Расчет и проектирование тарельчатой ректификационной установки непрерывного действия для разделения бинарной смеси метанол-вода




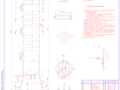
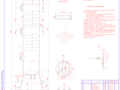
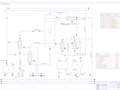
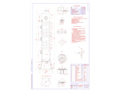
- Добавлен: 25.01.2023
- Размер: 2 MB
- Закачек: 1
- ВКонтакте
- РћРТвЂВВВВВнокласснРСвЂВВВВВРєРСвЂВВВВВ
- Telegram
Описание
Состав проекта
![]() |
![]() |
![]() ![]() ![]() |
![]() ![]() ![]() ![]() |
![]() ![]() ![]() ![]() |
![]() ![]() ![]() ![]() |
![]() ![]() ![]() ![]() |
![]() ![]() ![]() |
![]() ![]() ![]() |
![]() ![]() ![]() ![]() |
Дополнительная информация
работа.docx
Разделение жидкой смеси основано на различной летучести веществ. При ректификации исходная смесь делится на две части: дистиллят - смесь обогащенную низкокипящим компонентом и кубовый остаток - смесь обогащенную высококипящим компонентом.
Процесс ректификации осуществляется в ректификационной установке основным аппаратом которой является ректификационная колонна в которой пары перегоняемой жидкости поднимаются снизу а навстречу парам стекает жидкость подаваемая в виде флегмы в верхнею часть аппарата.
Процесс ректификации может протекать при атмосферном давлении а также при давлениях выше или ниже атмосферного. Под вакуумом ректификацию проводят когда разделению подлежат высококипящие жидкие смеси. Повышенное давление применяют для разделения смесей находящихся в газообразном состоянии при более низком давлении. Атмосферное давление принимают при разделении смесей имеющих температуру кипения 30 - 150°С.
Степень разделения смеси жидкостей на составляющие компоненты и чистота получаемого дистиллята и кубового остатка зависят от того насколько развита поверхность контакта фаз от количества подаваемой на орошение флегмы и устройства ректификационной колонны.
В промышленности применяют тарельчатые насадочные пленочные трубчатые и центробежные пленочные аппараты. Они различаются в основном конструкцией внутреннего устройства аппарата.
Тарельчатые контактные устройства в ректификационной колонне подразделяются на: колпачковые ситчатые клапанные и т.п.
Преимущественное использование тарельчатых колонн в процессах
ректификации объясняется их значительно большей производительностью по сравнению с насадочными.
ОПИСАНИЕ ТЕХНОЛОГИЧЕСКОЙ СХЕМЫ УСТАНОВКИ
Процесс непрерывной ректификации осуществляется в ректификационной установке включающей колонну ректификации подогреватель исходной смеси дефлегматор кипятильник кубовой жидкости холодильники дистиллята и кубового остатка сборники продуктов разделения и насосное оборудование.
Основным аппаратом установки является колонна ректификации в которой пары поднимающиеся из куба колонны взаимодействуют со стекающей сверху жидкостью.
Конечными продуктами разделения являются дистиллят (конденсированные пары легкокипящего компонента) и кубовый остаток (высококипящий компонент).
В данной установке производится разделение бинарной смеси метанол-вода.
Рис.1. Принципиальная схема ректификационной установки
- колонна 2 - подогреватель исходной смеси 3 - гребенка 4 - кипятильник 5 - конденсатор 67 - холодильники 8 - 10 - сборники;
- исходная смесь - дистиллят III - кубовая жидкость IV - пар V - флегма VI - теплоноситель VII - охлаждающий агент
Принципиальная схема процесса непрерывной ректификации бинарных смесей показана на рис. Исходная смесь 1 подогревается в подогревателе 2 (предпочтительно до температуры кипения или близкой к ней) и через гребенку 3 (обеспечивающую возможность варьирования места подачи) подается в ректификационную колонну 1 внутри которой размещены контактные устройства (тарелки насадка). Источником парового потока является кипятильник 4 источником жидкого потока - конденсатор 5. В схеме предусмотрены холодильники 6 и 7 продуктов отбираемых сверху (поток II) и снизу (поток III) а также емкости исходной смеси и продуктов 8-10. Перекачивающие насосы на рисунке не показаны.
Принята следующая терминология основных потоков и узлов ректификационной установки:
поток носит естественное название - исходная смесь;
поток II именуют дистиллятом (или дистиллатом);
поток III называют кубовым остатком (или кубовой жидкостью);
восходящий паровой поток IV так и называют: поток пара (иногда просто "пар");
нисходящий жидкостной поток V (в том числе - возвращаемый сверху в колонну на орошение) именуют флегмой (иногда просто "жидкостью").
Тарелку находящуюся в сечении подачи исходной смеси в колонну 7 называют тарелкой питания.
Часть колонны находящаяся выше тарелки питания (на выходе из нее получается "крепкий" НКК) носит название укрепляющей части колонны (иногда - укрепляющей колонны).
Часть колонны находящаяся ниже тарелки питания (в ней НКК отгоняется из жидкости исчерпывается) носит название отгонной (реже - исчерпывающей) части колонны (иногда - отгонной или исчерпывающей колонны).
