Разработка технологии изготовления и создание участка для серийного изготовления детали Шестерня для наклонного механизма




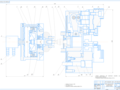
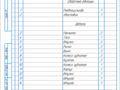
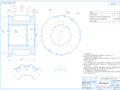
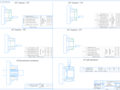
- Добавлен: 24.01.2023
- Размер: 6 MB
- Закачек: 5
Описание
Разработка технологии изготовления и создание участка для серийного изготовления детали Шестерня для наклонного механизма
Состав проекта
![]() |
![]() |
![]() ![]() ![]() |
![]() |
![]() ![]() ![]() ![]() |
![]() ![]() ![]() ![]() |
![]() ![]() ![]() ![]() |
![]() ![]() ![]() ![]() |
![]() ![]() ![]() ![]() |
![]() ![]() ![]() ![]() |
![]() ![]() ![]() ![]() |
![]() ![]() ![]() |
![]() ![]() ![]() |
![]() |
![]() ![]() ![]() |
![]() ![]() ![]() |
![]() ![]() ![]() |
![]() ![]() ![]() |
![]() ![]() ![]() |
![]() ![]() ![]() |
Дополнительная информация
3 Аннотация.docx
Проектом предусмотрено применение прогрессивного высокопроизводительного оборудования специального приспособления использования прогрессивного инструмента. Всё это позволило снизить трудоёмкость изготовления повысить производительность труда и улучшить качество обрабатываемых поверхностей.
Пояснительная записка содержит 66 страниц. Графическая часть выполнена на трёх листах формата А1 и трёх листах формата А2.
Операционные наладки.cdw

Токарный станок 16А20Ф3
Подрезать торец l=253.3 до 250
токарный станок 16А20Ф3
подрезать торец до 250мм
проверить шлицы калибром
резец контурного точения с мех.
подрезать торец на 70мм
подрезать торец до 250
ОГУ 15.03.05. 1222. 237
Теоретический чертеж
0Горизонтально-протяжная
Деталь.cdw

условное обозначение отверстий
ОГУ 15.03.05. 1222. 237
Качества не обработанных отверстий по группе 3 по
технологической инструкции ОГМ
Допускаемые отклонения линейных размеров по 2кл точности ГОСТ
09-55 (СТП 11388-78)
Ось симметрии одного из пазов должна совпадать с осью симметрии
допускается смещение на 1 мм. Нанесение риски l=10
Неуказанные предельные отклонения размеров обрабатываемых
поверхностей отверстий по А7 валов по B7 остальных СМ7
На поверхности Г допускаются черновины
На поверхности Д допускается технологическая выточка диаметр
0 мм глубиной до 2 мм
Заготовка.cdw

Планировка.cdw

Калибр-пробка.cdw

Приспособление.cdw

ОГУ 15.03.05. 1222. 237 00 00
Патрон предназначен для закрепления заготовки при
токарно-фрезерной обработке
Наибольший диаметр закрепляемой детали 670 мм
Внутренний диаметр пневмоцилиндра 60 мм
Спецификация приспособления.spw

Патрон трехкулачковый
ОГУ 15.03.05. 1222. 237 00 0
Болт М6 ГОСТ 7798-70
Болт М10 ГОСТ 7808-70
Болт М10 ГОСТ 7798-70
Болт М14 ГОСТ 7798-70
Винт М4 ГОСТ 1491-81
Винт М4 ГОСТ 17473-80
Винт М6 ГОСТ 1486-84
Винт М8 ГОСТ 1486-84
Винт М10 ГОСТ 1491-81
Кольцо 10 ГОСТ 13766-82
Кольцо 18 ГОСТ 983-81
Договор.docx
о передаче права на использование Произведения
г. Орск «17» января 2022 г.
Клименков Антон Олегович
(фамилия имя отчество)
1. Лицензиар безвозмездно предоставляет Лицензиату право на использование произведения в обусловленных настоящим договором пределах и на определенный договором срок.
2. Произведением по настоящему договору является выпускная квалификационная работа на тему: «Разработка технологии изготовления и создание участка для серийного изготовления детали «Шестерня» для наклонного механизма.» (далее – Произведение).
1. Лицензиар гарантирует что ему принадлежит исключительное право на Произведение указанное в разделе 1 настоящего договора и он обладает всеми полномочиями для заключения настоящего договора.
2. Лицензиар гарантирует что при создании Произведения им не были нарушены авторские или иные права третьих лиц.
3. Лицензиар гарантирует что передача прав на Произведение и его дальнейшее использование Лицензиатом в соответствии с настоящим договором не приведет к нарушению прав третьих лиц.
Права и обязанности Сторон
1. Лицензиар безвозмездно передает Лицензиату следующие права на использование Произведения:
1.1. Воспроизведение Произведения то есть изготовление одного и более экземпляров Произведения или его части в любой материальной форме.
1.2. Распространение Произведения путем продажи или иного отчуждения его оригинала или экземпляров.
1.3. Публичный показ Произведения.
1.4. Прокат оригинала или экземпляра Произведения.
1.5. Публичное исполнение Произведения с помощью технических средств.
1.6. Сообщение по кабелю.
1.7. Доведение Произведения до всеобщего сведения.
2. Лицензиат обязуется использовать Произведение строго в соответствии с условиями настоящего договора.
3. Лицензиат имеет право переуступать права указанные в п. 3.1 настоящего договора третьим лицам (сублицензионный договор) без предварительного согласия Лицензиара.
4. Лицензиар сохраняет за собой право использовать самостоятельно или предоставлять аналогичные права на использование Произведения третьим лицам.
5. Лицензиат не берет на себя обязательство по представлению Лицензиару отчетов об использовании Произведения.
Срок и территория использования Произведения
1. Лицензиар предоставляет Лицензиату право использовать Произведение в течение срока действия исключительного права на Произведение на всей территории Российской Федерации.
2. В случае прекращения исключительного права на Произведение настоящий договор прекращается.
Ответственность Сторон
1. Стороны несут ответственность за неисполнение или ненадлежащее исполнение своих обязательств по настоящему договору в соответствии с действующим законодательством Российской Федерации.
1.Условия настоящего договора конфиденциальны и не подлежат разглашению.
1.Все споры и разногласия которые могут возникнуть между Сторонами по вопросам не нашедшим своего разрешения в тексте данного договора будут разрешаться путем переговоров на основе действующего законодательства.
2.При не урегулировании в процессе переговоров спорных вопросов споры разрешаются в суде в порядке установленном действующим законодательством.
Порядок передачи прав
1.Датой передачи прав на Произведение является дата подписания акта приема-передачи Произведения являющегося неотъемлемой частью настоящего договора.
Заключительные положения
1.По вопросам которые не урегулированы или не полностью урегулированы настоящим договором Стороны руководствуются действующим законодательством.
2.Любые изменения и дополнения к настоящему договору действительны при условии если они совершены в письменной форме и подписаны Сторонами или надлежаще уполномоченными на то представителями Сторон.
3.Договор составлен в двух экземплярах из которых один находится у Лицензиата второй – у Лицензиара.
Адреса и подписи Сторон
Федеральное государственное бюджетное образовательное учреждение высшего образования «Оренбургский государственный университет»
Адрес: 460018 г. Оренбург пр. Победы13
Адрес: 462403 г. Орск пр. Мира 15А
Телефонфакс: (3537) 23-65-80
приема-передачи Произведения
По настоящему акту Лицензиар передает а Лицензиат принимает следующее Произведение:
Название файла в системе «Антиплагиат.ВУЗ»
Допустимый вариант размещения Произведения
Выпускная квалификационная работа
«Разработка технологии изготовления и создание участка для серийного изготовления детали «Шестерня» для наклонного механизма.»
ОГТИ_ВКР_КлименковВА_З-17КОМП(ба)ТМ.docx
Настоящий Акт составлен в двух экземплярах имеющих равную юридическую силу по одному экземпляру для каждой из сторон и является неотъемлемой частью Договора.
Адрес: 460018 г. Оренбург пр. Победы13
4 Содержание.docx
1Анализ конструкции детали и требования к её изготовлению6
2Технологический анализ конструкции детали7
3Определение типа производства и формы организации технологического процесса9
4Выбор и обоснование вида заготовки и метода её изготовления12
5Проектирование технологического маршрута обработки20
6Расчет режимов обработки с нормированием технологического процесса21
Конструкторская часть42
1Базирование заготовки42
2Расчёт станочного приспособления42
3Выбор и расчёт контрольного приспособления50
Организационный раздел53
1Расчёт потребного количества оборудования53
2Расчёт площади производственного участка57
3Расчёт численности персонала62
Список используемой литературы66
Отзыв.doc
высшего профессионального образования
«Оренбургский государственный университет»
Кафедра машиностроения энергетики и права
наименование кафедры
студента Клименкова Антона Олеговича группы 3-17КОМП (ба)ТМ
фамилия имя отчество
выполненной по теме: Технологическая подготовка производства детали «Шестерня» для наклонного механизма.
по направлению подготовки 15.03.05. Конструкторско-технологическое обеспечение машиностроительного производства
ВКР выполнена на 67 листах графическая часть на 6 листах.
количество лист страниц количество
Оригинальность решений ВКР: В связи с изменением типа производства был принят экономически целесообразный вариант заготовки применены высокопроизводительные операции механической обработки инновационное оборудование современные средства контроля и технического оснащения. Спроектирован механических участок.
Достоинства и недостатки оформления проекта. Все построения проводились с использованием конструкторского пакета КОМПАС-График V17 технологическая часть проекта – с использованием прикладных программ Microsoft Word текстовая часть проекта оформлена с использованием лицензионного программного продукты Microsoft Word и в соответствии с требованием стандартов ОГУ
Оригинальность работы составила – 5196%
Общее заключение о результатах ВКР: Полученные результаты имеют практическую значимость по использованию разработанной технологии. Студент заслуживает присвоение_ звания бакалавра по направлению подготовки 15.03.05 Конструкторско-технологическое обеспечение машиностроительного производства.
отлично хорошо удовлетворительно
Руководитель ВКР Сергиенко С. Н. канд. техн. наук. доцент_
фамилия имя отчество должность ученая степень ученое звание
1 Титульник.doc
ФЕДЕРАЛЬНОГО ГОСУДАРСТВЕННОГО БЮДЖЕТНОГО ОБРАЗОВАТЕЛЬНОГО УЧРЕЖДЕНИЯ ВЫСШЕГО ОБРАЗОВАНИЯ
«ОРЕНБУРГСКИЙ ГОСУДАРСТВЕННЫЙ УНИВЕРСИТЕТ»
Факультет инженерии экономики и права
Кафедра машиностроения энергетики и транспорта
ВЫПУСКНАЯ КВАЛИФИКАЦИОННАЯ РАБОТА
Направление подготовки 15.03.05 Конструкторско-технологическое обеспечение машиностроительных производств
Разработка технологии изготовления и создание участка для серийного изготовления детали «Шестерня» для наклонного механизма.
Пояснительная записка
ОГУ 15.03.05. 1222. 237 ПЗ
6 Доклад.docx
Вашему вниманию представлен дипломный проект на тему: «Разработка технологии изготовления и создание участка для серийного изготовления детали «Шестерня» для наклонного механизма.». Представлена пояснительная записка комплект технологической документации и графическая часть.
Целью работы является:
проектирование участка механического цеха по изготовлению детали «Шестерня».
-Разработка оптимального технологического процесса;
-Выбор более производительного оборудования;
-Расчет затрат для двух вариантов;
-Подбор и расчет приспособления;
-Выбор современных средств измерения;
-Проект участка механического цеха.
Шестерня – это колесо (диск) с зубьями (другим словом – зубчатое колесо (ЗК)) которое крепится ко вращающейся оси. Она может быть как с конической так и с цилиндрической поверхностью.
Деталь представлена на фрагменте чертеже.
Диаметр детали составляет 37909 мм. Длина 250 мм.125 кг. Материал: Сталь 35ХМЛ легированная качественная сталь позволяющая шестерне передавать большие крутящие моменты редуктора.
С точки зрения механической обработки внутренних и наружных поверхностей деталь не вызывает труда так как все поверхности являются открытыми и не требуют специальных инструментов и оборудования.
На основании качественной оценки деталь считается технологичной.
Деталь «Шестерня» входит в состав привода механизма наклона конвертора «КВК-30Ц». Конвертор «КВК-30Ц» предназначен для получения черновой меди или никелевого Фанштейна путем продувки штейнов воздухом обогащённым кислородом. Конверторы нашли широкое применение на предприятиях черной и цветной металлургии для получения легированных сталей и сплавов получение цветных сплавов.
слайд (про заготовку)
Для детали Шестерня выполненной из стали 35ХМЛ назначаются следующие варианты получение заготовки:
литье в песчано-глинистые формы. Этим методом получаются отливки массой до 250 тонн. Им характерна относительно простая форма имеют напуск для упрощения формы по сравнению с готовой деталью. Требуют значительной механической обработки.
