Ректификационная установка непрерывного действия для разделения смеси метанол - вода


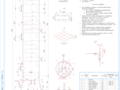
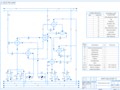
- Добавлен: 25.01.2023
- Размер: 1 MB
- Закачек: 1
Подписаться на ежедневные обновления каталога:
Описание
Ректификационная установка непрерывного действия для разделения смеси метанол - вода
Состав проекта
![]() |
![]() ![]() ![]() ![]() |
![]() ![]() ![]() ![]() |
![]() ![]() ![]() |
Дополнительная информация
Контент чертежей
Технологическая схема.cdw

Вода оборотная (подача)
Паро-жидкостная смесь
Колонна ректификационная
Вентиль регулирующий
КНИТУ 066.212.003 Т2
Технологическая схема
Колонна ректификационная 1600мм СБ.cdw

Выход кубового остатка
Выход жидкости на кипятильник
Техническая характеристика
Аппарат предназначен для разделения смеси метиловый
концентрацией 40 % (масс.).
Производительность по исходной смеси 1
Давление в колонне 0
Температура среды в кубе 98
Среда в аппарате - токсичная
Тип тарелок - ситчатые.
Технические требования
испытании и поставке аппарата должны
выполняться требования:
ГОСТ 12.2.003-74 "Оборудование производственное.
Общие требования безопасности";
ОСТ 26-291-79 "Сосуды и аппараты стальные сварные.
Технические требования.
Материал деталей колонны
соприкасающихся с разделяемыми
- сталь 08Х13 ГОСТ 5632-72 и сталь 20
остальных - Ст 3 ГОСТ 380-71.
Материал опоры - сталь 29Г2С ГОСТ 5570-29.
Материал прокладок - резина ГОСТ 481-71.
Аппарат испытать на прочность гидравлически в горизонтальном
положении под давлением 0
в вертикальном положении - под
Сварные соединения должны соответствовать требованиям
ОСТ 26-01-82-77 "Сварка в химическом машиностроении.
Сварные швы в объеме 100 % контролировать рентгенопросвечи-
Действительное расположение штуцеров и люков см. на схеме
Неуказанный вылет штуцеров 150 мм
Планка регулировочная
Болт М12х25 по ГОСТ 7798-70
Гайка М12 по ГОСТ 5616-70
Шайба М12 по ГОСТ 11371-58
КНИТУ 066.212.003 СБ
Колонна ректификационная
Схема расположения штуцеров и люков
ПЗ Расчет ректификационной колонны метанол-вода.docx
Федеральное государственное бюджетное образовательное учреждение
высшего профессионального образования
Казанский Национальный Исследовательский Технологический Университет
Кафедра процессов и аппаратов химических технологий
РАСЧЕТ РЕКТИФИКАЦИОННОЙ УСТАНОВКИ
Расчетно-пояснительная записка к курсовому проекту
на тему: «Ректификационная установка непрерывного действия для разделения смеси метанол - вода»
Рук. проекта Д.В. Прощекальников
Технологическая схема и ее описание 4
Выбор конструкционного материала аппарата ..5
Задание на расчет ректификационной установки ..6
Технологический расчет аппарата 7
1Материальный баланс .7
2Определение рабочего флегмового числа 9
3Средние массовые расходы по жидкости и пару 11
4Диаметр колонны и скорость пара ..12
5Выбор тарелки и определение скорости пара в рабочем сечении 14
Гидравлический расчет 15
1Гидравлический расчет тарелок в верхней части колонны 15
2Гидравлический расчет тарелок в нижней части колонны 16
3Минимальное расстояние между тарелками ..17
5Определение гидравлического сопротивления колонны ..24
Конструктивный расчет ..25
Механический расчет ..27
Тепловой расчет ..30
Список литературы .34
Ректификация — массообменный процесс который осуществляется в большинстве случаев в противоточных колонных аппаратах с контактными элементами (насадки тарелки) аналогичными используемым в процессе абсорбции. Поэтому методы подхода к расчету и проектированию ректификационных и абсорбционных установок имеют много общего. Тем не менее ряд особенностей процесса ректификации (различное соотношение нагрузок по жидкости и пару в нижней и верхней частях колонны переменные по высоте колонны физические свойства фаз и коэффициент распределения совместное протекание процессов массо- и теплопереноса) осложняет его расчет.
