Ректификационная установка непрерывного действия для разделения бинарной смеси ацетон-вода



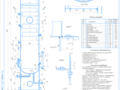
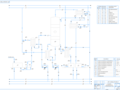
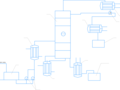
- Добавлен: 25.01.2023
- Размер: 905 KB
- Закачек: 1
Описание
Состав проекта
![]() |
![]() |
![]() ![]() ![]() |
![]() ![]() ![]() |
![]() ![]() ![]() |
![]() ![]() ![]() |
![]() ![]() ![]() |
![]() ![]() ![]() ![]() |
![]() ![]() ![]() |
![]() ![]() ![]() |
![]() ![]() ![]() ![]() |
![]() ![]() ![]() ![]() |
![]() ![]() ![]() |
![]() ![]() ![]() |
![]() ![]() ![]() |
![]() ![]() ![]() |
Дополнительная информация
Содержание.docx
Описание конструкции и принципа действия ректификационной колонны
1. Описание конструкции ректификационной колонны .
2. Принцип действия ректификационной колонны ..
Описания конструкции и принципа действия вспомогательного оборудования ..
Расчет ректификационной колонны
1. Исходные данные .
2. Материальный баланс колонны и выбор рабочего флегмового числа
3. Скорость пара и диаметр колонны ..
4. Высота светлого слоя жидкости на тарелке и паросодержание барботажного слоя ..
5. Гидравлический расчет тарелок
6. Определение числа тарелок и высоты колонны .
Подбор вспомогательного оборудования .. ..
1. Подробный расчет холодильника кубовой жидкости ..
2. Расчет холодильника дистиллята
3. Расчет кожухотрубчатого теплообменника-испарителя .
4. Расчет кожухотрубчатого конденсатора (дефлегматора)
5. Расчет подогревателя исходной смеси ..
6. Расчет центробежного насоса .
7. Расчет диметров штуцеров
Список используемых источников ..
Пояснительная записка 56 с. 19 рис. 4 табл. 5 источников.
РЕКТИФИКАЦИЯ КОЛОННА ПИТАНИЕ ДИСТИЛЛЯТ КУБОВЫЙ ОСТАТОК ТЕПЛООБМЕННИК НАСОС ДЕФЛЕГМАТОР
Целью выполнения курсового проекта является расчёт и проектирование ректификационной установки непрерывного действия для разделения бинарной смеси ацетон – вода.
Произведен расчет ректификационной колонны. Осуществлён подбор и расчёт вспомогательного оборудования: теплообменника-подогревателя для подогрева питания холодильника для кубовой жидкости и дистиллята кубового испарителя насоса для подачи исходной смеси.
В результате спроектирована ректификационная установка непрерывного действия для разделения бинарной смеси ацетон – вода.
Графическая часть включает:
- чертёж общего вида колонны – 1 лист А1;
- чертёж технологической схемы установки – 1 лист А1.
4 расчет колонны.doc
Производительность по исходной смеси 22000 кгч = 6111 кгc.
Массовая доля легколетучего компонента в: исходной смеси 044 кгкг; дистилляте 099кгкг; кубовом остатке 0035 кгкг.
Исходная смесь подается на тарелку питания подогретой до: температуры кипения; =33°С.
Греющий теплоноситель в испарители установки – водяной насыщенный пар.
Охлаждающий теплоноситель в дефлегматоре установки оборотная вода начальная температура 28°С.
Тип колонны: тарельчатая.
Тип контактных устройств: тарелки ситчатые.
Рабочее давление вверху колонны: 01 МПа.
Бинарная смесь ацетон – вода.
2 Материальный баланс колонны и выбор рабочего флегмового числа
Производительность колонны по дистилляту и кубовому остаткукгс определим из уравнений материального баланса колонны [1]:
где – массовые расходы исходной смеси кубового остатка и дистиллята соответственно кгс;
– массовые доли легколетучего компонента в исходной смеси кубовом остатке и дистилляте соответственно кмолькмоль смеси.
Температура кипения ацетона – 56°С воды – 100°С при давление ат. Следовательно легколетучий компонент – ацетон труднолетучий компонент – вода.
Из уравнения (4.1) выразим
Переведем массовые доли данные в задании в мольные [1]
где молярная доля легколетучего компонента в исходной смеси кмоль ацетонакмоль смеси;
М(ЛЛК) и М(ТЛК) – молярные массы легколетучего и труднолетучего компонентов кгкмоль.
Следовательно Мацетона = 58 кгкмоль и Мводы = 18 кгкмоль – молярные массы ацетона (ЛЛК) и воды (ТЛК) соответственно.
Аналогично рассчитываем молярные доли компонента в дистилляте и кубовом остатке :
Нагрузки ректификационной колонны по пару и жидкости определяют рабочим флегмовым числом R его оптимальное значение Rопт можно найти путем технико-экономических расчетов. Ввиду отсутствия надежной методики оценки Rопт используют приближенные вычисления основанные на определении коэффициента избытка флегмы (орошения)
где – минимальное флегмовое число.
Для дальнейших расчетов необходимо построить диаграммы равновесия между паром и жидкостью при постоянном давлении в координатах у – х и t – х у. Данные для построения диаграмм равновесия между паром и жидкостью при постоянном давлении приведены в таблице 4.1.
Диаграммы равновесия между паром и жидкостью при постоянном давлении в координатах у – х и t – х у изображены на рисунках 4.1и 4.2.
Таблица 4.1 Равновесные составы жидкости (х) и пара (у) в мол. долях (в %) и температуры кипения (t) в °С бинарной смеси ацетон вода при давлении 760 мм. рт. ст.
По диаграмме t – х у нашли концентрацию ЛЛК в паре находящемся в равновесии с исходной смесью = 08 кмолькмоль смеси.
Флегмовое число находим графически так как есть точки перегиба на линии равновесия. Из точки а проводим касательную к линии равновесия и отсекаемый отрезок рабочей линией на оси ординат будет равен 061 в соответствие с рисунком 4.2. Формула для расчета [ ]
По формуле (4.6) посчитаем Rmin :
Рабочее флегмовое число можно рассчитать по эмпирической формуле[2]:
Один из способов расчета R заключается в нахождении такого флегмового числа которому соответствует минимальное произведение N(R+1) пропор-циональное объему ректификационной колонны (N – число ступеней изменения концентрации или теоретических тарелок определяющее высоту колонны а R + 1 расход паров и следовательно сечение колонны).
Задавшись различными значениями коэффициентов избытка флегмы определим соответствующие флегмовые числа. Графическим построением ступе-ней изменения концентраций между равновесной и рабочими линиями на диаграмме состав пара у – состав жидкости х находим N. Определение рабочего флегмового числа R ведется путем построения графика N(R+1) от R. Минимальное значение N(R+1) будет соответствовать рабочему флегмовому числу.
Результаты расчетов рабочего флегмового числа представлены в таблице 4.2 и на рисунках 4.3 4.4 4.5 4.6 4.7 4.8 4.9 – определение числа теоретических тарелок соответствующих каждому значению R.
Оптимальное значение флегмового числа Rопт соответствует минимальному значению произведения N(R+1).Например для = 105
Из диаграммы изображенной на рисунке 4.3 видно что число теоретических тарелок . При данном флегмовом числе и числе теоретических тарелок рас-считаем произведение N(R + 1) для = 105
Для остальных значений аналогичные расчеты.
Таблица 4.2 – Результаты расчетов флегмового числа
Коэффициент избытка флегмы
Рабочее флегмовое число R
Число теоретических тарелок N
По диаграмме изображенной на рисунке 4.9 находим минимальное произведение N(R+1) =214 которое соответствует флегмовому числу 142 при коэффициенте избытка флегмы равном 24. Отрезок В будет равен
При рабочем флегмовом числе равному 142 по соответствующему ему отрезку В= 04003 графически определим теоретическое число тарелок. Нахожде-ние числа теоретических тарелок изображено на рисунке 4.10.