литье в кокиль. Эти методом получаются отливки массой от нескольких граммов до 3 тонн весьма разнообразных и сложных форм значительно приближенных к формам готовой детали в связи с чем требует меньших затрат на обработку резанием.
При Сравнении технико-экономических показателей двух вариантов получения заготовок ким составил для 1 варианта – 067 а во 2 варианте 08
при этом масса заготовки в 1 варианте 1864 кг а во втором более 15 кг.
На основании таблицы следует то что наилучшем вариантом получения заготовки будет литье в кокиль.
слайд (про графотехнологию)
на данном слайде представлена графотехнология базового варианта обработки детали «Шестерня». В качестве заготовки использовалось литье в песчано-глинистую форму. Обработка велась на универсальных станках время обработки детали составило 188 ч по базовому варианту а по проектному варианту обработка данной детали составила 115 ч. Использовались станки с ЧПУ.
-14 слайды (тех. процесс)
На данном слайде показана токарная черновая операция. Она необходима для технологических баз и снятие основного черного припуска
слайд про приспособление
Трехкулачковый самоцентрирующий рычажно-клиновой патрон с механизированным приводом применяемый для зажима заготовок обрабатываемых на токарных и револьверных станках и многошпиндельных полуавтоматах в крупносерийном и среднесерийном производствах. Для установки центрирования и закрепления деталей как правило применяется специальная оснастка что приводит к большим затратам вспомогательного времени. Недостатком специальной оснастки для станков кроме невысокой жесткости является дороговизна в обслуживании.
Разработанное приспособление состоит корпуса и рычагов расположенных под углом а также в состав комплекта приспособления входит пневмопривод с забором воздуха и установочная призма по которому выверяется расположение поверхностей относительно оси станка. При помощи сжатого воздуха центрируются рычаги по посадочному диаметру. Усилия зажима пневмоцилиндра согласно расчету достаточно для надежного закрепления детали при обработке. Так же пневмопривод очень выгоден по сравнению с гидроприводом дешевизной рабочего пространства (воздух) не требует утилизации после рабочего хода. Приспособление работает от стационарной заводской пневмомагистрали при давлении воздуха 04 МП.
слайд про контрольный инструмент
Шлицевое соединение как правило контролируется проходными калибрами. При этом поэлементный контроль осуществляется непроходными калибрами. При использовании калибров отверстие считается годным если калибр-пробка проходит а диаметры и ширина паза не выходят за установленные верхние пределы.
Расчетное количество станков составило 12по расчетам на 1 операцию токарных станков 4 на 2 – три
Наименование и модель станка
Расчетное число станков
Принятое количество оборудования Спр
Коэффициент загрузки станка
Средний коэффициент загрузки
Токарный станок с ЧПУ 16А20Ф3
Горизонтально протяжной станок 7534
Универсально фрезерный станок 6Р82Ш
Так же на участке организовывается заточное и ремонтное отделение склад заготовок и готовой продукции склад масел. Транспортировка груза осуществляется мостовым краном. Его грузоподъёмность 5т.
габариты цеха составили 24х48м
слайд заключение (разрешите не зачитывать?)
слайд Доклад окончен
2 Задание.doc
подпись инициалы. Фамилия
на выполнение выпускной квалификационной работы
студенту Клименкову Антону Олеговичу группа 3-17КОМП(ба)ТМ
(фамилия имя отчество)
по направлению подготовки 15.03.05 – Конструкторско-технологическое обеспечение машиностроительных производств.
Тема выпускной квалификационной работы «Разработка технологии изготовления и создание участка для серийного изготовления детали «Шестерня» для наклонного механизма»
Срок сдачи студентом ВКР « »__ г.
Цель ВКР Разработка и подготовка производства изготовления проектной детали
1Выбрать оптимальную заготовку для проектной детали.
2Спроектировать технологический процесс механической обработки проектной детали.
3Создать управляющую программу для станка с ЧПУ.
4Подобрать и рассчитать приспособление и средство измерения.
5Скомпоновать участок механической обработки проектной детали.
Исходные данные к выпускной квалификационной работе Чертеж детали. Годовой объем выпуска Nт= 13000 шт.
Содержание пояснительной записки.
1 Технологическая часть
1.1Анализ конструкции детали и требования к её изготовлению
1.2Технологический анализ конструкции детали
1.3Определение типа производства и формы организации технологического процесса
1.4Выбор и обоснование вида заготовки и метода её изготовления
1.5Проектирование технологического маршрута обработки
1.6Расчет режимов обработки с нормированием технологического процесса
2Конструкторская часть
2.1Базирование заготовки
2.2Расчёт станочного приспособления
2.3Выбор и расчёт контрольного приспособления
3Организационный раздел
3.1Расчёт потребного количества оборудования
3.2Расчёт площади производственного участка
3.3Расчёт численности персонала
Перечень графического (иллюстративного) материала:
Приспособление (А1);
Схема контроля (А2);
Наладки операционные (А1);
Планировка участка (А1);
Дата выдачи и получения задания
5 ОГТИ_ВКР_КлименковВА_З-17КОМП(ба)ТМ.docx
В настоящее время машиностроение является основой экономики всех стран и играет решающую роль в создании материально технической структуры хозяйства. Ему принадлежит важная роль в ускорении научно-технического прогресса. Машиностроение помогает обеспечить механизацию и автоматизацию производства за счет выпуска средств производства для разных сфер хозяйства в связи с этим данная тема является наиболее актуальной в нынешних условиях.
Целью работы является проектирование участка механического цеха по производству детали «Шестерня».
Задачами выпускной квалификационной работы являются: выбор вида заготовки; определение маршрута обработки; выбор и расчёт технологической оснастки; выбор и расчёт средств измерения (схема контроля); создание проекта участка механической обработки детали «Шестерня».
Технологическая часть
1 Анализ конструкции детали и требования к её изготовлению
Деталь «Шестерня» входит в состав привода механизм наклона конвертора «КВК-30Ц». Конвертор «КВК-30Ц» предназначен для получения черновой меди или никелевого Фанштейна путем продувки штейнов воздухом обогащённым кислородом. Конверторы нашли широкое применение на предприятиях черной и цветной металлургии для получения легированных сталей и сплавов получение цветных сплавов [1].
Деталь «Шестерня» изготовлена из легированной качественной стали 35ХМЛ ГОСТ4543-71. Сталь 35ХМЛГОСТ4543-71 применяется для изготовления таких деталей как оси вала шатуны зубчатые колеса валы экскаваторов муфты валы-шестерни шпиндели болты наживные винты рычаги штоки цилиндры полукольца и других ответственных деталей подвергающиеся вибрационным и динамическим нагрузкам и к которым предъявляются требованиям повышенной прочности и вязкости [2].Состав стали 35ХМЛ ГОСТ4543-71 приведен в таблице 1. Механические свойства приведены в таблице 2.
Таблица 1 – Химический состав стали 35ХМЛ ГОСТ4543-71 [2]
Таблица 2 – Механические свойства стали 35ХМЛ ГОСТ4543-71 [2]
Режим термообработки
гдет – предел текучести;
в – временное сопротивление разрыву (предел прочности при растяжении);
– относительное удлинение после разрыва;
– относительное сужение.
Наружная поверхность шестерни имеет диаметр 37909H14 с зубчатым венцом предназначенным для передачи крутящего момента выполняется с параметром шероховатости Ra125 мкм.
Шестерня имеет главное отверстие диаметром 180H12 посадочное в котором с одной стороны две фаски 3×45 и также одна фаска 2×45 данные отверстия с квалитетом точности 3. Также имеются шлицы для соединения шестерни с валом посредством шлицевого соединения.
К детали «Шестерня» предъявляются следующие технические требования:
– качество необрабатываемых отверстий по группе 3 по технологической инструкции отдела главного металлурга;
– допускаемые отклонения линейных размеров по 2 классу точности
ГОСТ 2009-55 (СТП 11388-75);
– шлицы проверить калибром;
– ось симметрии одного из пазов должна совпадать с осью симметрии одного из зубьев. Допускается смещение 1 мм;
– неуказанные предельные отклонения размеров обрабатываемых поверхностей отверстий – по А7 валов – по B7 остальных по СМ7;
– на поверхности Г допускаются черновины;
– на поверхности Д допускается технологическая выточка диаметр 210 мм глубиной до 2 мм;
– участок ВЖ на зубе выполнить по прямой параллельной оси зуба участок ЖЗ по радиусу R = 38 мм;
– поверхность Е проверить на станке. Изготовлять без припуска на механообработку;
– на поверхности зуба допускается без исправления рассеянные раковины глубиной до 2 мм общей площадью до 100 мм2 количество зубьев с указанными дефектами не более 3 кроме экспорта тропиков;
– литейные уклоны по длине зуба не более 30.
2 Технологический анализ конструкции детали
Анализ технологичности проводится по двум направлениям – качественным и количественным.
Качественный анализ.
Данная деталь типа шестерня материал – легированная качественная сталь 35ХМЛ ГОСТ4543-71 позволяющая шестерне передавать большие крутящие моменты редуктора.
С точки зрения механической обработки внутренних и наружных поверхностей деталь не вызывает труда так как все поверхности являются открытыми и не требуют специальных инструментов и оборудования.
На основании качественной оценки деталь считается технологичной.
Количественный анализ.
Обозначение поверхностей детали нумерацией – рисунок 1 таблица 3.
Рисунок 1 – Эскиз детали с обозначением поверхностей
Таблица 3 – Поверхности детали
Наименование поверхности
Шлицы поверхность 11
Фаска поверхность 12 2х45°
Фаска поверхность 13 3х45°
Коэффициент точности обработки детали (Kт) вычисляют по формуле [3 С.16]
Средний квалитет точности (ITср) вычисляют по формуле [3 С.16]
гдеIT – квалитет точности
ni – количество всех поверхностей шт.
Коэффициент шероховатости (Kш) вычисляют по формуле [3 С.16]
гдеШ – значение шероховатости i-той поверхности.
Данные расчеты доказывают что деталь технологична.
На основании проведенного количественного и качественного анализа доказано что деталь «Шестерня» является технологичной.
3 Определение типа производства и формы организации технологического процесса
Определение типа производства проводится табличным методом согласно ГОСТ 14.004-83 [3]. Тип производства является массовым.
Коэффициент закрепления операций показывает отношение числа всех технологических операций выполненных подразделением за месяц к числу рабочих мест коэффициент закрепления операций характеризует число технологических операций приходящихся на одно рабочее место за месяц.
Коэффициент закрепления операции (Kз.о.) вычисляют по формуле [3 С.16]
гдеПо – сумма чисел различных операций;
Pя – явка рабочих подразделений выполняющих разные операции;
Ф – месячный фонд работника в одну смену
Кв– коэффициент выполненных временных норм
NiTi– трудоёмкость выполнения i-ой операции.
Трудоёмкость выполнения операций представлена в таблице 4.
Таблица 4 – Технологический процесс заводского варианта
Наименование операции
Для массового типа производства согласно ГОСТ 3.11.0–74 k3.0. принимается равным [4 С.243]:
Важнейшей особенностью массового производстваявляется ограничение номенклатуры выпускаемых изделий что создает экономическую целесообразность широкого применения в конструкциях изделий унифицированных и взаимозаменяемых элементов тщательную разработку технологических процессов. Взамен универсальной оснастки применяют специальную. Оборудование на участке устанавливается с учетом точности процессов. Производительность выше а квалификация рабочих ниже чем в единичном производстве.
Выпуск изделий в сутки (Nc шт.) вычисляют по формуле [3 С.20]
где247 – численность рабочих дней в году.
Суточная производительность линии потока (Q) вычисляют по формуле [3 С.20]
гдеФс – действительный суточный срок работы оборудования (при двухсменном режиме работы 952 мин);
Tcp – средняя трудоемкость наиболее важных операций мин.
nз– коэффициент загрузки оборудования в крупносерийном и массовом производстве равен 065 – 075 [7 С.163].
Среднюю трудоёмкость важных операций (Tcp мин) вычисляют по формуле [3 С.20]
гдеТшт – штучное время основной операции мин;
По – численность основных операций (без учета операций точения фасок скруглений и др.).
После проведенных расчетов следует то что выпуск изделий в сутки больше суточной производительности линии потока при условии ее загрузки поэтому использование одно номенклатурной поточной линии целесообразно.
4 Выбор и обоснование вида заготовки и метода её изготовления
Заготовка должна быть выполнена из указанного на чертеже материала обладать соответствующими ему механическими свойствами также она не должна иметь внутренних дефектов.
Разработка технологического процесса изготовления детали Шестерня может идти по двум направления:
получение заготовок по форме и размерам готовой детали когда на заготовительные цеха приходится основная часть трудоёмкости и относительная часть на механические цеха.
получение грубой заготовки со значительными припусками когда на механические цеха приходится основная доля трудоёмкости и себестоимости изготовления.
