Технологический процесс изготовления детали вал



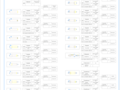
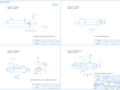
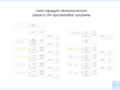
- Добавлен: 24.01.2023
- Размер: 1 MB
- Закачек: 0
Узнать, как скачать этот материал
Подписаться на ежедневные обновления каталога:
Описание
Технологический процесс изготовления детали вал
Состав проекта
![]() |
![]() |
![]() ![]() ![]() |
![]() ![]() ![]() |
![]() ![]() ![]() ![]() |
![]() ![]() ![]() ![]() |
![]() ![]() ![]() ![]() |
Дополнительная информация
Контент чертежей
Схема маршрута (Перспективная программа).cdw

Операционные эскизы.cdw

Схема маршрута (основная программа).cdw

Рекомендуемые чертежи
- 24.01.2023
Свободное скачивание на сегодня
Обновление через: 15 часов 51 минуту