Diploma project of the office center with underground garage


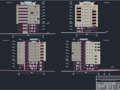
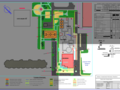
- Added: 02.02.2021
- Size: 13 MB
- Downloads: 1
Description
Thesis, Drawings, PP, Design Solutions
Project's Content
![]() ![]() ![]() |
![]() ![]() ![]() ![]() |
![]() ![]() ![]() |
![]() ![]() ![]() |
![]() ![]() ![]() |
![]() ![]() ![]() |
![]() ![]() ![]() |
![]() ![]() ![]() ![]() |
![]() ![]() ![]() |
![]() |
![]() |
![]() ![]() ![]() |
![]() ![]() ![]() ![]() |
![]() ![]() ![]() |
![]() ![]() ![]() ![]() |
![]() ![]() ![]() |
![]() ![]() ![]() |
Additional information
Contents
CONTENTS
INTRODUCTION
1. ARCHITECTURAL AND CONSTRUCTION SOLUTIONS
1.1. Geotechnical and climatic characteristics of the construction site
1.1.1. Geological characterization
1.1.2. Hydrogeological conditions
1.2. Architectural solution
1.2.1. Master Plan
1.2.2. Technological solutions
1.2.3. Volumetric planning solutions
1.3. Main decisions to ensure the living conditions of people with limited mobility
1.4. finishing
1.4.1. Exterior decoration
1.4.2. Interior decoration
1.5. technical and economic indicators of the master plan
1.6. Heat Engineering Calculation
1.7. Calculation of evacuation time from the floor
2. DESIGN SOLUTIONS
2.1. constructive solution
2.1.1. Design solution of underground parking garage
2.1.2. Office Center Design Solution
2.2. Calculation of office structures
2.2.1. Collection of loads on the paving slab
2.2.2. Collecting Loads on Slab
2.2.3. Column Calculation
2.2.4. Calculation of slab
2.2.5. Calculation for push-through
2.2.6. The results of the calculation of the plate in the Lira 9 program complex.
3. TECHNOLOGY, ORGANIZATION AND ECONOMICS OF CONSTRUCTION
3.1. calculation of standard construction duration
3.1.1. Preparatory period
3.1.2. Selection of installation crane
3.1.3. Determination of nomenclature, volumes, labor intensity, machine capacity and standard duration of construction
3.2. Routing for erection of monolithic floor slab of standard floor
3.2.1. Scope of Application
3.2.2. Procedure and organization of works performance
3.2.3. List of process accessories, tools, equipment and accessories
3.2.4.Qualification and acceptance requirements
3.2.5. Costing Labor and Machine Time
3.2.6. Work Schedule
3.3. Construction plot plan of the facility
3.3.1. Calculation of the area of temporary buildings
3.3.2. Calculation of storage areas
3.3.3. Calculation of temporary water supply
3.3.4. Calculation of water pipe diameters
3.3.5. Temporary power supply of construction site
3.3.6. Temporary roads
3.4. Estimate
4. OCCUPATIONAL SAFETY
4.1. Safety precautions during formwork
4.2. Safety precautions during reinforcement works
4.3. Safety precautions during concrete works
4.4. Safety precautions during installation works
4.5. Safety precautions during roofing works
4.6. Engineering solutions (tasks)
4.7. fire-fighting measures
APPLICATION
LIST OF LITERATURE
CONTENTS
7.4.1.1. The choice of earth-moving machines. Error! Bookmark is not defined
7.4.1.2. Choice of cars - dump trucks Error! Bookmark is not defined
7.4.2. Selection of set of machines for installation works Error! Bookmark is not defined
7.4.2.1. Technical and economic comparison of installation mechanization options. Error! Bookmark is not defined
7.4.2.2. Selection of lifting mechanisms for erection of structures Error! Bookmark is not defined
7.5.Define duration of works. Error! Bookmark is not defined
7.6. Object Construction Plan. Error! Bookmark is not defined
7.6.1. Calculation of temporary administrative buildings. Error! Bookmark is not defined
7.6.2. Calculation of warehouses of building materials and structures. Error! Bookmark is not defined
7.6.3. Calculation of temporary water supply. Error! Bookmark is not defined
7.6.4. Calculation of temporary power supply. Error! Bookmark is not defined
7.6.5. Heat supply of construction site and building. Error! Bookmark is not defined
7.6.6. Technical and economic indicators. Error! Bookmark is not defined
8. ECONOMY OF CONSTRUCTION IS A MISTAKE! BOOKMARK NOT DEFINED
Local estimate # 06-10-02 Error! Bookmark is not defined
Local Estimate Calculation # 1 Error! Bookmark is not defined
Local Estimate Calculation # 2 Error! Bookmark is not defined
Local Estimate Calculation # 3 Error! Bookmark is not defined
Local Estimate Calculation # 4 Error! Bookmark is not defined
Object estimate Error! Bookmark is not defined
Summary Estimate Error! Bookmark is not defined
Contract Price Error! Bookmark is not defined
Settlements to contract price Error! Bookmark is not defined
Calculation of technical and economic indicators of the project Error! Bookmark is not defined
9. SECURITY THERE IS A MISTAKE! BOOKMARK NOT DEFINED
9.1. The task of labor protection in construction Error! Bookmark is not defined
9.2. Design and aesthetics of the construction site Error! Bookmark is not defined
9.3. Analysis of hazardous and harmful production factors at the construction site Error! Bookmark is not defined
