Технологический процесс механической обработки вала




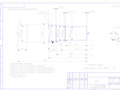
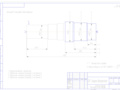
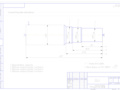
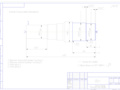
- Добавлен: 25.10.2022
- Размер: 725 KB
- Закачек: 0
Описание
Состав проекта
![]() |
![]() ![]() |
![]() ![]() |
![]() ![]() |
![]() ![]() |
![]() ![]() ![]() ![]() |
![]() ![]() |
![]() ![]() ![]() |
![]() ![]() |
![]() ![]() ![]() ![]() |
![]() ![]() ![]() ![]() |
![]() ![]() ![]() ![]() |
![]() ![]() ![]() ![]() |
![]() ![]() ![]() ![]() |
- Архиватор zip файлов
- Компас или КОМПАС-3D Viewer
- AutoCAD или DWG TrueView
- Microsoft Word
Дополнительная информация
0_15_tokarno-vintoreznaya_ustanov_v.dwg

Обточить начерно в размер 2 на длине 5
Обточить начерно в размер 3 на длине 4.
* - Размер для справок.
Общие допуски по ГОСТ 30893.1:
Сталь 45 ГОСТ 1050-88
Установ В(черновое обтачивание).
rrryesrrrs-microsoft-word-2.docx
путей сообщения императора Николая II (МИИТ)
Председатель комиссии
ТЕХНОЛОГИЧЕСКИЙ ПРОЦЕСС МЕХАНИЧЕСКОЙ
Курсовая работа по дисциплине
«Технология производства подъемно-транспортных строительных дорожных средств и оборудования»
Пояснительная записка
Руководитель Фомин В. И.
Студент гр. ТНД – Мирошниченко Е. В.
Технология машиностроения – это научная дисциплина изучающая процессы механической обработки деталей и сборки машин затрагивающая вопросы выбора заготовок и методы их изготовления.
Технологический процесс является частью производственного процесса связанного с непосредственным изменением состояния предмета производства. Технологический процесс должен обеспечивать рациональную организационную форму с использованием всех возможностей оборудования инструмента и приспособлений при оптимальных допускаемых на данном оборудовании режимах наименьшей затрате времени и наименьшей себестоимости работ. Исходными данными для проектирования технологических процессов обработки являются:
производственная программа
технические условия.
При проектировании технологического процесса обработки деталей решаются следующие основные вопросы:
установление вида производства и организационной формы выполнения технологического процесса;
выбор вида заготовок и определение их размеров; установление последовательности технологических операций;
выбор оборудования приспособлений режущего и измерительного инструмента и определение их потребного количества;
определение режимов работы по каждой операции;
определение нормы времени на обработку по каждой операции;
оформление технологической документации.
Цель курсовой работы - разработка технологического процесса изготовления вала цилиндрического редуктора по следующим исходным данным:
тип производства – единичный;
частота вращения вала n =1080 ;
a)подшипники –радиальные шариковые однорядные;
b)уплотнение - манжетное;
d)зубчатое колесо (m = 40 мм z = 100 степень точности = 8).
В работе необходимо выбрать вид заготовки определить ее размеры рассчитать точность промежуточных размеров и их величины составить план токарной и шлифовальной операции рассчитать режимы обработки и затраты времени составить эскизы этих операций.
Анализ технологических требований к конструкции детали
Изготавливаемая деталь – 6-и ступенчатый вал длиной 450 мм. Вал относится к группе цилиндрических изделий. Вал предназначается для передачи вращающего момента на тихоходной ступени редуктора. Вал изготавливается из стали 45 ГОСТ 1050-88. Твердость190 230 НВ обеспечивается термообработкой – нормализация. Тип производства – мелкосерийный.
Высокие требования точности предъявляются посадочным поверхностям вала под подшипники. Все нагрузки воспринимаемые валом
передаются через подшипники на корпус раму или станину редуктора.
Первая ступень длиной 140 мм диаметром 90 мм имеет шпоночный канавку 25х10х95. Обрабатывается с допуском n6 и шероховатостью Rа=63 мкм имеет фаску 2х45°.
Вторая ступень длиной 60 мм и диаметром 100 является посадочной поверхностью под манжетное уплотнение и имеет фаску 2х45. Поверхность обрабатывается с допуском а11 и шероховатостью Ra = 032 мкм.