Генератор пара называют кипятильником источник флегмы (чаще всего - и дистиллята) - конденсатором.
ВЫБОР КОНСТРУКЦИОННОГО МАТЕРИАЛА АППАРАТА
При конструировании химической аппаратуры следует применять стойкие металлические и неметаллические конструкционные материалы в заданных агрессивных средах. Важно учитывать все виды возможного коррозийного разрушения материалов в агрессивной среде при ее заданных рабочих параметрах. При выполнении прочностных расчетов в первую очередь сталкиваются с необходимостью оценки общей поверхностной коррозии выбираемого конструкционного материала характеризующегося проницаемостью ПМ ммгод.
В расчетах аппаратуры на прочность потеря по толщине материала на коррозию учитывается соответствующей прибавкой С определяемой амортизационным сроком службы аппарата и проницаемость по формуле:
С=ПМ·tа где ПМ ≤ 01 мм год tа – амортизационный срок примем tа=20 лет.
Материал деталей колонны соприкасающихся с метиловым спиртом и водой – сталь марки Х17Н13М2Т ГОСТ 3632-72 [1 с. 534] (корпус аппарата днища люки отбойник сетчатый камера уровнемера приспособление для выверки).
Материал прочих сборочных единиц – сталь 3 ГОСТ 380-71. Материал прокладок – паронит ПОН-1 ГОСТ 481-80.
ОСНОВНЫЕ СВОЙСТВА РАБОЧИХ СРЕД
Температура кипения 0С
Плотность жидкости кгм3
Теплота парообразования кДжкг
Метанол(метиловый спирт древесный спирт карбинол метилгидрат гидроксид метила)— CH3OH простейший одноатомный спирт бесцветнаяядовитаяжидкость.
С воздухом в объёмных концентрациях 672—365% образует взрывоопасные смеси (температура вспышки156°C). Метанол смешивается в любых соотношениях сводойи большинством органическихрастворителей.
При обычных условиях это бесцветная легколетучая горючая жидкость. иногда с запахом напоминающим запах этилового спирта. На организм человека метанол действует опьяняющим образом и является сильным ядом вызывающим потерю зрения и в зависимости от дозы смерть.
Вода- химическое соединение состоящее из 1111% водорода и 8889% (по массе) кислорода.Химически чистая водапредставляет собой бесцветную жидкость без запаха и вкуса.
Вода- единственная жидкость на Земле для которой зависимость удельной теплоемкости от температуры имеет минимум. Этот минимум реализуется при температуре +350С. При этом нормальная температура человеческого тела состоящего на две трети (а в юном возрасте и того более) из воды находится в диапазоне температур 36-380С.
Удельная теплоемкость водысоставляет 4180 Дж(кг·0С) при 00С. Удельная теплота плавления при переходе льда в жидкое состояние составляет 330 кДжкг удельная теплота парообразования - 2250 кДжкг при нормальном давлении и температуре 1000С.
Плотность водыпри охлаждении от 100 до 3980С возрастает как и у подавляющего большинства жидкостей. Но достигнув максимального значения при температуре 3980С плотность при дальнейшем охлаждении воды начинает уменьшаться. Другими словами максимальная плотность воды наблюдается при температуре 3980С а не при температуре замерзания 00С.
Вода - самый сильный универсальный растворитель. Если ей дать достаточно времени она может растворить практически любое твердое вещество. Именно из-за уникальной растворяющей способности воды никому до сих пор не удалось получить химически чистую воду - она всегда содержит растворенный материал сосуда.
ТЕХНОЛОГИЧЕСКИЙ РАСЧЕТ
1. МАТЕРИАЛЬНЫЙ БАЛАНС КОЛОННЫ.
Уравнение материального баланса.
Производительность колонны по дистилляту Р и кубовому остатку W.
Для дальнейших расчетов выразим концентрации питания дистиллята и кубового остатка в мольных долях.
где - молекулярная масса метанола () - молекулярная масса воды .
Относительный мольный расход питания:
Определяем мольные массы исходной смеси дистиллята и кубового остатка.
М=х*МНК + (1 - х) МВК
гдеМНК – молярная масса низкокипящего компонента;
МВК – молярная масса высококипящего компонента.
Переведем количества жидкостей из кгс в кмольc:
Таблица1. Составы и расходы потоков.
Средняя молярная масса кмолькг
Исходная смесь Дистиллят Кубовый остаток
Концентрация легколетучего компонента в паровой фазе .
Исходные данные введем в табл. 2:
Табл. 2 – Данные по парожидкостному равновесию для системы метанол-вода при нормальном давлении.
По данным табл. 1 построим диаграмму равновесия xy: находим:
Рис. 2 – Диаграмма равновесия между паром (у) и жидкостью (х) при постоянном давлении
Минимальное флегмовое число.
Рабочее флегмовое число.
R = 13 Rmin + 03= 13*0789 + 03=1326
Уравнение рабочих линий:
А) верхней части колонны:
В) нижней части колонны:
2. ОПРЕДЕЛЕНИЕ СКОРОСТИ ПАРА И ДИАМЕТРА КОЛОННЫ
Средние концентрации жидкости:
А) в верхней части колонны:
Б) в нижней части колонны:
Средние мольные массы жидкости в верхней и нижней частях колонны.