Одна из сложностей заключается в отсутствии обобщенных закономерностей для расчета кинетических коэффициентов процесса ректификации. В наибольшей степени это относится к колоннам диаметром более 800 мм с насадками и тарелками широко применяемым в химических производствах. Большинство рекомендаций сводится к использованию для расчета ректификационных колонн кинетических зависимостей полученных при исследовании абсорбционных.
Процессы перегонки и ректификации основаны на различной летучести компонентов смеси при одной и той же температуре. Компонент смеси обладающий большей летучестью называется легколетучим а компонент обладающий меньшей летучестью труднолетучим. Соответственно легколетучий компонент кипит при более низкой температуре чем труднолетучий. Поэтому их называют также низкокипящим и высококипящим компонентами.
В результате перегонки или ректификации исходная смесь разделяется на дистиллят обогащенный легколетучим компонентом и кубовый остаток обогащенный труднолетучим компонентом. Дистиллят получают в результате конденсации паров в конденсаторе-дефлегматоре. Кубовый остаток получают в кубе установки.
Задачей данного проекта является создание оптимальной конструкции аппарата и проведение расчетов обеспечивающих работоспособность данного аппарата.
Технологическая схема и ее описание
Рис. 1 - Принципиальная схема ректификационной установки
– емкость для исходной смеси; 2 – подогреватель; 3 – колонна;
– кипятильник; 5 – дефлегматор; 6 – делитель флегмы; 7 – холодильник; 8 – сборник дистиллята; 9 – сборник кубового остатка.
Исходную смесь из емкости 1 центробежным насосом подают в теплообменник 2 где она подогревается до температуры кипения. Нагретая смесь поступает на разделение в ректификационную колонну 3 где состав жидкости равен составу исходной смеси xF . Стекая вниз по колонне жидкость взаимодействует с поднимающимся вверх паром образующимся при кипении кубовой жидкости в кипятильнике 4. В результате массообмена с жидкостью пар обогащается легколетучим компонентом. Для более полного обогащения верхнюю часть колонны орошают в соответствии с заданным флегмовым числом жидкостью (флегмой) состава хР получаемой в дефлегматоре 5 путем конденсации пара выходящего из колонны. Часть конденсата выводится из дефлегматора в виде готового продукта разделения - дистиллята который охлаждается в теплообменнике 7 и направляется в емкость 8. Из кубовой части колонны насосом непрерывно выводится кубовая жидкость – продукт обогащенный труднолетучим компонентом который охлаждается в теплообменнике 7 и направляется в емкость 9.
Таким образом в ректификационной колонне осуществляется непрерывный неравновесный процесс разделения исходной бинарной смеси на дистиллят (с высоким содержанием легколетучего компонента) и кубовый остаток (обогащенный труднолетучим компонентом).
Выбор конструкционного материала аппарата
При конструировании химической аппаратуры следует применять стойкие металлические и неметаллические конструкционные материалы в заданных агрессивных средах. Важно учитывать все виды возможного коррозийного разрушения материалов в агрессивной среде при ее заданных рабочих параметрах. При выполнении прочностных расчетов в первую очередь сталкиваются с необходимостью оценки общей поверхностной коррозии выбираемого конструкционного материала характеризующегося проницаемостью ПМ ммгод.
В расчетах аппаратуры на прочность потеря по толщине материала на коррозию учитывается соответствующей прибавкой С определяемой амортизационным сроком службы аппарата и проницаемость по формуле:
tа – амортизационный срок примем tа=20 лет.
Для корпуса аппарата выбираем по рекомендациям [1] листовую сталь марки 12Х18Н10Т по ГОСТ 10885-75 для которой технические требования по ГОСТ 10885-75; рабочие условия: tR = -30 т- 200°С; р МПа - не ограничено. Виды испытаний и требования по ГОСТ 10885-75 (испытания проводятся на заводе-поставщике металла по требованию заказчика).
При выборе материала было учтено следующее:
-коррозионные свойства среды. При заданных рабочих параметрах скорость коррозии составляет менее 01 ммгод.
-технологические свойства используемого материала: свариваемость пластичность и другие.