Третья ступень диаметром 110 мм и длиной 50 мм является посадочной поверхностью под подшипник. Поверхность обрабатывается с допуском k6 и шероховатостью Ra = 25 мкм.
Четвёртая ступень диаметром 130 мм и длиной 50 мм служит упором для зубчатого колеса. Эта ступень не является рабочей и не будет использоваться в качестве технологической базы поэтому она не имеет специальной обработки.
Пятая ступень диаметром 120 мм и длиной 90 мм имеет шпоночный паз 25х12х45 для установки зубчатого колеса 8-ой степени точности а также фаску 2х450 . Поверхность обрабатывается с допуском r6 и шероховатостью Ra = 6.3 мкм.
Шестая ступень длиной 60 мм и диаметром 110 мм имеет фаску 2х45 и является посадочной поверхностью под подшипник. Поверхность обрабатывается с допуском k6 и шероховатостью Rа = 25 мкм.
В качестве конструкционных баз выбираем поверхности 3 и 6 так как они являются посадочными поверхностями под подшипник и определяют положение вала в редукторе как в сборочной единице следовательно к ним предъявляются повышенные требования.
Для шпоночных пазов назначаем шероховатость для основания Rа = 63 и для боковых поверхностей Ra = 32.
Необходимо при изготовлении детали выдерживать допуски формы и расположения.
Допуск цилиндричности:
для поверхности 1 ( 90n6) согласно рекомендации [1стр. 395 табл. 22.4] примем
где t– допуск размера поверхности. Согласно [1стр 452 табл.24.2] принимаем t = 25 мкм для поверхности 1.
для поверхности 4 ( 120r6) для поверхностей 3 и 6 ( 110k6) примем t = 25 мкм.
для поверхности 3 и 6 (110k6) согласно [1стр. 395 табл. 22.4] принимаем
где В1 – длина посадочной поверхности
Ттабл = 4 мкм – допуск соосности для шарикового подшипника.[1стр. 395 табл. 22.5].
Для поверхности 3: Т = 01224 = 88 мкм. Принимаем Т = 001 мм.
Для поверхности 6: Т = 01224 = 88 мкм. Принимаем Т = 001 мм.
для посадочной поверхности 4 ( 120r6) согласно [1 стр. 395 табл. 224] при 8 степени точности для зубчатого колеса с делительным диаметром
d= z m = 100 4=400 мм принимаем согласно [1стр. 398 табл. 227]
степень точности допуска соосности назначаем согласно [1стр. 398 табл. 226] Т=002 мм.
Допуск перпендикулярности:
поверхность в которую упирается подшипник установленный на ступени 6 задаем согласно рекомендациям книги [1стр. 394 табл. 224]. Степень точности допуска при базировании шариковых подшипников принимаем равной 8. На диаметре d=120 мм принимаем Т = 003 мм согласно [1стр. 399 табл. 22.8].
Допуски параллельности и симметричности шпоночных пазов определяем в соответствии с рекомендациями книги [1стр. 394 табл. 224]
где tшп – допуск ширины шпоночного паза.
Для шпоночного паза 25N9 tшп =0043 мм согласно [1стр. 452 табл. 242]:
Тогда для шпоночного паза 1-ой и 5-ой ступени:
Принимаем Т = 002 и Т = 008 соответственно.
Выбор вида финишной обработки конструктивных элементов детали.
-я ступень: ступень под МУВП. Из требований к шероховатости согласно [1 стр. 386 табл. 222] и получения точности размера по квалитету 6 применяется чистовое шлифование. Снимаем фаску 2х45º резцом с углом в плане 45º. Фрезеруем концевой фрезой шпоночную канавку длиной 95 мм.
-я ступень: ступень под манжетное уплотнение. Исходя из требований к шероховатости согласно [1] и получения точности размера по квалитету 11 применяется тонкое шлифование и полирование. Снимаем фаску 25х45º резцом с углом в плане 45º.
-я ступень: посадочное место под подшипник. Из требований к шероховатости согласно [1 стр. 386 табл. 222] и получения точности размера по квалитету 6 для подшипника применяется чистовое шлифование.
-я ступень: поверхность 130 не будет использоваться в качестве технологической базы так как она не является рабочей. Rz=80 обработка – токарная (черновое обтачивание).
