОСТ 166-89
Форма ГОСТ 3.1118-82 Форма 1а
Центровать торцы 1 2 023
1 210 ХХ ХХ Сверло 2317-0122 ГОСТ 14952-75
3 311 ХХ ХХ Штангенциркуль ШЦ-I-125-001 ГОСТ 166-89
ХХ ХХ ХХ 010 Контрольная 055
ХХ ХХ ХХ 015 4112 Токарная с ЧПУ
1 114 ХХ ХХ Токарный станок с ЧПУ 16М30Ф3 18225 4 1р 1 1 1 23 1805
А. Установить закрепить снять 095
6 110 ХХ ХХ Патрон 7102.0088-1-2 ГОСТ 24351-80
6 110 ХХ ХХ Центр А-1-6-Н ГОСТ 8742-75
2 190 ХХ ХХ Резец MSSNR 2525; Пластина 03124-120408 ГОСТ 19052-80
Точить поверхности 4 3 с подрезкой торца 2 941
2 190 ХХ ХХ Резец MWLNR 2525 Пластина 02114-100608 ГОСТ 19048-80
3 440 ХХ ХХ Штангенглубиномер ШГ-200-001 ГОСТ 162-90
3 120 ХХ ХХ Калибр-скоба АДК 8113.2083 h11
3 120 ХХ ХХ Калибр-скоба АДК 8113.2068 h11
Точить поверхность 1 265
ХХ ХХ ХХ 020 Контрольная 056
ХХ ХХ ХХ 025 4112 Токарная с ЧПУ
1 114 ХХ ХХ Токарный станок с ЧПУ 16М30Ф3 18225 4 1р 1 1 1 23 2047
Точить поверхность 5 с подрезкой торца 7 21
2 110 ХХ ХХ Резец 2103.0009 ГОСТ 18879-73
3 120 ХХ ХХ Калибр-скоба АДК 8113.2001 h11
Точить поверхность 4 с подрезкой торца 9 09
3 120 ХХ ХХ Калибр-скоба 8113.0147 h9 ГОСТ 18360-93
Точить поверхности 3 2 с подрезкой торца 1 101
3 311 ХХ ХХ Штангенциркуль ШЦ-II-300-001 ГОСТ 166-89
ХХ ХХ ХХ 030 Контрольная 11
ХХ ХХ ХХ 035 4261 Вертикально-фрезерная
1 861 ХХ ХХ Фрезерный станок 400V 18632 3 1р 1 1 1 31 852
А. Установить закрепить снять 11
ХХ ХХ ХХ ХХ Приспособление для фрезерования
Фрезеровать паз 1 (предварительно) 188
1 820 ХХ ХХ Фреза 2235.0053 №9 ГОСТ 9140-78
3 311 ХХ ХХ Штангенциркуль ШЦ-I-125-01 ГОСТ 166-89
Фрезеровать паз 1 (окончательно) 37
3 120 ХХ ХХ Калибр АДК 8158.4110
3 120 ХХ ХХ Калибр АДК 8158.4111
3 120 ХХ ХХ Калибр АДК 8353.4511
3 120 ХХ ХХ Калибр АДК 8141.6448
ХХ ХХ ХХ 040 Контрольная 078
ХХ ХХ ХХ 045 4123 Радиально-сверлильная
1 217 ХХ ХХ Радиально-сверлильный станок ГС 544 17335 3 1р 1 1 1 21 54
А. Установить закрепить снять 12
ХХ ХХ ХХ ХХ Кондуктор
Сверлить 2 отверстия 1 поочередно 078
1 267 ХХ ХХ Сверло 2301.0020 ГОСТ 10903-77
3 120 ХХ ХХ Калибр-пробка В8133.1847 Н7 ОСТ 3-2645-75
Зенковать фаску в 2-х отверстиях 1 008
1 630 ХХ ХХ Зенковка АДК 2352.0015
Нарезать резьбу в 2-х отверстиях 1 037
1 330 ХХ ХХ Метчик 2620-1435.2 ГОСТ 3266-81
3 140 ХХ ХХ Калибр-пробка В8133.1848 7Н ОСТ 3-2660-75
3 140 ХХ ХХ Калибр-пробка 8221.3044 7Н ГОСТ 17758-72
ХХ ХХ ХХ 050 Контрольная 108
ХХ ХХ ХХ 055 4121 Вертикально-сверлильная
1 213 ХХ ХХ Вертикально-сверлильный станок 2Н135 17335 3 1р 1 1 1 21 828
Сверлить отверстие 1 164
1 267 ХХ ХХ Сверло 2301.0069 ГОСТ 10903-77
3 311 ХХ ХХ Штангенциркуль ШЦ-I-125-005 ГОСТ 166-89
Рассверлить отверстие 1 20
1 267 ХХ ХХ Сверло 2301.0111 ГОСТ 10903-77
Зенкеровать отверстие 1 092
1 610 ХХ ХХ Зенкер 2320.2606 И8 ГОСТ 12489-71
3 120 ХХ ХХ Калибр-пробка 8133.0946 Н11 ГОСТ 14810-69
3 120 ХХ ХХ Калибр АДК 8328.5097
ХХ ХХ ХХ 060 Контрольная 052
3 311 ХХ ХХ Штангенциркуль ШЦ-I-125-005 ГОСТ 166-89
ХХ ХХ ХХ 065 4131 Круглошлифовальная
1 311 ХХ ХХ Круглошлифовальный станок 3М151Ф2 18873 3 1р 1 1 1 23 1038
А. Установить закрепить снять 04
6 110 ХХ ХХ Патрон 7108-0025 ГОСТ 2571-71
6 110 ХХ ХХ Центр А-1-6-Н ГОСТ 8742-75
Шлифовать поверхность 1 071
7 120 ХХ ХХ Круг шлифовальный 1500’ 50’ 305 25А 10-П С2 7 К1А 35 мс 1кл. ГОСТ 2424-83
3 120 ХХ ХХ Калибр-скоба 8113.0151 k6 ГОСТ 18360-93
Шлифовать поверхность 2 06
3 120 ХХ ХХ Калибр-скоба 8113.0150 h9 ГОСТ 18360-93
Шлифовать поверхность 3 054
3 120 ХХ ХХ Калибр-скоба 8113.0143 h6 ГОСТ 18360-93
Б. Переустановить закрепить снять 04
Шлифовать поверхность 1 07
Шлифовать поверхность 2 084
3 120 ХХ ХХ Калибр-скоба 8113.0150 h6 ГОСТ 18360-93
ХХ ХХ ХХ 070 Контрольная 08
3 120 ХХ ХХ Калибр-скоба 8113.0151 k6 ГОСТ 18360-93
3 120 ХХ ХХ Калибр АДК 8371.0021
3 120 ХХ ХХ Калибр АДК 8371.0023
3 120 ХХ ХХ Калибр АДК 8371.0025
3 120 ХХ ХХ Калибр АДК 8371.0046
ХХ ХХ ХХ 075 4110 Токарно-винторезная
1 101 ХХ ХХ Токарно-винторезный станок 1М63 18217 3 1р 1 1 1 27 857
А. Установить закрепить снять 14
6 110 ХХ ХХ Патрон 7100.0045 ГОСТ 2675-80
Сверлить отверстие 1 456
1 267 ХХ ХХ Сверло 2301.0076 ГОСТ 10903-77
3 120 ХХ ХХ Калибр-пробка 8133.0936 Н14 ГОСТ 14810-69
3 440 ХХ ХХ Штангенглубиномер ШГ-160-005 ГОСТ 162-90
Зенковать фаску 2 04
1 267 ХХ ХХ Сверло 2301.0094 ГОСТ 10903-77
3 120 ХХ ХХ Калибр АДК 8371.0006
ХХ ХХ ХХ 080 Контрольная 032
НТ2.frw

НТ4.frw

НТ1.frw

НТ3.frw

НТ8 уст Б.frw

НТ5.frw

НТ6.frw

НТ7.frw

НТ8 уст А.frw

номер детали.frw

6,3.frw

титуль на тех.процесс.doc
ГАПОУ СО «Карпинский машиностроительный техникум»
Зам. директора по УР
КОМПЛЕКТ ТЕХНОЛОГИЧЕСКОЙ ДОКУМЕНТАЦИИ
студент группы 1-ТМ-15 С.Б. Попова
Н.Контроль Рецензент
С.Б. Попова М.В. Берет
схема 1.frw