Рисунок 4.10 Графическое определение числа теоретических тарелок
Согласно рисунку 4.10 число теоретических тарелок равно 8.
Найдем Lв и Lн – средние массовые расходы (нагрузки) по жидкости для верхней и нижней частей колонны. Для этого найдем хср.в и хср.н – средний мольный состав жидкости соответственно в верхней и нижней частях колоны[1]:
Средние молярные массы жидкости в верхней и нижней частях колонны соответственно равны [1]:
где MТЛК MЛЛК – молярная массы тяжелолетучего и легколетучего компонента.
Молярная масса исходной смеси равна:
Молярная масса дистиллята равна:
Рассчитаем средние массовые потоки пара в верхней и нижней частях колонны по уравнениям [1]:
где – средние молярные массы паров в верхней и нижней частях колонны кгкмоль.
где уср.в уср.н – средние мольные составы паров в верхней и нижней частях колонны соответственно:
уср.в=(097+052)2=064 кмолькмоль смеси
уср.н = (уW + уF) 2 (4.22)
уср.н = (008 + 052) 2 = 018 кмолькмоль смеси
где yW yF – молярные доли ацетона в кубовом остатке и в исходной смеси соответс-твенно.
Подставляем полученные значения в уравнения 4.19 и 4.20:
Тогда массовые потоки пара равны:
3 Скорость пара и диаметр колонны
Найдём плотности жидкости рх.в рх.н и пара ру.в ру.н в верхней и нижней частях колонны при средних температурах в них tср.в tср.н по уравнениям [1]. Средние температуры паров определим по диаграмме t –ху которая представлена на рисунке 4.2.
Рассчитаем плотности жидкой фазы вверху и внизу колонны:
где xоб.вxоб.н – объемные концентрации жидкой фазы соответственно вверху и внизу колонны.
Плотности жидких веществ и водных растворов в зависимости от температу-ры приведены в таблице 4 учебника [2]. Плотность ЛЛК при tср.в =68°С получаем =7352 кгм3 а при tср.н=895°С получаем =7066 кгм3.. Плотность ТЛК при
tср.в получаем =9786 кгм3 а при tср.н получаем=9653 кгм3.
Найдем допустимую скорость пара в колоне с ситчатыми тарелками. Для этого определим допустимую скорость в и н в верхней и нижней частях колонны соответственно [1]
где средняя плотность жидкости кгм;
с коэффициент зависящий от конструкции тарелок расстояния между тарелками рабочего давления колонны нагрузки колонны по жидкости. Зададим расстояние между тарелками h=400мм. По h определим из графика с=f(h) приведенного на рисунке 7.2 учебника [2] значение коэффициента с=0059.
а)допустимая скорость в верхней части колонны:
б)допустимая скорость в нижней части колонны:
Рассчитаем отдельно диметры колонны для верхней и нижней части и возьмём больший
где G – средние массовые потоки пара для верха и низа колонны кгс;
– скорость пара в верхней и нижней частях колонны мс;
ρу – средние плотности пара в верхней и нижней частях колонны кгм3.
Выберем стандартный диаметр обечайки колонны D=18 м.
По ОСТ 26-805-73 выбираем для диаметра колонны D = 1800 мм ситчатую однопоточную тарелку ТС-Р со следующими конструктивными размерами приведенными в таблице 4.3.
Таблица 4.3 Основные характеристики ситчатой тарелки ТС-Р для диаметра колонны 1800 мм
Характеристики тарелки
Диаметр отверстий в тарелки dмм
Шаг между отверстиями мм
Высота переливного порога hпер мм
Относительное свободное сечение тарелки Fс%
Рабочее сечение тарелки Sтм2
Ширина переливного порога bм
Приняв стандартный размер обечайки равным 18 м уточним рабочую ско-рость пара в верхней и нижней частях колонны:
Определим скорость пара в рабочем сечении тарелки [1]
где Sт – рабочее сечение тарелки м2 (значение приведено в таблице 4.3).
4 Высота светлого слоя жидкости на тарелке и паросодержание барботажного слоя
Высоту светлого слоя жидкости hо для ситчатых тарелок находим по урав-нению
где удельный расход жидкости на 1м ширины сливной перегородки мс;
b – ширина сливной перегородки м;
высота переливной перегородки м;
динамический коэффициент вязкости жидкости мПа с;
m – показатель степени;
поверхностное натяжение жидкости мНм;
поверхностное натяжение воды мНм.
Для смеси нормальных жидкостей в верхней и нижней частях колонны значение вязкости см может быть вычислена по формулам:
где динамические коэффициенты вязкости ЛЛК и ТЛК вверху и внизу колонны при и значения которых приведены в таблице 9 учебника [3].
Поверхностное натяжение ацетона и воды при и взяты из таблицы 24 учебника [2] и равны
Высота светлого слоя:
а) для верхней части колонны:
б) для нижней части колонны:
Паросодержание барботажного слоя находим по формуле
где Fr – критерий Фруда.
где g – ускорение свободного падения мс.
Для верхней части колонны:
Для нижней части колонны:
5 Гидравлический расчет тарелок
Рассчитаем гидравлическое сопротивление тарелки в верхней и нижней частях колонны по уравнению
а) Верхняя часть колонны:
Гидравлическое сопротивление сухой тарелки
где - коэффициент сопротивления неорошаемых ситчатых тарелок со свободным сечением 188%.
Сопротивление обусловленное силами поверхностного натяжения
где 383310-3 Нм – поверхностное натяжение жидкости при средней темпе-ратуре в верхней части колонны 680С;
d0 – диаметр отверстий тарелки.
Сопротивление парожидкостного слоя на тарелке:
Общее гидравлическое сопротивление тарелки в верхней части колонны
б) Нижняя часть колонны.
Общее гидравлическое сопротивление тарелки в нижней части колонны:
Проверим соблюдается ли при расстоянии между тарелками h=0.4 м необхо-димое для нормальной работы тарелок условие
Для тарелок нижней части колонны у которых гидравлическое сопротивление Dр больше чем у тарелок верхней части
Следовательно вышеуказанное условие соблюдается.
6 Определение числа тарелок и высоты колонны
Теоретическое число тарелок 8: в верхней части колонны n=6 в нижней части n=2.
Число действительных тарелок рассчитываем по уравнению
Для определения среднего к.п.д. тарелок h нам надо знать динамический коэффициент вязкости для смеси нормальных жидкостей в верхней и нижней частях колонны. Значение вязкости и при tср.в=680°Сtср.н=895°С были вычислены в подразделе 4.4 по формулам (4.35)(4.36):
Также надо знать относительную летучесть которая рассчитывается по формуле
где давление насыщенного пара НКК и ВКК при таблицы 3243 учебника [ ] кПа.
В учебнике [1] по рисунку 7.4 находим к.п.д. тарелок для верхней и нижней частях колонны . Длина пути жидкостью на тарелке:
где 23Пb – приближенное значение площади сегмента П – периметр сливной перегородки и находим b и П из системы уравнений:
Решая систему уравнений получим b=0123 м и П=0908 м.
В учебнике по рисунку 7.5 находим поправки на длину пути D=0165. Средний к.п.д. тарелок для верхней и нижней частей колонны:
в верхней части колонны ;
в нижней части колонны
Общее число тарелок n=17 с запасом n=19 из них в верхней части колонны 13 и в нижней части 6 тарелок.
