Проектирование технологического процесса механической обработки детали - Вал




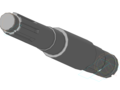
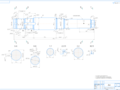
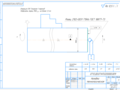
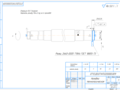
- Добавлен: 24.01.2023
- Размер: 895 KB
- Закачек: 0
Описание
Состав проекта
![]() |
![]() |
![]() ![]() ![]() ![]() |
![]() ![]() ![]() |
![]() |
![]() ![]() ![]() |
![]() ![]() ![]() |
![]() ![]() ![]() |
![]() |
![]() |
![]() |
![]() ![]() ![]() ![]() |
![]() |
![]() ![]() ![]() ![]() |
![]() |
Дополнительная информация
Наладка 2.cdw

Резец 2660-0005 Т15К6 ГОСТ 18855-73
12.ДО.07.КП.020000.009
Титульник.docx
Северо-Казахстанский государственный университет
Кафедра «Технология машиностроения»
ПОЯСНИТЕЛЬНАЯ ЗАПИСКА
по дисциплине «Технология производства машин»
на тему: «Проектирование технологического процесса механической обработки детали – «Вал»
(подпись дата) (подпись дата)
Петропавловск 2010 г.
ТП Вала новый.doc
12.ДО.07.КП.01.0000.009
Круг80 ГОСТ 2590-88 Сталь 40Х ГОСТ 4543-71
Код наименование операции
Обозначение документа
Код наименование оборудования
0 Токарная ИОТ №154 для токаря
Токарно-винторезный 16К40П 18217 3
А. Установить деталь закрепить снять.
Патрон 7100-0010 ГОСТ2675-80
Кулачки удлиненные цеховые
Подрезать торец чисто не более 13 мм.
Резец 2102-0031 ГОСТ 18877-73; Пластина 03111-150408 Т15К6 ГОСТ 19049-80
ГОСТ 3.1118-82 Форма 1 б
Поз. Наименование детали сб. единицы
Сверлить центровое отверстие.
Сверло центровое 2317-0106 Р6М5 ГОСТ 14952-85
5 Токарная ИОТ №154 для токаря
Подрезать торец чисто выдерживая размер 535-175
Штангенциркуль ШЦ-II-650-01 ГОСТ 166-89
Шаблон 3.8151-2479 ОСТ 3-2028-87
Центр 7032-0043 ГОСТ 13214-79
Точить диаметр 80 до диаметра 7704 на длине 133±05 мм
Резец 2103-0075 ГОСТ 18879-73; Пластина 03111-150408 Т15К6 ГОСТ 19049-80
Центр 7032-0043 Морзе 6 ГОСТ 13214-79
Точить диаметр 7704 до диаметра 7204 на длине 75±05 мм
Точить диаметр 7204 до диаметра 64 на длине 20 мм
Точить диаметр 7704 до диаметра 7084 на длине 58 мм
Штангенциркуль ШЦ-II-650-01 ГОСТ166-89
Точить диаметр 7204 до диаметра 6584 на длине 55 мм
Точить диаметр 80 до диаметра 7204 на длине 253 мм
Точить диаметр 7204 до диаметра 6704 на длине 202 мм
Точить диаметр 6704 до диаметра 48 на длине 25 мм
Точить диаметр 7204 до диаметра 6584 на длине 51±037 мм
Точить диаметр 6704 до диаметра 6084 на длине 178 мм
А. Установить закрепить в центрах снять
Центр А-1-5-Н ГОСТ 874275
Точить диаметр 6584 до диаметра 652 на длине 55 мм
Центра 7032-0043 Морзе 6 ГОСТ 13214-79
Точить диаметр 7084 до диаметра 702 на длине 58 мм
Точить диаметр 6584 до диаметра 652 на длине 51±037 мм
Точить диаметр 6084 до диаметра 602 на длине 178 мм
5 Фрезерная ИОТ №30 для фрезеровщика
Вертикально фрезерный 6Т12
А. Установить закрепить деталь снять.
Фрезеровать паз В=16 выдержать размеры чертежа
Фреза В=16 2234-0375 H9 Р6М5 ГОСТ 9140-78
Штангенциркуль 0-125 ГОСТ 166-89
Калибр 8154-0081-Н9 ГОСТ 24121-88
Штангенглубиномер 0-160 ГОСТ 162-80
Шлифовать диаметр 65k6 выд. требования чертежа
Круг шлифовальный ПВД 24А40НСМ25К8 35 мс 1 кл. А.
Микрометр МК 75-1 ГОСТ6507-78
Скоба рычажная СР75 ГОСТ 11098-75
Шлифовать диаметр 70u7 выд. требования чертежа
0 Контрольная ИОТ №116 для контролера
Стол ОТК 12 Асб 193 СТПАГБ 34-70 12939 3
Проверить деталь внешним осмотром на отсутствие заусенцев острых кромок и механических повреждений
ф65k6 (2 диаметра) ф70u7 ф60f7 М64×2-6g М48×15-6g 20±026; 75±037; 133±05; 149-04; 51±037
Скоба рычажная СР75 ГОСТ11098-75
Кольца Пр8211-0154-6g; Не8211-1154-6g
Кольца Пр8211-0192-6g; Не8211-1192-6g
Штангенциркуль ШЦ-II-125-01 ГОСТ166-89
Штангенциркуль ШЦ-II-250-005 ГОСТ166-89
Проверить шероховатость поверхностей
Образцы шероховатости ГОСТ 9378-75
Допуск радиального биения поверхностей ф65k6 ф70u7 относительно оси обеспечивается технологически
Клеймить клеймом ОТК в сопроводительной документации
Титульник ТП.doc
на маршрутный технологический процесс механической обработки детали «Вал»
Курсач ТПМ.docx
АНАЛИЗ ТЕХНОЛОГИЧНОСТИ КОНСТРУКЦИИ ДЕТАЛИ
ВЫБОР СПОСОБА ПОЛУЧЕНИЯ ЗАГОТОВКИ И ОПРЕДЕЛЕНИЕ
РАЗРАБОТКА МАРШРУТНОЙ ТЕХНОЛОГИИ ЗАДАННОЙ
ВЫБОР ОБОРУДОВАНИЯ ТЕХНОЛОГИЧЕСКОЙ ОСНАСТКИ СТАНОЧНЫХ ПРИСПОСОБЛЕНИЙ И СРЕДСТВ ИЗМЕРЕНИЯ
НАЗНАЧЕНИЕ И РАСЧЕТ РЕЖИМОВ ОБРАБОТКИ
РАСЧЕТ ТЕХНИЧЕСКИХ НОРМ ВРЕМЕНИ
СПИСОК ИСПОЛЬЗОВАННОЙ ЛИТЕРАТУРЫ
ПРИЛОЖЕНИЕ А (обязательное)
Совокупность методов и приемов изготовления машин выработанных в течение длительного времени и используемых в определенной области. Поэтому возникают такие понятия: технология обработки давлением литья сварки сборки машин. Все эти области производства относятся к технологии машиностроения охватывающей все этапы процесса изготовления машинной продукции.
