Проект комплексной механизации работ по межоперационному транспортированию и установке на металлорежущие станки заготовок массой до 10 тонн




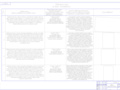
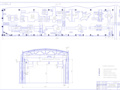
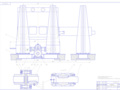
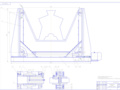
- Добавлен: 25.10.2022
- Размер: 4 MB
- Закачек: 0
Описание
Состав проекта
![]() |
![]() ![]() ![]() ![]() |
![]() ![]() |
![]() ![]() |
![]() ![]() ![]() ![]() |
![]() ![]() ![]() ![]() |
![]() ![]() ![]() ![]() |
![]() ![]() |
![]() ![]() ![]() ![]() |
![]() ![]() ![]() ![]() |
![]() ![]() |
![]() |
![]() ![]() ![]() ![]() |
![]() ![]() |
![]() ![]() ![]() ![]() |
![]() ![]() |
![]() ![]() |
![]() |
![]() ![]() ![]() ![]() |
![]() ![]() |
![]() ![]() ![]() ![]() |
![]() ![]() |
![]() |
![]() ![]() ![]() ![]() |
![]() ![]() |
![]() |
![]() ![]() |
![]() |
![]() ![]() |
![]() ![]() |
![]() ![]() |
![]() |
![]() ![]() |
![]() ![]() ![]() ![]() |
![]() ![]() ![]() ![]() |
![]() ![]() ![]() ![]() |
![]() ![]() ![]() |
![]() ![]() |
![]() ![]() ![]() ![]() |
![]() ![]() |
![]() |
![]() ![]() ![]() ![]() |
![]() ![]() ![]() ![]() |
![]() ![]() ![]() |
![]() ![]() |
![]() ![]() ![]() ![]() |
![]() ![]() |
![]() |
![]() ![]() |
![]() ![]() ![]() ![]() |
![]() ![]() ![]() ![]() |
Дополнительная информация
01 План цеха.dwg

- Канализационный колодец
- Вытяжная вентиляция
- Подвод сжатого воздуха
Условные обозначения:
- Зона перемещения груза
Мостовой кран электрический L= 22
03 Патентный поиск.dwg

его составные части)
охранного документа.
Классификационный индекс. Дата
Сущность заявленного технического
решения и цели его создания (по описанию
изобретения или опубликованной заявке)
Изобретение относится к сварке
в частности к устройствам для кантования изделий при
сварке. Кантователь содержит барабаны 2 и 3 с грузонесущим гибким полотном 5
в виде отдельных тросовых элементов 6
соединенных в кольцевые элементы путем заплетки
петли одного конца троса в петлю другого. Гибкое полотно расположено на барабанах 2 и 3
которые установлены на ступицах барабанов 2 и 3 с возможностью
свободного поворота относительно нее при вращении изделия.
Дата приоритета: 1993.12.27
Дата публикации: 1997.02.27
Заявитель и патентообладатель:
Волжское производственное объединение
цементного машиностроения "Волгоцеммаш
С целью упрощение конструкции
устранение повреждений
наружной поверхности изделия и повышение надежности работы
содержащий смонтированные на основании
поворотные барабаны с ребордами и охватывающее ступицы
барабанов грузонесущее гибкое полотно
состоящее из отдельных
концы которых соединены между собой
что реборды барабана выполнены выступающими
относительно ступицы на величину
грузонесущего полотна
и установлены на ступице с возможностью
свободного поворота относительно нее
на каждом конце тросового
элемента выполнена петля
а соединение концов тросовых
элементов выполнено путем заплетки петли одного
конца в петлю другого.
Изобретение относится к подъемно-транспортному оборудованию и может быть использовано
для кантования крупногабаритных изделий
особенно в затесненных условиях
Кантователь включает приемное и поворотное устройства
при этом последнее снабжено
силовым приводом. Приемное устройство кантователя имеет корытообразную форму каркаса с
приемной горизонтальной площадкой
по которой проложен транспортировочный путь в виде
центральной направляющей с продольным ограничительным пазом и уложенными: в него двумя
роликовыми дорожками
а также отводящий наклонный участок в направлении
корытообразног каркаса.
Дата приоритета: 1996.04.03
Дата публикации: 1998.03.27
Центральный научно-исследовательский
Использование кантователя позволяет получить надежное
простое по конструкции устройство
экономить производственные площади. Возможность
осуществления кантовки с предварительным вертикальным
загруженние изделия значительно расширяет возможности
использования кантователя. Для решения поставленной цели
предложен кантователь
включающий приемное и поворотное
при этом последнее снабжено силовым приводом.
Приемное устройство кантователя имеет корытообразную форму
каркаса с приемной горизонтальной площадкой
проложен транспортировочный путь в виде центральной
направляющей с продольным ограничительным пазом и уложенными
в него двумя роликовыми дорожками
а также отводящий наклонный
участок в направлении корытообразного каркаса.
Изобретение относится к области машиностроения
в частности к кольцевым кантователям для
технологических работ. Кантователь выполнен в виде двух колес плоского типа
которых крепится изделие
подлежащее окраске. Колесо выполнено в виде гнутого профиля
подкрепленного четырьмя ребрами сегментного типа
собой по углам. В прямоугольно-квадратных проемах колеса крепится изделие так
центр тяжести совпадал с осью колеса. Для установки изделия в заданное положение на
противоположных ребрах сегментного типа закреплены подвижные устройства
изделии через кнехты для его транспортировки.
Дата приоритета: 2001.05.10
Дата публикации: 2001.05.10
Концерн "Крюковский вагонзавод" (UA)
на решение которой направлено заявляемое техническое
чтобы разработать кантователь
обеспечивающий свободный доступ к окрашиваемым поверхностям
изделий непосредственно в камерах мойки и окраски
без кранов и поворотных устройств мог бы сам вращать изделие
и передавать его по потоку в камеры мойки
одновременно применяя поточную линию окраски изделий.
Кантователь характеризуется тем
что он содержит два колеса
обод каждого из которых выполнен из силового гнутого профиля
типа толстостенной трубы. Каждое колесо подкреплено изнутри
четырьмя ребрами жесткости сегментного типа
по осям колеса отверстиями для установки продольных
стягивающих устройств трубчатого типа.
Изобретение относится к подъемно-транспортному оборудованию
а именно к технологической
оснастке для захвата и транспортировки преимущественно валов большого диаметра.
Захват-кантователь содержит траверсу
навешиваемую на крюк грузоподъемного механизма
зажимные губки. Зажимные губки шарнирно соединены и подвешены на цепях
отверстия в траверсе
а механизм фиксации выполнен в виде крестообразного крюка
закрепленного на траверсе
прикрепленных к этим цепям и зацепляемых за
крестообразный крюк с возможностью расцепления с крюком в момент установки траверсы на
захватываемый вал. Технический результат заключается в осуществлении захвата валов разных
диаметров без регулирования захвата и в уменьшении габарита захвата
в радиальном направлении валов.
RU Патент 2148550 (13) C1
Дата приоритета: 1998.08.31
Дата публикации: 2000.05.10
Закопайло Дмитрий Валентинович
Задачей изобретения является: осуществление захвата нагретых
валов разного диаметра без соответствующего регулирования
захватного приспособления
что позволяет одновременно
термообрабатывать валы разных диаметров; уменьшение габарита
захвата-кантователя в радиальном направлении валов
позволяет увеличить количество валов
укладываемых на подину печи. Указанная задача достигается тем
что захватные органы
представляющие собой зажимные губки
шарнирно соединенные между собой
пропущенных через отверстия в траверсе
рабочую поверхность специальной криволинейной формы
механизм фиксации выполнен в виде крестообразного крюка
прикрепленных к этим цепям
и зацепляемых за крестообразный крюк.
Теоретический чертеж
Спецификация Электротележхка 1.dwg

Подкладка под редуктор
Подкладка под тормоз
Крышка люка аккумулятора
Спецификация Опорная стойка.dwg

07 Опорная стойка1.dwg

Непараллельность осей отв.
А относительно поверхности Б
Острые кромки не допускаются.
02 Схемы стровок1.dwg

Приспособление СН 16-47 ГОСТ 2319-70
Прилив на торце блока
Схема строповки турбокомпрессора
Приспособление Т 9694-021
Схема зачаливания блока
цилиндров дизельгенератора
Теоретический чертеж
Схема строповки рамы дизелй
04 Кран мостовой.dwg

Грузоподъемность: 10т
подъема главного крюка 10 ммин
передвижения тележки 35.4 ммин
передвижения крана 50 ммин
Технические требования
Размеры без допускаемых отклонений для справок
Кран по рельсам должен перемещаться свободно.
После сборки кран должен быть испытан в соответствии с
правилами Госгортехнадзора.
Спецификация Кран мостовой электрический.dwg

09 Тех.dwg

Шпоночно-фрезерный станок 692М
Операция 010. Токарная копировальная
Операция 015. Шпоночно-фрезерная
06 Кантователь цепной 21.dwg

Длина каждой цепи 10
Все размеры без допусков выполнять по 7 квалитету точности.
06 Кантователь цепной 11.dwg

Длина каждой цепи 10
Все размеры без допусков выполнять по 7 квалитету точности.
Спецификация Ведомость проекта2.dwg