базы1.frw

заготовка.frw

график.frw

титульный на диплом.doc
ОБРАЗОВАНИЯ СВЕРДЛОВСКОЙ ОБЛАСТИ
ГАПОУ СО «Карпинский машиностроительный техникум»
Зам. директора по УПР
РАЗРАБОТКА ТЕХНОЛОГИЧЕСКОГО
ПРОЦЕССА ИЗГОТОВЛЕНИЯ ВАЛА
Пояснительная записка
ДП.15.02.08.017.11.ООО.ПЗ
студент группы 1-ТМ-15 С.Б. Попова
Руководитель Рецензент
С.Б. Попова М.В. Берет
Литература.doc
Горошкин А.К. Приспособление для металлорежущих станков. - М.: Машгиз 1962.
Добрыднев И.С. Курсовое проектирование по предмету «Технология
машиностроения»: Учебное пособие для техникумов. - М.: Машиностроение
Журавлёв В.Н. Николаева О.И. Машиностроительные стали: Справочник. - М.: Машиностроение 1992.-480 с. ил.
Зенкин А.С. Петко И.В. Допуски и посадки в машиностроении. Справочник - К.: Техника 1990.-320 с.
Козьяков А.Ф. Морозова Л.Л. Охрана труда в машиностроении: Учебник для
учащихся средних специальных учебных заведений. - М.: Машиностроение
Марочник сталей и сплавовМ.М. Колосков Е.Т. Долбенко Ю.В. Каширский и др.; Под общей ред. А.С. Зубченко - М.: Машиностроение 2001.-672 с. ил.
Медовой И.А. и др. Исполнительные размеры калибров: Справочник. В 2-х. кн. Кн.1И.А. Медовой Я.Г. Уманский Н.М. Журавлёв - М.: Машиностроение 1980.-384 с. ил.
Нефёдов Н.А. Дипломное проектирование в машиностроительных техникумах: Учебное пособие для техникумов. - М.: Высшая школа 1986.-239 с. ил.
Нефёдов Н.А. К.А. Осипов Сборник задач и примеров по резанию металлов
и режущему инструменту: Учебное пособие для техникумов. - М.:
Машиностроение 1990.-448 с. ил.
Обработка металлов резанием: Справочник технологаА.А. Панов В.В. Аникин Н.Г. Бойм и др.; Под общ. Ред. А.А. Панова. - М.: Машиностроение 1988.-736 с. ил.
Общемашиностроительные нормативы времени вспомогательного на
обслуживание рабочего места и подготовительно-заключительного для
технического нормирования станочных работ.
Серийное производство. - М.: Машиностроение 2001.
Общемашиностроительные нормативы режимов резания для технического
нормирования работ на металлорежущих станках. Часть I. - М.:
Машиностроение 1974.-406 с.
Справочник технолога-машиностроителя. В 2-х. т. Т1Под ред.
А.М. Дальского А.Г. Косиловой Р.К. Мещерякова и А.Г. Суслова. - М.:
Машиностроение 2001.-912 с. ил.
Справочник технолога-машиностроителя. В 2-х. т. Т2Под ред.
Машиностроение 2001.-944 с. ил.
Экономика предприятия. Под ред. Волкова В.И. – М: Высшая школа 2005.
диплом вал.doc
Решение задач повышения эффективности и качества изготовления деталей предусматривает внедрение в производство технологии малоотходного производства заготовок; механизацию и автоматизацию процессов производства сборки и контроля; развитие методов пластического деформирования; внедрение новых высоко производственных процессов механической и термической обработки станков режущего инструмента и зажима приспособлений на базе достижения новой техники и передового опыта предприятий.
Дипломный проект направлен на решение конкретных задач. Необходимо разработать технологию механической обработки детали «вал» используя новейшие достижения науки и техники разработать организацию производства и рассчитать технико-экономические показатели работы участка.
Деталь «вал» – тело вращения. Вал входит в шпиндель дробемётного аппарата и выполняет функцию передачи вращательного движения от электродвигателя к ротору через клиноременную передачу.
Дробемётный аппарат предназначен для создания потока дроби с высокой скоростью движения в определенном направлении. Аппарат устанавливается на оборудование дробемётной обработки изделий: очистка отливок от земли стержней окалины; очистка поковок штамповок листового и профильного проката от окалины ржавчины; наклеп поверхности деталей с целью упрочнения.
Основной вид обработки вала – обработка резанием. Основные операции: токарная фрезерная сверлильная шлифовальная.
Материал детали – сталь 38ХС ГОСТ 4543-71 – сталь конструкционная легированная с содержанием углерода 034-042%. Эту сталь применяют для изготовления валов шестерней муфт пальцев и других деталей небольших размеров к которым предъявляются требования высокой прочности упругости и износостойкости.
Габаритные размеры: диаметр 84 мм длина 630 мм. Наивысшая точность размеров – 6 квалитет. Шероховатость Ra = 125 мкм достигается шлифованием.
Масса детали 2196 кг требует специальных грузоподъемных устройств для установки и снятия ее со станка.
2 Материал детали и его свойства
Вал изготавливается из стали 38ХС ГОСТ 4543-71.
Физико-механические свойства.
3. Анализ технологичности конструкции детали
Определение коэффициента точности
Квалитет точности Тi
Число поверхностей ni
где Ti – квалитет точности
ni – число поверхностей детали одинакового квалитета
Т.к. Кт.ч. > 08 то деталь является технологической.
Определение коэффициента шероховатости
Параметр шероховатости Ra
Число поверхностей mi
Произведение Ra и mi
где Ra – параметр шероховатости детали
mi – число поверхностей детали с одинаковым параметром шероховатости
Качественная оценка технологичности конструкции детали
Содержание требования
Конструкция детали должна состоять из
стандартных и унифицированных конструктивных элементов
Деталь должна быть изготовлена из стандартной заготовки
Размеры и поверхности детали должны иметь оптимальные степень точности и шероховатость
Возможность обработки одновременно нескольких деталей
Деталь не должна иметь труднодоступных мест для обработки
Обеспечена достаточная жёсткость детали
Предусмотрена возможность удобного подвода инструмента к зоне обработки детали
Обеспечен свободный вход и выход инструмента из зоны обработки
Конструкция детали должна обеспечивать возможность применения типовых и стандартных технологических процессов
Вывод: проанализировав рабочий чертеж детали вал по параметрам точности получили что критерии детали больше контрольного рубежа; по параметрам шероховатости коэффициент близок к единице; к детали стандартных требований на технологичность из 9 требований 8 имеют положительный эффект. Следовательно деталь считается технологичной.
ТЕХНОЛОГИЧЕСКИЙ РАЗДЕЛ
1 Определение типа производства
Тип производства согласно ГОСТ 3.1108-74 характеризуется коэффициентом закрепления операций за одним рабочим местом или единицей оборудования. Тип производства определяется коэффициентом:
где - число различных операций;
- число рабочих мест на которых выполняются данные операции.
Для предварительного определения типа производства можно использовать годовой объём выпуска и массы детали [3].
Тип производства - среднесерийное.
Серийное производство характеризуется ограниченной номенклатурой изделий изготовляемых периодически повторяющимися партиями и сравнительно большим объёмом выпуска чем в единичном типе производства.
При серийном производстве используются универсальные станки оснащённые как специальными так и универсальными и универсально-сборочными приспособлениями что позволяет снизить трудоёмкость изготовления изделия.
Количество деталей в партии для одновременного запуска определяется по формуле
где N r = 2000 - годовой объём выпуска;
а = 3 дня - периодичность запуска;
Др = 246 дней - количество рабочих дней в году.
Полученные значения подставляем в формулу (2.2):
п = 20003246 = 24 шт.
2 Разработка маршрута обработки
Маршрут обработки детали
Наименование операции
Фрезерно-центровальная
Вертикально-фрезерная
Радиально-сверлильная
Вертикально-сверлильная
Токарно-винторезная
3 Выбор приспособления и оборудования
Выбранное оборудование и приспособления внесём в таблицу 2.2
Выбор технологического оборудования и оснастки
Технологическая оснастка
Технологическое оборудование и его краткая характеристика
Фрезерно-центровальная
Призма 7033-0039 ГОСТ 12195-66
Пределы частот вращения шпинделя MinMax Об.Мин.: . 151700
Мощность двигателя главного движения кВт.: 550
Габариты станка мм.:
Масса станка кг.: 7700
Диаметр детали мм 200
Длина детали мм 1000
02.0088-1-2 Патрон ГОСТ 24351-80;
А-1-6-Н Центр ГОСТ 8742-75
Станок модели 16М30Ф3
Наибольший диаметр обрабатываемой заготовки:
над станиной 500 мм.;
над суппортом 320 мм.
Наибольшая длина обрабатываемой заготовки 1500 мм.
Наибольшая масса устанавливаемой заготовки 850 кг.
Количество инструментов одновременно устанавливаемых на станке 5 9
Продолжение таблицы 2.2
Подача суппорта мммин:
Число оборотов шпинделя
Мощность электродвигателя главного движения 30 кВт
Габаритные размеры мм:
Приспособление для фрезерования
Размеры рабочей поверхности стола мм 400900
Ширина направляющего паза мм 18Н7
