Diploma project "Design of office and warehouse complex in Khimki"


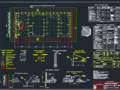
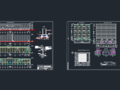
- Added: 15.11.2020
- Size: 7 MB
- Downloads: 7
Description
VKR NIU MGSU 08.03.01 Department of MDK "Design of office and warehouse complex in the Industrial Park" Skhodnya "of Khimki
Project's Content
![]() |
![]() |
![]() ![]() ![]() ![]() |
![]() ![]() ![]() ![]() |
![]() ![]() ![]() ![]() |
![]() ![]() ![]() ![]() |
![]() ![]() ![]() ![]() |
![]() ![]() ![]() ![]() |
![]() ![]() ![]() ![]() |
![]() ![]() ![]() ![]() |
![]() ![]() ![]() |
![]() ![]() ![]() |
Additional information
Contents
CONTENTS
1 Architectural and construction section
1.1 Initial data
1.2 Master Plan
1.3 Architectural and planning solutions
1.4 Constructive solution
1.5 Architectural solution of the facade
1.6 Interior Finishes
1.7 Fire prevention and evacuation
1.8. Engineering equipment
1.9.Basic construction indicators as per plot plan
2 Design section
2.1 Calculation of rafter truss
2.1.1 Design Assignment
2.1.2 Determination of design loads
2.1.3 Determination of forces in truss elements
2.1.4 Selection of cross section of stretched truss elements
2.1.5 Selection of brace section
2.2 Weld Calculation
3. Foundations and foundations
3.1. Introduction
3.2. Construction Site Geotechnical Conditions
3.2.1. Study of engineering and geological conditions of the work area
3.2.2. Geological and lithological structure and hydrogeological conditions of the site
3.2.3. Field studies of soils
3.2.4. Physical and mechanical properties of soils and chemical composition of water-soluble components in soils and underground water