-я ступень: посадочное место под зубчатое колесо. Из требований к шероховатости согласно [1стр. 386 табл. 222] и получения точности размера по квалитету 6 применяется чистовое шлифование. Снимаем фаску 2х45º резцом с углом в плане 45º. Фрезеруем концевой фрезой шпоночную канавку рабочей длиной 95 мм.
-я ступень: посадочное место под подшипник. Из требований к шероховатости согласно [1 стр. 386 табл. 22.2] и получения точности размера по квалитету 6 применяется чистовое шлифование. Снимаем фаску 2х45º резцом с углом в плане 45º.
Фаски получаем точением на токарном станке. Обработка нерабочих поверхностей вала – обтачивание черновое.
-ая ступень: 90n6 финишная обработка – чистовое шлифование.
-ая ступень: 100а11 финишная обработка – тонкое шлифование и полирование;
-ая ступень: 110k6 финишная обработка – чистовое шлифование;
-я ступень: 130 финишная обработка – черновое обтачивание;
-ая ступень: 120r6 финишная обработка – чистовое шлифование;
-ая ступень: 110k6 финишная обработка – чистовое шлифование.
Выбор способа установки детали на технологических операциях
Определим средний диаметр детали по формуле:
где n – число конструктивных элементов
– диаметр и длина конструктивного элемента
Определим коэффициент жёсткости заготовки:
Так как 4Кж12 то применяем установку в центрах.
Для обработки детали в центрах необходимо выбрать вид и типоразмер центровых отверстий.
В соответствии с [3] принимаем центровые отверстия типа В ГОСТ 14034-74 (рисунок 1). Такие центровые отверстия являются базой для многократного использования и сохраняются в готовых изделиях.
Рис. 1. Центровое отверстие.
Исходя из максимального диаметра вала 130 мм выбираем центровые отверстия с защитной фаской В 10 ГОСТ 14034-74 размерами L = 12 мм и d= 10 мм. С углами фасок 600 (для рабочей) и 1200 (для защитной).
Выбор вида и определение размеров заготовки
При единичном типе производства для изготовления детали типа вал не имеющей существенных перепадов диаметра рациональной является заготовка из круглого сортового проката (ГОСТ 2590-88) обычной точности прокатки В.
Исходя из рекомендаций [5] при максимальном диаметре детали 130 мм и при ldmax = 43 диаметр заготовки принимаем равный 135 мм. Материал детали – сталь 45.
Из реально выпускаемого сортового проката выбираем сталь горячекатаную круглую ГОСТ 2590-88 обычной точности прокатки (В)
d= 130. Допуск сотавляет TD= 28 что соответствует 16 квалитету.
Определяем длину заготовки
zт.о = 3 мм – припуск на торцевую обработку [5]
Zp – припуск на разрез.
Составление укрупненного маршрута изготовления детали
Отрезать заготовку от проката круглого сечения обычной степени точности длиной 456 мм и диаметром 135.
Подвергнуть заготовку улучшению до НВ 190 230 сталь 45.
5Токарно-винторезная
Выполнить обработку торцов в размер 450h14 и сверлить два центровых отверстия В 10 ГОСТ 14034-74. За несколько технологических проходов выполнить черновую и получистовую обработку по формированию контура детали. Снять фаски для
d= 90n6d= 100а11 d= 120r6 d= 110k6.
Выполнить предварительную и окончательную шлифовальную обработку поверхностей 12356.
Фрезеровать два шпоночных паза на поверхности 1 рабочей длиной 95 мм на поверхности 5 рабочей длиной 45 мм.
Полировать ступень вала под уплотнение d=100а11 на длине 30 мм обеспечивая шероховатость Ra = 032.
Подвергнуть закалке ТВЧ h 10 13; 48 58 HRC шейку вала под уплотнение диаметром d = 100а11.
Удалить окалину с поверхности детали.
Почистить деталь от загрязнений.
Произвести контроль детали по условиям рабочего чертежа.
Разработка операций по формированию контура детали.
1. Расчёт количества стадий обработки по каждому конструктивному элементу.
Заготовка: прокат круглый сталь 135 Тз=28 квалитет заготовки КВз=16.
Коэффициент ужесточения:
где: - допуск заготовки - допуск детали.
Число стадий механических обработок:
Найдём число стадий обработки по каждому конструктивному элементу. Результат приведен в таблице 1.