Высота тарельчатой части колонны:
Общее гидравлическое сопротивление тарелок:
1 GJZCY обоснование тех схема рис.docx
Рисунок 1.1 Схема непрерывно действующей ректификационной установки
Исходная смесь с расходом и составом насосом 2 (или 12 в случае неисправности 2) из емкости 1 подается в подогреватель 3 где нагревается от начальной температуры до температуры кипения. Затем поступает в ректификационную колонну 4 на питающую тарелку где смешивается с флегмой стекающей с верхней (укрепляющей) части колонны. Жидкая смесь стекает в нижнюю исчерпывающую часть колонны взаимодействуя при этом на тарелках с поднимающимся из кипятильника 11 паром. При этом на тарелках происходит частичное испарение жидкости и в паровую фазу переходит преимущественно низкокипящий компонент а при частичной конденсации пара в жидкую фазу переходит преимущественно высококипящий компонент. В результате в самый низ колонны стекает кубовый остаток состоящий преимущественно из высококипящего компонента воды. Паровая фаза поднимаясь от тарелки к тарелки обогащается низкокипящим компонентом и через штуцер вверху колонны в количестве поступает и конденсируется в дефлегматоре 5 который охлаждается оборотной водой.
РЕФЕРАТ.doc
РЕКТИФИКАЦИЯ КОЛОННА ПИТАНИЕ ДИСТИЛЛЯТ КУБОВЫЙ ОСТАТОК ТЕПЛООБМЕННИК НАСОС ДЕФЛЕГМАТОР
Целью выполнения курсового проекта является расчёт и проектирование ректификационной установки непрерывного действия для разделения бинарной смеси ацетон – вода.
Произведен расчет ректификационной колонны. Осуществлён подбор и расчёт вспомогательного оборудования: теплообменника-подогревателя для подогрева питания холодильника для кубовой жидкости и дистиллята кубового испарителя насоса для подачи исходной смеси.
В результате спроектирована ректификационная установка непрерывного действия для разделения бинарной смеси ацетон – вода.
Графическая часть включает:
- чертёж общего вида колонны – 1 лист А1;
- чертёж технологической схемы установки – 1 лист А1.
5 расчет вспомогательного оборудования.doc
1 Подробный расчет холодильника кубовой жидкости
Проведем подробный расчет холодильника кубового остатка. Для горячего теплоносителя (кубовый остаток) принимаем индекс “1” для холодного (оборотная вода) – “2”. Кубовый остаток охлаждается от t1н= 97°С до t1к=35°С при помощи охлаждающего агента. В качестве охлаждающего агента оборотная вода с t2н=28°С и t2к=44°С (принимаем).
Тепловая нагрузка со стороны кубового остатка определяется следующим образом
где – массовый расход кубового остатка кгс;
– удельная теплоёмкость кубового остатка при =97°С Дж(кгК);
– температура кубового остатка определенна по диаграмме t–xy °С.
где – удельная теплоёмкость ЛЛК и ТЛК при температуре кубового остат-ка; значения которых приведены в таблице 16 учебника [3].
Расход охлаждающей воды при нагревании на 16ºС
где – удельная теплоёмкость воды Дж(кгК).
Определим среднюю разность температур. Средняя разность температур tср зависит от схемы движения теплоносителей. Так как в холодильнике не происходит изменение агрегатного состояния теплоносителей и температура их изменяется то целесообразно выбрать противоток так как при противотоке достигается большая величина средней движущей силы теплопередачи tср.
Представим температурный режим теплообменника в виде схемы:
tк2 ← tн244°С ← 28°С
tб = 97 – 44 = 53°С; tм = 35 – 28 = 7°С так как tб tм > 2 то tср – определяется как средне логарифмическая между tб и tм [ ].
Средняя разность температур теплоносителей равна:
В соответствии с таблицей 2.1 [1] принимаем Вт(м2 К). Направим кубовый остаток в межтрубное пространство а в трубное – оборотную воду (хладагент) т.к. больший расход охлаждающей воды (=35 кгс =1355 кгс). Ориентировочные значение поверхности теплообмена найдём по уравнению:
Задаваясь числом Reo=20000 что соответствует развитому турбулентному режиму течения в трубах определим соотношение nz для трубы d=25×2 мм по уравнению:
где n – общее число труб шт.;
внутренний диаметр трубы мм;
динамический коэффициент вязкости воды при средней температуре воды tср2 определен из таблицы 9 учебника [2] Пас;
– наружный диаметр трубы мм.
Соотношение числа труб на число ходов nz определяем по уравнению:
Предварительно выбираем кожухотрубчатый холодильник для охлаждения кубового остатка оборотной водой по ГОСТ 15118 – 79 в таблице 2.3 учебника [1] параметры которого представлены в таблице 4.1.
Таблица 5.1 – Параметры кожухотрубчатого теплообменника
Параметры теплообменника
Поверхность теплообмена F м2
Площадь сечения одного хода по трубам Sтр м2
Площадь сечения потока между перегородками Fмтр м2
Уточним температуру холодного теплоносителя (воды):
Зададимся температурой стенки и вычислим среднюю разность температур:
При t2=5871°С найдем значения вязкости коэффициента теплопроводности и удельную теплоемкость холодного теплоносителя в таблицах 92016 учебника [3]:
Действительное число Reд находим по уравнению:
Рассчитаем критерий Pr:
Так как температура стенки мало отличается от температуры холодного теплоносителя то примем Prст2=Pr2.
Рассчитаем критерий Nu:
Коэффициент теплоотдачи определим по уравнению[2]:
Рассчитаем тепловой поток:
Тепловая проводимость загрязнений стенок со стороны холодного теплоносителя (вода среднего качества) и кубового остатка равны 1r1=1r2=2320 Вт(м2К) значения из таблицы 2.2 учебника [1]. Теплопроводность нержавеющей стали примем равной из таблицы 28 учебника [2]. Сумма термический сопротивлений стенки и загрязнений равна
где – толщина стенки м.
Коэффициент теплопередачи равен:
Температура стенки со стороны горячего теплоносителя вычисляется по формуле:
С учетом того что количество ацетона в кубовом остатке мало = 0035 кг ацетонакг смеси 005 будем применять при расчетах что кубовый остаток состоит только из ТЛК (воды). Определим среднюю температуру второго теплоносителя (кубового остатка):
tср1 = (97 + 35) 2 = 66°С.
При tср1 найдем значения вязкости коэффициента теплопроводности и удель-ную теплоемкость кубового остатка в таблицах 92016 учебника [3]:
Определим критерий Прандтля при средней температуре второго теплоносителя (кубового остатка) по формуле:
Определим критерий Прандтля со стороны кубового остатка при tст1=6227°С.
При tст1 найдем значения вязкости коэффициента теплопроводности и удельную теплоемкость кубового остатка в таблицах 92016 учебника:
Определим критерий Рейнольдса:
где Sм.тр=0045 м2 – по ГОСТ 15118-79 (таблица 5.1);
Определим критерий Нуссельта:
Удельная тепловая нагрузка со стороны второго теплоносителя (кубового остатка):
Зададимся другой температурой стенки и вычислим среднюю разность температур:
Рассчитаем тепловой поток по формуле (5.14)
Температура стенки со стороны второго теплоносителя вычисляется по формуле (5.17)
Рассчитаем тепловой поток по формуле (5.22)
Проведём аналогичные расчёты при . Вычислим среднюю разность температур по формуле (5.8)
Рассчитаем тепловой поток
Температура стенки со стороны второго теплоносителя
На рисунке 5.1 изобразим зависимость q1 и q2 от tст2 по которой найдём искомую tст2 для расчёта q1 и q2.
Рисунок 5.1 – Зависимость тепловых потоков от температуры стенки со стороны холодного теплоносителя
Из диаграммы tст2=5532. Найдём q1 и q2.