Количество Т-образных пазов 3
Наибольшее расстояние от торца шпинделя до стола мм 560
Наибольшая масса обрабатываемой детали 400 кг
Пределы частот вращения шпинделя обмин 0 8000 Диапазон рабочих подач по координатам мммин 1 15000 Число оборотов шпинделя 1465
Мощность двигателя главного
привода 7 кВт Габаритные размеры мм:
Радиально-сверлильная
Станок модели ГС 544
Размеры рабочей поверхности плитымм 1000 х 710 возможно 1100760
Размеры Т-образных пазов мм 18
Расстояние от торца шпинделя до плиты (maxmin) мм 1000 210 возможно 1100 320 (210 ниже плоскости плиты)
Расстояние от оси шпинделя до пола при его горизонт. положении (maxmin) мм 1510 560
Наибольший условный диаметр сверления мм в стали 40
Наибольший диаметр нарезаемой резьбы в стали М27
Частота вращения шпинделя мин-1 45-63-90-125-180-250 355-500-710 1000-1400-2000
Величина подач ммоб 0056-1 018-032
Суммарный угол поворота рукава град 360
Суммарный угол поворота сверлильной головки град 360
Конус шпинделя Морзе 4
Мощность привода главного движения кВт 22
Габаритные размеры станка (LxBxH) мм не более 1790х950х2040
Масса станка кг не более 1300
Наибольший диаметр сверления в стали 45 ГОСТ 1050-74 мм 35
Размеры конуса шпинделя по ГОСТ 25557-82 Морзе 4
Расстояние от оси шпинделя до направляющих колонны мм 300
Наибольший ход шпинделя мм 250
Расстояние от торца шпинделя мм:
- до плиты 700-4120 Наибольшее (установочное) перемещение сверлильной головки мм 170
Перемещение шпинделя за один оборот штурвала мм 122.46
Рабочая поверхность стола мм 450x500
Наибольший ход стола мм 300
Установочный размер Т-образных пазов в столе по ГОСТ 1574-75:
Расстояние между двумя Т-образными пазами по ГОСТ 6569-75 мм 100
Количество скоростей 12
Пределы частоты вращения шпинделя 1мин 315-1400
Пределы подач ммоб 01-16
Наибольшее количество нарезаемых отверстий в час 55
Управление циклами работы Ручное
Род тока питающей сети Трехфазный
Напряжение питающей сети В 380220
Габаритные размеры мм:
Масса станка кг 1200
А-1-6-Н Центр ГОСТ 8742-75; Патрон 7108-0025 ГОСТ 2571-71
Наибольшие размеры устанавливаемой заготовки:
Высота центров мм: 125
Диаметр шлифовального круга:
Частота вращения шлифовального круга мин-1: 1590 Частота вращения заготовки мин-1 50—500
Мощность электродвигателя привода шлифовального круга: 10 кВт
Скорость перемещения стола от гидропривода ммин: 005—5 Врезная подача мммин: 001-3
Габаритные размеры станка мм:
Патрон 7100.0045 ГОСТ 2675-80
Класс точности – Н по ГОСТ 8-77
Наибольший диаметр обрабатываемого изделия над
Наибольшая длина обрабатываемого изделия (без перестановки резцовых салазок) мм 1260
Наибольший диаметр прутка проходящего через отверстие в шпинделе мм 66
Высота резца установленного в резцедержателе мм 32
Количество скоростей вращения шпинделя:
обратного вращения 11
Пределы частот вращения шпинделя обмин:
прямого вращения 10-1250
обратного вращения 18-1800
поперечных 44 Пределы подач ммоб:
продольных 0064-1025
4 Выбор вида и метода получения заготовки
Технологические процессы получения заготовок определяются технологическими свойствами материала конструктивными формами и размерами детали и программой выпуска.
Метод получения заготовки для вала – поковка полученная методом штамповки на горячештамповочном прессе что обеспечивает высокую производительность и экономичное использование материала.
Форма заготовки должна быть как можно ближе к форме готового изделия. По мере усложнения конфигурации заготовки уменьшения припусков повышения точности размеров и параметров расположения поверхностей усложняется и удорожается технологическая оснастка заготовительного цеха и возрастает себестоимость заготовки но при этом снижается трудоемкость и себестоимость последующей механической обработки заготовки повышается коэффициент использования материала.
При выборе технологических методов и процессов получения заготовок необходимо учитывать прогрессивные тенденции развития технологий машиностроения.
5 Расчёт припусков и установление межоперационных размеров
В качестве исходной заготовки используем поковку стальную изготовленную горячей объемной штамповкой. Расчеты припусков допусков выполняем по ГОСТ 7505-89.
Исходные данные: Вал сталь 38ХС
В качестве основного деформирующего оборудования выбран горячештамповочный пресс. Нагрев заготовки в газовом пламени.
При использовании выбранного оборудования и пламенном нагреве принимаем класс точности Т3 [стр. 28]
Группу стали устанавливаем в соответствии с её химическим составом.
При массовой доле С равной 034-042% группа стали М2 [стр. 8]
Степень сложности С1 так как отношение свыше Ким = 063 [стр. 30]
Исходный индекс Ии устанавливаем с учетом конструктивных характеристик поковки. При Мз =3514 кг группе стали М2 степени сложности С1 классе точности поковки Т3 исходный индекс Ии = 16 [стр. 10]
Для определения межоперационных припусков для размера ∅58h6 используем расчетно-аналитический метод.
Межоперационные припуски
Элементы минимального припуска мкм
а) Определение последовательности обработки
Допуск размера на поковку устанавливается по исходному индексу
Ии = 16 по ГОСТ 7505-89
Т3 = 36 мм [стр. 18 табл. 8]
для размеров 50 80 мм соответствует 17 квалитету [14стр. 192]
Готовый диаметр имеет 6 квалитет точности.
Коэффициент ужесточения точности размера[10стр. 71]
где Тз – допуск заготовкимкм
Тд – допуск детали мкм
Данные значения подставляем в формулу 2.3
Количество потребных технологических переходов [10стр. 71]
где n – расчетное количество потребных технологических переходов;
- логарифм коэффициента ужесточения точности размера
Распределение общего перепада квалитетов 17-6=11 на 5 переходов:
Точение получистовое 12
Переходы и квалитеты вносим в таблицу 2.3
б) Данные к расчету припусков
Заносим в графы 3 и 4
Параметр шероховатости и толщина дефектного слоя определяется в зависимости от веса поковки [14стр. 186]
Заносим в графы 5 и 6
Суммарное пространственное отклонение [10стр. 59]
где - отклонение от соосности мм
- Кривизна поковки типа вал мм
= 20 мм = 2000 мкм [14стр. 186]
Данные значения подставляем в формулу (2.4)
Качество поверхности [14стр. 187]
Пространственное отклонение [9стр. 189]
где Ку – коэффициент уточнения
Ку = 006 [14стр. 190]
Данные значения подставляем в формулу (2.5)
Погрешность установки в 3-х кулачковый патрон Е = 400 мкм[14стр. 42
Качество поверхности [14стр. 188]
Пространственное отклонение [14стр. 189]
Ку = 005 [14стр. 190]
Данные значения подставляем в формулу (2.6)
Погрешность установки в 3-х кулачковый патрон Е = 200 мкм [14стр. 42
Ку = 004 [14стр. 190]
Данные значения подставляем в формулу (2.7)
Погрешность установки в 3-х кулачковый патрон Е = 100 мкм [14стр. 42
Ку = 002 [14стр. 190]
Данные значения подставляем в формулу (2.8)
Погрешность установки в центрах Е = 25 мкм [14стр. 44]
в) Расчет минимальных припусков
где - расчетный минимальный припуск на выполняемом переходе;
- высота неровностей профиля
-глубина дефектного поверхностного слоя на предшествующем переходе;
- погрешность установки заготовки на выполняемом переходе.
- кривизна заготовки на предшествующем переходе
Точение получистовое
Расчеты минимальных припусков заносим в графу 9
г) Расчеты номинальных промежуточных припусков
где - нижнее отклонение размеров соответственно на предшествующем и выполняемом переходе
- номинальный припуск на обработку внутренней поверхности
- минимальный припуск на обработку;
- верхнее отклонение размеров на предшествующем переходе;
- верхнее отклонение размеров на выполняемом переходе.
= 5582 + 1200 + 740 = 7522 мкм
= 828 + 740 + 300 = 1868 мкм
= 351 + 300 + 74 = 725 мкм
= 110 + 74 + 19 = 203 мкм
Расчеты номинальных промежуточных припусков заносим в графу 10
Номинальные принятые припуски
Точение получистовое:
Номинальные принятые припуски заносим в графу 11
д) Расчет промежуточных номинальных размеров
Расчет промежуточных номинальных размеров ведется путем последовательного сложения номинального диаметра готовой поверхности и номинальных промежуточных припусков.
А = 58 + 02 = 582 мм
А = 582 + 07 = 589 мм
А = 589 + 19 = 608 мм
А = 608 + 75 = 683 мм
Остальные припуски рассчитываем статистическим методом
допуски припуски мкм
Рисунок 2.1 –Эскиз заготовки вала
Степень сложности С1
Штамповочные уклоны 5 о
Неуказанные радиусы скруглений R5мм
Определяем массу заготовки по формуле:
где Vз – объем заготовки см3
- плотность материала заготовки гр см3
Определяем объем заготовки по формуле
где D – диаметр заготовки см