-влияние конструкционного материала на качество исходной смеси и продуктов разделения
-технико-экономические соображения: нержавеющая сталь широко применяется в
химическом машиностроении и других отраслях промышленности
Сварка автоматическая.
Тип электрода по ГОСТ 10052-75 - Э-04Х20Н9.
Опоры цилиндрические. Материал деталей опор должен выбираться из условий эксплуатации и в соответствии с техническими требованиями ОСТ 26-291-94. Предел текучести материала должен быть не менее 210 МПа при t = 20°С. Назначаем материал опор сталь 09Г2С-3 по ГОСТ 5520-79 технические требования по ГОСТ 5520-79.
Материал фланцев - сталь 12Х18Н10Т. Сварочные материалы по ГОСТ 10052-75 - Э-04Х20Н9.
Назначаем материал крепежных деталей: не контактирующих с агрессивной средой - сталь 35 по ГОСТ 1050-74; для деталей контактирующих с агрессивной средой - сталь 08X13 по ГОСТ 5632-72.
По рекомендациям [7] назначаем материал прокладок - резина по ГОСТ 481-71. Внутренние элементы аппарата выполняются из стали 12Х18Н10Т по ГОСТ 5632-72.
Задание на расчет ректификационной установки.
Рассчитать тарельчатую ректификационную колонну непрерывного действия для разделения бинарной смеси и нарисовать чертеж выбранного типового аппарата.
Обозначения и размерности
Производительность по исходной смеси F тч.
Содержание летучего компонента (н.к).
В исходной смеси X f
В кубовом остатке Хw
Давление в паровом пространстве дефлегматора Р=03Мпа.
Технологический расчет аппарата
1 Материальный баланс
Производительность колонны по дистилляту P и кубовому остатку W определяем из уравнения материального баланса колонны.
Уравнение материального баланса:
гдеD – расход дистиллята кгс;
W – расход кубового остатка кгс;
Отсюда находим производительность колонны по дистилляту D и кубовому остатку W:
D == F – W = 5 – 3351 = 1649 кгс
Нагрузки ректификационной колонны по пару и жидкости определяются значением рабочего флегмового числа R. Ввиду отсутствия надёжной методики оценки Rопт используют приближённые вычисления основанные на определении коэффициента избытка флегмы (орошения) равного отношению RRmin где Rmin – минимальное флегмовое число.
yF*-концентрация легколетучего компонента в паре находящегося в равновесии с исходной смесью кмолькмоль смеси.
Пересчитываем составы фаз из массовых в мольные доли по соотношению:
где MM MH2O – молекулярные массы метанола и воды;
MА = 32 MВ = 18 кгкмоль
Аналогично находим xD и xW :
Таблица 1. Равновесные составы жидкости (x) и пара (y) в мольных % и температура кипения (t) в °C двойных смесей при 760 мм. рт. ст. [2 стр. 255]
По данным приведённым в таблице строим диаграмму равновесия пар – жидкость (диаграмма y – x).
Рис. 2 – Диаграмма равновесия между паром (у) и жидкостью (х) при постоянном давлении
Из рисунка 1: yF*=061
Минимальное флегмовое число
Rmin=( xD - yF ) ( yF - xF )=( 0931-061)(061-0217)=08402
2 Определение рабочего флегмового числа R
где – коэффициент избытка флегмы (берем произвольно)
Равновесные данные для различных систем приведены в справочнике [2].
Результаты расчетов рабочего флегмового числа приведены в таблице.
Минимальное произведение N(R+1) соответствуют флегмовому числу Rопт=12603 (=15).