Расчет числа стадий обработки по каждому конструктивному элементу.
Диаметр вала d и допуск
Коэффициент ужесточения
Число стадий обработки
2. Расчет точности промежуточных размеров по каждому конструктивному элементу.
Расчет точности промежуточных размеров осуществляется по квалитетам. Распределение шагов квалитетов в последовательной обработке резанием описывается законом убывающей арифметической прогрессии. На промежуточные размеры стадий механической обработки для деталей типа вал назначается отклонение типа h кроме места для посадки под уплотнение.
Определим точность заготовки по каждой стадии механической обработки для каждой поверхности (Таблица 2).
Расчёт квалитетов по стадиям обработки.
Для поверхности 2 100а11 КВз = 16; КВд = 11; ΔКВ = 16 – 11 =5
Обтачивание черновое
Обтачивание получистовое
Шлифование окончательное
Для поверхностей 1 90n6 3 110k6 4 120r6 и 6 110k6 КВз = 16; КВд = 6; ΔКВ = 16 – 6 =10
Шлифование предварительное
Для поверхности 5 130h14 КВз = 16; КВд = 14; ΔКВ = 16 – 14 =2
3. Расчет величины промежуточных размеров по каждому конструктивному элементу.
При выборе припусков на обрабатываемые поверхности будем отталкиваться от принятых в практике примерных процентных отношений между общим припуском и припуском на черновую получистовую чистовую и окончательную обработки выбираемых из таблицы [2 Ч2.стр.13 табл.П1].
Исходя из этого условия и анализа требований к точности и шероховатости обрабатываемых поверхностей для удобства все данные сведём в таблицу. Так как тип производства единичный то припуски по стадиям обработки 2zi будем брать из таблиц [3 глава 16 с. 582 – 608].
Расчет производим по формуле:
zi – табличное значение припуска на текущую обработку.
Результат расчета сводим в Таблицу 3.
Расчет промежуточных размеров по стадиям обработки.
Расчет промежуточных размеров
Характеристика размеров
Предельное отклонение
Для поверхности 1 (90n6)
Для поверхности 2 (100a11).
Для поверхностей 3(110k6)и 6 (110k6)
Для поверхности 5 (120r6-)
Для поверхности 4 130h14
Выполним проверку исходя из условия что расчетный минимальный диаметр заготовки должен быть меньше фактического минимального диаметра заготовки.
Проведем уточнение диаметра заготовки. Выбираем сталь горячекатаную круглую ГОСТ 2590-88 обычной точности прокатки (В)
d= 130. Допуск сотавляет TD= 28.
d= 1318– 2 = 1298 мм;
Проверка выполняется (13041337). Расчетный размер находится в теле заготовки. Выбираем заготовку d = 135.
Составление планов операций по формированию контура детали.
1 Токарная обработка.
Расчет выполним исходя из характеристик станка 16К20[3 табл. П12]:
Допустимая мощность резания 75 кВт.
Максимальная длина заготовки – 1400 мм.
Максимальный диаметр заготовки – 400 мм.
Максимальный диаметр заготовки закрепляемой детали в трехкулачковом патроне 190 мм.
Частота вращения шпинделя – 125; 16; 20; 25; 315; 40; 56; 63; 80; 100; 125; 160; 200; 250; 315; 400; 500; 630; 860; 1000; 1250; 1600 обмин.
Продольная подача суппорта резца Sпродол – 005; 006; 0075; 009; 01; 0125; 015; 0175; 02; 025; 03; 035; 04; 05; 06; 07; 08; 1; 12; 14; 16; 22; 28 ммоб.
Поперечная подача Sпопер = 05 Sпродол.
Обоснование плана черновой токарной обработки.
Расчёт глубины резания при черновой токарной обработке.
Глубину резания для технологического перехода рассчитываем по формуле:
и сравниваем полученное значение с предельно допустимым для данного диаметра:
если обработка осуществляется за один переход
еслиобработка осуществляется за несколько технологических переходов.
В соответствии с рекомендациями [2 стр.6] назначаем в зависимости от значения коэффициента жесткости Кж.
Принимаем так как Кж= 43 9;
t ≤ [t]d– условие выполнения обработки по диаметрам.
t – глубина резания.
n – число рабочих ходов.
Для рассматриваемого технологического перехода будем назначать подачу инструмента исходя из условия не превышения допустимой мощности резания [N]=75 кВт.
