Жарков В.Н, Морозов В.В., Гусев В.Г. (сост.) Металлорежущие станки




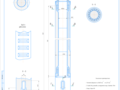
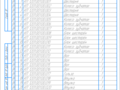
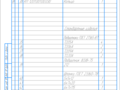
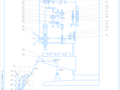
- Добавлен: 25.01.2023
- Размер: 1 MB
- Закачек: 0
Описание
Жарков В.Н, Морозов В.В., Гусев В.Г. (сост.) Металлорежущие станки
Состав проекта
![]() |
![]() |
![]() ![]() ![]() |
![]() ![]() ![]() ![]() |
![]() ![]() ![]() ![]() |
![]() ![]() ![]() ![]() |
![]() ![]() ![]() |
![]() ![]() ![]() ![]() |
![]() ![]() ![]() |
![]() ![]() ![]() |
![]() ![]() ![]() ![]() |
![]() ![]() ![]() ![]() |
![]() ![]() ![]() |
Дополнительная информация
Печать 4.doc
Сверлильные станки предназначены для сверления глухих и сквозных отверстий рассверливания зенкерования развёртывания растачивания и нарезания резьбы. Основными формообразующими движениями при выполнении сверлильных операций являются главное движение (вращение сверла вокруг своей оси) и движение подачи шпинделя со сверлом в металл заготовки. Кинематические цепи осуществляющие эти движения имеют самостоятельные органы настройки посредством которых устанавливается необходимая частота вращения инструмента и скорость его подачи.
Сверлильные станки подразделяются на вертикально-сверлильные горизонтально-сверлильные радиально-сверлильные одношпиндельные и многошпиндельные полуавтоматы. Настольные станки используют для сверления отверстий в стальных деталях (=500÷600 МПа) наибольшего диаметра 3; 6; 12; и 16 мм вертикально сверлильные горизонтально-сверлильные и радиально-сверлильные станки – для сверления и рассверливания отверстий диаметром 18; 25; 35; 50 и75 мм. Вылет траверсы радиально-сверлильных станков составляет 1300 – 2000 мм.
Целью курсового проекта является разработка привода главного движения по заданным максимальному диаметру сверления и материалам инструмента и обрабатываемой заготовки на базе существующего станка модели 2Н135.
Обоснование технической характеристики станка
1 Определение предельных диаметров сверла и рациональных режимов резания. Для основной известной модели вертикально-сверлильного станка 2Н135 наибольший диаметр сверления Dб=35 мм тогда наименьший диаметр сверла :
Dм=(015 03) Dб= 025х359 мм
При сверлении в сплошном материале глубина резания
Где D-диаметр сверла d-диаметр отверстия в заготовке полученное на предшествующей технологической операции.
Наибольший диаметр сверления Dб для универсальных вертикально- и радиально-сверлильных станков является их основным параметром и должен соответствовать ГОСТ 1227-72. При зенкеровании и развёртывании глубина резания равна величине припуска на сторону tм=05 мм tб=2 мм. При чистовом развёртывании отверстий диаметром 5-80 мм припуск на сторону tм=005 мм tб=025 мм. При черновом развёртывании припуск на сторону tм=01 мм tб=02 мм.
Находим наибольшую и наименьшую подачи на один оборот сверла для самого мягкого обрабатываемого материала при работе наибольшими и наименьшими диаметрами сверла ммоб
Определяем наибольшую и наименьшую скорости резания при сверлении деталей из стали с HB>155 ммин
где СV – коэффициент учитывающий свойства материала заготовки вид
сверления и характеристику инструмента; T – стойкость мин; Sм – подача наименьшая; D – диаметр инструмента; НВ – твёрдость заготовки.
Найдём предельные значения частот вращения шпинделя
Определим диапазон регулирования привода главного движения и привода подачи:
2 Определение силовых параметров процесса резания и эффективной мощности привода
Определим главную составляющую Pz силы резания при сверлении кН
Крутящий момент на шпинделе кН×м
Эффективная мощность кВт:
Мощность электродвигателя главного движения Nд определяется по наибольшей эффективной мощности резания кВт:
где k – коэффициент перегрузки станка k »12 – 13; h – к.п.д. привода главного движения h=07 – 085.
Так как модернизируемый станок имеет только один электродвигатель то при определении его мощности должна быть учтена мощность расходуемая также и в цепях привода подачи и вспомогательных движений. Мощность потребляемая на движение подачи обычно невелика и составляет от мощности привода главного движения для сверлильных станков – 4 5 %. Следовательно мощность электродвигателя станка
По найденной мощности выбираем двигатель типа – АИР160S2 у которого мощность Nдв=15кВт и частота вращения nдв=3000мин-1.
Кинематический расчёт привода.
Определение числа ступеней привода и построение структурной сетки
В этих целях задаёмся знаменателем геометрической прогрессии привода равным φ=141 как наиболее часто применяемый в универсальных станках. Тогда
Зная Zn запишем структурную формулу привода в общем виде:
где Р – количество передач в группах; m – число групповых передач.
В частном виде Zn=12=3×2×2; с учётом кинематического расположения основных переборных групп и их характеристик
Строим наиболее рациональную структурную сетку
Рис. 1 Структурная сетка привода
Для построения графика частот вращения валов привода построим его предварительную кинематическую схему с учётом одиночных передач. n=3000мин
Рис. 2. Кинематическая схема привода
Тогда график частот вращения валов привода будет иметь вид
Рис. 3. График частот вращения привода.
Определяем расчётные передаточные отношения колёс привода будут равны:
Расчёты передаточных отношений показывают что их численные значения лежат в допустимых пределах 025 ≤ i ≤ 2.0
Реальное передаточное отношение через числа зубьев колёс с использованием нормали станкостроения Н21-5 приведено в табл.1.
Числа зубьев колёс привода.
ΣZ – суммарное число зубьев пары зубчатых колёс которые могут зацепляться друг с другом.
Кинематическая схема привода главного движения и всего станка представлена в графической части.
Определение силовых и кинематических параметров привода
Так как для проектных расчётов нас интересует наиболее нагруженный режим то рассчитываем силовые и кинематические параметры для наименьших угловых скоростей валов.
Порядок и результаты расчета представлены в табл. 2.
Минимальная частота вращения n мин-1
Минимальная угловая скорость w с-1
Максимальный крутящий момент Т Н×м
Продолжение таблицы 2
соответственно к.п.д. зубчатой передачи и подшипника качения.
Определение модуля зубчатых колёс и геометрический расчёт привода.
1 Определение модуля зубчатых колёс.
Зубчатые колёса являются основным видом передач коробок скоростей. От их габаритов и качества зависят размеры и эксплуатационные характеристики всей коробки.
Основными причинами выхода из строя зубчатых колёс станков являются усталость поверхностных слоёв зубьев их износ смятие торцев зубьев переключающихся шестерён и реже поломка зубьев от усталости или перегрузок.
Расчёт зубчатых колёс ведётся в основном теми же методами которые рассматриваются в курсе «Детали машин». Однако при расчёте зубчатых передач станков модуль определяется не только исходя из прочности зуба на изгиб mизг но и из усталости поверхностных слоёв mпов.
В коробках скоростей размер шестерён в большинстве случаев определяется контактными напряжениями т.е. усталостью поверхностных слоёв зубьев. Специфика расчётов по сравнению с принятыми расчётами в курсе «Детали машин» заключается в том что число зубьев z известно из кинематического расчёта. Поэтому сначала следует найти наиболее нагруженную пару и для неё определить модуль исходя из прочности зуба на изгиб mизг к усталости поверхностных слоёв по формулам:
где и -допускаемые напряжения для контактной нагрузки и на изгиб
-номинальная передаваемая мощность ( мощность электродвигателя кВт; -к.п.д. передачи от электродвигателя до рассчитываемой шестерни); n – минимальная частота вращения шестерни (меньшего колеса зубчатой пары); y – коэффициент формы зуба; для Z=18 50 У=0.1 013; Z – число зубьев шестерни; K – коэффициент учитывающий изменение нагрузки на зуб шестерни по сравнению с её номинальным значением;
- коэффициент ширины принимается равным 6 10.
Из полученных модулей и выбирают наибольший и округляют его до ближайшего большего стандартного значения: m=10; 15; 20; 25; 30; 40; 50; 60; 80; 100; 130; 160 мм.
Найденный стандартный модуль принимается для всех зубчатых пар данной групповой передачи.
Коэффициент k который учитывает изменение нагрузки по сравнению с номинальной от действия различных факторов определяется по формуле
kд – коэффициент динамичности нагрузки; kд»2
kк – коэффициент концентрации нагрузки; kк»12
kр – коэффициент режима; kр»1.
Результаты расчёта модулей зубчатых колёс представлены в табл.3.
Диаметр делительной окружности определяем по формуле
m – модуль зубчатого колеса; z – число зубьев колеса или шестерни.
Диаметр окружности выступов мм;
Диаметр окружности впадин зубьев мм.
Ширина шестерни определяется по формуле
где а – межцентровое расстояние.
Ширина зубчатого колеса берётся меньше ширины шестерни на 3–5 мм.
Результаты расчёта диаметров колёс представлены в табл.3.
Результаты расчётов модулей и размеров зубчатых колёс
Продолжение таблицы 3
Определяем степень точности зубчатых колёс данной группы исходя из допускаемой окружной скорости. СТ СЭВ 641-77 устанавливает с 1 по12 степени точности зубчатых колёс. В станкостроении используются колёса с 3 по9 степени точности.
В зависимости от того какова окружная скорость зубчатого колеса назначается степень точности в соответствии с данными таблицы 4.
Степени точности зубчатых колёс в зависимости от окружных скоростей.
Прямозубые колёса скорость до мс
Косозубые колёса скорость до мс
Для проектируемого привода окружная скорость зубчатого колеса (шестерни) Z
поэтому назначаем 7-ю степень точности.
Диаметр валов рассчитываем приближённо по формуле
где M=T – крутящий момент равный крутящему моменту на валу Н×м;
– допускаемое напряжение на кручение.
Результаты расчёта диаметров валов.
Определение фактических контактных напряжений и напряжений изгиба зубьев зубчатых колёс привода. Выбор материала и термообработки.
Определим контактные напряжения в зацеплении sн Н по формуле:
Для цилиндрических колёс
где К – вспомогательный коэффициент (для прямозубых колёс К=438); – окружная сила в зацеплении; – коэффициент учитывающий распределение нагрузки между зубьями (для прямозубых колёс );
KHb – аналогичен KFb ;
коэффициент вида цилиндрических колёс.
Определим фактические напряжения изгиба для прямых зубьев шестерни и колеса
где KFa – аналогичен KFb – аналогичен KFu – аналогичен KНV;
YF1 и YF2 – коэффициент формы зуба шестерни и колеса; Yb=1
После определения контактных напряжений и напряжений изгиба подбираем материал и термообработку обеспечивающие прочность на изгиб и износостойкость.
Материал для обоих колёс – Сталь 40Х.
Термообработка: закалка до твёрдости HRCэ 45 50
Материал для обоих колёс – Сталь 18ХГТ.
Термообработка: закалка до твёрдости HRCэ 57 62; сердцевина HRCэ 30 32.
Термообработка: закалка до твёрдости HRCэ 45 50.
Термообработка: закалка до твёрдости HRC 57 62; сердцевина HRCэ 30 32.
Расчётные схемы валов коробки скоростей.
Рис.4 Эпюры и крутящих моментов действующих на вал 1.
Вертикальная плоскость YOZ
а) определим реакции в опорах:
б) строим эпюру изгибающих моментов относительно оси Х:
Горизонтальная плоскость XOZ
Строим эпюру крутящих моментов:
Определим суммарные реакции в опорах:
Определим суммарный изгибающий момент в опасном сечении:
Рис. 5 Эпюры и крутящих моментов действующих на вал II.
Рис. 6 Эпюры и крутящих моментов действующих на вал III.
Рис.7 Эпюры и крутящих моментов действующих на вал IV.
Рис.8 Эпюры и крутящих моментов действующих на вал V.
Проверочный расчёт подшипников
Пригодность подшипников определяется сопоставлением расчётной динамической грузоподъёмности cбазовой т.е..
Расчётная динамическая грузоподъёмность определяется по формуле:
где m-показатель корня для конических роликоподшипников m;
ч для зубчатых передач; – суммарная реакция подшипника; V – коэффициент вращения (V=1); – коэффициент безопасности; – температурный коэффициент ().
Требования к шпинделю станка и его опорам.
Шпиндель является одной из наиболее ответственных деталей станка. От него во многом зависит точность обработки. Поэтому к шпинделю предъявляется ряд повышенных требований. Конструкцию шпинделя определяют: а) требуемая жёсткость расстояние между опорами наличие отверстия (для пропуска материала и для многих других целей); б) конструкция приводных деталей (зубчатые колёса шкивы) и их расположение на шпинделе; в) тип подшипников и посадочные места под них; г) метод крепления патрона для детали или инструмента (определят конструкцию переднего конца шпинделя).
Шпиндели современных станков имеют довольно сложную форму. К ним предъявляются высокие требования по точности изготовления; часто до половины всех проверок на точность проводимых при изготовлении станка приходится на шпиндельный узел. Технические условия на изготовление шпинделей устанавливаются ГОСТом для станков данного класса.
Весьма важным является выбор материала шпинделя. Средненагруженные шпиндели изготавливают обычно из стали 45 с улучшением (закалка с высоким отпуском). При повышенных силовых нагрузках применяют сталь 45 с низким отпуском. Для шпинделей требующих высокой поверхностной твёрдости и вязкой сердцевины применяют сталь45 с закалкой ТВЧ и низким отпуском. При повышенных требованиях применяют легированные стали 40Х 38ХМЮА 38ХВФЮА (шпиндели быстроходных станков) 20Х с цементацией закалкой и отпуском 12ХНЗ (быстроходные и тяжело нагруженные шпиндели) и другие малолегированные стали. Сталь 65Г применяют для крупных шпинделей.
Шпиндель своей зубчатой (шлицевой) частью входит в гильзу коробки скоростей вращаясь вместе с ней перемещается в осевом направлении. В переднем конце шпинделя крепят режущий инструмент либо непосредственно в коническом отверстии либо посредством переходных втулок или других приспособлений.
Значительные осевые нагрузки возникающие при сверлении воспринимаются шариковыми или роликовыми упорными подшипниками смонтированными в шпиндельной гильзе.
Требования предъявляемые к опорам шпинделей
Работа шпинделя зависит от типа его опор. Как известно жёсткость шпиндельного узла его виброустойчивость а также точность вращения связаны с конструкцией опор. В качестве опор шпинделей применяют подшипники качения и подшипники скольжения с жидкостным трением. Иногда оба типа подшипников можно применять с одинаковым успехом. Однако в большинстве случаев условия работы шпинделя определяют и наиболее целесообразный тип подшипника.
К опорам шпинделей предъявляют следующие основные требования.
Высокая точность вращения так как отклонение оси вращения шпинделя непосредственно влияет на точность обработки. Эту точность могут обеспечить подшипники качения и скольжения. Однако и в последнем случае при изменении нагрузки или скорости происходит изменение положения оси вращения шпинделя так как изменяется толщина масляной плёнки.
Опоры шпинделей должны быть долговечны. Подшипники качения имеют ограниченный срок службы и чем выше частота вращения шпинделя тем ниже долговечность подшипников поэтому для скоростных шпинделей повышение сроков службы подшипников является важной задачей. Нормальный срок службы подшипника качения принимается до 5000 ч. Подшипники качения в основном изнашиваются только в период пуска останова или реверса станка поэтому при редких включениях станка они долговечны и могут работать длительное время без ремонта.
Виброустойчивость – важное условие для работы высокооборотных шпинделей. Современные прецизионные подшипники качения отвечают требованию виброустойчивости. Подшипники скольжения обладают способностью гасить колебания т.е. оказывать демпфирующее действие благодаря масляному слою.
Для универсальных станков необходимо чтобы подшипники работали одинаково надёжно во всём диапазоне применяемых скоростей и нагрузок. В этом отношении преимущество подшипников качение неоспоримо чем и объясняется их большое применение в станках.
Эксплуатационные преимущества – лёгкость замены меньший уход и т.п. Подшипники качения в результате эксплуатационных преимуществ получили наибольшие применение для опор шпинделей.
При работе шпинделя в подшипниках качения малая жёсткость внутреннего кольца подшипника приводит к тому что погрешность формы шейки шпинделя почти полностью переходит на дорожки качения. Поэтому допуски на форму и размер шейки шпинделя должны соответствовать допускам прилегающего элемента подшипника.
На основании исходных данных для проектирования выполнены расчёты внешней рабочей нагрузки действующей на привод вертикально-сверлильного станка диапазона регулирования числа скоростей групповых передач и привода в целом что явилось предпосылкой в дальнейшем для кинематического расчёта привода.
Определена структурная формула привода передаточные отношения пар зубчатых колёс групповых передач. Построена рациональная структурная сетка и график частоты вращения найдены частоты вращения промежуточных валов привода и шпинделя станка на основании чего разработана кинематическая схема привода соответствующая исходным данным проекта.
Выполнены расчёты модуля зубчатых колёс и геометрический расчёт элементов кинематической цепи привода главного движения что позволило конструктивно оформить и разработать сборочные чертежи (свертку развёртку) привода предварительно выбрав материал зубчатых колёс и вид термообработки обеспечивающий их высокую износостойкость.
Результаты прочностных расчётов валов зубчатых колёс свидетельствуют о правильности принятых технических решений и достаточной механической прочности и долговечности подобранных подшипников и других деталей привода.
На основе результатов выполнения предшествующих пунктов настоящего заключения разработаны техническая характеристика и технические требования к спроектированному приводу соблюдение которых в процессе производства обеспечит высокую его эксплуатационную надёжность.
Список рекомендуемой литературы.
Бобров В.Ф. Основы теории резания металлов.- М.: Машиностроение 1975.- 344 с.
Ващук И.С. Справочник по расчёту металлорежущих станков.- Красно-
Егоров С.В. Червяков А.Г. Резание конструкционных материалов. –М.:
Машиностроение 1976. - 568 с.
Косилова А.Г. Мещеряков Р.К. Справочник технолога машиностроите-
ля.- М.: Машиностроение -1972.- 568 с.
Металлорежущие станки Под ред. В.К. Тепинкичиева. – М.: Машино
строение 1973.- 472 с.
Нефёдов Н. А. Осипов К. А. Сборник задач и примеров по резанию ме-
таллов и режущему инструменту. – М.: Машиностроение 1976. – 286 с.
Общемашиностроительные нормативы режимов резания для техниче-
ского нормирования работ на металлорежущих станках: В 2 ч. - М.: Машиностроение 1973. – Ч.1. – 416 с.; Ч.2. – 260 с.
Рабинович А. Н. Смиленский В.И. Милевский Э. Б. Коробки скоростей
металлорежущих станков. – Львов 1968. – 376 с.
Обработка металлов резанием: Справ. технолога Под ред. А. А. Панно-
ва. - М.: Машиностроение 1988. – 736 с.
Справочник технолога Под ред. Г.А. Монахова. - М.: Машинострое-
Справочник технолога машиностроителя. Т.2 Под ред. А. Н. Малова.
- М.: Машиностроение 1972. – 568 с.
Точность обработки заготовки и припуски в машиностроении: Справ.
Технолога Под ред. А. Г. Косиловой. - М.: Машиностроение 1976. – 288 с.
Тарзиманов Г. А. Проектирование металлорежущих станков. - М.: Ма-
шиностроение 1980. – 288 с.
Тихомиров Р. А. Николаев В.И. Механическая обработка пластмасс. –
М.: Машиностроение 1975. – 206 с.
Печать 8.cdw

Печать 12.cdw

Технические требования
Отклонение от соосности опор валов не более 30 мкм.
Радиальное биение валов не более:
б) на расстоянии - 0
Осевое биение валов не более 0
Печать 11.cdw

Количество скоростей 12.
Мощность электродвигателя главного движения 15 кВт.
вертикально-сверлильного
Продолжение примера П 3.4
Печать 3.doc
Обоснование технической характеристики привода подач ..12
Кинематический расчёт привода подач . .18
Определение силовых и кинематических параметров привода. .. 25
Определение модуля зубчатых колёс и геометрический расчёт
Определение контактных напряжений и напряжений изгиба зубчатых
колёс привода. Выбор материала и термообработки . . .36
расчётные схемы валов коробки скоростей .. . 42
Проверочный расчёт подшипников .46
Требования к шпинделю станка и его опорам 50
Приложение 1 Графическая часть проекта . . .. 56
Приложение 2 Спецификации . 68
Печать 10.cdw

Наибольшее осевое перемешение шпинделя
Расстояние от конца шпинделя до стола
Частота вращения шпинделя
Число частот вращения шпинделя
Мощность электродвигателя главного движения
Частота вращения вала электродвигателя
П 3.4 Пример выполнения и оформления графической части испецификаций.