Рис. 3 Нахождение оптимального флегмового числа
Получаем уравнения рабочей прямой верхней и нижней частей колонны:
Где f – относительный мольный расход f=(XD - XW)(XF - XW)=4473
Рис. 4 Диаграмма равновесия между паром (х) и жидкостью (у) при оптимальном флегмовом числе Rопт=125
3 Средние массовые расходы по жидкости и пару
3.1. Средний мольный состав жидкости в верхней и нижней частях колонны
кмолькмоль смеси; кмолькмоль смеси;
3.2. Средние мольный массы жидкости в верхней и нижней частях колонны
3.3. Мольная масса исходной смеси и дистиллята:
3.4. Средние массовые расходы по жидкости для верхней и нижней частей колонны
3.5. Средний мольный состав пара в верхней и нижней частях колонны
По равновесной линии находим
3.6. Средние мольный массы пара в верхней и нижней частях колонны
3.7. Средние массовые расходы пара в верхней и нижней частях колонны
4 Диаметр колонны и скорость пара
4.1. Средняя температура верха и низа колонны
Построим диаграмму зависимости концентраций в паровой и жидкой фазе от температуры :
Рис. 5 Диаграмма зависимости концентраций в паровой и жидкой фазе от температуры
Из рис. 8 температура в средней части колонны равна tF=812C в верхней части температура tD=658C и в нижней части температура tW=985C. Тогда средние температуры равны:
Средние плотности жидкой и паровой фазы
4.2. Плотность жидкой фазы в верхней части колонны
При средней температуре верхней части 735°С плотности жидких метанола и воды равны соответственно: ρxMв=740 кгм3 и ρхН2Ов = 97528 кгмоль [5 с. 512 табл. IV]
По закону аддитивности:
ρхв = 740·0574+97528·(1 - 0574) = 840232 кгм3
4.3. Плотность жидкой фазы в нижней части колонны
При средней температуре нижней части 8985°С плотности жидких метанола и воды равны соответственно: ρxMн = 752 кгм3 и ρхН2Он = 96506 кгм3 [5 с. 512 табл. IV]
ρх н =725·0114+96506·(1- 0114) = 937658 кгм3
Принимаем среднюю плотность жидкости в колонне:
4.5. Плотность паровой фазы в верхней и нижней части колонны
Средняя плотность пара в колонне:
Расчет скорости пара и диаметра колонны
Допустимая скорость в верхней и нижней частях колонны соответственно равна:
В расчете используем среднюю скорость
Принимаем средний массовый поток пара G равным полусумме Gв и Gн:
Ориентировочный диаметр колонны определяют из уравнения расхода:
5 Выбор тарелки и определение скорости пара в рабочем сечении
Выберем ситчатую однопоточную тарелку типа ТС-Р по ОСТ 26-808–73 для колонны диаметром d=1800мм с конструктивными размерами [6]
Свободное сечение колоны Fc
Рабочее сечение тарелки Sт
Относительное свободное сечение тарелки
Диаметр отверстия dо
Шаг между отверстиями t
Относительная площадь перелива
Высота переливного порога hп
Ширина переливного порога b
Действительная рабочая скорость пара:
Скорость пара в рабочем сечении тарелки:
Гидравлический расчет
Общее гидравлическое сопротивление тарелки определяется по формуле:
где: Pсух – сопротивление сухой тарелки Па;
Р - сопротивление вызванное силами поверхностного натяжения Па;
Рпж – статическое сопротивление слоя жидкости на тарелке Па;
1 Гидравлический расчет тарелок в верхней части колонны
Гидравлическое сопротивление сухой тарелки:
где: - коэффициент сопротивления для ситчатой тарелки принимаем равным 185
у – средняя плотность пара в верхней части колонны;
т – скорость пара в колонне;
Гидравлическое сопротивление обусловленное силами поверхностного натяжения:
поверхностное натяжение =Нм при средней температуре 738С.
Гидравлическое сопротивление парожидкостного слоя на тарелке:
Высота парожидкостного слоя hпж по рисунку 6
Величину Δh – высота слоя над сливной перегородки рассчитываем по формуле:
V П – периметр сливной перегородки.
Следовательно гидравлическое сопротивление парожидкостного слоя на тарелке:
Следовательно общее гидравлическое сопротивление тарелки:Па;
2 Гидравлический расчет тарелок в нижней части колонны
где: - коэффициент сопротивления для ситчатой тарелки принимаем равным 1.85
у – средняя плотность пара в нижней части колонны;
Па; где поверхностное натяжение = Нм при средней температуре 9005С.
Следовательно общее гидравлическое сопротивление тарелки:
среднее гидравлическое сопротивление тарелки будет:
3 Минимальное расстояние между тарелками
Проверяем выбранное расстояние между тарелками: минимальное расстояние между ними должно быть равным:
Выбранное ранее расстояние между тарелками Hмин = 500 мм подходит.
