Foundry - Architecture of civil and industrial buildings and structures - coursework
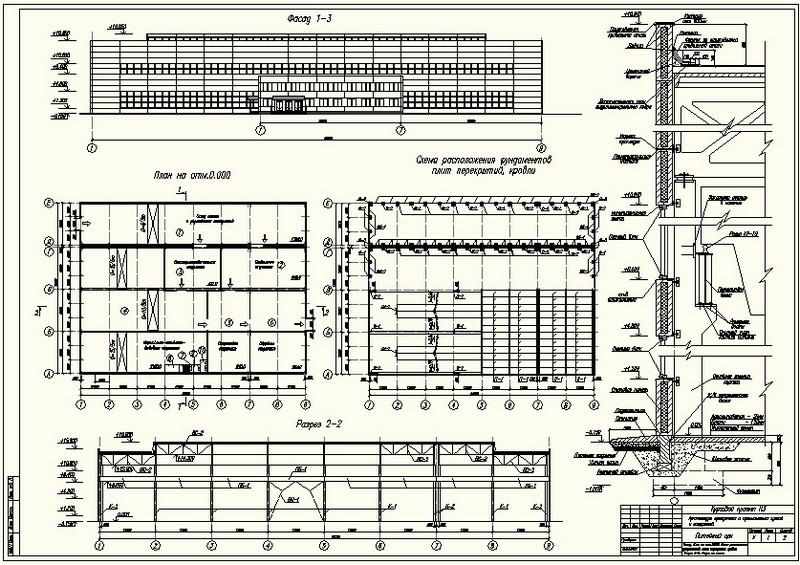
- Added: 01.07.2014
- Size: 343 KB
- Downloads: 2
Description
Project's Content
![]() |
![]() ![]() ![]() |
![]() ![]() ![]() ![]() |
![]() |
![]() |
Additional information
1. Introduction
The location of an industrial enterprise in the selected territory should be determined by the regional planning project and the master plan of the populated place.
When designing industrial buildings, it is necessary to strictly observe and take into account both the production process and the creation of optimal working conditions.
The process diagram compiled by a technologist in this industry determines the dimensions of the building, its saturation with technological and transport equipment. The peculiarities of technological processes of production of enterprises of various industries are reflected in the architectural solution of the entire enterprise and its buildings.
The internal environment of production and the proper organization of the workplace are of paramount importance for the creation of the necessary sanitary and hygienic conditions and the safety of production.
Despite the fact that at the moment the main emphasis is on the reconstruction of enterprises, industrial construction remains the main economic task of the country and requires the necessary consideration.
When designing industrial buildings of industrial enterprises, it should be borne in mind that in accordance with the technological process and the related certain mode, the nature of the loads, as well as other operational features, they are in specific and, as a rule, less favorable conditions than civilian buildings.
The course design of the industrial building should give practical confirmation that the volumetric and planning composition of production buildings of industrial enterprises is primarily determined by the production process for which the structure is intended.
Production processes, as a rule, require a strictly defined height of the premises, the size of the spans and the steps of the supporting structures, determined by the arrangement of technological equipment, the nature and movement of internal transport, the size and direction of the movement of raw materials and finished products. Various technological processes require a certain sanitary and hygienic solution of the premises, which includes the temperature and humidity of the air, providing the necessary level of illumination in the areas of workplaces, and sometimes certain color solutions. Production buildings are usually equipped with continuous systems of engineering equipment. All this has a decisive effect on the organization of their volumetric-spatial structure.
In addition, production buildings are solved in direct connection with specially equipped premises for consumer services of workers at the enterprise, the composition of which also depends on the nature of production processes.
Structures used in the construction of industrial buildings have their own distinctive features. During the development of the project, the practical development of the structural systems of single-story and multi-story industrial buildings, various coating structures, light and aeration lights, and other structural elements characteristic of these buildings is carried out. The development of the design of the production building contributes to an understanding of the features of industrial architecture, where scale, proportionality, while maintaining its artistic significance, receive a qualitatively different sound. This applies both to the external volume of buildings and to their interior.
It is necessary to start the development by studying the process flow diagram of the entire enterprise, which is a graphical representation of the functional relationship between all production processes.
2. Master Plan
The master plan of the enterprise is the starting point in the process of architectural and construction design, a drawing that coordinates the relationship and architectural solution of industrial and civil buildings. The development of the general plan solves the issues of planning, development and improvement of the territory of the enterprise on the basis of functional and technical connections between production sites, the direction of main people and cargo flows and natural and climatic factors.
The plot plan of the enterprise is made taking into account the orientation on the sides of the world and the direction of the winds.