Для детали Шестерня выполненной из стали 35ХМЛ ГОСТ4543-71 с учетом факта массового производства назначаются следующие варианты получение заготовки:
литье в песчано-глинистые формы. Этим методом получаются отливки массой до 250 тонн. Им характерна относительно простая форма имеют напуск для упрощения формы по сравнению с готовой деталью. Требуют значительной механической обработки.
литье в кокиль. Эти методом получаются отливки массой от нескольких граммов до 3 тонн весьма разнообразных и сложных форм значительно приближенных к формам готовой детали в связи с чем требует меньших затрат на обработку резанием.
Литье в песчано-глинистые формы.
класс размерной точности отливки 17 [4 С.430]
допуски размеров отливки 20мм
Расчет припуска ведется расчетно-аналитическим методом.
Припуск на поверхность детали (dпр мм) вычисляется по формуле [5 С.72]
гдеdпр – диаметр заготовки с припуском мм;
dдет – диаметр детали мм.
zтаб– табличное значение припуска мм.
Расчет припуска на шлифование:
Расчет припуска на чистовое точение:
Расчет припуска на черновое точение:
Полученные значения сводятся в таблицу 5.
Таблица 5 – размеры заготовки по заводскому варианту
Наружный диаметр заготовки
Выполняется построение эскиза согласно полученным значениям размеров заготовки (рисунок 2).
Рисунок 2 – Эскиз заготовки отливка по заводскому варианту
Коэффициент использования материала (Kи.м.) вычисляют по формуле [3 С. 40]
гдеmдет – масса детали кг;
mзаг– масса заготовки кг.
Массу заготовки (m кг) вычисляют по формуле [3 С.41]
гдеp – плотность стали
Объём (V мм3) вычисляют по формуле [3 С.41]
гдеVD– объём наружного диаметра см3;
Vd – объём внутреннего диаметра см3.
Объём наружного диаметра (VD мм3) вычисляют по формуле [4 С.361]
Полученное значение объёма (V мм3) переводят в систему СИ (м3)
V= 24 366 395569 = 00024366395569
Стоимость заготовки (Sзаг руб) вычисляют по формуле [3 С.40]
гдеS – цена за 1 кг материала заготовки руб;
Sотх – цена за 1 тонну отходов руб.
Расчет припуска ведется расчетно-аналитическим методом. Величина припуска на механическую обработку определяется согласно ГОСТ 26645-85.
Определение припуска на обработку наружных диаметров.
Расчёт припуска на черновое точение:
Расчёт припуска на чистовое точение:
Определение припуска на обработку внутренних диаметров.
Определение припуска на обработку торцов.
Определение припуска на фрезерование зубьев.
Расчёт припуска на шлифование:
Полученные значения сводятся в таблицу 6.
Таблица 6 – размеры заготовки по проектному варианту
Выполняется построение эскиза согласно полученным значениям размеров заготовки (рисунок 3).
Рисунок 3 – Эскиз заготовки по проектному варианту
Объём (V мм3) рассчитан программой «Компас 3Д» [10 С.41] и равен:
Стоимость заготовки (Sзаг руб.) вычисляют по формуле [3 С.40]
Экономию (ΔS руб.) вычисляют по формуле [3 С.41]
гдеSзаг1 Sзаг2 – стоимость заготовок представленных для сравнения руб.
Разница в стоимости изготовления заготовок данными методами составила 1170000 рублей.
Полученные значения для обоих способов получения заготовок сводятся в таблицу 7.
Таблица 7 – Обоснования выбора данного метода получения заготовки
Способ получения заготовки
Стоимость 1 тонны заготовок
Стоимость 1 тонны отходов
Стоимость заготовок руб.
Экономия по стоимости
На основании таблицы следует то что наилучшем вариантом получения заготовки будет литье в кокиль.
Экономическую эффективность с учетом годовой программы (Ф) вычисляют по формуле [3 С.41]:
Экономию металла с учетом годового выпуска (Q кг) вычисляют по формуле [3 стр 41]:
Таким образом метод получения заготовок литьём в кокиль дешевле метода литья в песчано-глинистые формы на 11 %. Экономическая выгода в год составила по стоимости 1170000 рублей по использованию материала 40820 кг.
5 Проектирование технологического маршрута обработки
Разработка последовательности обработки поверхностей. Операционный технологический процесс представлен в таблице 8.
Таблица 8 – Операционный технологический процесс
поз. 2 поз. 3 поз. 4 поз. 10.
Точить торцы: поз. 5.
Токарный станок модель 16А20Ф3
Патрон трехкулачковый ГОСТ 2675-80 Инструмент резец ГОСТ 10044-73
Штангенциркуль ГОСТ 166-89
поз. 2 поз. 3 поз. 4 поз. 9.
поз. 2 поз. 3 поз. 4 поз. 10
поз. 2 поз. 3 поз. 4 поз. 9
Продолжение таблицы 8
Горизонтально-протяжная
Горизонтально-протяжной станок модель 7534
Протяжка шлицевая ГОСТ 25158-82
шлицевых отв. ГОСТ 24969-81
Универсально-фрезерная
Универсально-фрезерный станок модель 6Р82Ш
Патрон самоцентрирующий с пневмоприводом ГОСТ52869-2007
Пальцевая модульная фреза ГОСТ 1643
6 Расчет режимов обработки с нормированием технологического процесса
Подробный расчёт для операций: токарно-карусельной (черновой) токарно-карусельной (чистовой) с ЧПУ горизонтально протяжной фрезерной шлифовальной.
Операция 005 токарная (черновая).
Токарный станок с ЧПУ 16А20Ф3
Паспорт используемого станка представлен в таблице 9.
Таблица 9 - Паспорт станка 16А20Ф3
Диаметр обработки над станиной мм
Максимальная длина заготовки мм
Диаметр обработки на суппортом мм
Наибольший поперечный ход суппорта мм
Наибольший продольный ход суппорта мм
Максимальная скорость продольной подачи мм
Пределы частот вращения шпинделя мин-1
Продолжение таблицы 9
Мощность электродвигателя привода главного движения кВт
Габаритные размеры мм:
Самоцентрирующий 3-х кулачковый патрон [6].
Резец проходной упорный для черновой обработки Т5К10 ГОСТ 26611-85 [6]. Геометрические параметры:
главный угол в плане 90
форма пластины трёхгранная
вспомогательный угол в плане 10
радиус при вершине 1
угол наклона главной режущей кромки 0
Штангенциркуль ГОСТ 66–80 [6].
Установить крепить выверить.
Расчёт режимов резания.
Точить поверхность 4.
Глубина резания определяется согласно таблицы [3 С.106]
Исходя из выбранной глубины резания и размеров заготовки подача определяется по паспорту станка - Sпасп = 056 ммоб.
Скорость резания (V ммин) вычисляют по формуле [3 С.92]
гдеCv = 350 [3 С.105];
T = 60 мин для одноинструментальной обработки;
kv коэффициент учитывающий различные факторы влияющие на скорость резания.
Коэффициент факторов скорости резания (Кv) вычисляют по формуле [3 С.93]
kv = kv · kuv · kφv · kφ1v · krv · knv.
Коэффициент (Кmv) вычисляют по формуле [3 С.93]
гдеkr = 07 [3 стр 106];
Значения коэффициентов [3 С.106]:
kv = 07 · 1 · 09 · 1 · 094 · 08 = 05
Частоту вращения планшайбы (n обмин) вычисляют по формуле [3 С.96]
Уточнение nym по паспорту до ближайшего меньшего числа принимается
Действительную скорость резания (Vd ммин) вычисляют по формуле [3 С.96]
Проверку по мощности (Pz Н) выполняют по формуле [3 С.98]
гдеСpz=300[3 С.101];
Коэффициент (Кpz) вычисляют по формуле [3 С.103]
kpz = kp · kφp · kγp · krp · kλp.
Коэффициент (Кuv) вычисляют по формуле:
Значения коэффициентов [3 С.106]
kpz = 1 · 1 · 11 · 1 · 093 = 1023
Pz = 10 · 300 · 31 · 056075 · 70-015 ·1023 = 31642
где[Pmax] максимальная осевая сила резания допускаемая механизмом подач станка из паспорта станка кН.
2 условие выполняется.
Проверку скорости резания по мощности (Nрез кВт) выполняют по формуле [3 С.107]
Сравнение (Nрез кВт) со станочной (Nст кВт)
гдеNэд мощность электродвигателя по паспорту станка
Необходимо выполнение условия Nрез ≤ Nст.
5 30 условие выполняется.
Машинное время (Т0 мин) вычисляют по формуле [3 С.108]
гдеLр.х. длина рабочего хода мм;
Величина перебега (y мм) вычисляется по формуле [3 С.108]
Число переходов i = 1.
Lр.х. = 206 + 2 + 1732 = 2097
Вспомогательное время на установку и снятие детали принимают по таблице 103 [3]; вспомогательное время на управление станком по таблице 106; вспомогательное время на контрольные измерения по таблице 107.
Норма времени (Тшт мин) определяется по формуле [3 С.108]
где – коэффициент определяющий соответственно время технического организационного обслуживания и время на отдых.[1]
Штучно-калькуляционное время определяется по формуле [3 С.108]
где – коэффициент [1]
Таким образом норма штучного времени составляет 278 мин. норма штучно-калькуляционного времени – 681 мин.
Операция 020 токарная (чистовая) с ЧПУ.
Токарный станок 16А20Ф3. Паспорт используемого станка представлен в таблице 10.
Патрон самоцентрирующий с пневмоприводом ГОСТ52869-2007.
Режущий инструмент резец твёрдосплавный Т15К6 с углом φ = 93о.
Штангенциркуль ГОСТ 166-70.
Точить поверхность 4
Снять фаску поверхность 13
Точить поверхность 10
Точить поверхность 2
Точить поверхность 3
Точить поверхность 5
Снять фаску поверхность 14
Точить поверхность 11
Глубина резания определяется согласно таблиц и составляет t =25 мм [3 С.106].
Исходя из выбранной глубины резания и размеров заготовки назначается предварительная подача S = 0246 ммоб .
Уточнение подачи по паспорту до ближайшего меньшего значения - Sпасп = 020 ммоб
гдеCv =420 [3 С.108];
T = 60 мин с неперетачиваемой твёрдосплавной пластинкой;
Коэффициент факторов скорости резания (Kv) вычисляют по формуле [3 С.93]
kv = kv · kuv · kφv · kφ1v · krv ·knv
гдеkr = 07 [3 С.108];
kv = 07 · 1 · 07 · 097 · 094 ·08 = 036
Частоту вращения планшайбы (nобмин) вычисляют по формуле [3 С.96]
Уточнение nут по паспорту до ближайшего числа принимается
гдеСpz = 300 [3 С.107];
гдеnp = 075 [3 С.108].
kpz = 1 · 089 · 10 · 093 · 10 = 182
Pz = 10 · 300 · 251 · 02075 · 754-015 ·182 = 20411
где [Pmax] максимальная осевая сила резания допускаемая механизмом подач станка из паспорта станка
5 44 условие выполняется.
i = 1 число переходов.
Lр.х. = 164 + 2 + 0 = 166
Вспомогательное время на установку и снятие детали принимают по таблице 103 [3]; вспомогательное время на управление станком по таблице 106; вспомогательное время на контрольные измерения по таблице 107:
Таким образом норма штучного времени составляет 1153 мин. норма штучно-калькуляционного времени – 2406 мин.
Операция 030 протяжная.
Горизонтально-протяжной станок модели 7534.
Паспорт используемого станка представлен в таблице 10.
Таблица 10 Паспорт станка
Номинальная тяговая сила кН
Количество плунжеров шт.
Длина рабочего хода мм
Скорость рабочего хода ммин
Скорость обратного хода
Мощность электродвигателя кВт
Калибр для контроля шлицевых отверстий ГОСТ 24969-81.
Установить крепить вымерить.
Протянуть отверстие диаметром 180 мм.
Эскиз обработки детали показан на рисунке 4.
Рисунок 4 Эскиз обработки
Расчёт режимов резания
Выбор технологической подачи (S мм)
Уточнение подачи по паспорту до ближайшего меньшего значения –
Проверку прочности механизма подач (P0 кН) выполняют по формуле [3 С.93]
Pо = 10 · Cp · Dq · Syp · kp
гдеnp = 075 [3 стр 108];
Pо = 10 · 67 · 25 · 028065 · 1=7323Н 7
гдеPдоп максимальная осевая сила допускаемая механизмом подач станка из паспорта станка;
Проверку хвостовика на прочность при растяжении (Mp Нм) выполняют по формуле:
Mp = 10 · Cm · Dq · Sy · km.
Мр = 10 · 009 · 251 · 02808 · 1 = 813.
Прочность ( мПа) вычисляют по формуле [3 С.93]
гдеWр полярный момент инерции опасного сечения протяжки мм3.
Полярный момент инерции опасного сечения протяжки (Wр мм3) вычисляют по формуле
где допускаемое напряжение для конструкционных сталей
Напряжение стали ( мПа) вычисляют по формуле:
35 условие выполняется.