Молярный расход пара по колонне:
Рабочая площадь тарелки:
Фактор скорости для ситчатых тарелок:
4.1 Определение вязкости пара в укрепляющей и исчерпывающей части колонны
Определим коэффициент динамической вязкости для пара в укрепляющей части колонны:
где коэффициент динамической вязкости метилового спирта мПа.с коэффициент динамической вязкости воды мПа.с при средних температурах в укрепляющей части колонны (735C).
Определим коэффициент динамической вязкости для пара в исчерпывающей части колонны:
где коэффициент динамической вязкости метилового спиртамПа.с коэффициент динамической вязкости воды мПа.с при средних температурах в исчерпывающей части колонны (8985С).
4.2 Коэффициент диффузии жидкости и пара при средней температуре
Для того чтобы определить коэффициент диффузии при средней температуре необходимо рассчитать коэффициент диффузии Dx20 при 20оС:
- диффузные мольные объемы компонентов в жидкой фазе при температурах кипения см3моль х = 0597 мПа.с – средний коэффициент динамической вязкости при 200С А=119 В=470 ;
Температурный коэффициент b:
Коэффициент диффузии при средней температуре:
Коэффициент диффузии пара при средней температуре;
Т – средняя температура Р – абсолютное давление в колонне Па
4.3 Коэффициент массоотдачи и массопередачи
Рассчитав коэффициенты молекулярной диффузии в жидкой Dx и паровой Dy фазах вычисляем коэффициенты массоотдачи отнесённые к единице рабочей поверхности тарелки для жидкой и паровой фаз:
Паросодержание барботажного слоя находим по формуле
Для верхней части колонны
Для нижней части колонны
Пересчитаем коэффициенты массоотдачи на кмоль(м2·с):
Общий коэффициент массопередачи Kyf:
где m – тангенс угла наклона линии равновесия;
Так как величина m является переменной по высоте колонны находим ее значения для различных концентраций используя диаграмму y – x. Предварительно на диаграмму наложим кривую равновесия и линии рабочих концентраций при рабочем значении флегмового числа R = 1.25 (рис.7). В пределах от xW до xD выбираем ряд значений x. Для каждого значения x определяем по диаграмме величины (y* - y) и (x – x*) как разность между равновесной и рабочей линиями а затем по этим значениям находим m (Таблица 4).
Далее подставляем в уравнение общего коэффициента массопередачи полученные значения xf yf и m для различных значений x. Результаты заносим в таблицу 5.
4.4 Общее число единиц переноса на тарелку
Далее подставляем в уравнение общее число единиц переноса на тарелку и значение коэффициента массопередачи Kyf для различных значений x. Результаты заносим в таблицу 6.
4.5 Локальная эффективность
Принимаем для паровой фазы модель идеального вытеснения.
Локальная эффективность для различных значений x. Результаты заносим в таблицу 7.
Для определения эффективности по Мэрфи необходимо рассчитать фактор массопередачи долю байпасирующей жидкости число ячеек полого перемешивания и межтарельчатый унос.
4.6 Фактор массопередачи
Локальная эффективность для различных значений x. Результаты заносим в таблицу 8.
Долю байпасирующей жидкости для различных конструкции можно определить в монограмме (5) при факторе скорости F=1.662 принимаем =0.1.
4.7 Число ячеек полного перемешивания
Число ячеек полного перемешивания S. Для ситчатых тарелок в колоннах диаметром более D=0.6 м отсутствуют надежные данные при продольном перемешиванию жидкости поэтому с достаточной степенью приближения можно считать что одна ячейка перемешивания соответствует длине пути жидкости: l=300-400 мм.
Примем l=350 мм и определим число ячеек полного перемешивания S как отношение длины пути жидкости на тарелке lт к l. Определим длину жидкости lт как расстояние между переливными устройствами:
где D - диаметр колонны;
Тогда число ячеек полного перемешивания на тарелке .
4.8 Относительный унос жидкости
Относительный унос жидкости e в тарельчатых колонах определяется в основном скоростью пара высотой сепарационного пространства и физическими свойствами жидкости и пара. В настоящие время нет надежных зависимостей учитывающих влияние физических свойств потоков на унос особенно для процессов ректификации. Для этих процессов унос можно оценить с помощью графических данных (Дытнерский). По данным унос на ситчатых тарелках является функцией комплекса .
