Разработка технологической оснастки для изготовления детали Корпус малый 342.05.01.072-А




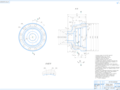
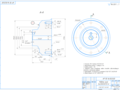
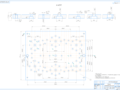
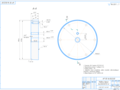
- Добавлен: 25.01.2023
- Размер: 2 MB
- Закачек: 0
Описание
Состав проекта
![]() |
![]() |
![]() ![]() ![]() ![]() |
![]() ![]() ![]() ![]() |
![]() ![]() ![]() ![]() |
![]() ![]() ![]() ![]() |
![]() |
![]() ![]() ![]() |
![]() ![]() ![]() |
![]() ![]() ![]() |
![]() ![]() ![]() |
![]() ![]() ![]() |
![]() ![]() ![]() |
![]() ![]() ![]() |
![]() ![]() ![]() |
![]() ![]() ![]() |
![]() ![]() ![]() |
![]() ![]() ![]() |
![]() |
![]() |
![]() |
Дополнительная информация
Модель верха 342.05.01.072-А _ КР ПО 16.10.02.00.cdw

Точность МК-5 металл ГОСТ3212-92.
Неуказанные уклоны 2°
Дефекты литья исправлять любым способом
точность и прочность моделей.
Общие допуски по ГОСТ 30893.2-тК.
Модель низа 342.05.01.072-А _ КР ПО 16.10.03.00.cdw

Точность МК-5 металл ГОСТ3212-92.
Неуказанные уклоны 2°
Дефекты литья исправлять любым способом
точность и прочность моделей.
Маркировать: 342.05.01.072-А шрифтом 8 Пр3 ГОСТ 26.020-80.
Общие допуски по ГОСТ 30893.2-тК.
Плита подмодельная низа _ КР ПО 16.10.04.00.cdw

Маркировать 342.05.01.072-А
1-0280-9303 шрифтом 10 Пр3
Общие допуски по ГОСТ 30893.2-тК.
Остальные технические требования по СТБ 1014-95.
Корпус малый 342.05.01.072-А _ КР ПО 16.10.01.00.cdw

Точность отливки 9-8-12-10 ГОСТ 26645-85.
Формовочные уклоны по ГОСТ 3212-92.
Неуказанные литейные радиусы 8 10 мм.
Твердость согласно ГОСТ 7293-85.
Материал-заменитель ВЧ50 ГОСТ 7293-85.
подлежащих обработке
исправлений любые дефекты (кроме трещин)
припуска на механическую обработку.
На необрабатываемых поверхностях отливки допускаются
газовые раковины диаметром не более 3 мм и глубиной не более 2
мм до 5на площади 100 см.
На обработанных поверхностях отливки допускаются одиночные
раковины диаметром не более 3 мм и глубиной не более 2 мм до 5
шт. на площади 100 см.
превышающие допустимые по чертежу нормы
допускается исправлять любым способом. обеспечивающим
прочность детали и не ухудшающим ее вид.
Остальные технические требования по ГОСТ 26358-87.
Маркировать обозначение отливки
завода-изготовителя шрифт 10ПрЗ ГОСТ 26.820-80.
Общие допуски по ГОСТ 30893.2-тК.
- база мех. обработки.
2 ОБОСНОВАНИЕ ВЫБОРА СПОСОБА ФОРМОВКИ.docx
Одним из наиболее активно внедряемых в производство способов для получения качественных литейных песчано-глинистых форм является Сейацу-процесс — способ уплотнения воздушным импульсом после которого происходит подпрессовка многоплунжерной головкой прессовой колодкой или другими способами. Ведущим поставщиком данного оборудования является фирма Heinrich Wagner Sinto которая предлагает свое оборудование литейным предприятиям во многих странах мира [3 с. 11–15].
С 1983 г. HWS использует для уплотнения формовочной смеси с глинистым связующим только метод формовки «Сейацу» — воздушным потоком с подпрессовкой.
