Расчет ректификационной установки непрерывного действия с решетчатыми тарелками для разделения бинарной смеси этанол-вода


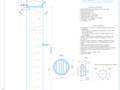
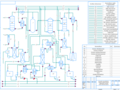
- Добавлен: 24.01.2023
- Размер: 2 MB
- Закачек: 0
Описание
Состав проекта
![]() |
![]() ![]() ![]() |
![]() ![]() |
![]() ![]() ![]() |
![]() |
![]() ![]() ![]() ![]() |
![]() ![]() ![]() ![]() |
![]() ![]() ![]() |
Дополнительная информация
Технологическая схема.doc
сернокислотной гидратацией этилена
Этан-этиленовая фракция с содержанием 50-60 % этилена из цеха газоразделения подаётся в нижнюю часть абсорбционной колонны КА. В верхнюю часть колонны подаётся серная кислота с концентрацией 96-98 %. В колонне КА при давлении 25 МПа и температуре 67-75 градусов происходит абсорбция этилена сернон кислотой с образованием этилсульфата.
Этан выходит из верхней части колонны КА с содержанием этилена 2-4 %. Отходящие из колонны КА газы после дросселирования до 07-08 МПа в дросселе ДР промываются водой в скруббере С1 нейтрализуются щёлочью в скруббере С2 и после сушки в брызгоуловителе Б направляются на гиролиз в виде возвратной этаноловой фракции. Насос H1 перекачивает раствор щёлочи из нижней части скруббера С2 на орошение в верхнюю часть. Распределитель Р1 служит для удаления части отработанной щёлочи.
Раствор этилсульфатов из нижней части колонны КА после охлаждения в холодильнике X1 поступает в гидролизер Г где смешивается в инжекторе с водой. Гидролиз этилсульфатов осуществляется при давлении 02 МПа и температуре 95-100 °С. В результате снижения давления и повышения температуры из раствора выделяются растворённые газы которые вместе с парами диэтилового эфира выводятся из верхней части гидролизера Г и подаются на промывку в скруббер С1 и нейтрализацию в скруббер С2 вместе с отработанным этаном.
В гидролизате отходящем из нижней части гидролизера Г помимо воды серной кислоты и этилового спирта содержится также диэтиловый эфир непрогидролизовавшиеся этилсульфаты и растворённые газы
Окончательный гидролиз происходит в отпарной колонне КО куда вместе гидролизатом вводят острый нар. В отпарной колонне КО при давлении 015 MПa и температуре куба 125 ºС и верха 95 °С происходит отгонка из гидролизата спирта диэтилового эфира и части водяных паров. Отработанная серная кислота с концентрацией около 40 % после отпарной .длинны КО направляется на очистку от смолистых соединений
Отходящая из отпарной колонны КО парогазовая смесь подаётся в нейтрализационно-отпарную колонну КН куб который обогревается острым наром. Парогазовая смесь нейтрализуется в колонне КН 5 %-ым раствором едкого натрия и направляется в конденсатор К. Сконденсированный этиловый спирт обрабатывается в сепараторе СП где из конденсата выделяются растворенные газы. Газы из сепаратора СП после промывки в скруббере СЗ выбрасываются в атмосферу.
После сепаратора СП спирт-сырец направляется и ёмкость Н 1 откуда насосом Н2 подастся в подогреватель П. Нагретый до температуры кипения равной 94 ºС спирт-сырец поступает в ректификационную насадочную колонну КР куб которой обогревается глухим паром. Ректификация идет при атмосферном давлении. Обогащенные этанолом пары конденсируются в дефлегматоре Д. Полученный дистиллят разделяется в разделителе Р2: одна часть в виде флегмы идёт на орошение колонны КР другая часть охлаждается в холодильнике ХЗ и попадает в ёмкость дистиллята Е3. Кубовый остаток охлаждается в холодильнике Х2 после чего скапливается в ёмкости Е2.
Емкости Е2 и ЕЗ оснащены насосами НЗ и Н4 для дальнейшего транспортирования жидкостей.
расчетная часть.doc
Задание. Рассчитать и спроектировать ректификационную установку непрерывного действия для разделения под атмосферным давлением бинарной смеси этанол-вода в схеме производства этанола сернокислотной гидратацией этилена.
Производительность установки по исходной смеси Gf=13тч. Содержание легколетучего компонента в исходной смеси af=330% масс. в дистилляте ap=89% масс. В кубовом остатке aw=1% масс. t см=250 tхолw=460ºC tхолp=340ºС.
Давление греющего пара Pr=03 МПа среднее давление в колонне-атмосферное. Разделяемая смесь поступает в ректификационную колону при температуре кипения. Тип контактного устройства-тарелка решетчатая.
1.1.Расчет ректификационной колонны.
Материальный расчет процесса. Определение минимального и рабочего флегмового числа.
Количество дистиллята и кубового остатка определим путем совместного решения уравнения материального баланса. Выразим Gp из первого уравнения системы
И подставим во второе:Gfaf=(Gf-Gp)*ap+Gw*aw
Определим количество кубового остатка
Gf·ap=Gf·ap-Gw·ap+Gw·aw или
Gf·ap=Gf·ap-Gw(ap-aw) откуда
=823 тч = 23 кгс тогда
Gp=13-827=437тч=131кгс.
Определение минимального и рабочего флегмового числа.
Флегмовое число определяется отношением количества флегмы возвращаемой в колонну к количеству отбираемого дистиллята. Оно является важнейшей характеристикой процесса ректификации отказывающей влияние на движущую силу процесса число тарелок и высоту колонны на расход греющего пара для проведения процесса ректификации и на расход охлаждающей воды в дефлегматоре.
Минимальное флегмовое число определяем двумя способами: графическим и графоаналитическим. Для реализации этих способов построим диаграмму
y-x по экспериментальным данным (таблица-1).
Для выполнения необходимых построений на y-x-диаграмме пересчитаем массовые концентрации в мольные по формуле.
Индексы a и b относятся к низкокипящему и высококипящему компонентам смеси соответственно.