Коэффициент m учитывающий влияние на унос физических свойств жидкости и пара:
х – поверхностное натяжение жидкости при средней температуре в колонне.
Высота сепарационного пространства.
В соответствии с каталогом [6] для колонны диаметром 1800мм расстояние Н=04м.
Нс в=04-000931=039069м
Нс н=04-001149=038851м
Н – межтарельчатое расстояние м; - высота барботажного слоя (пены) м.
h0 в=0787·02874·09808·00671·07006·08921=000931м
h0 н=0787·03601·09808·00671·07·08878=001149м
- вязкость жидких смесей мПа·с
хв= 03168 мПа·с; хн=02992 мПа·с
- уд. расход жидкости на 1м ширины переливной перегородки м2с;
qв=1729(840232·105)=000196
qн=5959(937658·105)=000605
m=0.05-4.6hпер=005-46·105= -478;
Высота сепарационного слоя в нижней части колонны меньше чем в
верхней поэтому расчет ведем для низа колонны.
При таком значении комплекса унос для всей колоны е= 015 кгкг;
4.9 К.П.Д. по Мэрфри
Эффективность по Мэрфри с учетом перемешивания на тарелке;
Эффективность по Мэрфри с учетом байпасирующего потока жидкости ;
Далее подставляем в каждое уравнение полученные значения λ S e и m для различных значений x. Результаты заносим в таблицу 9.
4.10. Построение кинематической линии
Зная эффективность по Мэрфри определим концентрацию легколетучего компонента в паре на выходе из тарелки yк по соотношению:
где: yвх - концентрацию легколетучего компонента в паре на входе в тарелку.
Результаты заносим в таблицу 10.
На диаграмме y – x (рис. 9) полученные точки соединяем плавной линией. Построенная кривая является кинетической кривой.
Рис. 9 Определение числа действительных тарелок
Число реальных тарелок которое обеспечивает заданную четкость разделения находим путем построения ступенчатой линии между рабочей и кинетической линиями. Построение ступенчатой линии проводим от концентраций xf xd и от xf xw.
Число ступеней в пределах концентраций xf xd равно числу реальных тарелок в укрепляющей секции колонны. Число ступеней в пределах концентраций xf xw равно числу реальных тарелок исчерпывающей секции колонны.
В результате построения получаем:
-число реальных тарелок в укрепляющей секции колонны – 8;
-число реальных тарелок в исчерпывающей секции колонны – 10;
-общее число тарелок – 18.
Высоту тарельчатой ректификационной колонны определим:
м zв zн – расстояние соответственно между верхней тарелкой и крышкой колонны и между днищем колонны и нижней тарелкой.
5 Определение гидравлического сопротивления колонны
Суммарное гидравлическое сопротивление колонны:
где ΔРв и ΔРн – гидравлическое сопротивление одной тарелки соответственно верхней и нижней частей колонны Па.
Конструктивный расчет
Расчет проходного диаметра штуцеров колонны и выбор фланцев
Основная расчетная формула
где G – объемный расход;
– рекомендуемая скорость перекачиваемой среды (жидкости или пара );
1 Штуцер для входа исходной смеси
При tF=81.2C плотности метанола и воды равны: [5 табл. IV]. Плотность смеси при температуре :
принимаем dy=65мм [7 с. 659 табл. 27.1]
2 Штуцер для выхода пара в дефлегматор
принимаем dy=400мм [7 с. 659 табл. 27.1]
3 Штуцер для входа флегмы в колонну
при [5 с. 512 табл. IV]
принимаем dy=50мм [7 с. 659 табл. 27.1]
4 Штуцер для выхода кубовой жидкости
при tW=98.5C [5 с. 512 табл. IV]
Так как жидкость вытекает самотеком принимаем ж=1мс
5 Штуцер для входа пара из кипятильника
6 Штуцер для выхода жидкости из куба на циркуляцию
принимаем dy=55мм [7 с. 659 табл. 27.1]
7 Изготовление штуцеров и выбор фланцев
Для упрощения конструктивных деталей колонны будем изготовлять штуцера из отрезков труб соответствующих диаметров. Внешний вылет штуцеров составляет 1.5 от диаметра штуцера внутренний - 0.3. Чтобы предупредить попадание жидкости во внутреннее пространство штуцера подающего циркуляционный пар труба из которой он изготовлен обрезается под углом книзу.