L – длина заготовки см
заг = V1 +V2 +V3 +V4 = 947 + 1660 + 908 + 238 = 3753 см3
Полученные значения подставляем в формулу (2.12)
mз = 3753 х 78 = 293 кг
Определим коэффициент использования металла заготовки.
где mд – масса детали кг
mз – масса заготовки кг
Значение подставляем в формулу (2.14)
Вывод: величина коэффициента использования материала в проектируемом варианте для получения поковки больше коэффициента использования материала в заводском варианте. Материал используется на 75%.
6 Выбор и обоснование баз
Рисунок 2.2 - Базовые поверхности
Выбор базовых поверхностей
7 Выбор мерительного и режущего инструмента
Выбранный режущий и контрольно-измерительный инструмент заносим в таблицу 2.6
Выбор режущего и мерительного инструмента
Мерительный инструмент
Фреза 2214-0397 ГОСТ 26595-85;
Сверло 2317-0122 ГОСТ 14952-75
Штангенциркуль ШЦ-III-250-800-005 ГОСТ 166-89;
Штангенциркуль ШЦ-I-125-001 ГОСТ 166-89
Резец MWLNR2525 М10;
Пластина 02144-100608
Пластина 03124-120408
Штангенциркуль ШЦ-I-125-001 ГОСТ 166-89;
Штангенглубиномер ШГ-200-001 ГОСТ 162-90;
АДК 8113.2083 h11 Калибр-скоба;
АДК 8113.2068 h11 Калибр-скоба
Резец 2103.0009 Т15К6
АДК 8113.2001 h11 Калибр-скоба;
Калибр-скоба 8113.0147 h9 ГОСТ 18360-93;
Штангенциркуль ШЦ-II-300-001 ГОСТ 166-89; АДК 8113.2083 h11 Калибр-скоба;
Фреза 2235.0053 №9 ГОСТ 9140-78
Штангенциркуль ШЦ-I-125-01 ГОСТ 166-89;
АДК 8158.4110 Калибр Б для контроля 75 +02;
АДК 8158.4111 Калибр М для контроля 75 +02;
АДК 8353.4511 Калибр;
АДК 8141.6448 Калибр
Сверло 2301.0020 Р6М5
Метчик 2620 - 1435.2 Р6М5
В8133.1848 7Н ОСТ 3-2660-75;
Калибр-пробка 8221.3044 7Н ГОСТ 17758-72
Сверло 2301.0069 Р6М5
Сверло 2301.0111 Р6М5
Зенкер 2320.2606 И8 ГОСТ 12489-71
Штангенциркуль ШЦ-I-125-005 ГОСТ 166-89;
Калибр-пробка 8133.0946 Н11 ГОСТ 14810-69;
АДК 8328.5097 Калибр
Круг шлифовальный 1500’ 50’ 305 25А 10-П С2 7 К1А 35мс 1кл. ГОСТ 2424-83
Калибр-скоба 8113.0150 h6 ГОСТ 18360-93;
Калибр-скоба 8113.0151 k6 ГОСТ 18360-93;
Калибр-скоба 8113.0150 h9 ГОСТ 18360-93;
Калибр-скоба 8113.0143 h6 ГОСТ 18360-93
Штангенциркуль ШЦ-III-300-001 ГОСТ 166-89
Сверло 2301.0076 Р6М5
Сверло 2301.0094 Р6М5
Штангенглубиномер ШГ-160-005 ГОСТ 162-90;
Калибр-пробка 8133.0936 H14 ГОСТ 14810-69;
АДК 8371.0006 Калибр
8 Расчёт режимов обработки и норм времени
8.1 Расчёт режимов обработки
Произведем расчет режимов резания на операцию 015 Токарную ЧПУ.
а) Определяем длину рабочего хода и заносим в таблицу 2.7
Lр.х.= l+lв.пмин (2.15)
где l- длинна резания мм
lв.п – величина врезания и перебега инструмента мм [13 стр. 373]
Lр.х 1.1 = 168 мм Lр.х 1.2 = 90 мм Lр.х 1.3 = 170 мм
б) Определяем глубину резания и заносим в таблицу 2.7.
в) Определяем подачу суппорта за оборот шпинделя в зависимости от шероховатости и обрабатываемого материала [13стр. 36]:
Корректируем подачу по паспорту станка:
Sкор1.1 = 025 ммоб Sкор1.2 = 025 ммоб Sкор1.3 = 02 ммоб
г) По табличным нормативам находим скорость резания [13стр. 45]:
Vтабл1.1 = 65 ммин Vтабл1.2 = 73 ммин Vтабл1.3 = 73 ммин
д) Рассчитываем число оборотов шпинделя по формуле:
где D-диаметр обрабатываемой поверхности мм
n11 = 272 обмин n1.2 = 319 обмин n1.3 = 308 обмин
Корректируем число оборотов шпинделя по паспорту станка:
nкор1.1 = 250 обмин nкор1.2 = 300 обмин nкор1.3 = 300 обмин
е) Определяем действительную скорость резания по формуле
Vфакт1.1 = 597 ммин Vфакт1.2 = 688 ммин Vфакт1.3 = 688 ммин
ж) Проверка результатов по мощности резания [13cтр. 48]:
з) Рассчитываем основное время по формуле:
где j- число рабочих ходов
То1.1 = 538 мин То1.2 = 12 мин То1.3 = 283 мин
Результаты расчетов занесем в таблицу (2.7).
Наименование операции и содержание перехода
Число оборотов п обмин
5 Фрезерно-центровальная
А: Установить закрепить снять
Фрезеровать торцы 1 2
Центровать торцы 1 2
Точить поверхности 4 3 с подрезкой торца 2
Точить поверхность 1
Точить поверхность 5 с подрезкой торца 7
Точить поверхность 4 с подрезкой торца 9
Точить поверхности 3 2 с подрезкой торца 1
5Вертикально-фрезерная
Фрезеровать паз 1 (предварит.)
5 Радиально-сверлильная
Сверлить 2 отверстия 1 (поочередно)
Зенковать 2 отверстия 1 (поочередно)
Нарезать резьбу в 2-х отверстиях 1 (поочередно)
5Вертикально-сверлильная
Сверлить отверстие 1
Рассверлить отверстие 1
Зенкеровать отверстие 1
5 Круглошли-фовальная
Шлифовать поверхность 1
Шлифовать поверхность 2
Шлифовать поверхность 3
Б:Переустановить закрепить снять
5 Токарно- винторезная
8.2 Расчёт норм времени
Техническая норма времени на обработку заготовки является одним из основных параметров для расчёта стоимости изготовляемой детали числа производственного оборудования заработной платы рабочих и планирования производства.
Техническую норму времени определяют на основе технических возможностей технологической оснастки режущего инструмента станочного оборудования и правильной организации рабочего места.
Норма времени является одним из основных факторов оценки совершенства технологического процесса.
В серийном производстве определяется норма штучно-калькуляционного времени:
Тшт.к.= Тшт. + Тп.з.п мин (2.20)
где Тшт. - норма штучного времени;
Тп.з - подготовительно-заключительное время на партию деталей мин;
п - количество деталей в партии шт.
Норма штучного времени определяется по формуле:
Тшт. = Топ + Тотд + Тобсл мин (2.21)
где Топ - оперативное время мин;
Тотд - время на отдых и личные надобности мин;
Тобсл - время на обслуживание рабочего времени мин.
Топ = То + Твсп мин (2.22)
где То - технологическое (основное) время мин;
Твсп - вспомогательное время мин.
Вспомогательное время находим по формуле:
Твсп = Ту + Тком + Тпер + Тконт мин (2.23)
где Ту - время на установку и снятие детали мин;
Тком - время не вошедшее в комплексы мин;
Тпер - время связанное с переходом мин;
Тконт - время на измерение и контроль деталей мин.
Точить поверхности 4 3 с подрезкой торца 2
Фрезеровать паз 1(окончат.)
Продолжение таблицы 2.8
Б:Переустановить закрепить
КОНСТРУКТОРСКИЙ РАЗДЕЛ
1 Описание принципа работы и устройства приспособления
Данное приспособление предназначено для фрезерования шпоночного паза в детали «Вал».
Приспособление устанавливают на стол станка так чтобы две шпонки(7) находящиеся в корпусе(1) были установлены в центральный паз стола по посадке и закрепляют при помощи болтов(15) гаек(16) и шайб(17). Шпонки(7) служат для правильной взаимной ориентации фрезы и заготовки в пространстве. Для обработки деталь устанавливают на призмы(4) упирают в упор(5) и фиксируют прихватами(3) прикрепленными шпильками(10) к корпусу. После наладки производится фрезерование шпоночного паза ось которого параллельна оси вала. Затем после обработки шпоночного паза деталь освобождают от зажима снимают с приспособления и укладывают на складочное место.
2 Расчёт необходимой силы зажима в приспособлении
Рисунок 3.1 – Схема сил действующих на заготовку.
Сила зажима определяется по формуле:
где К – коэффициент надежности закрепления;
М – крутящий момент от силы резания Н×м;
Dз – диаметр заготовки установленный на призму мм;
f1 f2 – коэффициенты трения;
-половина угла профиля призмы 0.
f1 = f2 = 025; [15; стр. 85]
Коэффициент надежности закрепления рассчитывается по формуле:
где К0 – коэффициент гарантированного запаса;
К1 – коэффициент учитывающий увеличение сил резания из-за неровности заготовки;
К2 – коэффициент учитывающий износ инструмента;
К3 - коэффициент учитывающий прерывистое резание;
К4 – коэффициент учитывающий непостоянство зажимного усилия;
К5 – коэффициент учитывающий удобство расположения рукояток;
К6 – коэффициент учитывающий наличие крутящего момента стремящегося повернуть заготовку.
К6 = 15 [15; стр. 85]
Крутящий момент рассчитывается по формуле:
где РZ – сила резания Н;
D – диаметр фрезы мм.
Сила резания определяется по формуле:
где СР – поправочный коэффициент;
t – глубина резания мм;
В – ширина шпоночного паза мм;
z – число зубьев фрезы;
D – диаметр фрезы мм;
n – частота вращения фрезы обмин;
x y u q w – показатели степени.
Кmp - поправочный коэффициент учитывающий качество обрабатываемого материала;
w = -013 [15; стр. 291]
где - предел прочности мПа;
n – показатель степени
n = 03 [15; стр. 264]
Полученные значения подставляем в формулу (3.4)
Полученное значение подставляем в формулу (3.3)
Полученные значения подставляем в формулу (3.1)
Так как приспособление изготовлено с двумя зажимами то сила зажима для каждого из них будет равна:
3 Конструирование и расчёт специального режущего инструмента