Ma=46 гмоль (этанол)
Для графического определения минимального флегмового числа Rmin на диаграмме y-x (рис.1)находим точки С(xp-yp) и В(xf-y*f). Проведем через эти точки прямую до пересечения с осью ординат отсекающей на ней отрезок Bmax. Из уравнения линии рабочих концентраций для верхней части колонны ( для минимального флегмового числа).
Проверим значение Rmin по формуле
Как видно результаты расчёта по обеим методикам хорошо согласуются. Принимаем минимальное флегмовое число Rmin=0621.
Задаваясь различными значениями коэффициентов избытка флегмы (рис.2-7)определим соответствующие флегмовые числа. Графическим построением ступеней изменения концентраций между равновесной и рабочими линиями на диаграмме Х-У находим число теоретических тарелок N.
Результаты расчетов рабочего флегмового числа представлены в таблице 2.
Строим график в координатах N(R+1)- R и из точки минимума находим оптимальное рабочее флегмовое число Rопт = 12.
Построение рабочих линий укрепляющей и исчерпывающей частей колонны
Рассчитаем отрезок Bотсекаемый рабочей линией укрепляющей части колонны на оси ординат при рабочем флегмовом числе
Откладываем на оси ординат отрезок B (рис.8) и проводим линиюкоторая пересекается с вертикальной прямой Xf в точке В.
Линия СВ-рабочая линия укрепляющей части колонны. Соединяем точки В и Xw. Линия BXw-рабочая линия исчерпывающей части колонны.
2.Определение числа теоретических и действительных тарелок методом теоретических ступеней изменения концентраций.
Для определения числа теоретических тарелок(ступеней изменения концентраций)между линиями рабочих концентраций(рабочими линиями) СВ и BXw и равновесной линией y*=f(x) строим ступенчатую линию состоящую из горизонтальных и вертикальных отрезков в пределах изменения x от xp до xw .
Количество ступеней соответствующих теоретическому числу тарелок nm=11 шт.
Для определения действительного числа тарелок необходимо определить коэффициент полезного действия тарелок .
КПД учитывает реальную кинетику массообмена на тарелках на которых обычно равновесие не достигается.
Величина зависит от ряда факторов в том числе от скорости фаз их перемещения взаимного направления движения физических свойств фаз и т.п. Значение КПД находится опытным путем и изменяется в широких пределах ( =03-08).
КПД можно определить по графику либо по уравнению =049(ж·α)-0.245.
Определение значений параметров по колонне физико-химических и термодинамических констант фаз.
Среднее значения параметров по колонне по жидкой фазе:
-средняя мольная концентрация в нижней части колонны
-средняя мольная концентрация в верхней части колонны
-средняя мольная концентрация по колонне
-средние мольные массы
Mxв=Ma·xв+Mb(1-xв)=46·046+18·(1-046)=3088 кгкмоль.
Mxн=Ma·xн+Mb(1-xн)=46·0082+18·(1-0082)=203 кгкмоль.
-средняя температура в нижней части колонны
-средняя температура в верхней части колонны
-средняя температура по колонне
При 8032: рэ = 7196 кгм3; рв = 9716 кгм3.
При 8794: рэ = 7099 кгм3; рв = 9667 кгм3
При 8032: э = 0569 мПас[23 табл. XXXIX]; в =0356 мПас [26 прил. 2].
При 8794: э = 055 мПас; в = 0328 мПас
- среднее поверхностное натяжение
При 8032: =1997· Нм =6254· Нм
При 8794: =192· Нм =6113· Нм
- коэффициент диффузии при средней температуре
Дx(t)=Дx(20)·(1+b·(t-20))
где Дх(20) - коэффициент диффузии при 20 °С; в - температурный коэффициент; t - средняя температура жидкой фазы по колонне.
Температурный коэффициент в может быть определён по эмпирической формуле :
где и ρ вязкость и плотность растворителя (воды) при 20 °С: = 119 мПа·с; р = 790 кгм3.
Коэффициент диффузии при 20 °С вычислим по приближённой формуле:
Дxв(20)=2·2·=16·10-8м2с
Где = 119 мПа· с - динамическая вязкость воды (растворителя) при 20°С; А = 1 В = 47 - коэффициент зависящие от свойств растворённого вещества и растворителя ; Мв = 18 кгмоль Мэ = 46 кгмоль - мольные массы воды и этилового спирта; vA vB - мольные объёмы воды и этилового спирта:
vb=37·2 + 74 = 148 см3моль
va = 148·2 + 37·5 +74+37=592см3моль.
Дx(8032) =16·10-8·(1+00236·(8032-20))=388·10-8мс
Дx(8794) =16·10-8·(1+00236·(8794-20))=417·10-8мс
-Молярная масса дистиллята
-Массовый расход жидкой фазыкгс
=3452·131·123928=1.236
=24076·131·123928=0.812
-Объемный жидкой фазы с
Средние значения параметров по колонне по паровой фазе:
- средняя мольная концентрация в нижней части колонны
- средняя мольная концентрация в верхней части колонны:
-средняя мольная концентрация по колонне:
-средняя температура в нижней части колонны:
-средняя температура в верхней части колонны:
-средняя температура по колонне:
-средние мольные массы:
Myв=Ma·yв+Mb(1-yв)=46·059+18·(1-059)=34.52 кгкмоль.
Myн=Ma·yв+Mb(1-yв)=46·0217+18·(1-0217)=24.076 кгкмоль
где yA и yB- динамическая вязкость водяного пара и паров этанола при t = 20 °С
- коэффициент диффузии:
D(8297)= ·=105·10-6м2с
D(934)= ·=108·10-6м2с.
-Массовый расход паракгс
=3452·131·(12+1)3928=253
=24076·131·(12+1)3928=177
-Объемный расход пара
3 Определение основных геометрических размеров колонны
Высоту колонны определяют по формуле . Для определения действительного числа тарелок в колонне найдем КПД тарелок вычислив относительную летучесть по формуле:
где TA=373KTB=3464K-температура кипения воды и этилового спирта.
m=049(056·0466)0245=068.