Спецификация Кантователь цепной2.dwg

05 Передаточная тележка.dwg

Грузоподъемность Q=10 т.
Скорость передвижения U=50 ммин.
Колея (рельс в свету) 1524 мм.
Пояснительная записка.doc
Ключевые слова: цепной кантователь привод червячный редуктор цепная передача патентный поиск технологический процесс режущий инструмент приспособление.
В данном дипломной работе разработан проект комплексной механизации работ по межоперационному транспортированию и установке на металлорежущие станки заготовок массой до 10тонн.
Целью дипломного проекта является снижение физических и энергозатрат при кантовании блока цилиндров дизельгенератора. Для поиска оптимального технического решения проведен анализ существующего рынка грузоподъемной техники и патентные исследования. По результатам просмотренного фонда спроектирован цепной кантователь который обеспечивает вращение заготовки вокруг горизонтальной оси массой до 5000 кг и габаритными размерами: длиной до 3000 мм шириной до 1500 мм. Натяжение цепи осуществляется под действием массы вращающегося груза. При включении электродвигателя через червячный редуктор приводится во вращение две цепные передачи установленные на двух парах опорных стоек. Цепные передачи приводят во вращение заготовку установленную на них.
Эффективность разработанного цепного кантователя подтверждена расчетами приведенными в пояснительной записке к дипломному проекту.
РАЗРАБОТКА ПРОЕКТА МЕХАНИЗАЦИИ РАБОТ ПО МЕЖОПЕРАЦИОННОМУ ТРАНСПОРТИРОВАНИЮ ИЗДЕЛИЙ НА УЧАСТКЕ ОБРАБОТКИ БЛОКА ЦИЛИНДРОВ 9
1.Анализ грузопотоков .. .. 9
1.1 Технология обработки блока цилиндров 9
1.2 Определение типа производства 12
1.3 Выбор транспорта для перемещения груза по цеху 13
1.4 Определение количества средств механизации 14
2.Анализ конструкций кантователей . . 16
3.Патентные исследования . . .. .18
4.Цель и задачи проектирования 23
РАЗРАБОТКА КОНСТРУКЦИИ ОСНОВНЫХ УЗЛОВ
КАНТОВАТЕЛЯ БЛОКА ЦИЛИНДРОВ .. .. 24
1.Краткая характеристика механизма . 24
2.Расчет привода кантователя .. .. .26
2.1.Определение мощности на валу рабочей машины . .. .. ..26
2.2.Выбор электродвигателя и кинематический расчет привода 26
2.3.Определение силовых и кинематических параметров привода 28
2.4.Определение сил действующих в зацеплении
червячной передачи .. ..33
2.5.Проверка червяка на прочность и жесткость .. .34
2.6.Предварительный расчет валов .. 37
2.7.Эскизная компоновка и предварительные размеры . 40
2.8.Подбор подшипников .. 41
2.9.Подбор шпонок и проверочный расчет
шпоночного соединении . 43
2.10.Конструирование корпуса. Выбор арматуры.
Компоновка редуктора . . .46
2.11.Смазка зацепления и подшипников 48
2.12.Тепловой расчет редуктора .. ..48
3.Расчет цепной передачи . .50
4.Расчет металлоконструкции опорных стоек . 54
ПРОЕКТИРОВАНИЕ ТЕХНОЛОГИЧЕСКОГО ПРОЦЕССА ВОСТАНОВЛЕНИЯ ДЕТАЛИ – ШЛИЦЕВЫЙ ВАЛ .. .57
1.Анализ технологичности конструкции детали .. ..57
2.Разработка маршрутного и операционного технологического
процесса восстановления детали .. .58
3.Определение типа производства . 59
4.Определение структуры технологического процесса
и методов обработки .. . .. ..64
5.Выбор оборудования режущих инструментов
и средств измерения . ..65
6.Расчет припусков и межоперационных размеров . 66
7.Расчёт режимов резания .. 70
8.Расчет технических норм времени .. ..77
ТЕХНИКО-ЭКОНОМИЧЕСКОЕ ОБОСНОВАНИЕ ПРОЕКТА 81
1.Расчет численности всех категорий рабочих 82
2.Расчет фонда заработной платы . ..84
3.Расчет себестоимости изделия . 85
4.Расчет затрат на энергоносители .. ..87
ОБЕСПЕЧЕНИЕ БЕЗОПАСНОСТИ ЖИЗНЕДЕЯТЕЛЬНОСТИ .. 92
1.Указание мер безопасности при обслуживании машины 92
2.Безопасность при механизированной транспортировке грузов 92
3.Техника безопасности при использовании
грузоподъемных механизмов . .93
4.Меры защиты от опасного поражения электрическим током 99
5.6. Расчет сопротивления заземляющего устройства ..104
СПИСОК ИСПОЛЬЗУЕМЫХ ИСТОЧНИКОВ . .. .107
ПРИЛОЖЕНИЕ А. Технологическая документация . 108
ПРИЛОЖЕНИЕ Б. Спецификации . .115
ПРИЛОЖЕНИЕ В. Ведомость дипломного проекта . 123
Ликвидация ручных погрузочно-разгрузочных работ исключение тяжелого ручного труда при выполнении основных и вспомогательных производственных операций комплексная механизация и автоматизация производственных процессов во всех областях народного хозяйства немыслимы без использования широкого комплекса подъемно – транспортных машин.
Грузоподъемные машины служат для погрузочно-разгрузочных работ перемещения грузов в технологической цепи производства.
В процессе обработки ремонта или сборки крупногабаритных изделий возникает необходимость обеспечить поворот заготовки вокруг горизонтальной оси.
На предприятии вращение крупногабаритных заготовок (рама дизеля блок цилиндров) вокруг горизонтальной оси для нужной фиксации на станках осуществляется при помощи мостового крана путем перестроповки изделий вручную стропальщиками. В следствии этого увеличивается время межоперационных простоев также заготовка имеет массу более 4 тонн и большие габариты и применение ручного труда требует большого физического усилия от работников. Но самым важным отрицательным фактором является вероятность травматизма и гибели стропальщиков в результате различных несчастных случаев: обрыва чалок поломки ответственных механизмов.
Для устранения данного недостатка необходимо разработать конструкцию специального кантователя.
Целью дипломного проекта комплексная механизация работ по межоперационному транспортированию и установке на металлорежущие станки заготовок массой до 10тонн.
РАЗРАБОТКА ПРОЕКТА МЕХАНИЗАЦИИ РАБОТ ПО МЕЖОПЕРАЦИОННОМУ ТРАНСПОРТИРОВАНИЮ ИЗДЕЛИЙ НА УЧАСТКЕ ОБРАБОТКИ БЛОКА ЦИЛИНДРОВ
1 Анализ грузопотоков
- Заданный годовой грузооборот: 1000 тонн
- Перевозимый груз: блок цилиндров
- Схема необходимого цикла переработки груза:
1.1 Технология обработки блока цилиндров
5 Транспортировочная – Передаточная тележка Q=10т. Транспортирование блока цилиндров из цеха №1 в цех №2.
0 Разметочная – Плита разметочная Т9570 – 015.Эл. мостовой кран Р=10 т.
5 Продольно фрезерная –Продольно фрезерный полуавтомат 6662. Фрезеровать верхнюю плоскость.
0 Кантование заготовки на 180° - эл. мостовой кран Q=10 т.
5 Продольно фрезерная –Продольно фрезерный полуавтомат 6662. Фрезеровать нижнию плоскость.
0 Разметочная – Плита разметочная Т9570 – 015. Эл. мостовой кран Р=10 т.
Разметить отверстия под втулки.
5 Горизонтально – расточная – Горизонтально-расточной станок ИР 302 – Ф1. Расточить ответстия под втулки предварительно.
0 Горизонтально – расточная – Специальный горизонтально-расточной станок ЛР – 88. Расточить ответстия под втулки.
5 Горизонтально – расточная – Специальный горизонтально-расточной станок ЛР – 74. Расточить ответстия под втулки распредвала.
5 Горизонтально – расточная – Специальный горизонтально-расточной станок ЛР – 74. Расточить ответстия под втулки.
0 Горизонтально – расточная – Горизонтально-расточной станок HVF 125D. Фрезеровать торцы блока.
5 Слесарная – Стенд слесарный цеховой.
0 Слесарная – Стенд слесарный цеховой. Нанести сетку для межоперационного контроля.
5 Контрольная – Подставка деревянная цеховая. Произвести межоперационный контроль блока.
0 Транспортировочная – Эл. мостовой кран Р=10.
0 Вибрационное старение.
5 Очистка блока от окалины и ржавчины – Дробеструйная камера.
0 Опресовочная – Стенд гидроопресовочный НО 321сб.
0 Контрольная – Подставка деревянная цеховая.
5 Транспортировочная – Эл. мостовой кран Р=10.
0 Окрасочная – Камера окраски.
5 Разметочная – Плита разметочная Т 9570 – 015. Разметить под окончательную обработку наружных поверхностей блока проверить расположение отверстий под втулки цилиндров.
0 Продольно строгальная – Продольно строгальный станок ЭА 256. Строгать верхнюю и нижнюю плоскости.
5 Кантование заготовки на 180° - эл. мостовой кран Q=10 т.
0 Разметочная – Плита разметочная Т9570-015. Разметить отверстия под втулки цилиндров под расточку.
5 Горизонтально – расточная – Горизонтально-расточной станок ИР 302 – ЗФ1. Расточить ответстия под втулки окончательно.
5 Горизонтально – расточная – Специальный горизонтально-расточной станок ЛР – 218. Расточить ответстия под втулки.
0 Горизонтально – расточная – Специальный горизонтально-расточной станок ЛР – 74. Расточить ответстия под втулки распредвала.
5 Радиально – сверлильная – Радиально – сверлильный станок RF – 5. Сверлить и нарезать резьбу верхней плоскости.
5 Радиально – сверлильная – Радиально – сверлильный станок RF – 5. Сверлить и нарезать резьбу нижней плоскости.
0 Радиально – сверлильная – Радиально – сверлильный станок RF – 5. Сверлить 8 отв. Со сторона распредвала.
5 Радиально – сверлильная – Радиально – сверлильный станок RF – 5. Сверлить 8 отв. Со стороны выхлопа.
5 Горизонтально – расточная – Горизонтально-расточной станок HVF 125D. Фрезеровать поверхности впадин в нижней плоскости блока.
0 Горизонтально – расточная – Горизонтально-расточной станок HVF 125D. Фрезеровать торцы блока сверлить и нарезать резьбу 8 отв. в торце блока предварительно.
5 Горизонтально – расточная – Горизонтально-расточной станок HVF 125D. Фрезеровать торцы блока сверлить и нарезать резьбу 8 отв. в торце блока окончательно.
5 Слесарная – Стенд слесарный цеховой. Нанести сетку для межоперационного контроля.
0 Слесарная – Стенд слесарный цеховой. Нарезать резьбу малого диаметра – 8 отв. со стороны выхлопа и торцах блока.
5 Контрольная – Подставка деревянная цеховая. Проверить блок на наличие дефектов литья.
0 Радиально- сверлильная – радиально-сверлильный станок RF-S. Сверлить отверстия и подрезать торцы.
0 Горизонтально – расточная – Горизонтально-расточной станок HVF 125D. Сверлить отверстия под резьбу.
5 Слесарная – Стенд слесарный цеховой. Нарезать резьбу малого диаметра со стороны воздушного пуска.
0 Контрольная – Подставка деревянная цеховая. Произвести окончательный контроль блока цилиндров.
Из 270 технологических операций 40% являются грузоподъемными. Для повышения производительности и безопасности труда необходима механизация подъемно-транспортных работ в цехе.
1.2 Определение типа производства
При проектировании участка производства исходными данными является информация о выпускаемой продукции тип производства. На участке в рассматриваемом случае производится корпусная деталь. В большинстве случаев в условиях рыночной экономики предприятию приходится менять номенклатуру производимой продукции поэтому на участке цеха размещено различное оборудование предназначенное для обработки корпусных деталей.
Определяем тип производства по приближённой таблице относительно корпусной детали для чего необходимо знать её массу и годовую программу выпуска.
Масса детали =4700 кг
Годовая программа выпуска :
По приближённой таблице находим что тип производства - мелкосерийный.
Выбор складской тары
В качестве складской тары можно использовать специальные настилы или поддоны. Применение настилов позволяет проектировать склады со значительно меньшей площадью на производстве. К тому же для поддонов легче применить стандартные промышленные захваты и транспортные средства (краны различных конструкций погрузчики и др.).
Т.о. в качестве тары для транспортирования и хранения заготовок и деталей выбираем настил.
Определим количество внутрицеховых погрузочно-разгрузочных операций с отдельной деталью w:
Исходя из технологии обработки блока цилиндров примем количество погрузочно-разгрузочных операций равное w=54.
1.3 Выбор транспорта для перемещения груза по цеху
В процессе выполнения предприятием своей задачи по изготовлению продукции непрерывно работают различные виды транспорта: межцеховой внутрицеховой. Внутрицеховой транспорт представлен множеством специальных напольных машин и подъёмников либо грузовыми автомобилями.
В качестве межцехового транспорта выгоднее всего было применить передаточную тележку грузоподъемностью 10 т.
Для обеспечения механизации в качестве внутрицехового транспорта был выбран кран мостовой однобалочный грузоподъёмностью 10 т и средней скоростью передвижения V=10 ммин.
Порядок работы транспорта
Для правильного определения порядка работы транспорта следует добавить что мостовой кран под своей зоной действия накрывает ряды станков. Каждый станок обслуживается консольным краном на колонне. Около каждого станка есть участок на который устанавливается тара с заготовкой.
В результате порядок работы транспорта получается следующий:
Передаточная тележка привозит заготовку и укладывает её на натил;
Мостовой кран перемещает заготовку конкретному станку на обработку.
Мостовой кран перемещает заготовку от одного станка к другому (от одной операции к другой). После последней операции он перемещает тару на передаточную тележку.
Передаточная тележка перемещает заготовку на другие участки.
1.4 Определение количества средств механизации
Определяем годовое количество операционных переходов:
Nг= (10000005200)54=10368
Определяем по план – схеме среднюю длину пути крана L:
=14 - кол- во станков.
Определяем среднее время на одну крановою операцию t :
Определяем годовое время работы крана Т
где tс и tр=53 мин – время страповки и растроповки блока цилиндров.
Т=(0643+53+53)10368=116567 мин
Определим годовой ресурс работы крана при 250 рабочих днях в году односменной работе и 96% времени работы без ремонта:
Тр=250860096=115200 мин
Коэффициент использования крана по времени определяется из условия ≤1:
Коэффициент не соответствует рекомендованным значениям.
При анализе технологии обработки блока цилиндров выявлены недостатки – при кантовании заготовки вокруг горизонтальной оси используется мостовой кран грузоподъемностью 10 тонн вследствие этого увеличивается время межоперационных простоев возрастает нагрузка на кран также заготовка имеет массу более 4 тонн и большие габариты и применение ручного труда требует большого физического усилия от работников. Но самым важным отрицательным фактором является вероятность травматизма и гибели стропальщиков в результате различных несчастных случаев: обрыва чалок поломки ответственных механизмов.
На основе проведённого выше анализа и расчёта делаем вывод что установленный внутрицеховой транспорт в цехе обработки блока цилиндров не обеспечивает заданного грузооборота. Данный цех нуждается в проведении комплексной механизации работ по кантованию заготовок. Для чего необходимо разработать конструкцию кантователя заготовок рамы и блока цилиндров.
