Разработка для условий серийного производства технологического процесса автоматизированного изготовления Корпус коллектора и конструкции станочного приспособления



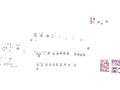
- Добавлен: 24.01.2023
- Размер: 13 MB
- Закачек: 1
Описание
Состав проекта
![]() |
![]() ![]() ![]() ![]() |
![]() ![]() ![]() |
![]() ![]() ![]() |
![]() ![]() ![]() |
![]() ![]() ![]() |
![]() ![]() ![]() ![]() |
Дополнительная информация
Обработка.dwg

А (увеличено) переход 6
Мерительный инструмент: штангенциркуль профильный с ценой деления 0
Инструмент: фреза одноугловая С12015 Г60 ø110 Р18
0 Фрезеровка режущего клина
Оборудование: станок горизонтально-фрезерный TOS KURIM FA5B
Приспопобление: тиски
кондуктор ЭИ-2128 к тискам 20Т-2020
Поворот стола переход 01
Кафедра МТ3 Группа МТ3-92
МГТУ им.Н.Э Баумана Кафедра МТ3 Группа МТ3-92
Операция 005 Изотермическая штамповка Операция 010 Термообработка Операция 015 Вертикально-фрезерная Станок вертикально-фрезерный
Операция 020 Радиально-сверлильная Станок радиально-сверлильный
Операция 035 Сверлильно-фрезерно-расточная с ЧПУ Обрабатывающий центр
Операция 040 Промывка Ванна Операция 045 Контрольная Контрольный стол Операция 050 Фрезерная с ЧПУ Обрабатывающий центр
Операция 025 Слесарная Верстак Операция 030 Контрольная Контрольный стол
Операция 055 Слесарная Верстак Операция 060 Промывка Ванна
Операция 065 Контрольная Контрольный стол
Операция 070 Электроэрозионная с ЧПУ Станок электроэрозионный с ЧПУ
Операция 075 Промывка Ванна Операция 080 Контроль приемочный Контрольный стол
Неуказанные предельные отклонения размеров h12
Поворот стола переход 06
Поворот стола переход 10
Поворот стола переход 12
Поворот стола переход 07
Поворот стола переход 08
Поворот стола переход 09
Операция 015 Сверлильно-фрезерно-расточная с ЧПУ
Оборудование: Обрабатывающий центр Willemin macodel 508S
Б (увеличено) переход 06
В-В (увеличено) переход 06
Г-Г (увеличено) переход 06
В-В (увеличено) переход 07
А (увеличено) переход 9
Г-Г (увеличено) переход 08
В-В (увеличено) переход 08
А (увеличено) переход 12
Б (увеличено) переход 12
А (увеличено) переход 13
Б (увеличено) переход 13
В-В (увеличено) переход 10
В-В (увеличено) переход 11
Приспособление специальное
А-А (увеличено) переход 03
А-А (увеличено) переход 04
А-А (увеличено) переход 05
А (увеличено) переход 02
Б (увеличено) переход 02
Техническая характеристика
Неуказанные радиусы скругления 1..2 мм
* Размеры для справок
Стопорить резьбовые соединения герметиком Loctite 243
Раздел А.docx
Назначение детали в узле доработка чертежа по действующим ГОСТам. Анализ технических требований выявление технологических задач возникающих при изготовлении и разработка схем проверки по заданным требованиям.
Назначение детали в узле.
При запуске двигателя топливо подается к I каналу топливного коллектора и через отверстия в корпусе равномерно распределяется по 8 форсункам попадая в I каскад форсунок к завихрителям I каскада. Одновременно ко второму каналу коллектора подается воздух от системы запуска двигателя. Из второго канала воздух через отверстия в корпусе коллектора поступает к распылителям II каскада. Топливо и воздух закрученные тангенциальными пазами соответственно завихрителей I каскада и распылителей II каскада и смешиваясь с воздухом из компрессора проходящим через воздушный завихритель образуют топливовоздушную смесь которая под действием центробежных сил выходит из центрального отверстия воздушного завихрителя в жаровую трубу образуя полный конический факел.
Подаваемый при запуске во второй каскад форсунок воздух интенсифицирует процесс распыла топлива первым каскадом. При выходе изделия на режим Малого Газа подача воздуха во II каскад форсунок прекращается.
На основных режимах работы двигателя для обеспечения заданной характеристика расхода топлива во второй каскад форсунок подается топливо.
В топливный коллектор камеры сгорания устанавливаются форсунки (8 штук). Форсунки предназначены для впрыска и распыливания топлива в жаровую трубу.
Форсунки - центробежные двухкаскадные с поочередной подачей во второй каскад воздуха и топлива.
Форсунка состоит из следующих основных деталей:
-воздушного завихрителя;
-завихрителя I каскада.
Корпусом форсунки является бобышка корпуса коллектора в которую устанавливаются распыливающие элементы форсунки: завихритель I каскада выполненный в виде конического шнека с двумя прямоугольными тангенциальными пазами сопло I каскада распылитель II каскада в виде плоской шайбы с двумя тангенциальными пазами. Завихритель I каскада поджимается к соплу I каскада с помощью пружины.
Воздушный завихритель поворачивается по резьбе на бобышку корпуса коллектора одновременно являясь колпачком форсунки который прижимает распылитель II каскада к соплу I каскада а сопло к торцу бобышки корпуса коллектора обеспечивая уплотнение по торцам распыливающих деталей. Воздушный завихритель содержит шесть изогнутых лопаток создающих радиальные каналы закручивающие воздух в сторону затяжки завихрителей по резьбе бобышек. Воздушный завихритель контрится с помощью кольца контровочного которое двумя выступами фиксируется на корпусе и после затяжки завихрителя обжимается в 4 его паза.
Описание конструкции: деталь корпус коллектора представляет собой кольцо с выступающими бобышками. Кольцо довольно тонкое и на нем имеются точные пазы поэтому оно не жесткое в радиальном направление при обработке и выборе баз это необходимо учесть поэтому необходимо выполнить прикладывая силу в осевом направление.
Деталь выполнена из титанового сплава ОТ4-1. Характерные особенности титана - малая плотность 451 кгдм3 высокая прочность которая сохраняется до 6000С коррозионная стойкость. Титановые сплавы сочетают высокую прочность (В= 800-1500 МПа) с хорошей пластичностью (= 12- 25%) относительно хорошую жаропрочность до 600- 7000С высокую коррозионную стойкость во многих агрессивных средах кроме HCL HF. α- титановые сплавы не стареют. Одним из недостатков титановых сплавов является их плохая обрабатываемость режущим инструментом.
Исходя из условий эксплуатации к корпусу коллектора предъявляются следующие требования:
Пазы на торце кольца выполнены по 8 квалитету точности 136 h8
85 H8 1495 h8 162H8. Данные пазы необходимы для того чтобы на сборке в них заложили соответствующие кольца которые в последствие приварят и данные кольца будут закрывать пазы по которым будут поступать топливо и воздух в форсунки. Поэтому для лучшего прилегания и приварки соответствующих колец к корпусу коллектора необходимо пазы выполнить точными.
Обеспечивается данный квалитет чистовым точением.
Для контроля данных пазов в серийном производстве целесообразней использовать шаблоны соответствующего размера.
Цилиндрическая поверхность на 8 бобышках 118 f7. На данную поверхность бобышки накручиваются форсунки и по этой поверхности происходит соприкосновение бобышки и форсунки так как в форсунке происходит смешивание топлива с воздухом недопустимо чтобы данная смесь выходила другим путем нежели чем через отверстие в форсунке поэтому данное соединение должно обеспечивать герметичность. Герметичность обеспечивается соответствующей посадкой.
Данную точность поверхности будем обеспечивать тонким фрезерованием.
Для контроля соответствующего размера будем использовать либо микрометр либо калибр-скобу на размер 118 f7.
Поверхности обрабатываемые с шероховатостью Ra 0.8 3.2.
Имеются 8 пазов с шероховатостью по боковым сторонам Ra 1.6.
Данная поверхность необходима для прилегания к ней соответствующей части форсунки. Обеспечение данной шероховатости не вызовет проблем при обработке зенкерованием.
На данной операции необходимо выдержать позиционный допуск R005 мм. Допуск будет выдержан точностью станка и точностью приспособления.
Для контроля торцевой канавки необходим калибр и кольцо.
Допуск расположения.
Имеется допуск симметричности равный 0.1 мм в радиальном направление относительно оси Р на сквозное отверстие сложной формы.
Соответствующее отверстие будет получено на электроэрозионной операций. Соответствующий допуск обеспечивается аттестованной программой.
Из функционального назначения видно что материал из которого выполнен корпус коллектора должен быть химически не активным с топливом. Деталь должна быть выполнена из сплава с малой плотностью. Должна обеспечивать герметичность выдерживать давление подаваемого топлива.
На детали имеется множество наклонных отверстий которые будем получать сверлением. Для отверстий с углом наклона не более 15° градусов предварительно будем только зацетровывать их положение. При большем наклоне перед зацентровкой будем создавать поверхность перпендикулярную оси сверлимого отверстия.
Технологический анализ конструкции детали с определением показателей технологичности.
Качественный анализ конструкции детали
В соответствии с ГОСТ 14.301-83 разработка технологических процессов производится для изготовления изделий конструкции которых отработаны на технологичность. Отработка конструкции изделия на технологичность направлена повышение производительности труда снижение затрат и сокращение времени на проектирование технологическую подготовку производства изготовление техническое обслуживание и ремонт изделия при обеспечении необходимого качества изделия.
Конструкция изделия может быть признана технологичной если она обеспечивает простое и экономичное изготовление этого изделия. Повышение технологичности конструкции изделия предусматривает проведение комплекса различных мероприятий в числе которых необходимо отметить приведенные ниже.
Уменьшение трудоемкости изготовления детали. Это достигается путем снижения требований к точности детали и использованием точной заготовки у которой высокий коэффициент использования материала. Точность данного изделия средняя. К корпусу предъявляются средние требования по точности при этом будем использовать точный метод получения заготовки.
Создание конфигурации детали и подбор материала позволяющего применение наиболее совершенных исходных заготовок сокращающих объем механической обработки. Данная деталь имеет среднюю конфигурацию и материал тяжело подающийся лезвийной обработке. Материал и конструкцию в данном случае изменить не имеется возможности. Объем лезвийной обработки удастся снизить за счет применения точных заготовок.
Простановка размеров на чертеже с учетом требований их механической обработки позволяющая выполнять обработку по принципу автоматического получения размеров и обеспечивать совмещение конструкторских и технологических баз. Все эти требования на чертеже учтены. Обработку будем вести с учетом требования неизменности баз.
Упрощение конфигурации детали предельно возможное расширение допусков на изготовление и снижение требований к шероховатости обрабатываемых поверхностей с целью уменьшения объема и облегчения механической обработки. В нашем случае все допуски и шероховатости максимизированы.
Создание конфигурации детали позволяющей применение наиболее совершенных и производительных методов механической обработки (обработка многорезцовым фасонным и многолезвийным инструментом накатывание и вихревое нарезание резьбы применение агрегатных и специальных станков и автоматов поточных и автоматических линий). В данном случае применение специальных методов обработки необоснованно т.к. изготовление режущего инструмента под данный сплав титана будет дорог.
Проведение нормализации и унификации детали являющихся предпосылками типизации технологических процессов унификации режущего и мерительного инструментов. Как было сказано выше деталь – кольцо с бобышками и поверхности простые стандартные канавки резьба. Для обработки необходим стандартный инструмент.