– обработка по диаметрам невозможна.
Обработка осуществляется за несколько технологических переходов. Назначаем глубину резания мм и подачу S = 02 ммоб при мощности
N 65кВт [3 табл. П13]. Обработка осуществляется в 3 прохода:
– обработка по диаметрам возможна.
При глубине резания 3 мм принимаем S = 02 ммоб при мощности
N 6.5[3 табл. П13]. t=5.15
При глубине резания 5.8 мм принимаем S = 025 ммоб при мощности
N 65кВт [3 табл. П13]. t=4.8
При глубине резания 5 мм принимаем S = 025 ммоб при мощности
N = 65кВт [3 табл. П13]. t=2.5
N = 65кВт [3 табл. П13]. t=4.63мм
N = 65кВт [3 табл. П13]. t=5.06
Обоснование плана получистовой токарной обработки.
Получистовую токарную обработку продолжим с установа Г обеспечив получистовое обтачивание ступеней вала в следующей последовательности: 1106 12073 фаска 25×45 фаска 25×45.
Выполним переустановку заготовки и завершим получистовую токарную обработку ступеней следующих диаметров: 907
031106 канавка А фаска 25×45 фаска 25×45.
План токарной обработки:
Операция 005. Заготовительная
Установить закрепить снять заготовку.
Отрезать заготовку по условиям эскиза.
Операция 015. Токарно-винторезная
Установ А (торцевание центрование заготовки).
Сверлить центровое отверстие по условиям эскиза
Установ Б (торцевание центрование заготовки).
Подрезать торец справа с соблюдением размера 1.
Сверлить центровое отверстие по условиям эскиза.
Установ В (черновое обтачивание).
Переустановить закрепить.
Обточить начерно в размер 1 на длине 3.
Обточить начерно в размер 2 на длине 4.
Установ Г (черновое обтачивание).
Обточить начерно в размер 1 на проход.
Обточить начерно в размер 2 на длине 5.
Обточить начерно в размер 3 на длине 4.
Установ Г (получистовое обтачивание).
Обточить получисто в размер 1 на длину 6.
Обточить начисто в размер 3 на длину 5.
Установ Д (получистовое обтачивание).
Обточить получисто в размер на длину 8.
Обточить получисто в размер 4 обеспечивая размер 9.
Обточить получисто в размер 3 обеспечивая размер 10.
Обточить получисто в размер 1 обеспечивая размер 11.
План токарной обработки приведен на операционных эскизах.
2 Шлифовальная обработка .
Характеристика шлифовального станка.
Выбираем круглошлифовальный станок 3Б151[3 табл. П26]:
Мощность электродвигателя привода 7 кВт.
Наибольший диаметр и длина шлифуемой поверхности 180х630(800)мм.
Частота вращения 63 – 400 обмин.
Скорость продольного перемещения рабочего стола 01 –0 6 ммин.
Диаметр и толщина шлифовального круга 600 и 63 мм.
Поперечная подача 00025 – 005 ммоб с шагом 00025 ммоб.
Непрерывная подача при врезном шлифовании 01 – 2 мммин.
Обоснование плана шлифовальной обработки.
Шлифовальная обработка является финишной при которой должны обеспечиваться требования соосности отдельных шеек валов. В соответствии с требованиями рабочего чертежа соосность шеек под подшипники качения составляет 001мм соосность шейки под зубчатое колесо – 004мм хвостовика вала – 005мм.
Для обеспечения минимальной несоосности конструкторских баз обработку шеек ведем без переустановки. На первом установе выполним шлифование консольного участка а на втором обработаем шейки под подшипники и шейку под зубчатое колесо.
План шлифовальной обработки:
Операция 020. Круглошлифовальная
Переустановить закрепить снять заготовку.
Шлифовать предварительно последовательно в размер 1 на длине 3.
Шлифовать чисто последовательно в размер 2 на длине 3.
Шлифовать предварительно последовательно в размер 2 на длинах 10 и 11.
Шлифовать предварительно последовательно в размер 4 на длине 9.
Шлифовать предварительно последовательно в размер 6 на длине 8.
Шлифовать чисто последовательно в размер 1 на длине 11.
Шлифовать чисто последовательно в размер 3 на длине 10.
Шлифовать чисто последовательно в размер 5 на длине 9.