Средние концентрации пара находим по уравнениям рабочих линий:
А) в верхней части колонны
средние температуры пара определяем по диаграмме t – xу:
Рис.3 Диаграмма равновесия системы метанол –вода
Средние мольные массы и плотности пара:
Средняя плотность пара в колонне:
Температура в верху колонны при хD = 0.937 равняется 65 0С а в кубе-испарителе при хW = 0.023 она равна 960С.
Плотность жидкого метанола при 65 0С :
Плотность воды при 960С:
Средняя плотность жидкости в колонне:
Принимаем расстояние между тарелками h = 300мм. для ситчатых тарелок по графику находим С=0032. Скорость пара в колонне:
Объемный расход проходящий через колонну пара при средней температуре в колонне tCP = (65+96)2 = 8050С:
Принимаем: D = 1600 мм.
Тогда скорость пара в колонне будет:
3 ГИДРАВЛИЧЕСКИЙ РАСЧЕТ ТАРЕЛОК
По каталогу для колонны диаметром 1600 мм выбираем ситчатую тарелку
ТС-Р 1600-300 ОСТ 26-805-73 со следующими конструктивными размерами [3 с217]:
Диаметр отверстий в тарелке do 4 мм
Шаг между отверстиями t 8-15 мм
Относит-ое свободное сечение тарелки при t в пределах 8-15 Fсеч = 147-408%
Свободное сечение колонны F 2.01 м2
Рабочее сечение тарелки Fр 1834 м2
Высота переливного порога hпер 30 мм
Периметр слива П 0795 м
Коэффициент сопротивления 182
Сечение перелива Fсл 0088 м2
Относительная площадь перелива FслFл 44%
Принимаем следующие размеры ситчатой тарелки: диаметр отверстий d0 = 4 мм высота сливной перегородки hП = 40мм. свободное сечение тарелки (суммарная площадь отверстий) 8 % от площади тарелки. Площадь занимаемая двумя сегментами составляет 20 % от общей площади тарелки.
Рассчитаем гидравлическое сопротивление тарелки в верхней и в нижней части колонны по уравнению: р = рсух + р + рпж.
А) Верхняя часть колонны.
Гидравлическое сопротивление сухой тарелки:
= 182 – коэффициент сопротивления неорошаемых ситчатых тарелок со свободным сечением 7 – 10 %;
w0 = 13 008 = 1625 мс – скорость пара в отверстиях тарелки.
Сопротивление обусловленное силами поверхностного натяжения:
– поверхностное натяжение жидкости при средней температуре в верхней части колонны 780С.
Сопротивление парожидкостного слоя на тарелке:
Высота парожидкостного слоя:
величину h – высоту слоя над сливной перегородкой рассчитываем по формуле:
где Vж – объемный расход жидкости м3с; П – периметр
сливной перегородки м; k = ρпжρж – отношение плотности парожидкостного слоя к плотности жидкости принимаемое приближенно равным 05.
Объемный расход жидкости в верхней части колонны:
Периметр сливной перегородки П находим решая систему уравнений:
где R = 09 м – радиус тарелки; 23Пb – приближенное значение площади сегмента.
Решение дает: П = 132 м; b= 0.289 м. находим h:
Высота парожидкостного слоя на тарелке:
hпж = hп + h= 004 + 001 = 005.
Сопротивление парожидкостного слоя:
рпж = 13hпжρпжgk=13 005 05 85665 981= 273Па.
Общее гидравлическое сопротивление тарелки в верхней части колонны:
р’ = рсух + р + рпж = 2355 + 178 + 273 = 5263 Па.
Б) Нижняя часть колонны:
– поверхностное натяжение жидкости при средней температуре в верхней части колонны 88 0С.
hпж = hп + h= 004 + 002= 006 м.
рпж = 13hпжρжgk=13 006 05 854665 981= 3277 Па.
Общее гидравлическое сопротивление тарелки в нижней части колонны:
р’’ = рсух + р + рпж = 1922 + 168 + 3277= 5367Па.
Проверим соблюдается ли при расстоянии между тарелками h = 0.3 м необходимое для нормальной работы тарелок условие
Для тарелок нижней части у которых гидравлическое сопротивление больше чем у тарелок верхней части:
Условие соблюдается.
Проверим равномерность работы тарелок – рассчитаем минимальную скорость пара в отверстиях w0min достаточную для того чтобы ситчатая тарелка работала всеми отверстиями:
Рассчитанная скорость w0m следовательно тарелки будут работать всеми отверстиями.
4 ОПРЕДЕЛЕНИЕ ЧИСЛА ТАРЕЛОК И ВЫСОТЫ КОЛОННЫ.
А)наносим на диаграмму у – х рабочие линии верхней и нижней части колонны и находим число ступеней изменения концентрации пТ. в верхней части колонны п’T = 5 в нижней части колонны п’’T = 4 всего 9 ступени. Число тарелок рассчитывается по уравнению: п = пТ .