Из всего сказанного выше можно сделать вывод что данный корпус коллектора является технологичным.
Количественные показатели технологичности
Основными количественными показателями технологичности являются:
абсолютный технико-экономический показатель - трудоемкость изготовления детали ТН;
уровень технологичности конструкции по трудоемкости
где ТН - достигнутая трудоемкость изделия 44ч.;
ТБН - базовый показатель трудоемкости изделия (определяемый по аналогичности конструкции уже освоенной в производстве) 56ч.;
8 > 05 => деталь технологична
уровень технологичности конструкции по технологической себестоимости
Расчет технологичности будем производить по дополнительным показателям ввиду отсутствия данных.
Дополнительные показатели:
коэффициент использования материала КИМ:
где mД - масса готовой детали 0141 кг;
mЗ - масса заготовки 112 кг.
Масса заготовки и масса готовой детали взяты из базового варианта производства детали.
3 06 => деталь не технологична
коэффициент технологичности по точности
где - средний квалитет обработки детали;
А - квалитет обработки;
n - число размеров соответствующего квалитета.
1 ≥ 08деталь технологична
коэффициент технологичности по шероховатости поверхности
где БСР - средняя шероховатость поверхности определяемая в значениях параметра Ra мкм.
где Б - числовое значение шероховатости (Ra);
ni - число поверхностей с соответствующими числовыми значениями параметра шероховатости.
К = 083 > 032 деталь технологична
коэффициент унификации конструктивных элементов детали
где QУЭ - число унифицированных типоразмеров конструктивных элементов;
QЭ - число типоразмеров конструктивных элементов в изделии.
Ку = 059 > 05 деталь технологична
Вывод из расчетов видно деталь является технологичной но метод получения заготовки не устраивает поэтому необходимо рассмотреть более приемлемый способ получения заготовки.
Выбор метода изготовления заготовки.
Деталь корпус коллектора является ответственной заготовка для нее должна быть получена методом обработки давления.
В базовом варианте в качестве заготовки применяют штамповку. Заготовка представляет собой кольцо 182 мм высотой 27 мм и отверстием 95 мм.
В предыдущем пункте установлено что коэффициент использования материала в базовом варианте технологического процесса низкий.
Одной из передовых технологий которая позволяет получать высококачественные заготовки и экономить металл является объемная изотермическая штамповка (или ковка).
В отличие от обычной объемной горячей штамповки при изотермической штамповке требуется чтобы штамп и штампуемая заготовка были нагреты в процессе деформирования до одной и той же высокой температуры что исключает нежелательное охлаждение поверхности заготовки и возникающий перепад температур. Это существенно улучшает условия для пластического течения материала и позволяет получать высококачественные заготовки значительно более близкие по форме к конечным требованиям.
Таблица 1. Сравнение объемной горячей штамповки и изотермической
Горячая объемная штамповка
Изотермическая штамповка
Скорость деформирования до 1 мс.
Штамповка осуществляется холодным или теплым инструментом.
Получение точных заготовок сложных конфигураций обычной штамповкой затруднительно или невозможно.
Быстрое остывание поверхности штампуемой заготовки от холодного инструмента создает неравномерное температурное поле; отсюда неравномерные деформации и неравномерная проработка материала.
Высокая скорость деформирования создает значительный тепловой эффект в зоне максимальной деформации вызывая еще большую неравномерность течения металла.
В результате возникают высокие и неравномерные напряжения течения металла и недостаточная его пластичность которые нередко ведут к появлению трещин разрывов утяжин и других дефектов.
Штамповки имеют высокие остаточные неравномерные напряжения наклеп которые не полностью снимаются при термообработке; это приводит к короблению и изменению размеров детали в процессе эксплуатации.
Скорость деформирования менее 0005 мс.
В процессе штамповки инструмент и заготовка нагреты до одной и той же высокой температуры.
Высокая точность штамповки заготовок сложных конфигураций особенно тонкостенных поковок характеризующихся большим отношением площади поверхности к объему.
Точность и качество заготовок штампованных в изотермических условиях достигается в результате:
-уменьшения упругих деформаций системы пресс-штамп из-за снижения сопротивления деформированию штампуемого металла и усилия штамповки;
-уменьшения колебаний температуры деформации;
-снижения остаточных напряжений в объеме штампованной поковки что уменьшает ее поводки при остывании и термообработке.
Изотермическая штамповка позволяет изготавливать:
- штамповки непосредственно из исходного литого материала имеющего плохую пластичность;
- штамповки с небольшими штамповочными уклонами или без них с резкими перепадами сечений малыми радиусами переходов и припусками на обработку резанием.
- осуществлять горячее изостатическое прессование для устранения микропористости;
- позволяет штамповать металлы в сверхпластичном состоянии.
Из всего упомянутого выше делаем вывод что деталь будем получать методом изометрической штамповки что позволяет снизить расход металла на деталь по сравнению с обычными процессами горячей штамповки в среднем в 3 раза и повысить КИМ до 05-08. Трудоемкость обработки резанием ШЗ полученных в изотермических условиях снижается на 30-50 и более процентов.
Рис. 1 Эскиз заготовки
Разработка маршрута обработки основных поверхностей.
В качестве заготовки приняли изотермическую штамповку.
Основные поверхности это наружные и внутренние поверхности вращения и резьба.
Наиболее точная поверхность это наружный цилиндр 118 f7.
Данную поверхность можно получить на токарном станке установив деталь на планшайбу при этом необходимо выполнить следующие переходы:
Заготовка выполнена по 12 квалитету.
Черновое точение 10 квалитет.
Получистовое точение 9 квалитет.
Чистовое точение 8 квалитет.
Тонкое точение 7 квалитет.
При данной последовательности выполнения переходов необходимо переустанавливать заготовку восемь раз. При этом способе мы не сможем обеспечить принцип совмещения баз.
Данную поверхность можно получить другим способом закрепив деталь на специальном приспособление и выполнив обработку на фрезерном станке с ЧПУ при этом необходимо выполнить следующие переходы:
Черновое фрезерование 10 квалитет.
Получистовое фрезерование. 9 квалитет.
Чистовое фрезерование 8 квалитет.
Тонкое фрезерование 7 квалитет.
Данную поверхность будем получать методом фрезерования.
Пазы на торце кольца выполненные по 8 квалитету точности 136 h8
Данные пазы можно получить на токарном станке при этом необходимо выполнить переходы:
Однократное точение 10 квалитет.
Чистовое точение 8 квалитет
Эту же поверхность можно выполнить методом фрезерования со следующими переходами:
В итоге мы выбираем получение этой канавки методом точения так как при этом поверхность перпендикулярная выполняемой будет с лучшими условиями плоскостности это необходимо для закладки в этих пазов кольца которые будут привариваться.
Выбор баз разработка маршрута изготовления детали выбор вида оборудования. Составление эскизов обработки с упрощенными обозначениями баз по ГОСТу.
В условиях серийного типа производства как правило используют оборудование с ЧПУ. Поэтому при выборе станка будет отдаваться приоритет станкам с ЧПУ.
Маршрут изготовления детали приведен на первом листе графической части курсовой работы.
5 Изотермическая штамповка.
0 Термообработка. Необходимо провести для снятия внутренних напряжений для улучшения условий резания.
5 Фрезерная операция
Операция выполняется на вертикально-фрезерном станке. Необходимо обработать поверхность для дальнейшего использования в качестве установочной базы. При этом заготовка ставится на необработанную поверхность и прижимается прижимами. На данной операции необходимо выдержать высоту заготовки в размер согласно чертежа.
0 Сверлильная операция.
На данной операции необходимо подготовить центрирующие бызы для последующей обработки детали. При этом заготовку установим на поверхность обработанную на предыдущей операции. В данной операции выполним 3 отверстия по 6 квалитету с жестким позиционным допуском.
5 Слесарная операция
Необходимо убрать все заусенцы.
0 Контрольная операция
Проверить точность выполнения отверстий их расположение и высоту заготовки.
5 Сверлильно-фрезерно-расточная операция.
На данной операции выполним обработку всех поверхностей располагающиеся на нижней плоскости для этого понадобиться сверлильно-фрезерно-расточной станок с ЧПУ. Базирование происходит по уже подготовленным поверхностям. Установочной плоскостью является фрезерованная поверхность при этом установка идет по плоскости. Центрирующей поверхностями будут являться три отверстия выполненные на сверлильной операции. Деталь будем прижимать с помощью прижимов.
5 Контрольная операция. Проконтролировать полученные размеры поверхностей.
0 Сверлильно-фрезерная с ЧПУ операция.
Пользуясь принципом неизменности баз в качестве центрирующих поверхностей используем заранее подготовленные отверстия. Установочной плоскостью будет являться перед этим обработанная плоскость. Деталь будем прижимать с помощью прижимов.
Деталь возможно выполнить на сверлильно-фрезерном станке с ЧПУ.
На данной операции получим все необработанные поверхности.
Необходимо снять все заусенцы и притупить острые кромки.
5 Контрольная операция.
0 Электроэрозионная с ЧПУ операция.
Используем электроэрозионный станок вырезка отверстия происходит с помощью проволоки по программе.
0 Приемочный контроль.
Расчет припуска на обработку и составление расчетной таблицы.
Все данные для расчета припусков на обработку поверхности взяты из источника [1] т.1 гл. 4 стр. 186 табл. 25.
Таблица 2 Расчет припуска на размер
Наименование детали – Корпус коллектора. Материал – ОТ4-1
Элементарная поверхность для расчета припуска –
Маршрут обработки мм
Элементы припуска мкм
Расчетный припуск zmin мкм
Расчетный минимальный размер мм
Допуск на изготовление T мкм
Принятые (округленные) размеры по переходам мм
Полученные предельные припуски мкм
Rz – высота неровностей профиля;
h – глубина дефектного поверхностного слоя;
– суммарное отклонение расположения поверхности;
– погрешность установки заготовки.
Погрешность установки заготовки не учитывается так как не производится выверка заготовки на станке.
zi min = Rzi-1 + hi-1 + Δ i-1 + i
Припуск под чистовое фрезерование:
zi min = 32+50+20 = 102 мкм
Определим размеры полученные после чернового фрезерования:
а'min i -1 = аmin i + zi min
а' min i -1 = 1489 + 0.102 = 14.992 мм
а'max i -1 = а'min i -1 + T i -1
а'max i -1 = 14.992+0.180 = 15.172 мм
Принимаем am ama zi min = 110 мкм.
Максимальный припуск:
zi max = zi min + T i-1- T i
zi max = 110 + 180 -110 = 180 мкм
Припуск под изотермическую штамповку:
zi min = 80+150+60 =290 мкм
Определим размеры полученные после изотермической штамповки:
а' min i -1 = 15 + 0.29 = 1529 мм
а'max i -1 = 1529+0.270 = 15.56 мм
Принимаем am ama zi min = 300 мкм.
zi max = zi min + Td i-1 - Td i
zi max = 300 + 270 -180 = 390 мкм
ZΣ max = zΣ min + T з - T д
0 = 410+ 270 - 110 = 570 следовательно расчет выполнен правильно.
Из расчета видны минимальные границы припуска на сторону для того что бы гарантировать качество обрабатываемых поверхностей мы завысим величину припуска и примем его равным 15 мм на сторону.
Расчет припуска на размер мм
Все данные для расчета припусков на обработку поверхности взяты из источник [1 табл.24 стр. 187]
Таблица 3 Расчет припуска на размер мм
Наименование детали – Корпус коллектора.