3.2.5. Design geomechanical model of the object
3.3. Calculation
3.3.1. Foundation loads
3.3.2. Determination of pile bearing capacity
3.3.3. Determination of the load allowed on the pile
3.3.4. Calculation of draft of conventional foundation
4.1 Job Instruction for Drilling Piles
4.1.1 Scope of Job Instruction Application
4.1.2 Construction Process Organization and Technology
4.1.3. Calculation of labor costs
4.1.4 Numerical and qualification composition of the link
4.1.5. Construction Schedule
4.1.6. Guidelines for Quality Control and Evaluation
4.1.7. Logistical resources
4.1.8. Safety precautions
4.1.9 Technical and economic indicators
4.2 Job Instruction for Construction of Cast-in-Situ Reinforced Concrete Foundations
4.2.1 Scope of Job Instruction Application
4.2.2 Description of working conditions
4.2.3 Construction Process Organization and Technology
4.2.4 Methods and sequence of works execution
4.2.5 Work Schedule
4.2.6 Methods and methods of labor of workers
4.2.7 Quality control of works
4.2.8 Calculation of labor costs
4.2.9 Safety and Health
4.2.10 Technical and economic indicators
4.2.11 Logistical resources
4.2.12 Calculation of Scope of Work
4.3 Job Instruction for Frame Installation
4.3.1 Characteristics of the building and structures
4.3.2 Scope of works covered by the map
4.3.3 Description of working conditions
4.3.4 Organization and technology of construction processes
4.3.5 Methods and sequence of works execution
4.3.6 Calculation of labor costs
4.3.7 Numerical and qualification composition of links
4.3.8 Work schedule
4.3.9 Organization, methods and methods of workers' work
4.3.10 Quality control of works
4.3.11 Safety precautions
4.3.12 Technical and economic indicators
4.3.13 Logistical resources
4.3.14 Selection of tooling and lifting cranes
4.4 Job Instruction for Installation of Sandwich Panels
4.4.1 Scope of application
4.4.2 Organization and procedure of works execution
4.4.3. Quality and Acceptance Requirements
4.4.4. Costing Labor and Machine Time
4.4.5. Work Schedule
4.4.6. Material and technical resources
4.4.7 Occupational safety
4.5. Job Instruction for Roofing Arrangement
4.5.1. Scope of Application
4.5.2 Organization and procedure of works execution
4.5.3 Requirements for quality and acceptance of works
4.5.4 Calculation of labor costs
4.5.5 Logistical resources
4.5.6 Occupational Safety Requirements
4.5.7 Work Schedule
5. Organization of construction
5.1. Description of the facility and construction conditions
5.2. Work Solution
5.2.1. Selection of the main mounting mechanism
5.2.2. Methods of production of main types of construction and installation works
5.2.3. Site Work Schedule
5.3. Construction Site Organization
5.3.1. Resources and construction facilities
5.3.2. Calculation of requirements for temporary buildings and structures
5.3.3. Calculation of water demand
5.3.4. Calculation of power demand
5.3.5. Calculation of compressed air demand
5.3.6. Heat Demand Calculation
5.4. Stroygenplan
5.5. Occupational and environmental protection
5.6. Main technical and economic indicators of the construction facility
6. Safety of life
6.1 Occupational Safety
6.1.1 Occupational safety measures envisaged in the project
6.1.2 Measures on labor safety on the construction plan
6.1.3 Safety measures in Job Instruction for Works for Steel Structures Installation
6.1.4 Safety measures in Job Instruction for Roof Production
6.1.5 Safety measures in Job Instruction for installation of sandwich panels
6.1.6 Safety measures in Job Instruction for Drilling Piles
6.1.7 Safety measures in Job Instruction for installation of foundations
6.2 Environmental Safety
6.2.1 Environmental safety measures
6.2.2 Environmental safety measures on the construction plan
6.2.3 Environmental safety measures in Job Instruction for brown-padded piles
6.2.4 Environmental safety measures in Job Instruction for Roof Production
6.2.5 Restoration (reclamation) of land plot, use of fertile soil layer.
6.2.6 Environmental safety measures envisaged during the construction of the facility additionally
6.3 Design Part
7. Estimates
7.1 Local cost estimate
7.2. Consolidated cost estimate for construction
BIBLIOGRAPHIC LIST
GRADUATION QUALIFICATION ASSIGNMENT
VKR topic: Design of the office warehouse complex in Khimki
Tasks to be solved: development of architectural, construction and calculation
structural section; Technology, Organization and Economics section
construction and section on occupational health, safety and environmental protection
Initial data: purpose of the building, construction area, dimensions and structural diagram of the building, number of floors
Contents of explanatory note: cover sheet, table of contents, introduction, architectural
construction section, design section, section on technology, organization and economics of construction and section on labor protection, life safety and environmental protection, conclusion, list of used literature
List of graphic/presentation material: architectural and construction section (4 sheets); design section (1-2 sheets); section on
technology, organization and economics of construction (3 sheets )
Master Plan
Decisions on the master plan are made taking into account the technological process, functional zoning, fulfillment of sanitary and fire protection requirements. The functional purpose of the designed facility is a warehouse complex, which is intended for the storage and sale of consumer goods that do not require special storage conditions that do not release pollutants and other harmful physical factors that affect the environment and human health into the environment. The warehouse complex consists of six warehouse buildings, an administrative building (hereinafter referred to as "ABK"), a checkpoint (hereinafter referred to as "checkpoint") and other auxiliary buildings and structures.
On the construction site, the project provides for the placement of the following buildings and structures (numbering corresponds to the explication of buildings and structures on the Master Plan):
Storage building No. 1. It has a rectangular shape in plan, with overall dimensions (in axes) of 96.0x96.0m. The total area of the building is 9216 m2.
Gas distribution point
Fire Fighting Pump Station
Fire tank
Waste water treatment facilities drains
Storm Water Treatment Facilities
Waste collection area
On the territory adjacent to the storage buildings, on the side of the loading and unloading front, it is provided:
production waste collection sites;
truck parking area;
car parking area;
lawns.
Due to the fact that the work of people with disabilities in the warehouse complex is not provided. Measures to ensure the life of persons with disabilities and people with disabilities are not carried out.
On the side of the loading dock zone, the ground elevation is 1.200 m.
Relative elevation 0.000 is the level corresponding to the level of clean floor of the first floor.
The section of the designed office warehouse complex, which is part of the Skhodnya industrial zone, is located in the urban district of Khimki.
On the eastern and southern sides of the site, entry/exit is provided through a checkpoint equipped with a barrier and designed for the entry/exit of cars and trucks, special equipment and fire vehicles. Also on the south side of the site there is a second entrance/exit for fire vehicles. Entrances/exits are spaced apart over 100 m
Car parks for cars (336 m/m) and trucks (394 m/m) are provided for parking in the warehouse complex.
Pavements of driveways, loading/unloading sites and car parks are provided from asphalt concrete. Road paving structures are designed for load from the movement of freight and special vehicles.
The vertical layout is solved by the method of design (red) contours with a relief section of 0.10 m in connection with the existing relief. Longitudinal and transverse slopes are designed for driveways and sites in accordance with the standards (0.52%). Lawns are separated from the roadway by side stone.
Drainage of rain drains from the designed driveways and platforms is carried out to the designed rain receiving grids.
Architectural and planning solutions
The designed standard storage bin is intended for storage and sale of consumer goods that do not require special storage conditions that do not release pollutants and other harmful physical factors that affect the environment and human health into the environment. Typical bins can be locked together in a warehouse building or used as stand-alone buildings.
A typical T1 cell is a plan rectangle with an axial dimension of 96.0 x 96.0 m and a total area of 9216.0 m2. The pitch of the structural grid of the axes is 12 x 24 m, the elevation of the parapet is 15.300 m. Along the unloading front (along the axis A), a 2-story antresol with a depth of 9 m is provided.
The typical cell is divided into 2 sections equal in area with axial dimensions of 48.0 x 96.0 m, with the possibility of their independent use by various tenants.
Each section has:
a separate input group;
storage area;
vehicle unloading/loading front;
charging for electric loaders;
Packing and packaging area (2nd floor of the antresol);
administrative and household premises (3rd floor of the restaurant);
technical rooms required for operation.
The height of the storage zone to the bottom of the supporting structures is 12,000 m, the height of the 1st floor to the bottom of the structures in the unloading-loading zone is 4.9 m, the 2nd floor of the antresoli is 3.3 m, the 3rd floor of the antresoli is 3.9 m.
Floor plans are developed on the basis of the technical assignment, in accordance with the planning, technological and fire safety standards:
At the elevation ± 0.000, there is an unloading and loading area and a storage area, security rooms for controlling access to the building, office rooms with a group of bathrooms, engineering and technical rooms, charging rooms for electric loaders, a fire station room, as well as staircases in fire walls with a fire resistance limit REI 90 and REI 150 (at the junction of different fire floors), providing access and evacuation from anti-tank tanks. Evacuation of personnel from the storage area is carried out through an evacuation corridor fenced off by fire partitions of the 1st type with fire resistance limit EI 45
At elevation + 5.550 there is a packing area, ventilation chambers and technical rooms. The 2nd antresol floor is arranged in the entire width of the cell in axes 117/AB, has a total area of 905.8 m2.
