Проектирование технологической оснастки для обработки детали на металлорежущем станке



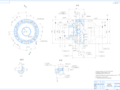
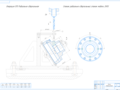
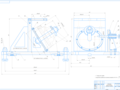
- Добавлен: 04.11.2022
- Размер: 1 MB
- Закачек: 0
Узнать, как скачать этот материал
Подписаться на ежедневные обновления каталога:
Описание
Курсовой проект - Проектирование технологической оснастки для обработки детали на металлорежущем станке
Состав проекта
![]() |
![]() ![]() ![]() |
![]() ![]() ![]() |
![]() ![]() ![]() |
![]() ![]() ![]() |
![]() ![]() ![]() |
![]() ![]() ![]() ![]() |
![]() ![]() ![]() ![]() |
Дополнительная информация
Контент чертежей
Чертеж.cdw

Эскиз операционный.cdw

Рекомендуемые чертежи
- 14.06.2023
Свободное скачивание на сегодня
Обновление через: 13 часов 20 минут