Элементарная поверхность для расчета припуска – цилиндр мм
Маршрут обработки цилиндра мм
Расчетный припуск 2zmin мкм
Допуск на изготовление Td мкм
Изотермическая штамповка IT12
Отклонение расположения необходимо учитывать: у заготовок (под первый технологический переход); после черновой обработки лезвийным инструментом (под последующий технологический переход).
Для изотермической штамповки
где 1 – отклонение торца от перпендикулярности 60 мкм
– отклонение от концентричности реально расположенной с идеально расположенной бобышкой [1 табл.17 стр. 186] 05 мм
zi min = 2 (Rzi-1 + hi-1 + Δ i-1 + i)
Припуск под тонкое фрезерование:
zi min = 2 (25+25) = 100 мкм
Определим размеры полученные после чистового растачивания:
d'min i -1 = dmin i + 2zi min
d' min i -1 = 11766 + 0.1 = 11866 мм
d'max i -1 = dmin i-1 + Td i -1
d'max i -1 = 11866 + 0027 = 11893 мм
Принимаем dm dma 2zi min = 100 мкм.
zi max = 2zi min + Td i-1 - Td i
zi max = 100 + 27 – 18 = 109 мкм
Припуск чистовое фрезерование:
zi min = 2 (40+40) = 160 мкм
d' min i -1 = 1187 + 0.16 = 1203 мм
d'max i -1 = 1203 + 0043 = 12073мм
Принимаем dm dma 2zi min = 160 мкм.
zi max = 160 + 43 – 27 = 176 мкм
Припуск получистовое фрезерование:
zi min = 2 (60+120+100) = 560 мкм
d' min i -1 = 1203 + 0.56 = 1259 мм
d'max i -1 = 1259 + 007 = 1266мм
Принимаем dm dma 2zi min = 570 мкм.
zi max = 570 + 70 – 43 = 597 мкм
Припуск под черновое фрезерование:
zi min = 2 (80+150+504) = 1468 мкм
d' min i -1 = 126 + 1468 = 14068 мм
d'max i -1 = 14068 + 018 = 14248мм
Принимаем dm dma 2zi min = 1470 мкм.
zi max = 1470 + 180 – 70 = 1580 мкм
ZΣ max = 2zΣ min + T з - T д
62 = 2300+ 180 - 18 = 2462 следовательно расчет выполнен правильно.
Разработка операционной технологии с выбором моделей оборудования и типов режущих инструментов и нормированием.
Станок должен позволять обрабатывать наклонные отверстия выполненные на одном радиусе поэтому для данной операции необходимо иметь круговой стол.
Для данной операции подходит обрабатывающий центр фирмы Willemin-macodel 508S
Характеристика станка:
Spindle speed: 42000 RPM
Tool magazine: 72 positions
T-slot table Ш 320 mm
High-pressure cooling through spindle at 80 bar
Cutting fluid thermostabilisation
Tool breakage detector and tool setting devic
Part probing system
Part loading and unloading robot
Рис. 2 Кинематика станка.
Режущий инструмент подбираем по основному каталогу режущего инструмента фирмы Sandvik Coromant.
Режимы резания подбираем с помощью программы PluraGuide поставляемой Sandvik Coromant для своего режущего инструмента. Для этого в программе выбирает титановый сплав с НВ 220 единиц и для каждого инструмента задаем соответствующую глубину резания и ширину фрезерования.
Переход 01 Фрезеровать контур по программе.
Выбираем цельную твердосплавную фрезу CoroMill Plura сплав GC1630
Код заказа инструмента R216.34-1545-AC26N
Режимы резания согласно программе:
Частота вращения фрезы n=2200 мин-1
Подача минутная S=1170 мммин
Подача на зуб Sz=0.133 ммзуб
Скорость резания V=103 ммин
Длину рабочего перемещения определим эскиза обработки L=1120 мм
Основное время обработки мин
L – длина фрезерования.
tосн = 11201170=0.98 мин
Переход 02 Фрезеровать контур по программе.
Код заказа инструмента R216.34-0545-AC11N
Частота вращения фрезы n=8200 мин-1
Подача минутная S=516 мммин
Подача на зуб Sz=0.021 ммзуб
Скорость резания V=129 ммин
Длину рабочего перемещения определим из эскиза обработки L=480 мм
tосн = 480516=0.93 мин
Переход 03 Точить пазы в размер 138 h10 145H10 153 h10
0H8 и глубиной 3 мм.
Выбираем двух лезвийную пластину 123 – GF Ширина пластины 35 мм Сплав 1125
Код заказа инструмента N123G2-0350-003-GF
Выбираем соответствующую державку RLS151.25. 2525-20
Частота вращения фрезы n=230 мин-1
Подача на оборот Sо=005 ммоб
Скорость резания V=100 ммин
Длину рабочего перемещения определим из эскиза обработки L=8 мм
tосн = 8(005230)=0.7 мин
Переход 04 Точить пазы в размер 136 h8 1485 H8 1495 h8 162H8 и глубиной 2 мм.
Выбираем двух лезвийную пластину 123 – GF Ширина пластины 5 мм Сплав 1125
Код заказа инструмента N123G2-0450-005-GF
Длину рабочего перемещения определим из эскиза обработки L=12 мм
Переход 05 Точить фаску согласно чертежа в размер 06х45°
Выбираем пластину CNMG 1204 05-PF Сплав 1025
Выбираем соответствующую державку PCBNRL2525M12
Подача на оборот Sо=01 ммоб
Длину рабочего перемещения определим из эскиза обработки L=1 мм
Переход 06 Зацентровать 24 места под отверстия
Инструмент: Сверло центровочное сплав 1020
Частота вращения фрезы n=3180 мин-1
Подача на оборот Sо=0006 ммоб
Скорость резания V=10 ммин
где i – количество отверстий.
Переход 07 Сверлить 8 отверстий 1 мм
Инструмент: сверло 1 мм сплав 1020
Код заказа R840 – 0100-70-A0B
Переход 08 Сверлить 8 отверстий 2.5 мм под углом 15° и отверстие под углом 10° на глубину 8 мм
Инструмент: сверло 25 мм сплав 1020
Код заказа R840 – 0250-50-A0B
Частота вращения фрезы n=3820 мин-1
Подача на оборот Sо=002 ммоб
Скорость резания V=30 ммин
Переход 09 Сверлить 2 отверстий 3 мм на глубину 15 мм и 12 мм согласно чертежа
Инструмент: сверло 3 мм сплав 1220
Код заказа R840 – 0300-30-A0А
Подача на оборот Sо=006 ммоб
Переход 10 Сверлить 4 отверстия 45 мм насквозь согласно чертежа
Инструмент: сверло 45 мм сплав 1220
Код заказа R840 – 0450-30-A0А
Частота вращения фрезы n=2120 мин-1
Переход 11 Зенкеровать 4 отверстия 53 мм насквозь согласно чертежа
Инструмент: Зенкер 53 мм сплав 1220
Частота вращения фрезы n=1800 мин-1
Переход 12 Сверлить 2 отверстия 6 мм на глубину 149 мм согласно чертежа
Инструмент: сверло 6 мм сплав 1220
Код заказа R840 – 0600-30-A0А
Частота вращения фрезы n=1590 мин-1
Подача на оборот Sо=008 ммоб
Переход 13 Зенкеровать 2 отверстия 88 мм на глубину 149 согласно чертежа
Инструмент: Зенкер 88 мм сплав 1220
Частота вращения фрезы n=1440 мин-1
Скорость резания V=40 ммин
Готовое.docx
«Московский государственный технический университет
(МГТУ им. Н.Э. Баумана)
РАСЧЁТНО-ПОЯСНИТЕЛЬНАЯ ЗАПИСКА
к курсовой работе на тему:
(Подпись дата) (И.О.Фамилия)
Раздел А. Проектирование автоматизированного технологического процесса изготовления детали.
Назначение детали в узле доработка чертежа по действующим ГОСТам. Анализ технических требований выявление технологических задач возникающих при изготовлении и разработка схем проверки по заданным требованиям .. 3
Технологический анализ конструкции детали с определением показателей технологичности .6
Выбор метода изготовления заготовки .9
Разработка маршрута обработки основных поверхностей 12
Выбор баз разработка маршрута изготовления детали выбор вида оборудования. Составление эскизов обработки с упрощенными обозначениями баз по ГОСТу .13
Расчет припуска на обработку и составление расчетной таблицы .15
Разработка операционной технологии с выбором моделей оборудования и типов режущих инструментов и нормированием ..20
Раздел Б. Расчет и конструирование технологической оснастки автоматизированного производства.
Разработка схемы приспособления .27
Расчеты обосновывающие экономическую целесообразность применения приспособления 29
Выбор установочных зажимных и других элементов приспособлений 30
Определение допустимой погрешности установки или условий собираемости из условий обеспечения точности обработки или сборки . .32
Составление схемы сил действующих на заготовку или собираемое изделие и расчет зажимного устройства 33
Назначение технических требований на приспособление обеспечивающих заданную точность . .37
Выбор материалов для основных деталей и назначение термической обработки ..39
Описание конструкции и работы приспособления ..40
Список литературы 41
Задание на курсовой проект составлено на основе заводской практики прошедшей на заводе “Салют” в проекте рассматривается процесс изготовления детали «Корпус коллектора» и проектирования станочного приспособления для одной из операций обработки данной детали. В проекте предложена новая технология обработки разработанная с целью повышения производительности и сокращения производственных затрат.
Записка состоит из двух разделов.
Раздел А посвящен разработке технологического процесса обработки детали «Корпус коллектора». Анализируются технические требования и задачи возникающие при обработке. Выбирается метод изготовления заготовки. Разрабатывается технологический процесс обработки с заполнением маршрутной карты. Разрабатывается операционная технология с выбором модели оборудования и типов режущего инструмента.
Раздел Б посвящен проектированию технологической оснастки на фрезерную операцию изготовления детали корпуса коллектора. Дается расчет обосновывающий экономическую целесообразность применения специального приспособления. Анализируются возможные схемы базирования и закрепления заготовки. Определяются допустимые погрешности вносимые приспособлением. Проектируется приспособление составляется спецификация на детали приспособления. Назначаются необходимые технические требования обеспечивающие заданную точность приспособления.
Назначение детали в узле доработка чертежа по действующим ГОСТам. Анализ технических требований выявление технологических задач возникающих при изготовлении и разработка схем проверки по заданным требованиям.
Назначение детали в узле.
При запуске двигателя топливо подается к I каналу топливного коллектора и через отверстия в корпусе равномерно распределяется по 8 форсункам попадая в I каскад форсунок к завихрителям I каскада. Одновременно ко второму каналу коллектора подается воздух от системы запуска двигателя. Из второго канала воздух через отверстия в корпусе коллектора поступает к распылителям II каскада. Топливо и воздух закрученные тангенциальными пазами соответственно завихрителей I каскада и распылителей II каскада и смешиваясь с воздухом из компрессора проходящим через воздушный завихритель образуют топливовоздушную смесь которая под действием центробежных сил выходит из центрального отверстия воздушного завихрителя в жаровую трубу образуя полный конический факел.
Подаваемый при запуске во второй каскад форсунок воздух интенсифицирует процесс распыла топлива первым каскадом. При выходе изделия на режим Малого Газа подача воздуха во II каскад форсунок прекращается.
На основных режимах работы двигателя для обеспечения заданной характеристика расхода топлива во второй каскад форсунок подается топливо.