At elevation + 9.450 there are administrative rooms, dressing rooms with sanitary blocks, eating rooms, bathrooms and utility rooms. The area of administrative and household premises is enclosed by fire barriers of the 1st type with a fire resistance limit REI 150. The 3rd antresol floor is arranged only in the central part of the cell in axes 513/AB, its total area is 493.2 m2.
In accordance with SNiP 210197 *, access to the roof of fire departments is provided by external metal fire ladders of type P1.
For each section of the roof 12x12m, one light lamp is arranged to provide natural light.
Due to the specifics of the production process, the work of people with disabilities in storage bins is not provided. Measures to ensure the livelihood of persons with disabilities and people with disabilities are not provided.
Engineering equipment
The water supply of the building is carried out from the city water supply. Fire-fighting tank is used as water supply source for internal fire-fighting systems
The project provides for the entry of CVS and GVS into the warehouse for household and drinking needs from the main pipeline passing under the ceiling of the warehouse. To account for water consumption by tenants, a water meter is installed in each cell in the CW room.
In the designed building, a dead end network of cold domestic and drinking water supply is provided. Hot water supply networks are annular, with circulation pipelines.
The project provides for the supply of hot and cold water pipelines to the bathrooms, to the eating room.
Lines and risers of domestic and drinking water supply are installed from steel water and gas galvanized pipes as per GOST 326275. The pipelines of consumers are routed by pipes made of cross-linked polyethylene (PEX - pipelines manufactured by Rehau).
The following sewage systems are provided in the designed building:
- domestic sewerage;
- Internal water flow;
- drainage sewer.
Rain and meltwater from the roof of the building by the system of internal drains is diverted to the on-site drainage network. Removal of rain and meltwater from the roof is carried out using the gravitational vacuum system of the Geberit pluvial storm drain through the system of internal drains from high-density polyethylene pipes HDPE, diameter 100200 mm.
The household sewage system removes effluents from the bathrooms .
Household wastewater discharge is carried out through the household sewage system of cast iron pipes Du 100 mm, with discharge of effluents to the designed on-site network. Supply to instruments is installed from sewage polypropylene pipes
The drainage system is made of steel electric welded pipes as per GOST 1070491.
Heat supply of the designed object is carried out from the boiler house located on the territory of the complex. Each cell has a room in which there is a distribution comb dividing the coolant into ventilation, heating of administrative and household premises, heating and ventilation of the warehouse room, air curtains. The coolant for heating and ventilation is water with parameters of 9070 °. Air is removed from the heating system through automatic air cranes installed on the devices.
Control of heat flow of air-heating units is performed by temperature in the warehouse room with control valves limiting coolant flow rate.
Main pipelines of the heating system shall be made: d < = 40mm - of steel water and gas pipes as per GOST 326285 and d > = 50mm - of electric welded pipes as per GOST 1070491 with anti-corrosion coating. All lines are heat insulated to prevent heat loss. Pipelines shall be coated with anticorrosive primer and heat insulated in accordance with SNiP 2.04.1488 *. Mineral wool cylinders coated with "Izotek" foil for pipelines with coolant temperature below 100 ° С shall be used as material for heat insulation of pipes.
The design provides for supply and exhaust ventilation with mechanical motive, to ensure a comfortable temperature regime in the administrative and auxiliary rooms of the building.
The charging ventilation system is provided separate from other systems by plenum units and exhaust explosion-proof fans.
Ventilation of the storage area is provided by air-heating units installed under the ceiling. Outdoor air is taken on the roof of the building.
The design solutions for telephony provide for the organization of an internal telephone distribution network
The internal distribution network is connected via on-site telephone networks to the PBX of the ABC building.
The radio broadcasting network of the warehouse complex consists of a radio receiver and an internal distribution network, according to TU No. 16/6838 dated October 31, 2007. From EMERCOM of Russia in the Moscow region.
Reception of emergency warning signal is performed using program source RUSH650I.
Power supply of the storage complex current collectors is provided from the separate 10/0.4 kV block type TPs manufactured by Schneider Electric, according to the II category of power supply reliability. The TP receives power from the RTP installed on the site of the complex, powered by 10 kV voltage from two supply centers in accordance with the specification.
All electrical equipment of the storage bin is mostly powered by category III power supply. The power supply system also provides for the power supply of the allocated current collectors according to category I of reliability of the power supply.
Power supply reliability category I includes the following electric receivers:
Emergency and evacuation lighting
Fire protection systems
The mains voltage is a three-phase 380/220 V frequency of 50 Hz with a deaf-grounded neutral.
The main electric receivers of the warehouse complex:
Electric lighting
Ventilation and air conditioning units
Engineering equipment
Tenant Process Equipment
Fire protection systems
For technical metering of power consumption, metering is arranged at GRF inputs. Commercial accounting of electricity is organized according to the specifications of "Power Generation" with output of parameters to the central control panel of the building.
Main construction indicators according to the master plan:
The area of the site within the boundaries of the branch is 2.85 hectares.
Building area - 9216m2
Building density - 32%
Landscaping area - 1415m2
Greening density - 49%
Area of roads, sidewalks and paved areas 4929 m2
Construction volume - 141000 m3.