Для определения среднего к.п.д. тарелок находим коэффициент относительной летучести разделяемых компонентов α = РМ РВ и динамический коэффициент вязкости исходной смеси при средней температуре в колонне равной 83 0С.
При этой температуре давление насыщенного метанола и воды соответственно равны:
откуда α = РМ РВ = 15264006=38
динамические коэффициенты вязкости метанола и воды соответственно равны [1]:
по графику находим = 047. Длина пути жидкости на тарелке
l = D – 2b = 16 – 2 0.289 = 1022
По графику находим значение поправки на длину пути = 007. Средний к.п.д. тарелок: l = (1 + ) = 0.47(1+0.07) = 0.5.
Для сравнения рассчитаем средний к.п.д. тарелки 0 по критериальной формуле полученной путем статистической обработки многочисленных опытных данных для колпачковых и ситчатых тарелок:
В этой формуле безразмерные комплексы:
где w – скорость пара в колонне мс; SСВ – относительная площадь свободного сечения тарелки; hП – высота сливной перегородки м; ρП и ρЖ – плотности пара и жидкости кгм3; DЖ – коэффициент диффузии легколетучего компонента в исходной смеси; – поверхностное натяжение жидкости питания Нм.
Коэффициент диффузии
В нашем случае: = 1; Ж = 03110-3 Пас; М = МF = 2185 кгкмоль;
= 374 + 148 + 74 = 37см3моль-мольный объем растворенного вещества при температуре кипения; Т = 83 + 273 = 356К.
Безразмерные комплексы:
Средний к.п.д. тарелки:
что близко к найденному значению l.
В верхней части колонны п = п’Т = 5 0.5 = 10;
В нижней части колонны п = п’’Т = 4 0.5 = 8.
Общее число тарелок п = 18 с запасом 22 из них в верхней части колонны 12 и в нижней части 10 тарелок.
Высота тарельчатой части колонны:
НТ = (п-1)h = (22-1)03= 63м.
Н = НТ + НС + НК где Нс = 05м – высота сепарационной части колонны;
Нк = 20м высота кубовой части колонны;
Общее гидравлическое сопротивление тарелок:
р = р’nв + р’’nн = 5263 12 + 5367 10 = 116826 Па
ТЕПЛОВОЙ РАСЧЕТ КОЛОННЫ
1 ПОДРОБНЫЙ РАСЧЕТ ХОЛОДИЛЬНИКА КУБОВОЙ ЖИДКОСТИ
Проведем подробный расчет холодильника кубового остатка. Для горячего теплоносителя (кубовый остаток) принимаем индекс “1” для холодного (оборотная вода) – “2”. Кубовый остаток охлаждается от t1н= 96°С до t1к=25°С при помощи охлаждающего агента. В качестве охлаждающего агента оборотная вода с t2н=12°С и t2к=44°С (принимаем).
Тепловая нагрузка со стороны кубового остатка равна:
удельная теплоемкость кубового остатка при средней температуре tср =
= 1.839*4.24 (96-25) = 553.61
Расход охлаждающей воды при нагреве ее на 200С:
Определим среднюю разность температур. Средняя разность температур tср зависит от схемы движения теплоносителей. Так как в холодильнике не происходит изменение агрегатного состояния теплоносителей и температура их изменяется то целесообразно выбрать противоток так как при противотоке достигается большая величина средней движущей силы теплопередачи tср.
Представим температурный режим теплообменника в виде схемы:
tк2 ← tн232°С ← 12°С
tб = 96 – 32 = 64°С; tм = 25 – 12 = 13°С так как tб tм = 492 > 2 то tср – определяется как средне логарифмическая между tб и tм
Средняя разность температур теплоносителей равна:
В соответствии с таблицей 2.1 [3] принимаем Вт(м2 К). Направим кубовый остаток в межтрубное пространство а в трубное – оборотную воду (хладагент) т.к. больший расход охлаждающей воды (=1839 кгс = 6.6 кгс). Ориентировочные значение поверхности теплообмена найдём по уравнению:
Задаваясь числом Reo=15000 что соответствует развитому турбулентному режиму течения в трубах определим соотношение nz для трубы d=25×2 мм по уравнению:
где n – общее число труб шт.;
внутренний диаметр трубы мм;
динамический коэффициент вязкости воды при средней температуре воды tср2 определен из таблицы 9 учебника [1] Пас;
– наружный диаметр трубы мм.
Соотношение числа труб на число ходов nz определяем по уравнению:
Предварительно выбираем кожухотрубчатый холодильник для охлаждения кубового остатка оборотной водой по ГОСТ 15120 – 79 в таблице 2.3 [1] параметры которого представлены в таблице 3.
Таблица 3– Параметры кожухотрубчатого теплообменника
Параметры теплообменника
Поверхность теплообмена F м2
Площадь сечения одного хода по трубам Fтр м2
Площадь сечения потока между перегородками Fмтр м2
Уточним температуру холодного теплоносителя (воды):
Зададимся температурой стенки и вычислим среднюю разность температур:
При t2=5407°С найдем значения вязкости коэффициента теплопроводности и удельную теплоемкость холодного теплоносителя [1]:
Действительное число Reд находим по уравнению:
Рассчитаем критерий Pr:
Так как температура стенки мало отличается от температуры холодного теплоносителя то примем Prст2=Pr2.