Однако под “технологией машиностроения” принято понимать научную дисциплину изучающую процессы металлической обработки деталей и сборки машин и попутно затрачивающую вопросы выбора заготовки и методы их изготовления. В процессе технической обработки деталей машин возникает большое количество простейших вопросов связанных с необходимостью выполнения технических требований поставленными конструкторами перед изготовителями.
Эти обстоятельства объясняет развитие “технологии машиностроения“ как научной дисциплиной в первую очередь в направлении изучения вопросов технологии металлической обработки и сборки в наибольшей мере влияющие на производственную деятельность предприятия.
В данной курсовой работе подробно изложена технология изготовления вала с подборкой оборудования режущего инструмента. Учтены нормы времени на обработку.
Деталь «Вал» служит для передачи крутящего момента от коробки отбора мощности к лебедке подъемной установки.
Данный вал расположен в коническом редукторе привода лебедки подъемной установки АПРС-40.
Деталь относится к классу деталей типа «тела вращения» т.к. отношение длины детали к ее наружному диаметру превышает 2 и составляет:
Деталь выполняется из конструкционной легированной стали 40Х ГОСТ 4543-71.
Химический состав приведен в таблице 1 а физико-механические свойства в таблице 2.
Химический состав стали 40Х ГОСТ 4543-71
Содержание элементов %
Механические свойства стали 40Х ГОСТ 4543-71 при Т=20
Относительное удлинение %
Сталь является многокомпонентным сплавом [1] содержащим углерод и ряд постоянных или неизбежных примесей: Mn Si S Р О N Н и др. которые оказывают влияние на ее свойства. Присутствие этих примесей объясняется трудностью удаления части из них при выплавке (Р S) переходом их в сталь в процессе ее раскисления (Mn Si) или из шихты - легированною
металлического лома (Cr Ni и др.). Эти же примеси но в больших количествах присутствуют и в чугунах.
Влияние углерода. Структура стали после медленного охлаждения состоит из двух фаз - феррита и цементита.
Твердые и хрупкие частицы цементита повышают сопротивление
движению дислокаций т. е. повышают сопротивление деформации
и кроме того они уменьшают пластичность и вязкость. Вследствие этого с увеличением в стали углерода возрастают твердость пределы прочности и текучести и уменьшаются относительное удлинение относительное сужение и ударная вязкость.
Влияние кремния и марганца. Содержание кремния в углеродистой стали в качестве примеси обычно не превышает 035—04% а марганца 05-08%. Кремний и марганец переходят в сталь в процессе ее раскисления при выплавке. Они раскисляют сталь т. е. соединяясь с кислородом закиси железа FeO в виде окислов переходят в шлак. Эти процессы раскисления улучшают свойства стали. Кремний дегазируя металл повышает плотность
Кремний остающийся после раскисления в твердом растворе (в феррите) сильно повышает предел текучести. Это снижает способность стали к вытяжке и особенно холодной высадке.
Марганец заметно повышает прочность практически не снижая пластичности и резко уменьшая красноломкость стали т. е. хрупкость при высоких температурах вызванную влиянием серы.
Влияние серы. Сера является вредной примесью в стали. С железом она образует химическое соединение FeS которое практически нерастворимо в нем в твердом состоянии но растворимо в жидком металле. Соединение FeS образует с железом легкоплавкую эвтектику с температурой плавления 988°С. Эта эвтектика образуется даже при очень малых содержаниях
серы. Кристаллизуясь из жидкости по окончании затвердевания эвтектика преимущественно располагается по границам зерна. При нагревании стали до температуры прокатки или ковки (1000 - 1200°С) эвтектика расплавляется нарушается связь между зернами металла вследствие чего при деформации стали в местах расположения эвтектики возникают надрывы и трещины. Это явление носит название красноломкости.
Присутствие в стали марганца обладающего большим сродством к сере чем железо и образующею с серой тугоплавкое соединение MnS практически исключает явление красноломкости. В затвердевшей стали частицы MnS располагаются в виде отдельных включений. В деформированной стали эти включения деформируются и оказываются вытянутыми в направлении прокатки.
Сернистые включения сильно снижают механические свойства особенно ударную вязкость и пластичность в поперечном направлении вытяжки при прокатке и ковке а также предел выносливости. Кроме того эти включения ухудшают свариваемость и коррозионную стойкость.
Влияние фосфора. Фосфор является вредной примесью и содержание его в зависимости от качества стали допускается не более 0025 — 0045%. Растворяясь в феррите фосфор сильно искажает кристаллическую решетку и увеличивает пределы прочности и текучести но уменьшает пластичность и вязкость. Снижение вязкости тем значительнее чем больше в стали углерода. Фосфор значительно повышает порог хладноломкости стали и уменьшает работу развития трещины.
Вредное влияние фосфора усугубляется тем что он обладает большой склонностью к ликвации. Вследствие этого в серединных слоях слитка отдельные участки сильно обогащаются фосфором и имеют резко пониженную вязкость.
Технологичность конструкции – это соответствие детали изделия заданным условиям производства которые обеспечивают изготовление данной детали или изделия с данной трудоемкостью и себестоимостью их изготовления.
Существует два вида показателей технологичности: качественные и количественные [2]. Качественная оценка при сравнении вариантов конструкций в процессе изделия предшествует количественной и определяет целесообразность затрат на определение численных показателей технологичности вариантов. Количественная оценка технологичности конструкции изделия выражается показателем численное значение которого характеризует степень удовлетворения требований к технологичности конструкции.
Оценка конструкции детали на технологичность:
Данный вал не является жестким т.к. .
Деталь состоит из стандартных и унифицированных конструктивных элементов: диаметральных и линейных размеров. Это способствует использованию стандартных режущих и измерительных инструментов.
