Exchange Rate Design "Centrifugal Cyclone Calculation"


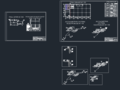
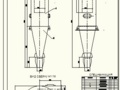
- Added: 23.10.2020
- Size: 2 MB
- Downloads: 1
Description
Process and Structural Calculation. selection of auxiliary equipment.
Source data.
Design a gas cleaning system at a known gas flow rate using a cyclone.
Gas volumetric flow Q = 29000m3/g
Dust content of gas at the exit from the =117.9g/m3 Svkh dryer drum
Dust content of gas at cyclone outlet Svykh = 23.42g/m3
Dynamic viscosity μr = 21.17 * 10-6 Pa * s
Gas density under operating conditions of αpt = 1930kg/m3
Dust particle density αh = 2800kg/m3
Required purification efficiency a > 80%
Content:
Introduction
1. Source Data
2. Theoretical part
2.1. Emissions and their suppression
2.2. Cyclones
2.3. Cyclones of NIIOGAZ design
3. Design part
3.1. Practical recommendations for selecting cyclones
3.2. Through Cyclone Size Selection
3.3. Select and calculate group cyclone parameters
3.4. Determining the overall dimensions of the cyclone
3.5. Calculation of additional equipment
Conclusion
Bibliographic list
Project's Content
![]() ![]() ![]() ![]() |
![]() ![]() ![]() |
![]() |
![]() ![]() ![]() |
![]() ![]() ![]() ![]() |
Additional information
Contents
Introduction
1. Source Data
2. Theoretical part
2.1. Emissions and their suppression
2.2. Cyclones
2.3. Cyclones of NIIOGAZ design
3. Design part
3.1. Practical recommendations for selecting cyclones
3.2. Through Cyclone Size Selection
3.3. Select and calculate group cyclone parameters
3.4. Determining the overall dimensions of the cyclone
3.5. Calculation of additional equipment
Conclusion
Bibliographic list
1. Source Data
Design a gas cleaning system at a known gas flow rate using a cyclone.
Gas volumetric flow Q = 29000m3/g
Dust content of gas at the exit from the =117.9g/m3 Svkh dryer drum
Dust content of gas at cyclone outlet Svykh = 23.42g/m3
Dynamic viscosity μr = 21.17 * 106 Pa * s
Gas density under operating conditions of αpt = 1930kg/m3
Dust particle density αh = 2800kg/m3
Required purification efficiency a > 80%
Introduction
In any production of construction, at most of its technological stages there are various emissions that pollute the environment. In particular, we will be interested in the pollution of the environment from dust, namely, the prevention of its release into the atmosphere.
For example, when unloading mineral materials into silos, a lot of dust is released, which is advisable to suck in the upper part of silo warehouses. When drying and heating sand and crushed stone, a large amount of dust and non-combustible particles of liquid fuel are released. The main places of intensive dust release are the chimney, loading and unloading boxes of the drying drum, as well as places of loading, unloading, screening of dry mineral materials. Sanitary standards allow the maximum dust content of the air layer at a height of 1.6 m from the ground surface - 0.5 mgm3.
The main task of environmental protection is to ensure the normal operation of dust treatment plants at the plant, since dust is the main source of pollution. Sources of pollution are divided into organized and unorganized. The former release harmful substances into the atmosphere of a pipe or mine, the latter - from large areas (warehouses of stone materials). There are sources of water pollution of the environment: from surface runoff from the plant; cooling water from material washing.
To suppress emissions, dusting plants are also used, which are designed to clean the exhaust gases from the drying drum and create a minimum discharge in it in order to direct the entire stream of contaminated gases to the dusting plant.
In this course work, we will consider the purification of exhaust gases by a dust-producing plant - a dry cyclone.
Theoretical part
2.1.Fetches and their suppression
The main sources of air pollution are aerosol emissions from dryers. There are one-time emissions of aerosols during storage and processing of filler, from roads on the territory of the plant and emissions of odorous resinous substances from asphalt storage sites and installations for its mixing.
The amount of discharge from the dryers depends on the size of the filler pellets and the type of fuel used. Emissions in the absence of suppression averaged about 20 kg/t of filler. Emissions are relatively large particles, more than 50% of which exceed 20 μm and depend on the filler used. Emissions from dryers are captured either by scrubbers or bag filters, in front of which cyclones are located. These devices reduce emissions by more than 99%.
Dust is formed during the operation of the drying drum (at the inlet) and sieves on a mixer (screen), a hot material elevator. In the composition of dust, almost 50% of the grains are less than 71 μm (mineral powder), while particles with a grain size of 5070 μm are caught by a completely dry dust cleaning system; Particles with a size of 105 μm are partially captured by a dry dust cleaning system (80%). In this regard, it becomes necessary to carry out wet dust cleaning by a cyclone. Particles less than 10 microns in size are not captured at all by the dry method.
To suppress emissions, dusting plants are also used, which are designed to clean the exhaust gases from the drying drum and create a minimum discharge in it in order to direct the entire stream of contaminated gases to the dusting plant. Usually, such a plant has two purification stages: 1st - dry cyclones
cleaning, 2nd - wet dust collectors.
The cleaning efficiency of such a plant is 99.2%. So in this work we consider cyclones then we will consider them directly.
Conclusion
As a result of the course work, the TsN15 1800 cyclone was designed and calculated all its technical and dimensional characteristics. This cyclone provides a predetermined level of flue gas purification by dry particle deposition. Auxiliary equipment was also selected for the designed cyclone. Traction equipment - BM20/750IIV type fan providing cyclone operation at the specified capacity and electrical equipment - three-phase asynchronous motor of A280S2 type with 110 kW power.
Циклон.dwg

Циклон.dwg