Рассчитаем критерий Nu:
Коэффициент теплоотдачи определим по уравнению[2]:
Рассчитаем тепловой поток:
Тепловая проводимость загрязнений стенок со стороны холодного теплоносителя (вода среднего качества) и кубового остатка равны 1r1=1r2=2320 Вт(м2К) значения из таблицы 2.2 [3]. Теплопроводность нержавеющей стали примем равной из таблицы 28 [2]. Сумма термический сопротивлений стенки и загрязнений равна
где – толщина стенки м.
Коэффициент теплопередачи равен:
Температура стенки со стороны горячего теплоносителя вычисляется по формуле:
С учетом того что количество метанола в кубовом остатке мало = 0023 кмолькмоль смеси 005 будем применять при расчетах что кубовый остаток состоит только из ТЛК (воды). Определим среднюю температуру второго теплоносителя (кубового остатка):
tср1 = (96 + 25) 2 = 605°С.
При tср1 найдем значения вязкости коэффициента теплопроводности и удель-ную теплоемкость кубового остатка в таблицах 92011 [1]:
Определим критерий Прандтля при средней температуре второго теплоносителя (кубового остатка) по формуле:
Определим критерий Прандтля со стороны кубового остатка при tст1=5697°С.
При tст1 найдем значения вязкости коэффициента теплопроводности и удельную теплоемкость кубового остатка в таблицах 92011[1]:
Определим критерий Рейнольдса:
где Sм.тр=0017 м2 – по ГОСТ 15120-79 (таблица 5.1);
Определим критерий Нуссельта:
Удельная тепловая нагрузка со стороны второго теплоносителя (кубового остатка):
Зададимся другой температурой стенки и вычислим среднюю разность температур:
Рассчитаем тепловой поток по формуле:
Температура стенки со стороны второго теплоносителя вычисляется по формуле:
Рассчитаем тепловой поток по формуле:
Проведём аналогичные расчёты при .
Вычислим среднюю разность температур:
Рассчитаем тепловой поток
Температура стенки со стороны второго теплоносителя
При построении зависимости тепловых потоков от температуры со стороны холодного теплоносителя tст2=5110С
Проверим равенство тепловых потоков:
Отклонение соответствует допустимому
Вычислим средний тепловой поток:
Вычислим коэффициент теплопередачи:
Расчетное значение поверхности теплообмена:
Оставляем выбранный кожухотрубчатый холодильник для охлаждения кубового остатка по ГОСТ 15120-79
Поверхность теплообмена F=24м2
F = (1.15 1.20)Fр=24357 м2
Требуемая поверхность теплопередачи:
Запас теплообменной поверхности:
Скорость исходной смеси в трубах определяется по формуле
где плотность воды при tcр2=22°С
Скорость в межтрубном пространстве
где плотность кубового остатка (воды) в межтрубном пространстве при tср1=605°С
Скорость в штуцерах для кубового остатка
Диаметр штуцера выбираем по таблице 2.6 [3] м.
Скорость в штуцерах для охлаждаемой воды
Коэффициент трения при Re≥2300 находим по формуле:
Гидравлическое сопротивление кожухотрубчатого теплообменника в трубном пространстве рассчитывается по формуле:
Гидравлическое сопротивление кожухотрубчатого теплообменника в межтрубном пространстве рассчитывается по формуле
где x=10 – число сегментных перегородок значения из таблицы 2.7 [3]
m – число рядов труб преодолеваемых потоком теплоносителя в межтрубном пространстве.
. Примем округлив в большую сторону
2 РАСЧЕТ ХОЛОДИЛЬНИКА ДИСТИЛЛЯТА
Рассчитать и подобрать нормализованный кожухотрубчатый теплообменник для охлаждения дистиллята. Горячий раствор в количестве кгс охлаждается от °С до °С (примем). Начальная температура охлаждающей воды равна =12°С. Зададимся температурой воды после прохода через теплообменник tк2=32°C.
Выбираем движение теплоносителей противотоком так как при противотоке достигается большая величина средней движущей силы теплопередачи tср.
tб = 56 – 44 = 33°С; tм = 34 – 28 =13°С так как tб tм ≥ 2 то tср – определяется как средне логарифмическая между tб и tм по уравнению
Расход теплоты отдаваемой охлаждающей воде в водяном холодильнике дистиллята определяется по уравнению
удельная теплоемкость дистиллята при средней температуре tср =
Определим расход охлаждающей воды
где – удельная теплоёмкость воды Дж(кгК).
По таблице 2.1 [1] принимаем Кор=450 Вт(мК).
Ориентировочная площадь теплообменника по уравнению
В соответствии с таблицей 2.3 [1] принимаем ГОСТ 15120-79 двухходовой кожухотрубчатый теплообменник со следующими характеристиками Dкож=400 мм F=16 м d=25×2мм L=2м N=100z=2.
Запас площади по уравнению (5.26):
Так как выбранный теплообменник имеет запас площади 2529 % что меньше 40% но больше 10% то он выбран верно.