В качестве материала для державки резца выбираем сталь 50 ГОСТ1050-82 с =650 мПа и допустимым напряжением на изгиб =200 мПа. Вылет резца – стр. 104]
Определяем радиальную составляющую силы резания:
где Ср – поправочный коэффициент;
Кр – поправочный коэффициент.
где - допускаемое напряжение мПа;
n – показатель степени.
n=075 [15; стр. 264]
Полученные значения подставляем в формулу (3.8)
Все полученные значения подставляем в формулу (3.7)
Определяем сечение державки резца
Для прямоугольного сечения:
где b – ширина державки резца мм;
Руководствуясь приведенными соотношениями определяем высоту державки резца:
Проверяем прочность и жесткость державки резца
а) Максимальная нагрузка допускаемая прочностью резца:
б) Максимальная нагрузка допускаемая жесткостью резца:
где f – допускаемая стрела прогиба резца при окончательном точении мм;
Е – модуль упругости материала резца кгсм3;
У – момент инерции сечения корпуса м.
Е=2×105 мПа=20000 кгсм3 [10; стр. 102]
Полученные значения подставляем в формулу (3.13)
Резец обладает достаточными прочностью и жесткостью так как отвечает условию:
Конструктивные размеры резца выбираем по СТСЭВ 190-75
а) Общая длина резца L=140 мм
б) Расстояние от вершины резца по боковой поверхности в направлении главной режущей кромки n=6 мм
в) Пластина из твердого сплава Т15К6 длиной l=16 мм
г) Радиус закругления вершины головки резца R=05 мм
4 Конструирование и расчёт специального мерительного инструмента
Определяем исполнительные размеры калибра-скобы для вала диаметром d=75 мм с полем допуска к6 (+0021+0002)
Определяем наибольший и наименьший размеры вала:
где es – верхнее предельное отклонение мм.
где ei – нижнее предельное отклонение мм.
Определяем наименьший размер нового проходного калибра-скобы:
где Z1 – отклонение середины поля допуска на изготовление проходного калибра для вала относительно наибольшего предельного размера мм;
Н1 – допуск на изготовление калибров для вала мм.
Н1 = 0005 мм. [3; стр. 125]
Определяем наименьший размер непроходного калибра-скобы:
Определяем размер изношенного калибра-скобы:
где Y1 – допустимый выход размера изношенного проходного калибра для вала за границу поля допуска изделия мм.
Y1 = 0003 [3; стр. 125]
На основании произведенных расчетов строим схему расположения полей допусков калибра-скобы для вала ∅75к6 (+0021+0002)
Рисунок 3.2 – Схема расположения полей допусков калибр-скобы ∅75к6 (+0021+0002)
ОРГАНИЗАЦИОННЫЙ РАЗДЕЛ
1 Определение количества оборудования и коэффициента его загрузки.
Исходными данными для проектирования участка для механической обработки является чертёж детали технические условия по её изготовлению режим работы участка производственная программа технологический процесс изготовления и маршрут обработки детали а также схема расположения коммуникаций всех видов.
Для проектирования участка механической обработки необходимо рассчитать количество оборудования на каждую операцию.
Расчётное количество оборудования определяется по формуле:
Ср = Тшт.к.NгФд 60 с (4.1)
где Тшт.к. - время обработки детали на одной операции мин;
Nг - производственная программа шт.;
Фд - действительный годовой фонд времени работы металлорежущего
Коэффициент загрузки оборудования:
где Спр - принятое количество оборудования шт.
Действительный годовой фонд времени:
Фд = [(365 - ВД - ПД) 82 - ПД] Кр час (4.3)
где ВД - количество выходных дней в году;
ПД - количество праздничных дней в году;
Кр - коэффициент учитывающий время пребывания станка в
Полученные значения подставляем в формулу (4.3):
По формулам 4.1 и 4.2 определяем количество оборудования и коэффициент его загрузки для операций:
5 фрезерно-центровальная
Ср = 074 20001970 60 1 = 0013 шт.
Принимаем Ср = 1 станок.
Ср = 171 20001970 60 1 = 0029 шт.
Ср = 181 20001970 60 1 = 0031 шт.
5 вертикально-фрезерная
Ср = 165 20001970 60 1 = 0028 шт.
5 радиально-сверлильная
Ср = 11 20001970 60 1 = 0019 шт.
5 вертикально-сверлильная
Ср = 122 20001970 60 1 = 0021 шт.
5 круглошлифовальная
Ср = 139 20001970 60 1 = 0024 шт.
5 токарно-винторезная
Ср = 148 20001970 60 1 = 0025 шт.
Средний коэффициент загрузки оборудования
Строим график загрузки оборудования
Рисунок 4.1 - График загрузки оборудования
2 Организация транспортировки заготовок на участке
Организация транспортировки заготовок на участке имеет целью ликвидацию тяжёлых и трудоёмких работ и сокращение продолжительности производственного цикла.
Заготовки на участке поступают в специальных контейнерах которые подвозят на автокарах со склада заготовок. При обработке заготовок передача их по операциям от станка к станку производится не поштучно а небольшими транспортными партиями. При транспортировке обрабатываемых деталей от станка к станку также используются автокары.
Стружка с участка транспортируется мостовым краном в специальных коробках которые устанавливаются на автокары и увозят на участок её переработки и брикетирования.
3 Планировка оборудования и рабочих мест на проектируемом участке
Планировка оборудования и рабочих мест на участке механического цеха зависит от величины завода характера производства особенностей и объёма производственного здания габаритных размеров и массы обрабатываемых заготовок.
При планировке механического цеха все его отделения участки и вспомогательные помещения располагают так чтобы обеспечить прямоточность и последовательность прохождения материалов заготовок и изделий по стадиям обработки (без обратных и петлеобразных перемещений) максимальное использование производственной площади удовлетворить требования охраны труда техники безопасности и противопожарной безопасности.
При проектировании участка определении расстояния между станками расстоянии главных и второстепенных проходов габаритов транспортных средств и мест складирования обрабатываемых заготовок руководствуются следующими принципами:
- для серийного крупносерийного и массового производства применяется планировка по порядку технологических операций;
- станки располагают в порядке последовательности операций технологического процесса изготовления детали.
Планировку оборудования на участке выполняем в масштабе 1:100. Лёгкие и мелкие изделия изготавливают в цехах шириной 18 м с шириной крайних пролётов 8 м и среднего проезда 4 м шаг колонн t=6 м. В пролёте цеха устанавливаем мостовой кран грузоподъёмностью 10 т для транспортирования партий заготовок готовых изделий стружки монтажа и демонтажа технологического оборудования.
Станки изображаем условно в принятом масштабе. Место рабочего у станка обозначается кружком диаметром 500 мм. (в соответствующем масштабе) половина которого затушевывается карандашом. Светлая часть кружка обозначает лицо рабочего и должна быть обращена к станку.
Нормы расстояний между оборудованием и элементами здания приведены в [9].
При планировке участка механической обработки капсюля предусмотрены место для мастера и места для контролёра (контрольная площадка).
4 Разработка мероприятий по охране труда технике безопасности и
противопожарных мероприятий
Обеспечение охраны труда связано с профилактикой травматизма и заболеваемости а также созданием условий труда для сохранения работающими высокого уровня работоспособности в течении всего рабочего дня.
Обеспечение оптимальных режимов труда и отдыха способствует снижению утомляемости снижению травматизма и заболеваемости. Содействует увеличению работоспособности также повышение культуры производства учёт при создании оборудования принципов эргономики а при разработке интерьеров производственных помещений - принципов технической эстетики.
Во всех случаях к работающим предъявляют ряд специальных требований безопасности. В частности к работе они могут быть допущены после профессиональной подготовки и обучения безопасности труда и овладения необходимыми навыками её ведения.
Размещение производственного оборудования и коммуникаций которые являются источниками опасных и вредных производственных факторов расстояние между единицами оборудования а также между оборудованием и стенами производственных зданий сооружений и помещений должны соответствовать действующим нормам и правилам.
При организации рабочих мест руководствуются следующими принципами изложенными в ГОСТ 12.2.061-81. Конструкция рабочего места его размеры и взаимное расположение его элементов (органов управления средств отображения информации кресел вспомогательного оборудования и т.п.) должны соответствовать антропометрическим физиологическим и психофизиологическим данным человека а также характеру работы.