2Анализ конструкций кантователей.
Анализ технической и патентной документации показал что существует несколько разновидностей кантователей для вращения изделий вокруг горизонтальной оси различной формы и массой.
Кантователь двухстоечный КД-05.
Рисунок 1.1 - Кантователь двухстоечный КД-05.
Кантователь предназначен для поворота балочных рамных и решетчатых конструкций при сборке и сварке. Кантователь состоит из передней приводной стойки 1 устанавливаемой на фундамент задней неприводной передвижной стойки 4 и рельсового пути 6. Передняя стойка имеет механизм вращения шпинделя 2 состоящий из асинхронного электродвигателя червячного редуктора и зубчатой передачи. Задняя стойка в зависимости от длины свариваемого изделия перемещается по рельсовому пути и закрепляется в нужном положении захватами 5. Она снабжена выдвижной пинолью 3. На шпинделе 2 и пиноли 3 устанавливаются приспособления для закрепления свариваемых изделий.
Кантователь с гидравлическими домкратами КГ 300.
Рисунок 1.2 - Кантователь с гидравлическими домкратами КГ 300.
Кантователь предназначен для поворота изделия при сварке. Состоит из поворотной рамы-кондуктора 1 основания 2 гидропривода 4 и пульта управления 3. Поворот рамы осуществляется двумя шарнирно закрепленными домкратами. Оси поворота рамы выдвижные и приводятся в движение четырьмя гидравлическими цилиндрами. Кантователь может быть снабжен передвижными тележками для сварщиков.
Кантователь цепной КЦ 10А.
Рисунок 1.3 - Кантователь цепной КЦ 10А.
Предназначен для установки заготовки в положение удобное для выполнения сварочных и других работ требующих её поворота вокруг горизонтальной оси. Механизм состоит из рамы опорных стоек электропривода цепной передачи.
В заключении можно сделать вывод что наиболее приемлемым (по простоте конструкции и др.) для объекта разработки является цепной контователь КЦ 10А который взят за прототип.
3 Патентные исследования.
Задачи патентных исследований: исследование технического уровня и тенденций развития кантователей крупногабаритных изделий.
Таблица 1.1 – Патентные исследования.
(объект исследования его составные части)
Страна выдачи вид номер охранного документа.
Классификационный индекс*
страна. Номер заявки
дата приоритета публикации*
Контаватель крупногабаритных изделий
Россия №9610649603 приоритет 1996.04.03 1998.03.27
Кантователь крупногабаритных изделий
Открытое акционерное московское общество "Завод им. И.А. Лихачева
Россия №200111135302 приоритет 2003.02.10
Сборочно-сварочный вращатель-контаватель
Открытое акционерное общество "Новосибирский завод химконцентратов
Россия №200111864428 приоритет 2001.07.05
Мармышев Валентин Николаевич
Россия №200110181828 приоритет 2001.01.19 2002.09.20
Закопайло Дмитрий Валентинович
Россия №9811653628 приоритет 1998.08.31 2000.05.10
Акционерное общество "АВТОВАЗ
Россия №9711284403 приоритет 1997.07.15 1999.05.27
Россия №9811380328 приоритет 1998.07.29 1999.04.20
Волжское производственное объединение цементного машиностроения "Волгоцеммаш
Россия №9305763708 приоритет 1993.12.27 1997.02.27
Воронежское авиационное производственное объединение
Россия №9304674611 приоритет 1993.10.08 1996.12.10
Россия патент RU 2281844 C2 6 B23K37047
Концерн "Крюковский вагонзавод"
Украина №200413702302 приоритет 2004.12.17 2006. 08.20.
Кантователь для сборки и сварки изделий
Анализ и исследование кантователей крупногабаритных изделий.
Область поиска: кантователи для вращения крупногабаритных изделий.
Цель поиска: выявление патентной и научно-технической информации позволяющей исследовать технический уровень и тенденции развития кантователей крупногабаритных изделий и обосновать выбор направлений выполнения дипломного проекта.
В результате просмотра фонда зарегистрированных и опубликованных охранных документов по состоянию выявлены источники информации относящиеся к области поиска.
Классы (рубрики) МПК: B05C 1302; B66C 144; B65G 700 708 4700 47252; B23K 3704 37047; B60S 500; F16M 1112.
Глубина поиска: патентная документация опубликованная с 1994 г. по настоящее время.
Перечень документов отобранных для анализа и приложены к настоящему дипломному проекту представлен в таблице 1.1 и на плакате формата А1. Аналоги представлены в виде рефератов описаний или выборочных частей описаний в объеме достаточном для понимания их сущности.
В основном технические решения отражают четыре направления совершенствования кантователей крупногабаритных изделий:
Схемные решения отражающие повышение надежности кантователей:
- с целью повышения надежности работы кантователя реборды барабана выполнены выступающими относительно ступицы на величину превышающую толщину грузонесущего полотна и установлены на ступице с возможностью свободного поворота относительно нее (№2074079);
- повышение надежности и производительности кантователя за счет изменения подъема и поворота траверс (№2281844).
- с целью повышения надежности работы кантователя рабочая площадка выполнена в виде нескольких уголков установленных на жестко связанных между собой взаимно-перпендикулярных прямоугольных направляющих смонтированных на кронштейне (2206816)
Схемные решения отражающие снижение энергоемкости при производстве деталей:
- с целью обеспечение возможности кантования крупногабаритных изделий различной формы в фазе подъема нагрузка от веса груза распределяется на крюк крана и низкую стойку опор с постепенным переходом на высокую стойку опор (№2070150);
- с целью повышения удобства при манипулировании с объектом и снижения энергоемкости в кантователе содержащем установленную на направляющих стойках раму с элементами фиксации кантуемого объекта и гибкий элемент связывающий раму с приводом тянущего устройства механизм возврата рамы в исходное положение (№2129087).
- с целью снижения энергоемкости и возможности расширения номенклатуры деталей предлагается поворотный механизм в виде T-образной кулисы которая посредством оси монтируется к кронштейну установленному на подающей линейке и снабжена роликами (2130889).
Схемные решения отражающие повышение производительности кантователей:
- с целью повышении производительности сборочно-сварочного вращателя-кантователя подшипники выполнены в виде втулок-ориентаторов с открытыми продольными пазами а также наличие штифтов которые введены в указанные втулки-ориентаторы перпендикулярно осям шпинделей с возможностью освобождения из открытых продольных пазов (№2210476);
- с целью возможности перемещения качением дискообразных деталей платформа кантователя снабжена ограничительными поворотными створками кинематически связанными между собой (№2189341).
Схемные решения отражающие снижение занимаемых площадей кантователем:
- с целью снижение занимаемых площадей приемное устройство кантователя имеет корытообразную форму каркаса с приемной горизонтальной площадкой по которой проложен транспортировочный путь в виде центральной направляющей с продольным ограничительным пазом и уложенными в него двумя роликовыми дорожками а также отводящий наклонный участок в направлении корытообразного каркаса (№2107651);
- с целью уменьшения габарита захвата в радиальном направлении валов захватные органы кантователя представляющие собой зажимные губки рабочую поверхность специальной криволинейной формы а механизм фиксации выполнен в виде крестообразного крюка закрепленного на траверсе и серег прикрепленных к этим цепям и зацепляемых за крестообразный крюк с возможностью расцепления с крюком в момент установки траверсы на захватываемый вал (№2148550).
В результате проведенных патентных исследований установлено что большинство технических решений направлено на:
Повышение надежности кантователей (№2206816) (2281844) (2074079);
Снижение энергоемкости при производстве деталей (№2130889)(2129067) (2070150);
Повышение производительности кантователей (№2210476) (2189341);
Снижение занимаемых площадей кантователем (№2107651) (2148550).
Анализ патентной информации показал что для заготовок формы близкой к паралепипиду и массой до 5т наиболее рациональным является конструкция кантователя в которой поворот заготовки производится на цепях подвешенными на стойках. Вращение цепей осуществляется от электропривода.
4Цель и задачи проектирования
На основании анализа существующих на рынке кантователей крупногабаритных изделий и патентного обзора поставлены следующие задачи проектирования:
разработать конструкцию цепного кантователя грузоподъемностью 5 т для вращения заготовок габаритами 40000х15000х10000 мм. и имеющих форму параллелепипеда;
предусмотреть средства механизации работы кантователя в качестве привода – электродвигатель;
разработать прогрессивный технологический процесс восстановления шлицевого вала грузоподъемной техники для повышения эффективности производства;
Все поставленные в комплексе задачи проектирования сводятся к единой цели: быстро и качественно с наименьшими затратами обеспечить изготовление данного изделия.
РАЗРАБОТКА КОНСТРУКЦИИ ОСНОВНЫХ УЗЛОВ
КАНТОВАТЕЛЯ БЛОКА ЦИЛИНДРОВ
1Краткая характеристика разрабатываемого механизма.
Цепной кантователь предназначен для установки блока цилиндров дизельгенератора в положение удобное для выполнения работ требующих её поворота вокруг горизонтальной оси.
Блок цилиндров представляет собой деталь массой 47 т габаритные размеры 36000х6000х8000 мм.
Рисунок 2.1 – Кантователь цепной.
Устройство и принцип работы
Кантователь (рис. 2.1) состоит из шести опорных стоек электропривода трех цепных передач.
Цепной кантователь обеспечивает вращение заготовки вокруг горизонтальной оси массой до 5000 кг и габаритными размерами: 40000х15000х10000 мм. Установка заготовки на кантователь осуществляется мостовым краном сверху. Натяжение цепи осуществляется под действием массы вращающегося груза. При включении электродвигателя через червячный редуктор приводится во вращение две цепные передачи установленные на двух парах опорных стоек. Цепные передачи приводят во вращение заготовку установленную на них.
2 Расчет привода кантователя
2.1Определение мощности на валу рабочей машины.
Необходимая мощность на валу кантователя для вращения блока цилиндров массой m=4700кг определяется:
где F – сила необходимая для вращения заготовки;
– скорость вращения оптимальное значение для данного типа оборудования равно 01 02 мс.
где - ускорение свободного падения равное 98 Нкг
2.2Выбор электродвигателя и кинематический расчет привода
Рисунок 2.2 – Кинематическая схема привода кантователя
– электродвигатель 2 – упругая муфта 3– червячный редуктор
Нагрузка постоянная нереверсивная технический ресурс передачи Lh =20000 ч.
Определим общий коэффициент полезного действия (КПД) привода:
обш= ч * п * м* ц где
ч = 083 – КПД червячной передачи (среднее значение) [1 табл 1.1]
п = 099 – КПД подшипников качения ( 2 пары) [1 табл 1.1]
м = 099 – КПД муфты [2 с.346 ]
ц = 098 – КПД цепной передачи. [1 табл 1.1]
= 083 * 0992 * 099 * 098 = 079
Определим требуемую мощность двигателя:
Рдв = 14 078 = 1774кВт.=1774кВт.
Выбираем тип двигателя [5 табл. 22.4 стр.38] с учетом Р ном ³ Рдв Рном = 22 кВт.
Двигатель асинхронный короткозамкнутый трехфазный общепромышленного применения закрытый обдуваемый степень защиты IP54 типа 5A200L8 с частотой вращения 750 обмин
n ном. = 735 об мин. [2 с.113]
Определение передаточного числа привода и его ступеней.
Частота вращения выходного вала редуктора:
=013 мс (по условию) – частота вращения рабочего вала машины тогда
Общее передаточное число привода:
U = nном1nрм = 73530 =245
Примем Uч=20 тогда Uц=24520=1225.
По рекомендации 9 [2 c.201] принимаем число заходов червяка Z1=2
2.3 Определение силовых и кинематических параметров привода
Из имеющихся данных:
Ррм =14кВт; Рдв =1774кВт; 3=013 мс;
Находим вращающий момент Т по формулам:
T=P или Т2=Т1*U* [2 c.113]
Для 1-ого вала: T1= Рдв где Рдв – расчетная мощность двигателя Вт.
T1=180007693= 23398 Н*м
Для 2-ого вала: Т2=Т1*Uч* ред где ред - КПД редуктора
ред=083* 0992 =0813
Т2=23398*20*0813= 380452 Н*м
=1 Uч=76.9320= 38465 мc;
Для 3-ого вала (кантователя):
Т3=Т2* Uч* ц=380452*1225*09=419448 Н*м
=2 Uч =036551225=013 мc-соответствует заданному.
В результате предварительных расчетов получили:
T1= 23398(Н*м) 1=7693 мc;
Т2=380452(Н*м) 2=036 мc;
Т3=419448(Н*м) 3=013 мc.
Расчет червячной передачи.
Число зубьев червячного колеса Z2 = U*Z1 [4 ф.1.1 с.8]
Марка материала червячного колеса зависит от скорости скольжения.
В первом приближении оцениваем скорость скольжения:
По рекомендации [2] примем для червячного колеса алюминиевую бронзу БрАЖ9 – 4 (отливка в песок).
Для червяка принимаем сталь 45х закаленную до твердости Н=45HRCэ с последующим шлифованием рабочих поверхностей витков.
По таблице 8.6 [3] находим допускаемое контактное напряжение
[s н ]=140МПа и вычисляем предварительное межосевое расстояние приняв коэффициент нагрузки К=1 (нагрузка постоянная):
Определяем модуль зацепления:
m=2a(q*Z2) [№3 с.185]
где q – коэффициент диаметра червяка
q=404=10 – соответствует стандартному значению [3 таб.8.2]
m=2*3532(10+40)=1412 мм
По ГОСТу 2144-66 [1 с.83] ближайшее стандартное значение m=14
тогда уточненное межосевое расстояние:
a=05*m*(q+Z2) [№3 с.179]
а=05*14*(10+40)=350 мм
Т.к. рассчитываемый редуктор не предназначен для серийного производства и по рекомендации [1 с.88] оставляем окончательное межосевое расстояние = 350мм.
Определим делительный угол подъема линии витка:
Т.к. делительный диаметр червяка:
d1 =14*10=140 мм=014 м то скорость скольжения в зацеплении
- что близко к расчетному значению.
По рекомендации [6 стр.97] назначаем для передачи 8-ю степень точности.
Проверим КПД передачи приняв по табл.8.3 [3 с.181] приведенный угол трения для безоловянной бронзы:
что достаточно близко к предварительно принятому значению.
Проверим прочность зубьев колеса на изгиб.
Определяем эквивалентное число зубьев колеса:
По табл.8.4 [3 с.186] находим коэффициент формы зуба
По табл.8.7 [3 с.192] находим допускаемое напряжение изгиба при нереверсивном нагружении и базе испытаний
Определяем заданное число циклов нагружений [3 с.190] колеса при частоте вращения
Вычислим коэффициент долговечности
- условие выполняется.