Действительное число тарелок в колонне
Принимаем действительное число тарелок в колоше nд=17 шт.
Принимаем расстояние между тарелками h = 05 м (ниже будет выполнена проверка принятого расстояния) конструктивная прибавка С = 12 м. Тогда высота колонны
Нк = (17 - 1)·05+1+2= 92 м.
Для определения рабочей скорости пара (газа) выберем следующую формулу:
где wпр – предельная скорость пара (газа) мс. dэкв – эквивалентный диаметр щели (удвоенная величина ширины щели: для b = 4 мм dэкв = 0.008 м) м. – относительное свободное сечение тарелки. x – динамический коэффициент вязкости жидкости Па·с. В – коэффициент равный 2.95 для нижнего и 10 для верхнего пределов работы тарелки. В – динамический коэффициент вязкости воды при температуре равной 20°С.
Для предварительного расчета величины wпр задаютсяи В = 6 и определяют рабочую скорость пара (газа) а затем – рабочую скорость w = 0.8·wпр. По каталогу выберем решетчатую тарелку со свободным сечением Fс=02 шириной щели =6 мм dэ=0012м
Для верхней части колонны:
-Диаметр колонны определим по объемному расходу пара (газа) где Vy – объемный расход пара(газа) м3с; w – скорость пара(газа) в колонне мс:
Для нижней части колонны:
Выберем стандартный диаметр колонны 12м. Далее уточняем скорость пара (газа) по уравнению:
При расчете процесса ректификации как правило выбирают один и тот же диаметр колонны для обеих частей: верхней и нижней. Скорректируем коэффициент В с учетом найденной рабочей скорости пара (газа):
Для выбранной стандартной колонны должно быть выполнено условие: 2.95B10.
По каталогу для колонны диаметром 12м выберем решетчатую тарелку типа ТР с основными характеристиками:
Диаметр колонны d=1200мм
Относительное свободное сечение тарелки = 021
Диаметр отверстий b = 4мм
Толщина тарелки s=2мм
4.Расчёт гидравлического сопротивления колонны
Высота газожидкостного (барботажного) слоя рассчитывается по следующим формулам:
где - критерий Фруда (оптимальный); w0 – скорость пара (газа) в свободном сечении (щелях) тарелки мс; hг-ж – высота газожидкостного (барботажного) слоя м; С – коэффициент.
Коэффициент С определяется по соотношению:
где U – плотность орошения м3(м2с); – поверхностное натяжение Нм.
В уравнении подставляется уточненный коэффициент В. Скорость пара (газа) в щелях определяется по уравнению:
Плотность орошения (приведенная скорость жидкости) U рассчитывается по формуле:
где L S – площадь поперечного сечения выбранной колонны м2
а) для верхней части колонны:
б) для нижней части колонны:
Высота светлого слоя жидкости h0 определяется по соотношению:
Величина газосодержания рассчитывается по соотношению:
Гидравлическое сопротивление ректификационной колонны определяется гидравлическим сопротивлением тарелок:
где ΔPm - гидравлическое сопротивление одной тарелки Па;ng- число действительных тарелок в колонне.В свою очередь гидравлическое сопротивление тарелки складывается из сопротивления сухой тарелки (ΔPсух) сопротивления столба жидкости и пены на тарелке (гидростатическое сот противление ΔPст) и сопротивления обусловленного силами поверхностного натяжения ( ΔP ).
Сопротивление сухой тарелки
где - коэффициент сопротивления сухой тарелки для решётчатых провальных тарелок = 14 - 15 принимаем = 145; Wyраб - рабочая скорость движения паров в колонне; ρ - средняя плотность паров в колонне; Fc- свободное сечение тарелки м2м2.
Гидравлическое сопротивлениеобусловленное силами поерхностного натяжения
Гидравлическое сопротивление газожидкостного слоя на тарелке
Где g = 9 81 мс2 - ускорение свободного падения; ρ -средняя по колонне плотность жидкой фазы; h0 - высота светлого слоя жидкости на тарелке м.
ΔPст=981·7836·0088=6765 Па
Гидравлическое сопротивление одной тарелки:
ΔPст=981·9418·0053=48967 Па
Гидравлическое сопротивление колонны
Проверка расстояния между тарелками
Расстояние между тарелками влияет на брызгоунос е величина которая не должна превышать 01 кг жидкг пара
е =(062·-1)2·0063=0093.
Условие на брызгоунос выполняется т.к. 0093 01.
е =(035·-1)2·0091=0033.
Условие на брызгоунос выполняется т.к. 0033 01.
Температуры кипения исходной смеси дистиллята и кубового остатка:
Тепловые расчёты процесса ректификации выполняются с целью определения поверхностей теплообменников обслуживающих колонну расходов греющего водяного пара и охлаждающей воды.
Площадь поверхности любого теплообменника определяется из основного уравнения теплопередачи
Расход пара и охлаждающей воды определяется из теплового баланса теплообменника соответственно:
В вышеприведенных формулах: Q- тепловая нагрузка Вт Atcp - средняя разность температур °С;Д - расход греющего пара кгс; . 4 - энтальпия пара и конденсата соответственно Джкг; х - степень сухости пара; св - удельная теплоёмкость воды Джкг К;tKt - начальная и конечная температура охлаждающей воды °С.
При использовании сухого насыщенного греющего пара расход его можно определить по формуле
Где r-скрытая теплота парообразования (конденсации) Джкг. пара r=2208·103 Джкг при P=2ата.
Подогреватель исходной смеси
Тепловой баланс подогревателя исходной смеси 05 – коэфициент учитывающей потери теплоты в окружающую среду (5%); Gf сxF- теплоёмкость исходной смеси при её средней температуре r=2171·103 Джкг при P =3атм
С нагретой смесью до температуры кипения Q3=GFc
С конденсатом греющего пара Q4 = Д·iк
На компенсацию потерь теплоты в окружающую среду Q5=0.05·Q
Q1+Q2=Q3+Q4+Q5 или Q2-Q4=Q3+Q5-Q1=Q.