Скорость резания вычисляют по формуле (V ммин) [3 С.92]
kv = kmv · kuv · knv · klv
гдеkmv коэффициент учитывающий влияние материала заготовки.
Значения коэффициентов:
kuv коэффициент учитывающий влияние материала режущей части сверла
knv коэффициент учитывающий влияния состояния поверхности заготовки
klv коэффициент учитывающий глубину обрабатываемого отверстия
kv = 07 · 1 · 08 · 1 = 056
Мощность резания (Nрез кВт) вычисляют по формуле [3 С.98]
Сравнение(Nрез кВт) со станочной (Nст кВт)
гдеNэд мощность электродвигателя по паспорту станка
5 224 условие выполняется
гдеi = 4 число переходов.
Lр.х. = 27 + 2 + 15 = 197
Таким образом норма штучного времени составляет 81 мин. норма штучно-калькуляционного времени – 5783 мин.
Операция 035 универсально-фрезерная.
Универсально фрезерный станок модели 6Р82Ш.
Паспорт используемого станка представлен в таблице 11.
Таблица 11 – Паспорт станка
Параметры паспортных
Размеры рабочей поверхности стола (длина х ширина) мм
Наименьшее и наибольшее расстояние от торца шпинделя до стола мм
Расстояние от оси шпинделя до хобота мм
Расстояние от торца шпинделя поворотной головки до стола мм
Расстояние от оси шпинделя поворотной головки до направляющих станины (вылет) мм
Наибольшее перемещение стола продольное механическое ручное мм
Наибольшее перемещение стола поперечное механическое ручное мм
Наибольшее перемещение стола вертикальное механическое ручное мм
Максимальная нагрузка на стол (по центру) кг
Число ступеней рабочих подач стола
Пределы рабочих подач. Продольных и поперечных мммин
Частота вращения шпинделя поворотной и накладной головок обмин
Количество скоростей шпинделя
Частота вращения шпинделя обмин
Продолжение таблицы 11
Наибольший крутящий момент на шпинделе Н.м
Допустимый диаметр фрез при черновой обработке. Горизонтальный вертикальный шпиндель мм
Электродвигатель привода главного движения кВт
Электродвигатель привода шпинделя поворотной головки кВт
Габариты станка (длина х ширина х высота) мм
Пальцевая модульная фреза ГОСТ 1643.
Установить крепить выверить. Нарезать зубья фрезерованием.
Эскиз обработки детали показан на рисунке 5.
Рисунок 5 – Эскиз обработки
Расчет режимов резания.
Сдвиг в направлении врезания зуба фрезы ( Lфр мм) вычисляют по формуле [3 С.108]
Определение глубины фрезерования (t мм) и ширины фрезерования (В мм)
Минутная подача (Sм) находится в следующем соотношении [3 С.124]
гдеSn – подача на один оборот фрезы;
n – частота вращения фрезы;
Z – число зубьев фрезы.
Величину подачи на один зуб (Sz мм) вычисляют по формуле [3 С.125]
Частоту вращения инструмента (n обмин) вычисляют по формуле [3 С.96]
Силу резания (Pz Н) вычисляют по формуле [3 С.103]
Мощность резания (Nрез кВт) вычисляют по формуле [3 С.107]
гдеL – расчетная длина обработки (L мм).
y – врезание при фрезеровании(у мм).
Таким образом норма штучного времени составляет 2497 мин. норма штучно-калькуляционного времени – 4048 мин.
Значения норм времени сводятся в таблицу 12.
Таблица 12 – Значения норм времени
Операция 005 Токарная черновая
Операция 010 Токарная черновая
Операция 020 Токарная чистовая
Операция 025 Токарная чистовая
Продолжение таблицы 12
Операция 030 Горизонтально-протяжная
Протянуть шлицы пов. 10 11.
Операция 035 Универсально-фрезерная
Фрезеровать зубья пов. 1
Шлифовать зубья пов. 1
Конструкторская часть
1 Базирование заготовки
Схема обработки шестерни (таблица 13) выбирается исходя из анализа конструкционных и технологических требований зависящих от типа детали и производства.
Таблица 13 – Технологическая схема изготовления шестерни
Технологическая база
Токарная ЧПУ (черновая)
Токарная ЧПУ (чистовая)
2 Расчёт станочного приспособления
Выполняется построение операционного эскиза (рисунок 6).
Рисунок 6 – Эскиз заготовки
Вид и материал заготовки – отливка сталь 35ХМЛ ГОСТ4543-71.
Вид обработки – черновая.
Материал и геометрия режущей части инструмента – резец расточной из Т15К10 φ=93о; γ=-3о; λ=+5о.
Режимы резания: глубина t=18мм подача S=056ммоб.
Коэффициент факторов скорости резания (Кv) вычисляют по формуле[3 С.93]
Металлорежущий станок – 16А20Ф3 (наибольший диаметр патрона – 200 мм.
kφp = 089; kγp = 10; krp = 093; kλp = 10.
Кру = 1.077.14.125 = 13475
Pz = 10 · 300 · 251 · 02075 · 754-015 ·182 = 20411
Pу = 10 · 243 · 309 · 04506 · 172-03 ·13475 = 854.
Расчёт усилий зажима.
В процессе обработки заготовки на нее воздействует система сил. С одной стороны действует составляющие силы резания с другой – сила зажима препятствующая этому. Из условия равновесия моментов данных сил и с учетом коэффициента запаса определяются необходимые зажимное и исходное усилия.
Суммарный крутящий момент от касательной составляющей силы резания стремящейся провернуть заготовку в кулачках равен
Повороту заготовки препятствует момент силы зажима (Мз’) которые определяются по формуле [3 С. 125]
Из равенства Мр’ и Mз’ определяется необходимое усилие зажима препятствующее повороту заготовки в кулачках (W Н)
Сила Ру стремится вывернуть заготовку из кулачков.
Данному моменту препятствует момент от силы зажима
Необходимая сила зажима равна
где d2=382мм Pу=854Н f=04 l=2527мм К=252
Для дальнейших расчетов принимается наихудший случай
Величина усилия зажима W1 прикладываемая к постоянным кулачкам
несколько увеличивается по сравнению с усилием W и рассчитывается по формуле [3 С. 126]
f – коэффициент трения в направляющих постоянного кулачка и корпуса;
вс - толщина сменного кулачка
вк+вз=20+30=50мм - толщина постоянного кулачка;
Вк - ширина направляющей постоянного кулачка
В1 - ширина сменного кулачка
Исходные данные подставляются в формулу.
Расчёт зажимного механизма патрона.
Приступая к расчету зажимного механизма необходимо определиться с его конструкцией. В самоцентрирующих механизмах установочные элементы (кулачки) должны быть подвижными в направлении зажима и закон их относительного движения необходимо выдержать с высокой точностью. Поэтому на движение кулачков накладываются условия: разнонаправленность одновременность и равная скорость движения. Данное условие можно выдержать обеспечивая движение трех кулачков от одного источника движения.
В кулачковых патронах наибольшее применение получили рычажные и клиновые зажимные механизмы движение которым передается центральной втулкой связанной с силовым приводом.
Рычажный механизм представляет собой неравноплечий угловой рычаг смонтированный в корпусе патрона на неподвижных осях и которые своими сферическими концами входит с посадкой в пазы постоянного кулачка и центральной втулки.
При расчете зажимного механизма определяется усилие (Q Н) создаваемое силовым приводом которое зажимным механизмом увеличивается и передается постоянному кулачку [3 C. 142]
где iс – передаточное отношение по силе зажимного механизма
Данное отношение для рычажного механизма (ie) равно [3 C. 127]
где А и Б – плечи рычага
На этапе расчета наружный диаметр патрона определяется по формуле:
Дп =382+2.80=542 мм.
Так как Дп>200мм выбирается рычажный зажимной механизм с iс=2.
Расчёт силового привода.
Для создания исходного усилия Q используется силовой привод устанавливаемый на задний конец шпинделя. В его конструкции можно выделить силовую часть вращающуюся совместно со шпинделем и муфту для подвода рабочей среды. В качестве приводов наибольшее применение получили пневматические и гидравлические вращающиеся цилиндры.
Следует попытаться применить пневматический привод так как в любом производстве имеются трубопроводы для подачи сжатого воздуха.
Диаметр поршня пневмоцилиндра (D мм) вычисляют по формуле [3 C. 142]
где Р – избыточное давление воздуха. Р = 04 МПа.
В конструкции станка 16А20Ф3 можно встроить силовой привод с диаметром поршня не более 120мм. Если при расчете по формуле диаметр получится более 120 мм то следует применять гидравлический привод где за счет регулирования давления масла можно получить большие исходные усилия. При заданном усилии Q подбирается давление масла (Рг = 1; 25; 5; 75 МПа) чтобы диаметр поршня не превышал 120мм.
Для гидроцилиндра. При Рг=1МПа
Принимается D=120мм.
Ход поршня цилиндра (SQ мм) вычисляют по формуле:
где Sw – свободный ход кулачков. Sw=5мм
Передаточное отношение зажимного механизма по перемещению (in) равно [3 С. 143]
Расчет погрешности установки заготовки в приспособление.
Погрешность установки (у мм) определяется по формуле [3 C. 143]
где – погрешность базирования равная нулю так как измерительная база используется в качестве технологической.
з – погрешность закрепления – это смещение измерительной базы под действием сил зажима. з=0
пр – погрешность элементов приспособления зависящая от точности их изготовления.
где 1 3 – погрешности возникающие вследствие неточности изготовления размеров А1 и А3
4 6 – погрешности из-за колебания зазоров в сопряжениях
– погрешность появляющаяся из-за неточности изготовления плеч рычага.
Z=0.0315; y Z; 00200315. Условие выполняется.
3 Выбор и расчёт контрольного приспособления
Для шлицевого соединения с прямобочным профилем зубьев выбирается вид центрирования посадки и размер b по ГОСТ 1139-80 [3 C. 132].
где Z - число зубьев
d - внутренний диаметр с полем допуска отверстия H12?
D - наружный диаметр с посадкой H9
b - ширина зуба с посадкой H8?
При центрировании по наружному диаметру D технология изготовления шлицевых деталей проще чем при центрировании по d так как твёрдость шлицевой втулки доступна для калибрования инструментами из быстрорежущих сталей
По ГОСТ 25346-82 определяют верхние и нижние отклонения размеров шлицевого отверстия
верхнее отклонение центрирующего диаметра 200 ESD= +25 мкм;
нижнее отклонение центрирующего наружного диаметра 200H9 ;
верхнее отклонение ширины шлицевого паза 30H8 мкм;
нижнее отклонение ширины шлицевого паза 30H8 мкм;
верхнее отклонение нецентрирующего внутреннего диаметра 180H12 мкм;
нижнее отклонение нецентрирующего внутреннего диаметра 180H12 .
Шлицевое соединение как правило контролируется проходными калибрами. При этом поэлементный контроль осуществляется непроходными калибрами. При использовании калибров отверстие считается годным если калибр-пробка проходит а диаметры и ширина паза не выходят за установленные верхние пределы.
Допуски калибров определяются по ГОСТ 7951-80:
ZD=7 мкм – расстояние от середины поля допуска на изготовление калибра-пробки по наружному диаметру до наименьшего предельного наружного диаметра втулки;
HD = 4 мкм – допуск на изготовление калибра-пробки по центрирующему диаметру D;
YD=13 мкм – допустимый выход размера изношенного калибра-пробки за границу поля допуска втулки по наружному диаметру;
Zb=12 мкм – расстояние от середины поля допуска на изготовление калибра-пробки по ширине шлица до наименьшего предельного размера ширины шлицевого паза отверстия;
Нb= 4 мкм – допуск на изготовление калибра-пробки по ширине шлица;
Yb = 18 мкм – допустимый выход размера изношенного калибра-пробки за границу поля допуска втулки по ширине шлицевого паза.
В соответствии с ГОСТ 25346-82 для центрирующего внутреннего диаметра определяют величину допуска калибра-пробки: H10=199 мм.
Наибольший предельный размер ширины шлица шлицевой калибр-пробки (bmax мм) вычисляется по формуле [3 С.118]
Наибольший предельный внутренний диаметр шлицевой калибр-пробки (dmax мм) вычисляется по формуле [3 С.118]
Исполнительные размеры шлицевой калибр-пробки: наружный диаметр 199995–0004 мм; внутренний диаметр 1799–0033 мм; ширина шлица 2999–0004 мм. Схема полей изображена на рисунке 7.
Рисунок 7 – Схема полей допусков шлицевой калибр-пробки на диаметр 200
Чертёж шлицевой калибр-пробки (рисунок 8) оформляется по всем требованиям ГОСТ ЕСКД. Конструкция и основные размеры этих калибров определяются по ГОСТ 24960-81 технические требования по ГОСТ 24959-81.