Тогда допускаемое напряжение изгиба:
Проверим напряжение изгиба
Т.к. =772(МПа) =5122 МПа – прочность колеса обеспечена.
Определим другие основные размеры червяка и червячного колеса.
Рисунок 2.3 – Червяк.
Диаметр внешних витков: [3 с.178]
Диаметр впадин: [3 с.178]
Длина нарезанной части червяка (при числе заходов Z1=2):
Т.к. червяк шлифованный принимаем b1=1876+35=2226(мм.) [№3 с.178]
b) Червячное колесо:
Рисунок 2.4 – Червячное колесо.
Делительный диаметр [3 с.178]
Диаметр вершин зубьев в среднем сечении:
Диаметр впадин в среднем сечении:
Наибольший диаметр червячного колеса:
Окончательно проверим зубья колеса на контактную усталость по условию:
[3 с185] (т.е значение должно лежать в интервале 126 147 МПа)
Т.к. - прочность зубьев на контактную усталость обеспечена.
По рекомендации [1 с.251] выполним червячное колесо составным. Венец и центр литые: венец – бронза центр – чугун СЧ15-32.
Соединение венца с центром осуществляется отливкой венца в литейную форму в которой заранее установлен чугунный центр колеса.
2.4 Определение сил действующих в зацеплении
Fа – осевая сила Ft – окружная сила Fr – радиальная сила Т1 – вращающий момент на червяке Т2 – вращающий момент на червячном колесе.
Окружная сила на червяке (Ft1) численно равная осевой силе на червячном колесе (Fa2):
Осевая сила на червяке(Fa1) численно равная окружной силе на червячном колесе(Ft2):
Радиальная сила(Fr) раздвигающая червяк и червячное колесо:
[3 182] где a – угол профиля витка червяка в осевом сечении: [3 с.178]
Рисунок 2.5 – Расчетная Н.
схема червячной передачи.
2.5 Проверка червяка на прочность и жесткость.
При проверочном расчете тело червяка рассматривают как цилиндрический брус круглого сечения лежащий на двух опорах и работающий на изгиб и кручение:
Где: Fа – осевая сила Ft – окружная сила Fr – радиальная сила Т1 – вращающий момент – расстояние между опорами по рекомендации [3 с.187] принимаем = (08 10)d2 тогда =560мм.
Из эпюр изгибающих моментов видно что опасным будет сечение в середине пролета и что результирующий изгибающий момент в этом сечении равен:
Максимальные напряжения изгиба:
Максимальные напряжения кручения:
[3 с.186] Па =103 МПа.
[3 с186] где = 45 60 МПа – допускаемое напряжение изгиба для стального червяка [3 с.186]
Т.к. =45 60 МПа >=1068МПа – условие выполняется.
Максимальный изгиб (стрела прогиба): [3 с.187]
где - равнодействующая окружной и радиальной силы [3 с.187]
- осевой момент инерции червяка [3 с.187]
Е – модуль продольной упругости материала червяка для стали 45х закаленной до твердости Н=45HRCэ МПа [1 с.87].
Условие жесткости червяка:
Т.к. - условие выполняется.
2.6 Предварительный расчет валов.
По рекомендации [3 с.225] для компенсации напряжений изгиба и других неучтенных факторов принимаем для расчета значительно пониженные значения допустимых напряжений кручения. Т.о. диаметр вала определится из условия прочности:
[4 с.53 ф.3.22] где Т – крутящий момент на валу
- допускаемое напряжение на кручение.
По рекомендации [3 с.225] принимаем материал выходного вала редуктора сталь 45 тогда
Полученное значение округляем до ближайшего стандартного значения из ряда Rа40 [3 с.226] тогда
мм – диаметр вала в месте посадки подшипника
мм - диаметр вала в месте посадки шестерни
мм - диаметр вала в месте посадки звездочки.
Определим длину ступицы:
По рекомендации [4 с.53] предварительно принимаем длину выходного конца тихоходного вала
расстояние между точками приложения реакции подшипников тихоходного вала
Выполним упрощенный проверочный расчет(рекомендации [3 с.229]) по формулам:
Из предыдущих расчетов имеем:
Приняв по табл.12.1 [3 с.229] допускаемое напряжение МПа
Т.к. в вместе посадки шестерни на валу будет шпоночный паз то увеличив расчетный диаметр на 10% в результате получим dp=95 мм.
Сравнивая расчетный диаметр вала с принятым:
видим что сопротивление усталости вала обеспечено со значительным запасом.
б) Определим размеры быстроходного вала (червяка).
расстояние между центрами приложения реакции опор подшипников
Для увеличения прочности вала примем что червяк изготовлен как одно целое валом [3 с.232].
диаметр вала вместе посадки подшипников
По рекомендации [4 с.54] принимаем диаметр выходного вала червяка равным 08 12 диаметра вала электродвигателя [5 табл. 22.4 стр.38] т.е.
Длину выходного вала примем .
По табл. 9.2 [2 с.203] назначаем 8 – ю степень точности.
2.7 Эскизная компоновка и предварительные размеры.
После определения размеров основных деталей выполним эскизную компоновку редуктора. Червяк и червячное колесо располагаем симметрично относительно опор и определяем соответствующие длины.
Рисунок 2.6 – расчетная схема червячной передачи для определения
По рекомендации [1 с.380] :
) принимаем диаметр вала под уплотнения для подшипников:
быстроходного - ; тихоходного - ;
) зазор между колесом (и другими деталями) и корпусом:
[1 с.380] принимаем
) ширину подшипников предварительно принимаем равной их диаметру [1 с.380] т.е. и .
2.8 Подбор подшипников.
Для вала червячного колеса предварительно примем роликовый конический подшипник легкой серии 7219 ГОСТ333 – 71 с размерами:
; ; ; ; ; ; [4 табл.5.34] рабочая температура
Рисунок 2.7 – Расчетная схема подшипника.
По рекомендации 13.4 [3 с.246] проверку подшипников только по динамической грузоподъемности по условию где - требуемая величина грузоподъёмности; - динамическая грузоподъемность подшипника (из таблицы).
[3 с.246] где Р – эквивалентная динамическая нагрузка: [3 с.247].
Определим коэффициент [2 т.16.5].
При коэффициенте вращения V=1 [2 прим. к ф.16.29] получим
Из табл.16.5 [2 с.335] находим коэффициенты радиальной и осевой нагрузок: ;
По рекомендации к формуле 1629 [2 с.335]:
коэффициент безопасности (умеренные толчки);
температурный коэффициент (до ).
Т.к. - обеспечен значительный запас прочности подшипниковых узлов вала червячного колеса.
Для вала червяка предварительно примем роликовый конический подшипник легкой серии 7220 ГОСТ333 – 71 с размерами:
По рекомендации [3 с.246] проверку подшипников только по динамической грузоподъемности по условию где - требуемая величина грузоподъёмности; - динамическая грузоподъемность подшипника (из таблицы).
Т.к. - обеспечен значительный запас прочности подшипниковых узлов вала червяка.
2.9 Подбор шпонок и проверочный расчет
шпоночного соединения.
Для выходного конца быстроходного вала d1вых =70 мм передающего вращающий момент Т1=24698Н*м.
Рисунок 2.8 – Расчетная схема шпоночного соединения.
По табл. 4.1 [4 с.78] выбираем призматическую шпонку со скругленными концами (исполнение А):
b=20 мм – ширина шпонки
h=12 мм – высота шпонки
t1=75 мм – глубина паза на валу
t2=49 мм – глубина паза на муфте.
Радиус закругления пазов 03r05 мм (интерполяция)
Учитывая длину вала и предполагаемую длину ступицы муфты = 130 мм принимаем по СТ СЭВ 189 – 75 [4 с.78] длину шпонки мм.
Расчетная длина шпонки [3 с.55]
Принимая материал шпонки сталь 45 с пределом текучести [3 с.57] а допускаемый коэффициент запаса прочности [s]=23 (нагрузка постоянная нереверсивная) [3 с.56]
определим допускаемое напряжение [3 с.57]
Проверим соединение на смятие:
Т.к. [3 с.55] – прочность шпоночного соединения обеспечена.
Напряжение среза [3 с.55] где - площадь среза шпонки:
Т.к. [3 с.57] – прочность шпоночного соединения обеспечена.
Для вала под ступицу червячного колеса d2ш =100 мм передающего вращающий момент Т2=380452 Н*м мм.
b=28 мм; h=16 мм; t1=10 мм; t2=64 мм; 04r06 мм; мм;
Т.к. – условие выполняется.
Т.к. – прочность шпоночного соединения обеспечена.
Для выходного конца тихоходного вала d2ЗВ =90 мм передающего вращающий момент Т2=380452 Н*м.
Учитывая длину вала и предполагаемую длину ступицы ведущей звездочки = 130(мм): шпонка призматическая со скрученными концами исполнение А:
b=25(мм); h=14 мм; t1=9 мм; t2=54мм; 04r06мм; мм;
2.10 Конструирование корпуса. Выбор арматуры.
Компоновка редуктора.
Для удобства сборки редуктора корпус выполняем разъемным; плоскость разъема совмещена со средней плоскостью колеса. Корпус и крышка литые из серого чугуна СЧ 15-32. При несущих корпусе и крышке корпуса толщины их стенок одинаковые. Расчетная толщина стенки
Диаметр фундаментных болтов
Для уменьшения габаритов и веса редуктора крышку и корпус соединяем шпильками ввернутыми в корпус. Диаметры шпилек:
для соединения крышки с корпусом
Крышки подшипников при диаметрах гнезд 180 и 170 мм прикреплены каждая шестью болтами диаметром (мм)[4 с.167].
Для снятия крышки корпуса предусмотрен отжимной болт.
Болты шпильки и установочные штифты располагаем так чтобы между ними (или соответствующими отверстиями для них) и ближайшей свободной поверхностью или отверстием оставалось тело толщиной не менее
[1 с.384] где — диаметр соответствующей детали;
оси этих деталей должны располагаться на расстояниях [1 с.384] от ближайшего отверстия или поверхности. Кроме того должна быть обеспечена возможность поворота гаечного ключа.
В принятой схеме редуктора подшипники червячного колеса и червяка находятся в верхнем положении.
При такой конструкции редуктора подшипники смазываются консистентной смазкой через пресс-масленки а так же масляным туманом образующимся в процессе работы [6 с.348].
При небольших габаритах редуктора для контроля уровня масла применен жезловой маслоуказатель ввернутый в стенку корпуса.
Компоновку и недостающие размеры рассчитываем по рекомендациям [1 с.261].
Компоновка узла червячного колеса.
Определяем все конструктивные размеры зубчатого венца и ступицы колеса и наносим их на чертеж по рекомендации [1 с.261].
Вычерчиваем подшипники вала колеса.
Определяем размеры подшипниковых гнезд крышек подшипников уплотнений и наносим эти детали на чертеж.
Определяем толщину поясов высоту бабышек для шпилек и проводим наружный контур корпуса.
Форму и размеры основания корпуса определяем конструктивно в зависимости от положения редуктора и способа его крепления к фундаменту.
Компоновка узла червячного вала.
Размещаем подшипники в соответствии с выбранным расстоянием между ними.
Определяем размеры гнезд под подшипники крышек подшипников и уплотнений и все эти детали наносим на чертеж.
Обводим внутренний контур корпуса.
Проводим наружный контур корпуса на проекции.
2.11 Смазка зацепления и подшипников.
Зацепление смазывается окунанием червячного колеса в масляную ванну. Глубина окунания – 13 радиуса колеса [6 с.349]. При скорости скольжения мсек по табл. 11.10 [1 с.275] рекомендуемая вязкость масла сст (интерполяция).
По табл. 11.11 [1 с.275] выбираем масло автотракторное АК - 15
Смазка подшипников - консистентная и масляным туманом образующимся в процессе работы [6 с.348]. Для конических роликоподшипников при рабочей температуре 110° С по табл. 11.11[1 с.277] выбираем смазку ЦИАТИМ-201.
2.12 Тепловой расчет редуктора.
Получив предварительно размеры корпуса производим тепловой расчет редуктора. Для увеличения поверхности охлаждения корпус редуктора сделан ребристым. При данной конструкции корпуса обеспечивается достаточно хорошая циркуляция воздуха и можно принять коэффициент теплопередачи [1 с.386]. Площадь поверхности ребер Fр Общая площадь поверхности охлаждения редуктора F' = F + 05* Fр[1 с.387]. Площадь поверхности редуктора (без учета днища) F. Тогда F'=31+05*05=335 кв.м. При температуре окружающей среды температура масла:
3Расчет цепной передачи
T1=4194 Н*м - крутящий момент на валу ведущей звездочки;
n1= 45 мин-1 - частота вращения ведущей звездочки;
u = 1 - передаточное число цепной передачи. Привод работает в одну смену; ожидаемый наклон передачи к горизонту 0°.
Назначим однорядную роликовую цепь типа ПР [7].
Ближайшие значения шагов по ГОСТ 13568-75: P=508 мм; значение А=646 мм2 Р=635 мм; значение А = 1000мм2.
Назначение основных параметров:
а) число зубьев ведущей звездочки.
Найдем рекомендуемое число зубьев Z1 в зависимости от передаточного числа;
Найдем число зубьев Z1 из условия: делительный диаметр ведомой звездочки не должен превышать 460 мм: Z1=p*dg2 (u*P)
Цепь с шагом Р=508 мм
Для этой цепи можно назначить Z1=28 что согласуется с рекомендуемым значением.
Цепь с шагом P=635 мм
Полученное значение меньше рекомендуемого. Следовательно эту цепь применять нежелательно.
Далее расчет будем вести для цепи с шагом P=508 мм;
б) межосевое расстояние;
в) наклон передачи по условию - 0°;
г) примем что смазывание цепи нерегулярное. Цепь будут смазывать периодически при помощи кисти.
Определение давления в шарнире [7];
Где A - площадь проекции опорной поверхности шарнира однорядной цепи мм2 (см. табл. 1);
mp- коэффициент рядности mp=1 при однорядной цепи mp=17 при двухрядной цепи mp=25 при трёхрядной цепи;
[s] - допускаемое давление в шарнире цепи (см. табл. 2) [7];
Ft - окружная сипа передаваемая цепью Н приближенное значение ее определяют по формуле Ft=628*10^3*T1(z1*p)
Kэ - коэффициент учитывающий условия эксплуатации цепи
Kэ=Kд*Ka*Kн*Kрег*Kсм*Kреж
здесь Kд - коэффициент динамичности нагрузки Kд=1 при нагрузке без толчков и ударов (ленточные и цепные транспортеры вентиляторы); Kд=12 15 при нагрузке с ударами небольшой интенсивности (компрессоры автоматические печи металлорежущие станки) Kд=16 19 при нагрузке с сильными ударами (прессы дробилки прокатные станы вибраторы);
Ka - коэффициент межосевого расстояния;
Kн - коэффициент наклона линии центров Kн=1 при y=0 60°;
Kн=125 при y=60 90°;
Kрег - коэффициент регулировки натяжения цепи Kрег=1 если регулировка автоматическая Kрег=125 при передаче с нерегулируемым натяжением;
Kсм -коэффициент смазывания; Kсм = 08 если смазывание цепи обильное (масляная ванна) Kсм =1 при непрерывном смазывании цепи при помощи капельницы; Kсм = 15 при нерегулярном смазывании цепи;
Креж - коэффициент режима Креж=1 при работе привода в одну смену Креж=125 при работе привода в две смены Креж=145 работе привода в три смены.
Найдем значение коэффициента Кэ:
Кд=12 - нагрузка с небольшими ударами;
Ка =1 - оптимальное межосевое расстояние;
Кн=1 - наклон передачи 0°;
Крег=125 - передача с нерегулируемым натяжением цепи;
Ксм- смазывание цепи нерегулярное;
Креж=1 - работа в одну смену;
Окружная сила передаваемая цепью Ft=2*p*103*T1 Z1*P=46060 H
Давление в шарнире однорядной цепи
s=KЭ*Ft (A * mP)=3468 Нмм2 > [s]=325 Нмм2
Однорядная цепь не подходит.