Печать 6.doc
Агурский М.С. Экономическая эффективность автоматизации металлорежущих станков. М.; 1968.
Аршинов В.А. Алексеев Г.А. Резание металлов и режущий инструмент. М.; 1975.
Бушуев В.В. Основы проектирования станков. – М. 1992. – 407 с.
Ващук Н.М. Справочник по расчету металлорежущих станков . Красноярск1965.
Воробьева Т.М. Электромагнитные муфты. М.-Л.1960.
Гжиров Р.И. Серебреницкий П.П. Программирование обработки на станках с ЧПУ: Справ. – Л. 1990. – 588 с.
Гидравлическое оборудование. Каталог-справочник. Ч.1 и 2. 1967.
Гусев В.Г. Жарков В.Н. Методическое указание по оформлению технологической дукоментации при выполнении курсовых и дипломных прпоектов. – Владимир 1998. – 56 с.
Данилевский В.В. Технология машиностроения. М. 1972.
Детали и механизмы металлорежущих станков Под ред. Д.Н. Решетова. Т.1 и 2. М. 1972.
Егоров М.Е. Дементьев И.К. Дмитриева В.А. Технология машиностроения. М.1976.
Ермаков В.В. Гидравлический привод металлорежущих станков. М. 1963.
Зазарский Е.М. Жолнерчик С.И. Технология обработки деталей на станках с программным управлением. Л. 1975.
Игумнов Б.Н. Расчет оптимальных режимов обработки для станков и автоматическиских линий. М. 1974.
Кедров С.С. Колебание металлорежущих станков. М.: Машиностроение 1978. 199 с.
Ильичев Д.Д. Системы с электромагнитными муфтами. М.-Л. 1965.
Ковшев А.Н. Технология машиностроения: Учеб. – М. 1987. – 320 с.
Колесов И.Н. Основы технологии машиностроения: Учеб. – М. 1999. – 591 с.
Корсаков В.С. Основы технологии машиностроения. М. 1974.
Кочергин А.И. Конструирование и расчет металлорежущих станков и станочных комплексов. – Минск 1991- 301 с.
Кучер И.М. Металлорежущие станки. Основы конструирования и расчета. Л. 1971.
Левашов А.В. Основы расчета точности кинематических цепей металлорежущих станков. М. 1966. -212 с.
Левина Э.М. Расчет жесткости современных шпиндельных подшипников. Станки и инструменты 1982 №10 с.1-3.
Левина Э.М. Решетова Д.Н. Контактная жесткость машин. М.: Машиностроение 1971. 231 с.
Металлорежущие станки и инструменты: Учебник машиностроительных втузов Под ред. А.С. Проникова. – М.: Машиностроение 1981. 497 с. ил.
Малов А.Н. Справочник технолога-машиностроителя. Т.1 и 2. М. 1970.
Маталин А.А Дашевский Т.Б. Княжицкий И.И.Многооперацион-
a.ные станки. М. 1974.
Миллер Э.Э. техническое нормирование труда в машиностроении. М. 1972.
Монахов Г.А. Станки с программным управлением. Справочник. М. 1975.
Новожилов В.И. Экономика использования металлорежущего оборудования. Л. 1977.
Общемашиностроительные нормативы режимов резания для технического нормирования работ на металлорежущих станках. Ч.1. и 2. М. 1974.
Проников А.С. Расчет и конструирование металлорежущих станков. М. 1967.
Пронин Б.А. Ревков Г.А. Бесступенчатые клиноременные и фрикционные передачи (вариаторы). М. 1967.
Пуш В.Э. Конструирование металлорежущих станков. М. 1977.
Пуш А.В. Шпиндельные узлы: качество и надежность. М.: Машиностроение 1992. 288 с.
Рабинович А.Н. Смилянский В.И. Милевский Э. Коробки скоростей металлорежущих станков.Изд. Львовского университета. 1968 376 с.
Расчетные нагрузки станков. Руководящие материалы. М. ЭНИМС ОТМИ1964.
Свирцевский Ю.И. Макейчик Н.Н. Расчет и конструирование коробок скоростей и подач. Минск 1976.
Спиридонов А.А. Федоров В.Б. Металлорежущие станки с программным управлением. М. 1977.
Справочник технолога-машиностроителя. Т.1 и 2 Под ред. Н.С. Кована. М. 1972.
Режимы резания металлов. Справочник Под ред. Ю.В. Барановского. М. 1972.
Станки с программным управлением. Справочник. М. 1975.
Тарзиманов Г.А. Проектирование металлорежущих станков. М.: Машиностроение. 1980. 242 с.
Фигатнер А.М. Прецизионные подшипники качения современных металлорежущих станков. М.: НИИМАШ 1981. 72 с.
Шаумян Г.А. Комплексная механизация производственных процессов. М. 1973.
Экономическая эффективность станков с числовым программным управлением. Киев 1976.
Обоснование технических характеристик проектируемых приводов 4
Разработка кинематической схемы проектируемого привода .36
Геометрический и силовой расчет привода 56
Описание узла станка 70
Темы курсовых проектов объем и структура расчетно-пояснительной записки 71
Объем и содержание графической части 78
Порядок выполнения и защиты курсового проекта 87
Приложение 1. Табличные данные необходимые для обоснования технических характеристик приводов .89
Приложение 2. Варианты заданий на курсовой проект 113
Приложение 3. Пример выполнения и оформления курсового проекта 121
П 3.1 Оформление титульного листа .121
П 3.2 Оформление содержания проекта 122
П 3.3 Пример выполнения и оформления пояснительной записки 123
П 3.4 Пример выполнения и оформления графической части 156
Список рекомендуемой литературы ..162
Жарков Владимир Николаевич
Морозов Валентин Васильевич
Гусев Владимир Григорьевич
Металлорежущие станки
Учебное пособие для выполнения проекта
Студентам дневного отделения специальности 120100
Компьютерная верстка: Аборкин А.В. Зудилов Р.Н. Анисимов А. А.
ЛР № Подписано в печать
Формат 608416. Бумага для множительной техники. Гарнитура Таймс.
Печать офсетная. Усл. печ. л. Уч.-изд. л. Тираж 200 экз.
Редакционно-издательский комплекс
Владимирского государственного университета.
0000 Владимир Горького 87.
Печать 2.doc
П 3.1 Оформление титульного листа
Министерство образования Российской Федерации
Владимирский государственный университет
по дисциплине «Металлорежущие станки»
Тема: «Спроектировать привод главного движения вертикально-сверлильного станка по типу модели 2Н135»
(фамилия и инициалы)
Принял преподаватель Гусев В. Г.
(фамилия и инициалы)
Печать 9.cdw

Печать 7.cdw

Гнездо для установки инструмента-конус: диаметр 70мм
Наибольший диаметр сверления 75мм
Технические требования
Отклонение от соосности опор шпинделя
Радиальное биение конического отверстия шпинделя
Осевое биение шпинделя не более 0.01мм.
Торцевое биение опорного торца шпинделя не более 0.018мм
Печать 1.doc
Владимирский государственный университет
Кафедра «Технология машиностроения»
МЕТАЛЛОРЕЖУЩИЕ СТАНКИ
Учебное пособие для выполнения
курсового проекта студентами дневного отделения
специальности 120100
доктор технических наук профессор
Печатается по решению редакционно-издательского совета
Владимирского государственного университета
Металлорежущие станки: Учебное пособие для выполнения курсового проекта студентами дневного отделения специальности 120100 Владим. гос. ун-т; Сост.: В.Н. Жарков В.В.Морозов В.Г. Гусев. Владимир 2005
Содержит методические указания по выполнению пояснительной записки графической части и варианты заданий на курсовой проект по дисциплине «Металлорежущие станки». Приводится список рекомендуемой литературы. Дается пример оформления и выполнения курсового проекта.
Предназначены для студентов дневной формы обучения по специальности 120100 – “Технология машиностроения” направление подготовки дипломированного специалиста 130000 – “Машиностроительные технологии и оборудование” в соответствии с Государственным образовательным стандартом профессионального высшего образования 2000 г.
Табл.43.Ил.13.Библиогр.:47 назв.
Выполнение курсового проекта является одним из важнейших этапов подготовки студента к самостоятельной инженерной работе и имеет своей целью:
-закрепить и углубить полученные студентом теоретические знания;
-развить способность студента анализировать и критически оценивать существующие металлорежущие станки с точки зрения современных требований направленных на создание и применение новых и усовершенствование существующих станков и их элементов;
-приобрести навык решать комплексные инженерные задачи имеющие целью разработку наиболее производительного и экономичного оборудования его наиболее рациональных конструкций применительно к конкретным условиям задания;
-показать умение применять полученные теоретические к решению практических задач в области станкостроения;
-показать способность оценивать качество конструкции изделия (узла агрегата станка) с точки зрения его технологичности и технологических условий исходя из назначения и эксплуатации станка;
-показать умение использовать техническую литературу ГОСТы нормативные материалы по проектированию и ЕСКД;
В курсовом проекте на должно быть общих описаний переписанных из книг не допускается также копирование существующих конструкций узлов станков и их элементов без серьезного и целесообразного их изменения.
За принятые в курсовом проекте конструктивные и технологические решения правильность и обоснованность приводимых расчетов оформление чертежей и содержание расчетно-пояснительной записки несет ответственность студент. Подписи руководителя на материалах проекта только удостоверяют что принятые в проекте решения принципиально правильные и соответствуют требованиям предъявляемым к курсовым проектам.
На основании качества курсового проекта соблюдения установленных сроков выполнения уровня его защиты комиссия утвержденная кафедрой ТМС проставляет оценку.
При модернизации или проектировании металлорежущего станка в процессе выполнения курсового проекта наибольшее затруднение для студентов представляют начало проектирования когда в соответствии с заданием обосновывают технические характеристики приводов с целью определения основных черт кинематики и динамики новых узлов модернизируемого или заново планируемого станка.
Несмотря на большое разнообразие типов и конструкций металлорежущих станков имеется общая методика определения обоснования технических характеристик их приводов что позволяет выдавать студентам единое задание по модернизации ил проектированию станков а наличие в работе примеров проектирования разных станков значительно облегчает студенту выполнение данного раздела курсового проекта.
При обосновании технической характеристики того или иного привода станка приходится определять оптимальные условия обработки изделий на станке что связано с использованием большого количества эмпирических формул содержащих еще большее количество различных эмпирических коэффициентов количественные значения которых приведены в таблицах справочников нормативных материалах и монографиях. Сведение воедино в пособии большинства основных вышеупомянутых табличных данных поможет студенту сократить время на их поиск и увеличить время на выполнение творческой работы по расчету и конструированию металлорежущего станка.
ОБОСНОВАНИЕ ТЕХНИЧЕСКОЙ ХАРАКТЕРИСТИКИ ПРОЕКТИРУЕМЫХ ПРИВОДОВ.
1. Исходные данные для обоснования технической характеристики приводов.
Модернизация или проектирование металлорежущего станка как и любой сложной машины всегда начинается с обоснования технической характеристики его приводов так как их определение является исходными данными для кинематического и силового расчета всех элементов проектируемого станка.
Обоснование технической характеристики приводов станка осуществляется в соответствии с техническим заданием (заданием на курсовой проект). В задании указываются сведения определяющие основное направление модернизации основные черты проектируемого станка: название и модель станка или его назначение; материалы обрабатываемых изделий; материалы режущего инструмента; тип привода главного движения и привода подач; серийность производства; число шпинделей и суппортов; система управления станком степень его автоматизации или программирования; особые указания по типу станка и другие сведения.
Название модель станка определяют группу и тип станка его габаритные размеры предельные размеры (диаметр длина ширина высота) обрабатываемых изделий размеры применяемого на станке инструмента и его тип (резец сверло фреза и т. д.). Указание в задании одного или нескольких обрабатываемых материалов позволяет определить степень специализации станка предельную толщину снимаемого материала за один проход оно выражается глубиной резания td. Величина td выбираемая по одному из наиболее трудно обрабатываемых материалов в сочетании с различной подачей определяет в скрытом виде ту максимальную силу резания которая принимается как предельная сила больше которой не должно быть в станке и которая определяет эффективную мощность резания.
В задании на проект станка указывается не марка а материал режущего инструмента (быстрорежущая сталь твердый сплав и т. д.). Марка режущего инструмента в зависимости от обрабатываемого материала и условий резания выбирается проектантом в процессе расчета. Серийность производства определяет степень специализации станка.
Заданное число шпинделей и суппортов определяет проектируемый станок как одношпиндельный многошпиндельный или многорезцовый. В станках токарной фрезерной или строгальной групп при силовом расчете принимается во внимание одновременная работа не всех шпинделей и суппортов а только 23 и их количества считая это наиболее вероятным случаем при тяжелых режимах работы станка.
Кроме рассмотренных выше все другие условия перечисленные в задании на проект станка необходимы лишь для уточнения кинематики конструкции и эксплуатационных качеств проектируемого или модернизируемого станка и не имеют прямого отношения к обоснованию технической характеристики того или другого привода станка. Поэтому указанные условия как второстепенные в дальнейшем не рассматриваются.
Этапы обоснования технической характеристики привода сводится к определению: габаритных предельных размеров обрабатываемого изделия или размеров его обрабатываемых поверхностей; оптимальных режимов обработки; предельных значений частот вращения шпинделя и подач; сил резания и эффективной мощности привода и электродвигателя.
2. Определение предельных габаритных размеров обрабатываемого изделия или размеров его обрабатываемых поверхностей
При модернизации металлорежущих станков из его паспортных данных и технической характеристики конструктору известны основные размеры станка например высота центров и расстояние между центрами токарного станка номер стола и следовательно размеры рабочей поверхности стола фрезерного станка максимальный диаметр обрабатываемого отверстия сверлильного станка наибольший модуль диаметр обрабатываемых шестерен для зубофрезерного станка и т. д. Исходя из этих данных определяют предельные габаритные размеры изделий которые можно обрабатывать на данном станке. На станке с высотой центров например H = 300мм можно закрепить и обрабатывать изделие диаметром равным двойной высоте центров т. е. = 600 мм и в то же время можно закрепить заготовку диаметром = 3 5 мм. Однако ясно что изделие очень большого диаметра с трудом устанавливаемое на станке и не помещающееся над суппортом лучше обрабатывать на станке большого размера а изделие очень малых диаметров - на меньших станках так как обработка их потребует очень больших для данного станка частот вращения шпинделя а мощность станка будет слабо использоваться. Наибольший и наименьший размеры обрабатываемых изделий или размеры обработки в (мм) можно установить по следующим практическим формулам:
Для токарных станков:
где Dd - наибольший диаметр обрабатываемого изделия над станиной; Dм - наименьший диаметр обрабатываемого изделия над станиной; H - высота центров.
Для сверлильных станков наибольший размер обрабатываемого отверстия как правило соответствует двум последним цифрам в шифре модели станка например у модели 2А135 максимальный размер обрабатываемого отверстия равен 35 мм у модели 2А150-50 мм. Минимальный размер обрабатываемого отверстия определяют как
Dм = (015 03) Dd (3)
где Dd Dм - наименьший и наибольший диаметр сверления.
Для фрезерных станков:
где Dd Dм- наибольший и наименьший диаметр фрезы; b - ширина рабочего стола.
где Bd Bм - наибольшая и наименьшая ширина фрезерования.
Размеры рабочей поверхности стола фрезерного станка с их номерами (номер - последняя цифра шифра модели станка) представлены в табл.1 приложения.
Примечание. Все таблицы пособия сведены в приложение.
Для зубофрезерных станков:
где mм и md - наименьший и наибольший нарезаемые модули шестерен.
На основании наименьшего и наибольшего нарезаемых модулей находят предельные значения диаметров червячных фрез в соответствии с табл.2. Предельные значения чисел зубьев шестерен большей частью можно принять Zd = 16 Zм = 100.
Для строгальных станков мм:
где L - длина стола; b - ширина стола; H - высота стола.
3. Расчет рациональных режимов обработки
Оптимальный режим обработки должен обеспечивать наибольшую производительность и наименьшую себестоимость изготовления при непременном условии получения требуемого качества обрабатываемой детали. Установление оптимального режима обработки заключается в определении характеристики режущего инструмента и ряда параметров режимов резания.
При выборе характеристик режущего инструмента на проектируемый станок следует учитывать: тип инструмента и его геометрические параметры размеры сечения стержней и державок материал режущей части и его вид обработки (черновая или чистовая) жесткость системы «Станок- деталь – инструмент» и другие условия резания.
Эти данные определяются исходя из типа станка его размеров габаритных предельных размеров обрабатываемых изделий и обрабатываемых поверхностей обрабатываемого материала для определения используются соответствующие справочники и ГОСТы. При проектировании универсальных станков должны быть выявлены все инструменты которые применяются на нем. Если станок специальный или специализированный то выбор инструмента определяется выполненными на нем операциями.
Металлорежущие станки особенно станки общего назначения должны обеспечивать применение скоростей резания и подач в широком диапазоне с целью получения наивыгоднейших режимов резания при выполнении разнообразных операций. Обычно оптимально предельные режимы устанавливают в следующей последовательности: устанавливают предельные значения припусков (глубины резания) td и tм определяют предельные значения подач Sd и Sм по известным t и S задавшись периодом стойкости инструмента определяют предельные значения скоростей резания Vd и Vм.
3.1. Расчет предельных значений припусков
(глубины резания) на обработку
Наибольший td и наименьший tм припуски (глубину резания) на обработку которые могут встретиться при обработке на данном станке находят по предельным размерам обработки.
Для токарных станков. Наибольший припуск на обработку равен
Числовые значения коэффициента Ct приведены в табл. 3. Наименьший припуск на обработку определяется по формуле
tм = 07+0025 D+00001 L. (13)
При черновой обработке глубина резания принимается равной припуску. При получистовой обработке и припуске на сторону t > 2 мм обработка осуществляется за два прохода: первый с t = (23 34) t а второй – с t = (13 14) t. При t 2 мм получистовая обработка производится за один проход. Для универсальных токарных и расточных станков средних размеров предельные расчетные значения глубины резания могут быть приняты 02 и 35 мм для крупных токарных и карусельных станков - 1 и 10 мм для малых токарных и расточных станков повышенной точности - 005 и 2 мм. При чистовой обработке с шероховатостью поверхности до 5-го класса включительно t = 05 - 20 мм; для 6-го и 7-го классов t = 01 - 04 мм.
Для сверлильных станков. При сверлении в сплошном материале глубина резания равна
где d - диаметр рассверленного отверстия мм.
Наибольший диаметр сверления Dd для универсальных вертикально - и радиально-сверлильных станков является их основным параметром и должен соответствовать ГОСТ 1227-72. При зенкеровании и развертывании глубина резания обычно равна величине припуска на сторону - 05-2 мм. При чистовом развертывании отверстий диаметром 5-80 мм припуск на сторону - 005-025 мм. При черновом развертывании припуск на сторону может быть увеличен в 2-3 раза.
Для фрезерных станков. Величину припуска на обработку при фрезеровании определяют по табл.4. и табл.5. По найденным величинам находят наибольшую и наименьшую глубину резания td и tм. При обдирочных работах припуск снимается за один проход и глубина резания может достигать например при фрезеровании цилиндрическими фрезами 15-30 мм при условии что td 01D где D- диаметр цилиндрической фрезы в мм. При получистовом фрезеровании фрезами из быстрорежущей стали припуск больше 5 мм снимается за 2 прохода а фрезами с твердосплавными пластинками – за один проход. Получистовое фрезерование при величине припуска меньше 5 мм осуществляют за один проход. Под чистовое фрезерование припуск оставляется небольшой порядка 05-25 мм и снимают его как правило за один проход. Наибольшую глубину резания при чистовом фрезеровании можно принимать в пределах 05-1 мм.
Для шлифовальных станков. При работе на кругло - внутри- и бесцентровом шлифовальных станках объем снимаемого в единицу времени металла определяется скоростью вращения заготовки Vз поперечной и продольной подачами.