Рисунок 8 – Шлицевая калибр-пробка на диаметр 200
Организационный раздел
1 Расчёт потребного количества оборудования
Расчетное количество станков (Ср) на каждой операции определяется по формуле (98):
Количество станков для серийного производства (Срасч шт) вычисляют по формуле [5 С. 58]:
где Т – трудоемкость производственной программы час (рассчитывается по формуле 1.8)
Квн – коэффициент выполнения норм на участке (принимается от 11 до 12)
Трудоёмкость производственной программы (Т час) [5 С. 59]
Коэффициент загрузки оборудования (Кз) вычисляют по формуле [5 C. 60]
где Срасч – расчётное количество оборудования;
Спр – принятое количество оборудования.
Операция 005 Токарная с ЧПУ.
Срасч = 3823 принимается Спр = 4 штуки станков.
Операция 010 Токарная с ЧПУ.
Срасч = 2132 принимается Спр = 3 штуки станков.
Операция 020 Токарная с ЧПУ.
Срасч = 0962 принимается Спр = 1 штуку станков.
Операция 025 Токарная с ЧПУ.
Срасч = 0659 принимается Спр = 1 штука станков.
Операция 030 Горизонтально-протяжная.
Срасч = 0324 принимается Спр = 1 штука станков.
Операция 035 Универсально-фрезерная.
Срасч = 1667 принимается Спр = 2 штуки станков.
Процент загрузки оборудования (Пзср %) определяется по формуле [3]
Пз = 084 100% = 84%.
Таким образом можно сделать вывод что оборудование используется эффективно.
В таблице 15 сведены все необходимые данные по выбранному и рассчитанному оборудованию.
Таблица 15 – Расчет потребного количества оборудования
Наименование и модель станка
Расчетное число станков
Принятое количество оборудования Спр
Коэффициент загрузки станка
Средний коэффициент загрузки
Продолжение таблицы 15
Горизонтально протяжной станок 7534
Универсально фрезерный станок 6Р82Ш
Так же на участке организовывается заточное и ремонтное отделение количество станков заточного отделения составляет 5 процентов от числа станков основного отделения ремонтного 3 процента.
Следовательно общее количество станков (Собщ) цеха составит согласно формуле (7)
Собщ = Со + Сзат + Срем
где Со – число станков основного производства;
Сзат – количество станков заточного отделения;
Срем – количество станков ремонтного производства.
Расчет стоимости производственного оборудования по всем операциям производится в таблице 16.
Таблица 16 – Стоимость производственного оборудования.
транспорта и монтажа
Горизонтально-протяжной станок
Универсально-фрезерный станок
2 Расчёт площади производственного участка
В состав механического цеха входят станочное отделение вспомогательные отделения и складские помещения к числу которых можно отнести:
заготовительное отделение;
ремонтное отделение;
мастерскую энергетика цеха;
отделение для приготовления и раздачи смазочно-охлаждающих жидкостей;
цеховой склад материалов и заготовок;
межоперационный склад;
инструментально-раздаточную кладовую;
склад приспособлений;
склад абразивного материала.
Размер станочного отделения при укрупненных расчетах определяется через среднюю величину удельной площади для станков различных размеров с учетов прохода и проездов. В среднем величина Sуд составляет для малых станков 10-12 м2 для средних станков 15-25 м2 для крупных станков 30-45 м2 для особо крупных и уникальных станков 50-150 м2
Учитывая количество станков проектируемого цеха которые входят в станочное отделение площадь данного отделения (Sст м2) определяется по формуле [3]
где Спр – принятое количество станков на участке;
Sуд – удельная площадь на один станок.
Площадь заготовительного отделения определяется в расчёте 25-30м2 на 1 станок учитывая количество станков заготовительного (Sзаг м2) отделения и рассчитывается по формуле [3]
где Sзаг.уд – удельная площадь на один станок.
Sзаг = 12 275 = 330.
Общая площадь заточного отделения определяется из расчетов 10-12м2 на 1 с учетом количества станков (Sзат м2) и определяется по формуле [3]
где Sзат.уд – удельная площадь на один станок.
Площадь ремонтного отделения определяется из расчётов 25-30м2 на основной станок. Общая площадь данного отделения с учетом количества станков (Sрем м2) определяется по формуле [3]
где Sрем.уд – удельная площадь на один станок.
Sрем = 12 275 = 330.
Площадь службы энергетика цеха составляет приблизительно 30% от всей площади ремонтного отделения (Sэн м2) и определяется по формуле [3]
Sэн = 30% 1925 = 5775.
Отделение для приготовления и раздачи смазочно-охлаждающей жидкости и склада масел. Площадь данного отделения может быть определенна в зависимости от количества производственного оборудования. При количестве оборудования менее 60 единиц – площадь данного отделения составляет 40-50м2. Площадь цехого склада масел составляет 10-20м2.
Принимается Sсож = 45м2 Sмасел = 15м2.
Площадь инструментально раздаточной кладовой (Sирк м2) определяется из расчёта на 1 металлорежущий станок цеха при работе в 1 смену в зависимости от вида производства для крупносерийного принимается 03м2 и определяется по формуле [3]
где Sрем.уд – удельная площадь на один станок на 1м2.
Площадь склада приспособлений (Sсклад м2) принимается равной для
единичного производства 05м2 мелкосерийного 04 м2 серийного м2
крупносерийного 02 м2 массового 01 м2 и определяется по формуле [3]
где Sрем.уд – удельная площадь на один станок принимается 04м2.
Площадь кладовых для абразивов (Sабр м2) (шлифовальных заточных и полировальных кругов) принимается из расчета 04м2 на 1 шлифовальный заточной или поправочный станок и определяется по формуле [3]
Sабр = Cшлиф Sабр.уд
где Sабр.уд – удельная площадь на один шлифовальный заточной или поправочный станок принимается 04м2;
Cшлиф – количество шлифовальных заточных и поправочных станков.
Рассчитав площадь всех необходимых складовых помещений определяется общая площадь складов (Sск.общ м2) по формуле [3]
Sск.общ = Sирк + Sс.п + Sабр
Sск.общ = 36 + 48 + 04 = 53.
Площадь склада материалов заготовок межоперационных и готовых деталей (Sз.д м2) равна 10 % от площади станочного отделения для каждого склада общий процент площади от складов составляет 30% от площади станочного отделения и определяется по формуле [3]
Sз.д = 30% 140 = 42.
Также в общую площадь цеха входит площадь занимаемая контрольно-разметочными плитами будками мастеров и санузлами необходимо предпринять дополнительную цеховую площадь. Площадь контрольного отделения составляет 3-5 % от площади станочного отделения. В проектируемом цехе предусматривается площадь занимаемая двумя санузлами по 8м2 каждый. Размер дополнительной площади цеха (Sдоп м2) определяется по формуле [3]
где Sкон – площадь контрольного отделения (определяется по формуле ?);
Sсан – площадь санузла (принимается 16м2).
Общая площадь цеха (S м2) представляет из себя сумму рассчитанных отделений и определяется по формуле [3]
S = Sст + Sзаг + Sзат + Sрем + Sэн + Sсож + Sмасел + Sск.общ + Sз.д + Sдоп
S = 120 + 330 + 132 + 330 +5775 + 53 + 42 + 896 = 110665.
2.2. Определение длины пролета
Общие размеры цеха определяются на основе планирования оборудования и всех помещений цеха. Размеры зданий состоящих из нескольких пролетов определяют по размеру и числу пролётов. Размеры пролетов для отдельных цехов. В зависимости от рода машиностроения и вида работ принимается для механической обработки и сборки цехов 18 24 30 и 36 м принимается 24 м. Длину пролета (L м) можно определить отношением общей цеховой площади (S) к суммарной ширине пролетов по формуле [3]
Общая длина цеха должна быть кратна величине шага колон которые для всех цехов и размеров пролетов принимаются 12 или 6 м. Если длина цеха по планировке не получилась кратна величине шага колон необходимо ввести поправку в планировку за счет увеличения или уменьшения размеров участка расположенных вдоль оси пролета.
Выполняется проверка кратности (Кр) длины пролета (L м) к шагу колон (Шк) принимается 12 [3]
Из результата следует что длина пролета не кратна шагу колон из чего принимается решение уменьшить длину пролёта до ближайшего кратного числа принимается L = 48 м условие выполняется.
Высота пролёта цеха определяется из размеров изготавливаемой продукции габаритов оборудования конструкции мостовых кранов а так же санитарных и гигиенических требований.
При определении высоты следует учитывать санитарно-гигиенические требования согласно которых на одного рабочего должно приходится не менее 15 м3 объёма помещения и не менее 45 м2 площади высота производственных помещений должна быть менее 32 м от пола до потолка а высота от пола до выступающих частей конструкции здания не менее 26 м.
Высота производственных помещений зависит от ширины пролетов чем шире пролет тем больше должна быть его высота. При малой высоте и большой ширине пролета получается недостаточная освещенность помещения.
Высота помещений (h) от пола до низа несущих конструкций в зданиях с мостовыми кранами следует назначать: для пролетов до 18 и 24 метра – 84 м; 96 м; 108 м. Принимается 96 м. Высота помещений от верха консолей для пролетов 18 и 24 метра – 46м; 54м; 66м. Принимается 54м.
Действительная производственная площадь (Sдест м2) определятся по формуле [3]
где l – ширина пролета.
Sдейст = 48 24 = 1152.
Объём здания (V м3) определяется по формуле [3]
где h – высота производственного помещения.
Стоимость здания (Цзд руб) определяется по формуле [3]
где р – стоимость одного квадратного метра здания руб. (29704).
Цзд = 1152 29704 = 34219008.
В качестве подъемно-транспортного оборудования в проектируемом цехе служат мостовые краны и тележки с различными грузоподъемностями в зависимости от массы транспортируемых на данном участке цеха заготовок и деталей.
Количество подъемных кранов укрупнено можно принять из расчета один кран на 40-80 м длины пролета.
Тоннажность кранов подбирается согласно максимальной массы оборудования. Это выполняется для проведения демонтажа и последующего ремонта вышедшего из строя оборудования.
Наибольшую массу имеет горизонтально-протяжной станок 7534 – 5200 килограмм следовательно стоит подобрать мостовой кран по второй группе грузоподъёмности (5-50 тонн) принимается кран с грузоподъёмностью 8 тонн.
3 Расчёт численности персонала
Общее количество участвующих в работе проектируемого цеха составляют:
производственные рабочие главным образом станочники;
вспомогательные рабочие;
младший обслуживающий персонал (МОП);
служащие инженерно-технические рабочие (ИТР) и счетно-конторский персонал (СКП).
Исходя из принятого количества станков (Спр) количество производственных рабочих (станочников) определяется по формуле (24):
гдеРст – количество рабочих-станочников чел.;
Спр – принятое количество станков ед.;
Кз – коэффициент загрузки станков;
Fд – действительный годовой фонд времени станка час;
Км – коэффициент многостаночности;
Fдp – действительный годовой фонд времени рабочего час.
Принимается Рст005 = 3 человека;
Принимается Рст010 = 2 человека;
Принимается Рст020 = 1 человек;
Принимается Рст025 = 1 человек;
Принимается Рст030 = 1 человек;
Принимается Рст035 = 1 человек;
На участке можно применять совмещение профессий. Это такое расширение трудовых функций рабочего при котором он выполняет функции двух или более профессий что обеспечивает наиболее полное использование рабочего времени приводит к повышению производительности труда.
Рассчитывают потребное количество инженерно-технических работников и младшего обслуживающего персонала. При этом должность мастера предусмотрена по нормативам если на 1 смену приходится свыше 15 чел. рабочих. На 1 старшего мастера должно приходиться не менее 40 рабочих и 1 сменный мастер. Начальник участка назначается если в его подчинении находится не менее 80 производственных рабочих. Уборщик принимается на производственное подразделение площадью не менее 400 .
Расчет состава работающих на участке производится в таблице 17.
Таблица 17 – Расчёт списочного состава работающих на участке
Наименование категорий работающих
Количество работающих чел.
Процент от основных и вспомогательных рабочих %
Продолжение таблицы 17
Вспомогательные рабочие:
Инженерно-технические работники (ИТР)
Младший обслуживающий персонал (МОП)
В выпускной квалификационной работе выполнен конструкционный анализ детали включая анализ служебного назначения детали и анализ технологичности конструкции. Определён тип производства.
Разработан проектный вариант технологического процесса изготовления детали «Шестерня» проведен анализ двух методов получения заготовок выполнен расчет припусков режимов резания и норм времени на две разнохарактерные операции.
Важным этапом проектирования является составление маршрутного технологического процесса обработки выбор оборудования режущего и мерительного инструмента станочных приспособлений. В результате проведенного анализа типового технологического процесса изготовления шестерни спроектированы такие технологические операции как: предварительно токарная обработка чистовая токарная обработка на станке с ЧПУ фрезерование зубьев протяжка шлицевого отверстия шлифование зубьев.
В ходе проведенной работы были решены поставленные задачи разработаны оптимальные условия обработки продумана эффективность в достижении лучшего результата с наименьшими материальными затратами.