9.4. Safety precautions for erection of metal structures of medium-grade rolling mill building Error! Bookmark is not defined
9.5. Roofing Safety Error! Bookmark is not defined
9.6. Calculation of the crossbeam for mounting a metal truss with a span of 36 m Error! Bookmark is not defined
10. ABSTRACT ERROR! BOOKMARK NOT DEFINED
LIST OF USED LITERARY SOURCES ERROR! BOOKMARK NOT DEFINED
1.1. Shared Part Error! Bookmark is not defined
1.2. Volumetric planning solution Error! Bookmark is not defined
1.3. Constructive Solution Error! Bookmark is not defined
1.4. Thermal calculation of the wall fence Error! Bookmark is not defined
4. DESIGN PART ERROR! BOOKMARK NOT DEFINED
4.1. Frame Layout Error! Bookmark is not defined
4.1.1. Characteristics of design frame cranes. Error! Bookmark is not defined
4.1.2. Vertical Frame Dimensions Error! Bookmark is not defined
4.1.3. Horizontal Frame Dimensions Error! Bookmark is not defined
4.1.4. Coating Constructions Enclosing Constructions Error! Bookmark is not defined
4.1.5. Link Schemas Error! Bookmark is not defined
4.2. Determining Frame Loads Error! Bookmark is not defined
4.2.1. Constant loads Error! Bookmark is not defined
4.2.2. Snow load Error! Bookmark is not defined
4.2.3. Wind load on the design frame Error! Bookmark is not defined
4.2.4. Crane loads Error! Bookmark is not defined
4.3. Static Frame Calculation Error! Bookmark is not defined
4.3.1.Frame calculation diagram Error! Bookmark is not defined
4.3.2. Static frame calculation. Error! Bookmark is not defined
4.3.3. Frame loading diagrams. Error! Bookmark is not defined
4.4. Calculation and construction of a rafter truss (span A - B). Error! Bookmark is not defined
4.4.1. Farm loads. Error! Bookmark is not defined
4.4.2. Calculation of the farm. Results. Error! Bookmark is not defined
4.4.3. Material and calculated lengths of truss elements Error! Bookmark is not defined
4.4.4. Picking Rod Sections Error! Bookmark is not defined
4.4.4.1. Top Belt Error! Bookmark is not defined
4.4.4.2. Lower Belt Error! Bookmark is not defined
4.4.4.3. Reference brace Error! Bookmark is not defined
4.4.4.4. Braces Error! Bookmark is not defined
4.4.4.5. Racks Error! Bookmark is not defined
4.4.5. Calculation of nodes Error! Bookmark is not defined
4.5. Calculation and Design of Crane Beam Error! Bookmark is not defined
4.5.1. Definition of crane loads Error! Bookmark is not defined
4.5.2. Static Beam Calculation Error! Bookmark is not defined
4.5.3. Dimensioning the cross section of the crane beam Error! Bookmark is not defined
4.5.4. Checks Error! Bookmark is not defined
4.5.4.1. Check the strength of the lower (stretched) belt: Error! Bookmark is not defined
4.5.4.2. Checking tangent stresses: Error! Bookmark is not defined
4.5.4.3. Check beam stiffness: Error! Bookmark is not defined
4.5.4.4. Check of local stability of beam wall Error! Bookmark is not defined
4.5.4.5. Strength check. Error! Bookmark is not defined
4.5.5. Calculation of reference edge Error! Bookmark is not defined
4.5.6. Check waist welds Error! Bookmark is not defined
4.6. Calculation of the middle column of row B. Error! Bookmark is not defined
4.6.1. Design forces and combinations. Error! Bookmark is not defined
4.6.2. Layout of the column. Error! Bookmark is not defined
4.6.3. Defines the estimated column lengths. Error! Bookmark is not defined
4.6.4. Select a section and check column features. Error! Bookmark is not defined
4.6.4.1. Select the section of the crane part of the column. Error! Bookmark is not defined
4.6.4.2. Calculation of the connection grid. Error! Bookmark is not defined
4.6.4.3. Check stability of the crane part of the column (as a single rod) Error! Bookmark is not defined
4.6.4.4. Select a section and check the top of the column. Error! Bookmark is not defined
4.6.4.5. Calculation of column base. Error! Bookmark is not defined
5. FABRICATION OF METAL STRUCTURES ERROR! BOOKMARK NOT DEFINED
5.1. Metal Treatment Error! Bookmark is not defined
5.1.1. Process Plans During Processing Error! Bookmark is not defined
5.1.2. Calculation of equipment and number of workers for processing Error! Bookmark is not defined
5.2. Assembly Works Error! Bookmark is not defined
5.2.1. Process Plan Error! Bookmark is not defined
5.2.2. Technocart for assembly works Error! Bookmark is not defined
5.2.3. Determine the number of jobs and workers. Error! Bookmark is not defined
5.3. Variant part - comparison of lateral and longitudinal directions of technological processes in the shop Error! Bookmark is not defined
5.4. Technical and Economic Parameters of Structural Manufacturing Error! Bookmark is not defined
5.4.1. Manufacturing Cost of Structures Error! Bookmark is not defined
5.4.2. Remove products from 1 m2 of production areas of the assembly shop, t/m2 Error! Bookmark is not defined
5.4.3. Annual production per one worker in the shop, t Error! Bookmark is not defined
6. BASES AND FOUNDATIONS ERROR! BOOKMARK NOT DEFINED
6.1. Site geotechnical analysis Error! Bookmark is not defined