Подставляя в последнее уравнение вместо Q1Q2Q4Q5Q их значения из теплового баланса и решая его относительно Д имеем
Примем начальную температуру исходной смеси °C температура кипения смеси равная конечной температуре исходной смеси = 105 °C.
Средняя температура исходной смеси в подогревания
Теплоёмкостью исходной смеси при её средней температуре
Где =418581 = 31425 –удельная теплоёмкость воды и этанола соответственно при = 55°С
Тогда = 033·418581+ (1-033)· 31425 = 3486
Q= ·3486 (8143 – 25) = 710141 Вт
Расход пара Д = = = 033
Средняя разность температур между паром и смесью
Так как = = 252 2 то ср = =
Коэффициент теплопередачи в дефлегматоре принимаем ориентировочно равным 300Втм2 · К [26]
Площадь поверхности теплообмена дефлегматора:
Принимаем двух ходовой вертикальный теплообменник с диаметром 600мм с числом труб 240(в одном ходе 120)диаметром 25 × 2 с длиной труб 3000мм.Площадь поверхности 57 м2.
Тепловой баланс дефлегматора
. С парами из колонны
Потерями теплоты в окружающую среду пренебрегаем
Q1+Q2-Q3+Q4 илиQ1-Q3-Q2
Подставляя значения Q1Q2 Q3Q4 и решая уравнение относительно расхода охлаждающей воды получим
Gy=Gp·(Rраб++1)=·(12+1)=2882кгс.
Скрытая теплота конденсации паровой смеси в дефлегматоре
где rвода=21192·103 Джкг Rэт.=85289·103 Джкг при txp=7842.
rсм= 2119200 089 + 852890 (1 - 089) = 19745659 Джкг.
Тепловая нагрузка дефлегматора:
Q = 2882 19745659= 56906989 Вт.
Принимаем температуру охлаждающей воды на входе в дефлегматор 11°С на выходе 28°С.Средняя разность температур при противоточной схеме движения теплоносителей:
Так как = = 133 2 то ср = = 5892.
Коэффициент теплопередачи в дефлегматоре принимаем ориентировочно равным 500 Втм2· К.
Принимаем одноходовой кожухотрубчатый конденсатор с диаметром 800мм с числом теплообенных труб 257 7 диаметром 25 × 2 с длиной труб 9000мм.
Площадь поверхности 329 м2. Расположение аппарата горизонтальное.
Холодильник дистиллята
Тепловой баланс холодильника
+2 = 3 +4 или 1 – 3= 4 – 2
Подставляя в это уравнение вместо 1 2 3 4 выражения из теплового баланса и решая относительность расхода охлаждающей воды получим
Gв = на охлаждение дистиллята; = 34 - температура охлаждённого дистиллята (принимаем); - конечная и начальная температура воды (принимаем)
Средняя температура дистиллята в холодильнике = 5621.
Теплоёмкость дистиллята при его средней температуре
Ср = ap · ca + ( 1 – ap)·cв
Тогда ср = 089·31844 + ( 1 – 089) ·41481 = 32904
Средняя разность температур в холодильнике при противоточной схеме движения теплоносителей:
Принимаем ориентировочно значения коэффициент теплопередачи в холодильнике 800 Втм2 ·К тогда площадь поверхности теплообмена холодильника дистиллята
Выбираем одноходовой вертикальный холодильник диаметром 325мм с числом труб 62шт (в одном ходе 31 шт)с длиной трубы 2000мм диаметр теплообменных труб 25 2мм. Площадь поверхности 10 м2.
Холодильник кубового остатка
С охлаждающем кубовым остатком
Потерями теплоты в окружающую среду 1 +2 = 3 +4 или 1 – 3= 4 – 2
Где сw теплоёмкость кубового остатка при его средней температуре txwc Джкг К
cx = aw ·ca·ca+ (1 – aw)·ca
ca = 3352 при txwcp = 72
Тогда; сw = 001 · 3352 + (1 - 001) · 4190 = 4181
Принимаем температуру охлаждающей воды на входе в холодильник tвн = 11 на выходе tвк = 50 тогда Gв = = 306
Средняя разность температур в холодильнике при противоочной схеме движения теплоносителей
= = 137 2 то cp = = 4155
Коэффициент теплопередачи в холодильнике кубового остатка принимаем ориентировочно равным 500Втм2 ·К. Площадь поверхности теплообмена холодильника кубового остатка:
Принимаем двухходовой холодильник диаметром 400мм с числом труб 100шт (в одном ходе 50 шт)с длиной трубы 4000мм диаметр теплообменных труб 25 2мм. Площадь поверхности 31м2.
Кипятильник колонны расчёт толщины изоляции
Тепловой баланс кипятильника
С парами покидающими колонну
Где 11 коэффициент учитывающей потери теплоты в окружающую средуGp = - массовый расход дистиллята; энтальпия паров Джкг;
= + iсм =сp · txp cp=32904
rсм =19745659 txp = 7842 .
Gf = 361 txf = 8143 .
Сw = aw·caa + (1- aw)·cвC=3458
Cf = 033·4190 + (1 – 033)·3451 = 3698187
Расход греющего пара на обогрев куба колонны
Средняя разность температур в кипятильнике ректификационной колонны равна разности температур насыщенного пара и температуры кипения кубового остатка.
cp = 1329 – 981=348.
При ориентировочно принятом коэффициенте теплопередачи К = 2000 Втм2 ·К площадь поверхности теплообмена кипятильника колонны
Принимаем шестиходовой кожухотрубчатый испаритель диаметром 1200 мм с числом теплообменных труб 958шт диаметром труб 25 2мм с длинной труб 4000мм. Площадь поверхности 3010 м2. Расположение аппарата-вертикальное.
Обозначения аппарата:
Испаритель гр. Б.ГОСТ 15122 – 79.
Кипятильник ректификационной колонны обогревается греющим паром давлением 3ата температура которого 1329.По санитарным нормам температура поверхности аппарата не должна превышать 40°С (с целью уменьшения потерь теплоты в окружающую среду и предотвращения ожогов при соприкосновение с поверхностью аппарата). Для уменьшения потерь теплоты в окружающую среду и снижения температуры поверхности стенки необходимо на наружную поверхность аппарата нанести слоя изоляции.