Список использованных источников
Меринов В. П. Козлов А.М. Схиртладзе А.Г. М 522Технология изготовления деталей. Курсовое проектирование по технологии машиностроения: учебное пособие В. П. Меринов А. М. Козлов А. Г. Схиртладзе. – Старый Оскол: ТНТ 2009. – 264 с.
Справочник технолога машиностроителя. В 2-х т. С74 Т. 1Под ред. А.Г. Косиловой и Р.К. Мещярякова. – 4-е изд. перераб. И доп. – М.: Машиностроение 1986. 656 с. ил.
Технология машиностроения: Практикум и курсовое проектирование: учебное пособие для студентов среднего профессионального образованияА. И. Ильяников В. Ю. Новиков. – С.: Издательский центр “Академия” 2012. – 432 c.
Гоцеридзе Р.М. Процессы формообразования и инструменты: учебник для студ. учреждений сред. проф. образования Р.М. Гоцеридзе. – 7-е изд. перераб. и доп. – М.: Издательский центр «Академия» 2016. – 432 с. ISBN 978-5-4468-2799-2
Новиков В.Ю. Технология машиностроения: В 2 ч. Ч. 1 В.Ю. Новиков. - 4-е изд. стер. - М.: Академия ИЦ 2014. - 352 с. - (Профессиональное образование)
Типовые технологические процессы механической обработки зубчатых колес: Методические указания к курсовой работе по технологии машинострое-ния Сост. Н.Н. Ситов А.М. Пейсахов; СПбГТУРП: СПб. 2015 59 с.
Версия для антиплагита.docx
В настоящее время машиностроение является основой экономики всех стран и играет решающую роль в создании материально технической структуры хозяйства. Ему принадлежит важная роль в ускорении научно-технического прогресса. Машиностроение помогает обеспечить механизацию и автоматизацию производства за счет выпуска средств производства для разных сфер хозяйства в связи с этим данная тема является наиболее актуальной в нынешних условиях.
Целью работы является проектирование участка механического цеха по производству детали «Шестерня».
Задачами выпускной квалификационной работы являются: выбор вида заготовки; определение маршрута обработки; выбор и расчёт технологической оснастки; выбор и расчёт средств измерения (схема контроля); создание проекта участка механической обработки детали «Шестерня».
Технологическая часть
1 Анализ конструкции детали и требования к её изготовлению
Деталь «Шестерня» входит в состав привода механизм наклона конвертора «КВК-30Ц». Конвертор «КВК-30Ц» предназначен для получения черновой меди или никелевого Фанштейна путем продувки штейнов воздухом обогащённым кислородом. Конверторы нашли широкое применение на предприятиях черной и цветной металлургии для получения легированных сталей и сплавов получение цветных сплавов [1].
Деталь «Шестерня» изготовлена из легированной качественной стали 35ХМЛ ГОСТ4543-71. Сталь 35ХМЛГОСТ4543-71 применяется для изготовления таких деталей как оси вала шатуны зубчатые колеса валы экскаваторов муфты валы-шестерни шпиндели болты наживные винты рычаги штоки цилиндры полукольца и других ответственных деталей подвергающиеся вибрационным и динамическим нагрузкам и к которым предъявляются требованиям повышенной прочности и вязкости [2].Состав стали 35ХМЛ ГОСТ4543-71 приведен в таблице 1. Механические свойства приведены в таблице 2.
Таблица 1 – Химический состав стали 35ХМЛ ГОСТ4543-71 [2]
Таблица 2 – Механические свойства стали 35ХМЛ ГОСТ4543-71 [2]
Режим термообработки
Относительное удленение
Относительное сужение
Наружная поверхность шестерни имеет диаметр 37909H14 с зубчатым венцом предназначенным для передачи крутящего момента выполняется с параметром шероховатости Ra125 мкм.
Шестерня имеет главное отверстие диаметром 180H12 посадочное в котором с одной стороны две фаски 3×45 и также одна фаска 2×45 данные отверстия с квалитетом точности 3.Также имеются шлицы для соединения шестерни с валом посредством шлицевого соединения.
К детали «Шестерня» предъявляются следующие технические требования:
– качество необрабатываемых отверстий по группе 3 по технологической инструкции отдела главного металлурга;
– допускаемые отклонений линейных размеров по 2 классу точности ГОСТ 2009-55 (СТП 11388-75);
– шлицы проверить калибром;
– ось симметрии одного из пазов должна совпадать с осью симметрии одного из зубьев. Допускается смещение 1мм;
– неуказанные предельные отклонения размеров обрабатываемых поверхностей отверстий – по А7 валов – по B7 остальных по СМ7;
– на поверхности Г допускаются черновины;
– на поверхности Д допускается технологическая выточка диаметр 210мм глубиной до 2мм;
– участок ВЖ на зубе выполнить по прямой параллельной оси зуба участок ЖЗ по радиусу R=38мм;
– поверхность Е проверить на станке. Изготовлять без припуска на механообработку;
– на поверхности зуба допускается без исправления рассеянные раковины глубиной до 2мм общей площадью до 100мм2 количество зубьев с указанными дефектами не более 3 кроме экспорта тропиков;
– литейные уклоны по длине зуба не более 30.
2 Технологический анализ конструкции детали
Анализ технологичности проводится по двум направлениям – качественным и количественным.
Качественный анализ.
Данная деталь типа шестерня материал – легированная качественная сталь 35ХМЛ ГОСТ4543-71 позволяющая шестерне передавать большие крутящие моменты редуктора.
С точки зрения механической обработки внутренних и наружных поверхностей деталь не вызывает труда так как все поверхности являются открытыми и не требуют специальных инструментов и оборудования.
На основании качественной оценки деталь считается технологичной.
Количественный анализ.
Обозначение поверхностей детали нумерацией – рисунок 1 таблица 3.
Рисунок 1 – Эскиз детали с обозначением поверхностей
Таблица 3 – Поверхности детали
Наименование поверхности
Шлицы поверхность 11
Фаска поверхность 12 2х45°
Фаска поверхность 13 3х45°
Коэффициент точности обработки детали (Kт) вычисляют по формуле [3 С.16]
Средний квалитет точности (ITср) вычисляют по формуле [3 С.16]
гдеIT – квалитет точности
ni – количество всех поверхностей шт.
Коэффициент шероховатости (Kш) вычисляют по формуле [3 С.16]
гдеШ – значение шероховатости i-той поверхности.
Данные расчеты доказывают что деталь технологична.
На основании проведенного количественного и качественного анализа доказано что деталь Шестерня является технологичной.
3 Определение типа производства и формы организации технологического процесса
Определение типа производства проводится табличным методом согласно ГОСТ 14.004-83 [3]. Тип производства является массовым.
Коэффициент закрепления операций показывает отношение числа всех технологических операций выполненных подразделением за месяц к числу рабочих мест коэффициент закрепления операций характеризует число технологических операций приходящихся на одно рабочее место за месяц.
Коэффициент закрепления операции (Kз.о.) вычисляют по формуле [3 С.16]
гдеПо – сумма чисел различных операций;
Pя – явка рабочих подразделений выполняющих разные операции;
Ф – месячный фонд работника в одну смену
Кв– коэффициент выполненных временных норм
NiTi– трудоёмкость выполнения i-ой операции.
Трудоёмкость выполнения операций представлена в таблице 4.
Таблица 4 – Технологический процесс заводского варианта
Наименование операции
Для массового типа производства согласно ГОСТ 3.11.0–74 k3.0. принимается равным [4 С.243]
Важнейшей особенностью массового производстваявляется ограничение номенклатуры выпускаемых изделий что создает экономическую целесообразность широкого применения в конструкциях изделий унифицированных и взаимозаменяемых элементов тщательную разработку технологических процессов. Взамен универсальной оснастки применяют специальную. Оборудование на участке устанавливается с учетом точности процессов. Производительность выше а квалификация рабочих ниже чем в единичном производстве.
Выпуск изделий в сутки (Nc шт) вычисляют по формуле [3 С.20]
где247 – численность рабочих дней в году.
Суточная производительность линии потока (Q) вычисляют по формуле [3 С.20]
гдеФс – действительный суточный срок работы оборудования (при двухсменном режиме работы 952 мин);
Tcp – средняя трудоемкость наиболее важных операций мин;
nз– коэффициент загрузки оборудования в крупносерийном и массовом производстве равен 065 – 075 [7 С.163].
Среднюю трудоёмкость важных операций (Tcp мин) вычисляют по формуле [3 С.20]
гдеТшт – штучное время основной операции мин;
По – численность основных операций (без учета операций точения фасок скруглений и др.).
После проведенных расчетов следует то что выпуск изделий в сутки больше суточной производительности линии потока при условии ее загрузки поэтому использование одно номенклатурной поточной линии целесообразно.
4 Получение заготовки
Заготовка должна быть выполнена из указанного на чертеже материала обладать соответствующими ему механическими свойствами также она не должна иметь внутренних дефектов.
Разработка технологического процесса изготовления детали Шестерня может идти по двум направления:
получение заготовок по форме и размерам готовой детали когда на заготовительные цеха приходится основная часть трудоёмкости и относительная часть на механические цеха.
получение грубой заготовки с значительными припусками когда на механические цеха приходится основная доля трудоёмкости и себестоимости изготовления.
Для детали Шестерня выполненной из стали 35ХМЛ ГОСТ4543-71 с учетом факта массового производства назначаются следующие варианты получение заготовки:
литье в песчано-глинистые формы. Этим методом получаются отливки массой до 250 тонн. Им характерна относительно простая форма имеют напуск для упрощения формы по сравнению с готовой деталью. Требуют значительной механической обработки.
литье в кокиль. Эти методом получаются отливки массой от нескольких граммов до 3 тонн весьма разнообразных и сложных форм значительно приближенных к формам готовой детали в связи с чем требует меньших затрат на обработку резанием.
Литье в песчано-глинистые формы.
класс размерной точности отливки 17 [4 С.430]
допуски размеров отливки 20мм
Расчет припуска ведется расчетно-аналитическим методом.
Припуск на поверхность детали (dпр мм) вычисляется по формуле [5 С.72]
гдеdпр – диаметр заготовки с припуском мм;
dдет – диаметр детали мм;
zтаб– табличное значение припуска мм.
Расчет припуска на шлифование:
Расчет припуска на чистовое точение:
Расчет припуска на черновое точение:
Полученные значения сводятся в таблицу 5.
Таблица 5 – размеры заготовки по заводскому варианту
Наружный диаметр заготовки
Выполняется построение эскиза согласно полученным значениям размеров заготовки (рисунок 2).
Рисунок 2 – Эскиз заготовки отливка по заводскому варианту
Коэффициент использования материала (Kи.м.) вычисляют по формуле [3 С. 40]
гдеmдет – масса детали кг;
mзаг– масса заготовки кг.
Массу заготовки (m кг) вычисляют по формуле [3 С.41]
гдеp – плотность стали
Объём (V мм3) вычисляют по формуле [3 С.41]
гдеVD– объём наружного диаметра см3;
Vd – объём внутреннего диаметра см3.
Объём наружного диаметра (VD мм3) вычисляют по формуле [4 С.361]
Полученное значение объёма (V мм3) переводят в систему СИ (м3)
V= 24 366 395569 = 00024366395569
Стоимость заготовки (Sзаг руб) вычисляют по формуле [3 С.40]
гдеS – цена за 1 кг материала заготовки руб;
Sотх – цена за 1 тонну отходов руб.
Расчет припуска ведется расчетно-аналитическим методом. Величина припуска на механическую обработку определяется согласно ГОСТ 26645-85.
Определение припуска на обработку наружных диаметров.
Расчёт припуска на черновое точение:
Расчёт припуска на чистовое точение:
Определение припуска на обработку внутренних диаметров.
Определение припуска на обработку торцов.
Определение припуска на фрезерование зубьев.
Расчёт припуска на шлифование:
Полученные значения сводятся в таблицу 6.
Таблица 6 – размеры заготовки по проектному варианту
Выполняется построение эскиза согласно полученным значениям размеров заготовки (рисунок 3).
Рисунок 3 – Эскиз заготовки по проектному варианту
Объём (V мм3) рассчитан программой «Компас 3Д» [10 С.41] и равен: V= 0002026м3
Экономию (ΔS руб) вычисляют по формуле [3 С.41]
гдеSзаг1 Sзаг2 – стоимость заготовок представленных для сравнения руб.
Разница в стоимости изготовления заготовок данными методами составила 1170000 рублей.
Полученные значения для обоих способов получения заготовок сводятся в таблицу 7.
Таблица 7 – Обоснования выбора данного метода получения заготовки
Способ получения заготовки
Стоимость 1 тонны заготовок
Стоимость 1 тонны отходов
Стоимость заготовок руб.
Экономия по стоимости
На основании таблицы следует то что наилучшем вариантом получения заготовки будет литье в кокиль.