Отличие метода: рыхлая насыпанная формовочная смесь уплотняется воздушным потоком и последующим прессованием.
Воздух проходит через смесь с обратной стороны формы по направлению к модели и уходит через венты на подмодельной плите и на держателе подмодельных плит. Смесь стекает с воздушным потоком в более низкие участки модели и достигает наибольшего предварительного уплотнения вблизи поверхности модели. Окончательную плотность форма получает в результате дополнительного прессования с помощью твердой или эластичной прессовой плиты водяной подушки или много плунжерного пресса. Величину усилия пресса а также напор и продолжительность воздушного потока можно регулировать. Благодаря этому для каждого случая применения можно достигать оптимальной прочности формы.
Преимущества метода «Сейацу»:
- высокое и равномерное уплотнение по всей толщина слоя смеси;
- возможность формования сложных контуров модели и выступающих болванов;
- уменьшение уклона формы;
- уменьшение удаления модели от стенки опоки и расстояния между моделями;
- уменьшение затрат на очистку благодаря получению отливки с минимальным гратом и с прекрасным качеством поверхности;
- метод «Сейацу» — малошумное формование благоприятное для окружающей среды без сотрясений и с уровнем шума менее 85 Дб [4 с. 224–225].
1 Конструктивные элементы для метода «Сейацу»
Станции автоматической смены моделей позволяют заменять комплектную модельную оснастку в пределах рабочего цикла.
Подъемный стол поднимает использованную модельную оснастку с поворотного стола и опускает на его новую приводные рольганги подают и отводят комплектные модельные оснастки.
Модельная оснастка состоит из держателя подмодельных плит и сменной подмодельной плиты. Держатели плит оснащаются на заводе стационарным венцом из вент для отвода уплотняющего воздуха. При необходимости их можно снабдить нагревательными элементами. Каждая подмодельная плита получает кодовый номер под которым хранятся все параметры для изготовления формы.
Устройство дозирования смеси устанавливается с возможностью перемещения и опирается на элемент взвешивания который прекращает подачу смеси как только в бункере будет достигнуто запрограммированное количество смеси. Засыпанная смесь равномерно распределяется в форме посредством жалюзийных заслонок на выходе из бункера-дозатора. Под этими заслонками находится устройство для нанесения на модель разделительного средства. Устройство дозирования смеси может быть дополнительно оснащено аэратором.
Клапан «Сейацу» — это тарельчатый клапан с гидравлическим управлением который в доли секунды открывает большое сечение и пропускает воздушный поток для первичного уплотнения смеси. Продолжительность открытия и ход тарелки клапана могут устанавливаться индивидуально чтобы обеспечить оптимальные условия для первичного уплотнения формы.
Формовочные линии HWS оснащаются центральной гидростанцией которая размещается в основном в отдельном подвальном помещении. Благодаря этому можно постоянно следить за всем объемом циркулирующей жидости очищать ее и поддерживать рабочую температуру. Клапаны монтируются на блоках гидрораспределителей так что их можно демонтировать без отсоединения трубопроводов. Для управления процессами перемещений используются в основном пропорциональные клапаны и сервоклапаны фирмы «Рексрот». Гидроцилиндры изготовляются своими силами на фирме HWS.
Формовочные линии HWS нового поколения оснащаются децентрализованными электронными устройствами управления. Они состоят из шкафа управления с центральным прибором автоматизации и нескольких местных пультов управления располагаемых в секторе обозреваемых групп устройств. На местных пультах размещаются панели операторов ряда «Сименс Корос» позволяющие контролировать и корректировать функции линии. Связь между прибором автоматизации и панелью оператора осуществляется по 2-жильной шипе или посредством световодов [4 с. 225–227].
2 Формовочные линии по методу «Сейацу»
Формовочные линии относятся к стандартному оснащению современных литейных предприятий. На них изготовляется большое количество точных форм с высокой точностью воспроизведения при малом числе обслуживающего персонала.
Обычно формовочная линия состоит из участка формовки центральным элементом которого является формовочная машина участков заливки и охлаждения и участка выбивки. Изготовление форм производится автоматически. Все движения подъема поворота и передачи форм совершаются в пределах времени цикла линии. Ручные операции сведены до минимума.