К выступающим отрезкам труб привариваются фланцы плоские стальные.
1 Расчёт толщины обечайки
Главным составным элементом корпуса большинства химических аппаратов является обечайка. В химическом аппаратостроении наиболее
распространены цилиндрические обечайки отличающиеся простотой изготовления рациональным расходом материала и достаточной прочностью.
Для ректификационной колонны диаметром 1800 мм примем стандартную минимальную толщину стенки корпуса = 10 мм и проверим выполняется ли условие
где Ск - прибавка к номинальной толщине детали учитывающая разрушающее действие среды на материал (см. раздел 2)
Проверяем выполнение условия
Поскольку условие выполняется принимаем толщину обечайки = 10 мм.
2 Расчёт толщины днища
Составными элементами корпусов химических аппаратов являются днища которые обычно изготовляются из того же материала что и обечайки и привариваются к ней. Днище неразъёмное ограничивает корпус вертикального аппарата снизу и сверху. Форма днища может быть эллиптической сферической конической и плоской. Наиболее рациональной формой днищ для цилиндрических аппаратов является эллиптической. Эллиптические днища изготавливаются из листового проката штамповкой.
Толщину днища принимаем равной толщине обечайки и проверяем выполнение условие
Следовательно условие выполняется.
3 Расчёт фланцевых соединений и крышки
Соединение состоит из двух фланцев прокладки которую размещают между уплотнительными поверхностями фланцев болтов гаек и шайб. Т.к. давление в аппарате P=03МПа25 МПа то выбирается фланец с гладкой поверхностью.
Прокладка – резина листовая техническая (ГОСТ 7338—65)
Dп =1890 мм; dп = 1848 мм.
При конструировании аппаратов выполняют проверочный расчет болтов в соответствии с ГОСТ 26–373–82:
Нагрузка действующая на фланцевое соединение от внутреннего давления
где средний диаметр прокладки
где ширина прокладки
b0–эффективная ширина прокладки: при
Болтовая нагрузка при сборке:
где – допускаемое напряжение для материала болта при 200С; ВСт3 – площадь поперечного сечения болта.
Наибольшее значение
Проверка прочности болтов при монтаже
Проверка прочности болтов в период эксплуатации
где – допускаемое напряжение для болта при рабочей температуре
Выполняются оба условия следовательно нет необходимости увеличивать число болтов z = 64 [4с.68 таблица 4].
4 Расчёт опор аппаратов
Выбор типа опоры зависит от ряда условий: места установки аппарата соотношения высоты и диаметра аппарата его массы и т.д. Аппараты вертикального типа с соотношением ≥5 размещаемые на открытых площадках оснащают так называемыми юбочными опорами цилиндрическими или коническими. В нашем случае берем цилиндрические опоры. [7с.672]
Вес аппарата при гидроиспытании:
Толщина стенки цилиндрической опоры S=10 мм. Напряжение сжатия в этой стенке с учетом наличия в ней отверстия для лаза d = 05 м при максимальной нагрузке от силы тяжести аппарата:
Kc=0105; Ku=013; [7с.418]
Допускаемое напряжение на сжатие в обечайке опоры:
Допускаемое напряжение на изгиб в обечайке опоры:
Условие выполняется.
Максимальные напряжения на сжатие в сварном шве соединяющем цилиндрическую опору с корпусом аппарата при коэффициенте сварного шва = 07:
Внутренний диаметр опорного кольца:
D2 = D — 006 =18 -006=174 м [7с.692]
Наружный диаметр опорного кольца:
D1 = D + 2S+02 = 18 + 2 001 + 02 = 202 м [7с.692]
Опорная площадь кольца:
Максимальное напряжение сжатия на опорной поверхности кольца:
Номинальная расчетная толщина опорного кольца при l= 01 м:
с учетом прибавки на коррозию принимаем округляя размер Sк = 54 мм.