6.2. Calculation of pile foundations. Error! Bookmark is not defined
6.2.1. Select the depth of the pile pile. Error! Bookmark is not defined
6.2.2. Selects a structural layer. Error! Bookmark is not defined
6.2.3. Pile foundation calculation for row B column Error! Bookmark is not defined
6.2.3.1. Determination of pile bearing capacity. Error! Bookmark is not defined
6.2.3.2. Design load on the pile Error! Bookmark is not defined
6.2.3.3. Location of piles in plan, requirements for pile pile design. Error! Bookmark is not defined
6.2.3.4. Actual pile load, vertical and horizontal foundation size assignment Error! Bookmark is not defined
6.2.3.5. Calculation for pressing. Error! Bookmark is not defined
6.2.3.6. Selection of valves. Error! Bookmark is not defined
6.2.3.7. Pressure check under the lower end of the pile. Error! Bookmark is not defined
6.2.3.8. Settlement calculation by layer-by-layer summation. Error! Bookmark is not defined
6.2.4. Pile foundation calculation for row A column Error! Bookmark is not defined
6.2.4.1. Determination of pile bearing capacity. Error! Bookmark is not defined
6.2.4.2. Design load on the pile Error! Bookmark is not defined
6.2.4.3. Location of piles in plan, requirements for pile pile design. Error! Bookmark is not defined
6.2.4.4. Actual pile load, vertical and horizontal foundation size assignment Error! Bookmark is not defined
6.2.4.5. Calculation for pressing. Error! Bookmark is not defined
6.2.4.6. Selection of valves. Error! Bookmark is not defined
6.2.4.7. Pressure check under the lower end of the pile. Error! Bookmark is not defined
6.2.4.8. Settlement calculation by layer-by-layer summation. Error! Bookmark is not defined
7. ORGANIZATION OF CONSTRUCTION MANAGEMENT ERROR! BOOKMARK NOT DEFINED
7.1. Split the main building into grabs. Error! Bookmark is not defined
7.2. Determination of nomenclature and scope of construction and installation works. Error! Bookmark is not defined
7.3. Selection of the method of work execution. Error! Bookmark is not defined
7.4. Selection of a set of machines and mechanisms. Error! Bookmark is not defined
7.4.1. Select a set of earthworks. Error! Bookmark is not defined
7.4.1.1. The choice of earth-moving machines. Error! Bookmark is not defined
7.4.1.2. Choice of cars - dump trucks Error! Bookmark is not defined
7.4.2. Selection of set of machines for installation works Error! Bookmark is not defined
7.4.2.1. Technical and economic comparison of installation mechanization options. Error! Bookmark is not defined
7.4.2.2. Selection of lifting mechanisms for erection of structures Error! Bookmark is not defined
7.5.Define duration of works. Error! Bookmark is not defined
7.6. Object Construction Plan. Error! Bookmark is not defined
7.6.1. Calculation of temporary administrative buildings. Error! Bookmark is not defined
7.6.2. Calculation of warehouses of building materials and structures. Error! Bookmark is not defined
7.6.3. Calculation of temporary water supply. Error! Bookmark is not defined
7.6.4. Calculation of temporary power supply. Error! Bookmark is not defined
7.6.5. Heat supply of construction site and building. Error! Bookmark is not defined
7.6.6. Technical and economic indicators. Error! Bookmark is not defined
8. ECONOMY OF CONSTRUCTION IS A MISTAKE! BOOKMARK NOT DEFINED
Local estimate # 06-10-02 Error! Bookmark is not defined
Local Estimate Calculation # 1 Error! Bookmark is not defined
Local Estimate Calculation # 2 Error! Bookmark is not defined
Local Estimate Calculation # 3 Error! Bookmark is not defined
Local Estimate Calculation # 4 Error! Bookmark is not defined
Object estimate Error! Bookmark is not defined
Summary Estimate Error! Bookmark is not defined
Contract Price Error! Bookmark is not defined
Settlements to contract price Error! Bookmark is not defined
Calculation of technical and economic indicators of the project Error! Bookmark is not defined
9. SECURITY THERE IS A MISTAKE! BOOKMARK NOT DEFINED
9.1. The task of labor protection in construction Error! Bookmark is not defined
9.2. Design and aesthetics of the construction site Error! Bookmark is not defined
9.3. Analysis of hazardous and harmful production factors at the construction site Error! Bookmark is not defined
9.4. Safety precautions for erection of metal structures of medium-grade rolling mill building Error! Bookmark is not defined
9.5. Roofing Safety Error! Bookmark is not defined
9.6. Calculation of the crossbeam for mounting a metal truss with a span of 36 m Error! Bookmark is not defined
10. ABSTRACT ERROR! BOOKMARK NOT DEFINED
LIST OF USED LITERARY SOURCES ERROR! BOOKMARK NOT DEFINED
Introduction
Offices and business centers are one of the main segments of the commercial real estate market. Renting offices and premises is becoming more and more relevant not only for large companies, but also for small businesses, entrepreneurs, and various organizations. The construction of business centers beyond the Moscow Ring Road is becoming a trend.