Найдем давление в шарнире для двухрядной цепи при mP=1.7:
s=225*2770(1897*17)=204 Нмм2 [s]
Для дальнейших расчетов принимаем двухрядную цепь 2ПР-254-11340. Ее параметры: шаг Р=50.3 мм диаметр ролика d1=1588 мм расстояние между внутренними пластинами BВН=15688 мм ширина внутренней пластины h=2413 мм расстояние между рядами Ap=2929 мм наибольшая ширина звена b=68 мм.
Число зубьев ведомой звездочки
Z2=u*Z1=1*28=28 Принимаем Z1=28
Частота вращения ведомой звездочки n2=n1u=951=45 мин-1
Делительный диаметр ведущей звездочки (в мм)
Dзв=Psin(180Z1)=460 мм.
Потребное число звеньев цепи
Уточненное межосевое расстояние
Полученное значение a уменьшаем на D=(0002 0004)а’=207 414 мм. Окончательное значение межосевого расстояния: a= aI -D=1600 мм.
Нагрузка на валы звездочек:
Fb=Kb*Ft*2000*T1dg1=115*200*28020266=63178 H.
где KB =115 при угле наклона передачи к горизонту менее 60°.
4 Расчет металлоконструкции опорных стоек.
Расчет усилий в опорной стойке.
Для равномерного распределения нагрузок при вращении блока цилиндров оптимальное количество стоек принимаем равным 6.
где m – масса приходящаяся на одну сойку
g = 98 – ускорение свободного падения.
Рисунок 2.9 – Расчетная схема опорной стойки.
Усилие F можно разбить на горизонтальную () и вертикальную () составляющие:
где - угол между сгибающей ветви гибкого элемента и стойкой.
Рассчитываем надежную высоту опорной стойки:
Расчет сечения опорной стойки (рис. 2.9) производится исходя из условия прочности стойки на изгиб:
где G – напряжения возникающие в стойке;
[G] – допустимое напряжение в стойке.
где - предел текучести материала стойки;
=2 – коэффициент запаса прочности.
В качестве материала для металлоконструкции выбираем Сталь30 [7]. Предел текучести у данного материала равен =30 кгмм2=294 МПа.
где М – изгибающий момент;
W – момент сопротивления сечения изгибу.
При данном значении момента сопротивления сечения изгибу выбираем сечение опорной стойки – тонкостенный прямоугольник полый [7].
H=200мм B= 150мм = 10мм [7].
Момент сопротивления данного сечения равен:
ПРОЕКТИРОВАНИЕ ТЕХНОЛОГИЧЕСКОГО ПРОЦЕССА
ВОСТАНОВЛЕНИЯ ДЕТАЛИ – ВАЛ
1.Анализ технологичности конструкции детали [8]
Технологичность – это свойство конструкции позволяющее изготовить ее с наименьшими затратами труда времени и средств для обеспечения заданных технических характеристик. В понятие технологичность входит удобство не только изготовления но и осмотров ремонтных работ. Из определения следует что конструкция детали или узла должна соответствовать масштабу производства те есть деталь технологическая в условиях среднесерийного производства в смысле применяемых материалов методов производства заготовок требований к точности обработки и сборке будет технологичной при крупносерийном и массовом производстве.
Количественная оценка технологичности конструкции
В качестве количественного показателя технологичности рассмотрен Ким – коэффициент использования материала который равен:
mд – масса детали кг;
mз – масса заготовки кг;
Ким = 2131·100% = 68 %.
Полученный коэффициент используемого материала является средним что свидетельствует о том что 32% материала идет в отходы.
Наиболее точные поверхности выполнены по 8 квалитету точности и шероховатости поверхности Rа=125. Форма детали позволяет получить легкий доступ к обрабатываемой поверхности.
Следовательно деталь технологична.
процесса востановления детали.
Вал изготовлен из стали 40Х термически обработан - закалка шеек ТВЧ. Износу подвергаются гладкие шейки и рабочие поверхности шлицев. По техническим условиям валы подлежат восстановлению наплавкой под флюсом с последующей механической и термической обработками.
Технология восстановления следующая:
Гладкие шлицевые шейки и рабочие поверхности шлицев вала предварительно прошедшего мойку очищают стальной щеткой до металлического блеска. Осматривают центровые отверстия вала и исправляют их на токарном станке.
Подготовленный к наплавке вал устанавливают на токарный станок оборудованный аппаратом для наплавки под флюсом А-580. Шлицевая шейка зажимается в патрон станка второй конец вала подпирается задним центром.
Гладкие шейки вала наплавляются электродной проволокой марки Нп-30ХГСА под слоем флюса АН-348-А. Электрод смещают против вращения на 15-20 мм вылет электрода 10 мм сварочный ток обратной полярности 230 А напряжение дуги 29 В. Скорость наплавки 10 мч скорость подачи электродной проволоки 50 мч частота вращения шпинделя 1 мин-1 продольная подача головки соответствующая шагу наплавки - 2 мм на оборот шпинделя.
Первый и последний витки наплавляются при выключенном шпинделе станка. Шлаковая корка удаляется в процессе наплавки. Наплавленная поверхность осматривается. Поры и непровары не допускаются.
Вал с наплавленными гладкими шейками переворачивают наплавляют изношенные шлицы продольным швом (при выключенном шпинделе станка) в три прохода.
Во избежание деформации в порядке очередности наплавляют диаметрально противоположные шлицы. Наплавка ведется электродной проволокой марки 30ХГСА диаметром 18 мм. Ток постоянный обратной полярности 230 А напряжение дуги 29 В. Обязателен контрольный осмотр наплавленных шлицев. Поры и непровары не допускаются.
На токарном станке обрабатываются наплавленные шейки; нарезаются шлицы на горизонтально-фрезерном станке.
Термическая обработка вала - закалка ТВЧ с последующим отпуском.
Шлифовка шеек на круглошлифовальном станке до чертежных размеров.
Технологические процессы восстановления всех валов с гладкими и шлицевыми шейками отличаются друг от друга только некоторыми параметрами режимов наплавки а именно: частотой вращения вала (12-3 мин-1 в зависимости от его диаметра); скоростью подачи проволоки (79-180 мч) и потребной величиной сварочного тока (180-300 А).
Все остальные параметры режима наплавки являются общими для процесса восстановления под флюсом гладких и шлицевых шеек валов: флюс АН-348-А; шаг наплавки 4-5 мм; скорость наплавки 12-16 мч; вылет электрода 15-25 мм; напряжение 32-34 В; марка проволоки Нп-30ХГСА; диаметр проволоки 18-2 мм.
3. Определение типа производства
Годовая программа деталей
где: N1 - годовая программа изделий;
m - количество деталей данного наименования на изделие;
b - коэффициент учитывающий запасные детали.
Тип производства можно определить согласно ГОСТ 14.004 – 83 по коэффициенту закрепления операций К30.
О К30 40 мелкосерийное
К30 20 среднесерийное
К30 10 крупносерийное.
При обработке деталей определяем тип производства по таблице. В зависимости от массы (mд = 21 кг) и годовой программы выпуска (N = 25000 шт) предварительно принимаем тип производства крупносерийный.
Уточняем тип производства по коэффициенту закрепления операций который определяется по формуле:
Р – число рабочих мест
О – число различных операций
– сумма операций закрепленных за каждым рабочим местом.
Число операций закрепленных за одним рабочим местом:
Qрм = знз где зн – нормативный коэффициент загрузки рабочего места всеми закрепленными за ним операциями; з – коэффициент загрузки рабочего места проектируемой операции.
где Cр – принятое количество рабочих мест
СR – расчетное количество рабочих мест.
где Тшт к = штучно – калькуляционное время
Fд = 4015 час – действительный годовой фонд времени работы оборудования.
Определяем штучно–калькуляционное время по операциям:
Маршрут обработки [10]:
а) наплавка изношенных частей вала
а) черновая обточка наружных поверхностей по контуру левой стороны
Т0 = 00001*d*l=00001*44*126=055 мин.
а) фрезерование шпоночного паза
Т0 = 0004*l*i=0004*30*14=168 мин.
а) фрезерование восьмишлицевой поверхности
Т0 = 0009*l*z=0009*44*8=317 мин.
а) наружное шлифование 2-х цилиндрических поверхностей
Т02 = 000015*d*l= 000015*50*44=033 мин.
Т0 = Т01 + Т02=028+033=061 мин.
Среднее штучно-калькуляционное время.
где - коэффициент зависящий от вида оборудования [10].
Тш-к=15*055=083 мин.
Тш-к=151*168=254 мин.
Тш-к=127*317=403 мин.
Тш-к=155*061=095 мин.
Расчетное количество рабочих мест.
Определим число рабочих мест:
О = 06+85+14+27+44=134.
Коэффициент закрепления операций
Коэффициент закрепления операций К30 = 27 что соответствует крупносерийному типу производства.
4. Определение структуры технологического процесса и
Операция № 005. Наплавочная.
Наплавление изношенных частей вала.
Технологическая база - поверхности торцовых отверстий.
Оборудование – Установка для наплавки под слоем флюса А-580.
Операция №015. Токарно-винторезная.
Черновая токарная обработка по контуру левой стороны заготовки.
Оборудование – токарно-винторезный станок1716Ц.
Операция №025. Шпоночно-фрезерная.
Фрезерование шпоночного паза.
Технологическая база - наружная поверхность с упором в торец.
Оборудование – шпоночно-фрезерный станок 692М.
Операция №035. Шлицефрезерная.
Фрезерование восьмишлицевой поверхности.
Оборудование – зубофрезерный полуавтомат 5К301П.
Операция №045. Круглошлифовальная.
Наружное шлифование 2-х цилиндрических поверхностей.
Технологическая база – поверхности торцовых отверстий.
Оборудование – круглошлифовальный станок 3М153.
Операция №055. Контрольная.
Оборудование – стол контролера.
5. Выбор оборудования режущих инструментов и средств измерения
Операция №005. Наплавочная.
Оборудование – токарный станок с аппаратом для наплавки под флюсом А-580.
Средства измерения – штангенциркуль ШЦ-I-125 ГОСТ 166-89.
Оборудование – токарно-винторезный станок 1716Ц.
Режущий инструмент – резец 2103-0695 Т15К6 ГОСТ 20872-80; резец первый фасонный Т15К6.
Средства измерения – штангенциркуль ШЦ-I-125 ГОСТ 166-89; калибр-втулка конусный специальный.
Режущий инструмент – фреза 2234-0363 ГОСТ 9140-78.
Средства измерения – штангенциркуль ШЦ-I-125 ГОСТ 166-89; калибр специальный.
Режущий инструмент – фреза червячная шлицевая специальная.
Средства измерения – штангенциркуль ШЦ-I-125 ГОСТ 166-89; калибр-скоба 502h9 ГОСТ 18360-93.
Режущий инструмент – круг шлифовальный специальный.
Средства измерения – калибры-скобы 40k9 и 50h7 ГОСТ 18360-93; радиусомер выпуклый специальный.
6Расчет припусков и межоперационных размеров [10]
Припуск – слой материала удаляемый с поверхности заготовки в целях достижения заданных свойств обрабатываемой поверхности.
Рассчитываем припуск на обработку поверхности 40 k6.
Назначаем маршрут обработки:
чистовое шлифование;
Расчёт припуска для заданного размера производим расчётно-аналитическим методом который базируется на анализе факторов влияющих на припуске предшествующего и выполняемого переходов.
Минимальный припуск на обработку
где Rzi-1 – высота неровностей профиля на предшествующем переходе
Ti-1 – глубина дефектного поверхностного слоя на предшествующем переходе - суммарное отклонение расположения поверхности - погрешность установки заготовки на выполняемом переходе.
Суммарное отклонение расположения поверхности.
- коробление заготовки
Δкор – коробление стержня заготовки мкм на 1 мм длины (1 мкм).
L – длина заготовки; L=620 мм
Δк = Δкор· L = 1 · 620 = 620 мкм.
Суммарное отклонение расположения поверхности по переходам с учётом коэффициента уточнения:
черновое точение1=006·1240 = 74 мкм
чистое шлифование3=002·1240 = 25 мкм.
Погрешность установки базирования.
Черновое точение = 60 мкм база – центровые отверстия.
Чистое шлифование = 60 мкм база – центровые отверстия шейки вала.
Качество поверхности допуски на заготовку и деталь по переходам
Заготовка: Rz = 150 мкм; h = 250 мкм; Td = 1300 мкм;
Rz = 100 мкм; h = 100 мкм; Td = 520 мкм.
Чистовое шлифование:
Rz = 6.3 мкм; h = 12 мкм; Td = 13 мкм.
Минимальный расчётный припуск на обработку:
·zmin1 = 2[(150+250)+] = 3280 мкм
·zmin2= 2[(12+13)+] = 280 мкм.
Предельные расчётные размеры
Dmin(i-1)=Dmin(i)+ 2·zmin
Dmin2 = 39987 + 028=40267 мм
Dmin1 = 40267+328=43547 мм
Dmaх(i-1) = Dmin(i-1) + Tdi-1
Dmax2 = 40987+0013=40 мм
Dmax1 = 40267+052=40787 мм
Dmax заг. = 43547+13=44847 мм.
·zmax1 =40787-40=0787 мм = 787мкм
·zmax2 = 44847-40787 = 406 мм = 4060 мкм
Правильность проведенных расчетов произведем по формуле:
·zmax - 2·zmin = T·d3 – T·dд.
Таблица 3.3 – Результаты расчета припусков и межоперационных размеров.
Технологические переходы обработки шейки вала
Элементы припуска мкм
Расчётный минимальный припуск 2zmin мкм
Расчётный предельный размер Dmin мкм
Допуск на изготовление детали Td мкм
Предельные припуски мкм
Предельные размеры мкм
Рисунок 3.1 – Схема графического расположения полей припусков и допусков на обработку шеек вала бетономешалки.
7 Расчёт режимов резания
Станок – токарный с аппаратом для наплавки под флюсом А-580.
Наплавка изношенных частей вала.
Частота вращения детали
Скорость подачи проволоки
Станок – токарно-винторезный 1716Ц.
Резец 2103-0695 Т15К6 ГОСТ 20872-80.
Мощность электродвигателя главного привода станка 185 кВт.
Черновая токарная обработка 412 левой стороны заготовки.
Черновая токарная обработка 512 левой стороны заготовки.
Резец первый фасонный Т15К6.
Станок – шпоночно-фрезерный станок 692М.
Фреза 2234-0363 ГОСТ 9140-78.
Режимы резания назначенные табличным способом: [11]
Станок - зубофрезерный полуавтомат 5К301П.
Фреза червячная шлицевая специальная.
Станок - круглошлифовальный станок 3М153.
Круг шлифовальный специальный.
Наружное шлифование цилиндрической поверхности 40k6.
Наружное шлифование цилиндрической поверхности 50h6.
8 Расчет технических норм времени.
В расчет принимается переход с наибольшим основным временем.
Операция №025 Шпоночно-фрезерная.
На шлифовальной операции:
ТЕХНИКО-ЭКОНОМИЧЕСКОЕ ОБОСНОВАНИЕ ПРОЕКТА
Целью экономических расчётов является обоснование экономической целесообразности разработки проекта комплексной механизации работ по транспортированию и установке на металлорежущие станки заготовок массой до 10 т.
Произведены следующие расчёты:
Расчёт численности всех категорий рабочих;
Расчёт себестоимости изделия;
Расчёт основного фонда заработной платы;
Дополнительный фонд заработной платы;
Транспортные расходы;
Общезаводские расходы;
Внепроизводственные расходы;
Расчёт затрат на электроэнергию;
Использовались следующие методы экономического анализа:
Таблица 4.1 – Исходные данные для расчёта
Годовой объем выпуска продукции
Коэффициент выполнения норм
Общезаводские расходы
Внепроизводственные расходы
Таблица 4.2 – Значение показателей базового варианта
Наименование показателей
Готовая продукция шт.