Шлифовать чисто последовательно в размер 7 на длине 8.
План шлифовальной обработки приведен на операционных эскизах.
Расчет режимов резания на операции по формированию контура детали.
Режимы резания рассчитывают или выбирают таким образом чтобы обеспечить требуемое качество обработки при наивысшей производительности труда и наименьшей себестоимости технологического процесса.
1. Токарная обработка.
Расчёт режимов резания осуществляется для конкретных переходов в последовательности установленной планом токарной обработки.
Согласно [8] выбираем резец Т15К6 из твердого сплава который содержит: вольфрам (79%) карбид титана (15%) кобальт (6%).
Рис. 2. Резец для чернового точения.
Для получистового точения воспользуемся токарным проходным отогнутым правым резцом с твердой отогнутой пластинкой Т15К6 с главным углом в плане 90 °по ГОСТ 188-79-73 (рис.4).
Рис. 3. Токарным проходным отогнутым правым резец.
Для изготовления канавки используем токарный канавочный резец с пластинкой Т15К6 по ГОСТ 18885-73 (рис. 5).
Рис. 4. Канавочный резец.
Определим скорость резания:
где Сv X Y m – расчетные коэффициенты определяемые согласно [7].
Т – расчётная стойкость резца. Т = 60 мин;
t – глубина резания;
для чернового обтачивания принимаем значение глубины резания из пункта 7.
для получистового обтачивания: мм.
для чернового обтачивания принимаем значение подачи из пункта 7.
для получистового обтачивания:
где Ks – коэффициент корректировки подачи.
Согласно [8] принимаем Ks = 045 для сталей с в= 500 700 МПа
(в= 650 для стали 45).
– табличное значение подачи. Согласно [8] принимаем при радиусе при вершине резца 05 мм.
ммоб. Принимаем S = 0175 ммоб.
Kv – поправочный коэффициент
где – коэффициент учитывающий материал заготовки.
где КГ – коэффициент характеризующий группу стали по обрабатываемости.
Принимаем согласно [8] = 1.
– предел прочности. Принимаем согласно [8] = 650 МПа.
nv – показатель степени. Принимаем согласно [8] nv = 1;
– коэффициент учитывающий влияние состояния поверхности заготовки на скорость резания. Принимаем согласно [8] = 09 для проката для первого перехода; для последующих переходов = 1.
– коэффициент учитывающий качество материала инструмента.
Принимаем согласно [8] = 1(для твердого сплава Т15К6).
– коэффициент учитывающий главный угол в плане.
Принимаем согласно [8] :
Kφ= 1 при φ = 45º – для чернового обтачивания.
Kφ= 07 при φ = 90º – для получистового обтачивания.
Согласно полученным данным рассчитываем коэффициент Кvдля
разных видов обработки:
Кv= 115 09 1 1 = 104 – при черновом обтачивании для первого
Кv= 115 1 1 1 = 115 – для последующих переходов при черновом
Кv= 115 1 1 07 = 081 – при получистовом обтачивании.
Определим частоту вращения:
Полученное значение принимаем согласно частоте вращения шпинделя.
Необходимые значения для расчета скоростей резания по токарно-винторезной обработке из п.7 сведены в таблице 4.
Расчеты режимов токарно-винторезной операции.
Установ В (черновое обтачивание)
Установ Г (черновое обтачивание)
Установ Г (получистовое обтачивание)
Установ Д (получистовое обтачивание)
Мощность резания при токарной обработке для наиболее нагруженного технологического перехода:
– фактическая скорость резания
частота вращения шпинделя выбранная по характеристике станка.
тангенцальная составляющая силы резания.
где: X YП – расчетные коэффициенты значения которых зависят от обрабатываемого материала стадии обработки и материала резца.
корректирующий коэффициент кчитывающий особенности обработки;
Согласно [5] принимаем:
X = 1 Y = 075 n = -015;
2. Шлифовальная обработка.
Расчёт режимов шлифования выполним исходя из характеристик шлифовального станка 3Б151:
Диаметр и толщина шлифовального круга – 600мм и 63мм;
Частота вращения детали – 63 400 (регулирование бесступенчатое);
Скорость продольного перемещения рабочего стола – 01 06 ммин (регулирование бесступенчатое);
Поперечная подача шлифовального круга – 00025 005 мм за 1 ход рабочего стола с шагом 00025 мм;
Непрерывная подача шлифовального круга при врезном шлифовании – 01 2 мммин (00005 001 ммоб.);
Мощность электродвигателя привода шлифовального круга – 7кВт.