Расчетная нагрузка на один болт:
Расчетный внутренний диаметр резьбы болтов:
Принимаем болты М1225. [7с.538]
Тепловой расчет установки
1 Расход теплоты отдаваемый охлаждающей воде в дефлегматоре-конденсаторе находим по уравнению:
где rM=1100кДжкг rH2O=1538.36кДжкг – удельные теплоты конденсации метанола и воды при температуре tD=65.3C
2 Расход теплоты получаемый в кубе-испарителе от греющего пара:
Qпот=3% от полезно затрачиваемой теплоты С – удельные теплоемкости смеси взятые в зависимости от температуры.
Таблица 11. Теплоёмкости компонентов при различных температурах [10].
Низкокипящий компонент
Высококипящий компонент
где– массовые доли метанола (низкокипящий компонент) кгкг;
Ср - теплоёмкости компонентов при различных температурах Джкг*К.
F:Cp F см= 262398·033+4198·(1-033) = 36785734Джкг·К;
D:C p D см= 257978·096+4187·(1-096) = 26440688Джкг·К;
W:C p W см= 266428·005+4213·(1-002) = 41820256Джкг·К.
3 Расход теплоты в паровом подогревателе исходной смеси:
tнач=20С удельная теплоемкость СF=0633·4190=265227Джкг·К взята при средней температуре (812+20)2=506 С. [5 c.562]
Здесь тепловые потери приняты в размере 5%.
4 Расход теплоты отдаваемой охлаждающей воде в водяном холодильнике дистиллята:
tкон=25 С удельная теплоемкость СD=0625·4190=261875 Джкг·К взята при средней температуре (653+25)2=4515 С
5 Расход теплоты отдаваемой охлаждающей воде в водяном холодильнике кубового остатка:
удельная теплоемкость СW=0645·4190=270255 Джкг·К взята при средней температуре (985+25)2=614 С
6 Расход греющего пара имеющего давление рабс=4кгссм2 и влажность 5%:
а) в кубе-испарителе:
где rг.п.=213295·103Джкг – удельная теплота конденсации греющего пара.
б) в подогревателе исходной смеси:
Всего: 2752+0428=318кгс или 112тч
7 Расход охлаждающей воды при нагреве ее на 20С
б) в водяном холодильнике дистиллята:
в) в водяном холодильнике кубового остатка:
Всего: 00595м3с или 2142м3ч.
Библиографический список
Воробьёва Г. Я. Коррозионная стойкость материалов в агрессивных средах химических производств. Изд. 2-е пер. и доп. М. «Химия» 1975. 816 с.
Коган В. Б. Фридман В. М. Кафаров В. В. Равновесие между жидкостью и паром. Т. 2. М.: «Наука» 1966.
Александров И. А. Ректификационные и абсорбционные аппараты. Изд. 3-е. М.: «Химия» 1978. – 280 с.
Основные процессы и аппараты химической технологии: Пособие по проектированиюПод ред. Дытнерского. М.: Химия 1983.
Павлов К. Ф. Романков П. Г. Носков А. А. Примеры и задачи по курсу процессов и аппаратов химической технологии. Учебное пособие для вузов.Л.: Химия1987.
Каталог «Ректификационные и абсорбционные колонны» ЦИНТИХИМНЕФТЕМАШ 1991г.
Лащинский А. А. Толчинский А. Р. Конструирование сварных химических аппаратов. Справочник. Л.: «Машиностроение» 1970. 752 с.
Белоусов В. П. Марачевский А. Г. Тепловые свойства растворов неэлектролитов. Л.: «Химия» 1981 264 с.
Расчет и конструирование химических аппаратов с мешалками: учебное пособие Островская Э.Н. Полякова Т.В.- Казань: Изд-во КГТУ2006.- 120с.
Гусев В.П. Гусева Ж.А.. Процессы и аппараты химической технологии. Физико-химические и термодинамические свойства веществ Методическое пособие к выполнению курсового проекта по процессам и аппаратам химической технологии в 2-х частях Часть 2. – Т.: ТХТК 1994. - 69 с.
Рекомендуемые чертежи
- 25.01.2023
- 17.03.2024
- 25.01.2023
- 25.01.2023
- 10.04.2022
- 25.01.2023
- 24.01.2023
Свободное скачивание на сегодня
Обновление через: 17 часов 11 минут