Трудоемкость программы с учетом Квн.
Средний коэффициент загрузки.
Трудоемкость изделия нч
Выработка на одного рабочего нч
Общее количество рабочих 3 разряда в том числе:
а:) производственных рабочих
б) вспомогательных рабочих
Годовой фонд заработной платы
а: производственных рабочих
б: вспомогательных рабочих
Полная себестоимость единицы руб.
Страховые отчисления %
Заводские расходы руб.
Полная себестоимость годового выпуска руб.
Затраты на электроэнергию в год руб.
1. Расчет численности всех категорий рабочих
Число рабочих дней в году:
где П – праздничные дни
Дн - дни невыхода на работу по уважительной причине.
Полезный фонд времени одного рабочего:
Таблица 4.3 – Структура годового действительного полезного фонда времени одного рабочего
Состав рабочего времени
Календарный фонд времени
Количество нерабочих дней
Количество календарных рабочих дней
Неявки на работу всего в днях
Число рабочих дней в году
Средняя продолжительность рабочего дня
Полезный фонд времени 1 рабочего
Трудоемкость изделия:
где tшт. – штучно калькуляционное время на изготовление изделия.
Трудоемкость программы:
Количество основных рабочих:
Таблица 4.4 - Численность основных рабочих 3 разряда
2. Расчет фонда заработной платы
Фонд заработной платы основных рабочих:
где Тст - тарифная ставка;
Кв - коэффициент вредности;
Прямой фонд заработной платы:
где Rопер=32277 руб. - сумма расценок операций;
Дополнительный фонд заработной платы:
Годовой фонд заработной платы:
Основной фонд заработной платы: 126329840 руб.
Дополнительный фонд заработной платы: 12632984 руб.
Годовой фонд заработной платы: 138962820 руб.
Фонд заработной платы ИТР:
Таблица 4.5 - Фонд заработной платы ИТР
Экономист-нормировщик
где ЗПитр. - оклад ИТР.
3. Расчет себестоимости изделия
Таблица 4.6 - Материальные затраты
Наименование покупных комплектующих изделий и полуфабрикатов
Норма расхода изделия
Электродвигатель 5A200L8 шт
Кнопочная станция ПУ2 шт
где Сизд - суммарная цена на изделие.
Неучтенные материалы:
Транспортные расходы:
Основная заработная плата:
Дополнительная заработная плата:
где ЗПосн. - основная заработная плата.
Единый социальный налог:
Общезаводские расходы:
Производственная себестоимость выпуска:
Внепроизводственные расходы:
где Спр. - производственная себестоимость выпуска.
Таблица 4.7 - Калькуляционная ведомость затрат
Основные материалы собственные и покупные и фабрикаты.
Основная ЗП производственных рабочих
Дополнительная ЗП производственных рабочих.
Итого цеховая себестоимость выпуска.
Общезаводские расходы.
Итого производственная себестоимость выпуска.
Внепроизводственные расходы.
Итого полная себестоимость выпуска
Себестоимость 1 изделия
4 Расчет затрат на энергоносители
Расчет годового расхода электроэнергии
Электрическая энергия расходуется на питание электродвигателей электронагревательных приборов аппаратуры и на освещение помещений.
Затраты на электроэнергию рассчитываются по формуле:
где Зэл – затраты на электроэнергию гр.;
Цэл – цена 1 кВтч электроэнергии Цэл = 180 копкВт×ч;
Муст – средняя мощность токоприемников цеха на одном рабочем месте
Спр – число рабочих мест Спр = 14
Р – число смен; Р = 3
КЗ. – коэффициент загрузки; КЗ = 026
Ко – коэффициент одновременности работы токоприемников цеха Ко =07 09; принимаем Ко = 08;
Кпот – коэффициент учитывающий потери в сети
принимаем Кпот = 096;
Кпд – КПД токоприемников Кпд = 08 09; принимаем Кпд = 085
Таблица 4.5. - Сводная таблица технико-экономических показателей
Трудоемкость программы с учетом Квн нч
Процент страховых расходов.
Процент заводских расходов
Таблица 4.6 – Сравнительная таблица технико-экономических показателей базового и проектируемого варианта.
Затраты на электроэнергию руб
Выводы: для обеспечения выпуска продукции (245 штук в год) необходимо организовать участок на 16 рабочих 3 разряда. По программе выпуска можно сделать вывод что данный участок будет организован в условиях среднесерийного производства.
Чтобы обеспечить выпуск машин необходимо производственных рабочих 10 человек вспомогательных рабочих - 2 человека и ИТР - 2 человек.
При внедрении разработанного проекта комплексной механизации и внедрении разработанного цепного кантователя стоимостью 2810290 руб. коэффициент выполнения норм Квн на участке получился больше единицы что привело к возможности высвобождение численности работающих в количестве 2 человек это позволит снизить затраты на заработную плату и на электроэнергию.
После проведения работ по комплексной механизации цеха увеличивается денежный фонд предприятия. Если до проведения комплексной механизации цеха денежный фонд заработанной платы составлял 15881465 руб то после проведения составляет 126329840 руб. Полученная разница от заработной платы в количестве 3248481 руб. и денежные средства полученные в результате снижения потребления электроэнергии в количестве 4975478руб. позволит увеличить фонд накопления и потребления средства из которого пойдут на приобретение нового оборудования на проведение своевременного ремонта и модернизации производственных фондов предприятия а также для выплаты премий пособий т.е. повышение заинтересованности работающих в более высоких показателях выработки качественной продукции.
ОБЕСПЕЧЕНИЕ БЕЗОПАСНОСТИ ЖИЗНЕДЕЯТЕЛЬНОСТИ
1 Указание мер безопасности при обслуживании машины.
Цепной кантователь должен устанавливаться на фундамент и надежно закрепляться.
Корпус машины должен быть надежно заземлен. Сопротивление электрической изоляции токоведущих частей должно быть не менее 05 МОм при напряжении 500 В.
Перед вводом в эксплуатацию необходимо проверить работу кантователя на холостом ходу и под нагрузкой.
Обслуживающий персонал должен соблюдать следующие указания:
а) начинать работу на кантователе только с разрешения лица ответственного за технику безопасности;
б) ежедневно перед началом работы проводить технический осмотр и опробование на холостом ходу;
в) при обнаружении неисправности во время работы кантователя немедленно остановить ее нажатием кнопки «Стоп»;
г) в конце смены отключить кантователь от электросети автоматическим выключателем;
д) при проведении наладочных и ремонтных работ кантователь отключить.
а) оставлять работающий кантователь без присмотра;
б) эксплуатировать кантователь при обнаружении дефектов.
2. Безопасность при механизированной транспортировке грузов.
Последние годы на промышленных предприятиях широко применяется механизация транспортировки грузов. Прямой производственный эффект выражается в сокращении необходимого числа рабочих занятых тяжелым физическим трудом в замене ручного труда высокопроизводительной работой механизмов и следовательно в ликвидации источников травматизма.
При механизации нужно использовать не только сложные и дорогостоящие машины и оборудование но и простые механизмы и устройства облегчающие труд и обеспечивающие условия безопасности при погрузочно-разгрузочных работах что имеет особое значение для небольших и средних промышленных предприятий.
На крупных металлургических и машиностроительных заводах при выполнении тяжелых и трудоемких производственных и транспортирующих операций больше внимания следует уделять внедрению комплексной механизации при которой используются все технические средства осуществляющие полный цикл механизированных операций. Применение грузоподъемных машин с крюковыми чалочными приспособлениями сводит труд рабочих к управлению этими механизмами и выполнению лишь вспомогательных операций. При использовании же электромагнитных шайб грейферов или сбрасывающей тележки эти вспомогательные операции выполняются механически или автоматически.
3 Техника безопасности при использовании
грузоподъемных механизмов.
Подъем грузов при транспортировки их внутри цеха чаще производится мостовыми кранами тельферами консольными и другими кранами.
Нарушение технических правил и требований безопасности при эксплуатации кранов персоналом занимающимися подцепкой укладкой и транспортировкой грузов может повлечь за собой несчастные случаи.
На основании данных органов надзора наибольшее количество
несчастных случаев происходит при работе на стреловых передвижных и башенных кранах и меньше несчастных случаев – при эксплуатации мостовых электрических кранов. Однако следует сказать что факторы обуславливающие несчастные случаи при работе на тех и на других кранах по существу одни и те же.
Аварии и несчастные случаи связанные с работой мостовых кранов большей частью возникали из-за низкого качества ремонтов превышения срока службы грузовых и чалочных канатов из-за конструктивных недостатков отдельных элементов крана и вследствие нарушения общих правил строповки и перемещения грузов а также при загроможденности и неправильной укладке грузов в зоне действия мостовых кранов.
Причиной падения крюка вместе с подвешенным грузом на мостовых кранах нередко являлись конструкционные недостатки крестовой муфты Ольдгема связывающей барабан механизма подъема с редуктором. Металл быстро срабатывался и кулачки муфты выходили из зацепления. Такие явления наблюдались на кранах с тележками типа МЭСГ-ЭТ5 КТК-5-Т-25 и другими.
Изношенность деталей муфты создает большие усилия направленные вдоль оси грузового барабана что как правило приводит к разрушению опорного подшипника барабана и к сдвигу барабана на величину сцепления муфты.
По правилам техники безопасности не допускается подъем грузового крюка или другого грузозахватного устройства выше допускаемого предела так как подтягивание их к неподвижной конструкции подъемного механизма при продолжающейся работе электродвигателя может вызвать обрыв каната и падение груза. Во избежание этого подъемные механизмы оборудуются автоматическим ограничителем высоты подъема который должен останавливать движение крюка или грузозахватного органа на расстоянии 50мм до верхнего упора у электротельферов и 200мм у всех других грузоподъемных машин.
На мостовых кранах для ограничения движения моста и тележки крана устанавливаются концевые выключатели которые работают на размыкание цепи тока.
Одним из основных условий безопасности эксплуатации грузоподъемных механизмов являются хорошо действующие тормозные устройства обеспечивающие в механизмах подъема остановку груза и удержание его в подвешенном состоянии а в механизмах передвижения и поворота – остановку механизма на определенной длине тормозного пути.
По своей конструкции тормоза разделяются на колодочные и ленточные а по принципу действия – на открытые и замкнутые.
Тормоза замкнутого типа более надежны. Поэтому они получили наибольшее распространение на кранах и в частности на механизмах подъема.
В тормозах замкнутого типа снабженных тормозным электромагнитом при отключении тока происходит автоматическое затормаживание механизма и удержание поднимаемого или опускаемого груза.
Все передвижные краны с машинным приводом должны быть снабжены хорошо слышными механическими или электрическими сигналами. При бездействии или отсутствии сигнального прибора работа крана не
Предупреждение аварий кранов и вызываемых при этом несчастных случаев зависит в значительной степени от соответствия и исправности канатных и цепных стропов а также от правильности примененного способа подвязки груза. Поэтому перед началом транспортировки груза необходимо тщательно осматривать чалочно-стропальные приспособления не допуская их к работе при несоответствии техническим требованиям и весу поднимаемого груза.
При транспортировке груза краном для выполнения операций по подвязке (зацепке) к крюку и отцепке груза должен назначаться опытный
стропальщик (чальщик).
Стропальщик в процессе транспортировки грузов подъемным механизмом является лицом ответственным за безопасное выполнение этого процесса. Между тем на некоторых предприятиях существует совершенно необоснованная тенденция недооценки роли и значения этой профессии.
При работе на грузоподъемных механизмах необходимо учитывать что вес поднимаемых грузов ни в коем случае не должен превышать подъемной силы механизма. В тех механизмах которые не имеют ограничителей грузоподъемности в сомнительных случаях следует проверять вес груза по документам или путем подсчета.
При обвязке поднимаемого груза канаты и стропы следует накладывать на основной массив относительно центра тяжести груза и в то же время так чтобы центр тяжести находился ниже точек приложения каната или стропа.
Для сохранения равновесия при подъеме длинномерных и тяжеловесных грузов необходимо производить скрепление не менее чем двумя стропами.
Для предупреждения раскачивания перемещаемого груза последний по возможности следует подтягивать в наивысшее положение. При наивысшем положении груза длина канатов должна быть не менее 1м.
При перемещении тяжеловесных и крупногабаритных грузов крановщик может перемещать их лишь после того как проверит прочность и надежность зачаливания. Качество зачаливания проверяется путем предварительного подъема груза на высоту не более 500мм от пола или земли. Поднятый груз осматривается стропальщиком. Зачаливание считается надежным если канаты или цепи не скользят по поверхности груза.
В тех случаях когда груз поднимается или опускается с места закрытого от глаз крановщика сигналы стропальщика передаются через специального сигнальщика. Сигнальщик должен находится в пункте видимому крановщику и стропальщику.
Сигнал остановки крановщик должен выполнять немедленно внезависимости от того кем этот сигнал подан и как он выражен.
При работе на грузоподъемном кране запрещается подтаскивать грузы волоком крюком механизма подъема отрывать груз углубленный или примерзший к земле а также выравнивать собственным весом поднимаемый груз. Запрещается вытаскивать крюком из-под груза защемленные канаты цепи и другие грузозахватные и чалочные приспособления.
Канаты и цепи для обвязки поднимаемых грузов надо подбирать такой длины чтобы угол между их ветвями был наименьший и не превышал 900. Рекомендуется снабжать стропальщиков таблицей нагрузок на стропы в вертикальном положении концов. При расхождении стропов от крюка на 300 допустимая нагрузка уменьшается на 5% при прохождении на 450 – на 10% при расхождении на 600 – на 15% при расхождении на 900 – на 30% а при расхождении на 1200 допустимая нагрузка снижается вдвое.