Толщину тепловой изоляции u находят из равенства удельных тепловых потоков через слой изоляции и от поверхности изоляции в окружающую среду
αв·(tст2-tв)= tст1-tст2)
где αв=93+0058·tст2-коэффициент теплоотдачи от внешней поверхности материала в окружающую средуВтм2; tст2-температура изоляции со стороны окружающей среды(воздуха). Для аппаратов работающих в закрытых помещениях tcm2 выбирают в интервале 35-45 °С принимаем tcm2 = 40°С; tст1- температура изоляции со стороны аппарата ввиду незначительного термического сопротивления стенки аппарата по сравнению с термическим сопротивлением слоя изоляции tст1 принимаем равной температуре греющего пара tгп = 1329 °С; t -температура окружающего воздуха принимаем tв = 20°С; λн - коэффициент теплопроводности изоляции материала Втм · К.
В качестве материала для тепловой изоляции выберем совелит (85% магнезии+15% асбеста) имеющий коэффициент теплопроводности λн =009 Втм2- К. Тогда
αв =93 + 0058·40=116 Втм2·К
Принимаем толщину тепловой изоляции кипятильника ректификационной колонны 36 мм
1. Конструктивный расчёт ректификационной колонны
Технические требования на аппараты колонные стальные сварные определяются по ГОСТ 24305-80.
Под колонным аппаратом понимают вертикально стоящий аппарат с внутренним устройством для ректификации.
Ранее были определены диаметр и рабочая высота колонны; Д =12м Нр = 92м .
Общая высота колонны: Н = Нр + Нсе + Нкуб где Нр- высота рабочей части колонны м; Нсеп - высота сепарационной (верхней) части колонны м Hкуб — высота кубовой части колонны м.
Высота сепарационной и кубовой части для нормализованных колонн различных диаметров. Для Д = 1200 мм Нис =08м Нкуй = 2м. тогда общая высота колонны Н=92 + 28 = 12 м.
В зависимости от диаметра колонны её корпус изготовляется в царговом (на фланцах) или в цельносварном исполнении. Колонны диаметром до 1000 мм могут изготовляться из отдельных царг. Так как в настоящем проекте диаметр колонны 1200 мм то её корпус цельносварный.
В качестве конструкционного материала для изготовления корпуса колонны и внутренних устройств выберем сталь XI7.
В качестве внутренних устройств колонны для проведения ректификации использованы решётчатые провальные тарелки (заданы) типа TP.
Основным элементом тарелки является дырчатый лист со щелевыми отверстиями. По технической характеристике решётчатых тарелок типа TP выбираем t = 10 мм в = 4 мм толщина листа S = 2 мм свободное относительное сечение тарелок F0= 02 м2м2
Рис. 9. Вид перфорации решетчатой тарелки
Решётчатые тарелки отличаются от тарелок других типов простотой малой массой и небольшим гидравлическим сопротивлением. Тарелки данного типа имеют производительность в 15-2 раза большую чем колпачковые тарелки низкую металлоёмкость. Их эффективность достаточно высока но в узком диапазоне скоростей. Эти тарелки рекомендуется применять при больших нагрузках колонны по жидкости.
Тарелки выполняют цельными или разборными. В данном проекте выбирают решетчатые разборные тарелки по Н964-63 Гипронефтемаша. Крепление полос тарелки (четыре полосы) толщиной S = 2 мм осуществляем на приварном к обечайке кольце и профиле жёсткости болтами или струбцинами. Для увеличения жёсткости кольца используют кронштейны приваренные к корпусу колонны и кольцу
Рис. 10. Крепление тарелки в колоне: 1-корпус колоны; 2-болг;
-тарелка; 4-прокладка; 5-колоцо; 6-косынки
При установке тарелок в колонне обеспечивают повёрнутое на 90° положение щелей на каждой из двух смежных тарелок [35]. Горизонтальное расположение тарелок в колонне обеспечивается расположением кольца и необходимой затяжкой прокладки на кольце.
Минимальная толщина стенок корпуса аппарата зависит от диаметра аппарата и при Д = 2400 мм составляет = 12 мм.
На корпусе цельносварного тарельчатого аппарата предусматривают люки для монтажа и обслуживания тарелок. Люки располагают через каждые 5-10 тарелок. Устанавливаем 1 люк через 8 тарелок. Люки изготовляют по ОСТ 26-2000-77. Диаметр люка 600 мм. В месте установки люка расстояние между тарелками 800 мм. Число люков необходимых для установки на колонне для обслуживания тарелок п = 1шт. При этом
расстояние между тарелками вместо принятых в колонне 500 мм увеличится до 800 мм т.е. возрастёт на 300 мм а число увеличенных до 800 мм межтарелочных расстояний для установки люков равно 1. Общее увеличение высоты колонны за счёт увеличения расстояния между тарелками при установке люков 300 х 1 = 300 мм. Следовательно высота колонны станет равной: Н= 12 + 05 =123 м.
Расстояние между люками по высоте колонны 2800 мм.
В колонну подаётся питательная смесь и флегма. Для равномерного распределения подаваемой жидкости на тарелку и орошения последующих тарелок вместо верхней и питательной тарелки устанавливаем в колонне тарелки типа ТСН-3.
Выбираем люки с эллиптической фланцевой крышкой и шарнирным устройством типа II исполнения 2 с Дв = 600 мм Ру = 02 МПа. Люк 1I-A-03-600 ОН 26-01-65.
Основные размеры люка:
Дф = 720 мм; Дв = 600 мм; S = А мм; Дб = 680 мм; 5 = 6 мм; L = 530 мм; Z = 530 мм;
h = 260 мм; H диаметры болтов М 20 количество 20 шт; масса люка 87 кг.
Сверху и снизу колонна оборудуется приварными крышкой и днищем. Крышка и днище являются составными частями корпуса колонны органически связанными с ним и часто изготовляются из того же материала.
