Расчёт ректификационной установки непрерывного действия для разделения 7 000 кг/ч смеси метанол - этанол


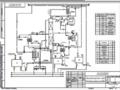
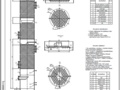
- Добавлен: 10.04.2022
- Размер: 3 MB
- Закачек: 0
Описание
Готовый курсовой проект по пахту на тему: Расчёт ректификационной установки непрерывного действия для разделения 7 000 кг/ч смеси метанол - этанол
Содержание:
Чертеж колонны в компасе;
Чертеж технологической схемы;
Пояснительная записка.
Состав проекта
![]() ![]() ![]() |
![]() ![]() ![]() ![]() |
![]() ![]() ![]() ![]() |
Дополнительная информация
Содержание
ТЕХНИЧЕСКОЕ ЗАДАНИЕ
ВВЕДЕНИЕ
РАСЧЕТ МАТЕРИАЛЬНОГО БАЛАНСА
ОПРЕДЕДЕЛЕНИЕ МИНИМАЛЬНОГО ФЛЕГМОВОГО ЧИСЛА
ОПРЕДЕЛЕНИЕ ОПТИМАЛЬНОГО ФЛЕГМОВОГО ЧИСЛА
СРЕДНИЕ МАССОВЫЕ РАСХОДЫ ПО ЖИДКОСТИ И ПАРУ В ВЕРХНЕЙ И НИЖНЕЙ ЧАСТЯХ КОЛОННЫ
РАСЧЁТ ФИЗИЧЕСКИХ СВОЙСТВ ПОТОКОВ В КОЛОННЕ ДЛЯ РАСЧЁТА ДИАМЕТРА КОЛОННЫ
СКОРОСТЬ ПАРА И ДИАМЕТР КОЛОННЫ
РАСЧЕТ ВЫСОТЫ НАСАДКИ
ГИДРАВЛИЧЕСКОЕ СОПРОТИВЛЕНИЕ НАСАДКИ
ТЕПЛОВОЙ РАСЧЕТ
Расчет дефлегматора
Расчёт холодильника дистиллята
Расчет холодильника кубового остатка
Расчёт подогревателя потока питания
Расчёт кипятильника
РАСЧЕТ ТРУБОПРОВОДОВ
РАСЧЕТ ЁМКОСТЕЙ
РАСЧЕТ НАСОСОВ
СПИСОК ЛИТЕРАТУРЫ
Техническое задание
Рассчитать и спроектировать ректификационную установку непрерывного действия для разделения бинарной смеси метанол–этанол.
Исходные данные:
Производительность по исходной смеси 7 т/ч.
Температура исходной смеси 20°С (смесь подается в колонну с предварительным подогревом до температуры кипения).
Содержание легколетучего компонента:
в исходной смеси – 33 % масс.,
в дистилляте (ректификате) – 96 % масс.,
в кубовой жидкости – 2 % масс.
Тип колонны – насадочная.
Тип контактных элементов – керамические кольца Рашига, неупорядоченные, размер 25×25×3 мм.
Конденсация паров в дефлегматоре – полная.
Хладагент в теплообменниках – вода. (температуры: начальная 20°С, конечную – выбрать)
Для подогрева исходной смеси использовать любой из продуктов ректификации.
Параметры греющего водяного пара выбрать.
Давление в колонне – атмосферное.
Материал установки – сталь марки 08Х22Н6Т.
Введение
Одним из наиболее распространённых методов разделения жидких однородных смесей, состоящих из двух и более числа компонентов, является ректификация.
Ректификация – массообменный процесс разделения жидкой смеси на компоненты путём противоточного многократного взаимодействия потоков пара и жидкости, имеющих различную температуру. Этот процесс в большинстве случаев осуществляется в противоточных колонных аппаратах с различными контактными элементами (насадка, тарелки).
В процессе ректификации происходит непрерывный обмен между жидкой и паровой фазой. Жидкая фаза обогащается более высококипящим компонентом, а паровая фаза – более низкокипящим. Такой двусторонний обмен компонентами, позволяет получить, в конечном счёте, пары, представляющие собой почти чистый низкокипящий компонент. Эти пары после конденсации в дефлегматоре дают дистиллят (ректификат) и флегму – жидкость, возвращаемую для орошения колонны и взаимодействия с поднимающимися парами. Пары получают путём частичного испарения в кипятильнике остатка, являющегося почти чистым высококипящим компонентом.
Чтобы интенсифицировать процесс массообмена применяют контактные элементы, увеличивающие поверхность взаимодействия фаз. В случае применения тарелок, пар в виде множества пузырьков, образующих развитую поверхность контакта, проходит через слой жидкости на тарелке. Процессы ректификации осуществляются периодически или непрерывно при различных давлениях, а также различными способами. Выбор того или иного способа проведения ректификации основано на технико-экономическом расчёте и анализе свойств разделяемой смеси. Так для разделения смесей высококипящих веществ используют ректификацию под вакуумом, а для разделения смесей веществ с близкими температурами кипения используют экстрактивную или азеотропную ректификацию.
Схема.cdw

Среда в трубопроводе
Паро-жидкостная смесь
Колонна ректификационная
Вентиль регулирующий
Технологическая схема.
Ректификационная установка
РХТУ им. Д.И. Менделеева
Колонна.cdw

Давление в колонне 1 атм.
Колонна насадочного типа
керамические кольца Рашига 25*25*3 мм.
испытании и монтаже аппарата
должны выполняться требования:
а) ГОСТ 12.2.003-74 "Оборудование производственное.
Общие требования безопасности";
б) ОСТ 26-291-79 "Сосуды и аппараты стальные
сварные. Технические требования".
Сварные соединения должны соответствовать
требованиям ОСТ 26-01-82-77 "Сварка в химическом
Сварные швы в объеме 100% контролировать
рентгенопросвечиванием.
Прокладка из паронита ПОН-1 ГОСТ 481-80
При заполнении царги насадкой ККР 25*25*3 мм
ввинтить в нижнюю ее часть поддерживающее
заполненное до верху кольцами Рашига
выход жидкости из куба
выход жидкости на испаритель
РХТУ им. Д.И. Менделеева
Техническая характеристика
Технически требования
Рекомендуемые чертежи
- 04.04.2021
- 24.01.2023
- 25.01.2023
- 17.03.2024
- 25.01.2023
- 15.04.2023