Для обеспечения при предварительном и окончательном шлифовании параметров шероховатости Ra08 125 для термически обработанных сталей выбираем шлифовальный круг прямого профиля размерами: d=600 мм D=130 ммb=63мм – следующего обозначения ПП-24 40HМ2 5 К8 А-35[6].
Расчёт выполняем в следующей последовательности:
Согласно [8] назначаем следующий режим шлифования:
Скорость шлифовального круга Vк = 35мс;
для предварительного шлифованияVз = 20ммин;
для окончательного шлифованияVз = 40ммин
Подача шлифовального круга:
для предварительного шлифования
s= 05 В = 05·63=315 ммоб где В – ширина шлифовального круга.
Принимаем s = 19 ммоб из-за перегрузки станка;
для окончательного шлифования
s = 03В = 03·63=189 ммоб.
Принимаем s = 19 ммоб;
Число рабочих ходов.
Так как за один проход согласно [6] снимается:
для предварительного шлифования t = 001 мм то необходимое число рабочих ходов шлифовального круга:
для окончательного шлифованияt = 0005 мм то необходимое число рабочих ходов шлифовального круга:
Частота вращения заготовки
Частота вращения шлифовального круга
Проверка шлифовального станка по мощности:
где СN r x y q – поправочный коэффициент и показатели степени.
Принимаем согласно [6]:
СN= 265; r = 05; y = 055; q = 0 при поперечной подаче на двойной ход с использованием шлифовального круга с зернистостью 40 и твердостью СМ1 – С1.
Если условие N[N]= 7 кВт соблюдено то проверка выполняется.
Все полученные значения сведены в таблице 5.
Расчеты режимов шлифовальной обработки.
Установ А(предварительное и окончательное шлифование)
Установ Б(предварительное и окончательное шлифование)
Расчет затрат времени на операции по формированию контура детали.
Расчёт затрат времени выполним для каждого технологического перехода в соответствии с картой эскизов.
Для токарной обработки штучно-калькуляционное время:
Где: Тшт – время непосредственно затрачиваемое на обработку детали.
Где: Кд – коэффициент учета дополнительных затрат времени
Согласно [10] принимаем:
- для токарной обработки Кд = 007;
- для шлифования Кд = 009;
tоп – оперативное время (для одного установа).
Где: - время затрачиваемое на установку закрепление и снятие заготовки.
- вспомогательное время связанное с конкретным технологическим переходом
=025 - для черновой обработки;
=04 - для получистовой обработки;
- затраты времени на перемещение инструмента в i-том технологическом переходе при котором происходит обработка поверхности.
Тп.з. – подготовительно-заключительное время.
Согласно [11] принимаем Тп.з. = 18 мин;
N – число деталей в партии N = 1.
Все полученные значения расчетов по определению затрат времени на токарную обработку сведены в таблице 6.
Расчет затрат времени токарной обработки
Наименование операции
5 Токарно-винторезная
Круг В-90 ГОСТ 2590-88
сталь 45 ГОСТ 1080-88
Токарно-винторезный 16К20
- Установ В (черновое обтачивание) Т=16
- Установ Г (черновое обтачивание) Т=16
- Установ Г (получистовое обтачивание) Т=16
- Установ Д (получистовое обтачивание) Т=16
Для шлифовальной обработки согласно [10] принимаем Кд = 009;
где: 12 – применяется для предварительного шлифования
- применяется для окончательного шлифования;
l – длина шлифуемого элемента.
Все полученные значения расчетов по определению затрат времени на шлифовальную обработку сведены в таблице 7.
Согласно [11] принимаем Тп.з. = 15 мин;
Расчет затрат времени шлифовальной обработки
5 Круглошлифовальная
Круг В-67 ГОСТ2590-88
- Установ А (шлифование предварительное окончательное)Т=16
- Установ Б (шлифование предварительное окончательное)Т=16
В ходе курсовой работы был разработан технологический процесс на изготовление детали – ступенчатый вал. Оформлена технологическая документация на операции и переходы применяемые в ходе получения детали. Установлены и применены в ходе разработки технологического процесса основные принципы и приёмы используемые при обработке металлов резанием. Составлен план токарной и шлифовальной обработок детали. Выполнен расчет режимов резания.