Until this year, the construction of business centers on the outer circumference of the Moscow ring road was rare. The first such office center was Country Park, built in 2004 in the city of Khimki near Moscow, Savatsky Group of Companies. Now the complex has no shortage of tenants, however, despite the modest size - 16 thousand square meters. meters - its areas were filled for about a year. In 2005, another business center appeared behind the Moscow Ring Road - the "1st km" on the Rublevskoye highway.
Potential tenants of office premises located in the vicinity of the Moscow Ring Road are companies that are not focused on customer flow: callcenters, firms engaged in ITtechnologies, as well as logistics structures, distributors and retailers, whose terminals and stores are located outside the ring road. Of course, the center will remain highly attractive for all kinds of representative offices, service companies or companies specializing in premium goods and services, but many managers are now going to separate the office: representative - in the center, worker - on the periphery.
The most serious problem that scares off tenants from business centers outside the Moscow Ring Road is due to reduced transport accessibility. A sufficient number of parking spaces should be provided in the office center and transport links should be provided so that employees without a car can easily get to the office. Be that as it may, all experts are confident that in the future the number of business centers outside the Moscow Ring Road will grow.
The realities of the market are such that in the city center there is still not enough space for everyone. Rental rates here will still increase, and those who are not ready to overpay for prestige will have to gradually transfer their offices closer to the outskirts of the city or beyond.
Architectural and construction solutions
1.1. GEOTECHNICAL AND CLIMATIC CHARACTERISTICS OF CONSTRUCTION SITE
1.1.1. Geological characterization.
Geologically, the construction site, within the explored stratum, is represented by the following engineering and geological elements:
Layer-1- bulk layer. Power 0.81.5 m. They are ubiquitous.
Layer-2, 2a, - Yellowtail loam, yellowtail in the roof, dusty, with rare limestone wood, soft plastic (Layer-2). The layer with a capacity of up to 0.91.8m is ubiquitous. The layer occurrence interval is from 0.81.5 to 2.02.6 m.
According to static probing, made after prolonged heavy rains at the same points in the same interval, loam of soft-plastic consistency became loam of fluidized-plastic consistency (Layer 2a).
Layer 3, 3a - Grayish-brown loam with soaps of gray and yellow, heavily deserted, in some places facially replaced by light clays, with interlayers and lenses of sand of small, medium density, saturated with water, up to 5 cm in power, refractory (Layer -3), soft plastic (Layer 3a). The layer with a total capacity of 0.7 to 2.2m is ubiquitous, the occurrence interval is from 2.02.6 to 3.14.4m.
Layer 4, 4a, - Loam is reddish-bored, heavily desiccated, in the roof with numerous layers of sand of fine, saturated with water, up to 0.5 m in thickness, refractory (Layer -4), to soft-plastic (Layer 4a). The layer with a total thickness of 1.6 to 4.6 m, the occurrence interval from 3.14.4m to 6.06.8 m, was opened everywhere.
Layer 5, 5a - Clay is brown, grayish-brown in the sole is dark gray, slightly deserted, in some places facially replaced by loams with wood and crushed stone limestone up to 20%, in the sole is solid (Layer -5), in the roof semi-solid (Layer 5a). Maximum open layer power 14 m.
1.1.2. Hydrogeological conditions
During the survey period - early June 2005, wells up to 20 m deep opened one aquifer of the headwater type at a depth of 1,63.4m, which corresponds to absolute elevations of 169,60171.90. The steady state level was recorded at a depth of 0.61.5m, which corresponds to absolute elevations of 171.50172.70. The horizon is quite water-rich, elephant, with a head value of 0.61.6m. Water-containing soils are sands in the thickness of loam and bulk sandy-loam soils. The horizon is ubiquitous and has now become permanent (due to poor surface runoff conditions and small filtration rates for loams), as it is opened by all wells passed in March, September, late November and early June, as also evidenced by the overwetting of loams Layer 3a, 4a (residual phenomenon of the headwater). The power source is infiltration of surface water and leakage of man-made water.
Groundwater level is subject to seasonal fluctuations and during the period of hydrogeological maxima water level should be expected to rise by 0.1 m
Water is not aggressive with respect to normal density concrete.
Soils are non-aggressive to concrete of all grades and to reinforced concrete structures.
1.2 ARCHITECTURAL SOLUTION
1.2.1. MASTER PLAN
The construction site is located in the western part of Mytishchi, Moscow Region, on Kolpakova Street, mn. 18. Kargin Street overlooks Volkovskoye Shosse, which, in turn, goes to the Moscow Ring Road.
The site is surrounded by a residential building. On the north and north-east sides are residential buildings. On the northwest side of the kindergarten. On the southwestern and southern sides is ul. Kolpakova. On the eastern side is Mytishchi Heating Network JSC.