Увеличение угла между ветвями свыше 900 может быть допущено только в исключительных случаях когда высота подъема грузозахватного органа не позволяет применять более длинные стропы и когда невозможно переместить чалки по грузу.
Всем стропальщикам должно быть вменено в обязанность при посадке или съеме стропов не давать крановщику сигнала на подъем крюка до тех пор пока руки стропальщика не будут сняты со стропов или крюка. Это правило нередко нарушается стропальщиком в расчете на то что пока натянутся стропы он успеет убрать руки.
Груз перемещаемый в горизонтальном направлении должен находится на расстоянии не менее 2м от пола и не менее 05м над встречающимися на пути предметами. Груз следует подавать на заранее подготовленное для его укладки место. Ни в коем случае не допускается выдергивание силой крана защемленных грузом стропов; это приводит к развалу груза и опасному
косому натяжению грузовых канатов крана и стропов.
Во время перемещения не следует допускать раскачивания груза а также нельзя оставлять его на весу в перерывах или после окончания работы.
При эксплуатации крана необходимо руководствоваться всеми правилами техники безопасности установленными главной государственной инспекции.
Ниже приводятся только основные требования техники безопасности:
На обеих сторонах крана должны висеть таблички указывающие его наибольшую грузоподъемность.
Подниматься на кран и подкрановые пути разрешаются исключительно по лестницам и в предназначенных для этого местах.
Переходить с одного крана на другой находиться на мосту или тележки крана во время его работы проходить на ходу осмотр смазку обтирку и ремонт механизма крана воспрещается.
Инструмент и запасные части на мосту и тележки должны хранится только в специальных ящиках: хранение их без ящиков категорически воспрещается.
Муфты ходовые колеса и открытые зубчатые передачи должны быть ограждены кожухами.
Во время работы крана когда электрооборудование его находится под током запрещается открывать для осмотра и ремонта сопротивления контроллеры щитки и пр.
Необходимо проводить наружный осмотр канатов при сдаче каждой смены и не реже одного раза в 7 – 10 дней а перед навеской на кран нового каната последний следует подвергнуть механическому испытанию
Периодически а также после каждого ремонта должны производиться испытания крана в присутствии инспектора по технике безопасности.
Необходимо выключить главные троллеи и рубильники крана после окончания работы или на время перерыва для ремонта.
В целях предупреждения пуска в работу не исправного крана на нем и в его кабине должны быть вывешены таблички «кран неисправен».
4 Меры защиты от опасности поражения электрическим током [16]
К защитным мерам от опасности прикосновения к токоведущим частям электроустановок относятся: изоляция ограждение блокировка пониженные напряжения электрозащитные средства сигнализация и плакаты. Надежная изоляция проводов от земли и корпусов электроустановок создает безопасные условия для обслуживающего персонала. Основная характеристика изоляции – сопротивление. Во время работы электроустановок состояние электрической изоляции ухудшается вследствие нагрева механических повреждений влияние климатических условий и окружающей производственной среды. Состояние изоляции характеризуется сопротивлением тока утечки. Согласно ПУЭ сопротивление изоляции в электроустановках напряжением до 1000 В должно быть не менее 05 МОм. Сопротивление изоляции необходимо регулярно контролировать. Для периодического контроля изоляции применяется мегаомметр для постоянного контроля – специальные приборы контроля изоляции (ПКИ).
Для обеспечения недоступности токоведущих частей оборудования и электрических сетей применяют сплошные и сетчатые ограждения. Сплошные конструкции ограждений (кожухи крышки шкафы закрытые панели и т.д.) а также сетчатые конструкции применяют в электроустановках и сетях напряжением как до 1000 В так и свыше 1000 В. В последних должны наблюдаться допустимые расстояния от токоведущих частей до ограждений которые нормируются ПУЭ.
Блокировку применяют в электроустановках напряжением свыше 250 В в которых часто производят работы на ограждаемых токоведущих частях. С помощью блокировки автоматически снимается напряжение (отключается питание) с токоведущих частей электроустановок при прикосновении с ними без предварительного отключения питания. По принципу действия блокировки бывают механические электрические и электромагнитные.
Для защиты от поражения электрическим током при работе с ручным электроинструментом переносными светильниками или в помещениях с особой опасностью применяют пониженные напряжения питания электроустановок: 42 36 и 12 В.
При обслуживании и ремонте электроустановок и электросетей обязательное использование электрозащитных средств к которым относятся: изолирующие штанги изолирующие и электроизмерительные клещи слесарно-монтажный инструмент с изолирующими рукоятками диэлектрические перчатки диэлектрические боты калоши коврики указатели напряжения. Для предупреждения персонала о наличии напряжения или его отсутствии в электроустановках применяется звуковая или световая сигнализация.
С целью предупреждения работающих об опасности поражения электрическим током широко используют плакаты и знаки безопасности. В зависимости от назначения плакаты и знаки делятся на предупреждающие («Стой! Напряжение» «Не влезай! Убьет» и другие); предписывающие («Не включать. Работают люди» и другие); указательные («Заземлено» и другие).
Защитное заземление предназначено для устранения опасности поражения электрическим током в случае прикосновения к корпусу и другим нетоковедущим частям электроустановок оказавшимся под напряжением вследствие замыкания на корпус и по другим причинам (рис. 4.16). При этом все металлические нетоковедущие части электроустановок 1 соединяются с землей с помощью заземляющих проводников 2 и заземлителя 3.
Заземлитель – это проводник или совокупность металлических соединенных проводников находящихся в соприкосновении с землей или ее эквивалентом. Заземлители бывают искусственные предназначенные исключительно для целей заземления и естественные – находящиеся в земле металлические предметы иного назначения.
Для заземления оборудования в первую очередь используют естественные заземлители: железобетонные фундаменты а также расположенные в земле металлические конструкции зданий и сооружений.
Защитное заземление применяют в сетях напряжением до 1000 В с изолируемой нейтралью и в сетях напряжением свыше 19000 В как с изолированной так и с заземленной нейтралью.
Рисунок 6.1 - Схема защитного Рисунок 6.2 - Схема защитного
заземления в однофазной зануления
С помощью защитного заземления уменьшается напряжение на корпусе относительно земли до безопасного значения следовательно уменьшается и сила
тока протекающего через тело человека. На схеме защитного заземления (рис. 6.1) показано что напряжение приложенное к телу человека в случае прикосновения к оборудованию можно снизить уменьшая сопротивления заземляющего устройства. Согласно ПЭУ сопротивление заземления в электроустановках до 1000 В не должно превышать 4 Ом.
Защитное зануление так же как и защитное заземление предназначено для устранения опасности поражения электрическим током при замыкании на корпус электроустановок. Защитное зануление осуществляется присоединением корпусом и других конструктивных нетоковедущих частей электроустановок к неоднократно заземленному нулевому проводу (рис. 6.2).
Защитное зануление превращает пробой на корпус в короткое замыкание между фазным и нулевым проводами и способствует протеканию тока большей силы через устройства защиты сети а в конечном итоге быстрому отключению поврежденного оборудования от сети. Из приведенной схемы (рис. 6.2) видно что при замыкании на корпус фаза окажется соединенной накоротко с нулевым проводом благодаря чему через защиту (плавкий предохранитель или автомат) потечет ток короткого замыкания который и вызовет перегорание предохранителя или отключения автомата. Чтобы защита быстро срабатывала ток короткого замыкания должен быть достаточно большим. Правила требуют чтобы ток короткого замыкания был в три раза больше номинального тока плавкой вставки предохранителя или расцепителя автоматического отключения. Это требование выполняется если нулевой провод имеет проводимость не менее 50% проводимости фазного провода. В качестве нулевых проводов можно использовать стальные полосы металлические оплетки кабелей металлоконструкции зданий подкрановые пути и др.
Системы защитного отключения – это специальные электрические устройства предназначенные для отключения электроустановок в случае появления опасности пробоя на корпус. Так как основной причиной замыкания на корпус токоведущих частей оборудования является нарушение изоляции то системы защитного отключения осуществляют постоянный контроль за сопротивлением изоляции или токами утечки между токоведущими и нетоковедущими деталями конструкции оборудования. При достижении опасного уровня оборудование отключается до того момента когда произойдет пробой на корпус и появится реальная опасность поражения электрическим током.
Таким образом системы отключения обеспечивают наибольшую электробезопасность при прикосновении к корпусам электроустановок. Однако являясь достаточно сложными электрическими устройствами с определенной надежностью срабатывания они применяются чаще всего в сочетании с защитным заземлением и защитным занулением.
Наряду с применение технических методов и средств электробезопасности важное значение для снижения электротравматизма имеет четкая организация эксплуатации электроустановок и электросетей профессиональная подготовка работников сознательная производственная и трудовая дисциплина.
К работам на электроустановках допускаются лица достигшие 18 лет прошедшие инструктаж и обученным безопасным методам труда. Весь персонал допущенный к эксплуатации электроустановок в соответствии с занимаемой должностью и применительно к выполняемой работе аттестуется присвоением соответствующей квалификационной группы электробезопасности (сI по V).
К организации безопасной работы на электроустановках относится также документальное оформление работы допуск к работе надзор во время работы. Оформление разрешения на проведение работ в действующих электроустановках может быть выполнено в виде наряда распоряжения или перечня работ.
Ответственным за безопасность работ являются: лицо выдавшее наряд или распоряжение ответственный руководитель работ (начальник цеха участка мастер) и производитель работ.
4Расчет сопротивления заземляющего устройства [15]
Расчет заземляющего устройства производят исходя из его максимально допустимого сопротивления установленного для соответствующего электрооборудования.
-грунт суглинок (удельное сопротивления f=50 Ом м).
-в качестве заземлителя используем одиночный стержень.
-Длина стержня Lc =25 м.
-а=5 м – расстояние между стержнями.
-h=08 м – глубина стержня.
Определяем сопротивление одиночного заземлителя.
Определяем число заземлителей
где - коэффициент использования заземлителей
Принимаем девять заземлителей коэффициент использования 074.
Определяем общее число сопротивлений заземлителей.
Определяем длину соединительной полосы
Определяем сопротивление полосы без учета влияния заземлителей
Определения сопротивления полосы с учетом влияния заземлителей
Определяем общее сопротивление заземляющего устройства
Рассчитанное сопротивление заземляющего устройства удовлетворяет все требования безопасности при эксплуатации кантователя.
В данном дипломном проекте была проведена комплексная механизация работ по межоперационному транспортированию и установки на металлорежущие станки заготовок массой до 10т а также был разработан технологический процесс восстановления детали – шлицевый вал.
В результате чего проведён анализ: грузопотоков производственных и патентных данных была произведена разработка конструкции основных узлов цепного кантователя проведен анализ технологичности конструкции разработан первоначальный и окончательный вариант маршрута обработки детали определён тип производства экономически обоснован выбор оборудования режущего и мерительного инструмента рассчитаны режимы резания технические нормы времени припуски и межоперационные допуски на размеры детали. На основании принятых технических решений произведен расчет экономического эффекта применения цепного кантователя а также расчет его себестоимости произведен анализ безопасной и безаварийной работы используемого оборудования и технологической оснастки и установлены соответствующие мероприятия.
Разработаны чертежи цепного кантователя рабочие чертежи деталей эскизы технологических наладок на операции.
Все принимаемые решения по ходу разработки дипломного проекта обоснованы техническими и экономическими расчётами данными ГОСТов и справочной литературы.
Список использованной литературы.
Пантелеев В.Ф. Расчеты деталей машин. - Пенза.: ПГУ 2002.
М.Н.Иванов и др. Детали машин. – М.: Высшая школа- 1991г.
А.А.Эрдели Н.А.Эрдели. Детали машин. – М.: Высшая школа- 2002г.
Пантелеев В.Ф. Конструирование деталей и узлов технологических и транспортных машин. Учебное пособие для вузов. – Пенза.: ПГУ 2003.
В.Н. Кудрявцев и др. Курсовое проектирование деталей машин. – Ленинград.: «Машиностроение» - 1984г.
Писаренко Г.С. Справочник по сопративлению материалов. – Киев.: Наукова думка 1975 г.
Коштальян И.А. Обработка на станках с ЧПУ И.А. Коштальян А.И. Клевзович. – Минск.: Высшая школа 1989. – 276 с.
Сидоркин В.Ф. Проектирование технологической оснастки В.Ф. Сидоркин В.А. Скрябин. – Пенза.: ППИ Учебное пособие 1992. – 120 с.
Технология машиностроения (специальная часть) А.А. Гусев Е.Р. Ковальчук И.М. Колесов и др. – М.: Машиностроение 1986. – 480 с.
Ансеров М.А. Приспособления для металлорежущих станков. – М.: Машиностроение 1973. – 652 с.
Сергеев И.В. Экономика предприятия. – М.: Финансы и статистика 1988. – 348 с.
Швалев А.К. Охрана труда в технологических процессах строительного производства. Казань. Высшая школа. 1988 – 496с.
Найфельд М.Р. Заземление защитные меры электробезопасности. М.: Энергия. 1971 – 312с.
Технологическая документация
Спецификация Кантователь цепной.dwg

