Технологический процесс изготовления детали типа Вал для гибкого автоматизированного производства




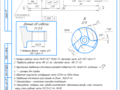
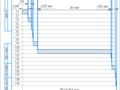
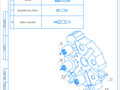
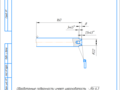
- Добавлен: 24.01.2023
- Размер: 5 MB
- Закачек: 0
Описание
Состав проекта
![]() |
![]() ![]() ![]() ![]() |
![]() ![]() ![]() ![]() |
![]() |
![]() ![]() ![]() |
![]() ![]() ![]() ![]() |
![]() |
![]() |
![]() |
![]() |
![]() ![]() ![]() ![]() |
![]() ![]() ![]() ![]() |
![]() ![]() ![]() ![]() |
![]() ![]() ![]() ![]() |
![]() |
![]() ![]() ![]() ![]() |
![]() ![]() ![]() ![]() |
![]() |
![]() ![]() ![]() ![]() |
![]() |
![]() ![]() ![]() ![]() |
![]() |
![]() |
![]() ![]() ![]() ![]() |
![]() |
![]() ![]() ![]() ![]() |
![]() |
![]() |
![]() |
![]() ![]() ![]() ![]() |
![]() |
![]() |
![]() |
![]() |
![]() ![]() ![]() ![]() |
![]() ![]() ![]() ![]() |
![]() ![]() ![]() ![]() |
![]() ![]() ![]() ![]() |
![]() |
![]() ![]() ![]() |
![]() ![]() ![]() ![]() |
![]() ![]() ![]() ![]() |
![]() |
Дополнительная информация
Новаяналадка6.cdw

Новаяналадка4.cdw

Новаяналадка8.cdw

Метчик мой.cdw

РГ.cdw

Новаяналадка14.cdw

общий.cdw

Новаяналадка12.cdw

Новаяналадка7.cdw

Новаяналадка9.cdw

Сверло.cdw

Новаяналадка3.cdw

Новаяналадка2.cdw

Новаяналадка15.cdw

Новаяналадка.cdw

Новаяналадка13.cdw

Новаяналадка10.cdw

Новаяналадка11.cdw

Новаяциклограмма.cdw

Новаяналадка5.cdw

Рекомендуемые чертежи
- 24.01.2023
Свободное скачивание на сегодня
Другие проекты
- 23.08.2014