3 РАСЧЕТ ТЕПЛООБМЕННИКА-ИСПАРИТЕЛЯ
Рассчитать и подобрать нормализованный вид конструкции кожухотрубчатого испарителя ректификационной колонны с GW=1839 кгс паров раствора органической жидкости при температуре кипения tW=t1н=t1к=96° С.
В качестве теплоносителя используем насыщенный водяной пар давлением р=2атм =1967 кПа температурой конденсации t2к=t2н=1196°С.
Расход теплоты получаемой в кубе-испарителе от греющего пара по уравнению
Расход тепла получаемого в кубе-испарителе от греющего пара равен
Находим теплоемкости метанола и воды (см. [1] стр.535 рис. XI).
=1.03(3122.57+1.161*2.75*65+1.839*4.243*96-3*3.608*78) = 3331.95 кВт
Qпотер - приняты в размере 3% от полезно затрачиваемой теплоты
паровой подогреватель смеси
Тепловая нагрузка аппарата QК=333195кВт.
Расход греющего пара.
где - удельная теплота конденсации греющего пара.
Давление греющего пара тогда и
(см. [1] стр.525 табл. LVII). x – степень сухости греющего пара = 095
t1н t1к1196°С 1196°С
t2к ← t2н 96°С ← 96°С
Средняя движущая сила
В соответствии с таблицей 2.1 [3] принимаем ориентировочное значение коэффициента теплопередачи Кор=1800 Вт(мК). Тогда ориентировочные значения площади теплообменника по уравнению
В соответствии с ГОСТ 15121-79 по таблице 2.9 [3] близкую к ориентиро-вочной площади имеет кожухотрубчатый теплообменник с Dкож=600 мм d=25×2 мм S=97 м N=206шт z=4 L= 6 м.
Запас площади по уравнению
Так как выбранный теплообменник имеет запас площади 2367 % что меньше 40% но больше 10% то он выбран верно.
4 РАСЧЕТ КОНДЕНСАТОРА (ДЕФЛЕГМАТОРА)
Рассчитать и подобрать нормализованный вариант конструкции кожухотрубчатого конденсатора смеси паров органической жидкости (дефлегматора) для конденсации кгс паров. Удельная теплота конденсации смеси кДжкг температура конденсации tD =65°С. Тепло конденсации отводится водой с начальной температурой .
Принимаем температуру воды на выходе из конденсатора . Средняя температура воды
Расход тепла отдаваемого охлаждающей воде в конденсаторе-дефлегматоре находим по уравнению
где - удельная теплота конденсации паров в дефлегматоре.
Удельные теплоты конденсации метанола и воды при (см. [1] стр.516 табл. XLV).
=1161*(1326+1)*11563 =3122.57кВт
Тепловая нагрузка аппарата
Средняя разность температур:
tб = 53°С; tм = 33°С так как tб tм 2 то tср – определяется по уравнению
В соответствии с таблицей 2.1 [1] принимаем . Ориенти-ровочные значение поверхности по уравнению
В соответствии с ГОСТ 15119-79 по таблице 2.9 [3] принимаем теплообменник со следующими характеристиками: Dкож=800 мм d=25×2 мм z=4 L=4 м S=127 м2 n=404.
Так как выбранный теплообменник имеет запас площади 22.4% что меньше 40% но больше 10% то он выбран верно.
5 РАСЧЕТ ПОДОГРЕВАТЕЛЯ ИСХОДНОЙ СМЕСИ
Исходную смесь необходимо подогреть от t1н = 24 °C до t1к = 78 °C. Темпера-туру греющего водяного насыщенного пара выберем t2н=t2к=1196 °C (давление 1967 кПа).
tб = 956°С; tм = 416°С так как tб tм ≥ 2 то tср – определяется как среднеарифметическая между tб и tм по уравнению:
Расход тепла в паровом подогревателе смеси
удельная теплоемкость исходной смеси при средней температуре tср = (t1 + tнач) 2 =
([1] стр.535 рис. XI)
Расход греющего пара в подогреватели исходной смеси рассчитаем по формуле
В соответствии с таблицей 2.1 [3] принимаем . Ориентировочные значение поверхности по уравнению
В соответствии с ГОСТ 15120-79 по таблице 2.9 [3] принимаем теплообменник со следующими характеристиками: Dкож=600 мм d=25×2 мм z=2 L=3 м S=57 м2 n=240.
Так как выбранный теплообменник имеет запас площади 284% что меньше 40% но больше 10% то он выбран верно.
В курсовой работе разработана тарельчатая ректификационная установка непрерывного действия для разделения бинарной смеси метанол-вода. Процесс проводится в вертикальной ректификационной установке. Высота тарельчатой части аппарата 6300 мм диаметр 1600мм. Используются ситчатые тарелки типа ТС-Р.
Для подогрева питания используется двухходовой кожухотрубчатый теплообменник с поверхностью теплопередачи 57 м2 диаметром кожуха D=600 мм с 240 трубами размером 25х2 и длиной L=3 м.
В качестве кубового испарителя выбран четырехходовой теплообменник со следующими характеристиками: D=600 мм n=206 размер труб 25х2 и поверхностью теплопередачи 97м2.