Design section
2.1 Calculation of rafter truss
2.1.1 Design Assignment
It is required to design a rafter farm of the warehouse building of the office warehouse complex, which is part of the Skhodnya industrial park in the city district of Khimki, with the following data: truss span 24 m, truss pitch in longitudinal direction 6 m. The roof is warm, consisting of galvanized profilist of H1146000.8 - 114 mm grade, laid on roofing structures, steam insulation - layer of polyethylene film, mineral-based insulation - Isover Dachoterm G, thickness - 150 mm, 180 = 1.5/1.0 kg/m3, PLC an kg d 2.0 membrane Arm The estimated snow cover area is III .
Farm material - C245 brand steel in accordance with GOST 3802005, Ry = 240 MPas. Rod joints in truss units - on welding, semi-automatic welding, welded wire of SV08A grade .
Foundations and foundations
3.1. Introduction
Engineering and geological surveys were carried out on the site of the office warehouse complex designed for construction, located on the territory of the Skhodnya industrial park in Khimki, Moscow Region.
The purpose of the surveys was to study the engineering, geological and hydrogeological conditions of the site; geologolithological structure; determination of physical and mechanical properties of soils; assessment of hydrogeological conditions. Surveys were carried out in connection with the new construction. On site, the construction of a warehouse complex is being designed. Type of foundations: stand-alone, on a pile base. Level of responsibility of buildings - II.
To solve the set tasks, wells were passed, laboratory and field studies of soils were carried out. The composition and scope of work are assigned in accordance with the current SP 47.13330.2016 "Engineering Surveys for Construction. Main Provisions, "SP 1110597" Engineering and Geological Surveys for Construction. "
Field works were carried out in October 2007. Drilling of wells was carried out by a mechanical impact-rope method, a drilling rig UGB1VS with a diameter of 168mm. A total of 30 wells were drilled, 15 of which are technical. Depth of boreholes 30m.
To determine the physical and mechanical properties of soils from all wells, in accordance with the requirements of GOST 120712000, samples of undamaged addition were taken with preliminary grinding of the bottomhole at 1520 cm. Sampling interval is 1.0m.
Static processing of the results of laboratory tests of soils is performed in accordance with the current GOST 2052296.
3.2. Construction Site Geotechnical Conditions
3.2.1. Study of engineering and geological conditions of the work area
Engineering and geological surveys were not previously carried out on the studied site.
3.2.2. Geological and geological structure and hydrogeological conditions of the site.
Geomorphically, the studied site is located in the watershed part of the river. Convergence and the river. Klyazma. Absolute surface elevations vary from 176.39 to 184.84 m.
Quaternary deposits are opened directly at the site, which belong in accordance with GOST 2510095 to the class of natural connected dispersed soils, mainly with mechanical and water-colloidal structural bonds of sedimentary genesis.
The following engineering and geological elements (EGE) are identified in the Geological and Geological section of the site up to a depth of 30.0 m according to the drilling data of well No. 130:
EGE-1 (eQIV) from 0.0 to 0.50.8 plant layer, dark brown, with root passages and worm passages, with plant residues;
EGE-2 (eQIII) from 0.50.8 to 7.39.4 m - yellow-brown loam, from solid to semi-solid, subsidence, unsalted, non-swelling, with rare inclusions of carbonates, gypsum and manganese hydrooxides. In the depth intervals of 5.99.4m, a blurred buried soil horizon was opened;
EGE-3 (eQIII) from 7.39.4 to 14.317.3 yellow-brown lugs, with brown tint, from refractory to soft-plastic, non-sedimentary, unsalted, non-swelling, with multiple ties of carbonates with a diameter of 2.0m and points of manganese hydroxides. In depth intervals of 8.211.8m; 10,515,2 m; 13.517.3m opened up to three eroded buried soil horizons;
EGE-4 (eQII) from 14,317,3 to 21,124, 6 m brown-brown clay, from solid to semi-solid, non-sedimentary, non-saline, non-swelling, with inclusions of manganese hydroxides and fine filamentous carbonates. In depth intervals of 14.617.6 m, a blurred buried soil horizon was opened;
EGE-5 (eQII) from 21,124,6 to 30, 0 m yellow-brown loam, with a brownish tint, from solid to semi-solid, non-sedimentary, unsalted, non-swelling, with points of manganese hydroxides and single inclusions of carbonate ties.
In October 2007, when drilling wells No. 130 to a depth of 30 m, underground water was opened by all wells at depths of 8.310.3m (abs.otm. 169.57175.42m) and was established at depths of 8.110.1m (abs.otm 169,77175,62 m). The regional water stop has not been opened. Water-containing soils are IGE3. The amplitude of the groundwater level fluctuation is 1.01.5m.
According to the totality of factors, the site belongs to the third category of complexity of engineering and geological conditions.
3.2.3. Field studies of soils
15 soil tests by static probing were performed at the site.
The purpose of probing was to clarify in plan and depth the boundaries between lithological varieties of soils, to obtain regulatory characteristics of strength and deformation properties of soils.
The work was performed in accordance with GOST 1991201 with the "Pica15" set, the type of installation is medium, the type of probe is II. The penetration rate of the probe into the soils did not exceed 1.01.2m/min. Stops were provided for increasing the probe rods, while the load on the probe did not change. Static probing was carried out to the maximum allowable for this type of resistance installation. The report was made at an interval of 0.1 m. depth of soil probing is 30.0 m.
3.2.5. Design geomechanical model of the object
Static calculations in accordance with GOST 2052296 were made to obtain normative and calculated values of soil properties.