Поперечная подача (глубина шлифования) определяется припуском на обработку требуемой точностью и шероховатостью обрабатываемой поверхности и выбирается в следующих пределах:
а) при круглом наружном шлифовании:
-с продольной подачей ( при черновом) - 0015-005 ммдв. ход стола и чистовом - 0005-001 ммдв.ход стола;
-врезанием (при черновом) 00025-0075 ммоб и чистовом - 0001-0005 ммоб.
б) при бесцентровом шлифовании:
-на проход (предварительном) 005-02 ммоб чистовом - 0005-002 ммоб;
-врезанием (предварительном) 0002-001 ммоб чистовом - 0002-0005 ммоб.
В плоскошлифовальных станках глубина шлифования представляет собой вертикальную подачу стола или шлифовальной бабки. Она составляет:
-при плоском шлифовании периферией круга (предварительном) 0015-004 мм чистовом - 0005-0015 мм;
-при плоском шлифовании торцом круга (предварительном) 0015-004 мм чистовом - 0005-001 мм.
Для зубообрабатывающих станков. Черновую обработку осуществляют за один проход. Когда мощность станка или жесткость системы недостаточны припуск на черновую обработку срезают за два прохода с глубиной резания 14 m при первом черновом проходе и 07 m при втором. Черновую обработку в два прохода применяют только при долблении зубьев цилиндрических колес дисковыми долбяками для получения шероховатости поверхности не ниже 6-го класса и точности не ниже 7-й степени при модуле 6 мм и выше.
Для строгальных станков. Для грубого строгания td принимается равной припуску но не более 15 мм. Для tм принимают припуск на чистовую обработку который обычно равен 075-15 мм.
Глубину резания при черновом и чистовом строгании можно назначить руководствуясь теми же соображениями что и при точении на токарных станках.
3.2. Расчет предельных значений величин подач
Для дальнейших расчетов режимов резания необходимо учитывать материал заготовки его физико-механические свойства величину припуска на обработку размеры детали и технические условия на ее обработку а так же иметь сведения о точности и жесткости металлорежущих станков которые модно получить в ГОСТ 2110-72 ГОСТ 26-75 ГОСТ 8-71.
При проектном расчете режимов резания для универсальных станков в качестве исходного материала обрабатываемых деталей следует выбирать малоуглеродистую сталь HB 170 dв 600 МПа (при определение Vd) и высокопрочную легированную сталь HB ³ 170 dв ³ 600 МПа (при определении Vм) при этом следует помнить что dв » 036 размеры заготовки (в виде поковки или проката) - максимально допустимые на проектируемый станок; припуски на механическую обработку выбираются по справочникам [6 11 12 14]. При выборе в качестве исходного обрабатываемого материала жаропрочных нержавеющих сталей и сплавов неметаллических материалов следует учитывать коэффициенты их обрабатываемости оптимально допустимые скорости резания и подачи которые можно найти в работе [13].
Наибольшие и наименьшие значения величин подач находят по допустимой шероховатости обрабатываемой поверхности.
Для токарных станков величины подач можно приблизительно находить по следующим формулам ммоб
-при черновой обработке:
Sd = 017 D+(td-2) 015; (16)
-при чистовой обработке
Максимальное расчетное значение подачи выбирается для условий черновой обработки при наибольшей жесткости заготовки; при этом заготовка считается закрепленной в патроне и поддерживаемой задним центром. Максимальное расчетное значение подачи выбирается для условий чистовой обработки при наименьшей жесткости заготовки и закрепления в ее патроне. Для более точного определения наименьшей подачи можно воспользоваться следующей формулой ммоб
Sм = (СмRr)(t). (18)
Значения См и показатели степени xyz и u приведены в табл.6. Придельные значения величин подач могут быть выбраны и по табл.7-10.
Для сверлильных станков. Подача при сверлении в сплошном материале и зенкеровании назначается по формуле ммоб
При развертывании - по формуле
Значения Сs приведены в табл.11.
Наибольшую подачу Sd следует определять при наибольшем диаметре Dсверления зенкерования развертывания отверстий в деталях из цветных металлов и сплавов для которых Сd имеет наибольшее значение. Подачи при сверлении принимают в 15-2 раза большими чем при сверлении.
Наименьшая подача Sм соответствует сверлению зенкерованию и развертыванию отверстий минимального диаметра Dм в стальной заготовке имеющей твердость HB > 240. В этом случае коэффициент Cs имеет наименьшее значение. Максимально допустимые подачи при сверлении зенкеровании и развертывании приведены в табл.12.
Для фрезерных станков наибольшую Szd и наименьшую Szм подачи на зуб фрезы можно брать по табл. 13 и табл.14 из условия шероховатости обрабатываемой поверхности при обработке самого мягкого материала.
Определяют так же по таблицам режимов резания Szd и Szм при обработке самого твердого материала. При черновой обработке наибольшая подача ограничивается прочностью и жесткостью оправки фрезы жесткостью технологической системы и прочностью режущей поверхности зуба фрезы.
При чистовом фрезеровании выбор подачи определяется требуемым качеством обработанной поверхности. При чистовом фрезеровании подачу на один зуб фрезы можно определять по формуле ммзуб
где Cs - коэффициент зависящий от материала обрабатываемой детали и типа фрезы; D - диаметр фрезы мм; t - глубина резания мм; R - высота микро неровностей мм; xyz - показатели степени.
Значения Cs и торцевые фрезы - 003-04 ммзуб; фасонные фрезы - 0007-02 ммзуб.
Для шлифовальных станков величина продольной подачи (в плоско- шлифовальных - поперечной) зависит от ширины шлифовального круга и принимается при чистом шлифовании равной 02-04 а при черновом - 04-07 ширины круга.
Поперечная подача является припуском и определяется как глубина резания определение которой рассмотрено выше. Круговая подача или скорость вращения заготовки (в плоскошлифовальных станках - продольная подача) изменяется в более широких пределах. В зависимости от вида шлифования ее можно рассчитать по формулам:
-шлифование периферией круга (наружное внутреннее плоское) ммин
-шлифование торцом круга ммин
-бесцентровое наружное шлифование ммин
где Сv - коэффициент учитывающий свойства материала заготовки вид шлифования и характеристику круга; Dз - диаметр заготовки мм; T-стойкость мин; t - глубина шлифования или поперечная подача мм; Sд - продольная подача в долях ширины круга на один оборот заготовки; S0 - продольная подача на один оборот детали мм; b - приведенная (сплошная) ширина шлифования мм; rmxyz - показатели степени зависящие от вида шлифования характеристики круга и материала заготовки.
Значения Сv и rm материал заготовки - незакаленная сталь; диаметр шлифуемой заготовки - наибольший; стойкость круга- экономическая (Т = 3-15 мин); глубина шлифования (поперечная подача) и продольная подача принимаются минимальными из условия получения наименее шероховатой поверхности.
При расчете наименьшей скорости заготовки Vм нужно исходить из следующих условий обработки: характер обработки - черновое шлифование; материал заготовки- наименьший; стойкость круга - экономическая (Т = 3-15 мин); глубина шлифования и продольная подача принимаются максимальной для условия чернового шлифования.
Для зубообрабатывающих станков предельные значения подач на один оборот заготовки выбирают в зависимости от модуля обрабатываемого материала и числа зубьев по табл. 17. Рекомендуемые величины подач при нарезании цилиндрических зубчатых колес на среднеуглеродистой конструкционной стали червячными и дисковыми фрезами и зуборезными долбяками приведены в табл. 18-20. а при нарезании шлицевых валов червячными фрезами - в табл. 21. Поправочные коэффициенты на подачу при изготовлении зубчатых колес и шлицевых валов из углеродистой и легированной сталей приведены в табл. 22. Рекомендуемые величины подач при нарезании червячных колес червячными фрезами приведены в табл. 23.
Наибольшая подача Sб характерна для самого мягкого материала когда шестерня будет иметь наибольшее число зубьев и наименьший модуль. Однако так как наибольшая подача нужна нам для определения наименьшей скорости резания и наибольшей мощности следует определить и самую большую подачу Sб при обработке твердого материала когда шестерня имеет наибольшее число зубьев и наименьший модуль.
Наименьшая подача Sм должна определить самую большую скорость резания поэтому выбирают ее для самого мягкого обрабатываемого материала. наименьшего числа зубьев и модуля.
Для строгальных станков выбирают наибольшую Sб и наименьшую Sм подачи для самого мягкого обрабатываемого материала а так же наибольшую Sб и наименьшую Sм подачи для самого твердого обрабатываемого материала. При черновой обработке плоскостей величину подачи S в ммдв. ход выбирают по максимальному значению из табл. 7 для точения в зависимости от сечения державки и глубины резания; при чистовой обработке - из табл. 10.
3.3. Расчет предельных скоростей резания
Следующий этап обоснования технической характеристики привода станка - отыскание наибольшей и наименьшей скоростей резания.
Для токарных станков скорость резания будет иметь максимальное значение при снятии стружки наименьших размеров с наименьшей подачей и наименьшей глубиной резания при обработке наиболее мягкого материала. При отыскании наименьшей скорости резания- при снятии максимальной стружки и обработке твердого материала. В зависимости от вида выполняемых работ предельные значения скоростей резания могут быть определены по формулам
- при точении и растачивании ммин
V= СvT t S(HB200) (25)
- при прорезке канавок и отрезке ммин
V= СvT S(HB200). (26)
Значения коэффициента Сv и показателей степеней приведены в табл. 24 при этом определяя Vб принимают для резцов с твердым сплавом типа ТК наименьшую стойкость Т = 25-30 мин а при поре делении Vм для резцов из быстрорежущей стали и твердого сплава- Т = 60-90 мин.
При проектных расчетах предельной скорости резания Vб станков предназначенных для тонкой обработки деталей из баббита алюминия латуни бронзы и неметаллических материалов следует ориентироваться на скорости резания 900-3000 ммин.
При определении скорости резания для операций сверления рассверления зенкерования и развертывания выполняемых на токарных станках используют формулы применяемые при отыскании данных параметров для сверлильных станков.
При нарезании резьб на токарных резьбонарезных и других станках резцами метчиками плашками и самооткрывающимися головками предельные значения скорости резания Vб могут быть определены по формулам:
- при черновой обработке резцами резьбовыми стержневыми призматическими и круглыми на инструментальной стали марки Р(8) в изделиях из углеродистой или легированной сталей с использованием в качестве охлаждающей жидкости сульфофрезола ммин
при в 600Мпа Сv = 40-50 при ³ 600Мпа Сv = 20-38; (Т = 120 мин); Т - средняя стойкость инструмента; t - глубина резания или поперечная подача на каждый проход резца мм; S - шаг резьбы мм;
- при чистовой обработке и указанных выше условиях резьбонарезания ммин
- при обработке машинными метчиками из стали P6M5 в изделиях из стали марки 45 с использованием сульфофрезола при стойкости инструмента Т = 190 мин ммин
- при обработке круглыми плашками из стали У12А в изделиях из стали 45 с применением в качестве смазывающе-охлаждающей жидкости эмульсии при стойкости инструмента Т=190 мин ммин
- при обработке резьбовыми гребенчатыми фрезами из стали Р6М5 в изделиях из стали 45 с применением эмульсии при стойкости инструмента Т = 180 мин ммин
Для сверлильных станков предельные расчетные значения Vб и Vм определяются по формулам ммин
- при сверлении деталей из стали с НВ 155
V = Cv D(HB) T S; (32)
- при сверлении деталей из стали с НВ > 155
V = Cv D T S (HB); (33)
- при рассверливании деталей из стали с НВ 155
V = Cv D(HB) T S t; (34)
- при рассверливании деталей из стали с НВ > 155
V = Cv D T t S (HB); (35)
- при зенкеровании деталей из стали с НВ 155
V = Cv D(HB) T t S; (36)
- при зенкеровании деталей из стали с НВ > 155;
V=Cv D T t S (HB); (37)
- при развертывании деталей из стали с НВ 155
V=Cv D(HB)T t S; (38)
- при развертывании деталей из стали с НВ > 155
V=Cv D T t S (HB); (39)
Значения Сv и xyzmn приведены в табл. 25.
При определении наибольшей скорости резания Ud следует принимать: диаметр инструмента наименьшим; глубину резания и подачу наименьшими; материал заготовки- малоуглеродистая сталь 750 МПа (НВ155); материал режущей части инструмента - быстрорежущая сталь с наименьшей стойкостью Т = 7-20 мин в зависимости от диаметра инструмента.
При определении наименьшей скорости резания Vм принимают: диаметр инструмента наибольшим; глубину резания и подачу наименьшими; материал заготовки - сталь с в ³ 750 МПа (НВ³155); материал режущей части инструмента - легированная или углеродистая сталь (ЭХС У12А) для которых скорость резания составляют 03-05 от скорости резания для инструментов из быстрорежущей стали.
Для фрезерных станков предельные расчетные значения скорости резания Vв и Vм определяют по формуле ммин
V = Cv D T t S zB. (40)
Значения Сv и xyzmnq принимаются в табл. 26.
При определении наибольшей скорости Vб следует принимать: материал обрабатываемой детали - сталь с в 750 МПа а материал режущей части инструмента - твердый сплав Т15К6; диаметр фрезы стойкость а так же глубину резания и подачу на один зуб фрезы (для чистового фрезерования) - минимальными; ширину фрезерования – наименьшей но такой чтобы обеспечивалось равномерное фрезерование.
При фрезеровании цилиндрическими фрезами с винтовыми зубьями последнее условие выполняется в том случае когда ширина фрезерования В равна осевому шагу фрезы tос или кратна ему а при фрезеровании торцовыми фрезами - когда в процессе резания участвуют не менее двух зубьев одновременно. При симметричном расположении фрезы относительно обрабатываемой детали последнее условие соблюдается при
В ³ D sin 360°z. (41)
При определении наименьшей скорости резания Vм принимают: материал режущей части фрезы - быстрорежущая сталь; диаметр фрезы и стойкость - наибольшие; глубина резания и подача на один зуб фрезы - наибольшие при черновом фрезеровании; ширину фрезерования: для горизонтально- фрезерных станков - при работе сдвоенными цилиндрическими фрезами максимального диаметра; для вертикально-фрезерных станков – на 10-20 мм меньше диаметра фрезы.
Для шлифовальных станков. Для обеспечения наибольшей производительности и уменьшения шероховатости поверхности или минимальном износе кругов частоту вращения шлифовального круга выбирают по возможности наибольшую допускаемую его прочностью зависящей от связки и профиля круга.
Рабочие окружные скорости абразивного инструмента допускаемые его прочностью следует выбирать в соответствии с ГОСТ 4785-64 в следующих пределах: для кругов на керамической связке 25-35 мс; для кругов на бакелитовой связке 30-35 мс; при скорости шлифовании для кругов на специальной высокопрочной керамической связке 50-65 мс и для кругов на бакелитовой связке- 50 мс; при обдирочных работах окружные скорости кругов обычно не превышают 15-20 мс.
Для зубообрабатывающих станков при нарезании зубчатых колес червячными и дисковыми фрезами а также зуборезными долбяками предельные значения скорости резания будут: наибольшая - при чистовой обработке самого мягкого материала по формуле ммин
V = ( CvT S m) Kv (42)
Наименьшая - при обработке самого твердого материала по такой же формуле. При фрезеровании шлицевых валов червячными шлицевыми фрезами - по формуле ммин
V = (Cv UT S h) Kv (43)
где Т - среднее значение периода стойкости мин; S - подача для червячных модульных и шлицевых фрез в мм на один оборот заготовки; для долбяков круговая подача в мм на двойной ход; для дисковых модульных фрез S = Sz в мм на один зуб фрезы; h - высота шлицев мм; m - модуль нарезаемого колеса мм; U - число шлицев шлицевого валика; Кv - общий коэффициент представляющий собой произведение из ряда поправочных коэффициентов учитывающих конкретные условия резания (табл. 28-29); Сv x y m q - коэффициенты и показатели степени приведенные в табл. 27.
Для строгальных станков наибольшая скорость резания определяется по формулам для точения при наименьшей глубине наибольшей подаче и самом мягком материале а наименьшая скорость резания - при наибольшей глубине и наименьшей подаче для самого твердого материала.
При строгании плоскостей проходными резцами при прорезании пазов и отрезании скорость резания рассчитывают по соответствующим формулам для точения с введением дополнительного поправочного коэффициента К (табл. 30) учитывающий ударную нагрузку.
При долблении или строгании на поперечно-строгальных станках скорость резания может быть определена как ммин
V = Сv T t S (HB200); (44)
где Cv = 432 m = 01; y = 05; n = 151 - при обработке инструментом из быстрорежущей стали и Сv = 267;
m = 0125; y = 035; n = 1 - при обработке инструментом оснащенным пластинкой твердого сплава.
Учитывая что период морального износа станков составляет 10-15 лет а технический прогресс в области режущего инструмента происходит непрерывно при проектировании новых станков необходимо обеспечивать достаточные резервы повышения режимов обработки в особенности скорости резания (табл. 31).
3.4. Расчет предельных значений частот вращений
(частот двойных ходов) рабочего органа
На основании определенных оптимальных режимов обработки заданных деталей различных габаритов и из разных материалов определяют предельные значения частот вращения шпинделя (числа двойных ходов) и выбирают величины подач а по найденным значениям определяют диапазоны регулирования привода главного движения и привода подач.
При определение максимальных и минимальных частот вращений шпинделя станка предполагают что работа с наибольшей скоростью Vб может производиться при обработке изделий наименьших размеров (диаметров) а работа с наименьшей скоростью Vм - при обработке изделий наименьших диаметров мин-1
nб = 1000 Vбp Dм; (45)
nм = 1000 Vмp Dб. (46)
Для приводов главного движения станков имеющих прямолинейное возвратно - поступательное движение максимальные и минимальные числа двойных ходов определяются по формулам дв.хмин
nб = (1000 VрбLnм) [k(k+1)]; (47)
nм = (1000 VрмLnб) [k(k+1)]; (48)
где Vрб и Vрм - наибольшее и наименьшее значение рабочей скорости ползуна принимаются равными максимальному и минимальному значению скорости резания;
Lnб и Lnм - наибольшая и наименьшая длина хода ползуна:
Lnб = (14-16) Lnм =
Lб и k - коэффициент
Зная предельные значения частот вращения шпинделя (величины двойных ходов) величин подач находят диапазон регулирования привода
4. Расчет силовых параметров процесса резания
Силу резания возникающую в процессе обработки рассчитывают для двух предельных значений.
Первый расчет необходим для последующих расчетов максимальных крутящих моментов а так же для последующих расчетов зубчатых колес валов шпинделей подшипников муфт и т. д. Второй расчет усилия резания необходим для определения эффективной мощности резания и максимальной мощности станка (привода).
Наибольшее усилие резания в процессе обработки изделия будет действовать при снятии наибольшей стружки (tб Sб) при обработке самого твердого материала. Сила резания или составляющие силы резания определяются по формулам приведенным ниже в зависимости от типа станка и выполняемых операций.
Для токарных и строгальных станков:
- при точении растачивании строгании кН
Pz = C1 t S (HB); (51)
Py = C2 t S (HB); (52)
- при отрезке и прорезке резцами кН
Pz = C4 t S (HB); (54)
Py = C5 t S (HB). (55)
Значения С Py - отжим резца от детали и величину ее прогиба; Px - нагрузку в цепи механизма подачи.
Наибольшие значения Pzб Pyб P глубина резания и подача наибольшие; материал режущей части резца - быстрорежущая сталь или твердый сплав с наименьшей стойкостью(15-30 мин).
При нарезании резьб на токарных резьбонарезных и других станках крутящий момент М определяется по формулам:
- для машинных метчиков при обработке стали 45 с применением смазочно-охлаждающей жидкости - сульфофрезола кН м
- для круглой плашки и тех же условий обработки кН м
- для самооткрывающейся резьбонарезной головки и тех же условий обработки кН м
Для сверлильных станков:
М = C2 DS (HB); (60)
- при рассверливании
М = C4 D tS (HB); (62)
Значения С материал режущей части инструмента - быстрорежущая сталь с наименьшей стойкостью; диаметр инструмента и подача - наибольшие.
Для фрезерных станков:
- при цилиндрическом фрезеровании кН
- при фрезеровании торцевыми дисковыми и отрезными фрезами кН
- при фрезеровании фасонными и угловыми фрезами кН
Значения С x y z n принимаются по табл. 32.
Наибольшие значения окружной силы резания определяются при следующих условиях: материал обрабатываемой детали - сталь средней твердости; материал режущей части фрезы при цилиндрическом фрезеровании - быстрорежущая сталь; при торцевом - твердый сплав; глубина фрезерования и подача на зуб фрезы - наибольшие; ширина фрезерования - такая же как и при определении Vм; диаметр фрезы - наибольший а ее стойкость - наименьшая.