Проверим равенство тепловых потоков:
Отклонение соответствует допустимому – вычислим средний тепловой поток:
Вычислим коэффициент теплопередачи:
Требуемая поверхность теплопередачи:
Запас теплообменной поверхности:
Скорость исходной смеси в трубах определяется по формуле
где плотность воды при tcр2=36°С значение взято из таблицы 5 учебника [3].
Скорость в межтрубном пространстве
где плотность кубового остатка (воды) в межтрубном пространстве при tср1=66°С значение взято из таблицы 5 учебника [3]..
Скорость в штуцерах для кубового остатка
Диаметр штуцера выбираем по таблице 2.6 [1] м.
Скорость в штуцерах для охлаждаемой воды
Диаметр штуцера выбираем по таблице 2.6 [ ] м.
Коэффициент трения при Re≥2300 находим по формуле:
Гидравлическое сопротивление кожухотрубчатого теплообменника в трубном пространстве рассчитывается по формуле:
Гидравлическое сопротивление кожухотрубчатого теплообменника в межтрубном пространстве рассчитывается по формуле
где x – число сегментных перегородок значения из таблицы 2.2 учебника [ ]
m – число рядов труб преодолеваемых потоком теплоносителя в межтрубном пространстве.
2 Расчет холодильника дистиллята
Рассчитать и подобрать нормализованный кожухотрубчатый теплообменник для охлаждения дистиллята. Горячий раствор в количестве кгс охлаждается от °С до °С (примем). Начальная температура охлаждающей воды равна =28°С. Зададимся температурой воды после прохода через теплообменник °C.
Выбираем движение теплоносителей противотоком так как при противотоке достигается большая величина средней движущей силы теплопередачи tср.
tб = 56 – 44 = 12°С; tм = 34 – 28 =6°С так как tб tм ≥ 2 то tср – определяется как средне логарифмическая между tб и tм по уравнению (5.4)
Определяем среднюю температуру воды
Средняя интегральная температура дистиллята
Расход теплоты отдаваемой охлаждающей воде в водяном холодильнике дистиллята определяется по уравнению
где удельная теплоёмкость дистиллята при tнD = 56°C.
где – удельная теплоёмкость ЛЛК и ТЛК при средней температуре дис-тиллята t1 = 447°C значения которых приведены в таблице 16 учебника [3].
Определим расход охлаждающей воды
По таблице 2.1 [1] принимаем Кор=450 Вт(мК).
Ориентировочная площадь теплообменника по уравнению (5.5)
В соответствии с таблицей 2.3 [1] принимаем ГОСТ 15118-79 двухходовой кожухотрубчатый теплообменник со следующими характеристиками Dкож=600 мм F=38 м d=25×2мм L=2м N=240z=2.
Запас площади по уравнению (5.26):
Так как выбранный теплообменник имеет запас площади 2612 % что меньше 40% но больше 10% то он выбран верно.
3 Расчет кожухотрубчатого теплообменника-испарителя
Рассчитать и подобрать нормализованный вид конструкции кожухотрубчатого испарителя ректификационной колонны с GW=352 кгс паров раствора органической жидкости при температуре кипения tW=t1н=t1к=97° С.
В качестве теплоносителя используем насыщенный водяной пар давлением р=2атм =1967 кПа температурой конденсации t2к=t2н=1196°С.
Расход теплоты получаемой в кубе-испарителе от греющего пара по уравнению
где QД расход теплоты отдаваемой охлаждающей воде в дефлегматоре-конденсаторе Дж;
удельная теплоемкость питания Дж(кгК);
температура питания определяется по диаграмме t
тепловые потери (3% от полезно затрачиваемой теплоты) Вт.
где средняя удельная теплота конденсации Джкг.
где удельная теплота конденсации ацетона (ЛЛК) при tD=56 ºС значение взято из таблицы 29 учебника[ ]; ;
удельная теплота конденсации воды(ТЛК) при tD=56ºС значение взято из таблицы 29 учебника[ ]; .
Рассчитаем удельную теплоёмкость исходной смеси
где массовая доля ЛЛК в исходной смеси кг ЛЛКкг смеси;
удельная теплоёмкость ацетона при значение которой приведено в таблице 16 учебника [3];
удельная теплоёмкость воды при значение которой приведено в таблице 16 учебника [3].
Тепловая нагрузка аппарата QК=3942кВт.
t1н t1к1196°С 1196°С
t2к ← t2н 97°С ← 97°С
Средняя движущая сила
В соответствии с таблицей 2.1 [1] принимаем ориентировочное значение коэффициента теплопередачи Кор=1800 Вт(мК). Тогда ориентировочные значения площади теплообменника по уравнению (5.5)
В соответствии с ГОСТ 15118-79 по таблице 2.9 [1] близкую к ориентиро-вочной площади имеет кожухотрубчатый теплообменник с Dкож=600 мм d=25×2 мм S=121 м N=257z=1 L= 6 м.
Запас площади по уравнению (5.26)
Так как выбранный теплообменник имеет запас площади 249 % что меньше 40% но больше 10% то он выбран верно.
4 Расчет кожухотрубчатого конденсатора (дефлегматора)
Рассчитать и подобрать нормализованный вариант конструкции кожухотрубчатого конденсатора смеси паров органической жидкости (дефлегматора) для конденсации кгс паров. Удельная теплота конденсации смеси кДжкг температура конденсации tD =56°С. Тепло конденсации отводится водой с начальной температурой .
Принимаем температуру воды на выходе из конденсатора . Средняя температура воды
Тепловая нагрузка аппарата (см. в подразделе 5.3).
Средняя разность температур:
tб = 28°С; tм = 12°С так как tб tм ≥ 2 то tср – определяется как средне логарифмическая между tб и tм по уравнению (5.4)
В соответствии с таблицей 2.1 [1] принимаем . Ориенти-ровочные значение поверхности по уравнению (5.5)
В соответствии с ГОСТ 15119-79 по таблице 2.9 [2] принимаем теплообменник со следующими характеристиками: Dкож=1000 мм d=25×2 мм z=2 L=6 м S=338 м2 n=718.
Так как выбранный теплообменник имеет запас площади 154% что меньше 40% но больше 10% то он выбран верно.
5 Расчет подогревателя исходной смеси
Исходную смесь необходимо подогреть от t1н = 33 °C до t1к = 64 °C. Темпера-туру греющего водяного насыщенного пара выберем t2н=t2к=1196 °C (давление 1967 кПа).
tб = 866°С; tм = 556°С так как tб tм 2 то tср – определяется как среднеарифметическая между tб и tм по уравнению:
Удельная теплоёмкость исходной смеси была найдена ранее в подразделе 5.3; сF =33665 Дж(кгс). Расход теплоты требуемой для подогрева исходной смеси до температуры кипения (64 ºС) находим по уравнению:
Расход греющего пара в подогреватели исходной смеси рассчитаем по формуле
где rгр.п. удельная теплота конденсации греющего пара при t = 1196 °C;значение которой приведено в таблице 29 учебника [3].
В соответствии с таблицей 2.1 [1] принимаем . Ориентировочные значение поверхности по уравнению (5.5)
В соответствии с ГОСТ 15119-79 по таблице 2.9 [1] принимаем теплообменник со следующими характеристиками: Dкож=600 мм d=25×2 мм z=2 L=3 м S=57 м2 n=240.
Так как выбранный теплообменник имеет запас площади 271% что меньше 40% но больше 10% то он выбран верно.
6 Расчет центробежного насоса
Подобрать центробежный насос для подачи исходной смеси в ректификационную колонну. По ходу движения исходной смеси стоит теплообменник в котором она нагревается от 33 С до температуры кипения. Расход исходной смеси 6111 кгс. Длина трубопровода на линии всасывания 10 м на линии нагнетания 15 м. Монтажная схема насоса приведена на рисунке 5.2.
