Разработать операционный технологический процесс изготовления детали ось




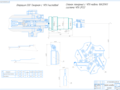
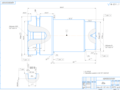
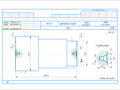
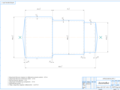
- Добавлен: 24.01.2023
- Размер: 2 MB
- Закачек: 1
Описание
Состав проекта
![]() |
![]() ![]() ![]() |
![]() ![]() ![]() ![]() |
![]() ![]() ![]() ![]() |
![]() ![]() ![]() ![]() |
![]() ![]() ![]() ![]() |
![]() |
![]() ![]() ![]() |
![]() |
![]() ![]() ![]() |
Дополнительная информация
Чертеж.cdw

Базы.cdw

Заготовка.cdw

Сталь 40Х ГОСТ 4543-71
Допустимая величина смещения по поврехности разъема штампа - 0
Допустимая величина остаточного облоя - 1
Величина высоты заусенца - 5 мм.
Допустимые отклонения по изогнутости - 1
Штамповочные уклоны - 7
Радиус закруглений наружных поверхностей - 4
КН.cdw

КП 15.02.08.014.2015 КН
Операция 030 Токарная с ЧПУ (чистовая)
Резец 2103-0713 Т15К6 ГОСТ 20872-80
КЭ.cdw

* Размеры для справок
* Размер для справок
ПЗ Стаценко.docx
ГОРЛОВСКИЙ КОЛЛЕДЖ ПРОМЫШЛЕННЫХ ТЕХНОЛОГИЙ И ЭКОНОМИКИ
по дисциплине "Технология машиностроения
на тему: «Разработать операционный технологический процесс изготовления
КДК 500.03.01.001 «Ось»
Студента 3 курса группы 3зТ
направление подготовки
02.08 «Технология машиностроения»
Руководитель: Анастасьев А.В.
г. Горловка 2016 год
Курсовой проект содержит: 30 страниц 6 таблицы 7 рисунков 9 источников 22 формулы 1 приложение.
Объектом курсового проектирования является технологический процесс используемый для изготовления детали среднего машиностроения с максимальным внедрением станков с ЧПУ.
Целью курсового проектирования является разработка технологического процесса изготовления детали типа «Ось» с использованием компьютерных систем применение станков с ЧПУ; закрепление полученных знаний и умений в ходе изучения дисциплины «Технология машиностроения».
Предметом курсового проекта является разработка и оформление технической документации для изготовления детали КДК 500.03.01.001 «Ось».
Курсовой проект состоит из разделов в котором рассмотрены следующие вопросы:
-анализ технологичности конструкции детали и определение соответствующего типа производства;
-определение возможных и наиболее эффективных методов получения заготовки;
-разработка операционного технологического процесса изготовления детали и выбор соответствующего оснащения для его реализации;
-определение режимов резания и норм времени на операции механической обработки и разработка управляющей программы для станков ЧПУ.
ЗАГОТОВКА ДЕТАЛЬ ОПЕРАЦИЯ ПЕРЕХОД УСТАНОВ МЕХАНИЧЕСКАЯ ОБРАБОТКА ИНСТРУМЕНТ РЕЖИМЫ РЕЗАНИЯ НОРМЫ ВРЕМЕНИ ОСНАСТКА ПРИСПОСОБЛЕНИЯ СИСТЕМА ЧИСЛОВОГО ПРОГРАММНОГО УПРАВЛЕНИЯ (СЧПУ)
1 Анализ технологичности конструкции детали
2 Определение типа производства и его характеристика
ТЕХНОЛОГИЧЕСКАЯ ЧАСТЬ
1 Выбор метода получения заготовки
2 Разработка маршрутного технологического механической процесса обработки детали
3 Выбор оборудования и средств технологического оснащения
3.1 Выбор станочного оборудования и приспособления
3.2 Выбор режущего инструмента
3.3 Выбор методов контроля
4 Выбор и расчет режимов резания
5 Нормирование операций технологического процесса
6 Проектирование управляющей программы для обработки детали на станках с программным управлением
Список использованной литературы
Приложение А – Карта кодирования информации
Машиностроения является главным технологом всех отраслей народного хозяйства. В связи с этим оно должно на базе новейших достижений науки и техники разрабатывать новые технологические процессы для осуществления которых нужно создавать и выпускать необходимые для промышленности изделия отвечающие своему служебному назначению при наименьшей себестоимости.