В топливный коллектор камеры сгорания устанавливаются форсунки (8 штук). Форсунки предназначены для впрыска и распыливания топлива в жаровую трубу.
Форсунки - центробежные двухкаскадные с поочередной подачей во второй каскад воздуха и топлива.
Форсунка состоит из следующих основных деталей:
-воздушного завихрителя;
-завихрителя I каскада.
Корпусом форсунки является бобышка корпуса коллектора в которую устанавливаются распыливающие элементы форсунки: завихритель I каскада выполненный в виде конического шнека с двумя прямоугольными тангенциальными пазами сопло I каскада распылитель II каскада в виде плоской шайбы с двумя тангенциальными пазами. Завихритель I каскада поджимается к соплу I каскада с помощью пружины.
Воздушный завихритель поворачивается по резьбе на бобышку корпуса коллектора одновременно являясь колпачком форсунки который прижимает распылитель II каскада к соплу I каскада а сопло к торцу бобышки корпуса коллектора обеспечивая уплотнение по торцам распыливающих деталей. Воздушный завихритель содержит шесть изогнутых лопаток создающих радиальные каналы закручивающие воздух в сторону затяжки завихрителей по резьбе бобышек. Воздушный завихритель контрится с помощью кольца контровочного которое двумя выступами фиксируется на корпусе и после затяжки завихрителя обжимается в 4 его паза.
Описание конструкции: деталь корпус коллектора представляет собой кольцо с выступающими бобышками. Кольцо довольно тонкое и на нем имеются точные пазы поэтому оно не жесткое в радиальном направление при обработке и выборе баз это необходимо учесть поэтому необходимо выполнить прикладывая силу в осевом направление.
Деталь выполнена из титанового сплава ОТ4-1. Характерные особенности титана - малая плотность 451 кгдм3 высокая прочность которая сохраняется до 6000С коррозионная стойкость. Титановые сплавы сочетают высокую прочность (В= 800-1500 МПа) с хорошей пластичностью (= 12- 25%) относительно хорошую жаропрочность до 600- 7000С высокую коррозионную стойкость во многих агрессивных средах кроме HCL HF. α- титановые сплавы не стареют. Одним из недостатков титановых сплавов является их плохая обрабатываемость режущим инструментом.
Исходя из условий эксплуатации к корпусу коллектора предъявляются следующие требования:
Пазы на торце кольца выполнены по 8 квалитету точности 136 h8
85 H8 1495 h8 162H8. Данные пазы необходимы для того чтобы на сборке в них заложили соответствующие кольца которые в последствие приварят и данные кольца будут закрывать пазы по которым будут поступать топливо и воздух в форсунки. Поэтому для лучшего прилегания и приварки соответствующих колец к корпусу коллектора необходимо пазы выполнить точными.
Обеспечивается данный квалитет чистовым точением.
Для контроля данных пазов в серийном производстве целесообразней использовать шаблоны соответствующего размера.
Цилиндрическая поверхность на 8 бобышках 118 f7. На данную поверхность бобышки накручиваются форсунки и по этой поверхности происходит соприкосновение бобышки и форсунки так как в форсунке происходит смешивание топлива с воздухом недопустимо чтобы данная смесь выходила другим путем нежели чем через отверстие в форсунке поэтому данное соединение должно обеспечивать герметичность. Герметичность обеспечивается соответствующей посадкой.
Данную точность поверхности будем обеспечивать тонким фрезерованием.
Для контроля соответствующего размера будем использовать либо микрометр либо калибр-скобу на размер 118 f7.
Поверхности обрабатываемые с шероховатостью Ra 0.8 3.2.
Имеются 8 пазов с шероховатостью по боковым сторонам Ra 1.6.
Данная поверхность необходима для прилегания к ней соответствующей части форсунки. Обеспечение данной шероховатости не вызовет проблем при обработке зенкерованием.
На данной операции необходимо выдержать позиционный допуск R005 мм. Допуск будет выдержан точностью станка и точностью приспособления.
Для контроля торцевой канавки необходим калибр и кольцо.
Допуск расположения.
Имеется допуск симметричности равный 0.1 мм в радиальном направление относительно оси Р на сквозное отверстие сложной формы.
Соответствующее отверстие будет получено на электроэрозионной операций. Соответствующий допуск обеспечивается аттестованной программой.
Из функционального назначения видно что материал из которого выполнен корпус коллектора должен быть химически не активным с топливом. Деталь должна быть выполнена из сплава с малой плотностью. Должна обеспечивать герметичность выдерживать давление подаваемого топлива.
На детали имеется множество наклонных отверстий которые будем получать сверлением. Для отверстий с углом наклона не более 15° градусов предварительно будем только зацетровывать их положение. При большем наклоне перед зацентровкой будем создавать поверхность перпендикулярную оси сверлимого отверстия.
Технологический анализ конструкции детали с определением показателей технологичности.
Качественный анализ конструкции детали
В соответствии с ГОСТ 14.301-83 разработка технологических процессов производится для изготовления изделий конструкции которых отработаны на технологичность. Отработка конструкции изделия на технологичность направлена повышение производительности труда снижение затрат и сокращение времени на проектирование технологическую подготовку производства изготовление техническое обслуживание и ремонт изделия при обеспечении необходимого качества изделия.
Конструкция изделия может быть признана технологичной если она обеспечивает простое и экономичное изготовление этого изделия. Повышение технологичности конструкции изделия предусматривает проведение комплекса различных мероприятий в числе которых необходимо отметить приведенные ниже.
Уменьшение трудоемкости изготовления детали. Это достигается путем снижения требований к точности детали и использованием точной заготовки у которой высокий коэффициент использования материала. Точность данного изделия средняя. К корпусу предъявляются средние требования по точности при этом будем использовать точный метод получения заготовки.
Создание конфигурации детали и подбор материала позволяющего применение наиболее совершенных исходных заготовок сокращающих объем механической обработки. Данная деталь имеет среднюю конфигурацию и материал тяжело подающийся лезвийной обработке. Материал и конструкцию в данном случае изменить не имеется возможности. Объем лезвийной обработки удастся снизить за счет применения точных заготовок.
Простановка размеров на чертеже с учетом требований их механической обработки позволяющая выполнять обработку по принципу автоматического получения размеров и обеспечивать совмещение конструкторских и технологических баз. Все эти требования на чертеже учтены. Обработку будем вести с учетом требования неизменности баз.
Упрощение конфигурации детали предельно возможное расширение допусков на изготовление и снижение требований к шероховатости обрабатываемых поверхностей с целью уменьшения объема и облегчения механической обработки. В нашем случае все допуски и шероховатости максимизированы.
Создание конфигурации детали позволяющей применение наиболее совершенных и производительных методов механической обработки (обработка многорезцовым фасонным и многолезвийным инструментом накатывание и вихревое нарезание резьбы применение агрегатных и специальных станков и автоматов поточных и автоматических линий). В данном случае применение специальных методов обработки необоснованно т.к. изготовление режущего инструмента под данный сплав титана будет дорог.
Проведение нормализации и унификации детали являющихся предпосылками типизации технологических процессов унификации режущего и мерительного инструментов. Как было сказано выше деталь – кольцо с бобышками и поверхности простые стандартные канавки резьба. Для обработки необходим стандартный инструмент.
Из всего сказанного выше можно сделать вывод что данный корпус коллектора является технологичным.
Количественные показатели технологичности
Основными количественными показателями технологичности являются:
абсолютный технико-экономический показатель - трудоемкость изготовления детали ТН;
уровень технологичности конструкции по трудоемкости
где ТН - достигнутая трудоемкость изделия 44ч.;
ТБН - базовый показатель трудоемкости изделия (определяемый по аналогичности конструкции уже освоенной в производстве) 56ч.;
8 > 05 => деталь технологична
уровень технологичности конструкции по технологической себестоимости
Расчет технологичности будем производить по дополнительным показателям ввиду отсутствия данных.
Дополнительные показатели:
коэффициент использования материала КИМ:
где mД - масса готовой детали 0141 кг;
mЗ - масса заготовки 112 кг.
Масса заготовки и масса готовой детали взяты из базового варианта производства детали.
3 06 => деталь не технологична
коэффициент технологичности по точности
где - средний квалитет обработки детали;
А - квалитет обработки;
n - число размеров соответствующего квалитета.
1 ≥ 08деталь технологична
коэффициент технологичности по шероховатости поверхности
где БСР - средняя шероховатость поверхности определяемая в значениях параметра Ra мкм.
где Б - числовое значение шероховатости (Ra);
ni - число поверхностей с соответствующими числовыми значениями параметра шероховатости.
К = 083 > 032 деталь технологична
коэффициент унификации конструктивных элементов детали
где QУЭ - число унифицированных типоразмеров конструктивных элементов;
QЭ - число типоразмеров конструктивных элементов в изделии.
Ку = 059 > 05 деталь технологична
Вывод из расчетов видно деталь является технологичной но метод получения заготовки не устраивает поэтому необходимо рассмотреть более приемлемый способ получения заготовки.
Выбор метода изготовления заготовки.
Деталь корпус коллектора является ответственной заготовка для нее должна быть получена методом обработки давления.
В базовом варианте в качестве заготовки применяют штамповку. Заготовка представляет собой кольцо 182 мм высотой 27 мм и отверстием 95 мм.
В предыдущем пункте установлено что коэффициент использования материала в базовом варианте технологического процесса низкий.
Одной из передовых технологий которая позволяет получать высококачественные заготовки и экономить металл является объемная изотермическая штамповка (или ковка).
В отличие от обычной объемной горячей штамповки при изотермической штамповке требуется чтобы штамп и штампуемая заготовка были нагреты в процессе деформирования до одной и той же высокой температуры что исключает нежелательное охлаждение поверхности заготовки и возникающий перепад температур. Это существенно улучшает условия для пластического течения материала и позволяет получать высококачественные заготовки значительно более близкие по форме к конечным требованиям.
Таблица 1. Сравнение объемной горячей штамповки и изотермической
Горячая объемная штамповка
Изотермическая штамповка
Скорость деформирования до 1 мс.
Штамповка осуществляется холодным или теплым инструментом.
Получение точных заготовок сложных конфигураций обычной штамповкой затруднительно или невозможно.
Быстрое остывание поверхности штампуемой заготовки от холодного инструмента создает неравномерное температурное поле; отсюда неравномерные деформации и неравномерная проработка материала.
Высокая скорость деформирования создает значительный тепловой эффект в зоне максимальной деформации вызывая еще большую неравномерность течения металла.
В результате возникают высокие и неравномерные напряжения течения металла и недостаточная его пластичность которые нередко ведут к появлению трещин разрывов утяжин и других дефектов.
Штамповки имеют высокие остаточные неравномерные напряжения наклеп которые не полностью снимаются при термообработке; это приводит к короблению и изменению размеров детали в процессе эксплуатации.
Скорость деформирования менее 0005 мс.
В процессе штамповки инструмент и заготовка нагреты до одной и той же высокой температуры.
Высокая точность штамповки заготовок сложных конфигураций особенно тонкостенных поковок характеризующихся большим отношением площади поверхности к объему.
Точность и качество заготовок штампованных в изотермических условиях достигается в результате:
-уменьшения упругих деформаций системы пресс-штамп из-за снижения сопротивления деформированию штампуемого металла и усилия штамповки;
-уменьшения колебаний температуры деформации;
-снижения остаточных напряжений в объеме штампованной поковки что уменьшает ее поводки при остывании и термообработке.
