Разработать технологический процесс изготовления вала редуктора поворота колонки




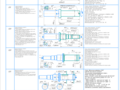
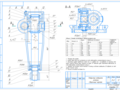
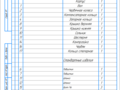
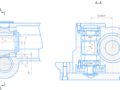
- Добавлен: 24.01.2023
- Размер: 9 MB
- Закачек: 0
Описание
Состав проекта
![]() |
![]() |
![]() ![]() ![]() |
![]() ![]() ![]() |
![]() ![]() ![]() |
![]() |
![]() ![]() ![]() ![]() |
![]() ![]() ![]() ![]() |
![]() ![]() ![]() ![]() |
![]() ![]() ![]() ![]() |
![]() ![]() ![]() |
![]() |
![]() |
![]() ![]() ![]() ![]() |
![]() ![]() ![]() |
![]() ![]() ![]() |
![]() ![]() ![]() |
![]() ![]() ![]() ![]() |
![]() |
![]() |
Дополнительная информация
Чертеж А3.cdw

Сборка А3.cdw

Спецификация.cdw

ЧертежА2.cdw

база 1.frw

Осн и всп базы.frw

Цепь.frw

Деталь.frw

база 2.frw

Рекомендуемые чертежи
- 24.01.2023