Технология машиностроения ХХI века – это комплексная наука изучающая действующие при изготовлении машин закономерности для их использования в производстве новых деталей и машин заданного качества на основе применения компьютерной техники и компьютерных систем автоматизированного проектирования. Машиностроение – самая распространенная и универсальная специальность необходимая на любых предприятиях машиностроения приборостроения ремонтных и многих других отраслей промышленности.
В настоящее время в машиностроительной промышленности разработаны теоретические основы технологии машиностроения научно обоснованы типовые технологии прогрессивной обработки различных деталей машин сформированы основные принципы проектирования технологических процессов наиболее производительной обработки деталей и сборки из них узлов и механизмов. Разработаны системы автоматизированного проектирования технологической подготовки производства (САПР ТПП) для различных типов производств в том числе для гибких производственных систем (ГПС). Внедрение новых технологий и современной техники в производство невозможно без высококвалифицированных специалистов обладающих передовыми знаниями и навыками для приобретения которых и служит курсовое проектирование как первая ступень применения полученных знаний на практике.
В курсовом проекте была рассмотрена деталь КДК 500.03.01.001 «Ось» предназначенная для поддержания вращающихся частей и не участвующая в передаче вращающего или крутящего момента. Деталь «Ось» относится к деталям типа вращения.
Для изготовления данной детали используем сталь 40Х ГОСТ 4543-71. Химические и механические свойства выбраны по [1;с. 160] и приведены в табл. 1.1; 1.2.
Таблица 1.1 – Химический состав стали %
Таблица 1.2 – Механические свойства стали
Предел прочности при растяжении
Относительное удлинение
Относительное сужение
Содержание легирующих элементов оказывают значительное влияние на свойства стали. В результате термообработки – улучшения – повышаются пластичность и ударная вязкость стали при этом прочность и твердость металла сохраняют хорошие показатели.
Годовая программа выпуска – 18000 шт.
Чертежом детали предусмотрены следующие требования:
радиальное биение 65 75h6 относительно оси центров не более 006мм;
радиальное биение 90g6 относительно оси центров не более 004мм;
радиальное биение канавки 808h9 относительно 90g6 не более 006 мм;
Основными конструкторскими базами которые определяют положение детали в изделии являются цилиндрические поверхности 90 65g6. Они определяют точность установки «Оси» в расточках стенок коробки скоростей что отображено на чертеже повышенными требованиями к радиальному биению этих поверхностей.
Технологическими базами являются центровочные отверстия и ось центров.
Деталь «Ось» имеет следующие конструктивные элементы:
шейки оси предназначены для ориентирования подшипника;
канавка предназначена для установки стопорных колес резиновых прокладок;
резьбовое центровочное отверстие предназначено для транспортировки детали;
лыска служит для закрепления деталей при помощи клина или шпонки.
Деталь достаточно жесткая имеет удобные базовые поверхности и не вызывает особых технологических трудностей при обработке.
Простота конструктивных форм и размеров детали жесткость конструкции надежность технологических баз и жесткость крепления под обработку обеспечивает стабильную и точную обработку. При этом может использоваться высокопроизводительное оборудование и оснащение. Например для токарной обработки могут применяться токарные станки с ЧПУ.
Простота конструктивных элементов детали позволяет наиболее продуктивно и точно обработать поверхности детали применением наиболее простых относительных движений инструмента и заготовки: прямолинейного поступательного и вращательного движений.
Заданная деталь имеет нормализованы диаметры и длины регламентированы ГОСТ 6636-69 в основном из рядов Rа20 Rа40 (например 16005; 65 фаска 2×45º).
Наиболее ответственные поверхности 65g6 90g6 75h6 ограничены более жесткими допусками которые определены условиями работы детали. Однако они не выходят за пределы экономической точности и получаются чистовым точением.
Для снятия внутренних напряжений деталь подвергается термической обработке – улучшению.
Вывод: Конструкция детали технологична т.к. изготавливается штамповкой материал детали хорошо обрабатывается резанием конфигурация детали позволяет её обработать на серийно выпускаемых станках токарной группы точность и шероховатость большинства поверхностей получаются на станках с нормальной точностью отдельные поверхности детали требуют дополнительных операций на серийно выпускаемых станках нормальной точности.