Для круглошлифовальных станков сила Рz при наружном круглом шлифовании может быть определена по формуле Н
5 Расчет эффективной мощности привода и мощности электродвигателя.
Максимальная мощность потребная на резание как известно из теории резания металлов будет при отделении стружки наибольшего сечения и при обработке наиболее мягкого материала.
Для токарных станков. Эффективная наибольшая мощность привода потребная для точения определяется по формуле кВт
где Рzб - наибольшая сила резания кН; V - скорость резания ммин определяемая при тех же условиях при которых определялось значение Рzб.
Для сверлильных станков:
где Мб - величина наибольшего крутящего момента при сверлении кН*м; V - скорость резания определяемая для условий получения наибольшего значения Мб ммин; D - диаметр сверла мм;
- при зенкеровании и развертывании кВт
где n - частота вращения шпинделя соответствующая условиям получения наибольшего значения Мб обмин.
Для фрезерных станков. В общем случае эффективная мощность при фрезеровании определяется по формуле кВт
Nэ = Рzб V612 . (70)
Для фрез цилиндрических конических дисковых прорезных из быстрорежущей стали при обработке конструкционной стали НВ = 235 (в = 750 МПа) кВт
Nэ= 3510t086 SB z n D. (71)
При обработке торцевыми твердосплавными фрезами серого чугуна с НВ = 190 кВт
Nэ= 2810tSB z D. (72)
Для шлифовальных станков. Эффективная мощность привода шлифовального круга подсчитывается по формулам: при шлифовании периферией круга кВт
- при шлифовании торцем круга кВт
где Cм - коэффициент учитывающий вид шлифования и характеристику круга; Vз - скорость вращения заготовки (в плоско-шлифовальных станках - продольная подача) ммин; t - глубина шлифования или поперечная подача мм; В - приведенная ширина шлифования мм; D - диаметр заготовки мм; S0 - продольная подача на один оборот детали ммоб; x y z q s –показатели степени зависящие от вида шлифования характера круга.
Числовые значения коэффициента Cм и показателей степени x y z q при проектных расчетах эффективной мощности могут быть взяты из табл. 33.
При нарезании резьбы (на различных станках) мощность определяется кВт
где М - крутящий момент создаваемый при резьбонарезании кНм; V- скорость нарезания резьбы ммин; d - диаметр нарезаемой резьбы мм.
При зубонарезании. При фрезеровании однозаходной червячной фрезой зубьев колес из стали эффективная мощность определяется по формуле кВт
где S0 - подача на один оборот нарезаемого колеса ммоб; m - модуль мм; D - диаметр фрезы.
При работе долбяками эффективная мощность определяется как кВт
Nэ = Рб Vср 612° (77)
где Рб - максимальная сила резания при работе долбяками кН; Vср - средняя скорость возвратно-поступательного движения долбяка ммин.
Для строгальных станков и долбежных. Эффективная мощность определяется по формуле кВт
Nэ = Рz Vср 7560136 (78)
где Рz - сила резания при строгании долблении кН; Vср - скорость резания при строгании долблении ммин (V = p×Dn 1000 обмин); n - частота вращения шестерни ведущей стол.
Мощность электродвигателя главного движения Nд определяется по наибольшей эффективной мощности резания кВт
где k - коэффициент перегрузки станка k » 12-13; h - к.п.д. привода главного движения; h = 076-085.
При предварительных расчетах можно принимать: для станков с вращательным главным движением h = 070-085; для станков с возвратно- поступательным главным движением h = 06-07.
Если в проектируемом или модернизируемом станке предусматривается только один электродвигатель то при определении его мощности должна быть учтена мощность расходуемая в цепях привода подач и вспомогательных движений. Мощность потребная на подачу обычно не велика и составляет от мощности главного привода для токарных и револьверных станков 3 4%; для сверлильных 4 5%; для фрезерных 15 20%.
При осуществлении подачи и других движений станка от отдельных электродвигателей их потребная мощность Nn подсчитывается отдельно для каждой кинематической цепи по формуле кВт
где hn- к.п.д. цепи привода подачи h = 015 02; Nэ - потребная мощность равная кВт
Nэ = QS 10260100 (81)
где Q - тяговая сила подачи Н; S - величина подачи мммин.
Тяговую силу подачи Q можно определять по формулам:
- для продольных суппортов токарных станков с призматическими или комбинированными направляющими
- для продольных суппортов токарных и револьверных станков и столов фрезерных станков с прямоугольными направляющими
- для столов фрезерных станков с направляющими в форме ласточкина хвоста
- для шпинделей сверлильных станков
Q = (1+05 ¦)Px+2М ¦ D » Px+2М ¦ D (85)
где P Pz - составляющая силы резания прижимающая каретку суппорта или стола к направляющим Н; G - масса перемещаемых частей Н; М - крутящий момент на шпинделе Нмм; D - диаметр шпинделя мм; ¦ - коэффициент трения между пинолью и корпусом и на шлицах или шпонках шпинделя; ¦- приведенный коэффициент трения на направляющих; k - коэффициент учитывающий влияние опрокидывающего момента.
Значения коэффициентов k и ¦ при нормальных условиях смазки направляющих неодинаково: для токарных станков с призматическими или комбинированными направляющими ¦ = 015 018 k = 115; для токарных и револьверных станков с прямоугольными направляющими ¦ = 015 k = 11; для столов фрезерных станков ¦ = 02 k = 04; для пинолей сверлильных станков ¦ = 015.
6 Особенности определения режимов резания для многоинструментной обработки
При выборе режимов резания для многоинструментной обработки следует исходить из условия установления периодов стойкости инструментов обеспечивающих экономическую рентабельность режима работы проектируемого станка т. е. из условий наибольшей производительности или наименьшей стоимости обработки.
При этом надо учитывать следующие особенности:
Производительность и экономичность обработки определяется не только режимом резания но и в значительной степени зависит от принятого варианта операционной технологии (выбора типов инструмента их количества расположения и т. д.)
Для отдельных инструментов подачи связаны определенными соотношениями например подача для всех резцов закрепленных в одном суппорте должна быть одинакова.
Период стойкости инструмента должен быть более высоким чем для одно-инструментной обработки во избежание простоев станка из- за переналадки и смены затупившегося инструмента. Чем большее число инструментов одновременно участвует в работе тем больше должен быть период стойкости например при одновременной работе десяти резцов их стойкости должна составлять в среднем 180 мин двадцати- 260 мин.
Скорость резания обычно меньше чем при одноинструментной обработке из-за больших значений периода стойкости инструментов. Для токарных автоматов и полуавтоматов последовательность установления режимов резания в общем случае принимается следующая.
Разрабатывают наладку. Наладка определяет возможный тип инструментов их количество длины хода максимальный и минимальный припуски на обработку. При выборе оптимального варианта наладки исходят из условий обеспечения возможно меньшего штучного времени при экономической стойкости инструмента. Геометрические параметры режущего инструмента выбирают как и для одноинструментной наладки в соответствии с ГОСТ.
Определяют предельные расчетные значения подачи Sб и Sм отдельно для каждого инструмента исходя из условий одноинструментной обработки. Основными факторами ограничивающими подачу являются: жесткость заготовки требуемая точность обработки шероховатость обработанной поверхности прочность и жесткость инструмента суммарная сила подачи. По выбранным для каждого инструмента подачам Sб и Sм определяют подачи для каждого суппорта и инструментального шпинделя. Эти подачи принимают равными наименьшим подачам Sбм и Sбм. Наименьшую подачу Sбм при черновой обработке имеет наиболее нагруженный инструмент (работающий с большой глубиной резания) наименьшую подачу Sбм при чистовой обработке имеет инструмент обрабатывающий поверхность более высокого класса шероховатости.
При выборе подачи следует иметь в виду:
а) при работе нескольких суппортов их подачи должны быть увязаны с продолжительностью работы каждого из них: это делают с целью достижения одинаковой стойкости инструмента без уменьшения машинного времени для суппортов работающих более короткое время;
б) суммарная сила подачи должна быть проверена по допустимой прочности механизма подач станка.
Подача для обычных резцов принимается в 2-3 раза меньшей чем при одноинструментной обработке. Максимальная подача фасонных резцов ограничивается следующими пределами: для многошпиндельных автоматов- 01 02 ммоб одношпиндельных автоматов - 008 002 ммоб.
Задавшись периодом стойкости Т Sб Sм определяют предельные расчетные значения скорости резания для каждого инструмента по формулам для одноинструментной обработки. Затем для каждого инструмента определяют частоту вращения пб и пм. Для одношпиндельного станка лимитирующим инструментом является тот для которого получено наименьшее число оборотов пб и пм. Это число оборотов принимают общим для всех инструментов. Поэтому для каждого инструмента производят проверочный расчет действительной скорости резания и периода стойкости. Этого в некоторых случаях можно достичь применением инструментов из различных инструментальных материалов. Материал лимитирующего инструмента выбирается с более высокими режущими свойствами.
Скорость резания и частота вращения каждого шпинделя многошпиндельного станка определяется как и для одношпиндельного полагая что каждый шпиндель изолирован от других. Максимальная и минимальная частота вращения шпинделей устанавливается по лимитирующему шпинделю. После этого осуществляют проверочный расчет действительных значений скорости резания и периода стойкости для каждого инструмента.
Для многошпиндельных станков с различными частотами вращения шпинделей устанавливают общее машинное время для всех шпинделей с учетом заданной производительности. При этом машинное время для нелимитирующих шпинделей можно увеличить в результате снижения скорости резания и подачи. Увеличения производительности и уменьшения машинного времени лимитирующего шпинделя достигают применением инструмента с более высокими режущими свойствами.
Исходными данными для расчета режимов резания и времени обработки на агрегатных станках и автоматических линиях служат: производительность коэффициент использования автоматического оборудования и ритм работы автоматической линии и агрегатного станка. Режимы резания выбираются как и для одноинструментной обработки с учетом особенностей многоинструментной обработки на одношпиндельных и многошпиндельных станках с различными частотами вращения шпинделей. режимы резания выбранные по нормативам или рассчитанные по эмпирическим формулам для агрегатных станков и автоматических линий занижаются на 20-30%.
Время обработки а следовательно и режимы резания выбираются по лимитирующей операции (шпинделю инструменту) аналогично многоинструментной наладке т.е. определяется глубина резания подача и скорость резания для всех инструментов шпинделей и операций при принятой стойкости лимитирующего инструмента. Принимаются допустимые режимы резания и осуществляется проверочный расчет действительной скорости и стойкости инструмента на всех операциях.
В общем случае при определении режимов резания следует пользоваться эмпирическими зависимостями и табличными данными приведенными в пособии.
На основании определенных оптимальных режимов обработки заданных деталей различных габаритов (d м) и из разных материалов выбирают предельные значения частот вращения шпинделя (числа двойных ходов) nd и nm и подач Sd и SM .
Далее определяют силы резания возникающие в процессе обработки. Усилия резания рассчитывают для двух предельных значений. Первый расчет необходим для последующих расчетов максимальных крутящихся моментов а также для последующих расчетов зубчатых колес валов. Шпинделей подшипников муфт и т.д. Второй расчет усилия резания и максимальной мощности станка (привода).
7 Примеры обоснования технической характеристики приводов металлорежущих станков
Пример 1. Рассчитать техническую характеристику токарного станка с высотой центров Н = 30 мм расстояние между центрами L = 2500 мм приспособленного для скоростного точения стали с sв = 400 1000 МПа резцами оснащенными твердым сплавом Т15К6.
Определяем предельные значения диаметров точения по формулам (1) (2) мм
Dd = (1 15)H = 1×300 =300;
DM = (025 05)H = 025×300 = 75.
Зная Dd и DM определим наибольший и наименьший припуски на обработку которые могут встретиться при обработке на модернизируемом станке. Припуски на обработку в зависимости от диаметра находим по формуле (12) мм
t = Ct D033 = 07 300033 = 5
где Ct – коэффициент зависящий от обрабатываемого материала. По табл.3 примем для стали Сt = 07. Полученный припуск снимаем при обработке за два прохода. Тогда получим небольшую глубину резания td = 25 мм.
Наименьший припуск таким образом определить нельзя ибо он имеет место не при обдирочном а при чистовом проходе и следовательно является не начальным а промежуточным припуском. Величина промежуточного припуска или наименьшая глубина резания находится по формуле (13) мм
tM = 07+0025 D + 00001L ;
tM = 07+0025 7512 + 00001 2500 »10
Далее определяем величины подач наибольшую и наименьшую Sd и SM по допускаемой шероховатости поверхности обработки; Sd - при обдирке изделия диаметром Dd с глубиной резания td а SМ при отделке изделия диаметром DM с глубиной резания tM . Подачи можно определить по формулам (16) (17).
Для черновой обработки ммоб
Sd = 017 D+(td-2) 015 = 017 30013 + (25-2) 015 = 1265
Для чистовой обработки ммоб
SM = 0015 D = 0015 7523 = 026
Наибольшую и наименьшую скорости резания определяем по формуле (25). Скорость резания при обточке равна мммин
V = CV [Tm tx Sy(HB200)n]
Значения коэффициента СV и показателей степени приведены в табл.24. Скорость резания будет иметь наибольшее значение при снятии стружки наименьших размеров с наименьшей подачей SM и наименьшей глубиной резания tM и при обработке наиболее мягкого материала наиболее производительными резцами (т.е. наибольшим СV). Для пластинок твердого сплава (без охлаждения) можно записать ммин
Vd = 267 [900125 1018 026035 055] = 520
Наименьшая скорость будет наоборот при снятии большей стружки при обработке твердого материала ммин
VM = 267 [900125 25018 1265035 (280200)1] = 849
В силу того что работа с наибольшей частотой вращения шпинделя nd должна производиться при наибольшей скорости резания Vd и обработке изделия наименьшего диаметра а работа с наименьшей частотой вращения шпинделя nM при наименьшей скорости резания и наибольшем диаметре изделия предельные частоты вычисляются по формуле (45) и (46) мин-1
nd = 1000 Vd p DM = 1000 520314 75 = 2208
nM = 1000 Vd p Dd = 1000 85314 300 = 90
Тогда по формулам (49) и (50) диапазон регулирования привода главного движения и привода подач будет
RV = nd nM = 2208 90 = 245; RS = Sd SM = 1265026 = 48
Далее следует определить наибольшую силу резания чтобы знать максимальное усилие которое должен преодолеть механизм станка а также максимальные крутящие моменты для расчетов деталей привода.
Наибольшее усилие резания Pz d будет действовать при снятии наибольшей стружки (td) самого твердого материала и определяется по формуле (51)
Значения С1; х; y; n берутся из табл.32.
Pz d= 00357 251 1265075 280075 = 7288 kH
Максимальное усилие подачи которое должен преодолеть механизм станка равно
Максимальная мощность необходимая на резание как известно из теории резания будет при отделение стружки наибольшего сечения и при обработке наиболее мягкого материала.
Наибольшие усилия при обработке самого мягкого материала кН
Р= С1 t S(HB)= 0279 251 1265075 (112)035 = 433
Далее по формуле (67) вычисляем максимальную мощность получаемую при обработке с наименьшей скоростью резания самого мягкого материала
Nэ= РVM 60 102 = 433 213660 102 = 151 kBт
VM = 267 900125 25018 1265035 (112200)1] = 2136 ммин.
Мощность электродвигателя который следует поставить на станок определим по формуле (79) кВт
Nд = Nэ k h =151125 08 =151
Поскольку токарный станок имеет один электродвигатель обеспечивающий и привод главного движения и привод подач рассчитанную мощность электродвигателя необходимо увеличить на 3-4% т.е.
Nст = Nд 104=151 104 = 157 кВт.
Пример 2. рассчитать техническую характеристику револьверного станка приспособленного для обработки конструкционной стали марок 10 20 35. 45 инструментом из быстрорежущей стали. Наибольший диаметр прутка 60 мм. По формуле (2) определяем наименьший диаметр обточки
DM = (025 05)Dd = 033 60 = 20 мм
Находим наименьшую глубину резания по формулам (12) (13) мм
td = Ct D= 07 6013 = 3
tM = 07 0025 D= 07 0025 2012 = 08
рассчитываем по формулам (16) (17) наибольшую и наименьшую подачи мммин
Sd = 017 D+ 015 (td - 2) = 017 6013 + 015(3-2) = 08
SM = 0015 D = 0015 2023 = 01 .
Определяем наибольшую скорость резания при обработке самой мягкой стали и снятии самой малой стружки по формуле (25) и табл.24 ммин
Vd = 5253001 01025 0805 07175 = 201.
При определении наименьшей скорости резания следует иметь в виду что потребная для обработки наименьшая частота вращения может получиться не при обточке а при сверлении развертывании или нарезании резьбы т.е. в данном случае необходимо найти наименьшую скорость резания на все виды обработки:
а) при точении самой твердой стали и снятии самой большой стружки ммин
VМ = 426001 08066 3025 (235200)175 = 26
б) при сверлении самой твердой стали сверлом диаметра 05Dd = 05 60 = 30 мм с подачей S = 008 ммоб по формуле (33) и табл.25 ммин
VМ = 124 30046002 0805 (235)09 = 24
в) при нарезании резьбы в самой твердой стали метчиком по формуле (29) ммин
VМ = 643 301219009 3505 = 17
где d0 – наибольший диаметр метчика = 05Dd = 0560 = 30 мм;
Р - шаг нарезаемой резьбы;
г) при развертывании по формуле (39) и табл.25 ммин
VM=СVDTm t S(HB)n=13103003 19004 0102 025065 (235)09=131
Находим наибольшую частоту вращения шпинделя используя формулу (45) мин-1
nd = 1000Vd p DM=1000 201 314 20 = 3200
Наименьшая частота вращения следующая (по формуле (46)):
а) при обточке nM = 1000VM p Dd = 1000 26 314 60 = 138 мин-1
б) при сверлении (D=30 мм) nM = 1000 24 314 30 = 255 мин-1;
в) при нарезании резьбы метчиком (D = 30 мм)
nM = 1000 17 314 30 = 18046 мин-1;
г) при развертывании (D = 30 мм) nM=1000 131 314 30=139 мин-1;
следовательно наименьшую частоту вращения дает обточка
Далее находим по формулам (54) (62) и табл.32 главную составляющую силы резания и крутящий момент в процессе обработки. При точении
Рz = С1 tх1 Sу1 (HB)n1 = 0036 3 08075 (235)075 = 5402 кH
М = С2 Dz2 Sу2 (HB)n2 = 08 302 01208 (235)07 = 80191 кHм .
Определим наибольшую мощность потребную для резания. Для револьверных станков наибольшая потребная мощность для резания по формулам (67) (69) (рассчитываем при одновременной работе нескольких инструментов лучше всего сверла и резца при снятии наибольшей стружки при обработке самого мягкого материала) будет равна кВт
Nсв = РVM 306 Dd = 602 24306 30 = 157
Суммарная мощность потребная на резание
N=Nр+Nсв=229+157=3.86 кВт
Мощность электродвигателя будет по формуле (81)
Nэ=N k h =386125 075 =411 кВт.
Пример 3. Рассчитать техническую характеристику токарно-карусельного станка с максимальным диаметром обработки Dd = 2300 м. Обрабатываемый материал – сталь в = 400 1000 МПа. Материал режущей части инструмента (резца) пластинки из твердого сплава Т5К10.
Определяем диаметр планшайбы Dпл = Dd112 = 2300112 » мм. Находим по формуле (2) наименьший диаметр обработки DM = (025 05) Dпл = 025 2100 = 525 мм.
Наибольшая и наименьшая глубина резания по формулам (12) (13) будет мм
td = C2 D= 08 230013 = 10
tM = 07 0025 D= 07 0025 52512 = 127
по формулам (16) (17) определяем наибольшую и наименьшую подачи ммоб
Sd = 017 D+ 015 (td-a) = 017 230013 + 015(10-2) = 344
SM = 0015 D= 0015 52523 = 097
Находим наибольшую скорость резания при обработке с охлаждением наиболее мягкого материала (в 750 МПа) и снятии малой стружки используя формулу (25) и табл.24 ммин
Vd = CV Tm tx Sy(HB200)n
Vd = 294 300125 127018 09702 (150200) = 251.
Находим наименьшую скорость резания при обработке без охлаждения самого твердого материала и снятии наибольшей стружки (для сталей в 750 МПа) ммин
Vd = 267 900125 10018 344035 (235200)1 = 5585.