Экономическую эффективность с учетом годовой программы (Ф) вычисляют по формуле[3 С.41]
Экономию металла с учетом годового выпуска (Qкг) вычисляют по формуле [3 стр 41]
Таким образом метод получения заготовок литьём в кокиль дешевле метода литья в песчано-глинистые формы на 11%. Экономическая выгода в год составила по стоимости 1170000 рублей по использованию материала 40820 кг.
5 Проектирование маршрута обработки
Разработка последовательности обработки поверхностей. Операционный технологический процесс представлен в таблице 8.
Таблица 8 – Операционный технологический процесс
поз. 2 поз. 3 поз. 4 поз. 10.
Точить торцы: поз. 5.
Токарный станок модель 16А20Ф3
Патрон трехкулачковыйГОСТ 2675-80 Инструмент резец ГОСТ 10044-73
Штангенциркуль ГОСТ 166-89
поз. 2 поз. 3 поз. 4 поз. 9.
поз. 2 поз. 3 поз. 4 поз. 10
поз. 2 поз. 3 поз. 4 поз. 9
Продолжение таблицы 8
Горизонтально-протяжная
Горизонтально-протяжной станок модель 7534
Протяжка шлицевая ГОСТ 25158-82
шлицевых отв. ГОСТ 24969-81
Универсально-фрезерная
Универсально-фрезерный станок модель 6Р82Ш
Патрон самоцентрирующий с пневмоприводом ГОСТ52869-2007
Пальцевая модульная фреза ГОСТ 1643
6 Расчет режимов обработки и нормированием технологического процесса
Подробный расчёт для операций: токарно-карусельной (черновой) токарно-карусельной (чистовой) с ЧПУ горизонтально протяжной фрезерной шлифовальной.
Операция 005 токарная (черновая).
Токарный станок с ЧПУ 16А20Ф3 рисунок 12
Рисунок 12 – станок модели 16А20Ф3
Самоцентрирующий 3-х кулачковый патрон рисунок 13 .
Рисунок 13 – трехкулачковый патрон
Резец проходной упорный для черновой обработки Т5К10 ГОСТ 26611-85 рисунок 14.
Рисунок 14 – проходной резец
Штангенциркуль ГОСТ 66-80 рисунок 15.
Рисунок 15 - Штанкенциркуль
Установить крепить выверить.
Расчёт режимов резания.
Точить поверхность 4.
Глубина резания определяется согласно таблиц [3 С.106]
Исходя из выбранной глубины резания и размеров заготовки подача определяется по паспорту станка - Sпасп = 056 ммоб.
Скорость резания (V ммин) вычисляют по формуле [3 С.92]
гдеCv = 350 [3 С.105];
T = 60 мин для одноинструментальной обработки;
kv коэффициент учитывающий различные факторы влияющие на скорость резания.
Коэффициент факторов скорости резания (Кv) вычисляют по формуле[3 С.93]
kv = kv · kuv · kφv · kφ1v · krv · knv.
Коэффициент (Кmv) вычисляют по формуле [3 С.93]
гдеkr = 07 [3 стр 106];
Значения коэффициентов [3 С.106]:
kv = 07 · 1 · 09 · 1 · 094 · 08 = 05
Частоту вращения планшайбы (nобмин) вычисляют по формуле [3 С.96]
Уточнение nym по паспорту до ближайшего меньшего числа принимается nym =65 обмин.
Действительную скорость резания (Vd ммин) вычисляют по формуле [3 С.96]
Проверку по мощности (Pz Н) выполняют по формуле [3 С.98]
гдеСpz=300[3 С.101];
Коэффициент (Кpz) вычисляют по формуле [3 С.103]
kpz = kp · kφp · kγp · krp · kλp.
Коэффициент (Кuv) вычисляют по формуле:
Значения коэффициентов [3 С.106]
kpz = 1 · 1 · 11 · 1 · 093 = 1023
Pz = 10 · 300 · 31 · 056075 · 70-015 ·1023 = 31642
где[Pmax] максимальная осевая сила резания допускаемая механизмом подач станка из паспорта станка кН.
2 условие выполняется.
Проверку скорости резания по мощности (Nрез кВт) выполняют по формуле [3 С.107]
Сравнение(Nрез кВт) со станочной (Nст кВт)
гдеNэд мощность электродвигателя по паспорту станка
Необходимо выполнение условия Nрез ≤ Nст.
5 30 условие выполняется.
Машинное время (Т0 мин) вычисляют по формуле [3 С.108]
гдеLр.х. длина рабочего хода мм;
Величина перебега (y мм) вычисляется по формуле [3 С.108]
Число переходов i= 1.
Lр.х. = 206 + 2 + 1732 = 2097
Вспомогательное время на установку и снятие детали принимают по таблице 103 [3]; вспомогательное время на управление станком по таблице 106; вспомогательное время на контрольные измерения по таблице 107.
Норма времени (Тшт мин) определяется по формуле [3 С.108]
где – коэффициент определяющий соответственно время технического организационного обслуживания и время на отдых.[1]
Штучно-калькуляционное время определяется по формуле [3 С.108]
где – коэффициент [1]
Таким образом норма штучного времени составляет 278 мин. норма штучно-калькуляционного времени – 681 мин.
Операция 020 токарная (чистовая) с ЧПУ.
Токарный станок 16А20Ф3.
Патрон самоцентрирующий с пневмоприводом ГОСТ52869-2007.
Режущий инструмент резец твёрдосплавный Т15К6 с углом φ = 93о.
Штангенциркуль ГОСТ 166-70.
Глубина резания определяется согласно таблиц и составляет t =25 мм [3 С.106].
Исходя из выбранной глубины резания и размеров заготовки назначается предварительная подача S = 0246 ммоб .
Уточнение подачи по паспорту до ближайшего меньшего значения - Sпасп = 020 ммоб
гдеCv =420 [3 С.108];
T = 60 мин с неперетачиваемой твёрдосплавной пластинкой;
Коэффициент факторов скорости резания (Kv) вычисляют по формуле [3 С.93]
kv = kv · kuv · kφv · kφ1v · krv ·knv.
гдеkr = 07 [3 С.108];
kv = 07 · 1 · 07 · 097 · 094 ·08 = 036
Уточнение nут по паспорту до ближайшего числа принимается nут = 70 обмин.
гдеСpz = 300 [3 С.107];
гдеnp = 075 [3 С.108].
kpz = 1 · 089 · 10 · 093 · 10 = 182
Pz = 10 · 300 · 251 · 02075 · 754-015 ·182 = 20411
где [Pmax] максимальная осевая сила резания допускаемая механизмом подач станка из паспорта станка
Сравнение(Nрез кВт) со станочной(Nст кВт)
5 44 условие выполняется.
i = 1 число переходов.
Lр.х. = 164 + 2 + 0 = 166
Вспомогательное время на установку и снятие детали принимают по таблице 103 [3]; вспомогательное время на управление станком по таблице 106; вспомогательное время на контрольные измерения по таблице 107:
Таким образом норма штучного времени составляет 1153 мин. норма штучно-калькуляционного времени – 2406 мин.
Операция 030 протяжная.
Горизонтально-протяжной станок модели 7534 (рисунок 16).
Рисунок 16 –протяжной станок
Протяжка шлицевая (рисунок 17).
Рисунок 17 – шлицевая протяжка
Калибр для контроля шлицевых отверстий ГОСТ 24969-81.
Установить крепить вымерить.
Протянуть отверстие диаметром 180 мм.
Эскиз обработки детали показан на рисунке .
Рисунок 4 Эскиз обработки
Расчёт режимов резания
Выбор технологической подачи (S мм)
Уточнение подачи по паспорту до ближайшего меньшего значения - Sпасп = 01
Проверку прочности механизма подач (P0 кН) выполняют по формуле [3 С.93]
Pо = 10 · Cp · Dq · Syp · kp.
гдеnp = 075 [3 стр 108];
Pо = 10 · 67 · 25 · 028065 · 1=7323Н 7.
гдеPдоп максимальная осевая сила допускаемая механизмом подач станка из паспорта станка;
Проверку хвостовика на прочность при растяжении (Mp Нм) выполняют по формуле:
Mp = 10 · Cm · Dq · Sy · km.
Мр = 10 · 009 · 251 · 02808 · 1 = 813.
Прочность ( мПа) вычисляют по формуле [3 С.93]
гдеWр полярный момент инерции опасного сечения протяжки мм3.
Полярный момент инерции опасного сечения протяжки (Wр мм3) вычисляют по формуле
где допускаемое напряжение для конструкционных сталей
Напряжение стали ( мПа) вычисляют по формуле:
35 условие выполняется.
Скорость резания вычисляют по формуле (V ммин) [3 С.92]
kv = kmv · kuv · knv · klv
гдеkmv коэффициент учитывающий влияние материала заготовки.
Значения коэффициентов:
kuv коэффициент учитывающий влияние материала режущей части сверла
knv коэффициент учитывающий влияния состояния поверхности заготовки
klv коэффициент учитывающий глубину обрабатываемого отверстия
kv = 07 · 1 · 08 · 1 = 056
Мощность резания (Nрез кВт) вычисляют по формуле [3 С.98]
гдеNэд мощность электродвигателя по паспорту станка
5 224 условие выполняется
гдеi = 4 число переходов.
Lр.х. = 27 + 2 + 15 = 197
Таким образом норма штучного времени составляет 81 мин. норма штучно-калькуляционного времени – 5783 мин.
Операция 035 универсально-фрезерная.
Универсально фрезерный станок модели 6Р82Ш (рисунок 19).
Рисунок 19 - станок модели 6Р82Ш
Пальцевая модульная фреза ГОСТ 1643 (рисунок 20).
Рисунок 20 – пальцевая фреза
Установить крепить выверить. Нарезать зубья фрезерованием.
Эскиз обработки детали показан на рисунке 5.
Рисунок 5 – Эскиз обработки
Расчет режимов резания.
Сдвиг в направлении врезания зуба фрезы ( Lфр мм) вычисляют по формуле [3 С.108]
Определение глубины фрезерования (t мм) и ширины фрезерования (В мм)
Минутная подача (Sм) находится в следующем соотношении [3 С.124]
гдеSn – подача на один оборот фрезы;
n – частота вращения фрезы;
Z – число зубьев фрезы.
Величину подачи на один зуб (Sz мм) вычисляют по формуле [3 С.125]
Коэффициент факторов скорости резания (Кv) вычисляют по формуле [3 С.93]
Частоту вращения инструмента (n обмин) вычисляют по формуле [3 С.96]
Силу резания (Pz Н) вычисляют по формуле [3 С.103]
Мощность резания (Nрез кВт) вычисляют по формуле [3 С.107]
гдеL – расчетная длина обработки (L мм).
y – врезание при фрезеровании(у мм).
Таким образом норма штучного времени составляет 2497 мин. норма штучно-калькуляционного времени – 4048 мин.
Нормы времени по опрерациям показаны в таблицу 12.
Таблица 12 –нормы времени
Операция 005 Токарная черновая
Операция 010 Токарная черновая
Операция 020 Токарная чистовая
Операция 025 Токарная чистовая
Операция 030 Горизонтально-протяжная
Протянуть шлицы пов. 10 11.
Операция 035 Универсально-фрезрная
Фрезеровать зубья пов. 1
Шлифовать зубья пов. 1
Конструкторская часть
1 Базирование заготовки
Схема обработки шестерни выбирается исходя из анализа конструкционных и технологических требований зависящих от типа детали и производства.
Таблица 13 – Технологическая схема изготовления шестерни
Технологическая база
Токарная ЧПУ (черновая)
Токарная ЧПУ (чистовая)
2 Расчёт станочного приспособления
Выполняется построение операционного эскиза (рисунок 6).
Рисунок 6 – Эскиз заготовки
Вид и материал заготовки – отливка сталь 35ХМЛ ГОСТ4543-71.
Вид обработки – черновая.
Материал и геометрия режущей части инструмента – резец расточной из Т15К10 φ=93о; γ=-3о; λ=+5о.
Режимы резания: глубина t=18мм подача S=056ммоб.
Металлорежущий станок – 16А20Ф3 (наибольший диаметр патрона – 200мм.
kφp = 089; kγp = 10; krp = 093; kλp = 10.
Кру = 1.077.14.125 = 13475
Pz = 10 · 300 · 251 · 02075 · 754-015 ·182 = 20411
Pу = 10 · 243 · 309 · 04506 · 172-03 ·13475 = 854.
Расчёт усилий зажима.
Суммарный крутящий момент в кулачках равен
момент силы зажима (Мз’) определяются по формуле [3 С. 125]
усилие зажима в кулачках (W Н)
момент от силы зажима
Необходимая сила зажима равна
где d2=382мм Pу=854Н f=04 l=2527мм К=252
Для дальнейших расчетов принимается наихудший случай
Величина усилия зажима W1 рассчитывается по формуле
усилие (Q Н) создаваемое силовым приводом
где iс – передаточное отношение по силе зажимного механизма
Данное отношение для рычажного механизма (ie) равно [3 C. 127]
где А и Б – плечи рычага
наружный диаметр патрона определяется по формуле:
Так как Дп>200мм выбирается рычажный зажимной механизм с iс=2.