Выбор трубопровода. Для всасывающего и нагнетательного трубопровода примем одинаковую скорость течения исходной смеси равную 2 мс; страница 16 учебника [1]. Тогда диаметр по уравнению
где плотность исходной смеси при tн = 33°С кгм3.
где плотности ЛЛК и ТЛК при tн = 33°С; значения которых приведе-ны в таблице 5 учебника [3].
Плотность исходной смеси рассчитаем по формуле (5.46)
По таблице на странице 16 учебника [1] выбираем стальную трубу наружным диаметром 76 мм толщиной стенок 4 мм. Внутренний диаметр трубы d=68 мм. Фактическую скорость в трубе находим по уравнению:
Примем что коррозия трубопровода незначительна.
Определим потери на трение и местные сопротивления. Определим число Рейнольдса по уравнению:
где вязкость исходной смеси при tн = 33°С .
где вязкости ЛЛК и ТЛК при tн = 33°С ; значения которых приведены в таблице 9 учебника [3].
т.е. режим турбулентный. Примем абсолютную шероховатость равной м. Тогда относительная шероховатость по уравнению:
Так как Re>560 то коэффициент трения рассчитывается по уравнению:
Определим сумму коэффициентов местных сопротивлений.
Для всасывающей линии:
)вход в трубу (принимаем с острыми краями): ;
)два прямоточных вентиля: для d=68 мм ;
)один поворот на 90о .
Сумма коэффициентов местных сопротивлений во всасывающей линии:
Потерянный напор во всасывающей линии находим по формуле
где l длина трубопровода на линии всасывания м.
Для нагнетательной линии:
) три поворота на 90 о: ;
) два выхода из трубы: .
Сумма коэффициентов местных сопротивлений в нагнетательной линии
Потерянный напор в нагнетательной линии по уравнению (5.52)
Общие потери напора:
Выбираем насос. Находим потребный напор насоса по уравнению
где – геометрическая высота подъёма жидкости (принимаем 10 м).
Такой напор при заданной производительности обеспечивается одноступенчатыми центробежными насосами.
Полезную мощность насоса определим по формуле(5.11)
Принимаем [4] найдем мощность на валу двигателя по уравнению(5.56):
где коэффициент полезного действия насоса
коэффициент полезного действия передачи от электродвигателя к насосу.
Заданным подаче и напору более всего соответствует центробежный насос марки Х2031 для которого при оптимальных условиях работы Q=55×10-3 м3с Н=18м . Насос обеспечен электродвигателем АО2-41-2 номинальной мощностью 10 кВт . Частота вращения вала (данные из приложение 1.1 [1]).
Запас напора на кавитацию находим по уравнению(5.57):
Рисунок 5.2 Монтажная схема насоса
чертеж колонны.cdw

выполнятся требования:
а) ГОСТ 12.2.003-74 "Оборудование производственное.
Общие требования безопасности".
б) ОСТ 26-291-79 "Сосуды и аппараты стальные сварные.
Технические требования".
Материал деталей колнны
соприкосающихся с обрабатываемыми
-сталь Х18Н10Т ГОСТ 5 632 -72
деталей -сталь Ст3 ГОСТ 380-71.
Материал прокладок -паронит ПОН-1 ГОСТ 481-80.
Аппарат испытать на прочность и плотность гидравлически
в горизонтальном положении под давлением 0
вертикальном положении-наливом.
Сварные соединения должны соответствовать требованиям
ОСТ 26-01-82-77 "Сварка в химическом машиностроении.
Сварные швы в обьеме 100% контромировать рентгено-
Действительное расположение штуцеров
Не указанный вылет штуцеров -120 мм.
Аппарат предназначен для разделения смеси ацетон-вода
концентрацией 44%(масс.)
Производительность 6.111 кгс.
Рабочее давление 0.1 МПа.
Температура среды в кубе 89.5 С.
Среда в аппарате - не токсичная
Тип тарелок - ситчатые типа ТС-Р.
Количество тарелок - 18
Колонна ректификационная
Приспособление для выверки
Опора цилиндрическая
Выход кубового остатка
Выход жидкости на циркуляцию
Для регулятора уровня
Для камеры уровнемера
Для замера температуры
Технические требования
Техническая характеристика
Устройство поворотное
ВВЕДЕНИЕ.doc
В химической промышленности особое место занимают массообменные процессы которые характеризуются переходом одного или нескольких веществ из одной фазы в другую. Используя эту возможность перехода вещества из одной фазы в другую осуществляют разделение гетерогенных и гомогенных систем. В зависимости от того из какой фазы в какую переходит вещество различают следующие процессы: абсорбция ректификация экстракция кристаллизация сушка. Продукты химической и нефтехимической промышленности используются практически во всех отраслях народного хозяйства: в машиностроении строительстве сельском хозяйстве – и в быту. Ускорение развития химической промышленности в нашей стране требует научного решения многочисленных и разнообразных проблем связанных с проектированием строительством и эксплуатацией химических заводов. Особое внимание должно быть уделено разработке новых высокоинтенсивных автоматизированных химических аппаратов и машин.
Ректификация – это процесс разделения жидких однофазных систем состоящих из двух или более компонентов основанный на разности их температур кипения и осуществляемый при многократном контакте пара и жидкости образующихся в процессе. В ректификации компонент который имеет более низкую температуру кипения называется низкокипящим он переходит в пар а также удаляется из жидкости в первую очередь. Компонент имеющий более высокую температуру кипения называется высококипящим и он остается в жидкости. Процесс широко применяется на многих заводах химической промышленности: «Гродно Азот» Мозырский НПЗ Новополоцкий НПЗ Речицкий газоперерабатывающий завод и т.д.
В курсовом проекте будет произведен расчет и подобрано типовое оборудование для проведения процесса ректификации бинарной ацетон – вода.
монтажная схема.docx
Рисунок 5.2 Монтажная схема насоса
техн. схему в пояснительную записку.cdw

четеж технолог. схемы.cdw

Колонна ректификационная
Аппарат теплообменный (дефлегматор)
Аппарат теплообменный (кипятильник)
Аппарат теплообменный (подогреватель)
Аппарат теплообменный (холодильник)
Вентиль регулирующий
Технологическая схема
Условное обозначение
Вода оборотная(подача)
Паро-жидкостная смесь
Вода оборотная(отвод)
Заключение.docx
Для подогрева питания используется двухходовой кожухотрубчатый теплообменник с поверхностью теплопередачи 57 м2 диаметром кожуха D=600 мм с 240 трубами размером 25х2 и длиной L=3 м.
В качестве кубового испарителя выбрал одноходовой теплообменник со следующими характеристиками: D=600 мм n=257 размер труб 25х2 и поверхностью теплопередачи 121 м2.
В связи с необходимостью охлаждать дистиллят используют холодильник (двухходовой кожухотрубчатый теплообменник ) с поверхностью теплопередачи 38 м2 диаметром кожуха D=600 мм с 240 трубами размером 25х2 и длиной L=2 м.
Для охлаждения кубовой жидкости используется двухходовой кожухотрубчатый теплообменник с поверхностью теплопередачи 50 м2 диаметром кожуха D=600 мм с 240 трубами размером 25х2 и длиной L=3 м.
Для подачи смеси из закрытой емкости в теплообменник-подогреватель используем центробежный насос марки Х2031 мощностью N=10 кВт обеспечивающий напор Н =18 м.
3 описание вспомогательного оборуд..docx
В ходе данного процесса необходимо подогревать и охлаждать жидкости до определенных температур. Для этого необходимо использовать теплообменную аппаратуру.