1.2.2. TECHNOLOGICAL SOLUTIONS
Technological solutions of the project for the construction of an office center with an underground garage at the address Mytishchi MO, 18 μr, ul. Kolpakova were completed on the basis of the design task and in compliance with the requirements of the current norms and rules:
SNiP 2.08.0289 * "Public buildings and structures,"
SNiP 2.09.0487 * "Administrative and residential buildings ,"
SNiP 210299 "Parking,"
SanPin 2.2.4.54896 "Hygienic requirements to microclimate of production premises";
ONTP-01-91 "Norms of technological design of road transport enterprises"
SanPiN 2.2.2 ./2.4.134003 "Hygienic requirements for personal electronic computing machines and organization of work."
An office center with an underground garage is envisaged for construction in the following composition:
- underground a garage parking in axes 1-7 and Zh-E,
- office center located in axes 1-6 and A-E.
Office Center:
The office center is designed to accommodate the administrative services of various organizations (as a rule, these are companies that are not focused on customer flow: callcenters, ITTe firms, as well as logistics structures, distributors and retailers whose terminals and stores are located outside the ring road). In addition to two escape stairs for employees and visitors to the office building, there are three elevators with spacious elevator halls. For ease of work, the building provides meeting rooms on all floors except the first, as well as a conference hall on the fifth floor. To provide office staff with hot meals, a self-catering cafe is provided on the ground floor.
You can assign class B to this office center. It meets all the classification criteria for this group of office buildings and business centers (the criteria are given in Appendix 1).
Service parking:
The project provides for the organization of closed-type service parking with a capacity of 73 cars intended for personal vehicles of employees of the office center.
The parking room (axes 1-7 and Zh-E) in the plan has dimensions of 54.0x18.6m and covers a total area of 2927 m2.
The parking lot has an entrance from the side of ul. Kolpakova. On a double-track entrance ramp, cars come to the parking lot. At the entrance to the ramp is a checkpoint. The parking lot has four evacuation stairs and access to the first floor of the office center.
The parking planning solution provides for a storage room for cars and technical premises.
In the storage room of cars, car parking lots are not fenced off, the method of storing cars is arena, the size of cars is 6.6x3.3 m. Wheelbarrow devices along the walls are provided in the storage places. The movement of cars is organized along internal driveways. The width of the carriageway in the narrowest place is 6.6 m.
The parameters of the parking areas and the width of the internal passageways provide the possibility of accommodating cars.
The nomenclature and number of cars are accepted in accordance with the task for the development of documentation and are specified during the development of the working project .
Parking building for explosion and fire hazard belongs to category B (NPB 1052003).
Evacuation exits are provided from each car storage room in accordance with the standards (SNiP 210197 *), the distance between exits is 40 m.
Cars arriving at the parking lot come through the checkpoint, where the arrival of the car is recorded in the register, which is located at the guard.
Then the car is sent to the place attached to it.
When the car leaves, the fact of departure is recorded.
To monitor moving cars at the entrance and exit from the parking lot, viewing glasses are provided in the checkpoint room.
Parking floor cleaning - dry, mechanized, harvesting machines.
The total analysis of cars on the most busy days, in% of the total number of parking spaces - 80%.
1.2.3. SPACE PLANNING SOLUTIONS
The office center is divided into an underground parking lot located in axes 1-7 and Zh-E and an office center located in axes 1-6 and A-E.
One of the parts of the center - office - is a 9-storey volume, with dimensions in the axes of 26.4 x 33 m.
Maximum elev. at an altitude of 38.85 m.
On the ground floor (elev. + -0.000) of the building there is an entrance group (lobby, wardrobe, security, stair lift unit), a cafe with a dining room with 80 seats, with a kitchen and utility rooms, an electric shield and a ventilation chamber.
Floors two through nine are occupied by office space. On each floor there are also 2 meeting rooms, on the fifth floor there is a conference hall. The height of the floors is 3.9 m.
Functional communication between floors is carried out by elevators, one of which is provided for transportation of fire departments (SNiP I0197 *).
Evacuation of people from each floor is provided by two stairs of the 1st type. Both stairs are unnamed:
- one - H1 (with output directly to the outside);
- the other - H2 (with exit to the outside through the lobby).
The second part of the complex is an underground parking garage.
Dimensions in axes 39.6 x 86.22 m, floor height 2.9 m.
Evacuation of people is carried out directly outside along one of three stairs.
Access to the floor of the parking garage is carried out using a double-track open ramp.
Due to the fact that this parking garage is intended for the office part of the complex, communication is provided between them at el. - 3.900 via tambour-gateway.
The office center has a basement for technical purposes (at el. -3.700). Evacuation from the basement is carried out along three dispersed stairs with access directly to the outside.
Parking garage rooms - not heated.
For the characteristics of building structures, see Table 3.
See Table 4 for technical data on the materials used below.
Refer to Table 5 for a description of the interior finish materials used in the design.
Liability Class I.
Degree of fire resistance of the high-altitude part - I,
The degree of fire resistance of the low part is II.
Structural fire hazard class C-I.