Определяем наибольшее усилие резания при обработке высокопрочной стали по формуле (51) и табл. 32 кН
Р= С1 t S(HB) = 0036 101 344075 235075 =5 445
Находим предельные значения частот вращения планшайбы по формулам (45) (46) мин-1
nd = 1000Vd p DM = 1000 251 314 525 = 1522
nM = 1000VM p Dd = 1000 5585 314 2300 = 773
тогда Rv = 1 522 773 = 197.
Определяем максимальную мощность необходимую на резание по формуле (67) при отделении максимальной стружки высокопрочной стали кВт
Nр = РVM 612 = 5445 5585 612 = 497.
В связи с тем что на карусельных станках обрабатываемые заготовки и планшайба имеют большую массу мощность расходуемая на трение в направляющих планшайбы должна также учитываться. Для этого определим момент трения в направляющих планшайбы
где G – вес всех вращающихся частей (изделия планшайбы венца шпинделей и т. д.).
Суммарный вес может ориентировочно приниматься равным кН
G = G + (015 02)G = 20 + 02 20 = 24
где G - вес изделия ;Рz - составляющая сил резания прижимающая планшайбу к столу 04 Рz = 04 5445 = 2178 кН;
f - коэффициент трения на направляющих принимается для чугунных направляющих равным 035; для направляющих с накладками из текстолита - 0025; Dн.ср - средний диаметр поверхности трения направляющих берется по конструктивным разработкам и может приближенно приниматься 055Dпл Dн.ср = 055 2100 = 1155 = 1155 м.
Следовательно имеем Мтр = (24 + 2178) 0025 11552 = 3779 кН м.
Потребная мощность электродвигателя привода главного движения кВт
Nд = Nр k h + Мтр n 975 h. В нашем случае n = 77 мин-1; Nр = 497 125 08 +3779 77 975 08 = 524 кВт.
Пример 4. Рассчитать техническую характеристику сверлильного станка для наибольшего диаметра сверления Dd = 35 мм при сверлении углеродистой стали в = 450 850 МПа сверлами из быстрорежущей стали. Определяем наименьший диаметр сверления по формуле (3) мм
DM = (015 03) Dd = 025 35 = 9.
Находим по формуле (19) наибольшую Sd и наименьшую SM подачи сверла при обработке самого мягкого обрабатываемого материала при работе наибольшими и наименьшими диаметрами сверла ммоб
Sd = CS D = 0064 3506 = 054
SM = CS D = 0064 906 = 024 .
Определяем наибольшую и наименьшую скорости резания используя формулу (33) ммин
Vd = СVDT S(HB) = 874 9065 1002 02407 20009 = 529
VM = СVDT S(HB) = 360 3504 2002 05405 23509 = 825
Значения CV у z m n для разных параметров режимов резания приведены в табл. 25.
Определяем наибольшую и наименьшую частоты вращения шпинделя по формулам (49) и (46) мин-1
nd = 1000Vd p DM = 1000 529 314 9 = 18719
nM = 1000VM p Dd = 1000 825 314 35 = 75.
Определим используя формулы (49) и (50) диапазоны регулирования привода главного движения и привода подач
RV = nd nM = 18719 75 = 249; Rd = Sd SM = 054 024 = 225.
По формуле (60) и табл.32 определяем значения наибольшего крутящего момента при сверлении самого твердого материала кНм
Мd = С D S (HB) = 0008 352 05408 (235)07 = 1740 .
Наибольшее осевое усилие действующее при сверлении находим по формуле (59) и табл.32. Оно будет равно кН
Рd = С D S (HB)= 0015 351 05407 (235)07 = 204
По величине Рd рассчитывается на прочность механизм подач сверлильных станков. Определяем максимальную мощность потребную на резание по формуле (68) кВт
Nэ= МVM 306 Dd =1740 825 306 35 = 134
Находим по формуле (81) мощность электродвигателя для привода главного движения
Nд = Nэ k h = 134 12 08 = 139 кВт.
С учетом привода подач имеем: Nст = Nд 105 = 145 кВт.
Пример 5. Рассчитать техническую характеристику горизонтального фрезерного станка со столом имеющим размеры 300х1250 мм предназначенного для обработки углеродистой стали разной твердости быстрорежущими фрезами. Используя формулы (4) и (5) определяем наибольший и наименьший диаметры фрез мм
Dd = (02 03)в = 025 ×300 = 75;
DM = (01 02)в = 017×300 = 20 где в - ширина стола.
Подсчитаем наибольшую и наименьшую ширину фрезерования по формулам (6) и (7) мм
Вd = (075 1)Dd = 1×75 = 75;
ВM = (075 1)Dd = 1×20 = 20.
В зависимости от обрабатываемого материала определяем по табл.4 припуск на обработку который равен h = 3 мм. Подсчитываем наибольшую и наименьшую глубину резания td и tM при фрезеровании по величине припуска на обработку. Для чистовой обработки примем tM = 1 мм для черновой обработки td = 5 мм.
Выбираем по табл.13 наибольшую и наименьшую подачу на зуб фрезы из условия шероховатости для самого мягкого материала.
При td = 5 мм Dd = 75 мм будем иметь для zф = 18
Sz d = 008 - 005 ммзуб zф = 8 S= 02 ммзуб где zф - число зубьев фрезы.
При tM = 1 мм Dd = 20 будем иметь zф = 5 S = 003 ммзуб. Определяем по таблицам S и S для самого твердого материала.
При td = 5 мм Dd = 75 мм zф = 18будем иметь S= 007 ммзуб.
При zф = 8 S= 02 ммзуб.
При tM = 1 мм Dd = 20 z ф= 5; S = 004 ммзуб. Находим по формуле (40) и табл.26 наибольшую скорость для самого мягкого и наименьшую скорость резания для самого твердого обрабатываемых материалов ммин
Vd = 616 20017 30033 1019 003028 501 20008 = 601
VM = 616 75017 60033 5019 02028 1801 75008 = 206 .
Предельные значения частот вращения шпинделя будут равны по формулам (47) и (48) обмин
nd = 1000 601 314 20=967; nM = 1000 206 314 75 = 874.
Находим предельные значения подач мммин
Sd = Szd zd nM = 02 18 874 = 314
SM = SzM zM nd = 003 5 957 = 143.
Определяем по формулам (49) и (50) диапазоны регулирования
RV = 957 874 = 109 ; RS = 314 143 = 219.
Определим по формуле (63) и табл.32 максимальную силу резания кН по формулам (71) и (79) наибольшую мощность потребную на резание и мощность электродвигателя кВт
Рd = 068 5086 02074 751 18 75086 = 2778;
Nэ = 35 10-5 5036 02072 18 874 75014 = 89
Nд = 89 12 08 = 927.
Пример 6. рассчитать техническую характеристику зубофрезерного станка. Наибольший модуль нарезаемых зубьев md=8 мм. Обрабатываемый материал – сталь разной твердости.
Определяем наименьший нарезаемый модуль по формуле (8) мм
По предельным значениям модуля диаметры червячных фрез по табл.2 находим Dd = 125 мм; DM = 55 мм
td = 14 md = 14 8 = 112; tM = 07 mM = 07 2 = 14
Определяем предельные значения величин подач. Подачи за один оборот заготовки выбираются в зависимости от модуля обрабатываемого материала и числа зубьев по табл.1 ммоб
Определим предельные значения скоростей резания по формуле (42) и табл.27-29
Vd = (560 24005 08085 2-05) 11 = 684;
VM = (350 480033 2801 805) 06 = 88.
Найдем наибольшие и наименьшие частоты вращения шпинделя по формулам (45) и (46) мин-1
nd = 1000Vd p DM = 1000 684 314 55 = 396
nM = 1000VM p Dd = 1000 88 314 125 = 224.
Диапазон регулирования привода главного движения и привода подач вычисляются по формулам (49) и (50)
RV = nd nM=396 224 = 176; RS = Sd SM = 28 08 = 35.
Мощность требуемая на резание находим по формуле (76) кВт
Nэ = 124 Sm DM = 124 2809817 55 = 19
Мощность электродвигателя при использовании формулы (79) запишем кВт
Nд = Nэ k h = 19 125 08 = 19.
Пример 7. Рассчитать техническую характеристику поперечно-строгального станка если известны: а) максимальные размеры заготовок
б) материал обработки – сталь - поковка с dв = 390 880 МПа и чугун – литье с НВ = 140-200; в) материалы резцов для стали Т5К10 для чугуна - ВК8; г) кулисный механизм с постоянной длиной кулисы при re = 05 где е = 500 мм и r = 250 мм длина кулисы L = 18 e = 18 500 = 900 мм.
Определяем размеры стола по формулам (9) (10) (11) мм
в = (06 07) Lc = 06 1000 = 600;
H = (075 1)в = 075 600 = 450.
Находим наибольшую td и наименьшую tM глубины резания используя формулы (12) (13) принимая Вd за Dd тогда ВМ = 05 Вd
td = Ct B= 08 500033 = 62 мм
tM = 07 0025 В+00001 Lc = 07 0025 25012+000011000 = 12 мм.
Выбираем наибольшую Sd и наименьшую SM подачи для самого мягкого и самого твердого материала на основании нормативов для технического нормирования работ на поперечно-строгальных станках по табл.7 и 10 для токарной обработки.
Для стали при чистовой и черновой обработке Sd = 14 ммдв.х;
SM = 01 ммдв.х; SM = 01 ммдв.х. Следовательно Sd = 16 ммдв.х;
Наибольшая скорость резания при наименьшей глубине резания и наименьшей подаче и самого мягкого материала при обработке резцами оснащенными пластинками твердого сплава по формуле (25) и табл.24 будет равна мммин
V = CV T t S(HB200)n = 267 300125 12018 0102 (155200)1 = 338.
Наименьшая скорость резания для самого твердого материала при наибольшей глубине резания и наименьшей подаче ммин
VМ = 267 1800125 62018 14035 (235200)1 = 7672.
Определяем наибольшую Ld и наименьшую LM длину хода ползуна
где l – длина заготовки l1 и l2 – величины врезания и перебега резца в начале и в конце хода. Для поперечно-строгательного станка l1 + l2 = 35-75 мм.
Ld = 800 + 75 = 875 мм
LМ = (01 025) Ld = 025 875 = 218 мм.
Находим наименьшую скорость резания при черновой обработке самого мягкого материала ммин
V = 267 1800125 6208 14035 (235200)1 = 116.
Наибольшее и наименьшее число двойных ходов дв.хмин
nd = 1000Vpd LM (1+m) = 1000 338218 (1+075) = 8859
где m = Vp Vx - отношение скоростей рабочего и холостого хода обычно
nМ = 1000VpM Ld (1+ m) =1000 766 875(1+ 075) = 50.
Диапазоны регулирования привода главного движения и привода подач по формулам (49) и (50) будут равны
RV = nd nM = 8859 50 = 171;
RS = Sd SM = 14 01 = 14.
Наибольшее усилие резания при черновой обработке самого мягкого материала по формуле (51) и табл.32 будет равно кН
Р= С1 t S(HB)= 0279 621 14075 (155)035 = 128
Зная величины V и Р определим по формуле (67) максимальную мощность потребную на резание при обработке наиболее мягкого материала при наибольшем сечении стружки
Nд = Р V 612 = 128 116612 = 242 кВт.
Тогда мощность электродвигателя по формуле (79) будет равна
Nд = Nэ k h = 242 125 085 = 227 кВт.
РАЗРАБОТКА КИНЕМАТИЧЕСКОЙ СХЕМЫ ПРОЕКТИРУЕМОГО ПРОИВОДА.
1 Определения множительной сложенной структур и связанных механизмов коробок передач.
Конструирование металлорежущего станка начинается с разработки кинематической схемы которая определяет качество работы будущей машины и поэтому должна быть продумана очень тщательно.
Современный металлорежущий станок в большинстве случаев имеет развитые коробки скоростей и подач с необходимым числом передаточных отношений и диапазоном регулирования которые подлежат разработке в курсовом проекте по станкам.
Курсовой проект по металлорежущим станкам является первой самостоятельной конструкторской работой студентов включающей методы кинематического расчета и рационального проектирования коробок скоростей и подач. Он выполняется студентами после изучения таких общетехнических дисциплин как теория механизмов и машин детали машин подъемно-транспортные машины кинематика металлорежущих станков гидравлика и др.
Любой металлорежущий станок имеет исполнительные органы: шпиндель суппорт стол и др. предназначенные для выполнения рабочих ходов. Чтобы переместить исполнительный орган станка необходим источник движения (например электродвигатель) и кинематическая цепь связывающая источник движения с исполнительным органом. Кинематическая цепь представляет собой совокупность кинематических пар расположенных в определенной последовательности. Примером кинематических пар (передач) могут служить два зубчатых колеса которые находятся в зацеплении и установлены соответствующим образом на валах червяк – червячное колесо винт – гайка ременная передача и др.
Кинематической схемой станка называется условное изображение кинематических цепей металлорежущего станка в одной плоскости – плоскости чертежа.
Существующие и вновь создаваемые металлорежущие станки со ступенчатым регулированием частоты вращения частоты двойных ходов и скорости подачи исполнительного органа могут иметь множительную сложенную структуру коробок скоростей и подач (коробок передач) а также могут включать в себя так называемые связанные механизмы.
Коробка передач станка характеризуется диапазоном регулирования который представляет собой отношение максимальной частоты вращения (или частоты двойных при возвратно-поступательном движении или скорости подач) исполнительного органа к минимальной частоте вращения или частоте двойных ходов или скорости почти соответственно:
- для вращательного главного движения характерного для шпинделей планшайб и др.;
- для поступательного перемещения характерного для коробок подач (движения подачи);
- для возвратно-поступательного главного движения характерного например для строгальных долбежных станков;
где -диапазон регулирования;
Nm Nmax. дв.х. - минимальная и максимальная частота двойных ходов исполнительного органа соответственно.
Числом скоростей Z привода называется количество различных частот вращения (двойных ходов) которое обеспечивает данный привод (коробка передач и электродвигатель).
Коробка передач состоит из одной двух и более групповых передач. Под групповой передачей или группой передач понимают количество рабочих скоростей которые можно передать с одного вала на другой. Каждая групповая передача характеризуется количеством передач Pa Pb Pc и т. д. а также характеристикой.
Характеристикой групповой передачи называют количество скоростей (частот вращения двойных ходов подач) кинематически предшествующее данной рассматриваемой группе. Между числом скоростей Z привода и количеством передач в группах Pa Pb Pc имеется определенная связь по характеру которой коробки передач делятся на множительные и сложенные.
Множительными коробками передач (множительные структуры) называют такие коробки для которых число скоростей Z получается путем перемножения количества передач имеющихся в каждой групповой передаче входящей в состав коробки т.е. структурная формула для множительных коробок передач запишется
Где k – число групповых передач в коробке скоростей или коробке подач.
Для коробки скоростей представленной на рис. 2.1 характерна множительная структура и число скоростей коробки будет равно
За счет передвижного блока Б1 шестерен с вала II можно передать на вал III скорость трижды: через зубчатые колеса Z1 – Z4 (блок Б1 передвинут влево) через колеса Z2 – Z5 (блок Б1 находится в среднем положении) и через зубчатые колеса Z3 – Z6 (блок Б1 сдвинут вправо) т.е. за счет групповой передачи Pa вал III может иметь три различные скорости.
Благодаря групповой передаче PВ три скорости которые имеет вал III могут быть переданы на вал IV дважды: через зубчатые колеса Z7 – Z9 (блок Б2 находится в левом положении) и через зубчатые колеса Z8 – Z10 (блок Б2 находится в правом положении).
Таким образом вал IV может иметь шесть разных скоростей. Аналогично за счет групповой передачи Pc шесть скоростей которые имеет вал IV могут передаться на шпиндель V дважды: через зубчатые колеса Z11- Z13 (блок Б3 передвинут влево) и через колеса Z12 – Z14 (блок Б3 передвинут вправо). Всего шпиндель V будет иметь 12 равных скоростей.
Характеристика групповой передачи Pa будет равна L так как этой групповой передаче кинематически предшествует одна скорость (электродвигатель M скоростной) и вал I имеет лишь одну частоту вращения (скорость). Характеристику групповой передачи обозначаем буквой X тогда X1 = I.
Рис.2.1. Коробка скоростей с множительной структурой:
Pa – первая групповая передача (основная группа);
PВ – вторая групповая передача первая переборная);
Pc – третья групповая передача (вторая переборная);
M – электродвигатель; Б1 Б2 Б3 – передвижные блоки шестерен; Z1 – Z14 -числа зубьев зубчатых колес.
Групповой передаче PВ кинематически предшествует три скорости (за счет блока Б1 ) следовательно X2 = 3 групповой передаче Pc предшествует 6 скоростей поэтому X3 = 6.
Как видно из рисунка 2.1 множительная структура привода состоит из одной кинематической цепи для которой общее число скоростей определяется вышеуказанным перемножением числа скоростей каждой групповой передачи.
Сложенной структурой называется такая структура которая состоит из двух или более кинематических цепей каждая из которой является множительной структурой. Общее число скоростей привода со сложенной структурой определяется сложением числа скоростей всех кинематических цепей привода. Таким образом сложенная структура составляется суммой множительных структур.
Структурная формула привода сложенной структуры при двух множительных составляющих структурах будет
где Z – общее число скоростей привода;
Z1 Z2 – число скоростей первой и второй составляющих структур.
Как правило у структур Z1 Z2 есть общая часть которую обозначим через Z0 тогда
Структуры Z1 и Z11 называются дополнительными и используются для получения только части скоростей из общего числа скоростей привода. Структура Z0 используется для получения всех скоростей на выходе привода и называется основной. Как правило дополнительные структуры Z1 и Z11 служат для получения низшей части диапазона скоростей а основная структура Является более короткой и служит для получения высшей части диапазона.
Примером применения сложенных структур может служить привод шпинделя токарно-винторезного станка 1616 IА61 16К20 и др.
Вращение от электродвигателя 1 (рис. 2.2) передается валу I на котором установлен двойной блок шестерен . С его помощью на валу II имеем две различные частоты вращения:
где - частота вращения электродвигателя 1;
- числа зубьев колес блока и колес входящих с ними в зацепление.
С вала II вращение может быть передано через зубчатую пару непосредственно на шпиндель (вал III) или через зубчатые колеса на вал IV далее через пару и блок – на шпиндель III.
Как видно из кинематической схемы колеса участвуют в передаче вращения на шпиндель как по цепи так и по цепи т.е. зубчатые колеса являются общей частью обеих кинематических цепей.
Дополнительными структурами являются:
Всего шпиндель III будет иметь десять скоростей
Как правило общую часть следует использовать для сообщения шпинделю III высоких частот вращения. Сложенная структура (см. рис. 2.2) имеет две дополнительные структуры и первая из которых представляет передачу c постоянным передаточным отношением
Рис. 2.2. Кинематическая схема привода имеющего сложенную структуру.
В металлорежущих станках кинематические цепи могут быть упрощены применением так называемых связанных зубчатых колес.
Зубчатое колесо называется связанным если оно принадлежит одновременно двум групповым передачам.
Зубчатое колесо (см. рис. 2.2)принадлежит как кинематической паре так и кинематической паре зубчатых колес т. е. оно участвует в передаче вращения с вала II как на вал III так и на вал IV. Поэтому это колесо будет связанным и чтобы отличать связанные зубчатые колеса от остальных несвязанных на кинематических схемах их штрихуют.
Зубчатый механизм имеющий в своем составе одно связанное колесо называется односвязным (рис. 2.2 колесо и рис. 2.3 а колесо ). Механизм имеющий два связанных зубчатых колеса называется двухсвязным (рис. 2.3 б связанные колеса ).
Подобным образом можно получить механизмы с тремя и более связанными зубчатыми колесами. Применение механизмов со связанными зубчатыми колесами позволяет уменьшить число колес и габаритные размеры механизма. Так механизм с одним связанным колесом (рис. 2.3а) имеет расстояние между крайними зубчатыми колесами механизм с двумя связанными зубчатыми колесами (рис.2.3б) имеет меньшее расстояние где - ширина зубчатого колеса.
Рис. 2.3. Механизмы со связанными зубчатыми колесами.
2. Кинематический расчет коробок передач с множительной структурой.
В задании на курсовой проект приводятся исходные данные в которые могут входить: максимальная минимальная частота вращения (частота двойных ходов) а также скорости подач число скоростей привода или знаменатель геометрического ряда частот вращения шпинделя (частот двойных ходов) скоростей подачи.