Изотермическая штамповка позволяет изготавливать:
- штамповки непосредственно из исходного литого материала имеющего плохую пластичность;
- штамповки с небольшими штамповочными уклонами или без них с резкими перепадами сечений малыми радиусами переходов и припусками на обработку резанием.
- осуществлять горячее изостатическое прессование для устранения микропористости;
- позволяет штамповать металлы в сверхпластичном состоянии.
Из всего упомянутого выше делаем вывод что деталь будем получать методом изометрической штамповки что позволяет снизить расход металла на деталь по сравнению с обычными процессами горячей штамповки в среднем в 3 раза и повысить КИМ до 05-08. Трудоемкость обработки резанием ШЗ полученных в изотермических условиях снижается на 30-50 и более процентов.
Рис. 1 Эскиз заготовки
Разработка маршрута обработки основных поверхностей.
В качестве заготовки приняли изотермическую штамповку.
Основные поверхности это наружные и внутренние поверхности вращения и резьба.
Наиболее точная поверхность это наружный цилиндр 118 f7.
Данную поверхность можно получить на токарном станке установив деталь на планшайбу при этом необходимо выполнить следующие переходы:
Заготовка выполнена по 12 квалитету.
Черновое точение 10 квалитет.
Получистовое точение 9 квалитет.
Чистовое точение 8 квалитет.
Тонкое точение 7 квалитет.
При данной последовательности выполнения переходов необходимо переустанавливать заготовку восемь раз. При этом способе мы не сможем обеспечить принцип совмещения баз.
Данную поверхность можно получить другим способом закрепив деталь на специальном приспособление и выполнив обработку на фрезерном станке с ЧПУ при этом необходимо выполнить следующие переходы:
Черновое фрезерование 10 квалитет.
Получистовое фрезерование. 9 квалитет.
Чистовое фрезерование 8 квалитет.
Тонкое фрезерование 7 квалитет.
Данную поверхность будем получать методом фрезерования.
Пазы на торце кольца выполненные по 8 квалитету точности 136 h8
Данные пазы можно получить на токарном станке при этом необходимо выполнить переходы:
Однократное точение 10 квалитет.
Чистовое точение 8 квалитет
Эту же поверхность можно выполнить методом фрезерования со следующими переходами:
В итоге мы выбираем получение этой канавки методом точения так как при этом поверхность перпендикулярная выполняемой будет с лучшими условиями плоскостности это необходимо для закладки в этих пазов кольца которые будут привариваться.
Выбор баз разработка маршрута изготовления детали выбор вида оборудования. Составление эскизов обработки с упрощенными обозначениями баз по ГОСТу.
В условиях серийного типа производства как правило используют оборудование с ЧПУ. Поэтому при выборе станка будет отдаваться приоритет станкам с ЧПУ.
Маршрут изготовления детали приведен на первом листе графической части курсовой работы.
5 Изотермическая штамповка.
0 Термообработка. Необходимо провести для снятия внутренних напряжений для улучшения условий резания.
5 Фрезерная операция
Операция выполняется на вертикально-фрезерном станке. Необходимо обработать поверхность для дальнейшего использования в качестве установочной базы. При этом заготовка ставится на необработанную поверхность и прижимается прижимами. На данной операции необходимо выдержать высоту заготовки в размер согласно чертежа.
0 Сверлильная операция.
На данной операции необходимо подготовить центрирующие бызы для последующей обработки детали. При этом заготовку установим на поверхность обработанную на предыдущей операции. В данной операции выполним 3 отверстия по 6 квалитету с жестким позиционным допуском.
5 Слесарная операция
Необходимо убрать все заусенцы.
0 Контрольная операция
Проверить точность выполнения отверстий их расположение и высоту заготовки.
5 Сверлильно-фрезерно-расточная операция.
На данной операции выполним обработку всех поверхностей располагающиеся на нижней плоскости для этого понадобиться сверлильно-фрезерно-расточной станок с ЧПУ. Базирование происходит по уже подготовленным поверхностям. Установочной плоскостью является фрезерованная поверхность при этом установка идет по плоскости. Центрирующей поверхностями будут являться три отверстия выполненные на сверлильной операции. Деталь будем прижимать с помощью прижимов.
5 Контрольная операция. Проконтролировать полученные размеры поверхностей.
0 Сверлильно-фрезерная с ЧПУ операция.
Пользуясь принципом неизменности баз в качестве центрирующих поверхностей используем заранее подготовленные отверстия. Установочной плоскостью будет являться перед этим обработанная плоскость. Деталь будем прижимать с помощью прижимов.
Деталь возможно выполнить на сверлильно-фрезерном станке с ЧПУ.
На данной операции получим все необработанные поверхности.
Необходимо снять все заусенцы и притупить острые кромки.
5 Контрольная операция.
0 Электроэрозионная с ЧПУ операция.
Используем электроэрозионный станок вырезка отверстия происходит с помощью проволоки по программе.
0 Приемочный контроль.
Расчет припуска на обработку и составление расчетной таблицы.
Все данные для расчета припусков на обработку поверхности взяты из источника [1] т.1 гл. 4 стр. 186 табл. 25.
Таблица 2 Расчет припуска на размер
Наименование детали – Корпус коллектора. Материал – ОТ4-1
Элементарная поверхность для расчета припуска –
Маршрут обработки мм
Элементы припуска мкм
Расчетный припуск zmin мкм
Расчетный минимальный размер мм
Допуск на изготовление T мкм
Принятые (округленные) размеры по переходам мм
Полученные предельные припуски мкм
Rz – высота неровностей профиля;
h – глубина дефектного поверхностного слоя;
– суммарное отклонение расположения поверхности;
– погрешность установки заготовки.
Погрешность установки заготовки не учитывается так как не производится выверка заготовки на станке.
zi min = Rzi-1 + hi-1 + Δ i-1 + i
Припуск под чистовое фрезерование:
zi min = 32+50+20 = 102 мкм
Определим размеры полученные после чернового фрезерования:
а'min i -1 = аmin i + zi min
а' min i -1 = 1489 + 0.102 = 14.992 мм
а'max i -1 = а'min i -1 + T i -1
а'max i -1 = 14.992+0.180 = 15.172 мм
Принимаем am ama zi min = 110 мкм.
Максимальный припуск:
zi max = zi min + T i-1- T i
zi max = 110 + 180 -110 = 180 мкм
Припуск под изотермическую штамповку:
zi min = 80+150+60 =290 мкм
Определим размеры полученные после изотермической штамповки:
а' min i -1 = 15 + 0.29 = 1529 мм
а'max i -1 = 1529+0.270 = 15.56 мм
Принимаем am ama zi min = 300 мкм.
zi max = zi min + Td i-1 - Td i
zi max = 300 + 270 -180 = 390 мкм
ZΣ max = zΣ min + T з - T д
0 = 410+ 270 - 110 = 570 следовательно расчет выполнен правильно.
Из расчета видны минимальные границы припуска на сторону для того что бы гарантировать качество обрабатываемых поверхностей мы завысим величину припуска и примем его равным 15 мм на сторону.
Расчет припуска на размер мм
Все данные для расчета припусков на обработку поверхности взяты из источник [1 табл.24 стр. 187]
Таблица 3 Расчет припуска на размер мм
Наименование детали – Корпус коллектора.
Элементарная поверхность для расчета припуска – цилиндр мм
Маршрут обработки цилиндра мм
Расчетный припуск 2zmin мкм
Допуск на изготовление Td мкм
Изотермическая штамповка IT12
Отклонение расположения необходимо учитывать: у заготовок (под первый технологический переход); после черновой обработки лезвийным инструментом (под последующий технологический переход).
Для изотермической штамповки
где 1 – отклонение торца от перпендикулярности 60 мкм
– отклонение от концентричности реально расположенной с идеально расположенной бобышкой [1 табл.17 стр. 186] 05 мм
zi min = 2 (Rzi-1 + hi-1 + Δ i-1 + i)
Припуск под тонкое фрезерование:
zi min = 2 (25+25) = 100 мкм
Определим размеры полученные после чистового растачивания:
d'min i -1 = dmin i + 2zi min
d' min i -1 = 11766 + 0.1 = 11866 мм
d'max i -1 = dmin i-1 + Td i -1
d'max i -1 = 11866 + 0027 = 11893 мм
Принимаем dm dma 2zi min = 100 мкм.
zi max = 2zi min + Td i-1 - Td i
zi max = 100 + 27 – 18 = 109 мкм
Припуск чистовое фрезерование:
zi min = 2 (40+40) = 160 мкм
d' min i -1 = 1187 + 0.16 = 1203 мм
d'max i -1 = 1203 + 0043 = 12073мм
Принимаем dm dma 2zi min = 160 мкм.
zi max = 160 + 43 – 27 = 176 мкм
Припуск получистовое фрезерование:
zi min = 2 (60+120+100) = 560 мкм
d' min i -1 = 1203 + 0.56 = 1259 мм
d'max i -1 = 1259 + 007 = 1266мм
Принимаем dm dma 2zi min = 570 мкм.
zi max = 570 + 70 – 43 = 597 мкм
Припуск под черновое фрезерование:
zi min = 2 (80+150+504) = 1468 мкм
d' min i -1 = 126 + 1468 = 14068 мм
d'max i -1 = 14068 + 018 = 14248мм
Принимаем dm dma 2zi min = 1470 мкм.
zi max = 1470 + 180 – 70 = 1580 мкм
ZΣ max = 2zΣ min + T з - T д
62 = 2300+ 180 - 18 = 2462 следовательно расчет выполнен правильно.
Разработка операционной технологии с выбором моделей оборудования и типов режущих инструментов и нормированием.
Станок должен позволять обрабатывать наклонные отверстия выполненные на одном радиусе поэтому для данной операции необходимо иметь круговой стол.
Для данной операции подходит обрабатывающий центр фирмы Willemin-macodel 508S
Характеристика станка:
Spindle speed: 42000 RPM
Tool magazine: 72 positions
T-slot table Ш 320 mm
High-pressure cooling through spindle at 80 bar
Cutting fluid thermostabilisation
Tool breakage detector and tool setting devic
Part probing system
Part loading and unloading robot
Рис. 2 Кинематика станка.
Режущий инструмент подбираем по основному каталогу режущего инструмента фирмы Sandvik Coromant.
Режимы резания подбираем с помощью программы PluraGuide поставляемой Sandvik Coromant для своего режущего инструмента. Для этого в программе выбирает титановый сплав с НВ 220 единиц и для каждого инструмента задаем соответствующую глубину резания и ширину фрезерования.
Переход 01 Фрезеровать контур по программе.
Выбираем цельную твердосплавную фрезу CoroMill Plura сплав GC1630
Код заказа инструмента R216.34-1545-AC26N
Режимы резания согласно программе:
Частота вращения фрезы n=2200 мин-1
Подача минутная S=1170 мммин
Подача на зуб Sz=0.133 ммзуб
Скорость резания V=103 ммин
Длину рабочего перемещения определим эскиза обработки L=1120 мм
Основное время обработки мин
L – длина фрезерования.
tосн = 11201170=0.98 мин
Переход 02 Фрезеровать контур по программе.
Код заказа инструмента R216.34-0545-AC11N
Частота вращения фрезы n=8200 мин-1
Подача минутная S=516 мммин
Подача на зуб Sz=0.021 ммзуб
Скорость резания V=129 ммин
Длину рабочего перемещения определим из эскиза обработки L=480 мм
tосн = 480516=0.93 мин
Переход 03 Точить пазы в размер 138 h10 145H10 153 h10
0H8 и глубиной 3 мм.