Конструкция рабочего места должна обеспечивать удобную рабочую позу человека.
Организация рабочего места должна обеспечивать устойчивое положение и свободу движений работающего безопасность выполнения трудовых операций исключить или допускать в редких случаях кратковременную работу в неудобных позах вызывающих утомлённость.
Общие принципы размещения технологической и организационной оснастки на рабочем месте можно сформулировать следующим образом:
- на рабочем месте не должно быть ничего лишнего всё необходимое для работы должно находиться в непосредственной близости от работающего но не мешать ему оснастка должна быть размещена так чтобы не приходилось принимать неудобные позы постоянно наклоняясь;
- те предметы которые берут левой рукой должны находиться слева а те предметы которые берут правой рукой - справа если используются обе руки место расположения оснастки выбирают с учётом удобства захвата её двумя руками;
- более опасная с точки зрения возможности травмирования работающего оснастка должна располагаться выше менее опасной оснастки однако при этом следует учитывать что тяжёлые предметы при работе удобнее и легче опускать чем поднимать;
- рабочее место не должно загромождаться заготовками и готовыми деталями организационной оснасткой.
Основные требования безопасности при работе на металлорежущих станках можно сформулировать следующие:
- перед установкой на станке обрабатываемые детали и приспособления особенно соприкасающиеся их базовые и крепёжные поверхности должны быть отчищены от стружки и масла;
- прежде чем приступить к работе на станке следует привести в порядок рабочую одежду застегнуть и подвязать обшлага рукавов надеть головной убор. Женщины должны убрать волосы под косынку подвязанную без свисающих концов;
- запрещается работать в рукавицах и перчатках а также с забинтованными пальцами без резиновых напальчников;
- при обработке хрупких материалов дающих отлетающую стружку а также при дроблении стальной стружки при обработке необходимо применять специальные очки или индивидуальные щитки для защиты лица;
- перед началом работы нужно проверить исправность крепления груза на тросе противовеса а на радиально-сверлильных станках – прочность крепления основания станка. Кроме того следует убедиться что обрабатываемые детали тиски и приспособления прочно и надёжно закреплены на станке. Крепление их производят специальными крепёжными деталями: болтами соответствующими пазу стола прижимными планками упорами и т.п. При работе нельзя применять патроны и приспособления с выступающими стопорными винтами и болтами. Выступающие части необходимо оградить.
- установку деталей на станок и снятие их со станка производят при отведённом в исходное положение шпинделе с режущим инструментом за исключением случая когда станок оснащён специальными многоместным приспособлением обеспечивающим загрузку детали вне рабочей зоны;
- при установке режущих инструментов следят за надёжностью и прочностью их крепления и правильностью зацентровки. Установку инструментов производят при полном останове станка;
- при смене инструментов шпиндель должен быть опущен. Смену инструмента на ходу станка разрешается производить только при наличии специального быстросменного патрона;
- нельзя устанавливать инструмент с затупившимися кромками в этом случае инструмент нужно заменить;
- нельзя пользоваться инструментами с изношенными конусными хвостовиками;
- режущий инструмент подводят к обрабатываемой детали постепенно плавно без удара;
- в процессе работы нельзя наклоняться близко к шпинделю и режущему инструменту;
- при обработке детали запрещается вводить руки в опасную зону;
- удерживать обрабатываемую деталь руками запрещается;
- в процессе обработки детали нельзя допускать скопления стружки удалять стружку только щёткой с ручкой;
- в случае заедания инструмента поломки его хвостовика и.п. станок необходимо выключить;
- при ослаблении крепления патрона инструмента и детали надо немедленно остановить станок. Крепить деталь приспособление или инструмент на ходу станка запрещается;
- перед остановом станка инструмент отводят от обрабатываемой детали. после выключения станка нельзя останавливать шпиндель и патрон нажимом руки и прикасаться к инструменту.
Для предотвращения возникновения пожара проводятся мероприятия организационные технические эксплуатационные и режимного характера.
К организационным мероприятиям относятся:
- обучение рабочих и служащих пожарной безопасности;
- проведение бесед лекций инструктажей.
Эксплуатационные мероприятия предусматривают:
- правильную эксплуатацию машин оборудования внутризаводского транспорта;
- своевременные регулярные осмотры установок и аппаратов их освидетельствование ремонт и испытания;
- правильное содержание зданий и территорий.
К техническим мероприятиям относятся соблюдение противопожарных правил и норм при проектировании зданий и сооружений устройстве электрических сетей и электрооборудования систем вентиляции отопления кондиционирования и т.п.
К мероприятиям режимного характера относят:
- запрещение проведения электрогазосварочных и других огневых работ в пожароопасных зонах помещения;
- запрещения курения в неустановленных местах и т.п.
5 Разработка мероприятий по охране окружающей среды
Наиболее эффективной формой защиты природной среды от выбросов промышленных предприятий является разработка и внедрение безопасных и малоотходных технологических процессов.
Безотходная технология - это активная форма защиты окружающей среды от вредного воздействия которая представляет собой комплекс мероприятий в технологических процессах от обработки сырья до использования готовой продукции в результате чего сокращается до минимума количество вредных выбросов.
К настоящему времени определились четыре основных направления в создании безотходных технологических процессов: разработка бессточных технологических систем и водооборотных циклов на базе существующих и перспективных способов очистки сточных вод; переработка отходов производства и потребления; разработка и внедрение принципиально новых технологических процессов позволяющих исключить образование основного количества отходов; создание территориально-промышленных комплексов с замкнутой структурой материальных потоков сырья и отходов внутри комплекса.
К пассивным методам защиты относят устройства и системы защиты окружающей среды которые применяют для очистки вентиляционных и технологических выбросов от вредных примесей рассеяния их в атмосфере очистки сточных вод глушения шума уменьшением уровней инфразвука ультразвука и вибраций на путях их распространения экранирование источников энергетического загрязнения окружающей среды.
Для очистки атмосферы от загрязнений широко применяют газо- пыле- и туманоулавливающие аппараты и системы.
Очистка сточных вод от механических примесей осуществляется процеживанием фильтрованием отделением механических частиц в поле действия центробежных сил от маслосодержащих примесей – отстаиванием обработкой в гидроциклах флотацией фильтрованием обработкой специальными реагентами.
Первичная обработка металлоотходов включает сортировку разделку и механическую обработку. Создаются специальные цехи для утилизации вторичных металлов.
Для уменьшения шума в окружающей среде применяют экраны кожухи глушители окна с повышенными звукоизолирующими свойствами зелёные насаждения между источниками шума и жилой застройкой.
Для снижения уровней вибраций необходимо виброактивное оборудование устанавливать на виброгасящие основания (фундаменты плиты) или на виброизоляторы (пружины резиновые пластмассовые прокладки пневмотические опоры и т.п.)
Важная роль в деле охраны окружающей среды отводится организационным мероприятиям и архитектурно-планировочным решениям выведение промышленных предприятий из крупных городов и сооружение новых в малонаселённых районах с малопригодными для сельского хозяйства землями с обязательным учётом топографии местности и розы ветров установление санитарно-защитных зон вокруг предприятия.
ЭКОНОМИЧЕСКИЙ РАЗДЕЛ
1 Определение стоимости основных материалов на проектируемую деталь
Расчет стоимости основных материалов производится по формуле:
где К – коэффициент учитывающий транспортно-заготовительные расходы;
- стоимость 1 кг. материала руб;
- стоимость 1кг. отходов руб;
- масса заготовки кг;
2 Расчет операционных расценок на проектируемую деталь
2.1 Определения потребного количества оборудования и затрат на него
