Calculation of a continuous rectification plant for separation of 7,000 kg/h of methanol -ethanol mixture


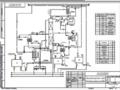
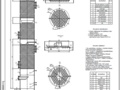
- Added: 10.04.2022
- Size: 3 MB
- Downloads: 0
Description
Ready course project on buttermilk on the topic: Calculation of a continuous rectification plant for the separation of 7,000 kg / h of methanol mixture
Content:
Drawing of the column in the compass;
Drawing of the technological scheme;
Explanatory note.
Project's Content
![]() ![]() ![]() |
![]() ![]() ![]() ![]() |
![]() ![]() ![]() ![]() |
Additional information
Contents
TERMS OF REFERENCE
INTRODUCTION
MATERIAL BALANCE CALCULATION
DETERMINATION OF THE MINIMUM PHLEGM NUMBER
DETERMINING THE OPTIMAL PHLEGM NUMBER
AVERAGE MASS FLOW OF LIQUID AND STEAM IN UPPER AND LOWER PARTS OF COLUMN
CALCULATION OF PHYSICAL PROPERTIES OF FLOWS IN COLUMN FOR COLUMN DIAMETER CALCULATION
STEAM VELOCITY AND COLUMN DIAMETER
NOZZLE HEIGHT CALCULATION
NOZZLE HYDRAULIC RESISTANCE
THERMAL CALCULATION
Deflegmator calculation
Calculation of distillate cooler
Calculation of bottoms cooler
Calculation of power flow heater
Calculation of reboiler
PIPING CALCULATION
CAPACITY CALCULATION
PUMP CALCULATION
LIST OF LITERATURE
Terms of Reference
Calculate and design a continuous distillation plant to separate the methanol-ethanol binary mixture.
Source Data:
Capacity of the initial mixture is 7 t/h.
The temperature of the feed mixture is 20 ° C (the mixture is fed to a pre-heated column to boiling point).
Content of light-volatile component:
in the initial mixture - 33 wt%,
in distillate (rectificate) - 96 wt%,
in bottom liquid - 2 wt%.
The type of column is packed.
The type of contact elements is Rashig ceramic rings, disordered, size 25 × 25 × 3 mm.
Condensation of vapors in the reflux condenser is complete.
Refrigerant in heat exchangers - water. (temperatures: initial 20 ° С, final - select)
Use any of the rectification products to preheat the feed.
Select the heating water vapor parameters.
The pressure in the column is atmospheric.
Installation material - brand 08X22H6T steel.
Introduction
One of the most common methods for separating liquid homogeneous mixtures consisting of two or more components is rectification.
Rectification is the mass exchange process of dividing a liquid mixture into components by countercurrent multiple interaction of vapor and liquid flows having different temperatures. This process in most cases is carried out in counter-current column apparatuses with various contact elements (nozzle, trays).
In the process of rectification, there is a continuous exchange between the liquid and steam phase. The liquid phase is enriched with a higher boiling component and the vapor phase is enriched with a lower boiling component. This two-way exchange of components makes it possible to obtain, in the end, pairs that are almost a pure low-boiling component. These vapors, after condensation in the reflux condenser, give distillate (rectificate) and reflux, a liquid returned for reflux of the column and reaction with rising vapors. Vapors are obtained by partially evaporating a residue in the reboiler, which is an almost pure high-boiling component.
To intensify the mass exchange process, contact elements are used that increase the surface of phase interaction. In the case of trays, steam in the form of a plurality of bubbles forming a developed contact surface passes through a layer of liquid on the tray. Rectification processes are carried out periodically or continuously at various pressures, as well as in various ways. The choice of one or another rectification method is based on a technical and economic calculation and analysis of the properties of the separated mixture. So for separation of mixtures of high-boiling substances rectification under vacuum is used, and for separation of mixtures of substances with close boiling points extractive or azeotropic rectification is used.
Схема.cdw

Колонна.cdw

Similar materials
- 25.01.2023
- 04.04.2021
- 24.01.2023
- 17.03.2024
- 25.01.2023
- 24.01.2023
Free downloading for today
- 24.04.2014