Разработка технологии и оснастки для изготовления детали Колпачок с применением компьютерного моделирования




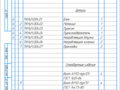
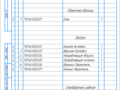
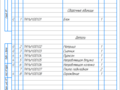
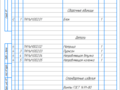
- Добавлен: 25.01.2023
- Размер: 3 MB
- Закачек: 1
Описание
Состав проекта
![]() |
![]() ![]() ![]() ![]() |
![]() ![]() ![]() ![]() |
![]() ![]() ![]() ![]() |
![]() ![]() ![]() ![]() |
![]() ![]() ![]() ![]() |
![]() ![]() ![]() ![]() |
![]() ![]() ![]() ![]() |
![]() ![]() ![]() ![]() |
![]() ![]() ![]() ![]() |
![]() ![]() ![]() ![]() |
![]() ![]() ![]() |
![]() ![]() ![]() ![]() |
Дополнительная информация
Машрутная карта.cdw

Чертеж колпачка.cdw

Спец для высадки.spw

Штамп обрезной.cdw

Штамп вырубной.cdw

Штамп для высадки.cdw

Спец для фомовки.spw

Спец выруб.spw

Спец для обрезки.spw

Штамп для формовки.cdw

Результаты комп. моделирования.cdw

Рекомендуемые чертежи
- 24.01.2023
- 04.11.2022
- 25.01.2023
- 24.01.2023
- 27.11.2021
Свободное скачивание на сегодня
Другие проекты
- 23.08.2014