Согласно ГОСТ 14.201-83 необходимо провести количественную оценку технологичности детали. Технологичность конструкции изделия оценивают количественно с помощью показателей а именно:
)По коэффициенту унификации:
Где Qун.э - количество унифицированных элементов детали;
Qоб.э - общее количество элементов
Так как Кун = 069> 06 то по этому показателю деталь технологична.
)По точности размеров
Если квалитетах точности размеров поверхностей не выше 6 - го то деталь считается технологичной.). Данная деталь имеет самый высокий квалитет точности обработки детали – шестой 65g6 90g6 75h6 - по этому показателю деталь технологична.
)По шероховатостью поверхности
Если обработка детали не требует доводочных операций (суперфиниш хонингование притирка) то по этому показателю деталь технологична
На основании качественной и количественной оценок технологичности детали следует - заданная деталь технологична.
2 Определение типа производства
Перед началом технологического проектирования устанавливают тип производства единичное серийное или массовое. Тип производства (единичное серийное или массовое) характеризуется номенклатурой и объемом выпуска изделий (годовой производственной программой) их массой и габаритными размерами а также другими признаками
Исходя из полученных данных – Мд =6 кг и Nгод – 18000выбираем серийное производство.
Серийное производство тип организации производства характеризуется одновременным изготовлением на предприятии широкой номенклатуры однородной продукции выпуск которой повторяется в течение длительного времени. Наибольшее распространение такой тип имеет в машиностроении и металлообработке. Выпуск продукции производится по продукту - сериями а по отношению к деталям - партиями. Изготовление серий изделий одного типоразмера обычно повторяется через регулярные промежутки времени. При повторных запусках серий машин часто вносятся изменения в конструкторскую и технологическую подготовку производства организацию рабочих мест повышается квалификация рабочих разрешается унифицировать конструкции деталей изделий добиваться типизации технологических процессов и оснастки.
При серийном типе производства обычно применяют универсальные специализированные агрегатные и другие металлорежущие станки. При выборе металлорежущего оборудования специального или специализированного дорогостоящих приспособлений вспомогательного инструмента необходимо производить расчеты затрат и сроки окупаемости а также - ожидаемый экономический эффект от использования технологической оснастки.
На выбор метода получения заготовки оказывают влияние: материал детали; ее назначение и технические требования на изготовление; объем и серийность выпуска; форма поверхностей и размеры детали.
Оптимальный метод получения заготовки определяется на основании всестороннего анализа названных факторов и технико-экономического расчета технологической себестоимости детали. Метод получения заготовки обеспечивающий технологичность изготовляемой из нее детали при минимальной себестоимости последней считается оптимальным.
Исходя из необходимости максимального приближения формы и размеров заготовки к параметрам готовой детали следует выбрать метод объемного горячего штампования.
Припуски на механическую обработку и допуски на изготовление штамповок регламентированы ГОСТ 7505-89 и зависят от массы заготовки точности изготовления группы стали степени сложности исходного индекса размеров и шероховатости обрабатываемых поверхностей.
Расчётная масса поковки:
где Мд – масса детали Мд = 236 кг
Кр – расчетный коэффициент
Кр = 13 15 [2 с 31 т 20]
Учитывая что поковку будем получать на прессах определяем класс точности Т4 [2; с.28; т.19]. Группа стали по содержанию углерода (С = 040%) М2 [2; с.8; т.1]
Определяем степень сложности:
где Мф – масса фигуры в которую вписывается поковка
где Vфиг – объем фигуры;
j - удельный вес гсм3 (j =785)
где Dфиг – диаметр фигуры;
Lфиг – длина фигуры.
Так как С=084 то принимаем С1 [2; c.30]
Конфигурацию разъема штампа выбираем (П) плоскую.
Для Мп.р.=9 кг; Т4; М2; С1 определяем исходный индекс – 13 [2 т.2].
Припуски и допуски выбираем по ГОСТ 7505-89.
Таблица 2.1 – Расчет припусков и допусков
Размер поверхности мм
Припуск на строну мм
Размер заготовки с допуском мм
Допустимая величина смещения по поверхности разъема штампа – 08 мм [2; с.13; т.9];
Допустимая величина остаточного облоя – 10 мм [2; с.13; т.10];
Величина высоты заусенца – 5 мм [2; с.14];
Допустимые отклонения по изогнутости – 10 мм [2; с.15; т.13];
Штамповочные уклоны - 7 [2; с.17; т.18];
Радиус закруглений наружных элементов – 4025 мм.