Деталь имеет точность и шероховатость которые можно получить стандартным унифицированным инструментом при стандартном технологическом процессе.
Материал заготовки отвечает требованиям технологии изготовления: при изготовлении нет необходимости применять сложные технологические процессы изготовления детали; для хранения материала нет необходимости создавать определенные условия хранения и транспортировки.
Шероховатость базовых поверхностей удовлетворяет требованиям точности установки детали ее обработки и контроля.
Деталь симметрична относительно своей оси.
На детали имеются канавки для свободного выхода режущего инструмента и фаски причем все эти элементы являются унифицированными что способствует повышению технологичности конструкции детали.
Все обрабатываемые поверхности имеют свободный подвод и отвод режущего инструмента за исключением шпоночного паза который является закрытым. Для его обработки можно использовать только концевую фрезу.
Все шероховатости обозначенные на чертеже соответствуют данным квалитетам точности а это также является одним из условий технологичности.
Коэффициент точности обработки [2]:
где – средний квалитет точности размеров;
где – число размеров заданного квалитета;
Коэффициент точности обработки детали следовательно деталь считается технологичной.
Коэффициент шероховатости поверхности детали [2]:
где – средняя шероховатость поверхности детали;
где – число основных поверхностей детали соответствующей шероховатости;
Коэффициент шероховатости поверхности детали следовательно деталь считается технологичной.
ВЫБОР СПОСОБА ПОЛУЧЕНИЯ ЗАГОТОВКИ И ОПРЕДЕЛЕНИЕ ТИПА ПРОИЗВОДСТВА
Для получения необходимой детали выбрали заготовку “прокат” (сортамент горячее катанный) сталь 40Х диаметром 80 мм и длиной 538 мм. Выбор именно такой заготовки связан с тем что необходимая нам деталь имеет наибольшую ступень 80 мм и она не обрабатывается ни на одной из операций.
Заготовка получена путем проката на прокатном стане и имеет в сечении форму круга. Необходимая нам деталь так же имеет форму круга в сечении а соответственно более удобна для обработки с экономической и технологической точки зрения.
Заданная годовая программа выпуска деталей составляет .
Годовая программа запуска деталей в производство рассчитывается по следующей формуле [2]:
где – коэффициент характеризующий технологический брак (45% от годовой программы выпуска);
– коэффициент незавершенного производства (23% от годовой программы выпуска);
Расчетный такт производства [2]:
где – расчетный фонд работы в часах при двухсменном режиме работы (принимаем );
Действительный такт производства [2]:
где – коэффициент загрузки оборудования ()
Тип производства определяется по таблице 19 (с. 56) [2]. По таблице данной годовой программе выпуска и массе детали соответствует крупносерийный тип производства.
Данный тип производства имеет следующие характеристики:
большая годовая программа выпуска изделий;
узкая номенклатура выпускаемых изделий;
заготовки имеют как можно меньшие припуски на обработку;
для механической обработки используется специальный инструмент;
невысокая квалификация рабочих (2-3 разряд);
закрепляемость операций (2 10 операций на одном рабочем месте);
трудоемкость изготовления деталей мала а т.к. трудоемкость является одной из составляющих себестоимости продукции то себестоимость также мала;
применение специального оборудования и инструмента снижает гибкость производства до минимума.
РАЗРАБОТКА МАРШРУТНОЙ ТЕХНОЛОГИИ ЗАДАННОЙ ДЕТАЛИ
Разрабатываемый технологический процесс должен быть прогрессивным обеспечивать повышение производительности труда и качества деталей сокращение трудовых и материальных затрат на его реализацию уменьшение вредных воздействий на окружающую среду [3].
Базовой исходной информацией для проектирования технологического процесса служат: рабочие чертежи деталей технические требования регламентирующие точность параметр шероховатости поверхности и другие требования качества; объем годового выпуска изделий определяющий возможность организации поточного производства.
Операция 005 – Заготовительная. Заготовка получена путем проката на прокатном стане и имеет в сечении форму круга. Необходимая нам деталь так же имеет форму круга в сечении а соответственно более удобна для обработки с экономической и технологической точки зрения.
Операция 010 – Токарная. Данная операция выполняется на токарно-винторезном станке 16К40П. На данной операции за два перехода обрабатывается торец и сверлится центровое отверстие при этом деталь закрепляется в трехкулачковом патроне.
Для первого перехода используется токарный проходной отогнутый правый резец. Марка материала режущей кромки – твердый сплав Т15К6 т.к. данная марка материала наиболее подходит для подрезания торцов [4].
Для второго перехода (сверление отверстия) используется комбинированные центровочное сверло. Марка режущей кромки – твердый сплав Т5К10. Комбинированные сверла являются весьма производительным инструментом т.к. они одновременно сверлят отверстие с обработкой фаски. Центровые отверстия позволяют обеспечить принцип постоянства баз для следующих операций.
Операция 015 - Токарная. Данная операция выполняется на токарно-винторезном станке 16К40П. На данной операции за два перехода обрабатывается второй торец и сверлится центровое отверстие при этом деталь закрепляется в трехкулачковом патроне.
Операция 020 – Токарная. Данная операция выполняется на токарно-винторезном станке 16К40П. На данной операции деталь зажимается в трехкулачковом и обрабатываются диаметры .
Для обработки используются токарный проходной правый резец. Марка материала режущей кромки – Т15К6.
Операция 025 – Токарная. Данная операция выполняется на токарно-винторезном станке 16К40П. На данной операции деталь зажимается в трехкулачковом патроне и обрабатываются диаметры .
Операция 030 - Токарная. Данная операция выполняется на токарно-винторезном станке 16К40П. На данной операции деталь зажимается в центрах и обрабатываются на чисто диаметры .
Операция 035 – Фрезерная. Данная операция выполняется на вертикально-фрезерном станке 6Т12. Деталь зажимается в призме и обрабатывается шпоночный паз шириной 16 мм глубиной 6 мм и длиной 78 мм.
Для обработки используется концевая фреза диаметром 16 мм. Марка режущей кромки - Р6М5.
Операция 040 – Шлицефрезерная. Данная операция выполняется на шлицефрезерном станке модели 5350. Деталь зажимается в центрах на поверхности диаметром 60 мм фрезеруют шлицы.
Для данной обработки используется червячная шлицевая фреза без усиков диаметром 100 мм. Марка режущей кромки Р6М5.