Выбираем двух лезвийную пластину 123 – GF Ширина пластины 35 мм Сплав 1125
Код заказа инструмента N123G2-0350-003-GF
Выбираем соответствующую державку RLS151.25. 2525-20
Частота вращения фрезы n=230 мин-1
Подача на оборот Sо=005 ммоб
Скорость резания V=100 ммин
Длину рабочего перемещения определим из эскиза обработки L=8 мм
tосн = 8(005230)=0.7 мин
Переход 04 Точить пазы в размер 136 h8 1485 H8 1495 h8 162H8 и глубиной 2 мм.
Выбираем двух лезвийную пластину 123 – GF Ширина пластины 5 мм Сплав 1125
Код заказа инструмента N123G2-0450-005-GF
Длину рабочего перемещения определим из эскиза обработки L=12 мм
Переход 05 Точить фаску согласно чертежа в размер 06х45°
Выбираем пластину CNMG 1204 05-PF Сплав 1025
Выбираем соответствующую державку PCBNRL2525M12
Подача на оборот Sо=01 ммоб
Длину рабочего перемещения определим из эскиза обработки L=1 мм
Переход 06 Зацентровать 24 места под отверстия
Инструмент: Сверло центровочное сплав 1020
Частота вращения фрезы n=3180 мин-1
Подача на оборот Sо=0006 ммоб
Скорость резания V=10 ммин
где i – количество отверстий.
Переход 07 Сверлить 8 отверстий 1 мм
Инструмент: сверло 1 мм сплав 1020
Код заказа R840 – 0100-70-A0B
Переход 08 Сверлить 8 отверстий 2.5 мм под углом 15° и отверстие под углом 10° на глубину 8 мм
Инструмент: сверло 25 мм сплав 1020
Код заказа R840 – 0250-50-A0B
Частота вращения фрезы n=3820 мин-1
Подача на оборот Sо=002 ммоб
Скорость резания V=30 ммин
Переход 09 Сверлить 2 отверстий 3 мм на глубину 15 мм и 12 мм согласно чертежа
Инструмент: сверло 3 мм сплав 1220
Код заказа R840 – 0300-30-A0А
Подача на оборот Sо=006 ммоб
Переход 10 Сверлить 4 отверстия 45 мм насквозь согласно чертежа
Инструмент: сверло 45 мм сплав 1220
Код заказа R840 – 0450-30-A0А
Частота вращения фрезы n=2120 мин-1
Переход 11 Зенкеровать 4 отверстия 53 мм насквозь согласно чертежа
Инструмент: Зенкер 53 мм сплав 1220
Частота вращения фрезы n=1800 мин-1
Переход 12 Сверлить 2 отверстия 6 мм на глубину 149 мм согласно чертежа
Инструмент: сверло 6 мм сплав 1220
Код заказа R840 – 0600-30-A0А
Частота вращения фрезы n=1590 мин-1
Подача на оборот Sо=008 ммоб
Переход 13 Зенкеровать 2 отверстия 88 мм на глубину 149 согласно чертежа
Инструмент: Зенкер 88 мм сплав 1220
Частота вращения фрезы n=1440 мин-1
Скорость резания V=40 ммин
Разработка схемы приспособления.
Необходимо разработать приспособление для 050 фрезерной операции. Исходя из эскиза данной операции видим что деталь можно установить различными способами:
Установить заготовку базируя по плоскости и наружной цилиндрической поверхности (призма) и зажав второй призмой таким образом лишив заготовку пяти степеней свободы. Это позволит нам однозначно определять ось заготовки но при этом нет возможности однозначно определить ее в пространстве. Так же при этом сила закрепления будет действовать на заготовку в радиальном направлении то есть – в направлении самых точных из выдерживаемых размеров что недопустимо с нежесткой заготовкой.
Установить заготовку в трех кулачковом патроне. Лишив детали пяти степеней свободы нет возможности однозначно определить ее в пространстве. Так же при данном закреплении сила закрепления действует в радиальном направлении и заготовка деформируется в силу малой жесткости в данном направлении.
Установить заготовку на плоскость с центрированием по трем ромбическим пальцам силу закрепления направив по оси в торец заготовки. Установив деталь по плоскости мы лишает ее трех степеней свободы. Оставшихся трех степеней свободы мы лишаем с помощью трех ромбических пальцев. При использовании трех ромбических пальцев в отличие от традиционной схемы с двумя пальцами где один цилиндрический а другой ромбический угол поворота заготовки немного меньше и легче устанавливать деталь на пальцы что позволяет уменьшить влияние зазора а так же погрешность базирования. Сила закрепления будет приложена перпендикулярно направлению самых точных размеров что позволит минимизировать погрешность закрепления.
Рассмотрев варианты приходим к выводу что необходимо применять 3 способ установки.
возможность обработки детали с 5 сторон за один установ;
возможность выдержать принцип постоянства баз;
минимальная погрешность установки
простота конструкции.
При выбранной схеме базирования и закрепления заготовка устанавливается на опорные пластины базируется на три пальца и сверху поджимается тремя прижимами.
Заготовка закрепляется механическими зажимными устройствами.
На данной операции необходимо выполнить обработку всех поверхностей кроме установочной плоскости поэтому в приспособление нам будет необходимо предусмотреть устройства убирания пальцев из зоны резания и смену прижимов при выполнении наружной контурной обработки детали.
Рис. 3 Схема действия сил
Силы стремятся сдвинуть заготовку с установочных элементов. Смещение заготовки предупреждается силами трения в местах контакта заготовки с установочными элементами.
Для данного случая подходит следующая схема закрепления.
Рис. 4 Схема закрепления заготовки.
где коэффициент трения между заготовкой зажимным устройством и заготовкой и опорами. Введем коэффициент запаса k и получим
Расчеты обосновывающие экономическую целесообразность применения приспособления.
Экономическая целесообразность выбора и применения станочного приспособления определяется его окупаемостью.
Все затраты на оснащение производства приспособлениями должны быть возмещены за счет экономии производственных затрат.
Экономическая целесообразность применения приспособления должна быть выражена условием
где Э – Ожидаемая экономия цеховой себестоимости обработки детали при применение приспособления;
- затраты на изготовление приспособления и на его эксплуатацию.
В условиях мелкосерийного и серийного производства целесообразней всего использовать сборно-разборное приспособление. По своему назначению оно будет являться специальным так как в собранном виде рассчитано на установку и закрепление однотипных деталей. Собирается из отдельных нормализованных и стандартизованных узлов но при необходимости можно дополнять специальными деталями.
Достоинства сборно-разборных приспособлений - несложность сборки и экономичность оснащения.
Недостаток: пониженная жесткость приспособления из-за использования резьбовых соединений.
Годовые затраты на приспособление [1 стр. 5]
где Ап – коэффициент затрат на проектирование приспособления Ап=05
Аа – коэффициент амортизации приспособлений Аа = 1
А – коэффициент годовых затрат на эксплуатацию СРП А=025
Сс – стоимость нормализованных специальных деталей и узлов включая затраты на доработку деталей узлов и компоновку. Сс = 25000 руб
Т – срок использования приспособления
Экономия цеховой себестоимости при применении данного приспособления будет достигнута в силу следующих причин:
- Увеличение производительности труда что позволит снизить затраты на заработную плату;
- Сокращение штучно-калькуляционного времени что позволит сократить расходы на электроэнергию.
Ожидаемая экономия цеховой себестоимости 90000 руб.
что экономически доказывает целесообразность применения приспособления.
Выбор установочных зажимных и других элементов приспособлений.
Рис. 5 Схема базирования
Установочная плоскость лишает трех степеней свободы (123)
Установочная плоскость разделена на 4 сектора они воспринимают силу закрепления. Возможности выполнить установочный элемент в виде кольца нет поскольку возникнет проблема при собираемости будет необходимо задавать жесткие позиционные допуски на отверстия для крепления кольца.
Зажимная плоскость будет плоскость противолежащая установочной так как деталь в данном сечении более жесткая. Зажимными элементами будут являться планки прижимающие деталь к установочной плоскости. Для равномерного прижима необходимо установить по возможности максимальное количество планок. В данном случае будет достаточно трех планок.
Роль центрирующей элементов будут выполнять три ромбических пальца которые лишают заготовку оставшихся трех степеней свободы.
Выбор типа зажимного устройства и зажимных элементов.
Привод может быть - ручной пневматический гидравлический пневмогидравлический электрический электромагнитный магнитный вакуумный.
В данном случае выбираем ручной так как он отвечает необходимым требованиям: простой по конструкции компактный максимально удобный и безопасным в работе а так же при обработке возникают не большие силы резания.
В качестве зажимного устройства можно использовать
Винтовые зажимные устройства
Преимущества: простые компактные надежные
Эксцентриковые зажимные устройства
Преимущества: быстродействие обладают свойством самоторможения.
Недостаток: чувствительны к вибрациям.
Рычажные зажимные устройства
Применяются как промежуточные звенья легкие быстродействующие самотормозящие.
В приспособление будем использовать винтовые зажимные устройства и рычажные в сочетание с винтовыми.
Определение допустимой погрешности установки или условий собираемости из условий обеспечения точности обработки или сборки.
Будем исходить из того положения что суммарная погрешность обработки складывающаяся из погрешностей вносимых приспособлением и погрешностей способа обработки не должна быть больше допуска на соответствующий заданный размер заготовки:
где Tпр - суммарная погрешность вносимая приспособлением;
Тоб - суммарная погрешность способа обработки включающая погрешности упругих деформаций системы СПИД размерного износа инструмента погрешности настройки станка температурных деформаций и т.п.;
Т-допуск на размер выполняемый на данной операции.
где k-коэффициент равный 06-08;
-экономическая точность обработки мм.
Экономическая точность при фрезерование по 10 квалитету для размера 15 мм принимаем 01 мм
Допуск на размер 15 по 12 квалитету равен 018 мм
Для обеспечения заданной точности приспособление не должно вносить погрешность более 01 мм
Составление схемы сил действующих на заготовку или собираемое изделие и расчет зажимного устройства.
Из схемы закрепления заготовки рис. 3 получим
где - коэффициент трения между заготовкой зажимным устройством и заготовкой и опорами;
В данном случае в опоре и прижиме происходит контакт сталь - титан
f1=f2= 04 - коэффициент трения сталь по титану
k – Расчетный коэффициент надежности закрепления детали
где К0 – гарантированный коэффициент запаса;
К1 – коэффициент учитывающий состояние поверхности заготовки;
К2 - коэффициент учитывающий увеличения сил резания от прогрессирующего затупления инструмента;
К3 – коэффициент учитывающий изменение сил резания при обработке прерывистых поверхностей;
К4 – коэффициент учитывающий непостоянство сил при закреплении;
К5 – коэффициент учитывающий удобство расположения рукоятки зажимного устройства;
К6 - коэффициент учитывающий наличие опрокидывающего момента.
Коэффициенты определяются в
Принимаем k = 25 минимальное значение коэффициента надежности закрепления.
Определим силу резания
Определим режимы резания
Глубина резания при фрезеровании t = h= 15 мм;
Ширина фрезерования В=7мм;
Sz=0.125ммоб; [2 табл.36стр. 176]
Выбираем диаметр фрезы и число зубьев. Фреза концевая из ВК8.
[ 2 табл. 71 стр. 176]
Среднее значение периода стойкости
В приспособление используется три прижима рис.1 поэтому действующая сила должна быть разделена на три.
