Конструирование переборной коробки




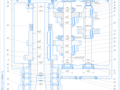
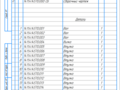
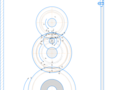
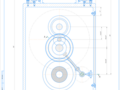
- Добавлен: 24.01.2023
- Размер: 1 MB
- Закачек: 0
Описание
Состав проекта
![]() |
![]() |
![]() |
![]() ![]() ![]() |
![]() |
![]() |
![]() ![]() ![]() ![]() |
![]() ![]() ![]() |
![]() ![]() ![]() ![]() |
![]() ![]() ![]() ![]() |
![]() |
![]() |
![]() ![]() ![]() ![]() |
Дополнительная информация
вид сверху силы.frw

Спецификация.spw

общий вид, вилка.cdw

вид сверху.cdw

главный вид. .cdw

Рекомендуемые чертежи
- 24.01.2023
- 24.01.2023
- 26.04.2019