Определяем коэффициент использования материала:
где Мпок – масса поковки кг
где Vпок – объем поковки;
Масса полученной заготовки рассчитывается путем определения масс элементарных фигур на которые можно распределить заготовку:
Расчетный коэффициент использования материала для заготовок полученных методом штамповки больше 06. Поэтому заготовка выбрана верно. Заготовку детали можно выполнить на молоте или прессе.
Таким образом принимаем штамповку на прессе КГШП630.
Рисунок 2.1 Эскиз заготовки детали
Технологический маршрут обработки разрабатывается в целях выбора общего плана обработки определение содержания технологического процесса выбора типов станков и технологической оснастки.
Разработку технологического плана обработки выполняем на основании технических требований чертежа вида заготовки размеров и массы детали типового технологического процесса.
В первую очередь обработке подлежат поверхности которые планируется использовать как технологические базы под последующую обработку. Затем обрабатываются поверхности с наибольшим припуском с целью выявления дефектов заготовки. Чистовые и отделочные операции выполняются в конце технологического процесса. Сочетание черновой и чистовой обработки на одном станке приводит к снижению точности обработки. Поверхности связанные точностью взаимного положения обрабатывают при одном установе. Операции обработки резанием необходимо связывать с термообработкой слесарными операциями и техническим контролем.
Одновременно с разработкой маршрутного технологического плана обработки детали необходимо принять решение в соответствии моделей станков на которых планируется выполнять технологические операции.
На токарные и сверлильную операции принимаем станки с ЧПУ что обусловлено типом производства (среднесерийное) а также конфигурацией заготовки имеющей в конструкции элементы для обработки которых необходимо использование циклов обработки что наиболее целесообразно реализовать на станках с ЧПУ.
Последовательность выполнения операций (маршрутный технологический план) обработки детали приведен в таблице 2.2.
Рисунок 2.2 Базы для обработки детали
Таблица 2.2 – Маршрутный технологический план обработки
Наименование операции
Обрабатываемые поверхности
Получение штампованной заготовки
Фрезерно-центровальная
Фрезерование торцев и сверление центральных отверстий
Токарная черновая с ЧПУ
Точение наружных поверхностей
Центр А-1-4-Н ГОСТ 8742-75
Слесарная обработка заусенцев
Закалка + высокий отпуск до НВ241 285
Шлифование центровочных отверстий
Центр 7032-0017 Морзе 2
Токарная чистовая с ЧПУ
Точение наружных поверхностей; обработка фасок канавок
Сверление отверстия нарезание резьбы
Патрон резьбонарезной 191221141А
Шлифование наружной поверхности
Центр 7032-0032 ГОСТ 13214-79
Хомутик 7107-0041 ГОСТ 2578-70
После разработки маршрута обработки проводится расчет межоперационных припусков (МУ).
Таблица 2.3 Межоперационные припуски
Обрабатываемый размер детали
Шероховатость Ra мкм.
Припуск на обработку мм.
Размеры детали с допуском
3 Выбор оборудования
Выбор оборудования является одной из главных задач при разработке технологического процесса механической обработки заготовки. От правильного его выбора зависит производительность изготовления детали экономное использование производственных площадей автоматизации ручного труда и в итоге себестоимость изделия. Выбор каждого вида станка должен быть экономически обоснованным.