Пустые и очищенные внутри опоки передвигаются на участок формовки и после тщательного контроля наружных конгуров и поверхностей прилегания подаются в формовочную машину. Требуемое количество смеси взвешивается в устройстве дозирования и равномерно распределяется по форме посредством жалюзийных заслонок.
На бункере может устанавливаться аэратор песка создающий слои «воздушного» песка непосредственно на модели. Для первичного уплотнения воздушным потоком открывается клапан «Сейацу» с гидравлическим управлением. Вторичное уплотнение производится с помощью гидравлического пресса и прессовой плиты или многоплунжерным прессом.
Перемещаемая вручную тележка для смены моделей или станция автоматической смены моделей позволяют быстро заменять комплектную модельную оснастку.
После выхода из машины полуформы кантуются таким образом чтобы поверхность формы была повернута вверх.
Пока в нижних опоках проставляются стержни в верхних опоках фрезеруются заливочные воронки и создаются вентиляционные отверстия на обратной стороне формы.
После обратного кантования верхних опок формы спариваются и передаются обычно на транспортных тележках по участкам заливки и охлаждения. Залитые и охлажденные формы попадают наконец на участок выбивки. Там ком смеси с отливкой выдавливается и передается на выбивную решетку. Пустые опоки очищаются от остатков смеси и передаются обратно на участок формовки.
Преимущества формовочных линий HWS:
- современные формовочные линии в состоянии экономично изготовлять и небольшие серии так как смена модели может осуществляться в пределах времени тактового цикла. Для одной и той же линии можно использовать различные виды смесей применять опоки различной высоты и заливать различные металлы;
- параметры для изготовления формы такие как количество смеси усилие и продолжительность прессования можно программировать и запоминать в зависимости от той или иной модели. Они определяют также позиции заливочных воронок и вентиляционных отверстий и регулируют прохождение форм по участкам охлаждения;
- длительность охлаждения можно устанавливать различной в зависимости от формуемой модели и имеется возможность прослеживать путь каждой опоки до участка выбивки на экране;
- компьютеры контролируют работу линии сообщают ее рабочее состояние на данный момент составляют протоколы и подают сообщение о месте возникшей неполадки.
Решающим моментом для оценки формовочной линии является производительность метода формования. HWS с 1983 г. использует только метод формовки «Сейацу» чтобы изготовлять точные по размеру формы с большой точностью воспроизведения с сохранением самой модели и с заботой об охране окружающей среды. Формовочные линии HWS до малейших деталей приспособлены к сложным условиям работы литейного предприятия. В цехах завода тщательно обрабатываются и монтируются проверенные временем конструкции. Они оснащаются надежными компонентами ведущих изготовителей гидравлики электрики и электроники [4 с. 227–229].
!1ТИТУЛЬНЫЙ ЛИСТ.docx
Учреждение образования
«Гомельский государственный технический университет
имени П. О. Сухого»
По дисциплине: Проектирование оснастки
(наименование учебной дисциплины согласно учебному плану)
ПОЯСНИТЕЛЬНАЯ ЗАПИСКА
Тема: «Разработка технологической оснастки для изготовления детали "Корпус малый 342.05.01.072-A"»
(должность) (подпись) (Ф.И.О.)
1 ОЦЕНКА ТЕХНОЛОГИЧНОСТИ ЛИТОЙ ДЕТАЛИ.docx
Анализ технологичности литой детали учитывает опыт производства подобных отливок и технические возможности предприятия-изготовителя. При определении недостатков в конструкции литой детали вызывающих возникновение брака из-за технологичности рассматривают общую конфигурацию детали основные размеры включая толщину стенок ребер и массивность сечений в различных зонах материал детали технические требований к ней. Одновременно проводится анализ экономической и технической целесообразности намечаемого метода изготовления отливки с учетом всех технологических особенностей обосновываются положение отливки в форме разъем модели формы число стержней конструкция литниковой системы наличие прибылей холодильников и т.п.