Так как наибольшее распространение получили поверхностные теплообмен-ники в которых тепло передается через разделяющую теплоносители стенку то целесообразно выбрать именно этот тип теплообменных аппаратов. В частности широко используются кожухотрубчатые теплообменники. Они довольно просты в изготовлении позволяют достигать высоких скоростей теплоносителя в трубах относительно хорошо доступны для очистки и ремонта в особенности для очистки труб. В многоходовых теплообменниках этого типа достаточно высокая интенсивность теплообмена.
В качестве подогревателя исходной смеси используем кожухотрубчатый двухходовой вертикальный теплообменник с неподвижными трубными решетками. Кожухотрубчатый двухходовой теплообменник изображен на рисунке 3.1.
– корпус; 2 – трубные решетки; 3478 – штуцера; 5 – трубы; 6 – крышки; 9 – перегородка в крышке; 10 – перегородки в межтрубном пространстве
Рисунок 3.1 – Кожухотрубчатый двухходовой теплообменник
Теплообменник состоит из цилиндрического корпуса (кожуха) 1 с установленными на торцах его трубными решётками 2 и штуцерами 34. В отверстиях трубных решёток своими концами закреплены трубы 5 . Совокупность этих труб называется трубным пучком. Трубчатка сверху и снизу закрыты крышками 6 со штуцерами 7 и 8. Один теплоноситель (ацетон) подают в трубное пространство другой (воду) в межтрубное. Горячий теплоноситель отдает холодному через стенки труб тепло. С помощью поперечной перегородки 9 установленной в крышке
теплообменника трубы разделены на ходы по которым последовательно движется жидкость протекающая в трубном пространстве теплообменника. Для увеличения скорости и удлинения пути движения среды в межтрубном пространстве служат сегментные перегородки 10.
В подогревателе исходной смеси в качестве греющего теплоносителя используем насыщенный водяной пар. Этот теплоноситель обладает существенными достоинствами. В результате конденсации пара получаем большое количества тепла при относительно небольшом расходе пара так как теплота конденсации его составляет приблизительно 226 106 Джкг при давлении 1 ат. Вследствие высоких коэфициентов теплоотдачи от конденсирующегося пара сопротивление переносу тепла со стороны пара мало. Это позволяет проводить процесс нагревания при малой поверхности теплообмена. Важным достоинством насыщенного пара является постоянство температуры его конденсации что дает возможность точно поддерживать температуру нагрева а также в случае необходимости регулировать ее изменяя давление греющего пара. Теплообменник выбранный согласно ГОСТ 15119-79: поверхностью теплообмена F= 57 м2 числом ходов-2 числом труб n=240длиной труб l=3 м с диаметром кожуха – 600 мм с числом сегментных перегородок – 8. Исходная смесь где подогревается от температуры начальной – 33°C до температуры кипения – 64°C. Давление насыщенного водяного пара принимаем 1967 кПа так как при больших давлениях требуется слишком толстостенная и дорогостоящая теплообменная аппаратура а также велики расходы на коммуникации и арматуру. Исходную смесь направляем снизу вверх а греющий пар в противоположном направлении. Такое направление движения каждой среды совпадает с направлением в котором стремится двигаться данная среда под влиянием изменения ее плотности при нагревании или охлаждении. Также наблюдается при таком направление сред равномерное распределение скоростей.
В качестве дефлегматора используем кожухотрубчатый двухходовой горизонтальный теплообменник с неподвижными трубными решетками. Кожухотрубчатый горизонтальный двухходовой теплообменник изображен на рисунке 3.2.
Рисунок 3.2 –Кожухотрубчатый двухходовой горизонтальный теплообменник
– корпус; 2 – трубные решетки; 3478 – штуцера; 5 – трубы; 6 – крышки; 9 – перегородки в крышках; 10 – перегородки в межтрубном пространстве
Теплообменник состоит из цилиндрического корпуса (кожуха) 1 с установленными на торцах его трубными решётками 2 и штуцерами 34. В отверстиях трубных решёток своими концами закреплены трубы 5 . Совокупность этих труб называется трубным пучком. Трубчатка сверху и снизу закрыты крышками 6 со штуцерами 7 и 8. Один теплоноситель (охлаждающую воду) подают в трубное пространство другой (пары ацетона) в межтрубное. С помощью поперечных перегородок 9 установленных в крышках теплообменника трубы разделены на ходы по которым последовательно движется жидкость протекающая в трубном пространстве теплообменника. Для увеличения скорости и удлинения пути движения среды в межтрубном пространстве служат сегментные перегородки 10.
Дистиллят конденсируется в горизонтальном кожухотрубчатом двухходовом теплообменнике выбранном согласно ГОСТ 15119-79: поверхность теплопередачи F=338 м2 диаметр кожуха – 1000 мм число ходов-2 трубы d=25x2 мм число труб 718 длинна труб l=6 м число сегментных перегородок – 10. В качестве охлаждающего агента используем оборотную воду. Конечную температуру воды принимаем 44°C чтобы свести к минимуму выделение растворенных в воде солей загрязняющих теплообменные поверхности и снижающих эффективность теплообмена. Направляем теплоносители противотоком для достижения большей величины средней движущей силы.
В качестве холодильника-дистиллятора используем кожухотрубчатый двухходовой горизонтальный теплообменник с неподвижными трубными решетками. Его конструкция аналогична кожухотрубчатому горизонтальному двухходовому теплообменнику изображенному на рисунке 3.3. Дистиллят охлаждается в холодильнике от 56°С до 34°С. Холодильник представляет собой кожухотрубчатый горизонтальный теплообменник с поверхностью теплообмена равной 38 м2 с диаметром кожуха – 600 мм с диаметром труб – 25х2 мм с длинной труб – 2 м с числом ходов и труб соответственно 2 и 240 число сегментных перегородок – 4. В холодильнике дистиллят охлаждается оборотной водой взятой при температуре 28°С. Конечную температуру воды принимаем 44°C чтобы свести к минимуму выделение растворенных в воде солей загрязняющих теплообменные поверхности и снижающих эффективность теплообмена. Направляем теплоносители противотоком для достижения большей величины средней движущей силы. В трубное пространство направляем оборотную воду а в межтрубное дистиллят. Дистиллят (горячий теплоноситель) охлаждается отдавая через стенки труб тепло оборотной воде (холодному теплоносителю).
Кипятильник представляет собой кожухотрубчатый вертикальный одноходовой теплообменник с поверхностью теплообмена равной 121 м2 с диаметром кожуха – 600 мм с диаметром труб – 25х2 мм с длинной труб – 6 м с числом ходов и труб соответственно 1 и 257. В кипятильнике часть кубового остатка подогревается греющим паром при давлении 01967 МПа. Выбираем такое давление так как при больших давлениях требуется слишком толстостенная и дорогостоящая теплообменная аппаратура а также велики расходы на коммуникации и арматуру. Направляем теплоносители противотоком для достижения большей величины средней движущей силы. Кипятильник изображен на рисунке 3.3.
– корпус; 2 – трубные решетки; 3478 – штуцера; 5 – трубы; 6 – крышки
Рисунок 3.3 – Кожухотрубчатый одноходовой теплообменник
Теплообменник состоит из цилиндрического корпуса (кожуха) 1 с установленными на торцах его трубными решётками 2 и штуцерами 34. В отверстиях трубных решёток своими концами закреплены трубы 5 . Совокупность этих труб называется трубным пучком. Трубчатка сверху и снизу закрыты крышками 6 со штуцерами 7 и 8. Один теплоноситель (кубовый остаток) подают в трубное пространство другой (греющий пар) в межтрубное. Кубовый остаток в трубном пространстве кипит под действием тепла передаваемого через стенки труб от греющего пара.