Fire hazard of building structures - K0
1.3. KEY SOLUTIONS TO ENSURE THE LIVING CONDITIONS OF THE SMALL POPULATION
The project provides for measures to create an accessible environment for people with limited mobility and people with disabilities in accordance with the code of rules for the design and construction of SP 3110299, VSN-62-91 *, SNiP 35012001.
During the formation of the site, the continuity of pedestrian and transport routes was observed, ensuring access of disabled people and low-mobility groups to buildings and across the territory, taking into account the requirements of urban planning standards. Exits with a slope of not more than 1:10 are provided at the intersection of sidewalks with the roadway of internal roads.
Elevators are provided for inter-storey communication.
1.4. FINISHING
1.4.1. EXTERNAL FINISHING
External enclosing structures of the office part are made of I/concrete blocks γ = 600 kg/m ^ 3.
The wall with insulation from the mineral wool plate "Rockwool" is 150 mm and the outer layer is a cassette panel made of aluminum composite or profilist.
Windows, stained glass windows, entrance doors and vestibules - aluminum with double double glazed windows of the company "SCHUCO" (GOST 31247.094)
Design solutions
2.1 DESIGN SOLUTION
The office center is divided into an underground parking lot located in axes 1-7 and Zh-E and an office center located in axes 1-6 and A-E.
2.1.1. DESIGN SOLUTION OF UNDERGROUND PARKING GARAGE
The design solution of the garage is a one-story building with beam-free floors. The spatial frame of the building is solved according to the frame scheme in both directions. Girders of single-storey multi-span frames are a beam-free plate rigidly connected to columns .
Internal supports are columns with a section of 400x400 mm. Column grid accepted 6.6x6.6 m.
Deformation seam is located between axes P and P. From the office center between the axes G and E, the underground garage is separated by a sedimentary seam.
The foundation for the underground garage is a foundation slab with a thickness of 300 mm. Reinforcement of foundation slab by separate rods with AIII class reinforcement in longitudinal and transverse direction. Upper reinforcement is laid on spatial supporting frames. In places of greatest moments additional rods are laid. The pitch of the main reinforcement is adopted 200mm. Cross-shaped intersections of rods are bound by binding wire. The two extreme crossings of the rods along the perimeter must be tied in each node, the internal crossings of the rods are tied through the node in staggered order. Under the slab, preparation is arranged from concrete of class B3.5 with a thickness of 100mm. For connection with monolithic column and walls, reinforcement with section area equal to design section of column and wall reinforcement at upper surface of foundation slab is released from foundation slab. Concrete for foundation slab is accepted as class B15.
Monolithic single-storey columns are accepted with a section of 400x400 mm. The columns are reinforced by four separate rods with A400 class reinforcement, which corresponds to the maximum permissible distance between the rods of the working reinforcement in the columns. The working rods in the cross section of the column are placed possibly closer to the surface of the element with observance of the minimum thickness of the protective layer, which, at the request of standards, should be at least the diameter of the reinforcement rods and at least 20 mm.
Transverse rods are installed without calculation, but in compliance with the requirements of the norms. The distance between them (according to the condition of securing the longitudinal rods from lateral bulging during compression) should be not more than 15d, but not more than 500 mm with knitted frames. Diameter of clamps in knitted frames shall be not less than 5 mm and not less than 0.25d, where d is the largest diameter of longitudinal rods. Hot rolled steel clamps of class AI with a diameter of 6 mm are accepted. The thickness of the protective layer of transverse rods shall not be less than 15 mm. Concrete for B25 columns.
The monolithic beam-free floor is a solid plate resting directly on the columns.
The thickness of the cast-in-situ beam-free plate is found based on the condition of its sufficient stiffness h = (1/32... 1/35) l (l- the size of a larger span with a rectangular grid of columns). Plate thickness is accepted as 200 mm. Concrete for class B25 slab.
Cast-in-situ beam-free slab is reinforced with separate rods from A400 class reinforcement. Span moments are perceived by lower working reinforcement, and support moments - by upper working reinforcement. Protective layer before working reinforcement is accepted as not less than 15 mm and not less than diameter of working reinforcement. With a large number of identical plates, in order to save reinforcement, the floor is divided into span and over-column strips. In both strips, the lower rods must be inserted from the span axis to each side by at least 0.35l. The rods of the upper reinforcement of the supra-column strip must be inserted beyond the axis of the row of columns in each direction also by at least 0.35l.
External walls - cast-in-situ reinforced concrete with a thickness of 200 mm.
2.1.2. OFFICE CENTER DESIGN SOLUTION
The structural solution of the center is a multi-storey building with beam-free floors. The spatial frame of the building is solved according to the frame scheme in both directions. Girders of multi-storey multi-span frames are a beam-free plate rigidly connected to columns. The mating of the plate with the column is dripless, in the zone of the columns in the plate additional transverse reinforcement is installed, designed for the force from pressing.
The supports are columns with a section of 400x400 mm. Column grid accepted 6.6x6.6 m.
The foundation is a foundation slab with a thickness of 600 mm.
Reinforcement of foundation slab, columns, slabs is similar to underground parking garage.
Standard calculation
Preparatory period
Organizational arrangements.