Конструкция литой детали должна удовлетворять следующим основным требованиям:
- функциональному назначению и качественным показателям (прочность точность жесткость надежность эстетичность и др.);
- возможности получения детали в литом состоянии с наименьшими экономическими затратами;
- удобству механической обработки;
- простоте и удобству сборки монтажа машины изделия.
Все требования предъявляемые к литой детали можно выполнить лишь при условии что ее конструкция будет отвечать как требованиям технологии механической обработки так и литейной технологии. Технологичной с точки зрения литейного производства считается деталь конструкция которой учитывает специфические особенности изготовления формы в целом и отдельных ее элементов явления происходящие в форме при заливке и кристаллизации сплава
а также необходимость легкой выбивки и очистки отливки [2 с. 315].
Внешние очертания отливки «Корпус малый 342.05.01.072-А» представляют собой тело вращения с переменными цилиндрами диаметрами 183.5 160 100 90 76 мм. Габаритные размеры отливки: 183.5 высота 125 мм. Имеются внутрнние
сквозные отверстия переменного диаметра: 125 119 76 45 мм. Также в нижней части отливки распологается сферическое отверстие 136 мм (рис. 1.1).
Рисунок 1.1 — Чертеж отливки «Корпус малый 342.05.01.072-А»
Толщина расположение и форма стенок отливки способствуют спокойному заполнению формы сплавом. Литая деталь равностенна с правильными переходами от тонких сечений к толстым без больших местных скоплений металла и острых углов что исключает дефекты усадочного характера усадочные раковины пористость и трещины. Переход от одного сечения к другому оформлен галтелью.
Поверхность разъема — плоская. Отливка располагается в двух полуформах. Внутреняя полость отливки будет выполняться с помощью стержня. Отверстия на фланце изготавливаются механической обработкой.
Литая деталь «Корпус малый 342.05.01.072-А» сводит к минимуму затраты труда и материалов для изготовления модельного комплекта. Используется минимальное число стержней что повышает размерную точность и качество отливок снижает трудозатраты на изготовление дополнительных стержневых ящиков и др. элементов модельного комплекта.
На основании вышеперечисленных фактов можно сделать вывод что деталь «Корпус малый 342.05.01.072-А» в полной мере является технологичной.
6 РАСЧЕТ ОСНОВНЫХ РАЗМЕРОВ ПРОМОДЕЛИ.docx
Металлические модели изготавливаются литьем в песчано-глинистые формы по деревянным промоделям.
Промодели изготавливаются отдельно для верхней и нижней полуформ. При
конструировании промоделей учитывается суммарная усадка металла модели и отливки а также припуски на механическую обработку поверхностей промодели и модели. Суммарная величина усадки материала СЧ20 и ВЧ45 по ГОСТ 1412–85 и ГОСТ 7293–85 соответственно равна 22%.
Высота верхней промодели определяется как сумма высоты детали () припуска на механическую обработку поверхностей модели () и промодели () умноженная на суммарный процент усадки литейных сплавов:
Для верхней промодели технология представлена на рисунке 6.1.
Рисунок 6.1 – Эскиз верхней промодели
Высота нижней промодели определяется аналогичным образом как и для верхней промодели:
Для нижней промодели технология представлена на рисунке 6.2.
Рисунок 6.2 – Эскиз нижней промодели
!ВВЕДЕНИЕ.docx
Для изготовления отливок применяется большое число различных приспособлений которые называют литейной оснасткой. Часть литейной оснастки включающей все технологические приспособления необходимые для получения в форме отпечатка модели отливки называют молельным комплектом.
Модельный комплект состоит из модели отливки и моделей элементов литниково-питающей системы; стержневых ящиков; модельных плит для установки или крепления модели отливки и моделей литниковой системы; сушильных плит и приспособлений для доводки и контроля форм и стержней.
При формовке кроме модельного комплекта используют опоки и различные приспособления — наполнительные рамки щитки штыри скобы и т. д.