Если не заданы то их следует определить путем расчета режимов резания на основе данных об обрабатываемом материале материале и геометрии режущего инструмента и т. п. Из расчета режимов резания известны максимальная и минимальная скорости резания и для коробок передач.
2.1. На основе известных скоростей резания находят максимальную и минимальную частоту вращения шпинделя
где - предельные диаметры заготовок предназначенные для обработки. В формуле (86) измеряются в мм а - в .
Если не задан а задан то находят по формуле
Для привода с возвратно-поступательным движением кроме должны быть известны максимальная и минимальная длины обработки.
2. Определяют диапазон регулирования:
- для главного вращательного движения;
- для главного возвратно-поступательного движения;
- для привода подач.
Учитывая непрерывное совершенствование режущего инструмента значения в формулах (88) (89) (90) необходимо увеличить на 15-20 %.
2.3. По известным значениям диапазона регулирования и знаменателю геометрического ряда находим число скоростей привода по формуле
Полученное значение округляют до целого числа и уточняют диапазон по формуле (заданный знаменатель геометрического ряда брать отличающимся от стандартного нельзя)
Если в задании число скоростей привода не дано то следует выбрать одно из стандартных значений знаменателя геометрического ряда и по формуле (б) определить число скоростей .
Нормаль станкостроения рекомендует применять при проектировании следующие знаменатели:
a) для крупных станков общего назначения = 126; 112;
б) для средних станков =141;
в) для небольших станков =158; 178;
г) для станков с настройкой кинематической цепи привода сменными зубчатыми колесами
д) для автоматов с большой точностью настройки на скорость резания
4. Для геометрического ряда частот вращения (частот двойных ходов скорости подач) находят промежуточное значение частот
Иногда в задании на курсовой проект задаются число скоростей и диапазон регулирования . В таком случае следует найти знаменатель геометрического ряда по формуле:
и округлить его до ближайшего стандартного а также уточнить после округления диапазон регулирования .
5. Число скоростей вращения шпинделя (частот двойных ходов или скорости подачи) разбиваем на количество передач в группах
где - количество групповых передач в приводе.
Для создания компактного привода следует выполнять неравенство
Например для кинематической схемы привода представленного на рис. 2.1.
Желательно чтобы число скоростей представляло собой произведение множителей 2 и 3. Этому требованию удовлетворяют значения: 2; 3; 4; 6; 8; 9; 12; 16; 18; 24; 27; 32; 36 и т. д. Одиночные передачи следует располагать ближе к шпинделю.
2.6. Определяют характеристику групповой передачи.
Для основной групповой передачи (см. рис. 2.1) для первой переборной групповой передачи для второй переборной групповой передачи .
Структурная формула привода (один из вариантов) изображенного на рис. 2.1 запишется
2.7. Построение структурных сеток.
Для определения передаточных отношений кинематических пар привода необходимо построить структурную сетку и график частоты вращения (частоты двойных ходов или скорости подач).
Для построения структурной сетки проводят ряд параллельных вертикальных линий с интервалом в количестве равном числу скоростей и ряд горизонтальных прямых с произвольным расстоянием между ними число которых равно количеству валов привода. На каждом валу привода (каждой горизонтальной прямой) наносят римскими цифрами его номер I II III IV и т. д. Между соседними валами (горизонтальными прямыми) т. е. Для каждой групповой передачи записывают число передач и т. д. в группе и характеристику и т.д. (рис. 2.4а). Так для групповой передачи число передач равно 3 а характеристика равна 1 поэтому между валами II – III написаны значения и т.д. Вал III имеет три частоты вращения (соответствуют трем точкам) и если на валу IV шесть точек то это означает что он имеет возможность получать шесть различных частот вращения. Поскольку вал II имеет одну скорость а вал III – три скорости и эти валы в кинематической связи то на структурной сетке указанные точки должны соединяться между собой лучами. Должны соединяться лучами также другие точки. Для соединения точек из каждой точки верхней горизонтальной линии проводят столько лучей (отрезков соединяющих точки двух соседних валов) сколько передач имеет рассматриваемая групповая передача с расстоянием между концами лучей исходящих из одной точки равным произведению .
Так для основной групповой передачи (см. рис. 2.4а) расстояние между концами соседних лучей выходящих из точки «0» равно для первой переборной групповой передачи расстояние между двумя соседними лучами выходящими из одной точки равно т.е. шести клеткам структурной сетки.
Построение структурной сетки для одной структуры например (см. рис. 2.1) неоднозначно. Количество возможных структурных вариантов (структурных сеток) определяется по формуле
где - число групповых передач в приводе (в нашем примере групповых передач три: (рис. 2.4 а-е).
Из построенных структурных сеток наиболее экономичным вариантом является вариант с веерообразной симметричной структурной сеткой (рис. 2.4 а).
Рис. 2.4. Варианты структурных сеток привода
Структурная сетка несет определенную информацию а именно: она дает относительные связи между передаточными отношениями групповых передач но не дает конкретных значений этих величин. Из структурной сетки (см. рис. 2.4 а) следует:
так как расстояние между лучами выходящими из одной точки 0 равно одной клетке;
-расстояние между лучами выходящими из одной точки вала II равно трем клеткам;
- расстояние между лучами выходящими из одной точки вала III равно шести клеткам.
2.8. Построение графика частоты вращения (частоты двойных ходов скорости подачи).
Для построения графика частоты вращения (частоты двойных ходов скорости подачи) необходимо пользоваться соотношениями (102) (103) (104) и неравенствами 14i 2 – для коробок скоростей 15i 28 – для коробок подач ограничивающими передаточные отношения с целью нормальной работы зубчатых пар.
Подбор численных значений передаточных отношений при известном знаменателе φ (пусть φ =126) следует начинать для лучей структурной сетки имеющих наибольшее расхождение. В нашем примере (рис. 2.4 а) наибольшее расхождение имеют лучи .
Передаточное отношение . Приступаем к построению графика частоты вращения. Как и при построении структурной сетки проводим горизонтальные прямые линии соответствующие валам I II III IV.
Наносим вертикальные линии на расстоянии nZ. Пусть в результате подсчета по уравнению (8) получается ряд: 80 100 125 160 200 250 315 400 500 630 800 1000 который откладываем на нижней горизонтальной линии V (рис. 2.5 а б).
Строим лучи графика соответствующие минимальным передаточным отношениям imin. Минимальное передаточное отношение между IV и V валами равно i7 =1318 (см. структурную сетку рис. 2.4 а).
Тогда частота вращения вала IV будет:
Полученную частоту вращения откладываем на валу IV и соединяем цифры 250 и 80 лучом i7 (рис. 2.5 а). Далее находим:
Наносим эти значения на график и соединяем их лучами i5 i3.
Аналогично строим лучи графика соответствующие максимальным передаточным отношениям imax пользуясь данными структурной сетки. Максимальное передаточное отношение между валами IV и V равно i6=φ поэтому луч i6 должен соединить числа 250 и 315 валов IV и V так как мин-1.
Наносим значения 315 500 630 мин-1 на соответствующие валы графика и соединяем их лучами.
Для окончания построения графика частоты вращения проводим лучи параллельные построенным лучам i7 аналогично лучам структурной сетки т. е. если в структурной сетке (см. рис. 2.4 а) для которой строим график частоты между валами IV-V проведено шесть параллельных лучей с левым наклоном значит такое же число параллельных лучей левого наклона должно быть и на графике частоты вращения (рис. 2.5 б).
Если на структурной сетке наибольшее расхождение между лучами выходящими из одной точки вала IV равно шести клеткам на валу V трем клеткам на валу IV и одной клетке на валу III то такие же расстояния должны быть выдержаны и на графике частоты вращения (рис. 2.5 б).
Для построения графика частоты вращения (частоты двойных ходов скорости подачи) не обязательно выполнять вычисления частот вращения по валам. Более просто построение можно выполнить следующим образом. Начинаем проводить лучи между последними валами (в нашем примере между валами IV-V). Для этого из точки соответствующей 80 обмин вала V проводят луч левого наклона величина угла наклона должна быть такой чтобы луч дойдя до вала IV перекрыл пять клеток так как передаточное отношение для данного луча . Иными словами количество перекрываемых лучом клеток графика частоты должно быть равно модулю показателя степени при знаменателе геометрического ряда.
Так это означает что i6 >1 (передача ускоряющая) и луч i6 должен иметь правый наклон и перекрывать одну клетку при соединении валов IV-V. В дальнейшем построение графика частоты должно проводиться по вышеописанной методике.
График частоты вращения содержит все данные имеющиеся в структурной сетке и кроме этого он определяет: количество элементарных передач необходимых для компоновки привода относительное расположение групповых и одиночных передач передаточные отношения передач всего привода частоту вращения всех валов механизма при всех включениях передач. Таким образом график частоты содержит структуру привода все кинематические связи и расчетные величины выраженные через знаменатель φ геометрического ряда.
На основе построенного графика частоты вращения шпинделя (частоты двойных ходов скорости подачи) строят кинематическую схему привода (для нашего примера кинематическая схема приведена на рис. 2.1).
Чтобы провести луч i0 на графике частоты вращения (рис. 2.5 б) необходимо предварительно подобрать электродвигатель и выбрать кинематическую пару соединяющую вал I электродвигателя и вал II коробки передач. В нашем примере выбрана ременная передача для которой передаточное отношение обозначим через i0. Обычно выбирают асинхронный короткозамкнутый электродвигатель по мощности необходимой для процесса резания и частоте вращения по каталогам.
Мощность необходимая для процесса резания определяется по формуле: (105)
где Pz – тангенциальная составляющая силы резания Н - берется из расчета режимов резания.
Если известен крутящий момент возникающий на шпинделе в процессе резания то: (106)
где nV – частота вращения шпинделя т. е. V вала.
Мощность электродвигателя находим по формуле:
гдеобщ=Пi – общий коэффициент полезного действия кинематической цепи по которой передается движение k-коэффициент перегрузки станка.
Обычно выбирают самую длинную кинематическую цепь.
П – знак произведения.
Для станков с главным вращательным движением общ=070 085.
Если и главное движение и движение подачи осуществляется от одного электродвигателя то его мощность определяют по формуле:
Подобрав по мощности асинхронный короткозамкнутый электродвигатель наносим частоту вращения его точкой на вал I (рис. 2.5 б) и соединяем эту точку с точкой на валу II получим луч i0. передаточное отношение ременной передачи находим как:
2.9. Определение чисел зубьев колес групповых передач.
Решение этого этапа упрощается когда зубчатые колеса групповых передач имеют одинаковый модуль. В этом случае зубчатые колеса кроме обеспечения требуемого передаточного отношения (см. рис. 2.1):
должны обеспечить также постоянную сумму зубьев в пределах данной двухваловой передачи т. е.:
Решая систему уравнений (110) и (112) получим:
где zвщ – число зубьев ведущей шестерни рассматриваемой кинематической пары;
zвм – число зубьев ведомого зубчатого колеса этой же пары.
Задаваясь суммой чисел зубьев z и зная требуемые передаточные отношения i можно найти числа зубьев zвщ и zвм. Однако во многих случаях трудно сразу получить удовлетворительные решения поскольку при расчете zвщ и zвм получаются дробными числами.
Для облегчения расчетов следует пользоваться данными табл. 2.1 где по горизонтали отложена z а по вертикали – передаточные отношения.
Пустые клетки таблицы означают что при данном z передаточное отношение не выдерживается в требуемых пределах.
Рассмотрим пример определения чисел зубьев трех пар шестерен которые должны обеспечить передаточные отношения i3=1φ =1126 и минимальное число зубьев которое можно назначать для зубчатых колес z =20.
Если по табл. 1 взять например z =45 то при для первого и третьего передаточных отношений можно брать z =45 тогда для i3 числа зубьев будут 20:25 т. е. зубчатые колеса следует поменять местами.
Для i2 =1 по колонке z =45 в табл. 2.1 есть пустая клетка что свидетельствует о невозможности обеспечения передаточного отношения i2 =1 при z =45.
По этой причине мы должны выбрать новое z которое удовлетворило бы все заданные передаточные отношения. Таким суммарным числом зубьев будет z =50 тогда для для i2 =1 zвщ = zвм =25 и для i3 =1126 zвщ=22 zвм=28.
Проверяем погрешности в передаточных отношениях: разница в передаточном отношении i1 составляет 1273 – 126 = 0013 или
Для передаточного отношения i2 =1 погрешность отсутствует а для передаточного отношения i3 погрешность составит:
абсолютная погрешность составит: Относительная погрешность будет: что допустимо. Следовательно подбор чисел зубьев зубчатых колес для групповой передачи Ра (рис. 2.1) выполнен правильно.
Данные для подбора чисел зубьев пар зубчатых колес коробок передач
Продолжение таб. 2.1
После подбора чисел зубьев основной группы приступают к подбору чисел зубьев для первой переборной второй переборной и т. д. переборной групповых передач. Если групповые передачи не имеют связанных
зубчатых колес то модуль зубчатых колес первой переборной группы может быть отличающимся от модуля зубчатых колес основной группы.
Подбор чисел зубьев основной первой второй и т. д. переборной групп аналогичен описанному выше подбору.
2.10. Определение модуля зубчатых колес.
На основе известного из расчета режимов резания момента действующего на шпиндель а также передаточных отношений зубчатых пар определяют крутящие моменты действующие на каждую зубчатую пару т. е. на каждый вал. От найденных крутящих моментов переходят к усилиям действующим в зацеплении на основе методики курса “Детали машин” находят наиболее нагруженную зубчатую пару для которой определяют модуль исходя из прочности зуба на изгиб mизг и из усталости поверхностных слоев mпов по формулам:
где доп и Rв - допустимые напряжения для контактной нагрузки и на изгиб МПа; N=Nэл.дв - номинальная передаваемая мощность ( Nэл.дв – мощность электродвигателя кВт – к.п.д. передачи от электродвигателя до рассчитываемой шестерни); n - минимальная частота вращения шестерни (меньшего колеса зубчатой пары) на которую передается полная мощность обмин; y - коэффициент формы зуба; для z =18 50 y = 01 013; z - число зубьев шестерни; К1 К2 - коэффициенты учитывающие изменение нагрузки на зуб шестерни по сравнению с ее номинальным значением; - коэффициент ширины принимается равным 6 10.
Из полученных модулей mизг и mпов выбирают наибольший и округляют его до ближайшего большего стандартного значения: m =10; 15; 20; 25; 30; 40; 50; 60; 80; 100; 130; 160 мм.
Найденный стандартный модуль принимается одинаковым для всех зубчатых пар данной групповой передачи.
Реальное передаточное отношение через числа зубьев колес с использованием нормали станкостроения H21-5 приведена в табл.2.2
Числа зубьев для пар колес выбираем позже исходя из габаритов станка и условий прочности.
ГЕОМЕТРИЧЕСКИЙ И СИЛОВОЙ РАСЧЕТ ПРИВОДА
Так как для проектных расчетов нас интересует наиболее нагруженный режим то рассчитываем силовые и кинематические параметры для наименьших угловых скоростей валов.
Порядок и результаты расчета представлены в табл. 3.1
Минимальная частота вращения n мин-1
Минимальная угловая скорость радс
Максимальный вращающий момент Т
1 Геометрический расчет привода
Расчет геометрических параметров зубчатых колес.
Для первой ступени выбираем модуль m = 3
Делительный диаметр мм
Диаметр вершин зубьев мм
Диаметр впадин зубьев мм
Для второй ступени выбираем модуль m = 4
Для третьей ступени выбираем модуль m = 45
Диаметр впадин зубьев
Для конической пары шестерен выбираем модуль m = 45
Угол делительного конуса для обеих шестерен
Длина образующей делительного конуса
Диаметр делительной окружности мм
Диаметр окружности выступов мм
Диаметр окружности впадин мм
Для колес z = 60 выбираем модуль m = 4
Диаметр делительный мм
Расчет диаметров валов
Диаметр валов рассчитываются приближенно по формуле:
где М = Т – крутящий момент равный вращающему моменту на валу
- допускаемое напряжение на кручение
2 Расчет контактных напряжений и напряжений изгиба зубьев зубчатых колес привода.
Определим контактные напряжения в зацеплении Нмм2 по формулам:
для цилиндрических колес
для конических колес
К – вспомогательный коэффициент (для прямозубых колес К = 436)
- окружная сила в зацеплении
- коэффициент учитывающий распределение нагрузки между зубьями (для прямозубых колес = 1)
- коэффициент вида конических колес (для прямозубых колес =1)
Определим напряжения изгиба зубьев шестерни и колеса
и - коэффициент формы зуба шестерни и колеса
После определения контактных напряжений и напряжений изгиба подбираем материал и термообработку обеспечивающие прочность на изгиб и износостойкость.
Материал: для обоих колес Сталь 40Х
Термообработка: закалка по сечению HRCэ 45 50
Материал: для обоих колес Сталь 18ХГТ
Термообработка: закалка по сечению HRCэ 57 62; сердцевина
3 Силовой расчет валов коробки скоростей
Рис. 3.1 Эпюры моментов действующих на вал 1
Вертикальная плоскость
а) определим реакции в опорах
б) строим эпюру изгибающих моментов относительно оси Х:
Горизонтальная плоскость
Строим эпюру крутящих моментов
Определяем суммарные радиальные реакции
Определяем суммарный изгибающий момент в опасном сечении
Рис.3.2 Эпюры моментов действующих на вал II
б) строим эпюру изгибающих моментов относительно оси Y:
Рис. 3.3 Эпюры моментов действующих на вал III
Рис. 3.4 Эпюры моментов действующих на вал IV
4Проверочный расчет подшипников
Пригодность подшипников определяется сопоставлением расчетной динамической грузоподъемности .
Расчетная динамическая грузоподъемность определяется по формуле:
где m = 3 для шариковых подшипников
часов для зубчатых передач
- осевая нагрузка подшипника
- суммарная реакция подшипника
V – коэффициент вращения (V = 1)
Х – коэффициент радиальной нагрузки
- коэффициент безопасности
- температурный коэффициент (=1)
ОПИСАНИЕ УЗЛА СТАНКА
Поворотная головка центрируется в кольцевой виточке горловины станины и крепится к ней четырьмя болтами входящими в Т – образный паз фланца станины.
Шпиндель смонтирован на шариковых и роликовых подшипниках с внутренним натягом в гильзе которая может двигаться в вертикальной плоскости. Шпиндель получает вращение через пару конических и пару цилиндрических колес смонтированных в головке причем последнее колеса сидит на втулке. Так как втулка вращается на независимых подшипниках то усилия в зацеплении не передаются шпинделю которым связан со втулкой скользящими шпонками. Смазка подшипников осуществляется разбрызгиванием от централизованной системы смазки.
Перемещение гильзы осуществляется с помощью передачи винт – гайка скольжения.
Также в поворотной головке смонтировано устройство электромеханического зажима. Оно предназначено для закрепления инструмента в шпинделе станка. Затяжка и выталкивание инструмента производится с помощью тяги расположенной внутри шпинделя. Возвратно поступательное перемещение тяги обеспечивается резьбовым соединением ее со шлицевым валиком получающим вращательное движение от головки электромеханического зажима инструмента. На конце тяги имеется Т-образная головка которая соединяется с Т-образным пазом захвата ввернутого в оправку с фрезой.
ТЕМЫ КУРСОВЫХ ПРОЕКТОВ ОБЪЕМ И СТРУКТУРА РАСЧЕТНО-ПОЯСНИТЕЛЬНОЙ ЗАПИСКИ.
Курсовой проект по металлорежущим станкам выполняется по индивидуальному заданию под руководством руководителя проекта назначенного из числа преподавателей кафедры ТМС.
Темы курсовых проектов для студентов закрепляются по вариантам заданий представленных в табл. 1 6. Варианты заданий разбиты на шесть групп и при выборе соответствуют номеру студенческой группы (например гр. ЗТ-102 выполняет варианты заданий для первой группы гр. ЗТ-202 выполняет варианты заданий для второй группы) и так далее. Номер варианта задания соответствует порядковому номеру стоящему против фамилии студента в журнале учета посещаемости группы.