Таблица 2.4 Оборудование для механической обработки заготовки
0 Фрезерно-центровальная
14-0007 ГОСТ 24359-80
14-0008 ГОСТ 24359-80
17-0008 ГОСТ 14952-75
02-0084 ГОСТ 18355-73
5 Токарная с ЧПУ (черновая)
А-1-4-Н ГОСТ 8742-75
03-0713 Т5К10 ГОСТ 20872-80
02-0053 (917) h10 ГОСТ 18355-73
02-0049 (766) h10 ГОСТ 18355-73
0 Токарная с ЧПУ (чистовая)
03-0713 Т15К6 ГОСТ 20872-80
02-0053 h8 ГОСТ 18355-73
02-0049 h8 ГОСТ 18355-73
1 221 141А ТУ 2-035-975-85
20-1933 ГОСТ 3266-81
Патрон резьбонарезной
Патрон быстросменный
Калибр-пробка резьбовая
61-3112 ГОСТ 17756-72
5-2301-1007 ОСТ 2И20-2-80
23-0502 ГОСТ 12489-71
33-0910 Н7 ГОСТ 14810-69
23-0007 ГОСТ 17026-71
3.1 Выбор станочного приспособления
Выбор станков при проектировании технологического процесса механической обработки детали выполняется из следующих соображений:
- выбранный станок должен обеспечить выполнение технических требований которые предъявляются к точности размеров обрабатываемой детали ее форме взаимного расположения поверхностей и шероховатости
- соответствие рабочей зоны станка размерам устанавливаемой заготовки
- соответствие станка по производительности заданному типу производства
- мощность жесткость и кинематические возможности станка должны обеспечить обработку детали на оптимальных режимах резания с наименьшей затратой времени и минимальной себестоимостью.
Далее рассмотрим паспортные данные токарного станка с ЧПУ.
Токарный станок 16К20Ф3С32 предназначен для токарной обработки наружных (диаметром до 400 мм) и внутренних поверхностей деталей (длиной до 1000 мм) со ступенчатым и криволинейным профилем в осевом сечении.
Устройство ЧПУ станка обеспечивает движение формообразования изменение значений подач переключение частот вращения шпинделя индексацию резцовой головки и нарезание резьбы по программе. Применяется в условиях единичного и мелкосерийного производства в цехах машиностроительных заводов и других отраслях промышленности.
Станок модели 16К20Ф3С32 оснащен системой программного управления «2Р22».
Основные конструктивные особенности станка:
широкий диапазон регулирования скоростей шпинделя и подач жесткость основных узлов станка;
перемещение пиноли задней бабки и зажима патрона механизировано;
повышены нормы точности станка.
Таблица 2.3 - Паспортные данные станка 16К20Ф3С32
Наименование параметра
Наибольший диаметр обрабатываемого изделия над станиной мм
Продолжение таблицы 2.3
Наибольший диаметр обрабатываемого изделия над суппортом мм
Диаметр отверстия в шпинделе мм
Наибольшая длина обрабатываемого изделия мм
Предельный диаметр сверления в стали мм
Мощность двигателя главного движения кВт
Количество рабочих скоростей шпинделя
Пределы чисел оборотов шпинделя обмин
Диапазон скоростей шпинделя устанавливаемый вручную обмин
Наибольшее перемещение суппорта: продольное поперечное мм
Максимальная скорость продольной подачи при нарезании резьбы мммин
Пределы шагов нарезаемых резьб мм
Диапазон скоростей продольныхпоперечных подач мммин
Количество позиций на поворотной резцедержке (число инструментов в револьверной головке)
Обозначение системы ЧПУ
Мощность двигателя главного привода кВт
Масса станка с ЧПУ кг
Рисунок 2.3 Токарный станок 16К20Ф3
При разработке технологического процесса механической обработки заготовки выбор режущего инструмента его вида конструкции и размеров предопределяется методами обработки свойствами обрабатываемого материала требуемой точностью обработки и качества обрабатываемой заготовки. Правильный выбор режущей части инструмента имеет большое значение для повышения производительности и снижения себестоимости обработки. Для обработки детали КДК 500.03.01.001 «Ось» используется стандартный и специальный режущий инструмент режущая часть которого изготовлена из титановольфрамовых твердых сплавов Т5К10 Т15К6 быстрорежущей стали Р6М5.
3.3 Выбор измерительного инструмента
Технические измерения являются одной из важнейших основ производства ни одна технологическая операция не выполняется без измерений размеров. При проектировании технологического процесса механической обработки заготовки для межоперационного и окончательного контроля обрабатываемых поверхностей используется стандартный и специальный измерительный инструмент. В серийном производстве применяется универсальный измерительный инструмент (штангенциркуль калибр-скоба калибр-пробка).