В качестве холодильника кубового остатка используем кожухотрубчатый двухходовой вертикальный теплообменник с неподвижными трубными решетками. Кожухотрубчатый двухходовой теплообменник изображен на рисунке 3.4.
Рисунок 3.4 – Кожухотрубчатый двухходовой теплообменник
Теплообменник состоит из цилиндрического корпуса (кожуха) 1 с установленными на торцах его трубными решётками 2 и штуцерами 34. В отверстиях трубных решёток своими концами закреплены трубы 5 . Совокупность этих труб называется трубным пучком. Трубчатка сверху и снизу закрыты крышками 6 со штуцерами 7 и 8. Один теплоноситель (оборотную воду) подают в трубное пространство другой (кубовый остаток) в межтрубное. Горячий теплоноситель отдает холодному через стенки труб тепло. С помощью поперечной перегородки 9 установленной в крышке теплообменника трубы разделены на ходы по которым последовательно движется жидкость протекающая в трубном пространстве теплообменника. Для увеличения скорости и удлинения пути движения среды в межтрубном пространстве служат сегментные перегородки 10.
Холодильник кубового остатка представляет собой кожухотрубчатый верти-кальный двухходовой теплообменник с поверхность теплообмена равной 50 м2 с диаметром кожуха – 600 мм с диаметром труб – 25х2 мм с длинной труб – 3 м с числом ходов и труб соответственно 2 и 240 число сегментных перегородок – 8. В холодильнике кубового остатка охлаждение ведется оборотной водой взятой при температуре 28 °С. Кубовый (горячий) остаток направляем сверху вниз а охлаждающую воду в противоположном направлении. Такое направление движения каждой среды совпадает с направлением в котором стремится двигаться данная среда под влиянием изменения ее плотности при нагревании или охлаждении. Также наблюдается при таком направление сред равномерное распределение скоростей.
Для подачи исходного раствора используем одноступенчатый центробежный насос. Центробежный насос изображен на рисунке 3.5.
– всасывающий трубопровод; 2 –рабочее колесо; 3 –корпус; 4 – лопатки; 5 – нагнетательный трубопровод
Рисунок 3.5 – Центробежный насос
В одноступенчатом центробежном насосе жидкость из всасывающего трубопровода 1 поступает вдоль оси рабочего колеса 2 в корпус 3 насоса и попадая на лопатки 4 приобретает вращательное движение. Центробежная сила отбрасывает жидкость в канал переменного сечения между корпус и рабочим колесом в котором скорость жидкости уменьшается до значения равного скорости в нагнетательном трубопроводе 5. При этом как следует из уравнения Бернулли происходит преобразование кинетической энергии потока жидкости в статический напор что обеспечивает повышение давления жидкости. На входе в колесо создается пониженное давление и жидкость из приемной емкости непрерывно поступает в насос.
Центробежными насосы марки Х2031: Q=5510-3 м3с H=18 м Насос обеспечен электродвигателем АО2-41-2 номинальной мощностью 10 кВт частота вращения вала .
Центробежные насосы являются одним из основных типов насосов применяемых в химической технологии. Они предназначены для перекачивания химически активных и нейтральных жидкостей не имеющих включений или же с твердыми включениями составляющими до 02% при размере частиц до 02 мм.
Сеть трубопроводов является источником повышенной опасности так как вследствие тяжелых эксплуатационных факторов происходит разрушение материала труб и разгерметизация фланцевых сооружений а из-за большой протяженности сети контроль за ее состоянием затруднен. Безопасность эксплуатации трубопроводов обеспечивается их правильной прокладкой качественным монтажом установкой компенсаторов.
Безопасность эксплуатации насосов обеспечивается подвижностью конструкции коррозионной стойкостью материала и герметичность уплотнения движущихся частей. При перекачивании горячих жидкостей предусматривается специальные меры защиты обслуживающего персонала от ожогов.
1 Описание и обоснование технологической схемы установки.docx
В данном курсовом проекте рассмотрена схема непрерывной ректификации. Непрерывный процесс характеризуется непрерывной подачей сырья в колонну и непрерывной выгрузкой продуктов разделения. При этом все стадии процесса (ректификация подогрев сырья дистилляция и другие) разделены в пространстве и проводятся одновременно в разных аппаратах. Много тоннажные производства в основном используют непрерывную ректификацию т.к. она как и все непрерывные процессы имеет ряд преимуществ перед периодической:
компактность установки;
возможность использования оборудования большой мощности;
однородность по качеству продукции;
стабильные условия работы что облегчает установление требуемого режима работы и автоматизацию процесса;
труд обслуживающего персонала легче безопаснее производительнее (т.к. отсутствуют простои оборудования между операциями);
уменьшенный расход тепла причем возможно использование тепла кубового остатка на подогрев исходной смеси в теплообменнике.
Однако наряду с существенными преимуществами непрерывная ректифика-ция имеет ряд недостатков по сравнению с периодической. Основными недостатка-ми является повышенная стоимость основных производственных фондов и необходимость использования более квалифицированных специалистов.
Таким образом в производствах крупного масштаба более целесообразно применять непрерывную ректификацию а в небольших неравномерно работающих производствах – периодическую.
При выборе схемы установки исходят прежде всего из экономической эффективности предлагаемых мероприятий. При этом так же учитываются технологические особенности того или иного производства. Таким образом все делается для того чтобы с наименьшими затратами добиться максимальной эффективности. Так при подборе оборудования главными показателями являются:
б) простота монтажа;
в) простота эксплуатации.
Описание непрерывно действующей ректификационной установки
Упрощенная схема непрерывно действующей ректификационной установки изображена на рисунке 1.1.
емкость с исходной смесью; 212 насосы; 3 – подогреватель;4 – тарельчатая колонна; 5 дефлегматор; 6 делитель; 7 –холодильник-дистиллятор; 8 – сборник дистиллята; 9 –холодильник кубового остатка; 10 сборник кубового остатка;11 – кипятильник (выносной).
Рисунок 1.1 Схема непрерывно действующей ректификационной установки
Исходная смесь с расходом и составом насосом 2(или 12 в случаи неисправности 2) из емкости 1 подается в подогреватель 3 где нагревается от начальной температуры до температуры кипения. Затем поступает в ректификационную колонну 4 на питающую тарелку где смешивается с флегмой стекающей с верхней (укрепляющей) части колонны. Жидкая смесь стекает в нижнюю исчерпывающую часть колонны взаимодействуя при этом на тарелках с поднимающимся из кипятильника 11 паром. При этом на тарелках происходит частичное испарение жидкости и в паровую фазу переходит преимущественно низкокипящий компонент а при частичной конденсации пара в жидкую фазу переходит преимущественно высококипящий компонент. В результате в самый низ колонны стекает кубовый остаток состоящий преимущественно из высококипящего компонента воды. Паровая фаза поднимаясь от тарелки к тарелки обогащается низкокипящим компонентом и через штуцер вверху колонны в количестве поступает и конденсируется в дефлегматоре 5 который охлаждается оборотной водой. Часть полученного конденсата возвращается на верхнюю тарелку в колонну в виде флегмы для орошения нижней части а другая часть с расходом отбирается в виде дистиллята который используется как готовый продукт содержащий преимущественно легколетучий компонент ацетон. Перед отводом готовых продуктов в сборники 8 и 10 они предварительно охлаждаются в холодильниках 7 и 9. В результате работы колонны их исходной смеси получают 2 готовых продукта кубовый остаток воду и дистиллят ацетон.
Сеть трубопроводов является источником повышенной опасности так как вследствие тяжелых эксплуатационных факторов происходит разрушение ма-териала труб и разгерметизация фланцевых сооружений а из-за большой протя-женности сети контроль за ее состоянием затруднен. Безопасность эксплуатации трубопроводов обеспечивается их правильной прокладкой качественным монтажом установкой компенсаторов.