Темы курсовых проектов и исходные данные для их выполнения представлены в заданиях в виде буквенно-цифрового шифра который имеет следующий смысл. Цифра один и буква за ней указывают на модернизацию определенной модели станка цифра два и буква за ней – направление модернизации цифра три и буква за ней – материал обрабатываемых деталей цифра четыре и буква за ней – материал режущего инструмента цифра пять и буква за ней – серийность производства деталей. Кодировка вариантов заданий представлена в табл. 7. Например студент группы ЗТ-302 имеющий порядковый номер 7 в журнале учета посещаемости группы выполняет задние для третьей группы вариант №7 (см.табл.3) имеющее шифр – 1.Ю 2.Г 3.АБ 4.АБ 5Б. Это соответствует теме курсового проекта «Модернизация станка модели 6Р81» (см.табл.7). Рассчитать и сконструировать привод подач с переключением от электромагнитных муфт. Исходные данные – материалы обрабатываемых изделий - сталь чугун; материалы режущего инструмента – быстрорежущая сталь твердый сплав; серийность – мелкосерийное производство.
Студенты заочного факультета могут сами предложить темы курсовых проектов исходя из потребностей предприятия где они работают в модернизации металлорежущего оборудования проектировании его узлов и т.д.
Темы курсовых проектов должны быть актуальными и подчинены важнейшим задачам станкостроения должны базироваться на реальных исходных данных отвечать текущим и перспективным запросам технологии машиностроения. Темы курсовых проектов могут быть двух направлений:
-конструкторские темы по модернизации существующего универсального или специального оборудования;
-научно-исследовательские реферативные работы по анализу методов повышения работоспособности точности надежности долговечности возможностей максимального достижения технико-экономического эффекта станков или их основных узлов.
Каждый курсовой проект независимо от его вида должен состоять из расчетно-пояснительной записки и графической части.
Расчетно-пояснительная записка должна иметь 40—50 листов формата А4 машинного текста при выполнении проекта конструкторского характера и 60-80 листов при написании рефератов.
Расчетно-пояснительная записка пишется на одной стороне листа белой бумаги формата А4 по ГОСТ 2.301-72 с интервалом между строками 8-10 мм. Выравнивание текста с правой стороны не требуется. Вся текстовая документация проекта имеет основную надпись. Основная надпись аннотации как заглавного листа выполняется по форме 2 ГОСТ 2.104-72 (рис.5.1 а). Основная надпись всех последующих листов выполняется по форме 2а ГОСТ 2.104-72(рис.5.2. б).
Расстояние от рамки до границ текста рекомендуется оставлять: в начале строк – не менее 5 мм в конце строк - не менее 3 мм. Расстояние от верхней или нижней рамки документа должно быть не менее 10 мм. Расстояние между заголовком и последующим текстом должно быть равно трем межстрочным интервалам (от 24 до 30 мм). Расстояние между заголовком и последней строчкой предыдущего текста ( для тех случаев когда конец одного и начало другого подразделов размещаются на одной странице) должно равняться четырем межстрочным интервалам от 32 до 40 мм.
Рис.5.1. Основная надпись для расчетно-пояснительной записки:
а - заглавного листа; б - всех последующих листов
Нумерация листов пояснительной записки должна быть сквозной:
первым листом является титульный лист вторым – задание третьим – аннотация и т.д. Номер листа проставляют арабскими цифрами в основной надписи. На листах 1 и 2 (титульный лист и задание) номера листов не ставят.
Если в пояснительной записке содержатся рисунки и таблицы которые располагаются н отдельных листах их необходимо включать в общую нумерацию. Если рисунок или таблица расположены на листе формата больше А4 что не рекомендуется их следует учитывать как один лист. Номер листа в этих случаях можно не проставлять. Список литературы и приложения необходимо включать в сквозную нумерацию.
Все оформление расчетно-пояснительной записки должно соответствовать общим требованиям к текстовым документам по ГОСТ 2.105-72.(прил.3)
Расчетно-пояснительная записка должна включать в себя:
-задание на курсовой проект;
-содержание (оглавление);
Титульный лист (обложка) оформляются черными чернилами или тушью чертежным шрифтом размером 10; 5 и 35. Форма заполнения титульного листа показана в прил. 3.1
Титульный лист подписывается руководителем по окончании выполнения всего объема курсового проекта что дает право на защиту проекта на комиссии.
Задание на курсовой проект оформленное типографским способом выдается руководителем и заполняется студентом от руки в соответствии с его вариантом задания. Оно является основным документом определяющим содержание объем сроки и ход выполнения проекта.
Задание на курсовой проект подписывается руководителем проекта студентом принявшим его к исполнению и утверждается заведующим кафедрой.
Аннотация – должна давать краткую характеристику выполненному курсовому проекту и излагать краткие сведения о содержании проекта являющиеся вместе с тем достаточными для его оценки т.е. в сжатой форме (на 05 – 1 с) указываются наиболее важные вопросы решенные в проекте новшества и разработки сделанные студентом в проекте полученные результаты о модернизации (проектировании) станка (узла).
В содержании (оглавлении) последовательно перечисляют заголовки разделов подразделов и указывают номера страниц на которых они помещены. Содержание должно включать в себя все заголовки имеющиеся в расчетно-пояснительной записке и приложения. Пример оформления содержания приведен в прил.3.2
Основная часть расчетно-пояснительной записки курсового проекта конструкторского характера включает в себя разделы:
-обоснование технической характеристики привода;
- разработка кинематической схемы привода;
-динамический расчет основных деталей привода;
-выбор типа конструкции и расчет специального узла в направлении модернизации станка;
-общая компоновка привода описание конструкции и принципа действия;
-заключение (выводы и предложения).
Введение является органической частью расчетно-пояснительной записки и входит в ее состав. Введение должно кратко характеризовать современное состояние технического вопроса которому посвящен курсовой проект а также цель проекта. Во введении следует четко сформулировать в чем заключается новизна и актуальность рассматриваемого в проекте вопроса и обосновать по существу необходимость его выполнения.
Объем введения 2-3 листа.
Обоснование технической характеристики станка или отдельного привода производят на основе исходных данных задания и сводится к определению:
-оптимальных режимов обработки;
-предельных значений частот вращения шпинделя (числа двойных ходов стола) nma
-сил резания возникающих в процессе обработки;
-эффективной мощности привода и мощности электродвигателя.
Рекомендуемая литература по обоснованию технической характеристики станка [2 3 6 8 10 11 13 16 18 21 29 32 37 39 40].
Объем разделов 10 – 15 листов.
Разработка кинематической схемы привода включает:
-обоснование и выбор типа привода;
-выбор кинематической схемы;
-выбор типов и расчет передаточных отношений одиночных передач и всей кинематической цепи в целом.
К кинематике привода предъявляются следующие требования:
-обеспечение высокой производительности станка;
-максимальная автоматизация станка;
-точность работы механизмов;
-высокий к.п.д. привода;
-технологичность конструкции;
-максимальное использование стандартных и унифицированных узлов и деталей;
-простота и удобство сборки наладки и обслуживания;
-безопасность работы.
Рекомендуемая литература [14 15 17 19 22 24 26 27 29 31 41 49].
Объем раздела 7 – 10 листов.
Динамическому расчету подвергаются только основные детали привода – валы зубчатые колеса опоры и т.д. (по одному представителю каждого вида) с тем чтобы они удовлетворяли требованиям нормальной работоспособности под которой понимается работа детали без поломок и значительного износа в течение определенного срока например до ремонта.
Статический или динамический расчет резьбовых шлицевых соединений муфт ременных и других передач студентами производится но в состав расчетно-пояснительной записки не вносятся.
При уточненных расчетах следует пользоваться руководящими материалами 25. Расчетные формулы последовательность расчета и другие указания по расчету деталей и узлов станков приведены в литературе [5 9 23 24 25 26 27 32 33-36].
Объем данного раздела 10 – 12 листов.
Выбор типа конструкции и расчет специального узла производят исходя из направления модернизации например электромагнитных муфт или направляющих качения или шпинделя на гидростатических опорах и т.д. Рекомендуемая литература для раздела [4 5 7 10 12 23 24 33].
Разработка общей компоновки привода т.е объединение увязка его отдельных деталей узлов и механизмов является ответственным этапом в проектировании как самого привода так и станка в целом. Отдельные детали и узлы должны быть скомпонованы так чтобы привод был точным экономичным производительным удобным в обслуживании безопасным для работающего а также отвечал современным эстетическим требованиям.
При выборе схемы компоновки в зависимости от назначения привода необходимо обратить внимание на удобство установки и крепления привода на станке удобство установки и крепления в нем заготовки смены инструмента наладки и подналадки привода его смазки наблюдения за работой сборки и разборки привода его ремонта. Кроме того нужно обратить внимание на устойчивость и жесткость привода габаритные размеры его массу а также необходимо стремиться иметь в составе привода минимальное количество деталей и узлов.
После разработки общей компоновки привода и привязки его на станке производят описание конструкции и принципа его действия.
Рекомендуемая литература по разделу [10 12 14 24 27 30 31 34] .
Объем описания 2-3 листа.
Экономическая эффективность станка.
Модернизируемый (проектируемый) станок должен обладать высокими техническими свойствами и иметь технико-экономические преимущества перед существующими конструкциями. Эти преимущества могут заключаться в более высокой производительности уменьшении расхода электроэнергии и массы станка использовании унификации повышении качества изделий обрабатываемых на станке автоматизации управления и обслуживания станка уменьшении эксплуатационных и ремонтных расходов и др.
Обоснование конструкторских решений должно охватывать весь комплекс определяющих вопросов например выбор кинематической схемы привода и станка в целом; применение конструкционных материалов; использование стандартных деталей; удобство эксплуатации и сокращение эксплуатационных расходов; обеспечение повышения точности обрабатываемой детали надежности и долговечности станка и т.п. Если расчеты показывают что при сравнении двух вариантов станков (приводов) более низкая себестоимость производимой продукции может быть достигнута лишь при увеличении капиталовложений то вопрос об эффективности такого более дорогого варианта решается путем соизмерения дополнительных капитальных затрат с экономией на текущих затратах.
Модернизирование (проектирование) должно сопровождаться анализом всех перечисленных технико-экономических показателей модернизируемого станка или отдельного узла и существующих конструкций с обоснованием экономической целесообразности. Экономическая целесообразность создания нового варианта металлорежущего станка с определенными производственно-техническими параметрами должна быть подтверждена расчетами фактических затрат на производство станка (узла) и экономическим эффектом который получит народное хозяйство от внедрения нового варианта станка.
Для этого должны быть установлены количественные соотношения между величиной параметров станков и себестоимостью их производства а также между фактическими затратами и максимально доступной ценой.
Рекомендуемая литература по разделу [1 20 33].
Объем описания 4 –6 листов.
Заключение (выводы и предложения) должно содержать оценку результатов работы по выполнению курсового проекта в частности с точки зрения его соответствия требованиям задания.
Заглавием должно служить слово «Заключение» (либо фраза «Выводы и предложения») написанные на отдельной строке.
В заключении необходимо указать техническую научную социальную ценность результатов работы дается оценка технико-экономической эффективности которая может быть получена при использовании результатов курсового проекта в промышленности
Список литературы использованной в курсовом проекте составляют по правилам библиографии: фамилия и инициалы автора (авторов) название книги (журнала справочника и т.д.) место издания год издания.
Использованную литературу в списке следует располагать в порядке появления ссылок в тексте пояснительной записки или в алфавитном порядке.
При ссылке в тексте расчетно-пояснительной записки на источники документальной информации следует приводить порядковый номер по списку литературы заключенный в квадратные скобки.
Приложения оформляются как продолжение расчетно-пояснительной записки на последующих ее листах. В приложения поместить спецификацию на курсовой проект и другие материалы вспомогательного характера.
Каждое приложение начинают с новой страницы. В правом верхнем углу пишут слово «Приложение» и его номер. Каждое приложение должно иметь содержательный заголовок.
ОБЪЕМ И СОДЕРЖАНИЕ ГРАФИЧЕСКОЙ ЧАСТИ
Объем графической части курсового проекта должен составлять 4-5 листов формата А1 ГОСТ 2.301-72.
Примерное расположение материала проекта по листам следующее:
- общий вид и кинематическая (гидравлическая) схема станка – 1 лист;
-развертка коробки скоростей (подач) – 1 лист;
-свертка коробки скоростей (подач) – 1 лист;
-механизм управления или рабочий чертеж детали привода средней сложности 05– 10 лист;
-конструкция специального узла 05– 10 лист.
Чертежи рекомендуется выполнять в масштабе 1:1 применяя уменьшающие масштабы только для крупных станков.
Весь объем графической части оформляется в курсовом проекте как последнее по номеру самостоятельное (не сшитое с расчетно-пояснительной запиской) приложение о чем в разделе «Содержание» пояснительной записки делается запись с полном перечнем наименований и количества листов.
Например: Приложение 2. Графическая часть – 4-5 листов:
-общий вид и кинематическая схема станка – 1 лист;
-развертка коробки подач – 1 лист;
-свертка коробки подач – 1 лист;
-механизм переключения подач 05– 10 лист;
-шарико-винтовая передача 05– 10 лист.
Требования к графической части проекта основаны на выполнении чертежей в соответствии с единой системой конструкторской документации (ЕСКД).
Оформление сборочных чертежей осуществляется по ГОСТ 2.109-73. Они должны содержать:
-габаритные размеры;
-размеры и предельные отклонения (посадки) определяющие характер сопряжения;
-размеры и предельные отклонения которые должны быть выполнены или проконтролированы по данному сборочному чертежу (например межосевые расстояния);
-установочные и присоединительные размеры;
-номера позиций составных частей;
-основные характеристики изделия.
Кинематические схемы выполняют в соответствии с требованиями ГОСТ 2.703-72 а элементы на схемах изображают условными графическими обозначениями по ГОСТ 2.770-72.
Выполнение гидравлических и пневматических схем основано на соблюдении ГОСТ 2.701-72 и ГОСТ 2.704-72. Линии связи элементы сетей аппаратура управления насосы и двигатели выполняют по ГОСТ 2.721-72 2.780-72 2.781-72 2.782-72.
Основные надписи их форма размеры порядок заполнения в конструкторских документах выполняют в соответствии с ГОСТ 2.104-72. Содержание и расположение граф основных надписей дополнительных граф к ним а также размеры рамок на чертежах и схемах должны соответствовать форме 2 2 а (рис.5.1 а б) а в текстовых документах и спецификации – формам изображенным на рис 6.1 и рис 6.2 а б.
Основные надписи дополнительные графы к ним и рамки выполняются сплошными основными и сплошными тонкими линиями по ГОСТ 2.303-72.
Основные надписи располагаются в правом нижнем углу конструкторских документов.
В графах основной надписи дополнительных графах (номера граф на формах показаны в скобках) указывают (см.рис.5.1 а и рис.6.3):
В графе 1 – наименование изделия (в соответствии с требованиями ГОСТ 2.109-73) а также наименование документа если этому документу присвоен шифр;
В графе 2 – обозначение документа;
В графе 3 – обозначение материала детали (графу заполняют только на чертежах деталей);
В графе 4 – в левой клетке проставляется буква «У» - учебный;
В графе 5 - массу изделия по ГОСТ 2.109-73;
В графе 6 – масштаб (проставляется в соответствии с ГОСТ 2.302-72 и ГОСТ 2.109-73);
В графе 7 - порядковый номер листа;
В графе 8 – общее количество листов графической части проекта (графу заполняют только на первом листе);
В графе 11 – фамилии лиц подписывающих курсовой проект (студента руководителя);
В графе 12 – подписи лиц фамилии которых указаны в графе 11;
В графе 13 – дату подписания документа;
В графе 26 – обозначение документа повернутое на 1800.
Графы 10 14-25 27-33 студентом не заполняются.
Дополнительные графы 19-25 27-33 вводить не обязательно.
В соответствии с ГОСТ 2.102-72 2.701-72 и практикой станкостроительных заводов и КБ предлагаются обозначения документов в обезличенной системе по следующей схеме:
где КП - шифр курсового проекта;
01–шифр специальности;
Рис. 6.1. Основная надпись для конструкторской части проекта
Рис.6.2. Пример заполнения спецификации: а - первый (заглавный) лист
Рис.6.2 Пример заполнения спецификации: б - последующие листы
0.– обозначение сборки;
– обозначение подсборки;
0 – обозначение детали;
Рекомендуются следующие шифры документов входящих в состав курсового проекта:
-чертеж вид общий – ВО;
-сборочный чертеж – СБ;
-расчетно-пояснительная записка – ПЗ;
-другие документы – ДР.
Шифр схем входящих в состав конструкторской документации изделий должен состоять из буквы определяющей вид схемы и цифры обозначающей тип схемы.
Виды схем обозначаются следующими буквами: кинематическая –К; электрическая – Э; гидравлическая –Г; пневматическая – П; комбинированная – С.
Типы схем обозначаются следующими цифрами: структурная – 1; функциональная –2; принципиальная – 3; соединений -4; подключения –5; общая – 6; расположения – 7.
Обозначение сборки подсборки детали схемы образуются из порядкового номера сборки подсборки детали или вида и типа схемы. Например КП. 1201.001. 01. 002 – вторая деталь первой подсборки первой сборки или КП. 1201.000. 00. 000 К3 – кинематическая схема принципиальная.
На выполненный курсовой проект составляется спецификация по ГОСТ 2.108-72 оформленная как приложение расчетно-пояснительной записки.
В спецификацию курсового проекта входят разделы:
-стандартные изделия.
Наименование каждого раздела указывают в виде заголовка в графе «Наименование» и подчеркивают.
В раздел «Документация» вносят документы составляющие основной комплект конструкторских документов курсового проекта кроме его спецификации т.е. чертежи общего вида схемы расчетно-пояснительная записка.
Рис 6.3. Пример заполнения формы 1 при выполнении кинематиеской схемы станка (привода)
В разделы «Сборочные единицы» и «Детали» вносят сборочные единицы и детали непосредственно входящие в специфицируемое изделие.
В разделе «Стандартные изделия» записывают изделия примененные по государственным стандартам; отраслевым и республиканским стандартам; стандартам предприятий.
В пределах каждой категории стандартов запись производят по однородным группам например крепежные детали) в пределах каждой группы – в алфавитном порядке наименования изделий (например болты винты гайки и т.д.) в пределах каждого наименования – в порядке возрастания обозначений и стандартов а в пределах каждого обозначения стандартов – в порядке возрастания основных параметров или размеров изделия.
Графы спецификации заполняют следующим образом:
В графе «Формат» указывают форматы документов обозначения которых записывают в графе «Обозначение»; если документ выполнен на нескольких листах различных форматов то проставляют «звездочку» а в графе «Примечание» перечисляют все форматы.
Для документов записанных в раздел «Стандартные изделия» графу не заполняют.
Для деталей на которые не выпущены чертежи в графе указывают: БЧ (без чертежа).
Графу «Зона» в курсовом проекте не заполняют.
В графе «Поз.» указывают порядковые номера составных частей непосредственно входящих в специфицируемое изделие в последовательности записи их в спецификации; для раздела «Документация» номера позиций не присваивают.
В графе «Обозначение» указывают:
-в разделе «Документация» - обозначения записываемых документов;
-в разделах «Сборочные единицы» «Детали» - обозначения основных конструкторских документов на записываемые в эти разделы изделия;
-в разделе «Стандартные изделия» графу не заполняют.
В графе «Наименование» указывают:
-в разделе «Документация» для документов входящих в основной комплект документов специфицируемого изделия и составляемых на данное изделие - только наименования документов например «Чертеж общего вида»;
-в разделах спецификации «Сборочные единицы» «Детали» - наименования изделий в соответствии с основной надписью на основных конструкторских документах этих изделий; в раздел «Детали» вносят наименования деталей одной сборочной единицы по указанию руководителя;
-в разделе «Стандартные изделия» наименования и обозначения изделий в соответствии со стандартами на эти изделия.
В графе «Кол.» указывают:
- для составных частей изделия записываемых в спецификацию - количество их на одно специфицируемое изделие;
в разделе «Документация» графу не заполняют.
В графе «Примечание» указывают дополнительные сведения для планирования и организации производства а также другие сведения относящиеся к записанным в спецификацию изделиям и документам.
После каждого раздела спецификации необходимо оставлять несколько свободных строк для дополнительных записей.
Пример заполнения спецификации показан на рис.6.2 а – первый (заглавный) лист и на рис. 6.2 б – последующие листы.
Спецификация помещается в разделе «Приложения» расчетно-пояснительной записки.
ПОРЯДОК ВЫПОЛНЕНИЯ И ЗАЩИТЫ КУРСОВОГО ПРОЕКТА
Сроки начала и окончания курсового проекта определяются учебным планом. Общий срок выполнения проекта планируется в пределах десяти недель. Контрольные сроки выполнения основных этапов проекта и дата защиты указывают в задании на курсовой проект выдаваемом индивидуально каждому студенту.