At the same time, the nature of spatial variability of soil properties indicators was taken into account. As a criterion of their degree of variability, the coefficients of variation recommended by GOST 2052296 are used. Based on the analysis of the results of static treatment and in accordance with the classification of soils, the following design soil elements (EWG) are identified:
- no EWG is allocated within EPE1;
- within IGE2 it is allocated RGE2suglinok heavy dusty, firm, collapsible, not salted, not bulking up;
- within IGE3, heavy dusty, refractory, non-sedimentary, unsalted, non-swelling RGE3loam is isolated;
- within IGE4 it is allocated RGE4glina easy dusty, semisolid, not collapsible, not salted, not bulking up;
- within IGE5 RGE5 loam heavy dusty, semisolid, not collapsible, not salted, not bulking up is allocated.
The module of total deformation of soils is calculated according to the formula En = Ek * mk.
Compression modules of soil deformation RGE2 are calculated according to the results of laboratory tests in the pressure range of 0.050.15mPa. The coefficient mk is derived from the correlation relationship mk = f (Ek; IL). Compression modules of soil deformation RGE3; 4; 5 are calculated according to the results of laboratory studies in the pressure range 0.10, 2mPa.
Specific adhesion and angle of internal friction of all soils are determined in laboratory conditions. For RGE2 soils, tests were carried out according to the scheme of unconsolidated undecorated cut at full water saturation. RGE3; 4; 5 soils were tested according to the consolidated slice scheme.
Job Instruction for Drilling Piles
4.1.1 Scope of Job Instruction Application.
Characteristics of the construction facility.
This TC was developed for the construction of bored piles during the construction of the office warehouse complex, which is part of the Skhodnya industrial park in the city district of Khimki.
The designed building is of a simple plan configuration with dimensions in axes 96 × 96 m (in axes). The base of the storage building is located in the axes:
- in longitudinal direction: 1 - 17;
- in the transverse direction: A - L.
The design provides for reinforcement of the foundation base for the column with bored piles with a section of 350x350. Design pile length is 13 m.
Piles are designed from concrete of class B35 on sulphate-resistant Portland cement, concrete grade by waterproof W4. The BNS barrel is reinforced with a welded frame 13.5 m long from reinforcement bars 12∅5BpII. Protective layer of concrete for working reinforcement of pile is provided by welding to three longitudinal rods of spatial frame of shorts-skids from round steel in the form of bracket.
Scope of works included in the Job Instruction.
This JI provides for execution of the following technological processes:
- drilling of wells by drilling rig 1BA15N.01;
- cleaning of soil from the pile mouth and loading of drilled soil into the dump truck;
- installation of reinforcement frame in the well and concreting of BNS;
- processes related to quality check of works.
Characteristics of the working conditions.
The works shall be performed in accordance with the working drawings and SP 45.13330.2017, SP 501022003, SNiP 12032001, SNiP 12042002.
This JI provides for work performance in summer time in two shifts.
4.1.2 Organization and technology of the construction process.
Instructions for preparation of construction site and requirements for readiness of previous works.
All works of the preparatory period, including fencing of the territory of the construction site, arrangement of temporary office premises and provision of sanitary and household needs of the workers, shall be performed at the construction site prior to the start of BNS construction works.
During construction, the pit should be opened to the design level and the exit to the pit should be made.
The required process equipment, accessories and accessories shall be delivered to the construction site.
Methods and sequence of work execution.
BNS fabrication is performed in the following sequence.
Drilling machine is installed on BNS manufacturing point. During penetration of the first 3 m of the well, soil to the surface is supplied by the working tool of the drilling rig 1BA15N.01. The drilled soil is loaded by a forklift truck into vehicles and taken out of the construction site.
In the process of drilling wells for piles, tool failures should be noted. When fixing a failure, it is necessary to stop the work and inform the author's supervision.
Well bottomhole during drilling shall be brought to design elevations. If the obstacles encountered during drilling above the design level of its bottomhole cannot be overcome, the decision on the possibility of using wells for piling should be made by the design organization.
Upon completion of drilling it is necessary to check compliance with design of actual sizes of wells, elevation of their wellhead, bottomhole and location of each well in plan, and also to establish compliance of soil of base with data of engineering and geological surveys (if necessary with the help of geologist). Scan results are recorded in the working log.
Prior to installation of the reinforcement frame and after its installation, the well shall be inspected for loose soil in the bottomhole, showers, dislocations, water and sludge.
Pile concreting is permitted only after inspection and execution of concealed drilling and reinforcement acts.
Pile concreting shall be carried out not later than 24 hours after completion of drilling. If concreting is impossible within the specified terms, drilling of wells should not be started, and those already started should be stopped, without bringing them by bottomhole by 1-2 m to the design level.
BNS concreting is performed by the method of vertically movable pipe (NRMM) and consists of the following operations:
- Reinforcement frame with fixators of well pile position is installed in the finished well for guaranteed creation of protective layer of concrete with thickness of 5060mm on pile shaft.
- Concrete mixture is laid in the well by the NRMM method. For concreting, a receiving hopper with a concrete cast pipe with a diameter of 250325 mm is used. The volume of the hopper shall not be less than the internal volume of the concrete-cast pipe. Joints of concrete-cast pipe sections shall be sealed. If there is (before concreting) water in the well with a layer of more than 20 cm, the concrete-cast pipe shall be equipped with a check valve.
Concrete mixture is fed into receiving funnel of concrete-cast pipe by means of non-rotating hopper with capacity of 1.0m supplied to place of concrete laying by car crane. As the well is filled with concrete, the concrete pipe is removed from the well. Compaction of concrete mixture in well is performed by means of vibrators fixed on concrete-cast pipes. The distance between the bottom of the well and the lower end of the concrete pipe at the beginning of concreting should not exceed 30 cm. During concreting, the concrete pipe should be lifted. At the same time, the lower end must be permanently buried under the level of concrete mixture by at least 1 m.