Операция 045 – Токарная. Данная операция выполняется на токарно-винторезном станке 16К40П. На данной операции за 6 проходов нарезается резьба . Деталь закрепляется в центрах.
Для обработки используются резьбовые резцы для метрической резьбы. Марка материала режущей кромки – твердый сплав Т15К6 т.к. данная марка материала наиболее подходит для нарезания резьбы на детали из Сталь40Х.
Операция 050 – Токарная. Данная операция выполняется на токарно-винторезном станке 16К40П. На данной операции за 4 проходов нарезается резьба . Деталь закрепляется в центрах.
Операция 055 - Термическая. Нормализация – вид термической обработки который заключается в нагреве стали до температур на 30 – 50ºC выше линии GSE выдержке при этой температуре и последующем охлаждении на спокойном воздухе. Нормализация применяется как промежуточная операция для смягчения стали перед обработкой резанием для устранения пороков строения и общего улучшения структуры перед закалкой.
Операция 060 – Круглошлифовальная. Данная операция выполняется на круглошлифовальном станке 3М131. Установка детали осуществляется на рифленые центра. Данная операция осуществляется за установ. На данной операции обрабатываются поверхности диаметром 65 70 мм к которым предъявляются требования к обеспечению низкой шероховатости и высокого квалитета точности. В качестве инструмента используется абразивный круг плоский с двусторонней выточкой на керамической связке с зернистостью 40. Марка круга: ПВД 24А40НСМ25К8 35 мс 1кл. А.
Операция 065 – Круглошлифовальная. Данная операция выполняется на круглошлифовальном станке 3М131. Установка детали осуществляется на рифленые центра. Данная операция осуществляется за установ. На данной операции обрабатываются поверхности диаметром 65 60 мм к которым предъявляются требования к обеспечению низкой шероховатости и высокого квалитета точности. В качестве инструмента используется абразивный круг плоский с двусторонней выточкой на керамической связке с зернистостью 40. Марка круга: ПВД 24А40НСМ25К8 35 мс 1кл. А.
Операция 070 – Моечная. Производится промывка деталей на моечных машинах.
Операция 075 – Контроль. Данная операция необходима для контроля полученных размеров. Инструмент применяемый при измерении размеров зависит от точности измерения (количества знаков после запятой). После измерения всех размеров следует сравнить их с допусками на размер. Если контролируемые параметры вписываются в допуск то можно производить дальнейшую обработку детали. Если же нет то имеет место брак. После обнаружения брака следует установить характер брака: исправимый или не исправимый. Если брак является исправимым то следует его исправить после чего продолжать дальнейшую обработку детали. Если же брак неисправимый то деталь отправляют на переплав. Данная операция проводится после всей механической обработки. После финишных операций для контроля размеров цилиндрических поверхностей следует использовать
калибры рычажные измерительные скобы. Для контроля шероховатости используем эталоны шероховатости.
Рассчитаем припуск на поверхность диаметром [5].
Данная поверхность до окончательного размера проходит через следующий ряд операций:
Токарная (черновая);
Токарная (чистовая);
Отклонение расположения поверхностей заготовки при обработке в центрах рассчитываем по формуле:
где - общее отклонение оси от прямой
- смещение оси в результате погрешности центров.
где - удельная кривизна сортамента ;
– длина обрабатываемой детали.
где T – допуск на заготовку. Т. к. заготовкой является сортамент T=087 мм.
Величина остаточных пространственных отклонений определяется по формуле:
где - пространственные отклонения полученные на предшествующем переходе
- коэффициент уточнения для черновой обработки
для чистовой обработки
Остаточные пространственные отклонения для черновой обработки:
Остаточные пространственные отклонения для чистовой обработки:
Минимальные припуски на диаметральные размеры для каждого перехода рассчитывается по формуле:
где – высота неровностей поверхности;
h – глубина дефектного слоя;
- суммарные отклонения расположения поверхности.
а) черновое точение:
б) чистовое точение:
в) шлифование однократное:
Расчет наименьших размеров по технологическим переходам начинаем с наименьшего (наибольшего) размера детали по конструкторскому чертежу и производим по зависимости:
а) чистовое точение:
б) черновое точение:
Расчет наибольших размеров по технологическим переходам производим по зависимости:
а) шлифование однократное:
в) черновое точение:
Фактические максимальные припуски по переходам:
Фактические минимальные припуски по переходам:
Определяем общие припуски:
Правильность выполненных расчетов можно проверить по формуле:
Рассчитанные припуски заносим в таблицу 4.
Припуски на обработку диаметра
Расчетный припуск минимальный
Допуск на промежуточные размеры мкм
Принятые размеры заготовки по переходам мм
Предельный припуск мкм
Т.к. и еще одна ступень при расчете припусков находятся в том же интервале размеров и к ним применяются те же операции что и для рассчитанного диаметра то на них можно принять припуски такие же как и для рассчитанной ступени .
Следовательно припуски по переходам равны:
а) на черновое точение:
б) на чистовое точение:
в) на шлифование однократное:
Припуски для подрезания торцов выбираются из табл. 7.28 (с. 178) [5] и равны 13 мм.
Выбор оборудования осуществляется в зависимости от типа производства.
Технологическое оборудование для обработки детали «вал»:
токарно-винторезный станок повышенной точности 16К40П;
круглошлифовальный станок 3М131;
Вертикально-фрезерный станок 6Т12;
Шлицефрезерный станок 5350.
Данное оборудование было выбрано на основе исходных данных о заготовке и типе производства. Так же данные станки удовлетворяют рассчитанным режимам резания при обработке данной детали.
Технологическая оснастка включает в себя приспособления установочно-зажимные режущие инструменты вспомогательные и мерительные инструменты [3].
В разработанном технологическом процессе основная номенклатура вспомогательного режущего и измерительного инструмента – стандартный инструмент:
Резец 2102-0031 Т15К6 ГОСТ 18877-73;
Резец 2103-0026 Т15К6 ГОСТ 18879-73;
Резец 2103-0075 Т15К6 ГОСТ 18879-73;
Резец 2660-0005 Т15К6 ГОСТ 18885-73;
Резец канавочный АГБ2126-4048;
Фреза 2234-0375 ГОСТ9140-78;
Фреза 2520-0754 ГОСТ8027-86;
Сверло 2317-0008 ГОСТ 14452-75;
Напильник 2820-0018 ГОСТ1465-80;
Надфиль 2827-0088 ГОСТ1513-77;
Щетка металлическая.