Используемые прижимы по техническим характеристикам могут обеспечивать усилие до 10000 Н значит конструкцию прижимов менять нет необходимости.
Так как для передачи усилия на прижимную планку мы используем винт растяжения момент необходимый создать на нем при закручивание гайки равен где
Q1 – реакция в точке прижима планки гайкой.
d – средний диаметр резьбы 8 мм = 0008 м
Рис. 6 Прижим и реакции возникающие при закрепление.
Из рисунка видно что поэтому
Определить усилие на ключе.
Руководствуясь ГОСТ 2839-80 длина рукоятки ключа для М8 равна 110 мм отсюда следует что сила необходимая для закручивания равна 11011=100 Н
Рис. 7 Прижим и реакции на нем при закреплении.
Необходимая сила на ключе равна 41110= 38 Н
Назначение технических требований на приспособление обеспечивающих заданную точность.
Ранее было определенно что приспособление не должно вносить погрешность более 01 мм. Исходя из этих условий необходимо назначить технические требования.
Назначим технические требования.
Для установочных элементов.
Допуск плоскостности сектора не должен превышать 001 мм
Допуск параллельности сектора относительно основания приспособления не должен превышать 002 мм
Для центрирующих элементов
Допуск перпендикулярности пальцев относительно основания приспособления не должен превышать 002 мм
Позиционный допуск расположения осей ромбических пальцев относительно угла между ними радиуса на котором они расположены не должен превышать 005 мм.
Для элементов определяющие положение приспособления на станке.
Допуск параллельности боковых сторон шпонок относительно пазов станка не должен превышать 002 мм
Допуск перпендикулярности боковых сторон шпонок относительно основания приспобления не должен превышать 002 мм
Расчет точности обработки
Анализ операционного эскиза показывает что от конструкции станочного приспособления зависит только выполнение одного линейного размера мм. Дополнительных условий нет.
Точностные расчеты таким образом сводятся к определению условий выполнения этого параметра точности.
Отклонение от номинального размера здесь возможно из-за следующих погрешностей
с – погрешность от неточности станка определяемая как отклонение от перпендикулярности оси вращения шпинделя к рабочей поверхности стола с принимаем равным 0001;
р.п. – погрешность расположения оси фрезы по отношению к установочным элементам приспособления р.п. принимаем равным 001;
у.п. – погрешность пространственного положения плоскости обрабатываемой поверхности при установке на опорные сектора и установочные пальцы;
н.п. – погрешность пространственного положения установочных элементов приспособления по отношению к опорной поверхности корпуса станочного приспособления;
- погрешность износа инструмента принимаем 13 допуска на размер. = 006 мм
Погрешности у.п. и н.п. – взаимосвязаны. Для их расчета возьмем принятый допуск параллельности Т=002мм на длине опорных секторов 100 мм. Расстояние от опорной поверхности корпуса до опорной поверхности заготовки равно 108мм. Таким образом имеем:
Рассчитываем величину суммарной погрешности по предельным значениям:
Анализ результатов показывает следующее. При расчете по предельным значениям условие точности обработки выполняется. Запас точности обработки составляет 49%.
Таким образом можно сделать вывод что приспособление обеспечивает требуемую точность лимитирующего размера т.к. запасы точности обработки относительно велики.
Выбор материалов для основных деталей и назначение термической обработки.
В качестве установочной поверхности используем сектор поз.4 который можно выполнить из стали У8А 20Х и 12ХНЗА. Детали из стали У8А закаливаются до твердости НRС 48 – 58. Детали из стали 20Х и 12ХНЗА цементируются на глубину 08 – 12 мм и закаливаются до твердости НRС 56—62.
Выбираем 20Х как самый дешевый.
Плита изготавливается из стали 12ХНЗА цементируются на глубину 12 – 16 мм и закаливаются до твердости НRС 58 – 62.
Прижим изготовляются из стали 40Х азотируются на глубину 03 – 05 мм и закаливаются до твердости НV 550—600.
Остальные детали выполнены либо по ГОСТ либо поступают к нам уже с определенными удовлетворяющими нас характеристиками заданными заводом изготовителем.
Описание конструкции и работы приспособления
Разработана конструкция приспособления для обработки детали “Корпус коллектора” на обрабатывающем центре. Обрабатываемую заготовку устанавливаем на плоскость выполненную из четырех секторов при этом происходит центрирование заготовки за счет трех убираемых ромбических пальцев. Фиксация заготовки производится тремя прижимами поз. 3 для чего необходимо затянуть гайки поз. 18 с помощью динамометрического ключа с моментом 11 Нм. Затем производим обработку заложенную технологическим процессом до перехода в котором выполняется обработка внешней стороны кольца. В этот момент программа делает технологический останов и оператор производит перезакрепление заготовки при помощи прижимов поз. 14 установленных с внутренней стороны кольца. Для этого необходимо закрутить винты на прижиме с помощью специального ключа с моментом 4.1 Нм после чего необходимо отвести вниз ромбические пальцы для чего необходим отвести рычаг изделия поз. 22 до упора по часовой стрелке затем нажать на пульт УЧПУ для продолжения операции в ходе которой производится наружная обработка кольца сфрезеровываются искусственно созданные базы.
Приспособление простое по конструкции несложно в изготовлении и надежно в работе.
Горошкин А.К. Приспособления для металлорежущих станков. Справочник. М. Машиностроение 1979 г.
Справочник технолога-машиностроителя в 2х томах. Под ред.
А.Г. Косиловой и Р.К. Мещерякова М. Машиностроение1985.
Васильев А.С. Кондаков А.И.. Выбор заготовок в машиностроении..- М.: Машиностроение 2007-506 с.
Приспособление.docx
Разработка схемы приспособления.
Необходимо разработать приспособление для 050 фрезерной операции. Исходя из эскиза данной операции видим что деталь можно закрепить различными способами:
Закрепить заготовку установив на плоскость и зажав в призме что позволит нам однозначно определять ось заготовки но при этом у нас нет возможности однозначно определить ее в пространстве так же при этом сила закрепления будет действовать на заготовку в радиальном направление что недопустимо с нежесткой заготовкой.
Закрепить заготовку в трех кулачковом патроне. При данном закрепление сила закрепления действует в радиальном направление и заготовка деформируется в силу не жесткости в данном направление.
Установить заготовку на плоскость с центрированием по трем ромбическим пальцам силу закрепления направив по оси в торец заготовки. При использование трех ромбических пальцев в отличие от традиционной схемы с двумя пальцами где один цилиндрический а другой ромбический угол поворота заготовки немного меньше и легче устанавливать деталь на пальцы что позволяет уменьшить влияние зазора а так же погрешность базирования.
Рассмотрев варианты приходим к выводу что необходимо применять 3 способ закрепления.
- простота конструкции;
- возможность выдержать принцип постоянства баз;
- возможность обработки детали с 5 сторон.
При выбранной схеме базирования и закрепления заготовка устанавливается на опорные пластины базируется на три пальца и сверху поджимается тремя прижимами.
Заготовка закрепляется механическими зажимными устройствами.
На данной операции необходимо выполнить обработку всех поверхностей кроме установочной плоскости поэтому в приспособление нам будет необходимо предусмотреть устройства убирания пальцев из зоны резания и смену прижимов при выполнение наружной контурной обработки детали.
Рис. 2 Схема действия сил
Силы стремятся сдвинуть заготовку с установочных элементов. Смещение заготовки предупреждается силами трения в местах контакта заготовки с установочными элементами.
Для данного случая подходит следующая схема закрепления.
Рис. 3 Схема закрепления заготовки.
где коэффициент трения между заготовкой зажимным устройством и заготовкой и опорами. Введем коэффициент k и получим
Расчеты обосновывающие экономическую целесообразность применения приспособления.
Экономическая целесообразность выбора и применения станочного приспособления определяется его окупаемостью.
Все затраты на оснащение производства приспособлениями должны быть возмещены за счет экономии производственных затрат.
Экономическая целесообразность применения приспособления должна быть выражена условием
где Э – Ожидаемая экономия цеховой себестоимости обработки детали при применение приспособления;
- затраты на изготовление приспособления и на его эксплуатацию.
В условиях мелкосерийного и серийного производства целесообразней всего использовать сборно-разборное приспособление. По своему назначению оно будет являться специальным так в собранном виде рассчитано на установку и закрепление однотипных деталей. Собирается из отдельных нормализованных и стандартизованных узлов но при необходимости можно дополнять специальными деталями.
Достоинства несложность сборки и экономичность оснащения.
Недостаток: малая жесткость приспособления из-за использования резьбовых соединений.
Годовые затраты на приспособление [1 стр. 5]
где Ап – коэффициент затрат на проектирование приспособления Ап=05
Аа – коэффициент амортизации приспособлений Аа = 1
А – коэффициент годовых затрат на эксплуатацию СРП А=025
Сс – стоимость нормализованных специальных деталей и узлов включая затраты на доработку деталей узлов и компоновку. Сс = 25000 руб
Т – срок использования приспособления
Экономия цеховой себестоимости при применение данного приспособления будет достигнута в силу следующих причин:
- Увеличение производительности труда что позволит снизить затраты на заработную плату;
- Сокращение штучно-калькуляционного времени что позволит сократить расходы на электроэнергию.
Ожидаемая экономия цеховой себестоимости 90000 руб.
что экономически доказывает целесообразность применения приспособления.
Выбор установочных зажимных и других элементов приспособлений.
Рис. 4 Схема базирования
Установочная плоскость лишает трех степеней свободы (123)
Установочная плоскость разделена на 4 сектора они воспринимают силу закрепления. Возможности выполнить из кольца нет возникнет проблема при собираемости будет необходимо задавать жесткие позиционные допуска на отверстия для крепления кольца.
Зажимная плоскость будет плоскость противолежащая установочной так как деталь в данном сечение более жесткая. Зажимными элементами будут являться планки прижимающие деталь к установочной плоскости. Для равномерного прижима необходимо установить по возможности максимальное количество планок. В данном случае будет достаточно трех планок.
Роль центрирующей элементов будут выполнять три ромбические пальца которые лишают оставшихся трех степеней свободы.
Определение допустимой погрешности установки или условий собираемости из условий обеспечения точности обработки или сборки.
Будем исходить из того положения что суммарная погрешность обработки складывающаяся из погрешностей вносимых приспособлением и погрешностей способа обработки не должна быть больше допуска на соответствующий заданный размер заготовки:
где Tпр-суммарная погрешность вносимая приспособлением;
Тоб-суммарная погрешность способа обработки включающая погрешности упругих деформаций системы СПИД размерного износа инструмента погрешности настройки станка температурных деформаций и т.п.;
Т-допуск на размер выполняемый на данной операции.
где k-коэффициент равный 06-08;
-экономическая точность обработки мм.
Экономическая точность при фрезерование по 10 квалитету для размера 15 мм принимаем 01 мм
Допуск на размер 15 по 12 квалитету равен 018 мм
Для обеспечения заданной точности приспособление не должно вносить погрешность более 01 мм
Составление схемы сил действующих на заготовку или собираемое изделие и расчет зажимного устройства.