Поэтому наряду с понятием «модельный комплект» употребляют понятие «формовочный комплект» т.е. полный комплект оснастки необходимый для получения разовой формы.
Модельный комплект должен удовлетворять следующим основным требованиям:
) обеспечивать получение отливки определенной геометрической формы и размеров;
) обладать высокой прочностью и долговечностью т.е. обеспечивать изготовление необходимого числа форм н стержней;
) быть технологичным в изготовлении;
) обладать минимальной массой и бьггь удобным в эксплуатации;
) иметь минимальную стоимость с учетом стоимости ремонта;
) сохранять точность размеров и прочность в течение определенного времени эксплуатации.
Требуемые точность прочность и долговечность модельного комплекта зависят от условий производства: единичного серийного массового. В единичном и мелкосерийном производстве чаще всего используют деревянные модельные комплекты; в массовом и крупносерийном производстве металлические модельные комплекты которые хотя и дороже но значительно долговечнее деревянных.
В серийном производстве во многих случаях успешно применяют модели из пластмасс например эпоксидных смол а также из гипса и цемента [1 с. 4].
В курсовой работе необходимо разработать технологическую оснастку для изготовления отливки «Корпус малый 342.05.01.072-А»: модель верха и низа плиту подмодельную верха и низа.
ЗАКЛЮЧЕНИЕ.docx
Была произведена оценка технологичности литой детали выбор и обоснование способа формовки определен тип и обоснован выбор материала модели.
Разработаны литейно-модельные указания: определена плоскость разъема и положение отливки в форме назначены припуски на механическую обработку определена величина литейных уклонов и размеры стержневых знаков.
Так же была определена конструкция и рассчитаны основные размеры моделей.
Были разработаны следующие чертежи: чертеж отливки чертеж моделей «верха» и «низа» чертеж подмодельной плиты.
Разработанная в результате данной курсовой работы технологическая оснастка позволяет получить оливку «Корпус малый 342.05.01.072-А» с заданными требованиями.
!2СОДЕРЖАНИЕ.docx
Обоснование выбора способа формовки10
1 Конструктивные элементы для метода «Сейацу» 11
2 Формовочные линии по методу «Сейацу» 12
Обоснование выбора материала модели15
1 Требования предъявляемые к модельной оснастке16
Разработка модельно-литейных указаний18
1 Обоснование выбора плоскости разъема и положения отливки в форме18
2 Определение припусков на механическую обработку19
3 Определение величины литейных уклонов20
4 Определение размеров стержневых знаков20
Определение конструкции и расчет основных размеров модели22
Расчет основных размеров промодели24
Список использованной литературы27
5 ОПРЕДЕЛЕНИЕ КОНСТРУКЦИИ И РАСЧЕТ ОСНОВНЫХ РАЗМЕРОВ МОДЕЛИ.docx
При разработке чертежа модельно-литейных указаний устанавливают величину линейной усадки которую необходимо учитывать при изготовлении модельного комплекта для данной отливки. Величина усадки материала ВЧ45 по ГОСТ 7293–85 равна 1%. Назначаем припуски на механическую обработку по ГОСТ 26645–85. Исходя из этого рассчитываем высоту верхней и нижней модели.
Высота верхнего стержневого знака определяется как сумма высоты верхнего знака () и технологического зазора ():
Высота верхней модели определяется как сумма высоты детали () и припуска на механическую обработку () умноженная на процент усадки литейного сплава:
Рисунок 5.1 — Эскиз верхнего знака и модели верха
Высота нижнего стержневого знака () берется равной высоте знака низа ():
Высота нижней модели () определяется как сумма высоты детали и припуска на механическую обработку () умноженная на процент усадки литейного сплава:
Рисунок 5.2 — Эскиз модели низа и нижнего знака
3 ОБОСНОВАНИЕ ВЫБОРА МАТЕРИАЛА МОДЕЛИ.docx
Учитывая крупносерийное производство литой детали «Корпус малый 342.05.01.072-А» и автоматизированную машинную формовку методом «Сейацу» материалом модели выбираем серый чугун марки СЧ20 ГОСТ 1412-85.