Станочные приспособления являются одними из основных элементов оснащения металлообрабатывающего производства позволяющих эффективно использовать в производственном процессе станки общего назначения. Применение приспособлений дает возможность специализировать и настраивать станки на заданные процессы обработки обеспечивающие выполнение технологических требований и экономически рентабельную производительность. Степень оснащенности станков приспособлениями и их выбор в каждом случае решаются условиями и программой производства.
Станочные приспособления:
Патрон 3-х кулачковый ГОСТ 2675-80;
Хомутик 7107-0069 ГОСТ16488-70.
Универсальные средства измерения предназначены для определения действительных размеров. Этим они и отличаются от калибров позволяющих убедиться лишь в том что размер лежит в заданных пределах. Любое универсальное измерительное средство характеризуется назначением принципом действия т.е. физическим принципом положенным в основу его построения особенностями конструкции и метрологическими характеристиками.
Выбор средств измерения и контроля основывается на обеспечении заданных показателей процесса технического контроля и анализе затрат на реализацию процесса контроля. К обязательным показателям процесса контроля относят точность измерения достоверность трудоемкость стоимость контроля. В качестве дополнительных показателей контроля используют объем полноту периодичность продолжительность.
При выборе средств измерения точность средств измерений должна быть достаточно высокой по сравнению с заданной точностью выполнения измеряемого размера а трудоемкость измерения и их стоимость должны быть возможно более низкими обеспечивающими наиболее высокие производительность труда и экономичность.
Образцы шероховатости ГОСТ 9378-75;
Скоба рычажная СР75 ГОСТ11098-75;
Калибр 8154-0081-H9 МН2990-61;
Калибр 8154-0226-4 ГОСТ64121-80;
Кольца ПР 8211-0192-6g НЕ 8211-1192-6g;
Кольца ПР 8211-0154-6g НЕ 8211-1154-6g;
Скоба 8316-0492d9 ГОСТ24966-81 (10f9);
Скоба 8316-0492h6 ГОСТ24964-81 ();
Калибр-кольцо 8312-0267-7 ГОСТ24960-80;
Радиусный шаблон №2 ТУ 2-034-228;
Калибр-пробка 8133-1029 Н14 ГОСТ 14811-69;
Микрометр МК 75-1 ГОСТ 6507;
Штангенциркуль II -125-01 ГОСТ 166-89;
Штангенциркуль II -250-005 ГОСТ 166-89.
Выбор инструмента производился с использованием соответствующей нормативно технической документации и приведен при написании комплекта документов на механическую обработку детали.
Уровень режима резания находится в зависимости от типа и конструкции инструмента материала и геометрии его режущей части качества заточки правильности установки и закрепления инструмента на станке состояния системы СПИД и определяет силы резания и расходуемую при резании мощность [6].
При назначении и расчете режима резания учитывают тип и размеры инструмента материал его режущей части материал и состояние заготовки тип оборудования и его состояния. При этом следует помнить что элементы режима резания находятся во взаимной функциональной зависимости устанавливаемой эмпирическими формулами что глубина резания и подача непосредственно влияют на стойкость инструмента с которой в свою очередь связана скорость резания.
Для назначения режим резания используем [4].
Назначаем режимы резания для подрезания торца.
I. Выбираем резец и устанавливаем его геометрические элементы. Тип резца – токарный проходной резец отогнутый правый. Материал рабочей части – пластины – твердый сплав Т15К6.
Принимаем размеры поперечного сечения корпуса резца ; длина резца 150 мм.
Из-за отсутствия рекомендаций по выбору геометрических элементов резца в используемом справочнике принимаем их по справочнику [7]: форма передней поверхности – плоская с фаской типа IIб (табл. 29 с. 187);; ; ; (табл. 30 с. 188); ; (табл. 31 с. 190); (табл. 32 с. 190 и табл. 4 примеч. 3 с. 420).
II. Назначаем режим резания.
Устанавливаем глубину резания. При снятии припуска на один проход .
Назначаем подачу (по табл. 14 с. 268). В таблице приведено значение . Корректируем значение по станку .
Назначаем период стойкости резца (с. 268).
Определяем скорость главного движения резания допускаемую режущими свойствами резца (с. 265) по формуле (7.1):
По таблице 17 (с.270) находим значения коэффициента и показателей степеней формулы. Для наружного точения твердого сплава Т15К6 и .
Учитываем поправочные коэффициенты на скорость резания.
- общий поправочный коэффициент равный произведению поправочных коэффициентов учитывающих измененные условия обработки.
Определяем значения этих коэффициентов:
– поправочный коэффициент учитывающий изменение механических свойств обрабатываемого материала (табл. 9 с. 424) по формуле (7.2):
где - предел текучести.
Исходя из марки материала [6]
- поправочный коэффициент учитывающий состояние поверхности заготовки (табл. 5 с. 263) так как заготовка – прокат.
- поправочный коэффициент учитывающий изменение материала рабочей части инструмента (табл. 6 с. 363) так как принят твердый сплав Т15К6.
- поправочный коэффициент учитывающий изменение главного угла в плане (табл. 16 с. 427) так как .
- поправочный коэффициент учитывающий вид обработки (табл. 17 с. 427) так как осуществляется наружное продольное точение.
Определяем общий поправочный коэффициент на скорость главного движения резания по формуле (7.3):
Подставив все найденные величины в формулу (7.1) получим:
Определяем частоту вращения шпинделя соответствующую найденной скорости:
Корректируем частоту вращения шпинделя по паспортным данным станка мод. 16К40П и устанавливаем действительное значение частоты вращения: [6].
Определяем действительную скорость главного движения резания:
Определяем главную составляющую силы резания по формуле (7.6):
По таблице 22 (с. 274) находим значения коэффициента и показателей степеней формулы. Для наружного продольного точения твердосплавным резцом конструкционной стали : .
Учитываем поправочные коэффициенты на силу резания.
– поправочный коэффициент учитывающий изменение механических свойств обрабатываемого материала (табл. 9 с. 264) по формуле (7.7):
где - предел текучести стали
- показатель степени.
Показатель степени определяем по табл. 22 с. 430. Для обработки конструкционной стали твердосплавным резцом . Тогда по формуле (7.7):
- поправочный коэффициент учитывающий изменение переднего угла (табл. 23 с. 275) так как .
- поправочный коэффициент учитывающий изменение угла наклона главной режущей кромки (табл. 23 с. 275) так как .