3.1.1. Maintenance of works:
- PDP in full, approved for work;
- Order on appointment of responsible manufacturer of works;
- Orders on appointment of responsible persons for:
- Maintenance of load-gripping devices and containers in serviceable condition;
- Responsible for electrical management;
- Occupational safety at the facility;
- Safety of cable routes and communications;
- Safe operation and movement of cargo by lifting mechanisms;
- Fire safety at the facility and compliance with sanitary standards;
Copies of the orders shall be attached to the PPR, with the murals of the performers, with familiarization with the orders.
3.1.2. Provide the facility with the necessary production documentation:
- Set of working drawings issued by the customer for work;
- General Work Log;
- Author Supervision Journal;
- Concrete Works Log;
- Welding work log;
- Safety Induction Log;
- Training log at the workplace;
- Log of inspection of load-gripping devices and containers;
- Incoming inspection log of delivered materials;
- Compendium of labor protection instructions on professions and types of work;
3.1.3. Obtain the necessary permits for construction and installation works.
3.1.4. Accept the construction site according to the act.
3.1.5. Prepare and install the object passport board, posters, safety signs, etc.
Perform the following preparatory work:
Install temporary fencing along the entire perimeter of the construction site, from steel profiled flooring by wooden posts, meeting the requirements of GOST 12.4.05989 SSBT "Safety barriers, inventory."
To place and equip temporary premises and structures for builders: construction headquarters, premises for changing clothes of workers, workshops and warehouses (containers), food room, containers for collecting household garbage, etc.
Clean the construction site from construction debris, perform planning;
Arrange temporary dirt roads and pavements from inventory road slabs;
Provide construction site with engineering communications:
- Water;
- Sewerage;
- Water drain;
- Heat supply;
- Telephony.
Install the electrical unit.
Install washes for wheels of vehicles, such as "Moidodyr," at the main departures from the construction site;
Organize site for storage of structures and materials with coating, excluding soaking of articles;
Split the axes of the designed building and remove the elevation;
Install safety signs, traffic signs, warning and prohibition posters;
Install warning fences for hazardous areas;
Install external lighting of the construction site;
Perform zero cycle works of the building;
Perform fire safety, and environmental protection measures.
According to SNiP 3.01.0185, the PPM for performance of certain types of works includes :
- Job Instructions for construction of cast-in-situ reinforced concrete structures, installation of metal structures and operational quality control diagrams, data on requirements for basic materials, semi-finished products, structures and products, as well as used machines, accessories and accessories;
- work execution schedule;
- construction plot plan of the facility;
- explanatory note with necessary calculations, justifications and feasibility indicators.
Job Instruction for erection of cast-in-situ reinforced concrete structures
Scope of Application
The process map was developed for the construction of monolithic reinforced concrete structures of a multifunctional trade and office center.
As an example, a typical floor is adopted. The Job Instruction provides for the installation of monolithic columns and walls, as well as floors.
The works include:
- Installation of formwork and scaffolding;
- Installation of valves and embedded parts;
- Laying and compaction of concrete mixture in walls;
- Concrete care;
- Decommissioning of formwork.
Work is carried out in 2 shifts in the winter.
Quality control of concrete works performance provides for its implementation at the following stages:
- preparatory;
- concreting (preparation, transportation and laying of concrete mixture);
- concrete holding and decompression of structures;
- acceptance of concrete and reinforced concrete structures or parts of structures.
1.6.1. During the preparatory stage, it is necessary to monitor:
- quality of used materials for concrete mixture preparation and their compliance with GOST requirements;
- preparation of concrete mixing, transport and auxiliary equipment for concrete works;
- correctness of selection of concrete mixture composition and purpose of its mobility (rigidity) in accordance with the design instructions and work conditions;
- test results of concrete control samples at selection of concrete mixture composition.
Concrete mix composition shall be selected by construction laboratory. Composition, preparation, transportation and laying of concrete mixture, rules and methods of its quality control shall comply with GOST 747394.
Before laying the concrete mixture, the bases (soil or artificial), the correctness of the installation of the formwork, reinforcement structures and embedded parts must be checked. Concrete bases and working seams in concrete shall be thoroughly cleaned from cement film without concrete damage, formwork - from debris and dirt, reinforcement - from rust deposit. The internal surface of the inventory formwork shall be coated with special lubricant, which does not impair the appearance and strength of the structures.
1.6.2.In the process of concrete mix laying it is necessary to monitor:
- condition of scaffolding, formwork, position of reinforcement;
- quality of the stacked mixture;
- compliance with the rules of concrete mixture unloading and distribution;
- thickness of layers to be laid;
- concrete mixture compaction mode;
- observance of the established concreting procedure and rules for arrangement of working joints;
- timeliness and correctness of sampling for making control samples of concrete.
The inspection results shall be recorded in the concrete work log.
1.6.3. The composition of measures at the stage of concrete maintenance, its care and sequence of structures expansion includes the following requirements:
- maintenance of temperature and humidity conditions ensuring concrete strength increase at the specified rate;
- prevention of significant temperature shrinkage and crack formation;
- protection of hardening concrete from impacts and other mechanical impacts;
- protection in the initial period of concrete hardening against atmospheric precipitation or moisture loss.