В связи с необходимостью охлаждать дистиллят используют холодильник (двухходовой кожухотрубчатый теплообменник) с поверхностью теплопередачи 16 м2 диаметром кожуха D=400 мм с 100 трубами размером 25х2 и длиной L=2 м.
Для охлаждения кубовой жидкости используется двухходовой кожухотрубчатый теплообменник с поверхностью теплопередачи 24 м2 диаметром кожуха D=400 мм с 100 трубами размером 25х2 и длиной L=3 м.
СПИСОК ИСПОЛЬЗОВАННОЙ ЛИТЕРАТУРЫ
Александров И. А. Ректификационные и абсорбционные аппараты. Изд. 3-е. М.: «Химия» 1978. – 280 с.
Борисов Г.С. Брыков В.П. под ред. Дытнерского Ю.И. Основные процессы и аппараты химической технологии. Пособие по проектированию 2-е изд.перераб.и дополненное М.: Химия.1991.-496с.
Колонные аппараты: Каталог. – М.: ЦИНТИхимнефтемаш 1978. – 31с.
ГОСТ 15118—79. Аппараты теплообменные кожухотрубчатые с не- подвижными трубными решетками и кожухотрубчатые с температурным компенсатором на кожухе. Размещение отверстий под трубы в трубных решетках и перегородках. Основные размеры.
ГОСТ 15119—79. Испарители кожухотрубчатые с неподвижными трубными решетками и кожухотрубчатые с температурным компенсатором на кожухе. Основные параметры и размеры.
ГОСТ 15120—79. Холодильники кожухотрубчатые с неподвижными трубными решетками и кожухотрубчатые с температурным компенсатором на кожухе. Основные параметры и размеры.
ГОСТ 15121—79. Конденсаторы кожухотрубчатые с неподвижными трубными решетками и кожухотрубчатые с температурным компенсатором на кожухе. Основные параметры и размеры.
ГОСТ15122—79. Теплообменники кожухотрубчатые с неподвижными трубными решетками и кожухотрубчатые с температурным компенсатором на кожухе. Основные параметры и размеры.
Общий вид.frw

Выход кубового остатка
Планка регулировочная
Болт М12х25 по ГОСТ 7798-70
Гайка М12 по ГОСТ 5616-70
Шайба 12 по ГОСТ 11371-58
Схема расположения штуцеров и люков
Техническая характеристика
Аппарат предназначен для разделения смеси метанол-вода
Номинальная емкость 22 м.
Производительность 10800 кгч.
Давление в колонне атмосферное.
Температура среды в кубе до 96 С.
Среда в аппарате - пожаровзрывоопасная
Тип тарелок - ситчатые.
Технические требования
испытании и поставке аппарата должны
выполняться требования:
а) Госгортехнадзора;
б) ГОСТ 12.2.003 - 74 "Оборудование производственное.
Общие требования безопасности".
в) ОСТ 26-291-79 "Сосуды и аппараты стальные сварные.
Технические требования.
Материал тарелок - сталь 08Х13 ГОСТ 5632 - 72 и сталь 20
остальные сборочные единицы и детали
из стали ВСт 3сп 3 ГОСТ 380 - 71.
Материал прокладок - паронит ПОН - 1 ГОСТ 481 - 80
Материал опоры - 29Г2С ГОСТ 5520 - 79.
Аппарат испытать на прочность и плотность гидравлически
в горизонтальном положении - под давлением 1.25 МПа
тикальном положении - под наливом.
ОСТ 26 - 01 - 82 - 77 "Сварка в химическом машиностроении".
Сварные соединения должны соответствовать требованиям
Сварные швы в объеме 100% контролировать рентгено-
Действительное расположение штуцеров и люков см. на схеме.
Не указанный вылет штуцеров 150 мм.
Размеры для справок.
Выход жидкости на кипятильник
Колонна ректификационная
ДГТУ КП 280.700.30000.ОВ
Колонна_1600.frw

Выход кубового остатка
Планка регулировочная
Болт М12х25 по ГОСТ 7798-70
Гайка М12 по ГОСТ 5616-70
Шайба 12 по ГОСТ 11371-58
Схема расположения штуцеров и люков
Техническая характеристика
Аппарат предназначен для разделения смеси метанол вода
Номинальная емкость 22 м.
Производительность 10800 кгч.
Давление в колонне атмосферное.
Температура среды в кубе до 96 С.
Среда в аппарате - пожаровзрывоопасная
Тип тарелок - ситчатые.
Технические требования
испытании и поставке аппарата должны
выполняться требования:
а) Госгортехнадзора;
б) ГОСТ 12.2.003 - 74 "Оборудование производственное.
Общие требования безопасности".
в) ОСТ 26-291-79 "Сосуды и аппараты стальные сварные.
Технические требования.
Материал тарелок - сталь 08Х13 ГОСТ 5632 - 72 и сталь 20
остальные сборочные единицы и детали
из стали ВСт 3сп 3 ГОСТ 380 - 71.
Материал прокладок - паронит ПОН - 1 ГОСТ 481 - 80
Материал опоры - 29Г2С ГОСТ 5520 - 79.