- поправочный коэффициент учитывающий изменение главного угла в плане (табл. 23 с. 275) .
Определяем общий поправочный коэффициент на силу резания по
Подставив все найденные величины в формулу (7.6) получим:
Определяем мощность затрачиваемую на резание по формуле (7.9):
Проверяем достаточна ли мощность привода станка. Необходимо проверить выполнение условия:
Мощность (кВт) на шпинделе станка по приводу по формуле (7.11):
В паспортных данных станка 16К40П находим:
Следовательно т.е. обработка возможна.
III. Определяем основное время (мин) по формуле (7.12):
В решении были определены следующие параметры формулы: число проходов частота вращения шпинделя станка подача резца .
Определяем длину рабочего хода резца по формуле (7.13):
Врезание резца определяем по формуле (7.14):
Перебег резца ; принимаем .
Режимы резания для обработки диаметра .
Обработка состоит из чернового чистового точения и однократного шлифования.
Назначаем режимы резания для чернового точения .
I. Выбираем резец и устанавливаем его геометрические элементы.
Тип резца – токарный проходной прямой правый. Материал рабочей части – пластины – твердый сплав Т15К6.
Геометрические элементы резца: форма передней поверхности – радиусная с упрочняющей фаской ширина радиусной лунки радиус лунки (табл. 29 с. 187); передний угол; передний угол на упрочняющей фаске ; главный задний угол ; угол наклона главной режущей кромки (табл. 30 с. 188); главный угол в плане ; вспомогательный угол в плане (табл. 31 с. 190); радиус вершины (табл. 32 с. 190 и табл. 4 примеч. 3 с. 420).
Определяем глубину резания. Припуск на обработку снимаем за один проход т. е. принимаем . Тогда по формуле (7.15):
Назначаем подачу (по табл. 2 с. 418). В таблице приведено значение . Принимаем значение .
Назначаем период стойкости резца (с. 415).
Определяем скорость главного движения резания допускаемую режущими свойствами резца (с. 415) по формуле (7.1).
По таблице 8 (с.422) находим значения коэффициента и показателей степеней формулы. Для наружного точения твердого сплава Т15К6 и .
- общий поправочный коэффициент равный произведению поправочных коэффициентов учитывающих измененные условия обработки.
– поправочный коэффициент учитывающий изменение механических свойств обрабатываемого материала (табл. 9 с. 424). определяется по формуле (7.2):
- поправочный коэффициент учитывающий состояние поверхности заготовки (табл. 14 с. 426) так как заготовка – прокат.
- поправочный коэффициент учитывающий изменение материала рабочей части инструмента (табл. 15 с. 426) так как принят твердый сплав Т15К6.
Определяем частоту вращения шпинделя соответствующую найденной скорости по формуле (7.4):
Определяем действительную скорость главного движения резания по формуле (7.5):
Определяем главную составляющую силы резания по формуле (7.6).
По таблице 20 (с.429) находим значения коэффициента и показателей степеней формулы. Для наружного продольного точения твердосплавным резцом конструкционной стали : .
- общий поправочный коэффициент равный произведению поправочных коэффициентов учитывающих измененные условия обработки. Определяем значения этих коэффициентов: – поправочный коэффициент учитывающий изменение механических свойств обрабатываемого материала (табл. 21 с. 430). определяется по формуле (7.7).
Показатель степени определяем по табл. 22 с. 430. Для обработки конструкционной стали твердосплавным резцом . Тогда
- поправочный коэффициент учитывающий изменение переднего угла (табл. 24 с. 431) так как .
- поправочный коэффициент учитывающий изменение угла наклона главной режущей кромки (табл. 24 с. 431) так как .
- поправочный коэффициент учитывающий изменение главного угла в плане (табл. 24 с. 431) .
Проверяем достаточна ли мощность привода станка. Необходимо проверить выполнение условия формула (7.10).
Мощность (кВт) на шпинделе станка по приводу определяется по
формуле (7.11). В паспортных данных станка 16К40П находим:
III. Определяем основное время (мин) по формуле (7.12).
Определяем длину рабочего хода резца по формуле (7.16):
По условию . Врезание резца определяется по формуле (7.14):
Назначаем режимы резания для чистового точения .
- общий поправочный коэффициент равный произведению поправочных коэффициентов учитывающих измененные условия обработки. Определяем значения этих коэффициентов:
Определяем главную составляющую силы резания по формуле (7.6).
- общий поправочный коэффициент равный произведению поправочных коэффициентов учитывающих измененные условия обработки. Определяем значения этих коэффициентов: – поправочный коэффициент учитывающий изменение механических свойств обрабатываемого материала (табл. 21 с. 430). определяется по
Проверяем достаточна ли мощность привода станка. Необходимо проверить выполнение условия формула (7.10).
формуле (7.11). В паспортных данных станка 16К40П находим:
Определяем длину рабочего хода резца по формуле (7.16).
Назначаем режимы резания для однократного шлифования .
I. Выбираем шлифовальный круг. Устанавливаем характеристику круга. (табл. 176 с. 346). Для круглого наружного шлифования с продолбной подачей параметра шероховатости поверхности Ra125 мкм конструкционной закаленной стали с рекомендуется характеристика: Э ЭБ40СМ2К.
В качестве материала абразивных зерен принимаем белый электрокорунд (ЭБ) марку которого Э9А устанавливаем по табл. 167 с. 332. Выбор этой марки обусловлен высокой твердостью шлифуемой заготовки и требованиями предъявляемыми к точности обработки и шероховатости обработанной поверхности. В характеристике приняты:
связка керамическая (К).
В используемом справочнике ряд характеристик обозначен по старому стандарту а некоторые не приведены. Поэтому вносим следующие уточнения и дополнения в принятую маркировку характеристики круга:
Переводим старое обозначение маркировки абразивного материала Э9А в новое 24А.
После принятой зернистости 40 проставляем буквенный индекс зернистости характеризующий процентное содержание основной фракции. Принимаем индекс Н указывающий что в принятой зернистости 40 содержание основной фракции составляет 45%.
Принимаем структуру круга №5 .
Указываем разновидность принятой керамической связки К8 (для электрокорундовых кругов).
Указываем тип круга по справочнику [4] табл. 170 с. 334. На круглошлифовальных станках применяют обычно круги ПП и ПВД. Принимаем тип ПВД (плоский с двусторонней выточкой) обеспечивающий удобное и надежное крепление круга на шпинделе шлифовальной бабки.