Чугуны широко применяются для изготовления оснастки. Высокая прочность и износостойкость хорошая обрабатываемость гладкая поверхность после обработки невысокая стоимость чугуна способствуют широкому его применению. Чугун является основным материалом для изготовления моделей н стержневых ящиков модельных плит для оболочкового литья а также при пескодувном пескострельном и пескомётном методах формовки и изготовления стержней. Чугун применяется для изготовления опок сушильных плит кондукторов для зачистки стержней. Чугунную модельную оснастку подвергают термообработке и естественному старению [1 с. 16].
Металлическая оснастка по сравнению с деревянной имеет большую начальную размерную точность которую она сохраняет в течение длительной эксплуатации. Повышенная чистота рабочих поверхностей литейных моделей и стержневых ящиков по сравнению с деревянными способствует получению отчетливого отпечатка модели в форме и стержней с четко выраженными очертаниями.
От качества и стоимости литейной оснастки зависит не только качество и стоимость отливок но также и стоимость обработки отливок и эксплуатация литых деталей. Машинная формовка и новые технологические процессы (оболочковое литье литье под давлением и др.) создают износ поверхности увеличивают потребность в металлической оснастке и предъявляют к ней новые требования.
Металлическую модельную оснастку по назначению делят на две группы:
-я группа — это приспособления которые используют при изготовлении формы для отливок только одного определенного наименования. К таким приспособлениям относятся модельные плиты стержневые ящики драйеры и калибры для их подгонки кондукторы для зачистки стержней шаблоны и приспособления для контроля н сборки стержней.
-я группа — это приспособления которые можно использовать при изготовлении форм для отливок разного наименования. К ним относятся опоки жакеты допрессовочные головки подоночные и сушильные плиты штыри для сборки форм скобы для скрепления частей формы и т.д.
В крупносерийном и массовом производстве отливок наиболее полный комплект металлической модельно-опочной оснастки включает следующие объекты: 1- модельные плиты 2- стержневой ящик 3- газоотводные плиты 4- сушильные плиты плоские стандартные и фасонные драйеры 5- приспособления для зачистки стержней – кондукторы 6- инструмент стандартный - измерительный и специальный для проверки стержней модели холодильника 8- опоки или жакеты для стержневых форм и для безопочной заливки 9- инструмент и приспособления для сборки форм 10- подопочные плиты 11- подпрессовочные плиты 12- штыри и скобы для соединения частей формы. Комплект металлический модельно-опочной оснастки в зависимости от вида разовой формы метода изготовления формы и сложности отливки может включать разное число объектов различного назначения. Чем сложнее отливка тем большее число объектов входит в комплект модельно-опочной оснастки [1 с. 12].
1 Требования предъявляемые к модельной оснастке
Прежде всего точность изготовления модельной оснастки должна быть значительно выше требуемой точности изготовления по данной оснастке отливки.
Требования по точности исполнения моделей стержневых ящиков опок модельных плит изложены в соответствующих ГОСТах и нормалях. ГОСТом 11961-66 установлены три класса точности обработки рабочих поверхностей моделей и стержневых ящиков соответственно принятым классам точности изготовления отливок.
В течение эксплуатации объекты модельной оснастки должны сохранять размерную точность. Поэтому материал объектов должен быть износостойким. При массовом производстве отливок необходимо иметь дублеры модельно- опочной оснастки.
Модельная оснастка должна быть по возможности дешевой. Одним из факторов снижающих стоимость оснастки является ее технологичность в изготовлении.
ЛИТЕРАТУРА.docx
Исагулов А.З. Проектирование литейной оснастки А.З. Исагулов С.Б. Кузембаев С.Г. Канунникова. – Караганда: КарГТУ 2003. – 140 с.
Кукуй Д.М. Теория и технология литейного производства Д.М. Кукуй В.В. Скворцов В.Н. Эктова. – Минск: Дизайн ПРО 2000. – 416 с.
Буданов Е.Н. Современное производство по Сейатцу-процессу сложных отливок типа «Корпус электродвигателей» Е.Н. Буданов. Литейщик России. – 2006. – №12. – С. 11–15.