Рис. 11. Люк с эллиптической фланцевой крышкой
Днищем называют узел ограничивающий корпус снизу или сверху т.е. стандартное днище является и крышкой аппарата.
Наиболее широкое применение находят эллиптические днища штампованные из листового материала по ГОСТ 6533-68. Условное обозначение днища из стали марки09Г2С: "Днище 2400*12-80-09Г2С ГОСТ 6533-68".
Основные размеры днища: Дв = 2000 мм; he = 500 мм;
h == 80 мм; S = 6 мм. Таким образом высота днища равна he+h = 580 мм.
Для установки колонны на фундамент используют опору гипа1 размещаемую снизу аппарата и жёстко соединённую с корпусом колонны. Опора применяется при установке колонны на открытой площадке.
Подъём и перемещение колонны при монтаже и демонтаже осуществляется различными подъёмно-транспортными средствами цепями или траверсами.
Для обеспечения надёжности и безопасности строповки на колонне предусматриваются специальные устройства за которые аппарат подвешивается к подъёмно-транспортному устройству.
В процессе работы колонны необходимо контролировать давление и температуру производить контрольные отборы проб с каждой тарелки.
Штуцера для замера уровня давления и температуры выбирают по ГОСТ 26-61-1348-75-26-61-1356-75 «Устройства для установки приборов измерения температуры уровня и давления на сосудах и аппаратах».Отбор фракций с тарелок может осуществляться с помощью устройства показанного на рис.
Рис. 12. Вариант устройства для отбора фракций с тарелок
2. Расчёт диаметров штуцеров подбор фланцев и прокладок
Штуцером называется устройство служащее для подключения (присоединения) аппарата к трубопроводу.
Основными штуцерами являются штуцера для питательной смеси кубового остатка флегмы и пара. Рассчитаем диаметры патрубков этих штуцеров и подберём к ним стандартные фланцы.
Диаметры патрубков определим из уравнения расхода:
Gr=Gp·Rраб=·12=1572кгс;
Плотность исходной смеси:
где рэт= 7589 кгм3 рв=971 кгм3.При txF = 8143 °С.
Плотность флегмы (принимаем что флегма и дистиллят - чистый низкокипящий компонент): рэт=7927кгм3 при txр=7842 °С.
Плотность кубового остатка (принимаем что кубовый остаток - чистый высококипящий компонент рв= 9593кгм3 при txF =981 °С . Плотность паров поднимающихся из колонны ру = 0955 кгм3.
А диаметры штуцеров:
- для вывода пара из колонны
Для изготовления патрубка парового штуцера используем стандартную трубу (ГОСТ 941-81) стальную бесшовную горячекатаную диаметром 426х 11 мм (внутренний диаметр 426- 2*11 = 404мм) Ду = 400 мм.
- для входа питательной смеси в колонну
Для изготовления патрубка штуцера ввода исходной смеси используем трубу стальную бесшовную горячекатаную диаметром 89 х 45мм (внутренний диаметр 89- 2·45 = 80 мм) Ду = 80 мм.
Для изготовления штуцера ввода флегмы используем трубу стальную бесшовную горячекатаную диаметром 76 х4 мм (внутренний диаметр 76 - 2-4 = 68 мм) Д = 65 мм.
-для вывода кубового остатка
Для изготовления штуцера вывода кубового остатка используем трубу стальную бесшовную горячекатаную диаметром 89 х 45 мм (внутренний диаметр 89 - 9 = 80 мм) Ду =80 мм.
Для изготовления штуцеров выберем фланцы арматуры соединительных частей и трубопроводов (ГОСТ 1235-67 1255- 67 12821-67 12830-67) . Основные размеры фланцев:
-для штуцера выводы паров из колонны
-Ду = 400 мм; dн = 426 мм; Дф = 535 мм; Дв = 495 мм; Д1 = 465 мм; h = 24 мм
Болты М20 16 шт.177 кг.
-для штуцеров ввода питательной (исходной) смеси и вывода кубового остатка
Ду = 80 мм; dн = 89 мм; Дф = 185 мм; Дв = 150 мм; Д1 = 129 мм; h = 15 мм
- для штуцеров ввода флегмы
Ду = 65мм; dн = 76 мм; Дф = 160мм; Дв= 160 мм; Д1= 130 мм; h - 13 мм Болты MI2 4 шт.163 кг.
1. Гидравлический расчёт
Целью гидравлического расчёта является расчёт части технологической схемы процесса ректификации замкнутой на насос 1 перекачивающий исходную смесь из ёмкости 2 через подогреватель 3 на питательную тарелку ректификационной колонны 4.
При расчёте насосной установки выполним расчет диаметров трубопроводов гидравлических сопротивлений трубопроводов и подогревателя подбор насоса и проверку условий его работы на сеть.
2. Определение геометрических характеристик
трубопровода скоростей и режимов движения в них теплоносителей. Расчёт сопротивлений на различных участках трубопровода.
Так как температура исходной смеси на разных участках выбранной для расчёта схемы различная то для повышения точности выполнения расчёта разобьём трубопровод на участки:
-участок всасывающего трубопровода от ёмкости (сборника смеси) до насоса;
-участок напорного трубопровода от насоса до теплообменника;
-участок напорного трубопровода от теплообменника до ректификацконной колонны.
Диаметры всасывающего и напорного трубопровода определим из уравнения расхода
Диаметр напорного трубопровода (участки 2 и 4) примем разным диаметру штуцера для ввода питательной смеси в колонну 89 х 4.5 мм (внутренний диаметр трубы 80 мм).
Рис. 9 Схема насосной установки
Скорость смеси на участке напорного трубопровода
Скорость во всасывающем трубопроводе примем равной Fв = 06 тогда
Для изготовления всасывающего трубопровода примем трубу диаметром 108 х 4 мм (внутренний диаметр 108 – 2*4 = 100 мм) Скорость смеси на всасывающем участке трубопровода
В качестве подогревателя исходной смеси нами выбран вертикальный двух ходовой вертикальный теплообменник с диаметром 600мм с числом труб 240(в одном ходе 120)диаметром 25 × 2 с длиной труб 3000мм
Скорость движения смеси в трубах теплообменника
Для выполнения гидравлического расчёта примем следующие размеры: участков:
-hвс= 07 м - высота всасывания;
-Н=17м - максимальная высота подъёма от насоса.
