Технологический процесс механической обработки вала ведущего



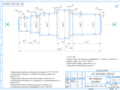
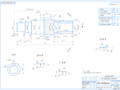
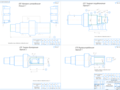
- Добавлен: 24.01.2023
- Размер: 3 MB
- Закачек: 2
Узнать, как скачать этот материал
Подписаться на ежедневные обновления каталога:
Описание
Технологический процесс механической обработки вала ведущего
Состав проекта
![]() |
![]() ![]() ![]() ![]() |
![]() ![]() ![]() |
![]() ![]() ![]() |
![]() ![]() ![]() ![]() |
![]() ![]() ![]() |
![]() ![]() ![]() |
![]() ![]() ![]() |
![]() ![]() ![]() |
![]() ![]() ![]() ![]() |
![]() ![]() ![]() |
![]() ![]() ![]() |
Дополнительная информация
Контент чертежей
заготовка.cdw

оп. эскизы.cdw

деталь.cdw

Рекомендуемые чертежи
- 24.01.2023
- 08.05.2023
- 26.05.2014
Свободное скачивание на сегодня
Обновление через: 9 часов 8 минут