Проектирование литейных цехов. Машины литейного производства: учебное пособие А.Н. Болдин [и др.]. – Москва: МГИУ 2010. – 435 с.
Кечин В.А. Проектирование и производство литых заготовок: учеб. пособие В.А. Кечин Г.Ф. Селихов А.Н. Афонин. – Владимир: Владим. гос. ун-т 2002. – 228 с.
Государственный стандарт союза ССР. Отливки из металлов и сплавов. Допуски размеров массы и припуски на механическую обработку: ГОСТ 26645-85. – Введ. 01.07.87. – Москва: ИПК Изд-во стандартов 1994. – 56 с.
4 РАЗРАБОТКА ЛИТЕЙНО-МОДЕЛЬНЫХ УКАЗАНИЙ.docx
1 Обоснование выбора плоскости разъема и положения отливки в форме
При определении плоскости разъема формы следует избегать сложных криволинейных линий и плоскостей так как это усложняет технологию изготовления оснастки формы и отрицательно сказывается на себестоимости и качестве отливки [5 с. 171].
Отливку «Корпус малый 342.05.01.072-А» располагаем в двух полуформах с линией разъема проходящей перпендикулярно оси симметрии (см. рис. 1.1) что позволит повысить точность и качество отливки засчет уменьшения вероятности брака по перекосу.
Данная плоскость разъёма обеспечивает и соблюдает ряд необходимых условий:
- направленное затвердевание и питание всех нижележащих элементов отливки через вышележащие из прибылей (наиболее массивные узлы отливки размещены в верхней части формы);
- наиболее простое оформление литниковой системы (ЛПС подводит сплав к полости формы по кратчайшему пути сплав поступает в форму спокойно не фонтанирует и не размывает стержни и выступающие части полости формы);
- преимущественный верхний отвод газов из стержней (через верхние знаковые части) для устранения образования газовых раковин;
- тонкие стенки и цилиндрическая часть располагаются при заливке вертикально что позволяет получать одинаковое качество отливки во всех сечениях;
- сборка формы и извлечение модели осуществляется без особых затруднений вследствие отсутствия выступов и поднутрений;
- надежное крепление стержней что исключает их деформацию под действием сил тяжести и давления жидкого металла.
2 Определение припусков на механическую обработку
По принятому технологическому процессу литья (литье в сырые песчаноглинистые формы) типу заливаемого сплава (ВЧ45) и наибольшему габаритному размеру отливки (1835 мм) принимаем степень точности поверхностей равную 12 [6 с. 36 табл. 11].
По степени точности поверхности назначаем ряд припуска отливки равный 6 [6 с. 43 табл. 14].
На основании принятого технологического процесса получения отливки наибольшего габаритного размера и типа сплава принимаем класс размерной точности отливки равный 9 [6 с. 32 табл. 9].
По отношению наименьшего размера элемента отливки к наибольшему (толщины к высоте элемента отливки) намеченной термообработке (отсуствует) и типу формы (разовые) определяется степень коробления элементов отливки равная 8 [6 с. 35 табл. 10].
Таблица 1 – Значения для определения припуска на механическую обработку
Номинальный размер мм
Вид механической обработки
На основании принятого технологического процесса получения отливки массы отливки и типа сплава принимаем класс точности массы отливки равный 10 [6 с. 40 табл. 13].
Точность отливки 9-8-12-10 ГОСТ 26645-85
3 Определение величины литейных уклонов
Величины литейных уклонов определяем по ГОСТу 3212-92. Величины формовочных уклонов показаны на рисунке 4.1.
Рисунок 4.1 – Формовочные уклоны
4 Определение размеров стержневых знаков
Размеры стержневых знаков определяем по ГОСТу 3212-92. Для данной отливки размеры стержневых знаков показаны на рисунке 4.2.
Рисунок 4.2 – Размеры стержневых знаков
Рекомендуемые чертежи
- 25.01.2023
- 25.01.2023
- 25.01.2023
- 14.06.2023
- 25.01.2023