Принимаем класс круга А.
Указываем допустимую скорость круга 35 мс (обычное шлифование).
Маркировка полной характеристики круга: ПВД 24А40НСМ25К8 35 мс.
Размеры нового круга по паспортным данным станка 3М131: диаметр ширина круга (или высота) .
Скорость главного движения резания (шлифовального круга) определяется по формуле (7.17):
По паспортным данным станка 3М131 у нового круга ; . Тогда по формуле (7.17):
т. е. в пределах рекомендуемого диапазона.
Скорость движения окружной подачи . Принимаем среднее значение 35 ммин (058 мс).
Определяем частоту вращения заготовки соответствующую принятой скорости движения окружной подачи:
Найденное значение может быть установлено на станке 3М131 имеющем бесступенчатое регулирование частоты вращения заготовки в пределах от 40 до 400 .
Поперечная подача круга . Учитывая высокие требования предъявляемые к точности обработки и шероховатости поверхности принимаем .
Определяем продольную подачу на оборот заготовки:
Для окончательного шлифования в справочнике рекомендуется
; принимаем . Тогда по формуле (7.19):
Определяем скорость движения продольной подачи (скорость продольного хода стола):
На используемом станке предусмотрено бесступенчатое регулирование скорости продольного хода стола в пределах 0055 ммин поэтому принимаем .
Определяем мощность затрачиваемую на резание (с. 469):
Выписываем из табл. 70 с. 468 коэффициент и показатели степеней формулы для круглого наружного шлифования с поперечной подачей на каждый ход стола обработки стали зернистости круга 40 твердости СМ2: . Тогда по формуле (7.21):
формуле (7.11). В паспортных данных станка 3М131 находим:
Следовательно 55 т.е. обработка возможна.
III. Определяем основное время (мин):
где - длина хода стола ;
h – припуск на сторону по условию h=01 мм;
K – коэффициент точности учитывающий время на «выхаживание» т. е. шлифование без поперечной подачи (осуществляется на заключительном этапе операции для достижения требуемых точности обработки и шероховатости обработанной поверхности); K=14.
Тогда по формуле (7.22):
Для обработки поверхностей выбраны такие же припуски как и для и выбраны такие же операции обработки. Поэтому режимы резания назначаем такие же как и для поверхности .
Подставив в формулу (7.5) получим:
По условию . Врезание резца определяем по формуле (7.14):
Основное время определяем по формуле (7.12):
Определяем основное время по формуле (7.12):
Однократное шлифование .
Определяем основное время по формуле (7.22):
Назначаем режимы резания для точения до
формуле (7.11).В паспортных данных станка 16К40П находим:
I. Выбираем резец и устанавливаем его геометрические элементы [4].
Определяем значения этих коэффициентов:
– поправочный коэффициент учитывающий изменение механических свойств обрабатываемого материала (табл. 21 с. 430). определяется по формуле (7.7).
Показатель степени определяем по табл. 22 с. 430. Для обработки конструкционной стали твердосплавным резцом . Тогда
Следовательно 4 т.е. обработка возможна.
Назначаем режимы резания для нарезания резьбы [6].
I. Выбираем резец и устанавливаем его геометрические элементы. Принимаем резьбовой резец для метрической резьбы. Материал пластинки – твердый сплав Т15К6.
Устанавливаем число черновых и чистовых рабочих ходов (карта 34 с. 101). Для наружной резьбы с шагом P = 2 мм i = 6.
Определяем скорость главного движения резания допускаемую режущими свойствами резца (карта 34 с. 101).
Для стали с наружной резьбы точности 6g и шага P=2 мм .
Поправочные коэффициенты на скорость главного движения резания при заданных условиях обработки не учитываем (каждый из них равен единице). Тогда .
Частота вращения шпинделя станка соответствующая найденной скорости главного движения резания определяется по формуле (7.4):
Корректируем частоту вращения по данным станка и устанавливаем действительную частоту вращения шпинделя: .
Действительная скорость главного движения резания определяется по формуле (7.5):
Определяем мощность затрачиваемую на резание (карта 34 с. 101).
Поправочные коэффициенты на мощность при заданных условиях обработки равны единице. Следовательно .
Проверяем достаточна ли мощность привода станка. У станка 16К40П
Следовательно 2 т.е. обработка возможна.
Врезание и перебег резца (мм) устанавливаем по прил. 6 с 375:
Устанавливаем число черновых и чистовых рабочих ходов (карта 34 с. 101). Для наружной резьбы с шагом P = 2 мм i = 4.
III. Определяем основное время (мин) по формуле (7.23).
По условию . Врезание резца
Припуск снимаем за три прохода:
Корректируем по станку
Назначаем режим резания для фрезерования шпоночного паза В=16 мм.
I. Выбираем фрезу и устанавливаем ее геометрические элементы. Принимаем концевую фрезу с нормальным зубом из быстрорежущей стали Р6М5. Диаметр фрезы принимаем равным ширине паза т. е. D = В = 16 мм; число зубьев фрезы z = 3 (карта 81 с. 215). Геометрические элементы (прил. 2 с. 369): = 15°; α = 14°; = 3°.
Устанавливаем глубину резания. При фрезеровании пазов концевой фрезой глубиной резания считается ширина паза в данном случае t=b=16 мм. Глубина паза при фрезеровании его за один рабочий ход принимается за ширину фрезерования В. В данном случае В = h = 6 мм.
Назначаем подачу на зуб фрезы (карта 81 с. 215). Для фрезерования стали D = 16 мм z = 3 и h = 6 мм Sz = 005 ммзуб.
Назначаем период стойкости фрезы (табл. 2 с. 204). Для концевой фрезы диаметром D = 16 мм из быстрорежущей стали Р6М5 рекомендуется период стойкости Т = 60 мин.
Определяем скорость главного движения резания допускаемую режущими свойствами фрезы (карта 87 с. 228). Для фрезы с нормальным зубом D = 16 мм z = 3 ширины паза 16 мм глубины паза до 18 мм и Sz до 007 ммзуб Vтабл =18 ммин.
Частота вращения шпинделя соответствующая найденной скорости главного движения резания:
Корректируем частоту вращения шпинделя по станку и устанавливаем действительную частоту вращения: .
Действительная скорость резания
Определяем скорость движения подачи (старое обозначение SМ)
Корректируем эту величину по данным станка и устанавливаем действительную скорость движения подачи .