The construction of the general plan of the enterprise is carried out in accordance with a clear production and functional zoning:
Zone I - pre-factory, it includes auxiliary buildings for general purpose - checkpoints, passageways, ABK
II zone - production - one-story universal building;
Zone III - auxiliary production - these are warehouses of finished products and raw materials.
Within each zone, during the placement of production buildings, the homogeneity of the technological process, transport equipment, power supply and energy consumption, the same fire requirements and the degree of industrial damage must be maintained.
The main entrance (passage) and ABK is located on the front side of the industrial site, on the path of the main flow of people from the settlement (residential development) to the enterprise, and the parking lot of individual vehicles is located in the pre-plant zone and is located to the right of the main entrance. For the exit and arrival of special vehicles, and freight transport, checkpoints are provided on the front side of the industrial site.
Warehouses of finished products and raw materials are located behind the main workshop next to the transport routes. Access roads have been laid throughout the enterprise for the mobility of fire engines in the event of an accident or emergency at the enterprise.
Roads for road transport on the territory of the enterprise are designed according to a mixed system, which includes ring, through and dead end systems. For the movement of human flow along the industrial site, footpaths and sidewalks are provided throughout the territory of the object. On the territory of the enterprise, the pre-plant square at the main passage, the intra-plant main driveways, lanes along the fence of the enterprise and a resting place are landscaped. The total area of landscaping is at least 1015% of the area of the enterprise.
This project adopted a dispersed building system. With dispersed development of the territory between buildings and structures, minimum fire and sanitary breaks are established. They are measured by the distance between the outer walls. Generally:
where H1, H2 - heights of opposing buildings.
When placing buildings, it should be possible to access fire engines along the entire length of the building. The width of the main driveways is adopted equal to 6 m. The width of the roadway with two-way traffic is adopted 10 m. The width of the gate for road entrances is 6 m. The width of the sidewalks is 2 m.
2.1 technical and economic indicators for the development site.
1. Area: 22574 m2
2. Area of the enterprise (workshop and ABK): 7775 m2
3. Road surface area: 9616 m2
4. Area occupied by landscaping: 3386 m2
5. Building area 42.4%
3. architectural and planning section.
FOUNDRY
Despite the variety of volume-planning solutions, some general principles of these solutions can be highlighted.
• the need to study the production process;
• blocking of several industrial premises in one industrial building;
• pavilion building;
• choice of storey;
• unification of the building solution;
• Increased versatility and flexibility
• durability of the building;
• Cost-effective use of space
• simple in form;
• isolation of hazards;
• fire safety requirements;
• safety of people evacuation;
• natural-climatic characteristics.
The choice of floors depends on the load of technological equipment, the size of equipment and products, the use of the gravitational principle for the movement of materials. In this project - 1 storey building.
The unification of the building solution, seeks to obtain a relatively better space-planning solution, contributes to increasing the flexibility or versatility of the space-planning solution of an industrial building, which is of great importance for accelerating scientific and technological progress.
In the construction industry, technological processes and related equipment, as well as labor items, are improving quickly. Under these conditions, equipment installed in the room is often changed, sometimes according to a completely new technological scheme. Therefore, the space-planning parameters of the building should not constrain or limit the processes of modernization of production.
Increasing the versatility and flexibility of the building is achieved as a result of freeing space, due to increasing the column grid, due to increasing the height of the room.
In connection with the acceleration of scientific and technological progress, the problem of the durability of the building arises. The designed building is designed to accommodate process equipment and production, which, according to forecasting data, even in a few decades or hundreds of years will not lose its value and will not be stopped, so if it is necessary to place another in this building
production, then in this case the versatility of space-planning parameters is provided. In principle, the designed building in the future can be converted to another production, since the space-planning solution is not strictly subordinate to any technological process. The durability of the building in this case is not determined by the life of this type of equipment.
The space-planning solution in its form is very simple. The building is rectangular in plan with parallel spans of the same width, which simplifies the design, increases the degree of assembly of structures, reduces the number of their types.
The degree of versatility of the building is increased. Space-planning solutions of the building allow the possibility of modernization of technological processes with replacement of equipment without significant reconstruction of the building.
In the building, production rooms are not isolated from each other.
Workshop latrines and rest rooms are located close to each other so that they can be used during regulated breaks during the shift. All these rooms are located near the external walls of the industrial building
чертеж.dwg
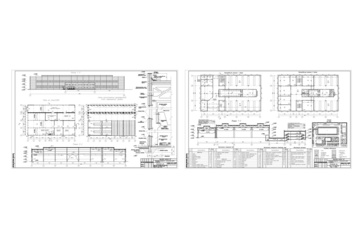
Similar materials
- 01.07.2014
- 06.11.2018
- 28.09.2021
- 01.07.2014