Различают два вида потерь напора (сопротивлений) на различных участках трубопроводов: потери по длине h1 и потери в местных сопротивлениях hMC.
Потери по длине будем рассчитывать по формуле Дарси-
а потери в местных сопротивлениях - по формуле Вейсбаха
Всасывающий участок изображён на рис.10
Режим движения на всасывающем участке
Рв= 997 кгм3 рэт =839 кгм3 при t = 25°С.
Рис. 13. Схема всасывающего участка
lg25=xF·lga+(1-xF)·lgв=016·lg0902+(1-016)·lg177=02011
а=177м Па·св=0902м Па·с при = 25°С.
Режим движения жидкости - турбулентный. Принимая трубу гидравлически гладкой определим коэффициент трения λ формуле Блазиуса
Проверим трубу на шероховатость рассчитав толщину вязкого подслоя по формуле
Сопоставляя толщину вязкого подслоя с высотой элементов выбранной трубы делаем вывод о шероховатости трубы.
Эквивалентная шероховатость для стальных бесшовных труб (трубы новые и чистые) кэкв = 0015 мм.
Высота выступов элементов шероховатости в трубе
Так как Δ ( 25 · 10 -5 7.210-4 )? то шероховатость
стенок не влияет на величину коэффициента трения λ при турбулентном движении потока. На остальных участках трубопровода
будем считать трубу гидравлически гладкой тогда потери по длине трубопровода составят
На всасывающем участке трубопровода находятся четыре местных сопротивления:
Вход в трубу 1 = 05;
Поворот на 135° 2 = 05;
Резкий поворот на 90° (колено) 3 = 12 ;
Плавный поворот на 90° (отвод) 4= 014.
Hм.с. = (05 + 05 +12 + 014)·
Суммарные потери на всасывающем участке трубопровода
hвс=hl+hм.с.=00102+00012=0011м
Напорный участок от насоса до теплообменника Критерий Рейнольдса:
Режим движения турбулентный
Рис.14. Схема напорного участка трубопровода до теплообменника.
На напорном участке трубопровода перед теплообменником имеется одно сопротивление - плавный поворот на 90° - = 014 (диаметр штуцера теплообменника принимаем равным диаметру напорного трубопровода).
Суммарные потери напора на напорном участке трубопровода перед теплообменником:
hнап.1.=hl+hм.с.=0198+00057=02037м.
Теплообменник представлен на рис.
Средняя температура смеси в теплообменнике
При этой температуре
ра = 818.25 кгм3 рв = 986 кгм3
lg52=xF·lga+(1-xF)·lgв=016·lg0544+(1-016)·lg0916=-00743
а=0916м Па·св=0544 м Па·с.
Режим ламинарный (Re 2300) и
Определим потери напора в местных сопротивлениях теплообменника. Предварительно вычислим площадь поперечного сечения штуцера f1 ; распределительной коробки теплообменника f2 равной 12 общей площади поперечного сечения теплообменника; сечения 28 труб одного хода теплообменника f3.
Коэффициенты местных сопротивлений
а) при входе потока через штуцер в распределительную коробку (внезапное расширение)
б)при входе потока из распределительной коробки в первый ход (внезапное сужение)
в)при выходе потока из первого хода в распределительную коробку (внезапное расширение)
г) далее согласно схеме
Рис. 15 Схема коэффициентов местных сопротивлений в теплообменнике
д) при выходе потока через штуцер (внезапное сужение)
При переходе из одного хода в другой поток делает 4 поворота под углом 90° (пов-12 ) тогда
Суммарные потери напора в теплообменнике
hтеп=h1+hм.с.1+hм.с.2+hм.с.3=00288+00009+000071+000234=00327м.
Напорный участок трубопровода от теплообменника до ректификационной колонны .
Температура смеси после теплообменника txF=84 °С
Рэт = 970 кгм3 рв = 795 кгм3
lg8143=xF·lga+(1-xF)·lgв=016·lg0351+(1-016)·lg0566=-028
м8143= 0525·10-3 Па·с
а=0566·10-3 Па·св=0351·10-3 Па·с.
Режим движения турбулентный тогда
На напорном участке за теплообменником имеется два местных сопротивления - повороты (плавные) на 90°= 014
Суммарные потери напора на участке за теплообменником
Hнап2=h1+hм.с.=00002+0004=000422м.
Суммарные потери напора на всех участках трубопровода
Требуемый напор насоса определяется по формулеHтр=H+hвс+
где H+hвс -геометрическая высота подъёма жидкости м;
- высота обусловленная: разностью давлений в колонне и в ёмкости м; - суммарные потери напора в сети м.
Так как давление в колонне и в ёмкости атмосферное то высота обусловленная разностью этих давлений равна нулю. Тогда характеристика сети примет вид
Hтр =(Н+ hec) + = (17 + 07) + 02516= 1795 м . По рассчитанному напору Нтр = 1795 м и заданной подаче VF =000409м3с (1472 м3ч)подбираем насос. Для перекачки водно-спиртовых смесей используют специальные спиртовые насосы однако в связи с отсутствием в литературе характеристики этого насоса выбираем центробежный консольный химический насос Х5032125 К(ЕИТ) с горизонтальным валом на отдельной стойке с п = 2900 обмин
Проверка условий работы насоса на сеть
Для проверки условий работы выбранного насоса на сеть наложим на рабочие характеристики насоса характеристику сети.
Для построения характеристики сети рассмотрим характеристику (уравнение)трубопровода
где Н + hec=Нст - статический напор м.
Hст= 170 + 07= 177 м.
Так как трубопровод эксплуатируется при турбулентном режиме движения то потери напора пропорциональны квадрату скорости а следовательно и подачи
где в - коэффициент пропорциональности:
Задаваясь различными значениями подач (00; 20; 40; 60; 80; 101214 м3с) рассчитаем напор Нтр.