Определяем мощность затрачиваемую на резание (карта 87 с. 228). Для Sz до 007 ммзуб ширины паза 16 мм глубины паза до 10 мм . Для заданных условий обработки поправочный коэффициент на мощность Kn = 1. Тогда Npeз = .
Проверяем достаточна ли мощность привода станка. У станка 6Т12 .
2 60 т. е. обработка возможна.
При фрезеровании концевой фрезой паза врезание определяется
Перебег = 1 5 мм; принимаем = 3 мм. Тогда
Тогда основное время
Рассчитанные режимы резания записываем в таблицу 5.
Режимы резания для обработки диаметра 65k6
Элементы режимов резания
Техническое нормирование в широком смысле этого понятия представляет собой установление технически обоснованных норм расхода производственных ресурсов. Под производственными ресурсами понимают энергию сырье материалы инструмент рабочее время и прочее [8].
Техническое нормирование труда — это совокупность методов и приемов выявления резервов рабочего времени и установления необходимой меры труда. Основным элементом технологического процесса является операция. Именно для выполнения операции устанавливают норму времени.
Норма времени — регламентированное время выполнения технологической операции в определенных организационно-технических условиях одним или несколькими исполнителями соответствующей квалификации. Технически обоснованной нормой времени считают время выполнения технологической операции в наиболее благоприятных для данного производства условиях.
Технически обоснованную норму времени устанавливают на каждую операцию для чего рассчитывают штучное время.
Штучное время — это отношение календарного времени технологической операции к числу изделий одновременно изготовляемых на одном рабочем месте. Для неавтоматизированного производства штучное время определяется по формуле (8.1):
где - основное (технологическое) и вспомогательное время;
- время организационного и технического обслуживания рабочего места соответственно;
- время перерывов в работе.
Основным (технологическим) называется время в течение которого непосредственно осуществляется изменение размеров формы и качества поверхностного слоя заготовки или взаимного расположения отдельных частей сборочной единицы и их крепление и т.д.
для каждого технологического перехода было определено в разделе 7:
Вспомогательное время — это время выполнения вспомогательных переходов и ходов: установки и снятия заготовки управления механизмами станка контрольных измерений и др. которые могут быть ручными механизированными (например установка и снятие изделия с помощью крана) и машинными (например автоматический обратный ход суппорта).
Вспомогательное время необходимо для осуществления действий создающих возможность выполнения основной работы являющейся целью технологической операции или перехода. Вспомогательное время операции определяют суммированием его составляющих элементов приводимых в таблицах нормативов по техническому нормированию.
Определяем операционное время для каждой операции по формуле (8.2):
Время обслуживания рабочего места представляющее собой часть штучного времени предназначено для ухода за рабочим местом и поддержания оборудования и оснастки в работоспособном состоянии.
Время организационного обслуживания рабочего места затрачивается исполнителем на уход за рабочим местом в течение смены: на раскладку и уборку инструмента в начале и конце смены на осмотр и опробование оборудования и его очистку смазку и пр. Время организационного обслуживания исчисляется в процентах к оперативному времени. По нормативам для условий крупносерийного и массового производства время составляет 0825% оперативного времени. .
Время технического обслуживания рабочего места — это время на уход за рабочим местом (оборудованием) в процессе выполнения работы. Время технического обслуживания непосредственно зависит от основного (технологического) времени поэтому его определяют в процентах к основному времени. По нормативам для большинства станков составляет 36% основного времени. .
Время перерывов работы затрачивается человеком на личные физиологические потребности и на дополнительный отдых. Время перерывов в работе исчисляется суммарно по нормативам в процентах к оперативному времени. .
Определяем штучное время для каждой операции по формуле (8.1):
В данном курсовом проекте был произведен анализ технологичности конструкции детали выбор получения заготовки определен тип производства разработана маршрутная технология изготовления заданной детали рассчитаны припуски и назначены режимы резания рассчитаны технические нормы времени.
Выполнены чертежи детали и наладок. Спроектирован технологический процесс механической обработки детали – «Вал».
Лахтин Ю. М. Леонтьева В. П. Материаловедение: Учебник для машиностроительных вузов — 2-е изд. перераб. и доп.— М.: Машиностроение. 1980.—493 е. ил.
Дунаев П.Ф. Леликов О.П. Конструирование узлов и деталей машин: Учеб. пособие для машиностроит. спец. вузов. – 4-е изд. перераб. и доп. – М.: Высшая школа 1985 – 416 с.: ил.
Шакирова М. А. Вельдяксова О. Г. Методическое пособие по выполнению курсового проекта дисциплины «Технология производства машин» - Метод. пособие для машиностроит. спец. вузов. – 2009 – 146 с.: ил.
Малов А. Н. В. Н. Гриднев Досчатов В. В. Справочник технолога-машиностроителя – том 2 – М.: Машиностроение 1972 – 568 с.: ил.
Радкевич Я. М. Тимирязев В. А. Схиртладзе А. Г. Островский М. С. Расчет припусков и межпереходных размеров в машиностроении: Учеб. пособие для машиностроит. спец. вузов – М.: Высш. шк. 2004 – 272 с.: ил.
Нефедов Н. А. Осипов К. А. Сборник задач и примеров по резанию металлов и режущему инструменту: Учеб. пособие для техникумов по предмету «Основы учения о резании металлов и режущий инструмент». – 5-е изд. перераб. и доп. – М.: Машиностроение 1990. – 448 с.: ил.
К. Ф. Антипов Б. И. Горбунов С. Н. Калашников и др. Под ред. А. Г. Косиловой и Р. К. Мещерякова. Справочник технолога-машиностроителя. Т1. Изд. 3-е М.: Машиностроение 1972. 694 с.
Общемашиностроительные нормативы времени и режимов резания – М.: Экономика 1990 – 473 с.: ил.
ГОСТ 3.1105-84 – ЕСТД. Формы и правила оформления документов общего вида.
ГОСТ 3.1118 – 82 – ЕСТД. Формы и правила оформления маршрутных карт.
Вал.cdw

Гр. III HB 212 248 ГОСТ8479-70
*Размеры обеспечиваемые инструментом
Допускается поверхность И без обработки
Наладка 1.cdw

Резец 2102-0031 Т15К6 ГОСТ 18877-73
12.ДО.07.КП.020000.009
Рекомендуемые чертежи
- 24.01.2023
- 23.04.2016
- 02.12.2024
- 24.01.2023
- 05.01.2022