3 Выбор и расчёт контрольного приспособления
Для шлицевого соединения с прямобочным профилем зубьев выбирается вид центрирования посадки и размер b по ГОСТ 1139-80 [3 C. 132].
где Z - число зубьев
d - внутренний диаметр с полем допуска отверстия H12?
D - наружный диаметр с посадкой H9
b - ширина зуба с посадкой H8?
При центрировании по наружному диаметру D технология изготовления шлицевых деталей проще чем при центрировании по d так как твёрдость шлицевой втулки доступна для калибрования инструментами из быстрорежущих сталей
По ГОСТ 25346-82 определяют верхние и нижние отклонения размеров шлицевого отверстия
верхнее отклонение центрирующего диаметра 200 ESD= +25 мкм;
нижнее отклонение центрирующего наружного диаметра 200H9 ;
верхнее отклонение ширины шлицевого паза 30H8 мкм;
нижнее отклонение ширины шлицевого паза 30H8 мкм;
верхнее отклонение нецентрирующего внутреннего диаметра 180H12 мкм;
Рисунок 7 – Схема полей допусков шлицевой калибр-пробки на диаметр 200
Чертёж шлицевой калибр-пробки оформляется по всем требованиям ГОСТ ЕСКД. Конструкция и основные размеры этих калибров определяются по ГОСТ 24960-81 технические требования по ГОСТ 24959-81.
Рисунок 8 – Шлицевая калибр-пробка на диаметр 200
Организационный раздел
1 Расчёт потребного количества оборудования
Расчетное количество станков (Ср) на каждой операции определяется по формуле (4):
Количество станков для серийного производства (Срасч шт) вычисляют по формуле [5 С. 58]
где Т – трудоемкость производственной программы час (рассчитывается по формуле 1.8)
Квн – коэффициент выполнения норм на участке (принимается от 11 до 12)
Трудоёмкость производственной программы (Т час) [5 С. 59]
Коэффициент загрузки оборудования (Кз) вычисляют по формуле [5 C. 60]
Срасч = 3823 принимается Спр = 4 штуки станков.
Операция 010 Токарная с ЧПУ.
Срасч = 2132 принимается Спр = 3 штуки станков.
Операция 020 Токарная с ЧПУ.
Срасч = 0962 принимается Спр = 1 штуку станков.
Операция 025 Токарная с ЧПУ.
Срасч = 0659 принимается Спр = 1 штука станков.
Операция 030 Горизонтально-протяжная.
Срасч = 0324 принимается Спр = 1 штука станков.
Операция 035 Универсально-фрезерная.
Срасч = 1667 принимается Спр = 2 штуки станков.
Процент загрузки оборудования (Пзср %) определяется по формуле [3]
Таким образом можно сделать вывод что оборудование используется эффективно.
В таблице 15 сведены все необходимые данные по выбранному и рассчитанному оборудованию.
Таблица 15 – Расчет потребного количества оборудования
Наименование и модель станка
Расчетное число станков
Принятое количество оборудования Спр
Коэффициент загрузки станка
Средний коэффициент загрузки
Токарный станок с ЧПУ 16А20Ф3
Горизонтально протяжной станок 7534
Универсально фрезерный станок 6Р82Ш
Так-же на участке организовывается заточное и ремонтное отделение количество станков заточного отделения составляет 5 процентов от числа станков основного отделения ремонтного 3 процента.
Следовательно общее количество станков (Собщ) цеха составит согласно формуле (7)
Собщ = Со + Сзат + Срем
где Со – число станков основного производства;
Сзат – количество станков заточного отделения;
Срем – количество станков ремонтного производства.
Расчет стоимости производственного оборудования по всем операциям производится в таблице 16.
Таблица 16 – Стоимость производственного оборудования.
транспорта и монтажа
Горизонтально-протяжной станок
Универсально-фрезерный станок
2 Расчёт площади производственного участка
В состав механического цеха входят станочное отделение вспомогательные отделения и складские помещения к числу которых можно отнести:
заготовительное отделение;
ремонтное отделение;
мастерскую энергетика цеха;
отделение для приготовления и раздачи смазочно-охлаждающих жидкостей;
цеховой склад материалов и заготовок;
межоперационный склад;
инструментально-раздаточную кладовую;
склад приспособлений;
склад абразивного материала.
Размер станочного отделения при укрупненных расчетах определяется через среднюю величину удельной площади для станков различных размеров с учетов прохода и проездов. В среднем величина Sуд составляет для малых станков 10-12 м2 для средних станков 15-25 м2 для крупных станков 30-45 м2 для особо крупных и уникальных станков 50-150 м2
Учитывая количество станков проектируемого цеха которые входят в станочное отделение площадь данного отделения (Sст м2) определяется по формуле [3]
где Спр – принятое количество станков на участке;
Sуд – удельная площадь на один станок.
Площадь заготовительного отделения определяется в расчёте 25-30м2 на 1 станок учитывая количество станков заготовительного (Sзаг м2) отделения и рассчитывается по формуле [3]
где Sзаг.уд – удельная площадь на один станок.
Общая площадь заточного отделения определяется из расчетов 10-12м2 на 1 с учетом количества станков (Sзат м2) и определяется по формуле [3]
где Sзат.уд – удельная площадь на один станок.
Площадь ремонтного отделения определяется из расчётов 25-30м2 на основной станок. Общая площадь данного отделения с учетом количества станков (Sрем м2) определяется по формуле [3]
где Sрем.уд – удельная площадь на один станок.
Площадь службы энергетика цеха составляет приблизительно 30% от всей площади ремонтного отделения (Sэн м2) и определяется по формуле [3]
Sэн = 30% 1925 = 5775
Отделение для приготовления и раздачи смазочно-охлаждающей жидкости и склада масел. Площадь данного отделения может быть определенна в зависимости от количества производственного оборудования. При количестве оборудования менее 60 единиц – площадь данного отделения составляет 40-50м2. Площадь цехого склада масел составляет 10-20м2.
Принимается Sсож = 45м2 Sмасел = 15м2.
Площадь инструментально раздаточной кладовой (Sирк м2) определяется из расчёта на 1 металлорежущий станок цеха при работе в 1 смену в зависимости от вида производства для крупносерийного принимается 03м2 и определяется по формуле [3]
где Sрем.уд – удельная площадь на один станок на 1м2.
Площадь склада приспособлений (Sсклад м2) принимается равной для
единичного производства 05м2 мелкосерийного 04 м2 серийного м2
крупносерийного 02 м2 массового 01 м2 и определяется по формуле [3]
где Sрем.уд – удельная площадь на один станок принимается 04м2.
Площадь кладовых для абразивов (Sабр м2) (шлифовальных заточных и полировальных кругов) принимается из расчета 04м2 на 1 шлифовальный заточной или поправочный станок и определяется по формуле [3]
Sабр = Cшлиф Sабр.уд
где Sабр.уд – удельная площадь на один шлифовальный заточной или поправочный станок принимается 04м2;
Cшлиф – количество шлифовальных заточных и поправочных станков.
Рассчитав площадь всех необходимых складовых помещений определяется общая площадь складов (Sск.общ м2) по формуле [3]
Sск.общ = Sирк + Sс.п + Sабр
Sск.общ = 36 + 48 + 04 = 53
Площадь склада материалов заготовок межоперационных и готовых деталей (Sз.д м2) равна 10% от площади станочного отделения для каждого склада общий процент площади от складов составляет 30% от площади станочного отделения и определяется по формуле [3]
Также в общую площадь цеха входит площадь занимаемая контрольно разметочными плитами будками мастеров и сан-узлами необходимо предпринять дополнительную цеховую площадь. Площадь контрольного отделения составляет 3-5% от площади станочного отделения. В проектируемом цехе предусматривается площадь занимаемая двумя санузлами по 8м2 каждый. Размер дополнительной площади цеха (Sдоп м2) определяется по формуле [3]
где Sкон – площадь контрольного отделения (определяется по формуле ?);
Sсан – площадь санузла (принимается 16м2).
Общая площадь цеха (S м2) представляет из себя сумму рассчитанных отделений и определяется по формуле [3]
S = Sст + Sзаг + Sзат + Sрем + Sэн + Sсож + Sмасел + Sск.общ + Sз.д + Sдоп
S = 120 + 330 + 132 + 330 +5775 + 53 + 42 + 896 = 110665
Выполняется проверка кратности (Кр) длины пролета (L м) к шагу колон (Шк) принимается 12 [3]
Высота помещений (h) от пола до низа несущих конструкций в зданиях с мостовыми кранами следует назначать: для пролетов до 18 и 24 метра – 84 м; 96 м; 108 м. Принимается 96 м. Высота помещений от верха консолей для пролетов 18 и 24 метра – 46м; 54м; 66м. Принимается 54м.
Действительная производственная площадь (Sдест м2) определятся по формуле [3]
где l – ширина пролета.
Sдейст = 48 24 = 1152
Объём здания (V м3)
где h – высота производственного помещения.
Стоимость здания (Цзд руб) определяется по формуле [3]
где р – стоимость одного квадратного метра здания руб (29704).
Цзд = 1152 29704 = 34219008
Тоннажность кранов подбирается согласно максимальной массы оборудования. Это выполняется для проведения демонтажа и последующего ремонта вышедшего из строя оборудования.
Наибольшую массу имеет горизонтально-протяжной станок 7534 – 5200 килограмм следовательно стоит подобрать мостовой кран по второй группе грузоподъёмности (5-50 тонн) принимается кран с грузоподъёмностью 8 тонн.
3 Расчёт численности персонала
Общее количество участвующих в работе проектируемого цеха составляют:
производственные рабочие главным образом станочники;
вспомогательные рабочие;
младший обслуживающий персонал (МОП);
служащие инженерно-технические рабочие (ИТР) и счетно-конторский персонал (СКП).
Исходя из принятого количества станков (Спр) количество производственных рабочих (станочников) определяется по формуле (24):
Принимается Рст005 = 3 человека;
Принимается Рст010 = 2 человека;
Принимается Рст020 = 1 человек;
Принимается Рст025 = 1 человек;
Принимается Рст030 = 1 человек;
Принимается Рст035 = 1 человек;
На участке можно применять совмещение профессий. Это такое расширение трудовых функций рабочего при котором он выполняет функции двух или более профессий что обеспечивает наиболее полное использование рабочего времени приводит к повышению производительности труда.
В выпускной квалификационной работе выполнен конструкционный анализ детали включая анализ служебного назначения детали и анализ технологичности конструкции. Определён тип производства.
Разработан проектный вариант технологического процесса изготовления детали «Шестерня» проведен анализ двух методов получения заготовок выполнен расчет припусков режимов резания и норм времени на две разнохарактерные операции.
Важным этапом проектирования является составление маршрутного технологического процесса обработки выбор оборудования режущего и мерительного инструмента станочных приспособлений. В результате проведенного анализа типового технологического процесса изготовления шестерни спроектированы такие технологические операции как: предварительно токарная обработка чистовая токарная обработка на станке с ЧПУ фрезерование зубьев протяжка шлицевого отверстия шлифование зубьев.
В ходе проведенной работы были решены поставленные задачи разработаны оптимальные условия обработки продумана эффективность в достижении лучшего результата с наименьшими материальными затратами.
Список использованных источников
Меринов В. П. Козлов А.М. Схиртладзе А.Г. М 522Технология изготовления деталей. Курсовое проектирование по технологии машиностроения: учебное пособие В. П. Меринов А. М. Козлов А. Г. Схиртладзе. – Старый Оскол: ТНТ 2009. – 264 с.
Справочник технолога машиностроителя. В 2-х т. С74 Т. 1Под ред. А.Г. Косиловой и Р.К. Мещярякова. – 4-е изд. перераб. И доп. – М.: Машиностроение 1986. 656 с. ил.
Технология машиностроения: Практикум и курсовое проектирование: учебное пособие для студентов среднего профессионального образованияА. И. Ильяников В. Ю. Новиков. – С.: Издательский центр “Академия” 2012. – 432 c.
Гоцеридзе Р.М. Процессы формообразования и инструменты: учебник для студ. учреждений сред. проф. образования Р.М. Гоцеридзе. – 7-е изд. перераб. и доп. – М.: Издательский центр «Академия» 2016. – 432 с. ISBN 978-5-4468-2799-2
Новиков В.Ю. Технология машиностроения: В 2 ч. Ч. 1 В.Ю. Новиков. - 4-е изд. стер. - М.: Академия ИЦ 2014. - 352 с. - (Профессиональное образование)
Типовые технологические процессы механической обработки зубчатых колес: Методические указания к курсовой работе по технологии машинострое-ния Сост. Н.Н. Ситов А.М. Пейсахов; СПбГТУРП: СПб. 2015 59 с.
Рекомендуемые чертежи
- 27.11.2021
- 08.06.2023
- 24.01.2023
- 10.03.2024
- 25.05.2024
- 20.02.2016
- 11.03.2024