где - коэффициент трения между заготовкой зажимным устройством и заготовкой и опорами;
В данном случае в опоре и прижиме происходит контакт сталь - титан
f2= 04 - коэффициент трения сталь по титану
k – Расчетный коэффициента надежности закрепления детали
где К0 – гарантированный коэффициент запаса;
К1 – коэффициент учитывающий состояние поверхности заготовки;
К2 - коэффициент учитывающий увеличения сил резания от прогрессирующего затупления инструмента;
К3 – коэффициент учитывающий изменение сил резания при обработке прерывистых поверхностей;
К4 – коэффициент учитывающий непостоянство сил при закреплении;
К5 – коэффициент учитывающий непостоянство сил зажимных устройств с ручным приводом;
К6 - коэффициент учитывающий наличие опрокидывающего момента.
Принимаем k = 25 минимальное значение коэффициента надежности закрепления.
Определим силу резания
Определим режимы резания
Глубина резания при фрезеровании t = h= 15 мм;
Ширина фрезерования В=7мм;
Sz=0.125ммоб; [ 2 табл.36стр. 176]
Выбираем диаметр фрезы и число зубьев. Фреза концевая из ВК8.
[ 2 табл. 71 стр. 176]
Среднее значение периода стойкости
В приспособление используется три прижима поэтому действующая сила должна быть разделена на три.
Используемые прижимы по техническим характеристикам могут обеспечивать усилие до 10000 Н значит конструкцию прижимов менять нет необходимости.
Так как для передачи усилия на прижимную планку мы используем винт растяжения момент необходимый создать на нем при закручивание гайки равен где
Q1 – реакция в точке прижима планки гайкой.
d – средний диаметр резьбы 8 мм = 0008 м
Рис. 4 Прижим и реакции возникающие при закрепление.
Из рисунка видно что поэтому
Определить усилие на ключе.
Руководствуясь ГОСТ 2839-80 длинна рукоятки ключа для М8 равна 110 мм отсюда следует что сила необходимая для закручивания равна 1264011=115 Н
Рис. 5 Прижим и реакции на нем при закрепление.
Необходимая сила на ключе равна 41110= 38 Н
Назначение технических требований на приспособление обеспечивающих заданную точность.
Ранее было определенно что приспособление не должно вносить погрешность более 01 мм исходя из этих условий необходимо назначит технические требования.
Назначим технические требования.
Для установочных элементов.
Допуск плоскостности сектора не должен превышать 001 мм
Допуск параллельности сектора относительно основания приспособления не должен превышать 002 мм
Для центрирующих элементов
Допуск перпендикулярности пальцев относительно основания приспособления не должен превышать 002 мм
Позиционный допуск расположения осей ромбических пальцев относительно угла между ними радиуса на котором они расположены не должен превышать 005 мм.
Для элементов определяющие положение приспособления на станке.
Допуск параллельности боковых сторон шпонок относительно пазов станка не должен превышать 002 мм
Допуск перпендикулярности боковых сторон шпонок относительно основания приспобления не должен превышать 002 мм
Расчет точности обработки
Анализ операционного эскиза показывает что от конструкции станочного приспособления зависит только выполнение одного линейного размера мм. Дополнительных условий нет.
Точностные расчеты таким образом сводятся к определению условий выполнения этого параметра точности.
Отклонение от номинального размера здесь возможно из-за следующих погрешностей
с – погрешность от неточности станка определяемая как отклонение от перпендикулярности оси вращения шпинделя к рабочей поверхности стола с принимаем равным 001;
р.п. – погрешность расположения оси фрезы по отношению к установочным элементам приспособления р.п. принимаем равным 002;
у.п. – погрешность пространственного положения плоскости обрабатываемой поверхности при установке на опорные сектора и установочные пальцы;
н.п. – погрешность пространственного положения установочных элементов присобления по отношению к опорной поверхности корпуса станочного приспособления;
- погрешность износа инструмента принимаем 13 допуска на размер. = 006 мм
Погрешности у.п. и н.п. – взаимосвязаны. Для их расчета возьмем принятый допуск параллельности Т=002мм на длине опорных секторов 100 мм. Расстояние от опорной поверхности корпуса до опорной поверхности заготовки равно 108мм. Таким образом имеем:
Рассчитываем величину суммарной погрешности по предельным значениям:
Анализ результатов показывает следующее. При расчете по предельным значениям условие точности обработки выполняется. Запас точности обработки составляет 38%.
Таким образом можно сделать вывод что приспособление обеспечивает требуемую точность лимитирующего размера т.к. запасы точности обработки относительно велики.
Выбор материалов для основных деталей и назначение термической обработки.
В качестве установочной поверхности используем сектор поз.4 который можно выполнить из стали У8А 20Х и 12ХНЗА. Детали из стали У8А закаливаются до твердости НRС 48 – 58. Детали из стали 20Х и 12ХНЗА цементируются на глубину 08 – 12 мм и закаливаются до твердости НRС 56—62.
Выбираем 20Х как самый дешевый.
Плита изготавливается из стали 12ХНЗА цементируются на глубину 12 – 16 мм и закаливаются до твердости НRС 58 – 62.
Прижим изготовляются из стали 40Х азотируются на глубину 03 – 05 мм и закаливаются до твердости НV 550—600.
Остальные детали выполнены либо по ГОСТ либо поступают к нам уже с определенными удовлетворяющими нас характеристиками заданными заводом изготовителем.
Описание конструкции и работы приспособления
Разработан конструкция приспособления для обработки детали “Корпус коллектора” на обрабатывающем центре. Обрабатываемую заготовку устанавливаем на плоскость выполненную из четырех секторов при этом происходит ее центрирование за счет трех убираемых ромбических пальцев фиксация заготовки производится тремя прижимами поз. 3 для чего необходимо затянуть гайки поз. 18 с помощью динамометрического ключа с моментом 1264 Нм. Затем производим обработку заложенную технологическим процессом до перехода в котором выполняется обработка внешней стороны кольца в этот момент программа делает технологический останов и оператор производит перезакрепления заготовки при помощи прижимов поз. 14 установленных с внутренней стороны кольца для чего необходимо закрутить винты на прижиме с помощью отвертки с моментом 4.1 Нм после чего ему необходимо отвести вниз ромбические пальцы для чего необходим отвести рычаг изделия поз. 22 до упора по часовой стрелке затем нажать на пульт УЧПУ для продолжения операции в ходе которой производится наружная обработка кольца сфрезеровываются искусственно созданные базы.
Приспособление простое по конструкции несложно в изготовлении и надежно в работе.
Горшкин А.К. Приспособление для металлорежущих станков. Справочник. М. Машиностроение 1979 г.
Справочник технолога-машиностроителя в 2х томах. Под ред.
А.Г. Косиловой и Р.К. Мещерякова М. Машиностроение1985.
Маршрутные карты.doc
МГТУ им. Н.Э. Баумана
Код наименование операции
Обозначение документа
Код наименование оборудования
5 Изотермическая штамповка ИОТ № ХХХ–ХХ
0 Термообработка ИОТ № ХХХ–ХХ
5 Вертикально-фрезерная ИОТ № ХХХ–ХХ
Вертикально-фрезерный станок 6540
0 Радиально- сверлильная ИОТ № ХХХ–ХХ
Радиально-сверлильный станок 2М55
5 Слесарная ИОТ № ХХХ–ХХ
0 Контрольная ИОТ № ХХХ–ХХ
Код наименование оборудования
Наименование детали сб. единицы или материала
5 Сверлильно-фрезерно-расточная с ЧПУ ИОТ № ХХХ–ХХ
Обрабатывающий центр Willemin macodel 508S
0 Промывка ИОТ № ХХХ–ХХ
5 Контрольная ИОТ № ХХХ–ХХ
0 Фрезерная с ЧПУ ИОТ № ХХХ–ХХ
Обрабатывающий центр Willemin macodel 408S2
0 Электроэрозионная с ЧПУ ИОТ № ХХХ–ХХ
Электроэрозионный с ЧПУ
5 Промывка ИОТ № ХХХ–ХХ
0 Контроль приемочный ИОТ № ХХХ–ХХ
Компоновка.dwg

Центральная заводская лаборатория
МГТУ им.Н.Э.Баумана Группа МТ3-102 Кафедра МТ3
Цеховое тех. бюро F=25м.кв.
Помещение для культурного обслуживания F=170 м.кв.
Женский гардероб и душевые
Мужской гардероб и душевые
Помещение для молодежного комитета и профсоюзов
Участок обработки деталей
из магниевых сплавов
МГТУ им. Н.Э.Баумана Кафедра МТ3 Группа МТ3-112
Грузопотоки заготовок
Проемы ворот и дверей
Наружные стены с остеклением
Цеховые проезды и проходы
Условные обозначения
приборов и устройств
и наладке электронных
Корпусная мастерская
Мастерская по ремонту
ЦЕХ 616 СТАНКОВ С ЧПУ И ОБРАБАТЫВАЮЩИХ ЦЕНТРОВ
настройке инструмента
Участок обрабатывающих центров
участка обрабатывающих
План на отм. 0.000 М 1:100
механической обработки
мелких и средних деталей
Комплектная трансформаторная подстанция
Участок механической обработки крупных деталей
Участок механической обработки мелких и средних деталей
Участок обработки деталей из магниевых сплавов
Участок механической обработки крупных деталей №1
участка механической
Участок механической обработки крупных деталей №2
Участок обработки корпусных деталей
Участок обработки тел вращения
Компрессорная подстанция
Помещение для хранения
План на отм. 0.000 1:200
С и т у а ц и о н н ы й п л а н
Зона расширения корпуса
МГТУ им. Н.Э.Баумана Кафедра МТ3 Группа МТ3-102
Компресорная подстанция
План на отм. 0.000 М 1:200
Зам. по произв. части
Хозяйственная служба
Инструментальная служба
Организационная структура управления цехом
Технологическая схема производства
Потребитель электроэнергии
Потребитель эмульсии
давления (до 7кгскв.см).
Потребитель сжатого воздуха низкого
План на отм. 0.000 1:100
необходимое в производстве
МГТУ им.Н.Э.Баумана Группа МТ3-112 Кафедра МТ3
бухгалтерская служба
Технологическая служба
Цех вакуумного литья
Кузнечно-пресовый цех
Цех листовой штамповки и сварки
Инструментальный цех
Склад инструмента и приспособлений
коллекторов и мелких деталей
Механосборочный цех компрессора
Механосборочный цех турбин
Механосборочный цех шестерен
Механосборочный цех коробок
агрегатов и средних деталей
Цех станков с ЧПУ и обрабатывающих центров
Цех термообработки и нанесения покрытий
Испытательная станция двигателя
Сборочно-переборочный цех ЦСГД и экспедиции
Склад готовой продукции
Кузнечно-прессовый цех
инструментально-раздаточная кладовая
Мастерская по настройке инструмента и
План на отм. 4800 1:200
низкого давления (до 7кгскв.см).
Потребитель сжатого воздуха
Розетка штепсельная 220В
Планировка оборудования 2 -х производственных участков цеха и вспомогательных отделений
Помещение общественного питания F=170 м.кв.
Помещение для буфетов
Кабинет начальника цеха F=25м.кв.
Кабинет зам начальников цеха F=30м.кв.
Охрана труда F=25м.кв.
Бюро труда и заработной платы F=50м.кв.
Отдел технического контроля F=25м.кв.
Экономический и бух. отдел F=30м.кв.
Помещение для медецинского обслуживания F=34 м.кв.
Трансформаторная подстанция
ремонта приспособлений
Технологическая схема
Сборочно-переборочный цех и экспедиции
Рекомендуемые чертежи
- 24.01.2023
- 24.01.2023
- 24.01.2023
- 25.05.2024
- 24.01.2023
- 20.12.2021
- 23.10.2015
Свободное скачивание на сегодня
Другие проекты
- 25.10.2022