Аппарат испытать на прочность и плотность гидравлически
в горизонтальном положении - под давлением 1.25 МПа
тикальном положении - под наливом.
ОСТ 26 - 01 - 82 - 77 "Сварка в химическом машиностроении".
Сварные соединения должны соответствовать требованиям
Сварные швы в объеме 100% контролировать рентгено-
Действительное расположение штуцеров и люков см. на схеме.
Не указанный вылет штуцеров 150 мм.
Размеры для справок.
Выход жидкости на кипятильник
Колонна ректификационная
ДГТУ 280.700.30000.ОВ
Технологическая схема.frw

Установка ректификационная.
Технологическая схема.
Условное обозначение
Паро-жидкостная эмульсия
Вода оборотная (подача)
Вентиль регулирующий
Колонна_1600.dwg

Емкость упаренного раствора
Ящик барометрический
Конденсатор барометрический
Сепарационная камера
Емкость исходного раствора
Вход паров из кипятильника
Выход кубового остатка
Планка регулировочная
Болт М12х25 по ГОСТ 7798-70
Гайка М12 по ГОСТ 5616-70
Шайба 12 по ГОСТ 11371-58
Схема расположения штуцеров и люков
Техническая характеристика
Аппарат предназначен для разделения смеси метиловый спирт-вода
Номинальная емкость 22 м.
Производительность 6000 кгч.
Давление в колонне 0.1 МПа.
Температура среды в кубе до 98 С.
Среда в аппарате - пожаровзрывоопасная
Тип тарелок - ситчатые.
Технические требования
испытании и поставке аппарата должны
выполняться требования:
а) Госгортехнадзора;
б) ГОСТ 12.2.003 - 74 "Оборудование производственное.
Общие требования безопасности".
в) ОСТ 26-291-79 "Сосуды и аппараты стальные сварные.
Технические требования.
Материал тарелок - сталь 08Х13 ГОСТ 5632 - 72 и сталь 20
остальные сборочные единицы и детали
из стали ВСт 3сп 3 ГОСТ 380 - 71.
Материал прокладок - паронит ПОН - 1 ГОСТ 481 - 80
Материал опоры - 29Г2С ГОСТ 5520 - 79.
Аппарат испытать на прочность и плотность гидравлически
в горизонтальном положении - под давлением 1.25 МПа
тикальном положении - под наливом.
ОСТ 26 - 01 - 82 - 77 "Сварка в химическом машиностроении".
Сварные соединения должны соответствовать требованиям
Сварные швы в объеме 100% контролировать рентгено-
Действительное расположение штуцеров и люков см. на схеме.
Не указанный вылет штуцеров 150 мм.
Размеры для справок.
Выход жидкости на кипятильник
Колонна ректификационная
Содержание.doc
ВЫБОР КОНСТРУКЦИОННОГО МАТЕРИАЛА АППАРАТА .7
ОСНОВНЫЕ СВОЙСТВА РАБОЧИХ СРЕД 7
ТЕХНОЛОГИЧЕСКИЙ РАСЧЕТ 9
1. Материальный баланс ..9
2. Определение скорости пара и диаметра колонны .12
3. Гидравлический расчет тарелок 14
4. Определение числа тарелок и высоты колонны .17
ТЕПЛОВОЙ РАСЧЕТ КОЛОННЫ .19
1. Подробный расчет холодильника кубового остатка ..19
2. Расчет холодильника дистиллята .29
3. Расчет теплообменника-испарителя 31
4. Расчет конденсатора-дефлегматора .32
5. Расчет подогревателя исходной смеси 34
СПИСОК ИСПОЛЬЗОВАННОЙ ЛИТЕРАТУРЫ ..37
ТИТУЛЬНЫЙ ЛИСТ и ЗАДАНИЕ.docx
Федеральное государственное бюджетное образовательное учреждение
высшего профессионального образования
«ДОНСКОЙ ГОСУДАРСТВЕННЫЙ ТЕХНИЧЕСКИЙ УНИВЕРСИТЕТ»
Кафедра «Безопасность жизнедеятельности и защита окружающей среды»
д.т.н. проф. Месхи Б.Ч.
ПОЯСНИТЕЛЬНАЯ ЗАПИСКА
к курсовому проекту на тему:
«Ректификационная установка непрерывного действия для разделения смеси: метанол - вода»
Автор дипломного проекта
Обозначение дипломного проекта
Специальность «Инженерная защита окружающей среды»
Руководитель проекта
Консультант по разделам:
Безопасность жизнедеятельности
Кафедра «Безопасность жизнедеятельности и защиты окружающей среды»
Срок представления проекта к защите
Исходные данные для курсового проекта:
Материалы практики ГОСТы и иная нормативная документация задание на курсовой проект технологические схемы.
Задание принял к исполнению
Схема.dwg

Установка ректификационная.
Технологическая схема.
Условное обозначение
Паро-жидкостная эмульсия
Вода оборотная (подача)
Вентиль регулирующий
Рекомендуемые чертежи
- 17.03.2024
- 24.01.2023
- 10.04.2022
- 04.04.2021
- 15.04.2023