Спецификация Электротележхка 2.dwg

010 Тех. наладки1.dwg

Зубофрезерный полуавтомат 5К301П
Операция 025. Круглошлифовальная
Операция 020. Шлицефрезерная
Доклад.doc
При анализе грузопотоков участка цеха №2 по обработке блока цилиндров и рамы дизельгенератора выявлены ряд недостатков: из 270 технологических операций 40% являются грузоподъемными связанными с перемещением заготовок по ходу технологического процесса кантованием и установкой на металлорежущие станки. Перемещение заготовок за пределы участка обеспечивает передаточная тележка грузоподъемностью 10 т представленная на листе 3. В пределах участка заготовку перемещают с использованием мостового крана грузоподъёмностью 10 т изображенного на листе 4.
Вращение заготовок вокруг горизонтальной оси для нужной фиксации на станках осуществляется при помощи мостового крана путем перестроповки изделий вручную стропальщиками. В следствии этого увеличивается время межоперационных простоев также заготовка имеет массу более 4 тонн и большие габариты и применение ручного труда требует большого физического усилия от работников. Для повышения производительности и безопасности труда необходима механизация процесса кантования.
Для устранения недостатков было предложено разработать конструкцию специального кантователя обеспечивающего вращение заготовки вокруг горизонтальной оси.
Для поиска оптимального технического решения проведен анализ существующего рынка специальной грузоподъемной техники и патентные исследования.
Промышленностью России выпускается несколько моделей кантователей:
Кантователь двухстоечный КД-05;
Кантователь с гидравлическими домкратами КГ 300;
Кантователь цепной КЦ 10А.
Однако рассмотренные модели кантователей имеют ряд недостатков: трудности обслуживания большие габариты сложность конструкции высокую стоимость.
В результате проведенных патентных исследований представленного на листе 5 установлено что большинство технических решений направлено на:
Повышение надежности кантователей;
Снижение энергоемкости при производстве деталей;
Повышение производительности кантователей;
Снижение занимаемых площадей кантователем (.
Анализ патентной информации показал что для заготовок формы близкой к параллепипиду и массой до 5т наиболее рациональным является конструкция кантователя в которой поворот заготовки производится на цепях подвешенными на стойках. Перемещение цепей осуществляется от электропривода.
На основе проведенного анализа выпускаемых кантователей и патентного поиска нами разработана конструкция цепного кантователя которая представленна на листах 5 и 6 которая состоит из шести опорных стоек электропривода трех цепных передач.
Цепной кантователь обеспечивает вращение заготовки вокруг горизонтальной оси массой до 5000 кг. Установка заготовки на кантователь осуществляется мостовым краном сверху. Натяжение цепи осуществляется под действием массы вращающегося груза. При включении электродвигателя через червячный редуктор приводится во вращение две цепные передачи установленные на двух парах опорных стоек. Цепные передачи приводят во вращение заготовку установленную на них.
Расчет мощности электродвигателя для привода кантователя производился с учетом сил необходимых для вращения заготовки.
В результате расчетов был выбран асинхронный электродвигатель мощностью 14 кВт.
Вращающий момент от электродвигателя передается при помощи червячного редуктора с передаточным числом равным 245.
На листе 6 приведен сборочный чертеж опорной стойки которая выполнена из листовой стали. Расчет металлоконструкции данной стойки производился исходя из условия прочности на изгиб. Исходя из полученного значения момента сопротивления сечения изгибу выбирано сечение стойки – тонкостенный прямоугольник полый.
Данная конструкция цепного контователя при установке в цехе №2 позволяет снизить нагрузку на мостовой кран обеспечивает поворот заготовки вокруг горизонтальной оси для нужного базирования на металлорежущие станки исключает применение тяжелого ручного труда при выполнении основных и вспомогательных производственных операций.
В технологической части проекта разработан процесс восстановления детали типа - вал. По техническим условиям валы подлежат восстановлению наплавкой под флюсом с последующей механической и термической обработками.
В пояснительной записке приведены расчеты припусков сил резания и других технологических параметров. На листах 9 10 и 11 приведены чертеж детали и технологические наладки при обработке вала.
В экономической части приведены результаты технико-экономического обоснования которые показали целесообразность применения данного оборудования в цехе обработки блока цилиндров и рамы дизельгенератора.
В разделе БЖД представлены меры безопасности при обслуживании машины техника безопасности при использовании грузоподъемных механизмов приведен расчет сопротивления заземляющего устройства.
Спасибо за внимание доклад окончен
Спецификация Кантователь цепной3.dwg

08 Шлицевый вал и тех. наладки1.dwg

Технологические наладки
Наплавлять до указанных размеров
степень сложности С1
Радиусы закругления 2 мм
кроме мест обозначенных особо
Острые кромки притупить
*Размеры для справок
Токарный станок с установкой для наплавки под флюсом А-580М
Наплавлять поверхности
Операция 005. Наплавочная
Спецификация Ведомость проекта1.dwg

Пояснительная записка
Документация графическая
Схема зачаливания блока
цилиндров дизельгенератора
Теоритический чертеж
Теоретический чертеж
План механизации участка цеха №2
Кран мостовой электрический
Электротележка грузоподъемностью 10т.
Технологические наладки
Рекомендуемые чертежи
- 24.01.2023
- 24.01.2023
- 24.01.2023
- 24.01.2023