Результаты расчёта заносим в таблицу 3 и по ним строим характеристику сети Нтр =f(V).
Точка А пересечения характеристик насоса Н =f(V) и трубопровода (сети) Нтр =f(V) называется рабочей точкой насоса.
Координаты рабочей точки: Va =142 м ч Hа = 179 м а =
Так как подача соответствующая рабочей точке А меньше требуемой (1421472) то необходимо отрегулировать работу насоса на сеть. В данном случае увеличения подачи (перемещения характеристики насоса вверх) можно добиться увеличением частоты вращения вала насоса.
Статистический напор Нст м
Суммарные потери напора
Полный напор Нтр = Hст+BV2 м
В данной работе была спроектирована ректификационная установка непрерывного действия с решетчатыми тарелками для разделениябинарной смеси вода-этиловый спирт.
В ходе проектирования были выполнен технологический расчет а именно:
– материальный баланс решетчатой колонны;
– тепловой расчет колонны;
– конструктивный расчет аппарата.
В материальном балансе данной ректификационной установки был определенно минимальное и рабочее флегмовое число.
В тепловом расчете процесса ректификации выполняются с целью определения поверхностей теплообменников обслуживающих колонну расходов греющего водяного пара и охлаждающей воды.
В конструктивном расчете осуществлен подбор стандартных элементов: выбор днища и крышки подбор тарелок (в данном случае решетчатой) расчет штуцеров. А также определены основные габаритные размеры аппарата: диаметр колонны – 2400 мм высота цилиндрической части равна 18500 мм.
Курсовой проект включает
чертеж: технологическая схема установки;
чертеж : ректификационная колона
Касаткин А.Г. Основные процессы и аппараты химической технологии. Учеб. для студ. хим.-технол. спец. вузов. 9-е изд. исправл. М.: Химия 1973. - 750 с.
Лащинский А. А. Основы расчета и конструирования химической аппаратуры : справочник Лащинский А. А. Толчинсшй А. Р. под ред. Н. H. Логинова. 2 изд. перграб. и доп. Л.: Машиностроение 1970. — 753 с.
Лебедев П. Д. Теплоиспользующие установки промышленных предприятий. Курсовое проектирование : учебное пособие Лебедев П. Д. Щукин А. А. М.: Энергия 1970. -408 с.
Логинов А. В Выбор конструкции экономичного и целесообразного режима эксплуатации теплообменных аппаратов : учебное пособие А. В. Логинов ВТИ Воронеж 1991. - 80 с.
Логинов А.В. Процессы и аппараты химических и пищевых производств : пособие по проектированию А.В. Логиноп Н.М. Подгорнова И.Н. Болгова; Воронеж:. гос. технол. акад. Воронеж 2003. - 264с.
Логинов А.В. Насосы и насосные установки пищевых предприятий : учеб. пособие. А.В Логинов М.И. Слюсарев А.А. Смирных ; гос. технол. акад. Вороне» 2001. - 220с.
Логинов.. А.В Практикум по процессам и аппаратам химических и пищевых производств. Учеб. пособие А В. Логинов Л.Н. Ананьева Ю.В. Красовицкий Е.В. Энтин; гос. технол. акад. Воронеж 2003. - 336с.
Машины и аппараты химического производства. Примеры и задачи. Уч(:б. пособие И. В. Доманский В. П. Исаков Г. М. Островский и др. ; под общей ред. В. И. Соколова - Л.: Машиностроение 1982. - 384 с.
Схема+.cdw

Пар кубового остатка
Этан-этиленовая фракция
Пар этанола загрязненный
Пар этанола обогащенный
Кислота серная концентрированная
Раствор этилсульфатов
Кислота серная отработанная
Раствор гидроокиси натрия
Раствор этанола сырца
Колонна абсорбционная
Колонна нейтразилационная
Колонна ректификационная
Установка производства
этанола сернокислотной
гидратацией этилена.
Схема технологическая
Колонна 1.cdw

Выход кубового остатка
Техническая характеристиа
Аппарат предназначен для разделения смеси этанол-вода
концентрацией 33% (масс.).
Емкость номинальная 16 м
Производительность 3
Давление в колонне - атмосферное.
Температура среды в кубе - 85
Среда в аппарате - токсичная
Тип тарелок - решетчатая.
Технические требования
испытании и поставке аппарата должны выполня-
а) ГОСТ 12.2.003-74 "Оборудование производственное. Общие требо-
вания безопасности";
б) ОСТ 26.291-79 "Сосуды и аппараты стальные сварные. Техничес-
Материал деталей колонны
соприкасающихся с разделяемыми жид-
- сталь Х18Н10Т ГОСТ 5632-72
остальных - сталь Ст3
Аппарат испытать на прочность и плотность гидравлически в гори-
зонтальном положении давлением 0
в вертикальном положении-
Сварные соединения должны соответствовать требованиям
ОСТ 26-01-82-77 "Сварка в химическом машиностроении".
Сварные швы в объеме 100% контролировать рентгенопросвечиванием.
Действительное расположение штуцеров
Не указанный вылет штуцеров - 120 мм.
Размеры для справок.
ГОСТ 14806-80-Н2-п-3
Схема расположения штуцеров
Содержание.doc
2.Определение числа теоретических и действительных тарелок методом теоретических ступеней изменения концентраций ..5
3. Определение основных геометрических размеров колонны .10
4.Расчёт гидравлического сопротивления колонны 13
1. Тепловые расчёты 18
1. Конструктивный расчёт ректификационной колонны ..27
2. Расчёт диаметров штуцеров подбор фланцев и прокладок 32
1. Гидравлический расчёт ..34
2. Определение геометрических характеристик
трубопровода скоростей и режимов движения в них теплоносителей.
Расчёт сопротивлений на различных участках трубопровода .35
3. Описание технологической схемы 43
4. Подбор насоса .47
Рекомендуемые чертежи
- 04.04.2021
- 25.01.2023
- 17.03.2024
- 10.04.2022
- 15.04.2023
- 25.01.2023
- 25.01.2023