Modernization of the main motion drive of the structure of the main technological equipment



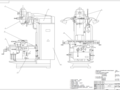
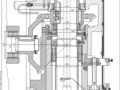
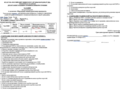
- Added: 10.02.2022
- Size: 3 MB
- Downloads: 5
Description
- Sheet 1. General view of the WMD indicating the working bodies and main parts.
- Sheet 2. Drawing of the machine assembly, according to the task.
- Sheet 3. Variants of structural grids, a graph of rotational speeds, a kinematic scheme of an upgraded gearbox.
- Sheet 4. Drawing of the convolution of the upgraded gearbox.
- Sheet 5. Sweep drawing of an upgraded gearbox.
- Folio 6. Drawings of detailing of the modernized gearbox.
Project's Content
![]() |
![]() |
![]() ![]() ![]() ![]() |
![]() ![]() ![]() |
![]() ![]() |
![]() ![]() |
![]() ![]() |
![]() ![]() |
![]() ![]() |
![]() ![]() |
![]() ![]() |
![]() ![]() |
![]() ![]() |
![]() ![]() ![]() ![]() |
![]() ![]() ![]() ![]() |
![]() ![]() ![]() |
![]() ![]() ![]() |
![]() ![]() ![]() ![]() |
![]() ![]() ![]() ![]() |
![]() ![]() ![]() ![]() |
![]() ![]() ![]() ![]() |
![]() ![]() ![]() ![]() |
![]() ![]() ![]() ![]() |
![]() ![]() ![]() ![]() |
Additional information
Contents
Summary
Introduction
1 Description of operation of special milling machine of SF model
1.1 Purpose of special milling machine of SF model
1.2 Technical Specifications
1.3 Classification of WMD
1.4 Brief description of the main units of the SF machine
1.5 Detailed description and operating principle of the given unit
2 Kinematic analysis of WMD
2.1 Description of forming process on WMD
2.2 Construction and description of WMD kinematic structure
2.3 Determination of kinematic circuit of WMD main motion
3 Development of versions of structural grids of the upgraded WMD
3.1 Calculation of processing mode parameters for different cutting conditions
3.2 Determination of range of control of RPM of WMD spindle
3.3 Determination of denominator of the series of geometric progression of RPM of WMD spindle
3.4 Choice of optimal multiplier structure
3.5 Plotting of speeds of WMD speed box (CC)
3.6 Construction of kinematic diagram of upgraded WMD speed box (in general form)
Conclusion
List of sources used
Summary
In this course work, the design of the specialized milling machine SF676 was analyzed.
An analysis of the classification of WMD, a kinematic analysis of the design of the machine, a structural analysis of the forming process on the machine was carried out.
To perform the graphoanalytic calculation of the speed box, the cutting forces and modes were determined, the range of control of rotation frequencies R = 7.14 was determined and the denominator of the series sound= 1.26 was calculated. The structural grid variants were analyzed, the optimal one was chosen, the rotation speed graph was plotted and, in general, the kinematic diagram of the machine speed box.
The course work consists of a 43-page explanatory note including annexes, as well as 3 sheets of A1 format of the graphic part of the project.
Introduction
Metal cutting machines are the main type of factory equipment intended for the production of modern machines, instruments, tools and other products, therefore the number and quality of metal cutting machines, their technical equipment to a large extent characterize the production power of the country.
The efficiency of design and implementation of advanced technologies, complex mechanization and automation of the production processes of metal cutting machines is ensured by a widely developed specialization of production based on aggregation, unification and normalization of parts and entire units. The advantage of domestic machine tools is the production of machine tools embedded in automatic lines.
The development of computer technology made it possible to create productive metal cutting machines with software control, including with automatic tool change. The production of unique machines equipped with modern equipment has also been established.
The target modernization of the metal cutting machine is designed to provide higher technical characteristics for expanding technological capabilities on the one hand and specializing equipment for solving a specific production task on the other hand.
This course work is an example of the structural modernization of the drive of the main movement of the specialized milling machine model SF 676, performed in accordance with the technical assignment (zks = 10, nmax = 2000 rpm) at the stage of the technical design, i.e. the general view of the upgraded machine, the kinematic diagram of the speed box, the design decisions made in the future should be justified by design calculations for strength, rigidity, durability, etc.
Description of operation of special milling machine model SF676
Purpose of Specialized Milling Machine Model SF676
The wide-university milling machine SF676 was developed by the Odessa Special Design Bureau of Precision Machines (SKB PS) at the Odessa Plant of Milling Machines named after Kirov (OZFS), which was appointed the head in the development of coordinate boring and wide-university milling machines.
The SF676 milling machine is designed for milling parts with cylindrical, disk and shaped cutters using a horizontal spindle, and with end, end and key cutters using a vertical rotary spindle.
On the machine, you can also drill and drill, center, counterbore, countersink, expand, spread.
Additional tooling and accessories offered by the machine manufacturer allow, in addition to milling, to perform, as well as cutting, thread cutting and other operations.
The universal milling machine SF676 is most preferably used in tool shops of machine-building plants or workshops for the manufacture of small devices, tools, relief dies and other products..
ersalny
"6" main parameter, 6 desktop size 250 x 630
By degree of specialization - wide-versatile - machines for processing various parts, designed to perform various operations on blanks, various in shape and size in single production;
By degree of automation - manual, with semi-automatic mode of operation
By accuracy class - "H" of normal accuracy
By weight - light (up to 1 t) with a mass of 1.050 tons
By transportability - transportable (up to 5 tons)
Kinematic analysis of WMD
Description of forming process on WMD.
The SF676 milling machine has two spindles - horizontal and vertical (rotary), which allow you to process a complex workpiece without reinstalling it on the desktop, which significantly increases productivity.
The SF676 machine can perform a number of milling and boring operations with high accuracy, which can be achieved if the machine is installed in a room with a constant temperature of 20 ± 2 ° C and a humidity of 65 ± 5%, if there are no sources of heat and vibration near the machine.
A wide range of spindle and feed revolutions, mechanical feeds and rapid movements provide cost-effective handling of various parts in optimal modes.
Horizontal and vertical spindles are located in spindle head and are connected to each other by means of gear train.
Spindle head is mounted on horizontal guides and provides transverse feed on machine. The spindle head can be fed transversely from the engine through the feed box (16 feeds from 13 to 395 mm/min) or manually from the flywheel.
The speed box informs the horizontal and vertical spindles of 16 different speeds of rotation (501630 and 63.. 2040 rpm, respectively).
Accuracy class of machine N.
Conclusion
In this course work, on the basis of the initial wide-universal cantilever machine, I conducted its design analysis and device. Kinematic analysis was carried out and some versions of structural grids of the modernized WMD were developed. A graph of rotation speeds for the optimal structural grid has been built and the kinematics of the speed box have been developed. Thus, during the course project they consolidated theoretical knowledge, got acquainted with special technical literature, learned to independently calculate and design machine units.
The graphical part of the work is presented on sheets of A1 and A3 format.
Kinematicheskaya_skhema.cdw

SF676_VO.cdw

Uzel_shpindelny.cdw

вал II.cdw

Зубчатое колесо.cdw

крышка вала.cdw

развертка коробки.cdw

развертка спец.spw

свертка спец.spw

Свертка коробки1.cdw

Similar materials
- 22.01.2022