Штангенциркуль – это универсальный инструмент для измерения с точностью до 01 или 001 мм внутренних и наружных размеров а также глубины отверстий. Что касается конструкции штангенциркуля то в качестве примера рассмотрим наиболее популярный ШЦ-I. Данный инструмент представляет собой измерительную линейку с верхними и нижними губками левая половина которых закреплена неподвижно а правая передвигается на подвижной рамке. Верхние губки резцы которых смотрят наружу используются для замеров внутреннего диаметра нижние с резцами внутрь – для наружных диаметров и линейных размеров. Передвижная рамка имеет фиксатор и шкалу нониуса для замеров с точностью до 01 мм. На конце линейки также имеется глубиномер для измерения глубины отверстий.
Штангенциркуль является дорогостоящим и точным инструментом поэтому бережное обращение с ним должно быть основным правилом работы.
Рисунок 2.4 Штангенциркуль
Смазочно-охлаждающие жидкости (СОЖ) применяют главным образом для отвода тепла от режущего инструмента. Они снижают температуру в зоне обработки и тем самым повышают стойкость режущего инструмента улучшают качество обрабатываемой поверхности и предохраняют от коррозии режущий инструмент и обрабатываемую заготовку.
В общем случае использование СОЖ обеспечивает высочайший уровень качества итоговой продукции безопасность и благополучные условия на производстве а также отличные показатели эффективности.
Так для черновых и чистовых операций на токарных станках с ЧПУ принимаем СОЖ №17 (петралатум эмульсольный окисленный - 224% асидол масляный - 5% масло индустриальное 20 - 623% едкий натр - 35% вода - 68%); для сверлильной – состав №46 (сульфофрезол 90% керосин - 10%).
Одним из важнейших вопросов при проектировании технологического процесса обработки является вопрос установления технической нормы времени. Техническую норму времени определяем на основе расчетов режимов резания с учетом полного использования свойств режущего инструмента и производственных возможностей оборудования. Ниже приведены примеры расчета режимов резания и норм времени для нескольких операций.
4.1 Выбор и расчет режимов резания для операции 010 – Токарная с ЧПУ (черн)
Резец контурный 2103-0713 Т5К10 ГОСТ 20872-80;
Операционный эскиз (рисунок 2.5).
Рисунок 2.5 Операционный эскиз – 015 Токарная с ЧПУ (черновая)
Определяем глубину резания на основании чертежа заготовки и выбранных ранее межоперационных припусков.
Подачи для чернового наружного точения определяем по [3 к.1 с.36]
Выбираем скорость резания по [3 к.6 с.44]
Тогда действительная частота вращения шпинделя равна:
Корректируем по паспорту станка n1=140 n2=150 n3=180 обмин.
Тогда действительная скорость резания равна Vд1=3607 ммин Vд2=403 Vд3=38 ммин.
Определяем мощность резания [3 с.48]
Мощность двигателя станка Nдв=10 кВт
рез Nст т.е. 56 85. Таким образом обработка возможна.
4.2. Выбор и расчет режимов резания для операции 025 – Сверлильная с ЧПУ
Метчик 2620-1933 ГОСТ 3266-81;
Операционный эскиз (рисунок 2.6).
Рисунок 2.6 Операционный эскиз – 025 Сверлильная с ЧПУ
Содержание переходов:
Сверлить отверстие 1;
Нарезать резьбу 4 (М20).
Выбираем подачу для сверления по [3 к.41 с.103]:
S=03-035 ммоб. Принимаем S=035 ммоб.
Выбираем скорость резания по [3 к.42 с.104]
Корректируем по паспорту станка n=350 обмин.
Тогда действительная скорость резания равна Vд=203 ммин.
)Выбираем режимы резания для нарезания резьбы [3 к.82 с.147]:
S=15 ммоб V=235 ммин n=250 обмин
Корректируем по паспорту станка: V=20 ммин n=250 обмин
Определяем минутную подачу:
Корректируем по паспорту станка мммин.
Мощность резания Nрез=34 кВт [3 к.82 с.147].
рез Nст т.е. 34425. Таким образом обработка возможна.
5.1. Нормирование операции 015 – Токарная с ЧПУ (черн)
Определяем основное время на обработку поверхностей:
где l – длинна обрабатываемой поверхности
l1 – величина врезания и перебега инструмента l1=8мм [4 с.379]
i - количество проходов.
Определяем вспомогательное время:
гдеtуст – время на установку и снятие детали tуст=17 мин [6 с.39];
tмв – машинное время tмв=019 мин [5 с.605].
