Проектирование технологических процессов для сборки вала ведущего и механической обработки детали вал




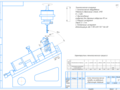
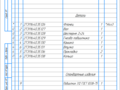
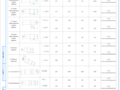
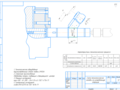
- Добавлен: 24.01.2023
- Размер: 3 MB
- Закачек: 0
Описание
Проектирование технологических процессов для сборки вала ведущего и механической обработки детали вал
Состав проекта
![]() |
![]() |
![]() ![]() ![]() ![]() |
![]() ![]() ![]() |
![]() ![]() ![]() ![]() |
![]() ![]() ![]() ![]() |
![]() ![]() ![]() ![]() |
![]() ![]() ![]() ![]() |
![]() ![]() ![]() ![]() |
![]() ![]() ![]() ![]() |
![]() ![]() ![]() |
![]() ![]() ![]() ![]() |
![]() ![]() ![]() ![]() |
![]() ![]() ![]() ![]() |
Дополнительная информация
сборка1!!!!.cdw

спецификация10.cdw

радиально-сверлильная.cdw

шпоночно-фрезерная.cdw

шлифовальная.cdw

размерный анализ.cdw

Вал стандарт.cdw

точность обработки.cdw

токарная гидрокопировальная.cdw

вал заготовка.cdw

Рекомендуемые чертежи
- 23.04.2016
- 22.05.2024
- 24.01.2023
- 24.01.2023