During concreting the concreting pipe shall be permanently filled with concrete mixture. Interruptions in the supply of individual portions of concrete mixture shall not exceed the setting period established by the laboratory at this cement grade and ambient temperature
Concrete mixture should be fed into the well until clean (without sludge) concrete mixture comes to the surface and finished with removal of contaminated layer of concrete mixture.
Upon completion of concreting of the well, concrete-cast pipe is removed and the pile head is formed.
Upon completion of BNS fabrication work, pile head shall be maintained for the period of strength gain.
The whole cycle described above is repeated with the arrangement of each well.
Job Instruction for construction of cast-in-situ reinforced concrete foundations.
4.2.1 Scope of Job Instruction Application
Job instruction developed for the device
reinforced concrete columnar foundations for multi-span columns
buildings with dimensions in the plan of 96x96 m. The size of the spans is 12 m. The pitch of the columns is 24 m. The length of the building is 96 m. Soil is loam. Soil layout for floors is performed at the same level as the foundation top, i.e. at elevation 0.150m.
The works considered in the map include:
formwork and reinforcement of foundations, concrete laying, concrete maintenance and maintenance, structure decoration and acceptance.
4.2.2 Description of working conditions.
The average outside air temperature is 15 ° С. Formwork of Monolit77 type, reinforcement and concrete are delivered by road at a distance of 5 km. The timeframe shall be set during the design process when selecting and comparing the most rational solutions.
The works should be performed in accordance with the requirements of the following regulatory documents:
SNiP 12012004. Organization of construction;
SP 70.13330.2012. Bearing and enclosing structures;
SP 45.13330.2012 Earthworks, foundations and foundations;
SNiP 12032001. Labor safety in construction. Part 1. General requirements;
SNiP 12042002. Labor safety in construction. Part 2. Construction production.
4.2.3 Construction Process Organization and Technology
Readiness of works preceding the foundation arrangement,
In accordance with the requirements of SNiPA 12012004 for the organization of construction, the following works were carried out before the construction of the foundations:
fenced the territory of the construction site with a fence 2m high;
surface water removal from the pit is organized;
access roads and roads are arranged;
household premises are arranged;
2 trips for equipment are arranged;
concrete preparation for foundations has been performed;
reinforcement nets and formwork sets were introduced in an amount that ensures uninterrupted operation for at least two shifts;
acts of foundation foundation acceptance are drawn up in accordance with the executive diagram;
welding devices are connected;
geodetic breakdown of axes and marking of foundation position in accordance with design; hairlines fixing the position of the working plane of the formwork panels are applied to the surface of concrete preparation with paint.
Earthworks are made in the form of solid pit. The natural slope is 2.6 m. The excavation depth is 3.45 m. The calculation is carried out in accordance with the requirements of SNiP 12042002.
The soil moves along the construction site and is laid in the embankment, for the possibility of backfilling. The soil is placed so that it does not interfere with the complex mechanization of the work on the construction of foundations.
Storage and stock of materials.
Shields and fasteners are delivered in accordance with the application. It is drawn up on the basis of the table indicated on the sheet for the first two captures. They are unloaded and stored in the area of the assembly site. The assembly site is a planned and packed section. It is located next to the first two grips so that the assembled enlarged panels and volume blocks can be immediately installed by crane at the place of their concreting.
Rebar grids for the first two and all other grips are started and stacked in sets on each gripper. They are stored on the concrete of the underlying layer. It is desirable to deliver the required formwork and reinforcement in preparation for operation. At the same time, for unloading and storage, the crane selected in item 5 for assembly and rearrangement of the formwork can be used.
4.2.4 Methods and sequence of works execution.
This section discusses the characteristics of the work and imposes basic decisions on the means and methods of its execution.
Installation processes and concreting occur in one shift. First, the formwork is mounted and its reinforcement takes place on the first grip. The next day, it is concreted in one shift.
The next morning, the structures are expanded, and the enlarged formwork shields are transferred to the second grip, waterproofing is applied. On the fourth working day (see Work Schedule), on the first gripping, the railway foundations are installed and the foundations-pillars are arranged for 3 days, side coating waterproofing is applied, while on the second gripping installation processes are started, etc.
Formwork arrangement and reinforcement of foundations.
The basis for the decision is the study of the material in paragraphs 2-5 of the annex and paragraph 2.2. the main part.
Start by dividing the building into grabs and assigning them numbers in the order of work. The gripping plan is shown on sheet 1. The procedure for the capture works is of great importance.
As previously noted in item 2.2, the assembly of formwork and panels up to 1m2 must be carried out on the assembly site. Full assembly of formwork sets is performed in the following sequence:
horizontal grid C-1 is set to the design position;
assembly and installation of lower stage of formwork;
the 2nd degree of formwork is collected;
S2 volumetric frame is installed in the lower formwork box on the pre-installed C-1 grid;
All operations for movement of formwork boards and rebar grids are performed by crane. The crane adopted by the parameters should provide such an opportunity. After assembling and installing all the foundations of the first and second grips, the entire stock of grids, fasteners and shields imported for them is exhausted and the need for an assembly site disappears.
After concreting the foundations of the first grip and holding the concrete, the formwork on each of the foundations is disassembled by large blocks using a crane, cleaned, lubricated, rearranged to the next grip and reassembled here. For the first grip, the next is the second, for the second - the fourth, for the third - the fifth, etc. This means that in order to allow the crane to rearrange the formwork from the gripper to the gripper at the selected departure and lifting capacity of the crane, the third gripper must be in the gripper plan next to the first, the second near the fourth, etc., that is, within the crane range.