Определяем оперативное время:
Определяем штучное время:
где tобс – время на обслуживание рабочего места и личные потребности tобс=10% [5 с.605]
Определяем подготовительно-заключительное время [5 с.605]:
5.2. Нормирование операции 025 – Сверлильная с ЧПУ
Определяем основное время на обработку поверхностей.
Определение основного времени:
l – длина обрабатываемой поверхности мм
l1 – величина врезания и перебега инструмента мм [5 с.369]
Основное время равно:
Определение вспомогательного времени.
где tуст = 240 мин. [9 с.54]
tмв=048 мин [5 с.607].
Вспомогательное время на измерение при обработке на станках с ЧПУ не учитываем.
Топ = То + Тдоп = 059+288=347 мин.
где tобс = 8% от оперативного времени на обслуживание рабочего места и личные нужды [3 с.607]
Подготовительно-заключительное время:
где Тп-з1 = 12мин. – время на комплекс приемов связанных с общей подготовкой к работе [3 с.606 табл.12]
Тп-з2 =14 мин.– время на выполнение дополнительных приемов [3 с.606]
Тп-з = 12 + 14= 26 мин.
Разработку управляющей программы осуществляем для операции 010 Токарная с ЧПУ. Обработка осуществляется на токарном станке с ЧПУ модели 16К20Ф3 с СЧПУ «2Р22».
Перемещения инструментов приведены в таблице 2.5. Циклограмма движения инструментов приведена на рисунке 2.6.
Текст УП на специальном бланке находится в приложениях (Приложение А).
Таблица 2.4. Технологические команды и координаты перемещения инструментов
Рисунок 2.7. Циклограмма движения инструмента
В ходе выполнения курсового проекта был разработан технологический процесс обработки детали КДК 500.03.01.001 «Ось». На основании чертежа детали был произведен анализ технологичности детали рассчитаны параметры заготовки составлен маршрутный процесс обработки детали выбраны припуски на обработку детали. Был осуществлен выбор оборудования режущего и вспомогательного инструмента. Приведены характеристики токарного станка с ЧПУ модели 16К20Ф3 с системой ЧПУ «2Р22».
Были проведены расчеты режимов резания и норм времени. В пояснительной записке подробно изложены расчеты для операций 010 – токарная с ЧПУ (черновая) и 040 – сверлильная с ЧПУ режимы резания и нормы времени для остальных операций приведены в технологическом процессе обработки детали.
Была составлена управляющая программа для операции 010 – токарная с ЧПУ. Бланк с управляющей программой приведен в приложениях.
СПИСОК ИСПОЛЬЗУЕМЫХ ИСТОЧНИКОВ
Марочник сталей и сплавов 2-е изд. доп. и испр.А.С. Зубченко М.М. Колосков. Под общей ред. А.С. Зубченко – М.:Машиностроение 2003г. 784с.
Поковки стальные штампованные. Допуски припуски и кузнечные напуски. ГОСТ 7505 – 89 М: 1990г.- 52с.
Общемашиностроительные нормативы режимов резания для технического нормирования работ на металлорежущих станках. Часть 1. М: машиностроение 1967г.- 416с.
Общемашиностроительные нормативы режимов резания для технического нормирования работ на металлорежущих станках. Часть 2. М: машиностроение 1974г.- 200с.
Справочник технолога-машиностроителя. В 2-х т. Т.1Под ред. А.Г. Косиловой и Р.К. Мещерякова 4-е изд. перераб. и доп.-М.: Машиностроение 1986г.-496с.
Справочник технолога – машиностроителя. В 2-х т. Т.2 Под ред. А.Г. Косиловой и Р.К. Мещерякова -4-е изд. перераб. и доп. –М.: Машиностроение 1986. – 496 с.
Общемашиностроительные нормативы режимов резания для технического нормирования работ на металлорежущих станках. Часть 3. М: ЦБНТ 1978г.- 360с.
Общемашиностроительные нормативы времени. Изд. 2-е. М: “Машиностроение” 1974 421 И. С. Добрыднев Курсовое проектирование по предмету Технология машиностроения” М: Машиностроение 1985г.- 184с.
Кузнецов Ю.И. и др. Оснастка для станков с ЧПУ: Справочник.-2-е изд. перераб и доп.-М.: Машиностроение.1980г.-512с.
Карта кодирования информации
Рекомендуемые чертежи
Свободное скачивание на сегодня
Другие проекты
- 24.04.2014