Процесс изготовления детали проходит на двух станках:
На токарно-винторезном станке 16К20 при помощи твердосплавного инструмента – резца Т15К6.
На круглошлифовальном станке 3Б151 при помощи шлифовального круга.
Конструирование узлов и деталей машин: Учеб. пособие для студ. техн. спец. вузов П. Ф. Дунаев О. П. Леликов.- 8-е изд. перераб. и доп. – М.: Академия 2003.- 496 с.
Фомин В.И. Проектирование технологических процессов изготовления деталей подъемно-транспортных строительных и дорожных машин. Методические указания к курсовому проектированию. Часть 2. - М.: МИИТ 2008. – 45 с.
Краткий справочник металлистаПод общ. ред. П.Н.Орлова Е.А.Скороходова. – М.: Машиностроение 1987.
Справочник технолога-машиностроителя. В 2-х т. Т.1. Под ред. А.Г.Косиловой Р.К. Мещерякова. Изд. 4-е. – М.: Машиностроение 1985.
Обработка металлов резанием. Справочник технолога Под ред. А.А. Панова. – М.: Машиностроение 1988.
Справочник технолога-машиностроителя. В 2-х т. Т.1. Изд. 3-е. Под ред. А.Г.Косиловой Р.К. Мещерякова. – М.: Машиностроение1972.
Общемашиностроительные нормативы режимов резания для технического нормирования работ на металлорежущих станках. Ч. 1. М.: Машиностроение 1974.
Справочник технолога-машиностроителя. В 2-х т. Т2. Под ред. А.Г.Косиловой Р.К. Мещерякова. Изд. 4-е. – М.: Машиностроение 1985.
Общемашиностроительные нормативы времени вспомогательного обслуживания рабочего места и подготовительно-заключительного для технического нормирования станочных работ. Серийное производство. М.: Машиностроение 1974.
Матвеев В.А. Пустовалов И.И. Техническое нормирование ремонтных работ в сельском хозяйстве. – М.: Колос 1979.
Справочник технолога авторемонтного производства. Под. ред. Г.А.Малышева. – М.: Транспорт 1977.
Анализ технологических требований к конструкции детали.
Выбор способа установки заготовки на технологических операциях.
Выбор вида и определение размеров заготовки.
Составление укрупнённого маршрута изготовления детали.
Список используемой литературы.
015_tokarno-vintoreznaya_ustanov_a.dwg

Сверлить центровое отверстие.
* - Размер для справок.
Общие допуски по ГОСТ 30893.1:
Сталь 45 ГОСТ 1050-88
Отверстие центровое В 10 ГОСТ 14034-74
Установ А(торцевание
центрование заготовки)
015_tokarno-vintoreznaya_ustanov_g.dwg

Общие допуски по ГОСТ 30893.1:
Обточить начерно в размер 1 на длине 6.
Обточить начерно в размер 2 на длине 5.
Обточить начерно в размер 3 на длине 4.
5. Токарно-винторезная
Сталь 45 ГОСТ 1050-88
Установ Г(черновое обтачивание).
015_tokarno-vintoreznaya_ustanov_b.dwg

Подрезать торец справа с соблюдением 1.
Сверлить центровое отверстие.
* - Размер для справок.
Общие допуски по ГОСТ 30893.1:
Сталь 45 ГОСТ 1050-88
Отверстие центровое В 10 ГОСТ 14034-74
Установ А(торцевание
центрование заготовки)
Установ Б(торцевание
015_tokarno-vintoreznaya_poluchistoe_ustanov_d.dwg

Обточить получисто в размер 4
обеспечивая размер 9.
Обточить получисто в размер 3
обеспечивая размер 10.
Обточить получисто в размер 1
обеспечивая размер 11.
* - Размер для справок.
Общие допуски по ГОСТ 30893.1:;
Сталь 45 ГОСТ 1050-88
Установ Д(получистовое обтачивание).
015_tokarno-vintoreznaya_poluchistovaya_ustanov_g.dwg

Обточить начисто в размер 1 на длину 6.
* - Размер для справок.
Общие допуски по ГОСТ 30893.1:;
Сталь 45 ГОСТ 1050-88
Установ Г(получистовое обтачивание).
Рекомендуемые чертежи
- 26.05.2014
- 07.09.2016