Decompression of concreted structures is allowed when concrete reaches strength.
When checking the strength of concrete, tests of control samples of concrete for compression are mandatory.
The results of concrete quality control shall be reflected in the work acceptance log and certificates.
Approximate list of hidden works to be edited after their completion:
- reinforcement of reinforced concrete structures;
- installation of embedded parts;
- anti-corrosion protection of embedded parts and welded joints (joints, linings);
- arrangement of formwork of structures with instrumental check of elevations and axes, joints of prefabricated monolithic structures (before their freezing).
Procedure and organization of works performance
Prior to the commencement of work on the construction of the underground part from cast-in-situ reinforced concrete, organizational and preparatory measures must be carried out in accordance with SNiP 3.01.0185 "Organization of Construction Production."
Prior to installation of the formwork, the following works shall be performed: wall axis splitting; leveling of wall surface, floors; marking of the wall room in accordance with the design; hairlines fixing the working position of the formwork must be applied to the surface of the slabs with paint; installation tooling and tool prepared; the base is cleaned of dirt and debris.
Formwork
Formwork shall be delivered to the construction site in complete, suitable for installation and operation, without additions and corrections.
The formwork elements received at the construction site are placed in the area of the KB6762 tower crane. All formwork elements shall be stored in the position corresponding to the transport, arranged according to grades and sizes. It is necessary to store formwork elements under a canopy in conditions that exclude their damage. Shields are laid in stacks with a height of not more than 11.2 m on wooden gaskets. The remaining elements, depending on the dimensions and mass, are stacked in boxes.
Installation and removal of the formwork is carried out using the tower crane KB6762.
Installation of the formwork should begin with laying of concreted structures of lighthouses along the entire contour. The inner face of the rack must coincide with the outer face of the concreted wall. After the lighthouse rivers are reconciled with bright paint, hairlines are applied on them indicating the boundary position of the formwork boards, after which the shields are mounted with a crane along the length of the wall. Shields of upper tier are installed on mounting scaffolds fixed to concreted wall. For layout of formwork panels of columns and floor beams, refer to sheet.
The condition of the installed formwork shall be monitored continuously during concreting. In cases of unexpected deformations of individual formwork elements or unacceptable opening of slots, additional fasteners should be installed and the deformation of the place should be corrected.
It is allowed to remove the formwork only after the concrete reaches the required strength, as per SNiP 3.03.0187 "Load-bearing and enclosing structures," and with the permission of the work manufacturer.
Decoupling of formwork from concrete shall be performed using jacks or installation slices. The concrete surface shall not be damaged during tearing. The use of cranes to break off the formwork is prohibited.
After the formwork is removed, it is necessary to:
- Perform visual inspection of formwork elements;
- Clean all formwork elements from stuck concrete;
- Perform lubrication of decks surface, check and apply lubrication on screw connections;
- Sort the formwork by marks.
Construction plot plan of the facility
This diploma project has developed a construction plan for the period of erection of above-ground structures.
The object construction plan shows the plan of the designed building with the reference of its axes to the coordinate layout grid; location of permanent and temporary transport routes of electric, water, and heat supply networks, sewers, installation cranes and mechanized installations with indication of crane tracks, direction of cranes movement, and hazardous installation areas; storage sites and pre-assembly of structures and process equipment; domestic premises, warehouses and other structures and devices necessary for construction, as well as basic measures necessary for safety.
The construction plan was solved in accordance with the fire safety standards of construction design and the requirements of safety and labor protection rules.
Construction of the construction plan is carried out taking into account the accepted symbols.
During the development of the construction plan, the following calculation was made:
requirements for temporary buildings and facilities ;
warehouses and open storage areas;
calculation of construction site lighting;
Calculation of water demand.
All calculations and justifications of the decisions made are given in the explanatory note .
3.3.6 TEMPORARY ROADS
Temporary roads to construction sites are intended for uninterrupted transportation of structures, materials, equipment throughout construction at any time of the year.
The road ensures the supply of materials to the crane area, unloading areas, pre-assembly, to vertical transport means, to workshops, storerooms, open warehouses, etc.
When routing roads, the distance between the road and:
1 m storage area
crane tracks 7.5m
fence fence 1.5 m
The intersection and junction of roads is performed at an angle of 9045 degrees, and with the railway 9060.
Construction roads are looped, a circular bypass is built around the object. Roads have a width of 6 m, the direction of movement is right-hand. Widening is provided in places of structures unloading.
For the construction of a temporary building road, a 1025 cm thick sand bed is arranged, on top of which inventory reinforced concrete slabs are laid.
Slabs - railway with non-directional reinforcement with a thickness of 1620 cm, 1-2 times turnover.
Passageways, crossings, sidewalks were built for the safe passage of workers to work sites, utility buildings and residential buildings. We arrange, depending on the intensity of pedestrian traffic 2 m wide, a towering sidewalk
by 3050 cm, has a transverse slope and a drainage.
архитектурные чертежи.dwg

СГП.dwg

сравнение.dwg

лист11, лист 12.dwg

Similar materials
- 04.11.2022
- 29.07.2014
- 24.10.2015
Free downloading for today
- 22.08.2014
- 29.08.2014