Безопасность эксплуатации насосов обеспечивается подвижностью конструк-ции коррозионной стойкостью материала и герметичность уплотнения движущих-ся частей. При перекачивании горячих жидкостей предусматривается специальные меры защиты обслуживающего персонала от ожогов.
Правила устанавливают специальные требования безопасности конструкции сосудов к материалам сосудов к изготовлению монтажу и ремонту к арматуре к контрольно-измерительным приборам. Конструкции должны быть надежными обеспечивать безопасность при эксплуатации и предусматривать возможность осмотра очистки промывки продувки и ремонта сосудов.
Важнейший источник сохранения и пополнения ресурсов пресных вод – рациональное использование речных вод широкое применение промышленных вод.
2 описание колонны.docx
1 Описание конструкции ректификационной колонны
В качестве ректификационной колоны выбираем тарельчатую. Она в отличие от других колон обеспечивает равномерное распределение жидкости по сечению колонны дает возможность разделять смеси с любой степенью чистоты применяются не только для малых диаметров но и для больших. Кроме этого незначительное гидравлическое сопротивление не требует большого увеличения давления а значит и температура кипения в нижней части колонны не связана с дополнительным расходом энергии.
Аппарат представляет собой вертикальный цилиндр состоящий из куба крышки тарельчатой части. В кубе имеются штуцера для отвода пробы термометр показатели уровня манометр. В крышке имеется штуцер для отвода паров дистиллята. В тарельчатой части имеются штуцера для подвода исходной смеси флегмы. Также имеются манометр и термометр.
Для обеспечения образования восходящего по колонне потока пара используем выносной кипятильник изображенный на рисунке 1.1 под номером 11. При его применении облегчается ремонт и замена кипятильника. Также кипятильники устанавливают ниже колонны для улучшения естественной циркуляции кубовой жидкости.
В данной работе выбраны ситчатые тарелки. Эти тарелки имеют большое число отверстий диаметром 8 мм через которые проходит газ в слой жидкости на тарелке. Уровень жидкости поддерживается переливным устройством. При слишком малой скорости газа его давление не может удержать слой жидкости соответствующий высоте перелива и жидкость может просачиваться через отверстия тарелки на нижерасположенную тарелку что приводит к значительному снижению движущей силы процесса. Поэтому газ должен двигаться с определенной скоростью и иметь давление достаточное для того чтобы преодолеть давление слоя жидкости на тарелке и предотвратить стекание жидкости через отверстия тарелки. Таким образом. ситчатые тарелки обладают более узким диапазоном работы. Вместе с тем ситчатые тарелки чувствительны к загрязнениям и осадкам которые забивают отверстия тарелок.
К достоинствам ситчатых тарелок относятся простота их устройства легкость монтажа и ремонта сравнительно низкое гидравлическое сопротивление высокая эффективность также они устойчиво работают в довольно широком интервале скоростей газа. Кроме этого немаловажным преимуществом ситчатых тарелок является их малая цена по сравнению с другими видами тарелок.
2 Принцип действия ректификационной колонны
В данной ректификационной колонне происходит разделение смеси ацетон – вода. Эта смесь предварительно подогретая до температуры кипения с целью уменьшения тепловой нагрузки кипятильника К подаётся на питающую тарелку где состав жидкости примерно равен составу исходной смеси xF. В нашем случае питающей является пятая тарелка. Она делит колонну на две части имеющие различное назначение. Та часть колонны находящаяся выше питающей тарелки (от питающей до верхней тарелки) обеспечивает как можно большее укрепление паров т. е. обогащение их легколетучим компонентом (ацетоном). Эта часть колонны называется укрепляющей. Та часть колонны расположенная ниже питающей тарелки (от питающей до нижней тарелки) обеспечивает удаление из жидкости легколетучего компонента т. е. исчерпывает жидкость для того чтобы в кипятильник стекала жидкость близкая по составу к чистому низкокипящему компоненту (воду).
Снизу вверх по колонне движутся пары поступающие в нижнюю её часть из кипятильника К который находится вне колонны т.е. является выносным. Стекая вниз по колонне жидкость взаимодействует с поднимающимся вверх паром. Начальный состав пара примерно равен составу кубового остатка xW т.е. обеднен легколетучим компонентом. В результате массообмена с жидкостью пар обогащается легколетучим компонентом. Для более полного обогащения верхнюю часть колонны орошают в соответствии с заданным флегмовым числом жидкостью (флегмой) состава xD.
Ректификационная колонна имеет 18 ситчатых тарелок. Также в верхней части колонны установлен брызгоуловитель (на втором листе графического материала обозначен номером 6) для улавливания капель жидкости уносимых паром. Также колонна имеет штуцер для подачи исходной смеси (на втором листе графического материала обозначен буквой К) штуцер для ввода паров жидкости из кипятильника (на втором листе графического материала обозначен буквой Ж) штуцер для ввода флегмы (на втором листе графического материала обозначен буквой И) штуцер для вывода паров дистиллята (на втором листе графического материала обозначен буквой Л) штуцер для вывода кубового остатка к кипятильнику (на втором листе графического материала обозначен буквой Н) и к холодильнику (на втором листе графического материала обозначен буквой М). В колонне предусмотрены штуцера для замера температуры (на втором листе графического материала обозначены буквой У) для замера давления (на втором листе графического материала обозначены буквой Ф) и для установки регулятора уровня (на втором листе графического материала обозначены буквой С).
Установка ректификационной колонны на фундамент или на специальную несущую конструкцию осуществляется при помощи опоры (на втором листе графического материала обозначена номером 9).
В колонне также имеется 3 люка (по одному в верхней и нижней части колонны и еще 1в середине аппарата).
Принципиальная схема ректификационной колонны представлена на рисунке 2.1.
– корпус; 2 – крышка; 3 – штуцер; 4 – гильза; 5 – тарелка; 6 – штырь;
– брызгоуловитель; 8 – опора; 9 – цапфа; 10 – штуцер для подачи исходной смеси; 11 – штуцер для отвода паров флегмы и дистиллята; 12 – штуцер для отвода кубового остатка.
Рисунок 2.1 – Принципиальная схема ректификационной колонны
Ректификационная колонна представляет собой вертикальный цилиндр состоящий из крышки тарельчатой части и днища. Также в аппарате имеются штуцера для подвода исходной смеси и подачи флегмы отвода дистиллята и кубового остатка. Ректификационная колонна имеет цилиндрический корпус внутри которого установлены контактные устройства в виде ситчатых тарелок.
Работают эти тарелки следующим образом. Жидкость поступая через переливное устройство распределяется равномерно по всей плоскости основания тарелки и затем сливается в другое переливное устройство. Газ проходит через направляющие элементы и барботирует через жидкость образуя вспененный дисперсный слой газ и жидкости.
Стекая вниз по колонне жидкость взаимодействует с поднимающимся паром образованным при кипении кубовой жидкости в кубе-испарителе. Пар кубовой жидкости образуется за счет части высококипящего компонента направленного на испарение. В результате массообмена с жидкостью пар обогащается НК – ацетоном а жидкая фаза ВК - водой. В верхней части колонны происходит укрепление паров при помощи флегмы орошающей пары поднимающиеся вверх. Пары конденсируются в дефлегматоре. Далее конденсат проходит распределитель потока. Часть конденсата идет на орошение колонны (флегма) а другая часть (дистиллят) поступает в холодильник и затем в емкость сбора дистиллята.
Рекомендуемые чертежи
- 25.01.2023
- 04.04.2021
- 25.01.2023
- 24.01.2023
- 25.01.2023
- 17.03.2024