In places where the crane booms are not enough to move the formwork from the grip to the grip, it is transported by transport with loading and unloading by a selected crane.
The crane installing the formwork immediately performs reinforcement of the foundations with nets introduced and laid in advance by separate units on the construction site. Since the C-2 nets are welded into a three-dimensional frame on each grip, when the crane is relocated, the welding transformer must move with it and the cable must be dragged to connect it.
Concreting of foundations.
The general plan of the foundations shows the path of concrete laying equipment, parking, places of example concrete, etc. Also the sections with characteristic moments of works are presented.
First portions of concrete mix enter lower stage along perimeter. The mixture is then fed through a receiving hopper and link hobs slowly and even intermittently in 11.5 hours. The mixture is subjected to vibration compaction by internal vibrators immersing them in the mixture through open faces of the lower stage and repositioning them along the perimeter of the stage towards the center of the foundation. Vibration compaction of the second stage concrete is carried out similarly, after which they are smoothed. Concrete mixture can be laid in pylons immediately after completion of laying in stages. Mixture in columns is compacted by internal vibrators lowering them from above.
In the course of keeping take care for concrete which provides: maintenance of the temperaturnovlazhnostny mode, prevention of considerable temperaturnousadochny deformations and formation of cracks, protection of the hardening concrete from blows, concussions, and other undesirable influences.
In summer, concrete on ordinary Portland cements is watered for 7 days. At air temperature above + 15 ° C during 3 day, watering is carried out every 3 hours and once at night, and in subsequent days - at least three times a day.
4.2.5 Work schedule.
The work schedule was drawn up on the basis of the in-line performance of work, calculations and decisions made on the turnover of the formwork, the schedule is located on sheet No. 6.
4.2.6 Methods and methods of labor of workers
Formwork arrangement.
The formwork is installed from shields, which are connected before installation in rectangular boxes by means of wire ties and spacers. Two bridges are laid on the lower stage box on the width of the next stage.
Boxes of the second and overlying stages have elongated lower boards, by means of which they rest on underlying boxes.
To reduce the adhesion of the formwork to concrete, the front surface of the installed formwork is covered with lubricant - lime milk, an aqueous solution of fatty clay, treated with mineral oils. The cladding of the formwork shall be lubricated prior to installation of the fittings. Accuracy of formwork installation is checked taking into account permissible deviations from nominal dimensions.
Job Instruction for Frame Installation
4.3.1 Characteristics of the building and structures
The process sheet was developed for the installation of metal structures of the framework of the office warehouse complex located on the territory of the Skhodnya industrial park in Khimki, Moscow Region. The warehouse building is 1-storey, with a total height of 16 m to the parapet, a multi-span industrial building with a plan size of 96x96 m. The warehouse complex is a building with a steel frame, the supporting structures are columns, fawl columns, column connections, building trusses, rafters and covering links are made of box bent profile. Connection of metal structures on high-strength bolts.
Height to the bottom of bearing structures (24 meter rafter truss) 12.0 m. Weight of structures is accepted up to 1 t.
4.3.2 Scope of works covered by the map
The routing includes the following process operations:
preliminary assembly of structures;
installation of columns and column links;
installation of framing trusses, rafters and plating links;
grouting of column joints with foundations
As well as combined processes related to unloading and laying out of building structures
4.3.3 Description of working conditions
Work is carried out in the summer at an average outdoor temperature of + 15 ° С per shift.
4.3.4 Organization and technology of construction processes
Instructions for preparation of the facility and requirements for readiness of previous works.
Prior to installation of the building frame, the following types of work shall be performed:
• fence the territory of the construction site with a fence 2 m high, meeting the requirements of GOST 2340778 "Fencing of inventory of construction sites and construction and installation work areas." In the fence for the passage of vehicles delivering building structures and materials to the construction site, perform the installation of an open gate with a width of 4 m;
place temporary buildings and structures;
perform partial vertical layout of the site with organization of surface water drains;
cut down trees according to the cutting list;
equip places for washing the wheels of builders' vehicles;
perform incoming quality control of used construction materials and products;
arrange a temporary road with a width of 4 m for vehicles to pass through the construction site from prefabricated reinforced concrete road slabs. The width of the temporary road at the turning point must be at least 5 m. The radius of the fillet is 12 m;
illuminate the construction site by installing spotlights PZS35 on supports along the perimeter of the construction site. Lighting shall be switched on by a separate chopper;
at domestic premises equip a place with primary fire extinguishing equipment;
for temporary water supply, lay a temporary water supply line from existing networks according to the specifications for temporary water supply of the construction site, or install a metal tank with a volume of at least 5 m;
deliver construction machines and mechanisms to the construction site;
provide the brigade with the necessary tools, equipment and devices;
prepare the necessary equipment, accessories and mechanisms, as well as temporary material storage sites for operation;
when entering the territory of the construction site, install an information board, as well as construction safety signs "Danger zone. Passage is forbidden! "or" Danger zone. The crane works ";
for external communication, the construction site should be equipped with a telephone from the city telephone network;
foundation erection was completed, backfilling and compaction were carried out;
draw up an executive diagram of the foundations and check the presence of acts for hidden works;
Material warehousing and stock
Materials shall be stored in the locations of certain PIC on leveled sites. The slope of storage sites shall not exceed 5 °. The areas shall be filled with 510 cm thick crushed stone or sand and the vegetation layer removed. Storage of materials, articles and structures on bulk unpressurized soils is not allowed.