Условием успешного и своевременного выполнения курсового проекта является еженедельная систематическая работа студента и строгое соблюдение сроков индивидуального задания что обеспечивается регулярностью консультаций у руководителя.
Законченный курсовой проект за два дня до защиты представляется для просмотра руководителю проекта который решает вопрос о допуске к защите на комиссии. Если проект выполнен не в соответствии с заданием или на низком уровне руководитель имеет право не подписывать проект и передать вопрос о допуске к защите на рассмотрение кафедры. Для представления проекта к защите на комиссии необходимо иметь подписи студента на расчетно-пояснительной записке (титульном листе заглавном листах и спецификации) и листах графической части проекта. При защите проекта студенту предоставляется слово для доклада на 7-10 минут. В докладе после изложения задания следует кратко осветить все узловые вопросы решенные в проекте. При этом можно рекомендовать придерживаться порядка принятого в пояснительной записке. Особое внимание должно быть уделено изложению и обоснованию спроектированных узлов. Следует четко выделить все то новое что внесено предложено или сконструировано самим студентом. В заключение надо отметить полученный в проекте технический эффект от модернизации или проектирования станка. Во время доклада студент имеет право пользоваться кратким конспектом.
При защите проекта члены комиссии могут задавать вопросы как по существу выполненной работы так и по различным разделам курса лекций на базе которых выполнялся проект.
Обязательным условием успешной защиты проекта является четкое представление о работе конструкции и ее отдельных узлов правильное обоснование выбора отдельных конструктивных элементов.
Если студент слабо разбирается в работе представленной им конструкции проект не защитывается. При определении дифференцированной оценки за проект комиссия учитывает:
Правильность обоснования выбора отдельных конструктивных элементов для заданного объекта производства и выполнения проектных расчетов.
Умение аргументировано ответить на заданные вопросы;
Содержание и характер оригинальной (самостоятельной) части проекта.
Художественную отработку деталей узлов и станка в целом.
Оформление расчетно-пояснительной записки и графической части проекта в соответствии с изложенными выше требованиями (выполнение требований ГОСТ и ЕСКД).
Своевременность получения задания регулярность консультирования и выполнение задания в срок.
Табличные данные необходимые для обоснования технических характеристик приводов.
Соответствие номера стола фрезерного
станка размерам его рабочей поверхности
П р и м е ч а н и е: в соответствии с ГОСТ 165-70 допускается применение столов размерами 100х400; 125х500; 160х320; 160х630.
Предельные значения диаметров червячных фрез
Значение коэффициента Сt
Значения припусков при фрезеровании стали
Припуск на обработку
Сталь 45ХНsв=650 МПа
Сталь 35Х sв=950 МПа
Сталь 15Х sв=400 МПа
Сталь 40Х sв=750 МПа
Сталь 15Г sв=400 МПа
Сталь 45Г sв=650 МПа
Сталь 15Г sв=500 МПа
Сталь 45ХН sв=650 МПа
Значение припусков при фрезеровании чугуна и цветных металлов
Припуски на обработку
Чугун СЧ32-52 НВ 220
Чугун СЧ21-40 НВ 170
Чугун СЧ21-40 НВ 200
Чугун СЧ15-32 НВ 170
Чугун СЧ32-52 НВ 190
Чугун СЧ21-40 НВ 210
Чугун СЧ32-52 НВ 210
Бронза Бр.ОЦ-3 НВ 70
Значение коэффициента и показателей степени
для расчета подач при токарной обработке
Материал обрабатываемой детали
Подачи при черновом наружном точении
Размер державки резца мм
Подача S ммоб при глубине резания t мм
Чугун и медные сплавы
Подачи при черновом растачивании на токарных
револьверных и расточных станка
Диаметр круглого сечения резца или размеры его сечения мм
Вылет резца или оправки
Подача S ммоб при глубине резании t мм
П р и м е ч а н и е: верхние пределы подач рекомендуется для меньшей глубины резания при обработке менее прочных материалов нижние - для большей глубины резания и более прочных материалов.
Подачи при черновом растачивании на карусельных станках
Вылет резца или оправки мм
Подача S ммоб при глубине резца t мм
Подачи для чистовой токарной обработки
Класс шероховатости поверхности
Радиус при вершине резца мм
Сталь углеродистая и легированная
Чугун бронза и алюминиевые сплавы
П р и м е ч а н и е: 1. При обработке стали со скоростью V>50 ммин подачу увеличить вводя поправочный коэффициент 125.
При обработке жаропрочной стали и титановых сплавов с V>50 ммин подачу уменьшить вводя поправочный коэффициент 07-08
Значение коэффициента Сs
Обрабатываемый материал
Конструкционная сталь
Чугун(НВ 170) и цветные материалы
П р и м е ч а н и е: для сверл оснащенных твердым сплавом (ВК8) рекомендуется
Сs = 01 при сверлении чугуна НВ 200 и Сs = 007 для чугуна НВ > 200.
Подача при сверлении зенкеровании и развертывании стали чугуна медных и алюминиевых сплавов инструментами из быстрорежущей стали
Диаметр инструмента D мм
Сталь и стальное литье
Чугун серый и ковкий медные и алюминиевые сплавы
П р и м е ч а н и я 1. приведенную для сверления подачу применяют при сверлении отверстий в жестких деталях с допуском не выше 10 квалитета точности под последующую обработку сверлом зенкером или резцом при глубине сверления l 5D. Подачу следует уменьшать: при l = 5D на 10 % при l = 10D на 25 %. Подачу также следует уменьшить учитывая технологические факторы:
а) при сверлении отверстий в деталях средней жесткости с допуском не выше 10 квалитета точности или под последующую обработку сверлом зенкером или резцом вводя коэффициент 075 ;
б) при сверлении точных отверстий под последующую обработку развертками или под нарезание резьбы метчиками при сверлении центровочными сверлами при сверлении отверстий в деталях малой жесткости и с неустойчивыми опорными поверхностями вводя коэффициент 05;
приведенную для зенкерования подачу применяют когда допуск на отверстие не превышает 10-го квалитета точности или под последующую обработку зенкером и разверткой или двумя развертками. Подачу следует уменьшить при зенкеровании отверстий по 8-му 9-му квалитетам точности с малой глубиной резания при повышенных требованиях к шероховатости поверхности при последующей обработке одной разверткой или нарезании резьбы метчиком вводя коэффициент 07.
Подача на зуб при фрезеровании черных и цветных металлов
Величина снимаемого припуска за один проход мм
Дисковые трехсторонние
П р и м е ч а н и е: при обработке бронзы и чугуна подачу надлежит увеличить в 15-2 раза в зависимости от условий обработки; при черновой обработке и последующими чистовыми проходами подачу можно увеличить в 15-2 раза.
Подачи при фрезеровании торцевыми фрезерными головками
Черновая обработка- подача на зуб фрезы Sz мм
Обрабатываемый металл
Марка твердого сплава и условия обработки
П р и м е ч а н и е: при чистовой обработке (подача на один оборот фрезы S0 ммоб) для получения шероховатости - S = 045-07 ммоб; при - S0 = 03-035 ммоб.
Значения коэффициента СS и показателей степени х y z
для расчета чистовых подач при фрезеровании
Значение коэффициента СV и показателей степени
для расчета скорости детали при шлифовании
Значения коэффициентов и показателей степени
ной подачей на двойной ход
Бесцентровое на проход
Бесцентровое врезное
Плоское периферией круга
Плоское торцем круга
П р и м е ч а н и е: материал заготовки – незакаленная сталь; при шлифовании заготовок из закаленных сталей скорость вращения (или перемещения) уменьшают на 5-10%
Величины подач при зубонарезании
Подача S в мм на один оборот или в мм на один двойной ход
Зубофрезерование однозаходной червячной фрезой:
Нарезание шлицевых валиков червячной фрезой:
Зубодолбление долбяком 75 мм
Подачи при нарезании цилиндрических зубчатых колес из стали 35 и 45 с НВ 156-207
Однородными червячными фрезами из быстрорежущей стали
Подача на один оборот заготовки S обмин
Для чернового нарезания при мощности
зубофрезерного станка кВт
Для чистового нарезания
По сплошному металлу
П р и м е ч а н и я: 1. При черновой обработке колес из чугуна НВ 170-210 подачу увеличивать на 10%. 2 Для многозаходных червячных фрез подачи уменьшать: при двух заходах - на 25% при трех - на 35%. 3. Для фрез с заточкой по задней грани (острозаточенных) подачи увеличивать на 20% . 4. При попутном фрезеровании подачи увеличивать на 20-25%. 5. При нарезании косозубых колес с углом наклона зуба b значение подач умножить на cos b.
Подачи при нарезании цилиндрических зубчатых колес из стали 35 и 45 с НВ 156-207 дисковыми модульными фрезами
временно работающих фрез
Подача на один оборот фрезы S мм
Зубофрезерные и горизонтальные станки
Зубофрезерные станки
Подачи при нарезании цилиндрических зубчатых колес из стали 35 и 45
с НВ 156-207 дисковыми долбяками из быстрорежущей стали
Подача круговая Sк ммдв.ход при мощности зубодолбежного станка кВт
Черновая в один проход под последующую чистовую обработку долбяком.
Чистовая по 6-му классу чистоты:
по сплошному материалу
по предельному обработанному зубу
Подачи при фрезеровании шлицевых валов из стали 35 и 45 с НВ 156-207
червячными шлицевыми фрезами из быстрорежущей стали
Подача на один оборот заготовки обмм
Черновая под шлифование
Чистовая по сплошному материалу ()
П р и м е ч а н и е: при черновой обработке червячными фрезами с усиками подачу уменьшать на 15%.
Поправочный коэффициент на подачу учитывающий механические
Сталь конструкционная
Сталь конструкционная легированная
ХН4А 20ХНМ 18ХГТ 12ХН3 20х
Коэффициент КМ при НВ
Подачи при нарезании червячных колес из серого чугуна НВ 170-210 и из бронзы НВ 120 червячными фрезами из быстрорежущей стали
Подача на один оборот заготовки мм
П р и м е ч а н и е: при нарезании многозаходных колес подачу уменьшить пропорционально числу заходов.
Значение коэффициентов и показателей степени
для определения скорости при токарной обработке
Материал режущей части инструмента
Быстрорежущая сталь
Точение и растачивание
Проверка канавок и отрезка
в формулах скорости при обработке отверстий
Сверление деталей из стали с НВ155
Сверление деталей из стали с НВ>155
Развертывание деталей из стали с НВ155
Развертывание деталей из стали с НВ>155
Рассверливание деталей из стали с НВ155
Раcсверливание деталей из стали с НВ>155
Зенкерование деталей из стали с НВ155
Зенкерование деталей из стали с НВ>155
Значение коэффициентов и показателей степени
в формулах скорости при фрезеровании
Торцевое фрезерование
Цилиндрическое фрезерование
Отрезка и прорезка пазов
в формулах скорости резания при нарезании зубчатых колес и шлицевых валов
коэффициенты и показатели степени
Фрезы червичные модульные :
Долбяки зуборезные дисковые
Фрезы червячные для шлице
с наружным центрированием(без усиков)
с внутренним центрированием (с усиками)
Фрезы дисковые модульные
Чугун серый НВ 170-210
Поправочный коэффициент К учитывающий влияние механических свойств конструкционной стали на скорость резания
ХН4А; 20ХНМ;18Х1Т; 12ХН3; 20Х
Поправочные коэффициенты на скорость резания в зависимости от конструкционных особенностей инструментов и других факторов
Факторы влияющие на скорость резания
Наименование инструмента
Значения влияющих факторов и величины коэффициента
Осевые перемещения инструмента
Фрезы червячные модульные
Фрезы червячные модульные и шлицевые
Фрезы червячные модульные при обработке стали
Число заходов 1 2 3 -
Коэффициент К 10 085 075
Количество 0 1 2 3 3
Коэффициент К 10 11 12 13 -
Класс точности С В А
Коэффициент К 10 08 -
Шлицы шлицевого вала
Положение зубьев нарезаемого колеса
Количество зубьев нарезаемого колеса
Фрезы червячные шлицевые
Фрезы червячные модульные и долбяки дисковые
Профиль зуба С уси- без уси
Коэффициент К 085 10
Число шлицев 4 6 8 10 16 20
Коэффициент К 085 10 11 12 14 15
Угол наклона 0 15 30 45 60
Коэффициент К 01 09 08 07
Число зубьев 12 30 40 80 120
Значения поправочного коэффициента К
Продольно-строгальный
Поперечно-строгальный
Скорости резания допускаемые станками и инструментом ммин
Перспективы увеличения скорости резания
Допускаемая станками
Допускаемая инструментами
Фактическая применяемая в промышленности
0-500 (минерало- керамика)
Коэффициенты и показатели степеней при расчете сил резания
Точение растачивание
Фрезерование торцевыми дисковыми и отрезными фрезами
Фрезерование фасонными и угловыми фрезами
Точение растачивание строгание
Отрезка и прорезка резцами
П р и м е ч а н и е: * при НВ ≤ 170
Значения коэффициентов и показателей степени для определения мощности при шлифовании
Круглое наружное с поперечной подачей на двойной ход стола
Круглое наружное врезное
Внутреннее с поперечной подачей
Плоское периферией круга на станках с прямоугольным столом
Плоское торцем круга на станках
Варианты заданий на курсовой проект
Варианты заданий для 1-й группы курса
режущего инструмента
Варианты заданий для 2-й группы курса
Варианты заданий для 3-й группы курса
Варианты заданий для 4-й группы курса
Варианты заданий для 5-й группы курса
Варианты заданий для 6-й группы курса
Кодирование вариантов заданий
Модернизировать станок модели
Рассчитать и сконструировать
Привод главного движения с расширенным диапазоном регулирования
Привод подач с расширенным диапазоном регулирования
Привод главного движения с переключением скоростей от электромагнитных муфт
Привод подач с переключением скоростей от электромагнитных муфт
Привод подач с применением винтовой шариковой пары
Привод подач с применением гидростатической винтовой пары
Привод подач с применением несоосной винтовой пары
Привод подач с перемещением стола на аэростатических направлениях
Привод подач с перемещением стола на гидростатических направлениях
Привод подач с перемещением стола на направляющих качения
Шпиндель станка на аэростатических опорах
Шпиндель станка на гидростатических опорах
О к о н ч а н и е т а б л. 7
Шпиндель станка на гидродинамических опорах
Привод подач с бесступенчатым регулированием скоростей
Привод главного движения с бесступенчатым регулированием скоростей
Привод подач с предварительным набором скоростей
Привод главного движения с предварительным набором скоростей
Гидросхема привода подач
Материалы обрабатываемых изделий
сталь чугун цветные сплавы пластмассы
Материалы режущего инструмента
быстрорежущий твердосплавный абразивный алмазный
Серийность производства
индивидуальное мелкосерийное серийное крупносерийное
СПИСОК РЕКОМЕНДУЕМОЙ ЛИТЕРАТУРЫ.
Агурский М.С. Экономическая эффективность автоматизации металлорежущих станков. М.; 1968.
Аршинов В.А. Алексеев Г.А. Резание металлов и режущий инструмент. М.; 1975.
Бушуев В.В. Основы проектирования станков. – М. 1992. – 407 с.
Ващук Н.М. Справочник по расчету металлорежущих станков . Красноярск1965.
Воробьева Т.М. Электромагнитные муфты. М.-Л.1960.
Гжиров Р.И. Серебреницкий П.П. Программирование обработки на станках с ЧПУ: Справ. – Л. 1990. – 588 с.
Гидравлическое оборудование. Каталог-справочник. Ч.1 и 2. 1967.
Гусев В.Г. Жарков В.Н. Методическое указание по оформлению технологической дукоментации при выполнении курсовых и дипломных прпоектов. – Владимир 1998. – 56 с.
Данилевский В.В. Технология машиностроения. М. 1972.
Детали и механизмы металлорежущих станков Под ред. Д.Н. Решетова. Т.1 и 2. М. 1972.
Егоров М.Е. Дементьев И.К. Дмитриева В.А. Технология машиностроения. М.1976.
Ермаков В.В. Гидравлический привод металлорежущих станков. М. 1963.
Зазарский Е.М. Жолнерчик С.И. Технология обработки деталей на станках с программным управлением. Л. 1975.
Игумнов Б.Н. Расчет оптимальных режимов обработки для станков и автоматическиских линий. М. 1974.
Кедров С.С. Колебание металлорежущих станков. М.: Машиностроение 1978. 199 с.
Ильичев Д.Д. Системы с электромагнитными муфтами. М.-Л. 1965.
Ковшев А.Н. Технология машиностроения: Учеб. – М. 1987. – 320 с.
Колесов И.Н. Основы технологии машиностроения: Учеб. – М. 1999. – 591 с.
Корсаков В.С. Основы технологии машиностроения. М. 1974.
Кочергин А.И. Конструирование и расчет металлорежущих станков и станочных комплексов. – Минск 1991- 301 с.
Кучер И.М. Металлорежущие станки. Основы конструирования и расчета. Л. 1971.
Левашов А.В. Основы расчета точности кинематических цепей металлорежущих станков. М. 1966. -212 с.
Левина Э.М. Расчет жесткости современных шпиндельных подшипников. Станки и инструменты 1982 №10 с.1-3.
Левина Э.М. Решетова Д.Н. Контактная жесткость машин. М.: Машиностроение 1971. 231 с.
Металлорежущие станки и инструменты: Учебник машиностроительных втузов Под ред. А.С. Проникова. – М.: Машиностроение 1981. 497 с. ил.
Малов А.Н. Справочник технолога-машиностроителя. Т.1 и 2. М. 1970.
Маталин А.А Дашевский Т.Б. Княжицкий И.И.Многооперацион-
a.ные станки. М. 1974.
Миллер Э.Э. техническое нормирование труда в машиностроении. М. 1972.
Монахов Г.А. Станки с программным управлением. Справочник. М. 1975.
Новожилов В.И. Экономика использования металлорежущего оборудования. Л. 1977.
Общемашиностроительные нормативы режимов резания для технического нормирования работ на металлорежущих станках. Ч.1. и 2. М. 1974.
Проников А.С. Расчет и конструирование металлорежущих станков. М. 1967.
Пронин Б.А. Ревков Г.А. Бесступенчатые клиноременные и фрикционные передачи (вариаторы). М. 1967.
Пуш В.Э. Конструирование металлорежущих станков. М. 1977.
Пуш А.В. Шпиндельные узлы: качество и надежность. М.: Машиностроение 1992. 288 с.
Рабинович А.Н. Смилянский В.И. Милевский Э. Коробки скоростей металлорежущих станков.Изд. Львовского университета. 1968 376 с.
Расчетные нагрузки станков. Руководящие материалы. М. ЭНИМС ОТМИ1964.
Свирцевский Ю.И. Макейчик Н.Н. Расчет и конструирование коробок скоростей и подач. Минск 1976.
Спиридонов А.А. Федоров В.Б. Металлорежущие станки с программным управлением. М. 1977.
Справочник технолога-машиностроителя. Т.1 и 2 Под ред. Н.С. Кована. М. 1972.
Режимы резания металлов. Справочник Под ред. Ю.В. Барановского. М. 1972.
Станки с программным управлением. Справочник. М. 1975.
Тарзиманов Г.А. Проектирование металлорежущих станков. М.: Машиностроение. 1980. 242 с.
Фигатнер А.М. Прецизионные подшипники качения современных металлорежущих станков. М.: НИИМАШ 1981. 72 с.
Шаумян Г.А. Комплексная механизация производственных процессов. М. 1973.
Экономическая эффективность станков с числовым программным управлением. Киев 1976.
Обоснование технических характеристик проектируемых приводов
Разработка кинематической схемы проектируемого привода
Геометрический и силовой расчет привода ..
Описание узла станка ..
Темы курсовых проектов объем и структура расчетно-пояснительной записки .
Объем и содержание графической части ..
Порядок выполнения и защиты курсового проекта .
Приложение 1. Табличные данные необходимые для обоснования технических характеристик приводов ..
Приложение 2. Варианты заданий на курсовой проект .
Приложение 3. Пример выполнения и оформления курсового проекта ..
П 3.1 Оформление титульного листа
П 3.2 Оформление содержания проекта ..
П 3.3 Пример выполнения и оформления пояснительной записки ..
П 3.4 Пример выполнения и оформления графической части ..
Список рекомендуемой литературы .
Рекомендуемые чертежи
- 25.10.2022