Определяем расчет количества оборудования по формуле:
где Т - трудоёмкость выполнения отдельных операций нчас;
Fэ - действительный годовой фонд времени работы оборудования час;
Квр - коэффициент учитывающий загрузку оборудования по времени;
Квн - коэффициент выполнения норм;
Кбр - коэффициент учитывающий бригадную работу.
Операция токарная с ЧПУ
Принимаем один токарный станок с ЧПУ.
Определяем затраты на оборудование по следующей формуле:
где Кб - балансовая стоимость оборудования руб
Все данные для других операций заносим в таблицу 5.1 и 5.2
Затраты на оборудование
2.2 Определение потребного количества основных вспомогательных
Расчет численности основных производственных рабочих производится по формуле:
где Вп – годовой объем выпуска деталей шт;
F – действительный годовой фонд времени одного рабочего час.
Принимаем 1 станочника.
Для остальных операций данные заносим в таблицу 5.2.
Наименование операций
Вертикально-сверлильная
Количество вспомогательных рабочих (наладчиков слесарей контролеров) составляет 10-20% основных производственных рабочих:
Принимаем 1 слесаря.
Численность вспомогательных рабочих
Слесарь V разряда (проект)
Слесарь V разряда (завод)
Количество ИТР (технологи мастера) составляет 10-20% от общего количества основных и вспомогательных рабочих:
Принимаем 1 технолога.
2.3 Определение фонда основной заработной платы основных рабочих производственных рабочих
Расчет прямой заработной платы производится по каждой операции раздельно на основе часовых тарифных ставок и трудоемкости.
где Сч - часовые тарифные ставки согласно квалификации.
Остальные расчеты заносим в таблицы 5.7.
Прямая заработная плата основных рабочих
Круглошлифовальная Токарно-винторезная
Фонд премии составляет 60% от фонда премий заработной платы:
Фонд основной заработной платы основных производственных рабочих включает прямую заработную плату и премию:
Расчет основной заработной платы с районным коэффициентом определяется по формуле:
2.4 Определение фонда заработной платы вспомогательных рабочих и ИТР
Фонд заработной платы вспомогательных рабочих определяется на основе тарифных ставок (должностных окладов) отработанного времени и расчетного количества вспомогательных рабочих и ИТР определяется по формуле:
где Рвсп(ИТР) – расчетное количество вспомогательных рабочих и ИТР чел;
Овсп(ИТР) - среднемесячная заработная плата вспомогательных рабочих (должностные оклады и ИТР) руб.
Определяем среднемесячную заработную плату вспомогательных рабочих:
где Сч – часовая тарифная ставка рубчас;
t – продолжительность рабочей смены час;
S – количество смен в месяце.
Фонд премии вспомогательных рабочих составляет 50% от фонда заработной платы:
Фонд премии ИТР составляет 40% от фонда заработной платы:
Основная заработная плата вспомогательных рабочих с районным коэффициентом определяется по формуле:
Основная заработная плата вспомогательных рабочих на одну деталь:
Основная заработная плата ИТР с районным коэффициентом определяется по формуле:
Основная заработная плата ИТР на одну деталь:
2.5 Определение фонда дополнительной заработной платы основных производственных рабочих
где Кд - коэффициент учитывающий дополнительную заработную плату.
Определяем дополнительную заработную плату вспомогательных рабочих по формуле:
2.6 Определение отчислений в фонды
Размер отчислений в фонды страхования составляет 356% от суммы основной и дополнительной заработной платы:
где Ксоц - коэффициент учитывающий отчисления в фонды.
2.7 Расходы на содержание и эксплуатацию оборудования.
Определение затрат на силовую электроэнергию
где Т – трудоемкость операции н-час;
Nдв – суммарная мощность электродвигателей оборудования кВт;
Квр – коэффициент учитывающий загрузку оборудования по времени;
ККПД – коэффициент полезного действия;
Кс – коэффициент учитывающий потери электроэнергии в сети;
Цэ – стоимость 1 кВтчас электроэнергии руб;
qдв – коэффициент учитывающий одновременную работу двигателей оборудования;
Квн – коэффициент выполнение норм.
Последующие расчеты заносим в таблицы 5.6
Затраты на силовую электроэнергию
Амортизационное отчисление рассчитывается по формуле:
где Коб – затраты на оборудование руб
На – норма амортизационных отчислений %
Последующие расчеты заносим в таблицы 5.7
Амортизационные отчисления (проект)
2.8 Определение общецеховых расходов
Общецеховые расходы составляют 300% от основной заработной платы основных производственных рабочих:
3 Составление калькуляции цеховой себестоимости детали
Цеховая себестоимость – это сумма статей затрат на изготовление вала
Цеховая себестоимость
Наименование статей затрат
Затраты на материалы
Фонд основной заработной платы основных производственных рабочих
Фонд заработной платы:
вспомогательных рабочих
Дополнительная заработная плата:
основных производственных рабочих
Расходы на содержание и эксплуатацию оборудования:
1 затраты на силовую электроэнергию
2 амортизационные отчисления
Цеховая себестоимость:
4 Экономическая эффективность проекта
Основные технико-экономические показатели проекта сводим в таблицу.
Основные технико-экономические показатели проекта
Годовой объем выпуска заданного изделия
Численность основных рабочих
Выработка на одного основного рабочего
Количество единиц оборудования
Общая стоимость оборудования
Суммарная мощность оборудования
Себестоимость единицы изготовления изделия
Разработка технологического процесса изготовления вала основанная на ресурсах предприятия позволила:
- использовать метод получения заготовки- поковку полученную методом штамповки на горячештамповочном прессе приближенную размерами к готовой детали что дает возможность сократить расход материала уменьшить затраты на режущий инструмент технологическую оснастку электроэнергию и прочее;
- ввести фрезерно-центровальную операцию что позволит снизить трудоемкость обработки и вспомогательное время на изготовление детали;
- использовать токарный станок с числовым программным управлением что позволит снизить трудоемкость и время на обработку детали;
- применение специального приспособления с пневмозажимом для фрезерования шпоночного паза что позволило сократить время на установку детали.
Себестоимость изготовления вала составила 760345 руб. Также в дипломном проекте разработаны мероприятия по охране труда и технике безопасности.
Белоусов А.П. Проектирование станочных приспособлений: Учебное пособие для учащихся техникумов. - М.: Высшая школа 1980.-240 с. ил.
Горошкин А.К. Приспособление для металлорежущих станков. - М.: Машгиз 1962.
Добрыднев И.С. Курсовое проектирование по предмету «Технология
машиностроения»: Учебное пособие для техникумов. - М.: Машиностроение
Журавлёв В.Н. Николаева О.И. Машиностроительные стали: Справочник. - М.: Машиностроение 1992.-480 с. ил.
Зенкин А.С. Петко И.В. Допуски и посадки в машиностроении. Справочник - К.: Техника 1990.-320 с.
Козьяков А.Ф. Морозова Л.Л. Охрана труда в машиностроении: Учебник для
учащихся средних специальных учебных заведений. - М.: Машиностроение
Марочник сталей и сплавовМ.М. Колосков Е.Т. Долбенко Ю.В. Каширский и др.; Под общей ред. А.С. Зубченко - М.: Машиностроение 2001.-672 с. ил.
Медовой И.А. и др. Исполнительные размеры калибров: Справочник. В 2-х. кн. Кн.1И.А. Медовой Я.Г. Уманский Н.М. Журавлёв - М.: Машиностроение 1980.-384 с. ил.
Нефёдов Н.А. Дипломное проектирование в машиностроительных техникумах: Учебное пособие для техникумов. - М.: Высшая школа 1986.-239 с. ил.
Нефёдов Н.А. К.А. Осипов Сборник задач и примеров по резанию металлов
и режущему инструменту: Учебное пособие для техникумов. - М.:
Машиностроение 1990.-448 с. ил.
Обработка металлов резанием: Справочник технологаА.А. Панов В.В. Аникин Н.Г. Бойм и др.; Под общ. Ред. А.А. Панова. - М.: Машиностроение 1988.-736 с. ил.
Общемашиностроительные нормативы времени вспомогательного на
обслуживание рабочего места и подготовительно-заключительного для
технического нормирования станочных работ.
Серийное производство. - М.: Машиностроение 2001.
Общемашиностроительные нормативы режимов резания для технического
нормирования работ на металлорежущих станках. Часть I. - М.:
Машиностроение 1974.-406 с.
Справочник технолога-машиностроителя. В 2-х. т. Т1Под ред.
А.М. Дальского А.Г. Косиловой Р.К. Мещерякова и А.Г. Суслова. - М.:
Машиностроение 2001.-912 с. ил.
Справочник технолога-машиностроителя. В 2-х. т. Т2Под ред.
Машиностроение 2001.-944 с. ил.
Экономика предприятия. Под ред. Волкова В.И. – М: Высшая школа 2005.
НТ5.cdw