Electrical safety at the construction site shall be ensured by:
possibility of disconnection of consumers by power cabinet chopper;
laying temporary power supply and lighting networks of the cabinet;
- connection of consumers through plug connectors with grounded
neutrality.
Fire safety at the construction site shall be ensured by compliance with the "Fire Safety Rules of the Russian Federation," as well as the following:
location of production, storage and auxiliary buildings and structures on the construction site shall correspond to the approved construction plan;
Free passage shall be provided to all buildings under construction and operation, to storage places of materials and structures.
do not clutter the driveways (entrances) to the construction site.
have an operable set of primary fire extinguishing equipment on the territory of the construction site.
Installation is carried out with preliminary layout of structures in specially designated storage places. The stock of structures, materials and products is created for 6 shifts.
4.3.5 Methods and sequence of works execution
Installation of metal structures is carried out in accordance with SNiP 3.03.0187 "Load-bearing and enclosing structures," SNiP 12012004 "Construction organization," MDS 531.2001 "Recommendations for installation of building structures," GOST 2311899 "Steel construction structures," GOST 2429787 "Incoming product control. Main Provisions, "MDS 125.2000" Manual for Employees of the State Archstroynadzor of Russia on Quality Control of Construction and Installation Works, "SNiP 12032001" Labor Safety in Construction. Part 1. General Requirements, "SNiP 12042002" Occupational Safety in Construction. Part 2. Construction production. "
Automotive cranes KS5473 (Dnipro), KS457191 (Galichanin) and self-propelled crane ST-2-2-40 are used for installation of structures. Car lifters (AGP22.04) are used to ensure that the installer operates at height.
Prior to installation of structures, their pre-assembly and layout in the installation area must be carried out. Pre-assembly of structures is carried out on a special bench in the acquired warehouse outside the installation area. Structures of the frame are supplied to the installation zone by road, long rafter and tuning trusses on semitrailer trusses SPF-20.
Installation is carried out by a complex method. With the complex method, all structures are mounted within one cell, columns, column links, substructure trusses, rafters and coating links are installed in series.
Installation of lifting machines, organization and execution of construction and construction works with their use is carried out in accordance with the PPRK developed by a specialized organization.
The design position of the columns in the plan is ensured by accurate execution of the foundations and correct installation of anchor bolts. The design position of the column in the vertical plane is provided by adjusted support nuts and washers installed on anchor bolts .
Installation of vertical links is performed immediately after installation of columns. Just before installation of vertical links, their pre-assembly is performed
After erection of columns and links on columns within one cell, adjustment trusses, rafter trusses and links on coating are mounted. Immediately before installation of rafter trusses, their pre-assembly is performed.
After installation of columns, column bonds, trusses and coating bonds within one cell, the joints of columns with foundations are ground.
Job Instruction for Installation of Sandwich Panels
4.4.1 Scope of application
The Job Instruction (hereinafter referred to as JI) has been developed for the complex of works on installation of wall barriers (wall panels) from light metal panels of "sandwich" type. The thickness of the sandwichpanels is 150 mm. External wall panels perform not only enclosing, but also aesthetic functions for the erected building.
The purpose of the presented JI is to show the process sequence of construction processes and installation works, the composition and content of JI, examples of filling in the necessary tables and schedules, assistance to builders and designers in the development of process documentation.
The Job Instruction is part of the Work Execution Project, for the execution of certain types of construction and installation and special construction processes, the products of which are the completed structural elements of the building or structure, process equipment, as well as for the performance of certain types of work.
The application of the TC contributes to improving the organization of production, increasing the productivity of labor and its scientific organization, reducing the cost, improving the quality and reducing the duration of construction, safely performing work, organizing rhythmic work, rational use of labor resources and machines, as well as reducing the time for developing the PPR and unifying technological solutions.
Works performed in series during panel installation include:
- before mounting the panels, the safety film is removed from the inner plates of the panels;
- marking of panel installation places, baselines for all steel structures are "beaten off" by leveling;
- installation of panels on support surfaces;
- alignment and fixation of panels in design position
- joints of panels and shaped articles are sealed with silicone sealant.
The works should be performed in accordance with the requirements of the following regulatory documents:
SNiP 12012004. Organization of construction;
SNiP 3.03.0187. Bearing and enclosing structures;
SNiP 12032001. Labor safety in construction. Part 1. General requirements;
SNiP 12042002. Labor safety in construction. Part 2. Construction production.
Organization of construction
5.1. Characteristics of the facility and construction conditions.
The project for the construction of the office and warehouse complex was developed in accordance with the requirement of SNiP 12012004 "Construction Organization." Space-planning and structural solutions are taken from the section of architecture.
The construction site of the office warehouse complex, which is part of the Skhodnya industrial park, is located in the city district of Khimki.
Table 1.1 gives the main technical and economic indicators of the building.
The construction of the office warehouse as a general contractor will be carried out by construction and installation management. Subcontractors are involved to carry out special works (painting, sanitary, electrical, etc.).
Delivery of building materials, structures, products and semi-finished products is carried out by road.
б.и. жб фунд.лист 6.dwg

б.и.Архитектура лист 1,2.dwg

б.и.Буронабивные сваи лист 5.dwg

б.и.Каркас ист 7.dwg

б.и.Кровля лист 9.dwg

б.и.мет строит конструкции лист 3,4.dwg

б.и.Стройгенплан лист 10 календарный план лист 11.dwg

б.и.Сэндвич панели лист 8.dwg

Similar materials
- 09.07.2014
- 15.05.2017
- 04.11.2022