Радиально-сверлильный станок ГС 544
Наименование оперции
и содержание перехода
ДП.15.02.08.017.11.000.НТ5
НТ4.cdw

Вертикально-фрезерный станок 400V
Наименование оперции
и содержание перехода
ДП.15.02.08.017.11.000.НТ4
НТ3.cdw

Наименование оперции
и содержание перехода
ДП.15.02.08.017.11.000.НТ3
Приспособление для фрезерования.cdw

*Размеры для справок.
Размер контрольного валика.
НТ7 устБ.cdw

Круглошлифовальный станок 3М151
Наименование оперции
и содержание перехода
Шлифовать поверхность 1
Шлифовать поверхность 2
ДП.15.02.08.017.11.000.НТ7
НТ8.cdw

Токарно-винторезный станок 1М63
Наименование оперции
и содержание перехода
Сверлить отверстие 1
ДП.15.02.08.017.11.000.НТ8
НТ6.cdw

Вертикально-сверлильный станок 2Н135
Наименование оперции
и содержание перехода
ДП.15.02.08.017.11.000.НТ6
НТ7 устА.cdw

Круглошлифовальный станок 3М151
Наименование оперции
и содержание перехода
Шлифовать поверхность 1
Шлифовать поверхность 2
Шлифовать поверхность 3
ДП.15.02.08.017.11.000.НТ7
Спецификация 2.2.cdw

Спецификация для калибр-скобы.cdw

Спец. к резцу. компас 5cdw.cdw

Спецификация 2.1.cdw

Спецификация для плана участка.cdw

Технологическое оборудование
Токарный с ЧПУ 16М30Ф3
Радиально-сверлильный ГС544
Склад готовых изделий
Токарно-винторезный 1М63
Фрезерно-центровальный 2982
Подъемно - транспортное
Вертикально-сверлильный 2Н135
Круглошлифовальный 3М151
Тара с полуфабрикатами
чертеж детали.cdw

ДП.15.02.08.017.11.000.ЧД
Сталь 38ХС ГОСТ 4543-71
заготовка.cdw

Степень сложности поковки С1.
Точность изготовления поковки Т3.
Радиусы скруглений R 5мм.
Сталь 38ХС ГОСТ 4543-71
ДП.15.02.08.017.11.000.ТШ
НТ1.cdw

Фрезерно-центровальный станок 2982
Наименование оперции
и содержание перехода
ДП.15.02.08.017.11.000.НТ1
НТ2.cdw

Наименование оперции
и содержание перехода
Точить поверхность 1
ДП.15.02.08.017.11.000.НТ2
Резец прямой проходной.bak.cdw

Материал державки: сталь 50 ГОСТ 1050-88.
Пластину паять припоем Л63 ГОСТ 15527-70.
Маркировать: ДП.15.08.017.11.000.РИ.
ДП.15.02.08.017.11.000.РИ
План участка.cdw

Калибр-скоба.cdw

Маркировать: ДП.15.02.08.017.11.000.МИ
Маркировать: D (НЕ) = 74
Маркировать: D (ПР) = 75
ДП.15.02.08.017.11.000.МИ
Рекомендуемые чертежи
- 04.11.2022